Manufacturing Operations Manager Resume Samples
4.5
(185 votes) for
Manufacturing Operations Manager Resume Samples
The Guide To Resume Tailoring
Guide the recruiter to the conclusion that you are the best candidate for the manufacturing operations manager job. It’s actually very simple. Tailor your resume by picking relevant responsibilities from the examples below and then add your accomplishments. This way, you can position yourself in the best way to get hired.
Craft your perfect resume by picking job responsibilities written by professional recruiters
Pick from the thousands of curated job responsibilities used by the leading companies
Tailor your resume & cover letter with wording that best fits for each job you apply
Resume Builder
Create a Resume in Minutes with Professional Resume Templates
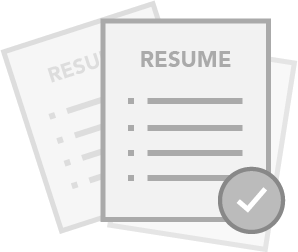
CHOOSE THE BEST TEMPLATE
- Choose from 15 Leading Templates. No need to think about design details.
USE PRE-WRITTEN BULLET POINTS
- Select from thousands of pre-written bullet points.
SAVE YOUR DOCUMENTS IN PDF FILES
- Instantly download in PDF format or share a custom link.
DB
D Boyle
Drew
Boyle
1385 Joseph Summit
Phoenix
AZ
+1 (555) 745 0998
1385 Joseph Summit
Phoenix
AZ
Phone
p
+1 (555) 745 0998
Experience
Experience
New York, NY
Manufacturing Operations Manager
New York, NY
Satterfield-Thompson
New York, NY
Manufacturing Operations Manager
- Contributes to the performance of suppliers including contributing to the development of SOW and performance feedback to drive improvement
- Oversees training and development of partners directly and indirectly managed and makes effective staffing decisions
- Manage the operation utilizing LEAN /Six Sigma principles. Daily Management tools and Continuous Improvement techniques
- Establishing and ensuring achievement of all unit Key Performance Indicators while ensuring adherence to and continuous improvement for all area MCRS elements
- Establish key performance indicators and drive shop floor metrics to lead improvements in quality, productivity, on-time delivery and cost reduction
- Develop and train staff of business unit leaders to establish shift production schedules and goals. Plan labor capacity and manage physical assets
- Establish, meet and report to management Key Performance Indicators (KPIs) on a monthly basis
Dallas, TX
EAS Manufacturing Operations Manager
Dallas, TX
Kuphal-Bednar
Dallas, TX
EAS Manufacturing Operations Manager
- Lead EMSD EAS Manufacturing Team
- Achieve EAS Supply Chain performance metrics related to service, order cycle time, inventory and turns improvement & NWI
- Achieve EAS P&L performance objectives in both operating and strategic plans
- Successfully launch EMSD EAS NPI ensuring cost and service performance
- Driving supply chain imperatives for order management process improvement, planning & systems improvement, fulfillment process improvement and SOS network optimization for the EAS
- Drive & Chair EMSD EAS IBP process
- Assist in preparing the EMSD Supply Chain team for BT and SAP implementation
present
Boston, MA
Senior Manufacturing Operations Manager
Boston, MA
Kuphal Inc
present
Boston, MA
Senior Manufacturing Operations Manager
present
- Lead the engineering industrialization team developing the drafting and programming department providing technical guidance and on hands support
- Process engineering includes tooling design, job tracking, fabrication and new process implementation
- Driving product commercialization project schedules including working through roadblocks to deliver new products on time and on budget
- Engages in problem solving in complex situations and process improvements in streamlining work processes and improving results
- Developing and leading quality, customer service and cost improvement programs in a field or company environment (5 years)
- Driving supplier and CM manufacturing improvement, optimization and cost savings
- Developing feasible actions plan within supply chain to address marketing objectives and response to customer feedback and expectations
Education
Education
Bachelor’s Degree in Business
Bachelor’s Degree in Business
University of California, San Diego
Bachelor’s Degree in Business
Skills
Skills
- In depth knowledge of CAPS and its products. Demonstrate basic pharmacy knowledge to include injectable drug names and CAPS catalogue
- Analytical and reasoning ability for problem solving, strategic planning and creativity/innovation, and excellent judgment for making complex decisions
- Strong leadership skills, with the ability to coach and mentor others
- Ability to manage large or multiple projects
- Ability to recommend and implement solutions
- Ability to work well with others and perform as a team
- Ability to handle multiple tasks and meet deadlines
- Ability to build relationships
- Strong communication skills
- Excellent verbal, written and presentation communication skills
15 Manufacturing Operations Manager resume templates
Read our complete resume writing guides
1
Furniture Manufacturing Operations Manager Resume Examples & Samples
- Work with Plant Management to plan and prioritize daily workload and achieve established productivity standards and goals
- Ensure that all products are manufactured at the best acceptable standards possible. All components should be correctly filled, set-up, upholstered and trimmed to Williams-Sonoma, Inc. specifications
- Work with the associates to maximize the productivity of the departments while ensuring quality and adhering to and complying with all safety policies and laws
- BS Business, Engineering or related field and 2-4 years related experience or equivalent combination of education and experience in high-end upholstery manufacturing environment
- Ability to read, comprehend, analyze, and interpret general business information. Requires the ability to write reports and communicate effectively using telephonic, written, and electronic means. Requires the ability to effectively present information one-on-one, in small and large group situations to customers, management, and associates of the organization
2
Manufacturing Operations Manager Resume Examples & Samples
- Ensures that production equipment and facility are maintained in accordance with established standards and schedules
- Establishes and implements quality and cost improvement initiatives that are supported and sustained by all manufacturing and/or distribution partners. Contributes to the development of effective cost-saving initiatives. May develop production scorecards to facilitate continuous improvement of quality, food safety, efficiency, inventory accuracy and reporting
- Manages the production schedule to support improved productivity and reliability and to maintain established safety stock levels. May provide buyers with raw material delivery schedules to enable buyers to execute purchase orders
- Supports all established plant and departmental goals and objectives. Supports development and implementation of programs and procedures that contribute to the success of the department and the Company
