Planner Maintenance Resume Samples
4.7
(119 votes) for
Planner Maintenance Resume Samples
The Guide To Resume Tailoring
Guide the recruiter to the conclusion that you are the best candidate for the planner maintenance job. It’s actually very simple. Tailor your resume by picking relevant responsibilities from the examples below and then add your accomplishments. This way, you can position yourself in the best way to get hired.
Craft your perfect resume by picking job responsibilities written by professional recruiters
Pick from the thousands of curated job responsibilities used by the leading companies
Tailor your resume & cover letter with wording that best fits for each job you apply
Resume Builder
Create a Resume in Minutes with Professional Resume Templates
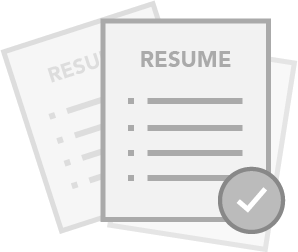
CHOOSE THE BEST TEMPLATE
- Choose from 15 Leading Templates. No need to think about design details.
USE PRE-WRITTEN BULLET POINTS
- Select from thousands of pre-written bullet points.
SAVE YOUR DOCUMENTS IN PDF FILES
- Instantly download in PDF format or share a custom link.
BJ
B Johns
Bonnie
Johns
6767 Langosh Throughway
Phoenix
AZ
+1 (555) 619 5866
6767 Langosh Throughway
Phoenix
AZ
Phone
p
+1 (555) 619 5866
Experience
Experience
New York, NY
Planner Maintenance
New York, NY
Dooley, Maggio and Cole
New York, NY
Planner Maintenance
- Assist in establishing and maintaining equipment parts catalog, equipment history, storeroom, min. / max. levels
- Maintain a high commitment to personal safety and integrity of the environment and equipment during the planning of work orders
- Schedule all maintenance events within the time interval of the task while accounting for manpower, ground time, parts, tooling, facilities, and weather
- Prepare weekly schedule and facilitate weekly scheduling meeting
- Assist user groups in identifying and resolving maintenance related problems, energy usage, mechanical integrity and safety
- Conduct field checks on work orders before planning sequence of operations, materials priorities, equipment, and trades times to complete the job
- Managing work to the maintenance budget
Los Angeles, CA
Planner, Maintenance
Los Angeles, CA
O'Conner Inc
Los Angeles, CA
Planner, Maintenance
- Managing and selecting suppliers/contractors, ordering and allocating parts for specific work orders
- Managing collection and quality of all data (accuracy, timing, etc) and auditing maintenance conformance with lean manufacturing principles
- Providing technical & problem solving support for recurring problems
- Efficiently planning and tracking predictive and corrective maintenance activities
- Serving as primary back-up to Maintenance Supervisor
- Publish the plan of the week for operations and maintenance to review and prepare for the coming distribute crew back logs for completion updates and to obtain scheduling feed back
- Schedule all active P3 work orders in a four week operational demand-based schedule. Work with operations/maintenance supervision to lock in the subsequent one week schedule
present
Boston, MA
Maintenance Schedule / Planner
Boston, MA
Shanahan, Wolf and Fritsch
present
Boston, MA
Maintenance Schedule / Planner
present
- Compiles all pertinent specification sheets, drawings, bill of materials from previous work and work history in the Work Order Package
- Perform administrative duties in the SAP maintenance management system
- Assist in planning and scheduling plant shutdown work activities
- Manage the status of work orders to completion
- Recommend improvements to make the Maintenance system more effective and efficient
- Manage, evaluate and report KPI’s for the Maintenance department
- Direct and execute the plants Proactive and Preventive Maintenance program
Education
Education
Bachelor’s Degree in Technical Field
Bachelor’s Degree in Technical Field
The University of Texas at Austin
Bachelor’s Degree in Technical Field
Skills
Skills
- Demonstrated ability to read and understand blueprints, machine drawings, process drawings and vendor manuals
- Proficient with Microsoft products (Excel, PowerPoint, and Word)
- Developing the best course of action based on available information
- Ability to build and maintain positive relationships with all associates
- Strong planning and organizational skills
- Verbal and written communication
- Thorough understanding of industrial mechanical and electrical maintenance activities
- Computer skills
- Thorough knowledge and understanding of SAP maintenance modules including work order creation, planning, scheduling, stores, inventories, backlogs, kitting, staging, and all auxiliary functions
- Success oriented
15 Planner Maintenance resume templates
Read our complete resume writing guides
1
Maintenance Turnaround Planner Resume Examples & Samples
- Coordinate and lead work scope development activities for assigned turnarounds
- Prepares detailed job packages by collecting engineering designs, drawings, specifications, and other pertinent information from engineering resources
- Prepares job package estimates, breaking down work scope into chronological steps (activities), estimating required skilled and auxiliary craft man-hours, and developing required material lists with costs
- Identify and purchase materials, ensuring on-time delivery for long lead or specialty items
- Initiate purchase requisitions for outside services, cranes, temporary shelters and rental equipment for turnarounds
- Support turnaround execution activities, providing timely response with job plans and cost estimates for discoverable work
- Collect and track turnaround work progress, prioritizing work and adjusting the schedule to facilitate efficient use of craft resources and on-time completion of turnaround work
- Provide administrative oversight and direction for contractors
- Responsible for preparing, forecasting, and explaining cost variance for turnaround work
- Knowledgeable in repair techniques for a broad range of mechanical equipment (piping, pressure vessels, tanks, boilers, heat exchangers, and furnaces)
- Will be responsible for other work as required
- 5 years of experience in planning, scheduling, coordinating, and executing large or multi-plant maintenance and/or capital construction events in an industrial / manufacturing environment
- BS in an Engineering Technology
