Plant Manager Resume Samples
4.7
(120 votes) for
Plant Manager Resume Samples
The Guide To Resume Tailoring
Guide the recruiter to the conclusion that you are the best candidate for the plant manager job. It’s actually very simple. Tailor your resume by picking relevant responsibilities from the examples below and then add your accomplishments. This way, you can position yourself in the best way to get hired.
Craft your perfect resume by picking job responsibilities written by professional recruiters
Pick from the thousands of curated job responsibilities used by the leading companies
Tailor your resume & cover letter with wording that best fits for each job you apply
Resume Builder
Create a Resume in Minutes with Professional Resume Templates
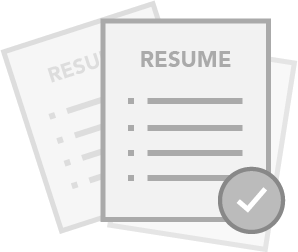
CHOOSE THE BEST TEMPLATE
- Choose from 15 Leading Templates. No need to think about design details.
USE PRE-WRITTEN BULLET POINTS
- Select from thousands of pre-written bullet points.
SAVE YOUR DOCUMENTS IN PDF FILES
- Instantly download in PDF format or share a custom link.
VJ
V Johnson
Vernice
Johnson
56001 Casper Squares
New York
NY
+1 (555) 430 5257
56001 Casper Squares
New York
NY
Phone
p
+1 (555) 430 5257
Experience
Experience
Houston, TX
Plant Manager
Houston, TX
Cormier and Sons
Houston, TX
Plant Manager
- Create a workplace that fosters a stellar safety work record and encourages constant improvement in our safety metrics
- Improve and develop organization capabilities through effective performance management and planning/utilization of human and capital resources
- Provides direction, ensures resources and manages programs to ensure the plant's safety and environmental performance meets established goals
- Provides direction, ensures resources and manages programs to ensure the plant's safety and environmental performance to meet established goals
- Develop and manage plant productivity and process improvement plans utilizing continuous improvement techniques
- Develop and manage direct and indirect reports through performance management
- Improve and develop organizational capabilities through effective performance management and planning/utilization of human and capital resources
present
Phoenix, AZ
Plant Manager
Phoenix, AZ
Larkin Inc
present
Phoenix, AZ
Plant Manager
present
- Establishes a baseline that monitors overall plant performance. Manages plant performance improvements based on Key Performance Indicator (KPI) measurements
- Develop and manage the team, including talent development, performance management, and labor management (Organization)
- Develop the plant staff and workforce through the performance management process, including training and development plans for each direct report
- Focus on talent and organizational development, develop an effective succession planning process, and creates a culture focused on continuous improvement
- Develop collaborative interdepartmental working relationships with customer support management, and sales management to maximize customer service
- Develops plant goals and works with and through subordinate associates to achieve results. Works with Plant Supervisor or Asst. Plant Manager to achieve goals
- Improve performance and assure management succession by training, developing and motivating department personnel
Education
Education
Bachelor’s Degree in Engineering
Bachelor’s Degree in Engineering
Ohio University
Bachelor’s Degree in Engineering
Skills
Skills
- Strong technical and analytical ability, including strong problem solving skills and solid judgment
- Considerable attention to detail and uncompromised concern for quality and food safety
- Knowledgeable of Quality Management System elements and application
- Strong written and verbal skills and the ability to complete detailed reports and make presentations
- Strong leadership skills, including the ability to influence key contributors and build a strong team
- Proficiency working with appropriate software programs; solid working knowledge of domain administration, user account management, network infrastructure
- Strong influential ability. Excellent communication and presentation skills
- A strong ability to be adaptable and flexible
- Strong believer in personal learning and self development and has a strong sense of 'self knowledge'
- Strong technical knowledge covering a wide range of production and manufacturing operating processes. Previous exposure to maintenance activities is desirable
15 Plant Manager resume templates
Read our complete resume writing guides
1
Plant Manager Resume Examples & Samples
- Responsible for managing the operation function concurrent with business growth, introduction of new operational systems, changes to systems and components, meeting subsidiary financial objectives, ensuring safety or operations and employees, on-time production and quality of output
- Assesses and assists in upgrading the supervisory and operators talent and skills bases to achieve growth and meet market needs such as reduced cost, efficient production cycle times and reliable delivery
- Researches, plans, targets and controls reductions in costs of operations. Achieves yearly financial objectives. Prepares, controls and forecasts departmental budget
- Ensure that operating plans and methods to achieve maximum plant performance and reliability while maintaining EH&S compliance requirements
- Coordinates plant maintenance schedules with the maintenance department and directs plant water chemistry program and plant security
- Insures proper implementation of LOTO clearance procedure by plant personnel and customers
- Implement other safety procedures as needed
- Works closely with customers, utilities, and other departments to coordinate maintenance work or required shutdowns
- Focus for long term goals are the formulation, planning and implementation of strategies in conjunction with those of the customer and the Company
- Bachelor's degree in Mechanical or Electrical Engineering with a concentration in power systems or equivalent work experience
- 10 years' experience in a power plant with knowledge of boiler plant design and operations, steam and/or chilled water production, heat transfer, thermodynamics and safety procedures
- 5 years' recent experience supervising a staff in a district energy/steam production facility, central plant, building or large facility as a Plant Manager or General Manager
- 5 years' experience in utility or industrial environment as operations supervisor or managing supervisors of non-exempt operations workers
- Ability to read, write and understand the English language in both written and verbal forms
2
Plant Manager Resume Examples & Samples
- Insuring safety rules and guidelines are inhered to by all
- Responsible for managing the production operation functions of the plant
- Assesses and assists in upgrading the supervisory and operators talent and skills bases to achieve growth and meet market needs such as reduced cost, efficient production cycle times, uptimes and reliable delivery
- Coordinates plant PM schedules with the maintenance department to insure equipment is maintained
- Lead the team in meeting or exceeding our quality goals and ejectives
- Works closely with customers and other departments to coordinate maintenance work or required shutdowns
- Setting manning requirements and schedules to meet customer demands
- Participates in formulating and administering company policies, directing and coordinating all department activities to develop and implement long range goals and objectives to meet business and profitability growth objectives
- Manages policy deployment in the areas of Lean Manufacturing techniques, quality, cost reduction, complete and on-time delivery, safety, customer satisfaction, employee relations, visual controls and plant performance measures
- Confers with the Operations Manager and other managers to review achievements and discuss required changes in goals or objectives resulting from current status and conditions
- Reviews analyses of activities, costs, operations, and forecast data to determine department progress toward stated goals and objectives
- Oversees manufacturing operating reports to resolve operational, manufacturing, and facility problems to ensure minimum costs and prevent operational delays and to meet future growth
- Oversees key projects, processes and performance reports, data and analysis related to production
- Reviews operations and confers with technical or administrative staff to resolve production or processing problems
- Reviews with staff processing schedules and production orders to make decisions concerning inventory requirements, staffing requirements, work procedures, duty assignments, considering budgetary limitations and time constraints
- Ability to analyze plant data and apply results to produce desired business objectives
- Demonstrated ability to lead and coordinate activities of others
- Kaizen and Lean Manufacturing techniques
- Technical skills in materials and inventory management, production scheduling, preventive maintenance and the day to day operations of a large manufacturing operation
- Planning: Ability to perform short and long range planning
- Excellent project and program management skills
- Quality orientation and attention to detail
- Problem analysis and problem resolution
3
Plant Manager Resume Examples & Samples
- A minimum of seven years' experience in both water treatment processes and mechanical/electrical systems
- An appropriate engineering qualification, third level degree or equivalent
- Supervisory experience in Preventative Maintenance and asset management planning
- Experience in leading a team of crafts people and sub-contractors
- Proven track record in efficiently managing energy and chemicals usage through Continuous Improvement tools and techniques
- Thorough understanding of the Contract and contract deliverables
- Build and maintain a good working relationship with the Client
- Liaising with regulatory bodies such as the EPA, HSA, and Local Authorities
- Managing all company and legislative H&S requirements for the Plant
- Managing the Contract within defined budgets and programme
- Ensure all ISO accreditations are maintained
- Ability to work on own initiative and effectively manage & coordinate site activities
- Practical site experience with good organisational and time management skills
- Proficiency in computing programmes including Microsoft Word, Powerpoint and Excel
- Commercial decision making including procurement of services and equipment
- Strong communication skills including report writing
- Good team player
4
Plant Manager Resume Examples & Samples
- Bachelor's or equivalent work experience in a related field
- 10 or more years of increasingly responsible experience in manufacturing, with a minimum of 5 years of supervisory and management experience
- Must have working knowledge of Lean Manufacturing, Toyota Production System, TWI, Takt Time, Kaizen, 5S, Pull and Kanban principles
- Desire to lead in a continuous improvement environment with the ability to use coaching techniques that stress root-cause problem solving
- Demonstrated project management skills
- Strong computer skills, particularly Microsoft Office and Shop Floor
5
Plant Manager Resume Examples & Samples
- Aid Production Manager in ensuring that all operators are properly trained to operate the equipment in a safe, efficient manner
- Help control costs of material, direct/indirect labor and equipment in accordance to budget
- Direct and supervise the production employees
- Maintain compliance with all Federal, State and Local laws/regulations that affect Market Center operations and safety, while promoting safety policies and awareness
- If in a union facility, aid in developing an effective management/labor relationship
- Assist Production Manager with performance evaluations for employees
- High School Diploma or equivalent; Bachelor’s Degree preferred
- Minimum one plus years of supervisory experience in a fast-paced production environment preferred
- Previous Budget and Profit & Loss responsibility preferred
- Familiarity with OSHA and safety regulations
- Ability to work in an adverse environment with varying temperatures and conditions seasonally
- Safely lift and carry up to 50 lbs when necessary
- Remain standing/walking for extended amounts of time daily
- Successful completion of Criminal Background and Drug Screen checks
6
Plant Manager Resume Examples & Samples
- Providing clear, strong leadership
- Ensuring that health and safety systems and processes are in place prior to commencement and are implemented and maintained
- Creating the framework for and then overseeing and reporting on site key performance indicators
- Ensuring there is in place a technical and development mechanism to bring together the commissioning and technical expertise of the existing structure and the new operating team to provide support to the managing staff and operators
- Along with the Site Technical Manager set appropriate quality and environmental standards and put in place the necessary procedures, traceability and targets to ensure standards are met
- Liase with the regulatory bodies and Site Technical Manager to ensure the Site meets all the necessary consents and report any contraventions in good time and through the Company structure
- Along with the Operations Engineer ensure the assets are well maintained and that all necessary inspections and audits are in place to ensure safe and efficient operation of all aspects of the site
- Driving the strategic improvement of the operation of the Works in line with the Company strategic plan
- Together with the Production Director controlling the commercial aspects and logistics of raw material supply, minimising product cost and overheads
- Financial responsibility the operational activities of the Works including maximising gross margin by reducing direct costs
- A degree or equivalent technical qualification, preferably in mechanical, electrical, chemical or process engineering
- Several years management experience in a heavy industry
- Commercial acumen with understanding of operational finance management, including full product costing experience
- Good management skills - must be able to get things done through people and have a highly 'visible' management style
- Experience of operating/maintaining safety systems, preferably with NEBOSH certificate qualification (or equivalent)
- Strong IT skills, including MS Office, and ideally experience of Access
- A 'team player' with excellent communication skills
- A self starter with the initiative and ability to lead other people in developing the operations and achieving KPI's
- Process driven with a pragmatic, hands-on approach
- Ability to work across all levels of the organisation
7
Plant Manager Resume Examples & Samples
- Deliver Plant results against KPM objectives (safety, quality, cost, service)
- Develop strategy and action plans (capital and non-capital) to improve plant performance over the short and long term
- Improve performance and assure management succession by training, developing and motivating department personnel
- Must deliver short term results
- Must have a can do attitude and project this to direct reports. Good communication and personal skills are essential
- Must maintain a positive working relationship with the Union
- Minimum 7 years management experience in related area
- Must have good leadership skills (communication, performance mgmt, motivational)
- Must have good planning and organizational skills
- Must have a technical background, understand plant systems
- Must have a working knowledge of the Collective agreement
- Must have a working knowledge of the Occupational Health & Safety Act
- Cross functional knowledge is definite asset. (Logistics, quality, planning, engineering, etc.)
- Negotiations skills are an asset
8
Plant Manager Resume Examples & Samples
- To develop and implement the on-going strategic programme for the business with particular emphasis on the operating performance through capacity enhancement and efficiency step change
- To implement world-class quality processes, which will generate a competitive lever in providing customer solutions
- To promote and implement best practice Health & Safety policies and procedures
- Continue to cultivate and implement performance measures to ensure that the business performs at world class manufacturing standards
- Ensure production targets (throughput, yields, recoveries) are met
- Continuously develop operating performance through the use of GPS tools (Lean Manufacturing) and techniques
- Ensure compliance with regulatory requirements
- Planning and preparation of annual operating and capital budgets
- Develop a strong integrated relationship with the Supply Chain, Commercial, Finance, IT, HR and Milk Assembly functions
- Third level qualification in an Engineering, Food Science or related discipline
- Minimum of 5 years experience at a senior level/Plant Manager level in a food or pharma manufacturing business or facility
- Experience in operating in a lean manufacturing environment which operated to GMP standards would be a distinct advantage
- Proven commercial acumen to meet strategic operational imperatives
- Results driven, performance capability in a fast moving business environment
- Excellent leadership and communication skills to motivate a multi-disciplinary plant management team
- Ability to liaise effectively with internal and external stakeholders
9
Plant Manager Resume Examples & Samples
- Major contact to customers in plant
- Contact to authorities
- Budget Plan and control of plant
- Decisions for investments within budget < $2000.00 (Financial commitments and small investments)
- Control of productivity
- Control of manpower vs. workload – Review amount of people to workload. Authority to hire staff (assembly/logistics workers) within budget plan and authority to approve overtime hours within budget constraints
- Preparing reports to Management
- Preparing meeting structure
- Stock Control
- Supervise Production and Logistics
- B.S. in Science or Engineering or related technical field required or sufficient experience
- 8+ years supervisory experience in an automotive supplier-related environment required, in automotive assembly and production related to convertible top systems preferred
- A high-level of organizational and analytical ability is essential to plan and manage a multitude of production activities to meet required production scheduling and quality standards
- Overall knowledge of JIT manufacturing and ergonomics is necessary
- Knowledge of manufacturing safety standards and requirements
- Specific knowledge reading drawings and sketches is required for following assembly documentation
- An understanding of computer-based automotive design process software is beneficial in this regard
- Excellent written and verbal communication skills are equally important to effectively interface with direct reports, advanced, project, quality and manufacturing engineering resources to support pre-production and production product development and collaborate on process improvements for cost-savings opportunities
10
Plant Manager Resume Examples & Samples
- Manage overall production and planning to control output and quality
- Manage all the resources of the plant
- Maintain all the manufacturing equipment, make sure the operation align with EHS standards
- Define budget with finance and manage it accordingly, tracking cost savings
- Work in partnership with marketing team to ensure new product introduction
11
Plant Manager Resume Examples & Samples
- Manage the production resources (manpower, machine and materials) to the optimum level of productivity and efficiency
- Implement production plans based on sales forecast and ensure availability of required products at the right quality and quantity, at the right cost to serve the needs of customer
- Handle project management, implementation and control
- Promote and ensure plant safety, orderliness and cleanliness. Plant compliance to all government requirements in its performance of business
- Manage manufacturing cost and takes immediate actions on deviations
- Lead and manage the performance of direct reports and employees in operations
- Graduate of Bachelor’s degree in Engineering or other relevant fields of study
- With at least five (5) years’ work experience as a Production and/or Plant Manager, including a comprehensive leadership background in a manufacturing environment
- Extensive experience and knowledge of safety and quality standards
- Customer-oriented and with good leadership and planning ability
- With ability to understand and analyze data, issues and manage a project from conception to implementation
12
Plant Manager Resume Examples & Samples
- Minimum 8+ years in Plant Operations management experience / Production / Maintenance related field
- Demonstrated ability to connect functional execution to business strategy
- Good communication skills both written and verbal
- Collaborative approach to problem solving
- Good analytical skills
- Self motivated, results oriented with focus on continuous improvement
- Billingual (English and Bahasa Malaysia and/or other appropriate language)
- Prior experience and knowledge in Manufacturing and Engineering : quality management systems, operations excellence, process improvement, six sigma’Lean manufacturing, TQM, TPM
- Prior experience managing multiple projects and Project managements
13
Plant Manager Resume Examples & Samples
- 50% - Productivity
- Understand the Model Mill program and accounting report and actively use them to measure and improve performance, develop costs and budget, and impact on business unit margin management and pricing
- Understand and use LRT or an up-to-date scheduling program to the best advantage to improve productivity in the areas of inventory control, production costs and services
- Develop and utilize warehouse square footage and cost return plan to evaluate products inventoried. Mins. and maxs have been developed for effective management
- Lead the location toward the achievement of World Class status
- 20% - Facilities Management
- Oversee the maintenance of the facility’s physical condition and appearance which reflect the standards of quality and service of our business
- Follow specifications that follow the guidelines for general repair and capital projects
- Use the preventive maintenance audit system to improve maintenance and operational efficiency
- Manage improvements and repairs as cost effectively while maintaining the business unit standards in housekeeping, safety, quality, service and brand image
- Develop and enforce a security program that protects Cargill assets and safeguards the corporation against third party liabilities
- Complete annual environmental audit and insure compliance in all areas
- Maintain a record of all location's environmental and operating permits, including expiration dates
- Apply for permit renewals, when necessary, or any time that physical or equipment changes are made to the facility
- Have a training program to insure that all employees are informed of hazardous materials, spill reporting and other pertinent environmental activities
- 10% - Product Quality/Food Safety
- Manage receipt of raw materials to assure they meet specifications
- Understands and complies with Cargill Animal Nutrition Quality Control and Food Safety Programs
- Assures the formulas are reviewed before manufacturing for projected quality control and takes necessary steps to assure all formulas will meet Business Unit quality control needs
- Participate actively in evaluation and effect of ingredients for their potential to impact costs and quality
- 20% - Employee Safety
- Ensure that employees are trained to perform their jobs safely and to accept responsibility for their own safety performance and safety behaviors
- Provide the leadership to develop and direct a safety program and a safety culture
- Actively assure that all incidents are investigated in depth and reported on time
- Understand safety statistics and how they compare to the company goals
- Get personally involved in all areas of safety management at meetings, inspections, investigations, and audits
- Understand and comply with the laws that relate to safety in our business, i.e., OSHA, local ordinances, etc
- Understand and manage the workers compensation claims, vehicle accident claims, property damage claims and insurance inspection reports
- Hold well planned, informative safety meetings with all plant and contract personnel at least monthly
- Have an active near miss reporting program and effectively follow up on the corrective actions
- 3+ years supervisory experience in a feed milling or similar industry OR 5+ years supervisory experience in a manufacturing environment
- Ability to relocate across the United States, potentially multiple times
- Ability to work in the United States without visa sponsorship
- Demonstrated mathematical skills and mechanical aptitude
- Must be able and willing to work from heights (i.e. ladders, catwalks, etc.)
- Working in an indoor/outdoor environment
- Must be able to be on-call to respond to plant emergencies
- Exposure to dust, noise, and temperature fluctuations
14
Plant Manager Resume Examples & Samples
- 40% Operational Effectiveness - Manage and direct the processing and shipment of steel product for timely delivery of material that meets customer requirements at minimum cost. Manage the efficiencies of our plants which will enable us to be the partner of choice for our customers. This focuses on the following: quality management, process improvements, operation costs, and staffing
- 30% Talent Management- Having a talent pipeline with effective, diverse leaders who are well trained, engaged, and focused on operational excellence for today and for the future. This focuses on the following: training and development, engagement, hiring and retaining diverse talent, fostering a balance between leadership and technical expertise, and building a culture focused on operational excellence
- 20% Manage day to day activities such as record keeping, scheduling of working hours, opening or closing of the plant, maintenance of equipment, ISO quality, enforcement of safety programs, as well as location, business unit and corporate policies. Operate JDE purchasing process and receive materials and supplies with proper documentation and waste minimization
- 10% Reliability Excellence - Having a strategic approach in which systems, structure, processes, and procedures are in place to create reliable, safe and sustainable plants at the best total cost of ownership. This focuses on the following: best total cost of ownership (operation and maintenance), on-time deliveries, higher plant availability, proactive approach to reliability excellence, and asset health management
- 5+ years supervisory experience
- Proven experience leading high performing teams
- Effective interpersonal communication skills, both verbal and written
- Decision making and problem solving skills
- Demonstrated excellent performance on safety and environmental compliance
- Mechanical, electrical, and hydraulic knowledge to manage preventive maintenance and equipment repair
- Basic operating knowledge of ISO steel quality systems
- Basic proficiency with computers, including familiarity with MS Outlook, MS Word, MS Excel, MS PowerPoint or equivalent. Ability to learn other software programs (STELplan – JDE)
- Must be able to work flexible hours, including some weekend work assignments
15
Plant Manager Resume Examples & Samples
- Thorough knowledge of high-speed manufacturing operations with extensive demonstrated managerial skills
- Proven leadership and communication skills with an emphasis on seeking and achieving innovative “Win-Win” outcomes in all areas including labor relations
- Proven ability to play a leading role in executing plant safety and environmental objectives
- BS plus minimum 15 yrs Manufacturing/business experience
- Or Masters degree plus minimum 13 yrs Manufacturing/business experience required
16
Plant Manager Resume Examples & Samples
- Bachelor's degree in industrial engineering, trade school, business administration or similar related discipline preferred; plus at least 5 years of experience in facility operations, preferably in a school setting
- Excellent interpersonal skills and an energetic attitude
- Extreme flexibility, with a strong work ethic and an entrepreneurial spirit to accommodate a high level of responsibility and multiple, changing priorities
- Ability to prioritize tasks and meet strict deadlines is key
- Ability to lead a group and provide constructive and instructive feedback to a team
- Proficiency using computers, printers, copy machines, and fax machines
17
Plant Manager Resume Examples & Samples
- HSE Critical Tasks: Operational management position, including maintenance and design engineering management, leadership of HSE commitments, review of HSE performance, setting priorities, action plans, responsibilities, performance of and supervision of staff performing HSE Critical Tasks
- Execution of R&D campaigns consistent with priorities and plans, delivering high quality operational and analytical data to the technology teams
- Deliver high equipment availability through preventative engineering and maintenance activities in the R&D and Manufacturing plant areas
- Management of capital projects and spending for the facility
- Development and continued application of physical security for the Site
- Oversight and implementation of IT software and equipment to support R&D data generation and engineering packages and corporate policy
- Represents the Plant and CBI to the community and local industry
- BS Degree in Chemical, Mechanical or Electrical Engineering preferred
- 15+ years of experience with line operation management responsibilities in chemical, petrochemical or refining industries
- Is knowledgeable regarding codes and standards including OSHA PSM requirements
- Ensure safe, effective and compliant operations and maintenance within the responsible areas
- Leading and managing a diverse workforce of regular and contract employees to deliver results using best practices in HSE, operations, laboratory and analytical services quality and costs
- Supporting the broader goals of a dynamic technology provider to the refining and petrochemical industry
- Staff and team development
- Production & Manufacturing Operational Management
- Infuses pride in organizational values and mission
- Understands R&D, Manufacturing needs
- Communicates effectively across many different levels, personalities, cultures
- Understands time management and operational costs
- Motivates the team
- Tracks, measures and holds accountable staff performance
- Sustains a positive learning environment
- Maximizes staff utilization
- Effective delegation of responsibilities
- Upholds standards
18
Plant Manager Resume Examples & Samples
- Direct the manufacturing support activities of maintenance, production control, purchasing, work in process and raw material inventories, accounting and service activities
- Represent the company in the community and promote the Company's goodwill and interests in the community activities
- Develop and maintain an effective staff to insure the continuity of the operation consistent with division objectives
- Confers with customers and representatives of association industries to evaluate and promote improved and expanded services in the area
- Direct and oversee customer activity for new products from initial production trials to full scale production. Ensure equipment and processes are established and plant workforce is properly trained to execute necessary requirements
- Ensure employee health & safety, and ensure compliance with all regulatory requirements related to Health, Safey & Environment
- Manage expenses and productivity to ensure that the location meets/exceeds the expected selling profit
19
Plant Manager Resume Examples & Samples
- 35% - Risk Management - focusing on reducing and managing risks associated with employees, contractors, customers, products, and facilities. This fundamental focuses on the following
- 20% - Operational Effectiveness – taking advantage of business opportunities while making continuous improvements. We need to manage the efficiencies of our plants which will enable us to be the partner of choice for our customers. This fundamental focuses on the following: Grain Quality Management, mix and blend, plant Efficiencies, Process Improvements, Operation costs, Energy management, and Staffing,
- 5% - Capital Effectiveness – using best practices for selecting, planning, developing and executing while consistently delivering successful projects. This fundamental focuses on the following: Contractor safety, Skilled and professional project management and execution, Best total cost of ownership (specification, procurement, and installation), Use the Project Delivery Process (PDP) tools (budget and schedule compliance)
- Bachelors Degree or 4+ years plant operations leadership experience
- 2 years as a Leader and Manager in a business, agricultural related or other
- Ability to influence decision-making
- Capable of delivering innovation
20
Plant Manager Resume Examples & Samples
- 35% - Coordination of functions to achieve corporate, BU, and functional strategy initiatives. Process deployment and results focus
- 20% - Local business strategy development and deployment. Focus on competitive positioning
- 20% - Management of community, Over the Fence (OTF)/JV, customer, and supplier relationships
- 15%- Employee relations, employee development, and culture definition
- 5%- Local risk Management
- 5% - Perform miscellaneous job-related duties as assigned
- Minimum 10 years of experience with plant processes, operations and management
- Business acumen as it relates to sales, marketing, and financial decision-making
- Extensive knowledge of general business functions: Finance, Supply Chain, Merchandising, Quality Assurance, Human Resources, and Sales
- Significant experience and/or exposure to multiple manufacturing locations as well as in multiple functions and/or processing departments
- Demonstrated ability to communicate and present effectively both verbal and written within multiple levels of the organization
- Demonstrated ability to promote and work within an inclusive environment
- Demonstrated ability to balance and achieve positive results in the areas of food safety, safety, quality, productivity, cost and employee relations
21
Plant Manager Resume Examples & Samples
- Manage all aspects of Manheim plant operations which includes inventory/scheduling, manpower, machinery, engineering, Quality, IT, budget and financial success
- Meet or exceed key measurements/KPIs determined for job role including DIFOT (on time delivery)
- Develop departmental budgets for order intake, billings, profit margin & spending for each business area. Manage, direct & motivate the efforts of business to assure that budgets are achieved or exceeded. Monitor & report performance on a monthly basis & develop action plans to correct deviations, as needed
- Lead, develop and motivate the plant management team to ensure operational excellence in all areas and targets (e.g. production, quality, profit, cost etc.) are met. Create and drive a collaborative work environment on the shop floor
- Manage the Union relationship including dispute resolution, contract negotiation, labor issues, etc
- Responsible for sales & delivery of spare parts. This includes organizing, staffing, directing & monitoring the performance of departments responsible for the sales & order execution, developing & implementing strategies to grow core business & identifying new opportunities for growth where our competencies are a good match & sustainable business can be expected
- Manage inventory levels to reduce slow moving items and ensure availability of critical items to support business needs
- Ensure safe work practices are practiced by all team members. Work with FLSmidth and plant safety teams to stay current on safety policy & guidelines and promote continuous improvement. Maintain compliance with all OSHA and EPA regulations and guidelines. Participate in the Safety Steering committee
- Maintain awareness of industry needs & trends, competitive action & opportunities to market new or improved equipment & solutions
- Maintain visibility as a leader with customers at a senior level as well as internally. Establish instructions, procedures, & policies to ensure that organizational performance is maintained in an efficient & professional manner
- Continuously review the organization to develop, grow & select personnel in order to achieve a desired organizational culture & performance
- Maintain an updated succession plan for all leaders in the business. Provide leadership which forms the foundation of a profitable & sustainable business
- Continuously improve manufacturing environment and the visual plant strategy through 5s organization, 6 Sigma initiatives and updating to the latest ISO and OSHA 18001 standards
- Takes corrective action where performance deviates from plan to ensure delivery of strategic and operational goals like, cost of poor quality, delivery on time in full, reduction of production cost, improvement of inventory turns, safety, etc
- Bachelor’s degree in manufacturing or related field, master’s degree preferred
- 7+ years progressive manufacturing management experience, including at least 5 years of experience in a similar role/level of leadership
- Proven record of safety performance in a manufacturing plant
- Strong business acumen and business management capability, with experience in supply chain, operations, purchasing, planning, materials management, customer service, engineering, product management and field services
- Manufacturing Technology – experience in CNC machining practices
22
Plant Manager Resume Examples & Samples
- Manage material requirements to increase inventory turns and reduce levels on hand
- Manages plant budget and balance work cell capacity/loading across the plant
- Determine operations headcount needs and ensures compliance with Company policies
- Bachelor’s degree
23
Plant Manager Resume Examples & Samples
- Minimum 7 years of related work experience with proven leadership in programs, P&L or supply chain role
- Master’s Degree in Business Administration or Manufacturing / Business / Engineering
- Lean Manufacturing & Six Sigma or Equivalent Quality training
- ISO 9001 Quality Management System knowledge
- Knowledge of the disciplines of manufacturing management such as production and inventory control, variable cost productivity, fulfillment metrics, quality systems, cost systems, and procedures
- ASTM standards knowledge
- Experience managing in a matrix organization
- Black Belt certified or equivalent quality certification
- Financial acumen and ability to interpret financial models
- Experience with proven leadership in manufacturing or supply chain role in a P&L environment
- Proven mentoring and coaching abilities
- Ability to successfully motivate and maintain high morale, employee involvement, safety and teamwork in a cross functional environment
- Ability to engage and energize others
- Strong oral and written communication skills with internal and external teams at all levels of the organization
- Ability to quickly build rapport with GE team and customer base
- Strong problem solving, business and analytical abilities
- Knowledgeable of manufacturing policies and regulations established by GE as well as international recognized standards and other customer requirements
- Previous experience working with P&L Functions
- Ability to effectively manage changing and conflicting priorities and resolve appropriately
24
Plant Manager Resume Examples & Samples
- 35% Risk Management - focusing on reducing and managing risks associated with employees, contractors, customers, products, and facilities. This fundamental focuses on the following
- 20% Operational Effectiveness– taking advantage of business opportunities while making continuous improvements. We need to manage the efficiencies of our plants which will enable us to be the partner of choice for our customers. This fundamental focuses on the following: Grain Quality Management, mix and blend, plant Efficiencies, Process Improvements, Operation costs, Energy management, and Staffing,
- 5% Capital Effectiveness – using best practices for selecting, planning, developing and executing while consistently delivering successful projects. This fundamental focuses on the following: Contractor safety, Skilled and professional project management and execution, Best total cost of ownership (specification, procurement, and installation), Use the Project Delivery Process (PDP) tools (budget and schedule compliance)
- 2 plus years supervising/managing employees
- Experience in administering and/or managing an effective and proactive safety program
25
Plant Manager Resume Examples & Samples
- Guides department managers in the development of labor usage strategies to better the utilize resources, reacting to changes in production demands and deadlines
- Communicates to management and plant personnel Company changes in Kraft Heinz policies, procedures, and strategies
- Oversees the development and implementation of companywide policies and procedures
- Ensures personnel adherence to Kraft Heinz policies, safety standards, and good manufacturing practices
- Actively supports all continuous improvement efforts throughout the plant
- Actively monitors and supports all safety projects and efforts throughout the plant
- Consults with corporate offices and plant management team to develop annual operating budget & ZBB
- Guides management team to ensure plant operates efficiently while meeting or exceeding corporate financial goals
- Reviews detailed labor standards by cost center to support annual budgeting process
- Actively works with the Human Resources Department in policy development, employee grievances, employee development issues, and employee motivation
- Work with Engineering and Maintenance departments to develop strategies to reduce production equipment downtime due to equipment failures
- Actively works with Continuous Improvement Coordinator, Engineering Manager, and Maintenance Manager on equipment process flows, optimization of plant layouts, coordination of shutdowns, and startups due to new production lines and equipment installations
- Oversees Cost Accounting on new products costing, developing standards, analysis of variances, and annual budget process
- Collaborates with department managers to identify and then recommends process improvements to reduce labor, ingredient, and packaging materials cost
- Analyzes plant daily/weekly/monthly spending to keep indirect and fixed cost within standards in order to
- Meet/exceed corporate financial goals
- Supports the R&D team in developing of new products processes, supports production runs, costing of labor, and scrap standards for new products
- With department managers analyzes downtime data to develop downtime reduction strategies
- Analyzes manufacturing variances of ingredient, materials, and labor usage and works with management team to implement strategies to reduce them
- Oversees the preparation of operational schedules and manufacturing activities to ensure that production and quality of products meet specifications
- Identifies and implement continuous improvement initiatives such is labor reduction, waste reduction, and reduction of indirect cost to contribute to factory objectives
26
Plant Manager Resume Examples & Samples
- Ensure plant operations are in compliance with federal and local regulations as well as Ashland Standard Practices
- Responsible for multiple batch reactor operations, blending, and packaging for multiple product lines serving a diverse customer base
- Represent the company to all regulatory officials/auditors; coordinate support from EH&S, Law and
- Bachelor of Science, Chemical Engineering, MBA preferred
- 10-15 years of relevant experience – preferably demonstrating a track record of increased responsibility in a chemical manufacturing environment including roles such as Process and Plant Engineer, Production Supervisor, Quality Control and Operations Management
- Demonstrated passion for safety
- Excellent Leadership and Communications Skills – Willing to serve as a change agent
- Good knowledge of manufacturing processes including financial, inventory management, supply chain, EH&S compliance programs and quality systems
- Experience with recruiting, people management and development
27
Plant Manager Resume Examples & Samples
- You will be responsible for the day to day running of a chemical plant
- Responsible for multi-batch reactor operations for multiple product lines serving a diverse customer base reactors
- Represent the company on all regulatory official auditors and coordinates support from EH&S, Law and other departments as needed to respond to regulatory inspections/audits
- Act as a company liaison with local, state and federal regulatory agencies (DOT, EPA, and OSHA) as well as community agencies, police and fire departments
- Implement and manage facility ISO Certification Policy and Procedure and Responsible Care Compliance
- Develop and manage a facility plan which ensures proper allocation of available assets to meet daily business requirements while effectively managing expenses
- Hire, train, develop and evaluate plant personnel
- Responsible for training programs for all new and current employees
- Assess and upgrade the quality of people performance at the plant
- Develop collaborative interdepartmental working relationships with customer support management, and sales management to maximize customer service
- Develop and manage plant productivity and process improvement plans utilizing continuous improvement techniques
- Manage facility expense budget. Responsible for the annual budgeting process, including capital and expense budgets
- Bachelor of Science, Chemical Engineering preferred
- Minimum of 5 years of experience
- A track record of increased responsibility in a batch chemical manufacturing environment including roles such as Process and Plant Engineer, First Line Supervisor, Quality Control and Operations Management
- Excellent Leadership and Communications Skills
- Willing to serve as a change agent
- Skilled at cultivating positive customer relationships
- Applicants must be authorized to work in the United States
28
Plant Manager Resume Examples & Samples
- Responsible for daily operations of the plant inclusive of trouble shooting and optimum
- Degree / Diploma in related discipline with minimum 3 years experience in manufacturing environment
- Strong leadership skills, highly motivated & mature
- Conversant in English & Bahasa Malaysia
29
Plant Manager Resume Examples & Samples
- Develops and implements plans to reduce environmental waste, meet applicable environmental regulations and handle emergency situations that may occur at the Plant
- Leads Plant's Operational Excellence initiatives
- Ensures the Plant achieves its annual operating cost objectives
- Directs production Managers/supervisors in the execution of their responsibilities to ensure meeting the Plant's objectives
- Effectively and consistently communicates Plant's manufacturing incentive plan goals to employees
- Ensures subordinates career development goals are identified and plans put in place to support them
- Demonstrated track record of success in managing a safe and environmentally sound work environment
- Must be able to interact effectively with employees at all levels of the organization as well as customers and suppliers
- Strong results orientation combined with ability to make sound, reasoned decisions
- Bachelor's degree in engineering, related technical discipline or business, Master's in operations management and/or APICS certification preferred
- Thorough knowledge of manufacturing operations and safety procedures; prior experience in extrusion and/or molding operations strongly preferred
- LI-CB1
30
Plant Manager Resume Examples & Samples
- Assures safe working environment for employees and environmental compliance
- Comprehensive knowledge of FDA, EU and ICH regulatory requirements and the implementation of cGMP processes used in the pharmaceutical and food industries
- Develops the annual operating plan/budgets and continuously reviews the plan compliance with respect to production, yields, and fixed costs. Answers variances from the plan
- Works with the Operations and business leadership team to develop strategy, annual operating and other business plans
- Manages the capital budget for the responsible location
- Implements necessary plant improvements as dictated by business needs
- Champions Six Sigma and Lean Manufacturing initiatives
- Directs manufacturing and shipping to assure timely delivery of product and receipt of raw materials
- Conforms to ISO 9001, ISO 14000 and other manufacturing standards
- BS Degree in a technical discipline (preferably Chemistry or Chemical Engineering)
- Minimum of 10 years of experience as an Operations Manager within a Manufacturing or Pharmaceutical environment to include knowledge of safety, cGMP practices, production, and quality
- Minimum of 5 years of plant and/or regional leadership experience
31
Plant Manager Resume Examples & Samples
- Develop and maintain an effective organization through recruitment, selection, training, compensation, and motivation of employees
- Direct Supervision in the management of their assigned areas to ensure that their responsibilities to attain objectives and satisfactory operations and performance are met in a way that is consistent with established objectives
- Ensure the efficient utilization of resources to enforce and comply with Health, Safety and Environmental (HSE) standards as set forth under various regulatory agencies and Solvay USA Inc
- Additionally, he/she will continually improve process, cost position, while ensuring compliance
- Responsible to deliver EBITDA and cash objectives
- Provide leadership for employee relations through effective communications, coaching, training and development
- Plan the use of facilities, equipment, and personnel to meet current and future production requirements
- Initiate various programs that lead to improved quality, decreased pollutants, waste reduction, overall efficiency and on-time delivery at the lowest possible cost
- Directs those activities that provide assurance that safety, health, and environmental rules
- Direct department managers in the preparation and implementation of plant operating plans and strategies consistent with business requirements
- Determine headcount needs and facilities policies, direct and supervise the application of such policies in the plant’s manufacturing and packaging operations
- Provides expertise to the line organization in the development of standards of performance in all areas of product manufacturing responsibility
- Ensure compliance with applicable laws and regulations issued by TTB, DEA, FDA, OSHA, EEOC, EPA, and federal, state, and local regulations
- Perform other responsibilities as required by the company
- BS in Chemical Engineering, Mechanical Engineering, Chemistry or Materials Science or other related Field. An MBA is Preferred
- Previous supervisory experience leading large scale organization required
- At least 10 years chemical manufacturing experience with increasing responsibilities
- Ability to lead, communicate, develop and direct employees is required
- Understanding of chemical manufacturing facility, in particular batch process design and analysis
- Project management with the Demonstrated ability to deliver projects on time with desired result/outcome within budget
- Experience in consolidating data, analyzing, and reporting results in a succinct style and with impact
- Excellent interpersonal and communication skills and ability to interact with all levels of personnel within and outside the company. Proficient skills in decision making / problem solving / analyzing to meet customer needs and maintain daily operations
32
Plant Manager Resume Examples & Samples
- 35% 1. Risk Management - focusing on reducing and managing risks associated with employees, contractors, customers, products, and facilities. This fundamental focuses on the following
- 20% 4. Operational Effectiveness – taking advantage of business opportunities while making continuous improvements. We need to manage the efficiencies of our plants which will enable us to be the partner of choice for our customers. This fundamental focuses on the following: Grain Quality Management, mix and blend, plant efficiencies, process improvements, operation costs, energy management, and staffing
- 5% 5. Capital Effectiveness – using best practices for selecting, planning, developing and executing while consistently delivering successful projects. This fundamental focuses on the following: Contractor safety, Skilled and professional project management and execution, Best total cost of ownership (specification, procurement, and installation), Use the Project Delivery Process (PDP) tools (budget and schedule compliance)
- Bachelor's Degree or 4+ years of experience in a production facility or management role
- 2+ years in a position as a Leader or Manager in a business, agricultural related or other
- Technical skills are not required upon initial hire into this position. Technical skills will be developed within the first 2 years and beyond for this position
33
Plant Manager Resume Examples & Samples
- Manage daily production on multiple shifts, ensuring compliance with company policies, GMP’s, quality assurance, and established regulations (FDA, EPA, OSHA)
- Be a safety champion by promoting safe behavior, implementing safety programs and oversight of safety training requirements
- Develop an annual operation plan to include productivity and efficiency improvements, automation and quality advancements and employee development
- Ensure facility is operating at best capacity and all equipment and inventory assets are maintained appropriately. Ensure capital and maintenance projects are completed on time and within budget
- Manage all production related expenses (payroll/overtime, inventory, equipment repairs and maintenance, and supplies)
- Work closely with Customer Service and Purchasing departments to help resolve problems with customers, customer service, and sales personnel
- Work closely with Quality to help implement food safety/sanitation/quality programs to ensure that the facility is compliant with the law, regulatory requirements, and company programs along with continuously looking for improvements in QA programs
- Work to find new and more efficient ways to manufacture, ship, and control costs to help add value to ADM and the shareholders
34
Plant Manager Resume Examples & Samples
- 8-10 years of experience in a high volume manufacturing environment, automotive preferred
- Proven experience in team management with leadership and coaching skills
- Ability to attract, retain, and develop high caliber talent
- Proven experience in production management and lean manufacturing
- Demonstrated experience with launching new programs
- Ability to build effective teams
- Ability to build and manage a P&L budget
- Ability to drive for results in all aspects
- Demonstrates a Customer Focused manufacturing philosophy
- Ability to easily navigate and lead others in ambiguious situations
- Develop a continuous improvement focused culture
35
Plant Manager Resume Examples & Samples
- Initially serve as the Project Manager to establish a Dynacraft Texas plant including planning and managing the facility build out, staffing ramp-up, and start of production for product programs
- Responsible for managing plant objectives including safety, quality, on-time delivery, timely product launches and profitability
- Oversee the daily activities of the plant management team and collaborate with on-site and Division support teams (HR, IT, Quality, Accounting, Customer Service, etc.)
