Coordinator, Maintenance Resume Samples
4.6
(137 votes) for
Coordinator, Maintenance Resume Samples
The Guide To Resume Tailoring
Guide the recruiter to the conclusion that you are the best candidate for the coordinator, maintenance job. It’s actually very simple. Tailor your resume by picking relevant responsibilities from the examples below and then add your accomplishments. This way, you can position yourself in the best way to get hired.
Craft your perfect resume by picking job responsibilities written by professional recruiters
Pick from the thousands of curated job responsibilities used by the leading companies
Tailor your resume & cover letter with wording that best fits for each job you apply
Resume Builder
Create a Resume in Minutes with Professional Resume Templates
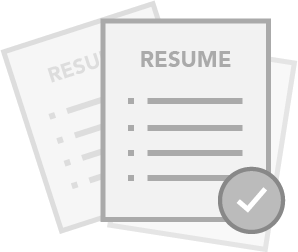
CHOOSE THE BEST TEMPLATE
- Choose from 15 Leading Templates. No need to think about design details.
USE PRE-WRITTEN BULLET POINTS
- Select from thousands of pre-written bullet points.
SAVE YOUR DOCUMENTS IN PDF FILES
- Instantly download in PDF format or share a custom link.
KG
K Goldner
Kamron
Goldner
32561 Federico Flat
Chicago
IL
+1 (555) 981 8764
32561 Federico Flat
Chicago
IL
Phone
p
+1 (555) 981 8764
Experience
Experience
San Francisco, CA
Coordinator Maintenance
San Francisco, CA
Prohaska, Padberg and Wilkinson
San Francisco, CA
Coordinator Maintenance
- Responsible for assisting Manager/Supervisor and Training Liaison in developing facility training programs consistent with Williams policies
- Previously involved with managing, scheduling, and/or communicating shutdown activities efficiently and effectively
- Monitor job progress during maintenance. After maintenance is complete, compare actual to estimates to apply knowledge into developing future job plans
- Monitor maintenance and project scope development and status, invoicing and quality control for all maintenance activities
- Working knowledge of Project Management and Construction Standards
- Monitor and approve contractor invoicing
- Effectively communicate, both verbally and in writing to other individuals, teams, customers, and stakeholders of the business
Houston, TX
Coordinator of Maintenance
Houston, TX
McCullough and Sons
Houston, TX
Coordinator of Maintenance
- Leads successful execution of routine maintenance activities through effective planning, executions, materials sourcing, manpower utilization, cost control, long range planning and project implementation
- Leads successful execution of non-routine maintenance and collaborate with the operations manager/supervisor and technicians to plan, manage, and coordinate related preventative maintenance, including repair and overhaul of equipment as necessary
- Ensures all work is planned and performed in accordance with Williams’ standards, processes and procedures (WIMS, PSM, Project Life Cycle, Integrity Management Plans, environmental testing and monitoring, etc.)
- Responsible for using the CMMS (Maximo/OMS) and coordinating with the operations manager/supervisor and technicians to create, assign, track and close all work orders such as PMs, BLM, and EMIS
- Ensures all reports and findings are communicated to operating area and the necessary internal subject matter experts
- Reviews all work orders for timely completion with adequate documentation
- Analyzes, recommends and implements process improvements in areas that are inefficient
present
Phoenix, AZ
Maintenance Systems & Capital Coordinator
Phoenix, AZ
Romaguera Group
present
Phoenix, AZ
Maintenance Systems & Capital Coordinator
present
- Work with Engineers to ensure capital projects are managed in compliance with designated project management techniques. Track late projects
- Ensure effective integration and support of key maintenance processes: work identification, planning and scheduling,
- Manage training for Engineers on SAP Project Systems
- Manage E- Time Reporting System and post Overtime refused weekly
- Initiate continuous improvement and streamlining consistent with other Plants
- Manage Printers and supplies in Maintenance and Engineering
- Capital and Asset Management
Education
Education
Bachelor’s Degree in Mechanics
Bachelor’s Degree in Mechanics
University of San Francisco
Bachelor’s Degree in Mechanics
Skills
Skills
- You continually seek greater knowledge about the systems, processes and hazards in the workplace, in order to understand not just what you do but why you do it
- Strong knowledge of specific equipment such as dozers, haul trucks, shovels, or other mobile mining equipment
- Knowledge of quality and risk management methods and practices related to mobile maintenance equipment
- Strong planning and organizational skills, with the ability to handle multiple projects
- Strong interpersonal and leadership skills, with the ability to influence others
- Good knowledge of tanks, pumps, piping, and loading equipment as they relate to terminal operations is an asset
- Good knowledge of maintenance workflow process
- Knowledge of Alberta Building Codes
- Proficient in the preparation of performance management evaluations, budgets, operational plans, safety reports and technical reports
- Proficient in manpower and resource planning
15 Coordinator, Maintenance resume templates
Read our complete resume writing guides
1
Maintenance Tech / Coordinator Resume Examples & Samples
- Maintain lighting system bulbs and ballasts
- Assist the operations team in the maintenance and repair of building and equipment
- General interior maintenance – hang pictures, install keyboard trays, and repair office furniture systems
- Minor plumbing repairs
- Completes special tasks that include but are not limited to; painting, locksmith work, tenant services requests, and general maintenance as assigned
- Moves office furniture, machinery, equipment and other materials as requested
- Perform assigned facility inspections and due diligence efforts, reporting on as found conditions impacting satisfactory client occupancy and operations
- Respond effectively to all emergencies
- Comply with all safety procedures, maintaining good housekeeping and safety of work areas. Recognize danger and safety hazards and propose methods to eliminate them
- Maintain compliance to State, County, or City Ordinances, Codes, or Laws
- Complies with all policies for the safe storage, usage and disposal of hazardous materials
- Participate in ongoing technical, safety, and operational process training programs
- Documents work performance and materials procurement as directed
- Other assigned operational tasks as may be typically expected of the Maintenance Mechanic role
- While performing the duties of this job, the employee is regularly required to stand, use hands to finger, handle, or feel, and talk or hear
