Quality Operations Resume Samples
4.8
(102 votes) for
Quality Operations Resume Samples
The Guide To Resume Tailoring
Guide the recruiter to the conclusion that you are the best candidate for the quality operations job. It’s actually very simple. Tailor your resume by picking relevant responsibilities from the examples below and then add your accomplishments. This way, you can position yourself in the best way to get hired.
Craft your perfect resume by picking job responsibilities written by professional recruiters
Pick from the thousands of curated job responsibilities used by the leading companies
Tailor your resume & cover letter with wording that best fits for each job you apply
Resume Builder
Create a Resume in Minutes with Professional Resume Templates
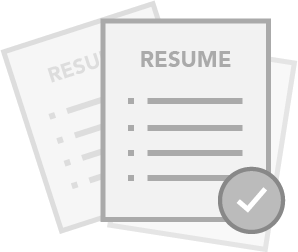
CHOOSE THE BEST TEMPLATE
- Choose from 15 Leading Templates. No need to think about design details.
USE PRE-WRITTEN BULLET POINTS
- Select from thousands of pre-written bullet points.
SAVE YOUR DOCUMENTS IN PDF FILES
- Instantly download in PDF format or share a custom link.
ML
M Lubowitz
Mariane
Lubowitz
5519 Mohamed Curve
New York
NY
+1 (555) 818 2179
5519 Mohamed Curve
New York
NY
Phone
p
+1 (555) 818 2179
Experience
Experience
Chicago, IL
Quality Operations Manager
Chicago, IL
Muller-Macejkovic
Chicago, IL
Quality Operations Manager
- Assist Plant QA Manager in the preparation of the Performance/Potential Appraisals for the Quality Operations related functions
- Facilitate and drive development of practices so that relevant parts of the manufacturing processes are continually improved
- Provides technical and business consultation to project development team and customer departments
- Assists with scorecard and other report development and production
- Champions performance improvement efforts
- Responsible for supporting and coaching Plant Quality Managers and launch managers on Quality tools
- Develop & Implement Improvement tools / indicators (like IDI)
Detroit, MI
Manager, Quality Operations
Detroit, MI
Ritchie, Hegmann and Jacobi
Detroit, MI
Manager, Quality Operations
- Directs and manages quality auditors, metrology personnel, department resources, and continuous improvement efforts to achieve the most efficient quality output as possible
- Ensures timely resolution to audit findings and customer complaints
- Utilize PMI strategies and techniques to manage Scope, Time, and Budget
- Maintain clear communication paths with stakeholders
- Conduct routine resource reviews with project Teams and management
- Review operating procedures to ensure compliance with all related procedures, instructions and the Quality Manual
- Investigate and ensure implementation of the corrective actions associated with non-conformances, including, customer audits and complaint reports
present
Dallas, TX
Director, Quality Operations
Dallas, TX
Brekke Group
present
Dallas, TX
Director, Quality Operations
present
- Quality oversight for decisions regarding quality and compliance for all batches and products, including discrepant batches (investigations, retesting and re-inspections). Manages the review of complaint investigations. Makes full batch rejection and recall decision in conjunction with Vendor Quality Manager and Executive Director, Quality Ops
- Oversees the establishment of all systems, procedures and specifications affecting product quality (e.g., batch records, SOPs, validation protocols and reports) to minimize errors and eliminate the possibility of non-compliant products being produced or released
- Provides leadership and direction and ensures achievement of all functional accountabilities
- Ensures support during Health Authority inspections of CSPs
- Represents Quality for establishment of Company-wide quality policies, strategies and practices
- Works with Quality Management to set site goals and objectives, determine policy and strategic direction, establish and oversee the site budget and coordinate site management
- Establishes and manages the Quality Operations budget for immediate group
Education
Education
Bachelor’s Degree in Microbiology
Bachelor’s Degree in Microbiology
Emory University
Bachelor’s Degree in Microbiology
Skills
Skills
- Strong knowledge of statistics and quality engineering / failure investigation techniques
- Knowledge of quality concepts and statistical tools
- Strong communication skills, negotiation skills, ability to work with all levels of the organization
- Ability to build strong relationships with internal and external customers
- Ability to make decisions which will effectively support the business and company policies
- Intermediate to Advanced proficiency in Word, Excel & Powerpoint
- Ability to organize and follow up on multiple priorities
- Strong analytical and problem solving skills and critical thinking abilities
- General knowledge of computer usage and applications
- Excellent oral communication and technical writing skills
15 Quality Operations resume templates
Read our complete resume writing guides
1
Senior Quality Operations Manager Resume Examples & Samples
- Has authority to stop production, issue product holds (stop orders), make decisions about budgets and people accountability, release products and sign off on project milestones (i.e. New Product Introduction)
- Maintains positive agency relationships-liaisons with regulatory agencies upon site inspections and participates in external technical forums
- Responsible for site education of non-Quality Assurance employees along with professional development of the site Quality Assurance team
- Provide leadership and coaching for the Quality Control team and ensure the timeliness of testing of our products manufactured
- Support and participate in the plant-wide efforts to reduce scrap and rework costs, and to identify root causes and solutions for quality defects
- Ensure the meaningful and timely resolution of Quality records including CAPA's, PSR's, and PQR's
- Coach the Quality teams on the tools and practices required to drive day-to-day improvements in the quality of our processes
- Work with Manufacturing, Engineering, Design, , Validation and NPI teams to drive changes that will reduce quality issues and result in higher long-term reliability
- Leverage our supplier quality and material resources to make real improvements in the quality of supplied materials
- Protect the integrity, effectiveness and timeliness of our change validation process
- Work seamlessly with the Operations / Site Leadership / Commercial / RA teams to ensure the optimal performance of the site in meeting our customer, business and regulatory commitments
- Bachelor's degree (or high school diploma/GED) plus 4 years working experience and understanding of product development, manufacturing, quality control and servicing in a pharmaceutical environment
- Significant Multi-Modality Sites: Minimum 5 years Quality Assurance, Regulatory Assurance, or Quality Control experience in the pharmaceutical industry
- Small and Sites: Minimum 3 years Quality Assurance, Regulatory Assurance, or Quality Control experience in the pharmaceutical industry
- Minimum 1 year supervisory/management experience
- In-depth knowledge in the applicable regulations (GMP, ISO etc)
- Prior experience using word processing, spreadsheet, and presentation software
- Demonstrated experience with regulations in the pharmaceutical industry
- Strong communication skills (verbal and written), ability to communicate using English and / or local language
- Black Belt or Green belt certification and Lean manufacturing experience
- Proven managerial/leadership skills such as work planning, delegating and evaluating
- Demonstrated knowledge of Quality Management System tools, continuous improvement methodologies and in-depth understanding of site level products and related processes
- Demonstrated expertise to effectively communicate within all levels of the organization around concepts of design controls, design verification and validation activities; production and process controls; Corrective and Preventive Action (CAPA), complaints and risk management; product quality improvement using tools such as six sigma, DFR, etc
- Excellent oral communication and report, business correspondence and procedure-writing skills
- Proven mentoring and coaching abilities, demonstrated ability to motivate and inspire others
- Proven leadership skills (experience successfully managing people/projects/issues)
- Demonstrated ability to lead, acknowledge, develop, communicate and implement a strategy under crisis situations to ensure compliance
- Change agent with energy, passion and enthusiasm to drive change
- Demonstrated effective interpersonal, teamwork and networking skills
- Exceptional analytical, problem solving and root-cause analysis skills
- Ability to make decisions, even when under pressure and take ownership for assigned projects and programs
- Demonstrated analytical, process management skills
- Ability to multi-task and handle tasks with competing priorities effectively
2
Market Quality Operations Specialist Resume Examples & Samples
- Strong communication skills both verbally and written
- HEDIS experience
- Prior health insurance experience
- Prior work history in a fast paced sales environment or market office
3
Market Quality Operations Analyst Resume Examples & Samples
- Reporting and Analysis: develops and implements processes to track and trend quality activity. Provides and analyzes reports in accordance with the established timelines
- Acts as the HEDIS Coordinator, if applicable, and/or supports the HEDIS coordinator as needed
- Supports the data collection process for medical record review audit, continuity of care studies, and other activity depending on the line of business. Supports committee structure, as needed
- Interface with internal, external resources to ensure the successful completion of all projects
- Prepare presentations and communication materials on behalf of the Quality Operation team
- Coordinate and plan meetings
- Bachelors degree in any field or equivalent work experience
- Possess strong organizational skills
- Data analysis skills
- Ability to use and learn new software programs
- Familiarity with Humana’s operating systems
4
Head of Pvrm Quality & Operations Resume Examples & Samples
- Bachelor of Science degree; graduate degree in scientific discipline desirable
- Experience in quality systems, establishing and tracking performance metrics, compliance monitoring, the development and maintenance of SOPs and training programs, and PV systems/ databases
- Generally 12 years or more in industry with majority in Pharmacovigilance with prior oversight of PV compliance; quality and training; external contracts; and database systems
- Solid knowledge of and experience with FDA and EU regulations and ICH guidelines related to pharmacovigilance including safety monitoring and reporting in clinical trials, post-marketing surveillance, case processing, safety agreement requirements and reporting to Health Authorities worldwide
- Must have experience with industrial interpretation of regulatory expectations and with preparation for and management of company pharmacovigilance inspections by major global Health Authorities (e.g. FDA, MHRA, EMA)
5
Quality Operations Specialist Resume Examples & Samples
- Excellent communication and reporting skills with all levels of the organization
- Ability to accommodate a flexible work schedule and building location and variant work hours as necessitated by compelling business need
- Ability to work independently with strong mechanical aptitude
- Exposure to standard spreadsheet and word processing usage
- Thorough knowledge of product and quality control and demonstrated ability to problem solve
- Ability to work with WMS mainframe systems, reporting tools, and proficiency with Microsoft Office (Word & Excel)
- High School diploma or equivalent, required
6
Quality Operations Resume Examples & Samples
- Participates in collection and review of annual HEDIS data. Participates in annual planning sessions. Act as HEDIS Coordinator and/or auditors, as needed
- Participate in required audits to meet all accreditation and regulatory requirements. Implementation of corrective action plans. Assist with survey preparation and participate with survey process as needed
- Conduct Medical Record Reviews and coordination and continuity of care studies
- Participate in work groups and/or task forces that may include but are not limited to analysis and improvement activities, community outreach and partnerships, investigation of provider performance improvement inquiries and other state/Region projects
- Review potential quality of care issues following prescribed guidelines and implementation of appropriate/timely actions
- Participate in Quality Management/Peer Review committee meetings
- Active RN license in the state(s) in which the nurse is required to practice
- Minimum of five years of prior clinical experience in any area but preferably in an acute care, skilled or rehabilitation clinical setting
- Valid drivers license and/or dependable transportation necessary
- Proficient in the use of MS Office (Word, Excel, & PowerPoint)
- Must be able to travel 20%
- BSN or Bachelor’s degree in a related field
- Managed care
- Health Plan experience
- Previous Medicare/Medicaid Experience a plus
- Documented experience with tasks/projects requiring detail oriented focus
- Experience with CGX, CCP2, and QMS
- Bilingual is a plus
7
Quality Operations Market Specialist Resume Examples & Samples
- 3-5 years health plan and/or administrative experience
- Valid driver’s license and ability to travel
- Clinical Quality and/or Health Plan experience
8
Quality Operations Market Analyst Resume Examples & Samples
- Bachelor degree and/or equivalent work experience
- Comprehensive knowledge of all Microsoft Office products, with emphasis on Excel & Access
- Excellent communication, analytical, time management and organizational skills
- Familiarity with various data operating systems
- Knowledge of NCQA, CMS and State requirements
9
FRO Data Quality Operations Analyst Resume Examples & Samples
- Engage with the Regional Finance DQ team, Finance, Chief Data Office (CDO) contacts in the analysis of DQ indicators (e.g., adjustments, regulatory/audit comments, process re-engineering reviews, and other sources) and subject those that qualify as issues to Citi’s Issue Management & Resolution (IMR) process
- Evaluate data quality issue submissions and proposals for completeness, materiality, clarity, and relevance to Finance objectives and priorities
- Drive the timely progress and resolution of assigned DQ issues in collaboration with CDO, Operations & Technology, system/process owners, and other subject matter experts
- Collaborate with other regions’ FRO DQ teams in addressing common issues and adopting best practices
- Execute DQ-related projects as may be required by Regional Finance DQ Lead or FRO Data Management Lead
- Minimum 5 years of progressive experience in major US banking institutions’ financial or regulatory reporting processes and systems
- BS in Business, Finance, or Information Systems Management from an accredited university or college or equivalent work related experience
- Industry certifications (e.g., Certified Information Systems Auditor, Certified Information Management Professional, Six Sigma Black Belt, Project Management Professional) an advantage
- Strong background in data mining, analysis, reporting, and resolution of system data quality issues
- Highly effective English oral and written communications and presentation skills for senior-level stakeholders
- Demonstrated ability in owning and completing concurrent deliverables in a fast-paced, virtual team environment
- Proficiency in MS Excel and Powerpoint; working knowledge in MS Access a plus
10
Head of Data Quality & Operations Resume Examples & Samples
- Management of a small team
- Setting data quality business rules to ensure high quality consistent data, including standardising, data manipulating and de-duplication methodologies from entry, storage and management
- Understand, audit and monitor data from various sources
- Ensure de-duplication methodologies, standardisation rules etc. are optimally set
- Define key performance indicators, reporting against data quality
- Define data quality rules and work with Information Management team colleagues to define business rules
- Data validation, issue identification and issue resolution
- Proven experience in data quality
- Proficient in SAS Data Management in particular DataFlux. Experience of using the Loqate module would be beneficial
- Knowledge of PowerShell, SAS LSF workflows, Tableau advantageous
11
Rnea Quality & Operations Excellence Manager Resume Examples & Samples
- Secures Ericsson Service Delivery Model (ESDM) implementation
- Adherence to ESDM and the updates on all the objects, covering Strategies, Functional models/blueprints, Frameworks and processes
- Drives the Operations Maturity Model implementation
- Creates and deploys the service delivery quality strategy and culture within Region Operations
- Develop and secure the effective understanding and implementation of Ericsson corporate requirements through the framework of EGMS, in Region Operations
- Manages proactive and reactive improvement programs focused on Quality and Innovation for Region Operations
- Service Delivery Local Process driver
- Drive & Support transformation project
- Minimum 5 years work experrience and minimum 2 years experience in process management, driving 2 or more cross functional process improvement projects in large corporates, bonus if in multiple countries
- Proficient in English speaking & writing, bonus if can speak Mandarin/Japanese/Korean
- Preferred black belt certification in lean six sigma for services (DMAIC)
- Proficient user of MS Visio for process mapping
12
Data Quality & Operations Analyst Resume Examples & Samples
- Help set data quality business rules to ensure high quality consistent data, including standardising, data manipulating and de-duplication methodologies from entry, storage and management
- Maintaining high quality of data by setting on-going checks and validations
- Work with the Data Engineers and Solutions team to form a data eco system with on-going quality checks and validations to ensure a high level of accuracy
- Help define data quality rules and work with Information Management team colleagues to define business rules
- Support test plans
- Own all first and third party data relationships and ensure that data is supplied effectively, securely and on time
- Be responsible for ensuring third party processes for data handling and management are established, maintained, implemented and measured
- Place appropriate controls and alerts to make sure all data feeds are supplied as agreed and securely
- Establish good working relationships and communication channels with relevant departments
- Provide project support where necessary
- University degree with a preference for a numerate, computer science, information technology degree with 2.1 or higher (or equivalent)
- Proficient in a data quality tool (SAS DataFlux is ideal otherwise others like Trilium, Informatica etc will do)
- Proficient in Microsoft SQL Server
- Good level of computer literacy
- The aptitude to quickly understand information, business models and the marketplace
- Always setting a high level of professionalism
- Ability to establish credibility and develop effective business relationships with colleagues
- Team player – ability to fit in with team and department colleagues
- Proven passion for data
- Pragmatic and detail orientated
- You will need to have a strong interest in 'big data'
13
Data Quality Operations Analyst Resume Examples & Samples
- Perform root cause and impact analysis related to data issues
- Convey complex technical issues/problems to developers in a clear and concise manner recommendations in the form of remediation
- Knowledge of databases, included big data technologies
- Knowledge of programming and software development lifecycle (SDLC)
- Exposure to agile development methodology
- Analytical with strong problem solving ability
- Strong prioritization and time management skills
- Ability to design and implement operational metrics
- Scorecards
- Thresholds
- 3+ years of relevant employment experience
- 3+ years writing technical requirements and business logic
- Exposure to the following a plus: Hortonworks, Hadoop, Teradata
14
Senior Analyst, Data Quality Operations Resume Examples & Samples
- Work closely with cross-functional team of technical and business experts, operational teams and managed services teams to identify and solve data issues
- Assist in preparation of Monthly Operations Review (MOR)
- Design and build enhanced ticketing metrics and automated alerts
- Technical Writing requirements, event summaries and recommendations (etc.)