- 5 years of experience in maintenance planning in a chemical, petrochemical, or manufacturing environment preferred
- Able to interpret and apply engineering standards and specifications
- Able to read and interpret mechanical drawings, P&IDs, and piping isometric drawings
- Basic knowledge of machinery, electrical, and instrumentation is preferred
- Experience and competency in the use of SAP for planning activities preferred
- Experience in Primavera or Microsoft Office Project is a plus
- Demonstrated ability to incorporate safety into foundations of work activities
- Demonstrated ability to work effectively with individuals or in a team environment at all levels of an organization
- Demonstrated ability to use influencing skills to accomplish goals and objectives
- Able to manage multiple priorities
- Ability to drive improvement in processes within the framework of Honeywell Operating System (or similar LEAN management processes)
- Strong leadership and organizational skills
- Proficiency with Microsoft Office Suite (Excel, Word, Outlook, and PowerPoint)
2
Maintenance Craft Planner Resume Examples & Samples
- ) Identifies and obtains necessary materials, work instructions, manuals, appropriate tools, etc. to execute the planned work order
- ) Plans and schedules preventive maintenance work in coordination with operations and maintenance managers
- ) If work contracted to outside vendor, the planner ensures the scope and cost of the work is clearly defined, purchase orders are approved, and equipment will be available for the work performed. Additionally, the planner will ensure the contractor personnel adhere to Mars contractor rules and regulations
- ) Analyzes maintenance performance metrics such as: accuracy of work plan estimates (time, labor, and materials), percent work orders awaiting scheduling, schedule compliance, overtime, contracted maintenance costs, overdue work orders, and returned work orders in order to improve work planning and reviews analysis and recommends corrective action with Maintenance Manager
- ) Performs other tasks and special assignments as requested by the Maintenance Manager / Team Leader
- ) Detailed knowledge of process equipment and unit operations, packaging equipment, HVAC, Steam and Hot Water Systems, controls, electrical and mechanical systems
- ) A 2-year associate's degree in engineering or sciences can substitute for work experience
- ) Equivalent training / experience in a technical career field
- ) Successful completion of a 2 year Associates Degree program in an electrical / mechanical / HVAC career field
- ) An EPA Refrigerant Handling License for Facilities Craft Planner
- ) Hydraulic and Pneumatic skills
- ) Able to read blueprints and shop drawings
- ) The craft planner must react quickly to changes in requirements based on their understanding of priorities
- ) High level interpersonal skills are required to negotiate and persuade
- ) Analytical and troubleshooting skills
- ) Ability to understand budgets, cost estimating, and value to business
3
Maintenance Control Planner Resume Examples & Samples
- Effectively utilizes the planning and scheduling system to conduct maintenance activities to minimize downtime and maximum productivity
- Forecast upcoming maintenance work load in terms of man-hours required and available
- Manages work priority, develops job plans, defines parts and material needed, defines trades and skills, and engage the proper resources and perform the proper research to develop safe and efficient work control plans
- Creates and generates preventative maintenance work orders for property, equipment, and assets
- Responsible in maintaining WO metrics and dashboards identifying and escalating validity, non-compliance, and excessive cost issues
- Follow up on accuracy of job plan for all preventative and corrective maintenance work
- Review all panned work from assigned area to determine validity, accuracy, compliance with regulatory requirements, due dates, accounting unit appropriation, and necessary enterprise approvals
- Obtains all info required for trades-persons to perform the planned work- drawings, manuals, instructions, special procedures, safety precautions, and estimation of supplies needed. Issues priority job plan packets to Shop
- Supervisors for induction into the workforce
- Five years of experience using a CMMS system within Facilities Management to management compliance/regulatory requirements, planning and scheduling work, and material procurement
- Ability to read and comprehend blueprints. Knowledge of Microsoft Software. Experience within the mechanical or electrical trades is preferred
4
Maintenance & Reliability Planner Resume Examples & Samples
- 45%-Key contributor to the work flow process, responsible for maintaining a healthy backlog of planned work orders for execution by additional members of the maintenance team. This will require a firm understanding of the Computerized Maintenance Management System, ASAP as well as an in depth knowledge of the facility’s systems and operations. This position will work closely with the site’s Reliability Coordinator to develop, track and implement maintenance best practices striving to continually improve the planning process and eliminate work order deficiencies
- 35%-Position will be responsible for managing the sites inventory warehouse. This will include managing the procurement, tracking, and organization of all spare parts necessary to maximize the equipment’s availability as well as complete planned/scheduled maintenance activities. This will require the position to be proficient in identifying critical spare parts, creating/modifying SKUs (which Cargill identifies as CCN’s), kitting, inventory, preventative maintenance strategies, and identifying/recording key inventory metrics
- 10%- Attend planning and scheduling meetings with assigned departmental personnel
- 5% - Active member of Maintenance and Reliability team
- 5% - Any other duties as assigned
- Minimum 3 years industrial maintenance experience
- Demonstrated understanding of Maintenance, Repair and Operations (MRO) stores management
- Ability to adapt and learn in a changing work environment
- Microsoft Office Suite experience
- Demonstrated strong problem-solving and analytical skills
