Manager, Manufacturing Resume Samples
4.5
(137 votes) for
Manager, Manufacturing Resume Samples
The Guide To Resume Tailoring
Guide the recruiter to the conclusion that you are the best candidate for the manager, manufacturing job. It’s actually very simple. Tailor your resume by picking relevant responsibilities from the examples below and then add your accomplishments. This way, you can position yourself in the best way to get hired.
Craft your perfect resume by picking job responsibilities written by professional recruiters
Pick from the thousands of curated job responsibilities used by the leading companies
Tailor your resume & cover letter with wording that best fits for each job you apply
Resume Builder
Create a Resume in Minutes with Professional Resume Templates
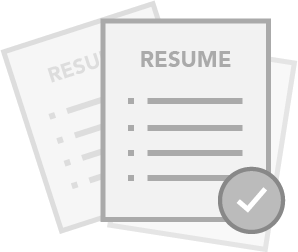
CHOOSE THE BEST TEMPLATE
- Choose from 15 Leading Templates. No need to think about design details.
USE PRE-WRITTEN BULLET POINTS
- Select from thousands of pre-written bullet points.
SAVE YOUR DOCUMENTS IN PDF FILES
- Instantly download in PDF format or share a custom link.
GM
G Mertz
Gunner
Mertz
1727 Schowalter Spur
New York
NY
+1 (555) 796 3934
1727 Schowalter Spur
New York
NY
Phone
p
+1 (555) 796 3934
Experience
Experience
Phoenix, AZ
Manager Manufacturing
Phoenix, AZ
Spinka LLC
Phoenix, AZ
Manager Manufacturing
- Establish and implement standard manufacturing and materials practices by implementing and executing the Honeywell Operating System, HOS
- Drive manufacturing team to achieve established targets for Safety, Quality, and Productivity by using Lean Manufacturing Tools and 6 Step Problem Solving
- Responsible for controlling and reducing costs, and improving productivity of both labor and capital equipment
- Expand your breadth of knowledge and challenge you with a broadly focused leadership role, working on cutting-edge products with an industry leading company
- Maintain high product quality and manufacturing yield while ensuring optimal use of resources and adherences to best safety practices
- Provide exemplary leadership in a fast pace environment subject to constant change while dealing with information and resource constraints
- Thorough knowledge of 9CFR and EU regulations, Good Manufacturing Practices (GMPs), and Good Laboratory Practices (GLPs)
Detroit, MI
Manager, Manufacturing
Detroit, MI
Goyette Inc
Detroit, MI
Manager, Manufacturing
- Supporting Management and functional leaders with planning production of PPU populations, production outcomes and troubleshooting actions
- Responsible for managing the assigned assembly process and the related workforce. Communicates goals and strategies to the workforce, which may include represented and unrepresented components. Manages issues, solves problems, and delegates to team to bring solutions. Coordinates and interacts with functional areas and business units that support the production floor, exercising indirect leadership. Gets results from professional and/or direct labor employees by establishing work plans and delegating assignments
- Build Powerful Networks - Involves networking internally and externally to develop and maintain relationships in all kinds of organizations – knowing what they do, how they can help you, and how you can help them. Internally, it is working together across organizational and cultural boundaries, functions and businesses. Externally, these networks include customers, but they also extend to suppliers, alliance partners, customers' customers and others – some of whom might fall well outside the normal sphere of the organization. (Networking and Relationship Management, Collaboration and Teamwork, Conflict Management)
- Leading and Managing the work of the reporting organization
- Unleash Energy - Focuses on tapping into and unleashing the incredible talent and passion of every person in the organization, starting with oneself. Leaders first reach deep inside themselves to embrace their hopes and dreams. They approach situations with passion. They then help others embrace their own hopes and dreams and guide them in applying their passion to achieve the goals of the organization and to open up new possibilities. Leaders express commitment to and confidence in people, often beyond the level of confidence people have in themselves. (Selecting Talent, Developing Self and Others, Inspiring and Motivating Others)
- Establish, monitor and track operational KPIs and performance to Master Plans
- Build a team, provide necessary training and ongoing coaching, discipline and recognition of direct staff, including performing annual performance reviews
present
Dallas, TX
Engineering Manager, Manufacturing
Dallas, TX
Lind-Miller
present
Dallas, TX
Engineering Manager, Manufacturing
present
- Plans, manages, and performs the activities of a professional staff of engineers that is responsible for
- Providing engineering support to the production area to maintain optimum levels of productivity in terms of cycle times and quality
- Coordinating the introduction of new assembly processes on to the production floor by preparing operation sheets that describe specific production tasks
- Partnering with design engineers throughout the design process from concept to prototype in order to ensure that maximum production efficiency is achieved
- Contributing to the preparation of the annual capital expenditure plan for the selection and purchase of new production equipment
- Developing facilities layouts and providing these to the Facilities Department to support the installation of new equipment
- Researching to estimate the cost of new equipment and develops options
Education
Education
Bachelor’s Degree in Life Sciences
Bachelor’s Degree in Life Sciences
University of Illinois at Chicago
Bachelor’s Degree in Life Sciences
Skills
Skills
- Strong analytical thinking, problem solving skills and communications skills (both written and oral) with attention to detail
- Good knowledge in continuous improvement practices and a proven record of success in implementation
- Strong attention to detail
- Strong working knowledge of manufacturing methods, techniques, and related
- Strong technical knowledge
- Excellent computer skills
- Knowledge of Excel, Word, PowerPoint, Project, Oracle or other related business software
- Ability to read, speak and write in English
- Ability to read and interpret documents such as Parts Manuals, safety rules, operating and maintenance instructions, and procedure manuals.
- Strong written and verbal communication skills
15 Manager, Manufacturing resume templates
Read our complete resume writing guides
1
Hardware Engineer Manager Manufacturing Resume Examples & Samples
- Responsible for research, analysis, design and specification to provide immediate and long term hardware solutions that will improve operational reliability, safety and serviceability
- Research, select and manage vendors in the production of hardware devices
- Research and material science analysis for hardware
- Responsible for the troubleshooting and resolution of systems issues related to hardware interactions
- Responsible for overseeing manufacturing& production operations as well as installation to provide high quality devices with little to no downtime
- Performs modifications to hardware specifications as directed by management or engineering
- Document and/or review vendor documentation for newly created systems and create Standard Operating Procedure documentation where appropriate
- Understand and actively participate in Environmental, Health & Safety responsibilities by following established UO policy, procedures, training and team member involvement activities
- Advanced Vendor Management & Negotiating
- Strong integrations skills, coordinates multiple disciplines at the same time
- Advanced wired, wireless and radio networking skills
- Ability to integrate software and hardware solutions
- Ability to “think outside the box” to deliver creative solutions to challenges
- Excellent Customer Focus
- Strong Communication skills
- Strong Team orientation and excellent interpersonal skills
- Critical Thinking and Problem Solving Skills
- Self-Motivated, particularly with regards to maintaining technical skills
- Ability to meet deadlines, multi-task, and work under pressure
- Passionate about coding world-class web and mobile solutions
2
Accounting Manager Manufacturing Industry Resume Examples & Samples
- Monthly financial statement, including financial statements for quarterly and annual SEC filings, financial statement footnote disclosures, etc
- Management of audit requests from external auditors
- Preparation and/or review of routine and non-routine journal entries
- Preparation and/or review of general ledger reconciliations and account analyses
- Management of Sarbanes-Oxley requirements
- Support the financial forecasting activities
- Lead, supervise and coach the development of the accounting team
- Drive process improvements and identify opportunities for cost savings
3
Engineering Manager / Manufacturing Engineer Resume Examples & Samples
- Managing engineering supervisors and overseeing the application of technical resources to support product development, product support issue resolution (Continuous Process Improvement, Dealer Solution Network), cost reduction initiatives, and other project work
- Capturing market place and customer future needs and developing strategies an Multi -Generational
- Product Planning to position the segment accordingly
- Effectively ensuring support of corporate CPS initiatives
- Managing a department through subordinate supervisors/managers and professionals
- Providing direction, focus, motivation, and encouragement for subordinates
- Responsible for all personnel issues and performance evaluation of subordinates
- Thai Nationals, Male or Female
- Bachelor’s degree or higher in any engineering fields
- At least 15 years’ experience related administrative management in manufacturing environment and minimum 5 years’ experience in management level
- Complete understanding with manufacturing performance management and tools
- Excellent interpersonal skills are required in order to deal with sensitive issues, develop others, or persuade others inside and outside the department to take specific actions
- Strong leadership skills and good team player
- Strong written and verbal in English communication skill
- BA or Higher in Mechanical, Mechatronic, Industrial Engineering or any other equivalent fields
- Minimum 3 years working experiences in manufacturing engineering, designing, developing and implementation of equipment automation and advance manufacturing project
- Experience in heavy manufacturing is preferred
- Knowledge in FMEA, 6-sigma, statistical analysis and strong skill in project management
- Be a good team player and able work with diverse work group
- Basic command of English
4
Technical Account Manager, Manufacturing Resume Examples & Samples
- Account Plan Development and Management: In partnership with Major Account Executives, develops technical account plan and executes on strategy/tactics for closing business. Coordinates with global account resources including the Client Success Manager and Strategic Account Manager (where applicable) on account strategy and customer initiatives. Uses Autodesk company standard sales methodologies to ensure technical closure and alignment with sales strategies
- Customer Relationship Management: Develops required level of knowledge of customers' business process, workflows, and technical requirements in order to build "trusted advisor" relationships with customers. Maintains a comprehensive knowledge of the business processes, technology trends, and workflows, within their domain of expertise, to provide insight and guidance required to position the value of current and new Autodesk solutions
- Technical Discovery & Solution Fit: Manages technical discovery. Provides leadership and guidance in the formulation of requirements definitions, scope documents, user needs studies, process assessments and project assessments for sales opportunities. Leverages Autodesk software, applications, and services together with other resources to develop innovative solutions that satisfy technical, fiscal and schedule constraints within the customer’s business
- Customer Closure: Responsible for aligning with key customer stakeholders to secure business and technical closure of the proposed solution. Manages technical evaluations, defines solution architecture, facilitates product demonstrations, "pilot" projects, etc. Provides technical validation and assesses feasibility, correctness and completeness of proposed solutions; applies best practices in solving business problems. Assesses and directs customers regarding strategic product issues involving license deployment, licensing structures and license management to maximize customer satisfaction and product revenue
- Collaboration: Develops and maintains trusted working relationships with the sales force and adjacent business resources (sales management, consulting, business development, global technical sales, marketing). Oversees and guides these resources within outlined account objectives to ensure customer satisfaction and business closure, coordinate global strategy and account coverage, and support broader decision making whilst enhancing the customer experience with Autodesk
- Internal Leadership: Shares best practices, competitive information, innovation, and thought leadership within the sales organization, product divisions, and technical sales organization locally and globally. Interacts and communicates with the various business units of Autodesk to ensure that Major Account needs are met. Provides answers and shares knowledge on technical product and integration information pertaining to Autodesk or competitor products
5
Field Marketing Manager Manufacturing France & Benelux Resume Examples & Samples
- Leading all regional marketing activities, including driving awareness, demand gen, and sales support
- Management of the France/BNL Field Marketing budget for Manufacturing, and planning and execution processes
- Working closely with Sales on market strategies
- Working in collaboration with internal Subject matter experts to drive plan and execution of all inbound marketing initiatives including, social media, content marketing, digital marketing SEO/SEM and nurturing programs
- Using marketing automation tools to monitor and execute programs
- Setting up metrics and analysis to identify target markets and refine campaigns
- Providing weekly reporting and making data driven decisions
- Planning and execution of traditional lead generation tactics such as events and telemarketing
- In collaboration with the PR team, driving awareness programs and key messages
- Participating in Autodesk software go-to-market strategy planning with global marketing counterparts
- Adapting global GTM strategies to build and execute end-to-end, integrated regional marketing plans
- Overseeing of asset localization
- You’re a regional expert. You understand your region inside out, including what makes it unique to other places around the world. You understand buyers, their behavior, communication etiquette, popular social channels, and you have insight into the competitive landscape in your region
- You’re strategic and tactical: You have experience providing input to global marketing strategy planning to ensure execution at the regional level. You know when to wear your strategic hat, as well as when—and how—to roll up your sleeves and execute on tactical plans to get things done
- You’re a modern marketer. You’re familiar with the tools modern marketers use to drive awareness, demand, and adoption of technology software and services. You have experience pairing marketing automation tools with buyer-centric content to attract and nurture leads across multiple channels
- You’re a communications pro. You’re convinced that effective marketing starts with a clear understanding of your target audiences. You know how to find these audiences in your region, the best channels to use to engage them, what to say once you’ve made contact, and how to say it
- You’re a natural leader. You have experience leading direct and indirect teams as well as external contractors and agencies. You understand the difference between “managing” and “leading” people; your style and tact help you inspire others to get behind your cause and take a journey with you
- 10 Things That Describe You
- Regional expert
- Execution focused
- Content savvy
- Marketing innovator
- Creative thinker
- Great coach
- Impact driven
- Highly accountable
- Decision driver
6
Manager, Manufacturing Excellence, AAC Resume Examples & Samples
- Support the develop, grow and maintain large accounts and strategic clients across Asia-Pacific
- Implement and deliver Manufacturing Excellence solutions together with local/regional teams
- Working in a fast growing and challenging environment with like-minded people across the region
- Delivering large-scale, complex supply chain management and transformation projects with a focus on manufacturing excellence and productivity improvement programs
- Working with client organizations to enhance shop floor performance through the implementation of TPM, Lean Six Sigma and other manufacturing improvement tools
- Assistance to the project Manager in delivering proposals and projects
- Building relationships with external clients and internal peers
- Working in a collaborative team analyzing client issues and developing solutions
- Anticipating and identifying risks and raising issues with senior members of the team
- Carry out reliability testing needs for R&D and production. This involves performing optical measurements on films, recording data, image capture of material under test and analysis of data
- Bachelor’s degree in an engineering (or equivalent) discipline
- Experience in deploying TQM-based analytics software/technology an added advantage
- 3-4 years of professional experience in Lean Manufacturing, Six Sigma, Line Management, Production Control etc. on a regional basis
- Tactical and process oriented problem-solving
- Strong commitment to professional client service excellence
- Excellent interpersonal relations and demonstrated ability to work with others effectively in teams
- Superior verbal and written communication and presentation skills
- Ability to develop and present new ideas and conceptualize new approaches and solutions
7
Industry Manager Manufacturing Resume Examples & Samples
- Driving regional thought leadership for MFG focused FOMT supporting IM in Japan
- Effectively promoting FOMT to partners and customers
- Effectively communicates strategies and GTM plans to achieve Autodesk’s and MFG goals
- Communicates Partner and customer needs
- Analyzes key metrics and biz health in order to initiate action plans for optimization
- Effectively networks and communicates with multiple regional and global internal stakeholders to ensures country pan development and execution
- Collaborates effectively with regional Managers, Sr. Managers and Directors and teams
- Supports innovations
8
Manager, Manufacturing Excellence Resume Examples & Samples
- Lead, manage and execute Manufacturing Excellence projects that deliver measurable and sustainable increase in manufacturing efficiency, quality and speed
- Ensure that lean manufacturing principles are maintained with all projects and that lean manufacturing metrics are continuously tracked
- Ensure KPI data for automation and other efficiency improvement initiatives is properly tracked and data made available
- Assist building platform for knowledge transfer accessible throughout the adidas-Group organization and supplier groups. (BPM, training material, news bulletin, etc.; supplier summits, exchange meetings, etc.)
- Communicate progress throughout LO and sourcing country utilizing knowledge transfer platform. (BPM, training material, news bulletin, etc.)
