Senior Manager Manufacturing Resume Samples
4.8
(149 votes) for
Senior Manager Manufacturing Resume Samples
The Guide To Resume Tailoring
Guide the recruiter to the conclusion that you are the best candidate for the senior manager manufacturing job. It’s actually very simple. Tailor your resume by picking relevant responsibilities from the examples below and then add your accomplishments. This way, you can position yourself in the best way to get hired.
Craft your perfect resume by picking job responsibilities written by professional recruiters
Pick from the thousands of curated job responsibilities used by the leading companies
Tailor your resume & cover letter with wording that best fits for each job you apply
Resume Builder
Create a Resume in Minutes with Professional Resume Templates
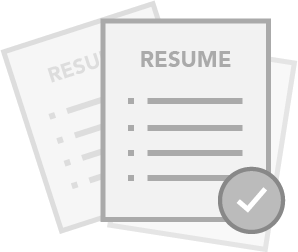
CHOOSE THE BEST TEMPLATE
- Choose from 15 Leading Templates. No need to think about design details.
USE PRE-WRITTEN BULLET POINTS
- Select from thousands of pre-written bullet points.
SAVE YOUR DOCUMENTS IN PDF FILES
- Instantly download in PDF format or share a custom link.
RT
R Toy
Rosanna
Toy
871 Grant Meadow
San Francisco
CA
+1 (555) 939 8615
871 Grant Meadow
San Francisco
CA
Phone
p
+1 (555) 939 8615
Experience
Experience
Houston, TX
Senior Manager Manufacturing
Houston, TX
Homenick and Sons
Houston, TX
Senior Manager Manufacturing
- Manages Production Product P&L, budgets and performance against AOP
- Optimizes department resources; ensures productive value added safe working environment
- Providing leadership and direction to Manufacturing Supervisors and support teams while embodying the principles of the Genzyme Global Leadership Model
- Planning, developing and maintaining the department budget
- Providing leadership and direction to Manufacturing Supervisors and support teams while embodying
- Ensuring timely issue escalation to manufacturing senior management and cross-functional support teams
- Partners with Operations Managers to resource and assign CAPAs and Tasks
New York, NY
Senior Manager, Manufacturing
New York, NY
Maggio-Boyer
New York, NY
Senior Manager, Manufacturing
- Manage and develop a staff of manufacturing associates, maintenance technicians and supervisors
- Manage staff to project timelines effectively while ensuring clear and concise communication to plant management
- Serve as subject matter expert during regulatory inspections, and collaborate with plant management to address any follow-up responses or corrective actions
- Effectively recruit and develop staff in accordance with company policies in support of effective succession planning
- Develop and manage portions of the departmental budget and spending in support of department objectives for cost control while maintaining effectiveness
- Day to day management of large teams and their execution of manufacturing activities in a safe manner
- Identify and drive continuous improvement activities
present
San Francisco, CA
Senior Manager, Manufacturing Operations
San Francisco, CA
Rau and Sons
present
San Francisco, CA
Senior Manager, Manufacturing Operations
present
- Apply project management concept to manage R&D and production projects
- Develop & implement policies and systems that standardize and improve labor efficiency to yield consistent on time order fulfillment, quality of product, and mitigate in warranty and out of box returns
- Develop & implement policies and systems to achieve near term and long term non-material productivity improvements
- Create employee development plans for incumbents in critical organizational roles and/or high potential team members that will increase depth and breadth of knowledge.Examples include: Six Sigma, IPC, Professional Certifications, etc
- 30% - Workforce Development & Planning
- Utilize KPIs to ensure current training, policies, and procedures directly translate to increased organizational effectiveness and continuous manufacturing improvement
- 30% - Global Organizational Performance Management
Education
Education
Bachelor’s Degree in Business
Bachelor’s Degree in Business
Colorado State University
Bachelor’s Degree in Business
Skills
Skills
- Coordination of full scale inventories and reconciliation projects; ability to understand warehouse versus manufacturing cost of goods issued errors
- Working knowledge of ERP/MRP principles and techniques
- Proven leadership experience and ability to drive results through a cross-functional team
- Ability to interface at all levels of management and leadership
- Active Secret clearance with ability to obtain Top Secret
- Strong communication, writing, and presentation skills
- Ability to present to senior management, departments, customers, and program teams
- Strong SAP skills/understanding
- Demonstrate an exceptional level of team building and project management skills under demanding pressure
- Developing solutions to a variety of complex problems
15 Senior Manager Manufacturing resume templates
Read our complete resume writing guides
1
Senior Manager Manufacturing Excel App Resume Examples & Samples
- Responsible for driving improvements in Quality, Cost and Delivery across the business and act as a facilitator to engender a culture of change and continuous improvement