- Ability to balance and achieve positive results in the areas of food safety, safety, quality, productivity, cost and employee relations
- Experience with CMMS software
5
Planner Maintenance Resume Examples & Samples
- Conduct field checks on work orders before planning sequence of operations, materials priorities, equipment, and trades times to complete the job
- Estimate time for work orders; prepare schematics or rough sketches, material lists, and specific tools necessary for safety precautions and work to complete the documentation cycle for completions. Develops maintenance labor standards for various maintenance tasks
- Requisitioning and ordering of repair parts from vendors of non-stock parts or working with the stock room on key stock parts in low reserve. (To minimize line down time in the event a spare part is not on site.) To coordinate delivery with the vendor through the most expeditious route to receive the spare parts and to support the efforts to proper store within the Plant
- Monitor, update, and maintain all spare parts between the Maintenance Department and the Stock Room. This excludes engineering capital project work, which will be supported within the Engineering Department
- Sort, distribute, and review maintenance work orders for all three maintenance shifts to include scheduled and non-scheduled work
- To timely, communicate with the customers on requested work and equipment availability and coordinate with the appropriate shift required work that is to be performed and period available to complete work. (Depending on the scope of the work, the planner may be required to be on site to supervise the work as approved by the Maintenance Manager or Maintenance Supervisor.)
- Perform the duties of a Multi-Craft Technician on emergency jobs or low manpower situations
- Check completed work to ensure conformance with workmanship, quality, and compliance
- Assist with maintenance departmental system documentation, updating prints, and (paper/electronic) files (i.e. electrical and mechanical schematics, building structure modifications, etc.) while supporting the Maintenance Department business requirements
- Monitor and direct outside vendors, engineers, contractors, and all other groups performing work at the Plant to assure proper adherence to plant safety requirements, environmental regulations, GMP policies, and Engineering Standards
- In respect to daily activities of planning, the plant operations determine work priorities. Freedom of the job is based on a proven record of performance and the full support and confidence of the plant managers and staff. The planner has the freedom and latitude necessary in an emergency to get the job done. In the course of routine daily events the job is controlled by the customers’ requests, the department manager, common sense and doing what is right
- If the error is not caught, the potential for tens of thousands of dollars of loses and production time lost. ie. Incorrect planning of time to complete job causing production not to start up for hours or days
6
Maintenance & Reliability Planner Resume Examples & Samples
- Possess a high school degree or an approved GED
- Two years experience in maintenance
- Working knowledge of Computerized Maintenance Management Systems, including Maximo or SAP
- Ability to organize, coordinate and accomplish multiple tasks independently
- Demonstrated effective systematic problem solving skills
- Routine physical activity including standing and walking for several hours at a time, typing, climbing, and lifting approximately 55 lbs
- Bachelors Degree in engineering or other technical disciplines
- 7+ years experience in maintenance or reliability
- Experience working with or establishing a team. Ability to be a team leader
- Conversant with Root Cause Analysis, Reliability Centered Maintenance and Failure Mode Effects Analysis
7
Maintenance & Turnaround Planner Resume Examples & Samples
- Lead the execution of the outage planning process within the region
- Assist plant management in identifying and prioritizing tasks during the planning process
- Ensure all projected and prioritized safety, policy, preventive, predictive, project, overhaul and corrective tasks requiring equipment, plant or site outages are included in outage plan
- Complete detailed planning for prioritized work in consultation with subject matter experts as needed
- Ensure completeness of final outage plans – including, but not limited to; equipment lockout, labor, parts, contractor services, tools, equipment, documents, permits, un-isolation, commissioning activities and other associated requirements to safely, efficiently and effectively complete tasks
- Ensure accurate estimating of time and costs for outage plans
- Create outage execution plans and MS Project schedules for significant plant maintenance and reliability projects within the assigned region
- Support timely and accurate procurement and expediting of all parts, equipment and services to execute outages on schedule
- Communicate and publish outage schedules as required
- Schedule and lead post-outage review activities
- Monitor planning KPI’s and assist in identifying and implementing opportunities for continuous improvement
- High school diploma with relative technical school/ completed apprenticeship OR relative experience will be given consideration in lieu of formal education and training
- Minimum 5 years of industrial maintenance, reliability or project management experience
- Minimum of 3 years of planning or maintenance leadership experience within an industrial maintenance and reliability environment
- Extensive experience developing schedules utilizing planning software
- Experience using CMMS systems
- Knowledge of common production equipment such as centrifugal compressors, reciprocating compressors, gearboxes, motors, electrical distribution systems, instrumentation systems and fixed equipment
- Knowledge of standard industrial safety procedures such as lock-out/tag-out, confined space entry, hot work permit, elevated work, blinding, isolations, purging, mobile equipment operation and permitting
- Knowledge of standard maintenance and repair procedures such as pipe-fitting, pressure testing, equipment alignments, precision measurements, disassembly and assembly procedures of rotating and fixed equipment, instrument calibrations, electrical testing and maintenance of motors, sub stations and electrical distribution equipment