- The employee frequently is required to walk; reach with hands and arms; and stoop, kneel, crouch, or crawl
- The employee is occasionally required to sit
- The employee must regularly lift and/or move up to 10 pounds, frequently lift and/or move up to 50 pounds, and occasionally lift and/or move up to 100 pounds
- Specific vision abilities required by this job include close vision, distance vision, color vision, peripheral vision, depth perception, and ability to adjust focus
- This position requires working outdoors, in mechanical/equipment rooms and possible extreme weather conditions
- While performing the duties of this job, the employee is regularly exposed to moving mechanical parts and heavy equipment
- The employee is frequently exposed to wet and/or humid conditions, high and precarious places, fumes or airborne particles, outside weather conditions, risk of electrical shock (high voltage), and vibration
- The employee is occasionally exposed to toxic or caustic chemicals, extreme cold, and extreme heat. The noise level in the work environment is usually loud
2
Maintenance Execution Coordinator Resume Examples & Samples
- Manage scheduling activities for maintenance personnel
- Ensure the Preventative Maintenance Program meets requirements
- Issue and follow-up on PM work orders and report on PM compliance
- Arrange contractor visits and ensure completion of contractor work orders
- Create reports and graphs for management team
- Report and maintain compliance with monthly maintenance budget
- Record keeping and data entry work will be required
- Perform other duties and projects as assigned
- Managing architecture to streamline communications (distribution lists, feedback cycle)
- Booking conference calls and compiling action items and minutes
- 2 to 5 years of experience in retail (telecommunications)
- Passionate about technology
- Superior communication and negotiation skills
- Strong written, verbal and presentation skills
- Ability to think critically and analyze data
- Strong Microsoft Skills (Word, Excel, PowerPoint)
- Proven track record in building and maintaining professional relationships
- Excellent Organizational skills with the ability to prioritize work load
- Ability to work in a fast paced, time sensitive environment
- Knowledge of maintenance department including VMS program an asset
3
Maintenance Storeroom Coordinator Resume Examples & Samples
- Facilitate company strategies for Storeroom Improvement Initiatives, develop Storeroom “Best Practices”
- Integrate the Storeroom with the Maintenance Planning process
- Provide training in SAP PM/MM to Storeroom, Planners, and Maintenance Personnel
- Develop and maintain Storeroom Standard Operating Procedures (SOP’s)
- Analyze and recommend adjustments to inventory levels, considering maintenance input and inventory optimization theory
- Develop, maintain and communicate timely and accurate reporting of Storeroom KPI’s
- Serve as a liaison between the Storeroom and Maintenance Planners to communicate part obsolescence, replacements, etc., and to assure equipment BOM’s are being maintained and updated
- Conduct daily review of cycle counts
- Drive MRO Inventory Management by engaging with the maintenance planners and finance
- Prioritize and oversee assigned daily work performed which includes MRP runs, Cycle Count Accuracy, Work Order Parts Reservations, development and training needs
- Lead re-engineering / alternate vendor initiatives to optimize inventory when needed
- Work closely with vendors to optimize inventory cost
- Ensure all Storeroom attendants comply with all Mondelez policies, procedures, and GMPs
- Ensure all storeroom attendants perform all work in a safe and efficient manner
- Control and approve all requests for new part ads, deletions, and obsoletes
- Ensure implemented cost saving measures are being executed and driven
- Ensure defined material kitting process for PM and planned work orders is being driven and executed
- Strong analytical and negotiation skills strong familiarity with multiple MRO commodities
- Ability to lead an autonomous Storeroom Team
- Experience in sourcing and buying indirect materials
- Minimum 3 Years of experience managing a Maintenance Storeroom; proficiency in MRO Inventory Management; proficiency in MRO Purchasing & Requisitioning; proficiency in SAP PM/MM; proficiency in Microsoft Excel, Word, Outlook
4
Maintenance Systems & Capital Coordinator Resume Examples & Samples
- Maintenance Systems Management (SAP)
- Manage all upgrades and new releases of SAP Plant Maintenance and store documentation on Sharepoint
- Ensure effective integration and support of key maintenance processes: work identification, planning and scheduling,
- Become expert on SAP PM/PDM, stores SAP issues, organizational structures, update equipment as needed in SAP
- Provide plant maintenance system training for maintenance personnel and all plant employees as needed
- Manage Printers and supplies in Maintenance and Engineering
- Initiate continuous improvement and streamlining consistent with other Plants
- Plant SAP Administrator and coordinator for maintenance and technical services
- Sharepoint Administrator for maintenance and engineering
- Run various Backlog Reports out of SAP
- Support Maintenance Transformation efforts
- Maintenance Budget Administration
- Track maintenance budget performance daily and monthly
- Identify & report monthly variances and trends
- Ensure maintenance systems are designed to reflect maintenance costs to equipment
- Track PM schedule compliance, PMG work generated & PM coverage
- Manage E- Time Reporting System and post Overtime refused weekly
- Capital and Asset Management
- Plant Asset Manager, create D projects as needed and track costs weekly,
- SAP Project Systems Gatekeeper manage all plant capital expenditures, forecasts and Corporate reporting requirements, including Obsolescence. Conduct 3 year Asset Inventory
- Work with Engineers to ensure capital projects are managed in compliance with designated project management techniques. Track late projects
- Manage training for Engineers on SAP Project Systems
- SAP & E-time experience preferred
- Knowledge and experience with managing budgets is highly preferred
5
Maintenance MRO & Contractor Coordinator Resume Examples & Samples
- Experience with computerized maintenance systems, specifically SAP
- Knowledge/Experience of operation and maintenance of plant utilities (i.e. steam, compressed air, cooling towers, chillers, HVAC, etc.) a plus
- Facilities maintenance experience (utilities, service contractors, general facilities upkeep) a plus
- Must be self-motivated and be able to work independently
- Must be able to multi-task
- Must be hands-on
- PSM experience preferred
- Experience with basic computer software programs (Word, Excel, etc.)