- Design, develop & build a standardised approach to product construction methodology that ensures quality, cost & practical execution in line with the adidas Group requirements & expectations
- Ensure construction standards are actively applied in the supply chain according to the specified method analysis
- Work with the adidas group Manager Industrial Engineering to build SMV data in the construction methods in order to develop cost sensitivity in our product creation process
- Influence the product creation process by delivering standard construction data to the development teams that allow them to select product features that are within cost & quality expectation
- Provide leadership & support to various teams of garment technicians/technical service teams
- Liaise and interact with the Supply Chain to determine practical application of construction methods
- Interact with internal and external counterparts to determine best methods
- Work closely with the Sourcing Technical Service team to develop and improve the adidas Group workmanship standards manual
- Liaise with Creation Centres to ensure construction methods data are current for the development season
- Interact with outside vendors to evaluate new technology, machinery & processes
- Use proven industry standards and quality driven results to develop construction method standards & continually challenge & improve them
- Analyze complex processes and recommend positive change
- Assist when needed the Sourcing leadership to provide advice & drive change within the business
- Able to utilize industrial engineering techniques effectively to produce tangible results
- Fluent in English (Reading, Writing and Speaking), BULATS level 3 or equivalent
- Degree in Industrial Engineering or equivalent qualification
- A minimum of 6-7 years of experience within an apparel manufacturing/industrial engineering environment
- Experience managing a department of engineers is highly desirable
2
Senior Manager Manufacturing Excellence Resume Examples & Samples
- Drive improvements in Quality, Cost and Delivery across the business via the application of Industrial Engineering best practices and continuous improvement activities within the supplier base
- Deliver a standard platform for SMV (Standard Minutes Value) and based capacity planning and costing by developing & promoting GSD (General Sewing Data) gthe supply chain
- Ensure improvements are sustained through the introduction of work instructions, quality standards, workplace organisation, training records and performance measurement
- Pro-actively identify and evaluate improvement opportunities within the business, prioritise improvement and deliver maximum benefit to the business
- Support the product creation process by delivering tools and information to support Right First Time behaviour
- Serve as an outside consultant to the Supply Chain, making recommendations to the T1/T2 Industrial Engineering management teams to improve internal and external processes
- Provide leadership & support to T1 Industrial Engineers & LO PCEs (Liasion Office Product Costing Engineer)
- Conduct feasibility studies of various projects to determine the value of an investment and provide an economical justification for capital appropriations
- Responsible for managing capital projects from conception to final acceptance
- Strong influencing skills
- Thorough understanding of work measurement and predetermined time system, such as GSD
- Fluent in English (Reading, Writing and Speaking),
3
Senior Manager Manufacturing Resume Examples & Samples
- At least 1-3 years leading direct reports
- Strong understanding of Quality systems
- Extensive experience and strong technical and management competence in vial manufacturing in cGMP environment
- Experience in managing multiple priorities in production environment and provide support to meet the manufacturing schedule while maintaining quality and compliance
- Strong working competence with Deviation Management Systems (eg.. TrackWise)
- Leader in troubleshooting, investigation, root cause and risk analysis in a cGMP environment
- Experienced in making tactical decisions on safety, process, scheduling and personnel- related issues
- Ability to effectively and appropriately escalate operational issues
- Experienced in establishment of safe practices in a cGMP environment
4
Senior Manager, Manufacturing Resume Examples & Samples
- 3-5 years’ experience in a cGMP manufacturing environment
- Bachelor’s Degree in Life Sciences (e.g. Biology, Chemistry, Biochemistry) or Engineering (e.g. Chemical Engineering)
- Extensive experience in vial manufacturing
- Strong working competence with ERP (SAP)
- Experienced working with cross-functional teams, including Quality, Manufacturing Technical Services, Facilities, Engineering and Validation
- Experienced authoring and reviewing standard operating procedures, on-the-job-trainings, and other controlled documents
- Experienced in managing direct reports who have leadership responsibilities
5
Senior Manager, Manufacturing Operations Resume Examples & Samples
- Develop annual operating budget, including establishing and meeting financial goals and objectives by forecasting requirements, and variances
