Lean Coordinator Resume Samples
4.8
(142 votes) for
Lean Coordinator Resume Samples
The Guide To Resume Tailoring
Guide the recruiter to the conclusion that you are the best candidate for the lean coordinator job. It’s actually very simple. Tailor your resume by picking relevant responsibilities from the examples below and then add your accomplishments. This way, you can position yourself in the best way to get hired.
Craft your perfect resume by picking job responsibilities written by professional recruiters
Pick from the thousands of curated job responsibilities used by the leading companies
Tailor your resume & cover letter with wording that best fits for each job you apply
Resume Builder
Create a Resume in Minutes with Professional Resume Templates
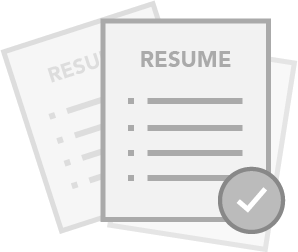
CHOOSE THE BEST TEMPLATE
- Choose from 15 Leading Templates. No need to think about design details.
USE PRE-WRITTEN BULLET POINTS
- Select from thousands of pre-written bullet points.
SAVE YOUR DOCUMENTS IN PDF FILES
- Instantly download in PDF format or share a custom link.
SC
S Cummings
Sandra
Cummings
321 Cummerata Extension
Chicago
IL
+1 (555) 204 7010
321 Cummerata Extension
Chicago
IL
Phone
p
+1 (555) 204 7010
Experience
Experience
Philadelphia, PA
Lean Coordinator
Philadelphia, PA
Feil, Haag and Fahey
Philadelphia, PA
Lean Coordinator
- Develop, plan and assist in implementation of strategic planning and lean strategy in all departments
- Help establish Formet Business Plan and Departmental Goals and Objectives; ensure that goals and objectives are met (People, Investor, and Customer)
- Educate our workforce on our Lean initiatives
- Lead a manufacturing planning activity through the product development/launch cycle
- This position will manage the lean and manufacturing engineering activities
- Manage without discrimination and personal bias, which includes race, creed or any prohibited grounds as outlined in Human Rights legislation
- Participate in the monthly Team Member meetings and provide timely feedback on issues and concerns
San Francisco, CA
Lean / Quality Coordinator
San Francisco, CA
Medhurst-Sawayn
San Francisco, CA
Lean / Quality Coordinator
- Establish and maintain product quality plans and control plans
- Audit processes to established control plans
- A culture that values opportunity for growth, development, and internal promotion
- Analyze data to predict potential problems and take preventive actions
- Group retirement savings program
- Health and wellness programs
- Highly competitive base pay
present
Chicago, IL
Lean Solutions, Portfolio Coordinator
Chicago, IL
Cole Inc
present
Chicago, IL
Lean Solutions, Portfolio Coordinator
present
- Use Lean principles to perform process reviews and aid in establishing standardized work procedures
- Monitor development of Standardized work documentation, material flow improvements, and progress tracking in areas assigned
- Facilitate and lead continuous improvement events that support team and employee development in Lean principals, tools, and concepts
- Develop programmes for record retention, continuous improvement and job training
- Conducts method analysis and improvements to work station design
- Develop programs for record retention, continuous improvement and job training
- Provide training and work instructions in the areas of, but not limited to, Health & Safety, TS 16949, ISO14001, job specific etc
Education
Education
Associate’s Degree in Technical Field
Associate’s Degree in Technical Field
Howard University
Associate’s Degree in Technical Field
Skills
Skills
- Relevant 3rd Level Qualification in a related discipline
- Plans work and carries out tasks without detailed instructions
- Prepares for problems and opportunities in advance
- Analyzes problems skillfully and uses logic to reach solutions
- Responds positively to instructions and procedures
- Able to work well with staff, co-workers, peers and managers
- Works effectively on projects that cross function with other departments
- Regularly procedures accurate, thorough and professional work
- Works hours necessary to complete assigned work
- Reliable and accountable for work assigned
6 Lean Coordinator resume templates
Read our complete resume writing guides
1
Lean Coordinator Resume Examples & Samples
- As the pivotal facilitator of the transformation to True Lean, develop and implement a site strategy that is aligned to the company standardised operating model
- Act as the change agent, coaching, mentoring and influencing at all levels
- Facilitate the education of the team in the principles, philosophies and tools
- Challenge management thinking and insist on appropriate practices such as taking decisions on fact based data, genchi genbutsu, panel review, team meeting governance etc
- Set-up, coordinate and direct the activities of the Jishuken team. Facilitate the execution of Jishuken activities, stabilisation and the transformation to True Lean. Set the pace of improvement with the site GM to deliver timely results and to ensure sustainability
