Manufacturing Operations Resume Samples
4.5
(110 votes) for
Manufacturing Operations Resume Samples
The Guide To Resume Tailoring
Guide the recruiter to the conclusion that you are the best candidate for the manufacturing operations job. It’s actually very simple. Tailor your resume by picking relevant responsibilities from the examples below and then add your accomplishments. This way, you can position yourself in the best way to get hired.
Craft your perfect resume by picking job responsibilities written by professional recruiters
Pick from the thousands of curated job responsibilities used by the leading companies
Tailor your resume & cover letter with wording that best fits for each job you apply
Resume Builder
Create a Resume in Minutes with Professional Resume Templates
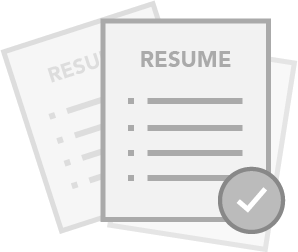
CHOOSE THE BEST TEMPLATE
- Choose from 15 Leading Templates. No need to think about design details.
USE PRE-WRITTEN BULLET POINTS
- Select from thousands of pre-written bullet points.
SAVE YOUR DOCUMENTS IN PDF FILES
- Instantly download in PDF format or share a custom link.
FH
F Harris
Freida
Harris
494 Ondricka Springs
Chicago
IL
+1 (555) 922 8057
494 Ondricka Springs
Chicago
IL
Phone
p
+1 (555) 922 8057
Experience
Experience
Philadelphia, PA
Manufacturing Operations
Philadelphia, PA
Russel and Sons
Philadelphia, PA
Manufacturing Operations
- Working closely with operations managers on improvement projects
- Utilize latest Maintenance Management measurements to develop maintenance activities to improve OEE
- Assist in the development and enhancement of Standard Operation Procedures and Conditions
- Working with stakeholders in plant operations to ensure facility efficiency and workplace safety
- Track productivity, quality and cost improvements associated with the application on automation projects and Maintenance improvements
- Provide input on process improvements
- Capacity and manpower planning, ergonomics analysis, method development, standardization of work, and material flow analysis objectives
Detroit, MI
Manufacturing Operations Supervisor
Detroit, MI
Hilpert, Okuneva and Schamberger
Detroit, MI
Manufacturing Operations Supervisor
- Drives personnel and team performance management including performance connections, acceleration of development action plans and succession planning
- Supervises the development and implementation of improvements and/or solutions to work processes and tools in support of business and strategic plans
- Provides regular feedback on performance to the manufacturing operators and also regular discussions on career development
- Perform other duties as described under the leadership of the production manager/factory manager
- Monitors daily progress/status and makes adjustments/corrections to ensure optimal performance and service
- Safety, manufacturing quality, on-time shipping, production management, labor relations, operations personnel training and development effectiveness
- Create and maintain a positive labor relations environment by engaging your teams in improvements and problem solving
present
Boston, MA
Director, Manufacturing Operations
Boston, MA
Smitham-Schimmel
present
Boston, MA
Director, Manufacturing Operations
present
- Ensures attainment of production and activities on a daily, monthly, quarterly, and yearly basis
- Oversees the quality and production level for the factory
- Responsible for weekly, monthly, and quarterly reports and presentations on activities, issues, and recommendations to executives
- Manages the hiring, staffing, and maintenance of a diverse and effective remote workforce including ongoing career development and performance management of the team
- Assures subordinate managers and employees complete individual goals and objectives and complete an annual appraisal of performance
- Determines and executes administrative policies through subordinate Managers
- Ensures the optimal operation of departments within the organization, such as Production, Materials, Engineering, and Maintenance
Education
Education
Bachelor’s Degree in Engineering
Bachelor’s Degree in Engineering
Liberty University
Bachelor’s Degree in Engineering
Skills
Skills
- Work closely with supplier quality, operations front line leaders, and on-site quality department to align high quality manufacturing and supplier processes
- Champions of built-in-quality and supplier quality playbook
- Providing leadership for employees to achieve department metrics for safety, quality, delivery, cost, people, and sustainability
- Leadership of problem solving and issue resolution as it relates to quality metrics in manufacturing to achieve Plant Quality metrics (FPY, CPH, NCM, PPM, FVA)
- Drive for results in a relentless pursuit of Voice of Customer (VOC) Quality in the midst of other objectives
- Ensuring overall product and process capability
- Demonstrated knowledge and experience utilizing technical problem-solving concepts and techniques
- Ability to provide clear and concise feedback to others
- 1st line of defense for quality issue containment; verify parts to print, processes in control
- Aseptic Operations knowledge
15 Manufacturing Operations resume templates
Read our complete resume writing guides
1
VP, Manufacturing Operations Resume Examples & Samples
- Oversees Pre-Press Services: Repurposed Materials team, ensuring work is distributed evenly to internal and external overflow resources to minimize peaks and troughs
- Oversees Archiving Services department, ensuring work is distributed evenly. Liaises with international Rights to assess future plans and plan fulfillment capacity accordingly. Works with Finance on developing new processes to capture Licensed Reprint and Licensed Order information affecting royalty calculations. Oversees the collection of, and communication about assets available to Digital Publishing, from which they develop their archival publishing plan
- Oversees Tech Ops, ensuring all current print and digital publishing assets are archived in a timely fashion. Liaises with Business Development to help assess and plan for sufficient fulfillment capacity, including future storage and cataloguing of foreign digital editions
- With Archiving Services and Tech Ops, will oversee the processing and transfer of the company archives to a new repository, upgrading the method of file storage, file transfer and order fulfillment. Plays a key role in defining the requirements of the new customer portal to alleviate many manual steps in order fulfillment, while ensuring the appropriate level of security and approvals are maintained
- Oversees Digital Production, ensuring work is distributed evenly to internal and external resources to support current and new distribution channels as necessary. Tracks quality and productivity goals. Work with in house and external lettering resources to streamline process, ensuring requirements are met
- Work with Manufacturing department management, other key internal departments and outside vendors to assess new technologies and vendor workflows. Plans for new systems and software upgrades; writes new workflows and oversees the training of department personnel
- Works with other Manufacturing management and WB Business Continuity to develop a Manufacturing business interruption plan
2
Manager Manufacturing Operations Resume Examples & Samples
- Determine staffing requirements
- Hire and train new staff
- Supervise direct reporting staff according to Lux Characteristics
- Set employee goals and objectives
- Develop staff to maximize potential
- Evaluate current business processes and systems
- Plan and implement procedures and systems to continuously improve operations
- Establish and maintain controls
- Formulate department/unit policies and practices
- Co-ordinate financial and budget activities for maximum operational efficiency
- Facilitate the preparation and analysis of reports
- Organize and manage business meetings
- 6-9 years of experience in related field
- Supervisory experience preferred, but not required
- Knowledge of business and management principles and practices
- Knowledge of strategic planning
- Knowledge of human resource management principles and procedures
- Proficient in relevant software applications
3
IT Manufacturing Operations Specialist Resume Examples & Samples
- Operative responsibility in problem management (incident management, problem management) on the production floor
- Create and maintain Technology Architecture documentation for transparency
- Create and Maintain Work Instructions
- Assess and Manage System Requirements and Production program fulfillment
- Work with the Production and planning department to determine, the current level of performance expected and risk with current process and systems. Create with the business area requirements plans for continuous improvement of the process and system
- Identify Automated Solutions which support business process maturity or improvement
- 3-7 years of professional work experience in related field
- Education - Management Information Systems or related discipline preferred
- Technical equipment (IBM Power Systems, Tivoli SAN & Tape Library)
- Unix (AIX), Linux, Windows
- Database Administration (DB2)
- Nights and Weekends Required
- Day to Day working relationship with the IT and Production community
- Day to Day working relationship with key Volkswagen business units and technology users
- Websphere, ITIL Process (Change/Problem Mgmt)
4
Manager Manufacturing Operations, Teavana Resume Examples & Samples
- Identifies and communicates key responsibilities and practices to ensure the immediate team of direct reports promotes a successful attitude, confidence in leadership, and teamwork to achieve business results
- Supports supervisors, leads and partners in their efforts to improve productivity, communications and morale
- Supports the implementation of company programs to ensure the success of the Company
- Adheres to established budget, cost objectives and service requirements to control expenses. Monitors and controls supply, material and labor costs. Ensures that costs contributing to finished cost of goods are within established goals
- Ensures compliance with Hazard Analysis and Critical Control Point (HACCP) and with American Institute of
- Developing and leading quality, customer service and cost improvement programs in a field or company environment 3 years
- Management 3 years
- Production planning and scheduling 3 years
- Managing budgets 1 year
- Food service or food company distribution center
- Manufacturing or related functions
- Ability to balance multiple priorities and meet deadlines
- Project management skills, including measurement, reporting and financial analysis
- Familiarity with American Institute of Baking (AIB), Good Manufacturing Practices (GMP), and Hazard Analysis and Safe Quality Food Institute
- Critical Control Points (HACCP) standard
5
External Manufacturing Operations Lead Resume Examples & Samples
- BS in chemical or biochemical engineering or related field with minimum twelve (12) years of relevant experience in biotech/biopharmaceutical industry. MS in chemical or biochemical engineering or related field with ten (10) years of relevant experience in pharmaceutical/biopharmaceutical industry
- Proficient in cGMP regulations, aseptic processing of medicinal products, and regulatory (FDA, EMEA) guidelines
- Background in manufacturing process development and equipment design for drug substance and drug product is desirable
- Management/leadership experience in Operations &/or manufacturing in the pharmaceutical/biopharmaceutical field is required
- Experience in authoring/reviewing regulatory submissions is preferred
- Experience in managing projects involving CMOs required
- Strong communication, presentation and analytical skills required
6
Manager, Manufacturing Operations Management Resume Examples & Samples
- Manages manufacturing operations: budgets, build status, input/output management, site performance reporting
- Through a combination of physical presence and remote collaboration tools, manages the Oculus China operations management team
- Establishes team objectives and work plans, delegates assignments to operation managers
- Participates in developing, modifying and executing Oculus policies that affect immediate operations
- Directs the development and implementation of activities in production sites to meet quality, delivery and cost objectives
- Responsible for product ramp-up and mass production operations
- Support the timely and orderly transition from new product introduction development stages into ramp and mass production
- Organize and conduct weekly and monthly operational reviews of contract manufacturer and key sub-supplier partners, and contribute to their quarterly business reviews in coordination with other supply chain and hardware engineering teams
7
Manufacturing Operations Senior Manager Resume Examples & Samples
- Prepares the manufacturing team to execute strategic company objectives. Leads initiative to ensure business growth and meet or exceed customer expectations through continuous improvement of manufacturing operations
- Adheres to established manufacturing and distribution processes and identifies continuous improvement opportunities to maintain inventory integrity
- Manages established budget and provides periodic budget reports to management. Monitors and controls expenses, equipment needs, partner and temporary staffing levels, overtime and throughput to attain annual budget improvement targets
- Manages manufacturing schedule to support improved productivity and reliability. Ensures manufacturing team meets or exceeds budget targets for limiting scrap and not-in-specification production
- Manufacturing or related functions (8 years)
- Ability to build an organization to support growth
- Problem-solving skills
8
Manufacturing Operations Lead Resume Examples & Samples
- Managing day to day operations ensuring functional area targets, objectives and performance criteria are understood and met
- Facilitate strategic planning of the manufacturing operations schedule
- Develop author and review production batch records
- Develop and author standard operating procedures and associated forms
- Develop /author user requirement specifications
- Execute manufacturing operations and batch execution under prescribed procedures and manage close out of associated documentation (batch records, log books, forms)
- Participate on project teams through all phases of projects; these phases will include equipment procurement, installation, start up, commissioning, validation, and qualification
- Integrate and collaborate with cross functional teams setting the operations expectations and driving execution
- Lead/participate in improvement projects, vendor enquiries and troubleshooting of process equipment
- Responsible for initiation and completion of deviations, CAPAs, and change controls for process systems
- Review and approve commissioning and qualification documentation as required
- Adhere to compliance, regulatory requirements, and cGMP
- Complies rigidly to processes that ensure intellectual property of the product/process is not compromised
- Support the technology transfer, demonstration batch and process validation project activities from documentation (protocols and reports) and execution perspective
- Support the generation of safety risk assessments and the implementation of site EHS policies
- Ensure safe operation of work is followed at all times and any safety risks identified are escalated / closed immediately
- Provide out-of-hours support during project as required
- Training, maintaining housekeeping, and 6S in all production areas while focusing on continuous process improvement using Lean Principles
- BSc in a science related discipline (Chemistry, Engineering, Biotechnology etc.) plus 5-8 years relevant experience in a cGMP commercial manufacturing environment
- Prior hands-on experience of operations functions within the pharmaceutical/biotech industry
- Prior experience in developing documentation protocols, reports, SOPs, batch records and management of deviations/CAPAs
- Experience in troubleshooting and providing technical support for cGMP manufacturing process equipment in a cGMP processing environment
- The individual in this position will be able to organize his/her own work on a routine basis and requires minimal supervision
- Experience in working in start-up desirable
- Proficient in working with Microsoft Office packages
- Good interpersonal and communication skills, verbal and written
- Thorough, diligent, good attention to detail
- Collaborator with strong levels of engagement with individuals and team
- High level of delivery and work completion
- Organised and effective in a support role to the Process lead
- High levels of integrity and trustworthiness
9
Manager Manufacturing Operations Resume Examples & Samples
- Apprises management of team progress toward departmental goals. Ensures effective and timely communication of company, plant and departmental information to managers, peers and own work team, including supervisors, leads and partners
- Ensures workplace safety and addresses safety issues promptly and completely
- Team-building skills
- Ability to form and develop effective leadership teams
- Ability to recommend and implement solutions
- Familiarity with American Institute of Baking (AIB), Good Manufacturing Practices (GMP), and Hazard Analysis and Critical Control Points (HACCP) standards
10
Manufacturing Operations Internship / Co-op Resume Examples & Samples
- Develop familiarity with and ability to analyze manufacturing and production processes by direct involvement and data analysis, failure analysis, root cause analysis
- Provide support to production and manufacturing by improving equipment uptime by troubleshooting, re-design (including automated systems)
- Identify bottlenecks in production and manufacturing systems and utilize data collected to propose, implement, and execute correction
- Support project schedules
- Organize and analyze data sets that outline the systemic improvement opportunities
- Manage projects involving multiple departments and/or outside contractors
- Identify areas for cost savings and develop corrective action plans
- Develop and implement system support process and documentation
- Read and interpret basic mechanical drawings and electrical schematics
11
Manufacturing Operations Supervisor Resume Examples & Samples
- Ensuring a safe working environment through modeling safe behaviors, leading audits/inspections, correcting unsafe behaviors, conducting safety meetings, and utilizing proper work methods, procedures and equipment
- Providing direct supervision to direct and indirect hourly maintenance mechanics and supporting team
- Handling shift administrative activities such as time/absence reporting, attendance control, vacation planning, overtime and etc
- Evaluating employees’ performance, provide feedback, identify training and growth opportunities for mechanics to improve team skills and operating level
- Driving continuous improvement in plant engineering work quality, safety, team skills and problem solving ability, customer satisfaction, on time performance, and effective control of spending
- Planning daily work schedules, determine priorities, allocate work assignments, and regulate production processes in order to meet specific daily maintenance requirements and react to time critical requirements
- Championing lean manufacturing efforts and projects
- Reports to Plant Engineering Manager with responsibility for maintenance teams at two operating sites in Irvine, CA
- High School diploma/GED or higher from an accredited institution
- Minimum of three (5) years of experience in a plant engineering/maintenance environment
- Minimum of one (1) combined year of supervisory and/or leadership experience
- Bachelor’s degree or higher in a science or engineering discipline from an accredited university
- Minimum three (3) years of supervisory experience in a plant engineering environment
- Experience leading cross functional teams
- Ability to create, lead and work in a team atmosphere
- Ability to drive and influence positive change
- Experience/expertise in electrical, hydraulic and/or mechanical systems a plus
12
Pepsico Manufacturing Operations Associate Resume Examples & Samples
- Demonstrate strong leadership skills to coach, develop, and influence various teams
- Use your analytical thinking skills through qualitative and quantitative analysis; demonstrating a strong drive to fix problems and design solutions
- Support various components and activities spanning the project management life cycle; such as business case analysis, detailed requirements, software design/testing/deployment, and issues management
- Learn PepsiCo's Operations framework through various placements in Production, Warehouse, Maintenance, Quality, and Fleet Operations
- Perform at fast pace, with self-motivation and strong initiative
- Be flexible - in order to understand our 24/7 operations, you may at times need to work various schedules; including early mornings, evenings and/or weekends
- Be completing their final year of undergraduate studies
- Hold a Bachelor's degree prior to the intended full time start date
- Be 21 years of age or older
- Pass a drug screen and background investigation
13
Pepsico Manufacturing Operations Intern Resume Examples & Samples
- Motivate operations team to achieve performance targets
- Support various components and activities spanning the project management life cycle; such as business case analysis, detailed requirements, software design/testing/deployment and issues management
- Gain understanding of various supply chain functions and disciplines
- Receive opportunities to build affiliation with associate peers and interact with senior leadership
- Assist in the analysis and development of supply chain metrics and business processes
- Report findings to other team members and management as required
- Work on large projects and manage time and effort without need for constant supervision
- Learn various statistical modeling and developing reporting tools
- Learn to manage production staff to attain production and quality goals
- Gain valuable insights between manufacturing & distribution/selling
- Assist in developing individuals and the team to solve operational issues
- Assist in organizing and facilitating team meetings to achieve continuous process improvement
- Graduate with Bachelor's degree within one (1) year of internship completion
- Be eligible to work in United States without work authorization sponsorship now or anytime in the future
14
Supervisor, Indirect Manufacturing Operations Resume Examples & Samples
- Studies production schedules and estimates worker hour requirements for completion of job assignment
- Suggests changes in working conditions and use of equipment to increase efficiency of the production department
- Manages two subordinate lead persons who monitor a total of 25 employees on the Production Shift
- Responsible for the overall direction, coordination, and evaluation of this shift
- Carries out supervisory responsibilities in accordance with the organization’s policies and applicable laws; responsibilities include interviewing and training employees; planning assigning, and directing work; appraising performance; rewarding and disciplining employees; addressing complaints and resolving problems
- Minimum 5 years combination of education and experience at least 2 years must have been in a Production environment
- Must possess a solid understanding of basic mechanical concepts. Experience with extrusion and/or molding desirable but not required
15
Head of Manufacturing Operations Resume Examples & Samples
- Complete, detailed ownership of all operational elements of out factories
- Define, evolve and execute a strategy that delivers world-class manufacturing capabilities to B8 and also tests new, unique, different and exciting manufacturing capabilities as required per project/product
- Hire a team of deeply experienced and highly capable experts who can unlock and unleash the capabilities of our manufacturing partners
- Set clear metrics providing real-time visibility to every node of manufacturing
- Hold partners accountable to the highest levels of quality at every level of the manufacturing process
- Partner with the Manufacturing Technology team to design, develop and evolve our test strategy
- Partner with the Manufacturing Technology team to execute new manufacturing technologies as required by project & by product
- Drive new ways of thinking and new methodologies in our factories to deliver high quality with urgency
- Build capacity ahead of our growth
- Drive excellence in cost execution in our manufacturing
16
Manufacturing Operations Analyst Resume Examples & Samples
- Build Positive Relationships - Consistently builds effective working relationships with other project leads, internal employees, and external customers. Probes for and provides information to clarify situations. Consistently seeks and expands on original ideas from other project leads, internal employees, and external customers, enhances others' ideas, and contributes own ideas about the issues at hand. Places higher priority on project and organization goals than on own goals. Guides others in gaining agreement from other project leads, managers, internal employees, and external customers to support ideas or take partnership-oriented action; uses sound rationale to explain value of actions. Establishes good interpersonal relationships by helping people feel valued, appreciated, and included in discussions
- Communication - Consistently clarifies purpose and importance; stresses major points; follows a logical sequence. Consistently keeps the audience thoroughly engaged through use of techniques such as analogies, illustrations, humor, an appealing style, body language, and voice inflection. Consistently frames even complex messages in line with audience experience, background, and expectations; uses terms, examples, and analogies that are meaningful to the audience. Consistently seeks input from audience; checks understanding; presents message in different ways to enhance understanding. Uses syntax, pace, volume, diction, and mechanics appropriate to the media being used; attends to both direct and indirect messages from others; correctly interprets messages and responds appropriately. Advises fellow project leads and other internal employees in effective communication techniques
- Cross Functional Partnerships - Analyzes the organization, potential external partners, and own area to identify key relationships that should be initiated or improved to further the attainment of own area's goals. Exchanges information with project leads, internal employees, and external customers to clarify partnership benefits and potential problems; collaboratively determines the scope and expectations of the partnership so that both areas' needs can be met. Collaboratively determines courses of action to realize mutual goals; facilitates agreement on each partner's responsibilities and needed support. Places higher priority on organization's goals than on own area's goals; anticipates effects of own area's actions and decisions on partners; influences others throughout the organization and in partner organizations to support partnership objectives. Implements effective means for monitoring and evaluating the partnership process and the attainment of mutual goals
- Customer/Supplier Knowledge - Extensive knowledge of customer's/supplier's organization, processes, policies and procedures, products, requirements, capabilities, practices, support resources, preferences, constraints, etc
- Project Leadership - Extensive and specialized ability to direct, delegate, and ensure performance of assigned responsibilities and tasks as a project team leader in support of the overall large scale and complex projects. Extensive and specialized ability to identify and resolve project related issues and provide solutions and/or recommendations to ensure the successful completion of the project
- Project Management - Extensive experience in creating comprehensive multi-tiered project schedules for significant Business Unit projects; identifies time frames for key project milestones and ensure alignment of sub tier activities for overall project visibility, tracking and completion. Directs and manages very complex project schedules requiring interfacing with multi regional or international activities. Independently identifies project resource requirements, integrate and direct multi project elements into a single collective overall project plan. Collaborates with others on the most complex projects assigned. Ability to direct, delegate and ensure performance of assigned responsibilities and tasks as a project team leader in support of the overall large scale and complex projects. Identifies and resolves any issues and provide solutions and or recommendations to ensure the successful completion of the project
- Schedule Management - Extensive and specialized knowledge of schedule management and Industrial Engineering principles and best practices highly desirable
- Problem Solving – Extensive experiences in problem solving utilizing standardized problem solving model to drive multi-functional team efforts for problem resolution is highly desirable
17
Manufacturing Operations Program Manager Resume Examples & Samples
- Experience in program management
- Experience in collaborating with employees within a department and across functions
- Fluent with MS Office products - PowerPoint, Project, Excel, Word
- Experience with ERP system in a manufacturing environment
- U.S. citizenship is required
- Experience with SAP in a low volume, high mix manufacturing environment
- Bachelor's degree in Engineering or Management
18
Manufacturing Operations Program Manager Resume Examples & Samples
- Bachelor's degree in a technical field
- Master's degree in Engineering or Management
- PMI certification
19
Manufacturing & Operations Intern Resume Examples & Samples
- Review overall equipment effectiveness in manufacturing location and identify improvements
- Utilize process mapping to develop Standard Operating Procedures for Customer Service and Purchasing departments
- Create appropriate documentation to support SOPs