6
Maintenance Control Coordinator Resume Examples & Samples
- Be familiar with duties assigned to all personnel within the Maintenance Control Work Center. Process Visual Information Display System/Maintenance Action Forms (VIDS/MAF) from aircrew or maintenance technicians in accordance with OPNAVINST 4790.2 Series, Navy, and Company Instructions
- Screen completed VIDS/MAFs for correct entries and data. Maintain Aircraft Discrepancy Book (ADB) in accordance with OPNAVINST 4790.2 Series
- When qualified and assigned by the Maintenance Control Supervisor, assist in scheduling aircraft into the maintenance program to ensure maximum availability of assets, become designated to release all TMS aircraft “Safe for Flight”
- Coordinate the daily flight schedule and configuration requirements with duty and applicable work centers
- Coordinate and screen Daily/Turnaround and special inspections as well as component and hi-time requirements to ensure aircraft are current for the flight schedule
- Assist in coordinating aircraft moves and static display requirements
- Liaison with base personnel for other requirements to include but not limited to fuel, hush house, corrosion hangar etc
- Will be required to work in conjunction with the down desk supervisor to accomplish all tasks at hand
- During detachments may be required to coordinate maintenance tasks, to accomplish the flight schedule
- Perform all other required duties as applicable and assigned by supervision
- Must be knowledgeable of technical directives, NAMP programs, and shall be knowledgeable of and understand basic supply procedures
- Maintenance Coordinator shall have experience writing with clarity and technical accuracy, and exhibit leadership and ensure adherence to all applicable policies and procedures
- Possess a high degree of expertise in the control and coordination of aircraft maintenance
- Thorough working knowledge of applicable maintenance/technical manuals and publications
- Thorough working knowledge of aircraft maintenance records
- Working understanding of the aircraft and aircraft systems
- Ability to schedule and track aircraft maintenance including inspections, preservations, oil sampling and engine washes and rinses
- Ability to operate two-way communication equipment and speak in a clear and concise manner
- Must be customer oriented
- Shall possess an extensive background in the field of aircraft maintenance and material support
- Minimum of eight years’ experience within the last 15 years in direct aircraft maintenance repair, inspection, and modification. Of the eight years’ experience in aircraft maintenance, six years shall be in a maintenance control position that includes responsibility for assigning workloads as well as duties for entire shifts
- Must have experience coordinating daily flight operations personnel supporting scheduled and unscheduled maintenance
- Recent experience with F-18 (A-F), EA-18G, E-2C, MH-60S or F-16A&B aircraft strongly preferred
7
Coordinator, Maintenance Resume Examples & Samples
- Review and plan priority work requests to ensure minimum interruption to the locked in schedule
- Coordinate contractor activities during outage events
- Work with the operations maintenance coordinator to ensure all scheduled maintenance is ready for execution
- Assist with the preparation of detailed job plans outlining all cost parts, materials, special tools, external services and documentation
- Interface with planners, project engineers and production specialists to set job priorities and develop work schedules
- Act on any non-conformance that appears and implement corrective action
- Actively drive results with respect to safety, quality, budget and schedule
- Fully understand the requirements of the relevant health and safety legislation, in particular, duties and responsibilities
- Liaise with coordinators from other disciplines including but not limited to (mechanical, electrical, instrumentation, insulators and scaffolders)
- Seven or more years of planning, scheduling and coordinating experience working in mining, oil and gas or a similar industrial environment
- Five or more years of experience in maintenance and reliability in mobile equipment, fixed plant, utilities or infrastructure
- Mechanical trade certificate or diploma in a relevant technical field or equivalent technical and operational experience
- Solid understanding of maintenance planning, scheduling and coordinating concepts as well as maintenance practices, performances measures, scheduling tools and techniques
- Strong working knowledge of the in situ process, facilities maintenance processes and procedures and Alberta Boilers Safety Association (ABSA) requirements
- Strong working knowledge of computerized maintenance management systems (preferably SAP) and material management systems
8
Maintenance Stores Coordinator Resume Examples & Samples
- Excellent written and verbal communicator
- Detail oriented with the ability to manage multiple priorities simultaneously
- Leadership or supervisory experience preferred but not necessary
- Experience in maintenance operations, manufacturing, or operations background helpful
- Bachelor Degree in related field or 5 -7 years closely related work experience in lieu of a degree
- Moderate skill level in MS Office Suite (Excel, Word, Power Point)
- SAP – Materials Management and Purchasing experience preferred
9
Coordinator, Maintenance Resume Examples & Samples
- Ensure plant maintenance, quality control, and maintenance performed by crews and/or contractors
- Lead work teams through example and motivation, instruction, coaching, discipline, and otherwise oversee employee work performance
- Resolve employee grievances to levels provided for within the Collective Bargaining Agreement
- Ensure compliance with corporate policies, plant rules, environmental and safety procedures, and laws
- Coordinate with other departments to ensure completion of work orders, preventive maintenance, and proactive identification of equipment reliability issues
- Must comply with company safety rules and regulations and wear proper safety equipment while on plant grounds
- 1-5 years of progressive maintenance experience in large industrial manufacturing industry
10
T Cba Maintenance Control Coordinator Resume Examples & Samples
- Monitors contract compliance by all maintenance activities through the audit and surveillance requirements as defined in the Quality Assurance Manual
- Performs final and in-process inspections of all maintenance actions involving safety of flight or requiring certification by an Aircraft Inspector
- Investigates safety incidents and assists in preparation of Engineering Investigation Request, Quality Deficiency Reports, Hazardous Material Reports, Technical Publications Deficiency Reports and Explosive Mishap Reporting as required
- Monitors operation of support equipment required for flight operations
- Performs spot checks for compliance with Tool Control Program
- Monitors calibration program of Precision Measuring Equipment (PME)
- Reviews applicable maintenance forms and deficiency data to determine discrepancy trends and specific problem areas
- Assist in the drafting and development of work instructions, maintenance instructions, local maintenance requirement cards, Quality Assurance alerts and routine and continuing correspondence to all work centers detailing maintenance and program procedures and requirements
- May be assigned as a training instructor as required
- Responsible for the establishment of the daily FCF requirements, briefing and debriefing the pilots and closing out the FCF documentation at the end of the flight schedule day
- Assists in preparation of Quality Assurance Monthly Data Report
- Assists in preparation of weekly/monthly/quarterly Quality Assurance Control Status Report for inclusion in report to the Program Management Office
- Reviews incoming technical publications and directives to determine their application to the Maintenance Department
- Performs other related duties
- Deals with the customer in courteous, professional and effective manner
- Complies with and monitors all established general and industrial safety rules and regulations as applicable to the contract, facility and job assignment
- Assists as directed to ensure safety, security and preservation of government/company owned equipment
- Maintains cleanliness of work center