- Liaise with Continuous Improvement Team on training and consulting needs for aSL suppliers and support driving direction for lean initiatives in footwear sourcing
- Expert knowledge and experience in Lean 6 Sigma practices and training techniques
- Innovative and challenge status quo
- Strong communication and interpersonal skills with all levels of business
- Capable of frequent travel
- 5–8 years footwear industry experience, or industry related experience
9
Manager Manufacturing Excellence App Resume Examples & Samples
- With support from the central M.E. team, be responsible for M.E. T1’s within the region
- Monitor, direct & support the M.E. T1’s with their efficiency improvement activities
- Provide relevant training to the local M.E. T1 teams & LO teams
- Assist the M.E. T1 with their GSD rollout & calibration of production environment to ensure accuracy of standard efficiency is within tolerance
- Manage the GSD audit process in line with the GASA expectation & milestone evaluation
- Responsible for driving improvements in Quality, Cost and Delivery across the business via the application of I.E. best practices and Lean Manufacturing activities
- Manage regular reporting & communication packages to M.E. Managers & Local Sourcing Teams
- Actively participate in all M.E. Manager visits, term reviews & forums
- Use industrial engineering techniques to develop positive change to current and existing processes throughout the T1 & T2 supply base
- Interact with internal and external stakeholders to determine best production methods
- Identify & evaluate problems and develop improvements to production, BOM utilisation, distribution, and standard work methods by using proven Industrial Engineering techniques
- Identifying, evaluating, and developing project solutions and recommendations for minimizing total operational costs
- Must be able to influence others in a multi-culture environment
- Developing & implementing direct labour standards for costing, capacity planning, and evaluating performance where required
- Recommend methods for improving operator efficiency and reducing waste of materials and utilities, such as restructuring job duties, reorganizing work flow, relocating work stations and equipment, and purchase of equipment
- Degree in Industrial Engineering or relevant qualifications within the field of Industrial Engineering
- Licensed GSD practitioner is a pre-requisite of this position
- A minimum of 4-5 years of experience within an apparel manufacturing/industrial engineering environment
- Understanding of Lean Manufacturing and/or 6 Sigma
- Excellent command of English (Reading, Writing and Speaking)
- Acceptance of frequent business travel
10
Manager Manufacturing Engineer Future Resume Examples & Samples
- Monitor and improve systems for ensuring quality materials and components in machine processes while enhancing productivity
- Maintain collaboration with external partners to guide and develop flexible ways of configuring new production lines
- Conduct scientific experiments to identify and implement enhancements for existing and future assembly line production systems
- Manage projects to assess quality and consistency in supporting the scale-up from prototype-level material processing lines to production-scale systems
- Support efficient production from existing assembly lines by running projects to evaluate individual process health
- Collaborate with manufacturing partners to design assembly lines to meet throughput, size, cost and sustainability criteria
- Evaluate production management tools with practical application and implementation in mind
- Educate and train colleagues by sharing knowledge on an on-going basis
- Prepare concept and results-based reports and presentations, communicating to technical and non-technical audiences
- Identify and partner with industry-leading organizations to extend the capability of the team
- Consider legal implications of innovative concepts, working with the legal team to protect product, technology, innovation, process, and design
- Fluent English (required), German (advantageous)
- Communicate and negotiate effectively
- Cooperate well, develop and maintain relationships
- Work independently as well as part of a team
- Plan working time efficiently, balancing short term tasks with long term goals
- Strong analytical skills, solution driven and result oriented
- Ability to travel domestically and internationally
11
Manager Manufacturing Resume Examples & Samples
- Provide exemplary leadership in a fast pace environment subject to constant change while dealing with information and resource constraints
- Drive manufacturing team to achieve established targets for Safety, Quality, and Productivity by using Lean Manufacturing Tools and 6 Step Problem Solving
- Hire, coach, lead and develop approximately 500 - 600 hourly production team members and 10 to 14 direct reports (Associate Managers / Production Supervisors). Conduct team member training
- Help with implementation of and continued adherence to Lean manufacturing and 5S initiatives
- Partner and Coordinate with Engineering, Materials, Maintenance, and other internal departments to resolve issues and concerns
- Provide program management to short term and long term projects across all areas of the department
- Support and collaborate with Sales, Marketing, Finance, Engineering, Test and Quality departments. · Lead by example of positive reinforcement and make Tesla a World Class Manufacturing Automotive company
12
IT Manager, Manufacturing Execution Resume Examples & Samples
- Project management including resources, budget, scope, timelines
- Liaison with the Central Operations Organization and BU leads on prioritization of Manufacturing Execution initiatives
- Provide status updates on key initiatives and IT involvement
- Lead and develop a team to help support project and critical issues in the production environment
- Provide Strategic Direction for the UTAS IT Manufacturing group
- Participate in Process improvement initiatives across the business
- Working knowledge of Solumina and other Manufacturing Execution Systems
- Location could be based in any of the following: Windsor Locks, CT; Rockford, IL; or Troy, OH
13
Product Manager, Manufacturing Resume Examples & Samples
- 1) Autodesk Vault
- 2) Autodesk Product Design Tool
- 3) Engineering release and change management processes
- 4) Software product sales, services and support
- 5) Leading product development to a product launch
- 6) Manufacturing industry and industry segments experience
- 7) Supplier management
- 8) Manufacturing techniques
- 9) Technical Presentations to large groups
- 10) Technical Documentation
14
Pl-finance Manager, Manufacturing Resume Examples & Samples
- This role provides to Corporate and local management financial support, reporting, planning and analytical interpretation based on sound financial judgment and expertise. This position is responsible for developing raw product standards, analyzing variances for raw material and managing the potato raw product management (RPM) system. This position will provide support to the Ontario finance group and the potato procurement group
- Under the leadership of the Ontario Plant Controller this position is a financial representative and is responsible for maintaining the integrity of all financial policies, maintaining internal controls, establishing operating budgets, and accurately forecasting and reporting financial performance for that unit
- The position is responsible for the financial performance of potato procurement; therefore he/she must drive accountability and search for ways to bridge any gaps
- Support delivery of financial target for potato procurement by analyzing costs to drive reductions and creating action plans to close gaps
- Develop annual budget (AOP), ensuring accurate costs by department/cost component
- Ensure completion of month end close requirements (journal entries, BPCS, SAP) and monthly reporting of results including analysis of the drivers of results
- Be an active member and contributor to the procurement agriculture department and leadership team, including training and feedback to users of financial information and support of frontline leaders
- Establish and maintain internal controls consistent with corporate requirements and good business practice
- Provide leadership for financial integrity, strong controls and transactional activities, including RPM and SAP daily/weekly/monthly responsibilities
- Show support for all department and plant initiatives, including quality and safety. Volunteer to lead or co-lead initiatives
- Bachelor’s Degree Accounting/Finance or similar degree
- Minimum 3 years Financial Analysis/Cost Accounting experience with emphasis in manufacturing preferred
- Strategic Thinking Skills
- Technical Learning Ability
- Solid understanding of General Accounting and Cost Accounting principles
- High level of integrity and ability to maintain strong controls environment
- Strong analytical and problem solving skills, ability to work with information
- Strong ERP and financial system background preferred
- Proficient with software such as Excel, Word, and PowerPoint, including the ability to create, modify and ensure accuracy of complex spreadsheets
- Excellent organization and time management skills
- Quality Orientation – Attention to detail
- Adaptability – Maintaining effectiveness in the face of changing priorities and tasks, ability to manage multiple assignments
- Teamwork/Collaboration – Working effectively with those outside the formal line of authority to accomplish organizational goals
15
Manager, Manufacturing Excellence Apparel Resume Examples & Samples
- Deliver a standard platform for SMV based capacity planning and costing by developing & promoting GSD across the supply chain
- Provide leadership & support to T1 Industrial Engineers & LO PCEs
- Present and sell recommendations to relevant parties including all levels of management
- Use proven engineering techniques to initiate and drive change to current and existing processes
- Assist the Sourcing leadership when needed to provide advice on Industrial Engineering related topics
- Competency with Excel, Word, Access and MS Project is required
16
Manager Manufacturing Services Resume Examples & Samples
- Maintain protection of the environment and the health and safety of our employees, customers, and the communities in which we operate and/or transport our products, as our highest priority
- Provide overall direction and leadership for the Process Safety Management (PSM) function. Ensure that Process Safety regulations as described by OSHA, EPA and OxyChem are communicated and carried out by personnel at all facilities within Houston Operations. Ensure adequate resources are available, including outside experts when needed, to carry out necessary programs and program evaluations
- Provide overall direction for the Mechanical Integrity of fixed equipment and piping for the Houston Operations plants. Ensure adequate and qualified staff of Engineering resources and Equipment Inspectors is maintained
- Provide overall management for the Stores/Warehouse function within Houston Operations. Ensure Stores inventory is received, tracked, and issued according to OxyChem policy and generally accepted accounting practices. Provide systems that control warehouse access, monitor security, and track items removed from Stores inventory
- Provide overall direction for the Contract Services function in Houston. The Contract Serves department provides the functional interface for the Houston Operations resident contractors regarding labor invoices and PeopleSoft approval. This group also performs contactor safety audits, and provides direction to the janitorial and grounds-keeping services for the Houston Operations plants
- Provide overall direction for the Manufacturing Service Engineers with specialized experience in rotating equipment, electrical engineering, and instrument-system engineering
- Provide overall direction for the Houston Operations underground pipeline program. Direct inspection, testing, and record keeping activities. Ensure coordination of DOT Pipeline issues with OxyChem Corporate Office
- Serve as the liaison between Houston Operations and the primary Maintenance Contractor for the Houston Plants. Coordinate quarterly (local) Management reviews to ensure common goals are being achieved
- Serve as the Responsible Care Coordinator for the Houston Operations plants
- Serve as the MOC Coordinator for Houston Operations wide MOCs
- Review all Corporate Engineering AFEs totaling more than $300 K for quality and consistency
- As an Oxy Level 3 trained Investigator, provide leadership to the Incident Investigation processes in Houston
- Ensure relevant data is provided for the Maintenance Excellence and Critical Success Factors teams
- Ensure that Process Safety and Risk Management principles are incorporated into the foundation of department operations. Ensure annual departmental goals and objectives include meaningful Process Safety activities for all levels of the organization
- Reviews and approves all changes to Manufacturing Services headcount and annual budgets. Serves as liaison to OxyChem Corporate Engineering. Reviews and approves all changes to the PSM/RMP programs for Houston Operations
- Bachelor’s Degree. Mechanical Engineering preferred with 10+ years of experience
- PSM/Mechanical Integrity
- Excellent interpersonal and communication (verbal and written) skills
- High proficiency in Microsoft applications (such as Word, Excel, PowerPoint and Outlook)
- Ability to read, write and speak in English
- Excellent interpersonal skills including the ability to work as part of a team
- Physical requirements – Must be able to lift 40 lbs., climb ladders and stairs. Walking, bending, stooping is required. Must be able to wear personal protective equipment including the use of a respirator. Must be able to respond to visual and audible alarms
- Maintenance/Outage experience
- Experience as a Maintenance Mgr/Supervisor
17
Campaign Manager, Manufacturing Isvs Resume Examples & Samples
- Defining the strategy to integrate Manufacturing ISVs across Microsoft field sales motions, corporate and field marketing engines, and strategic initiatives
- Successfully executing strategic campaigns to drive adoption of Manufacturing ISV solutions worldwide
- Identifying net-new opportunities to integrate Manufacturing ISVs within co-sell and co-marketing motions, and piloting new campaigns and approaches for driving ISV GTM
- Delivering resources to sales and DX teams to better identify top Manufacturing partner solutions and engage them in new and existing opportunities
- Collaborating with marketing, sales and DX teams to ensure Manufacturing ISV partner solutions are integrated in local area industry activities as well as global campaigns, events, and sales engines
- Evangelizing our Manufacturing ISV partner success on Microsoft platforms across internal and external channels, and through global campaigns, events, and sales engines
- Demonstrating thought-leadership and problem solving skills to tackle solutions based on sound hypotheses coupled with analytical reasoning and assessment
- Delivering ongoing industry, trend identification, and competitive insights to the organization
- Minimum of 7 years of experience in marketing or sales with a proven record of influencing and defining partner and programs to grow new businesses
- Industry Expertise: Experience working with customers and partners in Manufacturing (Discrete Manufacturing, Process Manufacturing, Power & Utilities, Oil/Gas/Mining)
- Technical Skills: Experience in Cloud computing and Mobile, with an understanding of industry technologies, business drivers, and emerging trends. Deep knowledge and passion for driving adoption of Microsoft Mobile and Cloud technologies
- Professional Skills: Executive presence and a proven record of building trusted relationships with and influencing senior executives. Exceptional leadership and community building skills. Cross-group collaboration skills with exceptional verbal and written communication. Highly motivated, results-driven with exceptional decision-making and follow through. Strong organization / prioritization and analytical skills are essential
- Qualifications: Bachelor’s degree in Business or Engineering or equivalent discipline required. MBA preferred
18
Manager, Manufacturing Resume Examples & Samples
- Utilizing knowledge of product technology, production methods, procedures and equipment capabilities
- Plans and directs manufacturing operations for most efficient manufacturing of products
- Evaluate and establish material, equipment, and manpower requirements to support the manufacturing of product
- Establish and satisfy manufacturing priorities while effectively maintaining operation and cost factors, customer demands and profitability
- Develops and implements methods and procedures designed to improve product quality and efficiencies and elimination of operating problems
- Reviews and analyzes data, reports and outputs to determine causes of non-conformity and implements corrective action
- Responsible for the assignment and supervision of work to ensure the most efficient completion of work assignments
- Develops plans and programs to meet demands and ensures deadlines are met
- Develops and establishes department standards and practices
- Develops department budget and maintains department expenses
- Develops, establishes and monitors training standards and practices for the most effective performance of work
- Coordinates production requirements with Quality, Supply Chain and other departments to ensure on time production of products
- Additional duties as needed
- Proven record of success as a "hands on" manager with at least 5-7 years of related experience
- Production/manufacturing management in low-medium volume / high mix (Engineered) product environment preferably in the aerospace industries
- Proven ability to successfully handle multiple projects and meet critical deadlines
- Must be a team player with excellent interpersonal skills and a commitment to relationship-building, both internally and externally
- Strong leadership, project management and organizational skills
- From an operations perspective, exposure to best practices, e.g. lean manufacturing, continuous improvement, JIT etc. is necessary in achieving operational excellence
- Strong customer relations skills
- Knowledge of Excel, Word, PowerPoint, Project, Oracle or other related business software
- Ability to read, speak and write in English
- Ability to read and interpret documents such as Parts Manuals, safety rules, operating and maintenance instructions, and procedure manuals
19
Manager, Manufacturing & Production Planning Resume Examples & Samples
- 30% - Provides direction to subordinate supervisors/assemblers based on general policies and management guidelines
- 20% - Plans and coordinates integrated schedules for personnel, material and facilities utilization
- 15% - Provides assistance to subordinates in meeting schedules
- 15% - Responsible for assigned department budgets
- 10% - Interprets and executes policies that typically affect subordinate organizational groups
- 10% - Coordinate work programs for shift operations
20
Manager, Manufacturing Resume Examples & Samples
- Lead MFG activities including upstream and downstream for mAbs and antibody-drug-conjugate production