- Data analysis, root-cause analysis, use of metrics
- Process development and process mapping
- Documentation
20
Manufacturing Operations Associates Resume Examples & Samples
- Weighs, measures and checks raw materials to ensure batches manufactured contain proper ingredients and quantities
- Posts weights and shipping charges, and prepares goods for final shipment
- Prepares goods for final shipment and unpacks and checks goods received against purchase orders and invoices, maintains records of received goods, rejecting unsatisfactory items if necessary
- Associate’s or Medical Technical degree or equivalent
- Ability to gown aseptically for work in a Clean Room environment
- Extensive use of laboratory equipment, chemicals and biological materials
- May be required to work alternate shifts
- Limited exposure to (2ºC - 8ºC); (-20ºC); (-75ºC); (-196ºC) areas
- Must have the ability to work around laboratories, manufacturing areas and equipment, and regularly lift 10 – 20 lbs and lift up to 50 lbs
- Must be able to work 3-days 12-hour overnight shifts
- Must have flexibility to work various shifts during training
21
Manager Manufacturing Operations Resume Examples & Samples
- Partner with Quality Assurance in implementing and maintaining the effectiveness of the quality system
- Assures compliance to all procedures and policies concerning all areas of quality, regulatory, safety and human resources
- Initiates and implements actions to maximize profits by containing expenses through improved operating and cost efficiencies. Develops, approves, and meets financial budgets, plans, and updates
- Assists in new product launches, production and engineering improvements, product testing, etc
- Assures timely and relevant communications to and from all levels. This includes assuring communications between affected reporting areas and to related departments. Responsible for establishing systems that would enhance intra- and inter-departmental communications
- Coaches, develops, and mentors direct staff. Conducts performance reviews; develops growth plans; interprets, implements and supports employee-related policies, procedures and programs. Assigns projects/tasks to direct staff. Responsible for recruitment, selection, development and retention of employees
- Develops strategic plans and objectives in accordance with overall Plant and Division strategy; execute business plans through functional reports while providing leadership, coaching and direction
- Knowledge of applicable regulatory standards and requirements for FDA regulated environment. 10+ years’ experience in a variety of roles in manufacturing to include significant experience in management/supervision
- This position is accountable for maintaining and complying with FDA, USDA, OSHA, MDEQ, MDA and Affirmative Action requirements. Noncompliance or failure to meet the above could result in failure to meet customers’ demands, thus affecting Ross business. Responsible for ensuring proper equipment/manpower utilization, good employee relations, a safe environment, quality products and observations/violations are given
22
Associate Director BDS Downstream Manufacturing Operations Resume Examples & Samples
- Recruit, retain and develop first class staff responsible for the manufacture and delivery of Alexion bulk drug substance at College Park Build and sustain employee engagement by creating a culture of efficient execution and an environment in which individuals and teams can excel and continuously improve
- Within the Downstream areas, ensure the manufacture of bulk drug substance is performed in a safe, compliant manner, meeting the regulatory requirements defined in relevant health authority submissions, cGMPs and local Health and Safety requirements
- Develop operations systems and processes such as gowning and scheduling, and assist with developing procedures, documentation and automation
- Manage an effective 24/7 shift operations team structure ensuring communications and human factors are optimized. Maximize the utilization of internal manufacturing capabilities to insure cost-effective, compliant and on-time supply of products
- A minimum of 10 years’ experience in Manufacturing Operations in a biopharmaceutical company
- Excellent people management, communications and decision-making skills
- Experience of leading operational excellence improvements is desirable
23
Associate Director BDS Upstream Manufacturing Operations Resume Examples & Samples
- Within the Upstream areas, ensure the manufacture of bulk drug substance is performed in a safe, compliant manner, meeting the regulatory requirements defined in relevant health authority submissions, cGMPs and local Health and Safety requirements
- During the start up project ensure there is appropriate user requirements input into design, commissioning and validation of equipment and processes as part of the multi-function project team
- Member of the BDS Leadership Team. Contribute to the BDS operating performance and utilization of resources, planned launches of new products, and need for continuous improvement of product flows to optimize the speed and efficiency of the supply chain while increasing robustness and decreasing costs
- Demonstrated leadership of technical and operational teams within a biopharmaceutical operations organization
- Experience of biological manufacturing processes
- Experience of capacity expansion and new product introduction project work is essential and experience of a green field start-up is desirable
24
Manufacturing Operations Resume Examples & Samples
- Development and monitoring of metrics
- Provide education on concepts
- Drive projects for improvement
- Provide a leadership role in the area of C4I and process improvements for the process team
- Projects as generated by Process Team and CAPA
- Investigate problems, conduct root cause analysis and implement countermeasures
- Potential to back up Leader and Team Leader
- Lead specific functions of the process team
- Lead by example in using data to influence change and improvement
- Ensure that all safety practices, policies, and rules are followed and enforced
- Complete safety audits Be an active participant in safety improvements and reduction of incidents
- Bachelor’s Degree-Science or Technical
- Minimum of 3 years of Pharmaceutical Experience
- 2 to 5 years Parenteral Operations experience or support
- Aseptic Operations knowledge
- Technical or science degree preferred
- Previous leadership/supervisory experience helpful
- Career interests in operations leadership
25
Manager, Manufacturing Operations Resume Examples & Samples
- Ensure plant compliance with company policies and government regulations
- Implement continuous improvement for increased productivity and cost reduction initiatives to minimize plant and labor expenditures and conduct on-going evaluations/improvements of methods and systems
- Conduct weekly process confirmation audits. Attend huddle meetings weekly and conduct monthly skip level meetings
- Assist and take the lead on preparing for the monthly and quarterly business reviews
- Proactively work with the SLT to develop and maintain a prioritized project hopper with resource loading for the top 25 projects
- Direct work priorities and allocate resources to assure overall goals, objectives and time-lines are met while complying with company policies/procedures and all regulatory requirements
- Participate in employee development, through coaching, mentoring, and professional development. Ensure that the annual performance review process is completed in an accurate and timely manner
- Prepare and review department budgets and lead cost and efficiency improvement efforts across Operations
- Partner with other plant leaders and collaborate to find the best possible solution and best practices
- Deliver Site Performance Objectives
26
Manufacturing Operations Specialist Resume Examples & Samples
- Proficient in all MS Office applications and database usage
- Bachelor's degree in Electrical, Manufacturing or Mechanical Engineering
- Strong background in WCM manufacturing system
27
Manufacturing Operations Supervisor Resume Examples & Samples
- Positive Attitude, Ethics and International Values which support our company’s values, and a healthy, high performance culture
- Demonstrated understanding in the compliance of Company Safety and Environmental policies
- Experience in supervising employees in a represented manufacturing environment
- Knowledge of the truck assembly process
- Working knowledge of basic Microsoft programs, such as Excel, Word and Outlook
- Ability to use logic and methods to analyze problems and make effective decisions
- Bachelor’s degree in Engineering or Business preferred
28
Director, Manufacturing Operations Resume Examples & Samples
- Ensures attainment of production and activities on a daily, monthly, quarterly, and yearly basis
- Oversees the quality and production level for the factory
- Responsible for weekly, monthly, and quarterly reports and presentations on activities, issues, and recommendations to executives
- Manages the hiring, staffing, and maintenance of a diverse and effective remote workforce including ongoing career development and performance management of the team
- Responsible for collaborating with cross functional organizations in procurement, global production planning, and demand/supply planning to ensure customer requirements will be met from a production and fulfillment perspective
29
Manufacturing Operations Director Resume Examples & Samples
- A minimum of a Bachelor’s degree with at least 10 years of manufacturing experience, OR an MS/MBA/Ph.D. degree with a minimum of 9 years of manufacturing experience is required
- A minimum of 5 years of experience leading or managing a team/direct reports in a matrixed environment is required
- Proven performance track record in the pharmaceutical, medical device, consumer, food or cosmetic or semi-conductor industry
- Experience working in a GMP Manufacturing or FDA regulated environment is required
- Experience managing business planning process and budgets is required
- Biologics Manufacturing industry experience is highly desired
- Create innovative technical and business solutions where none exist or need revision, to realize company objectives aligned with business plan
- Six Sigma Green Belt and/or Six Sigma Black Belt are preferred
- Experience working with safety regulations is preferred.Production
30
Director of Manufacturing Operations Resume Examples & Samples
- Serves as member of the senior Viqua leadership team
- Manages the Operations budget
- Participates in formulating and administering company policies and developing long range goals and objectives
- Directs and coordinates activities of department or division for which responsibility is delegated to ensure achievement of targets, goals and objectives
- Collaborates with other members of the management team to formulate objectives, implement countermeasures when required and drive continuous improvement throughout the organization
- Provides development and coaching to manufacturing operations team members
- Is a DBS champion and promotes / applies Danaher Business System practices and tools throughout the company
- Collaborates with other Operations Team Leaders within other Trojan Operating companies to ensure strategies and plans are aligned and tightly executed
- Bachelor’s Degree in Engineering or related field from an accredited university. MBA and/or APICS CPIM Certification highly desirable
- Ability to motivate, inspire, lead and develop a multi-disciplinary team
- Extensive related operations/manufacturing experience. Min 3 years at a senior management level
- Experience with directing a formal MRP II, ISO 9001 certified manufacturing process
- Solid understanding of manufacturing techniques involved in metal fabrication, welding and assembly and ability to initiate and lead continuous improvement efforts
- Ability to read, analyze, and interpret common scientific and technical journals, financial reports, and legal documents. Ability to respond to common inquiries or complaints from customers, regulatory agencies, or members of the business community. Ability to effectively present information to top management, Trojan corporate management, and public groups as appropriate and requested
- Ability to define problems, collect data, establish facts, and draw valid conclusions Ability to interpret an extensive variety of technical instructions in mathematical or diagram form and deal with several abstract and concrete variables
- Proficient with Microsoft Word, Excel, Project and PowerPoint
31
Manufacturing Operations Supervisor Resume Examples & Samples
- Safety, manufacturing quality, on-time shipping, production management, labor relations, operations personnel training and development effectiveness
- Communicate business unit and product operations goals, objectives, priorities, and progress to employees and management
- Lead factory employees by training them to standard work and drive accountability
- Coordinate production assignments and other activities to ensure that we have flow through the process
- Develop and lead in a team-oriented environment
- Create and maintain a positive labor relations environment by engaging your teams in improvements and problem solving
- Must be a champion of safety and eliminate hazards and ensure employees are behaving safely
- Lead production teams to implement engineering changes, MDI/RIE activities, or other projects in the factory unit
- Identify problems and opportunities and implement solutions relating to quality, safety, productivity, and cost improvements
- Support MDI/RIE product and systems projects
- Document and provide training
- Identify and coordinate equipment maintenance and TPM
- Support development, documentation, and implementation of processes, procedures, and shop documentation
- Follow and comply with ISO and environmental policies and procedures
- Perform other duties as described under the leadership of the production manager/factory manager
- Plan production manpower, allocate resources, and gain the necessary support resources from outside the operations product group
- Monitor performance versus plan and take necessary action to meet plan
- Serve as the product line representative on the La Crosse operations and product OPEX team
- Bachelor's degree in business and/ or engineering or related discipline and minimum 5 years of experience in manufacturing and/or operations required OR an equivalent combination of education and work experience required
32
Senior Manufacturing & Operations Specialist Resume Examples & Samples
- Accurately document each phase of inspection, assembly, and shipment according to GMP and internal SOPs
- Maintain equipment calibration records and scheduling equipment calibration
- Monitor inventory and create purchase orders to replenish supplies
33
Manager Manufacturing Operations Resume Examples & Samples
- Manage filling operations by directing the production activities on a daily basis. Ensure scheduled activities are performed as planned
- Ensure GMP compliance and meets requirements of Patheon quality systems
- Ensure production efficiencies are monitored and action taken to lower variable standard costs
- Manage the administrative aspects of the group by ensuring the preparation of performance plans, job descriptions, and conducting employee performance reviews. This also includes hiring, rewarding, and disciplining staff as required; providing direction for professional development; maintaining an environment that fosters teamwork; and assigning responsibility and accountability at proper levels
- Prepare expense and headcount budgets. Ensure budget targets are met while providing production operations with adequate resources in facilities, equipment, and personnel to meet customer demands
- Support the company’s safety program to maximize safety awareness and provide a safe work environment
34
Manager, Manufacturing & Operations Resume Examples & Samples
- Responsible for representing Manufacturing in the build-out, commissioning and validation of the League Island 2 facilities
- Staffing and training of the assigned Manufacturing group to be competent in current Good Manufacturing Practices (cGMP)
- Responsible for management of daily operations of gene-mediated cell therapy manufacturing operations for the on-time completion of client products being manufactured
- Maintains production schedule to meet customer and business goals
- Provides accurate production forecasting methods with continuous improvement through capacity optimization and cost reduction programs
- Implements and maintains personnel policies, procedures and production control systems
- Ensures cGMP compliance, ensuring that all production equipment is properly validated and production processes meet quality standards
- Bachelor's degree in Biology, Chemistry, or related Science major required
- Minimum of 8 years supervisory experience and 10 years’ experience in biologics manufacturing is required
- Direct experience in cell therapy, gene therapy clinical manufacturing required
- Has a thorough understanding of cGMP requirements for clinical manufacturing
- Experienced in commercial manufacturing requirements for biological or cell or gene therapy products
- Meets physical requirements of the job, as follows: must have the ability to lift a minimum of 50 pounds, the ability to bend, reach, stretch, climb ladders and work in tight spaces in order to complete job tasks
- Must be able to wear appropriate clean room attire and have the ability to wear surgical masks and all Personal Protective Equipment (PPE)
35
Manufacturing Operations Coordinator Resume Examples & Samples
- Read and interpret assembly procedures
- Understand and utilize tools (hand tools, meters and computerized test equipment)
- Assure that all paperwork is properly completed
- Use care and professionalism in the handling of assemblies and sub-assemblies
- Observe all safety requirements in the assembly area
- Control all non-conforming components to prevent unintended use
36
Manufacturing Operations Supervisor Resume Examples & Samples
- Generally requires a Bachelor Degree with 9 years of related experience preferred or equivalent combination of education and experience
- 5-10 years experience in the manufacturing field. Cable assembly background highly desired
- Demonstrated effectiveness in managing internal customer relationships, prioritization, and delegation
- Experience with coaching, developing talent, and maintaining accountability of direct reports
- Must be able to work collaboratively with other functional departments
- Experience with a manufacturing execution system desirable, specifically Solumina
- Must be detail-oriented but able to understand the big picture
- US Citizenship is a requirement. Applicant selected may be subject to a security investigation and must meet eligibility requirements for access to classified information
37
Quality Manufacturing Operations Inspection Supervisor Resume Examples & Samples
- Excellent leadership, communication, problem solving, analytical, prioritization and multi-tasking skills
- Ability to work with all levels of management
- Working knowledge of continuous improvement principles (e.g. lean manufacturing, ACE, QCPC)
38
Technical Expert / Manufacturing Operations Resume Examples & Samples
- Collect and analyse data (i.e. validation, CPV/AMB, APR/PQR, product technical files, analytical and related testing monograph) eventually including statistical analysis
- Discuss and formalize (e.g. technical report) the outcome of the technical reviews (all data discussed and reviewed with ad hoc Technical Manager)
- Support maintenance of the knowledge and the history of the product process throughout the entire commercial lifecycle (i.e. maintenance of technical documentation such as Technical Files or product specific Quality Risk Analysis)
- Collect and review the technical content and scientific rational of CPV/AMB related documentation provided by the CMO (protocols/report, risk analysis)
- Track CPV/AMB parameters provided by the CMOs. Monitor all critical variables and key variables as appropriate for the assigned product(s) (Critical Process Parameters CPP, In Process Control IPC parameters, Quality Attributes, Characteristics of raw materials. etc) using statistical analysis and conducting regular product specific data trending
- Collect, consolidate and review data to support investigations/deviation processes
- Collect and review the technical content and scientific rational of Validation related documentation provided by the CMO or Novartis site (protocols/report, Quality Risk Assessment, validation master plan)
- Graduate in Chemistry, Pharmacy, Chemical Engineering or Pharmaceutical Technology
- Fluent English and German
- 5 to 10 years experience in Manufacturing/ Manufacturing Science and Technology/Technical Development/Quality in Pharmaceutical Industry
- Thorough understanding of manufacturing processes and related process equipment
- Strong working knowledge of quality systems and Pharma regulatory requirements across multiple health authorities
- Experience in executing process and cleaning validation
- Experience with validation of packaging processes (blistering, bottling, cartoning and hand packaging) of solid oral dosage forms, liquids and suppositories. This includes knowledge of various packaging material types (raw materials), IPC and release test methods for package integrity
- Expert in reviewing and writing technical reports
- Proven project management experience in a cross-functional environment (e.g. multi-site, technical development, other functions)
39
Value Stream Leader Manufacturing Operations Resume Examples & Samples
- Responsible for continuous improvement deployment within the value stream in order to be an innovator of positive change that favorably impacts profitability, inventory turns, on-time delivery, lead-time, and quality (effectiveness is measured primarily through value stream metric performance)
- Lead / manage production, production material control, and manufacturing engineering to achieve company goals
- Analyze problems, account for variances, drive for root-cause analysis / resolution, and implement improved methods & procedures in order to create, review, and update improvement plans
- Allocate the necessary resources to meet external and internal commitments while maintaining budgetary control
- Assure that appropriate equipment is provided, adequately maintained, and safely operated; this person may also evaluate the potential of new equipment and initiate capital equipment requests accordingly
- Assure that capacity levels are maintained to match demand in the short-term and long-term; this may involve participating in long-range planning and budget preparation
- Work closely with engineering, supply chain, process engineering, marketing, and other functional organizations as well as customers & suppliers to meet or exceed customer needs
- Plan, establish schedules, and assign work while considering requirements & priorities; this involves utilizing the most effective equipment and considering the skills of staff members to cost-effectively achieve objectives while concurrently implementing efforts to continuously improve performance
- Monitor activities & initiate actions to eliminate problems, ensure that employees are properly trained, and work is performed in accordance with health & safety requirements
- Provide guidance & training, and ensure fair & equitable treatment of staff; this involves managing / documenting employee performance and developing associated recommendations
- Additional duties may be assigned, as needed
- 2 years of professional experience in project management and/or manufacturing operations
- At least 6 months of professional experience with Continuous Improvement, Process Improvement, and/or Value-Stream Leadership in an industrial environment
- Broad experience working in industrial manufacturing environments; experience working in unionized environments is a plus
- Proven ability to create and manage a Value Stream plan
- Ability to prepare comprehensive reports, forecasts, estimates, and budgets with a high level of accuracy
- Knowledge and experience with Lean Manufacturing, Six Sigma, Kaizen, and/or other Continuous Improvement / Process Improvement methodologies
- Ability to work all shifts and periodic weekend work
- Ability to effectively organize several distinct functions, establish levels of responsibility, delegate appropriate authority and review the work and performance of subordinates in a manner conductive to efficient performance and high morale
- Strong communication skills (verbal & written) are necessary to work effectively with all levels of the organization as well as with customers and suppliers
40
Senior Director, Manufacturing Operations FJI Resume Examples & Samples
- Establish and improve mechanisms to ensure the operations team provides products and services to our Customers around the globe in a timely, cost effective and quality manner, and in compliance with regulatory agencies’ standards. Ensures continuity of supply of regulated products, esp. companion Dx products
- Develop optimal and scalable processes to handle CDx and IVD projects (e.g. Cascades)
- Drive performance of the Division’s operations and internal and external “vendors” to drive COGS productivity of more than $20M over the next 3 years, without compromising quality or product availability
- Partner with business and functional leaders to identify projects and recommend appropriate course of action (e.g., product quality improvement, discontinuation, outsource, process improvement) to maximize profitability and supply
- Establish key performance indicators that drive change and visibility to the team and leadership. Track, trend, and monitor routinely with active data analysis to target and drive results
- Leverage people as a competitive advantage. Coordinate the hiring, training, coaching and annual performance reviews of manufacturing leaders. Define and establish clear objectives and expectations, routinely provide direct feedback for performance management and development
- Manage budgets, schedules and key operating metrics
- Minimum of 10-15 years of management experience in a complex, global, multi-site manufacturing environment, with significant focus on outsourced manufacturing & supplier / supply chain management
- Significant experience and expertise managing operations in a Regulated environment, including demonstrated experience with FDA and Notified Body inspections
- Significant experience leading large, highly complex global moves, including movement of products, people and associated global footprint in a highly integrated environment
- Excellent communication, collaboration and interpersonal skills with the ability to facilitate team interactions and to partner with and influence key stakeholders including Finance, R&D, Product Management and the Commercial team
- A track record of talent development and a demonstrated ability to make that talent mobile so that our team develops the necessary global mindset
- Strong leadership ability with the capability to leverage and flex diverse resources, respond quickly, understand the impact of changes and decisions, facilitate agreement, build collaborative relationships and focus on customer needs
- Practical application experience in continuous improvement methodologies to improve processes, strengthen quality and drive efficiency
- Strong analytical ability including the ability to effectively use data in problem solving and to evaluate process changes and impacts in order to significantly improve product quality and reliability in a Regulated environment
- Ability to develop high levels of credibility and forge solid and positive professional relationships with subordinates, peers, and executive leaders
- Willingness and ability to travel from 25-50%, including international
41
Manufacturing Operations Supervisor Resume Examples & Samples
- Diesel/Gas mechanic skills
- Strong leadership skills, preferably in a represented environment
- Experience managing in a process oriented work environment
42
Manufacturing Operations Professionals Resume Examples & Samples
- Experience in discrete manufacturing
- Driver mind-set combined with strong interpersonal skills
- Ability to adapt to clients at all levels
- Ability to manage people
- Solution focused
- Good communication, networking and presentation skills
43
Manufacturing Operations Administrator Resume Examples & Samples
- Enter SKU Bill of Material (BOM) into Windchill PDM System
- Update and maintain SKU BOMs with latest requirements and changes
- Maintain Windchill library for product SKUs
- Work with cross functional teams
44
Opex Lead, Manufacturing Operations Resume Examples & Samples
- Develop and roll-out the site OpEx strategy across the operations team
- Developing Operational Excellence (OpEx) Capabilities within the Manufacturing Operations team through formal / informal training and coaching
- Provide Coaching on OpEx methodologies to the Operations team e.g. Yellow and Green Belt and lean philosophy
- Support development of a Continuous Improvement culture through facilitation and coaching of teams in the identification and implementation of improvements
- Enable the operations teams to develop and sustain systems and behaviors which deliver excellence
- Lead initiatives to maximize the utilization of manufacturing capabilities to ensure cost-effective, compliant and on-time supply of commercial products
- As a member of the site OpEx team, support the site’s strategic planning and execution
- It is desirable that the incumbent is Black Belt or lean Master trained and certified
- It is preferred to have a BSc or higher in a Science/Engineering discipline
- The incumbent must be a certified Lean Practitioner or Green Belt with a minimum of two years’ experience of leading projects at this level
- The incumbent should have 5 years technical experience preferably in a cGMP manufacturing environment
- Behaviors: experience in the development of key behavioral indicators is an advantage
- The incumbent should have strong interpersonal, coaching, mentoring, facilitation and influencing skills
45
Intern / Co-op-manufacturing / Operations Resume Examples & Samples