- Process Modeling
- Knowledge of referential and large data formats and file structures
- Ability to apply the principles of data quality standards
- Convey complex technical issues/problems to programmers in a clear/concise manner
- Excellent data analysis skill
- Organized, structured, methodical
- Dashboards
- 6+ years of relevant employment experience
- 6+ years writing technical requirements and business logic
- 3+ years process documentation and depicting data lineage
- 3+ years interpreting data models, data dictionaries and queries
- Ability to write moderately complex SQL queries, PL/SQL a plus
- Knowledge of account, device, service, operations and marketing domains
- Exposure to the following a plus: Informatica, Tableau, Metric Insights
- Bachelor's degree required with related experience, or an equivalent combination of education and experience from which comparable knowledge and abilities can be acquired. Ability to analyze complex data, business processes, and information flow needs. Must have excellent communication skills with the ability to drive data quality concepts and solutions
15
Head of R&D QAC Quality Operations Resume Examples & Samples
- Managing Performance: Ensure every employee knows what is expected of them, what it takes to be successful, and how they are progressing. Hold everyone accountable to achieve results while demonstrating Shire values
- Developing People: Help employees continually grow through challenging opportunities so they can realize their potential
- Fostering a Brave Culture: Show employees what Brave looks like by being a role model. Create the environment in which people are able to be Brave and a culture where any risks are always in compliance with applicable laws and regulations
- At least 10 years of pharmaceutical experience
- Ideal candidate will have broad experience in product development, clinical operations, regulatory compliance, quality management systems, IT systems, training and education and at least 7 years of direct management experience
16
Quality Operations Resume Examples & Samples
- Active unrestricted RN license
- Education: BSN or Bachelor’s degree in a related field
- Medical record reviews for Quality of Care issues
17
Quality Operations Teamlead Resume Examples & Samples
- Manage the activities of a defined team of QA personnel. Management responsibilities to include day to day work allocation and prioritisation, performance and output quality review, coaching, training, internal communications and general personnel assistance during the course of their duties
- Actively support all defined Plant goals and objectives
- Co-ordinate all Six Sigma activities across the site
- Lead QA Manufacturing on existing products & new product development/transfers
- Responsible for recruitment, development and training of all QA Manufacturing Support personnel
- Work closely with other areas of QA and the business to promote compliance
- Administration/implementation of Traceability for C of C documentation, DHR systems
- Establish and administer Operator Inspection programme and provide initial training certification as required on an ongoing basis to support objectives
- Maintain manufacturing audit inspection and activity
- Implement and maintain CSOPs to ensure total compliance in areas of responsibility
- Resolve problems & eliminate constraints to ensure project targets are met
- Ensure that all relevant Quality Data is recorded, reported and actioned in an efficient manner. (Scrap, MRR etc.)
- Represent QA manufacturing at monthly CAPA meeting
- Be responsible for the release of product to the sterilization contractor for the plant
- Ensure that all DHRs are complete and accurate via appropriate system controls
- Identify and carry out required Quality inspection training
- Ensure resources are available for complaint investigation when required
- Ensure the plant complies with GMP, ISO and QSR requirements
- Manage repack from a QA perspective
- Ensure effective and timely communications both oral and written (weekly/monthly written reports, Project updates, daily / weekly direction to Quality personnel)
- Support preparation of and maintenance of Quality Process Specifications (QPS), Quality Control Test Specifications (QCTS), Raw Material Specifications (RMS) etc
- Represent Quality in Planning/Customer Service meetings to support timely delivery of service to ensure continuous supply of good product to distribution
- Co-ordinate the activities of the QA Manufacturing Support group in managing Operator Certification
- Ensure effective and timely closure on all Corrective Action Requests, Failure Investigation Reports and Close Call Investigation
- Maintains standards of housekeeping & GMP requirements
- Ensure QA Manufacturing personnel maintain a systematic control of documents
- Represent the Quality function as required by management
- Continuous Improvement Focus
- Demonstrate standards of leadership – Managing complexity
18
Director Quality Operations Resume Examples & Samples
- The site Director Quality Operations shall perform the role of Management Representative for DePuy Operations plant at Cork and DePuy Ireland (Global Supply Chain)
- Responsible for Compliance and Quality System, and Microbiology/Sterilisation functions
- Participates as a key member of the facility management team for Cork plant
- Responsible for the recruitment, supervision, training and development of all QA personnel
- Establishes and maintains QS procedures and controls ensuring that performance and quality of the product conforms to established company and regulatory standards
- Maintains quality standards and procedures for processing materials into partially finished or finished material or product, including responsibility for calibration and metrology activities
- Ensures accurate maintenance of applicable device history and device master files
- Oversees the implementation and execution of inspections prior to the processing of raw materials/components, the monitoring of environmental conditions, the validation of all manufacturing and sterilisation processes, and the timely management reporting of internal/external quality results with conclusions for all required corrective actions
- Works closely with Operations at Cork and Leeds plants in a team based environment to insure process and product compliance with all relevant quality standards, including the formal certification of operations personnel to perform quality related inspection/audit activities
- Ensures new products are transferred into routine production effectively with all development documentation completed
- Conducts statistical analyses to assess the cost of, and determination of, the disposition of products or materials that do not meet standards and specifications
- Ensure active participation and support for all Health & Safety related activities
- Ensure that all Health & Safety requirements are fulfilled in accordance with the responsibilities defined in the Company Safety Statement
- To actively promote Health & Safety within the department and ensure Health & Safety is a goal for all direct reports
- Responsible for ensuring a systematic control of documents on the Cork site
- Ensure document control of all HSE procedures at the Cork site
- All employees are responsible for minimising both the environmental and health and safety effects of the work that they perform
- Establish and maintain QS procedures and controls to ensure that the quality and performance of the product conforms to specified company standards and comply with the recognised Regulatory Standards for all markets in which our products are sold
- Review and approve/reject all declarations of conformance for product under the control of DePuy (Ireland) as legal manufacturer
- Ensure audits are conducted in accordance with requirements of ISO 13485, FDA QSR 21 CFR Part 820 or other recognised regulatory standards for all markets in which our products are sold
- Management Representative DePuy Cork manufacturing site and DePuy (Ireland)
- Review and investigation of complaints for product manufactured at Cork and Leeds plants
- Quality System Activities within facility including agreed supplier audits
- Resolution of Quality issues within Cork and Leeds facilities
- Facility Operator Certification System and GMP training
- Pro-active approach to Work
- High Standards
- Excellent Communication Skills (written & oral)
- High Level of Numeracy
- Highly Computer Literate
- Planner & Organiser
- Bright
19
Director, Quality Operations Resume Examples & Samples
- A minimum of a Bachelor Degree is required, preferably in Engineering or Science discipline
- A minimum of 10 years’ experience in a GMP and/or ISO regulated industry is required, Medical device is preferred
- A minimum of 5 years of direct people management experience is required
- Experience in Project Management; Risk Management; Cost Accounting Principles; Quality Auditing; Operations Processes; Systems Development & Integration are required
- Process Excellence and Lean experience desired
- This position will be based in Elmira, NY and will require up to 10% travel, including potential international.Quality (Generalist)
20
Quality Operations Specialist Resume Examples & Samples
- Ensure that during the project phase all activities related to establishing manufacturing processes for Drug Substance comply with cGMP and applicable regulations and Novartis Quality Manual
- Ensure that all required Quality procedures are in place to start up the manufacturing processes
- Participate as a representative of the Operational QA in project teams (eg: Master Batch records, equipment, cleaning and process validation)
- Participate in the general QA activities and assist in the different areas of the QA function (Compliance /Release/Change control)
- Manage quality issues and investigations (e.g. deviations; trends, OOS) with the respective departments
- Perform review of GMP relevant documents for compliance with SOPs across several customer groups (e.g. TEDI documents, SOPs, documents etc.), including filing and archiving documents owned by QA
- Prepare, review major system documentation to ensure consistency with quality standards and quality of deliverables, related to department activities and other departments
- Coordinate within site and with relevant global Novartis group/s with respect to implementation of Novartis Pharma Corporate Quality Manual, Policies and any other legislative requirements on site
- Support in establishing and follow up on site Quality Plans
- Ensure all health and safety procedures are followed and maintain complete compliance to all mandatory trainings
21
Quality Operations Specialist Resume Examples & Samples
- Bachelor Degree in a Natural Sciences (i.e. Biology, Chemistry), Pharmacy, or Engineering
- This position requires knowledge of quality / compliance management as well as regulations and standards affecting APIs and Biologics
- Minimum of 2+ years of pharmaceutical, biopharmaceutical experience in Quality and/or Compliance (GxP) environment
- Experience in SAP, Trackwise are preferred
- Ability to quickly know products and processes in order to assess quality issues
- Total commitment to quality and maintain a high standard of work at all times
- Demonstrates the highest levels of integrity and a strong work ethic
- Good knowledge of GxP requirements and regulations
22
Senior Director, Quality Operations Resume Examples & Samples
- Lead quality operations supporting Clinical and Commercial product disposition and supply
- Participate at a leadership level on Clinical Product Development Teams and allocate resources to each clinical program in support of program goals
- Oversee the development and implementation of quality assurance plans for clinical programs. Collaborate with key stakeholders in Global Operations, R&D, Pharmacovigilance, Clinical Audit and Regulatory to ensure robust quality plans are in place to further project objectives
- Lead the investigation of US based complaints and develop and participate in leadership reviews of complaint trends
- Prepare and lead onsite GMP and GDP Health Authorities inspections at New Haven. Ensure appropriate support for Health Authorities inspections at Alexion Sites and/or Clinical Supply CMO sites as required
- Participate at a leadership level with peers across the business on the development of Alexion global standards
- Establish key objectives and metrics for evaluation of the effectiveness of the QMS supporting functions and lead Quality Management Reviews. Manage quality continuous improvements and CAPAs as required
- Development and manage strategic plan and budget for the New Haven Quality Operations function
- Lead and develop the quality training function for key stakeholders and staff
- Lead and develop a team of Quality Professionals allowing for career progression and succession planning. Provide coaching and development and establish performance objectives and monitor progress
- 12+ years’ experience in related Clinical and Commercial Quality leadership covering related GMP and Clinical quality assurance in both tactical and strategic capacities
- Established expertise and training in GxP systems. Extensive knowledge of global regulations and standards
- Experience with product supply across a global footprint with working knowledge of pertinent regulations
23
Director, Quality Operations, Syracuse Resume Examples & Samples
- Knowledge of science generally attained through studies resulting in BS in Natural Science (Microbiology, pharmacy, biology, or a related pharmaceutical science.) Masters degree preferred
- An in-depth knowledge of regulatory requirements for filing Biologics in the US and Europe including past productive interactions with US and European regulatory agencies for the development and manufacture of biologics
- Demonstrated proficiency in interpretation of FDA and EMA cGMP regulations for biologics
- Direct involvement in securing a BLA, or sBLA regulatory filing of a commercial facility or process
- Successful demonstration of Compliance Leadership effectiveness in quality assurance and compliance management of commercial biologics manufacturing in a global regulatory environment
- Demonstrated success as a strong team leader who uses past supervisory experience to develop departmental staff through effective feedback and coaching
- Proficiency in developing and managing departmental budgets
- 1600344
24
Director, Quality Operations Resume Examples & Samples
- Ensures that all products manufactured at Contract Service Providers (CSPs) are produced, tested, and released in compliance with SOPs, cGMPs and FDA regulations. Ensures systems, resources, and action plans are reviewed and decisions made to attain sustainable compliance
- Quality oversight for decisions regarding quality and compliance for all batches and products, including discrepant batches (investigations, retesting and re-inspections). Manages the review of complaint investigations. Makes full batch rejection and recall decision in conjunction with Vendor Quality Manager and Executive Director, Quality Ops
- Oversees the establishment of all systems, procedures and specifications affecting product quality (e.g., batch records, SOPs, validation protocols and reports) to minimize errors and eliminate the possibility of non-compliant products being produced or released
- Provides leadership and direction and ensures achievement of all functional accountabilities
- Ensures support during Health Authority inspections of CSPs
- Represents Quality for establishment of Company-wide quality policies, strategies and practices
- Works with Quality Management to set site goals and objectives, determine policy and strategic direction, establish and oversee the site budget and coordinate site management
- Establishes and manages the Quality Operations budget for immediate group
- Supports/leads initiatives that accomplish continuous improvement and cost effectiveness and enhance efficiencies and compliance of processes and procedures
- Oversees the Quality Operations functions of human resources including determining the strategic staffing plan, interviewing and selection, organizational development, managing resources, mentoring and coaching and counseling and performance management and compensation. Ensures all direct reports staff is trained in cGMPs, SOPs, company policies and safety and those employees meet the qualification requirements
- Reviews and assures adequacy of site staffing, skills, and headcount to support and maintain compliance with cGMP requirements for those management and exempt technical positions directly related to manufacturing and packaging of pharmaceuticals
- Representative on Commercial Quality leadership Team for the Americas
- Requires a Bachelors degree in a related science from an accredited college or university with a minimum of 12 years related experience in a regulated industry, preferably in a pharmaceutical environment, including at least 5 years of progressive management experience
- Prefer a Masters degree in a related science from an accredited college or university with a minimum of 10 years related experience in a regulated industry, preferably in a pharmaceutical environment, including at least 5 years of progressive management experience
- Experience with manufacture of sterile/parenteral products
- Able to resolve global issues with demonstrated ability to provide innovative solutions
- Ability to critically interpret problems and propose strategic solutions
- Able to lead multi-disciplinary/global teams
- Experience leading Health Authority inspections, experience with third party manufacturers
- Leader that can mentor and guide development of others
25
Head of Quality Operations Resume Examples & Samples
- Support Operations by ensuring outgoing quality meets expectations for Operations through a strong collaboration with internal & external customers,
- Be recognized as an expert in identifying and defining quality expectations of internal and external customers. Implement proactive approaches to ensure the right level of competitive advantage through leadership and continuous improvement
- Manage Quality through leadership and product expertise (RCA, Audit, Complaints, QMS etc…)
- Develop and implement robust quality systems and data analysis. Implement systems to increase the speed and quality of key processes and drive business and process improvements with tools like SPC, FMEA, Quality by Design, Quality Value Proposition
- Develop the necessary networking to ensure Quality systems and processes are in place,
- Report & monitor all Quality metrics at the appropriate frequency
- Identify proactively changes /or trends of customers and develop plans to meet these accordingly
