Manufacturing Director Resume Samples
4.7
(128 votes) for
Manufacturing Director Resume Samples
The Guide To Resume Tailoring
Guide the recruiter to the conclusion that you are the best candidate for the manufacturing director job. It’s actually very simple. Tailor your resume by picking relevant responsibilities from the examples below and then add your accomplishments. This way, you can position yourself in the best way to get hired.
Craft your perfect resume by picking job responsibilities written by professional recruiters
Pick from the thousands of curated job responsibilities used by the leading companies
Tailor your resume & cover letter with wording that best fits for each job you apply
Resume Builder
Create a Resume in Minutes with Professional Resume Templates
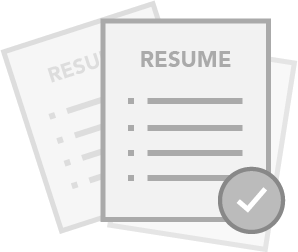
CHOOSE THE BEST TEMPLATE
- Choose from 15 Leading Templates. No need to think about design details.
USE PRE-WRITTEN BULLET POINTS
- Select from thousands of pre-written bullet points.
SAVE YOUR DOCUMENTS IN PDF FILES
- Instantly download in PDF format or share a custom link.
MH
M Homenick
Mason
Homenick
553 Robel Club
Los Angeles
CA
+1 (555) 742 4476
553 Robel Club
Los Angeles
CA
Phone
p
+1 (555) 742 4476
Experience
Experience
Philadelphia, PA
Manufacturing Director
Philadelphia, PA
Jakubowski Group
Philadelphia, PA
Manufacturing Director
- Analyze the performance of support functions for manufacturing departments and make recommendations for improvement
- Provide CI (Continuous Improvement) initiatives and tracking
- Leverage all operational resources across DP and API operations to establish agile and flexible work force that can respond to changing business conditions
- Adopt and nurture a culture of continuous improvement, both of business processes and personnel development
- As a member of the Site Management Team, develop strategies and plans for increasing efficiency and reducing unplanned downtime
- Ensure clear direction, performance goals, job profiles and job expectations are established for all Team Members
- Manage relationships internally and externally with executive level management, outside regulatory agencies, customers, vendors and/or suppliers
Detroit, MI
Director of Manufacturing
Detroit, MI
Rau Inc
Detroit, MI
Director of Manufacturing
- Developing short & long term strategic initiatives with overall coordination between 2 production facilities
- Ensure the Company complies with SOX regulations
- Identify, implement, and track both long and short term strategies that ensure positive results in the areas of financial performance, manufacturing excellence, material management, and inventory control
- Drives startup operations for new facilities through technical and organizational leadership from the Manufacturing lens to keep the project on schedule and within budget
- Ensures that production goals are being met around KPIs (Safety, Quality, Delivery, Inventory, Productivity) all while maintaining cost competitiveness
- Interacts with internal staff to identify areas for improvement or development and oversees improvement efforts delivering performance efficiencies to impact departmental gross margin
- Supervises, plans and reviews operations for assigned staff, including responsibility for training, managing and evaluating as well as coordinating, scheduling and assigning work and maintaining standards
present
New York, NY
Director, IS Business Partner Manufacturing
New York, NY
Flatley-Bednar
present
New York, NY
Director, IS Business Partner Manufacturing
present
- Work closely with business analysts, project managers, architects and/or other IS resources in providing IS services and initiatives to the business
- Work with Global IS teams to ensure IS services provided are consistent with business expectations
- Own and manage the IS Demand Management process for the selected area, ensuring demand matches value drivers to achieve business growth
- Work with Global IS teams to ensure services provided are delivered in a cost effective manner and to high standards
- Identify opportunities where conflicts/synergies/redundancies exist between business capabilities and systems to improve IS effectiveness
- Manage the IS budget and guide the business in effectively investing in Information Technology to meet strategic objectives
- Participate in the development of business and IS strategic plans
Education
Education
Bachelor’s Degree in Engineering
Bachelor’s Degree in Engineering
Ohio University
Bachelor’s Degree in Engineering
Skills
Skills
- Broad functional leadership and management experience, including experience in more than one of these functions: quality, CMC, Technical Operations, engineering, supply chain, manufacturing. Experience leading high performing cross-functional teams
- 10 years of background in science/engineering/manufacturing, with relevant experience of batch processing, automation, technical transfers, commissioning and validation in the pharmaceutical industry including
- Experience manufacturing high quality products while keeping a focus on cost efficiencies, continuous improvement and driving compliance
- Significant experience working with financials
- Progressively increased levels of responsibility leading diverse teams in multiple areas of operations
- Experience with device and/or drug regulations. Diversity of experience through having worked in other countries, functions and/or organisations
- Demonstrated leadership setting and executing strategies
15 Manufacturing Director resume templates
Read our complete resume writing guides
1
Senior Director, Operations & Manufacturing Resume Examples & Samples
- Directing the demand and supply planning functions including: master scheduling, order management, production scheduling, raw material planning, customer order fulfilment, and inventory planning
- Establishes plant capacity and ensures adherence of delivery performance to plan
- Reviews and sets standard product cost in collaboration with costing engineer
- Participates in developing operating budgets and managing to plan
- Works with designers and marketing to develop specific garments that meet our customers’ requirements
- Responsible for all quality related issues concerning the production of products, including all in-line audits, final inspection and packing/shipping details
- Establish and manage a contractor base that provides flexibility in our product demand
- Ensures that our facilities and contractors are operating in adherence to all Aramark standards including social and regulatory compliance
- Extensive knowledge of advanced statistical planning tools and processes
- Experience working with demand and supply planning software
- Project leadership and cross functional leadership experience
- Strong analytical skills and ability to interpret complex data
- Strong organizational and communication skills-both written and verbal
- Proficiency in Microsoft Word, Excel, Access, PowerPoint
- Strong sense of urgency
- Sound business acumen and analytical skills
- Ability to easily travel internationally
- Must be fluent in Spanish
- Experience with Oracle Demantra
- Experience managing an S&OP process
- CPIM, CSCP, or CPM certification
- Bachelor’s degree in Supply Chain or related field; MBA preferred
- Minimum 8 years’ experience working in the supply chain profession or apparel manufacturing profession
2
Director, Medical Manufacturing Resume Examples & Samples
- Directs, evaluates, and monitors effective manufacturing processes to meet on-time delivery and customer satisfaction
- Creates required documents such as Standard Operating Procedures (SOPs), reagent manufacturing work instructions, incoming material specification and performance verifications
- Analyzes procedures and production methods to improve quality, cost and productivity while keeping within product specifications, good manufacturing practices, federal safety regulations and policies
- Assures compliance with quality system. Ensures any issues relating to non-compliance, corrective and preventative actions is resolved in a timely and effective manner
- Provides support for regulatory inspections of the company as needed
- Formulates short-term to mid-term planning, policies, programs and objectives relating to the medical manufacturing division and ensures organizational goals/objectives are met efficiently and economically
- Directs and oversees the strategic integration and execution of company plan within the medical manufacturing division
- Establishes short-term to mid-term goals and objectives for division aligned with strategic plans set by top executives. Directs activities of subordinate managers in the accomplishment of division plan goals and objectives
- Counsels and advises subordinates concerning performance. Coordinates training of members to improve performance and ensure compliance to regulatory standards
- Initiates and/or recommends/approves personnel actions such as hires, promotions, transfers, discharges and corrective or disciplinary measures
- Supports validation and verification strategy for new and existing businesses processes
- Prepares reports on performance and activates of division and presents to executives
- Develops and maintains departmental budget. Ensures department operates within budgeted guidelines
- Requires a Bachelor’s Degree in Engineering or a related field. Master’s Degree preferred, with 8-12 years’ experience in medical device, clinical diagnostics and/or biotechnology and at least 5 years supervisory/management experience
- Proficient in relevant business experience in Enterprise Resource Planning (ERP) software
- Demonstrated ability to structure work, foster teams, use/share information and facilitate change
- Ability to manage complex projects and timeliness to meet deadlines
- Successful track record of demonstrating technical profanely, problem solving and troubleshooting abilities
- Experience with late stage process development and commercialization and writing/review of regulatory documents
- Experience with ISO 13485 quality system required
3
Associate Director of Process Development & Manufacturing Resume Examples & Samples
- At least 5 years of management experience including hiring, supervising, appraising employees. Matrix management experience desirable
- Experienced in the culture and expansion of human blood cells, mechanical isolation and analysis of cell populations, bioreactor-based growth of human blood cells, cytokine biology, molecular biology, tissue engineering, viral vector production and purification
- Demonstrated experience leading and managing technical staff
- Demonstrated experience leading complex projects or programs
- Demonstrated ability to work and communicate effectively with others
4
Director, Operations Manufacturing Services Resume Examples & Samples
- A minimum of 10 years of experience in global operations, ideally in a manufacturing environment
- A minimum of 5 years of people management experience
- MBA is a plus
- Device manufacturing experience
5
Manufacturing Director Resume Examples & Samples
- Clearly define and communicate the strategy and goals, to provide Quality, cost effective products in a Safe and environmentally sound manner as part of the AbbVie supply chain system
- Ensure that all Quality, Regulatory, Safety and Environmental requirements are adhered to
- Maximise the effectiveness of plant and people at AbbVie Sligo, to deliver the maximum return on investment to AbbVie
- Directly responsible for ensuring robust plans are identified and executed for R&D Pipeline activities to ensure successful execution of new product validation
- Control and report critical departmental performance metrics (KPIs), including departmental budgets