- Continuous Improvement - coordinate the site continuous improvement activities using master schedule and 8 Step PPS. Report on progress in a timely manner internally and externally as appropriate
- Lead the opportunity assessment and other processes to methodically identify& prioritise site cost base improvements
- Coach and mentor team members to learn to see waste and develop the skill Internally
- Set the site up to succeed through implementation of company standard ways of working
- In conjunction with the Lean Specialist Coach and the community of coordinators across the other sites hold consistency over the application and development of company 'One System - One Voice'
- Openly share knowledge and experiences with colleagues so that we can accelerate our journey to World Class Manufacturing
- Develop appropriate plans and schedules to ensure that company maturity targets are achieved for A) Strategy, Performance & Delivery, B) Manufacturing & Process Management, C) Jishuken and D) True Lean
- Experience of managing a multi-functional team in a high speed process environment for a minimum of 5 years is essential
- Relevant 3rd Level Qualification in a related discipline
2
Lean Coordinator Resume Examples & Samples
- Develop programmes for record retention, continuous improvement and job training
- Promote the benefits of becoming a Lean organization
- Develop, plan and assist in implementation of strategic planning and lean strategy in all departments
- Educate, train and motivate our workforce on our Lean initiatives
- Work independently with minimal supervision
- Supports Manager and Supervisor in program establishment and follows up all program stages (timing, concept, feasibility, design, construction, try-out, launch, final buy-off, prototype programs, engineering changes, program packaging requirements including unit load manuals) as needed and requested by Engineering Manager
- Supports Program teams in new\existing program development. i.e. flow analysis, material flow within the plant, plant layouts, new equipment layout, warehousing requirements, packaging studies, freight studies as required
- Develops and establishes appropriate key performance measurable
- Plans and executes time motion studies
- Analyzes, evaluates and makes recommendations for cost reduction projects and paybacks
- Must be able to apply standard industrial engineering practices
- Conducts method analysis and improvements to work station design
- Develops quotes for capital projects including racks and material handling equipment
- Engineering Degree or equivalent combination of education and work related experience
- Completion of a specialized course(s) taught in recognized community colleges and universities, consisting of more that two academic years. Or equivalent combination of education and work related experience
- Proven record of successfully planning, leading and closing assigned project on time and budget
- Documented experience in training
- A working knowledge (oral and written) of both English and Mathematics
- Good organizational, leadership, interpersonal and problem solving skills
- Ergonomics Training
- Six Sigma Black Belt would be an asset
- SPC Level 1
- Advanced Excel Knowledge
- Problem Solving including 7MPT (Management Planning Tools)
- A3 Planning knowledge
- AutoCad
- MRP System knowledge (Job Schedule, Production Planning, Costing)
- Budget Planning
- Basic Financial understanding
- Standard Operating Procedure
- Presentation and Facilitation skills
- Knowledge and proven application of lean tools
- 5-10 years related work experience with successful lean implementations in an automotive environment
- Plans work and carries out tasks without detailed instructions
- Prepares for problems and opportunities in advance
- Analyzes problems skillfully and uses logic to reach solutions
- Responds positively to instructions and procedures
- Able to work well with staff, co-workers, peers and managers
- Works effectively on projects that cross function with other departments
- Regularly procedures accurate, thorough and professional work
- Works hours necessary to complete assigned work
- Reliable and accountable for work assigned
- Takes personal responsibility for safety
- Treats people with respect
- Seeks and considers diverse perspectives and ideas
- Works to develop additional technical knowledge and skills
- Listens well and explains reasoning behind own opinions exercises a professional approach with others using all appropriate tools of communication
- Respects all external and internal customers
- Sees how a problem, and its solution affects other units
- Weighs alternatives against objectives and arrives at reasonable decisions
- Adapts well to changing priorities
- Analyzes current procedures for possible improvements
- Organizes and maintains a system of records
- Able to determine project urgency in a practical way
- Constructively helps and coaches others
- Can-do approach
- Develops a team spirit
3
Lean Coordinator Resume Examples & Samples
- Partner with assigned business unit on the implementation of lean manufacturing, and lean business process efforts. Work with colleagues to help identify, realize and optimize lean solutions within the economic capability of the plant