- Support Product Development Process for the Division to ensure new products are developed robustly in a risk-based approach. Be a strong liaison between the company and various external parties including member of key customer supplier relationship teams and regulatory bodies like FDA, ISO, etc
- Ensure that appropriate standards (ISO, FDA, GMP etc…) are followed in the area of responsibility
- Develop the organization to ensure the team is able to achieve both current and future goals through rigorous performance management, succession planning and personal development plans
- Similar experience and/or similar positioning in Operations environment
- Strong experience in Pharmaceutical, Biotech, Food & Beverage or Chemical industries
- Strong expertise in Quality Management & Quality systems
- Solid Project Management skills including the ability to provide strategy, priority and direction
- Strong leadership skills including the ability to influence cross functionally
- Ability to work in a cross-functional environment, strong interaction with manufacturing, marketing, R&D and sales
- Experience in government regulations, customer needs and business needs and translate those needs into programs, policies, procedures that ensure products and services meet establish quality standards
- Proven experience in change management, intercultural environment and cultural change
26
Senior Director, Quality Operations Resume Examples & Samples
- Responsible for ensuring that all investigational and commercial drug products manufactured for Ironwood are manufactured in accordance with the requirements stated in applicable regulatory filings and in compliance with the cGMPs
- As a senior Quality representative for the company responsibilities include being the primary interface with business and system related issues at contract manufacturing and laboratory organizations (CMO’s). The interface is coordination with senior representatives of supply chain operations
- Develop the procedures and systems required by cGMPs, FDA Regulations/Guidance’s and Ironwood’s Policies, to monitor and control the quality of the drug substances and products
- Incorporate risk management principles into the management and decision making process, while promoting quality awareness and continuous improvement
- Create an environment of compliance and operational excellence
- Mentor, coach, direct, lead, and motivate a team of professional, technical, and administrative staff in focused, collaborative and constructively coordinated execution of quality operations duties. As it applies to investigational and commercial products, such duties include
27
Associate Manager, Quality Operations Resume Examples & Samples
- Must possess knowledge of cGMPs applicable to pharmaceutical and/or medical device regulations. Must have knowledge of hazardous/safety material handling
- Must possess written and verbal communication skills, interpersonal skills, strong work ethic, strong attention to detail skills, consensus gathering skills, strong organizational skills and a strong working knowledge of PC based systems including, Microsoft Office including Word, Excel and internal e-mail system (i.e. Outlook)
- Preferred knowledge would include experience with Laboratory Information Management Systems (LIMS), Trackwise, and/or Documentum in addition to knowledge of revision (document) control processes and/or methods in both hardcopy and electronic formats
- Minimum of an Associate’s or Bachelor’s degree, or equivalent experience or education, and 2-4 years experience is required. A Bachelor’s degree and 5 years experience in an Health Authority-regulated pharmaceutical and/or medical device industry is preferred. A combination of experience and/or education will be taken into consideration
28
Director, Quality Operations Resume Examples & Samples
- Provides managerial support, direction and coaching to subordinates; maintains departmental employee recruitment, selection, training, development, safety, promotion and retention levels to ensure proper and effective staffing
- Responsible for over 100 direct and indirect staff members
- Provides assistance to the Site Head of Quality; prepares and presents staff reports and other necessary correspondence
- Directs the work activities of analytical testing groups to assure product and components comply with specifications; also reviews, evaluates/modifies, as needed, test methods and procedures
- Oversees Laboratory Investigations (analytical & micro)
- Reviews and prepares annual budget for assigned areas of responsibility in the Laboratory Operations department
- Reviews and approves new and revised Standard Operating Procedures (SOP's) and other laboratory documents
- Directs the work activities of the Training and Review group to assure that all documentation is complete and accurate and that new employees are properly trained
29
Quality & Operations Excellence Specialist Resume Examples & Samples
- Develop and execute quality processes across all functions within the Packaging Group, including marketing, order management, document control, engineering, project management and finance to drive continuous improvement
- 4 year accredited degree
- 5+ years of experience specifically in a Quality or Operations Excellence role
- A Masters Degree in required field = Credit given for 2 years of work experience
- BS in engineering degree preferred
- 5+ years’ experience in a factory or project management environment
- Candidates with work authorization that would permit them to work for ABB in the US
- Significant knowledge of Operational Excellence practices, supply chain management and quality processes
- Excellent English written, verbal and presentation skills required
- Ability to travel 40% or greater is required
- Candidates with extensive US business experience highly preferred
30
Quality Operations Specialist Resume Examples & Samples
- Causal evaluation certification, e.g., HFACS, RCA, ACE, 5-Whys, Fault Tree Analysis
- Experience with causal evaluation methods and investigations
- Microsoft Office Word, Excel, and Power Point skills
- Knowledge of corrective action programs
- Ability to interview personnel of all levels during incident investigations
- Working knowledge of process instrumentation and controls
- Ability to work independently and be effective in team settings
31
Director Quality Operations Ethicon Resume Examples & Samples
- Champions the creation and maintenance of Credo-based environment in his/her area of responsibility, living Credo values, building trust and caring for people
- Develops and disseminate strategy for talent attraction, development and retention to enhance the Quality Operation talent pipeline
- Ensuring the plant has appropriate resources with the right competencies to execute the Quality System
- Champions cross sites, regions and franchises assignments to foster Global QA Leadership development
- Provides active link and partnership between the manufacturing sites and Marketing Companies. Partners across the J&J enterprise in the Region through the Quality& Compliance Councils to influence the external environment and Local Regulatory bodies including SHFDA, India State FDA bodies, PMDA
- Participates in an active collaboration with the other regional leaders in developing cohesive, strategic and tactical responses for the business needs and QA initiatives
- Foster resource leverage across plants and region, ensure alignment or harmonization where required and/or appropriate
- Executes responses to field actions and coordinates global response with the other regional directors and corporate functions
- Ensures manufacturing sites implementation of Quality Systems and goals are integrated in a cost effective and productive manner also in collaboration with franchise and enterprise teams
- Leads the Quality Operations staff in the understanding, development and deployment of PE methodology, continuous improvement and customer focus
- Supports manufacturing sites in the investigation, evaluation and implementation of actions to eliminate root causes of non-conformances
- Provides support to multiple Medical Device Franchises in the region, to enable businesses to meet local customer and regulatory requirements
- Liaise with the Region and source company manufacturing sites to improve the customer experience through proactive management of complaints. Ensures the manufacturing sites address all customer feedbacks and complaint in appropriate and timely manner
- Direct subordinates are site Quality Operations Managers
- Reviews and participates in personnel development programs necessary to provide employee movement through prescribed promotional patterns
- Evaluates and recommends staffing requirements to insure maximum utilization of personnel to fulfill department objectives
- Approves salary increases recommendations and recommends salary increases and promotions for direct subordinates, interviews applicants for job openings, conduct performance reviews and provides guidance to subordinates
- Ten (10) years related experience and/or training; or an equivalent combination of education and experience
- Five(5) years of active management experience including direct supervision and matrix management
- Successfully managed a multinational department and or significant QA project
- Identified need for and directed development and implementation of at least one major process or system improvement at site or regional level
- Developed (not hired) ready now successor for leadership position (Mgr.-level)
- Fluency in English mandatory – both verbal and written
- Japanese, Hindi and or Standard Chinese preferred
- Universal Leadership Competencies
- Self-awareness & Adaptability
- Big Picture Orientation
- Specific Technical Skills Required
- QSR/ISO 13485
- Operations Processes
32
Quality Operations Analyst Resume Examples & Samples
- Bachelor’s degree and a minimum of five years of management experience, preferably in a medical or other regulated field, or an equivalent combination of education and experience
- Prior experience in plasma center operations is desirable
- Effective interpersonal, leadership, organizational, technical and problem-solving skills
- Ability to understand, communicate, interpret and apply technical documents and instructions
- Ability to interact effectively within a multidisciplinary and diverse team
- Aptitude for working with production, financial marketing and other statistical data. Effective written and oral communication and presentation skills
- Must be able to handle multiple projects concurrently, have computer experience and have knowledge of FDA Regulations, Application of Good Laboratory Practices, and Application of Good Manufacturing Practices
33
VP, Aftermarket Quality & Operations Resume Examples & Samples
- Lead overall organization in development of Best in Class dealer and customer experience via our Uptime Center support processes
- Develop customer-centric quality metrics
- Manage all quality activities, fleet improvement initiatives and all campaigns
- Engage with Operations and Technology groups to ensure full support to manage all open quality issues with strategic focus on meeting quality targets
- Develop segmented approach for incoming dealer and customer calls to ensure we match appropriate resources and competencies to solve issues and concerns
- Create a culture of accountability within the dealer and customer support departments that will reduce the number of handoffs while improving the response times
- Integration of dealer and customer facing organizations into single organization, with goal of eliminating redundancies and improving the overall effectiveness and customer support
- Manage all aftermarket processes and systems projects that are core to supporting our dealer and customer
- Ensure AM needs are successfully delivered by new product projects
- Work with the GTO in developing a sustainable parts availability strategy and performance metrics that will ensure Uptime
- Manage all aspects and successful system roll outs Aftermarket business intelligence initiatives
- Benchmark industry best practices for warranty administration to ensure we eliminate unnecessary procedures, while managing the unnecessary exposure for GTS
- Provide overall back office support for aftermarket sales & marketing, customer satisfaction and soft product development departments
- Bachelor’s Degree or Technical Degree or equivalent, MBA preferred
- Formal training in leadership, communication and people skills would be valuable
- 5 years of senior line management experience
- 5 years Dealer Parts and Service operations experience
- 5 years Fleet maintenance management experience
- Needs to have a good understanding of the Volvo Group Businesses
- Good understanding of the commercial vehicle industry and business analyses
34
Quality Operations Manager Resume Examples & Samples
- Investigate policy violations across Audience Network and respond to operations team inquiries
- Partner with cross-functional teams to solve for potential policy violations with consistent messaging and process
- Improve integrity operations by understanding global and local challenges and needs, build solutions to address market segment
- Identify automation opportunities as we take down malicious actors at scale while shielding our partners from automated actions
- Identify best practices and trends in the quality landscape to benchmark our processes and practices
- BA/BS degree required
- 5+ years of experience in an online operations, project management or policy enforcement environment
- Ability to perform in a complex, high-stakes, fast-paced environment
35
Director, Quality Operations Resume Examples & Samples
- The Director Quality Operations will perform all job duties in full accordance with the Worldwide Policies on Information Asset Protection, maintain password(s) as Confidential, and protect Critical Business Information
- Recommends and guides implementation of functional strategies. Incumbent knows, understands, incorporates and complies with all applicable laws and regulations relating to DePuy's business activities and Policies and Procedures of the Health Care Compliance Program and Code of Conduct
- Manage the activities of metrology, calibration, FAS, floor and final inspection to ensure quality of products manufactured by DePuy with emphasis on continuous improvement
- Assist in devising and implementing methods and procedures for inspecting, testing and evaluating production
- Provides technical Quality support to assigned inspection and manufacturing area(s). Requires consistent application of standard and advanced principles, theories, concepts and techniques - examples include process excellence/six-sigma tools, formal DOE methods, etc
- Develops, implements and conducts/coordinates training in Quality Systems procedures to enhance efficiency, compliance in the areas of Product/Component Disposition, Non Conformance System, Corrective & Preventive Action System(CAPA), and Device History Records/Retention
- Fosters harmony within functional and other areas. Contributes to the functional milestones associated with specific projects and to cross-functional teams
- Provides coaching, useful feedback and direction to direct reports and teams. Holds people accountable for measurable results. Mentors and facilitates successful team behavior within and across functional areas and promotes the business value of diverse perspectives
- Performs audits as required. Gathers and analyzes data and identifies trends to improve quality assurance systems' overall compliance, effectiveness, and efficiency. Participates in Management Review, CAPA and MAP meetings
- Investigates internal and external system failures and ensures successful resolution. Maintains quality assurance systems' inspection readiness. Compiles budgets, short and long range planning. Provides detailed justification for capital requests. Maintains compliance with company policies in regards to all safety, QSR and environmental issues
- A minimum of a Bachelor's degree is required, preferably in an Engineering, Life Science, or related discipline. A Master’s degree would be an advantage
- A minimum of 10 years of quality and/or manufacturing experience in medical device field is required. A minimum of 3 years of people management experience is required
- ASQ certification in quality engineering is preferred
- In-depth knowledge and hands on experience with all elements of ISO/QSR requirements applicable to medical device design and manufacturing is required; Experience with FDA/notified bodies is also required
- Excellent organizational and team building skills; Knowledge and experience with computer software including Word, Excel, Power Point and Access
- The ability to influence at senior levels and across functions building strong networks internally and externally is required. Experience delivering results through influence in a highly matrix environment are also required. Strong experience and proven record motivating leading and developing staff, in a highly changing environment is required. Must be a proven change agent
- This position is located in Raynham, MA and will require up to 15% domestic travel
36
Quality Operations Specialist, Expert Resume Examples & Samples
- -----------------------
- High School diploma or equivalent
- 7 years of progressive experience in utility operations
- Experience with causal evaluation methods and investigations in the utility industry
- 2 years in a utility operations supervisory position
- Experience with nuclear corrective action programs and causal
37
Executive Director, Quality Operations Resume Examples & Samples
- 10 years or more of pharmaceutical industry quality operations responsibilities, with demonstrated and progressively greater achievements in
- Departmental leadership for at least 5 years
- Strategic planning and leadership
- Proactive quality compliance while optimizing operational efficiencies
- Responsibilities for quality management of products from multiple sites/CMOs, including a variety of dose forms
38
Senior Manager Quality Operations Resume Examples & Samples
- Bachelor's degree or higher in Biology, Chemistry, Engineering, Industrial Management, Operations, Quality or Manufacturing (other degrees in combination with relevant experience may be considered)
- 6+ years of relevant work experience in Quality Assurance
- Proven ability to establish collaborative working relationships; team oriented and must be able to work independently
- Working knowledge of current federal, local and international regulations
- Very good understanding of cGMPs, industry and regulatory standards and guidelines
- Thorough knowledge and understanding of Deviations/CAPAS/Change Controls
- Experience in reviewing and approving GMP related documents (i.e., SOPs, Protocols, Validation Reports, etc.)