- Serve as primary interface with outside groups including but not limited to: QA, QCA, QCM, Supply Chain, and Facilities
- Ensure the timely generation of batch production records from Technical Reports
- Management of GMP suite for both mAb and ADC production activities including: scheduling of engineering, tox, and clinical material production activities, timeline management, GMP suite readiness
- Draft/review deviation reports, CAPAs, raw material specs, etc
- Proactive, frequent and timely communication with other PSM leads regarding issues related to Large-Scale activities, effects on timelines, and areas for improvement
- Determines resources needed to execute assigned projects
- Summarize and present data in departmental/project meetings and generation of campaign summary reports
- Ensure proper training and compliance of personnel working in controlled areas
- Comply with good housekeeping and company safety practices
- BA/BS with 7+ years of GMP production experience in biotechnology/biopharmaceutical industry with 3+ year(s) in a supervisor role
- Extensive knowledge of cGMP compliance
- Demonstrated experience in technical transfer and batch record preparation
- Ability to work closely and flexibly with process development
- Excellent inter-group collaboration/communication skills
- Ability to multi-task with attention to details and work effectively in a fast-paced environment
- Good problem-solving, communication, organization, and collaborative skills are essential
21
Manager, Manufacturing Resume Examples & Samples
- Build a team, provide necessary training and ongoing coaching, discipline and recognition of direct staff, including performing annual performance reviews
- Ensure performance of all process steps specific to the phase or stage of operation (e.g. upstream, downstream, support)
- Process monitoring, including manipulation of databases, documents and/or spreadsheets to support business reporting requirements
- Complete the final review of completed manufacturing documentation per compliance standards and established timelines
- Investigate and resolve problems, identifying root cause, and proposing process improvements through clear communication to senior management
- Interact with outside vendors and senior management
22
Manager, Manufacturing Maintenance Resume Examples & Samples
- Lead, Manage, Administer and Monitor the Maintenance Supervisors to assure efficient and compliant operation and maintenance of all manufacturing equipment operated by the department
- Oversee and Manage B5 Fractionation equipment failure investigations to ensure timely resolution of any issues thus assuring a continuous state of compliance with all applicable standards, methods, procedures, licenses and regulations
- Identify, Lead, Influence, Drive and Support improvements that result in stable, reliable, and efficient operations
- Search, Study, Identify and Understand all cost drivers for the B5 maintenance operation in order to reduce cost of operation year over year
- Oversee and Manage B5 Fractionation Engineering Projects that enhance reliability for all B5 Fractionation manufacturing equipment according to project demand
- Track, Monitor, Assess and Report operating and performance data that give insight and indication of the stability and robustness of B5 Fractionation and Pharma manufacturing equipment on an ongoing and forward-looking basis
- Complete, Administer and Manage all documentation to support change control and design work
- Facilitate and verify appropriate training for all employees on the shift (including but not limited to cGMPs, job skills, safety, etc.). Coordinate training as needed
- Coordinate, oversee and manage contractors as needed to meet the responsibilities of the department
- Maintain equipment in sound condition, report deficiencies and record in JDE
- Must be well versed in engineering disciplines (e.g. fluid flow, thermodynamics, heat transfer, static and dynamics, engineering materials). Must possess knowledge of related disciplines
- Must be able to work and facilitate a team-oriented environment
- Must have demonstrated ability to manage multiple priorities in a manufacturing setting and prioritize responsibilities of self and direct reports appropriately
- Must be well versed in purchasing practices and cost management
- Proficient with Computer Maintenance Management Systems
- May be required to supervise multiple groups
- BS degree in an engineering discipline
- 5-8 years of relevant technical experience
- Minimum 5 years relevant experience in managing facilities/maintenance employees and activities
- FDA/cGMP experience preferred
23
Manager, Manufacturing Resume Examples & Samples
- Develop the manufacturing department for continuously improving the high standards of manufacturing operations to ensure safety of personnel and processes; quality standards as they relate to customer complaints, internal rejects, audits, etc; customer service levels meet and/or exceed expectations; improving the profitability of the operation through management of efficiencies, material costs, CIPs, scrap and rework reduction
- Responsible for all production at the Moncks Corner facility
- Plan, prepare and recommend an annual manufacturing operating budget. Implement a monitoring system to analyze plant performance against that budget
- Coordinate the efforts of the staff functions within the manufacturing department
- Investigate, prepare, implement and integrate long range facility plans based on the forecasted needs of the business as well as recognize the need and implement techniques and devices for periodic updating of business controls and in process planning
- Determine and specify processes, methods, tools, equipment and controls for manufacture of products and components consistent with obtaining and maintaining optimum costs, quality, losses, cycles, inventories and investment in facilities
- Responsible for the proper implementation of our Company policies
- Provide training, development, and supervision of all production supervision personnel
- Support the installation/validation of manufacturing equipment
- Cooperate and participate in the product design activity to assure optimum design and costs
- Provide leadership and direction to assure daily production plans support overall supply chain objectives
- B.S. degree in a technical field
- Seven or more years of progressive manufacturing experience, five of which must be in a supervisory/management in an FDA regulated environment
- Established proficiency in leadership, communication, and project management skills
- Must have excellent verbal, written, and interpersonal skills
- Strong working knowledge of manufacturing methods, techniques, and related
24
Manager Manufacturing Eng Resume Examples & Samples
- Guide and coordinate Advanced Manufacturing activities within development and operational projects
- Ensure
- Process development and assembly sequencing (process flow chart) for new programs
- Plant and process layout for new products and plant launches
- Process specifications and recommendations regarding ergonomic improvements
- Specifications for manufacturing equipment and recommendations for equipment procurement
- Provide cost analysis of product and process alternatives
- Stimulate continuous improvement process in plants (KAIZEN, DO IT) with the objective of MEQ
- Work with SD-Teams to complete product launches
- Monitor assembly equipment through production start up
- Stimulate TPM in new projects
- Monitor and audit adaptation of manufacturing best practices and standards in the plant
- Cooperate with Center of Excellence for further development of Advanced Manufacturing tools and processes
- Ensure, support and develop manufacturing capacities in plants
- B.S. Degree in Engineering (Mechanical or Industrial)
- 6-8 years minimum experience in a Manufacturing Engineering or Industrial Engineering Capacity
- High volume automotive manufacturing engineer-in work experience
- Project management experiences in international environment
- Budgeting and cost control
- English - advanced level
25
Sales Manager, Manufacturing Resume Examples & Samples
- Lead a team of direct sales representatives to achieve quarterly and annual revenue and growth targets by establishing sales goals and monitoring the achievement of those goals; take necessary action to ensure sales targets are achieved
- Motivate, coach, and mentor your team to both grow existing accounts and capture new business throughout the region by developing effective sales strategies to ensure 100% achievement
- Design strategic sales plans through competitive analysis, customer segmentation, and thoughtful product positioning
- Provide disciplined, ethical, and focused leadership to the sales organization that will foster success based on a culture of respect for customers, employees, and Red Hat values
- Establish and evangelize a sales qualification and pipeline management process through the development and maintenance of executive and senior-level client relationships at key accounts
- Play a hands-on role with the field sales organization by maintaining a personal presence and being highly visible through direct customer engagements in the field
- Directly participate in closing deals at key accounts and supporting business initiatives for future success within the region
- Extensive experience with leadership within a technology (software highly preferred) sales organization, demonstrating success in achieving sales targets in both direct and channel routes-to-market
- Outstanding track record of delivering annual sales targets
- Proven experience developing sales organizations that consistently deliver 25% year-over-year increases in revenue
- Comprehensive knowledge of proven sales processes and solution-selling strategies
- Thorough understanding of the enterprise operating system and middleware marketplace; an understanding of a subscription model
- Excellent planning, financial, presentation, and analytical skills
- Proven ability to apply these skills and business acumen to complex situations with competing priorities
- Excellent customer focus with an ability to partner with senior business leaders to understand their needs and deliver solutions
- Fluency in Gernan and English
26
Manager, Manufacturing Resume Examples & Samples
- Working knowledge with disposable systems, filtration, CIP & SIP
- Knowledge and experience in all aspects of GMP manufacturing
- Ability to troubleshoot, identify issues and support resolutions with technical groups
- Ensure consistent product quality through implementation of effective systems and collaboration with key support groups (QA, MSG, Eng, Fac, etc.)
- Experience with process development, process transfer, validation and multi-product operations
- May have in excess of 4 direct reports overseeing a group of 50+ to manage
27
Manager, Manufacturing Resume Examples & Samples
- The Manufacturing Manager is responsible for an assigned area within a plant (Upstream, Downstream or Process Services). Collaborates with support groups to ensure accurate and well managed transfer of process changes/improvements to floor operations. Integrates best practices, where appropriate, into manufacturing. Oversees the planning, implementation and execution of manufacturing operations for new and/or existing products and technologies in a cGMP environment. Develop, implement and update all manufacturing SOPs, Batch Records and other documentation needed for cGMP compliance
- Assist with departmental contributions to regulatory submissions (INDs, BLAs); serve as primary technical reviewer for all contributions from the group
- Contribute to new facility design and existing facilities modifications, as necessary, as part of the manufacturing team
- Experience with Gene Therapy products a plus
- Experience with Fill Finish a Plus
- Experience with startup of new facility or processes
28
Manager, Manufacturing Resume Examples & Samples
- *Please note: This position will be on 2nd or 3rd shift***
- Manages, plans, and directly develops employees. Assists in the creation of efficient processes through hands-on development and training. Tracks departmental progress through analysis of recorded data and information of additional test-points. Correlates results with requirements/specifications
- Provides leadership through communication and knowledge transfer. Provides visionary leadership
- Defines department outcomes and goals, while establishing a productive and motivational working climate
- Oversees the communication/documentation of test methods, protocols, reports, and conclusions. Oversees the formulation of manufacturing methods that are well-developed, organized, and repeatable
- Leads the development of control experiments leading to process improvements that improve the overall quality of the product
- Directs, supervises, and coordinates the Manufacturing activities of assigned work centers through subordinate supervisors and technicians to achieve timely production of quality products at minimum cost
- Plans, organizes, and implements Manufacturing procedures in accordance with schedules, manpower skills and capabilities, as well as works toward accomplishing these objectives within established costs on estimates and budget allocations
- Develops budgetary requirements
- Develops and distributes reports which clearly define and show operational metrics, i..e. direct labor hours and cost, defective parts per month
- Participates in and implements staffing, job evaluation, employee training/relations, disciplinary actions, safety, etc
- Acts as liaison between all other areas of support management and direct laborers to maintain proper levels of communication
- Analyzes work requirements and outlines the schedules and methods to be followed or efficiency and safety
- Teaches Honda Philosophy within all areas through actions and leadership values
- *Honda Aircraft Company is an Equal Opportunity Employer***
- Bachelor’s degree in Business, Engineering, Operations or other related technical field of study required
- 12+ years of directly related work experience within the manufacturing aerospace industry
- Experience in Aircraft Completions including Paint, Interior, and Flight Line highly preferred
- A&P and/or related licensure strongly preferred
- Good knowledge in continuous improvement practices and a proven record of success in implementation
- Strong understanding of manufacturing, production planning, engineering, and finance
- Excellent understanding of routers and planning related items
- Excellent communication skills - both orally and written
- Strong Project management skills
- High competency in Six Sigma and Lean tools
- Familiarity with SAP and Teamcenter operations systems preferred
- Proficiency in Microsoft Office Suites (Word, Excel, PowerPoint, Project) and Lotus Notes
- Ability to work with cross functional areas
29
Manager, Manufacturing Resume Examples & Samples
- Maintain strong partnership with R&D to ensure breeding campaigns are aligned with clinical manufacturing schedules
- Manage and develop technician level staff
- Effectively manage operations in accordance to written procedures, guidelines and defined good practices. Coordinate all needed actions with GA Facility Supervisors, Managers and Directors
- As appropriate, coordinate and lead deviation, change control and process improvements for area of responsibility, identify root causes and implement appropriate corrective and preventive actions to prevent repeated occurrences
- Serve as subject matter expert during regulatory inspections, and collaborate with management to address any follow-up responses or corrective actions
- Ensure effective interactions with other departments and customer representatives as appropriate to support site metrics
- Effectively recruit and develop staff in accordance with company policies in support of effective succession planning
- Develop and manage portions of the departmental budget and spending in support of department objectives for cost control while maintaining effectiveness
- Continuously promoting collaborative mode of work within own facilities and across Manufacturing facilities and functions
- Report immediately any concerns with biosecurity, employees and housed PPU populations to Management
- Supporting Management and functional leaders with planning production of PPU populations, production outcomes and troubleshooting actions
- Ensuring collection of required data and submissions to defined databases
- Communicating effectively to Management about daily and/or operational plans and actions affecting short- and long-term production at each manufacturing facility
- Working knowledge of biopharmaceutical manufacturing operated under written procedures and cGMP and ability to maintain requirements for compliance with procedures at all times
- Must be able to provide hands-on leadership, coaching, and coordination, if needed. actions with a focus on achieving production goals
- Must have strong written, verbal, and presentation skills with a demonstrated ability to work effectively in a fast-paced team environment
- Must be able to communicate clearly, effectively, and concisely with subordinates, peers and management
- Proven success in collaborating effectively and efficiently on cross functional work teams
- Demonstrated ability to lead a team of manufacturing staff through successful CVM FDA inspections by internal auditors and external agencies, while ensuring a high degree of compliance
- Ability to inspire, organize and lead continuous improvement efforts within manufacturing operations and participate in site-wide continuous improvement efforts
- Demonstrated ability to organize and lead manufacturing operations and develop teams by provide opportunities for staff development and career growth
- Demonstrated ability to promote a positive work environment by effectively administering company policies and procedures, maintaining a satisfactory safety record and monitoring performance
30
Manager, Manufacturing Resume Examples & Samples
- Development and training of employees
- Planning and Scheduling GMP manufacturing operations
- Generate and implement manufacturing SOPs, BPRs, forms
- Coordinate manufacturing activities with supporting departments
- Manage department performance and personnel development
- Utilize Lean Manufacturing principles to improve operating systems
- Review the executed Batch History Records
- Identify and reduce areas of risk in existing processes
- Resolve deviations due to process constraints and/or technical challenges
- Comply with all safety policies, practices and procedures
- Assist in the transfer of technology from Process Development to GMP Manufacturing
- Provide leadership to others through example and sharing of knowledge/skills
31
Manager, Manufacturing Process Services Resume Examples & Samples
- Working knowledge of Lab Washers, Autoclaves, and Inventory/Space management with familiarity with Enterprise Resource Planning tools
- Experience in managing external contractors with oversight over GMP Facility Cleanings and gowning management
- Support the closure of manufacturing discrepancies and change requests
- Ensure consistent product quality through implementation of effective systems and collaboration with key support groups (QA, Materials Management, Supply Chain, FAC, etc.)