- Highly experienced with MS office products such as Excel, PowerPoint, Word and Visio
- Ability to work independently as well as lead/participate on teams
- Self-starter who effectively manages multiple tasks under time and cost pressure; assigns appropriate priorities to competing interests; and achieves results with minimal supervision
- Technical Associates or Bachelor’s Degree in Engineering or Engineering Technology
- Certification in Project Management or experience in project management
- Understanding of regulatory and industrial standards and codes
- Expert knowledge of MS Project planning and scheduling software
- 5 years + Maintenance and Project Planning in a Chemical, Refining or Air Separation Facility
- Experience in CMMS systems such as Infor EAM
- Hands-on experience in installation, maintenance and repair of production equipment such as centrifugal compressors, reciprocating compressors, pumps, gearboxes, heat exchangers, motors, electrical distribution systems, instrumentation systems and fixed equipment
8
Maintenance Outage Planner Resume Examples & Samples
- Develop and maintain the Plant’s Four (4) Week Plan by scheduling all maintenance activities for all departments
- Develop outage work packages and plans for Planned, Forced and Maintenance outages, and utilizing Critical Path Method (CPM) schedules when appropriate
- Enhance work productivity by providing detailed work plans and work packages, coordinating materials ordering and staging, and providing effective communication between maintenance groups and Planning & Scheduling
- Provide coordination during outages and for other on-site and off-site contract labor needs (i.e. equipment rebuilds and parts refurbishment), seeking out and recommending the most cost-effective solutions
- Actively support system owners in optimizing maintenance strategies
- Optimize spare parts, material and equipment stocking levels and inventories
- Administer the Enterprise Solutions Systems through development of the plant equipment database and warranty program, processing of prioritized work orders, updating equipment records, and maintaining equipment historical database, including bill of materials, equipment procedures, etc
- Provide planning activities that fully meet or exceed the expectation as listed in the Southern Generation Playbook
9
Planner, Maintenance & Turnaround Resume Examples & Samples
- Process approved work requests based on priority and risk rank
- Provide feedback to the cross-functional team on approved work request quality and/or flag any constraints that prevent planning as requested
- Verify the approved work requests in the field so that they can be planned effectively, and are environmentally, health and safety conscious
- Prepare structured job plans from approved work requests with effective breakdown of the work required including all operation steps and duration, resources, all relevant documentation, and planned cost
- Provide support to reliability to create and optimize program job plans and review and release cyclical program job plans
- Identify continuous improvement opportunities by using and improving plan templates and soliciting feedback from a variety of stakeholders both during the planning process and following work execution
- Understand and apply the maintenance and reliability standard, other applicable standards, policies, procedures, all relevant key performance indicators, guidance documents and updates
- Participate in field coordination activities during the turnaround execution window
- Five or more years of planning and coordinating maintenance and turnaround activities is an asset
- Experience in the oil and gas or similar industrial environment is an asset
- Post-secondary degree, diploma or trade certification in a relevant technical field is an asset
- Computer proficiency specifically in the Microsoft Office suite; working knowledge of computerized maintenance management systems (preferably SAP and/or Primavera) and material management systems
- General technical understanding of the oil and gas industry and mechanical equipment; knowledge of standard components, typical issues, regular maintenance expectations for exchangers, valves, compressors, piping circuits, analyzers, etc
10
Maintenance & Reliability Planner Resume Examples & Samples
- Develops and oversees the planning and execution of preventive and predictive maintenance activities
- Develops maintenance plans (daily, weekly, master)
- Responsible for the adaptation and implementation of CMMS Software - Computerized Maintenance Management System
- Continually reviews the PM Program to ensure proper content and frequency
- Develops and monitors the Reliability goals and objectives
- Ensure the workorder backlog is managed and controlled
- Monitors the development of Shutdown Plans, as needed
- Assists in the development and execution of an Autonomous Maintenance strategy
- Assists in reviewing equipment downtime data, performing Root Cause Analysis (RCA) and provides focus on problem areas
- Develops plans to eliminate or deal with systemic failures
- Provides guidance and priorities for increased Reliability
- Ensuring that all internal control procedure are correctly followed
- Responsible for managing all spare parts inventories and cost controls
- High School Diploma/GED with substantial experience in manufacturing maintenance and reliability required
- Bachelor's Degree in an engineering, technology or scientific related discipline is preferred
- Experience developing preventive and predictive maintenance plans
- Experience with CMMS Software required – (Computerized Maintenance Management System)
- Experience in a GMP regulated manufacturing environment is preferred
- Experience participating in LEAN manufacturing events, Maintenance Reliability, Set up time reduction, Kanban, Kaizen, SMED, RCA and Problem Solving, preferred
- Possess advanced computer literacyEEO/AA/M/F/Veteran/Disabled
11
Maintenance Supervisor / Planner Resume Examples & Samples
- Supervises and plans maintenance activities of Machinist as well as related outside contractors to ensure the plant operates safely and efficiently