- Complies with and monitors Foreign Object Damage (FOD), Hazardous Waste, and Tool Control programs
- May be required to perform off-site service on assigned detachments
- May be required to perform ADR analysis (Air Data Recorder)
- High school graduate or GED equivalent. Satisfactory completion of U.S. Armed Forces aviation maintenance courses or other schools with equivalent curriculum or five (5) years of on the job training and/or experience required. Must be able to meet any Government/Company licensing/qualification requirements for the position
- Must have five (5) years experience in military or civilian aviation maintenance/production control and scheduling
11
Coordinator, Maintenance Resume Examples & Samples
- Ensure contractors align with Suncor’s environment, health and safety (EH&S) policies and adhere to Suncor's Journey to Zero safety program
- Ensure that standards and procedures conform to relevant legislation, codes and guidelines for risk management and environmental protection
- Safely execute all planned maintenance work within scope
- Participate in planning meetings to drive out a planned, cost effective maintenance schedule
- Troubleshoot equipment failures, working hand-in-hand with the reliability group to identify root cause failures
- Operate and maintain your area of responsibility within the agreed annual budget
- Ensure business unit custodial needs are being met
- Perform regular inspections of contractor's work to ensure procedures and standards are being followed
- Work actively with supply chain to help administer solid vendor contracts, ensuring adherence to established price, quality and delivery schedules
- Support and steer to the maintenance budget
- Two to five years of contractor management/supervisory experience
- Two or more years of dynamic building services experience is an asset
- Experience working with and supervising a unionized and non-unionized workforce
- A diploma from an accredited post-secondary institution (preferred) or an equivalent combination of training and experience
- Certification as a Facility Management Professional is an asset
- Valid Alberta Journeyman Certificate or an Interprovincial Red Seal Journeyman Certificate, in any core trade; attach your Journeyman / Red Seal ticket with your application in order to be considered
- Knowledge of environmentally-friendly cleaning programs
- Knowledge of Alberta Building Codes
- Proficient in the preparation of performance management evaluations, budgets, operational plans, safety reports and technical reports
- You collaborate with others in order to achieve the best results and deliver the most value, through strong leadership and communication skills
12
Coordinator, Master File Maintenance Resume Examples & Samples
- Item Master File Maintenance-work to rationalize inventory items across multiple organizations within PolyOne DSS, take ownership of item master data integrity, analyze discrepancies, manage/control item input documentation and assist with PolyOne DSS catalog and category attribute updates as the business grows and changes
- Vendor and customer maintenance—Work to rationalize vendors and customers across multiple organizations within PolyOne DSS, take ownership of master file data integrity, analyze discrepancies and manage/control master file input documentation for all additions, deletions, and changes
- Communication-Respond to customer questions and requests in a timely and professional manner and provide occasional remedial retraining to customers submitting erroneous master file input documents
- Able to maintain professionalism and confidentiality of information
- Familiarity with SAP
- Self-motivated and quick learner
- Good written, verbal and interpersonal communication skills
- Data entry – 1 year
- Microsoft Outlook – 1 year
- Microsoft Excel – 1 year
- Microsoft Word – 1 year
13
Maintenance MRO Coordinator Resume Examples & Samples
- Purchasing
- Have good attendance and safety records
- Be able to work well in a team
- Possess great attention to detail
- Have financial acumen
- Possess strong computer skills and the ability to learn new ones
- Have strong communication skills both internal and with external suppliers
- Willing to work overtime and weekends when needed
14
Coordinator, Maintenance Area Resume Examples & Samples
- Provide visible field leadership in tool box talks, safety meetings, workplace observations and field tours
- Review field level risk assessment (FLRA) cards to support safe work
- Support and encourage our safety culture by following processes including near-miss reporting, incident reporting and leading investigations
- Collaborate with cross-functional teams to drive continuous improvement in support of our day-to-day activities while accommodating high-risk, urgent work
- Manage contractor performance and ensure the proper use of sign sheets, FLRAs, job hazard analysis, and appropriate contractor training
- Provide work completion and schedule updates to operations, the scheduler and the appropriate trades
- Provide job feedback to support planning, supply chain and reliability improvements
- Work with the foreman to remove roadblocks and ensure the successful completion of the work
- Five or more years of field supervision and/or planning experience
- Experience in the oil and gas industry is preferred
- Valid Journeyman Certificate or an Interprovincial Red Seal Journeyman Certificate or technical diploma is preferred
- Computer proficiency, specifically in SAP, Primavera and the Microsoft Office suite
- Technical understanding of the oil and gas industry and mechanical equipment, such as regular maintenance processes for exchangers, valves, compressors, piping circuits and analyzers
- Knowledgeable with a proven record of adhering to standards, policies and procedures
- Ability to balance competing priorities, stakeholder demands, and work within both short- and longer-term timelines
- You constantly interact with others across a multitude of business units and effectively collaborate with them to develop positive working relationships
15
Coordinator, Maintenance Resume Examples & Samples
- Develop job scopes, job plans, cost estimates, timelines and assessments for maintenance and capital projects
- Assist Engineering with pre-planning phase of capital projects
- Approves contractors for maintenance functions and identifies contractors for specific tasks
- Identifies, plans, coordinates and implements the planned and unplanned maintenance projects including ROW clearing, painting, depth of cover, etc
- Responding to and completing emergency repairs safely with appropriate materials and contract personnel and equipment
- Planning and execution of project assistance needed for new construction, smart pigging and rehab activities
- DOT compliance and documentation
- Working knowledge of industry standards and safety and environmental requirements
- Completes necessary reports; attends damage prevention meetings
- Orders and maintains materials and area materials for emergency stock
- Assists Pipeline Technicians with line locates as needed; line crossings and excavation
- Procedural manual items such as pipeline inspection reports, line flyer reports, corrosion inspection reports, foreign line crossing reports, hydrostatic test reports, critical material documentation and weld reports
- Dealing with various landowners including private, state, federal, etc
- Strong project management, planning, organizational and leadership skills
- Strong communications (verbal and written) and interpersonal skills
- Ability to organize and document status reports
- Ability to interface effectively with regulatory agencies, company contacts, customers and employees
- Strong working knowledge of product storage tank maintenance and repair including a working knowledge of API 653 standards
- Strong working knowledge of Marine terminal maintenance activity is preferred
- Strong computer skills and proficient in MS Office applications and in other menu driven programs used by the company
- Understand budgeting and financial processes
- Capability to provide technical guidance needed to perform tasks and maintain compliance with all company, state, and federal guidelines
- Capability to resolve operational problems and be able to work with location personnel to resolve the problem
16
Coordinator Maintenance Resume Examples & Samples
- Coordinate and accurately manage contract maintenance resources