- Develop and drive strong culture of high performance, excellent quality and teamwork
- Partner with Human Resources to ensure appropriate staffing levels, training, succession planning, and performance management
- Coordinate and direct major plant projects including but not limited to plant expansion, cost reduction and new product manufacturing setup and implementation
- Maintain and improve quality and environmental standards per ISO, QS and local regulatory requirements
- Plan, prepare, and administer annual capital budgets and develop capital requests for projects supporting plant efficiency, capacity and quality
- Plan, prepare, and administer annual operating budget including responsibility for fiscal management of operating expenses
- Oversee equipment maintenance and calibration programs
- Oversee logistics/returnable container deployment and administration
- Ensure compliance with Corporate and Division policies and procedures
- Bachelor’s degree in business administration, management, engineering or other appropriate field. Master’s degree preferred
- Demonstrated leadership capabilities including creating a culture of high performance and strong employee relationships
- Strong operations management and supervisory experience
- Ability to initiate, lead and implement change through continuous process improvements
- Ability to operate and actively participate in a team-oriented environment
- Excellent verbal and written communication skills including ability to present to executive leadership
36
Plant Manager Resume Examples & Samples
- Provide leadership for the successful day-to-day operation of the facility
- Organise the Plant’s capacity and technical capabilities to meet the planned production schedules as presented by the logistics teams
- Take action to ensure that late production orders or urgent orders are achieved and expedited
- Work closely with quality personnel to review product consistency while monitoring scrap rates to determine trends and areas of improvement
- Review established production schedules for wire and cable to insure established inventory levels are met while operating at the highest efficiency possible
- Coordinate the hiring and training of all manufacturing staff
- Monitor operation expenses and research ways to reduce costs while maintaining product quality
- Work closely with the Environmental Health and Safety team to ensure all members of the manufacturing team are aware of safety policies to provide a safe workplace for our employees
- Maintain and support a superior safety and housekeeping program, including all timely communication initiatives
- Develop and execute the plant manufacturing budgets
- Analyze workforce requirements
- Conduct performance appraisals and provide coaching and guidance to all operations employees
- Encourage and promote operating in a continuous improvement environment
- Remove production constraints; allocate human and equipment resources and direct production employees to attain all established goals
- Remove waste and constraints from the production process to improve efficiencies and enhance productivity
- Communicate with research and development as well as product management personnel to develop new product strategies
- Work with purchasing manager to develop and improve supplier relationships
- Monitor production performance on a daily / weekly basis and formulate corrective actions, where necessary
- Ensure that assembly / ancillary equipment, machine tools and other equipment necessary to maintain production to standard rates are maintained to required maintenance and safety levels by suitably planned maintenance procedures
37
Plant Manager Resume Examples & Samples
- Continually progress and maintain a safe, sustainable, and environmentally responsible workplace by addressing all physical, systemic, and behavioral issues while ensuring compliance with all governmental and UTC policies
- Develop and execute plant operating annual budgets and monthly forecasts. Lead the team in achieving targets, and proactively adjust according to volume and market requirements
- Continue developing and implementing an overall production and manufacturing strategy including infrastructure of systems, processes and personnel designed to accommodate the business strategy as well as maximize results
- Accelerate and successfully achieve UTC ACE (Achieving Competitive Excellence) Gold while applying Lean manufacturing principles
- Coordinate activities between departments promoting a collaborative environment to ensure the best business decisions are fostered to meet or exceed customer expectations
- Achieve plant metrics relative to safety, cost, product/process quality, productivity, and process improvement
- Promote the control of manufacturing processes according to approved methods, quality, and cost standards. Develop, analyze and review a variety of leading/lagging indicators to improve safety, quality, employee engagement, and cost implementing changes as required, to maximize results
- Support the implementation of a new Enterprise Resource Planning system supporting the business and manufacturing operations
- Build and maintain local relationships within the community in which we operate
38
Plant Manager Resume Examples & Samples
- Determines and provides the required resources to ensure the safe, environmentally sound, and efficient satisfaction of our stakeholder’s needs
- Ensures sufficient manpower, training, supervision, technical support, equipment, procedures and systems are in place to get the job done meeting or exceeding all regulatory, corporate and quality requirements
- Directs the actions of Nisku/Leduc staff in order to meet these requirements
- Upholds the principles of Responsible Care and maintains an environment conducive to safe and incident-free chemical production
- Understands, communicates and works to provide the necessary resources to continuously improve the quality, and cost effectiveness, of the process and products manufactured and warehoused in the Nisku and Leduc Plants
- Motivates and develops staff and continuously improves employee relations with all members of the production team
- Ensures facility is operated within, and meets all, governmental, corporate and industry regulations
- Bachelor of Science in Chemistry or Engineering degree (preferably Chemical, Mechanical or Electrical)
- Experience in a manufacturing environment
- Strong leadership and people management skills
- Computer literacy including SAP, WORD, WINDOWS, EXCEL
39
Plant Manager Resume Examples & Samples
- Bachelor’s degree required in business or engineering
- Minimum 5 years of experience in a manufacturing environment
- Minimum of 3 years of supervisory/managerial experience
- Master’s degree in business or engineering
- APICS Certification
- Six Sigma Certification
- Experience interacting with internal and external customers
- Strong analytical thinking skills; intellectual rigor and curiosity; problem-solving capability
- Data-driven, disciplined, objective, and detail-oriented
- Acts as a business partner; sees the big picture and works through ambiguity and change
- Ability to be energetic, a critical thinker, skilled in driving process improvement
- Leadership and sense of urgency: ability to drive to positive results in a complex environment
- Strong ability to develop and motivate people
- Effective use of communication and tact with internal and external stakeholders
- General knowledge of engineering, supply chain, manufacturing, operational excellence principles and systems
- Knowledge of manufacturing financial statements and the ability to analyze and interpret financial reports
40
Plant Manager Resume Examples & Samples
- Maintain effective communication and coordination with all internal customers, leaders, team members; maintain positive employee relations; listen to issues and concerns and respond (C48) within 48 hours
- Ensure production is maintained by ensuring quality is maintained
- Responsible for managing the production operation
- Assesses and assists in upgrading the supervisory and operators talent and skill base to achieve growth and meet market needs such as reduced cost, efficient production cycle times, uptimes and reliable delivery
- Researches, plans, targets and controls reduction of costs operations. Achieves yearly financial objectives. Prepares, controls and forecasts departmental budget
- Ensure that operating plans and methods to achieve maximum business unit performance and reliability while maintaining EH&S compliance requirements
- Lead the team in meeting or exceeding our quality goals and objectives
- Manages policy deployment in the areas of Lean Manufacturing techniques, quality, cost reduction, complete and on-time delivery, safety, customer satisfaction, employee relations, visual controls and business unit performance measures
- Confers with the General Manager and other managers to review achievements and discuss required changes in goals or objectives resulting from current status and conditions
- Oversees manufacturing Quality Operating Systems (QOS) to resolve operational, manufacturing, and facility problems within the operations to ensure minimum costs and prevent operational delays and to meet future growth
- Manages with staff processing schedules and production orders to make decisions concerning inventory requirements, staffing requirements, work procedures, duty assignments, considering budgetary limitations and time constraints
- To oversee the hiring, training, and evaluation of staff within their area of responsibility
- Validating that staff is giving direction and coordinating production, processing, distribution, and all other activities of industrial organization needed to operate a manufacturing operation
- Promote and facilitate Open Door Process without reprisal, effective communication and Fair Treatment
- Follow the principle of the Magna Employee Charter
- Measurement of performance to company goals and standards and establishment of targets for improvements in safety, quality, cost, delivery and employee relations
- Ensure departments successfully meet EOS objectives annually
- Ability to analyze business unit data and apply results to produce desired business objectives
- Automotive OGM customer experience
- 5- 10 years plus experience, in castings is a plus
- Proven record of supporting lean activities
- Ability to assist in the budgeting process
- 5 years plus of manufacturing experience leading departments in a supervisory role
- Skilled trade or engineering degree preferred
41
Plant Manager Resume Examples & Samples
- Lead a plant of 150-200 employees contributing over $100M of revenue annually in a configure-to-order (CTO) and engineer-to-order (ETO) environment
- Direct and coordinate all plant functions including Manufacturing, Materials, Production Control, Purchasing, Quality Assurance, Planning, Human Resources, Accounting, Mfg. Engineering and Environmental, Health & Safety to assure common direction toward plant goals
- Guide and support the plant EH&S program in improvements, investigations and corrective actions to meet and exceed Federal laws and IR standards and policies
- Guide and support the plant quality system in procedures and controls to improve overall customer satisfaction, DPPM, first pass yield and warranty results
- Be proactive and responsive to all facets of customer satisfaction including delivery, schedule changes and special instructions
- Guide and support plant maintenance, facilities and mfg eng. improvements, process improvements, facility improvements and capital expenditures
- Guide and support plant resources in meeting material and labor productivity plans
- Direct the submittal of the plant’s Annual Operating Plan and business’s financial forecasts and response plans
- Direct and guide the long term product strategy for the manufacturing business
- Maintain a positive rapport with all levels of the organization in order to foster and promote a diverse and inclusive work environment, high levels of morale, and high employee engagement
- Collaborate with all levels of the organization to insure alignment of goals and progress towards them along with short term and long term needs and plans
- Lead and support the development of plant employees and plant succession planning activities
- Experience with implementing Lean culture in a manufacturing environment is required
- 7-10 years progressive Operations/Supply Chain experience; 5 years of Management experience
- Leads and Drives the OPEX (Operational Excellence) culture in the plant
- Proficiency in developing and implementing strategic plans
- Proficiency in Supply Chain Management
- Strong technical problem solving skills
- Advanced management skills
42
Plant Manager Resume Examples & Samples
- Sets overall plant policies and procedures to ensure effective operations consistent with the Eaton Business System, Values and Philosophy
- Fosters an environment which promotes Eaton’s goals, encourages continuous improvement, and builds customer relationships
- Accountable for the day-to-day decisions that directly impact the quality, efficiency, and profitability of the Hutchinson Plant
- Assesses performance indicators, and takes appropriate actions, to ensure schedule, cost, and quality goals are met
- Provides leadership and commitment in support of continuing improvements in quality, productivity and delivery performance
- Supports product design organization through new product introduction phase to ensure customer product development and manufacturing delivery times are met
- Assures that Environmental, Health, and Safety issues are addressed considering local regulations, Eaton policy, and good corporate citizenship
- Evaluates operational performance of the group in order to facilitate performance management, merit promotions, job transfers, dismissals, commendations, etc
- Develop, recommend, and implement approved capital programs to support the profit and strategic plans with a minimum of capital
- Maintain direct communication style based on the plant with all employees with the overall objective of maintaining good employee relations
- Bachelor’s Degree from an accredited institution
- Minimum of 5 years of experience in a manufacturing environment
- MBA from an accredited institution
- Proficient communication skills
- Experience with Six Sigma/Lean Manufacturing
- Experience in a union environment
- Knowledge of Lean Manufacturing and Process Variation Reduction (Six Sigma) concepts and tool sets as they relate to materials management Knowledge of financial concepts and techniques utilized to establish value propositions of operational changes
- Must possess good communication skills (verbal, written) to be able to represent Eaton
- Strong Team work skills and ability to lead high performance teams
- Management and leadership skills and social understanding
43
Plant Manager Resume Examples & Samples
- 35%- Risk Management - focusing on reducing and managing risks associated with employees, contractors, customers, products, and facilities. This fundamental focuses on the following
- 20%- Operational Effectiveness – taking advantage of business opportunities while making continuous improvements. We need to manage the efficiencies of our plants which will enable us to be the partner of choice for our customers. This fundamental focuses on the following: Grain Quality Management, mix and blend, plant Efficiencies, Process Improvements, Operation costs, Energy management, and Staffing
- 5%- Capital Effectiveness – using best practices for selecting, planning, developing and executing while consistently delivering successful projects. This fundamental focuses on the following: Contractor safety, Skilled and professional project management and execution, Best total cost of ownership (specification, procurement, and installation), Use the Project Delivery Process (PDP) tools (budget and schedule compliance)
44
Plant Manager Resume Examples & Samples
- Ensure collaboration with other Plant Managers, and provide input into overall Integrated Supply Chain strategy
- Review established production schedules for all manufacturing departments to insure established inventory levels are met while operating at the highest efficiency possible
- Initiate, maintain and support a superior safety and housekeeping program, including all timely communication initiatives, and ensure all members of the manufacturing team are aligned and aware of the safety culture and guidelines
- Develop, execute and maintain the budget for the manufacturing facility
- Drive investment to ensure long-term conversion and usage competitiveness of the plants
- Elaborate and/or update an annual conversion and yield roadmap for the plant organization and identify specific projects to satisfy cost reduction targets as per productivity strategies
- Execute Mondelez Category growth initiatives and new product launches
- Analyze workforce requirements, and ensure Plant operating in the most efficient and cost effective manner
- Encourage and promote operating in an Integrated Lean Six Sigma environment
- Ensure a 0 waste and 0 loss mindset throughout the facility
- Coordinate the relationship with our union workforce and support the negotiation of union contracts as needed
- Ensure that all plant functions are working under best possible practices and environment regarding all existing internal and external policies and procedures in respect of Mondelez’s role within the community (i.e., safety regulations, plant security and environmental policies)
- Bachelor’s Degree in Business or Technical Field
- At least 8 years of fundamental knowledge and experience within a supply chain environment
- Black Belt Certification Preferred
- Ability to blend people into teams; creates strong morale and spirit in his/her work; defines success in terms of the whole team
- Effective at leading and managing change
- Trust and empowers team, while holding team and others accountable
- Strong communication skills at all levels of the organization
- Ability to deliver results through being an inspirational leader
45
Plant Manager Resume Examples & Samples
- Major accountabilities
- Sets the vision for the organization by formulating and guides the implementation of long- and short-range plans, policies and programs associated with assigned business unit product offerings, within the broad framework of operating unit and corporate strategy and under the direction of senior management to achieve approved objectives
- Provide overall leadership and direction to direct reports responsible for manufacturing and all aspects of performance
- Direct preparation of operational budgets and coordinates capital plans, appropriation requests, and project follow up
- Lead by example and reinforce the Alcoa Values in every interaction
- Bachelor's Degree from an accredited institution
- Minimum 10 years of experience in plant operations
- Minimum 5 years of management experience
- Strong leadership skills that creates an engaged employee environment
- Ability to drive improvement through the implementation of the lean manufacturing principles, six sigma
- Demonstrated results in leading manufacturing excellence
- Results driven and accountable for actions
- Effective communicator in every setting
- Strong technical understanding of manufacturing processes and working knowledge in all business activities
46
Plant Manager Resume Examples & Samples
- Ensure that both the manufacturing capacity & development initiatives are tightly aligned with the current and future needs of the customer base
- Develop a strong problem-solving culture across the operations team that addresses root causes and implements effective countermeasures whenever quality and/or fulfillment issues cause negative customer experiences
- Commit to implementing continuous improvement across all functional areas, and ensure that the division's quality and process improvement initiatives achieve the optimum results and widest acceptance. Further establish the Avery Dennison Enterprise Lean Sigma culture
- Establish goals and budgets with finance team for individual operating departments
- Monitor overall performance against annual operating and profit plans
- Develop and maintain a strong, collaborative relationship with customers, peers, strategic partners, the group level management, and the divisional management
- Transfer best practice and standardization of process and equipment
- Maintain site(s) focus on safety, health, and the environment
- Develop and retain key people, optimizing their talent and guiding their careers
- Accountable for delivery and significant year-to-year improvement of business operations / supply chain results: financial, quality, service, safety, employee relations climate, inventory, organizational development
- Responsible for long term capabilities of global operations / supply chain - capacity, organization, skills, etc
- Drive effective on-going communications with plant leadership teams, shop personnel, and union/works council leadership through a combination of large-group town hall meetings, small group round table sessions, and other written/visual communication methods
- Provide quality products to customers through the implementation of Avery Dennison's Quality System and through rigorous quality operations. Ensure defects are investigated and corrective action plans implemented
- Leading an ELS based culture, and driving widespread employee engagement
- Improvements in EHS, product quality, customer deliveries, and inventory
- Execution on financial commitments, driving margin improvements
- Develop site organizational culture that fosters continuous improvement
- Develop and assure successful implementation of annual and long term financial and business plans (financial, safety, service, organization, inventory)
- Effectively incorporate improvement programs (i.e. Six Sigma, Lean, Kaizen, behavioral based safety)
- Inspire and motivate a team to consistently perform above expectations in a very competitive and low margin business environment
- Implement, control and monitor critical performance indicators
- Align the organization to meet targets - federate other functions that do not directly report to operations
- Attract, retain, and develop high potential talent
- Coach and develop the organization
47
Plant Manager Resume Examples & Samples
- Provides strategic direction for the plant and related integrated supply chain activities and assists in the development of the business strategy planning document
- Develop and execute strategies for increased customer satisfaction, safety, quality, delivery, productivity, cost, working capital management, and effectively introduce new products/processes for growth
- Ensure that financial productivity and plant/product transition projects are successfully executed
- Build consensus across functional and lines of business, working with multiple internal and external customers and stakeholders
- Drive culture change, accountability and continuous improvement mindset throughout the organization
- Operational/Financial Responsibilities
- Oversee and promote effective Health, Safety and Environmental programs and practices, ensuring that high standards of site safety are established, met, and that facilities and grounds are maintained in accordance with relevant regulations, agency standards and fiscal considerations
- Develop and execute the Annual Operating Plan. Direct responsibility for departmental spend and managing budget
- Drive site to achieve/surpass financial commitments
- Provide customer interface and support as required; using customer feedback to improve quality and delivery while driving process and yield improvement
- Establish and implement standard manufacturing and materials practices by implementing and executing the Honeywell Operating System (HOS). Required to lead organization through the HOS deployment process and maintain performance levels stated by HOS maturity scorecard; including visual management and the tiered meeting communication process
- Develop and maintain an effective site leadership team. Model the HOS leadership expectations including use of, and adherence to, leadership standardized work. This requires spending considerable time walking the factory floor and auditing aspects of the operating system
- Manage inventories to achieve working capital goals
- Integrate key elements of Supply Chain to improve cycle time
- Manage capacity/schedules to achieve On Time Delivery, growth and productivity goals
- Ensures process and yield improvement is embedded into the factory culture and actions
- Improve and develop organizational capabilities through effective performance management and planning/utilization of human and capital resources
- Champion programs to address employee satisfaction and employee training, communications, and department structures to support operational and strategic goals
- Provide leadership and positive employee relations for a salaried and hourly workforce
- Bachelor's degree in Engineering, Business, Finance, or related discipline
- Minimum of 10 years related experience, including 5-8 of progressively complex managerial experience
- Experience or knowledge of the Honeywell Operating System, similar operating system, or lean manufacturing excellence
- Good knowledge of SMT, electronic and electro-mechanical assembly
- Ability to develop, execute and achieve tactical and strategic initiatives through active leadership that positively impact business plans, operating profits, practices, policies and procedures
- Six Sigma Green Belt certification
- Previous facility or product line transition experience
- Ability to effectively select, develop, coach, delegation skills and motivate others
48
Plant Manager Resume Examples & Samples
- Plans, organizes and directs all production activities
- Creates production schedule and workflow duty assignments
- Initiates plan and process which determine, clarify and exceed production goals
- Recruits, hires, orient/trains and retains production front-line supervisors and employees
- Leads an ongoing world-class production orientation program
- Strives continually to improve manpower utilization to align with production process in order to positively impact revenue
- Supervises the receipt of incoming material shipments, verifying that appropriate receipt and quality control inspections are completed in a timely manner and appropriate transactions are made to complete the receiving process
- Ensures that materials in the warehouse are stored properly, inspected and cared for through accepted material handling and warehousing principles
- Supervises and participates in the physical inventory process
- Supervises staging of materials to support timely delivery of materials, prepare shipments of items as required and prepare materials for processing to scrap
- Develops, implements and executes production tracking and quality control systems to analyze production quality control and capacity utilization
- Ensures that collective bargaining agreement is effectively administered and that employee grievance procedures are adhered to in compliance with the current collective bargaining agreement language
- Develops and implements a world-class safety culture that strives to continually improve workplace safety awareness and achieves an injury-free work environment
- Maintains individual knowledge/skill and experience as required to ensure optimal production acumen
49
Plant Manager Resume Examples & Samples
- Drive Improvement in Cost, Quality, and Service areas while developing the direct reports as well as plant wide capabilities of the plant personnel
- Ensure a safe and highly motivated work force by serving as a role model and providing proactive leadership in safety and environmental efforts, positive employee relations, organization design and work systems development
- Continuously improve the processes and technology by staying current in new technological developments and seeking capital when necessary; and championing continuous improvement efforts in all areas of the site in order to implement and sustain manufacturing best practices, procedures, and relevant certifications/qualifications (eg ISO 14001, AlB, GMP, HACCP)
- 4 Act as liaison between plant personnel and corporate by building solid relationships and effectively communicating division and corporate goals within the site, and knowing when and how to communicate plant issues upward
- Maintain a competent site leadership team by applying high standards for selection and performance, communicating and delegating key responsibilities, and actively utilizing all performance, development and career tools to their full potential
50
Plant Manager Resume Examples & Samples
- 35% Maximize facility optimization for greatest financial return through capital planning, budgeting, operating efficiencies and asset preservation
- 25% Lead employee development, career planning, employee relations, employee engagement and location cultural development
- 25% Lead a proactive approach to EHS, food safety and product quality management. Manage incidents in these areas and ensure that corrective actions are in place to prevent recurrence
- 10% Ensure compliance with applicable governmental regulations and company policies
- 5% Perform miscellaneous duties as assigned
- Bachelor degree in a Technical Field with a minimum of 5 years of production management supervisory experience OR a minimum of 10 years of production management supervisory experience
- Demonstrated effective leadership skills (change leadership, dealing with ambiguity, accountability)
- Demonstrated strong interpersonal skills (communication, coaching, recognition, conflict resolution)
- Demonstrated sound decision-making and problem solving skills
- Team oriented: ability to work with others and lead others to work cross-functionally
- Ability to hire, train, develop and retain talent
- Ability to effectively communicate (verbal, written, presentation skills) at various levels of Cargill and customer organizations
- Working knowledge of Safety, Food Safety, OSHA and Environmental regulations
- General knowledge of other business functions (Commercial, Supply Chain, Finance, R&D, HR)
- Food processing experience
51
Plant Manager Resume Examples & Samples
- Bachelor's Degree in a technical field with a minimum of 3 years of experience in power plant management (OR a High School Diploma / GED with a minimum of 5 years of experience in power plant management)
- Minimum of 5 years of experience working in a power plant environment
- Demonstrated ability to lead, coach and build a team to achieve higher levels of performance
- Highly organized, adaptable to change and the ability to work in a fast paced environment
- Leadership experience in a large combined cycle plant
- Extensive knowledge of NERC and environmental, health, and safety regulations
52
Plant Manager Resume Examples & Samples
- 10+ years of related managerial experience in a manufacturing environment
- 5+ years leading a manufacturing site operation with demonstrated performance improvements (P&L experience preferred)
- Serial assembly production experience (required) weld, paint, tube fabrication (preferred)
- Successful material sourcing (low cost/high quality) and logistics strategy experience preferred
- Strong leader that can motivate and empower the team with an affinity towards continuous improvement
- Proficient in practical lean manufacturing and problem solving techniques (Six Sigma, Toyota Production Systems or similar)
- Results driven with the ability to work under pressure and meet deadlines in a high performance manufacturing environment with an unwavering ethical commitment and behavior
- Ability to manage multiple, complex tasks with excellent attention to detail
- Strong verbal/written communication and presentation skills, with the ability to communicate effectively with multiple levels of the company. Ability to successfully interface with end-user customers
- Excellent analytical, planning, administrative and follow-up/follow through skills
- Strong strategic thinking skills with a proven ability to apply business principles and practices effectively driving metric and business performance improvements
53
Plant Manager Resume Examples & Samples
- Create, plan and implement programs to achieve strategic and profit plans that meet divisional and corporate objectives
- Sets overall plant policies and procedures to ensure effective operations consistent with the Eaton Business System, Values and Philosophy and Ethical Standards
- Coordinates and directs through managers, all functions of facility operations, including but not limited to Manufacturing, Engineering, Quality, SCM, OpEx, HR and Finance
- Accountable for the day-to-day decisions that directly impact safety, quality, delivery and cost for the overall plant
- Attracts, selects, develops, trains, coaches, appraises and motivates managers and other personnel for key staff positions and the facility
- Interact with customers to ensure understanding of their expectations and achievement of their satisfaction of plant products and services
- Develop and implement local policies and procedures to meet operational requirements, through clear communication and actions, with all levels of the organization, establish managerial leadership, credibility and trust
- Manage operating capital assets to achieve financial integrity and fiduciary responsibility
- Delegate and monitor plant operations for compliance with local, state, and federal regulatory agencies relative to affirmative action, safety, environmental and similar requirements
- Assists in maintaining an atmosphere of continuous improvement and team efforts for accomplishing department and plant goals
- Builds organizational capabilities to support a high performance culture through mentoring and developing of new talent
- Bachelor’s degree from an accredited institute
- Minimum of 7 years of progressive manufacturing experience
- Demonstrated knowledge of current manufacturing, materials/purchasing and quality assurance methods and practices
- Thorough understanding of financial practices and financial statement s, including capital equipment analysis, cost accounting, budgeting, project cost analysis, maintenance analysis and organizational techniques
- Ability to drive change and successfully lead and implement these change initiatives
- Demonstrated ability to manage direct reports and build organizational capability
- Strong communication skills and comfort with facilitating teams/groups and working with all levels in the organization
- Master’s degree (MBA)
54
Plant Manager Resume Examples & Samples
- Set the goals and objectives for the Parlin Plant Management Team in such a way as to maintain the capability to manufacture products for the existing business and product lines as well as embrace the development of new product lines to a point of full commercialization
- Ensure compliance with applicable regulations relating to OSHA/PSM, EPA, cGMP and other Federal, State and local regulatory agencies
- Set the administrative and operational goals and objectives for subordinate managers for broad compliance and allow the managers to set specific compliance objectives and action plans for their departments
- Monitor Plant operations and interact with department managers and plant personnel to maintain and improve plant performance
- Communicate with and keep Senior Management informed of Plant operations as appropriate
- Interact on a daily basis with department managers and regularly the entire plant workforce to sustain open communications and information flow
- Make operational decisions based on the information presented to insure the successful implementation of the Industrial Chemicals Business Plan and Strategy
- Develop, implement and monitor Operational expenses (GPS) and Capital budgets for the plant that includes long range planning and plant expansion
- Work with department managers to develop and monitor each individual department’s operating and capital budget
- Frequently interact with Financial team to evaluate the status of the business based on the budget and make adjustments to administrative and operational issues to insure the success of the business
- Chemical Process Expertise - Possess strong chemical process (technical) knowledge and skills focused on production operations at a plant
- Manufacturing Process Knowledge - Able to analyze manufacturing and business processes toward optimization using continuous process improvement tools (ie., Six Sigma and Lean Manufacturing Practices)
- Financial and Statistical Knowledge and Aptitude - Ability to interpret and analyze statistical data, information and financial reports. Understand financial statements, costing methodologies and various methods of cost/benefit analysis
- Employee and Labor Relations – Skilled in working within a unionized environment is a plus. Knowledgeable of collective bargaining agreements and informal and formal grievance procedures, mediation and arbitration is preferred
- Business Knowledge and Acumen - Understand the drivers that impact performance and growth of a business
- Regulatory Compliance Knowledge – Understand and able to work within various local and regional regulatory safety, environmental, quality and financial regulations, standards and laws as required for specific location, region or country
- Computer Skills - Working knowledge of current software systems, i.e. SAP, e-mail, Microsoft Office (Word, Excel, PowerPoint)
- This position is located in Parlin, NJ
- B.S. degree in Chemical Engineering or a related discipline
- 10+ years of experience in a manufacturing environment in roles of increasing responsibility and across several disciplines (ie. production, safety, engineering, etc.) in a chemical processing facility
- 8+ years of direct supervisory experience leading, influencing, building and developing diverse and cross-functional teams across various levels and skill sets including hourly, salaried non-exempt and professional exempt level staff
- Experience in effectively developing and managing Production and Financial/Budget plans and developing and implementing cost reductions and production efficiency improvements
- Experience in working within and complying to local, regional and governmental safety, environmental, quality and financial standards and laws regulations as required for specific area, country or region
- Continuous Improvement (six sigma, lean manufacturing, etc.) process and good manufacturing practices (cGMP) experience
- Project & capital management and SAP experience
- Regulated cGMP experience preferred as the site does produce some Cosmetic grade products
55
Plant Manager Resume Examples & Samples
- Bachelor’s degree in Mechanical, Chemical, or Industrial Engineering or Science
- Minimum of 15 years of experience in a manufacturing environment showing progressive increase in responsibilities over a broad array of manufacturing disciplines
- 10+ years of experience in a leadership role
- Knowledge and proven successful implementation of 5S, Lean Manufacturing, Kepner Tregoe and/or Six Sigma required
- Experience with primary oversight of all manufacturing, supply chain, engineering, and quality management, budget management, and knowledge of manufacturing financial metrics
- Excellent communication skills—both verbal and written required
- Statistical Process Control and OEE expertise required
- Knowledge of ISO 9000 standards and cGMP’s
- Excellent math skills. Ability to analyze data to assure schedules can be obtained
- Strong understanding of lean conversion tools and techniques is mandatory along with a track record of demonstrated results
- Proficient computer skills in handling spreadsheets, presentations, and new systems
- MBA Degree is preferred
- Six-Sigma Black Belt certification preferred
- Experience utilizing Enterprise resource planning ERP software – SAP preferred
- Product knowledge in thin film manufacturing, roll goods manufacturing, web handling experience, batch manufacturing and porous membrane measurement expertise
- Applicable safety training such as: RCRA, DOT, etc
56
Plant Manager Resume Examples & Samples
- Bachelor’s Degree from an accredited university or college
- Minimum of 8 years of work experience with proven leadership in manufacturing or supply chain role
- Bachelor’s Degree in Engineering from an accredited university or college
- Knowledge of the disciplines of building a manufacturing plant preferably a chemical plant
- Demonstrated capability in employee relations
- Proven mentoring and coaching abilities, demonstrated ability to motivate & inspire others
- Ability to successfully motivate and maintain high morale, employee involvement, safety and teamwork in non-union environment
- Proven ability to prioritize, plan and execute important business and supply chain initiatives
- Proven leadership skills (experience successfully managing people / projects / issues)
- Demonstrated ability able to influence and communicate well with all levels of the organization, including senior leadership
- Change agent with energy, passion & enthusiasm to drive change
- Master’s Degree in Manufacturing / Business / Engineering from an accredited university or college
- Six sigma certification or equivalent quality certification
57
Plant Manager Resume Examples & Samples
- Coordinates and directs through managers, all functions of facility operations, including but not limited to Manufacturing, Engineering, Quality, Supply Chain, Operational Excellence, Human Resources and Finance
- Aligns operational objectives with the overall business objectives to ensure a strategy-focused workforce
- Manages operating performance through the effective use of the Quality Operating System (QOS) process and structured problem solving
- Directs and mentors Beltsville leadership team in the performance of their respective roles and consistent with the Eaton Leadership model
- Drives the compliance to the ethics policy and holds others accountable for ethical conduct
- Develops, controls, and critically reviews results of operation in reference to planned objectives
- Accountable for the day-to-day decisions that directly impact the quality, efficiency, and profitability of the overall plant
- Maintains a workforce of highly motivated employees with a morale that is conducive to remaining non-union with performance being measured at or above minimum acceptable levels
- Represents the company in the local community to enhance its image and reputation
- Graduate degree (MBA)
- Previous plant manager experience preferred
- Thorough understanding of financial practices and financial statements including: capital equipment analysis; cost accounting; budgeting; project cost analysis; maintenance analysis and organizational techniques
- Bachelor’s degree from an accredited institution
- Minimum 10 years of progressive operations experience or experience in a manufacturing environment
- Minimum 5 years of management/supervisory experience
- This position requires use of information or access to hardware which is subject to the International Traffic in Arms Regulations (ITAR). All applicants must be U.S. persons within the meaning of ITAR. ITAR defines a U.S. person as a U.S. citizen, U.S. Permanent Resident (i.e. Green Card Holder'), Political Asylee, or Refugee
- Must be able to work in the United States on a permanent and ongoing basis without requiring corporate sponsorship
- Limited travel up to 25% of the time may be required
58
Plant Manager Resume Examples & Samples
- Must hold at least a Degree in Chemistry/Chemical Engineering
- Minimum of 5 years' experience in Pharma/API industry in a similar role
- Pharma processes, equipment, systems etc
- Project Management experience, ideally certified PM
- New Product/Process Introduction (NPI) experience
- Operational Excellence experience, ideally 6 sigma Black-Belt
- People Management experience ideally in a unionised environment
- Knowledge of Pharma industry
- Knowledge of regulatory and legislative and compliance requirements (Safety, Quality, Environmental)
- Technical knowledge of API production processes and operations
- Coaching
- Interpersonal
- Financial
- Decision making
- Performance Management (operational and people)
59
Plant Manager Resume Examples & Samples
- Responsible to motivate, train and develop team members to achieve maximum productivity levels and maintain a clean safe work environment
- Responsible to apply strategic thinking to meet customer product demands
- Responsible for the overall management, direction and coordination of Manufacturing Department. Communicates and executes Company production objectives, both functional and financial
- Responsible for hiring, firing, and disciplinary action of employees reporting to this position. Includes employee performance evaluations, training, and problem resolution. Promotes employee development to supervisory and/or leadership positions when available
- Determine plant policies consistent with Company policies and directs and supervises the application of such policies to the plant’s manufacturing operations
- Oversees the execution of the production schedule by the AMM’s to ensure Service Level excellence. Facilitates cross-functional problem solving regarding the schedule execution as needed
- Assures a safe and orderly work environment. Establishes and implements housekeeping policies and procedures
- Evaluates, initiates, recommends and implements process improvements in order to increase production efficiencies and reduce variable costs
- Develops short and long term capital needs and/or opportunities based on capacity, policy or cost savings
- Review processing schedules or production orders to make decisions concerning inventory requirements, staffing requirements, work procedures, or duty assignments, considering budgetary limitations and time constraints
- Develop or implement production tracking or quality control systems, analyzing production, quality control, maintenance, or other operational reports, to detect production problems
- Review operations and confer with technical or administrative staff to resolve production or processing problems
- Develop budgets or approve expenditures for supplies, materials, or human resources, ensuring that materials, labor, or equipment are used efficiently to meet production targets
- Oversee inventory cycle count program to evaluate facility yields
- Coordinate or recommend procedures for facility or equipment maintenance or modification, including the replacement of machines
60
Plant Manager Resume Examples & Samples
- Operate facility with a particular focus on safety—provide for employee awareness and participation, operating procedures and guidelines, training, substance abuse prevention, and fulfillment of OSHA and company compliance requirements
- Ensure optimum and efficient utilization of people, equipment, and resources through project management, supply negotiations, etc
- Utilize feedback/assessment processes to make employees aware of goals and achievements
- Meet facility permits/standards by operating within all applicable legal/environmental guidelines
- Lead, develop and implement policies and procedures to execute annual and long-range plans
- Identify, lead and develop talent
61
Plant Manager Resume Examples & Samples
- Drives overall operational excellence through the application of best in class lean practices and processes
- Builds capabilities, tools and processes to reduce total cost of ownership (TCO)
- Addresses key business performance challenges. Identifies and prioritizes these challenges based on root cause identification in operational key result areas
- Identify and address manufacturing issues and drive excellence in: SQDCC
- Participate with the Business Platform Leader on growth/acquisition strategies
- Drive Lean strategy leading to the Plant transformation
- Focus on talent and organizational development, an effective succession planning system, and a culture focused on continuous improvement
- Institute a culture of accountability and teamwork
- Drives processes to support lean (e.g. – SIOP, E&O, Inventory Management process)
- Builds a strong operations talent base. Partners with human resources to develop talent management strategies
- Leads daily operations ensuring customer expectations are consistently satisfied, products and services always meet the quality specifications and all resources are fully utilized to provide a cost-effective product and service
- Establishes performance goals and objectives for factory operations. Provides feedback and corrective action to maintain progress toward achievement of goals and objectives
- Champions change and drives out waste throughout manufacturing operations by deploying Lean methodology
- Manage labor utilization and manage operations within budget
- Prepare technical and progress reports and manage capital budget for site
- Develop, interpret, apply, and enforce company safety regulations and operating policies and procedures
- Provides leadership for problem resolution to facilitate faster improvements and improved working relationships throughout the manufacturing floor
- Builds, develops and manages manufacturing leadership team capable of carrying out needed operations strategies and improving employee relations. Develops training and education requirements and plans for all manufacturing management
- Support and maintain nondiscriminatory practices in accordance with the Division Affirmative Action Program