- Adopt and nurture a culture of continuous improvement, both of business processes and personnel development
- Leverage all operational resources across DP and API operations to establish agile and flexible work force that can respond to changing business conditions
- Maximise the potential of all team members and adept at helping them understand their value in support of the patients we serve and the ground breaking medicines we help to commercialize
- Manage relationships internally and externally with executive level management, outside regulatory agencies, customers, vendors and/or suppliers
- As a member of the Site Management Team, develop strategies and plans for increasing efficiency and reducing unplanned downtime
- Directly interface, as the facility and process owner, with regulatory agencies such as FDA, HPRA and EPA during site inspections
- Drive operational excellence within Manufacturing and champion it across the site. Play a central role in striving and positioning the site for future success
- Foster and nurture the AbbVie Way (the company culture) as a Senior Leader in site operations
- Broad functional leadership and management experience, including experience in more than one of these functions: quality, CMC, Technical Operations, engineering, supply chain, manufacturing. Experience leading high performing cross-functional teams
- Demonstrated leadership setting and executing strategies
- Significant experience working with financials
- Experience manufacturing high quality products while keeping a focus on cost efficiencies, continuous improvement and driving compliance
- Progressively increased levels of responsibility leading diverse teams in multiple areas of operations
- Experience with device and/or drug regulations. Diversity of experience through having worked in other countries, functions and/or organisations
- 10 years of background in science/engineering/manufacturing, with relevant experience of batch processing, automation, technical transfers, commissioning and validation in the pharmaceutical industry including
6
Executive Director, Biologics Manufacturing Resume Examples & Samples
- Ensure availability of bulk drug substances and clinical drug products to enable IMSC to meet all Global Project Team needs for clinical studies, and to support all other development activities
- Identify and qualify CMO’s to deliver the required quantities of DS and DP, executing supply agreements, overseeing technology transfer, and managing the execution of those agreements to meet these objectives
- Support a growing, diverse pipeline of biologics, addressing increased manufacturing complexity and cost
- Participate in initiatives to establish in-house clinical GMP production capabilities for drug substances and products
- Evaluate and establish strategic relationships with CMO’s to gain preferred customer status and security of supply for development and initial commercial quantities
- Lead the development of a commercial manufacturing strategy for biologics at Celgene, including CMO and in-house production, adapting the strategy to evolving pipeline and commercial priorities
- Lead a team of engineers engaged in these activities, ensuring their individual and organizational development
- Collaborate seamlessly with other Biologics Development groups, Quality Operations, IMSC and other business partners to establish high performing teams and ensure successful outcomes
- Prepare and manage the biologics supply budget, providing short/long term forecasts and regular updates as required
- Ensure project and investment decisions are anticipated and timely, and strategies are developed to balance financial, project and regulatory risk
- Provide membership, support and leadership as needed to cross-functional Biologics Development teams and collaboration joint CMC teams, and represent Celgene on JMC and other collaboration committees, as appointed
- Contribute to, review and approve regulatory CMC submissions to ensure their quality and technical content
- Participate in and lead due diligence assessments of new business development opportunities
- Serve as a member of the Biologics Development leadership team, participating in portfolio review and project governance meetings and providing guidance for best practices and direction for continuous improvement
- Report to the Senior VP Biologics Development, with accountability to Biologics Development, to Global Pharmaceutical Development and Operations, and indirectly to the Franchise Development Committees
- Ph.D. in relevant scientific or engineering discipline required
- 20 years pharmaceutical biologics development and/or manufacturing experience
- Experience of working with or in contract biologics manufacturing
- Experience in both drug substance and drug product development and supply
- Experience in early, late stage development programs and launch/commercial stage products
- Solid understanding and first-hand experience of the integration of Pharmaceutical Development activities to Quality, Regulatory CMC, Tech Ops, Non-Clinical, Clinical, and other functional areas
- Proven ability to lead cross-functional and technical teams and align, motivate and empower team members
- Able to engage and align other stakeholders outside the project team
- Demonstrated ability for critical thinking and innovation
- Ability to understand and communicate risks and develop and execute contingency plans
- Potential to take on increasing responsibilities as the Biologics portfolio and organization expands
7
Director, Clinical Manufacturing Resume Examples & Samples
- Manufacturing leader for process alignment, technology transfer and product/process related initiatives
- Create an environment where productivity and efficiency are achieved and recognized
- Establish operational objectives and assignments
- Anticipate and address inspection issues that impact plant operations
- Maintain a high level of compliance through effective monitoring and reporting of key quality metrics
- Ensure timely execution of CAPA, change control and continuous improvement initiatives
- Manufacturing leader for inspection activities, observation commitments, submission and agency requests for products for assigned manufacturing plant
- Identify key areas for change and alignment and mobilize organization to make changes happen
- Influence and/or develop broad-based programs and initiatives to meet executive level vision and mission
- Collaborate with functional leaders to set strategy and shared objectives
- Communicate, interact and influence with Manufacturing Leadership Team and functional department heads
- Accomplish results through the management of a team of managers, professional employees and/or other leaders
- Develop and administer budgets, schedules, objectives and goals
- Independently determine approach and requirements to managing teams and executing operations with strong collaborations with peer leaders
8
Director Vaccine Manufacturing Resume Examples & Samples
- Manufacturing of specific vaccines: Direct production of vaccines according to the production schedule; ensure availability of raw materials, trained staff and maintenance of facility and equipment; ensure adherence to standard operating procedures
- Safey, cGMP Compliance and Accurate Documentation. Ensures: operations are carried out in a safe manner and safety issues are effectively resolved; operating procedures are current and followed; ensure adherence to policies; production records are accurate, reviewed & signed by an authorized person; facilities and equipment are maintained to meet compliance requirements; process deviations are minimized and root causes are identified and corrected; staff training records are complete and current
- Production Efficiency and Financial Results:Establish annual departmental operating budget; maintain and control spending according to budget and provide explanation for variances; minimize product lost; Ensures effective and efficient use of personnel
- Trouble-shooting and Process Improvements:Identify root cause of production problems as required, and potential improvements in quality and/or yield; Implement solutions or changes via change control
- SAP Accuracy:Ensure accuracy of inventory and recipes, and that production order are maintained in a timely manner; ensure adequate SAP-trained staff
- Staff Development and CommunicationProvides training and development opportunities and guidance to staff; Contribute to site projects and committees; Communicate and co-operate with other departments to obtain consensus; Report issues and concerns to Senior Director; Provide monthly reports and other reports as requested. Reporting structure includes 7 direct reports and 130 Indirect
- Minimum university degree in scientific discipline. M.Sc. degree is an asset
- Minimum 10-15 years manufacturing experience in the biologics or pharmaceutical industry
- 5+ years of proven successful leadership experience in creating and leading large high performance teams with quality focus
- Sound knowledge and understanding of value chain i.e. QA, RA, Manufacturing & Clinical
- Experience in working on international teams
- Ability to influence and create effective partnerships
- Superior verbal and written communications skills
- Biologics experience is a major plus
- Bilingualism (English/French) is an asset
9
Manufacturing Director Finished Goods Resume Examples & Samples
- A minimum of a Bachelor’s degree is required, Engineering, Science or related discipline is preferred. An advanced degree, such as MBA or MS is preferred
- A minimum of ten (10) years of relevant experience in health care or another regulated industry is required
- A minimum of five (5) years of people management experience is required, previous management of global teams is preferred
- Ability to develop people, manage technology, embrace financial goals and utilize customer-focused decision making is required
- Knowledge of continuous improvement tools, lean manufacturing, six-sigma, flawless project execution is preferred
- Product life cycle knowledge and cost management is required
- Experience with capital and expense budgeting is required
- Assertive Influencing & Collaboration/Teaming Skills is required
- This position requires up to 40% domestic and international travelOperations (Generalist)
10
Director, IS Business Partner Manufacturing Resume Examples & Samples
- Align with Stryker Manufacturing Campus leaders in North America, ensuring this role is the trusted IS partner and aligned to strategic goals and objectives
- Build strong collaborative & influential relationships with business leadership and teams
- Manage the IS budget and guide the business in effectively investing in Information Technology to meet strategic objectives
- Own and manage the IS Demand Management process for the selected area, ensuring demand matches value drivers to achieve business growth
- Manage alignment of project deliverables with business requirements throughout the project and delivery life cycle
- Accountable for leading a team of IS Professionals, including IS Managers to ensure Global IS standards are maintained
- Align with Enterprise business program strategies related to Stryker Manufacturing; focused but not limited to PLM, ERP & MES
- Champion ERP strategy across SGS Manufacturing locations, ensuring that the strategy is defined for new and existing plants, including M&A, and fully aligned with the overall company ERP strategy
- Champion MES strategy across North American locations to ensure readiness & successful deployments
- Work with Global IS teams to ensure IS services provided are consistent with business expectations