- Developing and leading quality, customer service and cost improvement programs in a field or company environment (3 years)
- Management (3 years)
- Production planning and scheduling (3 years)
- Managing budgets (1 year)
- Organization and planning skills
3
Senior Manufacturing Operations Manager Resume Examples & Samples
- Provides leadership and support for managers, supervisors and partners to continuously improve productivity, communications and morale. Works as a team member with other managers in the plant and Starbucks to ensure consistency of operations and alignment with company goals and strategies
- Ensures compliance with Hazard Analysis and Critical Control Point (HACCP) and with American Institute of Baking and Starbucks quality standards
- Identifies and implements cost-savings measures that maintain quality and meet or exceed plant and company targets
- Maintains and improves customer service levels for all business units served. Ensures clear communications among business units and understanding of new and changing business requirements
- Supports all established plant and departmental goals and objectives. Develops and maintains programs and procedures
- Developing and leading quality, customer service and cost improvement programs in a field or company environment (5 years)
- Management (5 years)
- Managing budgets (5 years)
- Working in a major food service or food company distribution center (5 years)
4
Manufacturing Operations Manager Resume Examples & Samples
- Reports directly to VP, Operations
- Responsible for the daily manufacturing operations of multiple Value Streams as measured by meeting SQDP targets
- Participate in setting the vision and strategy to achieve breakthrough results while sustaining current KPIs
- Critical success factors for this role: maintaining a disciplined Daily Management process, utilizing DBS tools (DMP, SW, 5S, PSP, QSB), developing talent and building teams
- Bachelors degree - Business or Engineering preferred
- 3-5 years' experience in operations and/or 3+ years previous management experience
- Experience with lean tools such as Value Stream Mapping, Standard Work, 5S, Kanban, and Practical Problem Solving
- Other skills include leadership, team development, budgetary responsibility, and project management
5
Senior Manufacturing Operations Manager Resume Examples & Samples
- Travel 75% internationally and within the US
- Language skills a plus (Japanese, Mandarin)
- Strong presentation and facilitation skills
6
Manufacturing Operations Manager Resume Examples & Samples
- Drive Eaton Zero Incident Culture through his value stream by the effective deployment of MESH process and elements. Supports EHS department initiatives, and monitor performance indicators in order to execute action plans to mitigate any safety risk within his operation
- Pursuit Customer satisfaction and operational excellence by delivering high five goals, pursuit zero defects and drive continuous improvement activities in his area of responsibility through the deployment and utilization of Eaton Business System policies and processes, such as ELSS, CIF, Participate in PROLaunch as DGC member when required, EQS and others as applicable
- Develops in conjunction with Plant leadership policies related to the production area, builds synergies with functional areas for creating efficient and effective plans for workload balance, prioritization of task and resource utilization and coordination for achieving high productivity levels
- Maintains strong and healthy employee relationships with all personnel as well the Union to ensure a progressive workforce, a climate of high performance, accountability, team work and ethics in addition to promote and live “Power of One”
- Interacts with all departments to ensure the proper Safety and Quality of Eaton products. Provides direction and overall leadership and support for cost out initiatives at the plant and divisional levels
- Performs activities according to the Quality and Environmental policies established by the business
- Support and/or participate on Continuous Improvement Activities such as: Kaizen, Ideas Programs, cost out and/or demonstrate improvements in goals year over year in our processes or practices aligned to achieve or business goals and/objectives
- O Bachelor Degree in Industrial Engineering or similar
7
Manufacturing Operations Manager Resume Examples & Samples
- Implements the overall industrial structure (organisation, staff and skills, investments, teaming, partnering, etc.) covering all fields of the SIX industrial requirements, defined by the Operations Director and SIX Leadership Team, and proposes improvement actions plan accordingly
- Is accountable for all activities to do with the management of the physical and related information flow. That includes the preparation, planning, and execution of procurement, production and delivery. Manages end to end supply chain for both buy through materials and assembled/manufactured/serviced products
- Manages industrial activities in Industrial Supply Chain,
- Guarantees the Manufacturing Engineering of new products (from design phase, modelling to production) and the reliability and competitiveness of technological solutions
- Guarantees the internal and external manufacturing to meet cost, time and quality optimising inventory and WIP (Work in Process)
- Contributes to the effective deployment, maintenance and improvement of industrial tools and processes (ERP - Enterprise Resource Planning, CAD-CAM ...) and guarantees the maintenance
- Plays a key role in introducing and managing change and developing continuous improvement culture
- Guarantees the performance of the flow of information and the physical flow in term of I/O and internally (in-coming, inventories, CTA, served, distribution, management of returns) in accordance with the Industrial Plan
- Manages and develops the company computerised manufacturing systems ( planning and execution) and procedures to optimise efficiency and ensure production planning best practices
- Optimises the WIP (Work In Progress), inventories and lead-time of the entity through improvement and reduction actions whilst meeting customer requirements
- Contributes to the performance of suppliers including contributing to the development of SOW and performance feedback to drive improvement
- Manages the interface with the customers of the entity (Other Thales sites, Final customers, Sales administration )
- Guarantees the customer OTD (On Time Delivery) of the SIX Production and Service requirements
- Manage the preparation of budgets and ensure they are presented in a timely manner for the consideration of the Director Operations and Projects and recommending policy changes and developments
8
Senior Manufacturing Operations Manager Resume Examples & Samples
- 8+ years of experience in Manufacturing and experience in a GMP medical manufacturing environment required
- Management experience (either Production, Engineering, Quality, etc.)