- Promote good public relations for the Company within the community
- Special projects and other duties as assigned
- BS or BA degree plus 10+ years’ experience in manufacturing
- MBA Desirable but not mandatory
- Previous experience in demonstrating positive leadership in areas such as finance, manufacturing and materials
- Must have demonstrated experience working effectively across a site to develop and strengthen key business relationships
- Previous experience in a union environment
- Excellent analytical and communication skills. Experience with change management and driving continuous improvement activities
- Demonstrates clear understanding of all tasks and processes within manufacturing
- Has a high level of technical competence in employee management, assembly operations, continuous improvement techniques, quality systems, replenishment systems, Lean Manufacturing strategies, and manufacturing technologies
- Strong written and verbal communication skills and computer literacy (MS Office Suite)
62
Plant Manager Resume Examples & Samples
- Manages and supervises activities of hourly and salaried production and maintenance employees
- Approves the selection, hiring, training, change of status and separation of employees
- Plans and schedules production requirements (people & equipment) to support daily, weekly and monthly sales forecast to meet customer’s needs
- Provides coaching and disciplinary counseling to employees under his or her area of responsibility (includes employee relations and administration of collective bargaining agreements region specific)
- Identifies, assesses, prioritizes, and resolves production and employee related problems
- Administers and enforces Company and Region policies and procedures
- Ensures that the plant meets all SHE policies and practices at the site location and works with SHE Regional employees and Company officials to promote a safe work environment that meets all State and Federal rules and regulations
- Insures that employees receive proper training and instructions to perform assigned job duties
- Works closely with sales staff and customers to ensure that products meet customer needs and expectations
- Participates in developing an annual operating budget which includes production volume and capital improvements
- Manages plant production operation to ensure cost efficiency and optimal utilization of plant and equipment
- Responsible for ensuring that the site meets or exceeds operating budget
- Works with sales on identification and elimination of customer issues and concerns to improve customer satisfaction and relations
- Works on the implementation of cost saving programs and/or continuous improvement activities to reduce costs and improve operating efficiency
- Participates in Operation’s short and long range business planning
- Manages daily production meetings on the daily running and operations of the plant
- Initiates action for environmental permits and prepares reports for various public agencies and coordinates with Legal Department or outside legal counsel or regulating agencies on compliance issues
- Utilizes appropriate resources and recommendations in community relations and legislative efforts and actively participates in the area’s community outreach and educational programs
- Other duties may be assigned as required
- Minimum of 5 years prior work experience in supervising production employees preferably at either an aggregate, sand/gravel or asphalt plant. Construction materials industry experience preferred
- Experience in the management of union employees (region specific)
- Thorough working knowledge of plant operation (aggregate, asphalt, ready mix) and its associated products, processes and related equipment
- Knowledge of safety and environmental rules and regulations (MSHA and OSHA)
- Knowledge and understanding of business planning and financial forecasting requirements
- Excellent leadership, communication, organization, conflict and problem resolution skills
- Ability to plan and manage effectively using motivation and team building skills
- Good organization skills; excellent problem solving skills and practices
- Flexible to work long hours and travel when needed
- Must represent Vulcan in a professional manner to all customers, vendors, and internal employees
63
Plant Manager Resume Examples & Samples
- The position requires an individual with demonstrated leadership skills, broad based technical abilities and a basic financial background
- Strong organizational, planning, interpersonal, and communication skills are essential to the position
- Credibility and respect across the organization is important
- A minimum of 12+ years in maintenance, engineering and/or operations management roles are desired
- A BS engineering degree is preferred
64
Plant Manager Resume Examples & Samples
- Drive overall operational excellence through the application of best-in-class lean practices and processes. Champion implementation of the Pentair Integrated Management System (PIMS) Lean Enterprise principles and processes
- Address key business performance challenges through structured problem solving based on root cause identification and corrective action
- Identify and address manufacturing issues and drive excellence in: SQDCC (Safety, Quality, Delivery, Cost, and Cash). Lead daily operations. Drive processes to support lean (e.g. – SIOP, E&O, Inventory Management process)
- Establish and achieve performance goals and objectives for factory operations. Provide feedback and corrective action to achieve goals and objectives
- Build capabilities, tools and processes to reduce total cost of ownership (TCO)
- Focus on talent and organizational development, develop an effective succession planning process, and creates a culture focused on continuous improvement
- Build a strong operations talent base. Partner with human resources to develop talent management strategies
- Institute and exemplify a culture of accountability, positive energy and teamwork
- Lead daily operations ensuring customer expectations are consistently satisfied, products and services always meet the quality specifications and all resources are fully utilized to provide a cost-effective product and service
- Manage labor utilization and variable costs (supplies, energy, tooling, maintenance, etc) to budgeted targets and volume
- Develop and manage to the approved capital expenditure plan
- Enforce company safety regulations and improve safety culture and procedures
- Support and maintain nondiscriminatory practices in accordance with Affirmative Action Program
- Promote good public relations in the local community
- Support and execute special projects and tasks as assigned
- Support and partner with the Strategic Business Unit Leader on growth and operations strategies
- Plant operations, lean and materials experience. Quality and manufacturing engineering are a plus
- Previous experience/ strong understanding of budgeting/ expense management with a moderate understanding of financial accounting principles
- Develops and coaches talent
- Engages, inspires, and motivates
- Inspires trust and fosters open communication
- Quickly and effectively resolves conflict
- Effectively negotiates when necessary
- Builds and sustains relationships
- Actively listens to others
- Drives for results
- Analyzes situations and problems
- Acts with integrity
65
Plant Manager Resume Examples & Samples
- 25% - Leadership: coaching, performance management, engagement. Continue efforts to build high performing team; engage all employees; implementation of BU strategy; people development, champion recognition; collaborate effectively with experience teams and disciplines. Role Model and ensure compliance to laws, regulations and company policies
- 25% - Operational Excellence: operations management including product quality; maintenance reliability & energy management; innovation, efficiencies & best practices
- 15% - EHS Leadership: ensure compliance and commitment to policies, procedures, and regulations. Provide direction, coaching
- 20% - Customer Solutions & Innovation: focus on continuous improvement and process management and cost efficiencies to support positive customer experiences
- 15% - Project management, capital planning, P & L: business compliance; develop & meet budgets, develop capital spending requests & project management; aggressively & proactively manage operating expenses
- 3+ years supervisory experience in a feed mill or similar industry OR 5+ years supervisory experience in a manufacturing environment OR enrolled in the Associate Plant Manager Program
66
Plant Manager Resume Examples & Samples
- Manage the operation in support of plant objectives including safety, quality, on-time delivery and profit for all areas and product lines
- Develop and oversee best-in-class employee safety programs
- Oversee the daily activities of the plant management team (production, quality, HR, and engineering)
- In conjunction with Human Resources, ensure appropriate hiring, orientation, training and performance management
- Coordinate and direct major plant projects using Six Sigma and the PACCAR Production System in support of cost reduction and new product manufacturing setup and implementation
- Maintain quality and environmental standards per ISO and QS requirements as well as local quality and environmental programs
- Manage equipment maintenance and calibration programs including negotiations with equipment vendors for preventative maintenance programs
- Manage logistics/returnable container deployment and administration
- Prepare, plan and implement the annual operating and capital budgets as well as control of monthly operating expenses
- Partner as needed with the Louisville and Texas Plant manager and, as needed, act as a liaison between departments to ensure maximum cost-savings and efficient manufacturing and distribution operations
- Ensure compliance with division/corporate policies and procedures
- Bachelor’s degree in business administration, management, engineering or other appropriate field required
- Five or more years of supervisory experience required
- Thorough understanding of production facilities, assembly and distribution operations and heavy duty truck knowledge
- Experience in a non-union facility preferred
- Master’s degree strongly desired
67
Plant Manager Resume Examples & Samples
- Partner with business leadership team to develop strategy, annual operating, and business plans
- Drive the annual operating plan/budgets and continuously reviews the plan adjusting accordingly to ensure production, yields and other KPI’s are being met
- Responsible for driving change by championing and utilizing Lean Six Sigma tools
- Provide an environment which fosters the development of our people and defines accountability at all levels of the organization
- Assure regulatory compliance to National Aerospace Standards
- Implement necessary plant improvements
- Establish strong working relationship with sales, and R&T teams
- Identify opportunities to grow, develop and build organizational talent who deliver results
- At least five (5) years of plant management experience in a discreet manufacturing environment leading all operational functions
- Lean and Six Sigma experience
- Bachelor’s Degree in Mechanical or Materials Science Engineering
- Advanced Degree (Engineering or MBA)
- Effective oral and written communication skills with strong interpersonal skills to influence and drive positive change across all levels of an organization
- Excellent leadership, business, financial and administrative ability
- Strong technical background in manufacturing operations
- Proven innovative talent with a strong understanding and utilization of lean manufacturing and Six Sigma methodologies
68
Plant Manager Resume Examples & Samples
- Has primary responsibility regarding all the final results of the departments that comprise the plant
- Elaborates, negotiates and manages the objectives and company’s Budget, as well as the strategies and action plans to comply the objectives
- Is responsible for validating and authorizing the standard operating procedures of the company
- Determines the implementation of the organization’s administrative policies, through subordinate managers
- Assures optimum operation of the functional areas of the company such as: Production, Materials, Engineering in dotted line is responsible for the areas of Quality, Finance and Human Resources
- Represents the company before private, official and educative organisms in order to promote its interests; establish links and obtain updated and environment relevant information
- Has legal power of organization (POA)
- Participate in coordination with HR department in salary survey and causes and gathers information, regarding the cost of life in the locality in order to substantiate compensation policy for the organization
- Plant Manager is in charge to develop the managers in order to assure that the objectives are aligned and compliance
- Approve and review procedures to assure better manufacturing process, standards, equipment, quality and all general areas
- Participated in coordination with the staff in budget process for the organization for optimal resource management
69
Plant Manager Resume Examples & Samples
- 35% - Risk Management - focusing on reducing and managing risks associated with employees, contractors, customers, products, and facilities. This focuses on the following: Environmental, Health and Safety (EHS), Zero execution incidents, food and feed safety, process safety, and facility security
- 35% - Talent Management - having a talent pipeline with effective, diverse leaders who are well trained, engaged, and focused on operational excellence for today and for the future. This focuses on the following: training and development, engagement, hiring and retaining diverse talent, balance between leadership and technical expertise, and a culture focused on operational excellence
- 20% - Operational Effectiveness - taking advantage of business opportunities while making continuous improvements. Manage the efficiencies of our plants which will enable us to be the partner of choice for our customers. This focuses on the following: grain quality management, mix and blend, plant efficiencies, process improvements, operation costs, energy management, and staffing,
- 5% - Reliability Excellence - having a strategic approach in which systems, structure, processes, and procedures are in place to create reliable, safe and sustainable plants at the best total cost of ownership. This focuses on the following: best total cost of ownership (operation and maintenance), on-time deliveries, higher plant availability, proactive approach to reliability excellence, and asset health management
- 5% - Capital Effectiveness - using best practices for selecting, planning, developing and executing while consistently delivering successful projects. This focuses on the following: contractor safety, skilled and professional project management and execution, best total cost of ownership (specification, procurement, and installation), using the Project Delivery Process (PDP) tools (budget and schedule compliance)
- Ability to administer and manage an effective and proactive EHS program
- Knowledge of government regulations
- Inventory management skills
- Experience with electrical and programmable controllers
- Mechanical ability and maintenance experience
- General marketing or merchandising knowledge
- Operating efficiency and expense management skills
- 2 or more years of experience as a Leader and/or Manager in a business or agricultural related field
- Experience in administering and/or managing an effective and proactive Safety program
- 4 year post-secondary education
70
Plant Manager Resume Examples & Samples
- Assume the management of the Autonomous Production Unit Managers and of the support function managers (HR, Quality, Finance, Logistics, Purchasing,…)
- Ensure smooth inbound and outbound information flows
- Drive plant Quality, Cost, Delivery and People (QCDP) performance and build and meet the plant budget
- Drive product/process QCD improvement; optimise plant lay-out and equipment usage
- Ensure manufacturing readiness and launches at plant level
- Drive supplier performance improvement
- Define a deployment plan for the Faurecia Excellence System and implement it
- Drive plant improvement networks and involve everyone in continuous improvement processes
- Ensure employees safety, respect for the environment and security of the plant
- Fulfill legal responsibilities and interface with local authorities
- Ensure staffing, induction, training and development of plant employees
- Manage social climate and labour relations
- Develop future Faurecia experts and managers
- Proven experience in production management
- Proven experience in team management
- Ability to build and manage a budget
- Results oriention
- Minimum bi-lingual (English required)
71
Plant Manager Resume Examples & Samples
- Manufacturing Responsibilities: Manage all manufacturing operations at Golf Pride site located in Korat, Thailand plant. Manages a solid-line direct report team that includes production, materials, manufacturing engineering, quality, accounting, and human resources. Also provides dotted line leadership on site to customer service and program management and R&D. Participates actively in the SIOP process to set production plans for the plants and manages the entire manufacturing process from end to end with a focus on safety, quality, service, and cost. Responsible with the senior site team for delivering Profit Plan and High 5 Operational Goals for the plant site. Also fully deployment of the EBS at site
- Senior Site Leader Responsibilities: As a member of the Global Golf Pride SLT, encourage effective cross functional interaction amongst all GGD resources at the site, that (a) support Golf Prides front end growth objectives, and also support (b) plant specific manufacturing objectives. Actively cultivate a strong sense of teamwork across department and functions at the site and facilitate effective engagement with other sites include (a) sister plant and (b) head office in the NA. Lead by example, role model effective collaboration between manufacturing and R&D and between manufacturing and sales
- 8 years’ experience of increasing responsibility directly managing operations or manufacturing facilities
- 4 years’ experience working in a multi-national company with international reporting lines
- Demonstrated written and verbal fluency in English
- MBA or Masters in Engineering from an accredited institution
- 10 years’ experience directly managing operations or manufacturing facilities
- 6 years’ experience working in a multi-national company with international reporting relationships
- 3 years of experience managing employees across multiple functions such as SCM, Finance, HR, EHS or OpEx
- 3 years’ experience with planning and managing budgets
72
Plant Manager Resume Examples & Samples
- Developing a safety culture, zero accidents
- Managing two Operational Business Units on the Pamplona site
- Achieve Operating Plans financial targets
- Successful introduction of new programs
- Driving OEE improvements through lean initiatives and team working
- Managing a diverse multi union environment
73
Plant Manager Resume Examples & Samples
- Safety (with strong focus on behavioral based safety programs, assuring compliance with polish regulations and Mondelez standards, ensuring effective prevention from occupational diseases),
- Quality (ensuring compliance with ISO 9001/14001/22000 and OHSAS 18001 with strong focus on Consumer Inspired Quality and Food Defense),
- Delivery (delivering best in class conformance to production schedule and customer service level, ensuring production line flexibilities to meet orders complexity),
- Cost (ensuring all expenditures within budget, ownership of conversion cost optimization processes including investments projects),
- Sustainability (controlling and mitigating impact on environment),
- Morale (building Safety and CI oriented culture, setting factory vision, absenteeism reduction program governance, moderating quarterly town halls with all employees, assuring proper communication on all organizational levels in factory)
- Master’s degree
- Extensive knowledge of sales and financial key performance indicators
- Data-driven and result-oriented
- Strong communication skills with good interpersonal skills
- Ability to handle fast paced changing environment and ambiguity
- Well organized with good analytical, reporting and presentation skills
- Proven team management results
- Proven organizational agility
- Negotiations skills
- Fluent Polish preferred
- Ambitious approach and focus on achieving objectives
- Willingness to travel up to 10% of time
- Min. 2 years of experience in plant management or production area management
74
Plant Manager Resume Examples & Samples
- Drive the OpEx transformation and sustainment continuous improvement journey
- Guide and support plant maintenance, facilities and manufacturing engineering, improvements, process improvements, facility improvements and capital expenditures
- Lead and support the development of plant employees and plant succession planning activities, as well as the improvement of employee engagement
- Bachelor’s degree in engineering or equivalent technical discipline is required; MBA preferred
- Minimum of 10 to 15 years’ experience in manufacturing operations required and a minimum of 5 years in a manufacturing/plant operations leadership role, as Plant Manager of a medium to small sized manufacturing plant
- Keen sense and ability to perpetuate and sustain a Customer 1st/Performance environment down to the lowest levels in the organization. Embeds these attributes as part of the culture and as “a way of doing business”
- Blends manufacturing strategic vision with tactical execution across the organization. Successfully manages talent across the organization using key metrics, formal assessments and integrated calibrations to develop and execute a talent strategy
- Change leader – recognizes when and where change is needed and has the ability to be successful in selecting the right changes at the right time for the organizational culture to accept and embrace
- Brings thought leadership to a broad range and topics and has the ability to go deep on the majority of those topics
- Rich and deep experiences in developing relations with key stakeholders to optimize financials, productivity, and quality. Understands the key business drivers of our business and customers and builds trust and credibility from within the organization to deliver through consistently exceeding our metrics
- Deep experience with implementing Lean culture in a manufacturing environment is required
75
Plant Manager Resume Examples & Samples
- Responsible for Safety, Quality, Delivery, Cost, and Cash (SQDCC)
- Ensure that the site actively promotes and drives to this discipline
- Drive and participate in daily Managing Daily Improvement (MDI) process
- Act as a change agent and drive waste out of the manufacturing operation through the deployment of the Lean methodology
- Provide strategy and direction to Leads to meet manufacturing schedules and production plans
- Partner with Central Planning for ISOP activities
- Ensure that the Transformation Plan is established, executed and linked to strategy deployment for each Value Stream
- Create an environment of continuous improvement, putting in place cost-effective procedures, systems, tooling, equipment, etc., to continually improve manufacturing productivity
- Plan and schedule the work of the organization to make effective utilization of employees, equipment and material within budgetary requirements, and cost and quality standards to meet our customer’s expectations for quality and delivery
- Responsible for assuring strategic plans are in place for talent acquisition, employee development and performance management are in place
- Develop open lines of communication to continually monitor employee attitudes and concerns, and implement appropriate actions with input from Human Resources
- Coordinate and direct activities that respond to customer and market needs through contact with marketing and sales departments and district sales offices. Develop and maintain relationships with supply management and Engineering/Product Development
- Develop annual plan for our Richmond Plant focusing on the Value Stream
- Bachelor's degree in business, engineering or related field required
- Ideally 3-5 years in a manufacturing operations leadership role or equivalent
- Demonstrated understanding of Lean Manufacturing concepts an asset
- Knowledge of process improvement concepts and methods along with the flexibility and adaptability to accept, support, and deploy new processes in a changing business environment
- Skill to create and implement plans aligned with the division’s strategic vision
- Skilled at effective communications at both technical and leadership levels. Skills must include good interpersonal skills, as well as written and verbal communication skills, and ability to understand information and ideas as presented
- Skill in developing and delivering effective presentations
- Skill in conflict resolution including the ability to address difference of opinions or facts and use the most appropriate method to reach an effective solution
- Ability to build and maintain effective work relationships, both internal and external, and establish credibility with business partners
- Ability to plan, organize, and prioritize time/workload and delegate work in order to accomplish tasks and meet deadlines
- Ability to effectively coach and foster staff growth and development
- Ability to evaluate and motivate personnel
- Ability to adapt to rapidly changing business circumstances; must be able to thrive in a constantly changing business environment
- Approximately 10-15% of domestic travel with the potential for international travel is required
76
Plant Manager Resume Examples & Samples
- Act as a team champion to develop the best manufacturing, safety, maintenance and inventory management processes possible
- Encourage and empower teams to communicate openly regarding all issues and to pursue new avenues of action and improvement
- Identify, lead and develop talent in order to maximize individual, team and organizational effectiveness in meeting company goals
- Create a workplace that fosters a stellar safety work record and encourages constant improvement in our safety metrics
- Manage capacity requirements and efficiencies with an emphasis on improving both methods and quality while reducing costs
- Produce reliable, quality products to market rate of demand that best meet our customer needs
- Control inventory levels of finished and raw material goods to the optimum levels required to meet customer delivery expectations
- Manages budget, standards and measurement processes while profitably operating the plant within all applicable, legal, safety and environmental requirements
- Interface with Engineering and Supplier functions to develop a process that ensures absolute compatibility with product design and manufacturing process
77
Plant Manager Resume Examples & Samples
- Develop a work environment within manufacturing that promotes trust, teamwork quality and safety
- Ensure the adherence to policies and procedures
- Empower workforce and build a strong culture of food and personal safety, assign accountability, hire, develop, evaluate, train, coach, succession planning, and manage multiple union contract negotiations
- Accountable for delivering operational costs/goals, Plant EBITDA
- Identify and manage capital projects
- Strong partnerships with multiple departments and leaders throughout the organization. Implement efficiencies and cost cutting measures that will improve ROI
- Benchmark facility's costs and pricing to ensure competitive levels are maintained
- Utilize new technology and lean manufacturing principles and processes available to maximize efficiency
- Identify new market opportunities both internally and outside of the organization while expanding and supporting current business
- Ensure product quality standards meet Safeway, Federal and State guidelines. Ensure regulatory compliance as appropriate (BRC,OSHA, EPA, FDA, USDA, HACCP, Etc.)
- Travel – less than 15%
- B.S. or B.A. in Food Science, Business Management, Engineering, or related field
- The most appropriate level of experience is 10 years of Manufacturing, preferably in carbonated beverages
- Minimum 7 years Supervision/Management in a manufacturing environment with a minimum of three years of financial responsibility
- Knowledge of lean manufacturing principles
- Financial/budget management experience
- Capital project development, cost estimation and management skills
- Proven negotiation, management, interpersonal, coaching and team building skills
- Managing for results/ development skills
- Production engineering knowledge
- Ability to interface with regulatory agencies
- Interpersonal and team building skills
- Exceptional verbal/written communication skills
- Experience with equipment/maintenance
- Knowledge of MS applications including proficiency with Microsoft Word, Microsoft Excel, PowerPoint and ability to grasp additional business related applications
78
Plant Manager Resume Examples & Samples
- A Bachelor’s Degree or higher or equivalent work experience
- Five or more years of manufacturing experience
- Experience significantly improving Manufacturing, Safety, Maintenance, and Costs effectiveness
79
Plant Manager Resume Examples & Samples
- Responsible to manage the manufacturing engineering, logistics, SHE, quality and production operations
- Oversees the plans, designs and maintenance of the manufacturing facility
- Manages the operations of all production departments in the plant directly and/or through first-level managers and/or supervisors
- Ensures production meets the goals of product quality, cost effectiveness, safe conditions and customer satisfaction
- Bachelor’s Degree required
- Prior supervisory experience in a chemical manufacturing environment or in a related industry needed
- Bachelor’s degree in Chemical or Mechanical Engineering preferred
- Five years prior supervisory experience in a chemical manufacturing environment in a related industry
80
Plant Manager Resume Examples & Samples
- 5 years of progressive management experience (Manufacturing Leadership Experience)
- Bachelor's degree in engineering or operations management
- 3 years experience in Six Sigma and Lean Enterprise methodologies
- Previous Plant Management experience in low volume high manufacturing environment
- Broad knowledge of lean manufacturing and six sigma principles, along with sound manufacturing and operations experiences
- Advance degree
- In-depth understanding and application of Honeywell core processes - Strategic Planning (STRAP), Annual Operating Plan (AOP), and Management Resources Review (MRR)
- Ability to lead change and establish operational metrics/key indicators for process control, communication and performance improvement
- Ability to manage multiple, complex projects and changing priorities, make sound decisions and work effectively in a highly technical, team environment
- Cross-functional experience in operations and at least one other functional area
- Ability and experience working in the aerospace, medical and transportation markets
81
Plant Manager Resume Examples & Samples
- Builds high performance teams and is a strong team player
- Strong commitment to company values
- Able to manage conflict
- Demonstrated problem solving skills
- Strong organisational and planning capabilities
- Results orientated
- Proven influencing and stakeholder management skills – direct and indirect
- Ability to lead and work as a team
- High level of personal enthusiasm and self-motivation
- Inspires trust and open communication
- Influences others
82
Plant Manager Resume Examples & Samples
- Responsible for the assembly of products such as Automated Teller Machines and Spare Parts
- Responsible for a plant comprised of 150+ associates reporting directly or indirectly to the plant manager
- Exposure to various manufacturing processes - SMT, AI, PCB assembly, ICT & FCT
- Familiar with Assembly processes, sheet metal fabrication & plastic molding processes
- APQP / SPAP process familiarity
- Receiving inspection, test plan preparation, sampling standards
- Customer complaints analysis & action
- Customer focused process design approach
- Drive Quality and Productivity improvement projects including Lean and Six sigma
- Knowledge of statistical problem solving tools
- Knowledge of International standards for Product quality, safety & reliability
- Excellent communication & interpersonal skills
- Exposure to leading improvement initiatives for various processes & introducing new concepts
- Thorough knowledge of Minitab, FMEA, DOE, SPC, ISO9001/14001/18001
- Ensure adherence to Standards - ISO 9001: 2008, OHSAS 18001:2007 & EMS 14001:2004Education
- Administer all corporate policies and procedures
- Ensure quality products are produced
- Manage systems to ensure on-time product delivery
- Implement and manage preventive maintenance program
- Interact and is an active participant of a Global Operations team of Plant Managers
- Bachelor’s Degree or equivalent experience with 10 – 15 years manufacturing experience preferred. - Experience with assembly of electro/mechanical small mechanisms helpful
- Must be computer literate, possess good written and verbal communication skills and financial/budgeting knowledge
- Must be able to work in and manage in a matrix organization and team environment
83
Plant Manager Resume Examples & Samples
- Directs production Managers/Supervisors in the execution of their responsibilities to ensure meeting the plant’s objectives
- Directs the engineering and construction of all plant capital expansion and improvement programs
- Assures compliance to government laws and regulations
- Directs the maintenance of a safe and healthy working environment by eliminating hazards, training employees, and promoting safety awareness
- Directs and approves programs and plans to improve employee relations and employee productivity
- Monitors plant performance. Approves & directs the development of plans to improve output, quality and cost
- Knowledge of plant's manufacturing systems and processes
- Knowledge of budgeting, data collection and capital equipment analysis
- Computer skills: Proficiency with word-processing and spreadsheet applications required (MS Word & Excel preferred)
- Experience working with SAP
- 10 years or more of experience in a manufacturing environment to include prior manufacturing supervisory responsibility. *LI-CB1
84
Plant Manager Resume Examples & Samples
- Leads strategic and tactical operations/ quality management deliverables to ensure customer and product/ quality standards requirements are met within specifications under the suitable cost
- Collaborates/ partners with Logistics/ Procurement/ Sales/ Supply Chain professionals to ensure availability of raw materials and ability to meet customer specifications and timelines
- Ensures that customers are satisfied and that any inquiries, incidents and/ or issues are resolved in a timely manner
- Develops and oversees implementation of performance metrics for capturing, monitoring and reporting on the effectiveness of corporate quality management activities and programs at the plant level
- At least 7 years experience in Production and Plant Management with at least 3 years of Supervisory or Managerial level
- Strong leadership in People Management
- Having experience in implementing Six Sigma, LEAN, or TPM, or Continuous Improvement
- Have experience from Food manufacturing will be an advantage
- Good command of written and spoken English
- Good verbal and written communication skills and ability to communicate effectively with all levels of personnel within the organization
- Strong drive for results with practical, result, and outcome focused
- Demonstrated ability to learn and adapt
- Good computer skills including Microsoft Excel
85
Plant Manager Resume Examples & Samples
- Ensure plant world-class manufacturing activities based on EMS (Electrolux Manufacturing System)
- Continuous driving of Quality improvement
- Ensure maximization of overall productivity level and cost competitiveness
- Ensure timely and effective industrialization of new products up to a complete production ramp-up, according to the plans agreed with Product Development and Product Lines
- Cooperate with Pan European Staff (Quality, Purchasing, Industrial Engineering, HR, Controller , etc)
- Ensure appropriate logistics systems are in place in the plant and with external interfaces in order to achieve the service level requested
- Support Product Development/Product Maintenance in the continuous update and improvement of current products in terms of quality and costs
- Lead, motivate and develop people through customer focus
- University degree in Engineering or Business Administration or Supply Chain Management
- Strong Industrial background; 5+ years relevant experience in high volume serial production preferably at multinational environment
- Experience in different job areas, namely quality, manufacturing, industrial engineering or in general operational management of manufacturing units
- Entrepreneurial drive and capability to provide direction
- Process-oriented and cost-conscious mindset
- Is open-minded and demonstrates an improvement-oriented attitude
- Excellent communication skills (is able to interact both at local and at global level effectively)
- Ability to build and maintain a wide network of contacts (internationally)
- Strong leadership and ability in empowerment multidisciplinary teams
- Strong ability in defining objectives and monitoring progress
- Fluent English and Hungarian
86
Plant Manager Resume Examples & Samples
- Bachelor’s Degree in Business or Engineering from an accredited institution
- Minimum of 7 years progressive working experience in manufacturing
- Minimum of 5 years of managerial experience
87
Plant Manager Resume Examples & Samples
- Direct and manage plant operations for safety, quality, production, maintenance, facilities, human resources, and logistics
- Implement the Esterline Operating System throughout the facility – Our Values & Principles, People Philosophy, Esterline Enterprise Excellence Actively participates in the Quality Management System
- Establish and monitor overall plant performance for production and quality standards
- Create and maintain a trustful cooperation and coordination with other EAS Operational leaders (Plant and Purchasing Directors)
- Coordinate plant activities through planning with functional managers to insure the total manufacturing objectives are accomplished in a timely and cost effective manner
- Works with other departments in order to maintain high efficiency and output and reduce potential problems
- Ensure compliance of plant operations to all applicable state & federal laws
- Drive continuous improvements & standardization of best practices across the Plant to eliminate bottlenecks and improve productivity
- Implement cost effective systems of control over capital, operating expenditures, manpower, wages and salaries
- Maintain existing plant facilities and equipment; replace, or make adjustments to plant facilities and equipment when necessary
- Implement and maintain preventative maintenance programs
- Control and minimize labor overtime, premium freight and repair expenses
- Keep subordinates informed of changes in company/manufacturing procedures and ensure compliance to such
- 5 years plant/general management experience in a manufacturing environment
- Bachelor's degree in related field or 8 years of plant/ general management in a manufacturing environment
- Strong leadership skills; effective in developing a management team who will work well together for the good of the organization as a whole
- Advanced English communication skills – verbal & written
- Strong Lean Acumen – Experience driving lean transformation
- Experience in lean manufacturing management of technically complex products
- Working knowledge of budgets and financial statements
- Intermediate MS Office skills in Word, Excel, PowerPoint and Outlook
- Should be able to travel domestically and internationally with short notice on occasions up to 25% of the time
- Experience in the Aerospace, Automotive or Medical industries
- Bilingual/ Bicultural - able to read, write and speak English, Spanish
88
Plant Manager Resume Examples & Samples
- Plans and directs production activities and establishes production priorities for products in keeping with effective operations and cost factors
- Confers with management personnel to establish production and quality control standards; develop budget and cost controls and obtain data regarding types, quantities, specification, and delivery dates of products ordered
- Manages materials and controls plant spending by gauging production needs, overtime hours, bookings, scrap/waste material and utilizes lean processes to narrow and improve inefficiencies within assigned plant
- Coordinates production activities with procurement, maintenance, and quality control activities to obtain optimum production and utilization of human resources, machines, and equipment
- Reviews and analyzes production, quality control, maintenance, and operation reports to determine causes of nonconformity with product specifications and operating or production problems
- Develops and implements operating methods and procedures designed to eliminate operating problems and improve product quality
- Revises production schedules and priorities as result of equipment failure or operating problems
- Assure implementation of new systems according to company strategies (JCMS, TPM)
- Consults with engineering personnel relative to modification of machine and equipment in order to improve production and quality of products
- Conducts hearings to resolve or effect settlement of grievances and refers unresolved grievances for management union negotiations
- Complies, stores and retrieves production data
- Manage key projects as assigned
- Bachelor's Degree required. Emphasis in engineering or related discipline highly preferred
- Previous experience in the recycling industry preferred
- Previous experience in a smelting operation preferred
- 15+ years working in a manufacturing environment required
- 10+ years of experience in plant leadership required
- Demonstrated knowledge and experience required on Safety and Environmental regulations
- Experience in lean manufacturing preferred
- Experience working in a unionized environment preferred
- Experience working for a global manufacturing organization is strongly preferred
89
Plant Manager Resume Examples & Samples
- 5+ years experience in plant management in an automotive manufacturing environment
- Strong interpersonal and communication skills, including ability to work in a self-directed environment
- Extensive experience working/communicating with customers and suppliers
90
Plant Manager Resume Examples & Samples
- Bachelor’s degree business administration or similar from an accredited institution
- Minimum 7 years working experience in a manufacturing environment
- Minimum 3 years of managerial experience
- Experience with Lean Manufacturing/Six Sigma continuous improvement tools
- Demonstrated ability to motivate a team for maximum results
- Working knowledge of current manufacturing, engineering, materials/purchasing and quality assurance methods and practices
- Thorough understanding of financial practices and financial statements, including capital equipment analysis, cost accounting, budgeting, project cost analysis, maintenance analysis, and organizational techniques Demonstrated ability to drive change and successfully lead and implement change activities
- Working knowledge of information systems, human resources and driving key projects and plant initiatives
- Proficiency in business software programs (i.e. Microsoft Office)
- Demonstrated ability to build positive working relationships with all levels of employees
91
Plant Manager Resume Examples & Samples
- Bachelor’s degree in Mechanical, Chemical or Industrial Engineering or Science. MBA is desirable
- Knowledge of 5S, Lean Manufacturing, Kepner Tregoe and/or Six Sigma required. Six Sigma Black-Belt Certification preferred
- Must have proven experience with successful implementation and use of Six-Sigma and Lean Manufacturing principles and practices
- Experience with primary oversight of all manufacturing, supply chain, engineering and quality management
- Budget management. Knowledge of manufacturing financial metrics
- SPC (Statistical Process Control) expertise required
- OEE knowledge required
- A thorough understanding of the inter-relationship between manufacturing, engineering, supply chain and quality is mandatory with exposure in all of these areas
- Minimum of 15 years of experience in a manufacturing environment showing progressive increase in responsibilities over a broad array of manufacturing disciplines. Ten of the 15 years’ experience must be in a management-leadership role
92
Plant Manager Resume Examples & Samples
- Directs production and/or processing at a facility with multiple plants
- Responsible for associated facilities and live operations via oversight of those managers
- Develops plans for efficient use of materials, machines and human resources
- Monitors production costs and product quality
- Modifies production and inventory control programs to maintain and enhance profitable operations
- Prepares budget and makes recommendations to top management
- Sets production and processing goals for plants
- Typically requires 10+ years of DIRECTLY RELATED experience. DIRECTLY RELATED work experience will be accepted on a year-for-year basis in lieu of the educational requirement
- Experience in full processing
- Proven experience managing and motivating others for maximum performance
- EOE/M/F/Vet/Disabled
93
Plant Manager Resume Examples & Samples
- Directs production and ensures cost effectiveness and consistency with prescribed quality, accuracy, and performance standards
- Maintains plant property and equipment in good condition to ensure compliance with governmental regulations and to ensure effective and economical operations
- Prepares and submits operating reports to management to inform them of the current production status and to make recommendations to improve efficiency and effectiveness
- Selects, trains, develops, and motivates manufacturing staff to maintain plant operation
- Assures compliance of all plant operations with company policy and federal, state, and local regulations
- May set production and processing goals for plant
94
Plant Manager Resume Examples & Samples
- Lead and direct all production, distribution, and warehousing activities for the site
- Manage and coordinate the actions of four departments (Production, Maintenance, Quality Control, and Customer Service)
- Review and direct financials to assure that plant remains profitable
- Ensure maintenance of a safe and clean work environment for employees through direct supervision and guidance through corporate policies and standards
- Communicate with customers to assure that they are getting the best quality service that we can provide
- Research and evaluate opportunities for growth including existing business, new projects, external through acquisitions
- Develop/Establish successfully our brand on existing and targeted new territories
- Bachelor’s degree (BA) in chemical, mechanical engineering or other related field
- 2-4 years of industrial leadership experience
- Highly organized with ability to work well with customers, employees, management, and vendors
- Understanding of OSHA guidelines
- Knowledge of good business practices associated with the production of food grade products
- Proficient with system process controls
- Knowledge of pneumatic and physical conveyance of dry bulk compounds
- Knowledge of combustion systems and mineral processing techniques including milling, classifying, particle separation, and dust controls methods
- Excellent teamwork skills are required to coordinate all areas of business at the plant and corporate levels
- Ability to work with mathematical concepts such as fundamentals of geometry, and basic math skills such as percentages, fractions, and ratios
- Ability to interpret an extensive variety of technical instructions in mathematical or diagram form and deal with several abstract and concrete variables
- Ability to read, analyze, and interpret financial reports, production schedules, and legal documents
- Effectively develop budgets and forecasts
95
Plant Manager Resume Examples & Samples
- Ensure the availability of the incinerator and the whole facility within the SUEZ, Value Park and German EHS rules
- Implement optimisation and performance improvement projects
- Set up and maintain relationships with local authorities and stakeholders within the industrial area
- Build up a workforce and ensure a proper cooperation amongst all team members
- Take care of safety (OHSA) and the environmental performances
- Proper coordination with IWS sales teams and waste flow management - whether national or European
- In coordination with IWS Finance team, implement the financial processes and tools for keeping the P&L (budget, reporting, etc.)