- Works closely with the Maintenance Manager and others in the Maintenance department to establish and achieve specified goals and objectives
- Assists with planning and support for special demands, i.e., shut-downs, turnarounds or other projects. Assists Engineering groups with problem areas
- Maintains high safety standards by enforcing plant policies and providing immediate on-the-spot safety observations
- Works closely with Operations to plan and schedule maintenance work
- Troubleshoots equipment failures and implements new methods and repair strategies to optimize unit up-time. Seeks methods to minimize costs
- Trains people in Safety, Work Methods, Regulations, etc. Complies with parameters of the union contract and government regulations
- Participates in Safety and Environmental initiatives that will contribute to compliance of State/Federal regulations and improve existing Company programs
- Diploma or GED is required
- 8+ Years Chemical and/or Refining Industry Experience
- Minimum of 4 years of maintenance experience in the chemical and/or refining industries
- Minimum of 2 years planning experience or maintenance supervisor experience (step-up supervisor experience is acceptable)
- Knowledge and experience of how to specify, troubleshoot, install and maintain plant mechanical equipment
- Excellent interpersonal and communication skills (both oral and written) with the ability to effectively interact and communicate with all departments and levels of the organization
- Must be proactive, self-motivated and demonstrate ability to handle multiple projects, changing priorities and frequently heavy workloads which may require work in addition to normal working hours. Good problem solving skills a must
- Proficient computer skills with databases and spreadsheets and MS Office Suite
- Must have a valid drivers license
- Must be authorized to work in the US
12
Maintenance Technician Maximo Planner Resume Examples & Samples
- Performs duties and responsibilities as required per Work Instructions and S.O.P guidelines
- Participates in corrective maintenance and PM scheduling for all department employees, across all shifts, based on work load and production priorities
- Guides maintenance employees in documenting maintenance data in Maximo
- Supports daily shift changeover meetings to discuss machine priorities, projects and other department concerns
- Works directly with Maintenance Supervisor to ensure minimal production machine downtime
- Participates in the review and completion of weekly PMs, CMs, and Project work orders in the ECMMS system
- Assists with planning of all equipment installations, relocations and completion of required documentation
- Works with other department leaders and support groups to minimize equipment failures
- Performs other related job duties as required
- Knows and supports all safety laws and policies that apply to the maintenance department
- Demonstrates the highest level of professionalism, ethics and compliance at all times
- A minimum of an Associate’s Degree or equivalent is preferred
- Technical school preferred
- A minimum of 4 years related experience is required
- Experience working with CNC Mills, Lathes, Grinders and EDMs and Robots preferred. Experience maintaining mechanical, electrical/electronic, hydraulic and pneumatic equipment components preferred
- Basic computer skills required
- Must be able to communicate (read, write and speak) effectively in English
- Must have strong communication and interpersonal skills
- Ability to lift heavy loads, stand and/or walk more than 90% of the time and perform twisting and turning activities required
- Ability to work in confined or awkward areas, climb ladders and work from heights required
- A valid driver's license is required
- Must be a team player and be able to work with minimal technical supervision.Facilities (Eng)
13
Planner, Maintenance Resume Examples & Samples
- Efficiently planning and tracking predictive and corrective maintenance activities
- Serving as primary back-up to Maintenance Supervisor
- Ensuring equipment reliability adheres to plan and meets reliability metrics
- The ability to prioritize and manage multiple competing requests while maintaining a culture of accountability and execution
- Ability to effectively communicate and problem solve
- Strong technical aptitude and proficiency in Microsoft office
14
Planner Base Maintenance Resume Examples & Samples
- High School Diploma or equivalent
- One of the following
- Certificate of completion of accredited aircraft maintenance school
- Possess a two year college degree in an aircraft maintenance field
- One year experience in material management or two years’ experience in an aircraft maintenance and/ or flight operations/ logistics field
- Dependability and good work attendance records are essential
- Must not be on a disciplinary level
- Must remain in this position for a minimum of 18 months
- Good computer skills with strong working knowledge of current planning software requirements preferred
15
Planner Maintenance Resume Examples & Samples
- Maintain a high commitment to personal safety and integrity of the environment and equipment during the planning of work orders
- Makes safety procedures, including Lock-Out/Tag-Out/Try-Out and other isolation procedures are available to employees performing the work
- Ensures that all aspects of the company safety policy are incorporated into the job plan
- Responsible for initial screening of incoming work orders, identification of scope and analysis of required level of planning
- Conduct field walk downs to identify and document job requirements
- Develop and maintain an overall maintenance program that will ensure production goals are maintained
- Coordinate mobile and stationary crane and lifting device inspections/certifications
- Assist user groups in identifying and resolving maintenance related problems, energy usage, mechanical integrity and safety
- Plan Maintenance work orders for all work to be performed by the respective maintenance areas
- Maintain up to date history for each piece of equipment
- Participate in the application of Reliability Methodologies for supporting the continuous improvement of maintenance strategies (RCM, RCA, FMECA, Criticality analysis, etc.)