- Support the promotion of lean culture in the organization by working with business areas to complete events and projects required to implement the Future State Plans
- Support business unit using appropriate tools, methodologies, and timing, of improvement activities to achieve business objectives
- Learn and apply Lean principles and tools such as those listed for implementing creative solutions for system and process improvements: Standard work, Ergonomics, 3-P, TPM, SMED, KANBAN, Value Stream Mapping, and 5-S
- Use Lean principles to perform process reviews and aid in establishing standardized work procedures
- Work collaboratively with teammates and support areas, in a team environment
- Work effectively in an environment of change, and uncertainty
- Support/Coordinate the planning, scheduling and facilitation of future Lean events
- Support open communications and involvement of employees who work in the process
- Participate in Lean audits, 5S activities, and daily GEMBA walks
- Participate in the coordination and periodic updates of progress during the event
- May be required to perform additional duties as assigned
- High School diploma or equivalent. Additional experience, training or formal education is beneficial
- Past participation in Kaizen events and MDI continuous improvement program
- Basic computer knowledge desired
- Ability to build and maintain effective work relationships
- Ability to plan, organize, and prioritize time/workload to accomplish tasks and meet deadlines
- Ability to work effectively in an environment of change and uncertainty
- Ability to understand and accept work direction
- Ability to adapt to rapidly changing business circumstances; must be able to thrive in a constantly changing business environment
4
Lean Coordinator Resume Examples & Samples
- Enjoy challenging and fast-paced environment
- Broad business knowledge and ability to link customer needs with business processes
- Strong analytical problem solving skills
- Ability to support multiple projects and balance priorities
- Ability to work independently and with all levels of managers and associates
- Strong coaching, facilitation and organizational skills
- Demonstrated ability to work successfully in complex and emerging business and project areas, leveraging interpersonal skills and technical skills to optimize results
- An understanding of and proficiency in Change Management
- Must be proactive, creative and a hands-on change agent
- Should have team building and rapid execution abilities
- Systems thinker and passionate for lean principles
- Extensive experience leading Kaizen events that achieved value-stream level improvements is preferred
- Willing to manage the transformation of value streams, by participating in Lean events, projects, and organizational changes necessary to achieve a sustained transformation
- Goal oriented and able to complete assignments on time
- Available in after-hours (weekends and holidays not excluded)
- Computer skills (MS Office, MS windows, Email,)
- Excellent Oral/Written communication skills
- Able to effectively communicate with all levels of the organization
- B.S in Engineering, Business or related field and/or a minimum of 5 years of successful lean implementation experience with proven record of sustainable results is preferred
5
Lean Coordinator Resume Examples & Samples
- Foster teamwork and maintain a positive and professional attitude at all times, while consistently treating each employee in a fair, respectful, and consistent manner
- Provide clear communication of plant rules and policies, including Safety. Document and coach employees based on facts associated with any violation of plant policies and procedures
- Lead by example. Coach and mentor employees to achieve plant targets using lean principles. Provide the proper tools required to complete assigned tasks
- Assist employees in solving problems. (Process Issues, Quality Concerns, Safety, etc)
- Train and develop employees using lean principles and tools. This will require active communication with the Value Stream Manager
- Daily review of production requirements with Production Control and Value Stream Manager
- Direct employees and assign operators as needed to ensure maximum efficiency and productivity during the shift. You will also be expected to set-up, troubleshoot, and operate equipment as needed to achieve this objective
- Daily review of SQDC metrics. Must also set priorities that match the needs of the business as indicated through MDI
- Participate in Lean Manufacturing and Process Improvement efforts as required. Define and complete projects or drive initiatives that align with strategy deployment targets of the plant and value stream. Lead and facilitate kaizen improvements
- Create, audit, and improve standard work
- Provide leadership through active participation in the Environmental, Health and Safety Program. Ensure that all Safety policies and procedures are followed as required