39
Head, Quality Operations Resume Examples & Samples
- Assist with external regulatory inspections and corporate compliance audits
- Serve as a permanent QA member on project teams
- Ensure promotion of awareness of customer requirements throughout the organization
- Participate in and respond to all Health Authority, internal and external audits. Be or assign a GMP/QS spokesperson during external audits
40
Quality Operations Specialist, Senior Resume Examples & Samples
- 5 years of progressive experience in utility operations
- Experience with causal evaluation methods and investigations in
- BA/BS
- Experience in a utility operations supervisory position
- Experience with business process reengineering
- Causal evaluation certification, e.g., HFACS, RCA, ACE, 5-Whys, Fault
41
Quality Operations Manager Resume Examples & Samples
- Manage the in process control activities across the Hull site Manufacturing facility in compliance with relevant GMP and Quality Systems standards, specifically FDA Regulations, MDD and ISO 13485
- Work with QA to ensure the quality system framework is maintained and remains compliant
- Establishing and maintaining documented ways of working for all quality related activities within the manufacturing environment
- Facilitate and drive development of practices so that relevant parts of the manufacturing processes are continually improved
- Contribute to change control activities so that manufacturing team outputs are documented, communicated and closed out within defined timescales
- Lead root cause investigations into adverse quality trends and identify and control implementation of corrective actions
- Involvement in the GMP and Quality training of staff at all levels of the organisation
- Compilation and review of all batch records (DHR) for products manufactured in Hull to enable QA release of compliant products within defined timescales
- Investigation and resolution of failures, deviations and non-conforming products
- To ensure CAPAs, CARs, Customer Complaints and Deviations are correctly investigated and closed in a timely manner
- Contributing to audits (internal and/or external)
- Management and development of team performance to meet the needs of the business
- Significant experience of working in a Quality function associated with Medical Devices and/or Medicinal Products is preferred
- Science based degree or equivalent OR HNC or equivalent qualification and significant experience in a Quality related role
- Auditing experience (internal and/or external) is highly desirable
- Six Sigma training to Green Belt level is highly desirable
42
Manager Quality Operations Resume Examples & Samples
- Ensuring that all material and fabrication is certified in accordance with specified requirements
- Liaising with the Area Quality Manager to ensure that the Quality System meets requirements established in the Area Quality Manual
- Ensuring that Local Management Reviews of the Quality System are undertaken and reported in accordance with approved procedures
- Ensuring that Quality records are maintained (e.g. Audit Schedules, Audit Report file, CAR files, etc.)
- Develop the assigned annual operating budget, monitor budgeted performance to ensure adherence to budget, identify variances and implements cost reduction strategies when required
- Support and enforce the Compliance/Ethics program as described in the Corporate 'Code of Business Conduct'. Report possible or actual ethic violations to a member of the Regional Compliance Team or to direct Supervisor/Manager. Provide guidance and mentorship for direct reports related to Compliance/Ethics issues. Assist when requested with investigations into compliance/ethics investigations and reports. Maintain confidentiality of ethics issues and those who report possible or actual compliance/ethics issue
- Besides the above-listed, shall be responsible for other duties assigned by department manager or the company
- Minimum Degree holder in Quality Management
43
Technical Assistant Quality Operations Befristet für Monate Resume Examples & Samples
- Leading several projects and interacts with management on a day-today basis
- Managing Field Action reviews
- Coordinating and preparing Meetings and follow up on action tasks
- Actively participating of compliance initiatives such as Audit Readiness Programs, Audit Logistics, and Back-Room Support
- Interacting with several departments, consultants and clients
- Managing contract and PO database
- Tracking budgets and expenses
- Organizing complex domestic and international travel arrangements
- Preparing presentations, agendas and documentation
44
Quality Operations Manager Resume Examples & Samples
- Administers the deployment and utilization of resources for tactical day to day work. This includes working with Operations, Materials Management and QA to facilitate testing and release scheduling
- Administers the testing and controlling of raw material, finished product quality and in process quality, finished product quality and in process quality, assuring compliance with company standards and applicable government regulations
- Responsible for the evaluation and disposition of WIP and questionable raw materials
- Advises Business Units on inspection and testing procedures. Makes recommendations where necessary
- Initiates and maintains interplant communications of quality issues
- Maintains close interaction and network with peers at US Plants to address quality related issues
- Administers available resources to achieve a reliable, efficient and productive operation
- Facilitates QA support to new product launches to assure a successful implementation
- Fosters teamwork and supports total associate involvement
- Assists the QA Manager in the preparation of the Annual Departmental Budget
- Resides as back up to the QA Manager for signature authority and meeting representation
- Approves purchases and expense reports submitted by direct reports
- Analyzes plant reports for significant quality trends and report’s conclusions
- Supports Internal Regulatory Compliance Function as required
- Monitors Good Housekeeping practices, employee hygiene, and employee safety
- Participates in the development of procedures, specifications, cost control planning, self-inspection methods, and systems of QA. Enforces implements and follows up on all procedures and specifications
- Approves specification and process changes per applicable procedures
- Participates with Operations in developing, coordinating and implementing projects for improvement of processes and/or products
- Provide feedback to operations on problems related to quality and/or compliance
- Supports/initiates investigations of non-conformances
- Supports Operations in evaluation and implementation of action plans to eliminate root causes of non-conformances
- Support **and approve validations as required
- Provides support to plant wide initiatives such as ergonomics, safety, environmental, etc
- Responsible for the revision of the Device Master Record
- Actively supports other plant functions in the implementation of company programs and projects
- Enforces, promotes and observes all safety, industrial hygiene rules and regulations established by the Company
- Participate and support safety initiatives within the facility, such as emergency response, ergonomics, safe behavior program, etc
- Be aware of, and comply with, Company policies on Safety
- Report accidents, incidents, near misses, and hazardous situations in a timely manner and participate in the corrective action process
- Ensure proper use and maintenance of all personal protective equipment required to safely perform the job
- Ensure all personnel under their facilitation comply with all safety policies and procedures (Plant-wide and applicable to work area)
- Participate in the deployment of Safety policies
- Ensure department safety programs are implemented and maintained to meet corporate goals
- Assist Plant QA Manager in the preparation of the Performance/Potential Appraisals for the Quality Operations related functions
- Directly supervises QA Supervisors, **Quality Engineers, and non-exempt associates, Participates in the interview and selection of qualified employees for authorized job openings
- Trains, coaches and develops subordinates and Quality Operations function associates as valuable resources in the development of World Class Manufacturing initiatives
- Ensures that the disciplinary actions are executed in a fair and consistent manner, according to Company rules and policies
- Recommends salary increases and promotions for direct subordinates and Quality Operations function associates
- At a minimum, a BA/BS degree or equivalent in a Life Science, Engineering, or Physical Science
- Eight years of related experience in a World Class Manufacturing environment
- Three years of supervisory experience
- Physical Demands: Normal Office Environment
- Work Environment: Frequent travel, flexible to work on different shifts
- Contacts: Frequent contact with Ethicon facilities and Executive Management required
- English mandatory for all plants
- Spanish mandatory for San Lorenzo and Juarez
- Required proven leadership, teamwork, initiative, creativity, people and assertiveness skills
- Excellent oral communication and technical writing skills
- Ability to organize and follow up on multiple priorities
- Ability to make decisions which will effectively support the business and company policies
- General knowledge of computer usage and applications
- Knowledge of quality concepts and statistical tools
- Interpretation and application of ISO9001, **ISO13485, **ANVISA RDC 16, **CFR 21, Part 820, and **TGA standards
- Good decisions making skills. Erroneous decisions or recommendations, or failure to complete assignments would normally results in serious delays to assigned projects with considerable expenditure of time, human resources and funds
45
Director Quality Operations Ethicon India Resume Examples & Samples
- Champions the creation and maintenance of Credo-based culture and environment, living Credo values, building trust and caring for people
- Leads the Quality Operations staff in the development and deployment of key business, SC and Quality strategies, continuous improvements and customer focus activities
- Provides active link and partnership between the manufacturing sites and Marketing Companies. Partners across the J&J enterprise in the Region through the Quality& Compliance Councils to influence the external environment and Local Regulatory bodies
- Directs the Quality department engaged in the development of Design changes to existing Products/Processes/Packages throughout the product lifecycle
- Ensures the manufacturing sites assess QS effectively through internal audit and Management review and implement corrective/ preventive, improvement actions as appropriate
- Establishes and monitors metrics for the measurement of Quality indicators and Quality Costs to ensure effectiveness and value to the business
- Provides disposition for non-compliant products and assures escalation of potential quality or compliance problems to franchise and enterprise
- Ensures effective risk management processes are implemented to prevent unanticipated failure modes and ensure capability
- Ensures the manufacturing sites address all customer feedbacks and complaints in appropriate and timely manner
- May enable NPI localizations/customizations of solutions to deliver market appropriate product offerings, while ensuring adherence to Enterprise and Franchise Design control processes
- This individual has the necessary independence, authority and responsibility to initiate action to prevent nonconformities, enact remediation plans, identify and document quality problems, initiate, recommend, provide and verify solutions to quality problems and direct or control further processing and delivery of nonconforming product
- Direct subordinates are site Quality Operations Managers and staff
- Defines and ensures implementation of multiple new product development plans and programs
- Works effectively with marketing counterparts to prepare product pipeline strategies and to direct project execution
- A minimum of 15 years related experience and/or training; or an equivalent combination of education and experience
- Managed a plant-based organization (Quality or Operations) with multiple challenges; preferably in multiple companies and/or locations
- Experience in front-room role with FDA (or similar) inspection and Notified Body inspection
- Fluency in English mandatoryQuality (Generalist)
46
Manager Quality Operations Resume Examples & Samples
- Responsible to ensure that continuous improvement is made in all production MEQ quality deliverables
- Function as the primary point of contact for the operation in responding to critical customer issues, quality key measure performance and other customer specific initiatives
- Ensure that their plants successfully implement applicable world class quality systems and are certified / compliant with BOS, QS-9000, VDA 6.1, ISO/TS16949, etc. as appropriate
- Drive continuous improvement of post S.O.P. supplier development and quality performance. This includes leading the MQR and corrective action processes for supplier issues
- Assess and approve post S.O.P. supplier PPAPs and provide the appropriate technical support to help a supplier resolve a critical issue
- Development of manufacturing quality resource budgets staffing needs, participate in the interview process and add resources as needed
- Responsible to ensure that the quality team in their plants have the necessary skill levels and technical competence to execute their roles, by development and execution of individual development plans and performance reviews for each quality engineer that is part or their team
- Ensure that customer and internally identified quality issues are resolved using the Johnson Controls problem solving methods (8D Report, Problem Solving Document “PSD”, PCAD, Kepner-Tregoe, etc.)