- Supports the Value Stream by recommending and implementing methods for eliminating waste such as restructuring job duties, reorganizing work flow, relocating work stations and equipment, tool/fixture/cell improvements and purchasing of equipment
- Liaison between the tooling and quality needs of the Value Stream and cross functional support not in the cells such as planning, purchasing, and design engineering to provide technical information
- Establish point of use inventory for cell support and assist in Kanban systems and establishment
- Develop and maintain standard work, work instructions and quality check points
- Oversee facility improvements and upgrades
- Studies and records time, motion, methods, and speed involved in performance of maintenance, production, clerical, and other worker operations to establish standard production rate and to improve efficiency and identify waste
- Develops and recommends equipment specifications, performance requirements, cost analysis, and proposal for integrating machinery, equipment, and tooling into the manufacturing process
- Establish and implement safety procedures, identify and review safety issues, and review safety and accident reports and assist in corrective action
- Tests ability of machines to perform tasks
- Develops models of alternate processing methods to test feasibility of new applications of system components, and recommends implementation of improved procedures
- Working towards B.S. Mechanical, Manufacturing or Electrical Engineering
- Experience with modeling software, as well as thorough knowledge of all MS Office software (Word, Excel, PowerPoint, Outlook, Project and Access)
- Strong Communications and Organization skills
46
Manufacturing Operations Intern Resume Examples & Samples
- Create tooling and fixture changes as needed and coordinate with tool designers to specify or procure new tooling and fixtures
- Develop and update process documentation and procedure instructions
- Analyze and evaluate manufacturing methods and standards. Provide solution to problems that adversely affect operator safety, quality, productivity, and cost
- Assist in development and troubleshooting of manufacturing equipment
- Support day to day assembly line activity. Maintain a neat, clean, orderly work area
- Support on-going continuous improvement initiatives through identification and implementation
- Assumes other responsibilities as required by management
- 3rd or 4th year BA Student in the following degree programs: Graphic Communications Management, Manufacturing Engineering, Industrial Engineering, Logistics, Operations Management or related program
- Previous manufacturing experience and or internship experience is a plus
- Basic understanding of Lean Manufacturing principles
- Proven oral and written communication skills
- Planning and project management skills
- Ability to take direction on projects
- Ability to adapt well to change in a fast paced environment
- Working knowledge of MS Office
47
Manufacturing Operations Manger Resume Examples & Samples
- Monitors daily progress/status of production goals and makes adjustments/corrections to ensure optimal performance and service
- Improves efficiency, quality and service of ongoing work as well as provides day-to-day direction to assigned team
- Initiates and implements lean and Kaizen initiatives and process improvements
- Responsible for managing team for specific area within the factory, building positive relation across team members
- Delegating tasks and executing them on time
- Ensuring production department is aligned with company procedures, standards and H&S politics
- 6-8 years of relevant work experience
- Ability to prioritize tasks and meet deadlines
- Strong analytical skills, ability to identify problems and propose solutions as well as proactive, high initiative & creative
- Ability to work as an individual contributor and within team environment
- Being highly responsible
- Good knowledge of written and spoken English as well as MS office
- Engagement and focus on targets/goals realization
- Master’s degree in Management/Production or similar
- Knowledge of Lean Manufacturing
48
Manufacturing Operations Professional Resume Examples & Samples
- Experience from working with or implementing MES systems
- MSc or BSc in Engineering, such as Mechanical Design, Supply Chain Management, Industrial Engineering or Logistics
- Work in a team and independently
- Motivation to constantly improve and achieve your goals
49
Manufacturing & Operations Engineering Resume Examples & Samples
- Undergraduate degree in Mechanical Engineering, Industrial Engineering, or related field of study
- A minimum of a 3.0 out of 4.0 overall grade point average
- Willingness to relocate as required by the program
- Authorization to work in the country of application full-time without restriction
- Prepared to take a role in a new location post-graduation
50
Manufacturing Operations Seasonal Intern Resume Examples & Samples
- Plans, coordinates, and implements daily operations by shift of a production department. Works with hourly associates to ensure all requirements are met
- Manages the production operation
- Monitors Quality Control programs to insure process controls are met, document activities, and brings about corrective action as needed
- Institutes processes and procedures to assure that work in progress is held in a manner that precludes deterioration and does not compromise product quality
- Ensures finished product is properly accounted, sampled and disposition
- Monitors quality of product produced on daily sample pull, analysis and communicates any issues to production and Operation managers
- Manages and coordinates according to defined company policies and procedures the disposition of hold product
- Directs and coordinates food safety, Quality, HACCP and GMPs in the area
- Works closely with Quality Assurance, Planning and Operations to ensure smooth transitions are maintained between departments and shifts
- Support ongoing TPM, 5s, SMED, Centerline, AM, DDS and related initiatives
- Supports the Campbell Soup Supply Company work ethic, Mission Statement and the philosophy of teamwork
- Project work that supports advancing the plants’ achievement of high performance organization standards, world-class safety operations, employee technical training, continuous improvement, standard work, and others
- In pursuit of Bachelors degree (Engineering preferred)
- Availability to work from January to July/August (5 to 6 days per week)
- Ability to work any shift and to work with limited guidance
- Microsoft Office applications including Word, Excel, and PowerPoint
- Demonstrated ability to quickly learn new computer programs (SAP and Kronos)
- Demonstrated leadership ability (leading by example, holding others accountable, resolving
51
Manufacturing & Operations Internship Resume Examples & Samples
- Work with a Senior Engineer on a well-defined project related to active programs addressing new product development, manufacturing process improvements or current customer issues
- Have frequent opportunities for direct interaction with our internal manufacturing and marketing groups, as well as, our external automotive customers
- Prepare and present a report summarizing your project work
- Working towards an undergraduate, Master's or PhD degree in Electrical Engineering
- A minimum GPA of 3.2
- The demonstrated ability to learn on the job
- Be an effective problem solver with strong analytical skills
- Results oriented and a self-starter
- Proficient in Excel, Word and PowerPoint
- Ability to work in a team environment
52
Manufacturing & Operations Internship Resume Examples & Samples
- Be expected to perform your own work which may include but is not limited to polymer synthesis, paint making and application, physical testing, advanced analytical techniques and computational modeling
- Support Lean Loading project for the Manufacturing Area. Work with the team to improve the efficiency of finished product mixers and dispersions pre-mixers loading
- Perform task analysis to reduce total effort and time to load a batch. The implementation of this project should also contribute to improve consistency on product Quality
- Improve the Mix Center manufacturing process. Analyze current process, equipment and work practices used in the Mix Center
- Develop a plan to improve overall performance regarding Productivity & Quality while keeping the operation safe
- Help the areas' process engineers ensure all scenarios for hazardous events and consequences have the proper level of interlocks. Develop a plan to reconcile any gaps that may be identified by the team
- Help all process areas update their Chemical Interaction matrices
- Working towards an undergraduate, Master's or PhD degree in Chemical Engineering, Mechanical Engineering, Industrial Engineering, or Supply Chain Management
53
Manufacturing Operations Resume Examples & Samples
- 3+ years direct supervisory leadership experience
- Prior experience in a unionized manufacturing setting strongly preferred
- Previous experience in a high-volume production or manufacturing environment
- Experience with implementation and monitoring of Statistical Process Control systems, ISO9001 processes and an ability to jointly lead work groups with Union leadership a plus
- Demonstrated performance in the areas of leadership, change management and continuous improvement
- Experience with all facets of skilled trade activities which may include Performance Measurement, Cost Containment, HVAC, PLC, PC robotic interface, Predictive and Preventative Maintenance, Computerized Maintenance Management, Environmentally Safe Practices, Electrical, Electronic Systems, Injection Molding and Prototype/Product development testing
54
Manufacturing Operations Resume Examples & Samples
- 3+ years of related job experience
- Working knowledge with lean manufacturing methodology, quality issues, and problem solving
- Demonstrated experience with working independently in thoroughly analyzing data and influencing leadership to make decisions and to take actions
- Ability to work with and influence all levels within Harley-Davidson organization
- Hands on experience in leading projects with cross-functional teams to improve business performance and maintain sustainability
- Demonstrated proficiency in computer skills and network knowledge
- Excellent oral, written, listening and comprehension skills
- Willingness and ability to work within a group and/or team
55
Manufacturing Operations Resume Examples & Samples
- Meet or exceed metrics (Safety, Quality, Delivery, Cost, People/Engagement, and Sustainability targets) for a process area through process control
- Walk the floor providing leadership and coaching
- Ensure the process is designed properly through layered audits and
56
Manufacturing Operations Resume Examples & Samples
- 3+ years direct supervisory or similar leadership experience
- Previous experience in a unionized high-volume production or manufacturing focused environment
- Prior knowledge and/or experience advising high performance work groups and experience with implementation and monitoring of Statistical Process Control systems, ISO9001 processes and an ability to jointly lead work groups with Union leadership a plus
- Must be consistent and dependable in carrying out supervisor duties independently and with little direction
57
Manufacturing Operations Resume Examples & Samples
- 8 years of Environmental leadership experience with substantial experience in a manufacturing/industrial environment
- Must have excellent knowledge of Federal, State and local environmental regulations experience and demonstrated capability to develop and implement effective environmental programs, including all applicable recordkeeping, reporting, permitting, planning, and other compliance activities
- Previous experience developing and leading Environmental Management Systems (EMS) strongly preferred
58
Manufacturing Operations Resume Examples & Samples
- Operations and Manufacturing experience
- Quality Systems knowledge and experience
- Knowledge of H-D CIS operating system
- Root Cause & Problem Solving abilities
- Ability to effectively define and scope a problem
59
Manufacturing Operations Resume Examples & Samples
- Advocating for and identifying improvement opportunities in such areas as continuous educational development of the maintenance work force, waste reduction, yield improvement and Overall Equipment Effectiveness, fostering or driving a culture mindset around lean manufacturing, and world class asset maintenance methods
- Daily operational maintenance responsibilities and leadership include managing the onsite maintenance function / personnel. Additional responsibilities include budgeting and execution of capital programs within plant maintenance
- Provide leadership, technical support, and in-depth maintenance systems knowledge to insure all plant-wide systems are fully capable of meeting all production requirements. This includes hands-on and theoretical support of production and maintenance staff members, full immersion into all maintenance systems, equipment repair, and operational issue remediation
- Integrate / participate in the overall maintenance community by sharing and seeking information from other locations, exchanging technical and operational data, communicating status of operations, both internally and externally. Utilize common approaches to maintenance work, troubleshooting and problem analysis
- Minimum 3 years of maintenance experience in a manufacturing environment
- Minimum 3 years supervisory/ management experience
- Knowledge of processes required to trouble shoot, design and repair high speed manufacturing systems
- Ability to coach and provide guidance to staff
- Ability to manage a team of supervisors and work closely with other plant leadership
- Excellent problem solving and decision making skills
- Budget and cost control experience
- PC skills – SAP/AS400 (preferred but not required), Excel, Word, Outlook
- Knowledge of good manufacturing practices
60
Manufacturing Operations Resume Examples & Samples
- Determining metal flow in dies utilizing state of art systems such as circle grid analysis
- Selecting allowances for forming and sizing
- Setting up and operating complex and standard machine tools such as CNC equipment, Wire EDM equipment, Coordinate Measuring Machines, lathes, jig bores, all types of grinders and mills in the manufacture of tools, dies, jigs, templates, fixtures, gages and experimental parts of models of any complexity
- Providing input into tool design and development
- Reviewing tool and die designs from suppliers
- Altering existing tools, dies, jigs, fixtures, and gages to prepare them for other uses
- Performing heat treating functions as required
- Trouble shooting and repairing dies in the process area to ensure production readiness
- Operating overhead cranes, presses, die separator manipulator and laser
- Performing safety inspection on a daily basis (lights, horns, tires, fluid levels, emergency stops electrical wires, machine guards, etc.)
- Participating as needed in department or plant wide committees
- Ensuring updated process sheets and work instructions for ISO
61
Manufacturing Operations Resume Examples & Samples
- Development of systems and best practices associated with world class manufacturing and testing automation with a strong relationship to the ongoing operation and maintenance of production assets
- Development of systems to ensure reliable operation of equipment reduced production interruptions and consistently high levels of part repeatability and quality
- Coordination of projects and provide technical support on new and existing machine tools for the production operations
- Technical support: Provide maintenance and Project Engineering services to Production Departments. Use technical information to develop creative solutions to technical problems. Interface with Plant Engineers, Manufacturing Engineers, Tool Engineers, Product Engineering, and Maintenance Work Group Members. Develop and modify ladder logic and all machine control programs. Establish system of control program management including stabilization of installed data, accessible back up and protected master copies of machine tool logic
- Involvement with new equipment selection, approval drawings, component specification; recommend spare parts attainment, maintenance training requirements, preventive maintenance recommendations, manual and documentation procurement
- Develop and coordinate projects that enhance machine reliability, productivity, consistent improvement in quality and operational safety. Manage and track projects to ensure on time delivery
- Work with maintenance work groups to establish maintenance budgets and tracking capitol expediters. Develop machine spare parts lists with machine tool suppliers, work groups that meet the spare parts budget requirements. Coach the work groups in communicating with suppliers, and ordering operating supplies directly from the supplier
- Track productivity, quality and cost improvements associated with the application on automation projects and Maintenance improvements
- 5-10 years of experience in all aspects of machine tool controls (CNC & PLC)
- Electronic gauging and quality data collection environment. Demonstrated ability to manage multiple projects simultaneously
- Knowledge of Total Productive Maintenance, Preventive Maintenance and Predictive Maintenance
- Strong interpersonal skills in conflict resolution, coaching and mentoring are essential. Person must be a self-starter
- Experience in working in a team environment and fostering team concepts to build group commitments to goals and objectives. Must have strong organizational, problem solving skills
- Practical application of ergonomics and a good understanding of OSHA requirements Machine Tools
- Computer experience including AutoCAD, Allen Bradley & General Electric PLC software, Graphical design systems, numerical control, word processing and spreadsheet programs
- This job will require a high level of independent identification of organizational needs and formal communication to plant leadership on a timely basis
62
Manufacturing Operations Resume Examples & Samples
- Repairing process equipment
- Planning, laying out, installing and repairing wiring, electrical fixture apparatus and control equipment
- Working from blueprints, schematic and circuit diagrams, manufacturers’ specifications and oral instructions needed to perform the job
- Fabricating boxes, supports and performing any necessary functions required to properly achieve completion of the job
- Installing and connecting control distribution apparatus such as transformers, switches, relays, circuit breaker panels and motors
- Upgrading, modifying, repairing, adjusting and testing all types of programmable controls, numerically controlled and computer numerically controlled equipment
- Programming controls as they relate to equipment, input, output, subroutines and equipment parameters
- Performing all inspection and cleaning of all electrically and electronically operated equipment
- Inspecting, overhauling, lubricating and cleaning motors and controls on electronic and electrical equipment
- Operating necessary material handling equipment to transport supplies to the job and to make installations and repairs
- Performing Preventive Maintenance (PM fluids and oiling that are not operator specific)
- Performing necessary mechanical operations incidental to the job being performed
- Participating as needed in PWG or plant wide committees
- Volunteering for RWG action register items, to resolve action register items that involve leadership responsibilities and group training responsibility
63
Manufacturing Operations Resume Examples & Samples
- Apply the latest maintenance safety technologies to ensure best-in-class maintenance safety performance
- Develop detailed work packages from preventive and predictive findings and other maintenance activities for all maintenance teams
- Utilize latest Maintenance Management measurements to develop maintenance activities to improve OEE
- Organize and coordinate all maintenance PM, Work Order, and Projects to include: Break down Work Order and project work material take off and ordering, Kitting work order and project work for efficient downtime utilization, scheduling work order and project work against available hours and skill-sets
- Maintenance material ordering follow-up, material expediting, and planning and scheduling key maintenance equipment for PM (lift equipment etc.). Assist with coordinating with suppliers and OEM’s warranty returns/repairs
- 3 years supervising Maintenance Skilled Trades
- 2 years of project planning and scheduling
- 2 years of CMMS experience
- 2 years utilizing Maintenance predictive technologies and preventative maintenance activities
- Experience planning and scheduling skilled trade maintenance activity in a manufacturing environment is required
- Previous experience sourcing equipment, materials, and components (purchasing) and SAP experience is preferred
- Skills in cross-functional project management and execution
- Demonstrated knowledge and experience utilizing technical problem-solving concepts and techniques
- Ability to provide clear and concise feedback to others
- Requires strong interpersonal skills including conflict resolution, coaching, mentoring, training and facilitation
64
Manufacturing Operations Resume Examples & Samples
- 3-5 years of related experience in a high volume production environment
- Operations planning and control experience
- Knowledge of SAP, Office and ASI based software preferred. Ability to write and retrieve queried information
- Superior interpersonal skills and a willingness to evoke creative problem solving and analytical skills
- Strong willingness to learn and utilize data management systems
- Must be flexible to work any shift and able to perform in a fast paced and quick changing environment
65
Director, OSD Manufacturing Operations Resume Examples & Samples
- Demonstrated experience leading a large cross functional team in a high paced production environment. Leadership background must include supervising numerous experienced managers
- Proven experience in solving personnel, process and facility problems quickly, often working across functional groups. Successful candidate must have experience working as a leader with various types of production operators, engineers, supply chain personnel, and equipment technicians
- Demonstrated ability to be organized, self-motivated, dependable, and work well with other leadership in a multi-tasking environment
- Provable experience in hiring a full range of employees and contractors from operators through leadership. Experience must include creating job requisitions, finding candidates, interviewing, best candidate analysis, completion of administrative hiring requirements, and onboarding
- Excellent written and verbal communication skills. The individual must communicate effectively with production supervisors, managers, plant management, and technical experts
- Knowledge and experience using ERP system
- Knowledge and experience in a potent compound/DEA-controlled substance manufacturing environment
- Ability create and manage a detailed indirect and direct manufacturing budget that will be the basis for annual cost performance
66
Manufacturing Operations Shift Manager Resume Examples & Samples
- Lead a Health and Safety culture within operations; ensure the team consistently sets site safety best practices by demonstrating zero tolerance behavior, continually challenging and raising Safety standards
- Ensures compliance with all safety, GMP, and corporate policies and procedures
- Responsible for the ownership of all safety incidents and quality deviations that occur on shift. This includes triage, initiation, investigation, timely closure, and any resulting CAPAs
- Accountable for the supervision and execution of all manufacturing operations within their assigned shift. Including activities such as production schedule execution, area cleaning, environmental monitoring, maintenance, In-process sampling and testing, validation, and construction activities within their shift
- Participates in and advances critical site strategy initiatives such as STOP, Bravo Recognition, HOP, Strategic Leadership, LDR and Shop Floor Quality
- In-direct management responsibilities for laboratory, maintenance (including IFM), QA, and visitors working on their shift
- Drives opportunities to improve, simplify, and eliminate waste while reducing the opportunities for human error during manufacturing execution
- Responsible for area inspection readiness and provides direct audit support
- Works with Shift Supervisors to ensure timely and accurate reporting of Tier 1 metrics and issues
- Provides coaching and mentoring. Regularly meets with staff to discuss performance, career, and development
- Conducts personnel and team performance management including objective setting, performance appraisal reviews and succession planning
- Provides shift continuity by attending the daily shift huddles
- Leads Tier 2 meetings and ensures proper escalation of shift issues
- Leads area GEMBA walks that focus on safety, compliance, efficiency, and waste elimination
- Provides continuity in communications to area/site personnel for safety issues and significant deviations
- Shares metrics and performance data to all groups
- Accountable for 5S and other OpEx initiatives
- Collaborates with site and network groups to meet site objectives
- Strong working knowledge of cGMP practices, FDA/EMA, compliance requirements, OSHA requirements, etc
- Strong understanding of safety dangers (steam, pressure, chemical, etc.) and best practices for safe working behaviors
- Demonstrated ability to successfully coach and develop people and teams
- Ability to create an environment of trust, compliance, safety, continuous improvement and learning
- Excellent problem solving, decision making and communication skills
- Change agent with demonstrated history of continuous improvement
- Strong knowledge of MS Excel, Word and PowerPoint is preferred
- Extensive knowledge of SOPs and cGMPs and the know-how to work and manage within a regulated environment
- Strong change management skills and demonstrated ability to simplify and improve business processes
- Yellow or green belt certified in lean manufacturing/operational excellence
- Will supervise a direct staff of 4-10 employees with department level managerial responsibilities
67
Manager, Manufacturing Operations Resume Examples & Samples
- Management/facilitation of the manufacturing and packaging initiatives for multiple Horizon products with contract manufacturing organizations (CMO’s) performing development, clinical, and commercial supply manufacturing including
- BS in Chemistry, Biochemistry, Chemical Engineering or related field
- 8+ years industry experience in pharmaceutical manufacturing technical operations and supply chain environment, with at least 4 years in leadership/project management roles. Background in solid/oral dosage tablet manufacturing and dealing with contract manufacturing entities (CMO’s) preferred
- Comprehensive experience in drug development spanning bench top to commercial production inclusive of DOE, manufacturing, equipment qualification, process & cleaning validation, and regulatory submissions (IND/NDA/MAA)
- Thorough understanding of good manufacturing/laboratory practices (GMP/GLP) and regulatory compliance/documentation requirements
- Exceptional organizational skills in handling multiple priorities and demonstrated ability to meeting required forecasts, budget objectives, and milestones
- Proven record for leading successful implementation and optimization/continuous improvement efforts in a forward thinking cross-functional manufacturing environment
- Proactive professional with excellent problem solving skills
- Excellent oral/written communication skills
- Willingness and ability to travel domestically and internationally as needed
68
Manufacturing Operations Consulting Manager Resume Examples & Samples
- Perform assessments utilizing analytical skills to understand client environments and associated financial opportunities
- Develop and deploy internal controls and organizational metrics dashboards per regulations and/or client needs
- Develop, manage and lead continuous process improvement strategies and initiatives
- Deliver training, coach and mentor Project Champions
- Execute a portion of the scope of work as assigned and ensure deliverables are achieved on time and within budget
- Leverage the flexibility of Lean, Six Sigma and Performance Improvement tools to enhance productivity
- 6-10 years of manufacturing operations and consulting experience
- Operations consulting experience a plus
- Ability to build, manage and foster a team-oriented environment
- Ability to interact with internal management team and external client contacts using strong leadership and communication skills
- Proven ability to work creatively and analytically in a problem-solving environment
- Excellent communication (written and oral) and interpersonal skills
- Strong interpersonal communication, influencing, and advanced Excel, Power Point abilities are essential
69
Manufacturing Operations Resume Examples & Samples
- Minimum of three (3) years of experience in assigned functional production process focus area or other relevant experience (STP or PTP)
- Minimum 3 years work experience in supply chain, materials and/or manufacturing related functions such as MRP, DRP, purchasing, procurement, inventory management, warehouse management, supplier management, Manufacturing Execution, or Preventative Maintenance for OE, P&A, GM or MRO
- Demonstrated prior success developing solid business stakeholder relationships and credibility quickly through strong follow-up/follow through skills
- The ability to lead through influence and persuasion
- Strong process and principle-based problem-solving capabilities
- Project management and/or project implementation experience
- SAP experience a plus but not required
70
Manufacturing Operations & Quality Resume Examples & Samples
- Academic qualifications: Masters or PhDs degree in a Life sciences or Scientific discipline (e.g. Pharmacy/Industrial Pharmacy, ...)