- During any emergency situation you will be required to take a leadership role. You will also be required to contact the Area Manager/Supervisor and HR Manager as required for additional direction
6
Lean Coordinator Resume Examples & Samples
- Leads or facilitates projects or events such as Shop Floor and Variation Reduction Kaizens
- Implements effective measurement tools associated with continuous improvement and cost out. Contributes heavily in the identification of cost-out ideas and implementation of the ideas
- Works as required with supplier quality assurance, supplier development to ensure lean is deployed through the enterprise
- Supports best practice sharing and internal and external benchmarking
- Support implementing: Eaton Business System, Lean, Six Sigma, and other world-class operation management techniques
- Personally lead change to improve organizational effectiveness. Drive the change management necessary to implement effective lean manufacturing operations
- Support initiatives to improve EHS culture; Participate in a EHS team (Ergo, Safety, Green, etc); Include safety topics in departmental meetings; Achieve near misses goal
- Support and/or participate on Continuous Improvement Activities such as: Kaizen, Ideas Programs, cost out and/or demonstrate improvements in goals year over year in our processes or practices aligned to achieve or business goals and/objectives
- Bachelor’s Degree in Technical Field with lean manufacturing experience, preferred
- 3-5 years of experience in the same position preferred
- Expert in lean manufacturing system including training, planning and implementation of tools
- Position requires strong analytical skills and understanding of problem solving tools/methods (six sigma, 8D, QOS and other) and Balanced Scorecard goal setting process
- Understands role of quality and variation reduction in driving operational improvement (minimum of Green Belt in 6Sigma, preferred)
- Understands supplier quality, tools associated with new product development and launch, quality function deployment, quality management systems (QS, TS) and cost of quality
- Understanding of budgets and cost drivers
- Strong communication skills and comfort with facilitating teams/groups and working with all levels in the organization
- Strong computer skills (MS Office, Project, etc)
- Bilingual English-Spanish (100%)
7
Lean Solutions, Portfolio Coordinator Resume Examples & Samples
- Assist with portfolio level meetings, including: coordinating calendar times and logistics, setting and distributing agendas, capturing meeting minutes, and capturing and tracking actions to completion
- Prepare under the supervision of the Delivery and Lean Solutions director, presentations for various portfolio and status governance meetings
- Act as a single point of contact for SharePoint support, including visual board development, site maintenance and trouble shooting
- Plan and prepare schedules and milestones and monitor progress against established timelines
- As required, identify and escalate portfolio changes, risks, issues and actions to the Delivery Director
- Consolidate all Brighter Way portfolio information on a monthly and quarterly basis, or as required for various Brighter Way governance meetings
- Provide administrative support to ensure quarterly attestations of portfolio standards
- Manage the Lean Solutions Calendar, including rescheduling meetings, logistic changes
- LI-CA1
8
Lean Coordinator Resume Examples & Samples
- Provides formal training to employees on Lean and Six Sigma methodologies for our manufacturing operation in Reynosa
- Green Belt training
- Leads and coordinates Kaizen, lean and 5S events
- Provides regular reports on savings, progress of projects and KPIs
9
Lean Coordinator Resume Examples & Samples
- Performs value-stream-mapping, current and future state
- Leads lean projects and facilitate cross-functional teams to apply lean principles and tools, and assists in recording onto SOWs and entering into Sigma Trac
- Participates with peers to connect lean manufacturing to customer distribution networks and to the supply chain
- Prepares detailed plans, drives project performance and assures timely completion of product/process improvement, using standard tracking and reporting systems
- Establishes impact on operational cost and departmental expense budgets
- Assists in the gathering and reporting of JCMS assessment data
- Bachelor’s Degree in a related field or equivalent combined education and experience
- A minimum of two years experience in Continuous Improvement, or in a Manufacturing and Engineering environment
- Proficiency in a Windows operating environment, including email and Microsoft Office software
- Strong interpersonal skills and decision making abilities
- Effective and professional communication and organization skills
- Basic statistical knowledge and ability to apply statistics to process improvement projects
- Solid understanding of the application of lean principles
- Understanding of problem solving methodologies preferred
- Ability to exercise influence without authority