- Interact with operations and team leads to provide guidance on major maintenance functions
- Manage “break-fix” maintenance tasks, schedule PMs, order replacement parts, and manage work order data
- Ensure activities are performed as scheduled by competent, and if necessary, certified personnel
- Work with peers and leaders to ensure priorities between system operation and O&M teams are aligned
- Ensure scheduling and all completion of required tasks meet regulatory requirements
- Maintain records and documentation of all department equipment, safety systems, and regulation compliance requirement within the maintenance management system
- Review backlog work and partners with operations and maintenance to identify priority status
- Maintain records and documentation on all department equipment, safety systems and regulation compliance requirements in the maintenance management system
- Drive and influence consistent application and improvement of processes across the organizational area
- Manage of assigned work orders including review of requests, formulation of options, selection of the best option, and completion of the work
- Take direct action in assessing risk and utilize good judgment with making decisions that can impact the overall O&M, outage, and/or project costs and schedules
- Demonstrates and encourages professional conduct, ethical behavior, and safe and efficient operation of facilities
- Develop maintenance and outage plans that include material requisitioning, manpower estimating, job standards, preventative and predictive maintenance, and equipment cost estimating
- Monitor maintenance and project scope development and status, invoicing and quality control for all maintenance activities
- Integrate primary focus of safety and compliance into all O&M activities
- Monitor job progress during maintenance. After maintenance is complete, compare actual to estimates to apply knowledge into developing future job plans
- Monitor and approve contractor invoicing
- Provides guidance and support to contract and metric administrators for Master Service Agreement maintenance
- Possess a high school diploma or equivalent
- Ability to demonstrate five (5) years’ experience within Operations and/or related field
- Possess excellent technical, administrative, and interpersonal skills
- Demonstrate a comprehensive knowledge of facility operations, maintenance, and commercial impacts of maintenance activities
- Working knowledge of Project Management and Construction Standards
- Ability to proactively identify and resolve root causes of mechanical failures
- Previously involved with managing, scheduling, and/or communicating shutdown activities efficiently and effectively
- Effectively communicate, both verbally and in writing to other individuals, teams, customers, and stakeholders of the business
- Demonstrate an intermediate knowledge of general computer applications (Word, Excel, Outlook, etc.), with the ability to learn company specific programs
- Possess a degree in Mechanics, Instrumentation, Control Technology, or Electronics
- Prior experience in a leadership and/or relevant maintenance experience in the area of responsibility preferred
- Have prior success in the operation and maintenance of compression, gas gathering, treating and cryogenic gas processing facilities, either as a leader or in a hands-on role is preferred
17
Coordinator, Maintenance Resume Examples & Samples
- Work closely with the area manager on maintenance priorities and requirements to ensure equipment availability
- Understand work notifications in the area and provide feedback to the maintenance manager regarding work-order screening, priority, requirements, risks and operational impacts
- Support our planning and scheduling departments and monitor all related break-in and/or scheduled maintenance activities
- Provide area input to break-in and planned maintenance as well as equipment outage planning, scope of work and support activities
- Synchronize field operations with the maintenance schedule requirements by working closely with the shift supervisor and main shop coordinator
- Execute input to ensure maintenance work preparation is consistent with applicable standards and are monitored in a safe, environmentally acceptable and efficient manner
- Liaise with business units to meet the schedule for break-in work
- Assist the planning team with the preparation of work packages and support supervision on the availability of services and material to ensure all jobs are executed as planned
- Five or more years of maintenance and/or operations leadership experience
- Experience in mining or the oil and gas industry is preferred
- Post-secondary degree in engineering or a mechanical or electrical trade certification; attach your Journeyman / Red Seal ticket with your application in order to be considered, if applicable
- Basic knowledge of mining priorities and maintenance and planning activities in order to support planning, scheduling and supervision in a fast pace environment
- Knowledge of the Microsoft Office suite and SAP experience is preferred
18
Coordinator of Maintenance Resume Examples & Samples
- Leads successful execution of routine maintenance activities through effective planning, executions, materials sourcing, manpower utilization, cost control, long range planning and project implementation
- Leads successful execution of non-routine maintenance and collaborate with the operations manager/supervisor and technicians to plan, manage, and coordinate related preventative maintenance, including repair and overhaul of equipment as necessary
- Responsible for using the CMMS (Maximo/OMS) and coordinating with the operations manager/supervisor and technicians to create, assign, track and close all work orders such as PMs, BLM, and EMIS
- Collaborates with other operating areas to find and implement best practices
- Associate’s degree or a minimum of 3 years work experience coordinating oil & gas operations maintenance activities
- Proficiency in Microsoft office suite of tools (Outlook, Word, Power Point, Excel)
19
Coordinator of Maintenance Resume Examples & Samples
- Ensure all work is planned and performed in area of responsibility is in strict accordance with policies and procedures (PSM, Project Life Cycle, Integrity Management Plans, and other processes)
- Ensure all work is planned in accordance to the described compliance requirements
- Interact with the Manager/Supervisor and technicians to plan, manage, and coordinate compliance related preventative maintenance, including repair and overhaul of equipment as necessary
- Responsible for local deployment of the maintenance management system (Maximo/OMS) and coordinating with the Manager/Supervisor and technicians to create and assign all work orders such
- Coordinate the requirements around PSM such as Mechanical Integrity, Inspections, MOCs, Facility Siting, initial PHAs and revalidation, Environmental testing/monitoring, Baseline Maintenance
- Ensure all documentation (permits, Job Plans, etc.) are completed on a daily basis and in accordance with deadlines
- Ensure all reports and findings are communicated to the necessary internal subject-matter experts
- Ensure document integration and retention takes place through SharePoint
- Coordinates with Field Office Administrators to complete and submit Purchase Orders, Request For Service and Back Log orders
20
Coordinator of Maintenance Resume Examples & Samples
- Interact with local supervision, control room operations, lead technicians, and coordinator of maintenance to provide for day-to-day operations functions and prioritization of maintenance task
- Coordinator of all DOT and PSM tasks for the operating area, scheduling operations PM’s and Code work along with managing work order databases for all operations activities
- Scheduling and quality completion of operations tasks; maintaining an acceptable backlog of maintenance work identified by the operations group
- Ensure scheduling and completion of required tasks meet regulatory requirements
- Efficient use of O&M budget and other resources
- Ensure all PSM/DOT requirements are met per WIMS/SIP/WILSOP
- Ensure coordination with Pipeline Control on all station and plant operations and maintenance activities
- Complete documentation in maintenance management system and Management of Change (MOC) programs