- Being on-site and part of a resident team and providing support to the customer; preparation of necessary corrective / preventive actions, follow up, verification and release of corrective actions
- Assure that all quality activities are performed according BOS-, TS 16 949-, ISO 9000 standards and specific customer requirements
- Educated to degree level or equivalent experience
- Specific education and training in quality disciplines including QS9000, continuous improvement, total quality Management, PPAP, FMEA, control plans, DOE and SPC are also required
- Extensive experience within quality, preferably within the automotive industry
- Knowledge of the AIAG quality planning and control plan standard, FMEA, PPAP, dimensional layouts, gage/fixture design and performance/material testing
- People development and leadership experience is required
- Fluent German and English language skills
- Willingness to travel regularly
- Unique free space for your ingenuity and consistent implementation of good ideas
- Holistic work on complex tasks beyond the usual limitations of disciplines and responsibilities
- An international environment with people from 84 nations at our German sites alone
- Good development and career opportunities
- An authentic and open corporate culture
- The proverbial team spirit of Johnson Controls
47
Senior Director, Global Quality Operations Resume Examples & Samples
- Serve as the leader for Illumina’s global manufacturing groups in the production of medical reagents, instruments and consumable products
- Teach and lead improvements resulting in site operational metric improvements
- Drive measurable improvements in safety quality, material control, throughput, flexibility and cost
- Mentor site leaders, engineers, and shop floor supervisors to instill the disciplines to drive a transition to a higher level of quality and compliance
- Serve as a subject matter expert for quality operations in a regulated environment (cGMP or equivalent)
- Fully responsible for leading to achieve excellence in production and process controls
- Optimize in-process and final quality inspection efficiency
- Integrate quality systems with Illumina’s enterprise management systems and shop floor management execution system
- Develop, participate, and lead sessions in CAPA and problem solving methods
- Work with manufacturing department managers and team members to define the implementation strategies for continuous improvement across the organization
- Support policy deployment activities to define strategic objectives and metrics for the organization
- Develop appropriate tools and methods to sustain improvements across the organization
- Promote analytical problem solving through the application of statistical control methodology
- Develop data collection and retrieval tools for organizational use
- Build the world’s best team to guide Illumina to become the clear front runner in the delivery of high quality products and services
- The ideal candidate will be quick to establish collaborative relationships with business partners including quality’s corporate quality leaders, manufacturing site functional leadership, global supply chain leadership and others
- Responsible for the entire value chain of the product within Illumina’s manufacturing operations
- Supplier Quality
- IQC
- Manufacturing Quality
- Final Test/Outgoing Quality
- Post Sale Surveillance
- Customer feedback – voice of the customer
- 15+ years relevant experience; including 10+ experience in conducting compliance audits essential. Prior consulting experience helpful
- Demonstrated change management experience, guiding the organization to the desired state
- Ability to build a team leveling up and making improvements in the disciplines of compliance
48
Quality & Operations Excellence Manager Resume Examples & Samples
- Drive process improvements to improve business performance and customer satisfaction. This includes
- 4 years accredited degree
- Minimum 8 years of overall experience with 5 years specifically in Project Management, Quality, or Operational Excellence within a manufacturing or Industrial related environment
- A PhD/ Doctorate in required field = Credit given for 3 years of work experience
- Bachelor’s Degree in Engineering preferred
- PMI Project Management or Six Sigma Quality certification preferred
- Prior experience with Outdoor Power Utility Products or medium/low voltage electrical products
- Previous experience with Power Products such as Switchgear, Breakers, Relays, Transformers , Utility Electrical Products, and/or Industrial related manufactured products
- Candidates with previous US business experience highly preferred
- Previous experience complying with safety rules and programs; participating inl safety training as assigned
- Actively participate in safety programs in and outside of ABB factory
49
Manager Quality Operations Resume Examples & Samples
- Bachelor’s degree in a scientific or engineering discipline, or other related field, with an advanced degree beneficial
- Five plus years of management experience in a Quality and/or Operational role in the infant formula or a related highly regulated industry preferred
- Knowledge of the principles and practices of Quality Management
- Demonstrated excellent interpersonal, written and verbal communication skills, and demonstrated ability to prepare written reports/correspondence and presentations to senior leadership
- Managerial skills with ability to lead and develop teams. Experience in talent development and succession planning
- Demonstrated ability to effectively develop and manage both internal and external relationships with a broad range of stakeholders including senior management, floor level operations, customers, and key regulatory stakeholders. Experience in participating in regulatory related inspections preferred
50
Quality Operations Resume Examples & Samples
- Prior clinical experience preferably in an acute care, skilled or rehabilitation clinical setting
- Valid driver’s license and/or dependable transportation necessary (variable by region)
- Education: BSN or RN degree from an accredited nursing program
- Previous Medicare Experience a plus
51
Manager, Search Quality Operations Resume Examples & Samples
- Support and grow team of project specialists
- Lead all program management aspects and the successful execution of complex, cross-functional projects
- Support and act as an extension of executive level business project sponsors
- Build alignment among key project stakeholders and escalate key decisions as required
- Spot and creatively solve complex, cross-functional operational issues, often unique to each project
- Assemble and mobilize often large teams to execute on project objectives
- Continually refine best practices for cross-functional program management consistent with Facebook culture
- Manage and allocate operations budget
- Improve data collection efficiency and decrease costs
- 2+ years people management experience
- 5+ years in a management consulting, or similar strategic program management role for a tech or consumer company
- Experience in social media, software, Internet or digital media industries
- Experience working in and influencing global cross-functional teams
- Willing to wear multiple hats, able to deliver high-quality results in an often ambiguous and rapidly changing business environment
- Ability to influence at the leadership level
- Open to domestic and international travel
- Communicator with analytical skills and business sense
52
Director Quality Operations Ethicon India Resume Examples & Samples
- Directs the department engaged in the development of New Product Development and Design changes to existing Products/Processes/Packages throughout the product lifecycle
- Enables NPI localizations/customizations of solutions to deliver market appropriate product offerings, while ensuring adherence to Enterprise and Franchise Design control processes
- Ten (15) years related experience and/or training; or an equivalent combination of education and experience
- Integrity & Credo-Based Actions
- Results & Performance Driven
- Organization & Talent Development
- Differentiating Competencies
- Process Excellence
- Cost Accounting Principles
- Quality Auditing
- Systems Development & Integration
- Business AcumenQuality (Generalist)
53
Hedis Quality Operations Resume Examples & Samples
- Active unrestricted professional license
- Ability to be licensed in multiple states without restrictions
- Minimum of 3 years or more of prior clinical experience preferably in an acute care, skilled or rehabilitation clinical setting
- Ability to work independently under general instructions and with a team
- Valid driver's license and/or dependable transportation necessary
- Excellent computer skills and knowledge of Microsoft Word, Excel and PowerPoint
- RN or LPN license
54
Biological Critical Reagent Specialist Quality Operations Resume Examples & Samples
- Provide bioanalytical support to our Manufacturing sites, Oss Laboratories and other functional groups as needed
- Bachelor’s/ Master’s degree in Biology, Chemistry, Biochemistry, or a related biological science
- Experience (1–2 years for a Master’s and 2-4 years for a Bachelor’s degree) in the areas general biochemistry, analytical biochemistry or immunochemical techniques
55
Quality Operations Specialist Resume Examples & Samples
- Moderate work experience within own function
- Some work is completed without established procedures
- Basic tasks are completed without review by others
- Supervision/guidance is required for higher level tasks
- Previous experience in Healthcare
- Previous experience in Managed Care
56
Quality Operations Associate Manager Resume Examples & Samples
- Perform product disposition activities to ensure the timely supply of drug substance and drug product that meet commercial customer requirements while ensuring compliance with testing standards, SOPs, validation guidelines and regulatory filings
- Compile and maintain required disposition documentation needed for product disposition for BEM Contract Manufacturing Organizations (CMOs)
- Review disposition documentation from BEM CMOs and recommend disposition, escalating potential issues
- Create Certificates of Analysis, Certificates of Compliance, Release Notifications and other disposition documentation
- Ensure disposition documentation relative to BEM CMO materials and products are maintained
- Input required information into applicable enterprise systems (e.g. Trackwise, SAP) related to BEM products
- Assist in preparation of Quality Agreements, according to annual schedule and in managing the quality metrics programs in relation to CMO performance and represent Quality on cross functional teams
- Review CMO batch records working in alignment with CMO QA management and/or BMS person-in-plant at CMOs according to schedule and priority
- Work with CMOs to ensure PAI readiness plans are appropriate, and corrective actions are tracked to completion
- Provide BEM Quality support during self-inspections, internal audits, and regulatory agency inspections at CMO
- Support Supplier Relationship Management, Global Procurement, Supply Chain and MS&T teams for new projects, technical transfers programs, supplier selection programs, etc
- Review validation documents, deviations, and change controls and escalate any potential compliance gaps
- Escalate issues to BEM Senior Management to ensure that issues are resolved to support BMS business and compliance requirements
- Bachelor degree in a relevant scientific discipline e.g. Biochemistry, Microbiology, Pharmacy, Biological Sciences or related Pharmaceutical Science is required
- Minimum of 5 years’ experience in biopharmaceutical operations, with at least 3 years in Quality Assurance with expertise in medical device/drug combination products and packaging operations experience desired
- Prior experience with performing lot disposition is desired
- Candidates with a degree in Microbiology and/or prior experience with microbiology and aseptic operations are highly desirable
- Strong negotiation, communication and presentation skills across all levels both internal and external to BMS
- Able to rapidly adapt to changing environment and circumstances requiring flexibility, tolerance, and great sense of urgency while assuring that all cGMP and regulatory requirements are met
- Proficiency with the use of global systems (e.g. Trackwise, SAP, Microsoft Office)
- Be highly proficient in English – Fluency in German of advantage
57
Quality Assoc, Quality Operations Resume Examples & Samples
- Improve current practice to reduce cycle time using real-time review of batch records within the core manufacturing suite
- Review pertinent documents, records and reports such as Manufacturing Batch Records, lab test results, etc. against Standard Operating Procedures (SOPs) for accuracy and compliance to procedures based on Good Documentation Practices, regulatory requirements and internal guidelines
- Complete batch package release for drug substance and product, including communication of timelines and actions with other Shire and CMO sites
- Write, review, analyze and revise written Standard Operating Procedures (SOPs) and submit procedural changes as needed to meet Corporate, Divisional, Plant and other regulatory requirements
- Determine the logic, adequacy and effectiveness of Quality processes, systems and related requirements. Develop plans to correct identified risks including areas of non-conformance
- Participate in continuous improvement initiatives with the department and site-wide
- Provide training to employees on relevant Quality and compliance area(s)
- Participate in external assessments and audits by evaluating and solving product/process problems by providing technical and analytical skills
58
Senior Specialist, Quality Operations Resume Examples & Samples
- Manages aspects of the material control and/or release process as it relates to control of material for deviations and risk processing
- Performs review and approval for investigations, CAPAs, QCTS commitments, change requests, risks, IQ/OQ/PQ, validation, Master Batch Records (MBRs), LIMS CRs, etc
- Performs GMP walkthrough inspections to ensure compliance with cGMPs and regulatory requirements
- Actively participates in site inspections/audits by facilitating discussions with inspectors/auditors, fulfilling requests for information and presenting to inspectors on required topics as Quality representative for the IPT. Supports the preparation of regulatory filings
- Responsible for the review and release of intermediate or final bulk material for downstream formulation/filling for both domestic and international markets
- Prepares and submits release protocols to CBER. Prepares CoAs to support regulatory filings
- Performs duties of Quality Manager in his/her absence
- Minimum (5) years’ experience in a functional area, such as Operations, Quality, Technical Operations, Technology, and/or Engineering
- Strong understanding of cGMPs and regulatory requirements (domestic and international)
- Effectiveness and creativity in approaching and solving technical problems
- Proficiency in project planning and execution
- Demonstrated leadership expertise working with cross-functional teams
59
Associate Director, Quality Operations Resume Examples & Samples
- Reviews batch-related documentation, and ensures resolution of issues to release product
- Oversees the product and raw material disposition process
- Ensures all product-related Deviations and CAPAs are initiated, investigated and resolved, as needed
- Chairs the Material Review Board meetings to ensure non-conforming material is appropriately dispositioned
- Ensures change controls are initiated, evaluated and implemented appropriately for all regulated changes
- Develops and implements Quality on the floor process
- Ensures process control measures are in place and followed in product manufacturing
- Maintains and conducts internal site audits
- Maintain and reports monitoring and control metrics for process performance and product quality
60
Director, Quality Operations Resume Examples & Samples
- Unify entire organization through company wide initiatives to enhance, standardize, and broaden current quality systems
- Lead Quality Governance Committee (i.e. newly established direction to elevate and guide organization wide decisions)
- Lead manufacturing Quality functions through strong dotted line responsibilities providing each plant direction, coaching, goals, and training
- Initiate “best practices' communication and “past problem history' programs to improve operation and design standards while promoting strategic direction
- Align cohesive and clear reportable metrics for all functional areas to enhance internal and external consumer/ customer satisfaction
- Develop targeted “quality focus areas' to drive alignment of market related issues and guide information systems, business and technology investment
- Create and drive cross-functional teams that improve quality related activities and integration of new processes, information, and technologies throughout the product life cycle (cradle to the grave)
- Integrate internal visual management system to enhance work environment that persistently communicates quality thinking, brand enhancement, and consumer satisfaction
- Generate and improve supplier relationships and metrics to clearly evaluate data driven quality performance
- Lead strategic communication related to suppliers to increase speed countermeasure activity and recover monetary impact
- Build “product concept to market' quality activities that include thorough evaluation of tooling and production feasibility
- Tie-in critical control points mirroring design intent with error proofing tooling and manufacturing methods to ensure key quality characteristics are achieved
- Guide problem solving/performance analysis teams across all plants, division, and cross functional teams to prioritize initiatives and drive significant Quality Improvements and reduction in COQ/COF year-over-year
- Manage the Product Quality Focus Group (PQFG) to assure proper alignment, focus, and sustainable results are achieved, communicated, and documented
- Become the primary driver for “Brand Promise' Quality commitments and improvements to our customers. Design quality systems to enable and sustain the Brand Promise
- Develop, design, and implement the Quality Management Systems for the Cut and Sew Center (CSC) Mexico facility while providing ongoing direction for the Quality Team at the CSC
- Following the completion of corrective actions, monitor the affected product field failure trend data to verify the status of resolution. Communicate the improvements to the entire organization through various media (i.e. newsletter, meetings, town halls, plant meetings, staff meetings, etc.)
- Prepare periodic reports for management regarding the status of PST corrective actions
- Manage the action items and activities of the Dealer Customer Partnership program as they relate to product and process quality improvements
- Analyze feedback from the field to prevent recurring problems; assist in resolution of product and system weakness and controls
- Provide communications to the Sales Representatives on repair and product issues
- Work with documenting, implementing and monitoring consumer quality feedback
- Participate in the Division Internal Audit process recommending changes, realignment, and increased performance through more robust audits
- Apply and train the organization in the appropriate use of Quality tools, including DFMEA, PFMEA, IQ, OQ, PQ, Gauge R&R/measurement system analysis, control plans, process verification/validation plans, validation protocol development, Cpk, Cp, SPC, hard gaging applications, computer based inspection methods, operator work instructions, DOE, process data analysis and DMAIC
61
Quality Operations Manager Resume Examples & Samples
- Acts as the primary QO contact for their area of support. As such, they must have sound knowledge of a wide variety of process, analytical, chemical, microbiological, instrument and automation disciplines associated with operations. They are accountable for the shared operations, quality and technology objectives for their area within the IPT, including deviation and discard reduction, schedule adherence, cycle time reductions and right first time. Coordinates and executes all Quality Operations activities to ensure production plans are met, utilizing the tier process. Supports project work in the building
- Performs review and approval for investigations, CAPAs, QCTS commitments, change requests, risks, IQ/OQ/PQ, Master Batch Records (MBRs), LIMS CRs, ACRs, etc
- Perform GMP walkthrough inspections to ensure compliance with cGMPs and regulatory requirements
- Write, review, approve SOPs and other instructional documents for shop floor
- Expected to have presence on Shop Floor, and incorporate Quality On the Floor into their team objectives
- Provides training to incoming personnel and ensures compliance with departmental procedures
- Experience: Minimum of 5 years of experience in Quality Operations, Quality Control (Laboratory Operations or Environmental Monitoring), Quality Assurance, Manufacturing Operations, or related field
- Skills: Strong understanding of regulatory requirements (domestic and international)
- Aseptic/Sterile processing experience preferred
- Experience in a supervisory/management capacity preferred
- Demonstrated leadership expertise working with cross-functional teams on complex projects
62
Quality Operations Specialist Resume Examples & Samples
- Provide Validation Quality oversight for Process, Computer, Equipment and Cleaning Validation
- Provide leadership and coordination of validation activities
- Develop PPQ strategy for NPIs
- Develop/Update Validation Master Plans
- Quality review and approve Validation Documents including: DT, CRSIQ/OQ, RTM, FT/FTF, protocols, reports, etc
- Ensure alignment with regulatory guidelines and industry standards
- Review requirements and source documentation (MBRs, PDTs, PCSRs, SOPs, Specifications), for use in development of Validation documents
- Provide guidance for the generation, resolution and closure of deviations
- SOP development, review and approval
- Provide Change Control Assessments
- NC/CAPA initiation/ownership
- Generate/facilitate quality risk assessments for automation and equipment (QRAES)
- Participate in internal and external audits
- Interpret and execute policies/procedures and lead validation engineers on an ongoing project basis
- Coordination of activities between Amgen teams (Validation, Manufacturing, F&E, Automation, QC, etc.)