- Experience in an injection molding environment preferred
- Ability to plan, organize and prioritize
- Ability to make good judgment calls
- Getting work done through others that are not direct reports
- Motivating others
- Building relationships with other departments
- Interviewing and presentation skills
- Strong coaching and development skills
9
Manufacturing Operations Manager Resume Examples & Samples
- Recruits, trains, develops, rewards and recognizes personnel to achieve targeted strategies and goals. Creates the appropriate organization structure to reflect and achieve current/planned goals and objectives
- Ensures performance, quality, cost, schedule, profit and customer satisfaction targets are achieved with risks identified and mitigated and opportunities exercised
- Establishes interfaces with Divisional/Corporate management to assess customer needs and assures accurate project or program technical direction for operations engineering and manufacturing
- Works closely with peer Plant and Division personnel to develop plans/focus to assure continuous improvements that will benefit Operations. Provides leadership and valuable participation in team activities that will enhance the overall effectiveness of the Plant
- This position requires excellent interpersonal skills, demonstrated ability to effectively lead in a team environment, adaptable to change, able to manage competing priorities, excellent analytical and problem solving skills, excellent written and verbal communication skills and sense of business savvy
- This position operates with only general direction and minimal supervision from the Plant Manager, and has full responsibility to make decisions that directly impact site goal achievement. Requires broad range of management prerogative necessitated by a large number of operating decisions. Annual budgetary responsibility $20MM+
10
Paint Manufacturing Operations Manager Associate Resume Examples & Samples
- Lead Business Team meetings
- Responsible for interfacing with internal customers and developing operation/business plan
- Responsible for achievement of daily production requirements for all customers
- Responsible for ensuring timely receipt and shipment of materials from/to suppliers and customers
- Responsible for continuous improvement initiatives
- Demonstrated knowledge in lean manufacturing and automation in the manufacturing environment
- Proven ability to drive cultural changes from the top down, through all organizational levels
- Ability to communicate effectively across all levels of the organization
- Experience managing employees in a represented manufacturing environment
- Experience in truck paint applications including: pre-treat, ecoat, topcoat, and paint repair
- Ability to coach employees at all levels
- Experience with quality systems related to paint and the ability to perform root cause analysis on defects
11
Senior Manufacturing Operations Manager Resume Examples & Samples
- Supervise, lead and mentor a team of Operations Engineers and assistants in the planning and execution of program objectives
- Participate on the Program or Business Area Leadership team and provide the Operations perspective for successful program planning, organization and execution. Support “what if” analysis as needed during program execution. Lead an IPT or function as Production Program Manager if required
- Develop and guide the Manufacturing & Supply Chain strategy and approach for successful execution of the program at various maturity levels (Advanced Development through Full Rate Production)
- Develop and manage execution of production competiveness strategies to win production phase contracts
- Manage development and execution of program manufacturing plans including prototype and production configuration build schedules, material requirements, factory schedules, etc
- Define program’s operations staffing needs and skill sets required to support current and future phases of the program. Also provide input to program leadership on projected needs and skill sets for other functions as the program progress through its life cycle (ie subcontract management/administration, procurement, manufacturing, sustaining engineering, quality, test engineering, etc)
- Determine resource requirements, including labor, expense, space/facility, production capital equipment and business systems tools to support program
- Develop and represent the Manufacturing and Supply Chain Management portions of program proposals and contract negotiations
- Coordinate program requirements and manage interface with functional organizations (i.e. security, purchasing, warehouse, factory, quality, configuration management, etc…)
- Lead and conduct Manufacturing Readiness Assessments (MRA) and establish and manage plans to attain Manufacturing Readiness Level (MRL) requirements throughout the supply chain
- Plan and manage Transition to Production efforts (planning through execution) for assigned programs
- Create and manage Average Unit Production Cost (AUPC) models
- Drive producibility culture, including application of DFM/A techniques, with project teams to attain Average Unit Production Cost (AUPC) requirements
- Provide input to product evolution roadmaps and configuration planning activity. Review and evaluate engineering drawings and change notices as needed. Provide input to CCB on change effectivity and direct disposition actions as needed
- Plan and manage Value Stream analysis to optimize production and test flows (including make/buy trade studies) across supply chain
- Drive lean manufacturing culture, including application of process control and improvement techniques, with project and factory teams to attain AUPC, throughput and quality performance requirements
- Establish and manage the collection, analysis and reporting of manufacturing data (metrics) in an effort to promote continuous improvement
- Develop and present operations topics at major program reviews (ie SRR, PDR, CDR, PRR, QPRs). Participate with program leadership in creation of agendas and walk-thru preparatory reviews of all major program review presentation materials
- Execute assigned Cost Account Manager responsibilities with a strong emphasis on operations support, touch labor and material cost analysis
- Support development and use of operations standard procedures, tools, artifacts and metrics to enable the successful operations execution of program. Examples include: MRP, cost estimating, MRL analysis and planning, build readiness, material and job order status reporting, CDR, PDR, PRR, etc…
- Actively support Operations Engineering Team initiatives to implement defined roles, hand-offs, interfaces, etc, between Programs Operations Engineering, Supply Chain Management, Manufacturing and other operations execution functions
- Function as a Subject Matter Expert (SME) for one or more operations subject matters such as Costpoint, Property Control, DTUPC, DFMA, MRL, EVM, etc
- 15+ years operations planning & execution experience in manufacturing industries
- 7+ years supervisory/leadership experience
- Extensive proposal/cost estimating & management experience, including Earned Value Management
- Direct experience working in an Engineering Development environment
- Direct experience with Manufacturing Readiness Levels or similar transition to production tools
- Direct experience working in a Full Rate Production environment
- Direct experience in interfacing with senior level customers and company management
- Direct experience creating, championing, and implementing manufacturing operation related strategies
- Excellent people skills, with experience leading and collaborating in a multi-disciplinary, diverse and dynamic team environment
- Excellent analytical problem solving skills and capability
- Excellent organizational, leadership and delegation skills
- Outstanding work ethic and commitment to team success
- Excellent grasp of, and ability to articulate, the principles of product cost and its drivers
- Strong knowledge of business processes (from order contract receipt through invoicing) and accounting principles as applied to ERP systems
- Working knowledge of procurement practices and processes
- Strong knowledge of manufacturing engineering and planning
- Strong knowledge of ISO9000/AS9100 quality systems
- Proficiency with Excel & ERP systems (prior Costpoint experience desired)
- Excellent communication skills (written, verbal, & presentation)
- Proficient with MS office products
- Existing DoD Secret clearance
- Direct experience with deploying lean manufacturing strategies and techniques
- DoD (or other regulated industry) and commercial experience
- Prior experience in Design-to-Cost or Cost Estimating will be a significant plus
12
External Manufacturing Operations Manager Resume Examples & Samples
- BSc(Hons) or equivalent in an Engineering or Physics degree
- At least 10 yrs experience in the semiconductor Back End
- Experience managing Subcontractors or Material Suppliers (i.e. external companies)
- Management experience
- Background in Assembly and/or Test Manufacturing or Engineering mandatory
13
Senior Manufacturing Operations Manager Resume Examples & Samples
- BA/BS in Industrial Manufacturing ot Mechanical or Business Administration, or a 4-year technical degree in related discipline
- Lean Manufacturing expertise and or Six Sigma belt holder
- Prefer knowledge and functional usage of SAP MRP system
- 10+ years of experience in manufacturing management, preferably in a process-oriented operations and/or related industry
- Minimum of 5 years of experience managing a significant segment of a large manufacturer or the entire operation of a smaller manufacturer
- Ability to influence key members of the management team
- Proven cross-functional collaboration skills leading to successful business results
- Ability to apply broad business expertise to solve complex operational issues
14
Manufacturing Operations Manager Resume Examples & Samples
- Fabrication experience highly desired
- Experience with plasma cutters and brake press
- Mig welding experience a big plus
15
Manufacturing Operations Manager Resume Examples & Samples
- Serve as the primary interface between the Program Office, Design Engineering, and Manufacturing
- Work closely with engineering teams in early stages of designs to ensure designs are producible and affordable
- Coordinate and direct activities between Manufacturing, Engineering, Materials, and Test to develop and execute Manufacturing Build Plans
- Create and manager schedule and cost requirements and provide Manufacturing visibility to the Program Office and/or customer
- Solve complex technical problems related to engineering and manufacturing
- Demonstrate strong leadership, project management, and communication skills
- Use SAP/MRP and other software tools daily
- Demonstrate proficiency in MS Office Suite (Word, Excel, Powerpoint, etc.)