- Manage assigned operational work orders including review of requests, formulation of options, selection of options, and scheduling completion of work
- Evaluation and continuous improvement of regulatory compliance for all onshore facilities for both regulated and non-regulated assets
- Utilize and coordinate all necessary resources to effectively achieve all operational requirements
- Ensures activities are performed as scheduled by competent and, if necessary certified personnel, includes preparation of scope of work as needed, ensuring service contracts or purchase orders are in place, verifying qualifications of contractor and employees are in place for the task being performed, report, review and acceptance of all operations activities, and communication with local ALT as appropriate
- Works closely with Safety Representative to ensure all “safe work” practices are being followed and appropriate procedures are in place
- Acting liaison with Safety Representative and Subject Matter Experts (SME’s) to ensure all operational and regulatory requirements are continuously met and improved
- Partners with Coordinator of Maintenance (COM) to identify priority status of maintenance activities
- Ensures activities follow WIMS/SIP/WILSOP policies and procedures
- Maintains and records documentation on all departments equipment, safety systems and assures regulatory compliance requirements are in the required filing systems and data bases
- Minimum of five(5) years’ experience working within the Natural Gas Industry
- Ability to work in both a team setting and individually with minimal supervision
- Demonstrate a comprehensive knowledge of facility operations, maintenance, and the bottom-line impacts of maintenance activities
- Knowledge of PSM ,DOT, and State/Local regulatory agencies compliance requirements
- Ability to effectively communicate both verbally and in writing to other individuals, teams, customers, and stakeholders of the business
- Ability to demonstrate an intermediate knowledge level of Microsoft Office Applications (Word, Excel, Outlook, and PowerPoint), with the ability to learn other company specific applications
- Associates Degree or Technical Certification preferred
- Minimum of seven (7) years’ experience working within the Natural Gas industry preferred
- Knowledge of Mobile Bay systems, equipment, policies and procedures
- Understanding of WIMS/SIP/WILSOP policies and procedures
21
Coordinator, Maintenance Secondary Extraction Resume Examples & Samples
- Run the execution of daily maintenance activities performed by employees and contractors, as per approved weekly and daily schedules
- Drive a culture of safety through daily toolbox meetings
- Identify and remove roadblocks for our contractors to enable them to execute maintenance tasks effectively
- Supervise contractors and maintain contracts in a manner that ensures that our safety and work performance standards are upheld, that resources are managed effectively, and that our business objectives are met
- Review, develop, and update preventative maintenance strategies for equipment
- Collaborate with supervisors, the reliability team, the operations team, and management to understand all work notifications associated with operational commitments
- Experience as a maintenance planner, scheduler, coordinator, or supervisor
- Valid Alberta or Interprovincial Red Seal Journeyman Electrical or Instrumentation Certificate; attach your certificate with your application to be considered
- Deep understanding of mechanical systems and associated maintenance requirements
- Familiarity with computerized maintenance management systems, SAP is preferred
22
Coordinator Maintenance Resume Examples & Samples
- Ensures all work is planned and performed in accordance with Williams’ standards, processes and procedures (WIMS, PSM, Project Life Cycle, Integrity Management Plans, environmental testing and monitoring, etc.)
- Prepares the scope of work, ensuring service contracts or purchase orders are in place, verify qualifications of contractors, report review and acceptance, and communicate with other departments as appropriate
- Recommends to operations manager/supervisor and training liaison opportunities to improve facility training programs consistent with WIMS requirements and Williams’ Operator Qualification programs
- Ensures all reports and findings are communicated to operating area and the necessary internal subject matter experts
- Reviews all work orders for timely completion with adequate documentation
- Analyzes, recommends and implements process improvements in areas that are inefficient
- Coordinates with field office administrators (FOAs) to complete and submit POs, RFSs and back log orders
- Maintains controllable O&M expense metrics to improve budget development and review
- Understands operational economics of the operations
- Available for callouts, including nights, weekends, and holidays
23
Coordinator, Maintenance Primary Extraction Resume Examples & Samples
- Oversee the execution of daily maintenance activities performed by employees and contractors, as per approved daily and weekly schedules
- Lead daily toolbox meetings to drive a culture of safety
- Identify and remove roadblocks facing our contractors to enable them to execute maintenance tasks effectively
- Support the maintenance planning and scheduling team by providing current and accurate feedback on daily job completion
- Supervise contractors and maintain contracts in a manner that ensures that our safety and work performance standards are upheld, that resources are handled effectively and that our business objectives are met
- Review, develop and update preventative maintenance strategies for equipment
- Collaborate with supervisors, the reliability team, the operations team and management to understand all work notifications associated with operational commitments
- Minimum of five years’ experience working in maintenance in a heavy industrial environment
- Experience as a maintenance planner, scheduler, coordinator or supervisor
- Valid Alberta Journeyman or an Interprovincial Red Seal Journeyman Certificate; attach your Journeyman / Red Seal ticket with your application in order to be considered
- Familiarity with computerized maintenance management systems (SAP is preferred)
- Excellent understanding of maintenance and operations as they relate to the safe production of bitumen
- You continually seek greater knowledge about the systems, processes and hazards in the workplace to understand not just what you do but why you do it
24
Pre Maintenance Condition Coordinator Resume Examples & Samples
- Are interested being part of a team with two exciting rates of pace, were you can contribute to unscheduled repairs and/or improvements
- You're comfortable with Condition Based Monitoring practices such as thermal imaging, vibration analysis, oil analysis and visual inspections and interpreting data for faults and offering solutions
- Enjoy contributing to large projects and generating long term plans
- You're a relationship builder, enjoy connecting with people
25
Coordinator Maintenance Resume Examples & Samples
- Ensure all work is planned and performed in area of responsibility is in strict accordance with policies and procedures (WIMS, PSM, Project Life Cycle, Integrity Management Plans, and other processes)
- Prepare the scope of work, ensuring service contracts or purchase orders are in place, verify qualifications of contractors, report review and acceptance, and communicate with other departments as appropriate
- Responsible for assisting Manager/Supervisor and Training Liaison in developing facility training programs consistent with WIMS requirements and Williams’ Operator Qualification programs
- Responsible for local deployment of the maintenance management system (Maximo/OMS) and coordinating with the Manager/Supervisor and technicians to create and assign all work orders such as PMs, BLM, and EMIS. Will be responsible for the deployment of the Maximo system at the District level
- Ensure all reports and findings are communicated to the necessary internal SMEs, and document integration and retention take place through SharePoint
- Review all work orders to ensure they are being completed on time and with adequate documentation
- Participate in Contractor Management (involved in Contractor bids, selection, Qualification reviews, cost controls, Visitor Orientations, etc.)