- Fluent English (written and spoken)
- Fluent in French (written and spoken)
- Max. 2 years professional experience after your graduation
- Right to work in Belgium: we sponsor VISA & work permit
71
Lead Solution Developer Manufacturing & Operations Resume Examples & Samples
- Accountable for technical solution specification and the build of an integrated IT solution (applications, infrastructure and workplace)
- Responsible for the current and future state of the technical application, infrastructure and workplace architecture / landscape, will be leading and/or conducting system integration
- Analyses technology, business and technical requirements
- Deliver training and mentoring on technical application, infrastructure and workplace architecture practices
- Responsible for risk level determination and execution of impact analysis for all changes
- Calculates and plans the effort and needed lead time of the development work in terms of effort required and overall cost / validates the proposals of the vendors and various services, additionally guiding and monitoring the solution delivery for development work during project and changes
- Participates in the development of complex IT solution according the technical application, infrastructure and workplace design
- Accountable for the unit test of the solution to ensure first time right delivery for the IT solutions
- Collaborates with peers in the region to share knowledge and increase global usage of solutions
- Guides the developers to follow the development principles and practices of his/her domain
- At DSM’s Group Information Solutions (GIS) our vision is to provide a wide range of Desirable, Reliable, Efficientand Cost EffectiveDigital Solutions. We develop people who are passionate about delivering World Class servicesand solutions so DSM can fully realize its ambitions in business and in society
72
Manager, Manufacturing Operations Resume Examples & Samples
- Responsible for the production of portable and fixed pump skids, large volume gun trailers & associated components while meeting our Market and Business growth objectives
- Ensure the most efficient use of the available resources to meet the needs of the business
- Implement best practices and ensure employees are engaged in zero harm and other EHS initiatives
- Continuously improve manufacturing processes and product quality to meet and exceed customer expectations and support quality system certification initiatives
- Responsible for understanding and meeting customer commitments (internal and external), and driving initiative to improve customer satisfaction and overall customer experience
- Resolve employee concerns and issues by using effective people management skills to ensure a well-motivated workforce
- Hold employees accountable and provide appropriate feedback to ensure results are achieved while our company values are maintained
- Implement business strategies involving new product and custom built equipment to ensure the successful launch and build of product
- Technical resource for others helping to improve design, new product introductions and continuous improvement activities
- Interact with all functional groups and be a technical liaison between production employees and engineering
- Must have experience with methods of fabrication and welding
- Excellent problem solving skills, with an analytical approach to solving complex problems related to engines, pumps and other mechanical and fabricated equipment
- Experience with fire-fighting equipment and emergency response equipment is a plus
- Ability to communicate across all functions with a clear and concise message is a plus
- Proficient with typical Microsoft computer software
- Good written, verbal and interpersonal communication skills
73
Director of Manufacturing Operations Resume Examples & Samples
- Responsible for the Burnet, TX site security and safety of operations, personnel and regulatory compliance
- Overall accountability for the safety, quality, cost, throughput and delivery of ADM and SPI manufacturing operations in Burnet, TX
- Provides direction and prioritization to personnel regarding planning, scheduling, purchasing, manufacturing, manufacturing engineering, quality, inventory control and distribution/shipping;
- Leads and/or participates in cross-functional teams to resolve customer supply and quality issues and drives sustainable process improvements
- Develops and manages manufacturing performance objectives driving operational improvement
- Guides and supports new product transition activities from engineering to volume production
- Assists with the development, planning and execution of the overall SCEM divisions global manufacturing strategy
- Bachelor’s degree in Engineering (Chemical or Mechanical), with an advanced degree in Business or Management preferred
- 15+ years manufacturing or operations experience, with continuously increasing responsibility and oversight
- Management and development of manufacturing and operations personnel
- Chemical, gas or semiconductor experience strongly preferred
- Experience with new product introduction, commercialization and product transitions (in-source, out-source or site-to-site)
74
Manufacturing Operations Resume Examples & Samples
- Spend time on the floor providing leadership and coaching
- Ensure engineering support and processes are administered and designed properly through layered audits and discipline
- Manage Maintenance engineering processes ensuring they are flexible to meet changing needs
- 60% or greater floor time
- 1) Practical application of ergonomics and safety, understanding EJMS/JSRA process design work
- 2) The application of engineering practices
- 3) Competence with and application of costing methods and value analysis
- 4) The application of design for manufacturing practices
- 5) Full application of Just-In-Time manufacturing (JIT) principles
- 6) The application of problem solving, root cause and decision analysis techniques
- 7) Knowledge and experience with the principles of trade unions
- 8) PLC/Controls, automation, lean manufacturing principles
75
Senior Director, Manufacturing Operations Resume Examples & Samples
- Provide leadership and direction for all aspects of manufacturing operations globally
- Lead, structure, and plan the management of the overall manufacturing operation to achieve company goals for product quality, on-time delivery, effective inventory management and manufacturing profit and productivity
- Responsible for planning and executing Annual Operating Plans and overall responsibility for achieving Manufacturing Profit targets
- Lead implementation of comprehensive and sustained LEAN manufacturing and training of personnel
- Improve manufacturing and material management processes through use of LEAN manufacturing principles and productivity measurements and improve production metrics year over year
- Manage production to meet product inventory requirements
- Integrate the production of new products as developed
- Optimize production processes
- Evaluate and implement automated production systems as necessary
- Develop and implement effective supply-chain management practices to reduce overall costs, improve product quality and assure stable sources of supply
- Drive SAP and follow-on improvements to the ERP system functionality in order to facilitate better decision making and efficiency
- Support global sourcing efforts to find further supplier cost reduction opportunities while maintaining product quality
- Effectively manage, train, and motivate all direct and indirect subordinates, as a team, to maximize the overall productivity of operations
- Lead effective efforts to restructure/eliminate ergonomically adverse manufacturing procedures
- Manage preventive maintenance program for equipment and tooling in support of process and product excellence
- Drive safety throughout Operations and identify preventive plans to prevent accidents
- Education: Bachelor’s degree (B.A./B.S.) or equivalent from accredited college/university in a related discipline. Master’s degree preferred
- Experience: Ten or more years in a pharmaceutical, medical device or related cGMP manufacturing operations management position
- An equivalent combination of education and experience may be accepted as a satisfactory substitute for the specific education and experience listed above
- Certification/Licensure: None
- Other: Green Belt level Six Sigma preferred
76
Manufacturing Operations Supervisor Resume Examples & Samples
- Leads and or/participates in Value Stream Improvement efforts working with EHS, Quality, Operations, Plant Engineering, Supply Chain…etc
- Provides inspiring and inclusive leadership for supervision and production team to drive sustainable improvements and meet the needs of the business
- Determines priorities and timetables, assigns resources/tasks, and provides performance feedback. Accountable for the activities and results of their subordinates
- Proactively communicates project direction and status to appropriate personnel
- Active visible leader for the areas assigned
- Drives cost, quality, service and productivity of all metrics associated with assigned departments
- Willingness to be on-call
- Possess or in the last year of pursuing a Bachelor’s degree or higher from an accredited institution in a science, engineering, or business discipline
- Supervisory experience within a manufacturing environment
- 5+ years supervisory experience
- Experience leading Lean implementation efforts in a manufacturing environment
- Experience in managing and leading manufacturing plant functions
- Proven ability to effectively manage personnel
- Background in Six Sigma and especially Lean tools
- Master's degree or higher from an accredited university
77
Manufacturing Operations General Supervisor Resume Examples & Samples
- Provide direct supervision and coaching for production supervisors and other operational staff. Accountable for the activities and results of their direct reports
- Lead the development and implementation of improvements and/or solutions to work processes and tools in support of business and strategic plans
- Develop and be accountable for metrics which monitor plant performance, such as productivity, yield, customer complaints, operational costs, etc
- Provide manufacturing support to meet division NPI program objectives and timelines
- Collaborate with extended value stream partners to identify, prioritize and resource programs in alignment with business strategy. Proactively communicate project direction and status to appropriate personnel
- Implement and optimize processes to improve results. Champion Lean Six Sigma projects and coach employees on tool use to improve safety, quality, service and cost
- Determine priorities, timelines, resource assignments. Provide employee performance feedback and reviews on a regular basis
- Actively participate in relevant corporate programs/initiatives, comply with professional and quality standards, comply with corporate policies and procedures and act in a professional manner consistent with 3M’s values and ethical standards
- Bachelor's degree or higher from an accredited university
- Bachelor of Science degree in Engineering or related technical discipline from an accredited university
- Minimum of two (2) years of supervisory and/or managerial experience
- Strong communication skills to lead direct reports as well as manage customer interactions
- Excellent team building and interpersonal skills
- Lean Six Sigma, Black Belt or Green Belt experience
- Experience in Lean Management Systems
78
Director, Manufacturing Operations Resume Examples & Samples
- Assures subordinate managers and employees complete individual goals and objectives and complete an annual appraisal of performance
- Determines and executes administrative policies through subordinate Managers
- Ensures the optimal operation of departments within the organization, such as Production, Materials, Engineering, and Maintenance
- Formulates, negotiates, and manages the organization’s objectives and budgets, as well as the strategies and action plans to achieve objectives
- Establishes and authorizes Standard Operating Procedures (SOPs) for the site
- Leads a cultural shift in the organization focused on breakthrough improvements to move the facility to the next level of operational excellence
- Manages the operation budget
- Overall responsibility for managing the organization. Participates in establishing the objectives and strategies that will determine the plant’s direction
- Promotes safe work practices and safe building and equipment and the programs to support safety
- Represents the organization in Industrial, Commercial, or Professional Trade Associations to develop an acceptance of the Company, as well as to detect situations or trends that can affect the operation
- Responsible for selecting, training, motivating, and developing staff as well as acting as a facilitator. Responsible for promoting and maintaining interdepartmental harmony
- Ensures the optimal operation of departments within the organization, such as Production, Materials, Engineering, Maintenance and Human Resources
79
Manufacturing Operations Resume Examples & Samples
- Demonstrated experience in successfully achieving business process improvements
- Demonstrated experience in leading cross-functional teams to achieve project goals/objectives
- Demonstrated experience utilizing Advanced Product Quality Planning Methodology and the integrated product and process development techniques within it. (e.g. Process Flow Diagrams, PFMEA, Control Plans, I/PPAP, Standard Work)
- Proven success managing medium scale projects from concept development through successful implementation
- Possesses a demonstrated ability to: lead change, influence others, foster key stakeholder relationships, lead by example, identify and plan for technical process improvements, remain focused, non-confrontational and flexible while under pressure
80
Lead Printhead Manufacturing Operations Associate Resume Examples & Samples
- Performs moderate-complex tasks, such as testing high- end servers
- Monitors the execution of process-oriented tasks of others in lower-level roles
- Identifies complex and undocumented areas for process improvement
- Leads production tasks and operates machinery while continuing to support quality assurance measures
- Supports engineers with diagnostics, troubleshooting, and prototyping
- Serves as lead for an area within their shift and compiles data for reports to supervisors
- Responsible for auditing materials and builds for quality assurance
- Excellent multi-tasking ability
81
Printhead Manufacturing Operations Associate Resume Examples & Samples
- Performs specialized job assignments in the manufacturing process with minimal supervision
- Mentors lower-level employees
- Assists with products well into maturity life-cycle as well as new products
- Understands and executes to customer expectations, e.g., Customer to Order (CTO) expectations
- Associate degree preferred or equivalent experience
- Typically 4-6 years of experience in manufacturing operations, preferably in a technical environment
- Mastery in English and local language
- Excellent mathematics and reading comprehension skills
- Demonstrated physical capability (e.g., manual dexterity)
- Excellent understanding of how to navigate tools and procedures
- Very strong written and verbal communication skills
- Very strong teamwork skills; excellent coordination skills
- Excellent technical knowledge specific to business function and segment
- Strong computersoftware skills; good business application skills (e.g., Microsoft Excel)
82
Associate Manager, Manufacturing Operations Resume Examples & Samples
- Managing the routine operations of the GMP production suite during normal operations
- B.S. in Biology, Biochemical, Chemical, or Biomedical Engineering or related discipline with 5+ years of relevant experience in a clinical laboratory or blood/cell culture processing environment or M.S. with 3+ years of relevant experience
- Knowledge of internal quality systems including Oracle ERP, Celdox, eQRMs, and eRexS
- Proficiency in MS Office Applications including Word, Excel, Access, and Sharepoint
83
CIM, Manufacturing Operations Co-op Engineer Resume Examples & Samples
- Generate specification and Requirements document on Data Analytics use case identified
- Using Programming Skills, transmit raw data to cloud (or local storage), clean/prepare data, perform statistical and/or quantitative analysis on data, evaluate for veracity of data
- Build visualization (Charts, Graphs, etc.) layer to communicate information derived
- Data Mining, Statistical & Quantitative Analysis
- Currently enrolled in Master's program in Computer Science, Analytics/Data Science, Statistical Analysis
- Experience – Programming Skills in Python, Spark, MapReduce, Machine Learning, Data Mining, Statistical & Quantitative Analysis
- Travel – 5%
- Excellent Academic Standing (GPA 3.5 or higher)
- Self-motivated; able to take ownership of assignments, develop work plans and proactively seek feedback to ensure objectives are aligned and met
- Team player; able to succeed in a dynamic, fast paced environment
84
Manufacturing Operations Resume Examples & Samples
- A limited number of applications will be accepted at this time, and this position may be un-posted at any time
- Please do not call to confirm whether or not your application was received. You will be able to see the status of your application at any time from the Job Management link
- Employment under the Operations' classification will most likely be in one of two entry-level areas described below (other entry points such as 2nd Operator, Stock Keeper, and Security could be available, but these are much less likely)
- Individuals must successfully perform the duties of the entry-level position to be considered for advancement into one of our certified apprenticeship or structured training programs available in Manufacturing
- Must have valid driver's license
- Must be legally authorized to work in the United States
- Must follow all safety procedures
- Must wear company-provided personal protective equipment such as safety shoes, safety glasses with side shields, and hard hats at all times in designated areas. Dust mask, rubber gloves, face shields, and other protective equipment must be worn when required
- If required, must work a twelve (12) hour rotating shift schedule
- Overtime work is required from time to time
- Be familiar with basic computer functions such as creating, sending, and receiving e-mail and data entry
- Have a strong work ethic, demonstrating both initiative and a professional attitude
- Must have clear and concise verbal and written communication skills
- Must be able to apply mechanical fundamentals to properly operate and maintain the performance of the equipment within area of responsibility
- Must be able to perform the essential elements of the positions with or without reasonable accommodations
85
Director, Manufacturing Operations Resume Examples & Samples
- Direct the development and implementation of activities in production area(s) to meet all production, quality, and cost objective goals
- Establish operational objectives, work plans, and delegate assignments to appropriate team members
- In partnership with internal stakeholders and manager, identify and review the appropriate key performance indicators to measure the success of plant operations
- Prioritize production schedules based on product introduction, sales forecast, equipment efficiency, and materials supply
- Ensure alignment to department budget and offer recommendations on capital expenditures and direct/indirect labor
- Develop schedules and labor requirements for assigned work areas
- Identifies and prioritizes problems (or unexpected results) and drives them to resolution
- Ensures appropriate process controls to achieve targeted shipping and fulfillment
- Establish clear goals for employees within span of control that align with corporate objectives
- Able to transition programs from R&D development through commercialization
- Strong attention to detail and maintain a high level of independent work on projects
- Drive continuous improvement in collaboration with employees using lean techniques
- Knowledge of quality systems and medical device development
- Knowledge and experience with MRP/ERP systems required
- Strong proven leadership capabilities; demonstrated expertise in building strong organizations, sourcing, developing and engaging key talent and improving organizational performance as indicated by key metrics
- Strong interpersonal skills, able to work with staff at all levels
- Positive, self-confident, decisive leader able to influence across the organization
- High Energy and goal-orientated with desire to succeed in a business environment
- Ability to develop and manage cross-functional teams
- Minimum of 10 years’ experience in a managerial manufacturing/operations and planning role, preferably in a medical device company
- Experience with ISO requirements is mandatory and FDA knowledge and experience is preferred
- Create clear and comprehensive documentation
86
Senior, Manufacturing / Operations Resume Examples & Samples
- Demonstrated ability to read, write and comprehend instructions, short correspondence and memos
- A basic understanding of the ACSI Mixing computer system
- Able to learn to use
- Lifting 70 lbs of pail/bag and pushing/lifting light vat/drum
- Pushing/lifting heavy vat/drum with the help of equipment
- Experience of operating forklift truck preferred but will train if not
87
Manufacturing Operations Engineer Resume Examples & Samples
- Oversee subordinate certification and training, attendance, and yearly reviews
- Drive cycle time reduction through prompt hold lot release, high inventory step management, and exclusion investigation
- Bachelors in Engineering
- Excellent interpersonal and presentation skills, energetic and self-starter
- Individuals will be and must be able to understand complex automated systems and human interactions
88
Manufacturing Operations Resume Examples & Samples
- ELECTRICAL/ELECTRONICS
- HYDRAULICS/PNEUMATICS
- PLCs
- WELDING
89
Manufacturing Operations Resume Examples & Samples
- Enhancing component manufacturing by assuring that parts or assemblies are processed and tooled to meet optimum quality, quantity and cost requirements
- Providing technical support to analyze and develop manufacturing control systems
- Interfacing with Supervisors/Process Leader, Work Groups, Quality and Product Engineering, and Manufacturing Support Services
- Developing cost reduction programs through manufacturing efficiency improvements, schedule attainment, and first run capacity. Specific results include continuous improvement of safety, quality, cost, workflow, and on-time product delivery. Perform supervisory duties as required
- Detail process planning including work balancing, work standard development, operator and equipment utilization, ergonomics, PFMEA, quality controls, tooling,
- Process documentation / information using CAD, Network/software, PC
- ISO 9000 standards and their relationship to company policies, procedures and instructions
- Experience with formal problem solving methodology required
- Demonstrated project management skills required
- Knowledge of PLC programming, troubleshooting capability preferred
90
Manufacturing Operations Consulting Manager Resume Examples & Samples
- Ability to analytically evaluate client environments and associated financial opportunities
- Develop and deploy internal process improvement and controls, organizational metrics, dashboards and KPI’s per the client needs
- Conduct advanced financial analytics managing large, disparate datasets
- Leverage Lean, Six Sigma and Performance Improvement tools to enhance productivity
- 8-12 years of manufacturing operations and/or operations consulting experience
- Ability to interact, collaborate and influence internal management team and external client contacts
- Revenue enhancement experience
- Advanced Excel, Power BI and Power Point abilities are essential
- Must be willing to travel 80 - 100%
91
Director of Manufacturing Operations Resume Examples & Samples
- Define and implement manufacturing strategies, such as next generation supply/value chain technology, that guide the existing high performance organization to the next level and differentiate Agilent to become an industry leader in manufacturing
