Manufacturing Manager Resume Samples
4.7
(105 votes) for
Manufacturing Manager Resume Samples
The Guide To Resume Tailoring
Guide the recruiter to the conclusion that you are the best candidate for the manufacturing manager job. It’s actually very simple. Tailor your resume by picking relevant responsibilities from the examples below and then add your accomplishments. This way, you can position yourself in the best way to get hired.
Craft your perfect resume by picking job responsibilities written by professional recruiters
Pick from the thousands of curated job responsibilities used by the leading companies
Tailor your resume & cover letter with wording that best fits for each job you apply
Resume Builder
Create a Resume in Minutes with Professional Resume Templates
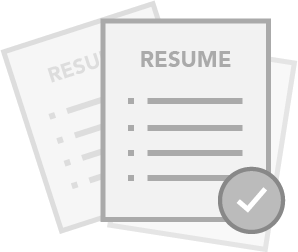
CHOOSE THE BEST TEMPLATE
- Choose from 15 Leading Templates. No need to think about design details.
USE PRE-WRITTEN BULLET POINTS
- Select from thousands of pre-written bullet points.
SAVE YOUR DOCUMENTS IN PDF FILES
- Instantly download in PDF format or share a custom link.
LM
L Medhurst
Lorna
Medhurst
25943 Rutherford Shore
Detroit
MI
+1 (555) 952 3352
25943 Rutherford Shore
Detroit
MI
Phone
p
+1 (555) 952 3352
Experience
Experience
Detroit, MI
Manufacturing Manager
Detroit, MI
Walker, Cummings and Prohaska
Detroit, MI
Manufacturing Manager
- Occasional stooping, bending, crouching, kneeling, pushing and pulling in order to move objects and equipment
- Participate in all aspects of personnel management (interviewing, training, coaching and developing). Assist with developing strategic staffing plans
- Engages in the typical responsibilities of a manager requiring planning, evaluating, organizing, integrating and delegating
- Leading, building, mentoring, motivating and managing strong teams
- Assist staff by recruiting, selecting, orienting, and training employees; developing personal growth opportunities
- Developing and sustaining Key Performance Indicators and driving discipline in measuring and maintaining them
- Leading the strategic direction of the manufacturing operation in the context of an ever-changing environment, including championing the implementation of WCM
Philadelphia, PA
Lean Manufacturing Manager
Philadelphia, PA
Roberts-Kiehn
Philadelphia, PA
Lean Manufacturing Manager
- Work closely with the Group Manager - Lean Manufacturing & the site leadership team to ensure the Divisional efforts are aligned with Group lean strategy & key priorities. Work with the site leadership teams to develop strategic deployment planning as well as specific goals and priorities that drive lean principles and concepts across the product group. Ensure vision, plans, & priorities are communicated throughout all locations
- Support the implementation of Mafact throughout the Division based on MPT’s Center of Excellence (“Training and Model Line”); Drive lean-based performance improvements and results throughout the site. In conjunction with MPT’s Manufacturing Strategy organization, identify, research, develop, and implement Lean tools and methods that follow the Magna Factory Concept (Mafact)
- Share knowledge with other Lean Specialists and teams across Honeywell for support and continued update of latest HOS enhancements/updates utilizing benchmarking efforts to lead development of "Best-in-Class" operational practices
- Coach and mentor Black Belts, Green Belts and new team members, support process owners to clearly link project metrics to strategic and operational objectives using Lean or six sigma principles
- Responsible for driving lean principles into capital equipment decisions & identifying high value-add, low cost solutions for improvements in key measurement areas with concentration on waste reduction; improved material flow; and streamlined internal process flow; work closely with other Lean and manufacturing leaders to solve complex problems that directly impact short and long-term business performance
- Work closely with the Director - Lean Manufacturing & Group VP to ensure product group efforts are aligned with global lean strategy & key priorities. Work with the site leadership teams to develop strategic deployment planning as well as specific goals and priorities that drive lean principles and concepts across the product group. Ensure vision, plans, & priorities are communicated throughout all locations
- Responsible for implementation of Mafact at all product group locations and the development of a Center of Excellence (“True North Model Line”); Drive lean-based performance improvements and results through all Product Group locations. In conjunction with MPT’s Manufacturing Strategy organization, identify, research, develop, and implement Lean tools and methods that follow the Magna Factory Concept (Mafact)
present
Detroit, MI
Senior Manufacturing Manager
Detroit, MI
Bradtke-Braun
present
Detroit, MI
Senior Manufacturing Manager
present
- Provides direction, ensures resources and manages programs to ensure the plant's safety and environmental performance to meet established goals
- Improve and develop organizational capabilities through effective performance management and planning/utilization of human and capital resources
- Lead and coach Operations Managers, guiding them in current positions and assisting with career development and training
- Identifies development opportunities and provides subordinates opportunities to meet career development plans
- Provide the direction and leadership to develop and promote a Lean/Sigma continuous improvement culture within Manufacturing
- Ensure clear direction, performance goals, job profiles and job expectations are established for all Team Members
- Provide leadership in the areas of staff selection, training and development, facility planning and construction, process, and procedure implementation
Education
Education
Bachelor’s Degree in Engineering
Bachelor’s Degree in Engineering
Strayer University
Bachelor’s Degree in Engineering
Skills
Skills
- Provide leadership to the production floor that promotes a positive work environment and delivers reliable, consistent and profitable results
- Good working knowledge in Lean Manufacturing Techniques and quality standards
- Knowledge of financial concepts applicable to manufacturing, including budgeting and cost controls
- Strong applied knowledge on statistical tools: DOE, AQL, SPC, etc
- Strong knowledge in assembly, welding and injection molding
- Solid use of PowerPoint and the ability to present to Sr. Leadership levels
- Excellent listening skills with the ability to size up situations in order to resolve conflict and solve problems with both people and processes
- Flexibility to respond quickly to changing business demands and the ability to assess priorities and act decisively on complex issues
- Maintain appropriate staffing levels in all areas of production and adjust as necessary for drops and spikes in sales to ensure profitability
- Excellent communication skill with the ability to deliver effective presentations at all levels
15 Manufacturing Manager resume templates
Read our complete resume writing guides
1
Manufacturing Manager Resume Examples & Samples
- 40% Processing
- Oversee the manufacturing area schedule to ensure market and inventory demands are met
- Monitor expenses and maintain departmental budget
- Provide technical expertise to drive resolution of manufacturing exceptions
- Identify and lead continuous improvement efforts
- Provide support for project portfolio management (capital projects and technology transfers)
- Support interdepartmental collaboration to provide continuity between manufacturing sites
- 25% People
- Conduct routine staff meetings to ensure communication and engagement
- Ensure staff development plans are in place and routine development discussions are held
- Establish department goals in accordance with site objectives
- Ensure Departmental Safety Training is performed and personnel attend Site Safety Meetings
- Maintain and promote a safe working environment
- Maintain audit readiness
- Staff positions
- Ensure adequate training of departmental personnel in cGMPs and SOPs
- 35% Quality
- Participate in facility and process inspections by domestic and international regulatory agencies
- Ensure that all SOPs and batch records are maintained to reflect current manufacturing methods and are in conformance with product licenses
- Assure that production equipment and facilities are maintained in proper working condition and in a validated state by assuring use of Change Control procedures
- Ensure timely submission and completion of all area quality documentation to meet established timelines
- Ensure that all compliance commitments are completed on time and provide documented evidence to support closure of each item according to the established timeline
- Bachelor's degree in Biology, Chemistry or related field with a minimum of 6 years relevant experience or Master's degree in Biology, Chemistry or related field with a minimum of 4 years relevant experience or 10 – 12 years of industry experience with 3 – 5 years of biologics manufacturing management experience
- 3 - 5 years of experience as an area supervisor in a bioprocessing manufacturing environment
- Knowledge of cGMPs, other regulatory requirements and aseptic processing is required
2
Mill Manufacturing Manager Resume Examples & Samples
- Delivers on Plant production plans, targets and KPI's as directed by the Head of Feed Operations
- Oversees and reviews the operations of the Mill; monitoring performance, managing process reliability and optimising efficiencies including the establishment of Performance System practises and culture
- Drive day to day manufacturing efficiency and operations excellence agenda
- Manages grain operations and Feed Mill team to deliver on production and processing requirements
- Supports the development and drives the implementation of product and customer quality service standards by championing quality and hygiene within the Mill and Grain Plant
- Collaborates and facilitates product development and launch activities within Mills
- Working with the Mill Engineering Manager and Head of Feed Operations to define capital requirements for development of new products, production improvements and asset replacements
- Ownership of capital projects from initial startup through to commissioning and full implementation
- Ensures compliance to standard work procedures
- Monitor, manage and be accountable for the quality of products manufactured in the Mill
- Work with the Engineering Manager to facilitate autonomous maintenance by Mill Operators
- Operator training, development and appraisals
- Third level production, engineering, science or business qualification, or equivalent experience
- Three to five years' experience in an operations management role
- Strong working knowledge of associated areas of quality, environmental management, health and safety and GPS
- Demonstrated high levels of financial and commercial acumen
- Proven people management and development skills are essential for this role
- Demonstrated ability to deliver capex projects on time and within budget
- Proven track record of implementing continuous improvement/operational excellence initiatives a distinct advantage
3
Advanced Manufacturing Manager Resume Examples & Samples
- Evaluate and improve manufacturing methods for maximum efficiency
- B.S. in Electronics or Manufacturing Engineering or equivalent
- Minimum 5 years of work experience in processing automotive electronics components and assemblies
- Computer skills to include Microsoft Office and AutoCAD
- Strong knowledge of state-of-the-art manufacturing technologies for electronic products
- Experience in Lean Manufacturing Techniques
- Hands-on manufacturing floor experience coupled with exposure to suppliers
- PC Experience: MS-Office, CompliantPro, SAP, MKS
4
Lean Manufacturing Manager Resume Examples & Samples
- Develop and create lean strategy and culture in the site with strategic advices to assess Lean Six Sigma opportunities
- Identify process improvement projects link with company goal, apply Lean Six Sigma methodologies to develop business
- Complement lean activities to optimize resources, priorities spending to meet targets and standards of the company
- Coach and mentor Black Belts, Green Belts and new team members, support process owners to clearly link project metrics to strategic and operational objectives using Lean or six sigma principles
- Deliver breakthrough levels of improvement in process capability and business processes to reduce defects and attain world-class levels of quality and cycle time reduction
- Develop and deliver project presentations to all levels of management
5
Upholstery Manufacturing Manager Resume Examples & Samples
- Work with management to plan and prioritize daily workload and achieve established productivity standards and goals
- Ensure that all products are manufactured at the best acceptable standards possible. All components should be correctly filed, set up, upholstered and trimmed to Williams-Sonoma, Inc. specifications
- Work closely with Frame Packing, Quality and Expeditor to make sure that the furniture is being produced in a timely manner
- Upholstery Manufacturing Experience Preferred
- Advanced PC skills – Microsoft Office
- Requires the ability to calculate figures and amounts. Must be able to read and interpret financial data
- Ability to work in a fast-paced environment and multi-task on a regular basis
- Strong sense of urgency and time management to meet deadlines
6
Lean Manufacturing Manager Resume Examples & Samples
- Work closely with the Group Manager - Lean Manufacturing & the site leadership team to ensure the Divisional efforts are aligned with Group lean strategy & key priorities. Work with the site leadership teams to develop strategic deployment planning as well as specific goals and priorities that drive lean principles and concepts across the product group. Ensure vision, plans, & priorities are communicated throughout all locations
- Support the implementation of Mafact throughout the Division based on MPT’s Center of Excellence (“Training and Model Line”); Drive lean-based performance improvements and results throughout the site. In conjunction with MPT’s Manufacturing Strategy organization, identify, research, develop, and implement Lean tools and methods that follow the Magna Factory Concept (Mafact)
- Responsible for coaching and training of all site employees in the use of Lean /Mafact tools and methodology. Responsible for leading lean / Mafact training for the site. Promotes the understanding, adoption & sustainability of improvement techniques across the site such as: kaizen, process mapping, waste identification and reduction, standardized work, problem solving, pull systems, 5S and visual management, lean sourcing, and other effective improvement techniques
- Responsible for driving lean principles into capital equipment decisions & identifying high value-add, low cost solutions for improvements in key measurement areas with concentration on waste reduction; improved material flow; and streamlined internal process flow; work closely with other Lean and manufacturing leaders to solve complex problems that directly impact short and long-term business performance
- Insures product Divisional lean initiatives are aligned with MPT-wide initiatives and consistently across the Division; coordinate Kaizen Activities across the site; seek, share and institutionalize best practices
- Challenge site leaders as necessary to create an action-based culture of continuous improvement and accountability to improve their KPI’s, including growth, productivity, asset utilization, inventory, and customer satisfaction. Report kaizen Improvement and best practices to Group Manager - Lean
- Serve as a change agent by influencing, communicating and institutionalizing a culture of simplification and standardization
- Conduct regular value stream reviews with assigned site leaders to assure the team drives significant and measurable business improvement; Communicate progress, status and issues to the site leaders; ensure all departments are compliant with the following: lean layout / machine design reviews and approval; program lean gate reviews; and follow-up with action lists, and kaizen activities
- Maintains working knowledge of safety policies and regulations to ensure duties of self and others are performed in a safe manner
- Additional duties and responsibilities as assigned
- Bachelor’s Degree required, Degree in engineering, or other technical field strongly preferred. MBA also a plus
- Passion for driving business improvement and leading change in a dynamic organization environment; Broad knowledge of multi-functional organizational processes and financial decision tools
- Proven track record for developing and coaching employee teams in a continuous improvement environment
- Must possess strong verbal and written communication skills, emphasizing interpersonal, group presentation, and team facilitation skills; must be comfortable and capable communicating at all levels of the organization. Must be fluent in English. Multi-lingual preferred (German, Spanish, & Chinese in particular)
- Strong analytical skills and computer skills (MS Office Suite) preferred. Detail oriented with the ability to see bigger picture and envision step-change scenarios; Experience coaching alignment between strategic business plans and lean improvement plans, (i.e. Strategic A3’s)
- Collaboration & Teamwork: Able to coach others in building effective relationships; involve others as appropriate in making decisions on behalf of the team; recognize and reward team players; share credit with others for team accomplishments; proactively address conflicts and disagreements that affect team effectiveness
- Continuous Quality & Performance Improvement: Able to encourage team members to share ideas that lead to improvement; minimize barriers to accomplish the team’s work; hold others accountable for identifying and removing obstacles that negatively affect quality; monitor the group’s processes for quality and efficiency issues that become targets for improvement; establish measures/benchmarks to track individual and/or team performance
- Creativity & Innovation: Able to apply innovative solutions to improve performance; challenge others to identify creative approaches to problems; provide support and encouragement to others when they attempt to innovate, even when they fail; generate new ideas that are often implemented by others; build on the suggestions/ideas of others to lead to new approaches and improvements
- Develops Capability: Able to proactively coach others to help improve their contribution; provide positive as well as constructive feedback on an ongoing basis; take responsibility for holding regular coaching and development discussions with team members; seek ideas from others in improving the team’s capability; ensure that others are taught key skills
- Open Communication: Able to give clear, understandable instructions to others; coach others in effective communication and listening skills; help others present their message effectively; initiate difficult or uncomfortable communications with others rather than avoiding them; encourage and facilitate candid and open communication within the team
7
External Manufacturing Manager Resume Examples & Samples
- Manufacturing leadership experience (5 years)
- Experience establishing and deploying safety and quality standards as they apply to operations (5 years)
- Supply chain operations experience in multiple functional areas such as Planning, Procurement, Capital Engineering and Manufacturing. Experience in the Food or CPG industry preferred. (5 years)
- Manufacturing P&L responsibility (2 years)
- Experience commercializing multi-market/region, multi-channel product introductions (3 years)
- Demonstrated ability to manage multiple priorities, projects, and deadlines
- Experience developing, implementing, and sustaining processes
- Capable of holding Contract Manufacturers accountable for meeting production supply requirements while adhering to cost expectations
- Detail oriented with strong analytical and reconciliation abilities
- Strong understanding of manufacturing cost drivers, ability to analyze and infer data, and capable of interpreting contract language
- Excellent relationship management skills with both external and internal constituents
- Operates independently and leads activities with little directions
- Experience interpreting and implementing technical changes (ie process, equipment, etc.) in a manufacturing environment
- Ability to translate Starbucks requirements into Contract Manufacturer's terms and systems
- Strong ability to influence internal and external partners to elevate performance against goals
- Demonstrated ability to identify issues and develop comprehensive action plans for resolution
8
Manufacturing Manager Resume Examples & Samples
- Diploma or degree in Engineering/Science
- 2 years previous experience in a similar environment
- A proven team player capable of ensuring standards are understood, communicated and adhered to
- An ability to analyse problems and determine solutions
- Should have a knowledge of manufacturing processes
- Self-motivated with the ability to work with minimal supervision
- Statistical knowledge
- Project work experience a preference
- Should have a basic knowledge of lean & continuous improvement tools. Six Sigma experience an advantage
- Excellent SAP ERP system or similar operational experience would be an advantage
- IT skills i.e. Microsoft Office
- Kaizen & DMAIC
- Lean 6 Sigma & lean techniques
- Performance Management
- Project Chartering & project planning
- Reporting
- Basis Statistical knowledge
- Team working/building
- Must be able to demonstrate leadership potential
- Excellent IT skills with a good working knowledge of SAP
- Technical based Problem solving
- Good interpersonal, communication & influencing skills
- Operation of basic process equipment
- Manage and improve operational processes
- Hands on operational
- Filling & packaging
9
World Class Manufacturing Manager Resume Examples & Samples
- Leads and/or facilitate highly skilled teams in resolving critical process and product problems both internally, with customers, and/or with suppliers
- Increases knowledge and skill level through advanced training, OJT, networking, and sharing best practices
- Assesses operations and identify key area for improvement prioritized by organization objectives & project selection
- Administers and ensures compliance with the Quality, Environmental, and Material Management System requirements as outlined in the policy manuals
- Champions the MAFACT integration and improvement metrics for the division
- Performs job elemental time studies using Magna Production System (MPS) techniques
- Performs kaizen activities, rebalance work content using MPS techniques
- Assists with developing standardized work for shop floor employees
- Root Cause analysis based on MPS problem solving framework
- Knowledge in shop floor management/andon
- Knowledge of incremental training methodology
- Displays a positive attitude towards safety, works safely, follows all company policies and reports all unsafe and unhealthy conditions
- Reports all accidents and injuries in a timely manner
10
Manufacturing Manager Resume Examples & Samples
- Production Background is a must
- 10-15 Years in FMCG companies with minimum of 5 years in Managerial role
- Arabic speaker plus
- Excellent English communication
11
Manufacturing Manager Resume Examples & Samples
- The core responsibilities of this highly challenging role
- Lead a Team of 5 Managers with approx. 25 staff
- Promote & implement Best Practice Health & Safety policies and procedures
- Prepare Annual Business Plan & manage all variable costs within budget
- Continue to cultivate and implement performance measures to ensure that the business performs at world class manufacturing standards
- Continuously develop operating performance through the use of GPS tools and techniques
- Produce 100% quality products (Right First Time) to meet agreed customer and product safety specifications
- Manage hygiene and cleanliness standards throughout the plants
- Ensure production targets (throughput, yields, and recoveries) are met
- Further develop and implement world-class quality processes, which will generate a competitive lever in providing customer solutions
- A part of the leadership group for the Operations group, play an active part in developing its future strategic direction
- Ensure compliance with regulatory requirements
- Third level qualification in Engineering or Manufacturing or related discipline
- Minimum of 5 years' experience at management level in a complex manufacturing environment such as Food, Pharma or Chemicals industries
- Proven acumen to meet strategic operational imperatives
- Experience in plant operations, manufacturing systems management and process engineering design and implementation
- Advanced organisational skills
- High energy levels
- Ability to lead and to implement the decisions required to deliver change
- Ability to liaise effectively with internal and external stakeholders
- High-level multi-tasking ability and experience of delivering large-scale projects to demanding targets
12
Lean Manufacturing Manager Resume Examples & Samples
- Lead the master plan definition inside the plant, in coordination with regional Lean and other internal areas
- Assign resources; organize topics and events to comply with the master plan execution and the Lean projects results
- Lead the audit process, coordinating other resources from region or global when available
- Continuously deploy the Lean manufacturing mindset, concepts and principles inside the plant, acting as an expert on Lean matters for other to refer to
- Participate in practice sharing sessions with other plants and organizing such sessions for other areas as well (finance, purchasing, engineering, quality, operations)
- Keep track of all activities performed, not performed and the results obtained from projects and Lean events
- Identify and organize training sessions or programs in coordination with other areas, HR and regional Lean to continue expanding the knowledge of Lean concepts in the plant
13
Lean Manufacturing Manager Resume Examples & Samples
- Work closely with the Director - Lean Manufacturing & Group VP to ensure product group efforts are aligned with global lean strategy & key priorities. Work with the site leadership teams to develop strategic deployment planning as well as specific goals and priorities that drive lean principles and concepts across the product group. Ensure vision, plans, & priorities are communicated throughout all locations
- Responsible for implementation of Mafact at all product group locations and the development of a Center of Excellence (“True North Model Line”); Drive lean-based performance improvements and results through all Product Group locations. In conjunction with MPT’s Manufacturing Strategy organization, identify, research, develop, and implement Lean tools and methods that follow the Magna Factory Concept (Mafact)
- Responsible for coaching and mentoring of site lean leaders in the use of Lean /Mafact tools and methodology. Responsible for leading lean / Mafact training for management-level staff. Promotes the understanding, adoption & sustainability of improvement techniques through all Group sites such as: kaizen, process mapping, waste identification and reduction, standardized work, inventory pull systems, 5S and visual management, lean sourcing, and other effective improvement techniques
- Responsible for driving lean principles into the CapEx approval process & identifying high value-add, low cost solutions for improvements in key measurement areas with concentration on waste reduction; improved material flow; and streamlined internal process flow; work closely with other Lean and manufacturing experts to solve complex problems that directly impact short and long-term business performance
- Insures product group lean initiatives are aligned with Mafact-wide initiatives and consistently across all sites within the Product Group; coordinate Kaizen Activities between the Plants; seek, share and institutionalize best practices
- Challenge organizational leaders as necessary to create an action-biased culture of continuous improvement and accountability to improve their KPI’s, including growth, productivity, asset utilization, inventory, and customer allegiance. Report kaizen Improvement and best practices to Global Director
- Proactively simplify the work instructions, procedures and processes within the value stream to drive continuous improvement of the Quality Management System; supports and adheres to policies, procedures, and operational guidelines related to established quality management system (TS 16949)
- Conduct regular value stream reviews with assigned Lean Leaders to assure the team drives significant and measurable business impact; Communicate progress, status and issues to the business leaders; ensure all group locations are compliant with the following: lean layout / machine design reviews and approval; program lean gate reviews; and follow-up with action lists, kaizen activities, and Performance Reviews
- A minimum of 3 years of supervisory / leadership-related experience in a manufacturing environment. Tier 1/2 automotive industry experience preferred. Progressive management experience and international work experience also desired
- Extensive formal lean training and comprehensive knowledge of Lean and continuous improvement methodologies and tools. A track record implementing successful TPS-based Lean programs (both at a strategic and “hand-on” level) including: value-stream mapping, facilitating kaizen training events, material flow, 5S, visual factory, Lean in the office, Lean sourcing, etc
- Passion for driving business improvement and leading change in a large, complex, global environment; Broad knowledge of multi-functional, multi-site, global organizational processes and financial business methods
- Proven track record for developing, training, and coaching employee teams in a continuous improvement environment
14
Senior Manufacturing Manager Resume Examples & Samples
- Ensure all manufacturing operations are completed in a safe and compliant manner
- Lead plant manufacturing team to achieve plant production goals and objectives
- Resolve production issues with plant manufacturing staff
- Ensure the maintenance and reliability of plant manufacturing equipment and machinery
- Supervise plant production scheduling and capacity analysis
- Ensure effective communication of manufacturing plan and status
- Monitor and take action to achieve and exceed plant metrics
- Ensure the implementation of a sustainable and consistent plant management system
- Ensure the timely availability of quality production-related materials and supplies
- Establish and communicate plant manufacturing goals and objectives consistent with the manufacturing business strategy
- Prepare and maintain plant budget
- Collaborate with, and serve as plant level liaison to manufacturing support organizations (QA/QC, EOS, PD, Logistics, HR, etc.)
- Ensure the coordination and goal alignment of plant production operations with plant support functions
- Resolve issues between plant manufacturing and various support organizations
- Ensure plant manufacturing practices (processes & methods) and policies comply with external regulatory requirements and the companies operating standards
- Approve, establish and ensure plant practices and policies are consistent within the manufacturing organization and company
- Represent the plant to regulatory authorities
- Coach and ensure the development of plant management and staff
- Partner with HR to ensure the plant is able to recruit, retain and motivate staff
- Ensure plant safety goals are communicated and supported with on-going plant safety programs
- Monitors and/or initiates the development and implementation of plant improvement projects
- Represent plant and/or manufacturing organization on projects, task forces, or various teams as needed
- Manage relations with union to ensure workforce flexibility and efficiency
- Demonstrate a high level of skill and competency at a level comparable to a Production Manager
- Experience leading a unionised organisation
- Demonstrated/potential skills and competencies in the following
- Drug Product Manufacturing Technologies
- Experience with Aseptic Filling Lines with Barrier Isolation Technology and/or RABS Technology
- Aseptic Operations and Techniques
- Ample knowledge of cGMP Regulations around Sterile Product Manufacturing
- Negotiating skills
- Overall understanding of mechanical systems
- Budgeting
- Goal setting
- Capacity Planning/Inventory
- In depth understanding of Manufacturing/Pharma Business
15
Manufacturing Manager Resume Examples & Samples
- Responsible for the safety of all employees in the FC and MF factories
- Provide adequate supervision for day and shift operations
- Ensure all employees are appropriately trained to undertake their daily duties
- All other H&S responsibilities as outlined in the SMS
- Ensure the highest standards of quality are achieved for all production in line with KPIs
- Achieve production targets for all machines in the FC and MF factories
- To achieve budget costings for both factories annually
- To liaise with the Works and QE Managers on all technical issues relevant to the manufacturing process
- To prepare reports on the FC and MF production performance as required
- Lead investigations of deviations from the normal manufacturing processes and customer complaints
- Liaise with the works & maintenance managers in relation to capital projects
- To ensure factory performance is in line with budget and EBMO reporting requirements
- Development of all direct and indirect reports ensuring continuous improvement in their performance and career development
- Address disciplinary issues that may arise in conjunction with the Works Manager and HR
- To carry out any other duties as outlined by the Works Manager
16
Manufacturing Manager Resume Examples & Samples
- Establish appropriate Global manufacturing strategies for Coca-Cola Freestyle Equipment to meet quality, On Time Delivery, cost and business objectives. Leverage existing TCCC supply base and a knowledge / processes developed by Sustaining Engineering, Strategic Procurement, Field/service organization knowledge and Parts Supply Chain
- Develop position and nurture a world-class supplier base for Coca-Cola Freestyle Equipment that exceeds the product quality, delivery and cost goals
- Drive continuous improvement and be held accountable for Mfg. metrics including
- BS degree in science or engineering
- A minimum of 10 years of relevant work experience in manufacturing or quality engineering or related fields with at least 5 years of progressive management experience
- Manufacturing Quality experience is a must
- Second Language is a plus: Spanish preferred
17
Manufacturing Manager Resume Examples & Samples
- To exhibit a fair and consistent management approach, which follows the principles outlined in The Magna Employee’s Charter to ensure a satisfied and productive employee workplace
- To persuade and support the following of Company policies and business objectives in the daily management of the operations of the Company
- To identify growth and developmental opportunities and on-going training needs of supervisory personnel, which provide for an overall positive working environment
- To lead and direct Company environmental, health and safety objectives which provide for a safe and healthful workplace for all Norplas employees that includes
- Regulatory compliance with Local, State and Federal Legislations
- Establishing plant-wide measurables and goals that are monitored, tracked and audited on a regular basis and communicated to employees that meet or exceed industry standards
- Recognition of accomplishments/milestones in the areas of safety, environmental, ergonomics and employee wellness
- Development of effective programs that increase employee awareness and involvement in the areas of safety, environmental, ergonomics and employee wellness
- Accountability of supervisors for enforcing safety rules and implementing the necessary training and corrective actions to ensure proper focus on established objectives
- Ensure that every Norplas Team Member has a safe work environment, free from recognized hazards. Promote and encourage safe work habits, and the immediate communication of unsafe conditions. Understand, support, implement, and enforce compliance to all company and governmental agencies safety policies, procedures and regulations. Interpret company policies to workers and enforce safety regulations. Actively prevent pollution/reduce waste to support the attainment of established goals. Maintain an understanding and instruct employees on how their specific job can affect the environment or the health and safety of themselves or others
- It is the responsibility of all Norplas employees to comply with the Environmental, Health and Safety Policy. Compliance with all applicable federal, state, local, customer and corporate requirements and regulations including OSHA, DEQ, and ISO 14001 is expected. Perform regular safety audits, conduct safety briefings during pre-shift meetings, be involved in the accident/incident investigation as needed, train new employees, correct unsafe acts of conditions through the safety observation forms, and conduct performance appraisals for workers safety performance
- Supervisors/managers are responsible for coordinating and directing employees within respective process area while upholding the principles of the Employee Charter. Responsibilities include but are not limited to interviewing, hiring, and training employees, the completion of audits within an assigned area, and proper rotation of employees to prevent fatigue. Also, the planning, assigning, and directing work, appraising performance, rewarding, housekeeping and disciplining employees, addressing complaints and resolving problems
- Track the activities of the Advanced Product Quality Planning Group to ensure that Launch activities and manufacturing practices are progressing toward satisfying the customer requirements for the successful launch of quality product that is capable of being manufactured at the Norplas performance level expectation for all manufacturing key operational indicators
- Exceed customer expectations by resolving problems quickly and professionally. Solicit the support of the APQP department to proactively help the customer solve their problems. Challenge the team to explore all possible alternatives for problem solving and provide the customer with advantages and disadvantages of each option
- Continuously improve the quality standards of all products manufactured by Norplas. Ensure that customer issues are responded to expediently and in a professional manner
- Track the effectiveness of all systems required to maintain on-time delivery of product. React immediately to resolve any issues, which have or may occur to interrupt the scheduled delivery of product to the customer
- Keep the entire organization focused on Continuous Improvement to ensure reduction of manufactured costs, and minimize the required on hand inventory of WIP, Tier II components, and finished goods to improve inventory turns
- Support Norplas Management in the ongoing effort to institutionalize the Decoma Innovation Initiative. Encourage all employees within the Manufacturing Departments to participate in the Innovation Innitiative
- Ensure that the organization is in place and that all individuals within the organization have their roles clearly understood. Work with the Manufacturing Department Managers to achieve the targets of each key operational indicator
- Participate as required in Continuous Improvement teams and provide leadership and support to teams in their efforts to meet or better targeted capital costs
- Employ the principles of synchronous manufacturing for elimination of waste and optimization of labor efficiencies
- Enforce the requirements of Decoma’s Capital Appropriation procedure. Analyze all capital expenditures for appropriate value
- Follow the Magna’s Employee Charter and ensure that all Norplas Management and Supervisory staff understand and follow the principles of the charter
- Follow the guidelines of the Norplas Employee Handbook and direct all Norplas manufacturing supervisory staff in the correct use of the handbook as required
- Guarantee that all Norplas manufacturing employees and supplier partners are following the guidelines of all State, Local and Federal requirements
- Must be degreed in a related field of study or twelve (12) years of directly related job experience combined with some formal training. Related formal training will be considered is lieu of degree requirements
- Must have completed or currently be enrolled in the Magna Management Development Program
- Minimum five years experience in the manufacture of molded or painted and assembled automotive exterior plastic parts
18
Senior Manufacturing Manager Resume Examples & Samples
- Drive manufacturing team to achieve established targets for daily going rate (DGR) and on-time shipments (OTS)
- Hire, coach, lead and develop approximately 200 hourly team members, and 5 - 10 to direct reports (Production, Maintenance, and Engineering Managers). Conduct team member training
- Assess and analyze current practices and drive improves
- Enforce proper material management procedures
- Support and collaborate with Sales, Marketing, Finance, Engineering, Test and Quality departments
19
Senior Manufacturing Manager Resume Examples & Samples
- Develop, organize, and lead projects related to Advanced Manufacturing Engineering, New Product Introduction (NPI) and Manufacturing
- Support shop manufacturing teams on existing product production yield problems, quality concerns, and Change in Design (CID) introductions
- Communicates recommendations and solutions across direct organization and with cross-functional partner organizations
- Involved in complex decision making sometimes with external parties
- Inputs and influences decisions within own discipline and area
- Is considered a senior and seasoned practitioner. Works on complex technological solutions
- Has authority in the network of experts and in project teams
- Presents product / program strategies, technical roadmaps, risks and recommendations to senior leaders (EB and SEB) across GE
- Minimum of 5 additional years of experience in Industrial Project
- Minimum of 5 additional years of experience in Industrial Projects in applicable product field
- Ability to develop alternative approaches to solve complex problems
- Demonstrated ability to lead programs / projects working with and motivating operational teams
- Project management skills defining and establishing program plans using MS Project or similar software
- Eight plus years prior jet engine airfoil blade and vane manufacturing experience
- Demonstrated knowledge and experience with fan and compressor airfoil forging/forming operations, machining operations, NDT, finishing operations, testing and quality methods, procedures, systems and requirements
- Knowledge of GE Aviation production cost and measurements systems
- Familiarity with, and the use of Unigraphics/NX CAD, NXNC and manufacturing software such as DEFORM, NXCMM, or Valysis
- Knowledge in jet engine assembly and testing related to applicable products
20
Manufacturing Manager Resume Examples & Samples
- Develop, coordinate, lead and execute daily production plans
- Actively participate and lead team in Health & Safety programs to achieve established goals
- Practice sound leadership, employee relations, and communication skills in order to motivate and direct the team towards safety, quality and productivity improvements
- Coordinate all first line activities (e.g. Safety, Quality, Methods, Production Control) to assure the meeting of production schedules and customer satisfaction, cost goals, and maintaining the highest standards of quality
- Coach and counsel employees regarding individual performance and development needs
- Provide prompt feedback to employees regarding individual performance and development needs
- Perform administrative duties to support the business, time & attendance, self-audits, absence reviews, regulatory training records, etc
- Develop knowledge and expertise in products and manufacturing processes
- Support process improvement initiatives to reduce cycle time, improve inventory turns, reduce manufacturing losses, and increase capacity
- Analyze and diagnose machine and/or assembly problems and take corrective measures to minimize downtime and interruption of schedules
- Bachelor's Degree form an accredited college or university
- Minimum 3 years of manufacturing industry experience
- Minimum of 2 years of leadership experience
- Strong analytical, problem solving, and project management skills
- Strong team building skills, with the ability to counsel and motivate the workforce
- Bachelor's Degree in Engineering from an accredited college or university
- Ability to manage multiple priorities under tight deadlines and bring assignments to successful closure
- Knowledge of manufacturing operation and production scheduling practices or systems (e.g. SAP)
- Ability to interact with all levels and functions of the organization
- Corporate Training Program graduate (manufacturing / operations / engineering)
- Strong understanding of business processes in a service environment
21
Manufacturing Manager Resume Examples & Samples
- Bachelor’s Degree in Industrial Engineering or an Engineering discipline from an accredited university or college (OR High School Diploma / GED with a minimum 4 years of work experience in the manufacturing industry)
- Minimum of 5 years of experience in manufacturing
- Minimum of one year of management experience
- Ability to make data driven decision and utilize Six Sigma and Lean tools or equivalent quality tools
- Strong background in the interpretation of engineering drawings / specification and manufacturing processes
- Strong organizational skills with a high attention to detail
22
External Manufacturing Manager Resume Examples & Samples
- Internally within a global matrix environment with key J&J Departments: Strategic Sourcing, Quality & Compliance and Planning, coordinating other internal stake holders such, R&D, SMP, commercial teams, Regulatory and Engineering
- Externally with a wide variety of stakeholders, including, but not limited to: EM top management, EM site leaders, EM Regulatory and technical team members, Statutory SMEs, etc
- EHSS, Regulatory and Quality Compliance/ Supplier compliance metrics
- Customer Service/ Reliability/ Supplier Delivery performance
- Financials/ Contribution to Continuous Improvement Initiatives (CIP, Services, Complexity Reduction) - Budget management of non-standard costs
- On-time Projects planning and execution (NPI, …)
- Min. 6 yrs relative Operational experience
- Experience working in cross-functional environment with international work experience preferred
- Experience in any of the following areas: Supply Chain/Operations, Production, Engineering, Quality, R&D, Project Management – Supply Chain Sourcing, Supply Planning or Distribution/Transportation
- Make Excellence, Process Excellence and Continuous improvement experience in Supply Chain and/or manufacturing environment preferred
- Experience working in the area of FMCG or OTC products or Medical Devices
- Knowledge of new product commercialization processes
- Knowledge of compliance requirements (cGMP, FDA, DEA, etc)
- End to End Supply Chain understanding and track record of improvements in processes that maximizes organizational value
- Cultural sensitivity – previous exposure to cultural diversityProduction
23
Lean Manufacturing Manager Resume Examples & Samples
- Successfully deploy FMOS across the network and establish a process for continuous improvement of this Operating System including integrating MSE
- Partner with the global MSE team to facilitate the deployment of TPM into targeted factories
- Working with counterparts in other regions develop and deploy strategies/initiatives that support continuous improvement and Do it Best pillars
- Perform Site OPEX audits to check adherence against standards & to ensure 2 way learning on the continuous improvement journey & improvements of operational performance of sites across region
- Set up an effective community of site IE/CI coaches and regional CI manager to develop new standards and to share Best Practice
- Ensure sites have strong CI foundation in place to support a successful MSE implementation
- Lead and teach associates primarily through implementation of CI Thinking principles and practices
- Drive continuous improvement through application of a variety of tools: TPM, value stream management, lean diagnosis/strategy & objective setting, Kanban, SMED, team problem solving, Kaizen, etc
- Develop and site level network of IE Coaches who will support the deployment of both network wide and site level continuous improvement initiatives
- Lean Toolkit Application Skills (value stream mapping, 5S, Kaizen, Kanban, Error proofing, SMED, team problem solving, TQM/Re-Engineering, etc.)