- Establish and submit capital budget planning
- Lead capacity planning activities for 3 Plants to deliver corporate S&OP planning requests
- Lead all business units in Continuous Improvement (CI) activities
- Provide day to day direction & exercise direct supervision over general and line supervisors
- Exercise matrix supervision over support functions in residence of the plant
- Promote employee safety in all production processes and activities
- 7+ years of experience in a leadership role in a manufacturing setting
- 5+ years of experience managing at least 3 of the 5 following value streams: machining, laser cutting, brake forming, manual welding, and robotic welding
- 3+ years of experience leading continuous improvement teams and projects
- 2+ years of experience managing salary and hourly employees in a union environment
- 2+ experience working within a low volume/high complexity OEM or tier-1 supplier
- Completed MBA
6
Senior Manager Manufacturing Resume Examples & Samples
- Achieving safety, quality, delivery, and cost goals; identifying and implementing improvement opportunities using six sigma and lean methodologies
- Depot related issues for GFP hardware received for satellite ground stations, link encryptors, and network encryptors
- Understanding and operating within the contractual requirements set forth in a union environment
- Manages Production Product P&L, budgets and performance against AOP
- Aggressively develop, implement, and sustain a lean manufacturing plan to drive process improvements, reduced lead times, lower costs, reduce WIP, reduced variation, improved quality, and expanded capacity
- Provides the status and visibility into Operations by advising on business strategy and potential program risks
- 12 years of experience in manufacturing, operations, or engineering in a leadership role
- Active Secret clearance with ability to obtain Top Secret
- Proven track record of managing a multi-disciplined team providing successful solutions across Manufacturing, Supply Chain and Operations
- Experience utilizing lean manufacturing concepts and/or six sigma project implementation
- Experience with unit hour performance, cost account management or other budgetary responsibility
- Developing solutions to a variety of complex problems
- Ability to present to senior management, departments, customers, and program teams
- Supply Chain Management experience including but not limited to material program management, acquisition, warehousing, planning, and production processes related to material flow
- Strong SAP skills/understanding
- Coordination of full scale inventories and reconciliation projects; ability to understand warehouse versus manufacturing cost of goods issued errors
- Aptitude to assess future state versus current state scenarios related to material storage requirements and proven record related to process improvement
- Excellent interpersonal, written, verbal & communication skills, with the ability to interact with not only team members but also all levels of the organization
- EVMS experience
- Demonstrate an exceptional level of team building and project management skills under demanding pressure
- Experience in the aerospace/defense industry
- SAP, VBS, PRISM, PDM systems
- Certified PM or MPM level 4 or higher
- Experience in EX/IM procedures
- Working knowledge of ERP/MRP principles and techniques
- Understanding of NSA certification requirements related to crypto products
- BS/BA in Manufacturing Engineering, Supply Chain, Business or related field
7
Senior Manager, Manufacturing S Resume Examples & Samples
- Responsible for resource management to achieve on time schedule execution, and the corresponding budget execution for the Manufacturing organization
- Manage and improve manufacturing processes in Electrical Assembly (EA), Mechanical Assembly (MA), Fabrication, Paint, Special Processes and Assemblies, Upholstery, and Cabinet building/finishing
- Identify and implement best in class technology infrastructure suitable to the scope and size of the business along with disciplines that support the Manufacturing operation
- Works with the appropriate teams to drive standardization and continuous improvement
- Supports the Operations, Engineering, and Business Areas in a team-based manufacturing environment. Performs activities in a variety of cross-functional areas including production planning and control, quality management, systems, manufacturing, material management, and process reengineering
- Will facilitate self-directed work teams, provide training in "core skill" areas to teams and peers, and interact with internal and external customers with respect to product planning, problem resolution, and process improvement
- Establish and monitor performance metrics and drive improved performance
- Sets the highest ethical standards for self and others
- Must have a minimum of 5 years of experience as Manufacturing Manager, Operations Manager or Engineering Manager
- Must have or be able to obtain a Security Clearance
- Leadership, strong interpersonal skills, outstanding oral and written communications, proactive, innovative, disciplined, team-builder, motivator, closer