- Assists company officers and senior staff members in the development and formulation of long and short-range strategies, policies, programs and objectives
- Provide leadership for the manufacturing organization, motivating, developing and building the team to develop the manufacturing plan and establish procedures for enhancing high standards of manufacturing operations to ensure that products conform to the established customer and company/regulatory quality standards
- Lead key technology manufacturing team to identify, recommend and implement changes to improve product value in quality, cost, delivery and productivity through value engineering and continuous improvement efforts
- Manage department managers to accomplish goals of the manufacturing/revenue plan, consistent with established manufacturing and safety procedures. Acts as liaison between R&D, Quality, Marketing, Product Support, Global Procurement & Logistics teams, as well as executive/department manager levels to inform personnel of communications, decisions, policies and all matters that affect their performance, attitudes and results
- Cultivate an ambitious, enthusiastic, and goal oriented work environment that is aligned with Agilent’s values through advanced leadership and employee career development programs
- Foster a customer-driven and operational excellence culture of execution, to deliver according to contractual commitments on quality, budget and timelines
- Requires proven skills in strategic management and developing an organization to a future ready manufacturing that can differentiate Agilent and become an industry leader
- Have a vision in applying supply/value chain technology model to enhance manufacturing capability
- Our ideal candidate will be technically aware with a landscape view of supply/value chain technology, in order to articulate future strategic trends. Global experience a strong plus
- Demonstrated track record of success in leading a world class team
- High energy, inspirational leadership skills with exceptional communication and team building ability
- Strong business acumen; knowledge and experience with project and product financial metrics
- Ability to participate in and lead cross-functional teams and to achieve results through cooperation with other business units and departments
- Strong analytic and problem solving skills
92
Manufacturing Operations Resume Examples & Samples
- A minimum of 3 years of direct supervisory or similar leadership experience is required
- Prior knowledge and/or experience advising high performance work groups and experience with implementation and monitoring of Statistical Process Control systems, and ISO9001 processes
- Ability to jointly lead work groups with Union leadership is a plus
- Must be consistent and dependable in carrying out supervisory duties independently and with little direction
93
Manufacturing Operations Resume Examples & Samples
- Identifying the level of human and capital assets required for given schedules and product mixes maximizing workflow and floor space utilization
- Working with stakeholders in plant operations to ensure facility efficiency and workplace safety
- Capacity and manpower planning, ergonomics analysis, method development, standardization of work, and material flow analysis objectives
- Providing input in development of both Operations and Capital budgets; therefore, demonstrating knowledge in the budget planning process is required
- 3 years of manufacturing experience
- Prior experience working in a Unionized manufacturing setting and implementing manufacturing excellence concepts including value stream mapping, work flow analysis, 5S (housekeeping), pull system/one piece flow and visual management
- Ability to respond to requests, ideas, and suggestions in a non-defensive manner, taking appropriate action that facilitates cooperation and trust
94
Additive Manufacturing Operations Specialist Resume Examples & Samples
- Responsible for receiving in metal powder used in additive manufacturing, performing incoming quality assurance tests, and managing powder inventory
- Perform machine set up activities prior to initiating part builds
- De-powder build chambers upon completion of part builds
- Post-processing of parts after build completion, including but not limited to 1) Heat-treatment furnace operation, 2) Power saw operation to remove parts from build plate, 3) Media blast metal finishing
- Develop expertise in maintenance and operation of all Additive Technology Center equipment. Tasks will include laser powder bed fusion machine programming, powder loading, sieving, de-powdering, calibration, sawing, chiseling, die grinding, heat treating and media blasting
- Support development of maintenance, operation, and material handling practice documentation for additive equipment
- Perform dimensional inspection of parts produced
- Continuously improve processes and procedures for efficient, repeatable part production
- Maintain and operate at peak operating condition additive and other operational equipment
95
Manufacturing Operations Resume Examples & Samples
- Demonstrated understanding and practical application of lean manufacturing techniques and SPC is required
- Experience should also include three years of detailed process planning and manufacturing engineering activities
- Responsible for technical/floor support for resolution of quality or process issues and improvements
- Support multiple robotic cells as a Tactical Engineer on the shop floor
- Shop floor presence is 85% or greater
- Capable of understanding and troubleshooting complex mechanical, tooling, part fitment and weld issues in a high volume fabrication plant
- Knowledge of gauges, gauge development and SPC
- Previous experience with multi-axis laser cutting
- Detail process planning including work balancing, work standard development, operator and equipment utilization, ergonomics, PFMEA, quality controls, tooling, fixturing, and gaging
- Process control and quality assurance, SPC, and process capability
- Process documentation / information using CAD, Network/software, PC applications
96
Manufacturing Operations Analyst Resume Examples & Samples
- Project phase responsibilities – Drive manufacturing operational readiness deliverables to ensure successful start-up,
- Identify manufacturing raw material needs and evaluate (and sometimes suggest) suppliers. This will include driving new material supplier identification, quantities, analytical specifications, sample requirements, and production requirements
- Develop and implement Bill of Materials (BOM) and material master data within key manufacturing IT systems including LIMS and JDE. Requires close collaboration with key support staff
- Ensure raw materials availability to support Covington start-up plan
- Identify manufacturing consumables and evaluate suppliers
- Ensure compliance of all material and waste flows as designed for the facility
- Author and revise SOPs GMP/Commercial Manufacturing phase responsibilities - Drive manufacturing deliverables to ensure successful
- Commercial operations, including
- Author and revise GMP documents and manufacturing records (e.g. Batch records, SOPs, change controls, etc.)
- Train staff in general manufacturing activities
- Specify production work order builds for materials resource planning system
- Ensure availability of all materials and consumables
- Collaborate in the mitigation of any environmental, Health, and Safety (EHS) needs and risks
- Lead any CAPA investigations to adequately identify root cause and implement appropriate corrective and preventative actions to prevent reoccurrence
- Identify and implement improvement initiatives to improve yield, reliability, and/or process robustness. This may require leading and implementing change controls
- Demonstrate continuous improvement with respect to increasing job knowledge and proficiency related to the biopharmaceutical industry, as well as technical understanding/problem solving capability
- Stay current with biopharmaceutical industry best practices and technologies
- Responsible for organizing data and preparing appropriate documentation, including presentation materials, for assigned projects
- Possess knowledge of core manufacturing principles and support systems
- Must have excellent organizational, verbal and written communication skills; able to efficiently communicate with crossfunctional
- May occasionally work in a clean-room environment and wear special garments (requires removal of make-up and
97
Global Manufacturing Operations Finance Internship Resume Examples & Samples
- Helping the business achieve financial plan objectives
- Supporting FP&A Activities (Closing, Latest Estimate, Capex Reporting)
- Maintain executive reporting packages and assist with key corporate initiatives
- Streamlining processes, SAP reporting solutions, and ACE development
- Enhancing the controls environment
98
Manufacturing Operations Resume Examples & Samples
- A demonstrated understanding and practical application of lean manufacturing techniques and SPC
- Experience with detailed process planning and manufacturing engineering activities including work balancing, ergonomics, PFMEA, tooling, fixturing, and more
- Prior responsibility for resolution of quality or process issues and improvements on the production floor
- Experience with process documentation using CAD, Network/software, PC applications
- Knowledge of ISO 9000 standards and their relationship to company policies, procedures, and instructions
99
Director, Manufacturing Operations IT Resume Examples & Samples
- Builds strong, collaborative partnerships with business leaders at all levels - global and franchise - as well as with IT colleagues. Leverages deep knowledge of the identified Operations domains to partner with business in the formulation of IT strategies to support identified objectives
- Collaborates closely with other Operations IT leaders to provide thought leadership and portfolio input to the Operations IT strategy. Leverages a deep understanding of business processes and the information technologies required to support these in contributing to strategy. Develops and maintains a current capabilities assessment, targeted end state, and requisite program roadmap to get there
- Oversees the portfolio of systems and projects supporting NA Operations, while enforcing IT policies, best practices, and processes set forth by the Operations IT Project Execution Office and Quality standards, to include the project lifecycle, funding approval processes, and resource management procedures. The Head is expected to be highly aware of details impacting any aspect of the portfolio they own
- Operates in compliance with the policies and guidelines set forth by IT’s Center of Excellence organization, to include the Capability Lifecycle, funding approval processes, and resource management procedures
- Defines, oversees, and spearheads delivery of a portfolio of projects that further the business goals of the Operations Functions while complementing global business objectives. Responsible the IT budget and human resources assigned to deliver new capabilities. Ensures that all relevant information related to the project portfolio is maintained in the Project and Portfolio Management (PPM) platform
- Works closely with global/regional/functional business leaders in driving towards harmonization of business processes. Helps develop clear, well understood business requirements to existing problems. Partners with other solution leaders, enterprise architecture, and the build and technical support teams to leverage existing assets or configure new ones to enable critical processes, minimizing the need for new technology unless required
- Owns the budget assigned to deliver IT and is responsible for the successful execution of every component of same
- Monitors the technology environment (including testing and validation), resolves issues, and drives improvements in IT operations support levels
- Leads, develops and influences direct reports and other IT resources through a matrixed environment in which some required resources do not have a direct reporting relationship
- Provides strategic technology leadership and forward-thinking ideas for the appropriate business units through the creation of strategy and development of technology road maps
- Minimum of a Bachelor's degree (or equivalent) and 10 years relevant manufacturing, quality and R&D support platforms management experience, or 8 years’ experience with Master’s Degree is preferred. However, a combination of experience and/or education will be taken into consideration
- Knowledge of pharmaceutical manufacturing and supply chain business processes a must. Experience implementing IT solutions in support of research and process development process desired, to include Manufacturing Execution Systems, ERP, Quality Systems, Weigh and Dispense and Plant Automation. Must be experienced in working with IT Project Management Office. Must be experienced in successfully managing multiple Operations IT projects simultaneously
- Must understand highly complex technology projects and concepts as they relate to high-level business objectives, and ability to present those concepts to both IT and non-IT audiences in a concise and easily-understandable manner
- Ability to develop strategic partnership with business partners. A graduate degree in a related scientific domain would facilitate relationship management in the IT environment and would be preferred
- A proven track record and demonstrated understanding of highly technical custom software solutions
- Proven ability to drive complex conceptual discussions in support of business analysis to develop system requirements. This includes the ability to generate innovative ideas to resolve problems
- Excellent verbal and written communication skills and the ability to interact professionally with a diverse group of executives, managers, and subject matter experts
- Position functions autonomously. Has 20+ individuals in reporting structure
- Proficiency in speaking, comprehending, reading and writing English are required
100
Associate Director External Manufacturing Operations Resume Examples & Samples
- The ExM Snr Ops Manager is the leader of the External Manufacturing “Tier 2” Team. This team consists of nominated representatives from SCM, External Manufacturing QA, GTO – Packaging Technology, Research, and Procurement. The Senior Ops Mgr must lead this team to delivery of weekly/monthly and annual business objectives and meet the required EHS and quality compliance standards
- Set shared objectives for the “Tier 2” team & gain alignment with the “Tier 2” team & their line management in an inclusive manner working for the common good
- Technology Issues
- MPS and Continuous Improvement Activities
- Managing Remediation and/or Improvement Plans
- Work on both Tactical and Strategic Supply Strategy
- The ExM Snr Ops Mgr must link to the customers and suppliers of their contract manufacturers and to other stakeholders involved in the end to end supply chain. They must
- Work directly with those customers and build and maintain relationships with key team members at those customer locations and with other stakeholders (eg: SCM, D&L)
- Understand the constraints and risks associated with supplying each customer, both at the contract manufacturer and also within the supply chain between the contract manufacturer and the downstream nodes
- Act as a conduit between the Contract Manufacturer and MSD Manufacturing
- The ExM Snr Ops Mgr participates on the cross-functional team that Product Source Management assembles following a Supply Chain Committee (SCC) approved siting/source change to an external party and assume primary ownership of the new source
- The ExM Snr Ops Mgr is responsible for maintaining the integrity of the Master Supply Agreement (MSA), ensuring alignment with the Supply and Quality agreements and appropriate document revision and distribution control
- The ExM Snr Ops Mgr is responsible for ensuring contract terms agreed upon by MSD Manufacturing and the External Party are executed including purchase orders, forecasts, deliveries, and approving invoice payments
- The ExM Snr Ops Manager is a leader in the organization and
- Is expected to deliver work & results within ExM & MSD Manufacturing beyond the specific contract manufacturers they manage
- Is expected to lead project/initiative teams
- Is expected to develop standardize work and best practices to ensure consistency in Quality/Compliance and Supply
- Is expected to back-up other Snr Ops Managers and/or Ops Managers and the operations Director or Snr Director
- Is expected to work independently & set a positive example for ExM Ops Mgrs. & other cross functional leads
- The ExM Snr Manager may be asked to take line management responsibility for a team. They must
- Provide leadership and coaching for this team
- Build develop and maintain this team to meet the business needs
- Set objectives for the team members and conduct appropriate period reviews and regular 1:1 with the team to manage these
- Experience in commercial/business and manufacturing (within at least two of the following: Operations, Quality, Technology, Planning, Procurement) function required (or equivalent combination of education/experience)
- Excellent Problem Solving, Partnership, and forward looking Strategy skills
- Demonstrated Business and Financial Acumen that can drive value for MSD and our customers
- Experience with Drug Delivery Systems / Devices
- Must possess excellent interpersonal, communication, collaboration, negotiation, and project management skills
- Must be decisive in ambiguous environment
- Must be able to lead work on both tactical and strategic objectives in parallel. Able to be the one face of MSD Manufacturing to the external party
- Must be willing to travel (International and Domestic), 50% of the time
101
Manufacturing Operations Resume Examples & Samples
- Minimum of 3 years quality assurance experience in a manufacturing environment
- Experience in Project Management, which may include planning, supervising, monitoring, and accomplishing the goals of specific project requirements
- Experience in problem solving/decision making methods
- Knowledge of QMS assessment, measurement techniques, and the product development process
- Ability to understand PC operations including systems and software
- Experience working in a team-based environment is a plus
- Professional society/organization certifications preferred (ASQ, APICS, etc.)
102
Manufacturing Operations Coord Resume Examples & Samples
- Aptitude to follow complex instructions
- Capability to adapt to changing priorities
- Skills in multi-tasking, planning and organizing workload
- Ability to work independently and within a team
- Talent for establishing and maintaining positive work relationships
- Willingness to work overtime as required
- Ability to follow verbal and written instructions
- Ability to see and work with small objects
- Ability to handle small volumes of chemicals and solvents
103
Manufacturing Operations Resume Examples & Samples
- A minimum of five (5) years direct supervisory or similar leadership experience
- Prior experience working in a front line leadership role in a unionized high-volume production or manufacturing environment
- Knowledge and/or experience advising high performance work groups and experience with implementation and monitoring Statistical Process Control systems, ISO9001processes and an ability to jointly lead work groups with union leadership
- A track record demonstrating the ability to effectively function in situations where things are unclear at times
- A reputation for building positive relationships across all levels of the organization to achieve objectives through mutual participation
- Demonstrated performance as a leader among peers and has demonstrated leadership in change management
- Can be consistently relied on to be proactive in providing direction, coaching and mentoring to peers and makes self available to be a resource to peers
- Has led continuous improvement initiatives positively impacting the business and or day-to-day site operations
- Ability to perform at a coaching level for all functions of the supervisor
- Can be relied upon to accomplish the best possible results in any given situation
104
Senior Manufacturing / Operations Engineer Resume Examples & Samples
- Provides advanced technical solutions and leads team through process
- Devises new approaches to problems encountered
- Initiates, justifies, and implements new advanced capital equipment purchases
- Creates cell layouts and leads process improvement initiatives of high complexity
- Uses solid Six Sigma and lean tools to improve processes
- Uses solid concepts of Design for Manufacturability and Assembly (DFMA) and implements them into new product introduction
- Represents the company with our customers
- Leads updates to management on operations status
- Participates in and promotes process improvements within assigned areas; assists with the development of department and organization procedures
- Supports the manufacturing floor for any process related questions. Lends lessons learned and leads training efforts for process understanding
- Creates, maintains and develops new process documentation and updates work order documentation. Creates new systems that support this effort
- Implements complex engineering changes. Leads and acts as a change agent for complex engineering changes
- Adheres to applicable Quality System requirements and supports process audits
- Leads Process Flow Charts, PFMEA, and Control Plan Reviews
- Mentors Level 1 and 2 Operations Engineers and/or Manufacturing Specialists
- Solid understanding of design for complex tools and fixturings
- Solid understanding of all applicable software
- May participate in multi-site projects
- Solid knowledge of vendors, manufacturing processes, and procurement methods
- Trains other members of the team on theory and design of existing/new equipment
- Manufacturing Engineering Specific Functions
- Solid knowledge of machining / manufacturing processes for components / piece parts is required
- Solid written/verbal communication and presentation skills
- Solid Six Sigma knowledge; Advanced understanding of Lean Manufacturing concepts
- Solid Project planning tools
- Solid troubleshooting and problem solving skills; Solid understanding of Root Cause Analysis
- Strong computer skills and solid technical writing skills
- Uses solid concepts of Design for Manufacturability and Assembly (DFMA) and implements them into new product development
- Solid understanding of electrical and/or mechanical machine drawings, including industry specifications
- Greater than 4 years professional engineering experience or a combination of experience and advanced degree required
105
Manufacturing Operations Resume Examples & Samples
- Manufacturing Leadership – direct the overall manufacturing production throughput and any related initiatives set by the Company for maintenance. The incumbent is responsible for optimizing the efficiency of the manufacturing operations in the area, and must understand key business drivers and successfully manage and influence positive return on investments using lean manufacturing techniques
- Functional Leadership – responsible for leading a team of first line supervisors in the management of the production schedule and managing the engineering staff supporting the process area
- Operational Management – meet or exceed safety, quality, cost, delivery, people/engagement and sustainability metrics (SQDCPS targets) for a process area. The individual will walk the floor providing leadership, layered process audits and coaching (floor time of 40% or greater)
- Maintenance experience
- The application of engineering practices
- Computer experience with a demonstrated competence in PCs and the use of on-line systems both manufacturing and engineering
- Practical application of ergonomics and safety programs
- Competence with and application of costing methods and value analysis
- The application of design for manufacturing practices
- Full application of Lean manufacturing principles
- The application of problem solving, root cause and decision analysis techniques
- A total understanding of factory personnel operating systems (i.e. vacation scheduling, job movement, etc.)