- Strong facilitation & Problem Solving abilities
- Manufacturing: Product and Process knowledge
- Supply Chain management processes
- Continuous Improvement/Lean implementation/facilitation skills
- Lean management experience and/or business process change management
- 5 – 7 years of relevant experience in Supply Chain (IE, Technical, Operations or Logistics)
- Knowledge of internal manufacturing and major business processes
- Track record in leading step-change initiatives/Best practice roll out
- Multi-functional experience/Broad perspective
- An undergraduate degree in Engineering or Business Management
- 5 – 7 years of relevant engineering or manufacturing experience
- Bachelor of Science in Industrial Engineering
- Operations line management – 2 years
- Site Industrial Engineer, Lean Manager and/or Continuous Improvement Engineer - 3 years
- MBA or advanced degree
24
Manufacturing Manager Resume Examples & Samples
- Knowledge of Quality System requirements, such as ISO and QSR
- Ability to identify opportunities and implement World Class manufacturing practices, including Lean Manufacturing, Six Sigma and ME2 concepts
- Excellent written and verbal communication skills in English and Spanish at different organizational levels
- Knowledge of Operations Management, including resource and capacity planning as well as project management
- Knowledge of financial concepts applicable to manufacturing, including budgeting and cost controls
- Good team work and collaboration skills
- Knowledge of word processing, spreadsheet analysis, data management, projects management, presentation graphics, engineering analysis and statistical software
- Knowledge of information systems including but not limited to Enterprise Resource Planning (ERP), CAF, and GoCart preferred
25
Manufacturing Manager Resume Examples & Samples
- Leadership & management of specified business unit
- Full operational and budget responsibility for the business unit
- Implement and develop key measurables to identify and drive improvements within the business unit
- Establish key strategic activity required to develop the business unit in line with overall objectives
- Ensure production efficiency and production schedule adherence exceeds the required level
- Maintain and develop the delivery of finished products in line with cost, quality and production schedule requirements
- Ensure proactive maintenance of all equipment and processes enabling full support to all manufacturing lines
- Lead the development and implementation of significant improvements in department wide processes, procedures and systems, ensuring adherence by employees and third party contractors while operating on site
- Ensure compliance of all production areas to the required operational standards
- Manage and lead staff in an efficient and flexible manner, ensuring all necessary training and development has been performed and necessary qualifications are in place
- Maintain and develop the emphasis on ownership and accountability throughout the department
- Promote and support Health and Safety guidelines
- Communicate, liaise and negotiate internally and externally using appropriate methods to facilitate the development of profitable business and sustainable relationships
- Achieve and sustain production efficiency targets
- Achieve and sustain production schedule adherence targets
- Positive feedback from team, peers and immediate manager
- Absence Management
26
Manufacturing Manager Resume Examples & Samples
- Creates and manages to an operational budget for assigned departments
- Prepares and delivers full performance evaluations for all direct reports
- Identifies and provides developmental opportunities for high potential employees. Regularly meets with employees and assists with the creation of individual development plans
- Makes technical and business risk decisions under real-time pressure
- Ensures department is operating within company policies and procedures
- Responds to internal and external audit observations and identifies and implements appropriate corrective and preventive actions
- Minimum of 7 years of experience in manufacturing environment, with at least three years of management experience/direct supervision of staff
- Bachelor’s degree, preferred in a scientific of engineering discipline
- Strong leadership abilities with capability to leverage diverse resources, respond quickly, understand impact of changes and decisions, facilitate agreement, build collaborative relationships and understand customer’s needs. written communications skills required
- Knowledge of molecular biology/chemistry/engineering principles and processes requirements
27
Manufacturing Manager Resume Examples & Samples
- Optimize performance of machining and dry pendant departments
- Manage NPI activities as pertinent to department
- Develop operational plans for the machining of sprinkler frames
- Organize human and capital resources as required to support metric goals and operational plans
- Manage day-to-day activities
- Resolve technical, operational, and HR issues
- Provide technical expertise and guidance
- Prepare periodic reports on metrics
- Collaborate with R&D/Product Engineering on the development and introduction of new products
- Manage the maintenance of standard routers
- Participate in the development of annual budgets
- Provide input for financial forecasts
- Strengthen the Plant’s core-competency in sprinkler frame machining
- The preferred candidate should have a Bachelor’s of Science degree in one of the following fields of study: Mechanical Engineering or MET, Industrial Engineering, Manufacturing Engineering
- Preferred candidates will possess the required educational background and at least 10 years experience; with at least 5 years’ experience in a high-volume machining environment
- Experience with manufacturing high volume, engineered products, including metalworking, machining (includes computer numerical controls (CNC), work holding, consumable tooling, statistical process controls, automation and testing
- Must have excellent communication skills, both verbally and in writing and be able to read and write business policies, procedures, general business periodicals, manuals, blueprints and other correspondence. Must have excellent organizational and managerial skills. Must have strong project management skills with leadership experience in a supervisory capacity. Experience in implementation of Lean Manufacturing, 5s, and Six Sigma techniques required, including work teams, Continuous Improvement, single piece flow systems, Statistical Process Control (SPC), Kanban material flow, etc
- Must be knowledgeable with using computers and multiple software applications that include Word, Excel, and others
- Preferred knowledge of mechanics, hydraulics, pneumatics, and machining methods
28
Senior Manufacturing Manager Resume Examples & Samples
- Coordinate and direct Manufacturing Services personnel in the cGMP filling and packaging areas to meet all scheduled manufacturing work
- Partner with Planning to ensure effective prioritization and schedule adherence and to meet all required capacity demands
- Partner with Quality to ensure a cGMP operation
- Guide and train employees to ensure QSR and ISO requirements have been properly implemented and are continually met
- Manage and maintain all system data to drive daily operations and to produce metrics and reports that support opertional excellence
- Represent Manufacturing Filling and Packaging during FDA, ISO, and Customer audits
- Develop emerging leaders among both direct reports and extended team to develop bench strength and a robust succession plan
- Identify opportunities for material and labor productivity and adequately resource projects to realize hard savings from key opportunities
- Develop aggressive goals and champion the use of appropriate metrics to monitor and drive progress in the above objectives
- Provide updates or presentations to site leadership regarding status of projects or programs
- Continually help to improve the company culture by practice and example to the 4”I” values of Thermo Fisher Scientific – Integrity, Intensity, Innovation and Involvement
- Complete all company required training programs
- Bachelor’s degree with ten years’ experience working in a cGMP Manufacturing operation
- 5+ years of supervisory experience
- Experience building effective teams and developing high potential talent
- Strong understanding of how continuous improvement tools drive customer and corporate value
- Superior organizational skills with ability to multi-task and balance complex and routine work activities
- Demonstrated ability to lead, cross-functional teams, influence business partners and get results through others outside a reporting relationship. High-level business acumen
- Advanced interpersonal and communication skills, both written and verbal, with the ability to work as a team player and team builder
- Excellent communication skills for group presentations and intercompany written and verbal communications
- Demonstrated experience using financial reports, budgeting and other related reporting tools
- Proficiency in common program management communication software tools (i.e. MS Project, PowerPoint, MS Word, Excel, etc.)
- Experience utilizing complex ERP software to drive daily operations and long-term business goals
- This position has not been approved for Relocation Assistance
29
World Class Manufacturing Manager Resume Examples & Samples
- Work with GM’s/AGM’s and Divisions to implement WCM
- Assist in assessing Capacity Utilization across Divisions
- Assist in the Tracking of Divisional Performance
- Leads long-term projects aimed at waste elimination/production efficiency and establishment of model WCM areas in conjunction with manufacturing sites (e.g. plant floor layout, material-handling routes, service parts, and key future launches)
- Attends and helps divisions prepare for MAFACT audit assessments to ensure success
- Leads employee classes related to MPS/WCM including, but not limited to, job instruction, standardized work, and Kaizen
- Coordinate/Support Divisional needs for training in WCM systems/tools
- Mentor/Train next level of WCM experts (Building bench strength to support company growth)
- Facilitates continuous improvement project teams to continuously improve processes and give support to areas within the organization
- Displays a positive approach to the continuous improvement of the Group and keeps current with new products, processes, materials and equipment technologies
- Leads employees through workshops designed to improve work processes to reduce cycle time, inventory, labor hours, scrap, etc. (Based upon team/management requests)
- Assist in the sharing of Best Practices between Divisions
- Work with VP and GMs to ensure consistency of MAFACT, approach
- May provide work direction and/or supervision to other staff
- Bachelor’s degree in related field; or equivalent
- Three years’ experience in lean manufacturing processes or related field; or equivalent
- Minimum of 3 years supervisory/management experience preferred
- Strong technical background in tooling,welding and assembly operations
- Genuine desire to work within the Divisions of Cosma Body Systems and effect change related to WCM
- Must have excellent communication skills and a proven ability to work with others in a team environment
30
Senior Manufacturing Manager Resume Examples & Samples
- Oversees all site functions – Operations, Facilities, Maintenance, Quality, Health and Safety, Procurement, Scheduling ect
- Owns financial oversight, projections, tracking and reporting
- Ensures internal, governmental, safety and customer policy compliance
- Partners daily with both internal and external customers on various items
- Works closely with HR partner on staffing, talent management, policy compliance and operational excellence initiatives
- Partners with local Union to enforce contractual obligations and to optimize productivity and eliminate waste production wastes
- Maintains relationships with local governmental and civic leaders
- Bachelors degree in Business, Operations, Engineering or a related field
- 8 years minimum manufacturing/automotive experience
- Proven leadership capabilities with the ability to drive change
- Proficient in Microsoft Office Suite – Excel, Power Point, Word
- Advanced degree – MBA, Operations, Engineering or Supply Chain
- Preferred SAP experience
- Manufacturing experience in Union/Labor environment
- 10 years experience in Aerospace manufacturing environment
31
Manufacturing Manager Resume Examples & Samples
- Serve as Forest City Staff member driving manufacturing excellence through department strategy and execution of daily requirement
- Building Organizational Culture to drive manufacturing excellence – must be able to drive a vision that develops the workforce to meet plant goals
- Manage manning plans to achieve customer delivery goals – must understand concept of flexible workforce and ability to develop plans to move up or down with volume
- Manage safe work environment driving a Zero Incident Culture
- Manage and maintain a highly engaged environment conducive to continuous improvement manufacturing
- Participate in annual / semi-annual / monthly / daily production and finance reviews for Forest City
- Support Eaton Business System integration through operational assessments such as: EBEA, OpA, MESH, EQS, Lean Six Sigma
- Manage team of production supervisors including hiring and performance management
- Must manage flow of complex manufacturing process
- Must understand concepts of Work In Progress and how to optimize material flowing from station to station
- Bachelor’s Degree from an accredited institution is required
- Minimum 3 years of managerial experience
- Minimum 3 years of experience in a Manufacturing environment or Operations
- Bachelor’s degree in Industrial Engineering is preferred
- Master’s Degree is preferred
- Proven analytical and problem-solving skills
- Knowledge of hose manufacturing process – or understand concepts of flow in manufacturing
- Knowledge of key financial measures
- Knowledge of kaizen and lean manufacturing concepts
- PC Skills: Proficiency in MS Word, MS Excel, MS Power Point, MS Outlook, MFG Pro
32
Paint Operations Manufacturing Manager M Resume Examples & Samples
- At least 5 years management or leadership experience required
- Previous aerospace or manufacturing paint operations experience is highly desired
- Experience implementing Lean+ principles desired
- Bachelor’s degree desired
- Proficient with Microsoft Office programs
- This position must meet Export Control compliance requirements, therefore a “US Person” as defined by 22 C.F.R.120.15 is required
33
Manufacturing Manager Resume Examples & Samples
- This team consists of Flight Test Technicians who maintain aircraft in a flight ready configuration
- This position coordinates with multi-disciplined teams of instrumentation, requirements/analysis, data processing and design engineers during preparations for and execution of the flight test program
- The successful candidates will provide leadership and coordination with a variety of levels of personnel that includes Flight Test Operations Analysis, Test Support Operations (Instrumentation & Data Systems), and Flight Operations, Mission Systems, Flight Technology, Design, Program Management, vendors, USAF and foreign customers
- Coordination topics include test requirements, instrumentation system definition/installation, test assets and spares, aircraft modifications/de-modifications, ground test, flight readiness reviews, flight test and reporting
- The selected individuals will be responsible for programmatic, flightline operations and personnel aspects of test programs for the maintenance operations team
- These positions report directly to the senior manager of the F-15SA Maintenance/Flightline Operations in Palmdale, CA
- This position require extensive knowledge of military fighter aircraft test and evaluation requirements
- A strong working knowledge of USAF Technical Order compliance, F-15 ramp operations such as Preflight, Launch, Recovery, Postflight and execution of required maintenance to support the test program
- Candidates must have demonstrated ability to safely direct flight test teams and flightline operations
- These positions require excellent interpersonal skills and the ability to establish effective relationships within the team and with internal and external customers
- Candidates must have strong leadership skills and have a demonstrated broad-based technical/test background with experience leading a technical team on Air Force development and/or production programs
- Significant experience with ground/flight test instrumentation and data acquisition systems is desired and experience with Air Force test programs, is preferred
- Working knowledge of Program Management Best Practices such as Risk/Issue/Opportunity Management, Performance Metrics, Customer Communication, Requirements Management, Supplier Management, and Earned Value Management is desired
34
Manufacturing Manager Resume Examples & Samples
- Leadership and Teambuilding. Foster a success-oriented environment built upon mutual respect and trust
- Individual department and aggregated manufacturing performance to safety, quality, delivery and cost goals. Assist in developing, assessing, and timely reporting of all manufacturing performance drivers
- Resource planning, allocation and deployment. Create and maintain a robust, cross-trained network of supervisory and production personnel. Ensure that manufacturing capabilities, capacity and throughput align with customer needs
- Staffing deployment and development. Coaching and mentoring of production leadership staff. Practice and facilitate open, effective communication at all levels within manufacturing and across functional organizations
- Continuous Improvement. Sponsor and lead process improvement/optimization efforts and ensure sustainment of completed initiatives. Seek and embrace innovation in all manufacturing areas
- Daily execution within Esterline Operating System (EOS). Communicate and reinforce EOS through demonstrated commitment to the prescribed principles, tactics, and behaviors
- Ensure Compliance with EH&S, Trade Right, Ethics and Business Conduct, Quality Policy and all established operating procedures
- Escalate issues to Senior Management as required in an effective and timely manner
- Assist to establish annual department operating budgets. Monitor monthly budget performance and investigate variances. Oversee production efficiency and costs (labor, rework, and scrap) against budgetary commitments
- Provide input as necessary to secure Capital Equipment funding for manufacturing-related assets
- Assist with Customer readiness activities, capacity planning, and equipment/manpower utilization. Assist with strategic manufacturing planning and co-production relationships
- Represent TA Aerospace manufacturing at other Esterline sites, Customers, and Suppliers as necessary. Perform other development assignments as offered
- Coordinate effectively across organizational boundaries to resolve issues impacting our ability to meet delivery commitments, maintain compliance, and execute EOS
- Demonstrated leadership skills with emphasis on motivation, teambuilding, and employee development. Strong coaching and mentoring skills
- Solid core knowledge of Lean concepts and Continuous Improvement theory/techniques. Solid track record of proactively pursuing and sustaining successful Continuous Improvement activities
- Skilled in a variety of Root Cause assessment techniques and solid track record determining and implementing robust corrective action
- Highly proficient in Microsoft Office programs including Outlook, Word, Excel, and PowerPoint. Working familiarity with ERP/MRPII systems
- Must be able to work effectively with minimal supervision and multitask to manage routine tasks in addition to special projects
- Excellent responsiveness and customer focus in a fast-paced environment
- Demonstrated commitment to lifetime learning through reading, continuing education and/or acceptance of new assignments
- Approachability -Easy to talk to, able to put others at ease
- Directing Others -Sets direction, distributes work, lays out clear plans, is organized
- Interpersonal Savvy -Relates well to others and can build rapport across the organization
- Motivating Others -Empowers others, creates a climate in which people want to do their best, shares ownership and visibility
- Sizing Up People -Good judge of talent; sees the importance of effectively using each person’s strengths
- Organizing -Able to orchestrate effective use of all available resources
- Planning -Ability to develop schedules and task/people assignments
- Priority Setting -Able to quickly zero in on the critical few leaving the trivial many
- Building Effective teams -Knows when and how to use teams and uses them effectively
- Managerial Courage -Takes appropriate action when necessary; faces up to problem people or situations
- Fairness to Direct Reports -Treats employees as adults and maintains equitable relationships
- Drive for Results -Reliable performer who can be counted on to achieve consistent results
- Bachelor’s degree in a related field or equivalent combination of education and experience
- 8 – 10 years progressive production management experience in a manufacturing environment. Aerospace experience is a plus
- Excellent English written and verbal communication skills. Solid presentation skills. Bilingual in Spanish is a plus
35
Manufacturing Manager Resume Examples & Samples
- Oversee the planning, scheduling, and management of manufacturing operations to achieve business, safety, quality, and financial objectives
- Act as the primary contact for high level manufacturing activities and oversee progress planning and review sessions to discuss schedule and cost
- Ensure all operations are monitored for regulatory and safety compliance
- Ensure a proactive approach to continuous improvement and oversee the implementation of lean principles
- Oversee production schedules based on product introduction, equipment efficiency, and materials supply
- Identify manufacturing issues and provide leadership in developing solutions
- Ensure manufacturing leadership and excellence is maintained by overseeing the planning, attraction, selection, retention, and development of the required management, professional, and technical talent
- Provide high level manufacturing expertise to the development of new and expansion of existing business opportunities to enhance the capabilities of the organization
- Typically requires a Bachelors degree in business administration, engineering or a related discipline and fifteen or more years of progressively complex manufacturing experience with at least eleven of those years managing manufacturing operations
- Must possess the ability to resolve unusually complex management and technical problems
36
Manufacturing Manager Avionics Assemblies Resume Examples & Samples
- Coordinate the planning, scheduling, and activities of manufacturing operations to achieve business, safety, quality, and financial objectives
- Act as the primary contact for manufacturing activities and participate in progress planning and review sessions to discuss schedule and cost
- Manage the avionics assembly and test operations
- Monitor all operations for regulatory and safety compliance
- Take a proactive approach to continuous improvement and implement lean principles
- Prioritize production schedules based on product introduction, equipment efficiency, and materials supply
- Ensure machinery, equipment, and tools are well maintained
- Pro-active on capacity issues, ensuring manpower and equipment are available to meet production needs
- Provide guidance to engineering regarding design concepts and specification requirements that best utilize the facilities equipment and manufacturing techniques
- Ensure manufacturing leadership and excellence is maintained by participating in the planning, attraction, selection, retention, and development of the required management, professional, and technical talent
- Provide manufacturing expertise to the development of new and expansion of existing business opportunities to enhance the capabilities of the organization
- Maintain the strict confidentiality of sensitive information
- Responsible for ensuring all laws, regulations and other applicable obligations are observed wherever and whenever business is conducted on behalf of the Company. Responsible for ensuring work is accomplished in a safe manner in accordance with established operating procedures and practices
- Typically requires a Bachelors degree in business administration, engineering or a related discipline and eleven or more years of progressively complex manufacturing experience with at least five of those years managing manufacturing operations. May substitute equivalent experience in lieu of education
- Must possess the ability to resolve unusually complex management and technical problems. Strong communication, leadership, presentation, and interpersonal skills are required. Customer focused, must be able to work on a self-initiated basis and in a team environment and able to work extended hours as required
37
Manufacturing Manager Resume Examples & Samples
- Using available resources manage the production output of the area to achieve quality, safety, service and cost requirements for both internal and external customers
- Promote a learning organization that embraces continuous improvement and leverages the talent of the organization to achieve its business objectives
- Champion Operational Excellence culture by ensuring Lean Six Sigma deployment develop an automation roadmap to deliver an efficient operational area
- Use headcount models to ensure area is adequately resourced and employees have the correct skills mix, are fully trained, motivated and empowered to achieve their objectives
- Be a role model and encourage the companies Values ethos at all levels in the organization
- Lead the preparation of annual budgets (including capacity planning) / monthly projections and ensure area operates within budget
- Meet New product and process introduction requirements. Lead future state production capacity planning
- Manage large scale projects and/or guide successful completion of major programs
- Ensure continual Quality System compliance by adherence to established and regulatory QS requirements
- Experience of organising and directing a team of Production Supervisors and Production Support staff
- Motivational, leadership and managerial skills gained through working in a large operational area
- Demonstrated Project management experience
- Lean Six Sigma Qualification, Black Belt preferred
- Knowledge of ISO/GMP requirements and FDA Medical Device Regulatory requirements
- Communication skills and decision making ability
38
Manufacturing Manager Resume Examples & Samples
- Ensures safety of employees by proactively identifying safety concerns and resolving open incidents in a timely manner
- Primary point of contact for all manufacturing issues within the value stream
- Engages with value stream peers and takes responsibility for ensuring team meets business goals (Safety/Quality/Delivery/Cost/Morale/Environment)
- Monitor productivity and ensure that staffing levels are appropriate to support the manufacturing plan
- Complete all Manufacturing Manager standard work duties
- Conduct regular and ongoing team meetings
- Share best practices with other Manufacturing Managers across value streams
- Ensure consistency of operations practices across the value stream
- Possess strong understanding of how components are manufactured in assigned value stream
- Responsible for ensuring all Assemblers understand and follow GMP
- Accountable for implementing GMP (good manufacturing practices)
- Participate in GMP manufacturing assessments in the value stream
- Drive a Quality focused culture by monitoring compliance to Quality System processes, such as system transaction compliance (i.e. FACTORYworks), documentation practices, non-conforming material, product holds, Line Clearance, etc
- Oversee timely resolution of PRB and FACTORYworks holds within the value stream
- Actively participate in quality and improvement activities including Lean Sigma projects
- Manage and deliver the Performance Acceleration process for all direct reports
- Provide coaching and mentoring to production leadership team, resulting in increased employee engagement and productivity
- Actively promote a positive environment that is focused on quality, compliance, and employee development
- Bachelor’s degree from an accredited college or university
- 3 years minimum of operations, engineering, or manufacturing exp
- Experience with processes such as Quality Systems documentation protocols
- Project mgmt experience
- Demonstrated Computer use
39
Manufacturing Manager Resume Examples & Samples
- 5+ years of experience in manufacturing management
- Medical Device experience required
- Knowledge of Good Manufacturing Practices (GMP) and applicable Quality System and Regulatory requirements
- Knowledge of Financial metrics and interactions
- Advanced skills in MS Office and statistical software packages (Minitab etc.)
- Ability to support multiple projects and balance priorities
- Excellent oral/written communication and platform skills
40
Manufacturing Manager Resume Examples & Samples
- Define and implement improvement projects aligned with business strategies
- Collaborate for effective solutions with other functions and departments
- Coordinate continuous improvement programs to ensure vertical and horizontal integration across organization
- Help leadership team progress in support of Standard Factory, Policy Deployment, Macro Plan, and ACE (Production System) Criteria by coordinating actions to ensure improvement
- Implement/lead Lean Transformation events and follow up action closure
- Roll up and monitoring of metrics and reporting to SBU and segment leadership
- Work with leaders to coach employees on improvement tools and their application
- Prepare, participate, and co-lead in site certification assessments and coordinate homework action closure for site
- Comply with the EH&S Policy and applicable regulatory and company EH&S rules and requirements
- Report to supervision conditions or practices that are either unsafe or that may adversely impact the environment, to ensure prompt resolution of potential hazards
- Recommend improved EH&S practices
41
Manufacturing Manager Resume Examples & Samples
- Responsible for the safety of all employees on factory floor
- Achieve production targets for all machines under supervision
- To achieve budget costings annually
- To liaise with the Works and QE Managers on all technical issues relevant to the manufacturing process and on process / product development related issues
- To prepare reports on production performance as required
- Liaise with the Works & Maintenance Managers in relation to capital projects
- Engineering degree or similar/related degree
- Have previous experience in departmental/resource management
- Six Sigma training
- 5S Methodology
42
Manufacturing Manager / Senior Manager Resume Examples & Samples
- Responsible for directing and coordinating one or more of the following areas; formulation preparation, spray-drying, aseptic filling and assembly, component assembly, injection molding, and component washing and sterilization
- Leads cross-functional team to manage and coordinate activities and performance of assigned staff to ensure the achievement of department objectives and performance goals
- Develops department employees through orientation, training, establishment of objectives, communication of rules and policies, while building employee morale and motivation
- Establishes and administers operational procedures for one or more of the following areas; formulation preparation, spray-drying, aseptic filling and assembly, component assembly, injection molding, and component washing and sterilization
- Assumes responsibility for proper maintenance of production equipment and GMP facilities
- Ensure manufacturing facilities and staff are cGMP inspection-ready at all times
- Takes necessary action to eliminate delays ensuring adherence to production and shipping schedules
- Provides reports concerning scheduling, production goals, equipment and maintenance problems and other studies or reports as requested
- Works in a team environment with other department management to coordinate a production schedule to achieve required deadlines, objectives and budgets
- Maintains compliance with company policies, cGMP’s, safety standards, and good housekeeping practices
- Conducts continuous review and follow-up on projects to ensure completion of assigned work
- Advises department management on matters relating to daily operations and makes recommendations for improvements when feasible
- Ensures adequate resources are available to manufacture product (equipment, supplies, and labor)
- Bachelors degree required: Engineering, Chemistry, or Biology Degree preferred
- Minimum five (5) years supervisory experience, in the pharmaceutical or medical device industry. Knowledge of sterilization and aseptic processes preferred
- Ability to lead cross-functional teams to manage the day-to-day business and deliver continuous improvement initiatives
- Excellent computer skills; Word, Powerpoint, Excel, and Database programs
- Proven leadership skills in managing matrix teams, influencing outcomes and key project decisions, and strategic problem-solving ability
- Demonstrated ability to clearly and concisely communicate/ prepare presentations for management
- Strong troubleshooting and technical skills
43
Senior Manufacturing Manager, Operations Resume Examples & Samples
- 8-10 years of experience in a cGXP environment
- 2-5 years of experience leading direct reports or teams
- Extended experience in Equipment Preparation, Cell Culture and Purification operations
- Experience working with cross-functional teams, including Quality, Manufacturing Technical Support, Facilities and Engineering and Validation
- Strong documentation practices including batch production records, SOP, OJT’s and other controlled documents
- Experienced leading the implementation of improvements to technical and business processes
44
Manufacturing Manager Resume Examples & Samples
- Manage plant assets, personnel and achievement of plant related business goals. The role delivers plant based business, technical and administrative leadership to an empowered plant organization
- Leads the Support and Focus for a Manufacturing facility
- Ensures an effective HSE program is in place to achieve HSE goals and compliance with regulatory requirements. Demonstrates a strong commitment to HSE compliance and continuous improvement
- Represents the plant in the business strategy development and goal setting process (operational costs, utilization, quality, reliability, etc.)
- Translates and communicates the business strategy to plant personnel. Provides leadership, coaching and expectations for setting plant, team and individual goals that are aligned with site and business strategy. Assures that budgets are aligned
- Creates an environment that fosters team and individual empowerment. Establishes and models expected behaviors
- Ensures implementation and ongoing effectiveness of global work processes, operating discipline, HOS management systems and roles
- Ensures necessary resources and utilities are available to meet production requirements and achieve plant specific business goals
- Ensures systems are in place to reduce variation, product quality products and meet customer needs. Interfaces with customers
- Provides administrative leadership and coaching to plant personnel and crisis response leaders (employee development, compensation, recognition systems, role clarity, expectations, etc.)
- Ensures the linkages between plant operations and other functions are effective (maintenance, laboratory, safety, IT, etc.)