- Broad technical knowledge in area of responsibility and ability to provide technical instruction on new/improved processes to appropriate audiences, primarily Manufacturing personnel
- Experience with Lean Six Sigma tools and Project Management skills are a plus
- 8+ years of directly related industry experience, including at least 4+ years with proven leadership role
- May have in excess of 4 direct reports overseeing a group of 10+ to manage
32
Manager, Manufacturing Resume Examples & Samples
- Implementation of Manufacturing Work Flow Planning when deploying “how to” instructions to production, aiming to perfect production line balance and the application of Industrial Engineering techniques
- Leading key manufacturing related projects
- Develop a team focused in “learning and apply” world class manufacturing tooling and concepts
- Integrating Manufacturing Requirements and Objectives, using an efficient First Article Inspection process to ensure all design change implementation in production will meet the manufacturing requirements
- Integration with the Change Management organization, provide adequate project schedule, allocation of resources and definition of tooling / processes to allow for a strong change implementation process in the manufacturing environment in line with rate changes
- Leading and Managing the work of the reporting organization
- Accountable for the quality of the work in his/her organization
- Accountable for the development of his / her Department Budget and Cost Management
- Engage the team in Lean Manufacturing Principles learning and applications
- Establishes, manages and monitors Continuous Improvement strategies that support the organizational objectives and Site Operating plan
- Support the employees to reach their business and professional development goals
- You have an Engineering or other degree relevant to Aerospace Manufacturing
- You have at least 8 Years in Aerospace Manufacturing Experience or similar
- You have at least 3 Years Supervisory or Management Experience
- You have demonstrated knowledge and experience with Major Production Programs in Methods, Industrial Engineering, Assembly and/or related activities in a manufacturing environment
- You have demonstrated good leadership, communication and interpersonal skills in past roles
- Must be results oriented and strive for continuous improvement
- You are recognized for your leadership, communication and coaching skills; and for your ability to mobilize and engage a team
- You must be pro-active, results-oriented and strive for continuous improvement
- You have good analytical and strategic planning/thinking skills and execution skills
- You have knowledge or familiar with Bombardier manufacturing process is an asset
- You have the ability to travel when needed
33
Manager, Manufacturing Specialists Resume Examples & Samples
- Review deviation investigations and provide coaching and mentoring to Specialists authoring deviations
- As needed, lead the authoring of manufacturing investigations, CAPA, and change control activities
- Prioritize and distribute workload across the team to ensure timely execution of deliverables
- Lead investigation discussions during regulatory inspections as required
- Own the deviation management process to ensure timely and effective closure of deviations
- Actively participate in and provide data as required for daily work center team meetings as part of the Integrated Management System
- Attract, develop, and retain top talent to create a High Performing Organization. Build and sustain a culture of inclusiveness and accountability and an environment in which individuals and teams can grow
- Support site management operating reviews via both written documents and oral presentations as required
- Must be able to use electronic systems such as SAP and Trackwise
- Must have the capacity to develop in-depth knowledge of manufacturing operations and various quality systems
- Must possess exceptional verbal and written communication skills
34
Manager, Manufacturing Resume Examples & Samples
- Engages all area members in formal and informal meetings to ensure thorough communication of business strategy and department/area goals and objectives
- Identifies training needs and ensures timely, up-to-date training as required
- Ensures ongoing performance dialogue between Team Leaders and unit members
- Establishes clear performance measures
- Bachelor’s Degree in engineering / scientific discipline, or the equivalent
- Minimum of 5 years sterile pharmaceuticals production experience, to include 3 years related supervisory experience. Demonstrated ability to motivate exempt and non-exempt employees and demonstrated management skills, (i.e., business knowledge, leadership, communication, ability to analyze technical issues, conflict resolution). Thorough knowledge of cGMPs
35
Manager Manufacturing Project Leads Resume Examples & Samples
- Provide support to manufacturing for both upstream and downstream process. Included but not limited to bioreactors, centrifugation, depth filtration, column chromatography, and Ultrafiltration/Diafiltration
- Manage team of project leads responsible for having the technical knowledge and ability to integrate their work with that of other functions and with strategic objectives
- Team will be responsible for change initiatives, investigation support, CAPA ownership and closure, and change control ownership
- Perform Supervisor functions in Trackwise and provide leadership and guidance to team
- Ensure coverage at investigation governance meetings and huddle as needed
- Able to use creative problem solving
- Provides technical expertise to management and less experienced professionals
- Support deviation and CAPA closure, and ensure SOP updates required are completed in a timely manner. Interface with MFG and Quality as needed
- Attend investigation governance meetings as needed
- Ensure team of project leads works collaboratively with Manufacturing, Manufacturing Engineering, Validation, Quality, Automation and MS&T to ensure change initiatives are driven to closure, and migrated to the production area in a timely manner
- Ensure changes are delivered with proper training to the floor (all shifts as needed)
- Oversee and own product changeover program for large scale manufacturing facility
- Actively participate in reviewing and discussing wider facility programs and strategies such as alarm management, gowning, and environmental controls
- Frequently interacts with area management, outside customers and functional peer groups across various departments. Interaction normally requires the ability to gain cooperation of others, conducting presentations of technical information concerning specific projects/schedules, etc
- Acts as operational expert to support troubleshooting of complex issue/problems, and ensures training of team
- Act as SME in procurement of equipment/instruments for the functional area
- Work in collaboration with Engineering , Mfg Technology and/or Technical Services to review/approve specifications and provide user requirements
- Drives investigation reduction strategies for manufacturing controllable deviations for MFG operations in partnership with upstream and downstream teams
- Provide support for facilitation of Kaizen, Lean, and greenbelt initiatives as needed
- Provide Audit support as needed, as a technical SME of the process, facility, and operational recipes
- Provide support as needed for technical transfer of new or modified processes into the Large Scale Cell Culture facility. Work cross functionally with MS&T, Manufacturing, Automation and Validation on development of recipes and Delta V functionality needed to support new/modified process
- Attend governance meetings for Site Quality Council, and Local Change Review Board as backup for Associate Director
- Work closely with site for Operational Excellence initiatives including yellow belt projects
- The successful candidate will have a BS in Engineering, Science or equivalent with 8 years plus experience (or equivalent) with manufacturing support in the Biotechnology manufacturing industry. Minimum of 4 years experience managing people highly desired
- Strong project management skills needed, and greenbelt/lean certification is desired
- Ability to work extended hours or a modified work schedule as required for coverage of 24/7 manufacturing operation
- The position is Monday through Friday, first shift, but requires on-call availability
- 1604501
36
Finance Manager Manufacturing Resume Examples & Samples
- Lead the development of the Annual Operating Plan, including product cost standards updates, VL&E and ZBB budgeting, bridging cost changes and preparing all applicable AOP schedules
- Analyze budget variances of indirect and fixed expenses. Provide detailed report of budget variances and breakdown of site-wide/department KPI measures to the management team on a monthly basis. Monitor ZBB compliance and provide guidance and insight to entity package owners
- Identify and initiate process improvements in the financial planning and reporting systems
- Support the unit financial analysts in identifying and quantifying savings surfaced by Continuous Improvement and Production teams, ensuring the values in 4 Site are current and represent the factory’s best thinking
- Lead and help complete month-end close process
- Perform various financial analysis/scenario studies
- Ensure completion of month end close requirements (journal entries, SAP, FAC Review) and monthly reporting of results including analysis of the drivers of results
- Provide oversight and auditing of operational BOM accuracy throughout the year
- Be an active member and contributor to plant manager and leadership team, including training and feedback to users of financial information and support of frontline leaders
- Establish and maintain internal controls consistent with corporate requirements and good business practice. Ensure inventory controls are working effectively
- Provide leadership for financial integrity, strong controls and transactional activities, including SAP daily/weekly/monthly responsibilities
37
Manager Manufacturing Quality Resume Examples & Samples
- Leads Oakley’s in-house Manufacturing Quality Program related to eyewear finished goods and related pre-assembly operations such as lens molding, lens cutting, lens tinting, eyewear frame painting/graphic, Frame injection molding and related quality engineering functions
- Manages approximately 10 direct reports (Quality Engineers and Supervisors) and 50 indirect reports (QA Leads, Technicians & Product Inspectors)
- Drives analysis related to Oakley's Internal Quality Cost of Quality & Topics of Extra Consumption (Scrap) & alignment for improvement projects
- Leads efforts & focus on product quality problems and gives direction to systematically drive improvements for those problems (Related to LQS (outgoing Quality), and Quality Service Levels)
- Drives improvement projects based on Market data and After Sales input
- Organizes and works a wide range of technical issues and understands product performance requirements and the efforts to manage the Quality Team in meeting expectations
- Works globally with other Luxottica Facilities producing Oakley products and aligns the brand expectations for quality and acts as a resource from Oakley Headquarters to assist those facilities as needed
- Builds strong collaboration and partnership with each Business Unit; Engineering, R&D, Manufacturing and other End to End supply chain functions
- Performs Annual Budgeting to align with Annual Operating Plan and/or 3 to 5 year manufacturing forecast
- Attracts, retains and mentors the highest caliber quality engineering personnel
- Works safety and maintains a safe, organized and clean working environment by complying with procedures, rules, and regulations
- Performs other duties and responsibilities as needed
- 8+ years of experience in Quality with specific leadership Quality Engineers/Managers (may also have graduate level education or degree)
- Working Knowledge of Quality Systems, quality process controls, material performance testing and has a solid understanding of Advanced Product Quality Planning
- Ability to lead Quality Engineers in a strong way & drive the quality culture in a fast paced manufacturing environment
- Ability to support the Quality Director in overall activity and setting stretch goals with the team (become a second in command for quality in the optics manufacturing business)
- CQE/CQM/Six Sigma Black Belt
- Background in TQM & Six Sigma or other key experience that enhances the Quality Team
- Solid background in Lean Manufacturing and Related Improvement Project Management
- Has a special focus in area of manufacturing/materials science/optics/etc
- Solid Understanding of manufacturing accounting and related cost of Quality
38
Manager, Manufacturing Resume Examples & Samples
- Manages conversion process improvements of a limited scope, utilizing PPI, 5S, Lean, and Six Sigma methodologies
- Creates work center performance goals and leads each work center and each individual towards achieving those goals using employee participation. Manages individual performance to ensure achievement of goals
- Provides continuous coaching to all employees for the purpose of improving their job skills and professional behaviors
- Acts as subject matter expert during customer and regulatory agency audits
- Interacts with diverse internal functional groups to solve moderately complex problems
- Minimum of 7-10 years of experience in manufacturing environment, with at least three years of management experience/direct supervision of staff
- Requires a Bachelor’s degree in a scientific of engineering discipline or an Associate's degree and equivalent experience
- Strong leadership abilities with capability to leverage diverse resources, respond quickly, understand impact of changes and decisions, facilitate agreement, build collaborative relationships and understand customer’s needs
- Practical application experience of Six Sigma and Lean Manufacturing or other process improvement methodologies
39
Manager, Manufacturing Engineer Resume Examples & Samples
- Lead engineering team, projects and programs in area of responsibility, and ensures that necessary preliminary activities (e.g., determination of outcomes, milestones, viability studies, and resource planning, among others) are completed to allow for effectiveness and focus during later stages of projects
- Ensures that all projects and programs assigned are completed in accordance with predetermined requirements, with specific attention to product/process specifications, project/program costs, resource utilization, and timeliness for completion
- Ensures that all phases of project, program and/or process development are documented and that information required in other functional areas is reported, disseminated, or transferred, as appropriate. Ensures compliance with company policies including (but not limited to) engineering/lab notebooks, patents, Intellectual property, confidentiality, ISO, safety and others as required
- Establishes departmental budgets and spending requirements. Ensures that the utilization of all material and financial resources is carried out in an effective manner in alignment with AOP to ensure maximum productivity for the area
- Effectively assigns work to subordinate staff, providing for professional development and coaching
- Spearheads research and development of new manufacturing technologies, as appropriate, and ensures that newly created processes, designs, and/or methodologies are incorporated into Applied Materials products/services, and/or disseminated to other areas as needed
- Demonstrates in-depth understanding of concepts, theories and principles in own job family and basic knowledge of other related job families
40
Manager, Manufacturing Engineer Resume Examples & Samples
- Managing projects and programs in area of responsibility, and ensures that necessary preliminary activities (e.g., determination of outcomes, milestones, viability studies, and resource planning, among others) are completed to allow for effectiveness and focus during later stages of projects
- Ensures that the utilization of all material and financial resources is carried out in an effective manner to ensure maximum productivity for the area
- Responsible for departmental budgets and spending requirements
- Works on issues where analysis of situation or data requires review of relevant factors
- Interaction normally requires the ability to gain cooperation of others, conducting presentations of technical information concerning specific projects or schedules
41
Manager, Manufacturing Engineer Resume Examples & Samples
- Thorough understanding of business processes related to Engineering Change Management
- Sound exposure and working knowledge of 3D CAD (preferably NX), PDM (preferably Team-center) and PLM (ORACLE, SAP & CORE)
- Understanding of ASME, GD&T standards
- Computer skills - MS Office
- Exposure to Semiconductor domain
- Bachelor's Degree or Equivalent experience in any engineering discipline (preferably Mechanical / Production Engineering)
- 6 - 10 years overall experience with 2 Years of demonstrated Technical Management / Supervisory experience would be an asset
42
Manager Manufacturing Excellence Resume Examples & Samples
- Ensure Lean Manufacturing Principles are maintained at all projects and Lean Manufacturing measurements are continuously tracked
- Facilitate cross-functional events (e.g. T1 visits to other industries) to identify short term, mid term and long term efficiency improvement opportunities
- Partner with A&G Costing to establish, refine and support tracking of KPI data for Automation and other efficiency improvement initiatives relating to cost savings
- Partner with machine manufacturers and attend industry trade fairs to keep educated on industry technology development that will impact productivity. Transfer knowledge into productivity improvement efforts across A&G factories
- Support ASPECT towards future capabilities by establishing criteria / evaluations for all T1 suppliers
- Strong Lean Manufacturing/Industrial Engineering background
- Ability to network with multiple customers
- At least 5 years of work experience in sports industry preferable Hardware
43
Manager, Manufacturing Sciences Resume Examples & Samples
- Lead, train and develop the Manufacturing Sciences team. Define and establish clear objectives and expectations, provide direct feedback routinely for performance management
- Three functional areas: packaging, product development and scientists
- Be a visionary of process change and documentation of processes and workflows to achieve operational excellence - guide others toward that vision
- Contributes to new product introduction documentation, ensuring that operations concerns are addressed
- Serves as the Cell Culture Media & Sera network operations product approval committee (PAC) member for new product introductions in the PCP process
- Establish key performance indicators for projects in area of responsibility that drive change and visibility to the team and leadership. Track, trend, and monitor routinely with active data analysis rigor performed to drive the continuous improvement culture
- Identify projects and recommends appropriate course of action (e.g. discontinuation, outsource, process improvement) to maximize profitability and supply
- Have a lead role in the harmonization and technology transfer process for the Media & Sera network to drive risk mitigation, productivity and quality and service improvements