- Reviews work requests for each significant piece of information, requirements for MOC’s
- Develop job plans for planned work
- Coordinate maintenance activity with production
- Develop and manage shutdown plans
- Maintain integrity of PM program, i.e., checklists, triggers, frequency, compliance, and schedules
- Assist in establishing and maintaining equipment parts catalog, equipment history, storeroom, min. / max. levels
- Compile weekly compliance reports and KPI’s
- Coordinate special programs (i.e. pressure vessel inspections, equipment surveys etc.)
- Identify recurring maintenance problems and report as required
- Managing work to the maintenance budget
- Prepare weekly schedule and facilitate weekly scheduling meeting
- Provide input on the daily schedule for the maintenance supervisor
- Review completed planned work for accuracy and adjust as necessary
- Responsible for the accuracy of Planned Work Orders
- This position will liaise with the Production Maintenance Coordinator and General Foremen to finalize and execute the Maintenance Plan and Schedule in a timely manner
- Will specify the internal and external resource requirements needed for planned work
- Responsible for ensuring that requirements for all permits are identified
- Liaise with site supply chain to
- Thorough understanding of JD Edwards Enterprise One and work management business processes as per RAM
- Mechanical understanding of mining equipment to support effective Planning
- Must be computer literate and have a good understanding of the process and equipment involved
- Understanding of condition monitoring information such as oil analysis, ultrasound, thermography and vibration analysis
- Five years previous experience with mining or similar industry experience with maintenance of heavy equipment is desirable
- A minimum of three years maintenance experience dealing with planning and scheduling processes
- Knowledge of Predictive/Preventive maintenance concepts is a plus
- Leadership and capital project experience in a heavy industrial production facility is an added factor in consideration
- Computer proficiency with Outlook, Excel, Word and CMMS is required. Proficiency with MS Project is a plus
16
Maintenance Process Planner Resume Examples & Samples
- Creation of detailed work plans to guide Maintenance Technicians through complicated repair work on test equipment, including
- At least two years experience working in an industrial process maintenance organization interacting with a CMMS package or SpaceX Warpdrive
- Skilled with Microsoft Office (Excel, Powerpoint, Word, Outlook)
- Experience with using lock out/tag out procedures (LOTO)
- Experience working in a maintenance mechanic or industrial electrician role with exposure to process control equipment (valves, regulators, pneumatic actuators, etc.) and industrial equipment (pumps, compressors, hydraulics, electric motors, etc.)
- Experience with writing lock out/tag out (LOTO) procedures on complex fluid process systems
- Experience with cryogenic or high pressure gas systems
- Detailed experience using a CMMS package (SAP, SpaceX Warpdrive, etc.)