- Assumes aspects of site leadership, integration responsibilities and other roles
- Provides technical leadership for products and processes at the Shreveport Plant and elsewhere in Honeywell UOP as needed
- Develops, manages, and is accountable for department budget and expenditures
- Includes direct reports of ~ 20 hourly, and 5 technical resources with indirect leadership of maintenance and process engineering personnel
- B.S. Chemical Engineering, Mechanical Engineering or equivalent degree
- Minimum 7 years experience in a manufacturing operations environment
- 5 years experience in a supervisory position
- Experience in operations management with focus on leading HSE, Quality, Production and Cost targets
- Previous experience and a production and or a process engineering role for a chemical manufacturing operation
- Operations experience with change management and driving a high performance team to meet business objectives
- Operations experience with capital projects, commissioning, and safe startups
- Experience with training operators and technical roles, including training manual and SOP development
- Experience with developing training programs, manuals and procedures
- Proven leadership skills as a team player/builder and a driver of value-added results
- Demonstrated commitment to HSE and Quality performance and continuous improvement
- Proficient Demonstrated experience with with root cause analysis, PHAs, process improvements,
- Demonstrated experience with ISO 9001 and RC 14001 programs
- Experienced in conflict resolution and team facilitation
- Organized and ability to manage multiple priorities for self and team toward the business objectives
45
Manufacturing Manager Resume Examples & Samples
- Modeling the personal and organizational leadership needed to deliver an effective safety process, ensuring safe work performance of production and shipping employees
- Ensuring the effective performance of production and shipping operations, including safety, quality, delivery and cost
- Promoting continuous improvement, including implementation of MDI disciplines
- Tracking plant and department performance, identifying areas for improvement, and implementing actions to improve performance
- Effectively managing and developing salaried and hourly personnel
- Promoting a positive work environment through strong leadership, employee relations, and conflict resolution skills
- Assisting in managing the plant budget, capital improvement projects and executing Hoshin productivity and continuous improvement projects
- Participating as a member of plant leadership teams, including the Safety Leadership Team and Lean Steering Committee
- Previous leadership experience in a Union workforce environment
- 10+ years of manufacturing experience with at least 5 years in a management role
- Successful track record in safety leadership and achievement of plant operational goals
- Demonstrated knowledge, understanding, and implementation of process improvement methodologies
- Lean and/or Six Sigma problem solving training
- Experience driving and supporting innovative manufacturing and maintenance systems
- Experience supporting and implementing organization development and HR initiatives
- Business knowledge of budget, asset and cost structure management
- Experience & track record of implementing and sustaining 5S practices
- Kaizen event training / experience
46
Manufacturing Manager Resume Examples & Samples
- Lead a team of approximately 50-60 employees to effectively carry out production operations and meet production schedules while maintaining product quality
- Ensures that safety standards are followed and safety remains top priority in all we do
- Lead / drive change using Lean Manufacturing techniques and TE Operating Advantage (TEOA) tools and initiatives
- Engage in continual process improvement and cost reduction projects
- Perform various administrative tasks such as training, resolving customer complaints, holding weekly communication meetings with associates and awareness of team goals
- Prepares employee job performance evaluations and conducts reviews
- Provides career counselling and training plans
- Administers company policies concerning hiring, promotions, disciplining and other related areas requiring guidance in conjunction with the plant manager and human resources
- Aptitude to drive the extended value stream success within the Landisville plant and with key external stakeholders
- Ability to think strategically and execute tactically (i.e. deliver results)
47
Manufacturing Manager Resume Examples & Samples
- Ensuring the effective performance of production and maintenance operations, including safety, quality, delivery and cost
- Promoting continuous improvement by developing and maintaining systems utilizing tools such as Lean, Six Sigma, etc
- Preparing and managing both annual production line budgets; Assisting in managing the plant budget and capital improvement projects
- Bachelor's degree in Engineering or equivalent field
- 10+ years manufacturing experience in a durable goods industry, with 5+ years in a management role
- Successful track record of achieving plant operational goals
- Demonstrated knowledge, understanding, and implementation of process improvement methodologies, including Lean and Six Sigma
- Experience driving and supporting innovative manufacturing systems
- Experience supporting and implementing organization development and human resources initiatives
- Must be able to complete the Ishihara test for color blindness and the Farnsworth-Munsell 100-hue color test
- Lean Certification
48
Manufacturing Manager / Production Manager Resume Examples & Samples
- At least 5 years manufacturing experience
- Knowledge of the cement manufacturing process
- Excellent people management skills
- Eingineering degree or similar
- Six Sigman
- Lean manufacturing
- SS Methodology
49
Lean Manufacturing Manager Resume Examples & Samples
- Support, train, mentor and coach plant leadership - Plant Manager, Steering Team, Site leadership inc./functions and Lean Specialists
- Support sites in Illinois, Ohio and Michigan
- Influence the Site HOS Leader and Lean Specialists on HOS principles, processes, and tools as defined in the Standard Implementation Framework
- In liaison with the HOS Team & Plant Leadership team, drive continuous improvement through the SIF implementation
- Partner with site to complete HOS maturity assessments and develop deployment plans & develop action plans to meet HOS maturity assessment phase criteria and develop deployment plans
- Share knowledge with other Lean Specialists and teams across Honeywell for support and continued update of latest HOS enhancements/updates utilizing benchmarking efforts to lead development of "Best-in-Class" operational practices
- Deploy tools, processes, and training needed to deploy the Standard Implementation Framework (SIF)
- Lead Projects, mentor and coach other sites and locations, as required, either at an implementation site or in preparation for eventual implementation with a focus on pre-implementation foundational work
- In liaison with the HOS Team & Plant Leadership team, drive continuous improvement following the SIF implementation
- Drive standardization and consistency of approach as we implement HOS throughout the site
- As required, drive supplier improvement
- Run events and rapid problem solving exercises and other learning events as detailed in the HOS specifications
- 5 + years in Lean experience with multiple cycles of learning is required
- Bachelor Degree on Industrial Engineering or Electronic Engineering is desirable
- 5+ years experience in manufacturing operations/ISC is required
- Bilingual 90% English
- An advanced technical or M.B.A. degree is highly desirable
- Green Belt certification is highly desirable
- Lean expert certification preferred (will train successful candidates if necessary). Experience with the Toyota Production System, Lean manufacturing, or similar operating systems preferred
- Experience as a Plant Manager or Operations Manager is preferred
- The successful candidate must demonstrate leadership skills, is a team player, has strong interpersonal skills, and a demonstrated record of driving results
- The candidate must be able to work independently across functions and at multiple levels
- Track record of driving solutions to assigned tasks utilizing a proactive approach to problem solving. Track record of achieving results in challenging assignments
- Demonstrated ability to lead change initiatives and drive process excellence. Demonstrated ability to make a significant change in a variety of environments, with multiple learning experiences
- Strong capability to coach and mentor plant leadership, including front line supervisors
- Strong success record of working in a matrix environment with a focus on building relationships and driving improvements
- Able to travel 75% of time as necessary to support HOS deployments and site readiness activities
- Excellent written and verbal communication and presentation skills, including presentation planning and delivery skills
- Strong organizational skills with project planning, program management expertise
50
Senior Manufacturing Manager Resume Examples & Samples
- Oversee and promote effective Health, Safety and Environmental programs and practices, ensuring that high standards of site safety compliance are established, met, and that facilities/grounds are maintained in accordance with relevant regulations, agency standards and fiscal considerations
- Develop and execute the Annual Operating Plan
- Management of Risk / Loss for the production process in Russia, with key focus on localization efforts with local supply base
- Management of customer relationship / experience, liaising with Customer Service team in Sofia
- Establish and implement standard manufacturing/materials practices and leadership standardize work by implementing and executing the Honeywell Operating System, HOS
- People management and LER management, Ensure Site is union free, Ensure PER (positive employee relationship) & LER (Labor employee Relationship) surveys are done on periodic basis and there is complete employee engagement. Coaching and mentoring of the key talent
- Manage capacity/schedules to achieve On Time Delivery, growth and productivity goals
- Ensures process and yield improvement is embedded into the factory culture and actions. Create a lean culture with engagement at all levels, helping to solve problems at lowest possible level. Focus on HOS and also ensure the initiatives like Cycle Time Reduction, PFEP (Plan for Every PART), BIQ (Built-in-Quality) to drive results for the business
- Drive culture change, accountability and continuous improvement mindset throughout the organization
- BS Degree in Engineering, Supply Chain Management or related field
- 10 years in ISC Leadership positions or related experience, including plant management experience
- Fluent in English and Russian - Excellent communication skills -both orally and in writing
- Business acumen including financial planning, budgeting and negotiation skills
- Experience of operating in a complex international/matrix organization, with relatively independent locations
- Able to effect change through results, leadership and influence
- Six Sigma qualification to at least Green Belt level
- Confidence and ability to build, develop, manage, energize, coach, and motivate teams and senior leaders within the organization. Builds high performing teams through talent hiring, development and performance management
- Proven history of achieving results despite challenges and barriers through utilization of Six Sigma / Lean continuous improvement systems, methodologies and tools
- Strong analytical and financial skills, ability to analyze data including financial and business performance information
- Demonstrated strong skills in change management, managing multiple sites, partnering with business management teams, and delivering corporate level reporting requirements
- Experience working with the end-to-end value stream including integration of the customer and supply bases into a holistic lean enterprise strategy
- Bias for action with ability to develop strategy, translate concepts and strategies into actionable plans, and achieve sustainable change and improvements through effective project management
- Integrative thinker with ability to apply creative solutions and make difficult decisions
51
Manufacturing Manager Resume Examples & Samples
- Advanced/ Fluent English
- Business acumen, vision & purpose and intellectual rigor
- Drive for results, change & adaptability and leveraging resources
- Managerial courage, holding self/others accountable and developing & motivating of direct reports
- Strong Interpersonal communication skills and professional presence
52
Assistant Manufacturing Manager Resume Examples & Samples
- Ensure 1st Shift production activities satisfy internal and external customer demands
- Maintain a safe, non-hazardous, non-threatening work environment
- Ensure compliance to strict quality standard
- Carry out and direct all production related activities in the most efficient manner per standard cost routings
- Support maintenance activities for production
- Scheduling of internal activities – daily, short term, and long term
- Train, motivate, and discipline employees as necessary on 1st Shift
- Perform annual performance reviews
- Responsible for shift hiring and staffing; must maintain adequate staffing and employee skill sets to achieve company objectives
- Enforces housekeeping and safety standards as defined by Permatex
- Must be able to utilize company ERP systems for material planning and inventory lot control purposes
- Must have experience with Microsoft Office 2013 (PowerPoint, Excel, Outlook, etc)
- Performs various other duties as required
53
Senior Manufacturing Manager Resume Examples & Samples
- Accountability for safety, quality, cost and throughput of the CMP pad conditioner operation
- Provide direction and prioritization to personnel regarding primarily production, manufacturing engineering, planning, procurement, and inventory control with influence on new product introduction, scale-up and quality
- Lead and/or participate in cross-functional teams to resolve customer issues, plan for business growth and drive process improvements
- Guide new product validation and qualification activities from development to high volume manufacturing
- Lead operations team planning and execution efforts for annual operating plans and long term manufacturing strategy
- Bachelor’s degree in Engineering, with an advanced degree in Business or Management and/or APICS certification preferred
- CMP or semiconductor experience and Lean/Six Sigma certification strongly preferred
- Demonstrated ability to establish organizational vision and direction coupled with execution on implementation with minimal oversight
54
Manufacturing Manager Resume Examples & Samples
- Responsible for overall capacity planning, scheduling and manufacturing of existing and newly developed products in areas of a Business Unit/Value Stream in compliance with all regulatory and QSR requirements in a cost effective manner and in accordance with planned budget
- Applies understanding of the correlation between SC metrics and customer service metrics to ensure relevance and business impact. Develops goals and objectives that support business plans and drives SC metrics and innovation goals
- Acts as a SME and leverages understanding of Industry leading best practices and connects with key stakeholders in order to gain support for deployment of business goals
- Fosters a work environment that leverages diverse perspectives, backgrounds and talent to generate innovative ideas or solutions. Accountable for pro-active people management and talent development. Sets the standards for performance assessment and feedback, effective communication, promoting positive morale and supporting employee involvement programs across assigned operations
- Responsible for Environment, Health, Safety and Sustainability performance to standards
- Ensure corrective actions for non-conformance issues identified by internal and external audits are implemented in accordance with Quality System requirements
- Foster a team environment within Business Unit/Value Stream and across the broader Manufacturing Site
- Drives timely and quality delivery to both internal and external customers and is accountable for project improvement activities, (ie., Lean and Process Excellence Initiatives, quality, cell development, new equipment start-ups, new product launch production plans)
- Personally uses Process Excellence tools effectively and creates a culture that ensures all levels in the department are using the tools along with metrics to improve the business
- Responsible for project leadership and implementation with impact on broad based departmental and organizational goals. Lead or actively participate on cross-functional Medical Device Supply chain and /or JJSC projects
- Establishes an inclusion environment conducive to support a diverse employee population
- Manages and drives improvement quality standards, resolves technical related issues and improves manufacturing procedures, processes, monitoring and measurement systems
- Fosters employee engagement through routine business unit/value stream meetings
- Analyzes root cause investigation outcomes to address quality and scrap issues and leads effective corrective actions for non-conformance issues identified by the quality system
- Ensures the maintenance of all production machinery by coordinating these functions as necessary with Facilities and Maintenance departments
- Collaborates with Engineering to forecast machinery, material and equipment needed to meet requirements of new and existing products. Continuously reviews and drives operation improvements with regards to production set up and layout of equipment and general work areas
- Promote and nurture the highest standards of professionalism, ethics and compliance, and actively support our compliance program-related initiatives and activities
- Knowledgeable and compliant with laws and policies that apply to one's job, and maintains the highest levels of professionalism, ethics and compliance at all times. Diligently participates in compliance programs
- Enforces employee compliance, including attendance at training programs, and promptly report any non-compliance in accordance with Business Code of Conduct
- Bachelor Degree in Engineering, Organizational Leadership or Business discipline is required
- Minimum of eight (8) years of experience in manufacturing or related operations is required with at least four (4) years of direct supervision of professional level employees required
- Demonstrated experience managing expense and capital budgets to business plans is required
- Proven track record with NCR process, CAPA and other quality system components is required
- Advanced understanding and working knowledge of Lean Six Sigma/Process Excellence Tools is required. Lean Six Sigma Training and/or Certification are preferred
- Demonstrated successful management of capacity planning including ERP and Manufacturing Processing Systems (MPS) is required
- Advanced PC experience using Windows and Microsoft Office software
- Demonstrated leadership capabilities to develop and drive talent development and supporting programs is required
- Ability to maneuver changing business environments, both internally and externally is required
- Ability to collaborate across functions and to influence and drive effective decision making is required
- Talent mindset / Change Agent is required
- Demonstrated strong project management skills are required; the ability to lead and facilitate project improvements is required
- Ability to effectively communicate and interface with all levels of management, and excellent written and verbal communication skills are required
- Based on site specific business needs
55
Manufacturing Manager Resume Examples & Samples
- Manages employees performing activities in multiple manufacturing disciplines. Develops and executes business plans, policies and procedures and develops organizational and technical strategies
- Acquires resources, provides technical management of suppliers and leads process improvements
- Develops and maintains relationships and partnerships with customers, stakeholders, peers, partners and direct reports
- Provides oversight and approval of technical approaches, products and processes
- Manages, develops and motivates employees
56
Manufacturing Manager Resume Examples & Samples
- Demonstrate decisive leadership skills with a relevant years of managerial experience
- Have experience of precision manufacturing processes, combined with relevant technical expertise and experience
- Have implemented lean manufacturing and continuous improvement techniques and proven track record in managing change within a manufacturing environment
- Bachelors Degree in Engineering, technical or other related discipline or an equivalent vocational/professional qualification
57
NPI Manufacturing Manager Resume Examples & Samples
- Drive early and on-going operations involvement to ensure new products are designed for manufacturability and propose alternative manufacturing approaches
- Working with Product Marketing and Engineering to embed and optimize best practices enabling more efficient operations and supply chain processes
- Lead operational team on mechanical and CMF advanced manufacturing study
- Interface with engineering teams on new and sustaining product process and value engineering improvements
- Develop NPI product value chain (make vs buy) and supply chain strategy
- Initiate, lead and drive CIP activities pertaining to lean manufacturing, cycle time, and process improvements
- Drive cross-functional teams to develop launch FMEA risk assessment and proactively manages mitigation and contingency plans
- Ensure NPI quality and supply chain readiness
- Represent operations on engineering, product marketing, and program management teams and facilitate crisis escalation
- Perform product teardown analysis to drive DfC, cost reduction CIP, and component cost benchmarking
- 8+ years of experience in high tech, consumer manufacturing environment including factory leadership experience
- A proven cross functional leader who has demonstrated the ability to influence across the organization
- Ability to promote change and innovation by developing creative manufacturing processes
- Design for Manufacturability expert with a proven track record of delivering improvements in efficiency, quality, costs, and product launch predictability
- Experience in FMEA and lean manufacturing tools
- Excellent verbal and written communication and facilitation skills
- BS/MS in Engineering, preferably Mechanical Engineering
- Fluent in Mandarin and English is required
58
Manufacturing Manager Resume Examples & Samples
- Prototyping Manufacturing Leadership Experience
- EVMS management exposure
- Experience on various types of aircraft and build assemblies
- Shop floor leadership experience
- LM21 certified (green/black belt)
- Program start-up experience
- Familiar with SFM/E4C execution systems
- Technical Degree (IE, ME, AE, etc...)
59
Manufacturing Manager Resume Examples & Samples
- To ensure the plant delivers its customer service, financial, energy management, quality and safety goals through the effective management of all activity in relevant manufacturing area
- To manage the resources in the assigned area so as to ensure targets are communicated and achieved while maintaining a harmonious employee relations climate
- Ensure Environmental Health and Safety standards are met and all EHS regulations and procedures are adhered to. Foster an awareness of Environmental Health and Safety in the plant and promote a culture of continuous improvement
- Carry out the responsibilities inherent in the position of a Manager in respect of Manufacturing Operations, including all aspects of safety, training, performance and people development
- Maintain GMP, HR, EHS, IT, financial and quality procedures and standards by encouraging an atmosphere of involvement, open communication and effective teamwork
- Motivate employees and build teams to foster culture of continuous improvement & “Right First Time”
- Ensure that all customer requirements are met and maintain product availability
- Ensure manufacturing department operates within agreed budgets
- Primary contact for new process transfers into the Manufacturing Area
- Implement and monitor new manufacturing strategies
- Liaise with the relevant Quality & Technical groups to identify, document, investigate and remedy the cause of product or process non-conformance
- Keep abreast of developments in manufacturing areas to ensure the plant continues to produce quality products while maintaining regulatory compliance
- Responsible for EHS performance and compliance through active participation and support of Abbott's EHS Program
- Recommend/Implement improvements to Safety standards and foster continuous improvement culture to safety
- Optimize the use of human resources by encouraging an atmosphere of involvement, open communication and effective teamwork
- The minimum education requirement is a Third level qualification in a Science/Engineering related discipline
- Ideally minimum of 5 years previous management experience in an operational excellence/ Total Quality Management environment
- Knowledge of GMP requirements in healthcare/pharmaceutical plant is desirable as would give understanding of requirements of the medical industry
60
Senior Manufacturing Manager Resume Examples & Samples
- Develop and execute a robust transition & operational start up plan to move manufacturing capability from current location into this new facility
- Partner with project and industrialization managers to prioritize transfer of products to this state of the art facility to manage ongoing delivery to the customer
- Champion new manufacturing philosophies to drive productivity and yield improvements
- Build robust operations strategies and governance to ensure maximum utilization of all new equipment and technologies
- Lead a team of circa 100 hourly and professional employees
- Create and drive a refreshed approach to training in order to accelerate adoption of new technologies
- Implement the right organizational structures, training plans and operational rhythms which establish this facility as a centre of excellence for the composites work stream on site
- Drive effective use of data generated through the ‘brilliant factory’ concepts which have been deployed within the facility
- Communicate with customers to ensure that all commitments are met or exceeded, working with them as well as functional leaders, and internal staff to meet production and product support requirements
- Champion Lean Six Sigma throughout the product area(s) to maximize improvement activities and opportunities. Direct process / product improvement programs and provide process method excellence throughout the product area(s)
- Provide overall manufacturing area leadership in the achievement of goals with respect to EHS, Quality, Production, Manpower and Compliance
- Provide leadership in the areas of staff selection, training and development, facility planning and construction, process, and procedure implementation
- Lead and coach Operations Managers, guiding them in current positions and assisting with career development and training
- Use scenario planning and other contemporary methods to drive market leadership and stay ahead of the competition
- Partner with external stakeholders to shape future outcomes and create mutually beneficial solutions
- Leverage industry relationships to provide information to customers about the industry, their competitors and their customers to create opportunities for GE
- Successful and extensive proven experience in Operations Management within a complex engineering environment
- Proven ability to develop and motivate a high-involvement team through commitment to meeting customer and organisation demands
- Comprehensive knowledge of the disciplines of manufacturing management such as production and inventory control, and standard cost systems
- Knowledge of manufacturing policies and regulations established by both business and government, regulatory agencies and other customers
61
Manufacturing Manager Resume Examples & Samples
- Have a strong understanding of the fundamentals of continuous improvement
- Six Sigma experience and training preferred
- Capable of influencing and getting cooperation and action from others
- Ability to effectively communicate (verbal and written), work and relate with people at all levels of the organization and be self-sufficient
- Ability to handle nebulous situations, with minimal guidance, effectively
- Effective team player, good coaching skills and can develop other co-workers
- Ability to encourage and motivate others to be successful
- Knowledge of manufacturing ERP systems
- Cross functional experience in Engineering, Materials or other Manufacturing function
- Excellent knowledge of MS office computer software including MS Word, Excel, PowerPoint, and Outlook
- Able to use Minitab or other statistical software preferred
- Ability to multi-task, organize and prioritize
62
Manufacturing Manager Resume Examples & Samples
- 6+ years experience in leadership roles within a manufacturing environment
- Position is subject to the International Traffic in Arms Regulations (ITAR) which requires U.S. person status
- BA/BS in Business Administration or Engineering from an accredited institution
- Strong leadership skills that creates an engaged employee environment
- Able to drive improvement through the implementation of the lean manufacturing principles, total quality practices, six sigma
- Demonstrated results in leading manufacturing excellence
- A strong technical understanding of manufacturing processes
- Strong analytical, problem solving, communication, interpersonal, organizational and negotiation skills
- Strong financial literacy
- Experience with tooling, molds and dies relating to the Investment Casting, Injection Molding, or Stamping Industries is preferred
63
Manufacturing Manager Resume Examples & Samples
- 10+ years experience in leadership roles within a manufacturing environment
- BS/BA in Business Administration or Engineering from an accredited institution
- Based on experience, this could be filled as Job Band 35
64
Manufacturing Manager Resume Examples & Samples
- Manage resources within given areas of responsibility to ensure staffing and equipment readiness levels match business activity levels
- Track competencies of subordinates and provide leadership and development as required to achieve the objectives
- Assign work according to designated priorities in order to maintain scheduled completion dates and throughput targets
- Provide operational input and guidance to technical staff for new product development, process improvement and process capability
- Identify and execute cost savings initiatives that directly impact the daily Flex Cost metrics and are aligned with business and operations goals
- Read and interpret drawings, specifications, processes and complete attendant paperwork
- Prepare daily production reports, employee time sheets and maintain appropriate records
- Supervisory Responsibilities - Carry out supervisory responsibilities in accordance with the organization's policies and applicable laws. Responsibilities include interviewing, hiring, and training employees; planning, assigning, and directing work; appraising performance; rewarding and disciplining employees; addressing complaints and resolving issues
- Ensure area Supervisors are trained to drive continuous improvement through TPM and 5S with an open dialogue and a bias for action
- LANGUAGE SKILLS: Ability to read and interpret documents such as safety rules, operating and maintenance instructions and procedure manuals. Ability to write routine reports and correspondence. Ability to speak effectively before groups of employees, customers, and outside regulatory agencies
- MATHEMATICAL SKILLS: Ability to apply concepts of basic algebra, geometry, percentages circumference and volume
- REASONING ABILITY: Ability to solve practical problems and deal with a variety of variable in situations where standardization exists. Ability to interpret a variety of instructions furnished in written, oral, diagram, or schedule form
- Bachelor’s Degree in from an accredited college or university
- Minimum 5 years of management experience in manufacturing
- Bilingual Spanish/English strongly preferred
- 10+ years management experience in heavy industrial manufacturing
- Experience with heavy manufacturing equipment (maintenance, troubleshooting, or working with maintenance personnel)
- Experience in the forging or other metal working industry is preferred
- Experience with AS9100 standards
- Experience and proficiency with Microsoft Office Suite and MRP systems
65
Manufacturing Manager Resume Examples & Samples
- Plan, schedule, assign work, and ensure activities are in compliance with Company policies & procedures, and with codes & regulations
- Monitor product quality & customer relations and initiate responsive measures, as applicable
- Anticipate & introduce timely / effective actions to resolve problems
- Manage activities and initiate measures to ensure efficient operations while achieving long-term cost savings
- Maintain awareness of new developments & technologies, and direct subsequent investigations regarding their utilization
- Participate in meetings & conferences, and act as a spokesperson for the organization on highly significant matters
- Negotiate such matters as costs, design features, and schedules with suppliers & customers
- Advise senior managers regarding such matters as most effective means of complying with new contract stipulations and improving customer relations
- Provide guidance & arrange for training of staff
- Provide administrative support to senior managers and advise less-experienced supervisors regarding the more complex aspects of their assignments
- Manage / document employee performance and initiate responsive actions
- Requires broad knowledge of diverse operations & ability to independently resolve complex problems
- Requires ability to communicate effectively, act decisively and influence decisions of senior managers & customers
- Erroneous decisions or failure to properly manage activities may adversely impact schedules, cause unnecessary expenses and be detrimental to the organization's reputation & business prospects
- Requires foresight to anticipate problems & recognize opportunities for cost-effectively improving operations
- Bachelor's degree and 8 years’ manufacturing and/or maintenance experience; OR
- Master’s degree and 6 years’ manufacturing and/or maintenance experience
- Broad experience working in industrial manufacturing environments, especially with operations leadership responsibilities
- Experience working in unionized environments is a plus
- Knowledge & experience with Lean Manufacturing implementation; Six Sigma training & certifications are preferred
- Proven leadership expertise, especially with previous supervisory and/or managerial experience
- Strong interpersonal skills to achieve cooperation with others
66
In Vitro Diagnostics Manufacturing Manager Resume Examples & Samples
- Development and tracking of manufacturing plans for multiple in-vitro diagnostic products
- Coordination of manufacturing process development and validation as applicable
- Coordinate production of oligonucleotide primers, probes, and assay controls under a designated CDC Quality System and compliant with FDA regulations when applicable (e.g. IVD manufacture)
- Monitoring and tracking of products, inventory, and stability
- Interact daily with internal regulatory and quality teams
- Deliver verbal and written reports to internal and external groups
- Direct experience with manufacture of in vitro diagnostic devices employing real-time polymerase chain reaction (PCR) technology
- Experience working with government contracts and subcontractors a plus
67
Manufacturing Manager Resume Examples & Samples
- Bachelor's of Science from an accredited university
- Minimum of 5 years experience working in a manufacturing environment
- Minimum of 3 years in a leadership role with direct reports
- Masters degree from an accredited university
- 7+ years of experience working in a management position with direct reports
- 3+ years of experience with P&L
- Experience working within the aerospace industry
68
Biologics Manufacturing Manager Resume Examples & Samples
- Drives site schedule by prioritizing resources/activities for manufacturing and support functions. Erroneous decisions or failure to achieve results may have financial implications or cause delays in schedules
- Leads one or more operational groups, ensuing department goals and metrics are meeting or exceeding expectations
- Identifies deficiencies, creates and executes action plans to mitigate issues
- Is responsible for the performance of all reporting team members
- Takes an active role in developing less experienced Supervisors and Technical leads. This includes leveraging both internal and external relationships to build the best team possible
- Leads response to any developing issues and escalates as appropriate
- Initiates response team for critical issues, managing team progress and providing detailed Tier communication to senior management
- Ensures daily work coordination and distribution of work as demanded through the manufacturing schedule. Manage to schedule and plan
- Recognize impact for cross functional impact. Any variance to be captured and communicated to cross functional groups in real time
- Build partnership with Manufacturing Operational Engineer to ensure daily data review and trends accomplished
- Manage decisions– acquire feedback, input, and consult as required
- Manages performance. Provide coaching, mentoring and development of staff
- Conducts powerful conversations and provides meaningful and actionable feedback for staff growth and development. Executes all phases of the performance review process with diligence and on time
- Develops operational schedule in conjunction with scheduling and planning team. Drives increased scheduled adherence and cycle time
- Demonstrated ability to lead manufacturing operations teams to achieve objectives
- Acts to promote a productive and cooperative climate
- Helps to promote team effectiveness by engaging in a trusting, supportive partnership with others
- Encourages or facilitates a beneficial resolution of purpose
- Resolve conflicts in a constructive manner that allows win/win solution
- Demonstrated ability to prioritize and coordinate activities within and across work groups; able to anticipate priority differences and issues and resolves these before problems occur, exceeds desired results
- Participates in the budget development process; effectively controls the controllable expenses (OT, Supplies, T&E) within their influence
- Develops stretch goals and uses effective motivation techniques to achieve them. Strong team diagnostic skill and strategy for team growth
- Shapes site goals and policies
- Able to effectively lead cross functional teams
- Provides shift continuity by attending the daily scheduling and triage meetings
- Attends active maintenance, frozen schedule, and IEF meetings as a standing member
- Owns and executes Ideas bank
- Provides direct audit support
- Acts as a consultant to project teams
- Provides on call support for the manufacturing team including active participation on the weekend calls
- Direct biologic manufacturing experience of 8+ years with minimum of 3+ years of previous supervisory experience which demonstrates proficiency in selection of team and effectively managing personnel issues is required
- Mastery of SOPs and cGMPs and the know–how to work and manage within a regulatory environment
- Extensive knowledge of pharmaceutical and biopharmaceutical manufacturing process with a proven record in pharmaceutical technology, technology transfer, process development, manufacturing support
- Previous cross-functional supervisory experience which demonstrates proficiency in selection, motivating and retaining a superior team, effectively managing personnel issues and planning and administering financial resources
- Effective communication and technical writing skills with support groups in the coordinating system to obtain needed cooperation and support as required in a timely and effectively manner
- 1604429
69
Senior Manufacturing Manager Resume Examples & Samples
- Ensure continuous business improvement according to benchmarks and standards
- Works on very complex technological issues or manufacturing processes
- Solving issues and developing new solutions requires new and innovative approaches
- Has the authority to guide others in different approaches
- Presents to top leadership in the business solutions (SEB, Sr.VP) on technical discipline and business solutions
- Works with cross business teams
- Is considered a subject matter expert
- Elaborates proposals for important technological choices, defines methodologies to solve issues and provide guidelines for projects
- A minimum of 5 additional years of experience in Operation Management
70
Manufacturing Manager Resume Examples & Samples
- Under General Direction and in accordance with all applicable federal, state and local laws/regulations and Corporate Johnson & Johnson, procedures and guidelines, this position
- Reviews production schedules and coordinates manufacturing resources to ensure timely delivery of products and components, while be sure to comply with Quality System requirements
- Interacts and collaborates with other departments to solve any restriction that may stop or slow down production, including material, personnel, equipment and process issues
- Responsible for planning budget and control expenses applicable to production area to comply or exceed Business Unit financial targets
- Identifies and coordinates cost reduction projects including labor productivity, land use, inventory optimization and defects reduction, using Lean Manufacturing and Six Sigma tools
- Coordinates research and implementation of preventive and corrective actions that may result from production non-conformances, audit observations, CAPA and others
- Ensures to comply with QSR, ISO and Environment, HS requirements, as well as all applicable company procedures and policies
- Provides timely and effective support for new products introduction and existent process transferences to Business Unit
- Develops and maintains department metrics to monitor performance and coordinates actions to ensure improvements
- Manages employee development and maintains updated and verified training records
- Recognizes and rewards performance and teamwork
- Identifies supports and solves labor issues in coordination with Human Resources Department
- Responsible for communicating business related issues or opportunities to next management level
- Responsible for ensuring subordinates follow all Company guidelines related to Health, Safety and Environmental practices and that all resources needed to do so are available and in good condition
- Responsible for ensuring personal and Company compliance with all Federal, State, local and Company regulations, policies, and procedures
- Performs other duties assigned as needed
- BS in Engineering or Business Administration
- Master Degree is desirable
- Green Belt / Black Belt Certification, Lean Manufacturing Certification, Six Sigma is desirable
- 5 years minimum Manufacturing experience preferably
- Medical industry experience preferably
- Knowledge of the requirements of Quality Systems such as ISO and QSR
- Ability to identify Improvement opportunities and Implement World Class Manufacturing practices, including Lean Manufacturing, Six Sigma and ME2 concepts
- Excellent written and oral English and Spanish communication skills for different organizational levels
- Knowledge for Operations Management, including resources, capacity planning and Project Management
- Knowledge of Financial concepts applied to Manufacture, including budgets and cost control
- Teamwork and collaboration skills.preferentemente
71
Manufacturing Manager Resume Examples & Samples
- University degree in Business, Engineering or food science
- 6 plus years of experience in Manufacturing or Research and Development, Food or Consumer Goods industry experience would be considered an asset
- Proven Project management experience, minimum 3 years
- Experience and knowledge of Lean Six Sigma tools and Continuous Improvement methodology
- Strong people management skills, managerial experience as we as leading without direct influence
- Excellent communication and interpersonal skills, working cross functionally across the business
- Superior analytical and conceptual skills
- Strong presentation and facilitation skills and exposure to senior management
- Willingness to travel based on business requirements, anywhere between 20-25% within Canada and the US
72
Senior External Manufacturing Manager, Russia Resume Examples & Samples
- Develop identified External Manufactures through identification of their needs and implementation of continuous improvement initiatives in the scope and in alignment with the defined Sourcing Strategies
- Manage and develop medium and long-term supplier capability and capacity overview
- Lead cross-functional groups and activities to solve issues to support the operational aspects of product supply on a local, regional and worldwide basis
- Implement for key suppliers best practice on SRM (Supplier Relationship Management) approach and drive improvement and alignment internally with key functions (Q&C, Planning, etc.)
- Identify and implement Continuous Improvement opportunities that will ultimately drive price competitiveness – focus on process simplification and operational efficiency improvement
- Control budget and manage spending of non-standard costs from projects and change controls with contract manufactures
- Leads periodically business reviews with Contract Manufacturers in partnership with the Sourcing Manager, Quality & Compliance and Planning
- Run data analysis in the scope of medium-term capacity planning and performance management with Contract Manufactures
- Coordinates / supports NPI/ NPD roll outs/ reformulations/ packaging & artworks changes/ technical transfers at External Manufacturing sites and deliver against established timelines, forecasted volumes and costs
- Coordinate / lead efficient implementation of new Supply Chain with new External Manufacturing sites / Inbound Logistics and / or new markets
- Bachelor Degree in Science, Engineering, or commerce with equivalent technical experience
- 5 years + of experience in Pharmaceutical or FMCG industry with OTC products
- Experience in any of the following areas: Supply Chain, Production, Engineering, Quality, R&D and Project Management
- Knowledge of general manufacturing principles and practices
- Fluent level of English and Russian
- Strong project management and communication skillsContract Manufacturing
73
Manufacturing Manager Resume Examples & Samples
- Support Operations Managers in achieving value stream SIOP goals for quality, cost, delivery, inventory, Safety Health and Environment (SHE), Defective Parts per Million (DPPM), Gross Margins (GM), Overall People Effectiveness (OPE) and On Time To Promise delivery (OTTP)
- Participate in value stream meetings focused on driving improvements to include the completion of improvement project work (SOF Tips)
- Develop budgetary plans on a yearly basis for the Manufacturing floor team
- Provide leadership for all manufacturing personnel, including responsibility of training and employee development for all manufacturing personnel
- Achieve a flexible workforce and maintain headcount, OT budget, technical competencies, and work policy compliance
- Drive company 5S and Safety, Health and Environment (SHE) compliance
- Ensure all operational processes are carried out in compliance with the Certified Operator System within the Systems and Procedures
- Contribute to monthly strategy deployment sessions in support of Value Streams and supply chain
- Assist and support business strategy and organizational transformation by seeking out best practices
- Actively participate in facilities management when required
- Seek out and implement best practices for material storage and movement
- Coach and mentor the Manufacturing leaders
- Develop a culture of visual management and maintain the cleanliness of the manufacturing floor areas
- Responsible for the ownership, coordination, and performance of the support areas: Mold room, model shop, spring room, lapping, solder/braze, aneroids, weld room, calibration, clean room
- Responsible for ensuring that Safety, Health, and Environment are included as part of everyday activities
- Demonstrated career progression in a manufacturing operations organization
- Ability to think strategically and develop operational plans
- Thorough working knowledge of Lean Six Sigma enterprise
- Excellent organizational, communication, and leadership skills
- Ability to lead and facilitate progressive change
- Ability to deal effectively with all levels of management and manufacturing personnel
74
Manufacturing Manager Resume Examples & Samples
- Work experience in a nuclear facility - please specify experience working in a nuclear facility
- Working knowledge of the TA-55/PF-4 safety and authorization basis requirements
- Working knowledge of existing NNSA/DOE requirements related to nuclear and high hazard facility operations
- Experience managing budget preparations, schedule development, and project tracking using resource loaded schedules and earned value management processes
- Knowledge of continuous improvement concepts and tools
- Knowledge of Laboratory programs with special emphasis on programs related to the MET-1 and TA-55 programmatic missions
- Knowledge of Classified Matter Protection and Control, Cyber Security, HRP Certification and Security Clearance responsibilities
- 2:This position is subject to DOE Order 426.2, Personnel Selection, Training, and Qualification Requirements for DOE Nuclear Facilities, which establishes entry-level requirements to ensure candidates selected for specific positions can successfully perform the requirements of the job
75
Manufacturing Manager Resume Examples & Samples
- OMLP Graduated only for GE employees
- English skills, written/spoken
- Union relations experience preferred
76
Manufacturing Manager Resume Examples & Samples
- Define the production strategy to organize and lead the conversion processes to ensure the fulfillment of the production plans and the Company strategy
- Prepare, follow up and control the budget, the action plans and continuous improvement programs, productivity increase and cost reduction
- Ensure and guarantee the implementation and fulfilment of the Quality Systems, Security and Environment Programs; aligned with Corporate policies and guidelines. Support zero accident initiatives
- Coach, train and evaluate the staff: Develop staff’s abilities and competencies according to their responsibilities, focusing on team work and development of ideas
- Lead, co-ordinate and control the projects of the new design and new products according to the Business Unit’s strategies
- Achieve the lowest imaginable cost and top and quality in all manufactured products
- Accomplish with international and mandatories standards (FSSC 22000 / ISO 9000/ISO 14000)
- Ensure that all quality and Food Safety Systems and safety regulations are in place, monitored, and followed by corrective actions
- Identify all area´s environmental aspects and its impact on it
- Identify and assess all health risks and dangers for their area
- Make sure all documents are up to date on their points of use
- Responsible for the Operational Control on health risks and environmental aspects and its impact on each area along with all needed measures
- Research all non-Conformities, incidents and accidents and adopt all corrective and/or preventive measures needed regarding SSE
- Autonomous maintenance pillar leadership
- Manufacture experience in multinational companies (Min 5 years)
- Bachelor Degree, MBA preferred
- Handling and application off WCM / TPM / LEAN manufacture
- Knowledge in international standards: OHSAS 18001 / HACCP/GMP/FSSC 22000 /ISO9000/14000
- Ability to manage multiple and diverse stakeholders
- General technical expertise in Manufacture, HS&E, Quality, Food defense, IL6S, RR.LL., KPI manage
- Advance English required
- Portuguese speaker preferred
77
Focus Improvement Manufacturing Manager for Nestle Purina Emena Resume Examples & Samples
- Govern the GAFI pillar within Purina Network on behalf of the Purina EMENA Management Team
- Apply Management Routines of GAFI pillar at Purina EMENA level (FI Governance) in synchronization within the different markets/Factories
- Ensure consistency and compliance with the GAFI Reference Guide
- Deploy the Focused Improvement Pillar with GA principles across the Zone / Business (apply the GAFI main roles: methodology, training, coaching)
- Train and coach the Factory GA - FI Pillar leaders on the methodologies (OMP, Measures, OR, Cascading of Objectives into Projects, Loss Tree Analysis, DMAIC, SMED...)