- 10 to 15 years of experience in chemical businesses with mandatory 5 years experience in Hazardous Waste business (e.g. as plant manager, BU manager …), knowledge in hazardous waste incineration desirable
- Final degree in Industrial Chemistry (or similar education) with proved technical skills in terms of process, process safety, chemical hazards, material and corrosion, maintenance
- Experience in managing a P&L and working in a commercial environment, proven track record in customer relationship management, knowledge in contract management would be a plus
- International mindset and experience in successful dealing with different countries and cultures
- Good leadership and communication skills
- Very good knowledge of German (fluent preferable), good English
- Willingness to travel from time to time
96
Plant Manager Resume Examples & Samples
- Direct supervision of approximately 4-6 full-time employees
- Indirect supervision of 10-40 full-time employees
- Process Control Technology
97
Plant Manager Resume Examples & Samples
- Bachelor Degree preferred
- 5+ years experience in an industrial plant environment required
- 3+ years managing and developing employees required
- Maintenance experience and/or experience with electrical, hydraulic, and pneumatic systems preferred
- Previous plant and/or industrial gas experience a plus
98
Plant Manager Resume Examples & Samples
- Meeting or exceeding budget and productivity goals
- Manage and lead the production process including
- Filling cylinders, liquid containers, production scheduling, maintenance scheduling, and manpower planning to ensure the plant is operating under an effective and economical environment while meeting customer demand
- Ensure products and personnel are in compliance with the Praxair Quality Assurance Program as well as Health Canada Good Manufacturing Practices for Medical Gases
- Select, train, develop and motivate staff to maintain plant operation and build team spirit
- Ensure compliance of all plant operations with company safety policy and government regulations
- Accountable to control annual budget, assets and expense of the plant location, including distribution and production costs
- Establish and maintain a leadership role in safety. Encourage safety teamwork and an ongoing high level of safety awareness. Create an environment, which encourages Operational Discipline
- Promote a clean, safe work environment and an atmosphere of teamwork and open communication to motivate, build morale and develop a positive attitude among employees
- Provide excellent customer service by meeting or exceeding customer expectations
- Develop and maintain an open line of communication with the sales team to meet customer expectations
- Industry experience in a technical, supervisory or management role
- Experience managing or supervising employees
- Technical and financial knowledge of the business
99
Plant Manager Resume Examples & Samples
- Safety: Ensure people are working in a safe environment. Conduct daily safety walks and address unsafe acts and conditions in a timely manner
- Customer Service: Ensure that orders are confirmed properly to achieve organizational goal
- Quality: Control plan audit
- Responsible for consistent product quality, meeting customer expectations, and for continuous improvement activities
- Responsible for the efficient operation of all processes and the optimization of production rates and downtime minimization in order to achieve production cost objectives
- Hires, develops, and promotes staff to achieve manufacturing objectives
- Trains and develops supervisory and operating personnel on an on-going basis with primary focus on continuous improvement, problem solving, employee participation and retention
- Establishes and enforces good housekeeping and Autonomous Maintenance practices at all times
- Meets or exceeds relevant OSHA and EPA regulations for the manufacturing plant
- Reviews safety, quality, productivity, and workforce issues daily with staff
- Champion World Class Manufacturing (WCM) practices. Drive the implementation of WCM through Visual Shop Floor Management (VSFM) and the Tarkett North America "roadmap." Lead and participate to WCM 7 Steps problem solving
- Cascade Plant KPI's to Team Leader Boards on the Shop Floor
- Cascade KPI's from Team Leader Boards to Line Boards at each work center
- Drive plant performance - as measured by the Plant Scorecard (KPI's) - through the daily use of VSFM tools including: ·
- Team Leader Boards
- Standard Task Confirmation
- Line Boards – Tier 1, Tier 2, and value stream boards
- SOP's, OPL's, SWI’s: Create and revise standards related to safety, customer service, quality, and cost
- Structured root cause analysis & countermeasure identification/implementation
- Place emphasis on sustained improvement through the rigorous use of performance metrics and problem-solving tools (e.g., 7 Step, 5-Why's, Kaizen, PDCA, etc.)
- Structure the Production Managers' personal "cadence" (daily calendar) to include substantial time on the shop floor using the structured VSFM system. As a guide, the Production Manager should spend 50- 70% of his or her time on the shop floor
- Responsible for individual training matrix and is responsible for periodic review and self-management of required training
- Works with engineering and operating personnel to develop standard operating procedures and detailed process specifications for every product/process
- Ensures production schedule is executed to achieve 100% on-time delivery
- Control the material consumption (MUV- Material Usage Variance) through scrap reduction
- Drive daily schedule attainment and effectively allocate resources
- Define problems, collect qualitative and quantitative data to establish facts – take decisive action
- Maintain composure, think logically, and make sound decisions often in urgent situations
- Actively monitor, evaluate, and report performance daily using the Shop Floor Management Tools in WCM. Take full ownership of shift and performance reporting management
- Evaluate and coordinate training needs and initiatives of team to drive continuous improvement
- Work closely with Engineering and Maintenance to help improve and document production processes and equipment operation
- Provide coaching and guidance as required, as well as executing consistent documentation within the corrective action process including absenteeism tracking
- Improves record procedures to ensure organizational effectiveness and ISO requirements
- Learn, understand, and communicate compliance issues related to company guidelines and employment laws
- TARKETT's 7 CORE COMPETENCIES
- Understands and anticipates customer needs (internal and external)
- Proposes improvements and takes action
- Exhibits empathy and patience – is flexible
- Results Orientation
- Identifies challenges as learning opportunities
- Remains focused on goals but can adapt to change
- Collaborative Working
- Works productively with a wide range of people
- Gives and receives feedback constructively
- Communicate a clear vision to foster people engagement and alignment
- Role modeling, empowering and developing employees
- Analysis & Decision making
- Gathers data, analyzes, and provides thoughtful data-based recommendations
- Exercises clear judgment in challenging situations
- Interpersonal Effectiveness
- Efficiently interacts with others, using empathy, tact, and diplomacy
- Effectively confronts conflict
- Organizing & Planning
- Executes projects from start to finish
100
Plant Manager Resume Examples & Samples
- Instrumentation and Electrical – Demonstrates an understanding of electrical principals in practical situations involving the operation and repair of complex electrical devices
- Leadership – Candidate must have demonstrated knowledge and ability for using basic leadership skills to effectively engage and manage a production staff
- Bachelor of Science in Engineering [Mechanical Engineering, Electrical Engineering or Chemical Engineering] or equivalent education and experience
- Prior operations management of an air separation facility a plus
- Ability to effectively present information and respond to questions from employees and/or customers
- Ability to read and interpret documents such as safety rules, operating and maintenance instructions, and procedure manuals using the English language
101
Plant Manager Resume Examples & Samples
- Operates and safely maintains the plant for pumping or repackaging of gases into cylinders while ensuring compliance with all federal, state, local and company policies, procedures, regulations and laws. Maintains a neat, clean and orderly plant appearance
- Studies production schedules and estimate worker-hour requirements for completion of job assignments. Establishes and/or adjusts work procedures to meet production schedules
- Implements measures to improve production methods, equipment performance, and product quality. Modifies working conditions and use of equipment to increase efficiency of work crew
- Ensures all safety rules are strictly observed and safety training is regularly scheduled, conducted and documented. Interpret company policies to workers and enforce safety regulations
- Ensures all injuries and accidents are properly investigated and reported within 24 hours
- Analyzes and resolves, or assists workers in solving, work related problems. Recommends and/or initiates personnel actions, such as promotions, transfers, discharges, and disciplinary measures. Ensures associate issues, grievances, etc. are effectively handled
- Manages and leads subordinate supervisors to provide leadership. Initiate and/or suggest plans to motivate workers to achieve goals. Provides coaching and corrective action promptly, to ensure that poor performers are identified, documented and improved to acceptable performance, or released
- Trains new workers and cross trains associates to continue production during personnel shortages
- Maintains time and production records and approves overtime when essential, while keeping overtime at acceptable levels
- Additional duties and projects as may be assigned
- A total of five (5) years of industry experience to include a minimum of two (2) years of demonstrated experience working in a supervisory/leadership role. Prefer prior experience with compressed/packaged gases
- Strong interpersonal skills with the ability to deal effectively with others in both favorable and unfavorable situations regardless of status of position. Accepts cultural diversity and establishes effective working relationships
- Self-starter; self-motivated; well organized; ability to work independently
- Detail oriented with the ability to complete handwritten compliance documentation neatly and accurately
- Demonstrated dedication to product quality and customer satisfaction
- Able to operate a fork-lift
- Employee may be required to remain stationary for extended periods of time
- Employee may frequently be required to transverse through manufacturing and/or office locations
- Requires use of computer, telephone and operation of a fork-lift
- Occasionally may be required to move up to 60 pounds or more with the aid of material handling equipment
- While performing the duties of this job, the employee is occasionally exposed to moving office/production machine parts
- Requires both indoor & outdoor environments in various seasonal weather conditions. Must be able to work in temperatures ranging from -10 to over 100 degrees
- Work environment may contain loud noises and odors that may last for long periods of time or on a continual basis
102
Plant Manager Resume Examples & Samples
- Managing all plant operations to insure budgetary goals are met or exceeded
- Insure our products meet or exceed our QC standards, using specified SOP testing methods
- Responsible for maintaining a safe and clean working environment; and, comply with Federal, State and Corporate safety and environmental regulations
- Responsible for the maintenance of the facility to include the understanding of and ability to explain basic mechanical theory to direct reports, coordinating vendors, projecting and establishing preventative maintenance programs and schedules, while directing the maintenance staff to insure that all equipment is properly maintained and operational
- Responsible for implementing new and best processes of production
- Responsible for process improvement and problem solving to lower cost and improve quality
- Manage any special projects / improvements as directed
- Work with other Plant and Branch Managers to insure accurate and timely delivery of production requirements
- Interface with regional sales, management, and customers to insure high customer satisfaction. Recruit, hire, train, and discipline employees according to corporate guidelines and policies
- Insure timely and accurate data entry related to product sales, purchasing, and receiving of raw materials and supplies
- Fulfill all record keeping requirements related to the day-to-day operations in a timely manner to include: shift scheduling, performance evaluations, safety training documentation, disciplinary actions, associate development, and specific job related training
- Perform other duties as assigned by upper management
- Five (5) years experience in a significant leadership role of more than 10 production personnel in an industrial, manufacturing environment
- Ability and desire to provide top notch leadership
- Understanding of financial reports, budgetary methods and forecasting
- Flexibility to maintain a Facility operating on a 24/7 schedule
- High potential Operations or Production Mangers ready for the next level are encouraged to apply
- Bachelor's degree preferred or equivalent experience, to include military experience. (Associates degree or High School diploma with formal technical training considered in conjunction with extensive, relevant experience)
- Additional formal training in one or more of the following is desired: Hydraulics, Industrial Refrigeration, Reciprocating and Screw type Compressors, Manufacturing processes
- Decision making to execute company policies and implement plant procedures
- Organizational skills to maintain safety, quality, and equipment system files
103
Plant Manager Resume Examples & Samples
- 24 hour on-call responsibility
- Bachelor of Science in Engineering [ME, EE or ChemE] preferred or equivalent education and experience
- Prior experience with supervising a staff
- Prior operations management of an air separation facility
104
Plant Manager Resume Examples & Samples
- Perform activities to promote the maintenance of FDA compliance in the plant environment. Increase FDA awareness in all areas of the workplace
- Ensure completion of all FDA reporting and recordkeeping requirements
- Prepare the facility budget and manage expenditures to ensure costs are adequately controlled
- Recruit and train as needed to ensure adequate levels of staffing exist
- Reinforce and correct employee performance. Conduct appraisals and recommend personnel for promotion
- Develop and maintain positive employee relations
- Operate plant to meet Airgas safety, health, environmental, and quality policy. Implement programs to achieve targeted goals
- Implement and evaluate project to improve efficiency and productivity
- Facilitate team activities and nurture project completion
- Conduct periodic reviews of facility performance against stated objectives
- Conduct orientation for new line managers
- Monitor employee compliance with safety, health, environmental, and quality requirements
- Continuously review the Airgas Specialty Gas Quality System and help improve on implementation
- Evaluate, assign responsibility and monitor actions against recommendations arising from compliance audits
- Bachelor Degree in Engineering, Chemistry, Industrial Technology, or related field, or equivalent experience in medical gases industry
- 5+ years experience supervising, motivating and leading first level supervisors and other employees, preferably in a medical manufacturing environment
- Specific vision abilities to include close vision, distance vision, color vision, peripheral vision, depth perception and ability to focus objects
105
Plant Manager Resume Examples & Samples
- Directly supervise plant operators and Maintenance Manager in operating a nitrous oxide plant 24 hours per day, 7 days a week
- Supervisory responsibilities include interviewing, hiring and training employees, providing feedback and conducting performance appraisals
- The Plant Manager submits budget requirements for operating expense and capital expenditures. The manager then tracks and controls production costs throughout the year
- Responsible for compliance with FDA, EPA, DOT and other applicable regulations
- Interface directly with suppliers and service providers
- Primary point of contact in managing our very important relationship with CF Industries
- Orders process chemicals and all other supplies required for plant operation
- Prior experience managing people is desired
- A Bachelor’s degree in chemistry or in Chemical or Mechanical Engineering is also desired
- Commensurate combination of experience and training will be considered
- Experience working with pumps, compressors, refrigeration systems, electrical systems, and controls is desirable
- The Plant Manager must be completely at ease using word processors, spreadsheets, and communication by electronic means
106
Plant Manager Resume Examples & Samples
- Bachelor's degree or an equivalent combination of education and experience
- Three years of related work experience
- Three to five years of relevant work experience
- Energy sector or solar energy experience in utility, commercial or residential/small commercial environment
- Demonstrate knowledge and expertise in the area of field support
- Light sedentary office work
- Minimal lifting (<25 lbs) may be required
107
Plant Manager Resume Examples & Samples
- Coordinate cylinder requirements with region branches or delegates to Asst. Plant Manager or Plant Supervisor
- Trains and develops assigned personnel. Responsible for conducting timely and quality performance appraisals of assigned personnel with Asst. Plant Manager. Recommends disciplinary action up to and including termination of plant personnel supervisor
- Delegates or directly directs and coordinates plant activities to obtain optimum efficiency and economy of operations and maximize production
- Analyses plant budget to identify areas in which efficiencies can be obtained and production costs reduced and then allocates operating budget
- Develops plant goals and works with and through subordinate associates to achieve results. Works with Plant Supervisor or Asst. Plant Manager to achieve goals
- Follows and maintains all FDA, OSHA, EPA, DOT requirements and regulations
- Supervises Plant Supervisor or Asst. Plant Manager if position part of operation
- Maintain all required computer and hand generated paperwork or delegates to Plant Supervisor or Asst. Plant Manager
- Reports any equipment or facility defects to Operations Management
- Reviews technical publications, articles, and abstracts to stay abreast of technical developments in the industry
- Responsible for safety and safety practices of assigned personnel
108
Plant Manager Resume Examples & Samples
- Establish and maintain effective safety programs to ensure an injury free workplace
- Ensure regulatory compliance with all Federal, State and local regulations and associated permits
- Achieve all station performance targets, including safety, environmental compliance, high unit performance and low unit production cost
- Oversee the direction and coordination of O&M work force in the day-to-day operations and maintenance of the power plant in order to meet production schedules including maintenance, emergency repairs and retrofits
- Direct plant performance and investigate and correct any abnormal conditions
- Develop and submit for approval annual budgets and business plans. Execute plant operations within the approved budgets and in accordance with the Station business plan
- Ensure alignment of all individual, team, and station goals with corporate goals
- Plan and implement equipment modifications and plant improvements
- Evaluate and manage plant for compliance with contractual requirements
- Oversee the direction of onsite subcontractors
- Provide input to Corporate O&M and Fuels in fuel planning, fuel procurement, compilation of fuel usage statistics and analysis, and participate in fuel-related regulatory proceedings if needed
- Authorize contracts and approves transactions in accordance with Company policy
- Ensure adherence to the Code of Conduct
- Oversee the development and implementation of personnel management programs including job definition/expectations, recruiting, hiring, training, performance feedback evaluations
- Assure proper working environment by maintaining discipline, morale and employee relations
- Maintain collaborative relationships with the union leadership
- Establish and maintain positive communications with the media, civic and community groups, customers, employees and government
- Recommend marketing strategies and programs to maintain and expand the customer base and enhance Company revenues
- Bachelor’s degree in engineering or related field
- Extensive knowledge of power plants operations including technical and maintenance practices
- Excellent verbal, interpersonal, and written communication skills
- Employee relations skills especially in a union environment
- Ability to formulate and execute appropriate technical and business plans and objectives
109
Plant Manager Resume Examples & Samples
- Manage production resources to meet customer commitments, with internal on-time delivery target. This will include managing leaders in Manufacturing Engineering, Supply Chain, EH&S, Quality, and Operations
- Manage cost improvement/lean manufacturing activities to meet quarterly financial productivity commitments. Projects must be identified and tracked, to continually improve the 4-wall operating costs, including material, labor, and base costs
- Oversee the inventory management function, to develop and meet turns/DSI goals, including reduction of excess and obsolete inventory. (Managed by Supply Chain Manager)
- Accountability for the plant EHS program, including 100% compliance with all requirements and regulations, plus achievement of goals on injury rate reduction, waste minimization, Road-Map, scorecard and other key EHS metrics. (Managed by EH&S Specialist)
- Support the annual operating planning cycle, including strategic plan, annual operating plan, budget development, and capital plan
- Support new product development, including participation in PRB, prototype development, and product launch
- Lead the plant communications program, including quarterly update presentations, departmental meetings, communications meetings, posted key metrics
- Develop the plant staff and workforce through the performance management process, including training and development plans for each direct report
- Ensure compliance with plant and corporate policies
- Solid background in operations management
- Ability to motivate employees and drive continuous improvement throughout the plant using progressive methods such as Lean Manufacturing and 6-Sigma methodologies
- Excellent human resource/interpersonal skills to communicate effectively and resolve conflicts
- Results driven with emphasis on keeping customer and business commitments
- Financial systems experience including understanding of P&L and inventory management
- Supply chain management experience (direct materials responsibility a plus)
- Demonstrated strategic planning and problem solving skills
- Quality systems experience. ISO and/or Six Sigma a plus
- BS in business, engineering or related fields preferred
- 6-10 years of experience in world class manufacturing environment
- 3-5 years in a related industry a plus
110
Plant Manager Resume Examples & Samples
- Review processing schedules and production orders to make decisions concerning inventory requirements, staffing requirements, work procedures, and duty assignments, considering budgetary limitations and time constraints
- Direct and coordinate production, processing, distribution, and marketing activities of industrial organization
- Hire, train, evaluate, and discharge staff, and resolve personnel grievances
- Develop and implement production tracking and quality control systems, analyzing production, quality control, maintenance, and other operational reports, to detect production problems
- Determines and reviews all manufacturing processes for cost effectiveness and feasibility, both before and after engineering releases to manufacturing
- Determines priorities with the Manufacturing Manager, and implements cost-reduction projects; maintains detailed documentation as required
- Coordinates company’s safety efforts with outside regulatory agencies such as OSHA, EPA, insurance carriers, etc.; ensures conformity to regulations as well as internal safety practices
- Prepares all departmental budgets as necessary; ensures conformance as required
- Coordinate and recommend procedures for facility and equipment maintenance or modification, including the replacement of machines
- Perform all functions in compliance with established quality standards
- Comply with and enforce all Company GMP Rules
- Comply with and enforce all Company Housekeeping Rules
- Comply with and enforce all Company Safety and Rules of Conduct
- Continuously improve self and department’s performance
- Responsible for maintaining high quality standards and supporting the Food Safety/Quality systems
- Responsible for initiating action on any food safety problems reported by personnel and for the follow-up to ensure problems have been corrected
- Responsible for supporting the development, implementation, maintenance and ongoing improvement of food safety/quality system
- Bachelor's Degree from an acrredited college or university required
- Minimum of 5 years experience in the food industry
- 3-5 years of continuous improvement and project experience required
- 8-10 years of production/plant experience
- Experience with new product launches
111
Plant Manager Resume Examples & Samples
- Direct daily plant activities, including supervision of salaried staff
- Plan and manage all financial aspects of the facility (AOP, capital, etc.)
- Plan and manage all quality, environmental health and safety compliance and regulator aspects
- Champion of plant continuous improvement activities (BOS, Lean, TVM, Kaizen)
- Identify and track key measures to monitor facility/function effectiveness, and set and monitor staff goals and objectives
- Drive development of facilities processes and future capabilities
- Ensure all people and customer requirements are maintained to the highest standard
- Champion development of all team members
- Succession Planning
- Interface, planning, visits with customers, engineers, and sales
- Supplier development
- Champion Strategic Planning team
- This list may not be all-inclusive and may include other duties as assigned by the supervisor
- Administration and Management – Knowledge of business and management principles involved in strategic planning, resource allocation, human resources modeling, leadership technique, production methods, and coordination of people and resources
- Customer and Personal Service – Knowledge of principles and processes for providing customer and personal services. This includes customer needs assessment, meeting quality standards for services, and evaluation of customer satisfaction
- Economics and Accounting – Knowledge of economic and accounting principles and practices, the financial markets, banking and the analysis and reporting of financial data
- Active Listening – Giving full attention to what other people are saying, taking time to understand the points being made, asking questions as appropriate, and not interrupting at inappropriate times
- Coordination – Adjusting actions in relation to others' actions
- Critical Thinking – Using logic and reasoning to identify the strengths and weaknesses of alternative solutions, conclusions or approaches to problems
- Time Management – Managing one's own time and the time of others
- Problem Sensitivity – The ability to tell when something is wrong or is likely to go wrong. It does not involve solving the problem, only recognizing there is a problem
- Oral Expression – The ability to communicate information and ideas in speaking so others will understand
- Guiding, Directing and Motivating Subordinates – Providing guidance and direction to subordinates, including setting performance standards and monitoring performance
- Bachelor’s degree from a four-year college or university or equivalent combination of education and experience
- 7+ years of related business and managerial experience required
- Held various levels of management positions with proven proficiency and effectiveness
- Working knowledge of automotive industry and related systems
112
Plant Manager Resume Examples & Samples
- Monitors operations for efficiency and safety ensuring that all applicable regulatory requirements are met/followed. Support and drive all company safety policies, practices and procedures to ensure 100% compliance
- Provide leadership for employee relations through effective communications, coaching, training and development and problem resolution
- Develops production schedules to meet internal goals as well as expectations of customers
- Help establish and direct plant policies and procedures
- Drive improvements in plant operations, manufacturing processes and standardized work procedures leading to productivity and efficiency gains through application of Lean Tools
- Work closely with finance and sales & marketing to partner towards sales objectives
- 8 years of operations management experience in a manufacturing environment
113
Plant Manager Resume Examples & Samples
- Develops a good working relationship with the customer’s leadership team and present themselves and Valspar in a positive and beneficial manner. Create an environment of cooperation and mutual respect
- Be responsible for meeting or exceeding production goals, including safety performance, cost, downtime, scrap, and quality
- Manage the finishing operations, including pretreatment, manual/automatic spraying, curing, and air drying
- Hire and manage employee relations and performance issues, employee development activities and ensuring an effective and productive workforce
- Participate and lead continuous improvement initiatives using tools such as Lean Six Sigma, and other process improvement techniques
- Develops operating policies and procedures to ensure the efficient use of resources, maintain a safe environment, and produce quality products
- Six years of production experience, including two years of supervisory experience
- Bachelor's degree required: engineering, business, operations, or a related field preferred
- Paint line management or has been a paint line engineer with progressive responsibilities
- Excellent customer service skills. Ability to work closely with end customer and provide high level of customer satisfaction
- Experience with paint application systems, spray operations, and finishing
- Knowledge of paint and application techniques, such as pretreatment and liquid coating applications
- Knowledge of Six Sigma, Lean, optimization, and other process improvement processes
- Strong management skills and demonstrated ability to effectively manage a diverse group of employees and build a team culture
- Experience with Nordson equipment a plus
- Working knowledge of safety and environmental practices and regulations, including OSHA compliance
- Strong communications skills
114
Plant Manager Resume Examples & Samples
- Manage financials of the plant
- Reduce employee turnover and increase employee engagement
- Manage and delegate projects that complement Enterprise Connectivity strategic initiatives
- Maintain target percentage on custom quotes delivered in two days or less
- Manage and deliver on KPI targets
- Manage and improve response time on quotations and drawing submittals for projects
- Manage and deliver on top line growth while maintaining profitability
115
Plant Manager Resume Examples & Samples
- Bachelor’s degree in Business/Engineering/Finance/Management/Operations or another related field
- 7+ years progressive experience in a key leadership/management role at a manufacturing facility
- Previous experience/best practices implementing and using continuous improvement/lean tools such as; Six Sigma, 5-S, Lean Manufacturing, Transactional Lean, etc. to drive improvement
- Previous experience/broad understanding of safety systems and enforcement of safety rules and policies
- Demonstrated strong leadership, team building and advanced coaching skills
- Demonstrated ability to motivate people, assess and develop employee skills
- Demonstrated understanding of the principles and applications associated with manufacturing operations, maintenance and engineering
- Lead by example and motivate all personnel on achieving and providing high quality products and services being provided on-time
- Coordinate and work with Quality and Regulatory teams to assure appropriate performance, documentation and compliance with Quality Management System (QMS)/ISO/GMP
- Coordinate the hiring and training of all manufacturing personnel
- Work closely with the team to ensure all members of the manufacturing and warehousing teams are aware of safety policies to provide a safe workplace
- Maintain Inventory levels and control flow of product to achieve efficient production and warehouse operations
- Maintain and support safety and housekeeping program, including all timely communication initiatives
- Lead, monitor and contribute to significant projects initiatives
116
Plant Manager Resume Examples & Samples
- Directing and coordinating all plant functions including Manufacturing, Materials, Production Control, Quality Assurance, Planning, Human Resources, Accounting, Mfg. Engineering and Environmental, Health & Safety to assure common direction toward plant goals
- Driving continuous improvement and operational excellence
- Guiding and supporting the plant Environmental Health & Safety program in improvements, investigations and corrective actions to meet and exceed local and Federal laws
- Guiding and supporting the plant quality system in procedures and controls to improve overall customer satisfaction, PPM and first pass yield
- Ensuring customer satisfaction in all areas, including delivery, schedule changes and special instructions
- Plant maintenance, including: facilities and manufacturing engineering, facility and process improvements and capital expenditures
- Achieving material and labor productivity plans
- Directing the long-term product strategy for the manufacturing business
- Maintaining positive relationships with all levels of the organization, in order to foster and promote a diverse and inclusive work environment, high levels of morale, and high employee engagement
- Ensuring alignment of goals - and progress towards them – across the organization
- Leading employee development succession-planning activities
- Rich and deep experiences in developing trust and credibility with key stakeholders through consistently meeting or exceeding commitments
- Deep experience with implementing Lean manufacturing tools and culture is required
- Able to motivate and sustain a high performance and “customer first” culture down to the lowest levels in the organization as “a way of doing business”
- Proven track record of selecting and developing leadership talent
- Ability to blend manufacturing strategic vision with tactical execution across the organization
- Proficiency in Materials Management
- Must be a US Person. (US Citizen or Permanent Resident)
117
Plant Manager Resume Examples & Samples
- Develops and administers financial budgets and activities to fund operations, maximize investments and increase efficiency
- Oversight of production, distribution, cost accounting, sales and customer services
- Directs and manages resources to implement tactical business plans and programs to see work through completion
- Communicate the vision for the plant and communicates strategy and objectives effectively
- Sets clear and consistent expectations for performance and leverages resources available to accomplish goals
- Follows up on critical tasks and holds people accountable for adhering to process and protocol
- Ensures that team has necessary resources and removes barriers where appropriate
- Stage work and recalibrate throughout the day as necessary to meet customer demand
- Prioritize the necessary resources and create the tactical steps required to accomplish goals on time
- Identifies talent correctly and shows ownership of all aspects of plant staffing and retention
- Exhibits a strong work ethic and focus on Lean manufacturing, safety, quality, productivity and cost
- Persistent in achieving desired results
- Bachelor’s degree or equivalent preferred
- Minimum of 5 years of experience in a rotary kiln, cooler, crushing and screening operation preferred
- Minimum of 5 years of experience in a MSHA regulatory environment preferred
- Minimum of 5 years of experience in a Title V regulated operational environment preferred
- Minimum of 3 years working in light weight aggregate operations management preferred
- Experience with complex to moderate project management in a quarry/aggregate environment
- Has led complex to moderate operations with products on multiple manufacturing lines
- Able to apply stringent quality control and federal regulatory requirements
- In depth knowledge of Lean Manufacturing principles and practices
- Strong mechanical/technical aptitude with a hands on leadership approach required
118
Plant Manager Resume Examples & Samples
- Primary owner of shop operations including safety, on-time delivery, costs, asset utilization and inventory. Responsible to deliver repair, refurbishment and/or other service operations
- Drive productivity and ensure delivery in accordance with cost budgets
- Manage the facility within operating budget
- Be responsible for the day-to-day operations at this site including all aspects from the reception of raw materials through the delivery of finished product. Develop and manage budgets to approve expenditures for supplies, materials, and human resources, ensuring that materials, labor and equipment are used efficiently to meet production targets
- Drive operational excellence across the site, developing and implementing best practices and making extensive use of Six Sigma and Lean Manufacturing techniques to simplify workflows and reduce cycle times. Lead and support initiatives such as cost of quality/Lean, total cost out initiatives
- Drive base/variable costs and promote initiatives to reduce bullet train costs
- Partner and integrate with the regional Sales/Commercial, Supply Chain, OTR, Operations Delivery Managers, Resource teams and Project Managers in order to help develop flexible and innovative shop strategies that improve product line competitive positioning. Own and drive operational excellence with processes and tools with a focus on continuous improvement through the application of Six Sigma and/or Lean principles within the Service Shop
- Establish and adjust an organizational structure that best supports the shop's goals and measurements. Provide technical expertise, coaching, encouragement, motivation and development to shop teams to ensure development of strong talent pool and robust execution. Responsible for the execution and technical skills of all Technicians, materials team members, Warehouse, Logistics ) in partnership with global Services & Offshore Operation COE
- EHS: Promote and own a working environment to achieve excellence in EHS, Compliance, Quality, Customer Service & Productivity
- EHS
- On-time delivery
- Cost excellence (product & organizational)
- Bachelor’s degree from an accredited university or college (preference of Engineering or other technical degree) or equivalent knowledge and experience
- Proven years of Oil & Gas or relevant industry experience is preferred
- Proven years of experience in a manufacturing or service shop environment including leading hourly employees
- Six-sigma or Lean certification is preferred
- Existing knowledge of the disciplines of manufacturing/shop management such as MRP/ERP systems, assembly and test systems, production and inventory control, variable cost productivity, and fulfillment metrics, quality systems, cost systems and procedures
- Existing or strong willingness to gain technical knowledge of Subsea production equipment and services
- Ability to manage & lead effectively in a dynamic, matrix and fast paced environment
- Ability to problem solve while staying objective and analytical
- Ability to effectively plan and organize in order to meet customer requirements
- Ability to apply statistical methods for process improvement
- Proven performance track record
119
Plant Manager Resume Examples & Samples
- Ensure a safe work environment for all employees and maintain a safe working record. Administer proper safety practices and procedures
- Oversee manufacturing operations. Meet or exceed quality, productivity and maintenance expectations
- Ensure excellent customer service through professional fleet operation, customer relations and proper inventory
- Manage proper staffing levels and facilitate employee training, development and career progression
- Prepare annual operating budgets for plant operations. Meet or exceed budget requirements
- Ensure proper management of all raw materials, finished goods and equipment inventories
- Facilitate various operational programs and ensure plant compliance
- Prepare weekly, monthly and annual financial reports
- Maintain appropriate communications with other ADS manufacturing facilities and offices
- Understand and practice ADS CORE VALUES
- Maintain and build job skills through company and outside training programs
- Promote a positive and transparent work environment
- Ensure proper management of operating supply purchases via the internal purchase order system or company credit card
- Excellent leadership skills
- Ability to communicate at different levels within the organization
- Minimum of 3-5 years experience in a Plant Manager role
- Plastic processing experience, including extrusion and/or vacuum-forming, is preferred
120
Plant Manager Resume Examples & Samples