- Coordinates with FOAs to complete and submit POs, RFSs and back log orders
- Associate’s degree (Experience in operations, engineering, or project management may be substituted for education)
- Industry specific operations experience, which includes, but not limited to, processing plants, gathering, NGL/Petchem and transmission pipelines
26
Maintenance Services Coordinator Resume Examples & Samples
- 5+ years experience working in a fast paced and demanding environment, with a focus on providing the best possible service to a demanding group of customers
- Candidate must have and demonstrate the following
- Demonstrated ability to plan and prioritize tasks in a self-directed work environment and maintain high levels of productivity
- Strong customer service and problem solving aptitude
- The ability to communicate effectively and provide direction to contractors and vendors performing services for the company
- Manages time efficiently with demonstrated ability to multi-task
- Familiarity with Mac platform and Microsoft Office programs
- Must work well under pressure in a demanding environment
27
Industrial Maintenance Technology Program Coordinator Resume Examples & Samples
- Associate's Degree required (although certifications in area(s) of instruction combined with experience may substitute) / Experience in teaching in an online environment and Bachelor’s degree or higher as related to Industrial Maintenance, Advanced Manufacturing, Engineering, Technology Management or similar preferred
- Experience in industrial maintenance/advanced manufacturing required
- Instruction and/or training experience required
- Understanding of industrial maintenance including, Blueprint Reading, Hydraulics/Pneumatics, Industrial Electrical and PLC (Allen Bradley)
- Robotic maintenance experience preferred
- OSHA safety certifications preferred
- Safety orientation/awareness a must
- Maintenance repair skills (lab equipment or installations of new equipment)
- Ability to build student rapport and exhibit compassion and a strong commitment to student success
- Understanding the maintenance needs in area industry
- Effective communication and computer/technology skills
28
Maintenance Control Coordinator Resume Examples & Samples
- Maintains a shift log including documentation of aircraft worked on during shift
- Reviews prior shift logs and is familiar with previous shift activity
- Other duties that maybe assigned by the M.O.D. or Senior Manager of the Department
- Reports to: Senior Manager MCC / Maintenance Planning, Technical Services
- Knowledge of airline maintenance practices, federal aviation regulations, and Frontiers General Maintenance Manual policies and procedures
- Airframe and Powerplant License is required
- FCC First Class Radio Telephone Certificate preferred
- Requires 5 years of Line Maintenance experience or 2 years C-Check experience and 2 years avionics troubleshooting experience
- Previous experience as a maintenance supervisor preferred
- Previous factory approved training on Airbus 320 Family preferred
- Must demonstrate behavior that portrays the company core values of Safety, Respect, Trust,
- Collaboration, Value, and Passion while communicating with personnel and acting on behalf of the company
- Must have the ability to plan, organize, and administrate workloads to subordinates
- Vol.D Must attend and successfully complete Maintenance Training Required Inspection Item course
- Excellent Airbus systems knowledge and troubleshooting skills
- Must have excellent written and oral communication skills, and be able to interface effectively with Engineering, Maintenance, Purchasing, Flight Operations Management, Flight crews, and Dispatchers effectively
29
Coordinator, Maintenance Contractor Resume Examples & Samples
- Assists with the preparation of departmental budget
- Coordinates and supervises the designated work (repairs and installation of equipment) by external contracted firms and personnel for work to be performed at the Gaffney Manufacturing Facility and at the Ryder Distribution Center
- Responsible for preplanning and organization of contractor activities during minor and major factory outages and shutdowns
- Generates and maintains Nestle Contracts and Service Agreements with specified third parties
- Achieves safety goals within department concerning doctor cases and reduce hazards contributing to injuries
- Recommends improvements to reduce cost and increase efficiency in area of responsibility. Implements improvements as approved
- Works closely with Maintenance & Facilities Planning, Production Planning and Warehouse to minimize contractor scheduling conflicts
- Consistently applies effective troubleshooting skills
- Completes cost-effective repairs in a timely manner
- Interprets and understands engineering drawings, manufacturer's instructions and plant maintenance procedures and specifications
- To perform back up duties on an as needed basis (i.e. LOA, Sick days and Vacations) for Planner Scheduler and Facilities Coordinator positions
- Maintains a positive working relationship with fellow department members and other departments
- Ensures that all machinery is in safe working condition. Adheres to safety policies and procedures and fosters a safe work environment
- Adheres to GMP, operational policies and procedures & ensures that contractors in area follow same. Provide and coordinate training programs for contractors (ie. GMPS, Safety, and Quality)
- Adheres to plant attendance policies
- Completes assigned work orders on a timely basis, including scheduled, emergency and preventative maintenance work orders. Recommends changes to PM program to improve productivity
- Solves repetitive problems in area of responsibility without the assistance of others
- Understands and follows factory management systems for human safety, food safety and/or environmental management. Understands and actively works toward achieving management system targets and objectives
- Follows the plant rules, procedures, and/or practices related to management systems. Team members will report incidents and unsafe conditions immediately, maintain compliance with regulations, and refer to the appropriate management system on all related procedures and programs
- Must have 3-5 years experience in a Maintenance or Facilities environment
- Must have demonstrated ability to assume lead responsibilities in the absence of relevant departmental personnel
- Demonstrates working knowledge of SAP / Globe for processing of work orders, generation of purchase requisitions, etc
- Demonstrates good mechanical, troubleshooting, and maintenance skills; has good maintenance knowledge and understanding of Nestlé facilities, refrigeration equipment/systems operation