- As part of Management routines, carry out visits to Factories to check adherence to FI methodology, provide support, create alignment, and review the FI drivers & actions with the Factory FI pillar leader (with synchronization with Nim if support Exist)
- Check / assess the progress of the implementation within the markets
- Lead /Assess the Factory FI pillars in terms of their maturity with FI methodology with the consultancy support an Nim support
- Competencies in DMAIC methodology (at least Green Belt certified)
- Minimum 4 years leading 6 Sigma/DMAIC projects. Coaching DMAIC project
- Previous leadership experience (managing people; leading project teams)
- Minimum 4 years in an operational function
- Significant experience in project management
- High flexibility to travel across European countries
- Bachelor Degree (2 year or higher)
- Advanced English Skills
78
Manufacturing Manager Resume Examples & Samples
- Manages production operation and work to meet production goals
- Establishes department policy and operations guidelines and maintains a regular communication and engagement approach with the team
- Plans production flow, troubleshoots manufacturing issues, and monitors production orders and schedules
- Analyzes production and operating reports and resolves operational, manufacturing, and maintenance problems to ensure minimum costs and to prevent operational delays
- Works closely with plant personnel in the areas of safety and quality
- To develop programs within these areas, ensure the plant is in compliance with the standards and establish training requirements for all employees
- Create and revise standard operational and working practices and observe employees to ensure compliance
- Establish and monitor operational budget for manufacturing
- Monitor Overall Equipment Efficiency & LEAN Practices
- Collaborate with maintenance department to evaluate reoccurring issues that may require equipment replacement
- Handle all aspects of managing wage associates including hiring and termination. Provides coaching and development opportunities to staff. Evaluates performance and provides feedback. Implements disciplinary actions as necessary
- Ensures the Quality System is regularly audited/ reviewed and that appropriate preventive and corrective actions are identified and executed to improve quality results
- Ensures fulfillment of all safety, industrial hygiene, environmental and labor regulatory requirements
- Work closely with sub-ordinates to develop their goals & objectives
- Mentor direct reports and provide leadership for advancing Credo behaviours for maintaining a healthy Industrial Relations Climate
- Review the regulatory laws and how they are being followed within the manufacturing setup. Ensure compliance to regulatory requirement in the shop floor and submission of necessary documents on time
- Work with people leaders to develop consistent, reliable practices to deliver high quality, productive, safe workplace environments
- Establish a high performance and continuous improvement culture driven by key performance metrics, benchmarking and sharing of best practices
79
Senior Manufacturing Manager Resume Examples & Samples
- Bachelor's degree in Engineering, Physics, Chemistry, Mathematics, or Business OR High School Diploma / GED with a minimum of 4 years of industry experience and/or Grid Automation experience
- Minimum of 10 years of industry experience and/or Grid Automation experience
- Minimum of 5 additional years of experience in a Supply Chain, Manufacturing operations position
- Knowledge of manufacturing leadership disciplines including; production planning, inventory control, variable cost productivity, fulfillment metrics, quality and cost systems
- Proven mentoring and coaching skills, demonstrated ability to motivate & inspire others
- Ability to successfully maintain high morale, employee involvement, safety, and teamwork in mixed union and non-union environments
- Inclusive leadership style, proven ability to build a connection with the team through personal involvement and trust
- Trained in Lean principles with demonstrated ability to apply tools and process rigor
- Six sigma certification or equivalent Quality Certification
- Demonstrated ability to deliver results in a complex, global, unique and sometimes ambiguous environment
- Proven ability to prioritize, plan and execute important business and supply chain initiatives
- Demonstrated ability to influence and effectively communicate with all levels of the organization, including senior leadership
- Clear, strategic, and critical thinker; proven experience in translating strategies into actionable plans
80
Manufacturing Manager Resume Examples & Samples
- Be passionate about leading teams that manufacture state-of-the art implantable medical devices
- Have a proven track record of building and maintaining strong interpersonal relationships
- Responsible for manufacturability of new products in the development pipeline. Working with the Project Manager to ensure successful transition of products from development to commercialization
- Leading manufacturing associates involved in new product development activities
- Guiding the design team to translate product design outputs into process design inputs in order to develop manufacturing line layout, product flow, and determine required skills needed by the manufacturing operators
- Working with Project Manager, Value Stream Leaders and Supply Chain associates to determine and implement end-to-end value stream goals to minimize inventory and lead time
- Mentoring other leaders to expand operations expertise and grow knowledge of lean concepts
- Responsible for operational considerations for production scalability and launch readiness of new products
- Working with the development team and value stream leadership to determine product manufacturing charter goals and responsible for attainment of those goals at product launch
- Developing and sustaining Key Performance Indicators and driving discipline in measuring and maintaining them
- Minimum of 3 years’ demonstrated leadership experience
- Minimum of 5 years of experience in new product development with a proven ability to support new product development process and teams and a thorough understanding of product development life cycle
- Demonstrated use of Design for Manufacturing (DFM) skills including the use of FMEA, process flow concepts, ergonomics, error proofing tools and lean line design
- Hands-on experience working with quality assurance systems (i.e. ISO, cGMP)
- Demonstrated project management abilities
- Proven ability to manage multiple priorities
- Demonstrated effective verbal and written communication and computer (Microsoft Word, Excel, PowerPoint, etc.) skills
- Ability to develop and execute plans and consistently produce the desired results
- Demonstrated ability to fairly address performance issues, establish expectations, and hold others accountable to their expectations
- Bachelor's degree in Engineering or Operations Management
- Experience in a medical device or regulated manufacturing environment
- Lean/Six Sigma certification
- Experience leading performance review processes
81
Manufacturing Manager Resume Examples & Samples
- Define and control production process including tooling and equipment. Validate design specifications and shop floor application of new product, tools, or equipment. Includes Manufacturing Engineers
- Develops operational plan for the own department
- Bachelor's degree from an accredited university or college (or a high school diploma / GED with experience in Manufacturing). - or equivalent knowledge or experience
- Experience in Production Process and Equipment
- Lead initiatives of moderate scope and impact
- Proven analytical and organizational ability
82
Manufacturing Manager Resume Examples & Samples
- Leading proactive customer initiatives that prevent and/or resolve delivery and quality issues
- Promoting organizational behaviors that interface and engage growth and customer focus concepts
- Embracing and driving Honeywell Operating Systems, Six Sigma, Lean and standard work methodologies
- Establishing and maintaining effective two-way communications with salaried and hourly workforce
- Serving as a contributing member of the Pottsville Plant Leadership Team that effectively interacts with all plant and business functions
- Managing production to ensure all orders are manufactured to customer specifications and meet critical on-time delivery
- Setting and achieving attainment in aggressive cost, production and yield objectives
- Directing reports include Front Line Supervisors, Operation Coordinators, and Traffic/Distribution Supervisor
- Executing the manufacturing schedules based on information and requirements from management and customer
- Overseeing and assisting in the ordering of all raw materials and consumables used in production and ancillary processes associated with general production requirements
- Leadership to include conceptualizing an issue, developing an action plan to address/solve the issue and executing the plan
- Creating or embracing a vision and inspire others to meet organizational goals
- Promoting Change Management
- Monitoring, controlling and protecting the operational process through regular training and Standard Operating Procedure review for thoroughness with an emphasis on process improvement
- Evaluating current production requirements designed to attain strategic site goals that ensures resource alignment for attainment in key areas: technology, machinery, manpower, delivery, and timing
- Driving HOS (Six Sigma methodologies) initiatives within the facility; utilizes Six-Sigma tools to evaluate existing and alternative production methods and integrates them into standard operations on a cost-effective basis
- Driving continuous improvement process for area of responsibility and actively supporting other areas; ensuring all employees are engaged in daily improvement activities
- Possessing intelligent risk taking with the ability to make sound business judgment using limited data
- Accurately diagnosing of technical problems and form sound solutions and guiding to conclusion
- Open and accepting of opportunities to expand knowledge, skills and broaden professional experiences
- Consistently meeting commitments to the business and other functions
- Rapid transitioning of production to business requirements into actions to ensure goals are attained
- Assisting Plant Manager in setting challenging but attainable goals for the operations
- Providing recognition for successful performance or behaviors
- Providing cost accounting information on inventory and labor
- Leading and driving Structured Safety Process activities
- Supporting and collaborating with the HS&E Department to maintain facilities, processes, and personnel in compliance with corporate health, environmental, and safety policies
- Conducting performance evaluations with performance development for all direct reports
- Teaching, mentoring and coaching of employees
- B.S. in an Engineering Technology or Technical field
- 7 years of experience in production environment managing a large team
- B.S. in Chemical or Mechanical Engineering a plus
- Ability to define and solve technical problems preferred
- Experience with Barrier and Flexible Packaging production preferred
- SAP software experience preferred
- Excellent verbal, written and presentation skills preferred
- Ability to effectively supervise, motivate and direct production personnel preferred
- Green Belt or Black Belt certification is a plus
- Experience with OSHA & EPA regulatory compliance preferred
83
SAP Manufacturing Manager Resume Examples & Samples
- Facilitating client process walkthroughs to understand business processes and alignment with solution functionality
- Acting in a client facing role to determine business requirements
- Identifying how the Manufacturing solution can be best utilised to meet client requirements
- Supporting testing, training and change management work streams
- Responsibilities for candidates with relevant team leadership experience may also include
- For Manufacturing consultants, we are looking for a minimum of two full life cycle implementations and a willingness to expand knowledge to of either module
- Proven experience of both configuration and functional design in Manufacturing is essential
- Preferably a consulting background which may include supplier / client relationship or as an internal IT or HR consultant working as an employee on an internal implementation project
- Exposure to SAP Project Management methodologies
- Strong team player with proven success in contributing to a team-oriented environment
- The successful candidate will be based in Dublin but you must be willing to travel to the UK
84
Senior Manufacturing Manager Resume Examples & Samples
- Ability innovate and drive change to improve team and production line performance; ability to adapt and work in a changing environment
- Set effective SMART goals, conduct team skill assessments and individual performance reviews, manage performance improvement
- Experience, Lean Manufacturing and Six Sigma tools in the support of production process improvement
- Six Sigma Green Belt DMAIC Certification required,
- Experienced in the use of SPC, DOE and other Six Sigma tools
- Expertise in Toyota Production System and/or Honeywell Operating System (HOS) implementation
- Self-starter, with excellent verbal, presentation and written communication skills
- Proactive in meeting program cost, schedule, and product performance
- Proficiency in team building and interpersonal skills
- Proven leadership skills with the ability to inspire and motivate
- Proven experience in achieving results
- Experienced negotiator, skilled in achieving results
- Ability to prioritize work and problems; and anticipate, identify, and take action on potential issues and problems
- Experience in problem solving, troubleshooting and root cause analysis of process, equipment and organizational problems
- A Bachelor's degree in Engineering
- Program / Project management experience a must
- 5 years experience Engineering
- Prior experience in a Leadership position, multiple direct reports, multiple disciplines
- English/Spanish Speaker
- 5 years minimum production, engineering management experience
- Honeywell Operating System (will train)
- Six sigma Black Belt or Lean Expert - (preferred)
85
Industrial Manufacturing Manager Resume Examples & Samples
- Master in engineering
- Professional experience requested: mini 5 years of seniority on industrial management with at least quality system management
- KOWLEDGES
- Quality standards
- Quality management and tools
- ISO / Audit
- Leadership & management
- Automation & Control
- French, English
86
Manufacturing Manager, Hardlines Resume Examples & Samples
- Contribute to category strategy and annual product planning roadmap
- Identify and prospect growth opportunities in assigned categories
- Serve as the manufacturing specialist and manager of day-to-day relationships between Blizzard and vendors in assigned categories
- Manage vendors to ensure consistent quality of product execution including cost improvements, efficient lead times, packaging requirements, and globally compliant for commercialization
- Understands and considers global trade agreements, labor, safety and material compliance regulations and overall international business environments to manage a capable and compliant vendor matrix
- Facilitate cross departmental meetings and supplier engagement regarding cost, innovation, quality, and production
- Work closely with product development and design teams to understand product requirements in order to align them with vendor capabilities and capacity
- Work closely with internal teams and designers to ensure adherence to design / merchandising calendar and each brand’s franchise goals
- Negotiate and review price quotes and draft manufacturing services agreements
- Supervise coordinator / specialist on a project basis
- Communicate status updates with director on a weekly basis
- Assist director with special events / projects
87
Manufacturing Manager Resume Examples & Samples
- Establish goals and expectations; define success
- Work closely with department leadership and other direct reports to make sure everyone in organization understands their role and responsibilities
- Set clear daily, weekly, monthly goals and objectives, along with plan to achieve results
- Working with Director of Operations and other leaders, align medium and long-term plan with overall plant and operations plan
- Provide vision and leadership in creating a stable, self-sufficient, self-correcting organization
- Administer department personnel functions
- Set PFT yearly goals/expectations for direct reports. Complete performance reviews and recommend salary changes or promotions when appropriate
- Work with salary employees on individual development plans and continuity plans
- Evaluate and recommend employees for hire, as required
- Establish open lines of communication with the production floor
- Enforce the company policies as documented in the Employee Policy Manual and promptly execute formal disciplinary action when required
- Represent corporate policy and communicate to employees as required
- Verify salary personnel complete online Ethics training requirements and also execute hourly training
- Drive Project and Kaizen improvements using the ACE Operating System
- Monitor and improve direct and indirect labor efficiencies
- Implement cost reductions where possible
- Ensure all processes have a clear standard work sequence and standard labor time, and hold employees accountable to these standards
- Set an execute plan to achieve zero recordable injuries
- Use PFEP and cell design to create efficient material flow
- Use ACE tools to reduce lead time and improve On-Time Delivery
- Improve pick and pack process for shipping
- Set discipline on inventory transactions
- Develop Lean workforce
- Interact with other support departments as required
- Project Engineering
- EH&S Coordinator, (Communicate and administer EH&S Policy as required)
- Record and interpret production related metrics, implementing corrective action when necessary
- First Pass Yields
- Cost per Standard Hour and other productivity and efficiency metrics
- EH&S Metrics and 5S Checklists
- Continuous Improvement ideas
- Execution of production schedule for productivity and on-time output
88
Manufacturing Manager Resume Examples & Samples
- 2 years related experience or an equivalent combination of education and experience
- Previous experience in a manufacturing position in printing preferred
- Previous experience is preferred
- Knowledge of printing and production operations helpful
- Attention to detail; superior organizational skills
- Deadline orientated
- Excellent written and communication skills
89
Hsse Manufacturing Manager Resume Examples & Samples
- Lead the development and delivery of HSSE strategy across the manufacturing operations within the Americas Region
- Provide guidance and assurance related to the implementation of the Lubricants & BP HSSE Operating Management System (OMS) and related programs
- Interface with global and Envelope leadership teams
- Develop and mentor direct and indirect professional staff
- Serve as a single point of HSSE engagement to the manufacturing organization
- Implement the HSSE strategic plan
- Provide technical guidance on HSSE matters
- Deliver HSSE performance results based on established Key Performance Indicators
- Provide HSSE risk mitigation and management of a diverse Supply Chain risk portfolio
- Integrate HSSE programs with other programs and initiatives lead by other Americas Envelope Teams
- Manage HSSE risks related to contractors, third parties and suppliers
- Act as a leader of change for the HSSE organization
- Ability to influence key stakeholders across the Envelope to achieve a high level of HSSE engagement and to meet HSSE targets
- Changing political and regulatory environment that require focus and vigilance to assure established HSSE systems, tools and procedures remain effective and compliant
- 5-7 years of HSSE background and experience in manufacturing settings
- Proven ability to develop and lead HSSE personal and programs and to deliver outcomes at strategic and operational levels
- Strong knowledge in understanding and implementing HSSE Regulatory Compliance Programs
- Ability and track record of engaging at regional levels of the organization and effectively building trust, support and commitment
- Experience and track record of working as part of a Supply Chain/manufacturing team
- Experience of working within a highly matrixed environment and across several operating sites
- Knowledge of the external competitive environment
90
Manufacturing Manager / Focus Factory Manager Resume Examples & Samples
- Focus Factory is responsible for overall operational leadership, tactical execution, and financial performance of the assigned Focus Factory
- Direct responsibility for providing the vision to develop and execute the following: continuous improvement initiatives, operational planning, product quality assurance, staff management/development, customer satisfaction, and effective communication both within the Focus Factory and with site associates/management
- Direct responsibility for representing the focus factory in the development of the quarterly forecast reviews held on a monthly basis
- Development of production schedules based on committed financial forecasts, customer commitments and validated by load/capacity analysis
- Based on financial/customer commitments execute focus factory resource reviews to assure sufficient human and equipment resources exist to meet customer and site business objectives
- Assure that product and process quality are compliant to internal, industry and customer quality standards
- Drive productivity and financial performance by managing focus factory achievement of corporate and focus factory level metric goals
- Provide input and participate in customer meetings, visits and quarterly business reviews as required. Report on focus factory performance to manufacturing financial, delivery forecast/goals and customer commitments
- Conduct focus factory level communications as necessary to provide the tactical direction and drive achievement of quality, delivery, productivity and financial performance goals/objectives
- Provide the direction and leadership to develop and promote a Lean/Sigma continuous improvement culture within the focus factory Interacts with site focus factory associates, site peers and customer representatives
- Communicates focus factory operational needs, objectives and performance results with the Director of Manufacturing/ General Manager
91
Truss & Wall Panel Manufacturing Manager Resume Examples & Samples
- Assigns work to department personnel in accordance with production schedule
- Monitors efficiencies within shops, such as manpower requirements, overtime and schedules
- Generates daily production reports to monitor the efficiency of operations. Responsible for inventory control of materials used at the truss and panel shops, ASI's, LVL, Parallams, saw blades, router bits, etc
- Accountable for maintaining the appearance of the component shop and the yard
- Works with department to schedule repair and maintenance of equipment. *Responsible for product integrity and the coordinating of trouble shooting in the field as needed
- Communicates with scheduling, projects, drafting, sales and engineering for job specifications and operating efficiencies
- Oversees and approves hiring, vacations, terminations, wage increases and training and development of new employees
- Oversees that all production schedules are met and work is completed on time
- P&L responsibility
- High School diploma or GED required with strong background in math
- Ability to manage and work with groups of 25-50 associates
- Extensive knowledge of lumber and component parts
- Knowledgeable of drawings and architectural blueprints
- Ability to schedule work
- Must have good interpersonal, managerial, organizational, and communications skills
- Must have 5 years experience in construction and production management in a supervisory role
92
Manufacturing Manager Resume Examples & Samples
- Directly supervise leads and manufacturing associates in the manufacturing areas identified above. Responsible for periodic performance evaluations of employees per Kohler guidelines
- Maintain a trained and efficient work force large enough to meet scheduled ship dates, yet do so with a minimum overtime
- Strictly and uniformly enforce quality standards, production requirements, and reporting accuracy, safety rules, environmental regulations, divisional work rules, and all applicable division, group, or corporate rules and regulations
- Familiar with a variety of metal fabrication and assembly concepts, practices, and procedures
- Ensure that high quality products are built and shipped on time as defined by the commitments documented in customer contracts
- Act as Robern’s coordinator for all Shipping and Receiving activities. Continuously seek to minimize outbound freight charges by working with existing and potential carriers on freight terms and conditions. Provide input to Customer Service and Sales Teams on freight matters including costs, delivery times and preferred carriers
- Collaborate with Sales, NPD, Purchasing, and Manufacturing Engineering on best manufacturing and materials practices and customer expectations
- Set a strategy that effectively addresses scheduling, planning, systems development and material/inventory control activities. Work with the Operations Manager to develop goals and objectives for the group which are quantifiable and measurable and for which performance is measured against
- Initiate and maintain programs that foster a safe work environment
- Manage expense budgets in the areas identified above
- Bachelor degree in a related discipline (Engineering/Manufacturing, Marketing/Design) preferred
- 10+ years of experience in concurrent manufacturing environment preferred
- 7+ years of direct supervisory experience required
- Demonstrated project management experience
- Lean Expert or Lean Champion certification preferred
- Six Sigma, Green or Black Belt certification is desired
- Ability to build teams, make sound decisions and drive action cross functionally
- Ability to create plans and communicate effectively throughout the organization are musts for this position
93
Lean Manufacturing Manager Resume Examples & Samples
- Utilize Lean and Six Sigma approaches to process improvements
- Develop recommendations for business processes that ensure alignment with strategic direction; integrate business processes between multiple organizations
- A history of leading change and producing documented improvements in plant costs and quality
- A proven track record of successful organizational and operational transformations utilizing the tools of Lean manufacturing
- Experience creating a Lean or Six Sigma strategy for a manufacturing organization
- Black Belt or Master Black Belt preferred
- Produced verifiable breakthrough results
- Ability to develop and lead execution of strategy for transformational change & continuous improvement efforts across the site
- A thorough understanding and ability to use all aspects of Define Measure Analyze Improve and Control (DMAIC) model
94
Manufacturing Manager Resume Examples & Samples
- Manage daily activities on the night shift for commissioning and qualification activities
- Provide support to supervisors during equipment startup and C&Q activities to meet project milestones
- 2 Direct reports with 6 indirect reports
- Setup 1:1 meeting with direct reports to drive schedule progress, SOPs/Work Instruction redlines, goal progress, coach/mentoring, professional development
- Learn/understand process and the logistics of support resources, materials, operations staff, etc
- Be an advocate for safety during the transition from construction through commissioning and qualification. Ensure operations personnel are using the safety training during C&Q activities
- Make sure process training is being conducted for operations personnel on nights
- Being flexible and adaptable to support/requests
- Be able to stand for long periods and actively participate in commissioning and qualification activities
- Provide oversight / manage night shift supervisors to stay on schedule for production, communicate scheduling issues as they arise, as needed, and work through on the floor developments/issues with on the floor QA, operation supervisors, and the investigation group
- Management responsibilities for direct reports (i.e. supervisors) working two separate shift work on nights and provide coaching/mentoring for the night shift operation teams
- Need to be proficient in the SAP and Work Day for approval time sheet approvals / time off requests, performance reviews, goal development plans, rewarding excellence (recognition program), scheduling tools (Aspen/MS Project)
- Be able to stand for extended periods and perform operation tasks in gowning attire / clean room environments
- Drive to results for production quotas and deviation resolution to support on time delivery of products to our customers
- Night Managers are expected to provide immediate response to Issues in Manufacturing Batch Production on nights, and lead cross-functionally with management, support departments, customers to determine a clear understanding of the problem, immediate actions to mitigate risk to product quality, employee safety, or schedule, implement action to prevent recurrence and document the details of the event
- The Night Manager is the technical point of contact for support group questions regarding production execution, and owner of the equipment in the suite, including change control assessments for equipment modifications or new equipment, owner/approver of Manufacturing relevant planned deviations and CAPAs ownership. They review/approve automation updates, validation and maintenance protocols and the primary point of contact for these changes
95
Value Stream Manufacturing Manager Resume Examples & Samples
- Maintains a safe work environment, a high level of safety awareness among associates, and implements 5S principles
- Provides guidance, direction and leadership to insure that products are manufactured with the highest level of quality in a safe, compliant, and timely manner that will meet or exceed customer expectations
- Oversees and manages Value Stream expenses to meet budgets and financial objectives
- Develops a standard operating mechanism and leads the Value Stream Key Performance Indicator review each month. Identifies gaps and implements countermeasures
- Incorporates Lean Leadership into daily work and into the organization to include Visual Management, Stand Up Meetings, Gemba Walks, and Leader Standard Work
- Conducts fact-based analysis using lean techniques to create value and manage to a future state Value Stream that eliminates waste and drives continuous process improvement related to safety, quality, delivery, cost, inventory, service, and productivity
- Builds strong alliances across all functions and is strategic liaison to Account Management, Sales, Customer Service, Engineering, and Finance to meet Customer and Stock Holder commitments
- Mentors and develops direct reports and the entire Value Stream Team. Listens, supports, engages and encourages employee suggestions and input to achieve excellent results while driving a culture of accountability
- Establishes goals, sets priorities and coordinates all related activities within the Value Stream to ensure drive and focus towards meeting or exceeding established common business objectives from the Site Goal Tree and Strategic A3
- Monitors, reviews, and improves manufacturing and quality related activities and drives investigations, corrective and preventative actions
- Proactively seeks opportunities to drive improvement throughout the value stream in support of this value streams and sites productivity target
- Owns and drives a culture of “Right First Time..On Time”
- Performs all job duties in a safe manner, consistent with the Code of Ethics and the 4-I Values
- Bachelor’s degree in business management or engineering strongly preferred. An advanced degree such as an MBA is a plus
- Strong leadership and decision making ability
- Knowledge, experience or training in Lean techniques and proficient in process auditing
- Possess business and/or technical engineering aptitude to understand advanced level of product line knowledge
- 5+ years working experience in a manufacturing environment with leadership experience
- Strong project management and organizational skills
- Possess a solid working knowledge of other business functions such as Logistics, Finance, Sales, Engineering, and Human Resources in addition to Manufacturing and Quality
- Must possess excellent communication skills and lives the Thermo Fisher Scientific 4-I core values of Integrity, Intensity, Innovation, and Involvement
96
Manufacturing Manager Resume Examples & Samples
- Technical and quality Problems ·
- Schedule/Project Management Issues · Generate and develop ways to improve project productivity · Resolve complex/major issues with other members
- Cost Related Issues · Major VA/VE efforts · Total project/product cost analysis
97
Plant Manager Manufacturing Manager Resume Examples & Samples
- 10+ years of increasingly progressive experience in manufacturing or closely related field with experience operating in a GMP environment, or equivalent combination of education and experience
- Experience managing biological operations in an FDA regulated industry preferred
- Proven experience evaluating and implementing large capital equipment and automation projects
- Leadership/management experience. Proven ability to lead and inspire large teams (100+ employees)
- Experience working with large ERP systems (SAP preferred)
- Intermediate experience with/knowledge of quality systems, materials management, production, purchasing, distribution, cost reduction, project management, engineering EH&S, new production introduction, product transfer management, production scale up, and/or planning helpful
98
Manufacturing Manager Resume Examples & Samples
- Manage all manufacturing and engineering activities to ensure completion of customer requirements
- Assess performance indicators, and take appropriate actions to ensure schedule, cost and quality goals are met
- Ensure required documentation and/or system transactions are executed to meet customer, manufacturing system and financial reporting requirements are met
- Provide leadership and commitment in supporting continuous improvements in quality, productivity and delivery performance through the deployment of continuous improvement framework. Supports product design through new product introduction
- Ensure that Environmental, Health and Safety issues are addressed in compliance with local regulations, Eaton policies and good corporate citizenship
- Evaluate operational performance of the group in order to facilitate performance management, merit, promotions, job transfers, etc
- Develop budgets and resource plans and monitors performance to achieve product delivery and cost requirements
- Coordinate and assist with plant initiatives, participating on teams in order to drive best practices across the organization
- Manages and coaches the manufacturing team. Coordinates with Human Resources to address labor relations issues as they arise
- Achieve labor productivity, reduction of overtime and lead cost reduction efforts to drive factory cost-out
- Manage site capital planning and execution processes
- Bachelor’s degree in business or engineering from an accredited institution
- Minimum 5 years of experience in a manufacturing environment
- Minimum 2 years of experience managing in a manufacturing environment
- MBA or Master’s in Engineering preferred
- Minimum 2 years of experience managing in a Union environment
- International business experience preferred
- Experience working within different functions
- Requires strong understanding of manufacturing technologies and processes
- Strong communication and interpersonal skills; strong leadership, coaching and influence management skills. Ability to manage multiple priorities
- Knowledge of materials planning systems (MRP/ERP) requirements and order generation process
- Knowledge of Lean Manufacturing and Process Variation Reduction (Six Sigma) concepts
- Understanding of Supply Chain Management operational concepts (production planning, scheduling, purchasing, supplier selection, inventory control, logistics, shipping/receiving)
- Project Management and facilitation skills
99
Manufacturing Manager Resume Examples & Samples
- Plan, schedule, assign work, and ensure activities are in compliance with Company policies and procedures, and with codes and regulations
- Monitor product quality and customer relations and initiate responsive measures, as applicable. Anticipate and introduce timely, effective actions to resolve problems
- Manage activities and initiate measures to ensure efficient operations and achieve long-term cost savings
- Maintain awareness of new developments and technologies and direct subsequent investigations regarding their utilization
- Establish production systems and practices to achieve the highest efficiency and lowest cost possible. Lead productivity improvements using the most efficient manufacturing methods available
- Directing activities to meet production schedule to ensure timely deliveries through proper material and capacity planning. Develop and execute to a budget
- Demonstrate ability to work in a team environment. Coordinate with ALL other departments to ensure all goals are met. Provide feedback to these departments to preclude recurrence of issues
- Hold employee safety in highest regard. Work directly with safety director to create the safest workplace possible. Help to develop plant culture that places highest value on customer satisfaction, workplace safety, housekeeping, environmental/OSHA compliance and teamwork. Enforce discipline to sustain all above items. Serve as LEADER of 6S, Visual Factory, and Lean Manufacturing, drive these concepts to the fullest extent
- A degree in engineering or business preferred
- Supervisor or Management experience
- Lean Manufacturing / Six Sigma knowledge desired
- Commitment to excellence, Action oriented, Innovative, Leadership, Strategy and Planning, Technical orientation
100
Manufacturing Manager RDC Resume Examples & Samples
- On-time delivery of Pressure Transmitters with Honeywell quality
- Align with requirements of respective Business Units to achieve "Business Goals" while complying with ISC policies
- Lead a team of Production supervisors / technicians, in order to meet the daily/ monthly production plan
- Coordination with Projects group for smooth delivery of project orders
- Coordination with internal ISC support functions (e.g. Planning, Quality, logistics, engineering etc
- Coordination for NPI / TRUN / SAP set up activities
- Lead a POG team to continuously improve the processes to meet changing business needs and operational excellence
- Review the project progress and drive timely actions to ensure timely delivery. Initiate timely actions to ramp up / down the capacities to match the business demand at minimum cost
- Lead the team for HOS implementation and following
101
Manufacturing Manager Resume Examples & Samples
- Bachelor Degree is required with a focus in Engineering, Organizational Leadership or Business discipline is preferred
- Minimum of eight (8) years of experience in manufacturing or related operations is required with of direct supervision of professional level employees required
- Experience within a Good Manufacturing Practices and/or ISO regulated manufacturing environment is required; ISO9001 or ISO13485 is preferred
- Demonstrated strong project management skills is preferred
- The ability to lead and facilitate project improvements is preferred
- Experience with clean room environment (ISO class 7 and 8) is preferred
- A minimum of 10% travel both domestically and internationally is required.Production
102
Manufacturing Manager Resume Examples & Samples
- Typical Education: Advanced degree beyond BS in Medical Technology, Biology, Chemistry, Biochemistry
- Typical Job Related Experience: 6+ Years in Diagnostics or Related Technical Operations
- Must have a good understanding and knowledge of polyclonal and monoclonal antibodies and principles of immunodiagnostic technology, as well as experience with diagnostic immunoassays
- Demonstrated ability to interpret data and to troubleshoot and resolve technical issues
- Must have a strong work ethic and be highly motivated to work independently with high energy
- Must have excellent written and communication skills, and the ability to work as a team leader
- Must be flexible and demonstrate the ability to switch priorities to meet business needs
- Education: PhD degree preferred
- Protein biochemistry and chromatography knowledge and experience
- A strong background and experience with automated immunoassay analyzers and/or ELISA and chemiluminescent technology, as well as, proficiency with Microsoft Office, Minitab
103
Manufacturing Manager Resume Examples & Samples
- Functions as a key member of the Leadership Team and directs and oversees the development of the production strategy in a make to stock / make-to-order facility
- Develop culture of workplace safety as the priority in all cases of daily work routines for all team members
- Develop team members' competency through training, coaching, communication and performance management
- Analyze manufacturing requirements, help develop / review labor resources / work assignments with supervisors according to order priorities to maintain customer service
- Identify continuous improvement opportunities through product/process performance metrics
- Enhance team building and motivate people through improving employee engagement and empowerment
- Bachelor's degree in an engineering discipline, business management, supply chain management, or equivalent experience
- Strong people skills and the desire to grow teamwork and engagement
- 5 years of experience in a lean manufacturing / continuous improvement environment
- Must possess excellent analytical/problem solving abilities and good communication skills both written and oral
- Experience leading a group of individuals in a manufacturing environment
104
Senior Manufacturing Manager Resume Examples & Samples
- 9-11 years of experience in a CGMP manufacturing environment
- 5 years leading direct reports
- Bachelor’s degree or equivalent with 8-10 years of experience in a cGXP environment. 2-5 years of experience leading direct reports or teams
105
Manufacturing Manager Resume Examples & Samples
- Proven leadership experience with the ability to work and communicate with all levels of the organization
- Must have a complete understanding of P&L responsibilities, budgeting, and cost control
- Requires a general knowledge of procedures for estimating, order entry, job processing, production capabilities, costing and billing
- Excellent verbal and written communication skills to interface at all levels, both internally and externally
- Requires a good general knowledge of all pre-press, press, die-cutting, bindery/finishing operations and the specific requirements for all supplies and materials
- Requires the ability to efficiently operate a computer and to understand and correctly use the various items on the menu
- A high degree of tact and diplomacy are needed because of frequent contact with sales, customers, vendors and company personnel
- Must be self-motivated and driven individual who is willing to take the initiative. Must be a leader and believe in strong commitment to values
- Must be willing to make difficult (possibly unpopular) decisions. Approachable with ego in check; flexible; high energy level; and integrity beyond reproach
- Must have 2-5 years demonstrated ability to supervise others
- Must be able to work any hours, including weekends, as needed to get the job done
- A Bachelors Degree or equivalent, preferably in Engineering, Business or Manufacturing Technology
- Minimum 5 years experience in manufacturing management, preferably in commercial print
106
Manufacturing Manager Resume Examples & Samples
- Engineering Bachelor’s Degree, Industrial, Electrical, Mechanical Major
- Minimum 8 years experience both supervisory and managerial. Two years minimum experience on Managerial role
- Six Sigma, ASQ, APICS, certifications preferred
- Technical knowledge – Engineering, electronic experience, production planning, customer service and materials
- Some Knowledge of labor laws and federal regulations
107
Manufacturing Manager Resume Examples & Samples
- Champion lean manufacturing excellence with focus on safety, quality, and operator-led process control
- Directs work activities of production in all departments, coordinating shifts into a cohesive manufacturing unit
- Ensure product quality expectations of the customer without compromising processes or design specifications
- Utilizes effective leadership skills in a manner to achieve proper motivation, performance, reward, respect and accountability for all operational resources
- Communicate expectations to production leaders regarding lowering costs and/or improving key performance indicators utilizing Lean initiatives
- Coach and develop front-line leaders to resolve day to day issues and generate improvement solutions
- Monitor performance of subordinates and assist in removing barriers identified
- Evaluates and identifies training needs for hourly workforce
- Monitor manufacturing data systems necessary to support the manufacturing process, and provide information for budgeting, capacity and planning processes
- Drives the use of data-driven improvements within the facility
- Utilizes Lean and Six Sigma tools for continuous improvement
- Executes the financial plans associated with the operational team
- A visible and vocal presence as the shop floor leader
- Creates, implements and drives key safety initiatives, assuring resources are sufficient to create an accident free culture
- Leads safety commitment and engagement from every team member, while creating an atmosphere of open and honest dialog and feedback
- Attention to details and the ability to see and manage the big picture
- Able to manage and execute multiple, complex tasks and deal easily with pressure on a daily basis
- Able to motivate, communicate, and drive continuous improvement
- Strong analytical and decision-making decisions
- High energy with a sense of urgency
- Proficient with Microsoft Office and a variety of manufacturing systems
- Utilizes great leadership attributes to interpret the toughest situations in a constructive and empowering way
- Individual familiar with and practicing lean manufacturing techniques and Six Sigma quality improvement tools that drive continuous improvement
- A creative thinker who values engagement, ownership and contribution of all our associates through empowerment and Operator Led initiatives
108
Manufacturing Manager Resume Examples & Samples
- Responsible for total production of the unit and cell metrics including safety, production quantity, customer service, defect levels, waste, work order attainment, etc
- Selects, mentors and coaches cell coordinators along with direct and indirect associates that help lead the manufacturing effort. Ensuring the correct skill sets and styles are evident and practiced in all cell coordinators
- Ensure resources are available and fully utilized, with a focus on continuous development of hourly associates
- Coordinate the maintenance of manufacturing data systems necessary to support the manufacturing process, and provide information for budgeting, capacity and planning processes.Ensures the use of data-driven improvements within the facility
- Effectively manages cross functional relationships with other departments to support effective use of manpower, materials, and equipment, as well as productivity and quality improvement initiatives
- Promotes “on-the-spot" problem solving activity, supporting associates in cells with decisions and needs, ensuring progress toward operator led process control
- Utilizes Lean and Six Sigma tools to continuously improve the business every day
109
Area Manufacturing Manager Resume Examples & Samples
- Ensure all system requirements are practiced for the management of HSE&R Hazards & Incidents
- Actively engage with the operators
- Provide coaching and mentoring support to the RST and Crew/Line Teams to achieve the team and their individual goals
- Perform other essential responsibilities as deemed necessary
- Bachelor’s degree in Mechanical, Electrical, or Industrial Engineering, or other related engineering field required
- Five (5) years of production leadership experience required, strong preference for related converting experience
- Strong communication, scheduling and organizing skills
- Proven ability in managing others as well as influencing and building partnerships
- Ability to lead teams through change and improvement
- Leadership experience with a customer focus on industrial reliability
- Ability to work and communicate with outside resources: OEM representatives, vendors, contractors, service companies
110
Area Converting Manufacturing Manager Resume Examples & Samples
- Lead and promote HSE&R practices within Shift/Line Crews
- Actively work with and support the RST structure
- Develop and deliver implementation programs that ensure operators are aware of and comply with any process changes
- Highlight operators not complying to performance and behavior standards and escalate as appropriate