- Serve as an Engineered Air & Process Gas Product Growth Team (PGT) Global Leader with counterparts from Engineering and Product Management to significantly improve and sustain performance around cycle, delivery, quality, cash generation and productivity
- Bachelor's degree in Engineering or equivalent technical discipline is required; MBA preferred
- Minimum of 10 to 15 years experience in manufacturing operations required; and a minimum of 5 years in a manufacturing/plant operations leadership roles, preferably as Plant Manager of a small to medium size plant
121
Plant Manager Resume Examples & Samples
- Gain and convey knowledge of the Biuret production process looking for opportunities to improve capacity and enhance plant efficiencies while lowering operating costs
- Build strong relations with plant operations and support both troubleshooting and continuous improvement efforts. Organize and lead diverse technical project teams towards the timely completion of project goals and to work across various functions including operations, business development and R&D to build project support and communicate results
- Work with Managers and Supervisors, Quincy Management, and Decatur, to ensure Safety training programs are being completed
- Work with QA technicians to help implement food safety/sanitation /quality programs to ensure that the facility is compliant with the law, regulatory requirements, and company programs along with continuously looking for improvements to the Quality Assurance programs
- Work to find new and more efficient ways to manufacture, ship, and control costs to help add value to ADM shareholders
- Strong interpersonal, written and verbal communication skills with proven success interacting with individuals and groups at all levels of an organization
- Be self-motivated with the ability to manage time and priorities, work independently and objectively
- Computer skills in Microsoft Office products (Word, Excel, PowerPoint and Outlook)
- History of working safely with a reputation of promoting and getting involved in safety improvement efforts
122
Plant Manager Resume Examples & Samples
- Provide leadership for the quality, maintenance, warehouse and production departments to develop organizational capability and capacity
- Ensure product and package quality standards are met to exceed customer and consumer expectations and protect CCBCC and Coca Cola system image and brands
- Ensure efficient and effective utilization of plant's physical and employee assets to minimize system cost of production while meeting customer (sales) needs
- Develop and manage expense, capital, and labor budgets to support CCBCC budgeting, cost-related decision-making, and long-term financial planning
- Provide a safe work environment for employees to reduce costs associated with injuries and illnesses and avoid employee-relations issues
- Serve as representative on Company committee and other centrally organized business initiatives to ensure plant-level input is being considered in decisions
- Expereince preparing and administering complex budgets
- Proven ability to establish and maintain cross funtional working relationships
- Expereinced with selecting, supervising, training and evaluating staff
- Proven ability to utilize problem solving and analytical skills
- Expereinced at planning and organizing work to meet schedules and timelines
- Proven ability to be attentive to detail in a fast paced and complex work environment
- 10+ years management/leadership/coaching experience
- 4 years experience in high-speed packaging industry
- Previous expereince in the beverage industry is strongly preferred
- Listening Skills
- Persistence
- Shared Company Ethics and Values
- Strong communication skills both Written and Verbal
123
Plant Manager Resume Examples & Samples
- Demonstrated structured problem solving skills
- Strong organizational and planning capabilities
- Results oriented attitude
- Ability to develop and lead a high performance team
- Results oriented with a bias for action
- Inspires trust through open communication and collaboration
124
Plant Manager Resume Examples & Samples
- Will be responsible for strategic and operational direction related to Manufacturing, Customer Liaison, Product Quality, Materials, Facilities, Finance, and Human Resources
- Will develop plans and strategies to ensure new technologies, products, and processes are integrated into production while maintaining a world-class manufacturing facility. Will also serve as a direct liaison with design center and sister plants in North America
- Will advance continuous improvement through appropriate systems implementation and will directly supervise a staff of eight managers
- Comply with and support the health, safety, and environmental programs, policies and procedures
125
Plant Manager Resume Examples & Samples
- Establishes and supports an organization capable of producing results consistent with performance criteria and plans at company level
- Responsibilities include production, maintenance, quality shipping/receiving and other related operations. Leads the workforce in continuous improvement activities, both systems and processes, and benchmarks appropriate standards of conduct throughout the operation
- Keeps employees informed of key issues, supports quality, consistency and integrity in all transactions
- Knowledge of all product lines within the production plant. Specialized knowledge of accounting and financial requirements
- 10+ year's experience in manufacturing environment. 5+ years management experience
- Comprehensive knowledge of manufacturing principles, concepts, theories and practices of area of responsibility
126
Plant Manager Resume Examples & Samples
- Responsible for all manufacturing operations including the safety, production efficiencies, quality, customer service, and financial performance of the plant
- Leads team members by managing and executing plant processes
- Leads team members in attaining plant production and quality targets
- Creates and maintains an engaged and team-oriented workforce to meet business demands
127
Plant Manager Resume Examples & Samples
- Set the cultural tone and continually improve personal and process safety awareness and results
- Establish Supervisor and Management systems to assure continual improvements in quality, reliability, and efficiency
- Interface with sales, corporate, suppliers, and the union
- Ensure plant meets or exceeds fiscal goals within approved budgets
- Negotiate union contracts and supply contracts with utilities
- Manage projects for installation of new equipment and equipment upgrades
- Manage all employees of the department and is responsible for the performance management and hiring of the employees within that department
- Expertise in risk assessment and risk management
- Negotiation/Mediation skills to resolve issues internally and externally
- Flexibility to perform multiple tasks simultaneously and follow each to completion
- Strong communication skills, both oral and written, with the capability of positively interfacing with customers
- Strong leadership skills, including the ability to influence key contributors and build a strong team
128
Plant Manager Resume Examples & Samples
- Responsible for planning and scheduling production activities, and supervising the production process
- Oversees maintenance of all equipment including managing downtime
- Responsible for inventory control, counts and audits
- Strong commitment to health, safety, quality, productivity, housekeeping, maintenance and environmental compliance
- Estimating production costs, maintaining high quality standards and ensuring good customer service
- Monitor product standards and implement quality control programs
- Responsible for maximizing the use of transportation/logistics
- Working with different departments (e.g. suppliers, sales, customers) effectively to execute the policies and goals of the organization
- Ensure compliance with SOX rules and regulations
- Ensure the business meets expected financial returns
- Ensures compliance with all local and federal environmental regulations
- Responsible for employee hiring, terminations and performance reviews
129
Plant Manager Resume Examples & Samples
- Bachelor's degree required or equivalent combinations of education, experience and training
- One to two years related experience and or training
- Finance and accounting skills
- Knowledge of Axapta sales order module
- Knowledge of labor laws
- Purchasing experience
- Knowledge of construction products
- Must have basic knowledge of electronics and programmable controllers
- Know the operation of the block producing equipment and accessory equipment
- Ability to calculate figures/amounts
- Good oral and written communication skills
- Ability to train and instruct employees
- Good analytical problem solving skills
- Strong Microsoft Word and Excel skills
130
Plant Manager Resume Examples & Samples
- Works closely with the Plant Manager to ensure on-going operations and production schedules
- Assists the Plant Manager in planning, scheduling and directing overall plant productions
- Assists in monitoring operating budget and production efficiency
- Monitor production and initiate corrective action as required to ensure plant follows and complies with safety guidelines, quality control and productions as established
- Must have strong mechanical background in order to assist with maintenance and repairs when needed
- Assists in adherence and development of security and maintenance programs and procedures for the facility
- Ensure all production, shift and plant supervisors are properly trained and motivated
- Coordinate production requirements and inventories with sales and market demands
- Assist in the resolution of job/customer complaints as needed
- Reporting on progress towards business, production and general operating objectives as may be required by the Plant Manager, Regional Operations Manager or company executives
- Coordinate training and development of supervisory and factory floor technical, maintenance and operative personnel
- Other duties and responsibilities related to the nature of the job may be assigned on a temporary or permanent basis as needed
- Responsibilities include interviewing, and training employees; planning assigning and directing work; appraising performance; addressing complaints and resolving problems
- Directly reviews and monitors efforts and initiatives carried out by the direct reports and other plant personnel
- Responsible for evaluating the performance, training needs, professional development and discipline of direct reports and quality control staff
- Bachelor’s Degree from four-year college or university, preferred in Mechanical or other Engineering discipline or related field, 3+ years related experience and/or training in related functions; or an equivalent combination of education, training and experience
- Prior experience in budgeting, profitability, products quality and process improvement in production/manufacturing environment preferred
- Detail oriented and strong accuracy and concentration skills
- Must be attentive to critical details and follow procedures while evaluating sample quality
- Must have ability to read, analyze and interpret common scientific and technical journals, financial reports and legal documents
- Proficient in MS Office suite, web-based data management tools and Internet applications
- Ability to respond to common inquiries or complaints from customers, regulatory agencies, or members of the business community and peers
- Ability to write speeches and article for publication that conform to prescribed style and format
- Ability to effectively present information to top management, public groups and/or boards of directors
- Must have ability to comprehend and apply principles of advanced calculus, modern algebra, and advanced statistical theory
- Must have the ability to define problems, collect data establish facts and draw valid conclusions
- Must have ability to interpret an extensive variety of technical instructions in mathematic or diagram form and deal with several abstract and concrete variables
131
Plant Manager Resume Examples & Samples
- Government Compliant Safety of Taylor, Michigan Plant Operations
- Ensure consistent quality of products and appearance of packages for delivery
- Manage daily operation of the plant to ensure accomplishment of the manufacturing plan
- Maintain plant assets to assure ability to meet manufacturing plan
- Uphold accurate financial records through work with local and corporate personnel
- Keep staffing levels consistent within budget and advise senior management of needs in excess of budget
132
Plant Manager Resume Examples & Samples
- Foster and enhance the safety culture to achieve safety excellence
- Provide operational and employee leadership to the facility
- Manage financial performance and make required changes as needed to meet business commitments
- Manage all aspects of the plant cost structure including direct and indirect labor, maintenance and consumable spending and proactively control to business volume swings to preserve profitability
- Assist operating management with budgeting, production statistics, cost analysis, justification of capital expenditures and asset management
- Lead the facility in establishing and meeting continuous improvement objectives
- Partner with department managers to develop and maintain a positive culture consistent with Berry Plastics’ values
- Encourage and support the development of all plant employees
- Participate in process improvement and cost savings efforts
- Responsible for incorporating continuous quality improvement principles into daily quality culture
- Assures compliance with state and federal regulatory matters including OSHA, EPA, EEO and Affirmative Action, Quality Audits
- Overall management responsibility for the implementation of mandatory and best practice sharing for cost savings, safety compliance and reduced employee hazard exposure
- Coordinates the effective utilization of production capacity, staffing and equipment through planning, organizing and scheduling
- Continuously improves customer satisfaction through programs to provide on-time delivery that meets and/or exceeds customer quality and cost expectations
- Maintains a sense of urgency and accountability in the plant to ensure prompt responses to employee needs
- Ensures the protection of company assets through appropriate maintenance methodologies
- Monitors raw materials and supplies on hand to ensure adequate supply
- Maintain 24 hour/day on call availability to deal with potential problems/issues
- 10+ years supervisory experience
- Knowledge of and experience with film manufacturing processes
- Strong organizational skills with proven ability to complete multiple tasks simultaneously
- Excellent analytical skills required
- Knowledge of Microsoft office tools
- Strong planning/organizing skills
- Ability to work in a fast-paced team setting
- Ability to effectively communicate/present findings to a wide variety of audiences
- Ability to supervise, coach, mentor and perform other functions associated with leading and managing a group
133
Plant Manager Resume Examples & Samples
- Oversee all plant operations and related support areas
- Coordinate technical service activities across a broad range of internal and external assignments
- Represent Briggs & Stratton interests in dealings with suppliers and customers
- Accountable for manufacturing costs, quality and production quantities. Manage the effective use of production hours, skills, equipment and facilities
- Participate in planning production schedules, requirements and manufacturing controls as related to manufacturing operations
- Work closely with Briggs & Stratton plant management personnel to develop and implement strategies for operational improvement. Ensure efficiency standards for all operations are met
- Responsible for development of capital and other annual budgeting including evaluating the economic Value Added (EVA) and Return on Investment (ROI) impact for location. Responsible for maintaining and managing established budgets throughout fiscal year to achieve financial goals
- Cost and evaluate new technologies and recommend strategies for acquisition and implementation
- Drive cost reduction and continuous improvement concepts and projects to achieve annual goals. Monitor and improve employee productivity and effectiveness related to Operations and maintain a commitment to employee involvement
- Manage all aspects of plant safety, security and environmental compliance
- Consistently administer company rules, regulations and policies
- Perform full range of managerial responsibilities which may include but not be limited to: interviewing, hiring, coaching and developing employees; planning, assigning and directing work; EEO/AA; performance management; department budget
- Perform other duties and responsibilities as requested or required
- Comprehensive knowledge of technical service practices, processes, procedures and production support activities including efficiency levels and productivity standards
- Excellent written, verbal and interpersonal communication skills to effectively work with diverse groups of people
- Demonstrated success in implementing large-scale improvements and changes in complex and diverse environments
- Proficient computer skills and familiarity with MS Office applications (Word, Excel, PowerPoint, Access) and business control software (SAP)
- Technical experience and familiarity with all facets of manufacturing process
- Familiarity with Purchasing and Industrial Engineering functions as well as plant layout efficiencies
- Ability to manage projects and activities in multiple locations with diverse groups of people
- Strong leadership and motivational skills and the ability to develop leadership qualities in others
- Ability to coordinate and organize multiple projects simultaneously
- Well-developed analytical skills and knowledge of analysis techniques that assist in report preparation for decision-making purposes
- Minimum ten years experience in a technical service or related field required
- Manufacturing and management experience preferred but not required
134
Plant Manager Resume Examples & Samples
- Must be able to establish operational goals, both financial and non financial, with clear work plans, and hold management staff accountable for achievement of goals
- Manager is also responsible for making recommendations for the planning of budgets, company assets, labor forecasts and capital expenditures for the purpose of short-term and long-range production and operation of the plant
- Past successful experience in operations, marketing, sales and office management in a metal recycling facility or other related industry a strong plus
- Preferred familiarity with material handling equipment and how to properly maintain (maintenance programs) and repair equipment
- Knowledge of transportation and logistics is critical
- Broad knowledge of marketing/sales is important
- Ability to forecast short and long-term buying of material to meet on-time delivery schedules to our consumers in conjunction with Plant Marketing
- Manager
- Must be able to control inventory dollars by meeting inventory turn standards set forth the company
- Must be able to manage an all office staff, (except marketing staff), an accounts payable clerk, a scale person and a dispatch clerk
- Proven track record of utilizing Lean Management, Kaizen, 5S, and other continuous improvement management systems is important
- Foreign language preferred
- Should be able to clearly communicate expectations, issues and feedback
- Must be able to problem-solve in all areas of plant
- Must be able to control budgeted labor and overtime costs; as well as, maintain fiscal responsibility for all departments’ budgets
- Proficiency in applications such as Internet, e-mail, Word and Excel is vitally important
135
Plant Manager Resume Examples & Samples
- Directs and motivates plant production, maintenance and staff personnel in the attainment of business and facility objectives
- Insures and maintains a safe, compliant, and efficient production facility
- Coordinates, guides, and plans daily plant production, maintenance, and administrative activities
- Reviews and analyzes daily productivity, waste and quality reports
- Reviews and analyzes financial, statistical and trend analysis reports
- Reviews and analyzes safety statistical and trend reports and safety incident reports
- Develops corrective actions and process improvement initiatives
- Controls expenditures and reviews operational budget
- Participates in the establishment of strategic business and project goals
- Facilitates and coordinates activities with other departments and functions
- Interfaces with outside vendors, contractors and customers in support of plant objectives
- Responsible for providing a safe and healthful workplace; controlling recognized hazards, enforcing safety policies and procedures, coaching safe behavior, and maintaining compliance with all regulations
- Incorporates and maintains safety observances, including but not limited to, use of all PPE by employees, ensuring guards and safety features are working, and promoting good daily safety practices and habits
- Communicates goals and objectives, applies company policy, staffs, trains, coaches, recommends salary increases, administers discipline, insures positive employee relations and reviews the performance of employees
- 5 to 7 years direct experience in production control and management
- Substantial experience in supervisory and management skills
- High degree of organizational skills
- Understanding of OSHA, labor and other federal regulations
- Understanding of basic engineering principles
- Exceptional abilities in prioritizing, delegating, and goal setting
- Fundamental understanding of computer operations and software
136
Plant Manager Resume Examples & Samples
- Explore and analyze technical, production and management disciplines to develop annual budgets and long-term plans
- Establish and approve financial goals, operating and capital budgets, work schedules and human resource requirements
- Develop, monitor and assign priorities to achieve or surpass goals. Monitor and adjust budgets and schedule human resources to meet changing conditions
- Provide general administrative direction to the accounting function to improve the company’s financial soundness, cash flow and expenditures and provide accurate accounting information and financial control data. Monitor year-end closing activities, reviewing and submitting the external auditor’s financial report
- Provide direction for materials management acting as a champion for cost effective purchasing decisions and inventory control methods
- Provide direction to all department managers, supervisors and plant personnel in the areas of safety, raw material utilization, rates and expenses consistent with the plant performance objectives and to maximize operating income
137
Plant Manager Resume Examples & Samples
- Plan, schedule, and coordinate the production of high quality, safe, and cost-effective turkey products
- Provide leadership to create an environment committed to product quality, food safety, team member safety, and positive team member relations
- Participate in the development of current and long-term plans and strategies, and provide input to the plant budget. Ensure production and labor costs comply with approved budget
- Develop and implement methods of achieving plant goals within established parameters
- Monitor all operations to evaluate yields, efficiency, labor utilization, and product quality, and take corrective actions as necessary to ensure continuous improvement of processes and procedures
- Provide for the maintenance and repair of plant facilities and equipment
- Coordinate with outside vendor to ensure proper plant sanitation
- Advise VP Turkey Operations regarding fluctuations and other issues
- Ensure a safe work environment and that all safety hazards are properly addressed
- Enforce consistent, fair, and inclusive employment practices. Collaborate with Human Resources to administer company policies and procedures, address staffing needs, and resolve issues
- Ensure compliance with GMP, SOP, HACCP, USDA, EEO, OSHA and other applicable laws and standards
- Communicate and monitor specific performance expectations for supervision and team members
- Prepare and maintain a variety of data for production reporting and analysis
- Establish and maintain positive working relationships with other management personnel and USDA representatives. Work in collaboration with other internal departments, and provide outstanding customer service to internal and external customers
- Maintain current in-depth knowledge of trends and developments in the poultry industry
- Perform other related responsibilities, as needed, to support HPPC business objectives
- Bachelor’s Degree in Poultry Science or Business, or equivalent in experience
- Minimum of 7 years experience in the poultry industry, including at least 5 years in management, with a demonstrated track record of accomplishments
- Demonstrated ability to work well with and guide other people effectively, and to positively influence the attitude and performance of others
- Considerable attention to detail and uncompromised concern for quality and food safety
- Strong technical and analytical ability, including strong problem solving skills and solid judgment
- Strong mathematical and written and oral communications skills
- Well-organized and self directed
- HACCP Certified
- Bi-lingual English & Spanish preferredEEO/AA/M/F/Veteran/Disabled
138
Plant Manager Resume Examples & Samples
- Directs and oversees ongoing performance efficiency of all plant functions through the establishment and monitoring of various organizational goals that seek to meet and/or exceed corporate objectives
- Completes all assigned key corporate projects, initiatives and production targets with a high level of quality and accuracy and within approved budget parameters and timeframes
- Partners with Finance to develop ongoing worksite budget(s) within corporate guidelines inclusive of managing resources to control costs and optimize profitability to meet internal and external client expectations
- Provides support and guidance in the management of product quality and ensures compliance with quality and sanitation policies, procedures and systems to include HACCP, GMPs and the management and reduction of consumer complaints
- Continuously evaluates manufacturing capabilities and recommends future capital expenditures to accommodate future growth and/or expand current operations
- Leads development and execution of all safety initiatives inclusive of designing customized action plans for various Food Safety and Quality emergency scenarios
- Provides support and guidance in the management of employee performance development and ensures the timely deployment of up-to-date training materials
- Ensures all performance issues are addressed in a timely manner and all employees adhere to company policies and procedures on an ongoing basis
- Reports food safety and quality issues and initiate action, as necessary
- Follow all Food Safety guidelines, but not limited to
139
Plant Manager Resume Examples & Samples
- Lead and coordinate all plant functions and collaborate with all levels of the organization to ensure alignment of goals and progress towards them along with short term and long term needs and plans
- Guide and support the plant EH&S program in improvement, investigations and corrective actions to meet and exceed applicable law and IR standards
- Lead and support the deployment of Lean Manufacturing and Operational Excellence throughout all plant processes
- Coordinate the Financial reporting processes, such as Annual Operating Plan, business’ financial forecasts and response plans
- Foster and promote a diverse and inclusive work environment, high levels of morale, and high employee engagement; lead and support the development of plant employees and plant succession planning activities
140
Plant Manager Resume Examples & Samples
- 30%Leadership: coaching, performance management, engagement. Continue efforts to build high performing team; engage all employees; implementation of BU strategy; people development, champion recognition; collaborate effectively with experience teams and disciplines. Role Model and ensure compliance to laws, regulations and company policies
- 25%Operational Excellence: operations management including product quality; maintenance reliability & energy management; innovation, efficiencies & best practices
- 15%EHS Leadership: ensure compliance and commitment to policies, procedures, and regulations. Provide direction, coaching, support to BBS & Wellness
- 10%Customer Solutions & Innovation: Focus on continuous improvement and process management and cost efficiencies to support positive customer experiences
- 10%Project management, capital planning, P & L: business compliance; develop & meet budgets, develop capital spending requests & project management; aggressively & proactively manage operating expenses. Oversee and direct key projects and initiatives. Ensure capital projects are completed on time and within budget
- 5% Develop and implement a business plan that allows Newark to achieve targeted earnings, EHS, personnel, and sustainability objectives
- 4 year college degree with 5 or more years Plant Manager experience of a process production facility OR in lieu of degree a minimum of 10 years operations related experience in a plant environment, including 7 of those years in a supervisory role
- Travel on a limited basis (5% per year)
- Bending, Stooping, Walking, Lifting (50#), Finger Dexterity, Grasping, Pushing, Pulling
- Facility safety process leadership
- Capital project management
- Demonstrated effectiveness in coaching, motivating and developing high performing individuals and teams
- Demonstrated ability to effectively communicate and interact with all levels of the organization
- Demonstrated expertise in process management and project management
- Demonstrated Change Leadership; resiliency
- Visionary, forward-thinking
141
Plant Manager Resume Examples & Samples
- Knowledge and experience of the railcar repair industry, including FRA /AAR rules and regulations
- General railcar repair procedures and work practices
- Highly Motivated; Persistent / Dedicated
- Perform/ prioritize multiple tasks with attention to details
- Excellent ability to reason, make decisions and exercise / use independent judgment in various situations
- Ability to interpret and follow oral and written instructions including diagrams, blue prints and schematics
- Excellent written, verbal communication and listening skills
- Ability to maintain appropriate levels of confidentiality and sensitive information
- Strong interpersonal skills with the ability to work effectively with people at all levels of the organization
- Strong knowledge of standard Desktop Microsoft applications including: MS Windows, Office, Word and Outlook. Use database, spreadsheet, and word-processing software effectively
- Ability to effectively present information and respond to questions from groups of managers, clients, customers, and general public
- Ability to complete additional training or education as needed for this position
- Understanding of Quality Program
- Bachelor's degree in Business or related field with 5+ years management experience
- At least 5 years minimum experience required in railcar repair industry, including FRA /AAR rules and regulations or similar manufacturing environment with Lean Manufacturing and 5-S background
142
Plant Manager Resume Examples & Samples
- Education/Experience: Requires a bachelor's degree and 5-10 years of experience in the field or in a related area. Hands-on familiarity with the field's concepts, best practices, and procedures
- Language Ability: Ability to read english, analyze, and interpret general business periodicals, professional journals, technical procedures, or governmental regulations. Ability to write comprehensive reports in english, business correspondence, and procedure manuals. Ability to effectively present information in written or verbal format and respond to questions from groups of managers, clients, customers or vendors
- Math Ability: Ability to perform basic math and geometry
- Reasoning Ability: Ability to define problems, collect data, establish facts, and draw valid conclusions. Ability to interpret an extensive variety of technical instructions in mathematical or diagram form and deal with several abstract and concrete variables
- Computer Skills: Word processing, Powerpoint, Spreadsheets, Internet software, E-mail, Manufacturing software, Database software, applicable ERP modules (Oracle)
- Certificates and Licenses: N/A
- Leadership Responsibilities: Carry out leadership and supervisory responsibilities in accordance with the organization's policies and applicable laws. Responsibilities include interviewing, hiring, and training employees; planning, assigning, and directing work; appraising performance; rewarding and disciplining employees; addressing complaints and resolving problems. Fostering a culture having a strong awareness for improving safety and striving for zero accidents by 2020. Daily actions having a bias in support of meeting Customers’ needs
143
Plant Manager Resume Examples & Samples
- Directs all plant functions including manufacturing, technical services, accounting, supply chain, human resources, quality and operations excellence. Indirectly leads product and design engineering and the plant flex center
- Fully deploys the APEX process and administers compensation and rewards and recognition plans. Develops employees through training and motivation. Assures subordinates are constantly improving their knowledge of manufacturing processes and in functional competencies
- Develops annual objectives for the plant and reviews with staff managers, employees and division personnel periodically
- Develops plant budgets and forecasts and assures timely implementation and control. Develops strategic plans for the facility, short term and long term
- Oversees maintenance of all plant facilities and layouts to minimize downtime
- Works with both development engineering and marketing in new product designs, coordinating customer requirements with manufacturing cost and feasibility
- Assures prompt and accurate reporting systems on all aspects of plant operations including inventory, labor, and production, shipping and receiving to monitor performance against plant objectives
- Participates in union contract negotiations and assures adherence to contractual obligations, maintaining good relations with the union representatives
- Directs the staffing, organizations and development of plant's personnel requirements
- Directs plant safety program (MESH) to minimize accident or injury occurrence and to meet all OSHA standards and EPA regulations
- Communicates information to employees on the state of the company, and leads the communications efforts of the facility
- Represents the company in community and professional activities
- Maintains an environment in keeping with all applicable regulations and legal requirements
- A bachelor's degree from an accredited university is required
- Ten years of management experience in a manufacturing environment is required
- The ability to work in the United States without sponsorship is required
- Proven ability and successful track record of growing sales, profits, leading operations, and delivering quantitative & qualitative results
- Strong and thorough understanding of the electrical industry and the competitive landscape to include an in-depth knowledge of market segmentation and market channel differences
- EBS experience or experience with the execution of similar business system
- Demonstrated experience in creating, developing and executing short and long-term strategic plans and effective implementation across cross functional & electrical businesses
- Demonstrated ability to build, communicate and execute a vision for strategic and operational change and will also possess excellent interpersonal and communication/presentation skills
- Ability to lead business initiatives to drive growth and profitability in a fast growing business
- Accomplished in meeting and exceeding the expectations and requirements of internal and external customers
- Strong understanding of markets, segments, and channel relationships
- Can get others on board and is engaged and committed to objectives; can overcome resistance
- Product and operations management experience. Product launch and product engineering experience is a plus
- Expertise in budget management and driving year over year improvement of financial metrics
144
Plant Manager Resume Examples & Samples
- Review job standards, develop cost studies, and systems for optimum efficiency
- Analyze and react to job and plant efficiency and cost comparison reports
- Review labor and material requirements to minimize overtime costs without jeopardizing necessary functions and customer delivery requirements
- Adapts departmental plans and priorities to address resource and operational challenges
- Drive continuous improvements to achieve maximum customer satisfaction levels and strategic business direction
- Actively lead (through training and mentoring) and execute LEAN and variation reduction activities and principles
- Must be able to work closely with all parts of the business including Customer Service, Quality/Material Functions, PD & E, and Compliance to ensure the strategy, development and execution of standards and cost containment are achieved across Plant Operations
- Direct problem solving activities in the manufacturing operations, forcing those activities to the lowest level for irreversible resolution
- Monitor production schedules for maximum labor utilization and to minimize inventory costs
- Ensure that all manufacturing, policies, procedures, and practices demonstrate compliance to regulations/policies
- Establish and manage budgets and targets for assigned area of responsibility
- Ensures, monitors and reports progress on projects, process changes, capital expenditures, barrier elimination and new technology development
145
Plant Manager Resume Examples & Samples
- Lead, manage, inspire and motivate the MEDC management team according to the Eaton Leadership Model requirements and in line with the applicable HR policies
- Carry out profit planning for the plant and ensure that the objectives for the site are met within approved budget, schedules and quality specifications. Support, develop and execute strategic capital spending plans for the local operation to assure adequate capacity to meet division and product line growth objectives
- Manage the financial performance of the business to achieve targeted EBT and growth
- Deploy the Eaton Business System in line with the agreed integration agenda. Utilise in house, HAC and Crouse Hinds personnel to develop appropriate plans and deploy lean tools throughout the plant to deliver Cost Productivity as target. Ensure an effective integration of all operational focused functions to deliver effective processes to achieve customer satisfaction
- Represent the plant to third (external) parties by having regular close contact to local and regional communities and ensure that environmental, health and safety regulations are both in compliance with applicable law and regulations and the company’s systems (EQS, MESH, Quality Management according to ISO9000 series and ISO14000 series)
- Ensure that Operational processes are in line with applicable national, divisional and corporate guidelines, procedures, law and regulations and have these actively audited and monitored by means of available systems
- Ensure clear communication of operational objectives and results to all MEDC employees. Create a high performance work culture through deployment of the Apex process across the business. Drive a culture change and improvement and build organisational capability to achieve goals
- Develop appropriate, accurate and timely measures to assess all aspects of plant and departmental performance. Implement processes to review these metrics at regular frequency and take appropriate action to ensure that SQDC and are metrics are achieved
- Ensure correct processes are implemented and maintained to ensure products manufactured are compliant with relevant certifications at all times
- Overall responsibility for functional safety policy and functional safety culture within MEDC site (SIL)
- Degree in Manufacturing Engineering/ Industrial Engineering
- Operations Management
- Financial accounting, planning and reporting
- Operational Excellence
- Lean Manufacturing, Six Sigma, Project Management, ISO 9000 and 14000 series
- English language
- Procedures, company rules, guidelines (national and international), law, rules & regulations, standards, safety, quality and environmental guidelines as far as applicable
146
Plant Manager Resume Examples & Samples
- Emergency Response incident command and communications - The Plant Manager will have primary responsibility for the safety of site personnel, the surrounding community, and for communication to emergency services and Linde support personnel
- Responsible for preparedness of On Alert team and must foster an environment of collaboration between Linde and community emergency services
- Responsible for overall Site Security and compliance with Department of Homeland Security regulations. As such, the Plant Manager must have an understanding of basic security principles and technologies, must be able to develop a security approach which meets the intent of the regulations, and ensure site compliance to related policies and procedures. Periodic updates and maintenance of security systems and procedures are expected
- Primary interface for third party oversight and regulatory entities, including but not limited to 1) local fire department and hazardous material response, 2) local law enforcement, 3) state and federal EPA, 4) State and Federal OSHA, 5) local Emergency Planning Commissions, 6) municipal water and sewer authorities, 7) local Industrial Park committees, 8) related industry associations
- Must lead and participate in local safety programs and initiatives. The plant manager ensures and participates with the Site Safety Committee. The plant manager ensures completion of regularly scheduled site safety meetings. The plant manager ensures regular completion and reporting of RBU SHEQ leading and lagging indicators (e.g. Lead Safe, Good catches, Housekeeping, etc.)