- Documents SOP’s and work instructions to capture and document processes and procedures
- Communicate with customers professionally via teleconferences, on-site visits, or customer visits around the services or products
- Ensure safety is a top priority with active measures in place to drive a safe culture
- Minimum of 5 years’ experience in a manufacturing or technical environment performing production/operations and/or project management functions
- Minimum 3 years of management experience
- Regulated environment is preferred - lifesciences related
- This position requires occasional travel to other Thermo Fisher Scientific, customer, and partner sites worldwide (approx 0 – 10%)
44
Manager, Manufacturing Resume Examples & Samples
- Bachelor’s degree in engineering, operations management, supply chain management, business, or related field. MBA preferred
- Minimum of ten years of manufacturing management experience with increasing levels of responsibility
- Demonstrated proficiency in continuous improvement tools and lean manufacturing
- Demonstrated success in leadership positions, which requires accomplishment of goals and objectives through subordinates and peers
- Strong technical knowledge
45
Dispensary Manager, Manufacturing Resume Examples & Samples
- Oversee start up activities for Media preparation group
- Minimum of 5 years leading a group with direct reporting responsibility
- Moderate to advanced knowledge of most processing equipment
- German and English fluent with good communication skills with all levels
- Experience with startup of new facility would be beneficial
46
Manager, Manufacturing, Global Resume Examples & Samples
- Maintain a robust product quality compliance program making full use of the Bombardier Quality gate process and progressive acceptance where applicable
- Work with Supervisors and production personnel to maximize workforce effectiveness & flexibility
- Establish departmental master plans and execute day-to-day actions in support of Bombardier strategic initiatives and operational objectives
- Develop departmental budgets. measuring and report on financial performance
- Establish, monitor and track operational KPIs and performance to Master Plans
- Cascade information on Department and Bombardier performance to production personnel
- Ensure compliance with all applicable regulations, policies and procedures
- You have a minimum of 15 years applicable experience in the Aerospace Manufacturing industry
- You have a minimum of 10 years practical experience in a supervisory position leading multi-disciplined teams in an aerospace environment
- You have experience manufacturing “First build” Flight Test Vehicles and working on a Start-up program in the Aerospace industry
- You possess excellent project management skills
- You possess a solid understanding of the change management process
- You are able to gain a high degree of credibility with all levels and functions within the organization and regulatory bodies utilizing excellent interpersonal and communication skills
- You have a persuasive and facilitative management style and the ability to assimilate, interpret and transfer information
47
Cdi-global Purchasing Manager Manufacturing Resume Examples & Samples
- BS/BA required; MBA preferred
- 8+ years’ experience in Purchasing, with prior management experience
- Business acumen and good knowledge of Manufacturing sector (stakes, key players, trends …)
- Leadership, dynamic and capacity to work in a multicultural environment
- Good relationship, with strong capabilities to communicate and influence decisions
- Likes challenges and negotiation
48
Operations Manager Manufacturing Resume Examples & Samples
- Minimum of six (6) years of experience with Operations Management working in an Integrated Product Team/Cross Business Team (IPT/CBT) environment
- Experience with transition of programs from design to manufacturing
- Production Control
- Related management experience
- Understanding of MRP and Shop Floor Management Tools (PRISM/VM)
- Proven experience in developing manufacturing strategies and proposals
- Proven ability to prepare and present reports and briefings
- Demonstrated results focus and ability to execute
- Communication skills: Negotiation, collaboration, creativity, presentation and communication (written and verbal), responsiveness, being open-minded, team player, facilitation
- Bachelor's degree (preferred fields but not limited to: Engineering; Operations Mgmt; Business Mgmt, Finance); Experience could be considered in lieu of a degree
49
Manager, Manufacturing Resume Examples & Samples
- Promote a culture of safety and continuous improvement
- Work with leadership in the creation and execution of VAC strategies
- Work with leadership in execution of low cost Global manufacturing initiatives within the LPO and SPO strategies
- Support each site P&L and balance sheet objectives
- Work in, support, and or lead cross functional VAC implementation teams
- Collaborate with all sites and departments throughout the business platform to identify financial, process, and efficiency improvement opportunities
- Develop and implement capital spending plans that meet the ongoing needs of the business for facilities, equipment, and productivity improvements
- Maintain and improve quality, safety and environmental standards
- Support efforts to improve deliveries, reduce and control costs, and improve lead-times while working with primary manufacturing locations
- Optimize operations by managing and executing to customer expectations
- Correctly identify and apply QA process and procedures to meet customer requirements
- Develop inventory controls and planning parameters to insure appropriate inventory levels and reduce receivables
- Align to working capital strategy
- Develop analytical reporting based on product mix, geography, industry, etc
- Detailed trend analysis related to start-up cost, investment, and ROI
- Provide weekly, monthly, and quarterly progress reporting
- Partner with representative sales team and leadership to support bookings growth
- Proper application of technical knowledge of valves and actuation
- Correctly apply applicable industry standards in product application and facility preparedness
- Effectively determine market and industry trends, competitive landscape, and customer activity, and present that information to leadership
- Experience leading an aftermarket or value-add business
- Automation, Actuation & Valve related experience highly preferred
- Experience in oil & gas, chemical, power and petro-chemical markets
- Proven track record in business development, operational excellence and management
- Experience in working with engineered products
- International experience a plus
50
Manager Manufacturing Resume Examples & Samples
- 9+ years of related manufacturing, quality or engineering experience
- 3+ years of experience in an Operations Engineer, Specialist or Manager role
- 3+ years of experience leading nonconformance investigations
51
Finance Manager, Manufacturing Resume Examples & Samples
- Assists in the preparation and determination of the strategy and plans
- Provides insight into operational performance by identifying issues, trends or interesting findings, offering recommendations for improvements
- Leads quarterly forecasts and annual budgeting processt. Participates in the monthly close process
- Manages the financials/costs for the facility. Understands the key drivers of variance, and proactively partners with leadership to control costs and mitigate risks
- Validates and monitors performance indicators (KPIs), highlighting trends and analyzing causes of unexpected variance
- Improves and enhances reporting to enable improved decision making
- Manages ad-hoc and urgent financial analysis requests
- Analyzes and prepares financial reports, statements and projections, and effectively communicate those to non-financial managers
- Ensures ongoing internal controls (periodic cycle counts, usage of procurement card, etc)
- Ensures the standardization and the validation of the data supporting the management of the plant
- 5 years of experience Accounting and Finance Planning & Analysis
- Manufacturing/Operations finance experience
- Process oriented, highly organized and strong attention to detail
- Team player and "whatever it takes" attitude
- Strong leadership skills with ability to drive results through team
- Strong interpersonal skills with proven ability to influence others
- Outstanding oral and written communication skills
- Strong working knowledge of MS Word, Excel, Outlook and PowerPoint
- MBA in Finance or Operations
52
Technology Manager Manufacturing Analytics Resume Examples & Samples
- Responsible for interfacing with all GE businesses and plants in China to identify the biggest needs and opportunities around using manufacturing analytics with data science for manufacturing process optimization and improvement
- Work with GE plants and R&D teams to define analytics solution requirements and project success metrics and develop solution approaches and generate project proposals
- Lead the design, development, and deployment of advanced manufacturing factory information systems and technical solutions using the latest sensors, control systems, software, and analytics
- Manage project timelines, budgets, and deliverables
- Responsible for
- M.S. Degree or Above in Computer Science/Engineering, Electronics, Electrical Engineering, or related technical discipline from an accredited college or university
- 5+ years of experience in software analytics, manufacturing, operations, automation design and implementation in an industrial setting
- Knowledge and Experience in data science and software analytics –
- Having the relevant experience is preferred in
53
Manager, Manufacturing Technology Operations Resume Examples & Samples
- Develop and mature the team members to continually solve more complex tasks
- Continually align priorities with production management and other main stakeholders
- Ensure team performance in solving day-to-day technical issues in the production
- Drive and support the team in the implementation of new work processes in relation to
54
Manager Manufacturing Services CMC Biologics Resume Examples & Samples
- Lead in developing processes and procedures for the Manufacturing Service group, to include
- Weigh & Dispense process flows, equipment identification, SOP’s, and batch documents
- Media and Buffer Prep process flows, equipment identification, SOP’s, and batch documents
- Autoclave and Washer process flows, load patterns, and SOP’s
- Lead and Perform cGMP operations within Clinical Manufacturing, to include
- CGMP operation to weigh & Dispense media and buffer components
- Formulation of Media and buffers to support cGMP production of clinical product manufacturing
- Put in place procedures to support product change over in BMF media and buffer formulation areas
- Maintaining a world class, clean, compliant, and safe work area
- Stocking of gowning supplies and removal of spent gowning from the Clinical Manufacturing facility
- Removal and management of waste from the Warehouse and Clinical Manufacturing Facility
- Knowledge of and ability to monitor and coordinate facility sanitization activities within the Clinical Manufacturing Facility
- Knowledge of parts washer and autoclave processes, load patterns and SOP’s
- Contribute to the qualification and manufacturing readiness activities for the Manufacturing Service team. This includes responsibilities such as
- Participate in FAT, SAT /IOQ and PQ activities for both facility and process equipment
- Responsible to author documentation such as master batch records, standard operating procedures and work instructions to meet safety, cGMP and corporate compliance requirements
- Participate in protocol deviation investigations and Change Controls
- Once operational, Lead cGMP Weigh & Dispense, Media / Buffer Prep, and Autoclave/ Wash operations in Clinical Manufacturing to include
- Weighing of raw materials as defined by batch documents and established SOP’s
- Preparation of media and buffer solutions utilizing manufacturing equipment such as single use mixers, pumps, pH meters, and conductivity meters, and consumables such as single use bags, filters, and tubing sets
- Operate a Washer and Autoclave to wash and sterilize supplies and parts needed for processing within the Clinical Manufacturing Facility
- Maintain 100% training compliance on all SOP’s and safety procedures
- Any other duties as assigned by supervisor, including assisting other functional groups as required
- S. in related life-Science field with up to 4 years of combined experience within cGMP manufacturing in a lead/supervisor role
- Experience with formulating media and buffer solution preparations within a cGMP environment
- Experience with performance of parts washer and/or autoclave
- Strong understanding of cGMPs as applicable to biologic operations
- Ability to stand, walk, bend, and reach for long periods of time
- > 5 years combined experience within cGMP Lead manufacturing role
- Experience with process control SCADA software (e.g., WonderWare )
55
Manager Manufacturing Processes & Systems Resume Examples & Samples
- Establishing high throughput strategy to achieve process scale
- Maintaining the manufacturing automation plan
- Expertise in Solidworks
- Expertise with industrial automation
- ISO13485 and FDA (FDA21 CFR210-211) Production / Manufacturing experience is a plus
56
Manager Manufacturing Technology Resume Examples & Samples
- Good Knowledge of PCBA assembly process, viz SMT & THT process, wave soldering,Manual soldering and Conformal coating
- Worked as a Team Lead and coaches/mentors team members on process improvement Initiatives
- Responsible to setup, review and analyze Temperature Profiling of both Reflow, Wave and CC oven
- Responsible in the evaluation and recommendation of improvements to the Manufacturing Process,
- Responsible to Closely Monitor the SMT PnP line & THT line activities / issues and investigate and resolve process issues to improve the product yield & quality,
- Responsible to review the PCB gerbers, Conduct DOE( Design of Experiments ), DFBA (Design for Board Assembly) on new product,
- Do PFMEA of the process, Design Line layout and Effective monitoring and implementation of EOHS standards
- He should IPC610 certified professional and working knowledge on 6 Sigma methodology of problem solving
- Should have good written and Oral communication skill in English language and working knowledge in MIcrosoft office
- Conducts changeover analysis, material handling analysis and overall equipment effectiveness
- Develops, validates, assesses suitability, reports, and implements KPIs (Key Performance Indicators) /Process Metrics on a facility level
- Coaches others on effective application of tolerance standards, material and process alternatives options, and product cost estimating
- Leads the risk assessment and reporting process
- Performs gap analysis and make recommendations
- Experienced in process simulation modeling, interpreting and optimizing processes
- Interprets results of process simulation models and use to optimize actual production facility
- Ability to apply basic Quality tools: conduct DFMEA,8D Functional Analysis of the needs
- Ability to update risks dashboards
- Ensuring adequate training on identification of training needs of his team
- Implementation of corrective and preventive action on Process issues
- Diploma in Engineering with Minimum 12 Years of experience PCBA Assembly equipment and Process in an Electronic Industry
- Graduate Engineering with Minimum 8 Years of experience PCBA Assembly equipment and Process in an Electronic Industry
57
Business Process Manager Manufacturing Systems Resume Examples & Samples
- Coordinate business process owners for front-end, engineering, production planning & execution, controlling, etc
- Establish business process for project / sales order costing, use of costing sheets, etc
- Order configuration and engineering investigation, evaluation, and recommendation to support the business processes & their implementation
- Design and implement cost-effective business processes using Information Systems-based solutions to business problems
- Prepare, implement, and improve order configuration & other sales configuration tools in alignment with the SAP back end
- Work closely with BU functions to harmonize the way business is conducted by implementing SAP standard concepts (e.g. SPEX)
- Coordinate with LBU functions and country IS organization while implementing SPEX
- Prepare future requirements for business engineering, marketing & sales, and manufacturing changes
- Preparation of flowcharts, diagrams, analysis and specifications
- Investigate / prioritize business requirements to define scope & objectives of the projects, and to prepare schedules (including limitations & timing) to achieve desired results
- Develop, prepare, and implement processes that insure reduced cycle time, reduced overhead, and improve overall process efficiency
- Troubleshoot, analyze, and resolve complex problems, and develop / implement measures to prevent reoccurrence along with devising modifications and recommending ways to improve
- Maintain (or provide guidance for maintenance of) a wide variety of systems
- Provide support and ensure accuracy of information & responsiveness to customers (for internal & external requirements)
- Lead and coordinate the work of less-experienced staff, and provide training & support to business process owners
- Continuously assess and understand the operational and commercial requirements of the facility to improve operational performance & business processes, and provide guidance & direction within the facility to ensure efficient use of processes and supporting applications such as Quotation System, ERP System, & Manufacturing Equipment
- Assess and translate improvement potential into projects & business solutions (e.g. processes, applications, and services)
- Manage the portfolio of business improvement projects (with or without systems content) and ensure benefits delivery & execution of these projects within desired quality, scheduling, and budget targets
- Ensure implementation of group, division and BU improvement projects, IS services, and applications
- Ensure efficient integration of processes and IS applications from global & local perspectives
- Ensure an adequate level of competence is in the processes and applications within the local unit
- Lead the continuous improvement process in Jefferson City with respect to cost, safety, quality, and productivity throughout the entire value chain to increase customer satisfaction & reduce operating cost
- Enforce consistent processes within Jefferson City in accordance to BU standards
- Drives change, including people, process, and technology
- Encourage collaboration by promoting open & constructive dialogue, and cooperation within the ABB Corporation, the division, the Operational Excellence [OpEx] team, and the Business Engagement Manager
- Bachelor’s degree in a technical discipline
- 12 years of professional experience working with Project Management and/or Information Systems in manufacturing environments
- Bachelor’s degree in Computer Science and/or Engineering
- Strong experience leading Information Systems [IS] teams and projects, especially with the implementation of new technology related to manufacturing systems
- Strong proficiency working with Microsoft development technologies, especially Visual Studio and .NET tools (e.g. VB.NET, C#, SQL, SharePoint, etc.)