- Identify any operator skill gaps and provide or recommend training
- Identify opportunities to implement HMex (Manufacturing Excellence) and other Operational Effectiveness tools to improve efficiency and eliminate waste in manufacturing processes
- Support growth and investment goals of Site Leadership
- Bachelor’s degree in Mechanical, Electrical, or Industrial Engineering, or other related engineering field preferred
- Minimum Five (5) years of production leadership experience with Three (3) years converting experience required
- Strong sense of urgency and teamwork
- Proven knowledge and track record in world class maintenance safety processes
- Knowledge of industrial mechanical equipment
- Problem solving and root cause analysis skills Personal computer skills, especially Maintenance Management software, e.g. Passport, Excel, Word, Outlook
111
Manufacturing Manager Resume Examples & Samples
- REQUIRED
- A minimum of 10 years of progressive experience in high speed manufacturing
- Ability to identify process improvements
- Previous Production and/or Manufacturing Management experience
- Strong team leadership skills
- Working knowledge of TPM/Lean Manufacturing / Six Sigma
- Ability to manage a diverse group of people
- Good understanding of basic financial analysis
- PREFERRED ADDITIONAL
- Proficient with Word, Excel, PowerPoint, Hyperion, E-Time, PeopleSoft and WMS
112
Manufacturing Manager Resume Examples & Samples
- Ability to read and interpret documents such as safety rules, operating and maintenance instructions and procedure manuals. Ability to write routine reports and correspondence. Ability to speak effectively before groups of employees, customers, and outside regulatory agencies
- Ability to apply concepts of basic algebra, geometry, percentages circumference and volume
- Ability to solve practical problems and deal with a variety of variable in situations where standardization exists. Ability to interpret a variety of instructions furnished in written, oral, diagram, or schedule form
113
Manufacturing Manager Resume Examples & Samples
- Oversee the implementation of manufacturing schedules, personnel requirements, quality control, production standards and safety programs
- He/she will also develop manufacturing strategies to provide quality/profitable products that meet customer needs and distribution schedules
- Leads and coordinates the implementation of programs which support these manufacturing strategies
- Provides a safe environment for all employees
- Promotes and implements ergonomic principles, environmental responsibility and overall employee health and wellness
- Ensures products and services meet world class standards
- Leads C2Q efforts to attain internal certification goals, ISO requirements and total customer satisfaction
- Provides world-class service to internal and external customers by meeting/exceeding distribution stock service goals and customer delivery requirements on non-stock orders
- Continuously monitors performance and takes corrective action when necessary
- Responsible for variable conversion cost and base cost management while driving continuous cost reductions
- Selects, trains and develops manufacturing staff and associates to achieve company goals
- Procures necessary resources to optimize staff productivity and efficiency
- Provides guidance and assistance to product and manufacturing engineers making product/process modifications
114
Manufacturing Manager Resume Examples & Samples
- Deliver to Ready, Run, Release priorities per Plan. Independently able to make decisions and run the suites. Provide immediate response to Issues in Manufacturing Batch Production, on days, 7 days a week, and lead cross-functionally with management, support departments, customers to determine a clear understanding of the problem, immediate actions to mitigate risk to product quality, employee safety, or schedule, implement action to prevent recurrence and document the details of the event. Must reduce variability of duration/time between runs related to equipment, process or document issues
- Proficient in Root Cause Analysis / Cause Mapping to ensure effective proactive identification to prevent issues or problem resolution to eliminate recurrence of issues
- Identification and implementation of preventative actions in response to safety near misses and/or incidents
- Equipment Cost Center Review for all areas of responsibility
- Runs major investigations and develops Storyboards as needed, e.g. contamination, etc
- Process Management. Create and maintain process-specific reference guide for troubleshooting, response, and escalation. Accountable for SOP clarity, accuracy and relevance. Responsible to organize SOPs for most efficient & effective ownership by supervisors and operators. Ensure owners have expertise required to own the SOPs. Follow up on DMS suite board actions/escalations as related to Equipment, Documents or Process
- Equipment and Process SME: Identify non-routine technical training associates may need, develop material via T&D or Expert trainer or via supervisors/associates. SME for analytical instruments; e.g. FIT, NOVA, SoloVPE, Density Meters, Vicell, etc. Develop associate SMEs for these technologies. Conduct Post Campaign MFG Lessons Learned which includes eDCF Review w MSAT (Face to Face). Addresses Regulatory and Customer Audit Requests and any observation responses for Documents, Equipment and Process
- Participate in inspections as Backroom Triage Manufacturing Representative
- Actively provide coaching and mentoring to supervisors, associates by involving employees in issue identification and resolution
115
Manufacturing Manager Resume Examples & Samples
- Provide manufacturing direction to support mission statement: To safely delivering quality, cost-effective products on time – every time by building effective partnerships with our customers, our suppliers, and our teammates… realizing that how we operate today is not good enough for tomorrow
- Maintain a safe working environment by insisting that all employees work safely
- Focus on machine capability / product specs and our ability to deliver good quality using a robust quality system
- Responsible to satisfy customer demand by producing products as scheduled at or below budgeted cost
- Develop and continually improve employee skills by providing proper training, coaching and direction to improve overall operations
- Provide constant feedback and support to all Company organizations to maintain efficient operations
- Maintains operational intensity through metrics and accountability
- Partner with all support groups to optimize efficiencies
- Selects and maintains qualified personnel in all positions
- Identifies training needs, initiates development of subordinates and takes necessary personnel action
- Ensures that duties, responsibilities, and authority and accountability of all direct subordinates are defined and understood
116
Projects Manufacturing Manager Resume Examples & Samples
- Manage the Production Part Approval Process (including Mass Production Trial and Extended Mass Production Trial)
- Minimum bachelor's degree in Engineering; or, minimum 5 years previous experience as Manufacturing Engineer
- Excellent analytical, problem solving, decision making and communication skills
117
Manufacturing Manager Thailand Resume Examples & Samples
- You are in charge of the overall manufacturing processes and performances of our production plant and will provide leadership and direction to the manufacturing team
- You take an active role within the manufacturing team to ensure that manufacturing performance and quality goals are met
- You ensure the highest level of customer support and the optimization of the supply chain processes
- You maintain compliance of company policies, safety standards, quality specifications, regulatory requirements, and sanitation practices
- You ensure optimization and continuous improvement of all manufacturing processes
- You train and develop your production and engineering team
- Hands on production manager with minimum of 5 years experience, preferably in plastic packaging
- Strong leadership and interpersonal skills
- Professionalism and dedication to develop and train employees
- Ability to work independently, under pressure, tight deadlines and pro-active in solving problems
- Open-minded towards the Asian culture
- Willingness to work in an attractive and challenging environment
- Proficiency in English is a must, Thai and German is an advantage
118
Cluster Manufacturing Manager Resume Examples & Samples
- Drive the Safety agenda in the Manufacturing area and embed processes to deliver an improved Safety Culture and performance across ASEAN through OMS (safe, systematic, sustainable)
- Build a Quality culture in our operations that matches our premium brand
- Ensure high plant reliability and flexibility in support of the Service agenda in a customer centric supply chain
- Deliver and Optimize the performance of the ASEAN manufacturing team in terms of Safety, Quality, Service, Cost/ Cash resulting in the delivery of the annual plan metrics and continuous improvement
- Identify Investment and efficiency opportunities and own the process to realize these opportunities
- Contribute in the manufacturing area to the delivery of Strategic Projects for the region, so as to drive growth, simplification and integration in operations of the businesses requirements in ASEAN. Specifies and manages policies, process and engineering solution to assure quality/ safety and environmental outcomes of new projects and process improvement initiatives meet objectives and align with OM
- Develop capability by building strong and committed plant organizations, with succession and talent management processes embedded and executed across the plants in ASEAN
- Develop a CI Culture to ambition World Class Operations Management based on loss intelligence / eradication
- Support and coach Plant Managers in ensuring harmonious and productive employee relations with Unionized staff and provide guidance on longer term people strategy
- University degree in engineering or chemistry/ allied fields
- Strategic level experience
- Extensive Supply Chain experience
- Proven leader of people across multi-site operations
- Systems / ERP experience
- Demonstrated successful MOC leadership
- Knowledge of lubricants, FMCG or specialist chemical
- Continuous improvement experience
- Network planning experience
- High level of written & spoken English
- Accountable for Capex 3-5 year plans
- Accountable for Plant yearly manufacturing Plans
- Accountable for design, implementation and readiness for ASEAN growth via transformation programme and major capital projects
119
Manufacturing Manager Resume Examples & Samples
- Plans and directs production activities and establishes production priorities for products and services in keeping with effective operations and cost factors
- Maintains quality and reduces inventory levels and lead times
- Analyzes production reports, makes adjustments if necessary
- Proficient in all Microsoft Office applications including Excel, Word and PowerPoint
- Demonstrated success in creating an engaged employee enviroment
- Ability build teamwork with the workforce
- A minimum of 3 years experience in a manufacturing environment
- Experience working in a lean manufacturing environment
120
Manufacturing Manager Resume Examples & Samples
- Responsible for managing and leading manufacturing to achieve greater efficiency and productivity through the use of quality improvements and cost containment methods in order to meet company’s operational and financial goals
- Responsible to develop and facilitate a cohesive team environment, which builds confidence & strong morale, and stimulates innovation and creative problem solving
- Responsible for manufacturing personnel including training, skill development, performance reviews, and necessary disciplinary action
- Work closely with General Manager, Customer Service, Human Resources and all other members of the management team
- Utilize measurement tools to establish production benchmarks (i.e. cycle/flow times and waste reduction)
- Schedule shop loading and provide capacity planning that will allow teams to schedule daily work
- Determine assembly methodology for assemblies of components and part features required to support the proposed product
- Provide technical support to Estimating and Fabrication plants in identifying detailed forming, chem milling, machining, and finishing and assembly process methods to meet customer requirements
- Identify tools needed to support the feasible process plan and configure to match available and appropriate LMI in-house equipment
- Assist fabricators as required in the process of tool fabrication from a design perspective, disposition non-conformances and specify corrective action to maintain tool quality and accuracy requirements
- Develop inspection plans for complex tooling, review Coordinate Measuring Machine (CMM) data and verify correct surface development through point comparisons with tooling or engineering part models
- Work with team members to ensure accuracy of work and provide constructive feedback as needed
- Lead manufacturing process improvement initiatives and drive to closure
- Create manufacturing plans identifying key process characteristics or process specific requirements in support of detail parts planner and supply chain management for purchase parts
- Other duties or special projects as assigned
- Bachelor’s degree in Mechanical, Industrial, or Manufacturing Engineering is preferred
- Minimum 5 years’ experience in manufacturing management
- Minimum 3 years’ experience with manufacturing of sheet metal and machined components
- Ability to read, analyze and interpret technical information such as blueprints, engineering drawings, and customer specifications required
- Experience in Lean manufacturing techniques and tools
- Experienced in Model Based Definition and Geometric Dimension and Tolerancing
- Proficiency with various computer software programs such as Microsoft Word, Excel, PowerPoint, Visio, Project, and others helpful in managing projects. Experience with advanced CATIA operations preferred
- Ability to mentor and train new team members
- Must be able to effectively utilize various communication and team management tools such as tele-conferencing, video conferencing, web-casts and web meetings, collaborative file sharing environments, and e-mail
- Must have the ability to define problems, collect data, establish facts, and draw valid conclusions
- Superior written and oral communication skills. Ability to successfully interface with all levels of employees and management, both internally and externally
121
Manufacturing Manager Resume Examples & Samples
- Will have solid technical skills and understanding of machinery and shop floor terminology, and experience/exposure to scheduling
- Experience with training and building strong work teams that require minimal management oversight through the use of good delegation skills and understand participative decision-making
- Experience in overcoming the hurdles and complications relating to the transition and continuation of JIT and lean manufacturing
- Strong & professional manager and leader a take-charge type of person with the ability to be firm but fair, hold people accountable for achieving results and able to impart disciplinary action when necessary
- Should have excellent communication (active listening) skills, oral and written to interact with employees, customers and vendors. Maintains a positive work atmosphere by behaving and communicating in a manner that he/she gets along with customers, employees, peers and management
- Must have a strong work ethic and be a hands-on, proactive manager that is willing to put in extra time and that takes pride in the quality of a product
- Must be well organized, and have the ability to prioritize, maintain focus and follow through and have good analytical skills
- Good computer skills (Microsoft Word, Excel, Access, PowerPoint), exp. with Vista (Epicor) MRP software preferred
- Must lead by example; must earn the respect of all levels of the organization
- Must support excellence through personal actions, behavior, high standards and quality in all endeavors
- Teacher and mentor
- Professional demeanor and presence; self-confident
- Be able to give clear definition to employees, and be a clear, concise communicator
- Should be an excellent problem solver - see the problem and know what needs to be done to fix it
- Must have good delegation skills and understand participative decision making
- Must be proactive rather than reactive
- Bachelor’s degree in manufacturing, engineering, business administration or related with a minimum of 5 years’ manufacturing experience including one year in a supervisory capacity
122
Manufacturing Manager Resume Examples & Samples
- Develops manufacturing operating plans in accordance with company policies, goals, and objectives
- Links established processes and leadership execution in the areas of environment, health, and safety in keeping with the company’s proud legacy of attention to safety, the environment, and the communities in which it exists
- Delivers determined financial objectives by reaffirming existing production goals or setting new goals and then leading the team to achieve these goals
- Delivers operational excellence through optimizing capacities, total cost effectiveness, and value to the customer base. Ensures operation plans achieve targeted cost and efficiency results that maximize value for the business unit
- Optimizes capital expenditures to sustain operations, drive EHS value, and deliver growth products
- Develops and executes lean and flexible production systems based on standard lean manufacturing principals- specifically 5S, time studies and productivity tools such as eAussie problem solving
- Executes plans for quality and process excellence that ensures consistent quality assurance and process excellence procedures, controls, and feedback
- Ensures adequate people development plans and capable succession plans are in place
- Minimum 5 years of plant operations and/or manufacturing management experience
- 5 years of experience in the aerospace industry or a company that produces highly engineered products
- Experience supervising in a unionized workplace
- Experience with industrial gas turbine investment casting process
- Bachelor’s degree from an accredited institution in Industrial, Mechanical, Metallurgical, or Materials Engineering
123
HTC Global Lean Manufacturing Manager Resume Examples & Samples
- Drive key Lean elements such as 6S, Cellular Manufacturing, Kanban replenishment, SMED, Visual management, Continuous Flow and Material Flow
- Improve manufacturing processes and methods for cost-reduction, quality improvement and efficiency using lean manufacturing and six sigma principles
- Establish and maintain Lean measures throughout manufacturing
- Develop and implement solutions based on Lean Production system design and transformation principles, tools and techniques including Six Sigma
- Stretch the organization by creating a learning environment/culture, problem solving, envisioning the future state condition, and leading towards fulfillment
- Continuously reduce manufacturing lead times
- Convert current manufacturing to continuous flow
- Work closely with production, maintenance and other support functions in managing equipment moves and improving facility layout
- Structure Lean events to dramatically reduce total cycle time across the various value streams
- Establish a pull system for the manufacturing operations
- Create and promote the Visual Factory concept
- Setup an on-going continuous improvement program that involves all employees
- Perform other special projects or duties as required
- Bachelor's degree in Mechanical, Industrial, Manufacturing Engineering or related field
- At least 8 – 10 years’ experience in a lean manufacturing environment driving a lean culture
- Proficient in Microsoft Word, Excel and Projects; SAP a plus
- Demonstrated experience in facility design including layout of manufacturing equipment and processes throughout the value stream
- Lean implementation experience in mechanical assembly, machining and forging preferred
- Strong analytical skills and process focus. Able to compile, analyze, and interpret complex data
- Expert knowledge of SPC, FMEA, Root Cause Analysis, Process Optimization and Control Plans
- Ability to demonstrate expert knowledge of Toyota Production System principles of continuous flow, 6s, visual factory, Kaizen, Kanban, SMED, etc
- Certified Six Sigma Black Belt a plus
- Candidate should be results oriented with good project management, organizational, prioritization, and able to work effectively in a team-oriented environment
- Position requires 50% international and domestic travel
124
Manufacturing Manager Resume Examples & Samples
- Promote and grow WCM/MAFACT within Operational areas
- Optimising process
- 7 waste studies to identify opportunities
- MAFACT Quarterly Audit & Drive Action Plans From Results
- To drive the efficiency and productivity within assigned projects
- To project a professional image of the company to customers/visitors
125
Manufacturing Manager Resume Examples & Samples
- Maintain manufacturing load plan, master schedule and inventory control plans
- Apply “hands-on” production planning and master scheduling expertise in the SAP ERP/MRP environment
- Identify, implement, and support lean manufacturing scheduling tools consistently across all manufacturing departments
- Demonstrated capability to drive the sales & operations planning process
- Ability to manage the efficiency and transparency of schedules and cost elements utilizing SAP
- Drive measurable improvement in on-time delivery, productivity, and customer satisfaction
- Bachelor degree in a relevant discipline
- APICS Certification and working knowledge of planning and inventory control fundamentals preferred
- Minimum of 10 plus years experience in a planning discipline within a manufacturing environment including 5 years in a Production Planning & Scheduling manager role
- Expert knowledge in application and use of SAP operating system
- Thorough knowledge and application of Lean principles and practices
- Experienced in the use of Microsoft office products
- Requires 5% Travel
126
Multi Functional Manufacturing Manager Resume Examples & Samples
- Accountable for production performance in support of Commercial Space
- Support cost reduction initiatives such as the Product Cost Catalog
- Ensure Production supports the LOB in new business endeavors
- Educate, drive and hold the IPTs accountable for their deliveries to the Manufacturing Centers
- Educate, drive and hold the Manufacturing Centers accountable for their deliveries to ATLO
- Foster a relationship with the external customer
- Mentor & develop the Production Leads and Project Engineers supporting the LOB
- Monitor and ensure that the Program IMS is traceable to the manufacturing supplemental schedules
- Streamline execution between the LOB, MPS and PPC&C functions
- Facilitate and implement process standards across the entire manufacturing organization
- The candidate shall possess and have demonstrated Full Spectrum Leadership qualities
- Minimum 8 years of experience in a Satellite Production Environment (Manufacturing or ATLO)
- A working knowledge of Master Planning, Resource and Capacity Planning, Manufacturing Engineering, Material Control, Inventory Control, Shop Floor Control, and Supply Chain
- Creative and innovative problem solver with proven ability to formulate business recommendations and implementable solutions to large-scale, complex issues
- Ability to develop enduring relationships and interact with leaders at all levels
- Consistent record of high performance, with the ability to accept responsibility, exercise authority and be held accountable for assigned tasks
- Experience in leading process improvements utilizing LM21 tools and processes
- Experience in a Manufacturing or ATLO leadership role
- Knowledge/experience in support of hardware development and work area flow optimization
- Green Belt/Black Belt or Master Black Belt Certification desired
- CAM Experience
- Experience with new business
127
Manufacturing Manager Resume Examples & Samples
- Plan and direct manufacturing resources to ensure that profit and strategic plans are met or exceeded
- Ensure quality systems are followed and executed in accordance with EQS and ISO policies
- Drive activities to reduce past due, scrap, rework and overtime costs while meeting quality objectives
- Implement and maintain ELS initiatives in all production areas
- Direct problem-solving activities and coordinate corrective action plans for production problems
- Plan and assist in designing strategies to improve positive employee relations and increase overall engagement
- Ensure that Eaton values and philosophies are integrated into the culture
- Minimum of 7 years of experience in manufacturing/operations
- Minimum of 5 years of supervisory experience
- 7-10 years of experience managing in manufacturing/operations
- ASQ, APICS-CPIM
- Basic level of corporate financial reporting
128
Manufacturing Manager Resume Examples & Samples
- Provides leadership to ensure employees demonstrate appropriate work skills, safety practices, quality standards, technical accuracy, efficiency and conformity to company policies
- Determines daily work priorities and adjusts work activities accordingly – communicates schedule and productivity goals to team directly or through subordinate leaders
- Authorizes absences or overtime in order to meet work requirements
- Completes necessary recordkeeping on SAP
- Understands the overall production flow, including role of feeder departments, home line, shipping support, transportation and so on
- Troubleshoots as needed
- Applies Theory of Constraints concepts; identifies constraints/bottlenecks that affect productivity
- Suggests solutions
- Teaches team how to identify constraints
- Listens to and acts on issues/suggestions raised by team
- Regularly monitors team member's adherence to safe work practices and company's safety policies
- Monitors production to ensure adherence to quality standards
- Reinforces use of PADs / Work Instructions and other documentation to ensure that quality standards for fit, function and appearance are met every time
- Works with newly hired and/or transferred employees to make sure they thoroughly understand and properly perform their job duties in accordance with the PADs
- Understands and communicates company and department metrics and results includingProfit Sharing, errors, nonconformities, quality, safety and material usage
- Communicates regularly and effectively with the team and other departments.Schedules meetings with team and attends meetings with other departments to ensure optimum communication
- Addresses employees’ concerns and questions promptly and with appropriate feedback to affected employee(s)
- Answers employees’ questions related to company policies or directs employees to proper resources
- Ensure employees follow policies
- Coaches as needed
- Attends intershift meetings
- Relays and shares information with employees, across shifts, and with other departments
- Reallocates labor per manufacturing needs
- Provides positive and negative performance feedback to employees verbally and in writing
- Documents feedback through Confirmation of Conversations (COC) and written reprimands
- Completes and delivers annual performance reviews for employees
- Assists employees with difficult or unusual issues and situations, making decisions about disposition of situation or the need to seek additional authorization for action
- Is sensitive to employee issues and knows when to refer employees to the proper resource person
- Helps employees identify training needs
- Ensures employees receive appropriate training necessary to meet and exceed job expectations
- Coaches employees requiring additional support and training
- Knows and uses technical skills needed for job, including Outlook, AS/400 & Frontier (options such as load availability, build report, ticket reprint, manufacturing scan, sales order tracking), and SAP (attendance functions)
- Participates in company programs to develop leadership and job skills
- Identify opportunities to improve the business, develop strategies, and implement strategic plans
- Four years manufacturing experience with at least two years experience as a leader
- Previous glass & manufacturing experience
- Proficient in MS Office (Word/Excel)
- Bachelor's degree preferred
- Knowledge of PGT products and processes
- SAP/AS400/Frontier preferred
- Work Keys Score/Test Requirements:Applied Math – 5, Locating Information – 5, Observations – 5, Reading for Information –Writing - 3
- Must be able to lift up to 100 lbs. depending on department
- Occasional bending and stooping
- Consistent daily attendance required to meet job duties
- Plant environment – may or may not be air conditioned, depending on location
129
Manufacturing Manager Resume Examples & Samples
- MS in organic chemistry or chemical engineering or related experience
- Minimum of 5-8 years experience in production and process systems in a chemical biotechnology, pharmaceutical or health science manufacturing environment
- Minimum of 10 years in management experience
- Experience in utilizing ERP system for master scheduling and manufacturing processing to assure sufficient resources to meet product demand requirements
- Experience in developing best practice operational metrics and goal setting to drive improvements
- Working knowledge and experience with Quality Control systems
- Strong safety mindset
- Experience in managing chemical waste processing
- Proven project/team leadership skills
- Outstanding critical thinking and troubleshooting skills
- Superior verbal and written communication skills
- Ph.D. in organic chemistry or chemical engineering
- Experience utilizing SAP in a manufacturing environment
- Understanding of material planning processes and best practices
- Experience in regulated industry
- Knowledge of green chemistry processes
- Strong history of effective process development
- Develop plans, priorities, and systems to efficiently and effectively utilize all resources (equipment, space, personnel) to meet production schedules, product standards, and operational costs. Ensure that manufacturing capability is adequate to meet existing and anticipated needs
- Investigate and implement most appropriate production technologies and quality assurance techniques for safe and cost effective manufacturing
- In conjunction with Process Research, plan and implement process improvement activities to increase product efficiencies, improve safety, reduce cost of production, and maintain high product quality
- Support strategic initiatives designed to drive continuous improvement in manufacturing department metrics, and transition from traditional to LEAN Manufacturing
- Establish best practices in quality, safety, and housekeeping standards
- Participate in strategic planning and budgeting for manufacturing department
- Assure that manufacturing is represented on new product teams and in operational meetings for existing products. Provide information to team concerning all aspects of the production and QC process. Provide logistical support as needed for launching new products
- Coordinate with Finance and Purchasing Department to ensure timely flow of information on costs of goods manufactured, raw material purchasing requirements, budget analysis, metrics applicable to manufactured items, etc
- Provide coaching, development and management to staff. Review training needs and provide training opportunities for staff to develop personal and job-related skills. Conduct performance, career development, and salary reviews
- Maintain effective interdepartmental communication and timely follow-up to assure that all manufacturing and corporate objectives are met
130
Manufacturing Manager Resume Examples & Samples
- Will guide and manage manufacturing team to achieve goals related to safety, quality, cost and on-time completion of quarterly build plan
- Support Operations team in strategic planning of labor, equipment, and other resources needed to achieve build plan and establish readiness for New Product Introductions
- Direct management of a team of 30+ employees comprised of Production Leads, Production Technicians and Test Technicians
- Drive a quality-focused, data-driven culture that leverages Lean tools and rigorous root cause analysis
- Collaborate with our Supply Chain, Quality Assurance, Manufacturing Engineering and Product Support Engineering teams to ensure the highest level of product quality and consistent material availability
- Serve on cross-functional teams to support New Product Introductions
- Coordinate implementation of engineering change orders and engineering deviation authorizations
- Provide employee performance management and compensation recommendations
- Develop a team oriented production environment focused on process improvement and continuous waste elimination
- Bachelor’s degree required, Master’s degree preferred
- 3+ years of direct people management required
- 3+ years of experience in Manufacturing/Operations required
- Strong leadership and written/oral communication skills required
- Experience with Lean tools and Continuous Improvement Methodologies
- Experience with instrument/medical device manufacturing a plus
- Must be able to exercise independent decision making skills for complex problems, methods, and corrective actions
131
Financial Controller Manufacturing Manager Resume Examples & Samples
- Working knowledge of French
- Requires high degree of interaction with different departments, ability to influence and to work in a matrix environment
- Important to have good organisational skills and an ability to manage priorities while ensuring good service level
- Analytical / financial skills
- Strong mastery of Excel
- Good communication, presentation and report writing skills
- Assertive, pragmatic and good team spirit
- Drive to deliver the financial targets for the MPU/SPU whilst respecting the prioritization of Quality, Supply, Cost as well as GSK and Vaccines' strategies and priorities
- Act as an enterprise leader in the leadership team giving strategic insights into business issues and decisions
- Prepare and drive the financial part of the monthly Business Performance Review (BPR) providing information and input that supports decision making
- Plan and drive the financial planning process in the MPU/SPU, challenging assumptions and ensuring a result aligned with objectives (Forecasts, Target setting and Budget)
- Participate in the preparation and running of the Supply Review Meeting to ensure finance input into the process as well as to track and monitor deviations in the declared capacity
- Ensure the availability of monthly Opex information, Capex information, headcount information, production value reporting, write-off information and cost/dose data
- Provide the MPU/SPU leadership with relevant analysis to support decision making and drive performance
- Perform monthly and yearly closing and reporting activities
- Perform variance analysis to ensure master data accuracy and perform standard cost data collection and updates for the unit
132
Manufacturing Manager Resume Examples & Samples
- Deploying Bio-Rad’s strategic, tactical, operational and business goals at Steenvoorde to contribute in making our worldwide manufacturing organization, our global supply chain organization and Bio-Rad successful
- Driving superior quality and performance
- Driving customer satisfaction
- Driving Innovation
- Developing our teams & organization
- Driving continuous improvement using Lean, 6 Sigma methodologies as well as automation
- Reaching our financial goals (Driving cost efficient production and cost reductions)
- Ensuring regulatory compliance
- Maintaining efficient partnership with our internal and external business partners and stakeholders
- Several years of experience in management and leadership function in a regulated manufacturing environment (Diagnostic, MD, Biotechnology or Pharma Business)
- Excellent management and leadership experience is a must
- Lean and 6 Sigma & automation
133
Manufacturing Manager Resume Examples & Samples
- Directs all Honeoye Falls machine manufacturing functions including assembly, calibration, testing, etc. Meets safety, delivery, quality, and cost objectives
- Takes appropriate actions and makes decisions consistent with achieving the POR for the factory schedule. Develops departmental budgets and performs to budget and/or business plan. Meets departmental objectives of quality, cost, and on-time delivery
- Ensures manufacturing areas are in safe, secure, and efficient operating condition and in compliance with all federal and local guidelines pertaining to materials and OSHA requirements. Ensures all direct reports are following proper procedures and use of PPE in compliance with OSHA and other applicable regulatory agencies
- Identify current workforce skill levels and identify and provide education and cross-training to achieve a highly involved, flexible workforce
- Communicate and coordinate needs with support staff. Maintain open communication with planning, purchasing, engineering, and all other operations roles. Obtain necessary support from Purchasing, Product Engineering and other personnel as needed to resolve issues and meet objectives
- Promotes a continuous improvement culture and facilitates actions to maintain and improve 5S, pull systems, and the contribution of cost reduction ideas and initiatives
- Ensure high level of product quality through the use of the quality system in order to meet internal ppm and COPQ targets. Ensure all customer complaints are resolved promptly with thorough root cause and corrective action
- Completes performance reviews on a timely basis. Establish development plans for both individuals with high potential and those with performance issues
- Contributes to the development of the S&OP, POR, Non-Ultrasonics Profitability Plan, and Planning Conference
- Trouble-shoot and resolve electrical/mechanical problems to maintain production schedule while securing support from engineering as needed. Resolves manufacturing issues, and assists with Root Cause Analysis, Corrective Action, and the disposition of Non-Conforming Material
- Assists with the master scheduling, capacity analysis and gap analysis to ensure that the people, and equipment are in place to support the manufacturing schedule and demand forecast
- Provides strong leadership and communication to promote a positive work environment and promote positive change. Communicates regularly with all team members throughout the day as needed and in regularly scheduled meetings: Daily production meetings, weekly backlog meetings, monthly meetings for new ideas, continuous improvement and cost reduction
- Maintains a safe work environment at all times in the machine manufacturing area. Assists with developing and supporting safety goals and participates as an active member of the safety committee
- Assists the Operations Manager with special assignments/projects as needed
- Skills / Technical Knowledge / Experience
134
Manufacturing Manager Resume Examples & Samples
- Set up, operate equipment, and monitor production processes, including clean-in-place (CIP) and steam-in-place (SIP) operations and report production in written and electronic documents in accordance with good documentation procedures (GDPs), troubleshooting issues and review documentation as appropriate
- Train other personnel on equipment operation, cGMPs, documentation, technical theory, or other tasks. Maintain individual training plan
- Review documentation (batch records, SOPs, Logbooks) for completeness, clarity, accuracy and submit edits to documents for revision as required
- Administrative tasks – leading shift exchange, meetings, sending/receiving emails, participating in projects
- Perform other duties as assigned
- 8-10 years’ experience in manufacturing (12-15 years’ experience without AS/BS) with 3-5 years supervisory experience; GMP experience and API manufacturing experience preferred
- None required - Demonstrates effective leadership
- Ability to work inter-departmentally and with customers
- High level of suite specific operations and technical skills
- Demonstrates role model behaviors for operating in a GMP manner
- Demonstrates role model EPS behaviors- e.g. 3 way communication, questioning attitude
- Demonstrates role model safety behaviors
- Demonstrate ability for effective Planning, Organizing and Controlling competency
- Demonstrate sound decision making, considering broad scope of factors
135
Manufacturing Manager Resume Examples & Samples
- Ensure compliance with state and federal regulations, AABB standards, ARCBS directives and regional policies and procedures
- Bachelor's degree in science, or equivalent related experience
- Five years related experience including three years management experience; related experience includes laboratory, pharmaceutical and/or GMP environment
- Primary schedule is Monday-Friday day shift, additional scheduling flexibility required to support 24/7/365 department
- Must meet NRC "trustworthy & reliable" requirements to participate in, & administer local compliance program for irradiator access
136
Additive Manufacturing Manager Resume Examples & Samples
- Responsible for identifying and pursuing new business opportunities where Additive Manufacturing technologies can be implemented
- Working with internal GKN development centers as well as external partners to identify competitive offerings using AM
- Establish strong relationships with key AM personnel from main customers
- Support in setting Market, Product and Technology strategies for the EPS business
- Help drive and prioritize Research and Technology (RoT) initiatives regarding AM, based on market need and opportunities
- Drive a behavior of Growth and promote a culture of innovation and constant search for new business opportunities within the organization
- Drives increased revenue and profit to achieve the EPS growth goals while building strong internal relationships with other Central Functions as well as external business relationships
- Effectively evaluate and analyze the competition for AM in the Aerospace market
- Work in close cooperation with CRD’s (Customer Relationship Directors) and Program Managers to grow the business through AM implementation
- Develops strategies and plans for AM-implementation with internal and external stakeholders and communicates same across relevant functions and to senior leadership
- Master's degree or equivalent work experience in engineering, or related discipline
- 5+ years’ experience in relevant roles required with excellent interpersonal and communication skills
- Strong technical knowledge of Additive Manufacturing techniques preferred
- Cultural flexibility and international business experience highly desired
- Excellent interpersonal skills and the ability to work with diverse and global internal and external customers
- Proven ability to network and communicate effectively at all levels of the organization
- Good presentation and communication skills
- Proven ability to manage multiple projects/issues and stay focused
- For further information please contact
137
Manufacturing Manager Resume Examples & Samples
- Leading the production team in the areas of safety, production, and quality control
- Leading the strategic direction of the manufacturing operation in the context of an ever-changing environment, including championing the implementation of WCM
- Leading the on-going production, trouble-shooting and continuous improvement of multiple technologies, process and packaging facilities and SKU’s
- As a member of the site Leadership Team, responsible for developing the strategic and long-term goals/vision for the facility and driving accountability at all levels to achieve these goals
- As the Autonomous Maintenance Pillar Champion the Site Production Manager has a key role in Culture change efforts
- Maintaining a close liaison with internal and external departments advising in production capabilities and plant operations (i.e., forecasting, financial, marketing and IT)
- Effectively managing the annual budget
- Developing a strong and supportive working relationship between management, the union and employees. This involves open communication, contract interpretation, and handling grievances to ensure a supportive and flexible culture
- Responsible for the Quality, Health and Safety performance of the site including completing root cause analysis for all issues
- Leading a team of supervisors in common ways of working towards both short and long-term goals to ensure success for the plant
- Developing employees for future roles within the organization
- Support quality and food safety programs including HACCP and FSCC-22000
- 7+ years of demonstrated success in a manufacturing capacity
- The ideal candidate will have demonstrated experience managing large scale change activities and union relations
- Experience in leading WCM in a foods manufacturing facility are ideal
- Excellent written, verbal and presentation skills
- Experience in most aspects of the Supply Chain (Make/Plan/Deliver/Source)
- Demonstrated ability to deliver large-scale change activities
- Proven Record of Accomplishment in People Development, particularly managing large teams
- Basic knowledge of Financial Supply Chain
138
Lean Manufacturing Manager Resume Examples & Samples
- Work closely with Plant Management to develop current and future state maps for the manufacturing Plant. Develop the plan on how to get to future state
- Manage and drive large strategic projects using Lean Sigma tools
- Develop and administer a productivity project deck that is based on biggest opportunity and supports the business objectives
- Responsible for developing an annual Kaizen event schedule and reviewing/revising periodically to better suit business needs
- Accountable for business results and responsible for measuring results
- Manage NB Plant facilities personnel, including coaching others to success and conducting employee performance appraisals
- Setting the stage for the best practice sharing, i.e., benchmarking against other companies, preparing any tools, materials, etc. in such a way that they are applicable across the business
- Oversee training for plant personnel
- Participate in Corporate Lean Sigma events, conference calls and meetings, as applicable
139
External Manufacturing Manager Resume Examples & Samples
- Q and EHS Compliance/ Supplier compliance metrics
- Must have
- Experience working in an international and cross-functional environment
- Knowledge of compliance requirements (cGMP, GMP’s, DEA, etc)
- Cultural sensitivity – previous exposure to cultural diversityContract Manufacturing
140
Senior Manufacturing Manager Resume Examples & Samples
- The Production Manager is a key position within Operations. The successful candidate will be responsible for daily production of laser systems
- Direct activities in production area to meet production goals, quality, and cost objectives
- Develop and ensure execution of production schedules based on staffing, equipment efficiency, and materials supply
- Develop staffing requirements for assigned areas
- Hire, develop, and evaluate qualified personnel to ensure efficient operation of production line
- Coordinate direct labor production and training activities
- Maintain up to date certification records, production travelers, and methods documents
- Lead Lean projects in manufacturing
- Receive, stock, and issue to the production line all materials needed for production and engineering requirements
- Maintain inventory integrity through orderly organization of stockroom, cycle counts, and physical inventories
- Perform material handling tasks as needed to keep the production line adequately supplied with production materials
- 5+ years of production supervision experience in high-tech industry
- Excellent leadership and people skills
- Solid management skills
- Familiar with Lean Production and Six Sigma principles
- Oracle 11i and Agile business suite experience also desired
- Proficiency with standard desktop software (Outlook, Word, Excel)
- Self motivated, driven personality
- Must work well in teams
141
General Manufacturing Manager Resume Examples & Samples
- Plan, prepare, issue and control production schedules and coordinates with material requirements to ensure a controlled flow of approved materials timed to meet production requirements
- Accountable for ensuring that the overall budgets, schedules, compliance and performance standards are met
- Determine and establish the reporting structure and supervisory relationships within the organization
- Develop strategic plans to promote and develop talent in the organization to ensure successful knowledge transfer and succession planning
- Accountable for positive employee relations and overall employee engagement targets are met
- Communicate regularly and influences all levels of the organization, including external customers, on matters related to the performance and technical capability of the operations
- Advise management of the status of work-in-progress, material availability, and potential production problems to ensure materials and services are provided as needed
- Coordinate interdepartmental activity with quality assurance, production and inventory control, supply chain management, purchasing, engineering, etc
- Additional scope of responsibility will include new build production, as well as overhaul and repair (O&R.)