- Strategic perspective with tactical implementation skills
- A responsive, fast-paced decision-maker who is highly driven to achieve business expectations. Results-oriented leader driven by personal and team accountability
- Exhibits a fact-based management style aggressively addressing business tactical issues and strategic needs
- Strong team-building and cross-functional collaboration skills
- Clear, concise written and verbal communications skills. Maintains transparent, performance-based communications with all levels of leadership
8
Senior Manager, Manufacturing Resume Examples & Samples
- Develop, implement and monitor departmental objectives and schedules including setting priorities and performance expectations while ensuring alignment with expected deliverables, site metrics, and company goals
- Manage and develop a staff of manufacturing associates, maintenance technicians and supervisors
- Manage staff to project timelines effectively while ensuring clear and concise communication to plant management
- Effectively manage operations in accordance with GMP guidelines. Coordinate all needed actions with Facility Supervisors and Managers
- Serve as subject matter expert during regulatory inspections, and collaborate with plant management to address any follow-up responses or corrective actions
- Ability to recruit top talent with every hiring opportunity
- Ability to drive personal accountability at every level of the organization
- Ability to align production staff in different manufacturing areas across different shifts
- Ability to function, with guidance, in a rapidly changing environment while balancing multiple priorities simultaneously
- 8 years experience in a cGMP biopharmaceutical manufacturing environment
9
Senior Manager, Manufacturing Resume Examples & Samples
- Day to day management of large teams and their execution of manufacturing activities in a safe manner
- Identify and drive continuous improvement activities
- Provide the knowledge and experience to inform site strategic development
- Support of organizational development and cultural leadership
- Partner with Quality Assurance to operate & improve quality & compliance systems aligned with Lonza standards
- Create a positive and motivated team-centric environment that attracts, retains and develops talent to deliver improved business performance
- Value training, mentoring and leads others to bring out their best as part of a high-performing team that emphasizes ownership, accountability, open communication & people development
- The ability to engage, interact and develop good working relationships with customer and Lonza staff quickly
- Capable of setting direction, clearly assigning objectives, measuring and monitoring progress
- Experienced at marshaling resources and handling competing priorities
- Ensuring that the department is in a continuous state of readiness for production and GMP audits
- Direct manufacturing planning, execution and batch release activity to ensure delivery per production plan
- Financial literacy, in particular OpEx budget setting & management, plus project scope and business case development
- BS in Biotechnology, Biology, Chemistry, or equivalent; Masters degree preferred
- Experience Level: Advanced
- Leadership/management experience in pharmaceutical manufacturing with experience in aseptic processing or biologic bulk drug substance delivery. Preference to have progressive experience in both operations & other functions
- Experience with 6S and Lean Manufacturing, Lean Six Sigma Green belt or black belt preferred
- In depth knowledge of pharmaceutical manufacturing, safe work environment leadership, delivery of RFT, and leadership and development of leadership teams delivering progressive continuous improvement in a multi-layered organization
- Demonstrate ability for effective Planning, Organizing and Controlling competency
- Demonstrate sound decision making, considering broad scope of factors
10
Senior Manager, Manufacturing Sciences Resume Examples & Samples
- Insuring effective and well-controlled manufacturing processes by over-seeing the team that performs the Manufacturing Sciences function for the Site. The Manufacturing Sciences function is responsible for correct formulation of prepared media products, engineering of production methods, and institutionalizing effective process controls in production
- Technical operations project leadership for significant product line extensions or OEM products. Acting as the project leader to assess and align customer requirements and manufacturing process capability to successfully drive new growth projects to completion. Driving rapid Root Cause/Counter Measure (RCCM) determinations to address product performance failures and motivate an organizational passion for protecting customers, while avoiding the financial consequences of ineffective problem solving
- Own the supervisory management accountabilities for the Manufacturing Science Team– including guiding subordinate managers and collaborating with HR to achieve correct employment decisions, appropriate disciplinary actions, and efficient use of talent and other resources. The Manufacturing Sciences team includes Process Engineering, Media and Process Development, Packaging Engineering, and Manufacturing Sciences