- Bachelor's Degree in Engineering, or other related STEM Field with a minimum of 5 years related work experience, or an MS Degree in a STEM Field with at least 3 years of related experience
- Experience with electronics manufacturing, test, or design
- 2+ years of experience in Project Management or Leadership including exposure to cost and schedule management
- Ability to obtain and maintain a Secret Security Clearance. An interim clearance is required to start. Secret Clearance must be obtained within three months of start. US Citizenship is a prerequisite
- Bachelor's Degree in Engineering, or other related STEM Field with a minimum of 9 years related work experience, or an MS Degree in a STEM Field with at least 7 years of related experience
- Experience with design and producibility requirements
- Ability to obtain and maintain a Secret Security Clearance. An interim clearance is required to start. Secret Clearance must be obtained within three months of start
- Active Secret or Top Secret Clearance
- CAM/EVMS knowledge
- Experience with proposal development, design reducibility, and production readiness
16
Manufacturing Operations Manager Resume Examples & Samples
- Plans and supervises execution of daily activities in assigned area(s) and assures leadership coverage on multiple shifts. Assigns and delegates tasks. Monitors schedule performance. Develops and implements corrective actions
- Develops and implements local and shorter-term solutions supporting departmental, divisional, and corporate policies and decisions. Contributes to policy-making process
- Establish, maintain, and monitors processes and procedures ensuring high quality of the area product/service, efficient operation. Upholds compliance with ISO 9001 requirements, EHS, and corporate policies
- Assures the product of service of the assigned area meets all applicable quality requirements (i.e. engineering, project specific, product and industry standards)
- Control cost of providing the products and services of assigned area(s). Monitors actual costs against standard costs and planned project costs and directs corrective action. Directs development and implementation of product, system, and project cost improvements
- Establishes and applies performance metrics. Identifies opportunities for process and quality improvement. Evaluates employee performance and opportunities for improvement. Develops and implements solutions to process, quality, and employee improvement opportunities
- Maintains operation of assigned area(s) in compliance with budgetary guidelines. Collaborates on budget development, monitors performance, takes corrective action and directs continuous cost improvements of all areas including labor, expenses, assessments, and capital
- Monitors demand for area services and adjusts staffing levels to meet requirements using available methods including internal resources, contract agencies, and direct hiring
- Ensures assigned staff are qualified and appropriately trained for assigned work. Create and maintain training plans and records. Assures that appropriate training program(s) are in place and yielding required results
- Manages employee performance development to maximize employee performance and satisfaction. Establishes area goals in alignment with cooperate initiatives and cascades goals to direct reports
- Acts as the primary representative of assigned area(s) including multiple shifts. Collaborates with internal and outside groups as needed to achieve area goals and to support goals of other areas within MTS
- Bachelor’s degree in business, engineering, industrial technology, or applicable discipline and 4 years or more experience in project execution, manufacturing, and operations management OR
- Associate's degree in business, engineering, industrial technology, or applicable discipline and 8 years or more in experience project execution, manufacturing, and operations management OR
- High School Degree/GED and 12 or more years experience in project execution, manufacturing, and operations management
- Minimum of 2 years prior manufacturing supervisory/management experience - to include leading large cross-functional teams and performance management
- Able to work 2nd shift hours, Mon-Friday, following training period on day shift
- While performing the duties of this job, the employee is regularly required to sit; use hands to finger, handle, or feel; reach with hands and arms; and talk or hear. The employee is occasionally required to stand; walk; and stoop, kneel, crouch, or crawl. The employee must occasionally lift and/or move up to 25 pounds. Specific vision abilities required by this job include close vision, distance vision, peripheral vision, depth perception, and ability to adjust focus
17
Manager of Manufacturing Operations Manager Resume Examples & Samples
- Manage the production execution for this Operating Units programs
- Manufacturing cost and schedule performance
- Manufacturing lead for all proposals in the Operating Unit
- Create and lead teams to resolve the issues adversely impacting the execution of the programs
- Understand and report on program production status at the required level of detail to program personnel, director, VP, and customers
- Ensure manufacturing has the needed resources (resources manufacturing needs as well as allocation of resources from manufacturing) to execute the programs
- Serve as Functional Manager for 3 to 7 direct reports
- Direct the work of your reporting Operations Program Managers
- Perform manpower planning and determine hiring needed to support your area
- Mentor, develop and assess direct reports
- Candidate must have demonstrated ability in working with cross organizational teams and customers
- 2+ years of experience in a people leadership role
- 5 + years of experience working in production, manufacturing, test, project engineering, IPT, Manufacturing Operations Manager, or similar roles
- Ability to set and clearly articulate goals/priorities and successfully communicate them to key staff
- Strong leadership skills and a track record of building high-performance teams, with a particular focus on employee development, engagement, inclusion and retention
- Ability to obtain and maintain a Secret Clearance, Interim Secret is required to start
- Bachelor's Degree in a Technical Field
- Experience in the manufacturing and testing of hardware
- 5+ years of recent programs experience
- Recent and related business area leadership experience
18
Manufacturing Operations Manager Resume Examples & Samples
- BS degree or higher in Engineering, Manufacturing, Business or related field
- 10+ years of experience working in a manufacturing environment
- 5+ years of Supervisory experience including coaching, providing feedback and conducting performance evaluations
- Demonstrated leadership in driving change throughout the organization or department
- Comprehensive knowledge of manufacturing and production concepts and practices
- Capable of planning and organizing work and processes
- Experience directing multiple projects and meeting deadlines
- Analytical and reasoning ability for problem solving, strategic planning and creativity/innovation, and excellent judgment for making complex decisions
- MS Office (Outlook, Word & Excel)
- Ability to travel up to 5%
- BS degree or higher in Ceramic Engineering
- 10+ years of experience with management responsibilities in a ceramic manufacturing or similar environment
19
Manufacturing Operations Manager Resume Examples & Samples
- Bachelors Level of Degree in the related field of study
- 10 years of demonstrated experience in a management/leadership positon within a manufacturing environment or 5 years of demonstrated experience in a management/leadership position within a manufacturing environment with a Bachelors Level Degree
- Preferred education, experience or certifications: Six Sigma Green Belt or Black Belt; Lean Certification or APICS preferred
20
Manufacturing Operations Manager Resume Examples & Samples