- Drive IS value creation and customer satisfaction
- Build and maintain strong relationships with business leadership and act as a liaison between IS and the business
- Work with Global IS teams to ensure services provided are delivered in a cost effective manner and to high standards
- Ability to influence in a matrix organization where delivery of projects & programs is dependant on indirect reporting relationships in the Global Services, ERP, Strategic partners & Infrastructure teams
- Ability to learn and understand business requirements, issues and processes
- Participate in the development of business and IS strategic plans
- Positively challenge and question requestors on needs and benefits
- Charter and prioritize program and project initiatives in conjunction with business leadership
- Ownership of business focused IS metrics that ensure transparency of IS Services
- Identify opportunities where conflicts/synergies/redundancies exist between business capabilities and systems to improve IS effectiveness
- Partner with Global IS teams to ensure compliance with regulations, policies, standards, procedures, and associated documentation including but not limited to Computer Systems Validation, Global Change Control, SOX, and PMO standards
- Contribute to the budgeting process and lead and recommend CERs for division IS projects
- Liaise with other IS stakeholders in project management, architecture and governance to ensure alignment and a smooth integration of process output with the rest of the IS environment
- Work closely with business analysts, project managers, architects and/or other IS resources in providing IS services and initiatives to the business
- Communicate on projects by ensuring regular status updates and managing communication within team, IS organization and business leadership and stakeholders
- 15+ years of professional work experience in IT/IS and/or business discipline
- Extensive knowledge (5+ years) of medical devices and/or pharmaceutical industry and basic knowledge of adjacent areas in terms of processes, organization, products and IS requirements
- Knowledge of SAP Manufacturing and Apriso MES preferred
- Project management experience, working with internal and external cross-divisional team members, preferably with IS projects
- Strong communication skills with ability to communicate effectively with both divisional leaders and technical teams
- Good business acumen and negotiation skills
- Strong negotiation & influencing skills
11
Director of Manufacturing Resume Examples & Samples
- Sets direction based on customer delivery requirements and drives his / her team to meet requirements
- All activities within the Reagent Manufacturing organization that affects the successes of the Company and customer satisfaction
- Ensures a safe work environment for all associates and drive to eliminate any environmental, health, and safety incidents
- Identify, implement, and track both long and short term strategies that ensure positive results in the areas of financial performance, manufacturing excellence, material management, and inventory control
- Determines and monitors the overall resource capacity (personnel & equipment) for the organization and set priorities to maintain production expectations
- Ensures that the quality systems for the Consumables Manufacturing operation are developed and sustained to ensuring our Customers receive the highest quality product possible
- Ensures that production goals are being met around KPIs (Safety, Quality, Delivery, Inventory, Productivity) all while maintaining cost competitiveness
- Acts as a role model to Company personnel and be recognized as a leader
- Assess, identify, and implement technological advancements
- Drive continuous improvements (DBS) activities utilizing lean manufacturing principles and tools
- Communicate with appropriate outside sources to provide resolution to customer and company questions and concerns production process effectiveness, and other quality related issues as they arise
- Establishes and approves operational objectives and assignments, delegating assignments to staff
- Leads the group’s involvement in the planning processes; participates in business unit strategic and tactical planning processes
- Communicates manufacturing issues to senior management, users and staff that can have company-wide impact
- Bachelor’s degree (technical discipline preferred) with 18+ years of experience,
- Master’s degree with 15+ years of experience in key leadership roles within operations with at least 6+ years in a management position
- Leadership and management experience in developing high performance teams across multi-departmental organizations
- Demonstrated ability leading a major sustained improvement effort
- Financial/cost accounting experience
- Team player with strong customer orientation and ability to work in multinational and multicultural environment
- Proven leadership skills, good negotiation and public presentation skills
- Excellent analytical, interpersonal, verbal and written communication skills
12
Director Logistics Manufacturing Resume Examples & Samples
- Oversea Production Managers in multiple locations throughout the US
- Ensure operations meets production targets
- Work with Production Managers to set and achieve long range goals to impact and improve department processes and procedures
- Analyze costs and continuously seek to improve margins
- Partner with 3rd party supplier
- Monitor the production process and adjusting schedules as needed
- Manage end to end forward and reverse logistics, transportation, and inventory across all categories
- Define logistics and inventory management operations (people, processes, technology, and facilities) to support corporate strategy at optimal cost and performance. Provide leadership for logistics by setting best practice policies and processes
- Ensure delivery of consistent and defined service levels to internal and external customers
- Design and implement systems and processes which balance cost, financial controls, service delivery, and consistency across inventory management and logistics functions
- Manage operational risks & issues with suppliers and internal operations
- Collaborate with business unit customers to continuously improve services delivery and overall cost
- Assist in the development of the annual financial business plan and reforecasts, including the setting of yearly standards, monthly forecast updates and identifying potential risk factors
- Travel within the U.S. and internationally to fulfill above duties
- Bachelor's degree and ten years related work experience or fourteen years related work experience post high school
- Five years of progressive management experience
- Education in Industrial Engineering
13
Manufacturing & Depot Operations Senior Director Resume Examples & Samples
- Demonstrate that they are developing leaders across the Operations organization through active, real time coaching. This includes the development of a deep talent pipeline in key skills areas that are aligned with current and future Business needs
- Ensure the organization meets all efficiency goals, demonstrating productivity and improvements through positive program EAC performance
- Demonstrate that they are actively collaborating with other discipline and functional leaders in a matrixed environment to deliver optimal business-level results
- Ensure that team leaders have awareness, ownership, and accountability for all Operations goals, and that the organization achieves these goals
- Demonstrate that they have built strong partnerships with senior leaders that are stakeholders in the Operations of the Business
- 16 years of professional experience, with a minimum of 10 years of factory and/or program management experience with proven ability to lead large diverse organizations (400 employees)
- Experience with process improvement (e.g. Six Sigma)
- PMX certification level 1 or 2
- R6s Specialist certification
- EVMS certification
- EX/IM working knowledge
- Proven ability to meet cost targets in a competitive market environment
- Established network across the RTN businesses
- Organizational Effectiveness (OE) experience – Design and implement cost effective, productive organizations
- Experience using balanced score card type metrics to drive productivity and business results
- Knowledge of Raytheon wide products and markets
- Experienced manager with a demonstrated history of complex problem-solving and effectively interfacing with
- Experience building relationships with Customers, Functional and Program Managers, Directors, & Vice Presidents (or equivalents) to negotiate in difficult situations both internally and externally
- Ability to influence all levels of the organization to meet goals and objectives
- Ability to work proactively on staffing and program execution
- Ability to understand the financial impact of decisions on the organization’s budget and the business/program
- Experience with creating and executing a large organization to an EAC
- Security Clearances Required: Minimum Secret, Top Secret desired
- Understanding of production or similar schedule driven environment within a profit driven business based on practical experience
- Experience in turning customer requests into proposals
- Experience with common PDM tools preferred
14
Director of Manufacturing Resume Examples & Samples
- Overall accountability for safety, quality, cost and throughput of the Specialty Gas Manufacturing operation
- Provide direction and prioritization to personnel regarding planning, scheduling, purchasing, manufacturing engineering, quality, inventory control and distribution/shipping;
- Responsible for the site security and safety of operations, personnel and regulatory compliance
- Lead and/or participate in cross-functional teams to resolve customer issues and drive process improvements
- Develop and manage manufacturing performance objectives driving operational improvement
- Guide new product transition activities from development to volume production
- Assist with the development, planning and execution of the global manufacturing strategy
- Bachelor’s degree in Engineering, with an advanced degree in Business or Management preferred
- Manufacturing or operations experience with continuously increasing responsibility and oversight
- Experience with new product commercialization and product transitions (in-source, out-source or site-to-site)
- Proven experience leading cross functional teams to achieve business objectives
- Lean and/or Six Sigma certification desirable
15
Director of Product Line & Fabrication Manufacturing Resume Examples & Samples
- Directs all phases of commercial and military manufacturing operations including Capacitors, Gulftronic Separator Systems, RMS (Radiation Monitoring Systems), Battery Systems, TAP (Terminal Automation Products), and miscellaneous commercial and space system products as well as oversite of all GA-EMS Welding Engineering and fabrication activities
- Oversees the Product Line Manufacturing Engineering Team that is dedicated to the Product Line factory floor support
- Performs senior manufacturing floor management oversite at both the GA-EMS Tupelo and GA-EMS San Diego Manufacturing sites, including management of direct manager reports at both locations
- Oversees direct manufacturing touch labor at both locations according to established budgets, as well as meeting schedules and delivering the highest quality of all responsible products
- Identifies and provides senior leadership oversite of various capital and IR&D Projects related to manufacturing floor improvements as well as identifies all necessary regulatory, safety, training and compliance improvements as required