- Two year technical degree or applicable industrial maintenance classes
17
Planner, Maintenance Resume Examples & Samples
- Process work requests into work orders for assigned areas
- Develop job plans and coordinate all job planning and preparation for scheduled work
- Coordinate the development of all required (regulatory, company and general practice) routine and preventative maintenance procedures and schedules
- Generate requisitions for the materials and contract services required to execute planned jobs. Assure all materials, equipment and support is available prior to scheduling the work to be performed
- Perform job cost estimating and tracking
- Schedule all active P3 work orders in a four week operational demand-based schedule. Work with operations/maintenance supervision to lock in the subsequent one week schedule
- Perform weekly work order updates with supervision to maintain an active back log of jobs
- Publish the plan of the week for operations and maintenance to review and prepare for the coming distribute crew back logs for completion updates and to obtain scheduling feed back
- Produce and post the weekly KPI reports and other information as required
- Generate and maintain assets and asset bill of materials in EMPAC
- Attend all scheduled planner/scheduler training and assistance with training of new employees or as needed
- Will interact with maintenance, plant and pipeline operations department as well as external customers to the fractionator
- High school diploma or G.E.D. equivalent is required
- 5+ years maintenance or operations experience in a natural gas processing/fractionation plant, petrochemical plant, gas gathering or transmission, or refinery is preferred
- Have or develop a broad knowledge of administrative operating procedures in order to effectively comply with company policies and regulatory requirements
- Specific training and/or experience in computer use including the use of word processing, spreadsheet, email, and maintenance management software is essential
- Technical certification or associates degree or equivalent training in a process or mechanical environment or energy related field preferred
- Experience with coordinating maintenance-related work including ordering supplies/materials, scheduling contractors and producing job plans is required
- Light lifting, squatting and climbing in an industrial setting
- Proficiency required in general computer use including word processing, spreadsheets, and email
- Experience using maintenance management software preferred
- Must have effective organizational skills
- Must be a team player that interacts effectively with co-workers in a group or in independent cooperative activities
- Must possess excellent communications skills and have a desire to be a part of a work group that strives for excellence in service to customers and the company
- Must be accountable and self-driven to learn and continuously strive for improvement
18
Maintenance Supervisor / Planner Resume Examples & Samples
- Directing, training and developing maintenance team members for assigned area/shift
- Planning and tracking predictive and corrective maintenance activities
- Using problems solving skills and root cause analysis to resolve and/or mitigate maintenance issues
- Identifying opportunities to eliminate cost and/or waste through applying LEAN manufacturing principals
- Identifying, implementing and documenting maintenance and reliability best practices
- Managing and selecting suppliers/contractors, ordering and allocating parts for specific work orders
- Incorporating a culture of inclusion and continuity within all departments
- Related work experience in manufacturing maintenance
- Strong technical aptitude along with proficiency in Microsoft Office
- Demonstrated ability to lead and motivate others and work with employees at all levels of the organization
19
Maintenance Schedule / Planner Resume Examples & Samples
- Verbal and written communication
- Thorough knowledge and understanding of SAP maintenance modules including work order creation, planning, scheduling, stores, inventories, backlogs, kitting, staging, and all auxiliary functions
- Thorough understanding of industrial mechanical and electrical maintenance activities
- Computer skills
- Ability to build and maintain positive relationships with all associates
- Developing the best course of action based on available information
- Adequate craft knowledge and skill to accurately estimate labor hours, materials, and labor skills needed to complete mechanical, electrical and process controls jobs
- Ability to prioritize work while balancing production needs with availability of parts, and skilled labor
- Demonstrated ability to read and understand blueprints, machine drawings, process drawings and vendor manuals
- Proficient with Microsoft products (Excel, PowerPoint, and Word)
- Perform administrative duties in the SAP maintenance management system
- Serve as a back-up for the Maintenance Mechanical and Electrical Supervisors
- Direct and execute the plants Proactive and Preventive Maintenance program
- Manage, evaluate and report KPI’s for the Maintenance department
- Work with store room, maintenance and purchasing personnel to ensure repair/replacement parts are on hand when needed
- Train co-workers as needed
- Recommend improvements to make the Maintenance system more effective and efficient
- Specify and purchase equipment
- Must be willing to work weekends and holidays as conditions require and provide support as needed
- Coordinate parts and material acquisitions for planned work between the Store Room personnel and /or vendors concerning parts needs, status, tracking and follow-up
- Compiles all pertinent specification sheets, drawings, bill of materials from previous work and work history in the Work Order Package
- Pick and stage parts, tools, instructions, etc. necessary for scheduled work
- Assist in planning and scheduling plant shutdown work activities
- Integrates and/or assists in ensuring that environmental, safety and health requirements are included in work plans
- Manage the status of work orders to completion
- Associates Degree in Engineering or equivalent
- 4+ years industrial experience in fast-paced production environments
- Mechanical/Electrical maintenance background
- In-depth knowledge of SAP maintenance management system
- Strong trouble shooting skills, with the ability to analyze and resolve issues in a timely manner
- Ability to read and comprehend equipment manuals, P&ID’s and schematics
- Bachelor’s degree in Electrical or Mechanical Engineering is preferred