- Ensure employee compliance to all health, safety and environmental program that includes a zero accident culture, and conforms with all company standards and local/national regulations
- Oversee the implementation of manufacturing schedules, personnel requirements, quality assurance, production standards and safety programs
- Supervise staff, including hiring, employee communications, training, discipline, evaluation, and termination responsibilities
- Direct and coordinate the production activities so that the manufacturing of products meets quality standards and cost objectives
- Set priorities and oversee the collaboration between operations, production planning, quality, purchasing and HR to positively affect operational efficiency,
- Develop plans for efficient use of materials, machines, and employees
- Drive accountability throughout the operation
- Lead efforts to establish a fully lean and profit-oriented culture
- Establish key performance indicators and drive shop floor metrics to lead improvements in quality, productivity, on-time delivery and cost reduction
- Create and maintain a positive team culture enabling the operation site to act as a high performing team
- Communicate the annual goals and strategies to the team to motivate, provide direction and align efforts
- Create a culture focused on safety, quality, lean manufacturing and accountability
- Develop team members’ skills to expand their contribution, and prepare them for advancement
- Measure and monitor performance and address performance issues appropriately
- Reward and recognize people for achievements
- Recommend budget to management
- BS: Engineering, Manufacturing, Business or related discipline
- Experience in a machine job shop type environment with high mix/low volume parts
- Minimum 10 years’ experience in operations management in a manufacturing environment
- Background with CNC machining, assembly components, and other specific operations knowledge, such as quality assurance, plant maintenance, and shipping knowledge
- Strong background implementing lean manufacturing concepts including, one-piece flow, 5-S, statistical engineering and kaizen with experience leading initiatives and implementing principles into manufacturing processes
- Capable of planning and organizing work and processes; ability to direct multiple projects and meet deadlines
- Financial acumen for planning and managing operations
- Interpersonal and supervisory skills, such as, coaching, providing feedback, and evaluating performance of subordinates, and the ability to coach and motivate employees to achieve management expectation and assigned performance criteria
- Excellent verbal and written communication/language skills required to include the ability to provide written and verbal instructions, compile and present business reports/ correspondence, present information clearly and effectively provide direction and present business information and updates
- Analytical and reasoning ability for problem solving, strategic planning and creativity/innovation, and excellent judgment for complex decisions
- Interpersonal skills to work in a team-oriented, collaborative environment
21
Manufacturing Operations Manager Resume Examples & Samples
- Plans, directs, and leads production with an intense focus on safety and quality while ensuring compliance with federal and state regulations and internal company policies
- Directs, manages and develops plant associates and supervisors to ensure efficient and safe operations of the plant. Ensures compliance with company policies and procedures
- Establishes, communicates, implements, and enforces safety programs and procedures; conducts routine safety inspections and meetings; ensures proper use and maintenance of equipment; identifies and implements safety improvements
- Establishes and monitors department operating budget; analyzes manufacturing costs and material usage reports; develops labor models; identifies and implements improvements to positively affect profitability. Recommends purchase of all capital equipment and plant expansion. Prepares and/or maintains various reports, records and/or logs (e.g., budget, production, environmental, safety, etc.)
- Fosters and maintains a high level of customer service through on-time deliveries, responsiveness to customer needs and ensuring that the quality of the shipped product meets all customer quality requirements
- Communicates with other plant leaders to share ideas and resources. Collaborates with operations leadership, sales people, and corporate office personnel to ensure safe and efficient operation of plant
22
Senior Manufacturing Operations Manager Resume Examples & Samples
- BA/BS in Mechanical Engineering, Package Engineering, Chemical Engineering, Quality Engineering or related field
- 7+ years of experience in CPG manufacturing, operations, and product & supplier quality management systems
- Experience in daily-use, high-repeat purchase product categories such as Grocery, Household, Personal Care, Beauty, Health & Wellness, and Baby Care
- Experience with cGMP, HACCP, manufacturing methods, process and continuous improvement programs and procedures
- Program management experience in new product introduction and successfully introduced new products to volume production
- Direct responsibility for defining production process/supply chain and equipment requirements for new product manufacturing
- Experience communicating and presenting to senior management
- Master’s degree
- Proven track record for cultivating strong relationships with key internal and external partners that have resulted in high customer satisfaction
- Strong analytical skills including the ability to distill, synthesize, and draw conclusions on large amounts of data
- Outstanding writing, presentation and communication skills
- The ability to manage multiple simultaneous projects requiring frequent communication, organization / time management and problem solving skills
- Demonstrated ability to own projects, think big, act quickly, and influence across all levels of an organization
- Curiosity to dig several layers deep into metrics, have an innate desire to understand key drivers and whether they are the correct or best metrics to measure / manage a business or process
- Diversified experience with entire product lifecycle and supply chain (R&D, scale-up, operations management, consumer feedback)
- Certification in Six Sigma Black Belt and Lean manufacturing
23
Manufacturing Operations Manager Resume Examples & Samples
- Manage Finished Goods & Semi Finished inventory target setting, reporting, and action planning to deliver NWC targets, including specific goals for SLOB inventory management
- Maintain Production data; validate production lead times, batch order quantities, and safety stocks, ensuring data integrity within appropriate planning tools
- Monitor schedule compliance and plan adherence measure. Lead reviews with appropriate partners and initiate corrective action discussions
- Responsible for initiating and drafting changes to existing processes, ensuring that the revisions are reviewed, approved, tested, and communicated as required
- Identify opportunities to achieve greater cost effectiveness across the supply base
- Identify high risk areas within the supply chain, propose solutions and lead implementation of aligned mitigation plans
- Develop the RCCP for critical materials within the supply base, to identify constraints and mitigation strategies
- Implement appropriate KPI’s and monitor and publish on a monthly basis. Ensure appropriate plans are put in place to course correct, where necessary
- Coordinate production sourcing moves to other intercompany facilities or TPM’s
24
Manufacturing Operations Manager Resume Examples & Samples
- 3 years of leadership experience with Perishable or Distribution/Manufacturing operations
- Openness to work across multiple departments/areas within Bakeshop
- Proficient in Microsoft Office