- Directs the planning, scheduling, and management of manufacturing operations and touch labor to achieve business, safety, quality, and financial objectives
- Acts as the primary contact for the Product Line Program Office and will assign Manufacturing Operations personnel to directly support the Program Office as required
- Acts as the primary contact for high level manufacturing activities and manages progress planning and review sessions to discuss schedule and cost
- Ensures a proactive approach to continuous improvement and directs the implementation of lean principles
- Champions production schedules based on product introduction, equipment efficiency, and materials supply
- Identifies manufacturing issues and provides leadership in developing solutions
- Provides guidance to engineering regarding design concepts and specification requirements that best utilize the facilities equipment and manufacturing techniques
- Ensures manufacturing leadership and excellence is maintained by overseeing the planning, attraction, selection, retention, and development of the required management, professional, and technical talent
- Provides high level manufacturing expertise to the development of new and expansion of existing business opportunities to enhance the capabilities of the organization
- Typically requires a Bachelors degree in business administration, engineering or a related discipline and fifteen or more years of progressively complex manufacturing experience with at least nine of those years managing manufacturing operations. May substitute equivalent experience in lieu of education
- A technical degree with an MBA or advanced technical degree is preferred along with the required years of experience
- Must have a detailed and comprehensive understanding of the principles, concepts, theories, and practices of manufacturing operations; extensive experience demonstrating a broad application of operations practices, techniques, and standards; as well as comprehensive project management and leadership skills, including organizing, planning, scheduling, and coordinating workloads to meet established deadlines or milestones
- The ability to develop new processes or systems and communicate new concepts to all levels
- Strong communication, leadership, presentation, and interpersonal skills are required
16
Discrete Manufacturing Industry Solutions Director Resume Examples & Samples
- Work closely with engineering, services and selected partners to develop a Discrete Manufacturing go-to-market solution package that will scale through the industry
- Work closely with the field teams to land industry solution Light House deals and develop the solution content, as well as services and partner engagement models
- Iterate and learn from initial Light House wins to improve the solution package to the point where solution content and engagement models are stable, well understood, and can be executed at scale by the field resources
- Demonstrate deep knowledge of competitive differentiation and ability to handle certification and compliance requirements specific to the industry
- Represent the field and customer voice and effectively liaison with engineering and other central corporate functions
- Support the recruiting of field resources to secure a high-quality team of industry experts
- Conduct industry solution and field onboarding and readiness, including community leadership with various specialist sales roles
- 10+ years of industry domain expertise and experience working in business roles at a company in the manufacturing industry
- Significant (10+ years) industry solution experience (i.e. as a business solution consultant in delivery and sales roles in areas like PLM, CAE, Simulation)
- Good understanding of enterprise IT systems including ERP, SCM, PLM, and MES systems
- Industry specialized sales or consulting position within an IT consulting or services company
- Solution sales or consulting position in a competing or partner company
- Business and market development skills
- Education: MS degree in Manufacturing, Mechanical Engineering, Industrial Engineering or Computer Science. MBA is a plus
17
Consulting Director, Heavy Manufacturing Resume Examples & Samples
- Lead multiple engagements delivering billable client work for a large Machinery client as the lead Consulting Partner
- Develop reusable consulting assets to improve the quality and accelerate speed of delivery for client engagements
- Articulate Cognizant’s point of view related to Manufacturing industry trends through thought leadership such as white papers, infographics, Webinars, and other marketing materials
- Help build, lead, and develop team of onshore/offshore manufacturing consultants
- Navigate Cognizant’s organization to build a network and form virtual teams with expertise manufacturing capabilities as well as emerging digital capabilities (e.g. analytics, cloud, social, mobile, etc.)
- Manage account-specific consulting plans for accounts across the entire spectrum of Cognizant Business Consulting capabilities
- Contribute to business development activities for consulting engagements through activities such as pre-sales client presentations, research, and writing proposal, RFP responses and SOWs
- Build deep CxO relationships and pursue up-sell opportunities with existing clients in partnership with the Cognizant account team
- A minimum of 15+ years of experience in management consulting with direct experience supporting and leading engagements in manufacturing, especially heavy machinery
- An understanding of digital trends with a focus on Web, Mobile, Social, Robotics, Sensors, Analytics, and Digital Marketing as it relates to Manufacturing
- The ability to drive programs across supply chain, S&OP, warranty, after market, and dealer management capability areas
- Strong written communication and presentation skills with the ability to influence senior executives to make positive decisions concerning capital allocations
- Experience in business development, client relationship management and pre-sales support
- Ability to analyze and share recommendations to improve/modify existing processes/ systems for clients
- Experience with client interaction by identifying client's priority needs for service and support
- The ability to manage teams of consultants and work with cross functional and client facing teams on a global basis
- Knowledge of process flows, systems and procedures which aids analysis and recommendations for solution offerings to exploit new business opportunities
- Advanced practical knowledge of business processes, requirements management, strategy development
- Ability to travel as necessary to support the client on a global basis
- Master's Degree in Business/Management highly preferred
18
Manufacturing & Logistics Account Director Resume Examples & Samples
- Forecast and manage talent retention and growth optimally
- Lead the team effectively
- Formulate creative deals and ability to innovate and raise the bar consistently
- Thought leadership in IT/Offshoring environment
- P&L management experience
- Experience in formulating creative deals
- The qualified candidate is preferred to reside within a daily commutable distance to Milwaukee, WI or be willing to relocate to Milwaukee, WI
- Minimum 10-15 years of experience
- 4 year bachelor’s degree or equivalent required
- Advanced degree (MBA or Masters) preferred
19
Director, Organ Manufacturing Resume Examples & Samples
- Lead and manage organ manufacturing efforts to print lung scaffolds out of bioabsorbable/compatible material, which will be cellularized once successfully achieved
- Create UT’s lung scaffold printing infrastructure capability within expanded leasehold space in Manchester, NH
- Pursue technology diversity in implementing the scaffold printing effort so as to reduce the risk of single stranding the technology development effort
- Make incremental progress in printing lung scaffolds each calendar year such that by 2021 entire lung scaffolds are being printed at a level of detail comparable to decellularized porcine lung scaffolds
- Manage the capital expenditures and systems processes such that by 2021 the printed lung scaffolds will be accomplished in a volume of not less than 100 per month and in accordance with GMP procedures
- Upon successful achievement of quantity GMP scaffold printing, commence work to cellularize the scaffolds initially with appropriate adult primary cells using internal UT Regen Med technology and ultimately with differentiated IPS cells from the intended organ recipient using newly acquired technology
- Demonstrated expertise in technologies related to organ manufacturing and other related platforms
- Strong communication (oral and written), presentation, and analytical skills
- Ability to work independently, prioritize tasks efficiently and meet expected time frames
- Ability to interact collaboratively with various departments, regulatory agencies and investigators
20
Global Sourcing & Manufacturing Portfolio Director Resume Examples & Samples
- Drive the development of a comprehensive portfolio strategy, including strategic analysis and facilitating portfolio definition, reviews, and prioritization
- Plan, coordinate, and facilitate regular portfolio review session with GSM Steering Committee and leadership
- Collaborate with GSM strategy team and other business partners to continuously improve alignment between long-term GSM strategy, the portfolio, and the organization’s operating plan
- Oversee portfolio financial valuation, risk assessment and support portfolio prioritization process
- Support project budgeting, risk assessment and resource management methods, tools and processes that inform decision making while minimizing the burden of data collection
- Partner with project teams across the organization to understand initiatives and ensure they are setup for success
- Partner closely with Finance, GSM Leadership team, and other key stakeholders to perform resource and capacity assessments; identify impacts and option scenarios
- Surface best practices and drive maturity of the portfolio management function
- Develop, maintain and encourage
- Bachelor's degree in Business Administration, Economics, Political Science, or related fields desired. MBA with Finance or Strategy and Ops focus preferred
- A minimum 10+ years' experience in progressive Project Management, Portfolio Management, Strategy, Operations, Innovation Management, and related disciplines within large dynamic organizations preferred
- Managed / operated in a Portfolio Management function with high level of operational maturity
- Ability to collect, synthesize and analyze data
- Proven leadership and influencing skills, and ability to work in highly matrixed, organization
- Ability to interface and build credibility at all levels of the company
- Experience developing, implementing and leading business processes
- Understanding of financial valuation and decision analysis
- Strong communications skills – written, presentation and verbal
- Experience with Organizational Change Management and/or Process Improvement initiatives as applied to a large globally-dispersed organization
- Consulting skills - ability to grasp the issue and situation, and recommend and implement a solution
- Strong risk/opportunity identification, analysis, and management skills
- Ability to work with high degree of independence while managing upward communications with executive leadership teams and management
- Experience in deployment and management of innovation/portfolio management tools preferred
21
Director, Viral Manufacturing Resume Examples & Samples