- Primarily responsible for the proper and timely handling and reporting of site incidents and near misses. The Plant Manager must manage personnel incidents and ensure proper care of injured or potentially injured employees. Every incident and near miss must be reported and evaluated per Linde guidelines. Root cause analysis, corrective and preventive actions, and communications are the minimum expectations for each occurrence. The Communication expectation for all Lost Time Incidents includes detailed analysis and presentation to RBU SHEQ and RBU Head of Operations
- Recruit plant employees that represent and maintain Linde’s Core Values and Vision
- Ensure implementation of a rigorous hiring mechanism which properly identifies and maximizes relevant core competencies
- Develop personnel to maximize productivity through challenging work environment and task diversity, while leveraging internal and external training resources
- Foster a cooperative, team environment, conducive to diverse backgrounds, opposing viewpoints, and open exchange of ideas
- Routinely and rigorously evaluate staff, providing timely and constructive feedback, with objective of continuous employee development
- Consistently and swiftly address behavioral and performance issues
- Responsible for evaluating existing resources and procuring assets to support new business, including plant equipment, cylinders, valves, and consumables
- Ensure timely and efficient supply of raw materials
- Develop inventory targets and ensure a purchasing mechanism to meet inventory targets. Inventory levels must be maintained to limit costs and ensure reliable and consistent supply
- Develop and ensure appropriate production planning to achieve short and long term production demands
- Schedule labor and overtime in line with plant capacity and customer demand
- Interface with logistics and planning personnel to establish and maintain proper stock levels at Linde and customer locations
- Create strong functional relationships with domestic and international shipping departments, develop expertise regarding domestic and international shipping regulations, and comply with all relevant shipping regulations and procedures
- Visibly lead and demonstrate a commitment to quality and continuous improvement
- Continually to strive to meet customer expectations and promptly take action to correct discrepancies; effectlvely prevent recurrence
- Foster a culture of continuous improvement at all levels of the organization through effective corrective and preventive actions for nonconformities
- An agent for change to strive for continuous quality, process, and system improvements through the facility utilizing tools including six sigma and lean
- Responsible to develop a yearly budget, periodically review against established standards, and report variances to Operations Management
- Must ensure timely and accurate processing of invoices to vendors and contractors
- Communicate site and division performance to local personnel
- Represent the voice of executive management and their vision for success and long term performance
- Manage the local engineering team to execute plant engineering projects meeting cost, schedule, and scope commitments
- Bachelor Degree - Engineering
- Minimum of 5 years in Operations
- Previous plant management experience is preferred
- Demonstrated commitment to SHEQ policies and principles
- Strong record of building and developing high performance teams
- Experience controlling and monitoring plant operating budgets and P&L management experience
- Quality management experience in an environment with a focus on process control and continuous improvement, preferably in the ISO or TS framework
- Computer literate including MS Word, Excel, PowerPoint, Access
- Basic working knowledge or ability to learn SAP
- Time and task management expertise
147
Plant Manager Resume Examples & Samples
- Responsible for Make products beyond just medical O2 (ex. Med N2, N2O, UE)
- Managing of multiple shift operations
- Oversee high level of SAP transactions (typically a multiplier of 5 compared to small plants (DWD)
- Typically an importer of 3rd party products and re-distribute throughout the regions
- May contain oversight of valve refurbishment operations
- Manages the day-to-day operational and financial operations of a CSCM Plant/Center
- Responsible for Center P/L (shared P&L responsibility between Healthcare and Supply Chain)
- Ensures all production is performed according to Good Manufacturing Practices (GMPs) as defined by Linde procedures
- Analyzes Center current financial and operational strengths, weaknesses, opportunities, and constraints in order to develop, prepare, and implement goals, projects, and policies that will enable the Center to achieve a competitive advantage in the market
- Forecasts future trends , needs and develops action plans which will enable the Center to meet the predicted situation
- Coordinates with sales on a regular basis with existing and new business to effectively support the growth strategy of the company, according to an agreed-upon product service offering
- Maintains strong customer service focus for all Center employees; develops and monitors distribution schedules to ensure customers are served in a timely manner
- Stay close to customer by maintaining and developing relationships with customers
- Responsible for representing company by ensuring employees and Center meet standards established by organization and cleanliness
- Develops profit plan for Center using strong P&L knowledge including actions required to meet cost and efficiency targets
- Facilitates communication within the Center by communicating with staff members keeping them informed of initiatives, strategies, and operational change
- Actively listens to staff input concerning daily operations to ensure staff members are aware of situations that may affect their work
- Responsible for building his/her team and developing our bench strength operationally
- Manage distribution personnel to ensure compliance with DOT and CSA program, ensuring all drivers are compliant with Linde, local, state and federal regulations
- Ensures all policies and procedures are adhered to
- Bachelor’s Degree required or equivalent 5 years direct experience
- Minimum of 3 years’ supervisory experience
- Minimum of 5 years’ related Operations/plant management experience in medical related preferred
- A working knowledge of US FDA requirements for medical gas manufacturing
- Operations/production/distribution management experience
- Ability to prioritize and manage in a crisis
- Creative problem solving abilities required
- Ability to coach employees to achieve results
- Excellent computer skills with experience in MS Office Tools and SAP preferred
148
Plant Manager Resume Examples & Samples
- Manage assigned operations associates
- Supervise branch administrative procedures
- Assist in the hiring of new operations associates to replace existing positions when necessary
- Provide training, motivation, leadership, support to operations associates
- Ensure that state and federal regulatory requirements (DOT, EPA, OSHA, DHS) and Airgas procedure manuals are understood and fully implemented with the assistance of Regulatory Affairs Department
- Work in conjunction with the Regulatory Affairs Department to perform hazard assessments of both the workplace and the rolling stock. Documentation and corrective actions based on findings will be required
- Coordinate business development with regional operations managers to ensure timely service of new business
- Develop and implement territory operations strategy to assist in generating business growth and increase financial results; experience with P&L statements
- Oversee distribution function within regional area
- Develop elective training for respective personnel; present both mandatory and elective monthly safety meetings
- Maintain adequate HR records and documentation. Corrective action plans taken under the Division Director of Human Resources guidance
- Assist sales support people within assigned regional areas
- Assist customers of assigned account representatives when direct contact to customer is not available
- Assist account representatives with acquiring new business while establishing rapport with existing key accounts
- Bachelor’s Degree preferred, but not required
- In lieu of degree, a minimum of 5 years experience in the chemical industry, preferably in a processing plant environment is required
- Strong aptitude for and understanding of basic business and financial principles
- Average or above interpersonal and communication skills, both verbal and written
- A self starter, detail orientated, possess an end to end supply chain mindset, and works well with a team
- Ability to analyze processes, organize data, draw conclusions based on facts, and provide implementation leadership
- Product knowledge, technical knowledge
- Handling and safety of ASP products a plus
- Knowledgeable in the regulations governing the hazardous chemical industry
149
Plant Manager Resume Examples & Samples
- Bachelor Degree preferred , High School Diploma/GED required
- 7+ years experience in an industrial plant environment preferred
- 7+ years Operations/Distribution/Quality experience required
150
Plant Manager Resume Examples & Samples
- Oversees plant quality and manufacturing processes to ensure compliance of ISO 9001:2016 standards and company policy
- Minimum of 5 years working with large , highly outfitted complex steel products with many steps in the manufacturing process
- Experience with complex to moderate project management in a steel fabrication environment
- Has led complex to moderate operations with products on multiple manufacturing lines including outfitting, setting, testing and coating
151
Plant Manager Resume Examples & Samples
- Confers with customers and employees to evaluate and promote improved operations and services within the plant and its service area
- Participates in the training of many employees within the plant
- Maintains outstanding and positive working relationships with any branch location(s) being serviced by the plant
- Participates in the appropriate and fair resolution of human resources issues when necessary
- Aggressively seeks and retains highly qualified and productive candidates for available positions through aggressive recruitment and retention activities
- Coordinates production and distribution in accordance with policies, principles, procedures established by our company
- Develops plans for efficient use of materials, machines, and employees
- Reviews production costs and product quality, and modifies production and inventory control programs to maintain and enhance profitable operation of the plant
- Ensures correct and safe operation of plant equipment
- Reviews and analyzes production, quality control, maintenance, and operational reports to determine causes of nonconformity with product specifications, and operating or production problems
- Develops and implements process improvements and streamlined procedures
- Leads all receiving, production and distribution activities to new performance levels
- Challenge yourself to achieve and exceed goals, and open up new career challenges
- 3-5 years' plant, operations and logistics management experience including TQM and process improvement
- Minimum 1-2 years of experience in human resources and related fields
- Bilingualism in French and English
- Familiarity with P&L analysis, performance measuring tools, operations innovations
- Bachelor's degree in Business Management or Equivalent
- Availability for relocation for career advancement
- Strong language and communication skills; including the ability to read and interpret documents such as safety rules and regulations, maintenance instructions and procedure manuals. Must have the ability to write routine reports and speak effectively in both French and English
- Mathematical skills; including the ability to add, subtract, multiply and divide. Able to compute rates, ratios and percents along with applying concepts to Profit and Loss (P&L) analysis. Demonstrated skills in planning, data analysis, problem-solving, workflow methodology and budgeting
- Reasoning ability; including the ability to apply common sense understanding to carry out instructions and deal with problems involving several variables in standardized situations
- Ability to Multitask; manage multiple priorities against tight deadlines in an industrial environment, while maintaining positive relationships with employees and customers at all levels
152
Plant Manager Resume Examples & Samples
- Safety and Environmental Compliance
- Customer Quality and Internal Scrap Reduction
- Delivery and Capacity Planning/On Time to Customer Request (OTTR)
- Cost reduction programs and productivity improvements, and the implementation of initiatives to align with ISC business goals
- Developing short and long range 'Best in Class' / 'World Class' vision, mission, site value proposition and supporting plans to maximize the utilization of all site assets and assure availability of resources in accordance with the changing business environment
- Ensure a safe work environment for all employees. Implement Honeywell HSE processes, policies, and metrics. Working with Corporate HSE and site HSE direct report(s): establish, manage and monitor standards, processes, communications, training and systems as they relate to Environmental and Safety
- Recruit, develop, support, and evaluate staff to manage roles and responsibilities for the achievement of results
- Provide for the personal and professional development of the entire organization to meet current and future challenges of the business
- Drive continuous improvement through deployment of Honeywell Operating System (HOS)
- Provide vision, direction, and leadership for the formulation and implementation of Customer Quality and site process improvements, employing Lean and Six Sigma tools
- Develop and deliver on the Annual Operating Plan (AOP) including financial and operational targets
- Ensure appropriate communications with both the Integrated Supply Chain (ISC) organization and the HSP business unit, to coordinate strategy, goals and actions necessary to achieve them
- Initiate and coordinate development activities in response to emerging business needs, interfacing with Product Development, Marketing, and Sales for alignment
- Establish and maintain relationships with community leaders, City, State and Federal agencies to address common industry-related issues and ensure regulatory compliance
- 5 years of progressive manufacturing management experience
- 5 years of experience in Total Quality, Six Sigma or Lean
- BS in Engineering or Operations Management
- 2 years of experience as a Plant Manager, with Manufacturing Site Leadership background
- Six Sigma Green or Black belt
- Six Sigma and DMAIC methodology
- Lean certification
- Demonstrated ability to lead cultural change and establish operational metrics/key indicators for process control, communication and performance improvement
- Demonstrated high quality of decision making
- Strong problem solver with the ability to 'learn on the fly'
- Clearly demonstrated ability to deal with ambiguity
- Strong at setting priorities and making timely decisions
- Strong time management and organizational skill set
- Has demonstrated the ability to size up people and successfully hires and recruits the best talent
- Action oriented with the ability to stand alone and yet operate successfully in a matrix organizational structure
- Demonstrated capability in change management and realigning of site culture as appropriate
- High approachability factor, strong builder of effective teams, and a strong motivator of others
- Open and receptive to discourse which occurs in a matrix environment
- Strong believer in personal learning and self-development and has a strong sense of 'self-knowledge'
153
Plant Manager Resume Examples & Samples
- Ensure Company assets and physical plant are secure and well maintained
- Achieve desired results in Safety and Quality through personal commitment and focus, and compliance with plant and corporate best practices and policies
- Ensure facility is in compliance with all appropriate environmental regulations and permitting requirements
- Responsible for production operations including Safety, Quality, Waste, Productivity, Maintenance, Planning and Shipping at assigned plant(s)
- Strive to provide world-class customer service via competitive lead times and maximum flexibility and response
- Manage facility's operations from a capacity planning/asset utilization standpoint
- Build effective partnerships with plant leadership and staff functions to drive expected results
- Control manufacturing and conversion costs within budgetary limits
- Aggressively monitor and manage slow moving finished goods inventory and roll stock
- Participate in weekly cost control meetings and create forecasts that closely mirror actual results by the end of the month
- Monitor variable operating expense to obtain msf objective as it pertains to production. Make adjustments to ensure staffing levels and other expenses such as utilities, etc. are on target
- Plan and prepare for capital expenditures in coordination with Controller, General Manager and appropriate corporate resources
- Lead an integrated talent management process for the department. Assess and develop competencies of management team
- Coach and develop supervisors and professionals to maximize their effectiveness as well as their teams' effectiveness. Identify and develop high potential employees for levels of greater responsibility and scope
- Recruit talent that will address needs of the facility and fill technical and competency gaps within organization
- Ensure performance feedback and appraisals are completed effectively and on a timely basis. Reward and recognize employees with a pay for performance approach
- Hold people accountable for performance; work with under-performers on training assistance, or put them in documented performance improvement plans and/or disciplinary programs as necessary
- Supervises subordinate employees. Carries out supervisory responsibilities in accordance with the organization's policies and applicable laws. Responsibilities include training employees; planning, assigning, and directing work; appraising performance; addressing complaints and resolving problems
- Develops objectives and general policies and procedures for a specific program or functional area of responsibility within general scope of established operational goals and plans. Day-to-day work and decisions do not require direction or review by immediate supervisor. End results are reviewed by supervisor. Strategic issues are referred to supervisor
- Develops strategic direction, goals, plans and policies for an area of responsibility. Sets broad objectives and is accountable for overall results in respective area of responsibility. Authority to make independent decisions on matters of significance. Requires high degree of independent judgment and problem solving of complex problems
- Performs duties within scope of general policies, procedures and objectives. Analyzes problems and performs needs assessments. Uses judgment in adapting broad guidelines to achieve desired result. Regularly exercises independent judgment within accepted practices. Makes recommendations that affect policies, procedures and practices. Refers exceptions to policy and procedures to the supervisor
- Minimum of 10 years of progressively more responsible operations leadership experience within a manufacturing company
- Led an operational department or function at a manufacturing site or significant operation within the facility
- Previous experience managing a group of employees or project team
- Possess a strong safety, operations and business background
- Have financial and process acumen, be results-driven and possess strong communications skills
- Will have proven management experience with a previous background in corrugated, paper or similar manufacturing environments
154
Plant Manager Resume Examples & Samples
- Consults with engineering personnel relative to modification of machine and
- Bachelor's Degree in engineering or related discipline required; Master's Degree preferred
- Minimum 10 years working in a manufacturing environment required; 5+ years of experience in plant leadership required
- Experience with environmental compliance required
- Knowledge of health and safety standards
- Experience working with poly/plastics or injection molding preferred
155
Plant Manager Resume Examples & Samples
- Leadership of a Seed Production and Processing activity in line with Syngenta culture and P&S strategy
- Manage the fixed, variable and capital cost performance for both plant and field in line with agreed budgets and targets
- Ensure full compliance against all Syngenta standards and local legislation. Ensure all HSE, Quality, Legal and fiscal standards are continuously improved and monitored, that risks are con-trolled and minimized, complaints are investigated and improvement actions implemented
- Develop and sustain a strong grower supplier base to enable seed sourcing and procurement requirements of annual crop plan to be met
- Ensure high levels of customer service and responsiveness in line with Syngenta strategy for all products supplied to all markets
- Identify, motivate and coach key resources to drive and deliver improvement projects, product establishments or performance improvement initiatives
- Bachelor’s Degree (Agronomic or Engineering discipline preferred)
- 5 years experience with seed production, processing, logistics and vendors
- Experience in logistic
- Advanced computer literacy - data management systems and office programs
- Working knowledge of SAP, MS Office programs strongly preferred
- High level of experience in all aspects of vegetable production
- High level of experience managing people and teams both directly and indirectly
156
Plant Manager Resume Examples & Samples
- Bachelor’s degree; or equivalent of ten years of progressive related experience and/or training; or equivalent combination of education and experience in a manufacturing environment
- Experience in planning, negotiating and organizational skills
- Strong leadership skills while maintaining a team atmosphere
157
Plant Manager Resume Examples & Samples
- Manage overall plant operations including manufacturing, quality, safety, planning and scheduling, manufacturing engineering, supply chain, and logistics
- Ensure optimal utilization and cost-effectiveness of equipment and personnel
- Partner with sales, engineering, and other personnel within and across the business to understand and satisfy customer and business needs
- Establish KPI’s and controls that allow for meaningful analysis of and response to performance and results
- Maintain overall financial responsibilities for the plant including budgets, financial projections, and capital expenditures
- Manage, mentor, and develop strong, talented team members and direct reports
158
Plant Manager Resume Examples & Samples
- Will manage production, shipping & receiving, and scheduling
- Approx. (90) Associates at the Plant
- 3 shift operation
- Will report to the VP Operations
- Seeking an excellent transformational leader
- Lead team from the floor
- Degree requiredMore Information
159
Plant Manager Resume Examples & Samples
- Plan, organize, and direct the day-to-day operations of the manufacturing plant
- Allocate resources effectively and fully utilize assets to align with Lydall’s lean manufacturing strategy
- Develop and/or enhance process tracking mechanisms to ensure performance targets are being met
- Responsible for production, product quality and on-time shipping
- Actively support and participate in Kaizen events that improve operations and employee knowledge of Lean manufacturing
- Promote safety and environmental compliance through active participation and support of company safety policies and programs
- Support and align with Strategic Plans set forth by Director of Operations
- Maintains standards for TS 16949 and ISO 14001 certifications
- Actively work to recruit qualified employees
- Use effective strategies to lower turnover and retain quality employees
- Effective coaching and development of direct reports and entire shop floor team
- Promote harmony in the workplace through open communication and fairness to all employees
- Ensure compliance with all company policies including HR policy manual, Quality, Safety, and Environmental policies
- Maintain cross functional dialog with Directors of Engineering, Quality, R&D, and Purchasing with issues and concerns related to manufacturing, design, launch and vendor management
160
Plant Manager Resume Examples & Samples
- Foster a safe, collaborative high-performance culture, and support Brewster’s use of values streams and MDI (Managing Daily Improvement) management and operating practices. Facilitate weekly Leadership Team meeting
- Lead production planning and production control
- Manage, coach and develop the team; assist in developing talent within the plant and across Materion
- Effectively analyze and plan for the most efficient staffing levels : hiring, training, performance management, rewards and recognition, employee engagement, discipline, and addressing complaints / resolving conflict
- Lead continuous improvement efforts using Six Sigma and LEAN operating principles. Drive the Toyota Production System (TPS) / KATA and minimize all types of waste
- Work closely with the plant team to enable and coordinate efficient scheduling and operations (cost, quality and service) based on sales requirements and plant capacity
- Ensure effective implementation of security and safety policies, procedures and guidelines; zero tolerance model
- Implement additional safety programs and employee committees
- Administer and direct plant policies consistent with organizational and regulatory requirements
- Support all functional areas, including: Quality/R&D, EH&S, Security, Sales, HR and Accounting
- With the V. P. Operations, develop plans for expansion, conversions and equipment planning and ensure maintenance of buildings and equipment
- Collaborate and participate in AMG’s yearly annual operating plan and budgeting process
- Support satellite operations as required
- Bachelors of Science degree
- Minimum of 5 years of related experience in manufacturing or comparable equivalent experience, with extensive experience in safety, engineering and environmental science
- 3+ years in management assignments, with demonstrated career progression
- Experience with Statistical Process Control (SPC) required
- Green Belt and/or Black Belt certification preferred. 5S, Kaizen, and VSM knowledge preferred
- Willing to relocate for career growth
- Position involves travel up to 15% to domestic locations
161
Plant Manager Resume Examples & Samples
- Identifies and implements optimal business processes and organizational structure for plant
- Implements, improves and maintains manufacturing policies & procedures, materials usage, shipping & receiving, capacity planning, production scheduling, safety, customer satisfaction, and Key Performance Indicators
- Identifies, recommends and implements strategic changes in manufacturing and operations
- Builds, develops and manages a capable operations leadership team
- Provides individual team members with aggressive and clear performance objectives
- Leads by example with a passion for customer service
- Champions initiatives to institutionalize Safety, Quality, Lean Manufacturing, Team Development and
- Bachelor’s degree and/or at least five years’ experience as a plant or operations manager in a manufacturing environment
- Minimum 5-7 years’ printing experience
- Demonstrated track record of manufacturing management excellence, evidenced by a track record of achieving production, quality and cost objectives while maintaining a safe and positive environment for line manufacturing employees
- Superior communication, interpersonal, and presentation skills evidencing the ability to effectively communicate with subordinates, superiors, peers, customers, etc
- Strong planning and budgeting skills
- Superior leadership and managerial skills indicative of the ability to instill teamwork, delegate effectively, and build collaborative relationships to facilitate the accomplishment of business objectives
- Strong organizational skills and a superior attention to detail
- Must be able to manage multiple priorities and objectives
- A proactive management style evidencing the ability to anticipate and resolve potential issues before they become significant problems
- Creativity and innovation indicative of an ability to identify new approaches, processes and systems to business operations and issues
- Strong personal computer skills including proficiency with Excel, Word, and PowerPoint, specific experience with PECAS manufacturing and financial systems would be a plus
- Must be able to perform all essential functions of this job with or without reasonable accommodations
162
Plant Manager Resume Examples & Samples
- Develops manufacturing organizational strategies by contributing manufacturing information, analysis, and recommendations to strategic thinking and direction; establishing functional objectives in line with organizational objectives
- Develops manufacturing financial strategies by estimating, forecasting, and anticipating manufacturing requirements, trends, and variances; aligning monetary resources; developing action plans; measuring and analyzing results; initiating corrective actions; minimizing the impact of variances
- Establishes manufacturing operational strategies by evaluating manufacturing trends; establishing critical measurements; determining production, productivity, quality, and customer-service strategies; designing manufacturing systems; accumulating resources; resolving problems; implementing change
- Improves quality results by studying, evaluating, and re-designing processes; implementing changes
- Maximizes equipment operation by developing and scheduling preventive maintenance; organizing change-overs
- Updates job knowledge by participating in educational opportunities; reading professional publications; maintaining personal networks; participating in professional organizations
- Focuses entire plant on quality, service, safety and cost as a top priority
- Ability to interact with the public and other employees in a positive manner and promote a cooperative working environment
- Consistently sets the example of professional appearance and standards of behavior
- Able to form and maintain effective partnerships across organizational boundaries
- Excellent oral and written communications skills in English
- Ability to handle sensitive information and maintain confidentiality
- Coordinates several projects at the same time while prioritizing competing demands on time frames
- Ability to synthesize complex or diverse information
- Ability to plan, monitor and appraise performance of location staff members
- Ability to listen objectively to employee concerns and complaints and act, or plan a recommended course of action, in accordance with all Company policies. Seeks counsel from Corporate Human Resources as required
- Responsible for compliance with Federal and State legislation pertaining to all operational matters
- Typically negotiates in a competitive or adversarial environment
- Ability to attend various meetings as requested with minimal advanced notice
- Bachelor Degree in business, supply chain management, logistics, engineering, food science or appropriate equivalent from an accredited university
- Seven to ten years of beverage plant management experience
- Strong knowledge of Production Scheduling and Inventory Control
- Strong project management, business writing and reporting skills
- Must be 18 years or older
- Ability and willingness to work a flexible Full Time schedule that may include weekends and holidays
163
Plant Manager Resume Examples & Samples
- Establish a top tier safety environment, including a behavioral based safety culture
- Foster a model environment based on the Newpark Core values of Integrity, Respect, Excellence, and Accountability
- Make this a best in class LEAN facility by deployment of appropriate LEAN and Six Sigma tools to achieve top tier SQDCI results throughout the Value Stream (from customer to supplier)
- Owns the P&L and balance sheets for the facility
- Develop and implement growth plans by actively promoting the facility to current and new customers to garner additional and profitable business for Newpark
- Develop a Distribution Center of Excellence for Newpark, and actively work with the Supply Chain organization and other stakeholders to deploy appropriate best practices at other warehouses globally
- Manage the timely and seamless introduction of new products into the facility
- Engineering Degree (Chemical Engineering highly preferred)
- 8 Years in Manufacturing/ Supply Chain/ Operations
- 5 Years in Chemical Toll Blending and Reacting
- 3 Years in a people leadership role
164
Plant Manager Resume Examples & Samples
- Creates production schedule and directs production activities to meet sales objectives at maximum efficiency and minimum cost
- Ensures order fulfillment at CRD (Customer Request Date- on time delivery) objective level
- Plans and coordinates work, trains and motivates team members, monitors and evaluates performance of team; counsels, documents actions and disciplines as appropriate
- Ensures communication, training and running operations is in compliance with local, state and federal laws and EHS standards
- Reviews production costs and product quality, and modifies production and inventory control programs to maintain and enhance profitable operation of plant
- Supports Continues Improvement by identifying and addressing any opportunities to reduce cost, improve product/process and/or improve overall operations
- Supports ERP integration into daily business functions of operations
- Assumes ultimate responsibility for the quality of products produced and shipped to Customers
- Management and leadership of production standards, metrics and efficiencies
- Responsible for hiring, staffing and retaining an engaged workforce
- Blends strategic vision with tactical execution across the organization
- Keen sense and ability to perpetuate and sustain a Customer 1st/Performance environment down to the lowest levels in the organization. Embeds these attributes as part of the culture and as “a way of doing business.”
- Successfully manages talent using key metrics, formal assessments and integrated calibrations to develop and execute a talent strategy which aligns to the organizations strategic growth plans
- Is decisive when pressed with critical business and talent decisions. Levels the appropriate analytics with the need to act and execute key decisions
- Rich and deep experiences in developing relations with key stakeholders to optimize financials, productivity, quality and Customer 1st Understands the key business drivers of our business and customers and builds trust and credibility from within the organization to deliver through consistently exceeding our metrics
165
Plant Manager Resume Examples & Samples
- Ensure manufacturing plans that align with overall company Objectives and Goals
- Develop a leadership team to create a pipeline of talent in the organization
- Execute the Continuous Improvement Playbook to improve across all metrics on People, Safety, Quality, Service, Sustainability and Costs
- Safety
- Minimum of six (6) years of Manufacturing Operations Leadership experience in a complex, fast paced manufacturing environment, required
- Management experience in a food manufacturing environment or food products industry, including familiarity with SQF Systems, preferred
- Experience with statistical analysis and practical application of Statistical Process Control (SPC) on the shop floor, required
- Experience leading continuous improvement processes in a manufacturing environment
- Experience driving business results in the areas of Employee Safety, Product Quality & Safety, Environmental Compliance, Customer Service and Cost
- Experience developing and executing against operating budgets and capital plans, within a manufacturing environment
- Experience leading the development and successful implementation of complex projects in a manufacturing environment
- Experience leading and working with a diverse group of people
- Good understanding of MRP and production planning process
- This position provides direct supervision to plant operations management, as well as direct or indirect supervision to plant support department management
166
Plant Manager Resume Examples & Samples
- Forecast and deliver performance; manage day-to-day activities to achieve targets and improve Safety, Quality, Delivery and Cost (SQDC) goals in a fast paced – high volume / low mix manufacturing environment (Execution)
- Develop and manage the team, including talent development, performance management, and labor management (Organization)
- Develop and implement the long-term operations strategy to create sustainable SQDC improvements which benefit stakeholders and customers (Improvement Strategy)
- Collaborate with the commercial leadership to align strategic initiatives including new product development, PLCM, and OpEx
- Align to PT Operations function initiatives for SQDC improvement
- Share best practices to support global product needs with other Coupling sites
- Bachelors Degree in Industrial or Mechanical Engineering, Business Management, Supply Chain Management or related degree
- 10+ years experience Managing in a manufacturing / lean environment (Injection molding, plastic extrusion and assembly)
- Commitment to continuous improvement culture – stretch, fact-based questioning
- Set and execute business strategy through a strategy deployment process
167
Plant Manager Resume Examples & Samples
- Provides leadership in the management and administration of the processing division to ensure the most efficient and highest quality production
- Provides consultation and direction necessary to enable departments to meet their operational objectives
- Helps develop and carry out strategic plans and programs in processing to produce the most profitable product mix and stable sales program
- Supervises and directs the programs and activities of plant department heads
- Develops, coordinates and follows through on strategic operational plans
- Works with Division Manager in assessing and action planning organization design in maintaining the most efficient and effective organization arrangement
- Selects and terminates department managers and other immediate subordinates
- Reviews on a daily basis reports on yield, grade, inventory and other cost reports to ensure awareness of any deviation from the norm and to spot trends and make necessary adjustments
- Reviews, evaluates and approves departmental budgets to insure their compatibility with division goals and objectives
- Implements corrective actions for substandard performance in each department
- Provides Division Manager with reports and information as necessary or required that will enable a critical review of the processing operations and to provide constructive advice for improvement
- Formulates and oversees development of short and long term strategic plans for the processing division
- Clarifies and works toward explicit understanding of Sanderson Farms’ policies and procedures
- Reviews and evaluates weekly & monthly reports
- Participates with Sales Manager in scheduling customer visits for prospective customers
- Establishes and maintains an effective employee relations climate as well as safety consciousness
- Maintains high level awareness of trends in the poultry industry
- Actively pursues acquisition of information and/or skills related to the management of processing division and related services
- Represents Sanderson Farms in industry groups, governmental bodies as well as community groups
- Maintains current awareness of governmental regulations as well as possible new legislation affecting the poultry industry
168
Plant Manager Resume Examples & Samples
- Establish cost savings and goals involving staff, vendors and customers to achieve the lowest possible manufacturing costs
- Develop and implement effective supply chain management programs linking procurement, processing, packaging, and distribution into a seamless process and insuring that adequate programs are in place in all disciplines to ensure maximum efficiency
- Establish and maintain effective working relationships with all business functions internal and external to the plant. Efficiently utilize all equipment, raw material, packaging materials and staff to insure the lowest possible cost
- Establish plant quality programs that insure the compliance with all federal, state, local and customer requirements. Insures that in line quality controls are established to detect and correct quality failures and reduce out of specification product. Insure that adequate reporting is in place to facilitate continuous improvement programs and provide efficient tractability and recall requirements
- Insure that all Health and Safety programs comply with state and federal regulations. Conduct monthly progress and training meetings. Insure that all accident reports and records are timely and in compliance
- Insure compliance with all company GMP’s, local, state, and federal regulatory agencies; organic certifying organizations and, Kosher organization and third party certifying agencies
- Work with current and existing customers to develop an environment of mutual trust and understanding establishing SunOpta Ingredients as the supplier of choice for manufacturing and packaging
- Coordinate all plant purchasing activities establishing and delegating accountabilities and signing authority as may be appropriate
- Work closely with the Maintenance Manager developing preventative maintenance programs and procedures to reduce mechanical downtime and insuring that breakdowns are repaired with a minimum of processing disruption
- Conduct weekly meetings with the Maintenance and Production Manager to develop corrective action plans and assigns priorities relative to improving production reliability and reducing downtime
- Establish effective communication practices that provide operating information to operators, staff and upper management on a daily, monthly basis insuring that all parts of the company have the information necessary to affect continuous improvement. Items to be covered; identify issues, production schedules, cost controls, budget compliance and implementation of corrective action plans
- Insure that Human Resources programs are in place addressing the selection, training, development, motivation, and cultural expectations of all plant employees and the company. Insure that job descriptions are up to date and that reviews are conducted on a periodic basis, at a minimum annually
- 5-10 years of experience in production engineering, production supervision and plant management
- Bilingual required
- Demonstrated ability to manage human relations issues in a non-union environment
- Must be a self-starter capable of developing and maintaining a team environment
- Demonstrate an ability to be proactive in all phases of the operation
- Have an operating knowledge of computer and computer applications
- Demonstrated ability in analytical problem solving
169
Plant Manager Resume Examples & Samples
- Establish policy, provide guidance and oversee the administration of all aspects of the plant operation to achieve established business goals and objectives
- Achieves all key metrics established for plant operations on annual basis
- Executes all elements of strategic/tactical plans for which he/she is designated as champion
- Ensure all laws and regulations are followed particularly in the manufacturing areas of Environmental, OSHA, EEOC,Employment Law as well as other regulations as appropriate
- Develop employees to their full capacity/capability to obtain short and long range goals and objectives
- Interface with other functional groups as well as the customer as is appropriate to ensure highest service levels as possibleare being provided to the customer
- As appropriate, represent Timken in the community to maintain a good community image and community support
170
Plant Manager Resume Examples & Samples
- Develop and execute plant-specific strategic vision, mission and objectives to assure continuous improvement and alignment with enterprise vision, mission and objectives
- Drive employee engagement, training and development to maximize safety, quality, equipment reliability, and productivity
- Provide direct oversight for the operations management team including production, engineering, maintenance, planning and scheduling, procurement, quality, safety and logistics along with a strong connection to both finance and human resources
- Develop and manage facility budget including capital expenditures and cost management
- Assure regulatory compliance including but not limited to OSHA, EPA, USDA, FDA, FLSA, EEO, OFCCP and NLRB
- Ensure all quality standards, specifications and policies are met or exceeded, drive continuous improvement process / manufacturing improvements and collaborate with Quality, Research and Development in product development and implementation
- Set clear priorities, KPIs, and align resources to deliver against business and regulatory requirements in the areas of cost, financial controls, quality, safety and business initiatives
- Communicate in a timely manner any and all situations that may adversely impact the quality and efficiency tied to operations and the business
- Review and analyze production / QA data
- Review and approve Standard Operating Produces
- Ensure leadership team maintains a positive, productive working relationship with the current Union and all employees. Ensure proactive Safety and Security objectives are set and achieved
- Work with all members of leadership team to ensure all cost-savings measures are put into effect and all needed capital projects are identified and completed to continuously improve plant’s productivity and profitability
- Must be well versed in the latest Manufacturing Improvement methods and procedures to drive business results and customer satisfaction
- Must be able to handle multiple priorities to achieve desired financial, quality and customer service goals
- Analytical skills to interpret /manipulate numerical data as part of decision making process
- Bachelor’s Degree required in Food Science, Operations or other pertinent field
- Experience in Lean manufacturing / certification preferred
- Experience in Acidified food manufacturing preferred
171
Plant Manager Resume Examples & Samples
- BS/BA degree; graduate degree preferred
- 5 years operations experience with supervision of both hourly and salaried employees
- Industrial manufacturing experience preferred
- Strong organizational, communication and leadership skills
- Team player and ability to promote team concept
- Ability to set priorities, analyze problems and manage time effectively
- General understanding of accounting/financial principles
172
Plant Manager Resume Examples & Samples
- Services and maintains positive relationships with current customer base
- Identify customers needs and solve problems
- Understand and perform cost savings analysis for customers
- Generates new sales by promoting product line to new and existing customers
- Troubleshoots problems for customer
- Monitors sales market in assigned region
- Prepares various reports as required
173
Plant Manager Resume Examples & Samples
- Maintaining advanced engineering and manufacturing facilities in NA
- Exchanging product, process and benchmarking information with sister units worldwide
- Continually improving processes, material and designs to ensure every product exceeds customer specifications while providing unparalleled value
- Actively analyze Key Performance Indicators for plant operation and adjust/implement lean manufacturing and quality processes and systems leveraging ITW Toolbox – PLS, 80/20, etc., lean principals, 5S and related world class manufacturing improvement techniques/framework
- BA or BS degree, preferably in engineering, operations management or business
- 3-5 years’ experience in a management role in a fast paced manufacturing environment
- Demonstrated experience to work with sales and engineering to grow the business
- Strong working knowledge of budgets and P&L statements
- Proven metrics driven management style
- Coaching and mentoring leadership style
- Must be process oriented with a strong bias to results
- History of holding employees at all levels accountable to results and rewarding outstanding efforts of team members
- Must be a change agent with energy, passion, & enthusiasm
- Self-motivated with excellent organizational, analytical, problem solving and leadership skills
- Strong PC skills, including proficiency with Excel, Word, PowerPoint and Outlook
174
Plant Manager Resume Examples & Samples
- Day to day running of a Direct market delivery and lubricant plant
- Responsible for manufacturing employees, drivers and warehouse employees
- Develop and manage plant & driver productivity as well as process improvement plans utilizing continuous improvement techniques
- Oversee labor relations in a union environment
- A track record of increased responsibility in a manufacturing environment including roles such as Process and Plant Engineer, First Line Supervisor, Quality Control and Operations Management
175
Plant Manager Resume Examples & Samples
- Prepare and administer large and complex budget
- Establish and maintain working relationships
- Select, supervise, train and evaluate staff
- Expert-level problem Solving and Analytical Skills
- Plan and organize work to meet schedules and timelines
- Communication Skills both Written and Verbal
- 10 years management/leadership/coaching experience
176
Plant Manager Resume Examples & Samples
- Responsible from production end to finishing end of materials up to 2 million tons
- Meet or exceed all safety, health & environmental expectations established for the site
- Consistently meet customer expectations by providing quality products in a cost effective and efficient manner
- Maintain the plant’s critical community relations role by working effectively with businesses, schools, civic groups, and corporate representatives
- Facilitate the growth and development of employees and supervisors through comprehensive performance management measures
- 4 years experience in aggregates or related industry
177
Plant Manager Resume Examples & Samples
- Bachelor degree in Business, Engineering, Manufacturing or a related field. Master’s degree preferred
- 8 – 10 years manufacturing experience or related
- A minimum of five years experience in related areas like quality, production or engineering in a plant or prior experience as a plant manager
- Experience in leading change
- Demonstrated knowledge and plant manufacturing operations and business leadership
178
Plant Manager Resume Examples & Samples
- Three (3) or more years of progressive experience as a Plant Manager, Production or Reliability Manager or Plant Superintendent
- Five (5) or more years of experience in an industrial/manufacturing or military environment
- Able and willing to lead profitable change in an organization
- Experience implementing and using continuous improvement/lean tools such as; Six Sigma, 5-S, Lean Manufacturing, etc. to drive improvement
- Experience leading and managing direct reports, including recognition of talent gaps, coaching, performance feedback, and incentives
- Experience and understanding of budgeting/expense management with a basic understanding of financial and accounting practices
- Experience and understanding of EHS management systems, risk assessment/mitigation, and enforcement of safety rules and policies
- Working knowledge and experience with Microsoft Word and Excel, and other PC-based production and operations applications
- Experience of formulating business improvement strategies that achieve results
- Associates Degree or higher in Business Management, Forest Products or Engineering
- Lumber Industry experience
179
Plant Manager Resume Examples & Samples
- HS Diploma or equivalent
- Five (5) or more years of progressive experience in a wood products facility in one or more of the following positions: Plant Manager, Production Manager, Plant Superintendent, Reliability or Maintenance Manager, or in an equivalent role
- Five (5) or more years of experience with manufacturing processes, which includes work processes, operations excellence, maintenance, reliability, and continuous improvement
- Ability to lead profitable change in an organization
- Experience and understanding of Environmental, Health & Safety (EH&S) management systems, risk assessment/mitigation, and project planning and execution
- Must be able and willing to work safely, and promote and enforce safe work practices
- Experience working with various computer software programs such as Microsoft Excel, Word, etc
- Experience formulating business improvement strategies that achieve results
- Bachelor’s Degree or higher in Engineering or Wood Science
- Master’s Degree in Business Administration
- Large capital project Engineering or Management experience
- Experience implementing and using continuous improvement/lean tools such as; Six Sigma, 5-S, Lean Manufacturing, Transactional Lean, etc. to drive improvement
180
Plant Manager Resume Examples & Samples
- Administer, in cooperation with other Group and Corporate Management, the coordination of approved plans for Division growth and development, informing the Director – Plastics Fixtures Operations, and others concerned, on progress being made in comparison with established objectives, budgets, and schedules for various programs and projects
- Develop and recommend short- and long-range plant goals in support of Division, Group and Corporate objectives and policies, for the approval of the Director – Plastic Fixture Operations
- Direct and approve the establishment of manufacturing methods, standards, techniques, and plans so as to assure the production at the lowest cost consistent with established specifications as to quality, quantity, and delivery schedules
- Direct and coordinate with the Director – Plastic Fixture Operations, Director – Fixtures Supply Chain, and Controller – K&B Americas the development of production schedules, economic inventory levels, and control procedures to meet sales forecasts
- Bachelor degree required, preferably in business, engineering or related technical field. MBA preferred
- Minimum 7 years of successful manufacturing management, preferably in the in the specific material of the business. Former experience managing a plant or large manufacturing or support areas required
- Experience in lean manufacturing, modern quality systems, inventory controls, labor efficiency, capital & material asset management preferred. Financial understanding, including P & L strongly preferred
181
Plant Manager Resume Examples & Samples
- Responsible for all functions associated with manufacturing within a single facility including but not limited to: safety, waste reduction, plant productivity, line efficiency and mechanical uptime
- Manage AOP and deliver on controllable costs. Set, monitor and deliver both short and long term plant performance targets
- Maintain a high level of customer service to both New Albertsons Inc., (NAI) and public customers
- Where applicable, manage and maintain non-union plant status
- Manage collective bargaining agreements for unionized employees
- Ensure NAI Albertsons policies, procedures and practices are met and maintained
- Cultivate and promote a positive and innovative work environment
- Plan and execute 5S improvement to ensure annual audit score meets corporate goal
- Drive continuous improvement using lean manufacturing principles
- Meet Key Quality Indicator targets and reduce customer complaints
- Meet all internal and external audit targets. (SOX AIB, PMO, 5S, FDA, BRC/SQF etc )
- Partner with labor relations to negotiate labor contracts
- Monitor and ensure compliance to NAI internal control (SOX) requirements (quarterly monitoring and biannual financial audits)
- Develop capital projects using new technology which meet ROI and IRR thresholds
- Develop and implement TPM and CPM projects
- Identify and manage working capital
- Identify new market opportunities both within NAI and public customers
- Identify and implement cost savings initiatives
- Identify, and implement efficiency and cost cutting measures that will improve ROI
- Utilize new technology and Lean manufacturing principles to maximize efficiency
- Hire, train and mentor plant staff to support strong succession plan, build the bench strength
- Manage Accountabilities and Measurements and Individual Development Plans for direct reports quarterly and annually
- Hold employees accountable for their deliverables
- Provide leadership and support of safety processes to ensure that corporate IFR and Lost Time IFR goals are met
- Responsible for Mentoring Program, written A&Ms, ACCT leadership initiative with IDPs and quarterly follow-up
- 4 year college degree preferred
- Six to eight years plus education listed above
- Minimum seven years supervision/management in a manufacturing environment with a minimum of five years of financial responsibility
- Proven production/manufacturing background
- Knowledge of Lean manufacturing principles
- Managing for Results/ Development skills
- Production Engineering knowledge
- Interpersonal and Team Building. Exceptional Verbal/Written Communication
- Experience with Equipment/Maintenance. Knowledge of MS applications including proficiency with Microsoft Word, Microsoft Excel, PowerPoint and ability to grasp additional business related applications
182
Plant Manager Resume Examples & Samples
- BS degree in Engineering of Business is required
- Lean or Six-Sigma certification preferred
- Considerable judgement is required on a daily basis, new procedures and policies will need to be implemented and devised on a regular frequency. Large amounts of individual interpretations and application will be required both in managerial and technical terms
- Must have a strong customer focus and serve as an agent for change
- Need to have the ability to formulate strong teams and to drive the teams for successful results
- Must be able to effectively resolve conflicts
- Able to provide and communicate a clear vision and strategic goals for the facility and to make sure that they are aligned to corporate and business unit goals
- Proven ability to manage people; train and motivate employees, as well as delegate effectively
- Must be able to function in a deadline driven environment
- Excellent project management and planning skills with the ability to effectively manage several projects at one time while providing high attention to details and excellent follow-through skills
- Must possess high degree of professionalism and ability to handle confidential information
- Demonstrate organization and time management skills
- Demonstrate excellent written and verbal communication skills
183
Plant Manager Resume Examples & Samples
- Control all costs that directly affect the plants performance
- Direct and lead all operations within their plant
- Mange a team of 6 direct reports
- Provide functional leadership within the plant
- Accountable for all QHSE initiatives across the site
- Responsible for all site capital projects
- Develop and maintain qualified personnel within the all departments
- Maintain plant infrastructure for future viability and growth
- Accountable for providing a safe working environment
- Set overall expectations/standards and motivate employees to perform
- Drive a continuous improvement mind-set within plant environment
- Support cluster leads around strategy, policy and risk management
- Ensure talent management and succession planning strategy are executed
- Build relationships with customers at all levels
- Ensure plant inventory is managed appropriately
- BS degree in Engineering, Food Science or Business required
- Must have 7-10 years of experience in a Plant Manager role
- Has been a part of starting up a plant and/or implement change and process within a plant
- Experience incorporating structure within a plant environment and driving forward
- Experience working in a fast placed plant environment; multi-tasking
- Must have experience managing a large number of priorities at one time
- Someone who enjoys challenge
- Minimum 5 years of food industry experience is required
- Minimum 10 years of management experience including hiring, training, performance reviews, career development and forming high performance teams
- Embraces new ideas and approaches while installing confidence in our employees and customers
- Builds relationships internally and with custsomers
- Minimum 8+ years of experience managing a plant budget and P&L
- Minimum 8+ years of experience developing and adhering to weekly, monthly, quarterly and yearly KPI's
- Must have experience presenting and working side by side with executive team
- Experience coaching, mentoring teams on how to be successful
- Experience and in-depth understanding of HACCP, ISO and FSAI
- Experience with resourcing and long term planning
- Responsible for implementing and driving capital projects throughout the plant, as well as project budgets
- Uses mapping to to support Process Optimization
- Supports the development of PIDS for KDM
184
Plant Manager Resume Examples & Samples
- Maintain a clean and safe plant. Provide an injury-free work environment for employees, staff, contractors, visitors through engagement, Job Hazard Analysis (JHAs), training programs, good work practices, Bunge standards, and proactive elimination of exposures. Continually improve safety culture by addressing both physical safety issues and employee safety behaviours. Maintain and improve housekeeping in all areas
- Plan, organize and direct the manufacturing and maintenance operations which ensure the most effective return on assets
- Initiate plans and processes which minimize manufacturing costs through effective utilization of manpower, equipment, facilities, materials, and capital. Assure attainment of business objectives and productions schedules while ensuring product standards that will exceed our customers' expectations. Reduce costs and improve efficiencies in all areas of plant operations
- Implement manufacturing strategies and action plans to ensure that the facility supports Bunge's strategic initiatives
- Responsible for the facility's environmental compliance
- Establish controls and procedures to ensure ongoing compliance and a positive relationship with local, provincial and federal agencies
- Foster a working environment that encourages employee involvement in the consistent improvement of plant processes, striving for optimal costs and efficiencies
- Establish group and individual accountabilities throughout all plant departments for safety leadership, problem solving and cost reduction
- Encourage use of new techniques and focus on fact based problem solving
- Manage spending against budget and in relation to changes in production volume
- Assure that collective bargaining agreements are effectively administered and that employee grievances are addressed in a timely fashion
- Maintain individual skills keeping up to date with latest production and production management concepts
- Ensure the proper planning, design and implementation capital and expense projects consistent with site strategy
- Establish and maintain a positive community relationship and promote sustainability activities
- Ensure proper maintenance of site equipment and infrastructure
- Confers regularly with senior management to ensure that manufacturing objectives and business goals are being met
185
Plant Manager Resume Examples & Samples
- Leading and developing a culture that promotes world-class environmental, health, and safety results
- Providing leadership to achieve and maintain effective quality, service, operational, and budget performance
- Leading and promoting continuous improvement initiatives using tools such as Lean manufacturing, Six Sigma, and other process improvement techniques
- Overseeing all hiring, employee relations, and employee development activities, ensuring an effective, engaging and productive workforce
- Defining and directing the administration of plant policies within the framework and intent of the Company's manufacturing policy
- Leading in a participative, employee empowerment culture, providing leadership and direction in the development of higher levels of involvement
- Providing personal direction in the resolution of current operating problems of a critical nature, in order to maintain maximum continuity of production
- Formulating operating objectives and strategies in areas such as cost reduction, quality improvement, budgeting, new process and product development and/or integration, equipment utilization, etc
- Bachelor's Degree in Engineering, Business, or a related field
- 8+ years of production management experience in a multi-shift environment
- Past experience leading and managing a diverse group of functions
- Comprehensive knowledge of Lean, optimization, and other continuous improvement processes
- Strong management, leadership, and influence skills
- Demonstrated ability to effectively manage a diverse group of employees in a participative, employee empowerment culture
- Experience in developing and managing operating costs and capital and maintenance budgets
- Working knowledge of environmental, health and safety practices and regulations, including OSHA compliance, and a proven record of improving safety results
- Master's degree in a related field
- 3+ years of experience working as a plant manager
- Black Belt and Lean certifications
- Experience in high-volume wood manufacturing, veneer production, and laminate press operations
186
Plant Manager Resume Examples & Samples
- BS Degree in an Engineering, Chemistry, or Operations discipline; MBA preferred
- Minimum of 10 years of progressive operations experience
- Experience with Change Management and Leadership development
- Experience in financial reporting with a proven business acumen
- Safety, health, environmental awareness. Experience with Responsible Care is a plus
- Strives to achieve operational excellence
- Strong organizational and communication skills
- Ability to interact with customers, suppliers, contractors and peer groups in a professional manner
187
Plant Manager Resume Examples & Samples
- Maintain a safe and clean working environment for all production associates and visitors
- Responsible for direct supervision of production supervisors, quality personnel, maintenance, and planning
- Leads the Sales, Inventory, Operations, Planning (SIOP) process and cross functional actions to drive overall plant success
- Improve key business metrics of OTD, productivity and EBITDA by implementing and supporting lean and continuous improvement activities
- Coordinate/Manage production schedules while following SQDC (Safety Quality Delivery Cost) requirements
- Develop training plans for your team members, whether direct reports or one-over-one
- Demonstrate a high level of energy, drive, enthusiasm, initiative, commitments and professionalism
- Excellent people, communication (written and verbal), negotiation and facilitation skills
- Strong PC skills required including a high level of proficiency with Microsoft Office Suite
- Must be a self starter with the ability to work autonomously as well as part of a team
- Ability to understand and follow written and oral instructions, with acute attention to detail
- Ability to adapt to unfamiliar processes and situations with minimal review/supervision
- Flexibility to adapt to deadlines, changing schedules, priorities, and unpredictable events within a fast-paced manufacturing environment
- Manage metrics with action plans and bowlers in accordance with the Strategic Deployment Process
- Competitive Base Salary
- Matching 401(k) contribution (50% match up to 8%)
188
Plant Manager Resume Examples & Samples
- Direct management responsibility for all Drivers & Plant Workers. Responsibilities will include, but not be limited to: associate hiring, coaching, training, safety, compliance and discipline
- Oversee and manage all plant operations including, but not limited to: safety, production, regulatory compliance, equipment ordering, parts ordering, and keeping office supplies and worker supplies stocked, etc
- Oversee and manage quality assurance program
- Oversee and manage standard operating procedures
- Share joint responsibility with the CSR to supervise product supply and inventory, and assist upper management with inventory planning and rail car demands as necessary
- Accountable for employee compliance with Airgas Safety Manual. This includes, but is not limited to: safety meetings, safety contacts, medical surveillance program, hazardous work program, plant inspections, ect
- Responsible for compliance with RMP/PSM procedures
- Accountability for employee training and documentation (WB Manager, DQ files, monthly safety meetings, safety contacts, etc.)