- Possess strong listening skills and hear many points of view without bias, asking clarifying questions to check for understanding
- Use available resources to pursue goals and challenges with the intent of achieving results, striving for continued excellence and taking appropriate risks (Managing the 5 Measures)
- Effectively deal with ambiguity, handling risk and uncertainty with comfort, maintaining effectiveness in the face of change and acting on decisions without having the total picture
- Coming up with new, unique ideas using creative thinking while making connections among previously unrelated notions
- Cross-functional collaboration: initiate dialogue around different points-of-view to find a common ground; lead interdepartmental teams, facilitating organizational consensus and creating synergies to arrive at the best business outcome
- Use multiple resources to analyze data for abnormal findings, further investigating where warranted and identifying cause-effect relationships impacting the data
- Practice process improvement, implements positive change and continuously looks for ways to improve work processes; separate and combine tasks into an effective workflow by maximizing resources and providing assistance when needed and supervise output ensuring high standards and quality are achieved
- Advise others within the organization, as well as external business partners, using relevant knowledge and skills to ensure that sound business decisions are made
- Use critical thinking to solve complex and difficult problems with effective solutions skillfully questioning multiple sources for answers, seeing the underlying and hidden problems and patterns beyond obvious symptoms to address root causes
- Experience with project coordination, communicating goals and responsibilities to the team being sure to monitor performance against a project plan and effectively applying project controls. Include project stakeholders, team members, and subject matter experts in order to get things done
- Experience with risk evaluation: proactively identifying areas of potential risk exposure, thoroughly analyzing the situation to ensure the financial investment of a solution makes sense and implementing cost-effective controls to mitigate risk
- Bakeshop Management experience
- Food Manufacturing experience
- American Institute of Baking (AIB) Certification or Culinary Arts Degree
- Bachelor’s degree and/or equivalent experience
25
Manufacturing Operations Manager Resume Examples & Samples
- Four year accredited degree and 12 years of progressive manufacturing leadership roles
- Experience working with international and matrix organizations preferred
- Demonstrated experience/ knowledge of Manufacturing Lean principles, use of Kaizen events, JIT, Kanban
- Previous knowledge /experience with electrical power distribution related products such as switchgear, breakers, protection relays
- Excellent verbal and written communication experience
- Ability to prioritize, make decisions in difficult or ambiguous situations
- Excellent interpersonal, coaching, and development skills
- Change management/facilitation skills
- Candidates with work authorization that would permit them to work for ABB in the US
26
Manufacturing Operations Manager Resume Examples & Samples
- Plan, schedule, assign work, and ensure activities are in compliance with Company policies and procedures, and with codes and regulations. Monitor product quality and customer relations and initiate responsive measures, as applicable. Anticipate and introduce timely, effective actions to resolve problems
- Manage activities and initiate measures to ensure efficient operations and achieve long-term cost savings. Maintain awareness of new developments and technologies and direct subsequent investigations regarding their utilization
- Participate in meetings and conferences and act as spokesperson for the organization on highly significant matters. Negotiate such matters as costs, design features and schedules with suppliers and customers. Advise senior managers regarding such matters as most effective means of complying with new contract stipulations and improving customer relations
- Provide guidance and arrange for training of staff. Provide administrative support to senior managers and advise less experienced supervisors regarding the more complex aspects of their assignments. Manage and document employee performance and initiate responsive actions
- Previous held engineering roles or experience working with production engineering preferred
- Previous knowledge /experience with electrical power distribution related products such as instrument transformers, switchgear, breakers, relays..etc
27
Manufacturing Operations Manager Resume Examples & Samples
- Bachelor's Degree, Post Secondary Degree is Preferred
- 10+ years of experience in Operations Management with a focus on Manufacturing and Distribution
- Minimum 5 years of experience working directly with internal and external customers (strong customer service focus)
- 7-10 years’ experience with Manufacturing operations and Inventory Management required
- 5 years’ experience in quality systems management such as ISO9001
- 2-4 years’ experience with LEAN Manufacturing principles, Green Belt certification preferred
- Strong working knowledge using an ERP system (JDE, SAP, MAPICS) is a requirement
- Strong working knowledge of Microsoft products (Word and Excel) preferred
- Working knowledge of bills of material structures and AutoCAD / CAD software applications preferred
28
Manufacturing Operations Manager Resume Examples & Samples
- Perform quality work within deadlines with or without direct supervision
- Interact professionally with other employees, customers, and suppliers
- Work independently while understanding the necessity for communicating and coordinating work efforts with other employees and organizations
- Comply with all applicable safety- and health-related rules, regulations, and procedures
- Work safely themselves and help their teammates work safely
- Assist supervisors and managers in identifying and mitigating potentially hazardous conditions; and
- Help the organization maintain a safe and healthy workplace
- Responsible for supervising rotating shift Shift Supervisors. This responsibility includes coordinating effective implementation of NASA/S3 procedures for site-wide utilities and related operations activities for scheduled and emergency operations
- Responsible for administering training, safety programs, and personnel
- Assists with the correct enforcement of the IUOE Union Agreements and its correct interpretation for administering shift operations
- Also required on occasion to substitute for and absent Shift Supervisor
- Eight to ten year’s experience as utilities operations operator
- Experience credit given for college education
- Strong interpersonal skills to establish/maintain customer and vendor relationships
- Strong comprehension skills for understanding needs and developing and applying solutions
- Ability to manage staff and work as part of a business development team
- Ability to troubleshoot technical problems either on-site or remotely
- Ability to work productively across diverse customer sites, with different levels of technical focus
- Ability to manage large or multiple projects
29
Manufacturing Operations Manager Resume Examples & Samples
- Management of current manufacturing backlog and equipment usage and development of future manufacturing opportunities
- Participating on the S3 MAF Site Leadership Team
- Interfacing with NASA personnel to insure NASA mission objectives are met
- Serving as the MAF point of contact and liaison for manufacturing operations in support of the Stennis Space Center and other NASA entities
- Establishing manufacturing priorities via coordination with NASA and the tenant community
- Being a champion for S3 manufacturing capabilities with NASA and its current and potential tenants
- Providing input into the NASA capital plan as it relates to Machine Shop and Weld Shop capital needs