- Knowledge and experience with the principles of trade unions
- An appreciation of the contribution of trade unions, and value of their role in the partnership
106
Intern, Manufacturing Operations Resume Examples & Samples
- Interact within cross functional teams and learn the different disciplines needed for a successful pharmaceutical product
- Learn about pharmaceutical processes, unit operations, labeling, and packaging
- Learn how prescription tablets, injectibles, biologics, and liquid formulations are manufactured
- Generate data compilations of finished product batches for trending and analysis
- Close gaps in databases for finished product quality and for finished product/intermediate stability
- Identify and resolve documentation gaps in shipping logistics of finished goods
- Cross-functional engagement with multiple business units
- Complete and present a milestone project that addresses current topics in the industry
- Strengthen communication and writing skills
- Gain experience working in a professional corporate environment
- Participate in ad hoc projects and tasks as needed
- Declared major in Engineering, Chemistry or related science required
- Currently attending an accredited 4-year undergraduate program. Minimum Junior or Senior standing
- Professional demeanor
- Self-starter attitude
- Drive for Results
- Strategic Agility
107
Manufacturing Operations Resume Examples & Samples
- Knowledge of and prior implementation of CNC programming, SPC, and Computer Aided Design is required
- Familiarity with the following is desired: Detail process planning, including specifying speeds, feeds, tooling, fixturing, and gauging. Practical application of ergonomics
- Machining operations and equipment, familiarity with Lean / cellular concepts
- Equipment justification and procurement, costing methods / value analysis
- Capacity planning, including productivity measurements, manpower planning, and material flow
- Process documentation / information using CAD
- ISO standards and their relationship to company policies, procedures and instructions
- Paint application, Lean/CIS, and Teach Pendant experience is a plus
108
Manufacturing Operations Resume Examples & Samples
- Assist in the development and enhancement of Standard Operation Procedures and Conditions
- Job shadowing all production positions, including but not limited to, Operations Supervisors and Operations Specialists
- Participate and lead continuous improvement activities
- Updating training materials, logging issues and other organizational tasks
- Coordinating and planning small training projects
- Inputting data and creating Key Performance Indicators
- Provide input on process improvements
- Must be currently enrolled in a minimum of 6 credit hours at an accredited college or university working toward a degree in Supply Chain & Logistics or related field
- Must be willing to commit to working a minimum of 20 hours per week
- Must live within a commutable distance to job location
- Ability to handle multiple and sometimes conflicting priorities
- Demonstrated ability to communicate effectively both written and verbally
- Proficiency with Microsoft Office Suite and the ability to learn new software quickly
- Ability to work within timelines and in pressure situations
- Strong problem solving, persistency and decision making skills
- Minimum of 3.0 GPA (Major); 2.7 GPA (Cumulative)
109
Manager of Launcher Programs Manufacturing Operations Resume Examples & Samples
- Set priorities and directs area supervisors and employees, as required, assigned to the manufacturing process areas of responsibility
- Establish annual time phased budgets with the assistance of Business Management for all assigned cost centers and track performance to those budgets and take actions based on performance
- Report Earned Value Metrics as well as maintaining quality and safety programs for all factory hourly labor performance for all ML&H programs and projects
- Coordinate with Programs Office, Scheduling and Engineering teams to ensure internal and external customer expectations and requirements are met
- Ensure all members of the team are adequately trained to accomplish assigned tasked safely, efficiently and accurately
- Lead the team in the implementation of Continuous improvement efforts in the fabrication and assembly areas to improve safety and quality while reducing cost and schedule
- Cultivating an environment of inclusion and diversity of the team to drive performance of the team
- BA/BS degree required. Minimum of 10 years of experience in the management of complex manufacturing. Experience in a DOD manufacturing environment highly desired
- Ability to multi-task and solicit data from various sources to make informed decisions to establish priorities and set team direction
- Excellent interpersonal and organizational skills, combined with a hands on leadership style
- A strong background in Manufacturing Operations Principles (CAL OSHA/Safe work practices, reading drawings, routing instructions, BOM’s, welding, and measurement processes)
- Experience in or working knowledge of Earned Value Cost Accounting
- Understanding of testing instrumentation, hand held precision measurement equipment, GDT techniques and preventative maintenance concepts is essential
- Knowledge and experience in metal fitting and welding processes, general machining and precision large industrial assembly is preferred
- Must be a US citizen with the ability to obtain a clearance
110
Manufacturing Operations Supervisor Resume Examples & Samples
- Provides process oversight, spending 90% of shift time out on the production floor
- Responsible for ensuring that all activities are carried out to the highest standards of GMP and EHS compliance
- Responsible for execution of manufacturing operations as well as interdisciplinary activities such as area cleaning, environmental monitoring, maintenance and validation activities within their shift
- Responsible for real time review of all manufacturing documentation and ensuring that all batch documentation has been completed by the manufacturing shift before handover
- Responsible for driving the execution of standard work, and reporting progress
- Responsible for managing Tier 1 board in manufacturing area to drive key performance indicators (KPIs), issue resolution and communication across the shift
- Owns Tier 1 meeting and drives standard agenda discussion
- Drives shift communications to ensure employees know what is required
- Responsible for verification of procedural and safety compliance and take responsibility for updating procedures, training and batch records, where required
- Ensures timely reporting of safety incidents and deviations
- Responsible for ensuring event reviews are conducted for both safety incidents and deviations
- Makes process decisions according to Decide, Action, Inform (DAI) matrix
- Provide troubleshooting for process, equipment and facilities
- Responsible for equipment handoff and room release activities
- Ensures that the area is inspection ready at all times through GEMBA walks on each shift, the execution of GMP walkthroughs with QA Field on a weekly basis and real time correction of issues
- Supports implementation of projects and new technology
- Performs weekly time management system approval of non-exempt staff
- Ensures all training for employees is completed on time, that the quality of the training is sufficient to enable understanding and provide on the job coaching and mentoring to ensure manufacturing operators are capable and confident in their daily tasks
- Provides regular feedback on performance to the manufacturing operators and also regular discussions on career development
- Drives personnel and team performance management including performance connections, acceleration of development action plans and succession planning
- Is responsible to own and embed OPEX principles in manufacturing including standard work, 5S, visual management and tier meetings
- Champion OPEX improvement ideas within the shift through lean leadership coaching
- Accountable to drive opportunities to improve, simplify and eliminate waste while reducing the opportunities for human error during manufacturing execution
- Supports Human Error related investigations through employee interviews, coaching and CAPA implementation
- Responsible for updating procedures and training material as part of CAPA implementation, errors identified by operators during execution, or as part of continuous improvement to ensure that documentation supporting the execution of manufacturing operations reflects activities as conducted and are being done in a safe, efficient and compliant manner
- Strong working knowledge of cGMP requirements and regulations FDA, EMA
- Strong working knowledge of both local, state and OSHA requirements in relation to environmental, health and safety
- Strong understanding of safety hazards (steam, pressure, chemical, etc.) and best practices for safe working behaviors
- Qualified trainer with ability to successfully coach and supervise people and teams
- Ability to work across the matrix to direct and support critical functions that support manufacturing including maintenance and quality
- Direct biologic manufacturing experience of 6+ years. Previous supervisory experience is desirable
- Extensive knowledge of working in a regulated environment and the importance of following procedures, cGMPs and EHS and the skillset to work and manage within a regulated environment
- Excellent leadership skills with the ability to motivate and manage a team with matrix reporting relationship
- Yellow and/or green belt certified in lean manufacturing/operational excellence
- Will supervise a staff of 6-10 employees
111
Engineer Manufacturing Operations Resume Examples & Samples
- Setup automation and inventory planning systems to optimize maximum utilization of tools relative to chamber and product mix
- Direct subordinates to achieve assignments using established guidelines, procedures, and policies
- BS, Engineering
- Fluent in English Language
- Demonstrated ability to communicate well with all levels of the organization and experience in working with external constituencies
- Demonstrated success in leadership roles
- Strong organizational skills along with demonstrated ability to manage multiple tasks simultaneously and able to react to shifting priorities to meet business need
- Demonstrated ability to meet deadlines and commitments
- Individual must be well versed in all Microsoft Applications (Excel, Word, PowerPoint …)
112
Manufacturing / Operations Resume Examples & Samples
- Bachelors degree in a technical or business-related field is required: consideration may be given to those who hold 6+ years of progrssively responsible and relevant work experience including 3 years of supervisory experience
- Strong written and verbal communication skills, including strong listening skills and proven ability to direct and instruct others in a positive manner, are essential
- Proven ability to interpret and apply written procedures and standards governing both manufacturing processes and employee performance is required; knowledge of cGMP
- Excellent problem solving skills; sound decision making skills; and demonstrated ability to meet deadlines in a team-oriented environment are critical
- Demonstrated project management skills are required
- Computer literacy and familiarity with automated record systems is necessary
113
Director, Manufacturing Operations Resume Examples & Samples
- Develop and support multi-year strategic plans for operations, regional AOP/operating budgets for plant operations, and capital expenditure plans
- Influence and drive change with the key stakeholders impacting plant operations to support growth and profitability improvements
- Establish, implement and drive a regional operating rhythm which reinforces continuous improvement, the achievement of key operational metrics, financial metrics and global initiatives
- Establish, implement and drive the manufacturing facilities to achieve forecast production levels to support customer service and planned inventory targets
- Act as the informal OES Regional leader for all functions and sites
- Ensure high levels of product quality are established and sustained
- Continue our focus on maintaining a world class safety culture by insuring an unwavering safety culture in all operations
- Develop a collaborative and strong working relationship with all business units and other key functional and OES stakeholders to gain alignment across the region and organization to meet business strategic initiatives and ensure cross-functional integration
- Ability to manage the complexity requirements of the role. Must be able to process, synthesize, and integrate information accordingly to make effective decisions. Must be able to effectively anticipate upstream and downstream impacts and make needs changes
- Lead systemic approach to workforce planning and succession planning, including identification and development of top talent
- Ability to embrace change, drive new change initiatives and consistently maintain a positive attitude while addressing barriers to move problems toward resolution
- Ability to delegate work effectively to ensure all business processes are controlled and enforced effectively
- Approaches problem solving from a global perspective that is inclusive of organizational buy-off and support where necessary
- Continuously develops and nurtures relationships across the organization
- Instills a culture of customer service at all levels of the organization
- Ensures the organization has a thorough familiarity with policies and procedures relating to standards of business conduct
- Trains and motivates employees in the importance of full compliance with the spirit of corporate policies and procedures and appropriate applies them in compliance with local laws
- Foster a performance based culture, including performance standards and career development planning for key talent in order to enhance the employee value proposition and positively impact employee engagement and retention
- Bachelor's degree in Engineering, Operations, or Supply Chain
- Minimum 12 years of varied management experience in production operations at manufacturing facilities, including responsibility for multiple functional areas within operations –production management, materials management and manufacturing engineering
- Financial business knowledge and strategic business planning experience to operate in an entrepreneurial business environment
- ERP knowledge and experience
- Experience driving continuous improvement and standardization
- Experience working in growth-oriented global organization with a high-mix, low volume diverse product portfolio with direct to customer and distributor driven channels
- Ability to travel within region and globally. Travel estimated at up to 25%
- Experience with global operations including integrated supply chain for make-to-stock, configure-to-order and engineered-to-order products
- Demonstrated strong presentation, verbal and written communications skills
- Formal training in Lean Manufacturing and Six Sigma - black belt or green belt certification preferred
- Experience in industrial/electrical equipment manufacturing
114
Manager, Fp&a-manufacturing Operations Resume Examples & Samples
- Consolidate Manufacturing and Operations Support reporting for Monthly Results, Latest Estimates (LE), Annual Operating Plan (AOP), and Long Range Plan (LRP)
- Drive continuous improvement across key processes including those stated above working with Plant Controllers and global finance teams
- Manage reporting and analysis around Inventory, Capital Expenditures, and strategic initiatives as needed
- Ad-hoc financial analysis to support operational team (Lake Forest / San Clemente Operations Support and Plants)
- Ensure strategic initiatives are on track both from a timing and financial results perspective
- Manage reporting and strategic analysis around TPM Spend and TPM PPV on a monthly, quarterly, and annual basis for actuals, budget, and LRP purposes
- Work on special projects as they arise
- Strong financial acumen including mastery of financial statement analysis, economic value added, and other valuation techniques; business case modeling, financial forecasting and an overall knowledge of accounting and budgeting principles
- Strong analytical and critical thinking skills
- Excellent written and oral communication skills and experience communicating quantitative and statistical analyses
- Ability to influence all levels of staff across different functional areas and lead in a matrix environment
- Highly collaborative across boundaries to build strategic relationships and achieve common goals
- Able to deal with ambiguity in a rapidly changing environment
- Excellent business sense with comprehensive understanding of all aspects of the enterprise
- Excellent time and organization skills, with the ability to handle multiple projects and meet deadlines while maintaining attention to quality and detail
- Expert proficiency with MS Excel and PowerPoint, with working knowledge of MS Access and/or statistical software packages
- Bachelor’s degree from an accredited college or university is required; Master’s degree preferred
- Minimum of 5-7 year of experience in operational finance, preferably at a manufacturing facility or in a support role as well as previous management experience. Preferably business partner support and continuous improvement experience as well
115
Manufacturing Operations Engineer Resume Examples & Samples
- Perform the daily operations of plants to ensure reliability and consistency on the production line
- Positions requiring understanding of a concepts, methods and procedures (technical Bachelor’s Degree or equivalent knowledge and experience)
- Manage an operation, business, unit, or part of a production facility in order to reach defined targets in quality, cost, delivery and safety
- Team management of salaried employees. This does not include production supervisors who oversee hourly employees
- Expected to resolve problems through the application of acquired expertise guided by precedent. Works together with people from the business unit
- Contacts are under guidance and/or geared towards specifying activities, planning of activities and giving explanations on technical issues
- Presents to internal teams on metrics, project status
- Develop manufacturing technology and realize new products and systems focusing on Continuous improvement, lean opportunities and labor productivity improvements
- Bachelor's degree from an accredited university or college with experience in Manufacturing or equivalent knowledge and experience
116
Head of Global Manufacturing Operations Information Technology Resume Examples & Samples
- Provide strategic technology leadership for Manufacturing Operations business units through the creation of strategy and development of technology road maps. Oversee the company’s portfolio of systems and projects, while enforcing IT policies, best practices, and processes
- Direct the development, implementation, and support of technology solutions that drive and enable business objectives; Ensure performance (schedule, budget, scalability, and agility), and continuously improve technology cost, performance, functionality, and innovation
- Lead and develop cross-functional, multi-disciplinary high-performing teams. Build collaborative partnerships as a trusted business advisor with Global Manufacturing Operations business leaders and oversee the activities of the IT solution leads partnering with the business functions
- Partner with Global Manufacturing Operations business leaders to assess the technology needs of their organizations; Direct the formulation of process and underlying system architecture to realize these needs
- Monitor the technology environment, resolve issues, and drive improvements in IT operations support levels
- Define, oversee, and spearhead delivery of a portfolio of projects that further the business goals of the Manufacturing Operation Functions while complementing global business objectives. Drive the global harmonization of cross-functional processes and their underlying systems
- Oversee IT services flow to business from appropriate IT support (shared) groups and make effective interventions wherever required. Gauge the internal customer satisfaction and provide necessary feedback to backend support streams for necessary corrections
- Facilitate business to achieve high standards of regulatory and other compliance through right set of IT solutions, services and procedures
- Bachelor’s degree (or equivalent) required with a specialization in Business Administration, Information Technology or Computer Science preferred
- A minimum of 10-15 years of Manufacturing Operations Information Technology experience required and a minimum of 5 years of experience in Management is preferred. Related experience may be considered
- Experience in a large multinational publicly traded company is preferred
- Experience in the pharmaceutical industry or other highly regulated process industry is preferred
- Must be willing and able to travel (domestically and/or internationally) up to 30%, or as needed
- May be required to stand, walk, stoop; bend; kneel; and climb steps. May require use of hands and arms to lift and scoop
117
Manufacturing Operations Resume Examples & Samples
- A minimum of three years of CI experience required
- Hands on experience in leading projects with cross-functional teams to improve business performance and maintain sustainability. Demonstrated proficiency in computer skills and network knowledge
- Communication skills: influencing, meeting leadership, change management, and facilitation
118
Manufacturing Operations Leader Resume Examples & Samples
- Will ideally be of degree education and have a track record in the Manufacturing sector
- Masters of Business Administration or similar degree preferred
- Manufacturing Operations Management, time served experience of managing a team
- Financial acumen, planning and reporting with strong analytical skills
- Lean Manufacturing, Project Management
- Procedures, company rules, guidelines (national and international), law, rules & regulations, standards, safety, quality and environmental guidelines as far as applicable
- Ability to travel within the UK and Globally
- Strong technical acumen – the ability to look at the product or the capital equipment from a technical view point and offer solutions and improvements
- SAP knowledge; MRP/ERP systems
119
Manufacturing Operations Supervisor Resume Examples & Samples
- Clear, concise communication and presentation skills
- Strong leadership skills, preferably in a manufacturing environment
- Ability to work well with represented and non-represented employees
- Microsoft and other database usage skills
120
More-manufacturing Operations Rotation Experience Program Resume Examples & Samples
- Supply Chain
- Materials Management
- Human Resources
- Complete rotation specific curriculum and deliverables
- Plan, manage and provide deliverables on projects as assigned
- Work closely with functional business groups to ensure efficiency and effectiveness of solutions deployed in support of business goals and objectives
- Gain buy-in from stakeholders in matrix organization structure
- Demonstrate close loop problem solving utilizing Lean and Six Sigma tools
- Identify opportunities for improvement and make constructive suggestions for change
- Demonstrate leadership ability in multiple scenarios; direct reporting team, peers, and on projects
- Report out to Executive Leadership on rotation experiences and performance
- Develop business acumen by taking the time to understand the business – the products, processes, channels, and the people
- Perform other duties as may be assigned at management's discretion
121
Manufacturing Operations Resume Examples & Samples
- Five (5) years of experience in all aspects of machine tool controls (CNC & PLC) Electronic gauging and quality data collection environment
- Knowledge of Total Productive Maintenance, Preventive Maintenance and Predictive
- PLC software, Graphical design systems, numerical control, word processing and spreadsheet programs
- Practical application of ergonomics and a good understanding of OSHA requirements machine tools
- Knowledge in one or more of the following software and systems is preferred
- GuardLogix 5000
- ControLogix/RSLogix 5000
- PowerFlex 700 Variable Frequency Drives
- DeviceNet Communication
- EtherNet IP Communication
- ControlNet Communication
- Allen Bradley Stratix/ Machine Networking
- RSViewME Programming for PanelView Plus
- Siemens Variable Frequency Drives
- Wonderware InTouch Comprehensive
- NFPA 70E Electrical Safety in the work place
- National Electric Code
- Pilz Safety Controllers
- ABB / Fanuc Robotics
122
Manufacturing Operations Resume Examples & Samples
- Working closely with operations managers on improvement projects
- Leading problem solving teams
- Assisting the production team to help solve issues
- Collecting and analyzing manufacturing data to drive root cause analysis and improvement measures
- Currently enrolled in a minimum of 6 credit hours at an accredited college or university
- Live within a commutable distance to the work location
- Ability to work in a team environment and across multiple business functions
- Ability to communicate effectively across business levels and functions
123
Future Leaders Program Manufacturing Operations & Quality Resume Examples & Samples
- Education: Masters Degree in Engineering (Chemical, Mechanical or Management Engineering preferred) with strong academic record; PhD or MBA will be considered an advantage
- Language: advanced oral/written Italian and English skills
- Real strong interest for production environment and challenges
- Strategic thinking with attention to detail and project management mindset
- Strong interpersonal and communication skills; self-motivation and proactive approach
- Analytical mind, multi-tasking and ability to adapt to change and keep focused under pressure
- Maximum of 2 year professional experience
- Availability to work in shift in one of the rotations
- Act as a reliable and hardworking professional with a practical hands-on approach, with a sincere interest on pharmaceutical industry from strategic and operational management point of view
- Manage the assigned activities and/or projects as part of the rotation program
- Elaborate clear individual objectives and assessment criteria for each rotation in collaboration with operational and functional manager, and work against their completion
- Provide regular updates on the activities performed and on the progress of assigned projects as required
- Contribute to continuous improvement initiatives within the assigned teams, process reviews and trend analysis and prepare reports when requested
- Provide timely notification to management of potential quality or regulatory issues that may impact product quality or regulatory compliance
- Experience people management, with direct or indirect reports
124
Director of Manufacturing Operations Resume Examples & Samples
- Development and formulation of long and short-range planning, policies, programs and objectives
- Champions a safety culture, ensures a safe work environment and cultivates safe behaviors
- Builds and develops a world-class operations team through talent development, effective coaching and counseling, motivation, and addressing performance gaps
- Develop a strategic manufacturing plan and establish procedures for maintaining high standards of manufacturing operations to ensure that products conform to established customer and company quality standards
- Direct and monitor department managers to accomplish goals of the manufacturing strategic plan that are consistent with established manufacturing and safety procedures
- Manage and control departmental expenditures within approved budgetary plan
- Ensures all established costs, quality, and delivery commitments are met
- Identify, recommend, and implement changes to improve productivity and reduce cost
- Formulate and recommend manufacturing policies and programs that guide the organization in maintaining and improving its competitive position and profitability of the operation
- Direct and coordinate various programs essential to manufacturing procedures such as training and development, lean manufacturing program, safety, housekeeping, cost reduction, security, etc
- Provide guidance to the development of a manufacturing process plan, including personnel requirements, material needs, installation of capital equipment, facility needs and repairs, and tooling and equipment needs
- Work effectively and relate well with others. Exhibit a professional manner in dealing with others and work to maintain a constructive working relationship