- Provide leadership and direction to ensure Deviations, Change Controls, CAPAs, and regulatory commitments are met on time and with the highest standards of quality. Responsible for ensuring assigned areas meet current FDA, International Regulatory agency and Corporate Quality requirements
- Provide direction and oversight for the shop floor and is accountable to ensure the highest safety and quality standards are maintained. Responsible for ensuring that all associates have what they need to complete their jobs safely
- Responsible for special projects including providing assistance and recommendations regarding buildings, equipment, and processes relating to the integration of the manufacturing area. Development of working relationships and strong communication links through all levels of the organization. Provides day-to-day support for the production floor to support completion of short-term projects
- Provides leadership and establishes departmental objectives to align with site vision for safety, quality, productivity, cost, continuous improvement, and employee involvement. Participate in development and execution of strategic initiatives
- Provide direction, evaluate and develop performance of direct reports
- Help in resolution of problems or introduction of changes in their respective areas
- Set performance standards and evaluate performance
- Provide career development and training advice and set short term and long term goals
- Provide regular feedback to direct reports on company and departmental operations
- Manages headcount and expenses in department to achieve site objectives and meet budget expectations
22
Director, Brand Development Manufacturing Resume Examples & Samples
- Achieve revenue goals by serving as a marketing consultant that identifies client objectives and then sells outcome based program designs that deliver measurable success against the clients’ success measure
- Develop a business plan that incorporates Catalina’s new advertising capabilities to increase client penetration and which leads to incremental revenue growth
- Build and manage relationships across multiple clients, multiple functions (brand marketing, field sales, consumer promotion) and at all levels of the organization
- Analyze data to design efficient and effective program solutions
- Manage accounts including revenue forecasting and the managing of programs, budgets and accounts receivable
- Education: Bachelor’s degree
- Experience: Five to eight years previous sales/marketing experience in CPG industry, emphasis in marketing, promotion or sales. Experience in digital/mobile roles in CPG industry or account management in digital/mobile agency a plus
- Strong knowledge of marketing and sales, with particular emphasis on the CPG manufacturer sales environment
- Excellent communication skills and the ability to interface and sell at all levels of management
- Proven track record of developing relationships with clients, co-workers, vendors and business partners
- Budget management, financial projection skills
- Ability to work independent of supervision and make decisions of wide variety and complexity
- Able to professionally perform multi-media sales presentations
- Organization and time management skills
- Strong working knowledge of Excel and proficiency with other basic software packages (Word, Outlook, PowerPoint)
- Able to understand several manufacturer categories and make recommendations to address strategic brand initiatives
23
Manufacturing Plant Director Resume Examples & Samples
- Applies knowledge of processes, equipment and system capability to set challenging individual and facility standards within manufacturing plant and warehouse operation
- Develops Annual Operating Plan for the plant
- Coaches supervisors and managers to achieve performance standards with regards to safety, line utilization and quality
- Manages direct and indirect controllable costs to meet overall cost index target
- Overall oversight of the scheduling process for receiving and delivering raw materials and finished products in a timely manner
- Overall oversight of the inventory process, ensuring optimal levels of full goods are maintained in order to fulfill daily sales needs
- Overall plant Profit and Loss (P&L) responsibility for production, maintenance, and quality control and warehouse
- A minimum of ten years of prior work experience in a high speed manufacturing environment
- A minimum of five years of prior work experience in a management position
- Prior experience in the consumer packaged goods industry
- Demonstrated ability to function successfully in a fast paced, changing work environment
24
Director of Manufacturing Resume Examples & Samples
- Establish and improve mechanisms to ensure the operations team provides products and services to our Customers in a timely, cost effective and quality manner to Biosciences Division
- Assess resource needs across the Division’s sites by working with site and functional leaders to assign resources per established priorities
- Provide thought leadership to site leaders across functions to achieve Division goals and create a culture of accountability and continuous improvement
- Drive performance of the Division’s operations to achieve and exceed financial targets through quality, cost efficiency and productivity
- Establish mechanisms to ensure high levels of collaboration across Network sites and global functions
- Develop a succession strategy and improve bench strength by facilitating and mentoring network and site leaders to be both exceptional players and coaches
- Identify projects and recommend appropriate course of action (e.g., product quality improvement, discontinuation, outsource, process improvement) to maximize profitability and supply
- Bachelor's degree in related discipline and/or equivalent experience. Advanced degree in related field is preferred
25
Director of Manufacturing Resume Examples & Samples
- Manage the company’s percentage of complete revenue recognition process by conducting twice a month project
- Plans, directs and coordinates the manufacturing of the New Iberia, LA site, which consists of 2 FBE coating facilities, 2 ID coating facilities, 2 concrete coating facilities, a 3 layer coating plant in one of our existing FBE plants and the Bayou Wasco plant, so that products are manufactured on schedule and within quality standards
- Responsible for planning the manufacturing capacity
- Formulates and implements manufacturing policies and programs to maintain and improve the competitive position and profitability of the operation
- Develop and formulate long/short range strategies and business plans for the business units that ensure business growth, profitability and alignment with corporate strategic objectives
- Develop, manage and control profits, plans, and budget, as well as implement cost effective systems of control over capital, operating expenses and human resources to maximize profitability
- Ensure the Company complies with SOX regulations
- Ensure all production metrics are captured and provide feedback to Operations on positive and negative trends
- Provide input to the project estimating process, participate in project bid review meetings and approve manufacturing estimates
- Develop the manufacturing plan and establish procedures for maintaining high standards of operations to ensure that products conform to established customer and company quality standards
- Achieve optimum employee levels with least amount of overhead and raw material costs to meet annual budgetary plan
- Identify, recommend and implement changes to improve productivity and reduce cost and scrap, monitor scrap and rework data. Direct the establishment, implementation and maintenance of production standards
- Direct and coordinate various programs essential to manufacturing procedures (e.g., training, safety, housekeeping, cost reduction, worker involvement, security, etc.)
- Bachelor’s degree in Engineering or Business Administration is required
- 12 years of manufacturing experience including 5 years of management experience preferred
- Successful experience in operations in a coating facility or related industry
- Must be experienced with manufacturing safety and environmental concerns
- Excellent communication skills, both verbally and written
- Highly independent, mature and strong leadership skills
- Proficient knowledge/ability with all Microsoft Office Applications required
- Ability to effectively communicate with all levels of the organization, both verbally and written
26
Senior Director ISC Manufacturing Resume Examples & Samples
- Manage all ISC related deliverables, activities, personnel, projects, and business alliance within the specific region of responsibility
- Primary responsibilities include regional supply planning, inventory planning, order fulfillment, and customer satisfaction within the specific region of responsibility
- Close collaboration with specific functions such as manufacturing, logistics, customer service, trade compliance, service and repair, demand planning, sales operations, and so forth
- Manage to Critical Growth Metrics – OTTR & DPPM and key performance metrics including but not limited to HSE, Delivery, Quality, Inventory, Cost, & New Product Integration
- Bachelor’s degree in a manufacturing, engineering or related discipline
- 10+ years of Operations background with strong experience in manufacturing, engineering, or sourcing required
- 5+ years’ Project Management experience required
- Honeywell or equivalent Six-Sigma certification at Green Belt level required
- MBA/Master degree
- Lean Expert or Black Belt preferred
- Previous experience successfully leading and developing a global team
- Experience with Project Management over a broad footprint or Multi-Site responsibilities
- PMP certification preferred. Previous experience of transitioning product lines and processes essential
- Strong knowledge of the Honeywell ISC Standard Transitions Process
- Highly developed influencing skills and able to be effective in delivering cross-functional solutions
- Highly self aware, recognizing the impact of communications, approach and behaviors on customers, peers, and other internal and external stakeholders
27
Manufacturing CI & Vave Director Resume Examples & Samples
- Drive and develop a sustainable cost out and cost productivity culture including VAVE, manufacturing footprint & LEAN across CPD
- Identify, sanction, support and facilitate robust, viable projects with business units globally to meet profit plan objectives
- Manage and direct VAVE and OpEx leadership teams to support business unit project activity
- Lead progress report outs to CPD leadership team reviewing current situation relating to established milestones and problem/high risk areas (e.g., technical, cost, and schedule)
- Identify and remove barriers to ensure progress and to mitigate risk, escalating to VP of Operations as needed
- Work directly with VP of Operations to gain approval at Electrical Product Groups level for major projects
- Plans, controls and integrates all project risks and requirements into the programs and measures all elements to ensure the requirements and goals are successfully achieved
- Gain approval for required capital appropriation request for assigned programs
28
VP / Director of Manufacturing Resume Examples & Samples
- Establish annual and monthly production objectives and operating budgets in support of the Company's long-term strategic plans and provide ongoing forecasts of anticipated results
- Establish short- and long-term production plans and strategies for the Company in collaboration with other colleagues and staff
- Set appropriate metrics and measure ongoing operating results to proactively manage production processes and individual team member performance