- Bachelor's degree with 5 years of experience in a manufacturing setting
- Must have at least ten years of progressive leadership experience, experience leading highly effective teams directly or indirectly
- Understanding of process controls and compliance oversight and ability to apply business based analysis
- Ability to communicate throughout the organizational structure
- Must be an excellent communicator, both written and verbally, with the ability to motivate on a one-on-one basis as well as in large presentation forums
- Must demonstrate leadership skills and behaviors that align with the companies Leadership Characteristics, Vision and Values
- Must have demonstrated customer confidence and credibility, including the ability to understand and interface with customers and senior leaders of the organization
- MBA or master’s degree in related discipline preferred
142
Toll Manufacturing Manager Resume Examples & Samples
- Ensure Syngenta HSES and quality policies, Crop Life and good stewardship are understood and adopted by the toller; enforce appropriate management processes of the toller
- Address any significant operational issues that arise with the toller appropriately
- Support HSES and quality audits and drive timely response on findings and action plans
- Investigate complaints and ensure resolution through the appropriate interfaces
- Measure toller performance and drive continuous improvement where appropriate
- Lead/participate in selected projects, including product introductions, issue resolution
- Proven professional experience in a supply chain, procurement or technical role
- Working experience in a manufacturing environment
- Basic understanding of formulation, fill & pack technology and processes
- Good grasp of 3rd party relationship management
- Good knowledge of HSE, Quality and Regulatory compliance frameworks
- Strong stakeholder management
- Self-starter/autonomous
- Experience of the Chemicals industry
- Additional European language
143
Manufacturing Manager Resume Examples & Samples
- Primary point of responsibility for plant daily operations management for the site
- Ensures optimization of all production activities for multiple product lines including productivity and cost control. Adheres to key premier performance metrics
- Develop plans for efficient use of materials, machines, and team members
- Review production cost, quality, and modifies production and inventory control programs to maintain and enhance profitability of the plant
- Plan and implement overhead and capital budgets for manufacturing operations
- Implement lean manufacturing principles based on Ingersoll Rand’s operating system including effectively managing problem solving, standard work, manage daily improvement, and 5S activities
- Develop and coach direct and indirect reports to build capability and drive employee engagement
- Facilitates daily GEMBA walks with hands-on approach with productivity improvements
- Responsible for the implementation, support and compliance of the operations standard work playbook processes and systems including conducting layered audits
- Facilitates with manufacturing engineering, materials, safety, quality, human resources, OPEX, finance as well as corporate functions in support of the business’ strategic goals
- Provide leadership in selecting, developing and evaluating personnel to ensure the efficient operation of materials functions and Ingersoll Rand’s operating goals and objectives
- Develop and implement a professional development program for operations personnel
- Ensure alignment of the production plan to the published scheduling plan
- Ensure production equipment, tools and processes have minimal downtime through proper preventive maintenance
- In-depth knowledge of assembly operations and manufacturing material flow in a manufacturing environment
- Must possess a strong customer service orientation and provide dedicated support of internal customer requirements
- Must be a proactive change agent and possess leadership skills to build and maintain a team oriented environment while leveraging lean methodologies
- Must have solid interpersonal skills with the ability to motivate staff and to interact with various departments throughout the organization
- Must be a flexible, decisive and proactive problem solver
- Must know how to influence bottom line results
- Must be a strong communicator and possess strong organizational skills, with ability to work on multiple priorities at once
- Must be able to work well in high pressure, fast-paced environment and be proficient at conflict resolution
- Must be proficient in information technology systems utilized in manufacturing operations
- Bachelor’s degree in business or engineering discipline (MBA desirable)
- A minimum of 8 years of experience in the integrated functions of manufacturing operations management in a manufacturing environment that has embraced lean concepts, MRP manufacturing practices, and strong quality processes
- Experience in operations, inventory management, quality, MRP and lean manufacturing processes
- Working knowledge of HR / labor management experiences
- Proficiency in launching new products and engineering changes
- Lean certification or Six Sigma certification is a plus
144
Manufacturing Manager Resume Examples & Samples
- Manages work assignments in staffing, scheduling, coordinating, and planning of personnel engaged in manufacturing engineering activities in order to meet customer requirements
- Oversees the development and implementation of manufacturing processes to maintain proper product functionality as well as cost efficiency through development and implementation of product assembly labor standards and work instructions, line layouts, properly designed and maintained tools and fixtures
- Monitors employee job performance such as attendance, quality, and productivity
- Ensures that all assigned personnel are properly trained and cross-trained as required
- Supervises assembly of cost control and statistical data
- Prepare documents as required in support of pursuing new business
- Prepares and controls departmental annual budget
- Reviews equipment maintenance logs to ensure that operational performance is maintained
- Encourages and nurtures a culture of continuous improvement activities such as Lean, Six Sigma, and Kaizen
- Develop, implement, and monitor written polices, processes, and procedures to maximize the effectiveness of the manufacturing operation and assigned staff
- Interfaces with all support functions such as quality, design engineering, materials, and production control to ensure that products are produced with the highest level of quality at the lowest cost and delivered to the customer on time
- Administers personnel functions, including recruiting, review and approval of job descriptions and salary classifications, and selection and placement of personnel
- Follows all policies and procedures in a legal and ethical manner
145
Manufacturing Manager Resume Examples & Samples
- Lead, manage, and develop 36+ direct reports and one supervisor across 3 shifts
- Engage the leadership team in strategic planning and strategy deployment
- Develop strategic plan that accounts for capabilities and limitations to ensure key metrics are met or exceeded
- Daily production/ manufacturing leadership
- Drive employee development and grow cross-functional skill capabilities through implementation and support of cross training
- Lead and drive Total Associate Engagement (TAE)
- Develop operational priorities based on production integration, equipment efficiency, material availability, and budgeted financial targets
- Coordinate Operations and Engineering efforts to address manufacturing issues
- Lead root cause/ countermeasure actions to resolve SQDIP gaps
- Initiate, innovate, and implement process changes to achieve company goals, including justification of capital equipment and utilization of new technology
- Lead and participate in Lean Enterprise activities, including Kaizen and process mapping events. Regularly uses Lean tools to solve problems
- Utilize continuous improvement activities through Rexnord Business System (RBS) to achieve KPI targets each year
- Drive quality initiatives to ensure year over year quality improvement
- Support facility safety and environmental initiatives
146
Senior Manufacturing Manager Resume Examples & Samples
- 3+ years as a Site or Production Manager in a manufacturing setting
- Chemical or Plastics experience preferred
- Medical or healthcare manufacturing a plus
- 5s and/or Lean Manufacturing experience
147
Manufacturing Manager Resume Examples & Samples
- Leads the plant operations managers, team leaders and team members in the manufacture of multiple lines of production across multiple shifts of operation
- Leads human safety and food safety initiatives
- Tracks key indicators of the production team’s performance including safety, efficiency, waste, downtime, labor costs, and industrial accidents and communicating these indicators to the team for further action
- Recognizes areas of needed performance improvements
- Organizes production activities in timely and cost-effective fashion to ensure that internal and external customer needs are met
- Participates as an active member of the Plant leadership team and attends meetings as required
- Interviews and assists with the hiring process for job applicants
- Ensures that all production requirements are met cost-effectively and safely
- Communicates the importance of GMP (Good Manufacturing Practices) compliance
- Supports facility audits
- Supervise and motivates team members by setting a good example with regard to attitude, work quality, safe practices, attendance, follow-through and organization
- Expertly trains or arranges training for assigned personnel on production-related topics
- Monitor performance and provides vacation approval for managers
- Mentor and coach manufacturing managers and team leaders on improving performance
- Provide performance counseling as needed
- A Bachelor’s degree in Food Science, Engineering, Business Management, Supply Chain Management or related field of study. Master’s degree is a plus
- Experience and additional training in: Lean Manufacturing, Continuous Improvement, Six Sigma, BRC/SQF and AIB are ideal
- Requires a minimum of 5 years in a production management role in a food, beverage or CPG environment
- Strong understanding of Microsoft Office suite and manufacturing systems
- Advanced verbal, reading, writing, mathematical and cognitive skills
- Demonstrated leadership experience, as well as building teams and the ability to work well with in a diverse culture
- Successful track record of achieving budgeted results while improving operations
- Ability to effectively collaborate with other senior managers to achieve Company and customer goals
- Demonstrated skill in coaching, motivating and team development
148
Manufacturing Manager Resume Examples & Samples
- Responsible for managing the activities within a production area to meet production, cost, quality and safety goals
- Plans, organizes and implements manufacturing procedures in accordance with managed quarterly and annual budgets
- May make budgetary recommendations and coordinate procurement for capital expenditures
- Selects, hires and trains personnel
- Bachelor's Degree or equivalent experience
- 8+ years’ experience in a production environment
- 3+ years’ management experience
- Good communication and interpersonal skills
- Knowledge of principles, concepts, theories and practices of area of responsibility
149
Manufacturing Manager Resume Examples & Samples
- Manage all operations in relevant areas of responsibility
- Meet budget and schedule objectives for the manufacturing process
- Provide employees with the necessary guidance, counseling, and tools to manufacture products using raw materials such as titanium, fiber metal, etc
- Manage the machining, polishing and testing functions
- Supervise a team of hourly, administrative/technical and exempt employees
- Creative thinking and problem solving skills to continually improve the manufacturing process
- Utilize leadership and motivational skills to expedite completion of critical project tasks with other functional groups
- Establishes manufacturing methods which meets performance and quality requirements
- Strong project management skills with the ability to coach, develop, and manage staff
- Proficiency with PCs using Microsoft Office Suite
- Demonstrated ability to learn and apply multiple skill sets determined by areas of responsibilities
- B.S. in Engineering or related field with 6-8 years of progressive experience in manufacturing engineering, operations or related field, or an equivalent combination of education and experience
- Some management experience preferred
150
Manufacturing Manager Resume Examples & Samples
- Cross Functional: Problem Solving Techniques, Lean Six Sigma, Cost Management, Budget Management, Manufacturing Industry, Managing Direct Reports, Leadership Experience
- Manufacturing: Safety Procedures and Manufacturing Operations
- Personal Skills: Conflict Resolution, Time/Priority Management, Work on a Team, Reading/ Comprehension, Stress Management, Training/Mentoring Others, Self Motivated, Organizational Skills, Analytical Skills
- Software Skills: Microsoft Excel and Word, SAP
151
Manufacturing Manager Resume Examples & Samples
- Optimize inter-organizational and external contacts
- Supervises multiple employees, several disciplines. Operations oriented to include exempt-level employees and/or supervisors
- Maintains high performance management
- Responsibilities for employees to include direction, hiring, firing and promotion decisions
- LI-AJK
152
Manufacturing Manager Resume Examples & Samples
- Works to increase productivity through the elimination of non-value added processes/ material by analyzing the layout of equipment, workflow, assembly methods and work force utilization
- Oversees and directs production control, assembly and sheet metal fabrication in order to minimize lead times and meet or exceed organizational on time delivery targets
- Diligently monitors material requirements coordinating closely with sales, Supply Chain Manager and purchasing to ensure appropriate inventory is maintained to satisfy customer demand
- Supervises and develops subordinates; establishing and prioritizing goals along with associated improvement actions
- Closely monitors product quality throughout the manufacturing process, taking swift and appropriate action when necessary to ensure customer satisfaction while minimizing warranty, rework and scrap expenses
- Conducts ongoing assessments of the manufacturing facilities and equipment initiating improvements and monitoring preventative maintenance for machinery
- Creates thorough and efficient manufacturing plans in support the timely launch of new products
- Creates and maintains up to date standard work instructions for various manufacturing processes, as appropriate
- Plans and directs production activities and establishes production priorities for products in keeping with effective operations and cost factors, including ISO and ATEX requirements
- Determine staffing requirements, interview, hire and train new employees and/or oversee those personnel processes
153
Manufacturing Manager Resume Examples & Samples
- Provides strategic and tactical direction for the plant and related integrated supply chain activities and assists in the development of the business strategy
- Develop and execute strategies for increased customer satisfaction, safety, quality, delivery, productivity, cost, working capital management, and effectively introduce new products/processes for growth
- Ensure that financial productivity and plant/product transition projects are successfully executed
- Build consensus across functional and lines of business, working with multiple internal and external customers and stakeholders
- Oversee and promote effective Health, Safety and Environmental programs and practices, ensuring that high standards of site safety are established, met, and that facilities and grounds are maintained in accordance with relevant regulations, agency standards and fiscal considerations
- Required to lead organization through the HOS deployment process and maintain performance levels stated by HOS maturity scorecard; including visual management and the tiered meeting communication process
- Develop and maintain an effective supervisor leadership team
- Improve and develop organizational capabilities through effective performance management and planning/utilization of human and capital resources
154
MJF Benchmarking Manufacturing Manager Resume Examples & Samples
- Develops and implements parameters and test plans for new and existing designs, including validation of mechanical, electrical, software, and other engineering specifications and requirements
- Leads a project team of other engineers and internal and outsourced development partners to develop reliable, cost effective and high quality solutions for moderately- complex products
- Provides guidance and mentoring to less- experienced staff members
155
Manufacturing Manager Resume Examples & Samples
- Execute operational plans including performance targets and budgets
- Develop and lead the execution of plans to meet all required Safety, Quality, Delivery and cost targets. Set standards of performance for personnel
- Promote and deploy the use of continuous improvement techniques and practices (lean mfg., 5S, factory physics, etc.).Assure internal metrics and improvement efforts support company goals and objectives
- Analyze operational data and use sound manufacturing science to make real time priority adjustments to optimize cycle time and output
- Manage a team of employees to meet departmental goals via appropriate allocation of workload and effective resource management
- Interview, select, train, and develop new employees
- Evaluate employee work and productivity and monitor for process adherence and compliance
- Formulate performance improvement plans and make termination decisions as necessary
- Ensure compliance with all local, state and federal laws
156
Manufacturing Manager Resume Examples & Samples
- Direct and lead all production and production support departments to satisfy internal and external customer requirements while ensuring Quality policies are followed within production, materials and maintenance departments
- Ensure operational efficiencies are achieved and focus is directed to cost control and continuous improvement
- Lead, manage and control all parts availability and inventory accuracy levels from stores and within the plant
- Improve Health and Safety performance in departments under direct control. Ensure safe systems of work are in place and adhered to. Ensure process improvements are implemented as a result of accident/incident investigations. Ensure environmental policies are followed within production, materials and maintenance areas
- Develop, implement and review DFT strategic plan for manufacturing and production support departments. Benchmark other companies and develop appropriate new strategies
- Implement product and process changes
- Minimum 10 years experience in a leadership role
- 3rd level degree or five (5) years experience in Engineering based plant
- 3rd level degree or five (5) years experience in materials discipline
- 3rd level degree or five (5) years experience in maintenance discipline
- Minimum of five (5) years experience in developing, tracking and delivering AOP plans and a clear understanding of overhead absorption and product costing process
- DFT knowledge
- Project Management knowledge – practical involvement in leading projects and utilizing IT tools to manage projects
157
Manufacturing Manager Resume Examples & Samples
- Safety and Environmental performance: Communicates expectations; conducts audits, investigates and documents all incidents; conducts safety meetings; authorizes work and signs permits; participates on the plant safety committee
- Production: Determines requirements and assigns personnel to each line to assure efficient operation; monitors operations including run rates, changeovers and line cleans; coordinates with maintenance, lab and warehouse personnel to meet line production expectations; troubleshoot process issues and determine the appropriate course of action to resolve; oversee the development/revision of operating procedures; identify and participate in documentation of Management of Changes
- Quality: Reviews finished goods laboratory test results; reviews in process test results; determines process running condition changes to be made; solicits input from tech support as needed; participates in on-site customer audits; participates in ISO audits; participates in customer trials/trial reviews; participates in complaint investigations
- Staffing; Participates in plant staffing activities including interviewing and selection. Conducts performance reviews for direct reports and ensures performance reviews are conducted for all operations personnel; recommends wage increases and promotions; identifies and prioritizes personnel developmental needs; conducts disciplinary discussions; reviews staff assignments; develops and communicates work schedules for production lines and assigns staff as needed
- Maintenance: Supports the PolyOne Reliability Program by coordinating shift maintenance activities and audits equipment checklists to verify proper monitoring by operations. Ensures work orders are written and entered into e-maint for scheduling; schedules line downtime as required for proactive maintenance
- Learns and uses all appropriate systems which may include SAP, IQS, LRM, CCS, CAID Charts, E-time, Ariba on Demand, Microsoft Office applications
- Financial: Must understand and manage financial performance from a cost to manufacture standpoint for lines assigned to them
- LSS: Must drive Lean Six Sigma events to improve overall performance for assigned lines
- Other projects/duties as assigned or needed
- Bachelors of Science degree. (In lieu of degree requirement, may accept four or more years of additional applicable process/manufacturing experience will be considered)
- Five or more years of manufacturing experience as well as previous supervisory responsibilities
- Computer skills: Proficiency with Microsoft Office applications required (MS Word & Excel)
- Strong organizational & problem-solving skills required
- Excellent oral and written communication skills required
- Knowledge of plant's manufacturing systems and processes
- Knowledge of budgeting, data collection and capital equipment analysis
- Knowledge of Lean Six Sigma processes and methodologies
158
Manufacturing Manager Resume Examples & Samples
- Management of, as well as participation in, fill/finish operations and all ancillary operations, such as component preparation, environmental monitoring, raw material testing and release, process and equipment validation, etc. All of the aforementioned duties and functions are subject to compliance with cGMP regulations
- Recommend, evaluate and/or procure new equipment, as needed
- Assure adherence to project budgets and timelines and plan and schedule activities accordingly
- Prepare and review process documentation
- Supervise 2-3 employees
- Bachelor’s degree from an accredited college/university according to the Council for Higher Education Accreditation (CHEA) in a scientific discipline or equivalent, or four (4) years of experience in lieu of a degree. Foreign degrees must be evaluated for U.S. equivalency
- A minimum of six (6) years of experience related to cGMP-compliant manufacturing operations, including two (2) years of experience in a leadership capacity
- Thorough knowledge of biopharmaceutical manufacturing operations, particularly with respect to aseptic processing and fill/finish operations
- Complete understanding of cGMP regulations relating to manufacturing operations
- Knowledge of regulatory issues related to products manufactured under cGMPs
- Ability to manage projects with diverse scopes
- Experience in other areas of cGMP manufacturing
- Experience performing analytical testing and working with analytical equipment
- Supervisory experience
- Experience with Flexicon monoblock filling unit
159
External Manufacturing Manager Resume Examples & Samples
- Manage China IC Assembly & Test subcontractors manufacturing execution including delivery, cycle time, yield and quality requirements
- Manufacturing Capacity Management and consigned Inventory management in subcontractors
- Work with Quality team to resolve any reported customer quality issues and drive continuous quality improvement with the subcontractors. Ensure that all customer audits and visits are well prepared and managed
- Perform assessment and qualify new China subcontractors to support business growth and improving profit margin
- Bring up new identified subcontractors in China to meet NXP requirements from Technical, Operational and Quality aspect
- This position is located in Shanghai, China. Frequent travel to visit subcontractors is required
- University degree in Engineering/Science
- More than 10 years work experience in IC assembly industry. Familiar with IC package assembly process and manufacturing operations
- Demonstrated experience on NPI start-up, production operation management, package yield & cost improvement,
- Good project management skills and able to work collaboratively with global organization. Ability to lead within a matrixed organization
- Demonstrated knowledge & application of statistical process controls, quality concepts & DOE
- Good Communication skills, Fluent in both spoken and written in English and Chinese
- Familiar with local China work practices and able to drive local subcontractor to change work culture to meet international work practices
- Experience in IC manufacturing subcontractors management is preferred
- Knowledge in bumping and flip chip is an added advantage
- Knowledge in wafer test and final test is an added advantage
160
MTB Assembly Manufacturing Manager Resume Examples & Samples
- Plan and Decide Production Priorities and Strategies
- Plan resources (ppl, machines, logistics) based on MPP (Manufacturing Production Plan)
- Attend daily thruput meeting - involving assembly manufacturing, Area planners, Engineering groups
- Execute production according to MPP and monitor production linearity
- Liaise with support groups to meet manufacturing needs
- Plan and implement continuous improvement activities
- Manage On-Shift Production Resources
- Discuss with shift supervisors to review production needs and issues
- Develop a plan to recover capacity requirements at critical process steps
- Walk the line to monitor safety, housekeeping and line discipline/compliance
- Maintain quality standards
- Ensure quality protocols/requirements are in compliance
- Review quality issues with the supervisors and follow up on neccessary corrective actions
- Plan and implement continuous quality improvement activities
- Participate in EO (Effective Ownership) audits and other internal/external audits
- Manage Team Members (Direct and Eventual Reports)
- Establish and comminucate performance goals for team members
- Monitor performance of area supervisors, process cordinators and provide ongoing performance feedback, mentoring, and career guidance
- Manage and track data for IPP (Incentive Performance Plan)
- Review team members training needs (using TNA - Training needs Analysis)
- Ensure training and cross-training goals are met for team members
- Develop team members for leadership positions
- Take part as an assessor during the JLSA (Junior Leadership Situational Assessment)
- Maintain a Safe and Clean Work Environment
- Ensure all established EHSS (Environmental, Health, Safety, Security) policies, requirements and procedures are met
- Report conditions or behaviors that are contrary to EHSS policies or procedures
- React to safety incidents and alarms by ensuring proper resources are notified
- Communicate issues and actions taken to staff to reinforce safety expectations
161
Primary Manufacturing Manager Resume Examples & Samples
- A degree in engineering from a recognised university / institute
- 2 to 3 years’ industry relevant experience
- Possess excellent leadership and team working skills
- Be a self – motivated individual with a proactive nature
162
Manufacturing Manager Resume Examples & Samples
- Minimum 5 years of work experience in manufacturing
- Minimum 3 of years of supervisory experience in manufacturing
- Management experience in heavy industrial manufacturing
- Experience in the forging or other metal working industry
- Experience with AS9100 Quality standards
163
Manufacturing Manager Resume Examples & Samples
- Bachelor’s degree required; Bachelor’s degree in an engineering or technical field preferred
- 8+ years of related business experience required
- 5+ years of experience in manufacturing and/or equipment development and/or project management and/or installation and qualification required
- 3+ years of experience managing direct reports as a Facilitator and/or Manager required
- Statistical and analytical problem solving required
- Experience in the medical device and/or pharmaceutical industry preferred
- Lean experience or training preferred; Lean certification highly preferred
- Experience managing compliance associated with quality and/or regulatory and safety policies preferred
- Previous experience working in a FDA and/or another regulated environment is preferred
- Computer proficiency required including Microsoft Office and database management skills; advanced computer skills preferred
- Requires up to 10% domestic and international travel6068170323
164
Manufacturing Manager Resume Examples & Samples
- Develop and execute strategies for safety quality, delivery and cost initiatives for respective business unit
- Champion a high commitment and performance culture by actively communicating MBCI’s vision, mission and values – anchored in MBCI’s Four Basics and 6 for Success
- Champion MBCI’s Zero Injury Mission through demonstrated commitment to the Always Aware program, site specific safety plans and targeted MBCI initiatives
- Establish, improve, sustain and report KPI performance; leverage data to prioritize actions and drive continuous improvement
- Drive customer satisfaction through strict adherence to product specifications, open communication, and timely follow-up
- Develop and manage business unit operating budget; ensure achievement of financial objectives
- Identify and implement measures to improve production methods, equipment performance, and quality of product
- Recruit, manage and continuously develop the business unit leadership team, engineering, quality and other support staff to achieve departmental and plant objectives
- Interpret and enforce company policies, rules, and safety regulations and quality methods to supervisors and employees
- Analyze and resolve work related issues/problems/complaints, and/or assist production supervisors in solving work related issues/problems/complaints
- All other duties as may be assigned at management's discretion
- BS in Engineering, Business or a related required; advanced degree or professional manufacturing certification(s) preferred
- 7+ years leadership experience with a large manufacturing organization
- Proven track record of building a team, managing change, streamlining processes and driving safety, quality, delivery and cost improvements
- Strong working knowledge and application of lean manufacturing principles; furniture industry experience preferred
- Strong analytical, problem solving, delegation, and conflict resolution skills
- Exceptional leadership, interpersonal, and organizational skills
165
Manufacturing Manager, Biopharmaceutical Resume Examples & Samples
- Possession of Master’s degree from an accredited college/university according to the Council for Higher Education Accreditation (CHEA) in a field related to biomedical research/scientific discipline or six (6) years relevant experience in lieu of degree
- PhD preferred
- In addition to educational requirements, a minimum of ten (10) years of progressively responsible job related experience including four (4) years of experience in a leadership capacity
- Must be detail-oriented and possess strong organizational, analytical and problem solving skills with the ability to prioritize multiple tasks/projects of highly complex scope
- Demonstrate strong communication skills, analytical ability and solid interpersonal skills
- Ability to perform job requirements independently and in team environments and must have ability to interface with all levels of management making decisions regarding complex issues
- Develop and maintain manufacturing operations under cGMP compliance
- Possess knowledge of production-related principles of biopharmaceutical development and production processes
- Working knowledge of cGMPs as they relate to biopharmaceutical manufacturing
- Ensure quality control and fiscal planning
- Ability to work in high-pressure, time-sensitive situations; ability to multi-task and appropriately handle competing priorities
- Proficiency in Microsoft Office® inclusive of Word, Excel, Access and PowerPoint
- Principles of timelines within Microsoft® Project
- Familiarity with interactive databases quality assurance, quality systems, auditing, metrics analysis, cancer
166
Manufacturing Manager Resume Examples & Samples
- Bachelor Degree in Science or Engineering is required; Master degree is preferred
- PMP/FPX and/or Process Excellence certifications are highly preferred
- 5 to 8 years of experience in medical, consumer or pharmaceutical environment is required
- A minimum of 3 years of supervisory experience is required
- Knowledge in OEE is required
- Experience in project management is required, including individual projects and project portfolio
- Proficiency in Spanish & English is required
- Advance computer skills and use of software applications such as: Excel, Windows, others
- Knowledge of Statistical Process Capability and quality standards is required
- Strong organizational, interpersonal, oral and written communication skills is required.5750170323
167
Manufacturing Manager Resume Examples & Samples
- Minimum of 5 years’ experience in engineering and/or operations function within a manufacturing environment
- Minimum of 3 years’ experience in a management or leadership role
- Bachelor’s Degree in Engineering is preferred, from an accredited institution
168
Manufacturing Manager Resume Examples & Samples
- Creates, implements and drives key safety initiatives, assuring resources are sufficient to create a zero and beyond (accident free at work and offsite) culture
- Determines appropriate skill sets for operators throughout the plant. Works to improve operator flexibility, work assignments and reduce labor costs
- Champions, with Cell Leaders, operator led process control, lean manufacturing and six sigma concepts
- Responsible for total production of cell metrics including safety, production quantity, customer service, defect levels, waste, work order attainment, etc
- Trains and facilitates Cell Leaders in achieving improved productivity and reduction of waste
- Analyzes KPIs, prepares charts/records and initiates remedial action
- Coordinate the maintenance of manufacturing data systems necessary to support the manufacturing process, and provide information for budgeting, capacity and planning processes
- Promotes “on-the-spot" problem solving activity, supporting associates in cells with decisions and needs and ensuring progress toward operator led process control
- Maintains a visible and vocal presence as the shop floor leader
- Results driven individual who has demonstrated ability managing in a high performance-manufacturing environment
- Critical thinker with excellent analytical abilities
- High energy, demonstrates urgency and fast pace
- Good understanding of business principles and practices
- Familiarity with Six Sigma and lean manufacturing
169
Manufacturing Manager Resume Examples & Samples
- Directs teams through department managers and shift department managers for all work activities of production departments, coordinating all departments and shifts into a cohesive manufacturing unit
- Selects and trains team leaders, production supervisors and other positions that help lead the manufacturing effort. Makes sure that their practices are consistent with authorized procedures
- Coordinates the activities of production with those of production control associates to insure that work is produced on a schedule in a balanced flow method fully utilizing essential tools such as Just- In- Time, Materials Requirement Planning, Cycle time Reduction, etc
- Work the manufacturing team, coordinate the activities of production with those of quality assurance personnel to insure that specifications and quality levels are met, and production ands maintenance areas are assured to be in compliance with ISO standards
- Coordinate the activities of production with those of Industrial engineers personnel to insure that labor, materials utilization standards are optimized and manpower leveled are monitored and adjusted, and actions to be taken for maintenance problems
- Direct teams in a manner to achieve proper motivation, performance, reward and discipline of production supervisors, and through them and their teams, to all production associates
- Enforce and be aware of all safety requirements
- 7 - 10 years’ experience in manufacturing management
- Managerial experience in a team based environment
- MRP systems implementation experience
- Strong database background, comfortable with a variety of software systems, including spreadsheets
- Strong manufacturing backgrounds; able to understand and develop appropriate product specifications
170
Manufacturing Manager Resume Examples & Samples
- Plans and oversees work to meet production and quality requirements while making effective use of labor, material, and equipment
- Directs associates to maintain operating efficiency
- Evaluates selection of new associates in hiring process
- Conducts training on new procedures and oversees new hire training
- Ensures operations are within specifications
- Establishes, maintains, and analyzes budgets, records, and other controls to keep costs at a minimum consistent with efficient operations
- Assures adherence to operating standards, assists in the Coordination of production schedules and budget planning
- Coaches and reviews performance of direct reports
- Reviews the production schedule in close collaboration with planning
- Manages plant production change overs to ensure adherence to production schedule
- Ensures plant production numbers are updated on all display boards in the different plant areas in collaboration with the plant supervisors and leads
- Stand in for the Plant Manager as and when required
- Daily coaching on safety, quality and production with all team members
- Actively involved in all process improvement and plant performance monitoring programs
- Ensures safe and healthful working conditions and an organized work environment
- Partners with maintenance and engineering for departmental operations
- Performs others duties as assigned
- 5 or more years of operations experience (Education counts towards experience). Minimum of 2 + years supervisory experience. Ceramic tile industry experience preferred. Mechanical/Electrical concepts and theories
171
Manufacturing Manager Resume Examples & Samples
- Responsible for the hands-on, daily supervision of GMP manufacturing operations and personnel
- Participate in all aspects of personnel management (interviewing, training, coaching and developing). Assist with developing strategic staffing plans
- Work effectively within the management team to execute goals, objectives, and tasks to achieve desired results
- Responsible for day to day operations in the GMP manufacturing suite. Specific responsibilities will include
172
Manufacturing Manager Resume Examples & Samples
- Create safety awareness by actively observing, auditing, and coaching safe work behaviors and conditions. Ensure compliance with Company Policies, Safety and Health Programs, safety and environmental rules and regulations as well as housekeeping standards
- Maintain the daily operations to assure customer specifications and requirements
- Direct, lead, and execute the long and short term strategies to ensure sustainable results that meet or exceed financial and operational targets
- Manage operations to meet or exceed planned budgets
- Plan, manage and direct manufacturing activities to achieve production, quality, scrap and safety goals
- Enforce established work rules and operating policies consistent with the Company’s vision and mission
- Ensure proper execution of policies and procedures within areas of responsibilities
- Oversee and coordinate all production department activities to meet quality standards and production schedules
- Ensure utilization of machines, materials and manpower to the best interest of the Albertville facility
- Assist the Plant Controller in the formulation and establishment of realistic annual budgets for all departments to meet established budgets
- Ensure the operations meets its monthly safety, delivery, quality, production, inventory and financial metrics
- Actively participate in the Strategy Deployment process
- Develop a high performing, data driven culture that deploys lean enterprise techniques to target and drive continuous improvement in every function and aspect of the business
- Partner with the Human Resource team to link individual performance with the achievement of organizational goals. Conduct performance appraisals for all direct reports
- Track and leverage manpower to drive optimal productivity
- Optimize inventory in support of JIT (just in time) requirements
- Assist staff by recruiting, selecting, orienting, and training employees; developing personal growth opportunities
- Maintain work flow by monitoring steps of the process; setting processing variables; observing control points and equipment; monitoring personnel and resources; studying methods; implementing cost reductions; developing reporting procedures and systems; facilitating corrections to malfunctions within process control points; initiating and fostering a spirit of cooperation within and between departments
- Maintain working relationship with the union by following the terms of the collective bargaining agreement
- Maintain the machining operations in a safe, neat and orderly manner by promoting good housekeeping and safety policies
- Prepare and monitor daily and weekly shift work plans and staffing in conjunction with production control; monitor and assure proper staffing of trained personnel in all key operational areas of the manufacturing department; immediately apprise the plant manager of any significant quality or productivity problems to assure immediate corrective action
- Provide direct supervision as well as motivational and training support to all hourly union employees in their department. Perform in a leadership role in implementing the policies and directions of the manufacturing manager as well as Company policies and goals for production, quality, efficiency and safety
- In coordination with production control, quality control and purchasing personnel, achieve perform-to-schedule goals. Work with maintenance and human resources personnel, within specific directions by the manufacturing manager, to achieve maximum production and staffing “up-time” consistent with trained manpower and equipment availability
- Participate in quality and safety reviews and audits to maintain and improve the ISO-9002 implementation of work procedures and policies. Advise the manufacturing manager of challenges, problems, improvements, ideas and opportunities that are fostered by salaried and hourly workers
- Work with human resources personnel, under the direction of the plant manager, to understand and effectively relate to the union contract so as to maximize productivity and minimize disruptions to production while fulfilling all company commitments contained in the union contract in a fair and professional manner
173
Manufacturing Manager Resume Examples & Samples
- Perform research design and development of manufacturing processes including production flow, assembly methods and production equipment
- Prepare and maintain detailed layouts of equipment (schematics, SOP’s etc.)