- 7+ years of experience in a leadership position within a manufacturing setting
- Bachelor’s degree or MBA preferred
- Ability to read, analyze and interpret financial statements and initiate the budgeting process to create workable and profitable plans
- Print industry experience preferred but not required
- Knowledge and experience implementing Lean/six sigma manufacturing techniques
- Demonstrated track record of efficiency and profitability improvements
- Demonstrated ability to lead change efforts
- Successful history of leading growth initiatives, while also believing in the importance of rolling up your sleeves to assist in getting the work done
- Knowledge and experience working with Sales and Marketing and R&D groups
- Proven experience with customer relationships
125
Specialist, Manufacturing Operations Resume Examples & Samples
- Perform as lead operator with supervisory authority in the production facility to guide and facilitate the manufacturing of products to support GPDO’s clinical and commercial timelines
- By way of continuous training and involvement in process development activities as appropriate, develop into a subject matter expert for at least one drug product, and serve as the primary GMP representative during further development and transfer activities
- Participate, as a manufacturing representative, on project implementation teams to provide a GMP perspective in order to transfer processes into the GMP production areas in an ordered manner, already having considered the implications of proposed process adaptations
- Represents the department on cross-functional/interdepartmental teams tasked with complex projects
- LI-EX
- Understanding of and ability to apply the regulations associated with 21 CFR 210/211
- Proficiency in MS Office Applications including Word, Excel, and Sharepoint
- Employees must work in areas where posted Universal Precautions must be observed and practiced. Associates work daily with potentially harmful and/or hazardous agents including asphyxiating gases (nitrogen), potentially carcinogenic and/or flammable chemical reagents and sharps
126
Manufacturing Operations Specialist Resume Examples & Samples
- 5 ) Work with planner to ensure the build plan quantity is firm order and tally with LTD report for team to meet the actual order
- 6 ) Help the team to meet 100% build plan linearity (weekly and monthly) and zero DEFOA through effective TO/QA/Build Plan follow up
- 7 ) Initiatives - 5S/Quality and LEAN/Spark Kaizen innovation/transfer
127
Manufacturing Operations Analyst Resume Examples & Samples
- Must be fluent in English
- The ability to work under pressure and respect tight deadlines
- Strong communication and negotiation skills are essential
- The ability to work as part of a diverse team
- Ability to work cross functionally
- Risk assessment skills
128
Manufacturing Operations Resume Examples & Samples
- A minimum of five years related of tactical engineering experience in a manufacturing environment. FABRICATION, WELDING/PRESS EXPERIENCE IS REQUIRED
- A knowledge and prior implementation of cellular manufacturing, J.I.T. and S.P.C. are required
- Direct experience in a variety of fabrication, machining, finishing and assembly processes including inspection, equipment selection, tooling selection, and new product/design introduction
- Detail process planning and continuous improvement, including specifying process parameters, process equipment, tooling, fixturing, and gauging, 3) computer oriented (CAD,
- Capable of understanding and troubleshooting complex mechanical, tooling and part forming issues in a high volume fabrication plant
- Previous experience with multi-axis laser cutting, G Code and C++
129
Manufacturing Operations Spcst, Matl Handling Resume Examples & Samples
- Demonstrated troubleshooting skills at sub assembly and final assembly levels
- Communication skills: demonstrated ability to give/receive oral or written information clearly
- Using standard/non-standard procedures in the subassembly and test of subassemblies and instruments
- Sets up and operates equipment or production processes in assembly, or follows techniques and operations in the fabrication, assembly and testing of assemblies or final products
- Provides first level of troubleshooting or corrective action, e.g., tracks materials, accounts for scrap, and monitors processes
- Managing the inventory function in the work area
- Provides feedback on defects and/or quality of test to engineering
- Assist engineering and tooling technicians in the development and evaluation of process tools and fixtures. Monitors processes and equipment to ensure same is functioning to specifications
- Perform standard maintenance on manufacturing processes (machinery and equipment)
- Orders and installs replacement parts as needed and notifies engineering of software issues. - Records/maintains historical test documentation and failure analysis data
- Analyzes results of operations or tests to determine if process or part problem exists and/or if engineering help is needed
- Clearly communicates with others, particularly other manufacturing functions to get information on materials or tasks to get the job done
- Generate and validate production procedures, bills of materials and general data collection and reporting
- Physically transfers supplies, components, assemblies, products, equipment, etc. between processes or areas
- Includes activities associated with Receiving, Stores and/or Shipping, e.g., counting, sorting, weighing, kitting, packaging
130
Manufacturing Operations Coord Resume Examples & Samples
- Demonstrated ability to make timely decisions
- Experience with troubleshooting and applying corrective actions
- Demonstrated ability to maintain accurate records
- Required to bend, stoop, and reach
- May be required to lift materials per entity specified and approved limits
- Previous manufacturing experience in an ISO certified environment
131
Manufacturing Operations Analyst Resume Examples & Samples
- Understanding of Tool Control Systems
- MS Excel and MS PowerPoint
- Ability to develop metrics
- Must be able to respond to emergent events quickly and resolve them with limited resources
- Must have a keen eye for safety
- Familiarity with audit processes
- Familiarity with building training materials for potential new team members and/or continuing education material
- Work in a team environment to drive change
132
Manufacturing Operations Resume Examples & Samples
- Mechanical/Electrical background
- Knowledge of CNC equipment and components
- Knowledge of Preventative/Predictive maintenance practices and technologies
- Demonstrated experience with Maintenance management systems
- Knowledge of Microsoft software including Access datase
133
Senior, Manufacturing / Operations Resume Examples & Samples
- Work with raw materials, batching, mixing, weighing and dumping ingredients, packaging, and operation of numerous types of equipment
- Operates machines which compact and process ingredients according to specifications
- Rotate job assignments & meet Daily Production Targets
- Handling of Hazardous Waste Material
- Maintains required product documentation for orders and material control
- Complete Employee worksheet daily
- Performs light maintenance on equipment and assist contractors when authorized by Manager
- Packages product according to customer specifications
- Follows all site safety procedures & guidelines
- Assist in review & updates of SOPs (Standard Operating Procedures)
- Notify Leadman or Manager of any issues or concerns regarding equipment, safety, production, or quality
- Performs other related duties as assigned by supervisor
- Accountability for clean & organize work areas, as well as, overall general housekeeping of the facility
- Ability to lift up to 55 pound drums, barrels, totes, etc
- Frequent lifting, working at heights, climbing stairs, standing, walking & reaching
- Must be able to work rotating shifts, weekends, and overtime as required; shifts can be either 8, 10 or 12 hour shifts
- Must possess good math and communication skills
- Position requires a high school diploma or equivalent
- Prior manufacturing batch operation experience preferred
134
Manufacturing Operations Resume Examples & Samples
- 8 years of manufacturing experience and a minimum of 3 years supervisor experience
- Detailed knowledge of manufacturing/assembly processes, lean manufacturing principles, tool and fixture applications, work measurement, ergonomics, quality/gauging principles and application, material flow and plant layout
- The ability to provide technical expertise to individuals in a way that can be utilized and built into the operating environment
- Demonstrated expertise in Manufacturing Engineering disciplines combined with interpersonal communications skills
- Ability to focus on results in complex situations, in a team environment, where many solutions are possible
135
Manufacturing Operations Resume Examples & Samples
- Minimum of 3 years experience in plastic injection molding is required. INJECTION MOLDING EXPERIENCE IS A REQUIREMENT
- 6 axis robotic experience is a plus with a preference toward Motoman
- Experience with 3D CAD software is desired, preferably ProE
- Ability to demonstrate effective leadership within a diverse work group comprised of both union hourly and salaried individuals is essential
136
Manufacturing Operations Resume Examples & Samples
- A minimum of five years related manufacturing experience
- Experience in a variety of cleaning and surface preparation processes, powder coat painting, robotic painting processes including inspection, equipment selection, tooling selection, and new product/design introduction
- Experience in the operation and continuous improvement of a high volume cosmetic finishing facility
- Must have knowledge of powder coat finishing processes for aluminum castings,
- Ability to manage projects, team with union partners, influence others and be able to handle multiple tasks
137
Manufacturing Operations Resume Examples & Samples
- 8 years of manufacturing experience and a minimum of 3 years supervisor experience. Maintenance experience is required
- Knowledge of predictive technologies including oil analysis, thermography, and vibration analysis is required
- Knowledge and demonstrated application of preventive maintenance systems required
- CNC equipment knowledge - both mechanical and electrical
138
Lead Manufacturing Operations Analyst Resume Examples & Samples
- Prepare and manage Orders, Revenue and CM and project performance - build measurement system, analysis and reporting throughout all cycles of GPB, SII, OP and actuals/estimates
- Prepare all post-closing plant financial analysis, performance reports, KPIs, with deep understanding of variances to plan for pitch outs to upper management
- Track various Projects (DMP/VCP/CoQ/Inventory) progress against plan at a granular level, recommend actions to get to planned performance. Ensure operational team are engaged and driving projects to closure
- Operating mechanism – systems & master data hierarchy, reporting calendar, standard processes - for efficient, transparent and accurate accounting and reporting
- Effectively partner with functional leaders, regional and HQ teams to ensure high quality and speed of financial analysis/reporting, facilitating efficient decision making, driving growth and productivity
- Actively participate in operation to ensure weekly pacing and CM numbers are accurate and provide analysis to bring transparency and accuracy in pacing numbers
- Solid understanding of PSI and factory capacity planning processes along with deep domain expertise on mix calculations, product line profitability and price analytics
- Support MSOs with validation of proper manning levels to various production scenarios, OT management and labor efficiency tracking
- Assist in preparation of capital appropriations requests and approval and budget of CAPEX and program expense processes
- Bachelor's degree in Accounting, Finance or Business Administration
- 8 -10 years of finance experience at multinational corporation, prior Supply Chain, Commercial and accounting experience is an advantage
- Graduate of GE’s Financial Programs (FMP/PFLP) or Corporate Audit Staff (CAS) preferred
- Exceptional communication skills at all levels of the organization, decision making, and self-learning attitude
- Strong interpersonal and influential skills, proven ability to build relationships across plant and functional organizations
- Strong analytic skills: able to clearly link financial results to operational performance drivers, generate alternatives and drive positive change
- Solid PC skills: experience with financial systems/applications (SAP, BI, HFM), strong Excel & PPT skills in data compilation and cost modeling
- Experience working in global business environment with sound understanding of global process and transactional flows
- Trained and/or certified in process improvement methodology such as LEAN or Six Sigma
139
Manufacturing Operations Analyst Resume Examples & Samples
- Manage standardize data bases (Dashboard, Ops Report, Dodexa) and enhance as needed by bakery users
- Design and develop standard analysis and reporting using KPIs to create visibility to operational trends both favorable and unfavorable and as a result, make recommendations for process improvements and cost reduction initiatives
- Work with each region to support with analysis involving capacity utilization, material and direct labor efficiency and overall cost improvement/containment
- Analyze operational data to highlight trends both favorable and unfavorable and communicate with bakeries and regional teams on findings
- Investigate internal as well as industry “Best Practices” and recommend feasibility and means of implementation including a projected potential savings
- Assist with developing the documentation of process and procedures for consistently collecting and reporting supply chain data
- Train bakery associates on standardized processes, procedures, and collection methods along with being a support for questions and issue resolution on an on-going basis
- Involvement with bringing new bakeries on board with regard to data collection and reporting
- Interface with the Grupo Bimbo Corporate team in all global initiatives and projects (WCS, MMS, GSFM)
- Establish a relationship with all production facilities in order to be valued resources for analysis and project work
- Use Oracle, BUSS, and DataWarehouse, Essbase, SmartView, Dodeca as the standardized data source
140
Process Engineer Manufacturing Operations Resume Examples & Samples
- Perform various engineering tasks involving such functions as analysis, design, development, testing, installation, and service (while working from instructions, drawings, proposals, specifications, and/or other pertinent information)
- Prepare specifications and related documents in accordance with requirements, established formats, and general instructions
- Review and analyze a variety of engineering data, documents, & reports
- Consult with other engineering groups to ensure that specified engineering criteria are suitable for the proposed application, and recommend revisions (as appropriate)
- Plan, conduct, or coordinate relatively straight-forward engineering analyses & tests; this will also involve preparation of related reports & summaries for review
- Participate in the investigation of technical problems and the establishment of procedures & CAPA (Corrective And Preventative Actions) to avoid recurrences
- Duties require thorough understanding of standard engineering theories, concepts, principles, and techniques
- Work is subject to general overview to ensure quality
- Bachelor’s degree in an Engineering-oriented field of study
- 2 years of professional experience working in manufacturing and/or engineering
- Bachelor’s degree in Industrial Engineering (i.e. BSIE), Mechanical Engineering (i.e. BSME), or related fields of study
- Experience working in broad aspects of manufacturing operations (Quality, Production, Operations, Maintenance, Engineering, etc.) – rotational experience is a plus
141
Senior Materials Manager Manufacturing Operations Resume Examples & Samples
- Ensure that entire Value Chain (VC) group is in full compliance with all ABB Policies, Laws & Regulations (including HSE requirements)
- Drive the Core Values & Behaviors defined by the Head of US Utility Sales
- Integrated Business Planning: lead the local IBP process to align demand, production, material, and financial planning for the entire value chain of the local unit
- Integrated Rolling Plan: develop the single integrated rolling demand & supply plan for business execution and improve the plan’s accuracy
- Inventory Management: establishes & maintains inventory management processes & guidelines in line with Business Unit (BU) instructions
- Develop End-to-End process optimization (externally and Intra-Company) to reduce overall VC lead-times and reduce inventory
- Own the Inventory Checkbook (ICBK) for the Local Business Unit (LBU)
- Fit Gap Solution/Assessments: make detailed gap analyses across the Value Chain and provide solutions to reach expected customer service levels at optimized inventory levels by utilizing Value Chain assessment methods on a regular basis
- Enterprise Resource Planning (ERP): provide local leadership to the units to use best practices in ERP for inventory management and control
- People Leadership & Development: ensure (with HRBP involvement) that their area of responsibility is properly organized, staffed, skilled, and directed
- Guide, motivate and develop direct & indirect subordinates within HR policies, for the benefit of both ABB & employee
- Train & mentor sales personnel, assess technical & sales skills, and develop where needed
- Provide technical & professional direction, resources, advice, and development opportunities to Value Chain Staff
- Foster strong & effective relationships with internal & external suppliers and customers
- 12 years of professional experience in Industrial Operations and/or Supply Chain Management
- 2 years of professional experience in a leadership role
- Bachelor’s degree in Supply Chain Management, Operations Research, Operations Management, and/or Industrial Engineering is a plus; Master’s degree is preferred
- Experience with Six Sigma (6S certification is preferred)
- Familiarity with supply chain and inventory management systems in industrial environments
- Strong understanding of forecasting and budgeting
- Excellent analytical, problem-solving, organizational, and leadership skills
- Experience working in industrial supply chain management functions within a manufacturing facility
- Recent strategic sourcing experience working with technical components, especially in manufacturing environments (multi-site and/or international experience is a plus)
- Demonstrated cost reduction track record; project management experience is a plus
- Proficiency in vendor management; negotiation skills are a must
- Excellent analytical capabilities to analyze commodity & business-relevant supply markets
- Experience working with SAP and/or other Material Requirements Planning [MRP] tools; advanced competency with SAP MM is highly preferred
- Proficiency with software applications such as MS-Office (e.g. Excel, Word, PowerPoint, etc.)
- Excellent communication skills in English (verbal & written); knowledge of additional languages is a plus
142
Executive Assistant, Manufacturing Operations Resume Examples & Samples
- Effectively and proactively manage the Vice President’s calendar, and email with attention to accuracy and detail, including keeping Executive informed of calendar changes and change requests
- Coordinate domestic & international travel, hotel accommodations, meeting schedules and all details for VP to optimize use of Executive’s time and schedule and ensuring compliance with existing policies and procedures
- Answer/screen calls and draft correspondence, proactively own and manage meeting agendas, meeting minutes and track deadlines
- Assist with on-boarding of VPs direct reports
- Pre-plan and execute on- or off-site meetings
- Provide administrative support as needed to other members of the TMTT leadership team, including global manufacturing leaders when visiting corporate offices
- Proactively coordinate all department meetings, plan special events and manage special projects
- Prepare, maintain, generate and process information, essential documents, records (e.g., expense reports, check requests and CPAs through Coupa) and related logistics
- Collaborate with Human Resources to facilitate interview schedules for TMTT positions
- Occasionally assist with VP’s personal appointments and travel to integrate seamlessly with business needs
- Interact professionally with all levels of Edwards employees, customers, vendors, and/or patients
- Work with cross-business unit management to obtain approval for agreements, purchase orders, and invoice payments
- Provide administrative support: Office supply orders, ITSRs, catering requests, conference room management and other vendor requests as needed
- Coordinate quarterly Ops Excellence Awards luncheons and awards ceremony
143
Manufacturing Operations Leadershiptrainee Resume Examples & Samples
- BS degree in business, engineering, forestry or related discipline
- Willingness to adapt to strong safety culture and ensure safe and efficient execution of work
- Ability to exercise good judgment in setting priorities and follow-through in a fast-paced results-oriented environment
- Strong desire to learn manufacturing processes, develop leadership capabilities and possess desire to progress in organization
- Demonstrated proficiency in MS Office Suite and other windows based programs
- Strong interpersonal and problem solving skills
- Experience/knowledge of project management
- Capability to prioritize work activities, assignments, demands and flexibility to adapt to changes
- Ability to develop partnerships and collaborative teaming
- Courage to challenge status quo and deliver results
- Excellent work ethic, strong time management and organizational skills
- Mobility within assigned region
144
Manufacturing Operations Resume Examples & Samples
- A minimum of three years related manufacturing experience
- A knowledge and prior implementation of cellular manufacturing, J.I.T. and S.P.C. are required. Experience should also include detail process planning and manufacturing engineering activities. Direct experience in a variety of fabrication, machining, finishing and assembly processes including inspection, equipment selection, tooling selection, and new product/design introduction
- Other responsibilities include
- 1) Machine programming, methods development, and technical/floor support for resolution of quality or process issues,
- 2) Detail process planning and continuous improvement, including specifying process parameters, process equipment, tooling, fixturing, and gauging,
- 3) Computer oriented (CAD, Network/software, PC applications),
- 4) Practical application of ergonomics, and safety process controls,
- 5) Machining operations and equipment, familiarity with cellular and JIT concepts,
- 6) equipment justification and procurement, costing methods/Value analysis,
- 7) process control and quality assurance, SPC, and process capability,
- 8) capacity planning, including productivity measurements, manpower planning, and material flow,
- 9) process documentation/information,
- 10) fabrication, machining, finishing and assembly principles with a basic understanding of programming and EASE work standards, and
- 11) ISO 9000 standards and their relationship to company policies, procedures and instructions
145
Manufacturing Operations Supervisor Resume Examples & Samples
- Production Operations and Scheduling experience in a Lean Manufacturing environment
- Experience with Kronos Time & Attendance system
- Strong Leadership, Interpersonal & Conflict Management skills
- Proficient with MS Office programs
- 3-5 yrs Metal fabrication experience (brake press, plasma tables, CNC operation, band saw, shear)
- Analytical Problem Solving
146
Global Engineering & Manufacturing Operations Resume Examples & Samples
- Leadership & Project Management – Be an effective project team member and leader by working on high-performing teams
- Analysis – Learn to evaluate quantitative and qualitative data to develop solutions to current business challenges
- Strategic Thinking – Challenge the status quo to keep SCJ a leader in the CPG industry and an indispensable partner to our customers and consumers
- Innovation – Be involved in the product commercialization process in action, from consumer insight to shelf
- Networking – Effectively gather pertinent information and build relationships with others in the organization. Meet & connect with executives in the Global Product Supply organization
- Full-time undergraduate or MBA student
- GPA of 3.2 and above preferred
- Strong analytical, technical skills
147
Executive Director Manufacturing Operations Resume Examples & Samples
- BA/BS in related field, preferably BS (Chemistry, Biochemistry, Chemical Engineering) or study of pharmacy
- Proven experience of operating at a senior level and managing people
- 15+ years industry experience, with 10+ of those years in Manufacturing and Technical operations in a pharmaceutical environment
- Experience with all dosage forms for small molecule manufacturing, especially solid/oral dosage forms and tablet manufacturing
- Proven track record in managing operational execution using 3rd parties
- Thorough understanding of good manufacturing/laboratory practices (GMP/GLP) and regulatory guidances/compliance requirements for the manufacturing of dosage forms for small molecules
- Experienced in manufacturing risk management processes and in using the risk management tools (FMEA, HACCP, HAZOP, etc.)
- Exceptional organizational skills in handling multiple priorities
- Well developed analytical, communication, and project management skills
- Proven record for the successful implementation and a continuous improvement in a forward thinking manufacturing environment
- Proactive professional with excellent leadership, and problem solving capabilities
- Excellent written and oral skills
- Good judgment and strong initiative
- Ability to effectively prioritise and manage a diversified workload, often to strict deadlines
- Professional approach with excellent written and verbal communication skills
- Organisation
- Functional/Technical Skills
- Intellectual Horsepower
- Dealing with Ambiguity
- Composure
148
Group Lead-manufacturing Operations Resume Examples & Samples
- Safety/People
- Must have current and/or previous Team Lead, Group Lead, Production Assistant, Cell Associate or Supervisor experience
- Must be willing and able to work weekends on a regular basis (estimated at equivalent to 1 weekend every 3-4 weeks)
- Experience with GMP/ISO procedures
- Experience working in a fast paced production environment
149
Senior Controls Engineering Specialist Manufacturing Operations Resume Examples & Samples
- Perform engineering assignments associated with various engineering activities
- Monitor processes; comply with safety, quality, & production requirements; and maintain reports & documentation as required
- Conduct routine operations & tests, perform analysis, and provide data for presentation
- Troubleshoot & resolve routine problems, and assist in resolving more complex issues
- Ensure parameter-driven requirements for components are met (this includes the ensuring the proper calibration and function of equipment)
- Maintain oil quality and continuously-improve oil filling technology at the plant
- Assist with the implementation of 5-S and Lean Manufacturing concepts
- Act as the local Subject Matter Expert for oil quality & component processing, and serve as a Trainer for operations development
- Serve as Project Manager for process improvements
- Manage process changes and ensure compliance to design specifications & QMS (Quality Management System) documentation
- Other duties may be assigned, as required
- Associate’s degree in an Engineering-oriented discipline with 7 years of professional experience working in engineering and/or manufacturing roles; OR
- Bachelor’s degree in an Engineering-oriented discipline with 5 years of professional experience working in engineering and/or manufacturing roles
- Associate’s degree in Electrical Engineering (i.e. ASEE) or related fields of study
- Experience supporting the installation, maintenance, operation, and repair of specialized manufacturing equipment in a factory environment; experience working in a union environment is a plus
- Hands-on experience with electro-mechanical Instrumentation and Controls [I&C] systems; especially Rockwell Allen Bradley and/or ABB automation technologies (e.g. RSLogix software, SLC-500 controllers, AC500 PLC, etc.)