- 2 years of Project Management experience with manufacturing systems is strongly preferred; experience in leading related change and business processes is a plus
- Requires broad knowledge of manufacturing operations, Information Systems, quotation tools, engineering, sales, marketing, and their applications
- Ability to influence decisions and cost-effectively provide cross functional support
- Requires strong analytical skills, initiative, and ingenuity to solve complex problems and implement remedial measures
- Requires strong communications skills (verbal & written), especially when discussing and negotiating resolution of controversial issues
- Recent experience working in project management and/or project coordination, especially in a manufacturing environment
- Proficiency with SAP ERP is critical; proficiency with other technical tools [such as MS-Office (e.g. Excel, Word, & PowerPoint), MS Project, etc.] will also be expected
- Excellent organization skills and detail-oriented nature
58
Manager, Manufacturing Resume Examples & Samples
- Drive world class safety performance through the implementation of behavioral based safety programs and ensure compliance to all Bombardier and regulatory requirements
- Enhance employee engagement through effective communications and interactions with operations personnel and production focus teams
- Drive continuous improvements in operational and business processes to deliver optimal results for Safety, quality, productivity, cost and labour relations
- Actively lead and drive execution of the Achieving Excellence System within area of responsibility (i.e. SQPEC, Visible Leadership, etc.) in line with Bombardier's strategic vision
- Coach, mentor and develop supervisory and non-supervisory employees in the department
- Ensure timely and effective communications regarding operational issues, schedules and compliance with internal and external Bombardier customers
- Maintain a strong cross-functional focus, ensuring the team members work collaboratively to meet program objectives
59
Manager, Manufacturing Resume Examples & Samples
- Holds accountability for daily operation and meeting production goals in a timely and accurate manner within an assembly process or similar assigned area
- Implements production plans and provides feedback around product introduction, equipment efficiency, materials supply constraints, schedules and staffing requirements to meet given objectives
- Implements activities in production area to ensure timely, high quality production at the lowest cost consistent with the quality requirements
- Provides focus to the production team to execute to quality, schedule and cost expectations
- Implements given operating plans and operating budget. Executes given priorities to ensure the most efficient and effective production schedule and staffing plan. Executes to the given budget targets. Develops daily plans to meet production needs
- Implements and executes specific components of quality improvement, Lean and Six Sigma programs. Accountable for reduction of cost and waste within production. Improves productivity by implementing best practices
- Is accountable for implementing given schedules and expenditure constraints for direct and indirect labor. May plan details of staffing and labor around given priorities
- Responsible for managing the assigned assembly process and the related workforce. Communicates goals and strategies to the workforce, which may include represented and unrepresented components. Manages issues, solves problems, and delegates to team to bring solutions. Coordinates and interacts with functional areas and business units that support the production floor, exercising indirect leadership. Gets results from professional and/or direct labor employees by establishing work plans and delegating assignments
- Interacts as needed with internal customers and related business units
- Oversees deployment of environmental, health and safety policies and procedures within area. Ensures workplace training and safety plans are fully implemented. Ensures the area complies with OSHA, EPA and other safety and health requirements. Operates as a working manager, participating in direct project activities
- Build Powerful Networks - Involves networking internally and externally to develop and maintain relationships in all kinds of organizations – knowing what they do, how they can help you, and how you can help them. Internally, it is working together across organizational and cultural boundaries, functions and businesses. Externally, these networks include customers, but they also extend to suppliers, alliance partners, customers' customers and others – some of whom might fall well outside the normal sphere of the organization. (Networking and Relationship Management, Collaboration and Teamwork, Conflict Management)
- Unleash Energy - Focuses on tapping into and unleashing the incredible talent and passion of every person in the organization, starting with oneself. Leaders first reach deep inside themselves to embrace their hopes and dreams. They approach situations with passion. They then help others embrace their own hopes and dreams and guide them in applying their passion to achieve the goals of the organization and to open up new possibilities. Leaders express commitment to and confidence in people, often beyond the level of confidence people have in themselves. (Selecting Talent, Developing Self and Others, Inspiring and Motivating Others)
- Communicate Masterfully - Goes beyond the communication of ideas – it achieves a shared understanding and level of trust that gives personal meaning to the work. The leader's message ties the overall objectives of the organization to the personal objectives of the individuals, team and organization. In doing so, the leader aligns employees to achieve the organization's goals by communicating what needs to be done, why it needs to be done, and what's in it for them. (Oral & Written Communication, Active Listening)
- Execute Flawlessly - Requires a relentless pursuit of end-goals and the discipline to do what it takes to plan, organize, and achieve those goals. This goes beyond just performing specific job responsibilities. It involves a deep sense of caring, respect for the team and a commitment to customers. This is supported through the continuous development of tools, processes and approaches that build a heightened sense of confidence in the organization's ability to achieve astonishing results. (Business Acumen, Customer Focus, Planning and Organizing, Drive for Results, Continuous Process Improvement and Quality Orientation)
- Exercise Insightful Judgment - Necessitates that in a competitive business environment, the organizations leaders balance the analysis of issues, problems, opportunities, and make timely decisions in the face of uncertainty. Effective decision makers will have confidence in their own analysis and instincts, and must be willing to make tough choices based on sound principles, values, and standards. (Critical Thinking, Decision Making, Accountability, Integrity and Ethics)
60
Manager Manufacturing Engineer Resume Examples & Samples
- You will have the responsibility for internal environment and personal health and safety
- Development and training of the co-workers competences, skills, behaviors and to become ready for new positions with increased responsibilities
- Resource capacity and flexibility in order to meet targets agreed with Businesses
- Ensuring visual leadership including recognition, coaching and constructive feedback to employees
- Continuous improvement, in the framework of Lean, for the working methods and processes that the department are involved in for to reach our business goals
- Being responsible for the department’s budget and results
- Represent the manufacturing organization in different management forums with cross-functional attendees
- You will be responsible for production commitments related to early stages in the product development process including reviews and milestones
- In addition, you will personally manage tasks that are of importance for Manufacturing Engineering within EPS, and lies within your area of expertise
- You have a technical education, preferably at academic level
- Good experience in Manufacturing Engineering, Project Management and/or other relevant experiences
- Knowledge in the areas of product knowledge, producability, PFMEA, SPC
- Demonstrated ability to inspire, motivate and lead a team in delivering results on time, with a high focus of robustness and quality, with a business mindset
- Have the ability work independently as well as through your team and cross functional in order to meet established goals and targets
- An analytical mind with the capability to communicate those skills in both Swedish and English
- An outgoing, open-minded, and positive person with a demonstrated talent to manage continuous improvement
- Have the ability to work proactively
61
Manager Manufacturing Quality Resume Examples & Samples
- Responsible to manage the safety, cost, quality, and productivity of the assigned VQA area. This position will be responsible for managing salaried and/or hourly employees. Position is responsible for all aspects of department leadership including safety performance, productivity, budget management and meeting quality objectives
- Works efficiently & effectively with Mfg., PE, & PQE to improve product quality
- Protects Nissan customers by ensuring rigid vehicle quality standards are met. Serves as a quality ambassador for Canton
- Manages major & minor model quality plan development & execution; addresses production concerns in PQA to ensure countermeasures are made in a timely manner
- Analyzes & reviews MFG CPU & prepares reports; conducts monthly reviews of information such as manpower requirements, future model plans, staffing plans, budgets, & prepares reports as required
- Manages a team of supervisors; provides direction & responsibilities for their team. Educates team on Nissan's NPW & Hoshin Kanri concepts; lead activities & classes which teach GGK MFG principles
- As necessary, performs other related duties of which the above are representative
- Job Knowledge and Skill: Excellent communication, interpersonal and motivational skills. Basic understanding of automotive assembly and function. Knowledge of ISO9000 and ISO14001. Project management skills and experience required
- Supervisory Experience: Five years in a full supervisory role, providing leadership, coaching, guidance and training and contributing to staff development
- Education: A related degree from a four-year college. Consider equivalent related college or technical courses, seminars and in-house classroom training
- Computer Skills: Working knowledge of word processor, spreadsheet, other PC applications, or mainframe applications to produce non-standard, creative products
- Travel: Infrequent day and overnight travel, including international travel
62
Materials Manager Manufacturing Resume Examples & Samples
- Studies receiving or shipping notices and reports of warehousing space available to develop schedule for material handling activities
- Coordinate all material and equipment related activities from receipt to turn over including shipping/receipt, loading and unloading, tagging, identification, traceability, storage and control, inventory management, warehousing and issue of material to ensure compliance with Department of Energy and Nuclear Regulatory Commission requirements
- Establishment and maintenance of up-to-date matrixes containing the status and requirements of incoming materials and equipment
- Interface and coordination with field activities to ensure that material and equipment requirements are met and that the turn-over of material, equipment, and spare parts is accomplished in a timely and efficient manner
- Establishment and coordination of the in-storage maintenance program for material and equipment, and coordination with Quality Assurance personnel to prevent and resolve non-conformance, stop work, and Deficiency Action Reports
- Oversee Shipping & Receiving, Warehouse, Data Entry and Inventory Control personnel for Multi-Billion dollar government project
- Establish Budgets and Controls in compliance with Government Accounting Practice
- Uses operational and supervisory expertise to solve problems within own area
- Interprets customer needs and assesses requirements
- Sets day-to-day direction for employees to support business objectives
- Resolves routine problems using defined processes and own experience
- Has in-depth knowledge of work processes and tools within own area
- 2 - 5 years of Industrial Construction Experience
63
Senior Finance Manager, Manufacturing Finance Resume Examples & Samples
- Lead, direct, and manage global mfg finance team to drive process improvement, and work closely with operation partners to execute company guidance and be able to exceed/meet the target/metrics
- Manage, support and partnering with operation business partners on budgeting and forecasting process, cost reduction roadmaps as well as strategic initiatives
- Manage the month-end closing process to analyze gross margin actual results, cost reduction and product mix
- Prepare monthly gross margin review and operations performance packages for internal executive management as well as business partners
- Lead the finance team in developing financial reporting systems, business processes and dashboards to provide timely data and analysis to support business decisions
- Execute the company policy and SOX compliance
- Coordinate with external auditors for quarterly and yearly audit engagement
- Prepare and review financial statement and inventory flux analysis and provide detailed explanations
- Assist with special projects as requested
- Bachelor’s degree in Accounting or Finance. MBA/CPA preferred
- Excellent analytical, organization and communication (both written and verbal) skills with the ability to work independently and interact effectively with all levels of management
- Accounting experience preferred
- Demonstrated detail-oriented work ethic
64
Manager Manufacturing Resume Examples & Samples
- Direct responsibility for departmental spend and managing budget
- Drive site to achieve/surpass customer and financial commitments
- Provide customer interface and support as required; using customer feedback to improve quality and delivery while driving process and yield improvement
- Establish and implement standard manufacturing and materials practices by implementing and executing the Honeywell Operating System, HOS
- Model the HOS leadership expectations including use of, and adherence to, leadership standardized work
- This requires spending considerable time walking the factory floor and auditing aspects of the operating system
- Manage inventories to achieve working capital goals
- Integrate key elements of Supply Chain to improve cycle time
- Ensures process and yield improvement is embedded into the factory culture and actions
- Champion programs to address employee satisfaction and employee training, communications, and department structures to support operational and strategic goals
65
IT Manager, Manufacturing Infrastructure Resume Examples & Samples
- A Bachelors degree with 7 years of relevant experience with demonstrated skills or 9–11 or more years of applied experience with demonstrated skills. Networking-CISCO, Aruba wireless, Windows OS, Voice, Video, Skype, Citrix, SharePoint, MOSAIC, etc
- Experience managing ITS Projects and/or Programs
- Experience with deploying and driving execution via performance measurement, benchmarking, and related visual management
- Held prior accountabilities that required influencing leaders outside of administrative authority
- Understands and is familiar with Infrastructure capability and delivery process(es)
- Experience working in a global IT organization; preferred experience working in or supporting a business
- Knowledge of business competitive landscape
- Strong leadership and service delivery skills
- Cultivates networking opportunities with peer organizations
66
Manager, Manufacturing Sciences Resume Examples & Samples
- Hire, develop, motivate, and deploy highly functioning team of tech transfer leaders. Establish team vision, goals, and priorities and ensure alignment with departmental, PO&T, and corporate goals and priorities, as appropriate. Routinely evaluate performance of individual leaders/collective team and calibrate as appropriate. Develop succession plan to ensure continuity of tech transfer function
- Develop relationships with external business partners and internal stakeholder groups, including (but not limited to) manufacturing, engineering, automation, technical development, quality, materials, site planning, technical operations, asset leaders, and supply chain planning
- Cultivate continuous improvement environment within tech transfer teams at the RTP site and benchmark tech transfer best practices both internal and external to Biogen, as appropriate. Lead/guide optimization projects resulting in improved (simplified, more robust, or clearer) business processes
- Ensure overall tech transfer system compliance with regulatory requirements
- Lead, facilitate, or coordinate all activities pertaining to tech transfer, which includes initial process/facility fit, process transfer, manufacturing readiness, production and testing, material disposition, and tech transfer/project closeout
- Advocate for and represent tech transfer in departmental and site leadership teams
- Established credibility within broad tech transfer functions
- Experience in hiring, developing, motivating, and deploying teams
- Capable of building relationships with external business partners and internal stakeholder groups, including (but not limited to) manufacturing, engineering, automation, technical development, quality, materials, site planning, technical operations, asset leaders, and supply chain planning
- History of identifying and leading optimization projects resulting in improved (simplified, more robust, or clearer) business processes
- Understanding of how tech transfer projects establish compliance within regulatory requirements
- Experience with activities including process/facility fit, process transfer, manufacturing readiness, production and testing, material disposition, and tech transfer/project closeout
67
Manager Manufacturing Excellence Resume Examples & Samples
- Address cost drivers in the manufacturing process of T2 suppliers to achieve transparency in material costing and create a fact-based costing basis through the support of the material costing tool
- With support from the central Manufacturing Excellence team, be responsible for M.E. with the T2s within the region, including providing relevant training to T2 teams and LO staff as appropriate
- Evaluate T2s production methods and introduce improvement guidelines to enhance output and quality
- Support the creation of individual vendor action plans to improve efficiency levels enabling successful achievement of milestones and business goals
- Work closely with the internal Continuous Improvement Team, Manufacturing Excellence and Apparel Sourcing Operations team to understand objectives, goals and expectations and apply steps locally to achieve our goals
- Responsible for driving improvements in quality, cost and delivery across the business via the application of I.E. best practices and Lean Manufacturing activities
- Use industrial engineering techniques to develop positive change to current and existing processes throughout the T2 supply base
- Assist when needed the Sourcing leadership to provide advice and drive change within the business
- Requires a broad background in Industrial Engineering technology and application
- Expected to be able to utilize any recognized industrial engineering techniques effectively and to produce tangible results
- 6S or Lean background would be an advantage
- Good presentation, communication, negotiation skills and project management
- Strong Costing background (either in Footwear or Apparel industry)
- Recommend methods for improving operator efficiency and reducing waste of materials and utilities, such as restructuring job duties, reorganizing work flow, relocating equipment and advise on the machinery investment
- A minimum of 4-5 years textile manufacturing experience within an apparel manufacturing/industrial engineering environment
68
Manager, Manufacturing Resume Examples & Samples
- Safety of personnel, quality of products, and on time shipment of products meeting customer’s expectations
- Direct labor talent management, including hiring and training of supervisors, assemblers and technicians, in a growth environment
- Implements the manufacturing operations strategy, monitors control systems and metrics to accurately measure progress and drive continuous improvement
- Maximizes efficiency, productivity and quality by analyzing process controls and capabilities, layout of equipment, workflow, assembly methods, and work force utilization
- Leads lean manufacturing methodology, where appropriate, by reviewing operations, observing, planning, coordinating, and facilitating process improvement, and Kaizen teams
- Demonstrate behavior consistent with the Company’s Code of Ethics and Conduct. Ensure that direct report(s) are trained and evaluated on their knowledge and adherence to the Company’s values, Code of Ethics and Conduct, and applicable compliance policies
- Manage, evaluate and develop team of employees to meet functional deliverables and responsibilities. Complete company people management requirements. Exhibit manager core competencies
- It is the responsibility of every Rapiscan/AS&E employee to report to their manager or a member of senior management any quality problems or defects in order for corrective action to be implemented and to avoid recurrence of the problem
- Uphold the company’s core values of Integrity, Innovation, Accountability, and Teamwork
- Bachelor’s degree, industrial or mechanical preferred, or significant industry experience
- 8 years supervisory experience in an industrial manufacturing environment
- Strong interpersonal skills, leading passionate people, and acting as an effective change agent
- Working experience with ERP systems, product life cycle management and ECO/NC systems
- Successful experience implementing ISO9001/AS9100 quality management systems
- Must be US Persons based on ITAR definition (US Citizen or Permanent Resident)*
69