- Responsible for driver dispatch for the Palmerton facility
- Responsible for managing and compliance of driver Hours of Service and DOT rules and regulation
- Responsible for effective use of all driver resources including minimizing the overtime, leveling the work load across all drivers, and cross training all drivers to handle all distribution equipment
- Oversee all truck and trailer maintenance and documentation including but not limited to: compliance and tracking of driver vehicle inspection reports, repairs, monthly inspections, annual and five year testing, etc
- Interact with Fleet Manager & Warner Fleet Services as needed regarding vendor invoicing, maintenance approvals and equipment issues and tracking
- Assist in planning & managing plant projects and upgrades with Regional Manager & Engineering as needed
- Work with the sales team to address any customer issues or concerns
- Work with Regional Management team to cover work load due to shifting business patterns
- 6+ years professional work experience including a supervisory role
- Bachelor Degree required
- Knowledge of Safety and Regulatory/DOT/OSHA/EPA Compliance
- Experience with hazardous material with knowledge in hazmat regulations
- Knowledge of industrial chemical distribution or logistics including inventory management preferred
- Strong computer skills, including proficiency with MS office including experience with MS Excel
- Good oral and writing skills as well as strong interpersonal skills. Fluent in the English language
- Communication skills in order to effectively communicate with branch associates and all levels of management within Airgas
- Exceptional leadership skills and the ability to motivate others
- Willingness to travel up to 25%
- Able to talk, hear, walk, sit; use hands to finger, handle or feel objects, tools, or controls; reach with hands and arms; stoop, kneel or crouch
- Travel - driving and airline flights – up to 25%
- Must be capable of wearing a chemical respirator if necessary
- Office environment
- Industrial Chemical Plants - Process Equipment, piping, chemicals
- Industrial Construction Sites - In progress construction sites with construction equipment and partially completed structures
189
Plant Manager Resume Examples & Samples
- Develop a manufacturing team to provide exceptional customer service at the lowest possible cost while maintaining a safe work environment. Specific duties include employee development/training, plant scheduling, interviewing, hiring/firing, customer contact, root cause analysis, financial tracking, safety implementation, supplier evaluation, and process improvement
- Implementation of Lean Manufacturing. This includes orderly housekeeping (5S), adequate inventory turns, throughput time reduction, and advanced manufacturing techniques. The Plant Manager is expected to be the “champion” of Lean Manufacturing at their facility
- Inventory control. This involves ordering all raw materials, supplies, and finished goods. The Plant Manager is also responsible for implementation of an inventory audit procedure to ensure accurate inventories are maintained at all times
- Creating an environment for success among supervisory and production employees. It is pertinent that the Plant Manager convey an attitude that is positive and confident. He/she must direct their staff to achieve their highest level of performance while treating them with respect and dignity
- Interaction with the rest of the company. Work with purchasing, environmental, health & safety, engineering, human resources, and corporate staff. The Plant Manager will be called upon to be the local expert for their plant regarding these
190
Plant Manager Resume Examples & Samples
- Responsible for effective planning, coordinating and directing overall manufacturing activities
- Coordinates the development as well as the execution of manufacturing schedules, supervises the application of policies, methods and production standards
- Ensures that products and services meet established goals for safety, quality, schedule and cost
- Keeps abreast of current business practices of manufacturing companies and evaluates what practices and concepts would be beneficial and feasible to implement in Manufacturing operations
- Coordinates efforts between individual departments in Manufacturing and ensures activities are in line with the Division and Business Unit goals, directives and policies
- Works with the needs of individual Manufacturing Team Managers to see that necessary resources are provided to accomplish desired goals and schedules, including the appropriate training and education
- Responsible for the development of and the compliance with the manufacturing budget. Responsible for supervision of 150-200 manufacturing employees, managing a $9 million employee expense budget, and a $10 million operating expense budget
- Responsible for determining the quantity of seasonal contract employees necessary to meet sales and customer requirements, while maintaining productivity standards. Works closely with Human Resources in managing this temporary workforce
- Ensure that all Team Managers properly supervise their employees and ensure that their employees carry out their waste management activities
- Ensure that the facility complies with all requirements of federal, state, and local laws and regulations covering the generation, storage, handling, and disposal of hazardous waste
- Understand the applicable hazardous waste regulations in order to maintain full compliance
- Possesses an understanding and has experience with Engineering processes, Safety and Environmental management and Human Resources principles
- PC skills and knowledge of word processing, spreadsheet and presentation software is required
191
Plant Manager Resume Examples & Samples
- As One
- Safe
- Innovative
- Driven
- PC literate with experience of Axapta, On-Guard and Microsoft Office
- Ability to demonstrate commercial acumen
- Demonstrate a clear understanding of logistics, operations and sales
- Ability to motivate and manage a large team
- Sound Financial acumen
192
Plant Manager Resume Examples & Samples
- Bachelor’s Degree Preferred
- Good interpersonal skills
- Ability to handle multiple tasks well
- Preference for blend processing experience
- Proficient in all Microsoft Office Suite, i.e. Excel, PowerPoint, Etc
- SAP or iScala experience would be beneficial
193
Plant Manager Resume Examples & Samples
- 10+ years of leadership experience in a fuels processing facility
- Plant leadership experience or experience leading a multifunctional team, including maintenance, environment health & safety, engineering, and operations
- Strategy development experience along with a broad business acumen
- Do you have a valid and current government issued driver's license?
- Experience in Biodiesel or Hydrocarbon processing or a related field
194
Plant Manager Resume Examples & Samples
- Ensure that all company personnel and guests on site comply with safety and environmental practices at a minimum. Further, the Plant Manager is the primary site advocate for our belief that we can work injury-free
- Successfully hire, supervise, orient, train and retain plant personnel
- Promote and maintain a clean workplace that is “tour-ready” at all times
- Collaborate with others to build a production schedule that exceeds customer expectations
- Ability to read drawings, plan production tasks from those drawings, and coach employees to produce product correctly
- Ability to operate some of the standard tools on the plant floor such as overhead cranes, hand tools, batch plant, etc. While the Plant Manager will not be asked to operate these things continuously, having some of these skills will make him/her a better coach and troubleshooter
- Be a leader and coach leadership. Motivate crews during morning huddles. Lead effective Mid-Day meetings. Coach Leads on how to set expectations on a whiteboard and have them followed. Lead inventory counts. Promote safety best practices in meetings with other Plant Managers
- Perform any other duties as assigned by the General Manager as deemed appropriate and necessary by them
- Work with ones hands in a manufacturing environment
- Understanding Spanish (helpful)
195
Plant Manager Resume Examples & Samples
- Preparation of budget (planning) for the plant, ensuring objectives for the site are met within approved budget, schedules and quality specifications
- Effective implementation of all logistics activities, particularly in the materials management, controlling, logistics and HR management
- Representation of the plant and the company to external stakeholders by having regulars close contacts to the local and regional communities
- Planning of regular meetings with employees and local works council to ensure communication of operational objectives
- Deployment of the Eaton Business System and lean tools throughout the plant
- Management of documentations and/or execution of system transactions in order to ensure consistent and compliant products are manufactured
- Monitoring of performance against objectives by using Eaton metrics and balance score cards
- Participation in employee representative consultations, pay talks and other union related obligations as needed
- Development and implementation of improvements in production methods, standards and procedures to ensure effective use of resources. Assessment of performance indicators and implementation of appropriate actions to ensure schedule, cost and quality goals of manufacturing operations are met
- Serving as key player in ensuring that environmental, health & safety issues are addressed, considering local regulations, by focusing on quality and environmental aspects
- University Degree
- Proficiency in Six Sigma tools is considered an advantage
- Excellent communication skills (fluency in both Czech and English is strongly preferred)
- Financial acumen, strategic ability, strong business, and strong change leadership capabilities
- Strong interpersonal and leadership
- Ability to communicate effectively at all levels of the organization
- Ability to thrive in a matrix environment
- Ability to build customer relationships via internal captive customers
- Ability to train others, adopting internal methodologies and programs
- Authority/power to assert and flexibility
- Analytical thinking plus good anticipation skills
- Multi-cultural awareness
196
Plant Manager Resume Examples & Samples
- Overall management of Environmental, Health, and Safety including ergonomics. Continue to drive Newell Brands SEAL process and other corporate Safety metrics. Implement and monitor manufacturing safety, procedures and training programs to ensure a safe working environment for all employees
- Quality – insure quality methods and processes are installed and maintained to meet exacting product specifications outlined by our Japan Marketing and R&D teams needed to meet customer and consumer requirements
- Drive performance measures to all levels of operations and ensure a culture of employee involvement and continuous improvement
- Establishes a baseline that monitors overall plant performance. Manages plant performance improvements based on Key Performance Indicator (KPI) measurements
- Responsible for all operations including production, planning, safety, and quality
- Ensures optimum daily productivity goals are met within customer and company deadlines for sales, delivery, and quality
- Perform to monthly financial operating plans, ensuring labor productivity and operating expenses meet or exceed plans. Accountable for four wall costs of the facility
- Develops improvement flow concepts from suppliers all the way through the manufacturing facility
- Promote and maintain a culture and environment of continuous improvement based on comprehensive development and execution of Lean business practices
- Consistently administers company rules, regulations, and policies
- Ten years progressive operations experience in a manufacturing environment, assembly experience preferred, automotive background a plus, sewing experience a plus
- Manufacturing and management leadership experiences
- New Product Development team experience
- Results-oriented leader with a high level of work intensity and a bias for action
- Excellent written, verbal, and interpersonal communication skills to effectively work with a diverse group of people
- Working in a matrix environment with many different interaction points
- Must be able to speak Mandarin and English – Japanese would be a plus
- Excels in principles of Lean manufacturing and 5S programs
- Experience with flow manufacturing
- Assembly experience
- Passion to continuously improve processes and results
- Ability to work in a fast paced, dynamic work environment
197
Plant Manager Resume Examples & Samples
- 3-5 years Plant Management experience in a complex, fast paced manufacturing environment, required
- Experience with union negotiations, grievance resolution and labor relations, strongly preferred
- Demonstrated commitment for results
- “Change Agent”, with a demonstrated ability to “think outside the box” and a proven talent for driving innovative solutions and ideas
- Demonstrated ability to analyze information, evaluate risk, and employ excellent judgment in effective and timely decisions
- Demonstrated flexibility, versatility and negotiation skills necessary to operate with organizational savvy across functional work teams
- Demonstrated ability to mentor, motivate and positively influence others
- Demonstrated ability to maintain high expectations for self and others
- Demonstrated ability to react to situations with a strong sense of urgency
- Excellent problem solving, project management and prioritization skills
- Excellent customer focus, both internal and external
- Knowledge of computer applications as they relate to work, specifically Microsoft Office Suite (Excel, Outlook, Word and Project) applications
198
Plant Manager Resume Examples & Samples
- Maintain equipment files, maintain inventory, and manage the expeditious purchase and/or re-supply of components as necessary to complete assigned projects
- Power Wiring - Must know 3-phase theory and wiring techniques including troubleshooting, component replacement, and motor wiring. Must know general wiring techniques for 110V system
- Air Pneumatics - Must have experience with general air pneumatics, including air compressor operation and maintenance, regulator replacement, solenoid valve replacement, 2-way and 3-way valve, tubing installation, and general system troubleshooting
- Hydraulics – Must know how to maintain a hydraulic system including cylinder seal repair, cylinder replacement, bushing replacements (usually by outside machine shop), hose-crimper operation (includes matching hose to fitting), fluid maintenance including filter change out, hydraulic pump replacement, valve stack repair and maintenance, fitting specification, and general troubleshooting and adjustments. Must be able to read a hydraulic flow diagram
- Machining and Welding – Must be familiar with the use of all power tools associated with metal machining, including power drills, chop saws, reciprocating saw, grinder, and pneumatic hammers. Must be able to use soldering/brazing torches, and acetylene torches for cutting steel. Must be able to operate a stick welder to fuse carbon steel and perform repairs; ability to weld stainless steel or higher alloys or operate a TIG welder are pluses
- Capable of performing all maintenance functions
- Understanding of boilers, maintenance and associated programs related to the efficient operation of boilers. Must possess basic understanding of PLC’s. Ability to troubleshoot and complete programming as required on a variety of legacy systems, preferred but not required
- Basic understanding of waste water systems, pumps and associated equipment including maintenance and preventative maintenance to ensure optimum performance of the system. Provide leadership to all-shift operations crew. Ensure their compliance with the District Manager’s directives on Environmental Safety and Health, permit compliance, customer service, productivity, cost reduction, care of equipment, housekeeping, and paperwork completion
199
Plant Manager Resume Examples & Samples
- Operates Air Liquide Biogas facility in Walnut, MS, safely and reliably by complying with regulatory requirements, developing and leading personnel, managing costs effectively, and developing personal skills and competencies, including testing, maintenance strategies, monitoring plant processes and maximizing productivity
- Demonstrate leadership in process and operational safety at all times, and demand that of others, including plant personnel, visitors, contractors
- Define, design, specify, control costs and implement projects intended to improve, safety, efficiency, and profitability
- Recommends changes in process to effect greatest economy in production methods and material cost
- Evaluates plant equipment and processes, and recommends design modifications to eliminate malfunctions and improve efficiency
- Sets up and conducts tests of complete units under operational conditions and analyzes test results in relation to design specifications, modifies or adjusts equipment to meet specifications
- Suggest innovative tools and software to improve control and efficiency
- Plans utilization of production facilities to improve efficiency of operations
- Directs, coordinates, and exercises functional authority for planning, organization, control, integration, and completion of engineering project within area of assigned responsibility
- Provides technical support for plant production as required
- Supports safety procedures and personnel policies directed by local and corporate personnel and safety departments
- Manages biogas source (landfill) gas collection system to safely and cost-effectively maximize both the quantity and quality of biogas for processing
- Interfaces with biogas source management team to support good relations and coordinate efforts
- Bachelor's Degree in an Engineering or Technical discipline
- 2+ years plant management or engineering experience
- 2+ years supervision or management experience in a manufacturing environment
- Ability to travel up to 25%
- Ability to work extended hours and shift work as business needs dictate
- On call nights, weekends and holidays as required - rotation with plant operators
- Proven "hands-on" mechanical and troubleshooting ability
- General understanding of accounting principles and working knowledge of plant operating budget
- Ability to use Google Docs, Google Sheets, and Google Slides; Working knowledge of Excel is a plus
- Knowledge of industrial gases
- Working knowledge of commercial agreements and customer relations
- Willing to be relocated for promotional opportunity
- Experience in environmental sustainability industry such as biogas, renewable energy or waste treatment
200
Plant Manager Resume Examples & Samples
- College degree in a business, technical or scientific field or 10 to 12 years related experience and/or training; or any combination of education and experience at the supervisor's discretion
- 5+ years progressive experience in a key leadership/management role at a manufacturing facility
- Strong process and batch manufacturing experience
201
Plant Manager Resume Examples & Samples
- Implementing process improvement methods and ensuring non-stop production in an effective, safe and profitable manner
- Responsible for inventory management, labor, production, shipping, and associated costs
- Providing leadership to staff, assessing performance, and directing all operational activities to ensure product quality and consistency
- Ensuring workplace safety through implementation, adherence and enforcement of company business standards, as well as safety and development programs
- Two year degree, and/or equivalent combination(s) of education, industry experience and training
- A minimum of 2 years manufacturing management experience
- Must have excellent analytical and communication skills
- Must be available to work 10-12 hour days, six to seven days a week specifically in high season
- Must be physically able to walk/stand/bend/stoop/crouch/climb 80% of time; office duties 20% of time
- Flash arc (must wear specific clothing for safety reasons with the high voltage of electricity): 24 to 12 DC; 110-480 AC – must be able to work with and around
- Must be able to work in a high stress and high paced environment at all times
- Work environment is not temperature controlled and can range from zero to 110 degrees – must be able to work in the these conditions as well as dirty/dusty/mulch/rain/snow – outdoor environment
- Must be able to help and assist with any maintenance requirements in the facility
202
Plant Manager Resume Examples & Samples
- Support the Company''s mission, vision, values and goals in the performance of daily activities
- Provide direct leadership, mentoring, and coaching and supervise the leadership team and all salaried staff in the plant
- Responsible for the development, performance feedback, direction and leadership of all colleagues in the plant including mentoring, coaching, counseling and corrective action when situations dictate
- Responsible for the identification, selection, training and coaching management talent
- Drive the utilization of problem solving methods for related plant and customer problems / issues
- Directs, drives, establishes and implements new programs and plant productivity improvements to achieve plant productivity goals and customer cost reduction goals
- Responsible for plant manning levels and assures compliance and improvements to the budget
- Provide plant input into quoting and business development activities (ex. pricing, program management, plant capacity, etc.)
- Responsible for leading the plant safety committee
- Assign clear responsibilities for Environmental Health and Safety (EHS) and hold all direct reports accountable for enforcement
- Responsible for ensuring the entire team has the necessary tools and materials to properly perform their roles safely and efficiently
- Utilize teamwork to develop plant synergy
- Maintain high standards of housekeeping throughout the plant
- Maintain a positive working relationship with all levels of the organization
- Provides model behavior to demonstrate corporate values
- Responsible for interactions with outside groups including local, state and national government officials
- Responsible for customer and supplier interface
- Represent the company during customer visits / surveys and during meetings / presentations at customers location
- Provide key input into the development of North America''s strategic business plan
- Develop and drive the plant''s strategic business plan along with identifying key measurable to support the plant business goals
- Responsible for the financial performance of the plant
- Direct the utilization of the company performance metric format to effectively track, monitor, and implement required improvement activities related to business plan, goals, issues, etc
- Responsible for the safety, quality, productivity and delivery of all plant operations and colleagues
- Ensure accountability and discipline within the plant
- Responsible for overall coordination and communication of North America and plant goals
- Drive implementation of a progressive production system and required operating procedures and work instructions to improve plant performance metrics and meet or exceed customer expectations
- Provide active leadership role in meeting / exceeding customer expectations in all related areas
- Develop, drive and support plant activities towards achieving customer awards and Quality registrations (ex. TS 16949/ISO14001)
- Responsible for assuring that all internal and OSHA required procedures are being followed in the performance of daily activities
- Assure all safety devices are properly in place and utilized, and to verify individual usage of personal protective equipment by the entire work team
- Comply and oversee compliance with all internal and OSHA required safety procedures in the performance of daily activities
- Adherence to all company policies & procedures (ex. Quality Policy Manual, Colleague Handbook, Level II Procedures, etc)
- Directly supervises the leadership team and responsible for all salaried staff in the plant
- Responsible for leading, coaching and mentoring the leadership team and providing them with the skills to lead, coach and mentor their direct reports
- Bachelor''s Degree in business related field, prefer manufacturing, engineering or quality, with a Master''s preferred
- Minimum five to seven years experience as a Plant Manager, Operations Manager or Department Manager in a manufacturing environment with experience in a metals environment preferred, or a combination of degree and experience
- Possess knowledge of plant department functions and corresponding roles and interactions to facilitate overall plant synergy
- Vision and ability to translate progressive operating techniques into applications and results
- Excellent organizational, analytical and communication skills
- Ability to mentor and teach the team effective problem solving methods
- Experience in applying lean manufacturing concepts
- Proven leadership ability and excellent interpersonal skills
- Ability to interpret financial and performance data
- Experience in quality and environmental measurables such as TS 16949 and ISO 14001
- Ability to read and write in English and to perform mathematical calculations
203
Plant Manager Resume Examples & Samples
- Direct and manage all aspects of plant operations including safety, environmental compliance, production, maintenance, quality, and shipping and receiving
- Coordinate plant activities through planning with production manager and production supervisors to insure the total manufacturing objectives are accomplished in a timely and cost effective manner
- Monitor and streamline plant key inputs including, energy, labor and mining feed to optimize utilization, throughput, and cost
- Continually develop and execute key business initiatives that drive production safety, product quality and cost efficiency
- Develop, review, analyze, and communicate key KPI’s on a daily basis with organization and implement corrective action plans to address any issues that arise
- Develop site budget plans and control profits
- Continually monitor and adjust costs throughout the year to assure they remain within budgetary guidelines.Control expenses for overtime and maintenance repairs
- Manage site capital plan and assist with the design of plant capital projects and securing funding of capital projects by preparing CERs with capital expense justification information.Maintain plant equipment and facility
- Effective participate in any required customer related activities, representing operations; communicates to customers when needed and support commercial teams in developing and maintaining customers
- Investigate new opportunities for increasing revenue and profitability
- Work to maintain a positive employee relations environment to promote teamwork and productivity
- Foster employee development, granting appropriate training levels and business exposure; ensure report development plans are in place and continuously monitored and updated
- Collaborate with key business partners in Community Relations
- Union experience preferred
- Strong technical knowledge covering a wide range of production and manufacturing operating processes. Previous exposure to maintenance activities is desirable
- Proven ability to drive culture change with demonstrated impact to the business
- Demonstrated people management skills, preferably covering several different functions and technical formations usually present in manufacturing environment
- Demonstrated communication skills, both verbal and written, and possess the ability to facilitate communication within their own department, interdepartmentally, and externally
- Strong problem solving abilities
- Ability to provide in-depth analysis of all issues related to manufacturing, including technical and economical/financial aspects. Capacity to properly generate reports and analysis to be communicated to upper organizational levels
- Ability to interact and present effectively at all levels of the organization
- Organizational skills with the ability to meet deadlines
- Proven ability to juggle multiple tasks
- Strong computer skills including MS Office suite and MS AX
204
Plant Manager Resume Examples & Samples
- Operate and safely maintain the high pressure gas repackaging plant while ensuring compliance with all federal, state, local and company policies, procedures, regulations and laws
- Manage and lead subordinate supervisors to provide leadership to Plant Operators
- Assigns job tasks to plant operators according to customer needs, current stock levels, and workers’ expertise
- Analyze production schedules and estimates man-hour requirements for completion of job assignment
- Establishes or adjusts work procedures to meet production schedules, using knowledge of capacities of machines and equipment
- Implement measures to improve production methods, equipment performance, quality of product, and changes working conditions and use of equipment to increase efficiency of work crew
- Provide coaching and corrective action promptly, to ensure that poor performers are identified, documented and improved to acceptable performance, or released
- Ensure employee complaints, grievances, etc. are effectively handled
- Corrects unsafe acts or conditions without delay
- Analyze and resolves work problems, or assists workers in solving work problems. Initiates or suggests plans to motivate workers to achieve work goals
- Initiates personnel actions, such as promotions, transfers, discharges, and disciplinary measures
- Train new workers and cross trains employees to continue production during personnel shortages
- Maintain time and production records
- High school diploma or equivalent (GED). Bachelor’s degree in related field a plus
- 5+ years of production experience, preferably in our industry or a manufacturing or distribution environment
- 3+ years of experience supervising, motivating and leading associates
- Analytic ability demonstrated by working knowledge of gas chromatography using FID, TCD, PID detectors, nondispersive infrared and component-specific analyzers for analysis of gaseous samples
- Thorough knowledge of manometric and gravimetric gas blending procedures, and working knowledge of laws of Partial Pressure
- Working knowledge of planning and blending mixtures containing fuel gases and oxidizers as well as other non-compatible gases
- Working knowledge of OSHA, DOT, and FDA regulations as they apply to the compressed gas industry
- Excellent organization, documentation and follow-up skills
- Computer skills, including working knowledge of Microsoft Office or similar software
- Ability to routinely lift 25 – 60 lbs
- Ability to perform functions during occasional climbing, balancing, kneeling, pushing, pulling and finger activities
- Must be able to work flexible schedule to meet management requirements and customer expectations
- Must be able to work outdoors in temperatures ranging from -10 to over 110 degrees
205
Plant Manager Resume Examples & Samples
- Cascade strategic objectives from Segment, Business Unit and Operations functional leadership. Set and clarify requirements and expectations for direct and matrixed reports based on the strategic direction and needs of the business
- Plan, direct and monitor production activities with the objective of maximizing the use of organizational resources to meet or exceed established targets for TEOA (LEAN), Safety, Quality, Delivery, Cost, Employee Engagement and Talent Development
- Drive the creation and deployment of Continuous Improvement initiatives which enable functional areas and the site to meet or exceed its Operating plan. This includes process changes and other TEOA (LEAN) initiatives, techniques and enhancements focused on STAR level certification. Source and creatively nurture process improvement ideas from others at the site through daily GO meetings, GEMBA walks and other creative incubation processes. Take proactive steps to ensure best practices are shared. Drive standard work for safety, quality, inventory, scrap rate/yield, TPM, 5S+1
- Develop action plans and make operational decisions on policies, tactics and resources critical to the site’s operational success thus ensuring successful delivery against targets and strategy (Capex)
- Own the environmental, health and safety for the site. Drive the successful resolution of building issues and repairs
- Deliver an extraordinary customer experience. Understand the demand from the customer and plan materials and production in alignment with plan. Understand the extended value stream from procurement, through production to delivery and beyond. Focus on quality expectations of the customer and creating an extraordinary customer experience including but not limited to continuously improving ship to request rate, reduction of customer complaints/issues while balancing cost
- Plan materials and production around the needs of the customer. Develop and implement production operating budget and plan. Allocate appropriate resources and monitor goal attainment. Develop headcount requirements and work to align with achieving operations plan
- Partner with support staff and matrixed reports to ensure the support and resources provided align with the needs of the operation. As the plant manager, responsible for P&L, conversion and material productivity
- Measure performance (results and behaviors) while providing timely performance feedback and coaching. Mentor, coach and engage team. Resolve issues with people or functions to achieve targeted performance targets/metrics. Retain your key talent. Hold others accountable based on their personal performance results/behaviors as well as team results/behaviors versus expectations/targets
- Demonstrate and proactively drive all people management responsibilities including hiring, training, coaching, performance management (performance objective setting, development planning, mid-year & year-end performance reviews, calibration), compensation planning and employee relations for direct and matrixed reports. Proactively address potentially difficult or complex employee relations issues while pulling in the necessary stakeholders (i.e. HR, Legal, etc.)