10
Lean Program Coordinator Resume Examples & Samples
- Ability to manage multiple, concurrent work streams
- Self-starter and effective problem solver
- Proficiency in all Microsoft Office applications with the ability to quickly learn new applications
- Ability to operate in a demanding environment and handle challenging organizational issues
11
Lean Coordinator Resume Examples & Samples
- Ability to effectively communicate between all Production and Support Groups
- Ability to coordinate with suppliers to ensure accurate and timely delivery
- Planning of available resources for better utilization, including Visual Management implementation and sustainment
- Assist in developing evolving strategies and tactics to improve efficiency, effectiveness, and the reduction of waste, while supporting and adhering to the Lean Strategy for the plant
- Ability to develop and effectively deliver training to large groups, including Front Line Leaders
- Ability to objectively audit and assess the need for continuous improvement
- Responsible for maintaining the Lean Calendar, Intranet, and Lean Controlled Documents
12
Lean Coordinator Resume Examples & Samples
- Provide active design, leadership, and advocacy of a continuous improvement culture
- Utilizing Value Stream Mapping, support the plant Lean strategy
- Facilitate teams of employees engaged in lean activity planning and execution of these plans
- Develop clearly defined deliverables for Lean in accordance with the company’s scorecard system
- Serve as a facilitator for Lean activities, working with leadership across the business enterprise to train, communicate, standardize, sustain and facilitate the implementation of Lean
- Build strong and positive working relationships with all functional areas across the location, including them in the improvement activities and understanding their needs
- Provide training and develop appropriate programs to educate employees in the principles of Lean manufacturing
- Drive Kaizen events and follow-up to ensure proper progress and the continuity of the lean efforts toward the optimization and removal of waste
- Assist location through best practice sharing and the implementation of Lean concepts from AWC and other within their operations
- Conduct all activities and behave in a method that is strictly consistent with the Company’s CITE Principals and Supporting Values while striving to help the Company achieve its Vision
- B.S. degree in technical field or equivalent hands-on training required
- Must have a demonstrated history of successfully leading and facilitating changes that involve all levels of employees with measurable results
- Prior lean certification and experience in implementation of lean manufacturing is a strong plus, however individuals that meet the other skill requirements will receive the appropriate training in lean manufacturing
- Ability to learn new concepts and pass the knowledge along to others in classroom and practical experience
- Proven ability to lead associates through coaching and mentoring
- Candidates should be highly energized and self-motivated with experience working with teams to implement change and be adept at communicating with all levels to get everyone on board
- Excellent written and verbal communication skills are required
- Track record of successful project management and team experience
- Personal computer skills in a networked environment, Microsoft products (Word, Excel, Outlook, and Access) required
- Management style and duties must be consistent with and support the 2019 Vision and CITE principles
13
Lean / Quality Coordinator Resume Examples & Samples
- Prepare Quality documentation and reports by collecting, analyzing, and summarizing data and trends including failed processes, stability studies, and corrective actions
- Establish and maintain product quality plans and control plans
- Audit processes to established control plans
- Analyze data to predict potential problems and take preventive actions
- Develop and follow up on action plans for critical process variables in order to meet critical product characteristics
14
Lean Coordinator Resume Examples & Samples
- Facilitate and lead continuous improvement events that support team and employee development in Lean principals, tools, and concepts
- Direct, support, and promote proactive process improvement programs and associate training to uphold elimination of process waste and variation reduction
- Promote a team environment through effective communication and associate involvement to achieve departmental and business objectives
- Train employees in APS tools and methods; Value Stream Mapping, Kanban(Pull Systems), Level Loading, heijunka, PFEP, Supermarket, Milk Run design, Waste identification, 5S, Visual Management, JIT, SMED, Takt Time, and Poka Yoke
- Collaborate with cross-functional teams including: Manufacturing Engineering, Quality, Human Resources, Engineering, Materials Planning, Shipping, and Purchasing
- Monitor development of Standardized work documentation, material flow improvements, and progress tracking in areas assigned