Manager, Manufacturing Resume Examples & Samples
- Responsible for the management of laboratory staff including, but not limited to, hiring, training, coaching, evaluating and disciplining to ensure a well-qualified team and to enhance operational success and compliance
- Coordinate the implementation of new or revised tests, procedures, and equipment with SOPs, CFR and OSHA regulations
- Ensure laboratory training and annual competency assessments are completed in compliance with established guidelines in the ARC training system. May act as trainer for department specific curricula
- Write, organize and maintain technical sections of departmental procedure manual
- Responsible for the accuracy of computer and physical blood component inventories
- May be responsible for tracking and trending and analysis of laboratory data and the generation of reports
- Participate in documenting, investigating, troubleshooting and preventing recurrence of department problems, concerns, and complaints
70
Manager Manufacturing Resume Examples & Samples
- Bachelor’s Degree in Life Sciences, Engineering or Management
- A minimum of five (5) years’ working in manufacturing, preferably a regulated environment
- A background in continuous improvement/CAPA implementation
- Previous experience with biologic manufacturing and firm understanding of equipment associated with their manufacture with focus in downstream manufacturing including centrifugation, purification, and filtration
- Involvement with Regulatory Agency inspections including shop floor tours and documentation audits
- Demonstrated customer focus through meeting commitments and deadlines
- Demonstrated ability to build networks and relationships at various organizational levels with strong interpersonal skills
- Ability to learn and understand complex processes quickly, then explain those processes with ease to various internal and external audiences with level appropriate detail
71
Named Account Sales Manager, Manufacturing Resume Examples & Samples
- Achieve assigned financial targets by guiding team to expand and develop existing named accounts through a direct sales model
- Engage and inspire team members to look at near and long term visions of the accounts by helping to formulate appropriate account strategy
- Provide guidance on customer-facing account planning and industry account plans and coach direct reports to improve their plans including, but not limited to, customer ROI, political alignment/executive support, risk identification/mitigation and alignment with ADSK
72
Engineering Manager Manufacturing Resume Examples & Samples
- Provide technical leadership and strategic direction for the cluster of production plants in areas of process engineering, maintenance, projects, new product introductions, automation, and innovation management
- Responsible for developing the engineering & technology roadmaps to drive a competitive advantage and to meet future customers’ needs
- Develop and manage expense and capital budgets per strategic plans and forecasts
- Successfully integrate new products and process into existing manufacturing facilities ensuring good performance metrics and capability planning
- Responsible for the management, continuous development and performance of teams
- Ensure compliance in all aspects of Environmental, Health and Safety per J&J standards and local regulations
- Promote a quality-focused culture within the global engineering team, ensuring adherence to cGMP’s and Quality Systems as defined in the Quality Manual
- A minimum of Bachelor degree in Engineering, Science or related discipline
- An advanced degree such as MBA, MSc/P.h.D in Science, Engineering or related disciplines is desirable
- 8-10 years of experience in Manufacturing or Manufacturing Engineering area, preferably in the medical device or regulated industry. A minimum of 5 years of managerial experience with people responsibility
- Experience in areas of process engineering, maintenance and project management in a manufacturing facility
- Outstanding leadership capabilities – demonstrate ability to form, motivate, and inspire teams to drive significantly increased performance through strong communication and empowerment
- Results and performance driven: willing to be in charge and take ownership and poses a proactive and driving attitude
- Must demonstrate working knowledge of process development and validation, including design of experiments, statistical analysis, and project management
- Must demonstrate strong technical, analytical and organizational skills
- Demonstrated ability to work within tight deadlines with proven experience in meeting goals in a timely manner
- Ability to deal with a variety of abstract and concrete variables
- Ability to work effectively with peers both internally and externally
- Fluent in English, conversational level of German
73
Buffer Preparation Manager, Manufacturing Resume Examples & Samples
- Oversee start up activities for Buffer preparation group
- Minimum of 3 years of experience leading a group with direct reporting
- Very good command of English and the desire to learn German if you do not speak German
74
IT Manager, Manufacturing Plant Operations Resume Examples & Samples
- Provide direct supervision to an on-site IT operations and applications team/responsible for talent acquisition, training, mentoring and performance management
- Member of plant’s sr. leadership team/must translate complex business requirements into well-defined, actionable
- Manage team of up to technical specialists (including consultants/contractors)
- Demonstrate solid technical knowledge and business acumen
- Works with limited oversight/comfortably address complex problems in a manufacturing environment regulated by the FDA
- Strong knowledge of corporate IT/IS policies, standards and procedures and have excellent interpersonal communication skills
- Establish departmental objectives/ensure they align with the Global IT vision and objectives
- Plan/implement procedures and systems to maximize operating efficiency
- Implement IT security best practices to ensure safety of data and systems
- Interact regularly with internal/external customers to understand business needs/determine potential solutions
- Review team, group and business deliverables to ensure quality (design walk-through, test results, etc.) and adherence to specific processes, standards and regulatory requirements
- Participate in budget process/adhere to a fixed operating budget. Assist the business with identifying IT capital and operating expense requirements
- Participate in the research, analysis, selection and implementation of new tools, technologies and/or services
- Provide business-level support by analyzing requirements, researching potential solutions, recommending hardware and/or software, and partnering with Plant leadership to introduce technologies
- Participate in the strategic planning process and align with the Global IT mission
- Develop, gather and measure relevant productivity metrics
- Manage and participate on Plant projects as required
- Excellent interpersonal communication and public-speaking skills
- Ability to hire, train, coach, motivate, inspire and influence technical personnel
- Extensive experience leading technical personnel responsible for supporting all Microsoft Windows operating systems (Windows XP, Windows 7, Windows Server 2008/2012)
- Proficient with all Microsoft Office applications (Outlook, Word, Excel, PowerPoint, Access)
- Basic knowledge of VMware, ESXi and vCenter configuration, administration and utilization
- Knowledge of Manufacturing Operations and Enterprise Management Systems
- Ability to drive results through others by collaborating with other Global IT organizations and personnel
- Familiarity with performance management concepts and execution tactics
- Experience providing executive-level briefings and presentations
- Strong analytical, communication, and organizational skills
- Strong leadership and presentation skills
75
Product Manager, Manufacturing Collaboration Resume Examples & Samples
- Create the product roadmap and manage the entire product/product line life cycle from concept through strategic planning to tactical activities. Drive revenue for the division through competitive distribution, pricing, and positioning. Manage decisions to continue or discontinue product offering based on profitability
- Assess and investigate different technologies (both inside and outside the company) and consider how they might be applied to solve a given market problem or to add to a current product offering
- Provide ongoing guidance to product design in the development of product specifications that deliver on market requirements. Help set priorities of the development organization. Drive the solution set across product development and product marketing through market requirements definition, product release requirements, product contract and product positioning
- Identify, create and maintain relationships, leverages, and act as main point of contact for key thought leaders in the industry, including industry specialists, research analysts, key editors in the press, and other third parties
- Experience doing customer interviews
- Able to easily transition between high-level strategy to day-to-day implementation
- Risk management assessment and planning
76
Manager Manufacturing Excellence, Sialkot Resume Examples & Samples
- Ensure Lean Manufacturing Principles and Modules are implemented and continuously used and tracked
- Facilitate cross-functional events (e.g. T1 visits to other industries) to identify short term, midterm and long term efficiency improvement opportunities
- Partner with LO Operations Management to foster and sustain a Manufacturing Excellence culture among suppliers. Work together to drive the best practices to the factories
- Partner with A&G Costing to establish, refine and support SMV data structure with data measurements and quantifying savings
- Maintain platform for knowledge transfer throughout the adidas-Group organization and supplier groups. (Best Practice Manual, Training Material, Presentations, supplier summits, exchange meetings, etc.)
- Liaise with Manufacturing Excellence Footwear and Apparel team to identify synergies in Innovation, automation and other efficiency measures for future cost mitigation opportunities
- Focus continuously on product and processes improvements providing the best quality/price value
- Support development towards future capabilities by establishing criteria / evaluations for T1 suppliers
- Strong quality and manufacturing knowledge of the A&G or equivalent industry
- Advanced skills in Project management
- Ability to cope with change, make decisions and act comfortably with risk and uncertainty
- Ability to network with multiple stakeholders
- Strong communication and interpersonal skill with all levels of business
- Fluent English / Urdu
- University degree with focus on industrial engineering related area
- At least 5 years of work experience in the assembly industry preferable textile or sportswear (hardware) industry
- Experience in Lean 6 Sigma implementation is a plus
77
Manager Manufacturing Resume Examples & Samples
- Advanced supervisory and leadership skills
- Ability to interpret and analyze data and write technical reports
- Manage multiple priorities seamlessly
- Lead the workforce hiring process and effectively communicate work execution strategies
- Support the implementation of the applicable employee work-time management software for manufacturing hourly employees
- Promote and support a perfect equipment culture, by assisting maintenance team during implementation of programs such as Total Preventive Maintenance (TPM), equipment reliability, Preventive Maintenance (PM) and Predictive Maintenance (PdM) programs, etc
- Review and approve SOPs and Job aids, associated to manufacturing processes
- Actively drive Electronic Batch Management (EBM) process steps development and implementation
- Support process technical transfer and any change with BOM materials
- Drive the implementation of appropriate measures to ensure availability of all materials and consumables and lead the implementation of Kanban and 5S systems to assist from CQV to Full production environment
- Build a culture of safety first in compliance with Environmental, Health, and Safety (EHS) through all manufacturing associates and production engineers. Support development and communication of Job Hazard Analysis (JHA) packets
- Support project deliverables to completion and meet timeline and budget objectives
- Coordinate availability of manufacturing resources to execute qualification activities and execute production batches per schedule
- Responsible for reviewing and modifying related training material and support training of manufacturing personnel
- Through regular visits to the manufacturing floor (Gemba), assist in the generation of punch list on associated discrepancies and lead/support the resolution of them
- Assist the development of Key Performance Indicators (KPI’s) such as process yields, plan attainment, conversion loss, manufacturing events, safety, etc
- Manage daily OMT meetings (shift change, daily production meeting) as required
- Responsible for meeting production plan & delivering high quality products to customers in a timely fashion and cost-efficient manner
- Lead the daily manufacturing operations across multiple shifts and/or department
- Drive operational excellence on the shop floor using lean tools like 5S, Kanban, visual management, SMED
- Emphasize training and implement control systems on the shift or multiple shifts to eliminate product discrepancies
- Lead and support manufacturing event investigations from initiation to closure in a timely manner to assure compliance with plan. Serve as Mfg main point of contact / SME for product impact decisions as appropriate
- Drive and ensure the right KPIs are implemented and tracked on a regular basis
- Lead by example and production floor presence and focus. Mentor supervisors and production engineers/SMEs on projects and activities
- Coordinate necessary manufacturing resources and rally support groups to resolve production-related issues
- Rapid and relentless approach to address production-related issues by providing sustainable long-term solutions
- Conduct impartial assessment of shift performance – main priority is overall performance of applicable business unit
- Constant calibration with other Superintendents focusing on technical background of issue as well as consequences considered when making decision
- Build trust and unwavering collaboration with key support personnel and peers
- Manage shift/team and investigate and resolve disciplinary issues
- Support and emphasize the Safety and Quality commitments of department
- Identify/prioritize/provide resources to assist the department manager to meet the annual operating plan and budgetary commitments
- Will be responsible for driving operational excellence and flawless execution in day to day operation of the plant
- Advanced supervisory and leadership skills. Must have a demonstrated track record of successfully executing within manufacturing environment supporting production issues, in a FDA-regulated manufacturing environment. Green field experience is desirable
- Possess knowledge of core principles in various manufacturing disciplines (i.e. cell culture / fractionation / purification / aseptic filling / packaging / cGMP facility design), support systems (WFI /RO / clean steam / compressed gases / HVAC) and facility design. Experience with large-scale protein ultrafiltration and column chromatography is desirable
- Must have the ability to effectively lead manufacturing production floor and drive results. Direct experience with manufacturing operations and biotechnology processes is strongly preferred
- Provide a positive and equitable working environment emphasizing the Shire Shared Values: Respect/Responsiveness/Results
- Ability to solve routine and challenging manufacturing problems without assistance
- Ability to travel at a minimum of 5%
- Must have proficient computer skills and be experienced using MS Office software (Word, Excel, PowerPoint, MS Project)
- In general, the position requires a combination of sedentary work and walking around observing conditions in the facility
- Must be able to work in controlled environments requiring special gowning. Will be required to follow gowning requirements and wear protective clothing over the head, face, hands, feet and body
- No make-up, jewelry, contact lenses, nail polish or artificial fingernails may be worn in the work environment
- Will work around chemicals such as alcohol that may require respiratory protection
- This is a 3rd shift Manager position. May be required to work or be assigned to a different shift as needed
- Must be able to work weekends or overtime as required
- Inside working conditions
- Some clean room and cool/hot storage conditions
78
Accounting Manager, Manufacturing Resume Examples & Samples
- Leads a team of 10-12 teammates responsible for preparing journal entries,
- A minimum of 9 years of professional finance/accounting experience
- Experience in financial reporting ,analysis, month end closing and budgeting, forecasting
- Experience leading a team of finance and/or accounting professionals
- MBA/CPA
- Knowledge & experience with SAP
79
Manager, Manufacturing Resume Examples & Samples
- You have a university degree or college diploma in a technical or related discipline
- You possess excellent leadership skills including strong ambition and desire to succeed, a strong professional ethic and proven planning, prioritizing and organizational skills
- You possess strong computer skills and the ability to work with MS Excel, Word, and PowerPoint
80
Associate Department Manager, Manufacturing Resume Examples & Samples
- Responsible for the oversight of the Manufacturing Technical Team Department formed by Deviation Investigation Team (DIT) and Technical Writers Team (TWT)
- Responsible for staffing, training and retaining energized, motivated, team oriented staffs
- Responsible for continuous learning, development and advancement of staffs
- Utilize work staffs in an efficient and effective manner through cross training/ flexible resource planning
- Provide supervision over the performance of deviation investigation and closure. The completion of a deviation report includes and is not limited to root cause analysis, product impact assessment and design of appropriate CAPA(s)
- Provide supervision over the performance in order to deliver Master Batch Records (MBRs) in timely manner for scheduled campaigns/tech transfers
- Responsible for ensuring the timeliness closure of deviations and MBRs modification and creation
- Review deviation investigation reports generated by Technical Investigators
- Resolve timeline and resource constraints via appropriate prioritization and escalation. Prevent project delays proactively by working closely with internal and external teams to remove obstacles to delivery
- Provide supplementary support in deviation investigation as necessary
- Ensure consistency and high standards in technical writing and investigational skills
- Ensure interactions between both teams and customers are constructive and of high quality
- Close collaboration with Program Management and QA Operations to facilitate customer meetings, scheduled campaigns and lot releases
- Work inter-departmentally to identify appropriate actions to facilitate deviation closure
- Attend the weekly Lot Release meeting and to provide appropriate feedback especially in case of potential deviations that could impact Lot Releases
- May be involved in projects, not directly associated with deviations or investigations, as project manager
- Work closely with Manufacturing Managers in the development/tracking of manufacturing performance metrics in Quality/Delivery Hoshin and identify opportunities for continuous improvements
- Any other duties as assigned by your Supervisor/ Manager
- 10+ years of relevant work experience in a regulated manufacturing environment with at least 3 years in a supervisory capacity
- Bachelor degree/ Diploma in a Science/ Engineering related discipline
- Strong knowledge of GMP applications
- Strong knowledge of and past experience with mammalian cell culture and/or purification processes
- 7+ years of relevant cGMP experience
- Excellent leadership skills in team based management
- Skillful knowledge of Microsoft Windows and Microsoft Office (Excel, Word, Project, PowerPoint)
- Experience in technical writing, root cause analysis and FMEA
- Excellent written and oral presentation skills
- Excellent interaction skills with development scientists, customers and auditors
81
Manager Manufacturing Resume Examples & Samples
- Selection, training, supervision (performance appraisals) and development of 4 – 6 staff members
- Responsible for compliance with cGMP and Safety requirements
- Ensures plant/site safety programs and goals are supported
- Ensure schedule adherence for tasks including but not limited to manufacturing, validation, and maintenance. Adjust schedule as necessary to accommodate changes and rework
- Ensure staff is fully trained and proficient on tasks performed
- Ensure SOPs, batch records and completed documentation are accurate and up to date. This includes timely review of documents and coordination with other organizations to ensure accurate and complete documentation
- Investigation and troubleshooting of equipment and the process
- Utilize appropriate systems for job responsibilities (SAP, QMTS, LIMS, MAXIMO, etc)
- Interact with internal and external regulatory agencies (FDA, EMEA etc) as directed
- Interact with various support departments to assist with scheduling of services performed in the plant
- Identification and implementation of process improvements
- Application of Lean Principles
- Development of processes that will support staff and department evaluation and growth
- Managers must ensure that all work is completed in accordance with requirements including but not limited to CFR’s, cGMPs, SOPs, Amgen policies and department performance standards
- Ability to cover shift work as needed
- Master’s degree and 3 years of Manufacturing & Operations experience OR
- Bachelor’s degree and 5 years of Manufacturing & Operations experience OR
- Associate’s degree and 10 years of Manufacturing & Operations experience OR