- Management oversight of technical staff, supervisory staff, and collective bargaining agreement craft
- Coordination with Quality personnel to insure parts meet design requirements and written specifications
- Coordination with Safety, Environmental and Health personnel to insure use of best practices and compliance with regulations
- Coordination of operation and maintenance of equipment assigned to the National Center for Advanced Manufacturing (NCAM)
- Oversight of Machine Shop operations, to include responsibility for
30
Manufacturing Operations Manager Resume Examples & Samples
- Responsible for facilitating efficient operation, including direct management and control over manufacturing, production, equipment maintenance and engineering support
- Will coordinate efforts with other department heads and corporate entities in areas of Product Development, Supply Chain, Finance, Quality, Service and Repair, Marketing, Customer Service, and Human Resources
- Supervisory duties and responsibilities include: a) responsibility for performance management and development of direct reports including written performance appraisals; b) administration of company policies and procedures at the Ohio location; c) compliance with QSR's and ISO, safety policies, and good housekeeping; d) responsibility for initial training of new employees and on-going training of subordinates to ensure quality of work, QSR's and ISO, and other regulatory compliance; e) Promotes continuous improvement and emphasizes an environment to foster teamwork; and f) ensuring effective staffing of organization, including hires and dismissal of employees when needed g) Responsible for safety of all employees within their organization
- Performs other duties and responsibilities, as required
- Position requires occasional domestic/international travel
- Ten (10) years management experience in a high mix/complex manufacturing work environment, preferably in the medical products field
- Ability to work in a Continuous Improvement environment
- Lean manufacturing and Six Sigma
- Enterprise Resource Planning (ERP), including: Bills of Materials (BOM’s), Routers and Travelers, Pick Lists, Trace Sheets, Material Returns, Production Quality Sheets
- Barcode labor tracking/Material tracking
- Statistical Process Control/Defect tracking
- Food and Drug Administration (FDA), International Standards Organization (ISO), EPA, OSHA and other requirements and regulations
31
Manufacturing Operations Manager Resume Examples & Samples
- Provide leadership the local team of process engineers
- Apply lean manufacturing principles to design, specify, and validate world-class manufacturing processes to achieve cost, quality, and capacity goals
- Lead the planning and implementation of facility and line layouts
- Lead strategic improvement projects to support continuous improvement of Lutron's manufacturing processes
- Establish metrics to track improvement over time
32
Manufacturing Operations Manager Resume Examples & Samples
- Ensure a safe work environment for all employees as well as the utilization of safe work procedures
- Ensure Production, Quality, Maintenance, Building Maintenance department personnel have a clear understanding of their expectations and measures used to guage performance
- Ensure compliance with all Consolidate Management System, ISO and quality regulating agencies, as well as all Company Quality standards and procedures
- Facilitate inter-department actions in conjunction with the Consolidated Management Sytem which drive continuous improvements in productivity, quality, safety and customer service
- Assist in the development of capital expenditures and departmental budgets
- Manage and ensure the personal development of all subordinates
- Ensure satisfaction of all internal/external customers, as well as other CCBCC plants and corporate interactions. Develop strong partnerships with all suppliers
33
Manufacturing Operations Manager Associate Resume Examples & Samples
- Experience in metal forming and welding fabricated components
- Knowledge of metal forming and welding tool usage, maintenance and capital tooling procurement
- Experience and proven track record on delivering on projects from design to implementation
- Ability to understand performance, quality, and cost data generated from daily manufacturing operations
- Previous Management experience within a manufacturing setting
- Experience with overseeing Union and non-Union workforces
- Ability to manage a diverse workforce and form strong relationships across all levels of the organization
34
Senior Manufacturing Operations Manager Resume Examples & Samples
- . Plans, directs and coordinates the manufacturing functions including Primary Machining, Milling, assembly, secondary Operations, Casting and Welding production
- Prepares annual manufacturing budget, monitors and manages department budget and resource allocations
- Ensures that metrics are posted and displayed, lean audits are conducted, and visual management systems are maintained
- Establish manufacturing metrics and goals within the context of the SBM Flight Plan and ensures attainment of goals including on-time delivery, Inventory turns and first pass yield
- Lead the engineering industrialization team developing the drafting and programming department providing technical guidance and on hands support
- Lead the processing engineering team developing the standard work strategy, improving manufacturing process capabilities providing technical guidance and on hands support
- Improve productivity/throughput/safety by utilizing Industrial Engineering techniques (SWS, Standard Work, % load, ergonomic evaluations, delay studies, predetermined time, simulation, and line balancing)
- Lead the development of key industrial engineering systems such as: routing or workflow definitions, cost analysis, standard work definition, performance tracking, line balancing and process documentation
- Support shop operations by providing solutions and alternatives for manufacturing with hands on activities and training of manufacturing personnel. Optimize existing processes and implement new techniques and technologies
- Analyze work force utilization, facility layout, material flow and operational data such as production costs, process flow charts, and production schedules, to determine efficient utilization of workers and equipment
- Define and generate required documentation in support of manufacturing products and processes, including engineering protocols, reports, manufacturing instructions, manufacturing drawings, procedures, work instructions and training documents
- Process engineering includes tooling design, job tracking, fabrication and new process implementation
- Maintain process documentation, including process flow diagrams, operating instructions, DCN forms, etc
- Champions and supports Lean Enterprise and Continuous Improvements Philosophy within SBM with hands-on involvement and reinforcement of lean practices
- Engages in problem solving in complex situations and process improvements in streamlining work processes and improving results
- Mentors, motivates and develops employees to reach their maximum potential and to ensure organization staffing match with business objectives
- Ensures that company policies, safety standards, and good housekeeping practices are followed within all departments
- Implement, coordinate, contribute and assist with other projects as assigned, including team participation. Encourages and maintains a productive, high output, respectful and positive work environment
- Prior management experience in an machining turning and milling manufacturing environment and/or Aerospace a must
- CNC Machining for different types of products using Lathes with 2 & 3 axis, Multi-Tasking machines with Live Tooling, 2 turrets, 2 spindles, Vertical and Horizontal Machining Center with 3,4,5 axis
- Expertize in NC Programming (Mastercam, CATIA, etc.)