- Relentlessly demonstrate Role Model Leadership by establishing and communicating the future state visions for the Team, and motivating the actions that drive the attainment of Customer Focus and Manufacturing Excellence at the Lenexa Site
- Drive effective and timely application of the PMD (Performance Management and Development) System to establish and properly cascade goals and insure talent development
- Participate effectively as a member of the OLT – driving daily pacing and accountabilities, while insuring collaboration and teamwork in the Tiered Meeting Systems and OLT Staff Meetings
- Direct the Manufacturing Sciences function to insure correct product formulations, institutionalization of TPM (Total Productive Maintenance), and consistent adherence to effective process control methods and actions
- Establish and drive a Customer-focused culture that is relentless in the rapid pursuit of RCCM (Root Cause / Counter Measure) and PPI actions. Demonstrate the importance of speed in solving problems in relation to Customer Experience and effective cost controls
- Participate/lead the global manufacturing sciences council with other MBD sites with aim to drive best practices and harmonized processes across the division. Expand network to other technical leaders in Thermo Fisher Scientific to develop resource contacts to aid in specific technical challenges as needed
- A minimum of a Bachelor’s Degree in Microbiology, a closely-related science, or Engineering is required. An MBA with an under-graduate degree in a scientific discipline is preferred
- A record of continuing education in Continuous Improvement Methods, LEAN manufacturing, process control, TPM, and Quality Best Practices is essential to effective performance in this key leadership position
- A minimum of 8 years of experience as a Role Model Leader, including at least 5 years of directly-related supervisory management experience in a fast-paced, customer-focused organization in an FDA-regulated industry
- Must be able to lead and influence in ways that demonstrate a clear passion for optimizing the customer experience and eliminating waste
- Comprehensive knowledge of LEAN and Continuous Improvement methodologies with proven ability to develop and implement Standard Work
- Broad knowledge of Quality Systems and common methods of Quality Management in an FDA-regulated industry
- A thorough understanding of Manufacturing Process Control and TPM methodologies
- Proficiency in the use of PC-based and Internet-based software applications
- This position may require occasional business travel
- Proven ability to lead a diverse organization involving cross-functional teams in a matrix organization – preferably, in a global organization
- Track record of implementing process improvement which has directly impacted the customer experience
- A minimum of a Bachelor Degree from an accredited institution – preferably in microbiology, a related science, or engineering
- A minimum of 5 years of directly-related supervisory management experience in a fast-paced, customer-focused organization in an FDA-regulated industry
- A self-motivated leader, with a high bias for action, who can inspire a teamwork, a passion for continuous improvement, and the attainment of manufacturing excellence
11
Senior Manager Manufacturing Operations Resume Examples & Samples
- Manages staff (operatives, maintenance, mechanics, etc.) ensuring that these groups are adequately trained, motivated, and developed, and that responsibility and accountability are assigned at the proper levels
- Works with existing customers and new potential customers to execute the strategic plan and grow the business
- Responsible for ensuring that all unit indicators support company’s objectives and that favorable results are being achieved or appropriate action is being taken
- Responsible for ensuring that all operations are performed in the most economical manner practical
- Responsible for ensuring that the department is in position to deliver new products or product extensions to the customer in minimal periods after approval
- Responsible for budgeting and ensuring that the division has adequate resources in facilities, equipment, and personnel to produce the customer demand
- Establishes direction for the department by developing goals that support O&T and company goals and strategies
- Ensures that all operations are validated and fully comply with all cGMP’s. Responsible for area compliance in the face of internal, customer, and regulatory inspections
- Establishes/approves the technical requirements for production documentation including equipment and systems specifications, manufacturing formulas, POMS procedures, filling and packaging work orders, SOP’s, Environmental Procedures, PM’s, etc
- Using input from Operations Planning, plans, schedules, and executes production workload to ensure product availability when demanded, while maintaining product inventory at its lowest level
- Responsible for ensuring that all products and drugs are available at point of demand in sufficient quantities to prevent product backorders