- Doctorate Degree OR
- Master's Degree and 2 years of Quality experience OR
- Bachelor's Degree and 4 years of Quality experience OR
- Associate's degree and 10 years of Quality experience OR
- High school diploma/GED and 12 years of Quality experience
- 6 years of experience in pharmaceutical or biopharmaceutical environment with cGMP FDA regulated operations/engineering/manufacturing/quality environment Technical understanding of pharmaceutical/biotechnology unit operations
- Direct Validation experience with pharmaceutical or biopharmaceutical processes including the development of strategies, master plans, protocols and reports
- Proven experience in multiple regulatory inspections and knowledgeable in current industry standards and regulatory trends as they pertain to Validation of pharmaceutical or biopharmaceutical processes
- Strong skills in communication, presentation, organization, team development and leadership
- Knowledge of risk-based validation methodologies, such as GAMP5, regulatory agency expectations, biopharmaceutical processes, project management, strategic resource management and business analysis
- Ability to evaluate compliance issues and interact with regulatory inspectors
- System knowledge and experience with EBR, Delta V, NC, CAPA and Change Control processes
- Demonstrated experience in investigations, change control, validation and risk
- System knowledge and training in Trackwise, SAP, MES (Werum PAS/X), and Maximo
- Ability to manage multiple complex tasks at one time
63
Quality Operations Analyst Resume Examples & Samples
- Ownership and execution of a process adherence quality program
- Oversee compliance and adherence to JPMC Technology Standards within the Customer correction Team
- Identification of gaps and implementation of enhancements to controls and processes
- Accountable for adherence to policy, procedure, and controls
- Interface with various levels of management to report progress against plans and goals
- Manage communication and interface between the Quality team and other Correction functions (i.e. On-boarding, Project Management, Testing, and Execution)
- Prior experience in a quality, audit, or testing environment
- 5+ years experience in finance industry; regulatory compliance, operational risk, audit or risk management, including broad knowledge of banking laws and regulations associated with CCB Business Processes, Technology, and Information Security best practices preferred
- Ability to collaborate with business and functional experts to provide risk assessment guidance, recognize risks, and design enhancements
- Demonstrated ability to influence, negotiate, and lead change
- Strong decision making, analytical, and creative thinking skills
- Teamwork and communication (written and verbal) required
- Strong organizational, project management and multi-tasking skills with demonstrated ability to manage expectations and deliver results
- Strong background in metrics based monitoring and reporting
- Proficiency in Microsoft Office Suite, 8
64
Quality Operations Manager Resume Examples & Samples
- Ensure Product Quality: Processes, Control Plans and Trainings must be in place in order protect the finish good quality and its brand equity
- Ensure “Global Manufacturing Quality Manual” implementation / maintenance: RB global quality guidelines (including GMP’s) on what are the minimum requirements for a manufacturing site, in terms of process, practices and technologies special conditions; in order to improve and sustain quality operations standards that will reduce risk to have processes and/or products not complying with specifications
- Change Control implementation: Essential process of the manufacturing sites, with the final objective to launch and new product, extend its category or modify the structure of a current product (or production equipment); meeting a specific “success criteria” that will ensure its quality (product or production equipment)
- Consumer Experience (Shelf & Home use): RB measure of quality; how our products look on shelf (without issues, like: leaking, broken, dirty, etc.) and how’s the performance when the product is used at home. RB measures those 2 processes by performing Store Checks and collecting feedback from Consumers (Phone and/or Social Media). When opportunities are detected to improve; action plan must be developed and lead
- Operations Departments support: Providing constant support to the operations manufacturing lines, in order to keep production a) Safe, b) with Quality, c) OEE and d) output (cases); supporting on identifying root causes of problems; coaching operations team on how to develop their own assessments, actions and reports; and leading communication and actions related to Suppliers issues
- Ensure that the “Global Manufacturing Quality Manual (plus the corresponding appendixes)” is implemented and well understood by Operations personnel
- Responsible to self-assess or audit the “GMQM” yearly in order to assure compliance and risks
- Ensure that the Operations Team is following GMP’s
- Responsible to evaluate / approve (reject) Product Specifications (TDS & Part List)
- Ensure that Finish Goods are complying with their specification (TDS)
- Ensure that Quality Processes (documented & implemented) are in place on the manufacturing & packing areas; in order to support the CORRECT product manufactured
- Ensure that Control Plans are well designed in order to detect issues with low volume impact
- Ensure that a robust CAPA is in place, including its Non-Conformance report, root cause analysis and detailed actions plan (Corrective and Preventive Actions)
- Responsible to issue “Hold Notices” to the Logistics Centers, when potential issues are detected
- Responsible to communicate and manage issues related to Suppliers
- Responsible to communicate to Suppliers, RB Quality Standards & requirements; in order for them to provide RB only “inside specification materials”
- Responsible to detect and implement Quality Trainings to the Operations team (i.e. Control Plans, GMP’s, etc)
- Ensure that for every Project (Change, New Product, Extension of Product or Cost reduction); appropriate Change Control process is in place, by making sure that the following process / requirements are being followed
- Success Criteria
- Risk Scorecard / FMEA (Costumer or Design; when applicable)
- Employees & Consumer Test support (design and evaluation)
- Product & Process Validation
- GFS (plus follow up on any post launch action)
- Product Launch Summary – sharing learning’s
- Responsible to lead investigations related to Consumer Complaints and/or Store Checks issues; and ensure that appropriate actions are taken in time & validation of its effectiveness
- Ensure that the Operations Team has every “Quality Tool” (Documentation, Training, and Measurement Equipment) in order to perform their job
- Responsible to create a “good communication relationship” between Quality and Operations departments, so when issues are presented; communication will help with effective results
- Minimum of a BA or BS degree in the sciences or food science area
- Minimum of 5 years of progressively responsible quality assignments in Consumer Products, Food, or Pharmaceutical business
- Experienced in quality systems such as ISO 9000, GMP, HACCP, and Auditing
65
Quality Operations Head Resume Examples & Samples
- Knowledge of cGMPs and understanding of the concepts of GLP, FDA and Health Authority Guidelines, applicable State and Foreign regulations and standards routinely used in the industry (ANSI, ISO)
- Understanding of Global requirements for product Disposition (e.g. Qualified Person, Technical Release)
- Diplomacy and persuasion used in obtaining cooperation for completion of projects, investigations and continuous improvement
- Ability to communicate effectively with cross-functional groups in various aspects of company operations
- Detail oriented with expertise in problem solving and solid decision making ability
- Strong interpersonal skills, which include a professional demeanor and the ability to influence and promote a culture of continuous learning and improvement
- Strong written and verbal communication skills are essential
66
Quality Operations Associate Manager Resume Examples & Samples
- Assist in preparation of Quality Agreements, according to annual schedule
- Assist in managing the quality metrics programs in relation to CMO performance and represent Quality on cross functional teams
- Assist in preparation of Annual Product reviews as required for end to end product monitoring
- Minimum of 5 years experience in biopharmaceutical operations, with at least 3 years in Quality Assurance
- Good verbal, written and presentation skills
67
Intermediate Engineer, Quality Operations Resume Examples & Samples
- Minimum 1-3 years in an engineering role
- Bachelor’s Degree in Science or Engineering with Mechanical Engineering focus, or equivalent
- Demonstrated initiative and problem-solving skills; critical thinking skills
- Ability to design experiments, analyze and interpret data, and document conclusions
- Analytical skills, creativity and innovative approach to problem solving
- Ability to collaborate effectively with multidisciplinary team members and also to work independently
- Willingness to work in labs, manufacturing areas, and office environments
- Very strong investigational skills, drive to understand and solve problems
- Propensity for continuous learning and experimentation
68
Senior Biological Critical Reagent Specialist Quality Operations Resume Examples & Samples
- Support transfer of BCRs of new Biological products from our Manufacturing Division Commercialization / our Research Laboratories to Biotech BCR Hub
- Support complete life cycle (acquisition, qualification, implementation, ongoing monitoring and stability) of BCRs within the global Biologics franchises
- Support distribution (in time delivery) of BCRs to MSD laboratories, contract laboratories and regulatory agencies
- Provide bioanalytical support and knowledge to our Manufacturing sites, Oss Laboratories and other functional groups as needed
- Provide bioanalytical support in responding to regulatory questions, authoring appropriate CMC sections or appropriate technical support during regulatory inspections
- Conform to current Good Manufacturing Practices (cGMP) as they apply to the functions of the group
- Support/drive required GMP/GLP activities like change requests, deviation notifications/management
- Master’s or PhD degree in Biology, Chemistry, Biochemistry, or a related biological science
- At least five years of experience in the areas general biochemistry, analytical biochemistry or immunochemical techniques
- At least several years of experience and up to date knowledge on GMP and regulatory requirements in the pharmaceutical industry
- A thorough understanding of Bio-analytical methods (Elisa, HPLC, CE-SDS) and validations
- Basic to strong technical knowledge and a high level of technical performance
- Ability to achieve productivity by managing time, priorities and personal effort in a fast-paced environment
- Strong and proven leadership capabilities to lead investigational teams, as needed
- People management potential is a plus for this function
69
Quality Operations Associate Resume Examples & Samples
- 1) Why document standards are so important in a cGMP environment
- 2) The basics of Good Documentation Practices (GDP)
- 3) The different type of documents and records
- 4) General requirements of GDP
- 5) The importance of traceability of cGMP records
- 6) Records control
- 7) Storage and archival of cGMP records
70
Quality Operations Manager Resume Examples & Samples
- 5-8 years of experience in Quality, Manufacturing and/or Engineering with a minimum of 3 years in the aerospace industry
- A thorough understanding of P&W Quality Procedures, Quality Management Systems fundamentals, AS9100 and Regulatory Agency Requirements
- Demonstrated ability to interface with all levels of management and internal customers/stakeholders
- Knowledge and experience in data analysis and problem solving using Six Sigma, Red X and process control tools
- Experience in using ACE/Lean/Six Sigma tools to make process improvements in a fast-paced, high volume aerospace manufacturing environment
- Ability to lead projects, develop and mentor other leaders
- Strong interpersonal and communication skills and ability to facilitate and motivate teams
- Formal certification as a Six Sigma Green Belt highly desired
- Formal Certification as a Six Sigma Black belt and/or Lean Expert preferred
71
Business Control & Quality Operations Specialist Resume Examples & Samples
- Assist in the design of operational control processes for pricing functions
- Project manage the design and build phase for the centralization of operational processes working with the BCQ Managers
- Identify opportunities for continuous improvement within Operations activities and work to implement them with the BCQ Managers
- Check Bids, Offers and Trades (BOTE’s) for Singapore, London and Houston Oil and Shipping Benchmark assessments daily, informing price reporters of errors
- Run daily rationale check for Oil for Singapore, London and Houston Oil and Shipping Benchmark assessments daily. Following up if these are not complete
- Manage the scheduling of some recurring operational tasks with front line managers, monitor and report on completion. These include updates to How to Guides, Source Lists, Methodology & Specification Guides, amongst others
- Monitor the quality of methodology change projects
- Support production of month end metrics files related to operations function
- Liaise with BCQ Managers globally for escalation of operational errors and issues
- Work with the price reporting roles in the resolution of daily operational outstanding items
- Be the ‘go to’ resource with the offshore team in Mumbai (GAC – Crisil) working to resolve raised queries and close out the escalation log findings
- Support offshore team to streamline processes globally and providing feedback for offshore development and reduction in erroneous issues being raised
- Highlight control breakdowns to the BCQ Managers for escalation daily and through monthly roll ups
- Aid BCQ Management in documenting deep dive and shadow session analysis to gain a greater understanding of the business to greater support the operations activities
- Assists in gathering data or documentation to support team’s analysis or audit reviews
- Builds effective relationships with the business and teams you support / work with within Content, COG and Crisil
- Able to effectively communicate the internal controls to internal and external parties
- 3+ years of financial services industry experience within operations functions
- Strong attention to detail and ability to meet deadlines
- Must identify opportunities and take action to build more efficient operations functions
- Proficiency in Microsoft Office products required
- Ability to work with reduced supervision
- Background in commodities operations functions (preferred)
- Project management experience (preferred)
72
Quality Operations Specialist Resume Examples & Samples
- Experience in related field (5+ preferred)
- Six Sigma Competencies
- Business Acumen - Understands how businesses work; is knowledgeable in current and makes recommendations regarding future policies, practices, trends, and information affecting the organization
- Problem Solving - Demonstrates an advanced level of root-cause analysis; helps to lead/facilitate teams to solve problems; assists with the implementation of continuous breakthrough improvements; seeks guidance as needed
- Functional/Technical Skills - Advanced level of knowledge of product manufacture and inspection, testing and technology; in-depth knowledge of problem solving methods and techniques; assists others in process management, technical specifications, regulatory guidelines, contractual requirements, and the application of Quality Standards and Specifications; excellent presentation skills
73
Associate Director, Quality Operations Resume Examples & Samples
- Maintaining a program to comply with the requirements of the FDA, EU and ISO 13485:2003, and other relevant regulatory bodies for the site
- Oversee investigation and corrective actions for non-conformances related to supplier quality and packaging and as needed support quality investigations outside of these areas
- Work closely with Waco management peers and colleagues to ensure that quality representation is activity engaged in facility and capital project initiation and execution
- Ensures commissioning and validation activities are in compliance with industry and site procedures
- Lead and participate in, as appropriate continuous improvement initiatives
- Manage the change control processes for the site,
- Manage the in-process QC teams responsible for packaging and plastics, ensuring that these production operations have the right level of quality support and oversight
- Responsible for the QA support of FDA or other regulatory inspections
- Demonstrated project management skills and the ability to influence others effectively
- The individual must be result orientated and able to demonstrate the use process measurement tools to achieve metrics
- Demonstrated process thinking skills and familiarity with knowledge management
- Developing team members
- Support corporate initiatives as necessary
- A Six Sigma Black belt certification or a formal qualification in statistics is beneficial, but not required
- Trackwise, and SAP highly preferred. Experience in EBR deployment highly desirable
- Master’s degree preferred but not essential
74
Quality Operations Laboratory Manager Resume Examples & Samples
- A minimum 3 years experience in a GMP Quality laboratory environment
- Working knowledge of GMP's as they pertain to Active Pharmaceutical Ingredient manufacturing
- Experience with/knowledge of laboratory instrumentation troubleshooting/repair techniques
- Must be able to provide effective technical direction and training as necessary within the section
- Possesses strong problem solving skills, strong interpersonal skills, and the ability to work independently and with minimal supervision
- Required to work with hazardous chemicals while wearing personal protective equipment
- Must be able to work in and around the manufacturing and laboratory areas associated with chemicals related to Beta Lactum antibiotics
- Required to work a rotating shift schedule to support 24 hour operations. This will include day/night shifts and weekend shifts
75
Director, Quality Operations Resume Examples & Samples
- Oversees all Quality Operations supporting Solution and Dialyzer manufacture and release including but not limited to Microbiology and Chemistry Laboratories, Methods Development and Support, Sterilization, Incoming and Final Product Inspection and Supplier Management