- Physically fit to access equipment and site locations, including the ability to bend, climb stairs/ladders, crawl, twist, walk and lift
- Possess strong communication skills
- Effectively work with others
- Ability to think outside the box
20
Planner Maintenance Resume Examples & Samples
- 70% - Plan future proactive work for the maintenance craft. Includes developing and continuously improving upon job plans, PM's, and PdM activities and the follow-up work generate from the CMMS. Manage and promote plant safety incorporating safety plans, hazards, and precautions into daily planning activities
- 5% - Provide input and support to the maintenance and reliability team, purchasing, and maintenance departments. Track and provide meaningful measures to improve the planning department and efficiency of the craft personnel
- Good knowledge of Maintenance process and activities
- Advanced computer skills
- Extensive knowledge of Maintenance Management System
- Minimum 5 years maintenance experience
- Fluent verbal and written English
- Understanding operating context of site assets / process systems
- Bachelor's degree in engineering or equivalent knowledge
- Working knowledge of Maintenance Management systems
- Conversant with RCFA
- Conversant with RCM / FMEA
- Develop and conduct training/toolboxes (concerning P (d) M Maintenance)
- Working and practical knowledge applicable Pd.M. technologies such as: Vibration Analysis, Oil Analysis, Infra-Red, Ultra Sound, and Motor Circuit Evaluation
21
Maintenance & PSM Planner Resume Examples & Samples
- High School Diploma or GED required with 5-7 years experience. Bachelor’s degree in Engineering, Process Safety, Occupational Safety or related field with 1-2 years experience preferred
- Process Safety Management or Mechanical Integrity experience required
- Maintenance experience – planning projects required
- CMMS experience required. PCMS or Maximo experience preferred
- Experience writing, implementing and following process safety programs required
- API Certification preferred
- Microsoft office suite experience required
- Ability to work independently requiring little supervision
- Ability to set goals and objectives based on team direction
- Time and project management skills
- Excellent written and oral communication skills with the ability to work across teams and functions
- Able to lift 25-50 lbs. unassisted and regularly
- Able to read, write and understand basic English
- Able to see, with or without correction
- Able to wear a respirator
22
Planner Maintenance Resume Examples & Samples
- Review short, mid, and long term maintenance forecasts
- Schedule all maintenance events within the time interval of the task while accounting for manpower, ground time, parts, tooling, facilities, and weather
- Build work packages within M&E System Maintenance & Engineering
- Build Heavy Check Packages and support changes, as needed
- Balance workload and ensure timely publication of the daily workload
- Proficient in TRAX and Sabre/FliteTrac Plot
- Knowledge of Federal Aviation Regulations (FAR), Airworthy Directives (AD) and Service Bulletins (SB) preferred
- Must be legally eligible to work in the country in which the position is located
- Two (2) years aviation experience in Maintenance, Maintenance Planning and/or Materiel Planning
- Prior experience in Maintenance Planning/Routing environment
- Establishing credible cross-divisional relationships
- Results oriented with the ability to balance diverse and dynamic operational requirements
- Strong organizational skills with the ability to manage multiple projects simultaneously
- Ability to work under pressure, multitask and make critical decisions in a fast pace environment
- Identify safety concerns, issues, incidents or hazards that should be reported and report them whenever possible and by any means necessary including JetBlue’s confidential reporting systems (Aviation Safety Action Program (ASAP) or Safety Action Report(SAR))
23
Planner, Process Maintenance Resume Examples & Samples
- Plan, estimate and prepare warehouse materials and major tools. Plan, estimate and obtain procured materials and contracted services according to authorization limits. Manage weekly, monthly and quarterly spend according to budget. Facilitate monitoring, review, approval and payment of suppliers
- Prepare and issue the daily work schedule. Plan capacity for support equipment, logistics, manpower, and workshop space. Filter, prioritize, and arrange for the approval of work requests from all sources. Communicate with 'owners' for approval of work requests. Organize staging of materials and tooling in line with the weekly plan
- Maintain a full and complete equipment register for work area. Maintain key standard jobs and APL part listings for all equipment. Ensure accurate register and tracking of rotables and components. Ensure that equipment and material is available when required
- Issue and follow up on preventative maintenance inspections and procedures. Identify, capture, analyze and act on condition monitoring data. Maintain integrity of preventative maintenance triggers and job creation. Prepare and issue schedule of proposed equipment downtime
- Attend daily meetings with Process Maintenance and Process Operations representatives. Monitor deviations from maintenance plans and provide feedback to operation areas. Prepare weekly summary and exception reports. Facilitate weekly maintenance scheduling meetings
- Prepare long term plans and schedules for review and approval by management. Assist with preparation of annual budget and quarterly forecasts. Prepare and issue recommendations for long-range schedules, budgets and forecasts. Forecast life-of-mine maintenance requirements based on Planning forecasts. Forecast long-term materials requirements in conjunction with SCM
- Prepare short- and medium-term maintenance plans, reducing down time and maintenance costs
- Lead by example in all aspects of Newmont's visions, values, and social responsibility. Comply with state and federal health and safety regulations, company policies and procedures and the company's environmental compliance policy
- Mining or heavy industry experience desired
- Supervisory experience a plus Experience with manual and computerized maintenance planning systems
- Ellipse experience will be highly regarded
- PC skills using office software such as MS Project, Excel, Word and Power Point
- Knowledge of relevant standard operating procedures, especially in maintenance
- Interpersonal relationship skills and problem solving skills are required
- Awareness of the Mines Safety and Inspection Act and Regulations