- Responsible for ensuring equipment and facilities are adequately maintained through effective P.M. and facility upgrade programs
12
Senior Manager Manufacturing Resume Examples & Samples
- Bachelor’s or Associate’s Degree with 9-11 years of experience in a CGMP manufacturing environment
- 5 years leadership or supervisory experience
- Extended experience in Equipment Preparation, Cell Culture and/or Purification operations
- Demonstrated ability to execute production and project schedules
- Demonstrated ability to lead continuous improvement of technical and business processes
- Strong documentation practices including batch production records, SOPs, OJTs and other controlled docuents
- Experienced in troubleshooting, investigation, root cause and risk analysis in a CGMP environment
- Experienced in making tactical decisions on safety, process, scheduling and personnel-related issues
- Ability to gown and gain entry to manufacturing areas
- Primarily day shift, with flexibility and accessability to work with rotating shift operation
13
Senior Manager, Manufacturing Operations Resume Examples & Samples
- 30% - Global Operations Oversight
- Develop & implement policies and systems that standardize and improve labor efficiency to yield consistent on time order fulfillment, quality of product, and mitigate in warranty and out of box returns
- Develop & implement policies and systems to achieve near term and long term non-material productivity improvements
- 30% - Workforce Development & Planning
- Develop and execute short and long term human resource plans (talent acquisition, performance and leadership management) to mitigate skills gaps within aligned headcount requirements, ensuring current and future customer demand is sustainable
- Develop and maintain training programs to increase/maintain the knowledge, skills and abilities for direct labor and support personnel, thereby ensuring on time order fulfillment
- Create employee development plans for incumbents in critical organizational roles and/or high potential team members that will increase depth and breadth of knowledge.Examples include: Six Sigma, IPC, Professional Certifications, etc
- 30% - Global Organizational Performance Management
- Develop and monitor organizational KPIs
- Utilize KPIs to ensure current training, policies, and procedures directly translate to increased organizational effectiveness and continuous manufacturing improvement
- 10% - Self Development – Work with JADAK Leadership Team to identify and participate on projects or special assignments to further your personal skill set and knowledge base (ex. Corporate Development-M&A, Remote MFG Site Development, & Site Transfers.)
- Operations Management
- Warehouse and Materials Handling
- Electro-Optical Systems
- AutoID Technologies (I.e. Barcode, RFID, Machine Vision)
- Cost Accounting
- Team Building
- Employee Development
- Lean Six Sigma (Continuous Improvement & Defect Reduction)
- 8-12 years of progressive experience in leadership roles within operations & manufacturing environments
- 2-5 years of experience with electro-optical or electro-mechanical technologies preferred
14
Senior Manager Manufacturing Excellence FW Resume Examples & Samples
- Manage and execute Manufacturing Excellence projects within sourcing country that deliver measurable & sustainable increase in manufacturing efficiency, quality and speed
- Drive manufacturing efficiency by managing and overseeing projects and processes that focus on implementation of automation systems, driving lean manufacturing, optimizing streamlined production processes and optimizing products for highest manufacturing efficiency while maintaining product quality and performance integrity
- Manage factory performance reporting on manufacturing excellence related measurable such as, manufacturing efficiency, technology adoption rates, Lean KPI, selected range of key products efficiencies and others
- Sets up and runs regular strategic progress review meetings with all factories to identify challenges and opportunities and align on general strategic direction
- Collaborate actively to identify opportunities and run projects with relative adidas Group functions in Sourcing and HQ Brand Operations such as Quality, Materials, Costing, PCT, Planning, and others as business develops
- Facilitates and run cross functional events, summits, exchange meeting, workshops and training sessions with all internal and external stakeholders
- Collaborate actively with peers across other sourcing location, exchange ideas & best practice examples and adopt best practices within area of responsibility
- Liaise with Manufacturing Excellence Apparel and A&G team to identify opportunities and learnings to be adopted for continuous drive in manufacturing efficiencies
- Support FACT criteria evaluations at all suppliers for defined FACT milestones
- Strong project management skills, able to lead several cross functional projects with diverse project teams
- Strong knowledge and experience in Lean 6 Sigma practices
- Good problem-solving skills and a creative approach for new ideas
- Ability to effectively interact with different departments and functions