- Serves as official alternate management representative for all regulatory matters and primary site leader for quality operations issues
- Reviews and complies with the Code of Business Conduct and all applicable company policies and procedures, local, state and federal laws and regulations
- Ensures all employees within the assigned team(s) understand and comply with the Code of Business Conduct and all applicable company policies and procedures, local, state and federal laws and regulations
- Ensures Quality Operation and programs are effectively established and maintained according to local, corporate and applicable state, federal and international requirements. Assures products achieve acceptable quality levels
- Assures the development, establishment and maintenance of a robust Quality Operations for the assigned plant that, complies with all country, federal and state regulations, and European or International Quality Standards, as required
- Standardizes/harmonizes policies and laboratory procedures, where appropriate, to ensure consistency between the plant, Corporate and other FMCNA Plants
- Investigates, assesses and implements new technologies to improve outputs for Quality, Safety, cost, efficiency reliability and accuracy
- Establishes systems to monitor the quality initiatives and laboratory outputs for cost and efficiency. Reviews capital expenditure requests for Quality impact and appropriateness
- Assures timely and appropriate investigation, communication, disposition and corrective actions associated with product and/or process quality issues
- Assures timely and accurate presentation of key Quality performance metrics to plant personnel and Executive Management. Assess adequacy of overall Quality Function including resources and deployment
- Reviews, standardizes and harmonizes Quality policies, guidelines and procedures for both the plant and its suppliers. Insures compliance with cGMP, regulatory guidance and recognized standards, where appropriate
- Interacts with all levels within the organization to manage functional area. Overall responsibility for hiring, coaching and counseling employees, including performance reviews, disciplinary action and terminations
- Provide technical guidance
- Assist with various projects as assigned
- 10+ years’ related experience
- 5+ years’ experience as a Manager; or 5+ years’ experience in a senior managerial role
- Strong knowledge of FDA regulatory requirements (cGMP/QSR) and of standard quality assurance practices for medical manufacturing operations
- Experience with liquid filling and/or aseptic filling and microbiological/environmental control
- Professional quality discipline certifications (CQE, CQA, CQM or RAB) desired
- Ability to read, analyze and interpret blueprints, technical manuals, specifications, test methods and procedures/equipment manuals
76
Quality Operations Quality Agent Resume Examples & Samples
- Safety, Quality, Result and Customer oriented
- Back up the shift leader
- Perform the GMP documentation review for each packaging batch recorded and ensure that all records are compliant with GMP and GSK Corporate requirements
- Ensure that the GMP documentation ( MBRs, executed manufacturing and packaging records, raw data generated during manufacturing & packaging operations and API HR Operations) is reviewed and complies with GMP Novartis Corporate requirements (Quality manual) and registration file
- Ensure that all operations are recorded and archived in compliance
- Ensure that all pression in the packaging area are in compliance
- Perform the purges and pipe sterilisation in the washing room
- Suggest, lead and manage Continuous Improvement actions : EHS, Quality and cost
- Support Quality training of the operators
77
Manager, Quality Operations Resume Examples & Samples
- Directs and manages quality auditors, metrology personnel, department resources, and continuous improvement efforts to achieve the most efficient quality output as possible
- Ensures timely resolution to audit findings and customer complaints
- Utilize PMI strategies and techniques to manage Scope, Time, and Budget
- Maintain clear communication paths with stakeholders
- Conduct routine resource reviews with project Teams and management
- Manage and maintain an effective Quality Assurance program for the plant in alignment with Site and Enterprise Procedures and capable of maintaining ISO 13485 certification status
- Review operating procedures to ensure compliance with all related procedures, instructions and the Quality Manual
- Investigate and ensure implementation of the corrective actions associated with non-conformances, including, customer audits and complaint reports
- Establish procedures and methods to comply with applicable GMP, ISO requirements and customer expectations
- Manage Quality Staff at site to assure knowledge and execution of site Quality System
- Drive continuous quality improvement projects at plant based on site data and customer expectations
- Drive compliance to global harmonization initiatives
- Assure proper use of change management associated with validated processes used by site
- Adjust in process/final sampling plans & related accept/reject criteria to ensure compliance to specification
- Minimum six (6) years in Quality Assurance / Quality Control
- Minimum four (4) years managing others directly
- Experience with sterilization requirements and classified environments for production
- Experience with Customer interface and meeting customer expectations
- Working familiarity with Project Management Tools and Quality Risk Management
- Experience with microbiology and particulate lab testing
- Working knowledge of Medical Device requirements
78
Manager, Quality Operations Resume Examples & Samples
- Interfaces with local Operations, Quality Management and Development to assure all products and processes are in accordance with company standards and quality systems. This is accomplished through Strategic Quality Planning, Quality System execution and maintenance, non-conformance, corrective and preventive action reporting and follow-up, quality audits, performance metrics, continuous improvement projects, and other activities
- Determines and implements best strategic direction for local site Quality Assurance with regard to organization, competencies, human and fiscal resource planning, quality planning and in support of Manufacturing Operations and associated Development activities
- Supervises the Quality Assurance staff in daily support activities to manufacturing, material control and component and product disposition, validation protocol and report review and approval, nonconformance, validation deviation and planned variance handling, and shop floor and internal auditing
- Performs hands-on activities including nonconformance review and approval, validation protocol and report review and approval, documentation change workflows, planned deviation review and approval
- Participates in cross-functional meetings/initiatives and sets and maintains the standards for interdepartmental actions and the integration of quality planning with production and operations planning
- Assures local organizations are trained on RSS – San Jose policies and procedures, and QSR and ISO requirements through the development and implementation of compliance education and training courses
- Performs administrative functions including performance management, goals and objective setting and personal development planning
- Assures short term training needs for local staff are addressed and longer term individual and organizational development needs are identified, planned, and implemented
79
Quality Operations Associate Manager Resume Examples & Samples
- Perform product disposition activities to ensure the timely supply of drug product that meet commercial customer requirements while ensuring compliance with testing standards, SOPs, validation guidelines and regulatory filings
- Minimum of 5 years experience in biopharmaceutical Drug Product operations, with at least 3 years in Quality Assurance with expertise in medical device/drug combination products and packaging operations experience desired
- Good verbal, written and presentation skills in English and preferably fluency in German
- Strong strategic and analytical thinking, problem solving and rapid decision making skills
- Demonstrated capability in implementing challenging goals, objectives and practices in a complex and ambiguous environment
- Strong ability in negotiating and influencing without authority in complex, high impact situations
- Demonstrated ability in technical writing, computer knowledge and communication skills is required
- Strong presentation and communication skills both, oral and written in English, German language skills are desired
80
Quality Operations Manager Resume Examples & Samples
- At least 8 years of experience in Quality, Manufacturing and/or Engineering with a minimum of 5 years in the aerospace industry
- An understanding of P&W Quality Procedures, Quality Management Systems, AS9100 and Regulatory Agency Requirements
- Experience in supervising bargaining unit hourly associates is highly desired
- Demonstrated ability to interface with all levels of management and external customers
- Knowledge and experience with Six Sigma and process control tools
- Experience in using ACE tools to make process improvements in a manufacturing environment
81
Principal Quality Operations Engineer Resume Examples & Samples
- Using fundamental principles in science and engineering, guide new product development teams to determine critical-to-quality properties of raw materials, components and services
- Collaborate to define, write, review and approve of component qualification and supplier qualification protocols and reports
- Perform supplier audits
- Collect and evaluate supplier quality data to identify process improvement opportunities
- Identify repeat quality issues by supplier and maintain supplier quality scorecard
- Collect and maintain supplier and manufacturing performance metrics
- Working with the supplier and operations directly, to address corrective actions (SCAR’s) and MRR’s as required
- Perform or lead root cause analysis on manufactured and purchased part or product quality issues and work issue through containment phase of corrective action process
- Review supplier manufacturing processes, collaborate with suppliers on process improvement and value enhancement opportunities
- Develop and implement procedures to comply with corporate and industry standards
- Maintain a professional working relationship with internal and external customer and support staff
- Participate on cross functional teams to improve current process requirements
- Assess implementation of changes to manufacturing at multiple sites
- Lead implementation of updates to manufacturing process for correction, corrective actions, and improvements
- Bachelors degree in Engineering or a closely related technical field or related experience
- A minimum of 6 years experience in the medical device or closely related
- Working knowledge of FDA GMP/GLP, Medical Device Directive, ASTM, AAMI, CEN and ISO
- Working knowledge of component qualification, supplier qualification, and supplier audits
- Quality Engineering Certification (ASQ) or Lead Quality Auditor
- Extensive knowledge of FDA GMP/GLP, Medical Device Directive, ASTM, AAMI, CEN and ISO guidances and requirements
- Combination device/pharmaceutical and coating technology experience preferred
- Experience supporting product, design & prototyping a plus
82
Quality Operations Manager Resume Examples & Samples
- Degree in engineering / manufacturing or related field. Minimum of five (5) years of progressive quality assurance experience
- Breadth and depth of quality generalist knowledge. Applies advanced concepts, practices, and procedures of the field. Thorough understanding of ISO 9001, GMP knowledge is an advantage
- Considerable demonstrated skills in listening and communicating effectively with diverse individuals, groups, facilitating trust and understanding. Coaching, counseling and feedback skills. Facilitation skills to provide QMS training to the organization
- Superior interpersonal abilities. Good reasoning abilities. Sound judgment. Resourceful and well organized. Well-developed administrative and management skills
- Computer literacy and knowledge of quality / information systems to support HR activities. Knowledge of Microsoft Office Package (Word, Excel, Outlook, Powerpoint, Internet Explorer), desired SAP and QMS applications. Must be proficient at Excel / Minitab and able to analyze and interpret data
- Good oral and written communication skills. Ability to function effectively in a global / matrix organization
- Strong knowledge of applicable federal and local product / application laws and regulations
- Internal auditing experience. Certification preferred
- Implementation of effective QMS in line with Corporate, BU and local requirements
- Continuous improvement of Core Value Drivers in support of quality and business growth
- Undertake customer complaint CAPA and NCR process providing escalation as appropriate
- Identification and implementation of controls and reporting to cover industry specific regulatory requirements. Ensure regulatory compliance, maintaining an effective Internal Audit program, achieving and maintaining compliance to appropriate quality system requirements that includes ISO 9001 (version 2008 and 2015)
- Lead, mentor and rigorously develop talent within the quality function. Ensure that the site quality staff has appropriate skills, training, tools and organizational structure to achieve the business goals
- Interface with supplier quality engineering function to drive supplier quality at plant and BU level. Improve supplier quality management practices to drive continuous improvement of product quality and on time delivery and development of partnerships with key suppliers
- Assist the development, formulation and implementation of policies, systems, strategic plans/objectives for the management of manufacturing product quality and systems, including establishment of appropriate quality metrics to measure product quality and effectiveness of the quality system
- Oversight for the implementation an effective management release and distribution of the site products, ensuring that processes required for the qualification and release of new products are established, implemented and maintained
- Collaborate with Commercial / Technical business units to ensure the promotion of awareness of customer requirements and quality throughout the site. Is part of the Site Leadership Team and in this capacity is responsible to collaborate with site organizations to meet key sites performance goals and to address day to day operational issues
- Design and deploy quality systems and processes to improve focus of the organization for continuous improvement and improved product quality and service to our customers
- Manage timely resolution of customer issues and complaints to increase customer satisfaction by use of effective root cause analysis to identify and eliminate the sources of customer dissatisfaction
- Assure effectiveness of corrective and preventive actions provided to our customers to prevent recurrence and reduce DPPM
- Increase QA participation in new product introductions and build quality and customer requirements into the process
- Reduce product variability by introducing and sustaining an SPC program that also results in improved customer satisfaction
- Perform other related activities as required by management
- Understand and comply with all company Quality, Safety and Security, Finance and HR policies and procedures as related to this position, including reading all relevant safety and security literature, using the required protective equipment and practicing good housekeeping
83
Director / TL, Quality Operations Resume Examples & Samples
- Leads the QO functions at the site, including the quality assurance, quality control, system and compliance, vet services and regulatory compliance functions
- Achieves site and corporate quality objectives through leadership, development and coaching of staff
- Assures systems and processes are in place to meet or exceed Zoetis and regulatory requirements for the quality of the products manufactured; chiefly USDA and EU GMP requirements
- Being a quality culture role model, and championing a continuous quality improvement culture
- Interfacing with diverse stakeholders (internal and external) across the organization
- Leading and developing a diverse team of talented and engaged colleagues to assure site and corporate quality objectives are met
- Defining, executing and updating stakeholders on strategic (multi-year) quality initiatives
- Planning, implementing and achieving (annual) site and global quality objectives
- Overseeing the Site Quality Review Team (S-QRT) meetings and escalation of quality issues to the Quality Platform Leader
- Interface with global regulatory agencies during audits
- Identify and resolve quality, process and GMP issues
- Manage overall assurance and disposition of products produced at Charles City
- Oversee approval of quality and production quality assurance reports and investigations
- Review key quality and regulatory documentation and implement appropriate corrective/preventive actions
- Develop and maintain a lean organizational structure, to assure achievement of site budget objectives
- Must have excellent verbal and written communications, presentation and planning skills
- Ability to lead and motivate others, while consistently modeling the Zoetis leader behaviors
- Must have a thorough understanding of EU GMP and USDA (9CFR) requirements
- Thorough knowledge and understanding of biological manufacturing processes (including aseptic, sterilization, depyrogenation processes) and related biologic/analytical testing
- Demonstrated record of successful interaction with regulatory agencies (e.g. APHIS, USDA, VMD, MCA, FDA) and other internal and external auditing groups
- Familiarity with statistical analysis and strong problem solving skills
84
Quality Operations Manager Resume Examples & Samples
- To drive continuous improvement actions in function of quality results
- To ensure the implementation of the methods to achieve the quality objectives
- Establish and develop Quality organization within plants of his region and ensure appropriate staffing
- Ensure that an adequate control plan is applied to meet customer requirements
- Ensure that Significant Characteristics and Critical Characteristics are secured
- In charge of the methods used for the Quality convergence plan for every plant (the plant manager being responsible for the Quality convergence plan)
- Ensure the compliance with FES, Safety & Regulation and Automotive Standards (PDCA)