- Demonstrates basic electrical skills including troubleshooting of motors, electrical control circuits and instrumentation on facility and support equipment. Demonstrates the ability to read electrical drawings and schematics
- Demonstrates knowledge of Nestlé equipment and SOP’s in the following areas: NH3 refrigeration systems, water systems; fire systems; HVAC; buildings & grounds (infrastructure); and all other Nestlé facilities equipment/systems
- Ensures that all local, state, and federal regulations; polices; and procedures are being met by self and external contractors
30
Coordinator, Maintenance Resume Examples & Samples
- Train operating staff to conduct quality operator routines and to use our management system online to record the completion of the routine and report exceptions found in the field
- Create and update online maintenance plans for each facility
- Visualize the hazards associated with completing preventative maintenance activities during planning phase and identify steps in plans for safe execution
- Coordinate with vendors on the execution and reporting requirements to meet the needs of the preventative maintenance program
- Participate in incident investigations and root cause analysis for equipment related issues
- Interface with engineering and operations on additions and deletions or modifications to the program requirements
- Participate as a member of distribution’s response management team
- Electrical, mechanical and/or technical experience is preferred
- Experience as a maintenance planner, scheduler, coordinator or supervisor is preferred
- At least five years of experience in dealing with the maintenance of hydrocarbon handling equipment is preferred
- Post-secondary education in an applicable field is preferred
- Familiarity with computerized maintenance management systems is preferred
- Good knowledge of maintenance workflow process
- Knowledge of industry preventative maintenance techniques and best practices
- Good knowledge of tanks, pumps, piping, and loading equipment as they relate to terminal operations is an asset
- Strong interpersonal and leadership skills, with the ability to influence others
- Strong planning and organizational skills, with the ability to handle multiple projects
31
Maintenance Rule Coordinator Resume Examples & Samples
- Must have a BS in Engineering from an ABET accredited college or university
- Must have a minimum of 8 years of operating nuclear plant experience
- Must have at least 5 years of experience in Equipment Reliability
- Knowledge in Life Cycle Management
- Knowledge in Single Point Vulnerabilities
- Knowledge in Preventive Maintenance
- Knowledge of System Health Reporting, Monitoring, and Trending
32
Coordinator Maintenance Resume Examples & Samples
- Assisting the supervisor by allocating tasks to crew members in accordance to the daily plan making sure they understand their tasks and activities to be performed during their shift
- Reporting to the shift supervisor the status of all maintenance activities throughout the shift to ensure compliance to the plan
- Managing unscheduled work parts, freight and tooling where required
- Ensuring the CMS compliance with all contractors and equipment brought to site
- Ensuring that accurate and comprehensive shift handovers are conducted
- Trade qualification -mechanical, diesel fitter etc
- A Current WA C Class Driver’s License
- Similar experience in a leadership role managing maintainer crews
- Proficient in SAP and MS Office suites
- Good communication skills and the ability to understand and articulate technical issues
- Previous experience as a maintainer in heavy industry
33
Coordinator, Maintenance Resume Examples & Samples
- Own the maintenance schedule and break-down work for the mine equipment maintenance department
- Collaborate with supervisors and operations to execute work while giving direction on priorities
- Act as the key contact between field and shop maintenance
- Work with scheduling, planning and supply chain groups to ensure deliverables from supporting groups are met
- Provide input to maintenance area managers and the cross-functional teams regarding priority, requirements, risks, and maintenance impacts of all work required on a daily basis
- Provide major equipment outage and servicing recommendations
- Maintain a high level of safety through effective communication and ensure compliance with all workplace rules, procedures, and occupational health and safety codes
- Set up maintenance work orders and requisition system for parts and supplies for all mine equipment maintenance assets
- Five or more years’ experience in a supervisory and/or maintenance coordination role
- Experience in oil sands, pipeline construction, or a related field
- Trade certificate or relevant diploma (mechanical, electrical, welding)
- Strong knowledge of specific equipment such as dozers, haul trucks, shovels, or other mobile mining equipment
- Proficient in Microsoft Office and at least one industry standard enterprise resource tool (SAP is preferred)
34
Maintenance & Calibration Coordinator Resume Examples & Samples
- Ensure maintenance and calibration are performed on time as required per calibration and maintenance procedures, and that the schedules are met
- Notify responsible personnel/user of upcoming calibration and maintenance due dates
- Contact calibration and maintenance service providers and initiate purchase orders for the service
- Ship equipment to service providers for calibration or maintenance
- Once received back from service providers, verify calibration report is acceptable and document the information
- Initiate Non-Conforming Material Report if equipment is found to be out of tolerance during calibration or any time during use
- Make arrangements to deliver the calibrated equipment back to responsible personnel/user
- Create calibration and maintenance reports on a regular cadence
- Track and trend calibration and maintenance data
- Review change orders related to calibration and maintenance
- Support verification/validation activities for new equipment or based on need
- Support internal and external audits and inspections
- Report unsafe conditions
- Support projects or activities as required by the company
- Perform other duties or special projects as assigned by management
- Proficient with MS Office Suite (Outlook, Excel, and Word)
- Knowledge of Good Documentation Practices
- Knowledge of Good Manufacturing Practices
- Previous experience with metrology
- Ability to understand and interpret tolerances
- Proficiency with Microsoft Access or other database software
- Knowledge of FDA and ISO requirements pertaining to calibrations and maintenance, and control and monitoring of Measuring Devices