- Innovative and creative, challenges status quo
- Excellent interpersonal and English communication skill
- University degree in Business, Industrial Engineering (IE) or a related field
- 3 – 5 years of experience in Lean/6 Sigma implementation in the field or equivalent industry experience
- 8+ years’ experience in Footwear Sourcing & manufacturing or related field
- Management experience in multinational companies
15
Senior Manager Manufacturing Resume Examples & Samples
- 5 years supervisory or leadership experience
- Experienced in managing direct reports whom have leadership responsibilities (supervisors and managers)
- Experienced in establishment of safe practices in a CGMP environment
16
Senior Manager Manufacturing Resume Examples & Samples
- Focuses on the people in the organization to ensure engaged motivated workforce; ensure consistent clear communication aligned with Manufacturing Leadership Team
- Establishes department wide business practices; communicates consistent messages
- Optimizes department resources; ensures productive value added safe working environment
- Interacts with site efforts to ensure consistency in policies and practices; ensures staff compliance
- Establishes department mission, translates vision, engages organization, and delivers team results to achieve organizational vision
- Develop, maintain, and deliver results to departmental goals
- May lead plant operation teams; advocates resolution of issues by partnering effectively
- Assess department capacity against the Long Range Plan for products or potential products manufactured in the plant
- Planning, developing and maintaining the department budget
- Doctorate degree and 2 years of Manufacturing or Operations experience OR
- Master’s degree and 6 years of Manufacturing or Operations experience OR
- Bachelor’s degree and 8 years of Manufacturing or Operations experience OR
- Associate’s degree and 10 years of Manufacturing or Operations experience OR
- High school diploma / GED and 12 years of Manufacturing or Operations experience AND 2 years of managerial experience directly managing people and/or leadership experience leading teams, projects, programs or directing the allocation of resources
- Bachelor’s Degree in Life Sciences, Physical Sciences, Engineering or Process Manufacturing
- 8+ years of related lab, manufacturing or healthcare operational experience
- 6+ years of leadership experience with 2+ years as a cross-functional team leader including experience in performance management, technical problem solving, and managing projects
- 5+ years of aseptic processing practical experience (e.g. in a microbiology or cellular immunology lab), or aseptic production expertise (e.g. manufacturing production or process validation), or aseptic area (e.g. maintenance or troubleshooting) expertise
- 4+ years’ experience with a compliant highly regulated organization, cGMP or other
- Managing and coaching conflict effectively
- Overall understanding of mechanical, technical and operational systems
- Budgeting, goal setting, capacity planning, inventory control, lean principles, value stream mapping
- In depth business understanding of manufacturing or operations in biotechnology / biopharmaceuticals / pharmaceuticals industry
17
Senior Manager Manufacturing Downstream Resume Examples & Samples
- HS diploma and 9-11 years experience in a CGMP manufacturing environment and
- 5 years leading direct reports in an operations environment
- Strong understanding of cGMP
18
Senior Manager Manufacturing Resume Examples & Samples
- Responsible for business operations, cost, schedule, quality, communications, and team dynamics for the production product lines
- Regularly interfaces with customers to understand gaps in production across two shifts and works within the span of Raytheon to bring talent to the program to ensure production success
- Responsible for the financial, applicable technology, and schedule performance of production programs within cost limitations and established standards
- Experience interfacing with internal and external clients for the definition of requirements
- Analysis, project planning, and execution experience
- Experience managing large scale production programs
- Ability to collaborate and partner across multiple business segments and functions
- U.S. Citizenship is required as this position needs an active DOD Secret Security Clearance as of day one of employment
- Active DOD Secret Security Clearance
- Strong communication, writing, and presentation skills
19
Senior Manager, Manufacturing Excellence Resume Examples & Samples
- Seven to ten years of experience in Lean transformations, programs and projects in manufacturing
- Bachelor’s degree in a related field
- Demonstrated experience in lean process design and transforming manufacturing from push systems to pull systems in pursue of Just-In-Time production
- Extensive experience in analyzing end-to-end value chains and driving process improvement
- Demonstrated proficiency in IT applications to organize and analyze data (MS-Access, MS-Excel, Minitab, MS-Projects)
- Working knowledge of statistical process control concepts, data analysis, diagnostic tools and techniques