- Responsible for supporting and coaching Plant Quality Managers and launch managers on Quality tools
- Responsible for identifying the performance variability issues and having them fixed (product/process changes, supplier changes, transfer)
- Support (and coach if needed) the Supplier Quality Assurance activities and initiatives
- Evaluate the status of Processes based on PQA & drive continuous improvement based on the findings
- Develop & Implement Improvement tools / indicators (like IDI)
- Ensure that Quality Customers needs transmitted by Quality Customer function relationship are taken into consideration by operations
- Ensure that Regional operations report the right Quality results to all relevant parties
- Ensure that quality procedures are applied for all transfers activities
- Ensure that quality procedures are applied for all VA/VE activities
- Stop the manufacturing and the delivery of products when Quality is not assured
- Minimum of 10 years of professional experience
- Ability to manage a complex network in a matrixed organization
- Manufacturing and Quality experience
- Process orientation
- Multi-site management experience
- Customer Relationship experience
- Minimum bi-lingual (English required, German strongly recommended)
85
Quality Operations Engineer Resume Examples & Samples
- Bachelor degree in a technical field desired, preferably Mechanical Engineering
- 5-7 years experience in quality assurance field in a medical device manufacturing environment
- In-depth knowledge of SPC, and process capability studies
- Working knowledge of the FDA medical device Quality Systems Regulations and ISO 13485
- Experience with failure investigations, risk management and failure report writing,
- Ability to create concise, accurate report
- Ability to read technical reports and specifications
- Proficiency in the use of personal computers and computer database software, including Microsoft Office applications (Access, Excel, Word and PowerPoint)
- Must have capability to review, analyze, summarize and interpret quality systems data, draw conclusions, make appropriate decisions and recommendations, write reports and give oral presentations
- Must show self-initiative but be comfortable in the role of a team player. Must be able to manage multiple projects and report progress against goals in an objective manner
- Excellent written, verbal and organizational skills required
- Must be detail oriented and able to work independently
- Minimum travel is required
86
Quality Operations Engineer Resume Examples & Samples
- Identifies and resolves complex exceptions to work assignments
- Summarizes, analyses, draws conclusions and makes appropriate decisions from test results or other process related findings
- Has the responsibility and independent authority to make decisions related to product quality, including the disposition of non-conforming product
- Participates in Customer Complaints investigation for areas under their control
- Continually seeks to drive improvements in product and process quality
- Knowledgeable on QSR and ISO/MDD standards, constantly promoting awareness of best industry practices, making appropriate decision on a daily basis utilizing the quality engineering manager/site QA Director as the final arbitrator on critical quality decisions
- Fully conversant with validation techniques and associated regulatory requirements including analysis of customer feedback and complaints
- Evaluates in conjunction with EHS new equipment/processes/chemicals for environmental impact/effect to eliminate or lessen such impacts/effects
- Knowledgeable on Risk Management , BSEN 14971 requirements
- Compiles and analyses operational, test and validation data to establish technical specifications and performance standards for newly designed or modified products and processes
- May participate directly in a new product/technology transfer to ensure compliance to all internal and regulatory requirements
- Uses knowledge of Six Sigma, Statistical Analysis and Lean principles to investigate and solve problems and improve quality
- Gives technical guidance to Associate Quality Engineer, Technician and Inspection staff
- Is a good team member, fully motivated to achieve and demonstrate best practices in line with the department and Site objectives
- Deals with suppliers, other engineering disciplines within and outside of the Site and customers should the need arise
- Is familiar with the internal auditing process
- HETAC Level 8 qualification in a relevant area with a min. of 3-4 years relevant experience
- Good technical capabilities, communication skills, teamwork abilities and initiative
- Proven ability to work well both as part of a team but also able to work on own with minimum supervision
87
Quality Operations Manager Resume Examples & Samples
- Post-Secondary Degree/ in Science or Engineering in a related Science
- Sciences (Chemistry, Biology, Physics) or Engineering in a related Science
- Quality background
- Previous supervisory or management experience in a regulated health products environment
- Knowledge of GMP, ISO standards, and Canadian regulatory requirements for drugs and medical devices
- Minimum 5 years experience in medical/therapeutic products manufacturing sector with minimum 3 years managerial/supervisory experience
- People Management Experience – excellent people management, coaching and team development skills
- Ability to work in a fast paced environment and balance multiple priorities
- Strong communication skills, negotiation skills, ability to work with all levels of the organization
- Ability to build strong relationships with internal and external customers
- Strong analytical and problem solving skills and critical thinking abilities
- Intermediate to Advanced proficiency in Word, Excel & Powerpoint
88
Manager, Quality Operations Resume Examples & Samples
- Coach and mentor others on validation processes and strategy develop. Approve IQ, OQ, PQ, TMV or Software Validation
- Partners with J&J Global Supply chain, Finished Goods and material suppliers to ensure appropriate application of process validation, process control, and risk management; and the investigation/correction of process failures when needed
- Develop measurement systems/capabilities, destructive tests, non-destructive tests for manufacturing processes
- Develop, interpret and implement appropriate process monitoring and control methods consistent with the level of process/product risk
- Ownership of test method qualifications
- Collect data and execute/conduct various analytical/statistical analysis and interpretation as part of process improvements and day-to-day support
- Standardize and develop methods/techniques of analytical/statistical analysis and interpretation
- These may include descriptive, graphical, gage R&R/measurement system, reliability, capability, control chart analysis, confidence intervals, hypothesis testing, analysis of variance, design of experiments, etc
- Develop, interpret and implement standard and non-standard sampling plans
- Assess effectiveness of measurement tools, destructive tests, non-destructive tests, measurement system analysis
- Accountability and ownership for sampling plans of all types including acceptability of risk given the product classification, potential defect types, defect frequency, severity, patient risk, process capability, process controls, etc. including assessing, applying and interpreting acceptance sampling standard for manufacturing data
- A minimum of a Bachelor’s Degree is required, preferably in Engineering or related technical field
- Advanced Technical Training and experience using Statistics, Measurement System Analysis and SPC
- A minimum of 5-8 years’ experience in a GMP/ISO regulated environment
- Understanding of the NPI (New Product Introduction) process and Process Validation expertise
- Direct or indirect experience in a management/supervisory role
- This position will be based in Raynham, MA and requires up to 20% travel (international and domestic)
89
Manager, Quality Operations Resume Examples & Samples
- Leadership of a high performing quality team, that provides direct support and technical guidance / direction to the operational and functional areas on site, fostering an environment of proactive and continuous improvement approach to Quality
- Ensure that the organisation’s conformance and commitment to producing products meets or exceeds customer requirements and the relevant regulatory standards
- Drive an environment of compliance within Stryker by working with all function managers and their support staff to define expected quality standards and the roles/responsibilities in the maintenance of these standards
- Champions a positive employee environment by promoting open communication, engagement and development of team members. Promotes a culture of trust, flexibility, teamwork and inclusiveness, ensuring all relevant Quality functions (e.g. Shared Services Quality, Supplier Quality) are included in decision making processes as part of continuous improvement, problem solving and projects
- Selects competent talent and supports the development of their future potential. Ensures effective training and performance management of the teams
- Ensures the site(s) maintains continued certification to all regulatory bodies. Plays a lead role in all internal and external audit programmes such as Corporate, notified body & FDA audits
- Ensures effective management and control of product/process deviations for all released product and for the implementation of effective corrective action when non-conformances arise. Manages product & patient risk
- Develop a quality planning pipeline of quality improvement activities including initiatives to increase product quality, NCR & CAPA resolution, reduce cost, decrease in-efficiencies and improve risk management
- Oversight and responsibility to ensure site maintains adherence to Quality KPIs performance indicators, and takes timely action to address adverse trends and deviations. Continuously monitors and partakes in global forums to assess opportunities for improvement
- Foster strong collaboration on a global scale by participating in and leading cross functional and global process improvement initiatives
90
Manager, Quality Operations Resume Examples & Samples
- Receipt and disposition of incoming materials
- Review batch-related documentation, and ensures resolution of issues to release product
- Perform product disposition and lot closure
- Oversee the packaging and shipping process; authorize shipment
- Ensure all product-related Deviations are initiated, investigated and resolved. Ensures that associated CAPAs are nitiated and resolved, as needed
- Maintain metrics related to batch record review and product disposition in support of the Management Review
- Train, manage, and coach staff
91
Senior Manager, Quality Operations Resume Examples & Samples
- Review batch-related documentation, and ensures resolution of issues to release and ship product
- Ensure all product-related Deviations are initiated, investigated and resolved. Ensures that associated CAPAs are initiated and resolved, as needed
- Review and approve Change Control, as needed
- Implement QA on the floor processes, including batch record review
- Ensure process control measures are in place and followed in product manufacturing
- Maintain metrics related to batch record review and product disposition in support of the Management Review and continuous improvement
- Schedule staff to support manufacturing and packaging processes in order to ensure on-time delivery of product to patients
- Train, manage, coach, and mentor staff
92
Manager, Quality Operations Resume Examples & Samples
- Ensure that the organization's conformance and commitment to producing products meets or exceeds customer requirements and the relevant regulatory standards
- Ensures the site(s) maintains continued certification to all regulatory bodies. Plays a lead role in all internal and external audit programs such as Corporate, notified body & FDA audits
- Responsible for driving unnecessary cost from Quality & Manufacturing processes through execution of continuous improvement & lean principles
- Has a strategic view in identifying global alignment and developing strategies for best in class practices and benchmark against industry leads and regulatory requirements for the Quality function
93
Senior Quality Operations Associate Resume Examples & Samples
- To Manage and lead the Quality System and Compliance team providing competent and professional support to the business
- To provide technical advice on GMP and related issues
- To provide technical/compliance input to resolution of problems facing the company
- Lead/drive operational excellence from a quality perspective
- Be responsible for motivation, training and development of Quality System and Compliance team members to ensure high standard of staff performance
- Assist the Quality Manager in performance of duties and responsibilities
- To ensure all documentation processes are performed in compliance with GMP and quality requirements
- To ensure investigations of customer complaints are thoroughly investigated with appropriate, realistic and meaningful CAPA’s assigned and completed to prevent recurrence
- To ensure the site is audit ready and that all previous findings have been thoroughly investigated with appropriate, realistic and meaningful CAPA’s assigned and completed to prevent recurrence
- Oversee the facilities validation program
- Ensure that all jobs are conducted in accordance with GMP requirements and the Company's Quality Assurance System
- Ensure all departments are aware of the status of their Controlled Documents and ensure all Controlled Documents relating to the Quality Department are current and compliant
- Sound understanding of the pharmaceutical industry
- Understanding of the Code of Good Manufacturing Practice (GMP)
- Management of personnel
- Ability to lead and develop members of the Quality department
- Ability and willingness to be a positive influence on teams
- Must be willing and able to work in Production environment
94
Quality Operations Manager Resume Examples & Samples
- Manage and effectively lead quality engineers, lab supervisors and other quality team members as deemed necessary. Hire, train, develop, and manage exempt and non-exempt employees
- Ensure effective and meaningful development plans are in place for direct reports
- Administer the testing and controlling of raw material, in-process, and finished product quality, assuring compliance with company standards and applicable government regulations
- Coordinate / perform customer complaint investigations according to plant and corporate QA guidelines, conduct trending on customer complaints, and effectively communicate to upper management
- Coordinate and conduct routine and directed audits as needed to assure compliance with domestic and international regulations, local SOP’s and corporate standards.[i.e. QMS , QSIT, Combination Products, Regulatory requirements; Notified Bodies, etc]
- Participate / lead quality improvement activities pertaining to customer complaints or adverse quality trends
- Conduct internal audits and coordinate corrective actions and closure for internal and external audits as necessary
- Perform continuous quality control evaluation and trend analysis on product quality issues, resolve quality issues and initiate corrective actions with other departments as required
- Assist with the preparation and maintenance of department budgets. Maintains comprehensive knowledge of applicable regulatory authority quality and regulatory requirements and their interpretation
- Facilitate QA/QE support for new product launches to ensure robust development, validation (IQ, OQ, PQ), rollout, and implementation
- Coordinate with Operations and Engineering in developing and implementing projects for improvement of processes / products
- Provide feedback to Operations on opportunities related to quality and/or compliance
- Draft appropriate documents to support the Quality systems. Support the document control and project management systems
- Support the vendor qualification/assessment requirements of the facility
- Make decisions on product/process quality based on evaluations
- B.S. in Science or Engineering field
- 5+ years quality, compliance and regulatory experience in the medical device industry preferred. Combination product and/or pharmaceutical experience preferred
- 2+ years personnel management experience
- Demonstrated ability to effectively collaborate and partner with all levels of management in corporate and division level sites while maintaining an appropriate assertive style is critical
- Strong knowledge of statistics and quality engineering / failure investigation techniques
- Effective project management, communication, and organizational skills
95
Quality Operations Manager Resume Examples & Samples
- Daily supervision of Quality Analysts assisting with performance appraisals, counseling, and annual performance reviews, contributing to development of the content of performance appraisals and annual reviews, and assisting with counseling to ensure adherence to applicable policies/procedures. Also includes managing the distribution of work across analysts
- Provides technical and business consultation to project development team and customer departments
- Ensures compliance to local, state and federal regulations and/or rules, organization policies/procedures, and systems/applications utilization
- Ensures successful validation surveys
- Manages various information systems and data flow between them
- Ensures the accuracy of data. This includes, but is not limited to, developing plans or scripts for functional system, integration, volume, parallel, and stress testing
- Assists with scorecard and other report development and production
- Champions performance improvement efforts
- Supports QualityNet Administrators
- Ensures appropriate cross training to ensure stability of operations
- Bachelors Degree with 4 years clinical healthcare (hospital operations) experience and/or in combination with information technology related experience
- Functional knowledge and understanding of healthcare quality processes, principles and practices
- Functional knowledge of general business and/or administrative practices, processes and systems
- Must be able to communicate in English (verbal/written)
96
Quality Operations Analyst Resume Examples & Samples
- Improving the customer experience by ensuring high quality data and accurate content is provided to customers
- Conducting Quality check on Dell.com for EMEA/Global region
- Conduct content quality audits and assist in driving improvements in error reduction through prevention and quick resolution
- Cooperation with global teams to provide clear guidance on issues that need to be resolved
- Determine and prioritize the severity of issues