- Support the conversion of small scale processes into commercially viable large scale operations
- Initiate, engineer, and coordinate major projects, (e.g., plant layout changes, machine design, process design, installation of capital equipment, major repairs, etc.)
- Develop and coordinate Quality Management System (QMS) compliance. Develop procedures, processes, programs, and practices, to assure the company of continuous conformance with appropriate standards and regulations
- Lead quality efforts including APQP activities and process control procedures to ensure integrity of data collection to maintain compliance with specifications and systems
- Interface with customers and suppliers as required facilitate quality discussions
- Follow safety rules and keep work area in a clean and orderly condition
- Hire, train, develop and evaluate staff. Take corrective action as necessary on a timely basis and in accordance with company policy
- Direct and coordinate various programs essential to manufacturing procedures (i.e., training, safety, housekeeping, cost reduction, worker involvement, security, etc.)
- Work effectively and relate well with others. Exhibit a professional manner in dealing with others, working to maintain constructive working relationships
- Perform miscellaneous duties and projects as assigned and required
174
Manufacturing Manager Resume Examples & Samples
- Experience with Cell Culture processes (perfusion systems is a plus)
- Experience with automated process equipment and control
- Working knowledge with disposable systems, filtration, centrifuge
- Experience with troubleshooting and problem solving with process and equipment
- Experience with Buffer and Media operations
- Broad technical knowledge in area of responsibility for and provide technical instruction on new/improved processes to appropriate audiences, primarily Manufacturing personnel
- May have in excess of 4 direct reports overseeing a group of 30+ to manage
175
Global Process & Digital Manufacturing Manager Resume Examples & Samples
- Several years’ experience as a sales/technical/engineering position in the Danfoss Power Solutions target markets
- Technical and commercial expertise related to connectivity, digitalization and Cloud technologies would be strongly preferred
- Knowledge on hydraulics and technical experience in products produced by Danfoss Power Solutions as well as related applications would be a plus
- Commercial experience working with different Sales Channels (B2B, Authorized Service Centers)
- Ability to work in a global environment in a matrix organization
- Bachelor’s degree in mechanical /electrical engineering discipline or sufficient experience in electronics/ analytics / hydraulic/ design or technical support
- Good knowledge of key IT tools (incl. SAP, salesforce)
- Excellent oral and written communication skills in German and English
176
Technical Production / Manufacturing Manager Resume Examples & Samples
- Ensure that the necessary level of quality technical management service is being provided by the Technical team to all the clients within the Region
- Coordinate with the Product Engineering Division to implement new products or processes
- Coordinate with the Costing Department to optimize all products
- Provide the required training to the Regional Technical Team
- Define and Manage the Value Engineering Process within the Region
- Provide support to Technical Marketing activities
- Bachelor’s Degree (4 Yrs) in Mechanical Engineering or equivalent
- 5 – 7 Years of Technical Management experience in the field of Fiberglass piping
- 6 – 10 Years of Engineering experience
- Knowledge of Composites and Fiberglass Piping design, manufacturing, and installation
- Experience in managing a medium-to-large sized technical department
- Detailed knowledge of Fiberglass Piping Component Design, System Design, and installation
- Detailed understanding of production methods and testing techniques for composite products
- Ability to act as an expert in composite design related issues within the department
- Ability to understand and link theoretical possibilities to practical limitations and possibilities
- Ability to analyse the costs and benefits of different designs and productions methods
- Ability to prioritise work on the basis of customer requirements and operational imperatives
- Exceptional communication skills and ability to work in a dynamic, fast paced, diverse environment
- Fluent in reading, writing, and speaking in English
- Prepare and deliver high level presentations to Clients and End Users
- Preparation of high quality professional reports
- Advanced knowledge and understanding of Excel use in solving engineering problems
177
Manufacturing Manager Resume Examples & Samples
- Responsible for the overall completion of work required to support all manufacturing activities in compliance with all regulatory requirements in a cost effective manner and in accordance with planned budget
- Plans, directs, and controls activities of supervisors and area leads in order to meet overall departmental and plant objectives
- Ensures that duties, responsibilities, accountability, and authority of all direct reports are defined and understood
- Develops and implements consistent department procedures. Communicates methods, policies, and procedures to managers and supervisors. Anticipates, investigates, and evaluates future process need
- Interfaces with all Management groups, including Customer Service, Quality, Materials, Finance, EHS and Human Resources in order to meet production, quality, and compliance requirements
- Ensures the use of ethical business practices in dealing with customers, employees, vendors, suppliers, and the community
- Performs as a resource for customers by providing expert advice and technical support throughout the production of a job and customer tours
- Analyzes trends to continually improve Operational Efficiency
- Implements and manages cost reduction and profit improvement programs
- Evaluates the current workflow, and creates improvements based on current needs
- Participates in identifying continuous improvement goals in Quality, Safety, Cost Control, Scheduling, Personnel and Compliance for the organization and plays a key leadership role in attaining those goals
- Responsible for pro-active people management. Sets the standards for performance assessment and feedback, effective communication, promoting positive morale and supporting team effectiveness
- Assess employee talent and capabilities, including issuing employee performance reviews
- Actively drives safety culture, ensures that safety policies and procedures are followed
- Maintains quality control at a level that meets or exceeds the demands of the individual jobs, maintains training in accordance with quality guidelines
- Bachelors Degree in Engineering, Manufacturing, Print Management or related field, or equivalent combination of education and experience in a manufacturing environment is required
- 5-10 years experience in the printing industry is required(web or sheet fed offset press)
- Experience with G7 Certification a plus
- Experience with 5S or Lean Manufacturing a plus
- Strong verbal and written communication skills required to exchange information with diverse types of personnel, customers and vendors
- Demonstrated success at managing a fast pace, highly transactional production operation
- Demonstrated sound executive judgment and keen business acumen that includes strategic thinking
- Proven ability to lead and guide others through high performance and participative management
- Proficient with MS Office, Google Apps and electronic job tickets
178
Manufacturing Manager Resume Examples & Samples
- Direct support of all operating production environments
- Assuring Daily targets and KPI’s are met
- Support and oversight of all personnel
- Direct involvement in individuals performance measures and reviews
- Daily interface with department supervisors and plant management
- Daily communications of tactical objectives, performance and underlying strategies to production personnel
- Lead training programs and coaching for personnel
- Responsible for plant emergency response, safety of plant personnel and equipment
- Minimum of High School Diploma or GED
- Previous supervisory experience in a fast paced machining/manufacturing environment is required
- Proven ability to lead teams and managing through influence
- Strong conflict management skills
- Strong technical background in mechanical and or manufacturing disciplines
- Previous Lean Manufacturing Experience is desired
- Strong interpersonal communications skills (oral & written)
179
Manufacturing Manager Resume Examples & Samples
- Driving continuous improvement
- Be an ambassador for our Zero Harm safety culture
- Ensure resources are aligned to deliver parts on time to program
- Optimise operations to deliver world class OEE
- Create and maintain good communication methods with all contributors in the supply chain both inside and outside of the department, engaging them in the challenge
- Make continuous daily improvement the norm
- Reporting KPI’s
180
Blood Component Manufacturing Manager Resume Examples & Samples
- Responsible for management of Manufacturing. Ensure all functions are performed in accordance with all applicable regulatory policies and/or procedures and in a timely manner to meet customer needs
- Serve as a resource for supervisors for complex technical issues
- Manage and evaluate workflow and processes to ensure efficient and streamlined manufacturing processes to meet customer demand and required timelines
181
General Manufacturing Manager Resume Examples & Samples
- Planning and program performance addressing cost, schedule, technical performance, and quality of a work package, subsystem, or related group of work packages on a large system development-type contract or full responsibility for all aspects of program performance on a large delivery order or mid-size technical services-type contract as related to aircraft maintenance programs
- Bachelors Degree and 6 years of relevant experience. In lieu of formal education, High School Diploma or equivalent (GED) and 10 years relevant experience
- Ability to navigate stands, lifts, ladders, work platforms etc
- Able to collaborate in a team environment and to negotiate and integrate different viewpoints
- Able to prepare and analyze data and figures to compose materials such as detailed reports, work‐related manuals, publications
- 8 years of experience in a program management field
182
Manufacturing Manager Resume Examples & Samples
- Oversee the management of production processes in accordance with the production schedule and product specification
- Ensure that cost and quality standards, in line with regulatory guidelines, company standards and current Good Manufacturing Practice are met
- Actively develops staff to drive increased effectiveness and readiness for internal promotion
- Develops and deploys strategy to improve process capability, right first time and productivity across operations
- Prepare, manage and control budgets for operational activities within the Newcastle ASR business
- Drives successful on time execution of projects and changes within operations to meet objectives effectively (right first time)
- Proactively engages with all relevant business functions to ensure align to Operations strategy and business goals
- Drive an improvement culture utilizing DBS tools within manufacturing operations to promote greater efficiencies and robust supply processes
- Assure all manufacturing activities are maintained to current Good Manufacturing Practices and within validated processes
- Drive “Best Team Wins” thinking to ensure the coordination of activities between Procurement, Planning and Global Supply chain to ensure effective and efficient supply of product to customers to meet demand
- Drive effective communication across the business on supply status. Leads communications plans in the event of low stock availability
- Ensure inventory control is undertaken utilizing kanban methodology where appropriate, at an agreed level to be cost effective while meeting production and customer needs
- Responsible for stock accuracy within operations and minimizing risk of financial write-off through monitoring and effective scrap avoidance actions
- Responsibility for the recruitment, training and appraisal of staff within operational departments
- Proven track record within a Production/Operations Management background
- Strong understanding of life science related production processes
- Experience of working in a strongly regulated environment (MHRA / FDA / ISO13485)
- Relevant, proven and demonstrable experience of working with and driving Good Manufacturing Processes
- Good understanding of process validation with experience of managing validated processes
- Demonstrable ability to promote, support and manage Lean Manufacturing activities
- Highly developed People management skills and experience within a technical operational setting
- Relevant experience of working within the life sciences sector is essential
183
Manufacturing Manager Resume Examples & Samples
- BSME or MSME - 7+ years of experience (BS) or 5 + years (MS)
- A minimum of 7 years in manufacturing engineering in the medical device industry
- A minimum of 5 years manufacturing engineering experience
- Supervisory/Management Experience
- Experience in high/low volume production
- Experience in production time studies with process/equipment optimization
- Production Transfer Experience (pilot to full production or another site)
- Proficient at SolidWorks
- Working knowledge of standard machine shop equipment
184
Manufacturing Manager Resume Examples & Samples
- Supervises the development, design, and manufacturing of assembly processes, tools, and machines that will effectively and efficiently manufacture the company’s current and new products
- Supervises the development, design, and manufacturing of tooling and assembly machines that will effectively and efficiently manufacture the company’s products
- Responsible for the development and maintenance of timely schedules for department projects and activities
- Apply knowledge of industrial engineering principles and practices. Responsible for Bill of Operation updates relating to methods analysis, work measurements and standards maintenance
- Responsible for analyzing manufacturing problems, determining the cause, and developing cost-effective solutions
- Monitors capacity of manufacturing processes and makes recommendations to the organization when action is required
- Coordinate the annual capacity planning models that are utilized to establish multi-year planning for capital projects. Prepares and submits recommendations to management for capital budget operation
- Identify and implement cost reduction initiatives to meet annual metrics
- Directs the preparation of cost estimates of fabricating tools and related production processes. Responsible for the accuracy and timeliness of cost estimates
- Responsible for the construction or alteration of facilities, including the establishment of estimated costs and schedules
- When applicable, investigates new and/or used machines and equipment and makes recommendations
- Is responsible for maximum efficiency and production of subordinates. This is accomplished through proper selection, training, and development of subordinate personnel
- Is responsible for the proper application of established department employee relations, policies, wage and salary adjustments, administration policies, and safety and health regulations
185
Manufacturing Manager Resume Examples & Samples
- Plans, directs and supervises the materials manufacturing programs
- Reviews sales and inventory requirements and allocates staff to appropriate areas to insure priority is assigned to materials needed for inventory and timely customer shipments
- Orients, instructs, trains and supervises materials manufacturing supervision and personnel
- Insures supervisor cross trains personnel in all areas for maximum flexibility in production
- Manage departmental performance measures, including visual controls and provides regular progress reports to manager
- Approves requisitions for the purchase of supplies and equipment for use in department activities
- Responsible for the care, maintenance and repair of materials manufacturing equipment and coordinates equipment repairs and maintenance
- Ensures work areas are kept clean and orderly and all safety rules are followed
- Tracks absenteeism and timekeeping
- Mentors supervisor and coaches employees
- Bachelor degree preferred
- Lean Six Sigma Black Belt preferred
- 3-5 years of experience in a production environment
- Previous experience as department or plant manager is preferred
- Demonstrated experience implementing lean manufacturing practices
- Experience in driving quality improvement results and leading quality teams
- Knowledge of batch manufacturing preferable
- Ability to solve practical problems and interpret a variety of instructions furnished in written, oral, or schedule form
- Familiar with Windows operating systems and Microsoft Office, PowerPoint slide presentations
- Self-motivated with a results driven approach
- Experience managing a flexible daily production schedule based on customer demands and priorities
- Experience with basic production documentation, including production work orders, procedures and work instructions, and quality records
- Experience in building collaborative teams
- Lean Manufacturing training/experience, preferred
- Experience with ERP systems, Oracle 11i or R12, preferred
- Ability to focus on detail oriented tasks
186
Manufacturing Manager Resume Examples & Samples
- Foster a safe work environment ensuring work practices are followed and proper PPE is worn
- Follow ISO 9001 standards to deliver Exceptional Quality and First Pass Yield targets
- Ensure work is maintained to SOPs and standard work guidelines
- Oversee Labor Management, Time & Attendance, and Staffing Planning to ensure labor efficiency
- Conduct daily GEMBA meetings and regular team communication meetings (at least weekly)
- Drive 6S processes on the shop floor
- Support the Stanley Fulfillment System (SFS) 2.0 initiatives to drive productivity and cost reductions
- Successfully implement the Hourly Tier Progression and Performance Feedback Programs
- Implement Smart Factory Initiatives and applicable technology improvements
- Track and drive performance improvement for Bowler Metrics
- Actively manage the Engineering Change Notice (ECN) process and MIN Numbers on the shop floor
- Perform Manufacturability Checks for new products
- Partner with Human Resources to enable and carry out employee engagement activities
- Bachelor’s Degree in Industrial, Mechanical, Electrical, or Chemical Engineering or Related Field
- 5+ years of experience leading manufacturing teams, preferably within high performing systems
- Solid working knowledge of manufacturing principles and procedures including ISO 9001 and 5/6S
- Ability to effectively communicate at all levels within the organization
- Master’s Degree in Engineering, Business Administration, or Related Field
- Project Management and / or Lean Manufacturing Certification
- Experience with SAP, SalesForce, and ADP
187
Manufacturing Manager Resume Examples & Samples
- Establishing priorities and scheduling of production with VAST, Sales Production Control and Clients
- Report information relating to equipment statistics, scheduling/capacity, and key quality measurements
- Initiate and participate in cross facility communications and best practice activities with Prod. Ops Managers across BCS
- Gives performance reviews to six area supervisors using performance measures based on key budget action items identified by corporate and divisional management. Performance objectives are rated based on predetermined measurement criteria. Assists the area supervisors in setting new performance objectives based on divisional direction and individual goals
- Administers company policies relating to assigned areas and coordinates with Human Resources to develop training and educational programs for the associates
- Initiates purchase of new equipment based on new product development, new technology, facility capacity, and EVA contribution. Assists with the preparation of CER’s and associated business cases as they relate to new equipment and/or capacity issues. Develop a day to day relationship with vendors and internal staff to ensure that the proper equipment is purchased and maintained
- Serve as production representative to support VAST, Sales and Clients during discovery and development opportunities. Represent VP of Manufacturing when requested to do so
- Assists in the preparation of the annual and quarterly budgets for electronic printing and production control to ensure that the best practices are being used in the purchasing area relating to costs and quality
- Assists and recommends salary and overtime policies for the area of responsibility
- Works with Human Resources to resolve employee relations issues
- May include other duties as assigned
- This position strongly influences the quality process within the facility. The manager is directly responsible for the enforcement of QCPs and SOPs for the assigned areas. Managerial influence and control has a significant impact
- This position has a high degree of influence on the operating profits and company growth, as well as manufacturing of the products and the delivery of these products to market
- This position has complete responsibility for the Production area
- Recognition, support and compliance with relevant company policies & recruiting and employing qualified job applicants regardless of race, color, religion, sex, sexual orientation, age, national origin, ancestry, disability or veteran status
188
External Manufacturing Manager Resume Examples & Samples
- Operation, Technical and Talent Management
- Weekly and monthly reporting of key performance indicators and project execution updates
- Development and proliferation of best practices and best known methods
- 7 to 10 years of experience in the semiconductor industry, with minimum of 3 years managing and leading a team of engineers
- Imager product and/or standard IC semiconductor assembly & test process knowledge (laminate and leadframe based)
- Quality Management and Quality Assurance standards including ISO 9001, IATF 16949 and VDA 6.3 along with associated tools – APQP, FMEA and Control Plan, Statistical Techniques and Design of Experiments
- Strong proficiency and command of the English language, as regular communications will be required
- Demonstrated leadership and supervisory skills including interpersonal and people development skills
- Ability to travel at short notice, typically within South East Asia region
189
Manufacturing Manager Resume Examples & Samples
- World class leadership abilities and motivational skills
- Commitment to success
- Minimum of two years' experience in manufacturing management
- Strong understanding of the sport fishing industries
190
Manufacturing Manager Resume Examples & Samples
- Responsible for overall planning, scheduling, manufacturing and packaging of existing and newly developed products in areas of assignment in compliance with all regulatory and GMP requirements in a cost effective manner and in accordance with planned budget. 30%
- Maintains and improves quality standards and production processes. 30%
- Responsible for proper maintenance of all production machinery by coordinating these functions as necessary with Facilities/Engineering Department. 10%
- Forecast machinery, material and equipment needed to meet requirements of new and existing products. Responsible for appropriate set up and lay out of equipment and general work areas. 10%
- Maintain training completion rate of >=95%, stay current with corporate initiatives and maintain business partner relationships. 10%
- Responsible for pro-active people management. Sets the standards for performance assessment and feedback, effective communication, promoting positive morale and supporting employee involvement programs. 10%
- Ensure that training of designated area personnel is up to date on applicable policies and procedures
- A minimum of a Bachelor’s Degree is required. An advanced degree or MBA is preferred
- A minimum of 8 years of overall work experience is required with 5 years of responsible hands on managerial experience in a metal cutting and/or packaging manufacturing environment preferred
- Knowldege of FDA regulations is preferred
- Strong verbal and written communication skills required to exchange information with diverse types of personnel; hiring and developing employees and addressing employee relations issues is also required
- Candidate is required to be familiar with lean manufacturing principles
- Experience creating budgets and explaining actual spending variances to budget is preferred
- Travel up to 10% domestically is required.0963170511
191
Manufacturing Manager Resume Examples & Samples
- Lead facility Operations Team in developing, prioritizing, and managing the execution of cost savings initiatives for the facility
- Achieve targeting cost savings results through urgent execution of organic and capital project execution
- BS/BA in Related Field or Equivalent Experience
- 5+ Years of manufacturing experience, preferably in pulp and paper
- In depth knowledge of paper manufacturing processes and technology
- Ability to motivate and drive others to achieve results
192
Manufacturing Manager FL Resume Examples & Samples
- Budget, monitor and control production expenses, capital spending and headcount
- Develop and manager short/long term plan of manufacturing capacity based on operation strategy and business growth
- Develop and implement management tools to ensure the material storage accuracy, FEFO and minimize the discard
- Reward SMOG to reduce the write offs
- Manufacturing expenses
- Discard
- SMOG
- Capital spending
- Bachelor degree in Chemical or Food Engineering
- 10 year work experience in MNC, with Production experience in petrol/chemical, Food or pharmaceuticals. 5+ years in a production managerial position
- Solid EHS/GMP/Food safety knowledge
- Be familiar with MRP and SAP knowledge
- Good English in speaking, reading and writing
- Honest, proactive, hardworking mindset
- Both process and result oriented, both hand on and strategic thinking skills
- Real team builder and team player
- Expert in SAP, DMA, MRP
- Very strong team leader and team player
- Value added driving
- Very strong “Do more with less” mindset
- Broad knowledge of Lean manufacturing and launching experience
193
Manufacturing Manager Resume Examples & Samples
- Represents Tech Op’s while supporting QA in the areas of batch record review, deviation investigations, change controls and CAPA support
- Will be responsible for the organization, safeguarding and management of all CMC documentation including but not limited to CMO batch records and protocols that have been reviewed and approved by the Specialist
- Will support on-going manufacturing campaigns at CMO sites either directly as the SME or managing the Specialist on site
- Supports the Specialist in writing and review of batch record development for new small molecule processes including lot development for all semi solid and DP production at the CMO; will represent TO’s in the final review and sign-off of these documents
- Will be responsible for preparing and submitting to senior management the periodic review of manufacturing campaigns including deviations, investigations, change controls and CAPA
- Ensures that data is compiled and analyzed and prepares reports and presents data to CMC and management as required
- May support other manufacturing campaigns in the area of BR review outside of small molecule programs on an as-needed basis but is not the primary function of this position
- Travel requirements: 50– 70% of time spent at CMO’s during manufacturing campaigns
- Familiarity with mixing, batching and formulation of topical creams in a GMP environment
194
Lean Manufacturing Manager Resume Examples & Samples
- At plant level, provide FES expertise and coaching (HSE, Quality, Employee Empowerment, Production Control & Logistics, and Production system) based on Faurecia' 11 lean manufacturing principles to contribute to achieve operational business targets
- Be accountable for the Plant MOD cost budget construction and achievement, through efficient MOD cost management and MOD cost improvement plan
- Animate the FES network within the plant, as well as participate to the Division network
- Minimum 5, ideally 10 years of lean manufacturing practice in the automotive industry
- Has a recognized experience and ability to improve process KPIs in a plant by using lean manufacturing principles
- Masters degree or equivalent level of experience
- Very good interpersonal relationship skills and trainer's skills
- Minimum bi-lingual (fluent English mandatory)
- Accept frequent business travel
195
Manufacturing Manager Resume Examples & Samples
- Consults with leadership team to set short-term strategic direction and operating plans for assigned area of responsibility and defines guidelines/methods. Decisions are typically limited by business or functional area objectives/guidelines. Initiates and approves projects to continuously improve efficiency and competitiveness
- May have direct responsibility or work with functional leader for functional strategic planning, including establishing and managing budgets for one or more departments in the immediate organization
- Management responsibility usually encompasses one work group/department within a functional discipline, such as production, quality, engineering, materials control, warehousing, maintenance, health/safety/environment, etc. Determines priorities, timetables and assigns resources/tasks. Accountable for the activities and results of their functional area
- Typically, provides direct supervision to professional and support levels which include objective setting, performance management, and motivating, as well as training and coaching
- Problem solving requires hypothetical thinking to determine best solutions for complex problems. Utilizes resources across work areas and departments to create solutions. Most complex problem solving may require in-depth interpretation and analysis for significantly different situations
- Resolves issues and conflicts related to direct reports
- Has a moderate impact typically on a small to medium, established business
- Decisions impact one area of the organization and occasionally may impact multiple areas
- Has responsibility for establishing and enforcing multiple concepts relative to the function. Working tasks might include
- Shares vision and demonstrates company values
- Negotiates and counsels on an expert level, justifies controversial positions and demonstrates intermediate persuasion skills. Interaction involves convincing others to cooperate, grant approval, or take action of a certain kind
- A Bachelor level university/college degree is generally required. Master’s degree is preferred. In addition, a minimum of 7-10 years of relevant working experience is normally required
- Expert/master knowledge and experience with the most current theories and practices in a related discipline and a thorough knowledge of more than one related discipline, such as production, quality, engineering, materials control, warehousing, maintenance, health/safety/environment, etc. In-depth knowledge of 3M’s business areas, structure, and organization, as well as of the external market (competitors, trends, etc.)
196
Manufacturing Manager, Biopharmaceutical Resume Examples & Samples
- Must be able to obtain and maintain a security clearance
- In addition to education requirement, a minimum of ten (10) years of progressively responsible job related experience including four (4) years of experience in a leadership capacity
- Experience in cellular therapy manufacture or vector production
- Ability to work in a high-pressure, time-sensitive situations; ability to multi-task and appropriately handle competing priorities
197
Manufacturing Manager Resume Examples & Samples
- Bachelor's Degree from an accredited university or college (OR a high school diploma / GED with a minimum of 4 years of experience in Manufacturing)
- Minimum of 1 additional year of experience in Production Quality
- Ability to manage multiple priorities under tight deadlines
- Knowledge of Lean / Six Sigma tools or equivalent quality tools and evidence of their application to solve complex problems in a manufacturing environment
- Motivated self-starter with a willingness to learn
- Ability to work a flexible schedule coincidental with manufacturing functions and global suppliers
- Ability to communicate effectively across all business functions including Manufacturing and Sourcing
- Highly motivated individual with the ability to work effectively within a team environment while managing priorities and multiple tasks
198
Junior Manufacturing Manager Resume Examples & Samples
- The effective management of resources to deliver agreed yield, productivity and customer service targets
- The management and development of a multi skilled, multi-disciplined team operating on shifts in a unionised environment
- To assume the duties and responsibilities of the Supervisor or Manufacturing Manager during periods of holiday/absence
- Maintaining Health, Safety and Welfare of yourself and other employees in accordance with the Health & Safety at Work Act 1974 as well as adhering to COSSH regulations
- Ensuring good GMP
- Meeting KPI’s
- Ensuring continuous improvement and lean manufacturing procedures
199
Manufacturing Manager Resume Examples & Samples
- Assure all production operators are following the assigned STEMCO safety guidelines including PPE, safe practices, reporting, training, and accident prevention. First responder and care manager in the event of an accident
- Work with team leads and supervisors to maximize potential by giving regular feedback, defining expectations, ensuring training, and removing obstacles. Implement corrective action with team leads, supervisors, and production operators as necessary
- Assure all defined quality expectations of both product and process are met. Encourage continual improvement and constant pursuit of operational excellence. React appropriately when defective product and process are identified, protecting both the customer and STEMCO
- Work within the organization to assure Kanban levels and OEM scheduled requirements are met, keeping constant communication with interested parties to assure on time delivery requirements are met as efficiently as possible. Identify obstacles and drive to overcome them
- Financial awareness of how decisions affect the bottom line, with a constant focus on cost control. Budget management is critical to this position
- Servant leadership
- Strong unbiased interpersonal skills with ability to communicate
- Manage multiple priorities
- Self-motivated and strong initiative
- Utilizing Lean Manufacturing techniques
- Working 5S Knowledge
- Performance Calculations and Monitoring (PPWH, Efficiency, Productivity, etc)
- Ability to travel as necessary
- 6 Sigma Green Belt a plus
- Machining or engineering background a plus
- 5-7 years experience in supervision/management of manufacturing operations
200
Manufacturing Manager Resume Examples & Samples
- Safety, manufacturing quality, on-time shipping, production management, manufacturing budgets, labor relations, operations personnel training and development effectiveness
- Communicate business unit and product operations goals, objectives, priorities and progress to employees and staff
- Plan production manpower, allocate resources and gain the necessary resource support from outside the operations product group
- Monitor performance versus plan and take necessary action to meet the plan
- Manage the assigned factory that operates 24/7
- Bachelor's degree in Business, Engineering, Technology or Finance and minimum of 5 years’ experience in manufacturing operations required OR an equivalent combination of education and work experience required
- Minimum 5 years of supervisory experience preferred
- Cross functional work experience required
201
Manufacturing Manager Resume Examples & Samples
- Ensure customer’s expectations are being met with particular attention to on-time deliveries, quality and service
- Work with scheduling department to set realistic schedules
- Determine manning of full time employees and temp workers as necessary
- Ensure the companies policies and procedures are being followed
- Train employees on company policies
- Authorize overtime as necessary
- Ensure all employees are utilizing appropriate PPE and working safely
- Attend daily production meetings
- Maintain an open line of communication with the President and Controller
- Advise executives on special issues, problems, or general information
- Make recommendations for equipment purchase and workflow adjustments
- Complete necessary paperwork to make official requests of the Corporate office
- Attend regular management and executive meetings
- Hire, discipline, and evaluate all employees
- Provide leadership to the production floor that promotes a positive work environment and delivers reliable, consistent and profitable results
- Track/measure employee productivity and performance in all areas of production using objective data on an ongoing basis
- Set performance level goals and update on an ongoing basis to create a culture of continual improvement with engaged and accountable employees
- Maintain appropriate staffing levels in all areas of production and adjust as necessary for drops and spikes in sales to ensure profitability
- Anticipate problems before they occur
- Self-motivated team player
- Above average mechanical aptitude
- Above average communication skills – both verbal and written
- Above average organizational and time management skills
- Ability to problem solve and troubleshoot
- Ability to make decisions with above average judgement
- Ability to motivate and delegate tasks to subordinates and ensure follow through
- Must be able to work a flexible schedule and work overtime as necessary
- Above average computer skills, particular MS Office and Google
- Bachelor’s degree is preferred but not required
- Experience in the print and folding carton industry required
- Supervisory experience required
- Actively involved and engaged as a leader in all areas of the company
202
Manufacturing Manager Resume Examples & Samples
- Minimum high school diploma and five-years manufacturing experience; preferred Bachelor degree
- 3-5 years of supervisory experience in a manufacturing environment
- Experience leading and managing groups of over 35 employees
- 3-5 years of experience with advanced problem solving and change management methodologies consistent with establishing a culture of CI
- Prefer regulated industry experience that includes knowledge of FDA and ISO requirements
- Strong leadership skills; able to motivate and create engaged teams
- Communication – displays developed interpersonal skills: leadership, team orientation, ability to communicate at all levels
- Problem Solving – able to lead team in root cause analysis and implement effective corrective actions
- Results Oriented - Must be detail oriented and have strong drive and a sense of urgency to resolve issues
- Flexibility and Adaptability – make effective decisions and maintain effectiveness under changing circumstances and priorities
- Computer Skills – Excellent computer skills including but not limited to Microsoft Office Suite and ERP systems
- Strong planning and organizational skills
203
Manufacturing Manager Resume Examples & Samples
- Ensure that short term and long term operating targets are met on time and in full
- Ensure the Compression Process Stream is adequately resourced to meet demands and that all staff perform tasks in accordance to current cGMP, Safety and Environmental requirements through appropriate training programs
- Ensure that all cGMP & EHS requirements in the Process Stream are defined in the factory’s Standard Operating Procedures
- Prepare the annual budget for the Process Stream in discussion with the Operations Director ensuring budgeted targets can be achieved and to address any issues arising from performance reviews against budget
- Ensure that staff carry out procedures in accordance to SOPs and where necessary to review SOPs in conjunction with the Quality and EHS Departments, ensuring strict adherence to all company SOPs and procedures and guidelines
- Maintain the Process Stream within regulatory compliance
- Implement appropriate staff development programmes; measure and evaluate team performance and take appropriate corrective actions where performance is below standard
- Foster a 'can do' attitude at all levels
- Plan, allocate and manage resources using standard work principles
- To be responsible for the housekeeping in the Process Stream manufacturing areas
- To continually undertake a system of review to ensure that systems in operation are efficient and optimised
- To ensure that all personnel in the Process Stream strictly adhere to legislation and the Company’s standards with respect to EHS, GMP and all company SOP's, procedures and guidelines
- To ensure that all documentation is available for audit and review by QA in a timely manner
- Provide strong leadership and coaching so that personnel actively engage and support performance and business improvement initiatives
- Drive a right first time approach in their work area, identifying and enthusiastically driving continuous improvement opportunities and prepare and manage improvement events
- Support all new product introductions and launches
- Liaise cross-functionality with the relevant Managers to ensure that the facility and equipment used are fit for purpose
- Support site Operational Excellence Programs through leadership and participation and to ensure the ongoing efficiency and competitiveness of the operation
- Minimum 10 years in front-line experience in pharmaceutical drug product QA/QP/QC/Manufacturing position in a wide portfolio of dosage forms (preferably to include oral solid dose)
- Extensive Quality/Manufacturing experience in commercial drug product manufacturing organisations
- Have a clear track record of leadership in manufacturing and previous management responsibility. At least 3 years managerial experience
- Must be a clear communicator and able to make clear reasoned decisions under pressure
- Experience of managing budgets
- Have a clear understanding of the practical application of the rules of pharmaceutical GMP
- Experienced in delivering “right first time” and continuous improvements
- Practical first-hand experience in drug product manufacture
- Not afraid to get hands on when required in support of his team
- Educated to at least degree level in Life Sciences, Engineering or related discipline and/or 5 years experience in a similar role in the Pharmaceutical Industry with a demonstrated capability in Lean, root cause analysis and problem-solving and process improvement
204
Cluster Manufacturing Manager Resume Examples & Samples
- University degree in engineering or chemistry
- 5-7 years of Strategic level experience
- 10 years of Extensive Supply Chain experience
- 5 years leadership of people across multi-site operations
- Lean Six Sigma Green Belt is advantageous
- A post-graduation in supply Chain Management or general Management will be an added advantage
205
HID Manufacturing Manager Russia Resume Examples & Samples
- Extensive experience within a cross section of manufacturing operations and supply chain management roles within the medical device, pharmaceutical or life sciences sectors
- Experience in a GMP and regulated environment is an advantage
- Strong communications, team-building, and leadership skills
- A track record for developing high performance teams and developing talent
- You'll have an understanding of key quality, environmental, health and safety standards
- Degree in an Biotechnology
- Experience in Production Management / Operations Management / Engineering Discipline
- An MBA or Lean Six Sigma Black Beltwould be highly advantageous
206
Manufacturing Manager Resume Examples & Samples
- Provide leadership for the successful day-to-day operation of the facility
- Assure compliance to all EH&S requirements, regulations, and permits. Continuously improve plant effectiveness in Safety and Environmental by providing clear and visible leadership as consistent with the philosophy that every incident is preventable
- Gather and analyze data to measure asset utilization, capacity, cycle times, yield, downtime, raw material efficiency, waste water, waste generation, and utility efficiency
- Optimize process throughput through de-bottlenecking studies and conduct long term capacity planning in conjunction with the business leaders. Develop capital plans to meet the needs of the business
- Develop and deliver annual capacity plans for all work cells
- Lead the continuous improvement effort for all aspects of process performance including cycle times, yields, downtime, raw material efficiency, waste generation, energy efficiency, and quality
- Review established production schedules for all manufacturing departments to insure established inventory levels are met while operating at the highest efficiency possible
- Coordinate the hiring and training of all manufacturing personnel
- Maintain and support a superior safety and housekeeping program, including all timely communication initiatives
- Analyze workforce requirements
- Conduct performance appraisals and provide coaching and guidance to all Manufacturing employees
- Encourage and promote operating in a continuous improvement environment
- Remove production constraints; allocate human and equipment resources and direct production employees to attain all established goals
- Communicate with Research and Development as well as product management personnel to develop new product strategies
- Work with the Purchasing Manager to develop and improve supplier relationships
- Create purchase orders for the Purchasing Manager to place orders
- Chemical Manufacturing Experience
- Strong chemical safety exposure
207
Senior Manufacturing Manager Resume Examples & Samples
- Has depth of understanding and ability to manage manufacturing production daily operations
- Has depth of understanding business units (BU’s) direction and technical background to understand product quality
- Has depth of understanding process and manufacturing operations matters and can give correct total priorities of cycle time, output and product qualities to direct reports
208
Manufacturing Manager Resume Examples & Samples
- Performing tasks in the work area on a daily basis within the team including
- Being an on-the-floor work participant with associates
- Covering for unplanned absences and vacations
- Understanding and maintaining all department reports and procedures
- Coordinating breaks and lunch schedules
- Overseeing and understanding the maintenance of equipment, PM's and work orders
- Assisting managers with scheduling of associates
- Understanding production and ability to execute department requirements
- Maintaining Good Manufacturing Practices (GMPs)
- Promoting and enforcing quality and food safety standards
- Being a role model for associates
- Planning and conducting job skill training for all associates including writing Skill Breakdown Sheets (SBSs) and conducting Job Instruction Training (JIT)
- Leading and driving improvement of plant operations
- Analyzing and understanding KPI's and data
- Performing the day to day tasks and responsibilities of the Department Manager/Assistant Department Manager in their absence, such as production scheduling and planning
- Must be able to learn and perform all positions in the department
- Must be able to understand plant policies, practices, procedures, and requirements
- Must be able to plan, organize and follow-through on assignments
- Must be willing to travel to any specialized training
- Must have a high level of maturity, discretion, tact and judgment
- Must have good computer and software skills, including Microsoft Outlook, Excel and Word
- Must have thorough knowledge of Good Manufacturing Practices (GMPs) program
- Must be able to use industrial strength chemicals
- Must have basic mechanical skills
- Must demonstrate leadership skills
- Must have good human relations skills (the ability to work well with others and be a team player)
- Must show enthusiasm, initiative, and pride in work
- A commitment to Publix and our mission
- Bachelor’s Degree in Business or a related field
- Experience as a quality leader and/or a safety leader
209
Manufacturing Manager Resume Examples & Samples
- Manage production to meet the production schedules, productivity, output, quality, delivery and KPIs
- Provides leadership to resolve operational or administrative issues on a timely and effective manner
- Plan for the necessary training and development needs of the production personnel for them to acquire the needed skills and knowledge in order to excel in their performance
- Effectively execution of manufacturing strategies to meet the business needs
- Work with upstream and downstream operations as well as other departments to ensure the harmonization and well coordination of the work flow to achieve optimize performance
- Review and update of SOPs as required
- Lead and drive to promote teamwork, "can do" attitude within the organization
- Lead improvement projects and support Lean manufacturing to create a continuous improvement culture
- Establish and maintain an effective communication platform for feedback and discussion
- Create a motivating workforce and focus on driving excellence performance
- Ensure the enforcement of shop floor discipline to meet company core values and HR policy
- Perform duties as and when required by the Superior that are within the capability and competency of the employee and within the employment framework
210
Manufacturing Manager Resume Examples & Samples
- Day-to-day responsibility of the Manufacturing business unit
- Responsibility of the manufacturing staff – recruiting, organization, development, coaching
- Responsibility for the strategic direction of Manufacturing to enhance productivity, performance, quality and cost reduction
- Work with other departments (maintenance, supply chain, validation…) to setup a flawless production schedule to drive performance excellence and ensure smooth product flow on site
- Budget responsibility – manufacture a high quality product against the most competitive cost
- Launch and support continuous improvement initiatives
- Work closely with the other site departments to ensure On Time Delivery and compliance with Quality standards
- Inspire permanent inspection readiness
- Attract, train, develop and retain top talent
211
Manufacturing Manager Resume Examples & Samples
- Functional and disciplinary leadership of the department production. Coordination of human resources and promotion, qualification and training of subordinate employees (education and training, training, etc.)