- Experience with SCADA (Supervisory Control And Data Acquisition), PLC (Programmable Logic Controller), and/or other Industrial Control Systems [ICS]; proven experience with PLC Programming is a plus
- Experience working with the manufacturing of Power Products; experience working with the manufacturing of High-Voltage Instrument Transformers is a plus
- Experience working with the optimization of vacuum chamber and/or oil-purification systems
- Recent experience working with Lean Manufacturing and/or Six Sigma methodologies (e.g. Kaizen, 4Q, Process Improvement, Continuous Improvement, DMAIC, Gemba/Genba, etc.)
- Basic aptitude working with computer applications such as Microsoft Office (e.g. MS-Word, MS-Excel, etc.); experience working with SAP MRP is a plus
150
Director, Manufacturing Operations Resume Examples & Samples
- Organizing, managing and improving Operations activities in support of the development of new products or processes and the manufacture of clinical and commercial products according to cGMPs in a timely manner, right first time in accordance with Business Unit objectives
- Maintain the operational facility in the highest level of cGMP compliance per FDA, MHRA and customer expectations
- Ensuring the full compliance to OSHA and cGMP regulations of the entire manufacturing operations at all times and working in concert with QA, Engineering and Supply chain to ensure that the manufacturing operations area is performing as required to meet customer commitments
- Working with the Metrology, Engineering and Facilities groups on site ensuring compliance and effectiveness through maintaining appropriate Engineering standards, maintenance and calibration of equipment according to all required standards
- Staff to ensure the timely delivery and right first time execution of manufacturing operations for development projects and commercial batches
- Ensure that all operations are compliant with Catalent Safety Standards and OSHA requirements at all times
- Ensure Operational teams are adequately trained, knowledgeable and competent to perform all task requested
- Build, maintain and motivate a multi technology operations team capable of achieving all productivity targets and output requirements to service customers with product on time – In Full and Right First Time
- Assist the Site GM in establishing strategic directions for manufacturing resources and activities, and setting objectives to maximize the value of the organization's contributions
- Ensure continued operational efficiencies are realized with reliable schedule adherence, lower conversion cost and increased productivity
- Establish priorities and assure adequate resources to complete projects in a timely manner
- Assist in the introduction of new
- Represent the organizational unit as the prime internal and external contact for site manufacturing operations
- Ensure there are daily, weekly, monthly and quarterly manufacturing operations meetings to drive safety, cGMP compliance and adherence to plan
- Complete investigations in a timely manner and ensure root causes are correctly identified
- Represent Manufacturing operations on the Site Leadership Team
- Share responsibility for short and long term resources and facility planning, and perform managerial duties as required, e.g. budgets, personnel performance appraisals, etc
- Work directly with Validation, Quality Assurance, Analytical Services, Engineering, and Project Management functional areas to plan and implement the execution of cGMP activities in manufacturing operations for both development processes and commercial operations
- Work on complex problems of diverse scope where analysis of data requires evaluation of intangible factors. Exercises independent judgment in developing methods, techniques and evaluation criteria. Demonstrates success in technical proficiency, creativity, collaboration with others and independent thought
- Monitor and report progress of projects within agreed upon time lines, ensuring customer and Company objectives are met
- Responsible for participating and representing all manufacturing operations in Pre-approval Inspections, FDA audits and client audits
- Develop quality and business metrics for assessing of manufacturing
- Develop and manage the budget requirements for each fiscal year. Agree with GM and organize the purchase of appropriate capital items as required for projects
- Use Lean Six Sigma tools in day to day operations and to improve the operation according to the Site plan
- Ensure all company and site policies are adhered to and ensuring appropriate company disciplinary policies are followed consistently
- Liaise with vendors and suppliers as a technical representative
- Keep abreast of technical and regulatory developments in the pharmaceutical field which are directly/potentially applicable to Oral Solids, Zydis ODT products, Softgel Technologies services, and technologies
- Other responsibilities as assigned
- A minimum of 8 years’ experience in Pharmaceutical Operations with 4 years’ of this being in a managerial position
- Significant experience with Oral Solid Dose manufacturing and production processes and
- Experience working in a highly regulated environment and managing teams of >25 is necessary
- Experience in logistics/planning of commercial manufacturing operations is
- Clear leadership qualities and demonstrated success in management of change
- Has extensive understanding of pharmaceutical industry and contract services business issues and trends is preferred
- Must have knowledge of regulatory requirements for OSHA and Food and Drug Administration federal agency
- Analytical ability, both interpersonal and issue-related; good judgment and ethics; professional presence and demeanor; strong interpersonal skills and political savvy
- Strong business orientation and financial skills
- Excellent negotiation and contracting skills
- Ability to “get the job done” and take responsibility for results without direct authority
- Ability to coordinate, facilitate and organize resources
- Ability to develop strategic relationships; strong verbal and written communication skills; excellent presentation skills
- Superior customer service orientation with strong follow-up skills and attention to detail
- Must possess good to excellent writing and PC skills with a knowledge base in Microsoft Word, Excel, Power Point, and Project
151
Purchasing Manager, Manufacturing Operations Resume Examples & Samples
- Raw Materials (limited)
- Maintenance, Repairs & Operations (MRO)
- Engineering Design and/or Contract Services
- Plant Support Equipment (i.e. Electrical Switchgear, Lighting, Compressed Air Systems, HVAC Equipment, Controls, Valves, Boilers, etc.)
- Professional Services
- Prior designated commodity and/or materials buying experience
- Advanced commodity knowledge
- Global (as applicable) and regional markets/supply base insight
- Cost driver structure
- Business, industry and commodity acumen
- Ability to multi-task and adapt priorities quickly
- Effective and advanced communication skills
- Advanced planning and analytical capability
- Advanced purchasing fundamentals
- Strategic Sourcing; RFQ/RFP
- Bid analysis/award
- Negotiation strategy & teammate coaching/development
- Supplier leadership interface
- Advanced, complex problem solving; able to identify key issues and effectively coordinate effort to achieve resolution across assigned team
- People leadership & teamwork; able to build alliances with focus on customer orientation
- Proficient in Microsoft Office suite products and SAP
152
Senior Director, Manufacturing Operations Resume Examples & Samples
- Required Competencies: Knowledge, Skills, and Abilities
- Advanced proficiency in MS Word, Outlook, and Excel
- Advanced proficiency in PowerPoint, Project and Visio
- Advanced knowledge of cGMP’s, compliance standards, regulations and guidelines in all major world markets
- Ability to deal appropriately with all major world regulatory agencies
- Requires flexibility and ability to multi-task
- Advanced written, oral, and presentation development and delivery skills
- Advanced organizational and time management skills
- Advanced critical reasoning and decision making skills
- Advanced teamwork and facilitation skills
- Ability to develop others, delegate and motivate
- Requires strategic thinking and the ability to work independently
- Ability to interpret/write general, technical and complex business documents
- Requires strong qualitative training skills: responsiveness, enthusiasm, humor, sincerity, honesty, flexibility and tolerance
- Advanced critical thinking and decision making skills
- Ability to solve routine and complex problems
- Demonstrated ability in financial management, leadership and systems thinking
- Bachelor’s degree required; preferably in related Science or Business
- 12-15 years’ relevant work experience required, preferably in an FDA regulated industry
- Experience working closely with senior level management
- An equivalent combination of education and experience may substitute
153
Manufacturing Operations Applications Manager Resume Examples & Samples
- Manage support for the application services under the current support model until transitioned to the agreed Target Operating model
- Manage our staff through the transition to the Target Operating Model working closely with other senior leaders to coordinate these activities as part of the overall transition activity for all services
- Design and agree the globally consistent Target Operating Model for the support of the Manufacturing Operations Management applications / service layer, as part of the overall BIS Operating Model design
- Shape and mobilise implementation and transition to the agreed support model, handing over to a permanent management team to take forward at the appropriate point in the process
- You will have experience in defining and changing application services across multiple geographies and experience in applications support and lifecycle management of Manufacturing Operations Management applications
- You will have experience of managing the successful transition of applications support ownership, along with experience of leading people through a period of significant change
- You will demonstrate the ability to lead through vision and values with authenticity, building collaborative relationships and facilitating change to deliver true customer focus
- You will be adaptable with strong communication skills, experience of driving continuous improvement and the ability to work effectively with individuals of diverse cultures, abilities and backgrounds
154
Senior Manufacturing Operations Finance Manager Resume Examples & Samples
- Bachelor’s Degree in Accounting, Finance, Business, Economics or related field
- Minimum of 5 years of finance experience including; general accounting knowledge, reporting, analysis, and project management with increasing responsibility
- Master’s Degree of Business Administration (MBA)
- Certified Public Account (CPA)
- Ability to work across functions at all levels
- Self-motivation and proven ability to lead others to drive positive change
- Financial Management Program ( FMP ), Corporate Audit Staff ( CAS ), or Plant Finance Leadership Program ( PFLP ) Graduate (GE Employees only)
- Ability to multi-task assignments and appropriately prioritize tasks to meet deadlines
- Excellent verbal / written communication skills to clearly and concisely report results
155
Manufacturing Operations Lead Resume Examples & Samples
- Partners with Manufacturing Supervisors and Value Stream Manager to establish daily department goals
- Facilitates value stream communications and process flow
- Serves as first point of contact for all production issues within value stream
- Coordinates preventive maintenance and 5S related tasks
- Assists Value Stream Managers and Production Planners in setting detailed production schedule as well as provide feedback for monthly SRM (Supply Review Meeting)
- Works with production operators to support their achievement of individual goals and objectives
- Support Manufacturing Continuous Improvement targets (CIPs)
- Supports new hire training coordination
- Supports all new product launches
- Works with other departments, department leads, trainers and engineers to resolve quality issues
- Analyzes data in order to optimize processes and eliminate waste within and across value streams
- Develop and maintains reports as required
- Reviews hourly, daily and weekly production rates against schedule
- Assists with quality non-conformance investigations and product dispositions
- Assist in development of SOP's, other control processes and practices
- Supports efforts to meet goals and metrics for the value stream
- Supports department communications across the value stream
156
SVP, Global Manufacturing Operations Resume Examples & Samples
- Drive net productivity while supporting revenue growth to increase gross margins over the current strategic plan horizon
- Assess the manufacturing footprint to maximize asset utilization across business units to drive process and optimize manufacturing strategy initiatives across the enterprise to reduce lead times and create a competitive advantage in customer service
- Drive working capital efficiencies through the supply chain achieving year-over-year performance improvements in inventory and working capital management
- Manage the business system and continuous improvement programs across this group, tracking and reporting on cost savings, cost avoidance, and operational efficiency gains on a routine basis
- Manage a direct team of operations leaders including Lean, Distribution, and Facility directors
- Build culture of excellence in quality standards and systems, metrics, and reporting for all manufacturing locations. Provide leadership in driving overall execution of lower working capital and overall product quality metrics
- Ability to strategically review, plan and due diligence, and integrate the manufacturing assets of acquisition candidates
- Partner with General Counsel to instill Environmental Health and Safety systems, processes, and standards across the enterprise that protect the workforce and the environment and exceed industry standards. Work to develop performance tracking and field expertise in performance remediation, developing enterprise-wide environmental and safety programs for internal and external reporting
- Provide talent management leadership to ensure continuous development of the supply chain and operations talent across the enterprise. Partner closely with HR to work towards best in class supply chain and operations capability through improved staffing process, campus relations, people development, and succession planning. Identify key skill and capability gaps and develop talent development strategies to support the long-term enterprise-wide business strategies
157
Manufacturing Operations Supervisor Resume Examples & Samples
- Bachelor’s Degree in Supply Chain Management preferred
- 3+ years of leadership and/or production management experience
- Proven analytical, problem solving and organizational skills
- Proficiency in Microsoft Office applications, including Word, Excel and PowerPoint
158
Director, Manufacturing Operations Resume Examples & Samples
- Direct manufacturing staff to ensure the timely delivery and right first time execution of batch-manufacturing activities
- Provide operations and strategic support for capital projects
- Maintain the operational facility in the highest level of cGMP compliance in accordance with FDA, MHRA and customer expectations
- Build, train, sustain and motivate a multi technology operations team capable of achieving all productivity targets and output requirements to service customers with product on time, in full and right first time
- Assist the Site GM in establishing strategic directions for the manufacturing operation and setting objectives to maximize the value of the contribution of the organization
- Develop and sustain an environment of continuous improvement, optimizing schedule adherence, refining operational efficiency, and increasing profitability and productivity
- Support the identification and introduction of new technologies
- Represent all manufacturing operations on the Site Leadership Team
- Work directly with Validation, Quality Assurance, Analytical Services, Engineering, and Project Management functional areas to plan and implement the execution of cGMP activities across all manufacturing operations
- Support project governance activities (e.g., S&OP and NPI)
- Responsible for participating in and representing all manufacturing operations in Pre-approval Inspections, FDA audits and client meetings/audits
- Develop and employ quality and business metrics for assessing productivity/profitability of manufacturing
- Develop and manage the budget requirements for each fiscal year. Agree with GM and VP Operations to organize the purchase of appropriate capital items as required for projects
- Keep abreast of technical and regulatory developments in the pharmaceutical field that are directly/potentially applicable to site manufacturing operations and growth areas
- Has extensive understanding of pharmaceutical industry and contract services business issues and trends. External/internal recognition in broad area of expertise; acknowledged expert with proven insight in extending boundaries of existing knowledge
- Has intimate knowledge of practices and interpretation of legal and regulatory requirements of OSHA and Food and Drug Administration federal agency
- Must possess good to excellent writing and PC skills with a knowledge base in Microsoft
- Word, Excel, Power Point, and Project
- Must have working knowledge of best in class clinical supply operations
159
Manufacturing Operations Supervisor Resume Examples & Samples
- Ensuring a safe working environment through modeling safe behaviors, leading audits/inspections, correcting unsafe behaviors, and utilizing proper work methods, procedures and equipment
- Incident investigation, problem solving and root cause analysis (EHS, quality, and production misses)
- Facilitate daily Tier meetings to communicate plans, review execution of plans, identify opportunities to improve and engage production teams in continuous improvement process
- Communicate with supporting functions, escalate critical operation issues
- Manages department spend, and implements cost control measures as appropriate
- Leads Lean Six Sigma Projects, Kaizens, and other Problem Solving efforts to enable Continuous Improvement in manufacturing operations
- Guides activities and personnel in order to achieve quality production, on schedule and at the lowest possible cost
- Develop and be accountable for metrics which monitor area performance, such as productivity, yield, customer complaints, operational costs, etc
- Manages employee performance in adherence to site policies and procedures
- Active member of the Prairie du Chien Site Extended Leadership Team: Leads site wide sub-teams and projects or improvement efforts as assigned
- Reports to a General Supervisor with responsibility for operations and employees in the same plant areas
- Off shift coverage and a willingness to be on-call as many operations run 24 hours a day
- High school diploma/GED or higher from an accredited institution
- Minimum of three (3) years of experience in a manufacturing environment
- Minimum of two (2) years of crew/team lead or supervisor experience
- Excellent team building, interpersonal, communication, prioritization, organizational skills, and computer skills
160
Manufacturing & Operations Program Director Resume Examples & Samples
- Provide deep and expert level experience in Manufacturing and Operations as part of a multi-disciplinary engineering based program team
- Lead and facilitate the Innovation Transition of Adaptive Products into Manufacturing; be the bridge between the Smart Systems team and the core businesses of Footwear, Apparel and Equipment
- Define and map the essential manufacturing and operational inputs that allow integrated technical program teams, stakeholders, and leadership to make informed decisions and align on the most critical program success criteria
- Apply “positive skepticism” with appropriate consideration and weighting of company goals against the objectives of the team and program deliverables, especially when coaching engineering program teams through complex issues
- Demonstrate mastery of vendor engagement practices, proposal evaluation processes, contract negotiation techniques, directing scope of work at highest value proposition levels, and ultimately successful delivery of contracted scope of work
- Draft, forecast, manage and optimize operational budgets; drive efficiencies in the process to reduce operational expenses YoY
- Drive and manage pricing negotiations with Contract Manufacturers and Suppliers for both FOB and NRE to hit or exceed business targets
- Identify key supply risks; assist with the drafting, negotiation and maintenance of Master Supply, RFQ and other Agreements
- Be a strategic contributor to Next Generation Supply Chain. Develop strategies to diversify our contract manufacturing base both in number and/or geographic locations
- Master's or Bachelor's degree in Engineering or related technical field
- Minimum 10 years of work experience in Manufacturing, Operations and/or NPI program management. PMP a plus
- Proven NPI, manufacturing and/or operational hardware program management leadership experience in the consumer electronics, fitness, or medical industry
- Proven history of engaging, negotiating and developing EMS contract manufacturers and suppliers
- Proactive, solution-orientation approach with a history of solving unique, complex problems that have a broad, inter-connected impact on the business
- Superior communication, troubleshooting, time-management, and analytical skills
- Available for occasional late afternoon/evening conference calls
161
Manufacturing Operations Supervisor Resume Examples & Samples
- Monitors daily progress/status and makes adjustments/corrections to ensure optimal performance and service
- Improves efficiency, quality and service of ongoing work
- Provides day-to-day direction to assigned team
- Implements and ensures adherence to service delivery standards
- Responsible for managing team for specific area within the factory
162
Manufacturing Operations Specialist Resume Examples & Samples
- Oversee the Supply/Demand matching for the Metals products out of Belgium Operations
- Period end management and coordination across Direct Metal Printing
- Operations coordination locally as well as with global counterparts in Logistics, Procurement, Planning, Spares management
- Definition of the Metals Manufacturing & SC Network strategy
- Definition and Implementation of the order fulfillment model for DMP, current and future products (Configure to Order, Build to Order, Build to Stock)
- Lead and Coordinate the manufacturing engineering change management across Direct Metal Printing
- Project Management for operations specific initiatives
- Plan of record management for Metals Manufacturing Engineering and SC Operations
- 3-5 years of experience in Supply Chain Operations and or Manufacturing
- Experience in end to end supply chain planning preferred
- Working knowledge of an ERP systems (preferred Oracle)
- Self-organized
- Well structured
- Analytical and data driven
- Work with a sense of urgency and accuracy
- Excellent interpersonal, verbal, written communication and analytical skills
- Comfortable interacting with all levels of employees across organizations up to senior leaders in the company
- Excellent Presentation skills
- Project Management Fundamentals
- Leadership and standing in driving topics to completion
- Good balance of operational grounding and strategic direction setting
- Expert level English language skills
163
Manufacturing Operations Associate Resume Examples & Samples
- Performs varied and general tasks of a transactional nature involving the manufacturing process
- Follows detailed documentation and instructions to execute basic tasks such as assembling and building product, cabling or installing servers
- Basic mathematics and reading comprehension skills
- Strong manual dexterity
- Basic teamwork skills
164
Manufacturing Operations Resume Examples & Samples
- Experience with practical application of safety programs
- Experience with application of engineering practices
- The application of design for manufacturing practices. Full application of Just-In-Time manufacturing (JIT) principles
- Knowledge and experience with a union environment
165
Manufacturing Operations Resume Examples & Samples
- A minimum of 3 years direct supervisory or similar leadership experience
- Prior knowledge and/or experience advising high performance work groups and experience with implementation and monitoring of Statistical Process Control systems, ISO9001 processes
- Ability to jointly lead work groups with Union leadership a plus
166
Manufacturing Operations Resume Examples & Samples
- A knowledge and prior implementation of cellular manufacturing, J.I.T. and S.P.C.. is required
- Experience in Detail Process Planning, including specifying speeds, feeds, tooling , fixturing, and gaging
- Computer oriented (CAD, Network/software, PC applications)
- Practical application of ergonomics
167
Senior Director Manufacturing Operations Resume Examples & Samples
- Provides leadership and mentoring in the development and execution of tactical and operational plans, including quality, new product introduction, manufacturing engineering, inventory management, demand and flow management, lean and other continuous improvement initiatives
- Develops and executes annual manufacturing and operational plans, including production, cost reduction programs, capital spending requirements, manufacturing engineering and maintenance. Develops annual operating budget in support and accomplishment of the business goals and business unit operational plan
- Continuously identifies improvement opportunities by securing relevant information, asking effective questions and guiding the manufacturing team to implement improvements
- Drives operational alignment and continuous improvement using a variety of lean techniques. Introduces continuous improvement techniques (Lean) to the manufacturing environment in a meaningful way
- Participates in Senior Staff meetings designed to establish and drive long-term company strategies
- Takes a leadership role in the local organization supporting the corporate quality compliance program
- Resolves problems relating to materials, operations, quality or other factors that may result in production delays
- Develops the technical capability of the manufacturing workforce and leadership through on-going training and education
- Is responsible for driving organizational effectiveness and for ensuring high levels of organizational health
- Maintain facility compliance to all OSHA and Safety requirements
- Minimum of a Bachelors Degree, Advanced Degrees MS or MBA preferred
- Leadership and management experience in developing high performance teams across multi-department organizations
- 10+ years experience at a functional level in a multinational organization with 5 years at a senior level
- Experience in business operations management and a solid track record in delivering results in a dynamic and growing manufacturing business
- Ability to operate effectively across organizational boundaries from product design through distribution
- Previous experience of managing New Product Introductions in a related high technology and dynamic industry sector
- Experience in promoting a culture of continuous improvement through lean manufacturing and 6 sigma methodologies
- Previous management experience in a regulated environment (FDA) would be a distinct advantage
- Thorough understanding of financial measurements and P&L responsibility
- Must have excellent interpersonal, organizational, presentation and motivational skills as well as the ability to be an enthusiastic champion, motivator and leader for all levels of the organization
- Solid leadership, management and communications skills
- Strong analytical and problem solving aptitude
- Excellent computer skills and knowledge of Information Systems management tools