- 50% time on the production floor and 50% time creating and maintaining LDMS and Kanban systems
- Support LDMS teams as well as update and drive assigned Action items to closure
- High diploma AND 2+ years of experience in manufacturing environment with assembly, welding, machining, and/or painting processes with a knowledge of continuous improvement methodologies OR Technical Associates degree or Bachelor’s degree related to manufacturing engineering/continuous improvement
- Proficient in MS Office including Word, Excel, and PowerPoint (basic knowledge)
- Experience working with SAP or another ERP system
- Experience in lean, flow-through manufacturing
15
Lean Coordinator Resume Examples & Samples
- Auditing lean processes post improvement activities and ensuring actions are being completed
- Leading projects and coordinating team activities, as assigned, to complete company goals and initiatives
- Facilitating and managing LEAN activities, ensure on-time completion and report results to Lean Steering Committee and make updates to area lean boards
- Implementing communication tools to foster the lean environment and improve a lean culture
- Leading improvements in on time delivery metrics while reducing costs and inventory
- Leading Kaizen events from inception thru tracking measurement
- Responsible for LEAN metrics and tracking files sent to corporate as needed
- Participating in LEAN conference calls to align corporate vision with plant activities
- Updating and maintaining Plant Layouts
- 1+ years of experience in a Lean leader position or continuous improvement role
- Demonstrated success in leading and sustaining change using Lean methods
- Proven facilitation skills and ability to energize others to productive action
- Must be able to work closely with others to collaborate on completion of common goals
- Knowledge of Lean methods (related practices and procedures), principles and practices of operations improvement
- Ability to effectively manage multiple projects, to prioritize work tasks and maintain focus
- Strong communication skills. Must be able to work closely with others to collaborate on completion of common goals
- Familiarity with the Microsoft Office Suite (Word, Excel, and PowerPoint)
16
Lean Coordinator Resume Examples & Samples
- Coordinate Job of the Lean Manufacturing Activities
- This position will manage the lean and manufacturing engineering activities
- Lead and support several significant manufacturing engineering activities
- Lead a manufacturing planning activity through the product development/launch cycle
- Lead cross-functional teams in lean and process improvement initiatives
- Establish plants and strategies to meet corporative lean and six sigma goals and programs
- Train, coach, or mentor others in lean and manufacturing initiative’s
- Implementation of ELSS, productivity and cost out focus
- Lean Manufacturing Expert
- Bachelor of Mechanical Engineering degree is required. Management training or experience is preferred
- Basic understanding of Finance and Accounting
- Pro launch knowledge
- Minitab
- Strong problem solving and Project Management skills
- Effective communication skills at all levels of the organization
- Ability to work with functions outside of Quality for the common good of Eaton
- Fully bilingual (Spanish/English)
17
Lean Coordinator Resume Examples & Samples
- Analyzes and measures the effectiveness of existing business processes and develops sustainable, repeatable and quantifiable business process improvements
- Works closely with Operations and Functional Teams to identify process bottlenecks, conducts root cause analysis and implements process improvements across the business or organization
- Drives productivity and process improvement projects aligned with business initiatives
- Coaches project teams to fulfill certification requirements, quality and process improvement objectives
- Initiates and leads projects that improve end-to-end processes: setup, validation, and audit measurement systems to deliver business impact
- Proactively promote and create a safe work environment for all associates. Provide associates with the tools and resources necessary to work safely. Ensure accountability with respect to safety rules and processes. Conduct root cause analysis and implement corrective actions to prevent safety incidents
- 1+ years Manufacturing Management experience in a fast paced environment
18
Lean Coordinator Resume Examples & Samples
- An Associate’s Degree and three years of work experience in Lean role or a High School diploma/GED and five years professional work experience in a Lean role
- A demonstrated understanding of Lean principles and methodology
- A working knowledge in Microsoft Word, Excel, and Outlook
- The ability to speak in front of a group of co-workers or visitors
- The ability to bend, squat, twist, reach outward and move about the plant during a third of the shift
- The ability to collaborate with a group to reach consensus
- The ability to schedule daily workload without supervision or direction