- Proficient with Outlook email, Microsoft Office (Word, Excel) and IQMS system or similar MRP system
- Bilingual in English and Spanish, able to speak, write and read
- Able to travel (valid U.S. visa)
- BA/ BS, in engineering discipline, (MBA is preferred)
- 5 - 7 years operations management experience in an Aerospace manufacturing environment
- Proven experience with CAD-CAM systems, CNC Machine programming, setup and operation. 2D and 3D and above drafting and modeling
- Strong knowledge of manufacturing processes and disciplines
- Strong business acumen and customer interaction experience
- Strong Leadership skills - effective in motivating and directing a team for positive results
- Strong knowledge of MRP (IQMS) and automated scheduling systems
- Knowledge of Lean Manufacturing methods and Philosophies
- Strong organizational, presentation and communication skills
35
EAS Manufacturing Operations Manager Resume Examples & Samples
- Bachelor's degree or higher from an accredited university in Science or Engineering
- Minimum of ten (10) years of experience in Manufacturing Supply Chain
- Master’s degree or higher from an accredited university in Chemistry or Chemical Engineering
- Strong Customer First Mindset
- MBB or BB certification
- Direct customer engagement experience
- Strong familiarity with corporate supply chain objectives and strategies
- Expert knowledge and experience with demand planning, distribution and import/export
- Comprehensive knowledge of 3M systems related to supply chain product/order management, inventory management and global service fulfillment
- Proven history of collaboratively working with Manufacturing Plants & Business teams
- Demonstrated leadership behaviors in leading teams and process improvement
- Strong written and presentation skills
36
Manufacturing Operations Manager Resume Examples & Samples
- Serving as a member of Plant Management Leadership Team by holding the department accountable for adherence to plant direction and policy
- Establishing and ensuring achievement of all unit Key Performance Indicators while ensuring adherence to and continuous improvement for all area MCRS elements
- Participating in the business planning and budgeting process by developing short and long-term cost containment/reduction strategies
- Execution of projects within assigned area by monitoring project plans and status to ensure completion
- Ensuring raw materials are efficiently converted into finished goods for assigned area/shift
- Responsible for application of Lean tools
- Accountable for compliance with all Employee Safety, Food Safety and Sanitation policies and regulations
- HS Diploma/GED with significant managerial experience in a manufacturing setting
- Experience with leading and applying lean principles in a manufacturing environment
- Ability to operate in a union environment, promoting positive labor relations
- Demonstrated ability to lead and motivate others
- Strong problem solving, negotiating, and decision making skills with the proven ability to manage complex situations
- Proficiency with computers, including the Microsoft Office Suite (Word, PowerPoint, and Excel)
- Business Acumen – must have worked in 2-3 different Functional areas of a manufacturing organization (i.e., Logistics, Operations, Human Resources, Finance)
- Collaborative work style, able to partner with leaders of other functional areas and business partners to drive overall site performance in a manner that aligns with Kellogg Values
37
Manufacturing Operations Manager Resume Examples & Samples
- Implement and develop an Associate Relations Strategy that ensures involvement and ownership by all Associates. This achieves a motivated and capable team who are engaged in an environment of continuous improvement. The outcomes are Associate safety, morale/well-being, commitment, improved performance and development
- Identify and implement operational strategies that ensure customer satisfaction in product quality, service and responsiveness
- Provide leadership and development of a methodology and work environment where continuous improvement is a natural approach to achieve site based strategic operational opportunities
- Ensure that appropriate Performance Management exists to ensure role clarity for both individuals and teams. This includes clear plans for both skills and Associate development leading to improved capability and improved job satisfaction and/or career opportunities
- Manage the fixed and variable cost of the MCC for the site and ensure operating plan targets are achieved and also opportunities to further reduce the MCC are identified and implemented
- Leadership and development of the site shift management team to ensure suitable standards for achieving consistent long term safety, quality and productivity expectations which links back to creating an environment where Associate morale/wellbeing are assured
- Responsible for delivery of the Site OGSM ‘Do it Best’ targets including the Sustainable in a Generation Site Operations targets
- Responsible for development and deployment of lean strategy within Manufacturing on Site
38
Manufacturing Operations Manager Resume Examples & Samples
- Adhere to Federal and State regulatory requirements governing 503B Outsourcing Facilities and ensure compliance with CAPS Standard Operating Procedures (SOPs)
- Responsible for the financial performance of the facility. Establish annual financial plan and forecast financial and operational performance to meet corporate revenue goals and product cost goals. Manage operating and capital expenditures
- Prepare and present financial, performance and operating reports and recommendations to executive management
- Establish, meet and report to management Key Performance Indicators (KPIs) on a monthly basis
- Meet all manufacturing goals to support the customer demands and responsible for facility production goals
- Develop and train staff of business unit leaders to establish shift production schedules and goals. Plan labor capacity and manage physical assets
- Administer cooperation with the various departments to establish teamwork from the purchasing, production, and distribution departments
- Effectively work with cross functional work teams such as Sales, Marketing, Quality, EH&S, Information Technology and Human Resources
- Conduct employee performance reviews for direct reports. Recruit and hire staff as required
- Schedule and conduct plant meetings on a regular basis
- Collaboratively work with Quality Department to maintain an active role in review and revision of standard operating procedures and development and implementation of new procedures
- Plans, inspects and monitors facility operations to ensure safe and efficient operation
- Establish and maintain relationships with key customers, suppliers, staff, vendors, contractors and company executive personnel
- Develop long-term strategic manufacturing plans
- Establish and maintain an environment of continuous quality control through the utilization of progressive quality management techniques such as Six Sigma and Lean
- Provide technical expertise and knowledge in Risk Management activities in all stages of product life cycle
- Engineering, financial, regulatory, documentation, financial analysis, production planning, project management systems, organizational structure and motivation skills
- Computer, internet, calculator, financial planning, report writing, and analytical planning skills. Planning, supervision, motivation, communication skills, organization sequence and priority management, time management, multiple and diverse activity management, diverse culture interaction, objective setting and deadline management, follow up skill and abilities
- In depth knowledge of CAPS and its products. Demonstrate basic pharmacy knowledge to include injectable drug names and CAPS catalogue
- Excellent verbal, written and presentation communication skills
- Problem solving , analysis skills and project management skills
- Ability to handle multiple tasks and meet deadlines
- Ability to work well with others and perform as a team
- Communicate effectively with staff, management and operations personnel, both orally and in writing
- Bachelor’s degree in Operations Management, Business Administration, Engineering or a related field
- Ten (10) years experience in operations management with cGMP Pharma experience, related experience in executive management, manufacturing management, project management, regulatory understanding, and engineering
- Licensed as a Pharmacist or expertise in Pharmacy industry
- Master in Business Administration (MBA)
- Engineering degree with Coursework, training or certification in world class manufacturing, engineering, total quality management systems, Lean manufacturing practices, and Six Sigma quality management
- Business travel, Driver’s License