- Mentor and train multiple department managers and supervisors to achieve objectives
- Optimize and manage departmental operating procedures, processes, and policies to achieve operating margin, delivery, and quality performance targets
- Acquire detailed knowledge of product logistic, production, and functional requirements
- Coordinate new product launches with the Business Development and Engineering departments
- Occasional domestic travel for vendor, technology, or customer meetings
- Five plus years of experience managing and coordinating automated electronic manufacturing equipment and processes
- At least 10 years of manufacturing management experience in established organizations manufacturing electronic industrial products
- Detailed practical knowledge of electronic technology and systems
- A proven record of achieving production, delivery, and quality objectives in a growing technology or industrial product organization
- Demonstrated leadership skills to build, inspire and retain a high performance manufacturing team
- Proven ability to plan and manage at the operational level
- Ability to work collaboratively with colleagues and staff in a results-driven, team-oriented environment
29
Manufacturing Director, Suzhou, SPS, SPS Resume Examples & Samples
- Minimum 5 years experience on supervisor or manager position
- Expert on Six Sigma and Lean
- Experienced on project management
- Good at leadership and comminication skills
- Knowledge of cost accounting and ERP system is preferred
- Good English skill on reading, writing, listening and speaking
- Familiar with end to end ODM value stream and operation
- Good leadership, coaching, communication, negociation skills to drive results out of internal and external team
- Good at planning and organization to resolve issues and drive improvements
- Good knowledge on Lean and Six Sigma concepts
- Strategic thinking for long term targets, and capable to sturcture future org to support achiving these targets
- Good at innovate people, focus on team developement
30
Director of Manufacturing Procurement Resume Examples & Samples
- Leading sourcing projects to identify, evaluate and select preferred suppliers. This includes qualitative and quantitative analysis of suppliers for raw materials for laundry manufacturing such as steel and resin; Components for laundry manufacturing such as injection molds, press, die casting, electric/electronics parts; and packaging and printing materials
- This individual will be responsible for Contract Management for all designated H&A commodities
- Establish purchasing strategy and organization for this new manufacturing facility
- Review suppliers’ price & quality and analyze the cost table
- Lead project prioritization and execution
- Lead and influence manufacturing team and stakeholders on a course of action
- Formulate plans with minimal or vague information
- Lead and develop cost decomposition analysis leading to the discovery and elimination of waste
- Gather and analyze key procurement metrics using data collection techniques (downloading of transactional data to spreadsheet format) in order to report results to Senior Management
- Lead and develop savings reports, PowerPoint presentations and any other ad hoc reports
- Position will be responsible for communicating with internal stakeholders (internal departments including HQ) and external suppliers or 3rd party providers
31
Director of Manufacturing Excellence Resume Examples & Samples
- Customer order fulfillment across 3 NA locations (US, Canada, Mexico)
- Set performance targets and monitor performance to targets and strategic goals
- Ensure that Lean Manufacturing Principles are fully implemented, maintained and that Lean Manufacturing metrics are continuously tracked
- Evaluate talent and build organizational strength through coaching and team building
- Define and implement new technologies, processes, and tools that will support World Class manufacturing performance
- Drive cross functional collaboration with Customers, Materials Management, S & OP, Procurement, R & D, Suppliers, Project management,
- Project Engineering, and Installation to achieve improvements
- Collaborate on the development of annual and long range strategic roadmaps
- Build platform for knowledge transfer throughout NA production facilities and create best practice sharing group globally
- Facilitate change management through training, coaching and hand-holding of teams for sustaining the gains
- Fluent in Spanish and English
- Experience working internationally (Canada and/or Mexico)
- Experience in turnaround situations
- Demonstrated knowledge of ERP systems
- Skilled performance coach with ability to build strong, cohesive, high performing teams
- Ability to network and communicate with all levels of the company and across the globe
- Visionary, continuously updating industry knowledge
- Innovative and able to challenge the status quo
- Ability to travel approximately 50% to other NA facilities
- Demonstrated success leading cross functional teams
- Excellent written and verbal communication skills; day-to-day management and communications is a must
- Experience with Union workforces
- High attention to detail with solid organization, project management, and planning skills
- 15-20 years of overall manufacturing management experience to include
- Demonstrated success in Lean/6 Sigma Implementations
- Manufacturing management experience in multinational companies
32
Manufacturing Director, ES Resume Examples & Samples
- Work closely with Business and Operation Leaders to develop and implementation of the regional manufacturing strategy, roadmap and budget
- Lead effort around development of new /standardized technologies and manufacturing system/processes/equipment to support the product lines
- Develop and maintain an atmosphere which fosters mutual respect and continuous improvement in every discipline
- Develop high performance team & workforce to achieve & sustain manufacturing excellence performance
- Develop business and technical infrastructure to rollout new manufacturing technologies
- Provide environmental, health, safety and security leadership to locations by supporting the EHS initiatives including machine guarding, electrical testing and others manufacturing safety related matters
- Support major NPD projects and transfer projects and troubled sites
- Manufacturing: Process/Manufacturing, Equipment Test, IE, Facility Engineering
- Ten plus years’ experience in multiple Operations/manufacturing engineering/advanced manufacturing engineering, CI/LEAN functions
- BS in Engineering/Technology required, advanced degree in Engineering/Business preferred, additional post graduate academic studies in Operations Management a plus
- Significant management experience in a multi-national, matrix company, which goes to market through multiple channels
- Strong Leadership Competencies (Leveraging Resources, Vision and Purpose, Strategic Thinking, Accountability)
- Strong ability to influence and manage matrix resources
- Ability to drive change and continuous improvement. Must be highly knowledgeable in Lean, Six Sigma
- Strong problem solving and creativity skills
- Excellent communication and collaboration skills
- Electrical/Mechanical industrial experience
- Proactive, sense of urgency, structural approach problem solving, and leadership savvy
33
Senior Director of Manufacturing Controlling Resume Examples & Samples
- Provide strategic leadership of short- and long-term goals through the use of thoughtful techniques in the communication of the company’s mission and core values as a means to implement positive change and/or create organizational structure within GMQ
- Lead operational efforts through subordinates to complete the administration of business processes and services to ensure the operations effective achievement of goals
- Direct and control the broad activities of GMQ through the interpretation, application and implementation of company-wide policies and processes appropriate to the functional areas
- Ensure that budgets and schedules are within company requirements with significant organizational responsibility for the overall control of planning, staffing, budgeting, expense priority management, and recommendation and implementation changes of current methods
- Provide overall direction and guidance of all accounting and finance reporting, budgeting and forecasting processes within GMQ on a routine basis; acting as a business partner by analyzing operational data and providing recommendations as appropriate
- Oversee accounts payable operations; ensuring vendors, invoices and other expenses are paid in a timely and accurate manner
- Coordinate all required internal and/or external audit activities on a routine basis; serving as the primary point of contact as necessary
- Manage internal controls within GMQ through process reviews, business process analyses and internal control testing; ensuring compliance with company policies and procedures, GAAP, SOX and other regulatory requirements
- Collaborate with cross-divisional teams in the analysis and reporting of capital spend activities
- Provide leadership, guidance and coaching for all direct reports to maintain an engaged and productive workforce; partnering with Human Resources on employee matters
- Collaborate with employees in the establishment of clear and concise development plans to ensure succession planning and the advancement of future leaders within the organization
- 10+ years’ related experience
- 5+ years’ experience as a Manager; or 5+ years’ experience in a senior managerial role
- Certified Public Accountant (CPA) license preferred
- Strong computer skills with advanced proficiency in word processing, spreadsheet, database, presentation and email applications. Experience with SAP preferred
- Strong management skills with the ability to lead cohesive and productive teams
- Strong interpersonal skills with the ability to communicate with all levels of management through diplomacy and tact
- Proficiency in Spanish a plus
34
Director of Manufacturing Resume Examples & Samples
- Develop, implement and lead safety program and ongoing efforts. Role model a safe work culture, prioritizing employee safety and food safety in all activities
- With input from the Plant Managers, develop production & scheduling plans based on sales requirements, raw material supply and plant capacities
- In conjunction with the Director of Field Operations, determine long and short-term action plans that will provide most effective production and delivery of raw product to processing facility
- Reduce costs and improve efficiencies by optimizing and establishing production standards including labor, material, scrap and rework
- Develop and implement a preventative maintenance program and minimize equipment downtime
- Act as liaison between business unit and other sister companies within the organization
- With the support of the Division Engineering, provide direction of engineering activities and capital projects related to manufacturing locations consistent with division needs and capital plans
- Develop & maintain budgets and control costs related to areas of responsibility
- Implement a daily management system to ensure accountability against performance metrics and timely reporting of performance metrics
- Establish & maintain and enforce programs and policies that ensure production objectives are met at the lowest cost and foster positive employee relations. These programs and policies must be consistent with company directives as well as applicable laws and relations (e.g. GMP, HACCP, OSHA, ISO, etc.)