- The ability to work quickly and efficiently with employees as well as suppliers and vendors
- The ability to organize and manage multiple, simultaneous priorities and meet aggressive deadlines
- Strong leadership, problem solving and planning skills
- Attention to detail with accuracy while working in a fast-paced environment with multiple deadlines
- Knowledge of the material, costs, techniques and processes used within the manufacturing industry
- Judgment and decision making skills while comparing relative cost and benefit potential
- Deductive reasoning ability to formulate answers to specific questions that make sense
- The ability to motivate, develop and direct people without having authority over them
- The ability to communicate effectively with all levels of the workforce and management
- Bachelor’s Degree in business or related Lean field
- Proven capabilities to improve office/administrative jobs through the utilization of lean tools including the facilitation of project teams utilizing the Agile methodology
19
Lean Coordinator Resume Examples & Samples
- Help establish Formet Business Plan and Departmental Goals and Objectives; ensure that goals and objectives are met (People, Investor, and Customer)
- Develop and support Departmental leadership succession plans
- Ensure that short and long term planning is established for department in the areas of, but not limited to, Operating budget, manpower planning, CIP and cost reduction plans, Quality, Safety, Environmental and Employee satisfaction and motivation
- Develop programs for record retention, continuous improvement and job training
- Participate in the creation and implementation of clearly defined rules of conduct and communications
- Provide training and work instructions in the areas of, but not limited to, Health & Safety, TS 16949, ISO14001, job specific etc
- Reinforce the Open Door process
- Participate in recruiting of personnel by conducting interviews as required
- Participate in the monthly Team Member meetings and provide timely feedback on issues and concerns
- Ensure policies and procedures are created objectively and reviewed and approved as required
- Educate, support and promote corporate initiatives i.e. Employee’s Charter, EOS, Hotline, Fairness Committee, the Employee Advocate and our Lean Initiatives
- Manage without discrimination and personal bias, which includes race, creed or any prohibited grounds as outlined in Human Rights legislation
- Educate our workforce on our Lean initiatives
- Training of teams members on lean
- Evaluation of new processes
- Completion of a specialised course(s) taught in a recognised community college/ university, consisting of more than two academic years. Or equivalent combination of education and work related experience in lean manufacturing
- Minimum five years’ work related experience in an automotive environment utilizing lean tools
20
Lean Coordinator Resume Examples & Samples
- Assist with the training and Lean concepts to the plant. Must work closely with, and assist as needed, other managers within the plant and with other locations to ensure program effectiveness and approach in making improvements
- Auditing Lean processes post improvement activities and ensuring actions are being completed
- Capable of use of Lean tools and concepts as the methodology for significant, effective, measurable and sustainable improvement
- Lead projects and coordinate team activities, as assigned, to complete company goals and initiatives
- Reports to the Plant Manager with dotted line reporting to corporate Lean Champion for vision and improvement objectives
- Facilitate and manage Lean activities, ensure on-time completion and report results to Lean Steering Committee and make updates to area Lean boards
- Implements communication tools to foster the lean environment and improve a lean culture
- Capable to train to Lean principles in particular to associates on the floor
- Leading Kaizen events from inception through tracking measurement
- Increase visuals within the plant and facilitating flow
- Responsible for Lean metrics and tracking files sent to corporate as needed
- Participates in Lean conference calls to align corporate vison with plant activities
- Update and Maintain Plant Layouts
- Associate’s degree or equivalent experience
- Previous experience of 3-5 years working in a Lean environment
- Strong desire to learn and grow in Lean Methodology and Six Sigma
- Have excellent written and verbal communication skills
- Excel in fast paced, high pressure situations
- Familiar with the Microsoft Office Suite (Word, Excel, and PowerPoint) A site test will be issued
- Previous experience of 1-3 years in a Lean leader position or continuous improvement role is preferred but not required
- Basic understanding of Lean tools and methods
- Excellent organizational and teamwork skills
- Ability to follow established policies and procedures
- Ability to present to various groups of people
- Proficient computer skills including MS Office
- Ability and willingness to work core hours to support the needs of our brokerage firms and plant locations