- Responsibility for the production of pharmaceuticals and nutritional supplements convey; Monitoring and ensuring compliance with international and national legal requirements by AMG, EU GMP Guide and FDA Regulations
- Ensuring a smooth and cost efficient production process and its permanent optimization. Budget planning for property, investment and personnel costs
- Creating and sharing the PI according to § 13 AMWHV, the batch, validation and qualification documentation in manufacturing. Ensuring compliance with instructions (in cooperation with the QP). Ensuring compliance with packing instruction, regular review and adjustment according AMWHV. Creating test and / or release of SOPs and other regulations and documents
- Responsibility for the maintenance and creation of maintenance documents of manufacturing machines, equipment, rooms and other equipment in the area of production. Ensuring the qualification of equipment, facilities and premises for manufacturing and R & D. Responsible for the HVAC system (Heating, Ventilastion, Air Conditioning) and the water system by AMG as operator of the water system
- Ensuring and monitoring the health conditions in the Department of Production
- Coordination and handling of all administrative matters including the conversion of official orders for the department production. Participation in and support of customer audits in the house. Handling customer complaints and cause disposal (in cooperation with the Department Quality). Implementation of CAPA (in cooperation with the Department Quality)
- Assistance in obtaining new business (participating in customer visits - both internally and externally)
212
External Manufacturing Manager Resume Examples & Samples
- Ensure the timely routing and review of all master manufacturing records (MRs), standard operations procedures (SOPs), tech transfer reports, validation master plans, and other documentation related to clinical and commercial drug product manufacturing at contractors and/or business partners
- Coordinated all DP Manufacturing activities at contract and/or business partner manufacturing sites, including but not limited to: scheduling of all batches, supply of materials, direct shipment of bulk and finished product at manufacturing site, track and monitor cycletimes, and providing any required associated reports and technical expertise
- Maintain required training status on Regeneron specific work instructions and SOP’s
- Lead sub-team in continuous process improvements, system/equipment implementation and/or strategy development
- Support all investigations which concern DP Manufacturing or associated shipping operations, when required
- This role will report to a Strategic Relations leader within the External Manufacturing organization
- Understands and listens to team members and stakeholders needs while supporting productive team environments toward one common objective
- Driven for proactive resolution of technical challenges with tact, diplomacy and composure
- Shows resiliency and flexibility in the face of challenges and adversarial situations
- Able to provide clear direction to others in ambiguous situations and environments
- Senior Manager requires a minimum of a BA/BS in any physical or biological science with 12+ years industry relevant experience, 11+ years with MS or 8+ years with PhD
- Associate Manager requires a minimum of a BA/BS in any physical or biological science with 8+ years industry relevant experience, 7+ years with MS or 2+ years with PhD
213
BTD Manufacturing Manager Resume Examples & Samples
- Establishes performance standards, monitors employee performance and focuses the Department’s attention to areas of opportunity to maximize performance
- Maintains ethics and integrity congruent to the Company’s mission and values
- Assists in the development of personnel through positive reinforcement and coaching techniques
- Responsibilities include hiring, planning, assigning and directing work; appraising performance, rewarding and disciplining employees; addressing complaints and assuring problems are resolved; developing leadership in all
- Provide coaching and direction for development of direct reports
214
Manufacturing Manager Resume Examples & Samples
- Assisting in setting aggressive performance targets and challenging associates to consistently meet or exceed such goals. The diversity of operations requires all departments to work closely together and interact with sales, technical functions, customers and suppliers in order to meet established goals and financial objectives
- Managing and directing the activities of Production Supervisors, Engineers, and hourly employees
- Providing appropriate training, work direction and guidance to ensure that specific performance standards are consistently met
- Creating a cohesive team environment through enthusiastic leadership, coaching and performance management is critical to successful supervisory performance
- Identification, participation, and leadership of projects to address the needs of the department, the company and customers
- Minimum of 3+ years of experience as a manager or supervisor in a manufacturing environment
- An understanding of glass fabricating technology is an asset
- Previous manager level experience with Tier 1 Automotive manufacturing practices
- Experience using Lean Six Sigma to improve and control processes with documented favorable results (Yellow, Green or Black)
- Knowledge and use of standard work
- Experience performing in a 24/7 manufacturing operation with significant accountabilities
- History of personally making improvements in Key Process Indicators
- Strong interpersonal skills in problem-solving, leadership, team-building and written and verbal communications
- Flexibility to respond quickly to changing business demands and the ability to assess priorities and act decisively on complex issues
- Ability to act with long-term perspective, accept responsibility, mobilize resources, plan and organize and share information
- Excellent listening skills with the ability to size up situations in order to resolve conflict and solve problems with both people and processes
- Solid experience with Microsoft Office Excel, Word, and Outlook
- Solid use of PowerPoint and the ability to present to Sr. Leadership levels
215
Manufacturing Manager Resume Examples & Samples
- Establish proper staffing and machine capacity levels to ensure production goals are achieved
- Manage overall production to ensure on-time delivery, quality standards and due dates are met
- Ensure employee safety and adherence to safety policies and procedures
- Support functional managers in managing employee-related issues
- Supports the Manufacturing COP and Preventative Maintenance MOP
- Direct continuous improvement activity to increase efficiencies and eliminate wasted resources
- Oversee all departmental projects and provide input for projects affect their departments
- Coordinate ST/LT planning activities affecting staffing, capital and development
- Support all Quality and Environmental projects, objectives, policies and procedures to ensure full compliance
- Bachelors of Science in related field or equivalent
- 3 - 5 years direct supervisory experience in a heavy manufacturing environment (metals machining, fabrication, etc.)
- Strong interpersonal and leadership skills along with well developed written and verbal communication skills
- Proficient computer skills, esp. MS Office applications
- Must be task oriented, self-directed and capable of managing change and ambiguity
- Working knowledge of ISO/TS 16949 quality management system (COP’s & MOP’s) that are applicable to the respective work areas
- Bilingual (English/Spanish) skills desired
216
Manufacturing Manager Resume Examples & Samples
- Converting raw wire to nut bodies on the progressive die nut forming machines and tapping the nut bodies, conserving & reprocessing and reusing oil with the briquette and centrifuge, processing parts through the wash/rust preventative and friction modifier application as well as managing all associated tooling, supplies, etc
- This position has overall responsibility for the efficient management of the day to day activities of the Manufacturing department
- This position requires the active management to continuously improve and move the training programs, department performance metrics, product quality and work force professionalism towards world class
- Hire, develop and retain departmental staff through training, procedure development, evaluations, corrective feedback, setting expectations of culture, continuous improvement, clean well organized work areas, etc. to assure that the Manufacturing department is well positioned to meet the needs of the company
- Responsible for maintaining safe working conditions relative to equipment & facilities
- Manage departmental expenditures for replacement machine parts and tooling, supplies, labor, etc
- Actively manage equipment capacity and utilization to meet planning and scheduling requirements
- Work with equipment manufacturers, representatives and independent consultants as required to solve technical issues
- Identify capital needs to assure that capacity and capability of the assets of the department will meet the needs of the company
- Continuously improve against departmental performance metrics. Work with Operation Director and Finance to establish targets, budgets and standard costs
- Share/learn/teach best practices with Europe team and NA and incorporate ideas that can benefit that Manufacturing department
- Work with Purchasing to quote new parts to manufacture in-house
- Participate in root cause investigations and corrective & preventative actions for equipment, process and quality problems
- Continuously improve equipment availability through preventative & predictive maintenance practices
- High School Diploma is a minimum requirement
- 4 year degree in Engineering or a relevant curriculum is a strong preference
- Remain current on Industry trends, seminars, relative training topics, etc
- 5 or more years of supervisory or management experience in a similar or closely related industry. Specifically, an industry that requires certification and audits by regulating bodies and/or customers and independent certifying bodies
- 2 or more years of management of supervisory experience working directly with cold forming, progressive die machines
- In addition to the above, experience in MRP/ERP systems is preferred
- Management or supervisory experience in a large, well known, work class company that manufactures automotive components, assemblies or fasteners is preferred
- High level organizational skills in efficiently coordinating multiple tasks & responsibilities
- Working knowledge of mechanical, electrical, pneumatic & hydraulic systems
- Proficient use of computers; Microsoft Office (Excel, Word, PowerPoint, etc.). MRP/ERP systems (Microsoft NAV)
- Strong communication skills in all areas of contact; manufacturing staff, other departments, upper management, suppliers, contractors, etc
- EMS/ISO 14001
- Safety orientation
- Evacuation of facilities
- ISO/QS/TS introduction
- Fundamentals of Cold Forming
217
Manufacturing Manager Resume Examples & Samples
- List the essential functions (i.e. key responsibilities with expected end results) which must be accomplished in order to fulfill the purpose of your position as described above
- Plan, organize, staff, direct and control effective overall operation to optimize safety, headcount, quality, delivery and cost-out
- Deliver profit plan commitments adjusted for volume on productivity, expense control and absorption
- Plan, direct and control the implementation of continuous improvement and capital projects to maintain and upgrade equipment, tooling, processes, facilities and utilities
- Develop, motivate and coach team members. Act as a champion for development planning, succession planning and goal setting for supervisors
- Develop and maintain constructive working relationships with employees to effectively lead cultural change that embodies the Eaton Values & Philosophies. Communicate and demonstrate Eaton best practices, ethics, values and philosophy throughout the organization
- Remain knowledgeable of required personnel related guidelines, policies and procedures of the company and take action necessary to ensure adherence. Insure that all site guidelines are administered fairly and equitable
- Manage and maintain a highly engaged team conducive to continuous improvement
- Participate in annual / semi-annual / monthly / daily production and finance reviews for Middlesex
- Support Eaton Business System integration through operational assessments such as: EBEA,
- OpA, MESH, EQS, Lean Six Sigma
- 3 years of experience within a Manufacturing or Operations environment
- Minimum one year of prior management experience
- 4+ years of Manufacturing or Operations experience
- 2+ years of leadership experience
- Knowledge of hose manufacturing processes/prior experience within the Hydraulics industry
- Lean or Six Sigma experience – Black Belt
- Prior experience with ERP Systems
- Excellent interpersonal, communication, negotiation and organizational skills
- Financial and business acumen
- Strong problem solving and root cause analysis skills
- Ability to work simultaneously through prioritization and time management skills
- Working knowledge of continuous improvement tools (Lean, Six Sigma, Kaizen etc.)
- Proven record of motivating, engaging and developing direct and indirect reports
- Proficient in MS Word, MS Excel, MS Power Point, and MS Outlook
218
Manufacturing Manager Resume Examples & Samples
- Establishes and maintains an efficient and safe operation. Deploys MESH to support a Zero Incident Culture. Assures that Safety Regulations and OSHA Requirements are adhered to with regard to manufacturing practices and equipment. Supports plant safety policies and rules and administers them
- Coordinates manufacturing and preventative maintenance and other maintenance schedules and priorities within the production plan to satisfy customer requirements
- Develops objectives and goals and assists in formulating and implementing procedures and programs to attain or improve upon such objectives and goals. Communicates and reviews these goals with direct reports and plant manager on a periodic basis. Plan and monitor key metrics to ensure quality, cost, delivery and safety requirements are met
- Assists in the selection, training and development of department managers and participates in their performance evaluation and development of personnel. Makes recommendations for changes in personnel and salary adjustments. Supports all plant affirmative action and EEO policies and procedures
- Participates in labor negotiations and assists in grievance settlements. Provides judgment and counsel in operating the plant within the provisions of the labor agreement. Drive positive labor and employee relations
- Assists in operating the total plant functions of production and maintenance within the established budgets
- Initiates and participates in formal cost and expense improvement programs. Supports employee teams and employee projects for cost reduction and process and plant improvement. Drives continuous improvement throughout manufacturing
- Maintains good housekeeping practices. Supports 5S activities
- Participates in the interpretation and enforcing of corporate policies and standards. Ensure required documentation and/or system transactions are executed to meet customer, manufacturing system and financial reporting requirements
- Reviews with the plant manager the organizational structure, responsibilities, authorities, accountabilities of the management organization and the performance of the management personnel in relation to established objectives. Also, advises the Plant manager of all major significant deviations that occur within the total plant activity
- Studies manufacturing trends and markets and provides management with information for decision making. Supports Lean Enterprise and Lean Manufacturing Initiatives. Helps to drive the Lean Process
- Performs other routine or special duties as directed by plant manager
- 5 years of prior management experience within a Manufacturing or Operations environment
- 10+ years of prior Manufacturing or Production experience
- Bachelor’s degree in business or engineering preferred
- Prior experience leading cultural changes – being a change agent
- Working knowledge of corporate, division, and plant policies and procedures
- Working knowledge of engineering principles and practices
- Prior experience working in a union environment - IAM
- Working knowledge of OSHA and EPA requirements
- Lean or Six Sigma experience – certification a plus
219
Manufacturing Manager Resume Examples & Samples
- Manage the workforce and plant assets to meet customer demand while complying with inventory goals set by the business
- Ensure smooth functioning of plant by supervising/coordinating production, shipping, HSES, maintenance and other activities
- Manage programs for continual improvement of prime quality, raw material efficiency, and customer complaint goals
- Manage the Health, Safety & Environmental Programs. Ensure that we operate with a philosophy that every incident is preventable. Be accountable to statistical goals based on these programs and this philosophy (e.g. prevention programs, hazard elimination, PPE requirements, incident investigations, audits, safety meetings, etc.)
- Manage capital and department expense spending according to budget
- Manage personnel related issues (career development, succession planning, staffing, performance reviews, discipline, etc.) for direct reports
- Develop a culture that is responsive to the manufacturing environment and business needs through team work and personal responsibility and ownership of the process
- Bachelors of Science in Chemical or Mechanical Engineering
- Minimum of 7 or more years previous plant experience plus manufacturing supervisory/managerial experience is required
- Proven ability to effectively lead with minimal supervision, demonstrating an entrepreneurial attitude
- Proficient in leading, providing direction, support and development for manufacturing teams across the plant
- Can effectively work in a matrix organization
- Proven communication and networking skills
- Proven PC skills, including MS Office software, SAP experience a plus
- Must demonstrate enthusiasm, a sense of urgency, attention to detail, commitment and follow-through while maintaining confidentiality and meeting deadlines
220
Manufacturing Manager Resume Examples & Samples
- 5-8 years’ experience in manufacturing environment
- 5-8 years’ experience in warehouse management
- Motorsports experience preferred
221
Manufacturing Manager Resume Examples & Samples
- Undergraduate degree with emphasis in Operations, Engineering, Supply Chain, etc. Masters Degree preferred
- 7+ years with increasing responsibility in a regulated environment
- Demonstrated results with continuous improvement toolkits such as Six-Sigma, Lean, VSM, etc
222
Manufacturing Manager Resume Examples & Samples
- Exercise complete ownership over entire day to day and strategic manufacturing operations of unique multi-process and multi -assembly operation
- Manage overall production and capacity
- Responsible for developing processes and methods to manufacture product in the most effective manner with an emphasis on efficiency by analyzing layout of equipment, workflow, assembly methods, manufacturing footprint, and work force utilization
- Develop and design robust manufacturing concepts and simplify/improve manufacturing processes to ensure best-practice and lean manufacturing concepts to meet quality standards and exceed customer expectations
- Create and maintain process documentation including Process Flow Charts, Work Instructions, Standard Operating Procedures, Process Illustrations, PFMEA, Control Plans, Process Sheets, visual aids, gage instructions, control charts, capacity and utilization charts and others
- Drive the usage of Engineering Change Management documents, manage manufacturing engineering documentation
- Establish and maintain Quality Management System, QC Process, quality documents, standards and guidelines for parts manufactured internally as well as parts purchased
- Perform tact and cycle time studies for all processes
- Review process for material savings, scrap reduction, material handling reduction and efficiency improvements
- Utilize Lean Manufacturing, problem solving, and root cause analysis for internal complaints, quality rejections and failures. Formulate corrective actions, lead troubleshooting process
- Understand and comply with all OSHA, safety and PPE requirements
- Establish and maintain equipment specifications and performance requirements for manufacturing equipment
- 5 years minimum managing manufacturing operations
- Bachelor's degree in Manufacturing Engineering, Mechanical Engineering, or Business degree with three to five (3 to 5) years of industrial experience
- Understanding of Lean manufacturing concepts, corrective action and root cause analysis programs or tools
- Quality management experience
- Experience working in TS/QS/ISO manufacturing environment
- Distinctive problem solving and analysis skills, combined with impeccable business judgment
- Strong computer skills in MS Office
- Results orientated with strong written and oral communications skills
- Strong leader, motivated, assertive personality,
- Time Management: Organizes work, sets priorities, and determines resources requirements; determines necessary sequence of activities needed to achieve goals while effectively managing time with limited supervision. Ability to manage multiple high priority projects simultaneously
- Adaptability: Adapts well to changes in assignments and priorities; adapts behavior or work methods in response to new information, changing conditions, or unexpected obstacles; approaches change positively and adjusts behaviors accordingly
- Collaboration: Builds constructive working relationships with clients/customers, suppliers, other departments, organizations to meet mutual goals and objectives. Behaves professionally and supportively
223
Manufacturing Manager Daltile Resume Examples & Samples
- Requires a Bachelor’s degree or equivalent experience in Management/Ceramics/Engineering
- Requires knowledge of Microsoft Office (Excel and Word)
- Knowledge of ceramic industry and ISO quality standards preferred
- Knowledge of hydraulic and electrical manufacturing equipment. Familiarity with SACMI presses and dryers used in ceramic tile pressing, as well as punches, dies, grids, and spare parts. Familiarity with roller hearth kilns, line setup, production changes and electrical/electronic troubleshooting of presses and driers
- Experience with ceramic tile processes, and factors affecting efficiency and quality (min 8 years)
- Ability to troubleshoot production problems relating to the pressing and kiln departments by identifying root causes and implementing solutions
- Calculate machine settings and material requirements, using concepts of algebra and engineering
- Core competencies include strong communications and listening skills, strong organizational skills, ability to delegate, and ability to organize, analyze and interpret data. Ability to plan, schedule, relate ideas and coordinate priorities. Ability to train, motivate, and coach employees. Strong electrical background
224
Manufacturing Manager Resume Examples & Samples
- Ownership of Weld, Heat-Treat, Clean, Compression Molding (diaphragms), Material Testing process execution
- Accountable for meeting or exceeding the safety, quality, delivery and cost expectations of internal and external customers within the process center
- Ensures plans are developed and executed to meet internal and external customer requirements; Analyze and use data to drive action and make decisions
- Collaborate and coordinate with Master Scheduling, Machine Shop Process Center Leader, Ops functional management and Business Support Functions (Program Managers, Engineering, Finance, Contracts, HR) to achieve product and site goals via sharing of resources, tools, equipment, and processes
- Ownership of employee development and cross-training
- Develop and implement process standards and ensure discipline and continuous improvement of all process standards
- Bachelor’s degree in Engineering, Business, Supply Chain, or related with a minimum of 5-7 years of leadership experience and 5-7 years’ of Supply Chain, Operations, and / or Engineering experience in a manufacturing environment; Aerospace manufacturing environment preferred
- Production scheduling/planning skills required
- ERP experience required; CostPoint, Dynafact and TipQA preferred
- Skilled in demonstrating all Competencies noted above
- Proficiency with MS Office; MS Word, MS Excel, MS PowerPoint
- NOTE - This position can be filled at 1 lower level at a Manager, Operations
225
Manufacturing Manager Resume Examples & Samples
- Bachelor's degree in engineering with a specialisation in Production
- At least 8-10 years of production experience
- 3-5 years team management experience
- Operational knowledge of Production methods (Kanban, 5S, Hoshin, TPM, GPAO)
- Minimum bi-lingual (English required)
226
Senior Manufacturing Manager Resume Examples & Samples
- Direct responsibility for representing Manufacturing in the development of the quarterly forecast reviews
- Based on financial/customer commitments execute Manufacturing resource reviews to assure sufficient human and equipment re- sources exist to meet customer and site business objectives
- Assure that product and process quality are compliant to internal, industry, and customer quality standards
- Drive productivity and financial performance by managing Manufacturing achievement of corporate and Manufacturing level metric goals
- Provide input and participate in customer meetings, visits, and quarterly business reviews as required
- Report on Manufacturing performance to manufacturing financial, delivery forecast/goals, and customer commitments
- Financial P&L responsibility as follows: labor, scrap, material usage, fixed and variable costs
- Conduct Manufacturing level communications as necessary to provide the tactical direction and drive achievement of quality, delivery, productivity and financial performance goals/objectives
- Provide the direction and leadership to develop and promote a Lean/Sigma continuous improvement culture within Manufacturing
- Ensure compliance with relevant safety regulations including, Quality System Regulation (QSR 21 CFR 820), ISO 13485 Canadian Medical Device Regulation (CMDR) and EU Medical Device Directive (EU MDD 93/42 EEC), Quality Business System and Key Corporate Policies by subordinates, as well as compliance with federal, state, and local regulations. All activities must be performed in compliance with the Quality System
- 7+ years of previous experience in manufacturing management; 5+ years with a Master’s degree
- 5+ years of managerial experience
- Medical device experience
- Strong experience in Operations, Lean, and Six Sigma
- Solid past performance as a project manager
- Strong analytical/statistical problem solving tools
227
Manufacturing Manager Resume Examples & Samples
- Bachelor's Degree in Industrial, Mechanical or Electrical Engineering
- Minimum of 5 years of experience in operations and manufacturing /process engineering experience
- Strong knowledge in assembly, welding and injection molding
- Deep Knowledge on UL Program and Requirements
- Strong applied knowledge on statistical tools: DOE, AQL, SPC, etc
- Proven ability to work with minimum supervision
- Demonstrated troubleshooting / problem solving / qualitative / analytical skills
- Demonstrated project management skills and strong quantitative & analytical skills
- Solid computer skills and PLC programming is a plus
- Good computer skills & proficiency in excel & project planning software’s (Gantt chart)
- Good oral and written communication in English and Spanish; proven presentation and facilitation skills
- Comply with EHS regulations and requirements
- Quality Engineering experience desirable
228
Manufacturing Manager Resume Examples & Samples
- Academic Knowledge
- Engineering degree or equivalents
- University post-grade preferred (MBA, Finance or Food Process)
- Background on continuous processes, leadership and projects co-ordination
- Knowledge on Quality system
- Capability for cost administration
- Five years experience to manage plants with more then 1,000 employees
- Food specialization
- HS&E
- Food defense
- Team Work
- RR.LL
- KPI manage
- High complexity due to technologies
- Product changes
- Plant lay out
- People skills and commitment
- Lead cultural change process
- Fluency in English is prepared
- IL6S
229
Technical & Manufacturing Manager Resume Examples & Samples
- Minimum of 7 years in Industrial or manufacturing environment
- Experience at leading production teams
- Experience leading technical or engineering function
- Evidence of developing teams to maximize performance
- Team Player, able to lead a team and be part of a team
- Excellent communicator and motivator
- Solutions oriented problem solver
- Expertise: people management skills, technical and manufacturing experience, analytical, decision maker, strong leadership, problem solver
- Safety, Health & Environmental Management
- Expert knowledge of Lean Manufacturing
- Strong understanding of Kaizen and 5S
- Business Management qualification/experience
- Computer Skills: Microsoft office, advanced understanding of Management Information systems
- Languages: local language, Company language (English)
230
Co-manufacturing Manager Resume Examples & Samples
- Min 3 - 5 year’s industry knowledge
- Experience with frequent interactions with co-manufacturing companies, suppliers & external influencers
- Responsible for monthly reporting on in-plant improvements and departmental budget
- Proven track record of facilitating multiple locations
- Ability to work remotely with flexible travel capabilities (70-80%)
- Must be on call for issues 24/7
231
Manufacturing Manager Resume Examples & Samples
- Make the working plan and manage related resources to improve the production performance by closely cooperating with related department
- Analyze manufacturing requirements, prepare labor resources, and arrange work assignments according to order priorities
- Arrange production and guarantee production quality, timing and optimize efficiency to reach company KPI. (IE,Safety, Service level)
- Coordinate with related departments to solve problems and optimize production process as per SPS requirements
- Audit processes, operation procedures, products quality and guarantee safe & healthy working environment for compliance with defined requirements. (KPI: NDL)
- Establishes and maintain work performance measurement and report system to present work results and indicate improvement direction
- Enhance team building and motivate people to involve in improvement teams activities
- Masters of Business or Engineering Discipline
- Proficiency in Spanish
- Previous Manufacturing Management Experience
232
Manufacturing Manager of Specialty Products & Projects Resume Examples & Samples
- O Project management in low volume, high mix, custom product a manufacturing plant. Responsible for coordinating activities necessary to manufacture high quality products in a job shop environment to customer specifications in a timely manner at optimal cost
- Minimum 7-10 years manufacturing experience
- 2 to 5 years experience in a Lean manufacturing environment
- Ability to promote and drive continuous improvement
- Proven Project Management skills
- Ability to make and manage good relationships
- Analytical skills and good judgement
- Exercises latitude and technical judgement in decision making
- Good understanding of customer expectations and deliverables with an awareness of the impact of failure/cost of poor quality
- Bachelor's Degree in a related field from an accredited institution required; in Engineering or Operations preferred
- Project Management experience – PMP certification a plus
- Minimum 1 year management of people
- Advanced Microsoft user to include Excel software
- Experience in creating project plans in Microsoft Project / Visio
- 2-5 years working experience of Lean Principles
- Able to read and understand engineering drawings
- Six Sigma Green/Black Belt - preferred
- Professional accreditation - preferred
- Critical Competencies
233
Manufacturing Manager, Blind Bolts Resume Examples & Samples
- Responsible for the management of all aspects of the manufacturing activities (production, planning, manufacturing engineering, safety)
- Department consists of 20+ employees and a sales average of $1.5M/month sales
- Works with Global Investment group on outsourced product
- Manage planning function to ensure smooth product flow through manufacturing cells and delivers customer product on time
- Sets expectations, provides recourses, audits performance, counsels employees, trains, and sets policies and practices to exceed department goals
- Leads team to achieve monthly, quarterly, and annual performance goals
- Ensures operations metrics are well known; tracks daily progress towards achieving objectives and mitigating risks
- Works with managers across all functional lines to accomplish organizational objectives
- Actively participates in implementing and sustaining ABS (TPS) principles and practices
- Oversees maintenance of equipment
- Implements company policies such as attendance, overtime, safety, environmental, etc., and directs the application of such policies to the product group's operation
- Assesses employee performance and mentors staff
- Excellent interpersonal, leadership and conflict resolution skills
- Proficient with Microsoft Office applications including Excel spreadsheets
- Ability to prioritize and complete multiple and diverse work assignments with minimal direction and supervision
- Minimum 5 years of supervisory experience
- Experience in the Aerospace industry
- Experience with ABS (TPS) initiatives and principles
- Experience and proficiency with Microsoft Office applications including Excel spreadsheets
- Experience in the Fastener industry
234
Manufacturing Manager, Inserts Resume Examples & Samples
- Department consists of 120+ employees and a sales average of $4M/Month
- Coordinates all manufacturing activities with Procurement, such as outside processing, to eliminate delays and meet production/shipping schedules
- Sets expectations, provides recourses, audits performance, counsels employees, trains and sets policies to exceed department goals
- Ensures operations metrics are well known, tracks daily progress, and mitigates risks
- Actively participates in the implementation and sustaining ABS principle and practices
- Demonstrates continual focus on improvements and enhancements
- Exhibits and promotes behaviors on the plant floor that leads to an engaged workforce
- Strong verbal and written communication skills; strong presentation skills
- Excellent interpersonal, leadership, and conflict resolution skills
- Minimum 5 years of experience in manufacturing
- Experience with CNC machines
- Experience with Lean Manufacturing and Continuous Improvement initiatives and principles
235
Manufacturing Manager Resume Examples & Samples
- Monitor, track and analyze production efficiencies in Manufacturing
- Develop programs for continuous improvement
- Manage Manufacturing, Maintenance and Tool Room activities through the Department and Production Supervisors
- Meet operational needs and requirements within budget
- Generate capital requests and manage capital budget for Waynesboro
- Plan and organize jobs to meet schedules and timelines in an environment with constantly changing priorities
- Analyze situations accurately and adopt an effective course of action
- Plan, develop and implement strategic action plans in conjunction with fiscal budget planning
- Recommends revisions to standard operation procedures and observes team to ensure compliance with standards and procedures
- Must communicate to the organization the importance of meeting customer as well as statutory and regulatory requirements
- Ensure safe working environment for all employees and enforce company and plant safety policies
- Promote plant goals such as Safety/Housekeeping, Quality, GMP, AIB, ISO and Gung Ho
236
Manufacturing Manager Resume Examples & Samples
- Provide leadership and technical direction for manufacturing tasks and personnel
- Provide engineering recommendations to management and guide product development for manufacturability
- Lead and oversee quality management and execution to cost and schedule
- Focus on improvements in standard product quality, cost reduction, and reduction in time to market
- Provide sustaining engineering support to manufacturing and design engineering
- Attends internal design reviews conducted by design engineering in order to critique and recommend design solutions
- Establish work group goals within the framework of schedule, quality, technical and financial objectives
- Maintain awareness of the group to assure quality excellence, timely completion of work and reviews, appropriate use of resources, and responsiveness to customer / program needs
- Facilitate communication of technical and business information between organizations and within work group
- Drive the development and application of consistent manufacturing practices, standards and software tools
- Communicate with management on technical, quality, organizational, resource and personnel issues
- Managing approximately six to eight assemblers
- Direct and coordinate the establishment of production schedules and the resource allocation including personnel to meet schedules
- Establishes departmental standards of performance and productivity
- Responsibilities include interviewing, hiring and training employees; planning, assigning, and directing work; appraising performance; addressing and resolving issues
- Collaborate with the Safety Committee on safety initiatives
- Technical background and experience in electronics and RF design
- Computer Aided Design and Automated Testing Experience
- Demonstrated understanding of product costing and cost management skills
- Effective team building ability
- Strong oral and written communications skills
- Experience in an aerospace electronics manufacturing environment
- ISO 9000, Six Sigma and Lean experience is desirable
- Believes in the continuous improvement philosophy
- The selected applicant should be a fast-thinking problem solver and should thrive in a dynamic environment
237
Manufacturing Manager Resume Examples & Samples
- 5 years documented leadership experience
- 5 years of documented work experience supporting a production/manufacturing environment
- 3 years of documented experience managing schedules and Plan of Action and Milestones (POAM) to meet mission objectives
- Documented history of leading a group of exempt (salary) and/or non-exempt (hourly) employees
- Current interim Secret Security Clearance
- Must be able to obtain and maintain a DoD secret security clearance
- Must be US Citizen
- 10 years Fleet Ballistic Missile experience or 10 years on a Space Systems Company program
- Ability to create, collect and analyze production metrics in order to make data based decisions
- Understanding of the Collective Bargaining Agreement (CBA) and experience leading union represented hourly employees
- Familiar SAP systems
- Experience interfacing with other organizations to include Lockheed Martin, Government representatives, associate contractors and other Lockheed Martin sites
- Green belt trained/certified. Proactively drive continuous improvement in the areas of technical competencies, talent, behaviors, cost and performance
- Excellent communication skill with the ability to deliver effective presentations at all levels
- Must have strong problem solving and conflict resolution skills
- Must have strong commitment to industrial and personnel safety