- Provides training for Plant Managers and staff to ensure their knowledge and understanding of all policies and procedures relating to the quality, safety and productivity of products
- Developing short & long term strategic initiatives with overall coordination between 2 production facilities
- Employ an active leadership style, spending 50% of time on manufacturing shop floor
- Develop and execute individual development plans for leaders within team
- Lead focused teams to proactively achieve incremental improvements in manufacturing
- Ability to solve practical problems in situations where only limited standardization may exist
- Ability to learn and use computer business applications
- Self-Motivated and willing to learn and adapt to a variety of situations
- Good planning skills and attention to details
- Strong project management skills from inception to completion
- Good communication skills (oral and written)
- Must possess the ability to learn, understand, and develop all processes/procedures
- Knowledge and understanding of TQM and SPC principals, GMP’s etc
- A working knowledge of vegetable crop production is desirable
- BS, BA in Engineering or equivalent experience in related field
- 15+ years of manufacturing experience
- CPG experience required. Food production experience preferred
- Direct experience with process flow, high speed automated production systems
- Understanding of continuous improvement concepts and application
- Critical thinker with strong analytical, numerical, and reasoning abilities
35
Director of Manufacturing Resume Examples & Samples
- Directs subordinates in meeting all quality and regulatory standards such as (OSHA, FDA, AIB, etc.)
- Maintains a pleasant and safe working environment for all employees and contract workers
- Ensures compliance with all company policies and procedures
- Directs subordinates in daily production activities and demands
- Sets production goals for subordinates to meet
- Reviews and approves purchases and expenditures and assists in requests for capital projects
- Orders, receives, and stores supplies
- Position may be responsible for operating the facility metal detector(s). For this job responsibility, operator must be fully trained and certified
- Practices and complies with all Company policies and procedures (EEO, Harassment, Safety, Sarbanes Oxley, etc.)
- Performs other duties which are deemed by management to be an integral part of the job, including but not limited to fulfillment of work schedules, adherence to attendance policies, and practicing and complying
36
Manufacturing Excellence Director Resume Examples & Samples
- Leads the Focused Factory Planning Sessions by providing the training to the site and supporting the selection and number of focus factories at the sites
- Supports the implementation of focused factories at the critical sites
- Develop and maintain critical deliverables tracker for FF implementation
- Develop key success factors for each implementation phase of the Focused Factory
- Create monthly reporting around the Focused Factory implementation at the critical sites
- Partner with learning and development to identify training programs needed to support FF implementation
- Partner with communications to develop a standard communications plan for the Focus Factory roll-out at the critical plants
- Identify and share best practices within the focused factory
- Drive the lessons learned activity following each focused factory planning session
- Partner with Core Competency leaders to align maturity models, standards, templates and training to the standard focus factory process
- Bachelor's degree, preferably in an engineering or business discipline
- Must have 10+ years’ experience in Manufacturing Operations & Engineering
- Must have 5-7+ years’ proven hands on experience with driving lean and continuous improvement in a manufacturing environment with documented breakthrough results
- Must have 3-5 years’ project management and change management related experience
- Proven experience improving processes with bottom line results in a global automotive matrix environment
- Understanding of manufacturing processes
- Strong knowledge of lean manufacturing
- Strong communication skills and the ability to interface and influence at all levels of the organization
- Ability to manage in a matrix environment
- Challenges the status quo and champions new initiatives
- Must be results oriented and possess a drive for meeting deliverables and deadlines
- Leadership skills in problem solving and change management are required
- Be a self-starter with excellent organizational skills in planning and organizing to handle multiple tasks concurrently
- Advanced problem solving capabilities, attention to detail and numerical aptitude
- Proficient with Microsoft Applications: Word, Excel, Outlook, and PowerPoint
- Master’s degree in engineering or business
- Strong knowledge of automotive processes
37
Manufacturing Director Resume Examples & Samples
- Leads, plans and budgets for all manufacturing production, quality and shipping in an efficient manner in accordance with policies, principles and established by the Company
- Utilized effective leadership skills to develop and motivate skilled management team and workforce and maintain an effective relationship with all parts of the organization
- Improve the business processed for each department through analysis and collaboration
- Gets involved in long-term business planning at the managerial and executive level
- Provide Strategic direction to the Plant Managers in all aspects of the business operation
- Provide reports of performance results and corrective planning when required to executive team
- Analyze the performance of support functions for manufacturing departments and make recommendations for improvement
- Provide Analysis and justifications of CAPEX requirements
- Provide CI (Continuous Improvement) initiatives and tracking
- Works with Corporate team to develop growth strategies
- Develops forecast and growth strategies for new projects
- Reviews production costs and product quality, and modifies production and inventory control program to maintain and enhance profitable operation of Company
- Recognized production problems or problems and takes corrective action to continually produce quality product to customers
- Assure reasonable accurate distribution of time to specific jobs
- Ensure all employees are following proper policies/procedures in the different areas
- Bachelor’s Degree in Business Administration or related field (MBA preferred)
- 10+ years’ experience in a leadership role
- 5+ years’ experience in the manufacturing sector
- Strong analytical, problem-solving, communication (both oral and written), organizational skills
- Strong computer skills and solid presentation skills
- Experience with developing budgets and writing business plans
- Able to travel with the United States, Mexico and overseas
38
Director of Manufacturing Resume Examples & Samples
- Oversee the Manufacturing management involved in a variety of production and/or operation functions such as assembly, inspection, test and/or final test which is related to the manufacturing of the company’s capital equipment and systems, electronic, mechanical, electro-mechanical, and/or components, subassemblies and subsystems
- Prioritizes production schedules based on customer commitments, available manpower, equipment efficiency, capacity and materials requirements
- Responsible for establishing and meeting manufacturing metrics such as; service, inventory, etc., as well as improving cycle time performance
- Ensures timely response to operations issues impacting customer satisfaction; acts as an interface in the establishment of and ensuring conformance to customer requirements; prepares detailed analysis of cost of quality opportunity and initiates corrective action
- Oversees the prevention of workforce accidents and injuries. Responsible for ensuring and documenting that all department workforce (including temporaries) receive and follow appropriate department training including Environmental, Health and Safety training. Implements, emphasizes importance of and monitors compliance to appropriate safety policies and procedures
- Develops personnel to include training and career development; manages the performance management process to include the development of team and individual employee selection, hiring, reward and discipline processes
- Identify, communicate, and resolve production, personnel, quality, and safety issues
- Ensure that equipment and team conform to ISO 9001, QMS and VPP requirements
- Integrate Lean techniques to identify inefficiencies, make recommendations and support/follow through on process improvements
- Develop, lead, and execute daily production plans, implement a strategy to reduce cycle time, and drive variable cost productivity, reduce in process inventory levels, and improve quality, service, and safety
- Partner with Engineering, Quality, and Product Management teams on new product development as required
- Provides leadership to managers and professional staff
39
Director of Domestic Manufacturing Resume Examples & Samples
- Lead the Domestic Manufacturing organization that includes the development of new product, planning, purchasing/sourcing and manufacturing operations
- Champion company objectives for safety, quality, cost and delivery of domestically made footwear to our customers and drive quantitave lead time reduction
- Guide, develop, inspire and lead a team of managers across the domestic organization to achieve objectives and strategies
- Implement strategic manufacturing initiatives and drive continuous improvement initiatives across the organization that will reduce waste and positively impact the Domestic P&L
- Partner and champion new digital manufacturing solutions with other NB innovation teams
40
Director, Advanced Cellular Manufacturing Resume Examples & Samples
- Knowledge of FACT and FDA cell manufacturing guidelines
- Ability to problem-solve independently and make decisions
- Ability to develop and manage budget
- Knowledge of laboratory operations and equipment
- Ability to plan and schedule tasks and projects, including writing of reports and contribution to proposal/grant applications
- Respect: Demonstrate respect for self and others--behave professionally
- Integrity: Act with integrity and honesty
- Teamwork: Commit to and demonstrate teamwork
- Excellence: Ensure excellence, quality, and high ethical standards in conduct and performance
41
Manufacturing Director Resume Examples & Samples
- Drive Execution
- Exercise Business Acumen
- Build Organizational Talent
- Encourage Innovation
42
Regional Manufacturing Director Asia Resume Examples & Samples
- 10 years+ manufacturing management experience in chemical industry, rich experience on high HSE risk product manufacturing
- Bachelor’s Degree, Science preferred, MBA is plus
- Strong leadership skills with a proven ability to drive a performance based culture and motivate organizations
- Strong capability on long term strategy planning and short term execution
- Mindset on continuous improvement and capability to push change happen
- Excellent written and verbal communication skills, must be fluent in English
- Strong coordination capability to gain stake holders’ commitment
- Understanding if multi-culture in Asia and has ability to lead multi-functional teams
- LI-IRY
43
GMP Manufacturing Director Resume Examples & Samples
- Provide senior leadership for the CPF and PD departments including hiring of manufacturing staff and providing mentorship and staff development