- High school diploma / GED and 12 years of Manufacturing & Operations experience AND Previous managerial experience directly managing people and/or experience leading teams, projects, programs or directing the allocation of resources
- Demonstrated ability to work under minimal direction
- Able to adapt to changing business needs and operational requirements
- Knowledge of applicable regulatory requirements
- Ability to resolve issues and influence across support organizations
- Ability to pull together and interpret a large amount of data
82
Manager Manufacturing Resume Examples & Samples
- Motivate and lead the team towards consistently high performance
- Manage operations ensuring consistent output and with continuous improvement toward key department metrics
- Partner with your peers (Operations, Engineering, Equipment, R&D) to achieve overall fab results as planned
- Manage performance and development of a production supervisor team
- Manage and direct the LED chips training department
- Assure operators are trained and process requirements are being followed, in a supportive and collaborative environment
- Foster teamwork and high morale while achieving results
- Work with engineering staff to control and improve production yields
- Work with equipment engineering to provide highest possible uptime
- Assist in planning staffing requirements in support of business objectives
- Responsible for controlling and reducing costs, and improving productivity of both labor and capital equipment
- Support R&D as a customer for product/process development
- Ensure consumable and raw material inventory availability within budgeted levels
- Reduce cycle times
- Proactively ensure Quality System compliance
- BS Engineering or equivalent technical degree
- Semiconductor manufacturing management experience preferred
83
Manager, Manufacturing Technology Transfer Resume Examples & Samples
- Implementing key processes to enable technology transfer to new manufacturing sites
- Partnering with engineering to provide process inputs for process fit assessments within existing manufacturing facilities and to define process requirements for new manufacturing facilities
- Maintaining scientific and technical support of commercial manufacturing at partners to support corporate goals for supply strategies, productivity, quality, and compliance
- Utilizing external networks to identify resources and build partnerships in manufacturing supply
- Partnership with internal and external partners to create and continually optimize communication and escalation of program issues both within Takeda and with external manufacturing partner
- Utilizing external networks to identify resources and build partnerships in the areas of engineering and process equipment technologies to drive best in class manufacturing operations
- Providing technical operations ownership for Vaccine Business Unit (VBU) Quality Systems interactions with Drug Product manufacturing processes at Takeda’s internal and external manufacturing partners
- MS or PhD and a minimum of 7 years experience, or BS with a minimum of 10 years experience in start-up, tech transfer, and/or sustaining cGMP for commercial sterile process operations in vaccines or biopharmaceuticals
- Demonstrated expertise in process transfer for drug product operations, including formulation/filling, lyophilization and/or visual inspection, experience in single use technologies, and the ability to manage vaccine-specific nuances and strategies
- The Manager should be a self-starter and team player who can balance the needs of an entrepreneurial environment with the requirements of structured product development
- Direct interaction / experience with regulatory agencies during inspections for licensing of commercial manufacturing operations is highly desirable
- Proven ability to work with efficiency across multiple project teams and business functions in a matrix environment. Able to lead and manage technical teams, serve as a partner and influence others. Previous experience with direct reports is highly desirable
84
Engineering Manager, Manufacturing Resume Examples & Samples
- Plans, manages, and performs the activities of a professional staff of engineers that is responsible for
- Providing engineering support to the production area to maintain optimum levels of productivity in terms of cycle times and quality
- Coordinating the introduction of new assembly processes on to the production floor by preparing operation sheets that describe specific production tasks
- Partnering with design engineers throughout the design process from concept to prototype in order to ensure that maximum production efficiency is achieved
- Contributing to the preparation of the annual capital expenditure plan for the selection and purchase of new production equipment
- Developing facilities layouts and providing these to the Facilities Department to support the installation of new equipment
- Researching to estimate the cost of new equipment and develops options
- Developing manufacturing plans and makes presentations to customers
- Ensure that staff members monitor Cost Performance Input (CPI) and take appropriate action
- Acting as a technical consultant to vendors to help them resolve manufacturing problems with regard to the parts they are producing for Telephonics
- Planning and assigning work to subordinates to balance workloads based on project priorities and staff competencies to ensure its timely completion and a high quality outcome
- Reviewing and checking work to ensure quality
- Reviewing options for resolving production problems or improving production efficiency with staff members
- Developing or implementing improvements to operating policies and procedures
- Ensuring that all staff members are properly trained to handle work assignments
- Planning staff training and development activities
- Evaluating the performance of staff members in formal review. Managing performance disciplinary problems that may arise. Coaching and counseling staff members to improve their performance on the job
- Hiring new staff members to fill open positions. Ensuring that new employees are properly oriented
- Providing input to the preparation of an operating budget annually by evaluating the capabilities and condition of existing production equipment and projecting future needs based on technological trends and market place demands
- Supervises cross-functional project team members in order to meet project objectives, which involves
- Developing and implementing project plans
- Establishing measurable milestones through multiple levels and coordinating work with other functional departments and divisions to ensure that project objectives are met
- Scheduling meetings with various project team members on a regular basis to discuss and resolve problems and to seek better solutions
- Initiating corrective actions as required and reporting to management
- Manages special projects, i.e. lean manufacturing, to improve the production efficiency of the Company
- Develops labor estimates for proposals being prepared for customers
- Calculates and estimates through-put metrics and production capabilities
- Responds to audits of production processes requested by customers
- Makes presentations to the customer
- Attends meetings on military contracts
- Handles production readiness reviews
- Coordinates internal audits with quality assurance organizations, e.g. Underwriter Laboratories
- Troubleshoots technical problems with the departmental computer systems to ensure maximum departmental efficiency
85
Manager, Manufacturing Resume Examples & Samples
- 3-5 Years of experience in and FAA repair station environment
- 2 Years min in a supervisory position
- Proficiency with FAA regulations
- Experience with Repair and overhaul requirements
86
Manager Manufacturing / Continous Improvement Resume Examples & Samples
- Minimum of 10 years of manufacturing experience or operations experience
- No relocation is being offered for this position. Only candidates residing within a 50 mile radius of Syracuse, NY will be considered
- Experience with VAVE and New Product Development
- Documented experience using Lean and Six Sigma tools and experience
87
Manager Manufacturing Resume Examples & Samples
- Provide leadership for Team Leaders to full achieve each of the Zoetis Core Beliefs and Department Objectives
- Manage and own shop floor performance, including leadership and/or participation in Gemba walks, shift changes etc
- Identify, Prioritize and Drive Continuous Improvement initiatives to ensure targets are met
- Ensure effective utilization of the GMP process for all direct reports, including annual objectives, individual development plans, one-on-one meetings, mid-year reviews, and year-end reviews. Continuously improve the capabilities of the team. Manage all colleagues making sure the right colleagues are in the right roles for success
- Continuously develop direct reports to build a strong team and site. This includes the use of performance management tools, direst feedback, and open communication
- Perform safety related M1 investigations, including initial event summary to site leadership
- Ensure direct reports are compliant with all training requirements
- Perform Human Performance Evaluation as applicable
- Effective and timely management of employee relations in accordance with company policies and procedures
- Participate and/or lead special projects as directed by Site Leadership
- Respond to process and/or equipment events by ensuring communication with process specialist, quality, regulatory, EHS, finance and OE specialist(s) as necessary
- Compliance and execution of EHS-regulations (of Zoetis, US). Compliance and execution of standards and instructions of company rulings, manufacturing specifications and SOPs
- Responsible for completion of Manufacturing Batch Record Review and other application department documentation
- Department Specific Responsibilities as indicated
- Manage budget and expenses for departments to meet company financial expectations
- BA/BS with 9-13years of experience OR MBA/MS with 7-11 years of experience. Bachelor’s degree in Business Management, Microbiology, Biology, Engineering, or other scientific discipline or equivalent
- Demonstrated commitment to the Zoetis Core Beliefs and leadership competencies
- Demonstrated ability to effectively lead, develop and motivate teams
- Demonstrated ability to interact positively with all process team colleagues including senior leadership
- Demonstrated ability to achieve results
- Strong communication (oral and written), interpersonal, and team/group interactive and leading skills. Strong commitment to product quality, customer service, and continuous improvement
- Thorough knowledge of 9CFR and EU regulations, Good Manufacturing Practices (GMPs), and Good Laboratory Practices (GLPs)
88
Manager, Manufacturing Administration Resume Examples & Samples
- Analyze Parts Depots Network/Logistics for planning and operational needs to further optimize order fulfilment and cost
- Facilitate & Support KAC & Kltd Management meetings
- Support management & staff in establishing, tracking and reporting SQDC metrics at Manufacturing locations
- Assist in review of Contracts & Capex decisions in order to standardize current business practices
- 5 Lead projects to automate/improve Manufacturing processes by collaborating with Information Technology and Accounting organizations
- BS in Engineering or Business Administration or Supply Chain Management or related field from a top ranked University
- 5 - 10 years of total experience - preferably in manufacturing or engineering or operations role with an engineered goods manufacturer
- Demonstrates adequate knowledge of production/assembly/procurement/engineering and service-parts operational principles, concepts, industry practices, and standards
- Demonstrates excellent verbal, written and interpersonal communication skills
- Demonstrates strong MS Office (Excel, PowerPoint), Analytics/Statistics, Programming and Project Management skills. Knowledge of ERP systems preferred
89
Associate Manager Manufacturing Packaging Resume Examples & Samples
- Execute production to meet department output goals and targets
- Support the release process and cycle time targets
- Responsible for daily operation on the production floor, including scheduling, staffing, training, and troubleshooting to ensure that all operations are in full compliance with applicable BPRs, SOPs, safety guidelines, and BU contract
- Issue discrepancies and work with cross-functional departments to close the discrepancies and implement appropriate corrective actions
- Analyze/assess the potential quality or business impact and escalate appropriately
- Identify and execute on continuous improvement opportunities and mid-size projects to support reduction of cost of goods produced
- Identify technical issues, assist in analysis, and implement solutions
- Ensure all equipment is operational and properly maintained, maintain cGMP compliance of process facility and equipment, and provide support for Validation activities
- Provide effective leadership including: individual goal setting/performance reviews; training and coaching employees; ensure appropriate staffing levels are met, effectively manage employee performance issues and corrective actions; recognize and appreciate employee contributions, supporting workforce diversity, quality and safety; and all other activities/functions which support achievement of individual/department/business objectives
- Maintain the area in a continuous state of compliance and inspection-ready
- BS with 6+ Years of industry experience; or
- MS or PhD with no prior industry experience; or
- Equivalent combination of education and experience
- 5+ Years of experience leading people
- Position requires flexibility and adaptability
- Working hours / days may shift due to business reasons and include work on weekends, off-shifts, overtime, and holidays
- Demonstrates appropriate level of adaptability, maintains positive outlook, and demonstrates composure under pressure
- Establishes open, candid, and trusting relationships, demonstrates integrity by standing by decisions
- Effectively employ all methods of communication (oral, written, presentation) to provide ongoing communication to employees
- Ability to effectively prepare written reports, investigations, etc
- Demonstrates a bias for action, fully delivers on commitments by holding self and others accountable for actions
- Recognizes the strengths and development needs of others, provides formal and informal feedback, and creates development opportunities for direct reports
- Possesses a thorough knowledge of the theory and principles of the operations being conducted – be able to be called upon as a subject matter expert and able to troubleshoot problems and take corrective action
- Acts as a mentor and provides leadership for direct reports
- Ability to follow written standard operating procedures, good manufacturing practices, safety regulations, and corporate policies
- Must be able to work in an independent manner
- Knowledge of business systems such as SAP, LMS, Dev@com (DR/CAPA System), etc
- Provide direction to direct reports towards achieving department goals and objectives
- Enforce systems and practices to assure compliance with state-of-the-art standards, cGMP regulations (domestic and international) and corporate requirements
90
Manager, Manufacturing Processes & Systems Resume Examples & Samples
- The candidate will be qualified to at least graduate level in Manufacturing, Biochemistry, Life Sciences or a relevant discipline
- Must have sufficient technical and management experience (8+ years) in a manufacturing operation, preferably within healthcare or related GMP industries
- Experience with SAP PTM business processes or system configuration is essential
- Must demonstrate an ability to work effectively in a matrix environment where some functions are shared, and communicate effectively with internal and external customers and stakeholders
- Familiarity with Lean Methodology is preferred
- Experience with project management, or implementation of business systems is essential
- Able to work with a team to identify and solve complex problems
- Able to execute one on one and group training in business system use
- Intermediate skills in applications such as PowerPoint, Excel, Word, etc
- Demonstrated ability to work effectively with cross functional teams
- Able to be flexible and adapt to different work groups, work styles, and work environments
- Strong verbal and written communication and presentation skills, including presenting to large groups
- Proven influence and collaboration skills and ability to effectively interact with management to identify, develop, and implement process improvements
91
Account Manager, Manufacturing, St Paul Resume Examples & Samples
- Demonstrate appropriate knowledge of the customers’ products and services to formulate business strategies to drive revenue
- Develop and implement account penetration strategies to include regular business reviews for key customers to maximize sales
- Demonstrate full compliance to company sales and pricing guidelines
92
IT Service Manager, Manufacturing Solutions Resume Examples & Samples
- At least five years of experience from core Service Management process execution
- Bachelor degree or higher in relevant field (Engineering, Information Sciences etc.)
- Solid IT process knowledge with good ITIL understanding
- Vendor management experience in multi-vendor environments
- Excellent collaboration and negotiation skills
- Experience in working in a cross-cultural environment with numerous stakeholders
- Interest in supply chain management, especially the manufacturing domain
- Leadership experience is considered as a strong plus
93
Manager, Manufacturing Maintenance Resume Examples & Samples
- Support the factory analysis for capacity, footprint, material flow, PFEP (plan for every part), labor cost/roll up, model line-up feasibility, make vs. buy studies and equipment/tooling scheduling and CAPEX approval. (5%)
- Drive safety, quality, and productivity of the department and factory through effective leadership (25%)
- Responsible for the day-to-day plant operations of the building and equipment including interactions and accountability for safety with outside contractors. (25%)
- Provide leadership to develop departmental strategy to prepare Maintenance and Facilities organizations for the future. (10%)
- Responsible for development and forecast of Departmental Budgets. (5%)
- Develop training plans to ensure that team is up to date and current with technological advances and equipment. (5%)
- Develop and execute requirements of the PM Pillar (Professional Maintenance) including Predictive Maintenance and Reliability. (10%)
- Responsible for Department key performance indicators. (15%)
94
Manager, Manufacturing nd Shift Resume Examples & Samples
- Develop and foster a strong Company and Union partnership
- Operate in accordance with Corporate, Operations, and Division policies and practices and in compliance with accepted business ethics
- Ensure thorough familiarity with policies and procedures relating to Standards of Business
- Responsible for managing all resources related to a cell or group of cells including personnel, equipment, materials, and budget
- Interprets and implements production and human resources related policies, procedures, and safety standards
- Organizes, plans, and guides the work load of the assigned area and carries production plans to completion, emphasizing safety, quality, schedule, cost performance and productivity
- Provides leadership, education, training, guidance, and technical assistance to assigned personnel
- Responsible for performance management of direct reports; performance reviews, development plans and mentoring
- Assists with quality improvement methods by participating in the resolution of production and technical issues
- Represents Rockwell Collins to customers in internal tours or visits
- Champions Lean Transformation activities within assigned areas
- Provide technical assistance to sub-assembly and top-level testing
- Assist in analyzing test failures and communicate with key technical resources
- Collaborating with Test Technicians to setup necessary training on new products and test systems
- Responsible for assisting with test procedures and processes to optimize test effectiveness and efficiency
- Assist Manufacturing Management in determining appropriate test staffing and skill levels
- Support Lean/Six Sigma initiatives
95
Manager, Manufacturing Services Resume Examples & Samples
- Lead and direct activities and technicians to carry out cGMP manufacturing activities including parts washing, preparation, autoclave and depyrogenation operations, product kitting and packaging, as well as facility cleaning
- Build a critical team of individuals to ensure complex projects are executed
- Ensure all technicians are fully trained to complete their job duties
- Participate in all aspects of personnel management (interviewing, training, coaching and developing)
- Work with project team, scheduler, and manufacturing technicians to ensure all activities are executed
- Clean and sanitize manufacturing equipment and production areas
- Maintain stocking and inventory management of cleanroom supplies
- Periodically perform safety inspections or observations. Ensure that a safe work environment is maintained at all times
- Work with small parts and perform a wide range of repetitive motions
- Degree / Diploma in life sciences or engineering discipline or equivalent experience required
- Minimum 4 years supervisor experience in pharmaceutical manufacturing, medical device or related industry
- First shift position, supporting 2nd and 3rd shift teams
- Must be able to occasionally work evening or night shifts as required
- Will supervise a 3rd shift supervisor
- Strong influencing and leadership skills
- Self-motivated, resourceful, flexible, and responsible with follow-through and conflict-resolution skills
- Knowledge and experience with complex scheduling and tight deadlines
- Knowledge of aseptic manufacturing techniques
- Results oriented and possess the ability to work independently, as well as within a team environment and maintain positive, productive relationships with others
- Experience in training manufacturing technicians, coaching and providing feedback
- Proficiency using MS Word, Excel, Outlook is required
- 4+ years’ GMP experience in pharmaceutical manufacturing or related industry