- In-depth working knowledge of Lean Tools and process/system analysis
- Demonstrated ability to handle multiple projects
- Excellent interpersonal, written and verbal communications skills
- Effective internal consulting skills with all levels of management
- Able to deliver feedback that is clear, articulate and non-threatening
- Exceptionally good listening skills, recognizes and manages resistance
- Results oriented-will take action when needed
- Manage Change & Influence Others
- Bio/pharmaceutical industry experience
- Deep understanding and application of TPS
- Deep understanding and successful application towards Shingo Operational Excellence Award
- Six Sigma Green or Black Belt certified from a recognized program
- APICS certification as Certified Supply Chain Professional (CSCP)
- Experience with the SCOR model and application
20
Senior Manager, Manufacturing Resume Examples & Samples
- Ensure thorough familiarity with policies and procedures relating to Standards of Business Conduct
- Conduct and trains/motivates subordinates in the importance of full compliance with the letter and spirit of such policies and procedures
- Organizes, plans, and guides the work load of the assigned area and carries production plans to completion, emphasizing safety, quality, schedule, and cost performance
- Assists IPT Manufacturing Mgr. by taking lead role in the development and implementation of improved manufacturing methods, training, and troubleshooting problem areas
- Develops and implements root cause and corrective actions
- STEM degree
- US Citizenship or Permanent Residence
- Engineering experience: has participated in design requirements for programs and helped implement them in manufacturing
- Test back ground: Has helped design or troubleshot Manufacturing related test issues
21
Senior Manager Manufacturing Excellence FW Resume Examples & Samples
- Manage and execute Manufacturing Excellence projects at key Strategic Technologies suppliers within sourcing country that deliver measurable & sustainable increase in manufacturing efficiency, quality and speed
- Manage factory performance reporting on manufacturing excellence related measurable such as, manufacturing efficiency, OEE, technology adoption rates, Lean KPI, selected range of key products efficiencies and others
- Sets up and runs regular strategic progress review meetings with all suppliers to identify challenges and opportunities and align on general strategic direction
- Excellent interpersonal and English communication skills
22
Senior Manager, Manufacturing Operations Resume Examples & Samples
- Meet objectives for inventory due dates
- Plan and implement process improvement activities to increase production efficiency and reduce cost of production
- Identify and meet customer expectations for quality and performance of products
- Implement most appropriate production technologies and quality assurance techniques for manufacturing of products in area of responsibility
- Establish appropriate quality, safety, and housekeeping standards in all areas of responsibility
- Ensure that production planning process is efficient and effective in meeting production schedules
- Manage staff: conduct performance reviews, career development, salary reviews and personal development plans for employees; review needs and provide training opportunities for staff to develop personal job-related skills and to improve operational flexibility to meet strategic needs
- Participate in strategic planning, budgeting and operations' planning within area of responsibility
- Maintain ongoing analysis of key issues, goals and metrics to provide regular updates to manager and business areas as needed
- Apply project management concept to manage R&D and production projects
- Act as a manufacturing representative on new product teams and in operational meetings for existing products. Provide information to team concerning all aspects of the production and QC process. Provide logistical support as needed for launching new products
- Understand and comply with ethical, legal and regulatory requirements applicable to our business
- B.S. in Molecular Biology, Biotechnology, Microbiology or related discipline
- Ten or more years experience in production and process/systems optimization in a health science, biotechnology or pharmaceutical manufacturing environment, including a minimum of five years experience in managing a large, diverse staff
- Working knowledge and experience with biological manufacturing and QC system
- Minimum five years project management experience in a technical area within a cross-functional team environment
- Outstanding troubleshooting skills
- Successful in implementing ideas and influencing people in a team environment
- Demonstrated record of improving manufacturing processes in a multiproduct manufacturing environment
- Experience in planning for resource and equipment to meet manufacturing needs
- M.S. or Ph.D. in a biological or engineering field
- Strong organizational and communication skills and a demonstrated ability and desire to share experience and knowledge with staff
- Excellent business management understanding
- Ability to wear personal protective equipment