- Use of strong communication and teamwork skills to build relationships with stakeholders
- Demonstrate outstanding technical acumen, operational understanding and GMP compliance in the maintenance and continued expansion of the Cell Processing Facility
- Lead the improvement and implementation of all GMP procedures and policies related to Manufacturing operations
- Identify and mitigate risks in manufacturing operations that could adversely impact project outcomes and timely delivery of critical treatment to patients
- Champion the implementation of new technologies and systems
- Foster a culture of strong GMP compliance
- Ensure all staff maintains appropriate level of training and meets compliance standards
- Establish and effectively manage project-specific and departmental annual operating budgets for the Cell Processing Facility
- Evening and/or weekend work may occasionally be required based on project need
- A BS degree in bioengineering or the biological sciences
- At least 8 years of experience in cell culture based GMP manufacturing operations and cell culture based manufacturing methods, which may include cell selections, cell culture, harvest and cryopreservation
- Experience in cell therapy applications with T-cells and stem cells
- At least three years of managing a multi-product GMP manufacturing facility involving the complex scheduling and coordination of staff, materials, and manufacturing operations
- At least three years of experience of direct supervisory experience of technical professionals and in providing guidance, mentorship and support to direct reports so that they can best manage their teams and projects
- Expert knowledge of FDA regulations, GMP systems and operational excellence required for the manufacture of therapeutic products
- Demonstrated ability to perform long-term project planning with meaningful timelines and budget forecasting
44
Director of Manufacturing Resume Examples & Samples
- Bachelor’s degree in Manufacturing or Business, or a related engineering field required
- Ten+ years of leadership experience in world class manufacturing
- Skills and experience with manufacturing business process, lean manufacturing and business process improvement
- Experience managing a large group of direct and indirect reports
- Experience and skills in budgeting, planning and organizing
- Experience with consumer products or durable goods manufacturing
45
Director of Manufacturing Resume Examples & Samples
- Analyzes truss plants, then devises and implements a plan for improving the operations of each plant
- Implements systems to benchmark the performance of each plant on a recurring basis
- Ensures that the company is optimizing the use of computer technology in its manufacturing operations
- Conducts market feasibility studies and oversees the opening of new plants, as requested
- Develops a strategy for using structural engineering as a strategic tool
- Motivates and leads manufacturing, including setting short and long-term goals and forecasts, establishing and implementing improvement programs and policies and providing training and leadership
- Enhances the bottom line by optimizing lead times, improving on-time delivery performance, reducing labor and scrap, maximizing all resources, and increasing output
- Contributes to the development and execution of the company’s operating objectives and facilitates significantly increased growth and profitability
- Recommends methods, materials, and layouts for improvement based on the current needs and capabilities of current manufacturing processes. Develops prioritized, annual capital improvement plans
- Keeps abreast of current manufacturing processes and philosophies
- Improves product quality and maintains high customer satisfaction
- Maintains and facilitates high standards including housekeeping and safety
- Ensures productive and effective relationships with vendors and entities, thereby facilitating highly competitive products at profitable costs and with high quality
46
Manufacturing Director Resume Examples & Samples
- Production Operations Management
- Related field of study
- Has depth of understanding on Lean Manufacturing and Theory of Constraint for Line Management
- Ability to escalate critical issues and communicate with upper management
- Has agility to manage and execute prioritized action items from both tactical and strategic point of views
47
Manufacturing Director Resume Examples & Samples
- Bachelor’s degree – Engineering, Business Administration or other discipline related to the manufacturing environment
- 10 years of direct experience in manufacturing / operations
- Experience comprehending and training others on Quality System Process Documents
- Experience understanding proper documentation/quality requirements for a regulated environment
- Experience with manufacturing systems such as JDE, FACTORYworks, or SAP
48
Manufacturing Director Resume Examples & Samples
- Effectively plan manufacturing and staffing to meet production scheduled on time and achieve quality goals using equipment, materials and human resources efficiently
- Administer department’s budget
- Responsible for ensuring that the Production Planning are accurately received, communicated and attained, while maintaining and acceptable level of customer service
- Responsible for managing all processes, equipment, operations personnel and other resources associated with the assembly, packaging and delivery of manufactured medical devices
- Manufacturing Director is also responsible for the processes and products continuous improvement. This is achieved by managing operations, monitoring its performance and providing the required resources and environment to ensure timely execution of production schedules
- Provide management and direction in the master schedule of the Bard Juarez facility
- Leads efforts to expeditiously resolve manufacturing and service issues coordinating with BOC, Suppliers and Quality Assurance
- To interact with other Staff Managers as needed to assure high level of support of the manufacturing operations
- Assure compliance to Bard’s Policies and Procedures
- Mandatory compliance to general and safety procedures applying to this position
- Previus experience in Medical Device Industry
- Fluent in both English & Spanish
- World Class Manufacturing skills application experience
- ISO13485:2003 knowledge
- Certified in Production and Inventory Management (CPIM) a plus
- College degree in Engineering or Administration Field
- Five years of experience as a Director or in a Manufcaturing Sr. Manager position
49
Manufacturing Director Resume Examples & Samples
- BSEE, 15+ years of experience in power module development & manufacturing. MSEE or PhD is preferred
- 10+ years of experience with a top semiconductor module manufacturer
- In-depth knowledge of IGBTs/MOSFETs and WBG technologies and their use in power modules
- Experience working with Tier 1 customers, Sales, FAE, Business Units, Technology Development, Technical marketing & packaging development in a matrix organization
50
Director of Manufacturing Resume Examples & Samples
- Prepares / approves process specific protocols, Policies, and Standard Operating Procedures (SOPs)
- Ensures MFG schedule is maintained assuring customer timelines remain intact
- Supervises, plans and reviews operations for assigned staff, including responsibility for training, managing and evaluating as well as coordinating, scheduling and assigning work and maintaining standards
- Evaluates / Recommends hire / transfer / promotion / discharge and salary changes and acts on employee problems
- Conducts employee performance appraisals in a timely and objective manner
- Interacts with clients to discuss project planning and requirements
- Reviews and recommends execution content for proposals for MFG programs
- Design production schemes and process improvements
- Interpretation of MFG PD and /or verification run results
- Provides strong in-house guidance on science and technology
- Interacts with internal staff to identify areas for improvement or development and oversees improvement efforts delivering performance efficiencies to impact departmental gross margin
- Travels with other WuXi AppTec staff to visit clients / vendors as appropriate
- Presents technical seminars at external professional meetings
- Prepares and report key performance measures weekly, Quarterly and Annually
- Drives startup operations for new facilities through technical and organizational leadership from the Manufacturing lens to keep the project on schedule and within budget
- Drive financial performance of department through industrial efficiency, human capital management and greater utilization of physical assets
- Specific responsibilities include specifying equipment, identification and development of Standard Operating Procedures (SOPs) and Master Batch Records, commissioning and validation as well as staffing and training of the Manufacturing group to be competent in current Good Manufacturing Practices (cGMP). Interacts with Engineering, Maintenance, Validation, Quality Assurance, Quality Control, Materials Management groups, and material/equipment vendors and commercial partners
- Knowledge of cGMP guidelines is required
- Ability to make decisions based on a wide knowledge of factors where application of advanced or technical concepts is predominantly required
- Ability to use judgment as dictated by complexity of situation
- Ability to work under limited supervision and to handle problems of a difficult nature
- Ability to accomplish the described duties through the use of appropriate laboratory equipment (i.e. biohazard hood, centrifuge, incubator, and autoclave) and computer equipment and software. (i.e. Microsoft Word, Outlook)
- Ability to record data accurately and legibly
- Ability to understand and follow verbal or demonstrated instructions
- Ability to express or exchange ideas by means of the spoken word
- Ability to work effectively as part of a team and to exhibit effective interpersonal skills
- Ability to receive and comprehend and to effectively communicate detailed information through verbal and written communication
51
North American Regional Manufacturing Director Resume Examples & Samples
- Identifies, develops and ensures delivery of RM manufacturing strategies for the region; ensures that these strategies are capably implemented at the facility level by local leadership teams
- Leads the process and measurement system and indicators at each plant of the region to ensure the standardization and transference of the best practices among all the plants
- Directs regional efforts to achieve highest levels of customer service, including new product manufacturing, on time delivery, and quality requirements
- Ensures that global capital execution processes are in place in each plant and projects are executed on time and within budget
- Implements clear budgeting processes for expense and capital budgets. Champions reliability and cost-appropriate investment in maintenance replacement and upgrade capital projects. Leads and coordinates plans and initiatives in the region to manage cost control to be able to efficiently use the investments and to reduce costs. Develops and proposes mid term investment plans to maintain technological competitiveness. Provides sponsorship, guidance, implementation resources and priority to reduce maintenance costs while increasing overall unit uptime
- Ensures that production plants are producing products within agreed upon specifications and that continuous improvement plans are in place