- Drive strategic workforce planning and successful talent development strategies aligned to business needs, OLR and strategic succession planning outcomes/requirements, and seasonality
- Drive employee engagement at the site through an appropriate daily, weekly, bi-weekly, monthly and quarterly communication strategy with a strong focus on recognition. Hold town hall meetings and conduct skip-levels with your report’s direct reports
- Minimum 10+ years of experience required
- Minimum 3+ years management experience required
- Prior experience managing a team of direct and matrixed reports preferred
- Prior experience in supply chain, materials or operations management preferred
- Strong demonstrated engineering/technical acumen and finance/financial acumen preferred
206
Plant Manager Resume Examples & Samples
- Fill plant experience
- Experience in welding industry and working knowledge of cylinder fill operations
- Must be able to substitute for plant technicians at each position
207
Plant Manager Resume Examples & Samples
- Create and communicates a clear vision for the future to inspire and drive the business to achieve and surpass business goals and objectives (such as Safety, Productivity, Inventory levels, etc)
- Develop strategies for growth, set stretching but achievable targets and monitor performance to target for each functional area: Operations Engineering/Maintenance, Planning, Purchasing, Quality, Inventory Control, Safety
- Responsible for production improvements and efficiency of operations, demonstrate an ability to identify and drive continuous improvement initiatives. Use process mapping to support Process Optimization
- Seek opportunities to optimise cost and demonstrates an understanding of all cost drivers and their impact
- Work closely with Human Resources on staffing needs and budget
- Responsible for corporate and plant level safety, quality and financial initiatives and on-going training and compliance
- Understand the key success factors of the business, exercise sound judgement and inspire confidence in our customers. Learn EUM and gain an insight understanding of customer strategic objectives
- Interact with external parties including government agencies. vendors, and insurance companies
- Foster a successful, accountable 1Kerry oriented work environment
- Manage 4 direct reports
- Hiring, performance reviews, training and career development of staff
- Bachelor’s Degree required, Mechanical/Chemical Engineering or Food Science preferred
- Understanding of USDA/FDA regulations, as well as HACCP, GMP’s, SOP’s, AIB, Organic, and Hazard Analysis
- Minimum 5 years of progressive experience in manufacturing environment
- Fluency in English, knowledge of other languages is a plus
- Openness to the opportunities in developed and emerging markets is a plus
- Minimum 5 years of experience in a Plant Manager role is required
- Knowledge in regards liquid processing; liquid processing environment background and experience required
208
Plant Manager Resume Examples & Samples
- Leadership: Coach and provide developmental opportunities to subordinates
- Production Levels: Ensure that production levels are at an optimum with minimum plant downtime. Coordinate by-size production with sales market demands and long range planning. Work closely with the quality control technicians to ensure that all production meet the customers needs
- Maintenance Program: Proper utilization and maintenance of all stationary and mobile equipment so that equipment cost and downtime are minimized and the equipment is available when needed
- Safety, Health, and Environment: Champion the highest standards of safety and environmental behavior and performance. Be proactive in the safety of all personnel and activities in the plant area. Inspect and maintain dust control systems to ensure a healthy work environment. Be knowledgeable of waste products, their impact on the environment and their proper disposal
- Supervision: Provide an example of good leadership, keep open and effective lines of communication with division staff and plant level personnel
- Inventory Control: Maintain proper levels of inventories to support local sales activities and long range market demands
- Quality Control: Work closely with the QC Technician onsite to ensure we maintain consistency in the quality of our products and services to the customer
- Minimum 3-5 years of mining experience
- Experience in Safety, Health, and Environment functions
- Knowledge of mining and production techniques and equipment, safety and environmental regulations (MSHA and OSHA), equipment application and operation, and material specifications
- Strong communication skills and interpersonal skills including conflict resolution
- Ability to plan and manage effectively
209
Plant Manager Resume Examples & Samples
- Responsible for ensuring all EHS policies and procedures are implemented within the facility; supporting the site to achieve EHS Excellence by executing the journey to EHS excellence program. (J2EE)
- Core responsibility for ensuring that the site meets business objectives by delivering robust leadership, management and control to the plant Machine Shop and Assembly Shop
- Responsible for the overall planning, management and control for all manufacturing, machining, test and assembly activities
- Responsible for acting as the site Operational Lead for the Culture Compass survey, promoting best practice and implementing change based on employee feedback to ensure results improve year on year
- Schedule and conduct plant meetings (salaried and hourly populations); foster employee engagement and ensure that business and operational goals are effectively communicated to all employees
- Demonstrate and deliver strong leadership through utilizing the GE store and Global Network to bring in non-subsea business to meet or exceed plant utilization and recovery
- Support site leaders in strategic planning of manpower, supporting staff development and succession planning
- Drive the annual Session C (Talent Management and Succession Planning Processes) acting as a business Talent Champion at all times
- Lead the setting of the annual manufacturing budget setting processes (Blue Print Reviews, Session 2, Op Plan and monthly business reviews)
- Ensure sufficient capacity exists to meet production output targets
- Champion Brilliant Factory and digital strategy and maintain status as 1 of the top 100 GE sites worldwide. Execute Lean and digital roadmap strategy and attain Brilliant Factory status by 2019
- Proven Manufacturing/Engineering background
- Preferable Degree qualification minimum HNC or equivalent knowledge and experience
- Experience of working successfully and leading others in a dynamic, rapidly changing environment
- Track record of developing strategy and driving manufacturing excellence
- Effective in engaging with peers within the broader business network to share in best practice, lessons learned and to exploit business capability
- Effective in engaging hourly and salaried workforce
- Track record of developing others
- Strong leadership skill, dynamic, action./results focused
- Safety leader
- Process Improvement background with experience/qualifications in Six Sigma/Lean Manufacturing
- Preferably Manufacturing/ Engineering degree or Masters or equivalent knowledge and experience
- Track record of moving an organization to a higher level of success
- Ability to perform and contribute in a matrix team environment
210
Plant Manager Resume Examples & Samples
- Monitors operations for efficiency and safety ensuring that all applicable regulatory requirements are met/followed
- Drives improvements in plant operations, manufacturing processes and standardized work procedures leading to productivity and efficiency gains through application of Lean Tools
- Establishes and directs plant policies and procedures
- Drives all company safety policies, practices and procedures to ensure 100% compliance
- Facilitates Lean Six Sigma process improvement opportunities throughout the plant and be the plant ambassador for quality and process excellence
- Full P&L responsibility; works closely with finance and sales & marketing to partner towards sales objectives
- Bachelor’s degree in Business or Operations Management
- Intermediate computer skills in programs such as MS Word, MS Excel, and Outlook are required, fast, and accurate data entry skills
- Strong time management skills
211
Plant Manager Resume Examples & Samples
- 10+ years as a Site or Plant Manager in a Manufacturing setting
- Chemical or Plastics experience preferred
- 5s and/or Lean Manufacturing experience
212
Plant Manager Resume Examples & Samples
- At least 10 years of Plant Management experience
- P&L experience and experience with cost cutting measures
- 5S and/or Lean Manufacturing experience
213
Plant Manager Resume Examples & Samples
- THIS POSITION REQUIRES US CITIZENSHIP OR GREEN CARD HOLDER**
- B. Eng Mechanical Engineering or equivalent
- Recent experience of manageing a team in a porduction enviornemnt
- Familiarity with gathering and analyzing production, quality and maintenance data
- Regular experince of compiling and presenting production and financial reports
- Interpersonal Skills: must be able to speak with employees, other department managers and senior management
- Leadership Skills: must be able to motivate employees to keep operations running smoothly
- Problem-Solving Skills: must be able to quickly ascertain a situation and be decisive in solving it, such as identifying defects in the production line
- Time Management: face production deadlines, shipping dates and more and must manage their time accordingly
214
Plant Manager Resume Examples & Samples
- Bachelor’s degree or higher in a technical or science discipline from an accredited university
- Minimum seven (7) years of manufacturing engineering experience
- Minimum three (3) years of production management experience
- Previous 3M Plant manager assignments
- Master's degree in Engineering or Business management
- Experience in leading Strategic and organizational development, operational excellence, lean implementation, Financial accounting,
- Demonstrated history of leading high performance teams
215
Plant Manager Resume Examples & Samples
- Safety and Employee Focus - Manage & promote Plant, Business Unit & Corporate programs and processes. Ensure implementation of Oldcastle Enclosure Solutions philosophy of sincere concern for the health and safety of all employees
- Customer Service and Product Quality Management - Provide leadership for the business unit in creating and communicating superior value for our customers. Manage resolving customer complaints and concerns and help to identify root cause and implement corrective action for product and service offerings that do not conform to the expectation of internal and external customers
- Operating Excellence - Manage the facility within the agreed upon budgeted cost for expense, capital, and staffing guidelines. Lead continuous improvement efforts in production, product quality, maintenance reliability, housekeeping and logistics through root cause analysis (RCA). Lead maintenance team to achieve world class performance in machine availability
- Growth - Identify key Capital investment projects to meet current and future production capacity requirements in conjunction with strategic business objectives and forecasts of sales growth
- People & Team Development- Hire, train, develop and engage people so they have opportunity to learn and achieve their maximum potential to create highly effective, high performing teams. Provide leadership to staff, assessing performance, and directing all operational activities
216
Plant Manager Resume Examples & Samples
- Develop and implement a lean conversion strategy that will drive the necessary results to support the site’s Policy Deployment Matrix and to support our Quality, Supply, Responsiveness, Cost, and Organizational Excellence Operating Imperatives
- Develop communication and performance management methodologies which serve to keep the value streams informed relative to business requirements, performance and how the Danaher Business Systems (DBS) is used to exploit core competencies and create competitive advantages
- Review financial statements, sales and activity reports, and other performance data to measure productivity and goal achievement and to determine areas needing cost reduction and program improvement
- Create an organizational development strategy which will drive the necessary skills and competencies in the workforce to meet its customer requirements
- Provide successful implementation of Six-Sigma and Lean Manufacturing principles and practices
- Provide coaching and development opportunities for direct reports that will allow each individuals potential to be maximized and used effectively
- Work with cross-functional teams in order to drive new products into manufacturing to reduce time to market and maximize our profit and return on investment models
- Develop a relationship based on trust, mutual respect and business requirements
- Effectively lead the organization through significant change
- Manage site budget and meet and or exceed financial targets
- Policy compliance
- Ensure a safe working environment exists consistent with OSHA and safety equipment is maintained and effectively used
- Ensure the adherence to environmental regulations and best practices
- Responsible for making business decisions which will improve product quality yield and reduce waste
- Ensure the correct use of the facility, buildings, machinery, equipment and company property, and consistent with city permits and regulations
- Ensure building and property security is maintained
- Assure emergency information is current with local authorities such as Regulatory, Police, Fire Department, etc
- Carries out supervisory responsibilities in accordance with the organization's policies and applicable laws
- Dealing calmly and effectively with high stress situations
- Excellent interpersonal skills to interact effectively with all departments and levels of management
- Result driven and detail oriented with strong analytical abilities
- Active listener giving full attention to what other people are saying, taking time to understand the points being made, asking questions as appropriate
- Time management skills managing one's own time and the time of others
- Critical thinker using logic and reasoning to identify the strengths and weaknesses of alternative solutions, conclusions or approaches to problems
- Monitoring performance to make improvements or take corrective action
- Organizing, planning, and prioritizing work; Developing specific goals and plans
- Takes initiative, has a willingness to take on responsibilities and challenges
- Leads, takes charge, and offers opinions and direction
- Strong negotiation and influential skills
- Analyze data to assure schedules can be obtained
- Computer skills in handling spreadsheets, presentations, and new systems
- Applicable safety trainings such as: RCRA, DOT, etc
- 15+ years of experience in a manufacturing environment showing progressive increase in responsibilities over a broad array of manufacturing disciplines
- 10+ years’ experience in a management-leadership role to include 6+ direct reports
- 6+ years of Knowledge of 5S, Lean Manufacturing, Kepner Tregoe and/or Six Sigma – to include experience with successful implementation and use of Six-Sigma and Lean Manufacturing principles and practices
- 6+ years of Experience with primary oversight of all manufacturing, supply chain, engineering, and quality management
- 6+ years of Budget management experience to include Knowledge of manufacturing financial metrics
- 6+ years of Experience with Statistical Process Control and OEE (Overall Equipment Effectiveness)
- 6+ years of Knowledge of raw materials, production processes, quality control, costs, and other techniques for maximizing the effective manufacture and distribution of goods
- 6+ years of knowledge of the practical application of engineering science and technology. This includes applying principles, techniques, procedures, and equipment to the design and production of goods
- 6+ years of knowledge of business and management principles involved in strategic planning, resource allocation, human resources modeling, leadership technique, production methods, and coordination of people and resources
- 6+ years of Product knowledge in thin film manufacturing, roll goods manufacturing, web handling experience, batch manufacturing and porous membrane measurement expertise
- 5+ years of ISO 9000 standards and cGMP’s Knowledge
- MBA degree in Mechanical, Chemical, or Industrial Engineering or Science
- Six-Sigma Black Belt certification
217
Plant Manager Resume Examples & Samples
- Ensure the plant's safety and environmental performance meets established goals
- Ensure standards for product quality, equipment and operator performance are maintained and that cost-effective technology is used to maximize production
- Develop employees through training and other programs to create a strong team environment
- Determine what resources are required to successfully implement the operating plan and then secure them
- Ensure plant performs at or below annual budgeted cost levels
- Develop and implement plans to reduce waste, meet applicable regulatory standards and handle emergency situations that may arise at the business site
- Develop a plant operating plan that is consistent with and supports the overall business plan
- Develop capital plan to improve and expand plant operations
- Act as a primary technical contact to raw material suppliers
- Represent PolyOne to the external community in a professional and positive manner and act as a first point of contact to local authorities in respect of any legal matters
218
Plant Manager Resume Examples & Samples
- Bachelor’s degree in Engineering (highly preferred), Supply Chain or other related field
- 5-7 years overall manufacturing experience
- Experience in a supervisory or lead role is highly desired, specifically in associate development and safety
- Experience in the following functional areas is required: budgetary, capital planning, P & L responsibilities, associate development, and safety
- Experience in the following functional areas is preferred but not required: commodity/processing plant management, inventory controls management, sales and customer service
- Working knowledge of all facets of manufacturing including continuous improvement, team building, safety, associate relations, quality, customer service, purchasing, distribution, marketing and financials
219
Plant Manager Resume Examples & Samples
- Support and provide hands-on leadership for operations improvements, optimal production output, manufacturing cost reduction, lowering targeted material levels, health and safety, and environmental compliance
- Oversee and directions operations managers to meet safety, quality, product and cost objectives
- Develop a yearly/monthly business plan with the operations team
- Communicate and executive plan through effective leadership of the management team Benchmark and report progress on a weekly/monthly basis to senior management
- Lead and manage long-term business development for optimization and utilization of equipment and materials for Lindsay Corporation
- Adhere to and ensure on-time delivery to the customer
- Manage of all projects within budgets and timeframe
- Demonstrates a passion for the manufacturing/operations business, with a strong work ethic and commitment to Lindsay values
- Demonstrate customer service as a priority
- Coach and mentor employees to be innovative and lead LEAN manufacturing projects
- Communicates concisely
- Applies company policy fairly and objectively
- BS in Business Management. Operations, Engineering, or related degree
- 7+ years of plant supervisory experience in large equipment manufacturing to include project scoping, budgeting, scheduling, logistics, managing quality assurance, management and tracking lean projects
- 5+ years lean manufacturing experience with proven results
- Demonstrate ability to manage traditional manufacturing personalities and styles; ability to synergize the benefits of experience and the concepts of new technology, approaches, and new processes
- Strong interpersonal and relationship building skills, experience at successful high performance team building
- Strong analytical and organization skills, creative problem solving ability
220
Plant Manager Resume Examples & Samples
- Requires education generally equivalent to a Bachelor’s degree (preferably in Engineering, Safety, or Environmental Science) and five plus years related experience in a manufacturing setting
- Requires a minimum of three or more years experience in supervisory capacity
- Six sigma and lean manufacturing experience preferred
221
Plant Manager Resume Examples & Samples
- Plant commissioning and start up experience
- Computerized Maintenance Management System development and implementation
- O&M Contract and/or Power Purchase Agreement management experience
- Demonstrated strong leadership and supervisory skills in the areas of health, safety and environment; change management; employee development; performance management; and team building skills
- Successful P&L experience
- Experience with GE LM6000 aero derivative gas turbines with SPRINT and high temp SCR's, highly desirable
- Demonstrated knowledge of power markets
- Demonstrated budget development
- Effective communicator
- Possesses optimistic 'can do' attitude
- Accepts responsibility for successes and failures
- Shares credit and recognition
- Demonstrates authority and asserts influence over events to achieve goals
- Inspires others' commitment and values differences in people
- Ability to set priorities and goals
- Open to ideas from anywhere
- Utilizes individual employee strengths to maximize team performance
- Provides frequent candid feedback and coaching
- Competent computer skills
- Bachelor degree in engineering and/or business management desired but will consider solid equivalent experience
- Minimum of 15 years’ experience in Power Plant O&M
- Minimum of 5 years combined cycle and/or peaking plant experience
- Minimum of 5 years of Power Plant related leadership experience or an equivalent
- Have and maintain a valid driver's license
- Provide a driver's abstract for review
- Successfully complete a security clearance/criminal record check
222
Plant Manager Resume Examples & Samples
- Responsible for plant performance in accordance with SBA objectives for absorption, manufacturing variances, safety, quality, sustainability, cost center budgets, and capital project management
- Responsible for implementation and advancement of continuous improvement work system and practices
- Responsible for development and advancement of JMS culture across the organization
- Responsible for managing the customer-supplier relationships with corporate services, marketing, research and development, engineering and our external suppliers and vendors
- Responsible for staffing and professional development of plant leaders
- Responsible for developing the plant vision and master plan, capital budget, expense budget, and other strategic planning
- Manage the relationship with local city representatives to ensure compliance with all regulations and maintain positive community relations
- Own Safety Key Element 1, Quality Key Element 1, and Leadership Pillar; sets the standard for safety and quality across the organization
- At least 10 years of manufacturing experience is required
- Continuous improvement, TPM, Lean Six Sigma and/or other experience with the implementation of High Performing Work Systems is required
- Successful experience leading, coaching and managing leaders
223
Plant Manager Resume Examples & Samples
- Responsible for P&L/Budget management for entire branch
- Supervise and motivate a large staff of managers, employees and temporary workers
- Monitor and manage all revenues and expenses that impact P&L performance
- Ensure that customer's service expectations are met, including achieving all service levels metrics and quality performance goals
- Communicate and interact with customers and various internal functional departments (i.e. IT, HR, Accounting, etc.) in order to resolve issues, capitalize on opportunities and improve business and service performance
- Ensure customer-specified and CTDI Corporate service level agreements and quality standards are met
- Generate, cultivate and communicate ideas for continual improvement of processes and activities across all areas of the operation
- Prepare various reports and analyses as required by the customer or CTDI internal organizations
- Research and reconcile forecasted financial results with posted General Ledger results as part of the Monthly Close Process
- Support and ensure compliance with CTDI safety programs and initiatives as well as all applicable OSHA and state workplace safety laws
- Ensure compliance with all building security requirements set forth by CTDI and its customers
- Excellent leadership ability
- Strong coaching and employee development skills and experience
- Strong interpersonal skills with the ability to motivate others
- Advanced customer interaction skills with the ability to communicate effectively
- Superior verbal and written communication skills
- Proven organizational and analytical skills
- Proactive problem solving ability
- Strong financial skills/background
- Results driven mentality
224
Plant Manager Resume Examples & Samples
- Will oversee all daily operations of the plant from production and manufacturing to ensuring polices and procedure area followed. Develop processes that will maximize stewardship, safety, quality and productivity
- Increasing production, assets capacity and flexibility while minimizing costs and maintaining quality standards
- Planning, organizing, directing and running optimum day to day operations to exceed customers expectations
- Be responsible for production output, product quality and on time shipping
- Allocate resources effectively and fully utilize assets to produce optimal results
- Implement strategies in alignment with strategic initiatives and provide a clear sense of direction and focus
- Share a trusting relationship with workgroup
- Commit to plant safety procedures
- Develop systems and processes that track and optimize productivity and standards, metrics and performance targets to ensure effective return on assets
- Develop growth plans for the plant, as well as manage growth projects
- Responsibility for Business Management Reviews
- Manufacturing management: ESH, Quality, Finance, Supply Chain, Operations
- Responsible to transmit company´s policy to the entire team inside the plant (Ethic, quality, compliance)
- Responsible for the annual Budget and financial result of the Unit
- Responsible for the elaboration for the plant Strategic Plan, with the correspondent targets deployments between Departments in order to reach the expected results in terms of Profitability, Production Efficiency, Quality Improvement and Customer/Employees Satisfaction
- Define the personnel evolution of all directed reported persons (Managers and Coordinators), and support them with their correspondent strategies inside their teams
- Bachelor degree in business administration, engineering, or technology
- Minimum 10 years experience in manufacturing or related field
- Adequate knowledge of business and management (budgeting, strategic planning, resource allocation and human resources)
- Be knowledgeable of safety, quality, productivity, demand creation and inventory
- Ability to create accountability and lead bye example
- Have a comprehensive technical financial concepts
- Strong team building and people management skills
- Bilingual: English- Spanish
- Willingness and ability to travel, both domestically & Internationally
- Experience working in a Lean Manufacturing Environment
225
Plant Manager Resume Examples & Samples
- Leads the manufacturing department with full operational and budget responsibility
- Develops and implements key measurables to drive business improvements within the department
- Establishes key strategic activity required to develop the manufacturing department in line with overall business objectives
- Ensures that production efficiency and schedule adherence exceeds the required level
- Ensures maintenance responsiveness and total cost of maintenance exceeds the required level with good management of all third party facilities/site service contracts
- Maintains and develops the delivery of finished products in line with cost, quality, and production schedule requirements
- Leads the development and implementation of significant improvements in department wide processes, procedures, and systems, ensuring adherence by employees and third party contractors, while operating on site
- Develops a continuous improvement philosophy with goals and timelines
- Manages and leads staff in an efficient and flexible manner, ensuring all necessary training and development has been performed and necessary qualifications are in place
- May manage the production operations at a manufacturing facility. Or, may supervise the day-to-day production operations at a manufacturing facility. Typically, oversees Team Lead roles in a single job family or group of job families
- Bachelor’s Degree in Business, Engineering, Engineering Management or Operations Management from an accredited institution
- Must demonstrate strong team building and delegation skills
226
Plant Manager Resume Examples & Samples
- Maintain care, custody, control and safe operation and maintenance of a 242 MW coal fired power plant
- Provide motivation and strong leadership to 58 site personnel. Promote a proactive culture and a safe work environment
- Ensure regulatory and corporate environmental, health and safety compliance
- Manage plant to ensure optimum availability, reliability, and budgetary performance
- Develop and implement procedures and systems for plant personnel to operate and maintain the plant in a safe and effective manner
- Prepare annual budget for customer and effectively manage plant expenditures
- Hire, train, manage, and evaluate an effective workforce
- Delegate and monitor work activities for safe and efficient plant operation
- Effectively execute the O&M contract requirements
- Prepare and submit daily, weekly, monthly, quarterly and annual operational reports and records as required by the O&M contract, Power Purchase Agreement, and the plant owners
- Bachelor's degree in a technical field and at least three years of power plant management experience OR minimum of four years of power plant management experience
- Coal power generation experience
- Highly organized, adaptable to change and the ability to work in a fast-paced environment
227
Plant Manager Resume Examples & Samples
- Directs and mentors the plant leadership team in the performance of their respective roles and consistent with the Eaton Leadership model
- Bachelor's degree from an accredited institution required
- Minimum 5 years of manufacturing leadership experience is required
- Demonstrated written, verbal, and interpersonal communications skills
- Demonstrated success in effectively and confidently providing “leadership” to employees in a constantly changing environment
- Technical degree is preferred
- MS or MBA degree preferred
228
Plant Manager Resume Examples & Samples
- Must have minimum 5 years of experience in a Plant Manager role
- Builds relationships internally and with customers
- Minimum 5+ years of experience managing a plant budget and P&L
- Minimum 5+ years of experience developing and adhering to weekly, monthly, quarterly and yearly KPI's
- Uses mapping to support Process Optimization
229
Plant Manager Resume Examples & Samples
- Establishes plant short and long-range strategic operating objectives. Oversees plant operations including production, field, warehouse, shipping and receiving, maintenance and office management; ensures compliance with federal and state regulations; monitors and enforces quality control standards; forecasts and schedules production; develops and/or approves all plant operating policies
- Directs, manages and develops supervisory personnel to ensure efficient and safe operation of the plant
- Establishes, communicates, implements and enforces safety programs and procedures
- Establishes and monitors plant operating budget; prepares and analyzes profit and loss statements; identifies and implements improvements to positively affect profitability. Recommends purchase of all capital equipment and plant expansion
- Identifies all possible sources of raw material while monitoring quality and cost effectiveness; negotiates supplier and vendor contracts and ensures the quality of all purchased supplies and services
- Establishes and monitors plant compensation levels to ensure internal equity and external competitiveness; reviews subordinate recommendations for salary adjustments of lower level supervisory, office and hourly personnel
- Fosters and maintains a high level of customer service through on-time deliveries, responsiveness to customer needs and ensuring that the quality of the shipped product meets all customer quality requirements
- Communicates with other plant managers to share ideas and resources. Works with Director of Regional Operations, salespeople and corporate office personnel to ensure efficient operation of plant
- Develops and maintains positive community relations: participates in community activities and/or organizations to promote good will and a positive company image
230
Plant Manager Resume Examples & Samples
- Proven experience in Management preferably within an international regulated environment. Proven track record of driving change through team work and strong articulation of a well constructed plan with experience of World Class Manufacturing techniques
- Solid Leadership, Management, Teambuilding and Coaching skills with a passion for achieving results
- Ability to think and operate strategically
- Strong collaborative and influential skills
- Ability to work for the success of the site within the context of being a part of a high performing regional and global team
- Ability to manage with facts and data
- Good knowledge of safety policies and legal regulations within the UK and the EU regarding plant operation
- Fluent in English (spoken and written) – beside country language
- Clear, direct and participative communication style
- Use of relevant computer systems including MRP, MPS, SAP and Microsoft office
- Degree level education or equivalent suitable for this role
- Lean six sigma qualification an advantage
- Demonstrated ability in a senior operations manager role within a regulated company, preferably Aerospace , with significant people management responsibility
- Experience of Manufacturing Planning and Inventory control
- Ability to work in an international / multi-cultural environment
- Ability to drive Continuous Improvement through the execution of DBS (Process Excellence, 6-Sigmas, Kaïzen, etc.)
- Proven experience of driving positive change in a regulated environment whilst respecting the quality standards to ensure competitive advantage
- Proven experience of system and processes implementation (ideally SAP)
- Proven experience of developing and implementing strategic business plans
231
Plant Manager Resume Examples & Samples
- Leadership of Plant Safety through plant Gemba walks with the management team, cascade of safety initiatives to all level of the business and active participation in all matters relating to ESH to achieve a zero incident culture and a zero incident safety culture
- Sets overall plant policies and procedures to ensure effective manufacturing operations
- Develops and maintain a cohesive, efficient operating team. Maintains the operational cadence through tier meetings, SLT meetings, Management Review, Quality Review Meetings, Program Management Reviews, Succession Planning Meetings, Health & Safety meetings, Round Tables with employees etc
- Directs subordinate staff in the performance of their respective roles, utilizing the performance management process APEX, 1:1 meeting etc. to set objectives and agree development plans in order to deliver High Performance from the individual and for Eaton
- Leads the SIOP process at the site in order to ensure good short, medium and long term plans are in place that ensure resources are available when required to meet customer and shareholder requirements. Leads key decisions around inventory management and policies, people resourcing and plant investment
- Represents the company in the local community to enhance its image and reputation through participation in charitable or community projects
- Ensures that the plant achieves World Class Plant recognition by delivery of the Hi5 metrics (Safety – TRCR OTD, CONC, Inventory – DOH, Productivity – FLEX) and implements all Eaton Quality Best Practices and Quality Leading Metrics are at Green as a minimum per the Aerospace Criteria
- Guides strategic development planning at the plant level and ensures alignment with Divisional, Operations and Group plans
- Delivers the Aerospace Division CI Vision. Makes clear the links between the top level aerospace objectives, the division objectives and the site objectives
- Bachelor's degree in technical area or equivalent
- Professional-level competence in operations, management, and technology
- Broad operating, manufacturing, technical and/or functional business and management experience or equivalent
- Leadership experience
- Aerospace background would be an asset
- Good communication skills and ability to communicate at all levels
232
Plant Manager Resume Examples & Samples
- Develop and manage the approved Plant budget to ensure adherence
- Manage Raw material, packaging, work in process inventory, production cost for all finished goods and quality of finished goods
- Manage in plant inventory levels (raw, packaging, WIP, finished goods)
- Customer service levels (on time delivery, customer complaints and etc.)
- Goals to meet or exceed plant safety performance standards
- Production capacity and flexibility to handle various changed in production needs
- Attainment of all Plant Operation Key Performance Indicators (KPI’s) – see below
- Manage staffing levels - use of regular staff and temporaries to ensure availability of needed labor, without incurring overstaffing or understaffing costs
- Capital Investment - prepare and present as needed the justification for capital equipment addition(s) to improve plant effectiveness/efficiencies and the overall footprint value of manufacturing capabilities
- Guide the implementation of and effective use of Production System within the program delivery guidelines
- Development and implementation of projects for equipment, process and people performance improvement in the areas of safety, product cost, delivery, and quality
- Lead and/or participate in delivering the results of special individual or team projects as assigned by the VP of Operations
- Drive improvements in the areas of Safety, Quality, Productivity, Service, and Inventory performance
- Establish and maintain a personal presence on the shop floor - open an effective and positive culture of communications with all regular and temporary staff so that all employees are willing and able to communicate to the Director of Operations all suggestions, ideas, concerns and any other important information
- Ensure that all employees have development plans established and there is proactive training and activities in place to ensure that all employees are incented to take actions to reach his/her full potential as an employee
- Manage all supervisory staff to ensure that objective, fair and honest performance evaluations and personnel improvement plans are developed and communicated in accordance with policy, without delay when required
233
Plant Manager Resume Examples & Samples
- Effective leadership implementing Lean Manufacturing and change management
- Evaluate financial implication of changes made in the operation, with objective of achieving maximum profitability
- Manage, report, document and plan production performance, continuous improvement activities, action plans, strategic plans and employee utilization
- Assist in development of budgets that support Operating Plan
- Ensure that employee and plant conditions are suitable for production
234
Plant Manager Resume Examples & Samples
- 10 years manufacturing operations management experience in a LEAN environment required
- LEAN certification preferred (Green Belt, Black Belt)
- A passion for employee development and improvement
- Excellent Team Building Skills for diverse groups
- Excellent written and verbal communications skills and ability to communicate with those at all levels
- Strategic Planning experience preferred
- Experience managing and leading multiple product lines for a business operation
- Lean and Six Sigma experience preferred
235
Plant Manager Resume Examples & Samples
- You will lead efforts to achieve a “Zero and Beyond” safety culture; eliminate all injuries, and position the plant as a good community partner through our Corporate Social Responsibly efforts
- You will lead and direct all plant operations to meet the performance goals of the business team and corporation through superior leadership and delegation/mentoring of departmental managers
- You will analyze the overall performance of the operation and drive continual improvement in plant performance, resulting in year to year productivity improvements, optimal inventory levels and superior delivery performance
- You will be the standard bearer for our Operational Excellence philosophies driving our lean six sigma efforts to eliminate waste, improve day to day operations and empower all team members with a passion and culture for continual improvement
- You will demonstrates a passion for Talent Management by hiring and developing the best team members and leaders in the industry; both the hourly and salaried ranks
- You will manage labor and employee relations in accordance with the collective agreements, federal/state legislation and corporate policies; ensuring pay rates, promotions, demotions and termination of employment are applied consistently and with due process and diligence
- You will be responsible for reviewing capital, expenses and material/facility usage to ensure the plant operates in a cost effective manner, recommending and approving all major purchases of equipment, material and supplies for the facility
- You will provide direction and lead the preparation of the plant annual business plan and budget. Set objectives for all departments consistent with meeting business plan/metrics
- You will work with sales and product management to optimize customer relations and plant productivity
- You will be expected to perform other related duties as required
236
Plant Manager Resume Examples & Samples
- Supervisory oversight of shift managers and supervisors across all production shifts
- Work with employees to ensure production/yield requirements are met daily
- Analyze, develop, and implement processes to maximize yields and throughputs
- Analyze, develop, and implement processes to minimize downtime, accidents and turnover
- Oversight management of Sanitation procedures including understanding of chemicals used in sanitation processes and cleaning procedures required for different pieces of machinery
- Review and assess daily reporting for all shifts (i.e. production reports, attendance/staffing report, etc.) as necessary
- Know, understand and effectively implement requirements and expectations
- Assure compliance for/to customer, regulatory requirements, production specifications, and management requirements
- Maintain effective practices to ensure safety of all employees
- Work with Quality Assurance Department ensuring all food safety, USDA and customer specifications requirements are met
- Participate in the development of all employees within designated area
- Minimizes downtime, accidents and turnover
- Plan and implement process improvements
- Work to build and maintain effective relationships with employees and customers
- Enforce Company policies and procedures
- Administer corrective action plans or disciplinary action on a consistent basis
- 4 - 8 direct reports
- 125 - 250 indirect reports
- Associate Degree from an accredited institution
- 7+ years relevant manufacturing experience
- Bachelor of Science Degree in Operations Management, Food Science, or related technical discipline from an accredited institution
- 5+ years relevant experience in a food manufacturing or similar environment
- 5+ years previous supervisory/leadership experience
- Knowledge of cook operations and other food processing systems, as well as SPC and CAD
- Knowledge and experience with sausage manufacturing and associated equipment
- Knowledge of regulatory requirements, especially those governing the food industry and a thorough understanding of the required support for maintaining utility function, such as various refrigeration/freezing system, boilers, HVAC, PLC controls etc
- High level of interpersonal skills
- Demonstrated high level of organizational skills
237
Plant Manager Resume Examples & Samples
- General Manager fully accountable for the corresponding operational P&L and BS
- Having direct responsibility of Production, Quality, Logistic, HR, Methods and Maintenance
- Functional responsibility of Finance & Controlling
- Strong Management and Leadership competences ensuring the successful achievement of the Business Unit short and long term goals in accordance with the respective yearly Forecast and 3 years Strategic Planning
- Tasks and Responsibilities
- Responsible for S@W and HSE
- Strict Quality management and Customer Satisfaction
- Ensure compliance with local external legislation and regulations
- Ensure successful internal and external mandatory Audit certifications
- Plan, develop and implement new strategies and tools developed with support of Business Unit to meet customer expectations and organizational performance plans within agreed budgets and timescales
- Establish and maintain appropriate controlling and systems for measuring operational management and development
- Optimize manufacturing processes, cycle times and structures
- Report to Business Unit on organizational plans and performance figures
- Direct responsibility of HR topics. All the matters related to organizational training, recruitment and selection of candidates is looked after by the Plant manager in consultation with the HR supervisor
- The responsibility of a Plant manager is to actively participate in the feedback session and performance evaluation of the employees. Plant manager also monitor and track the performance and achievements of the employees as well of the entire company
- A Plant manager ensures that matters related to finance and transactions are within his supervision
- The Plant manager also direct people to various goals and targets
- Hiring good middle level Managers is another important duty of Plant manager
- Middle level Managers assist the Plant manager in managing the different tasks. Besides these, keeping a record and check of firm's growth is also done by the Plant manager
- Bullet 2
- Bullet 3
- Automotive working experience
- University degree or above, engineering education preferably with additional commercial education or skills
- Minimum five years of experience in a similar position; preferably in an international company, manufacturing industry, developing structures, processes, and reporting tools
- Strong affinity to production, sales and organization
- Decisive and strong implementer with excellent project management and organizational skills
- High competence in recruiting and developing shop floor operators and supporting staff
- Excellent communicator (also English) with a natural affinity for international companies and their business culture
- Responsible corporate actor and self-starting operator
- Aged between 35-45
- Good in English (both spoken and written)
- Shows the ability to translate local business objectives into plans
- Develops various alternatives to solve problems
- Sets objectives and goals and breaks down work into process steps (schedules, measures, follow up, etc)
- Is open to change and deals constructively with change
- Entrusts responsibilities to the right people, based on their abilities
- Shares ideas and opinions openly with others and invites them to do the same
- Reacts appropriately/positively when confronted with frustrations, opposition,pressure
- Key Interfaces and Stakeholders
- Outside Customers
- BU Boots Managers and Specialists
- Trelleborg key stakeholders such as ME, S@W, Talent Management
- Geography to cover and Travel requirements
- The responsibility is primarily local
- Travelling abroad is required (5 to 6 times per year during 2-4 days’ max)
- Behavioral Characteristics
- Strong analysis and negotiation skills
- Outstanding interpersonal skills
- Entrepreneurial and goal-oriented
- Mature, highly initiative and strong sense of responsibility
- Likes to be challenged
- Likes diversity, intercultural exchanges and is open minded
- 2017/04/07
238
Plant Manager Resume Examples & Samples
- Manage, train, provide performance feedback and assign duties of direct reports to ensure
- Bachelor’s degree in engineering, business or related field; or 4 years manufacturing
- 7 years manufacturing operations leadership role experience
- Total Work Systems development and refinement experience
- Knowledge of health, safety and environmental management system elements
- Demonstrated successful ability to build positive partnerships and work collaboratively with
- Excellent interpersonal and communication skills with the ability to interact with all levels of
- Familiarity with the cabinet/countertop industry and product
- Six Sigma Black Belt or Green Belt Certification or comparable problem solving certification
239
Plant Manager Resume Examples & Samples
- Directs and manages plant operations for production, maintenance, quality and shipping and receiving
- Coordinates plant activities through planning with departmental managers to insure the total manufacturing objectives are accomplished in a timely and cost effective manner
- Ensures safety of all residents, visitors and staff
- Ensures the interior and exterior of all buildings and grounds are maintained
- Must pass pre-employment tests if applicable
- Typically requires BS/BA in related discipline. Generally 7+ years experience in related field. May require certification. Advanced degree may offset less experience in some disciplines
- Experience with scheduling experience
- Ability to multitask
240
Plant Manager Resume Examples & Samples
- Establishes an organizational structure by assigning responsibilities, delegating authority and selecting, orienting and training direct reports. Leads facility organizational staff by coaching, counseling, motivating and disciplining as needed; plans, monitors and appraises job results; directs and maintains activities designed to achieve and maintain high employee morale; fosters intra- and inter-department cooperation
- Achieves financial objectives by scheduling expenditures, analyzing variances, and initiating corrective actions; requesting assistance from internal financial support as needed
- Ensures a safe, clean, and secure working environment by establishing and enforcing procedures, rules and regulations; by initiating fixed capital requests; monitors all production related safety and security systems and procedures on a regular basis; chairs plant safety meetings that evaluate plant machinery, equipment and working conditions
- Ensures compliance with Corporate Quality procedures by initiating and monitoring related training programs. Ensures compliance with all pertinent corporate, federal, state and local regulations and licensing requirements by keeping abreast of current and developing requirements; instituting and monitoring internal compliance programs and procedures; ensures that plant tours for visiting external regulators are properly conducted
- Monitors predetermined preventative maintenance measures designed to minimize equipment related downtime supporting production/warehouse. Monitors & supports overall building maintenance, security, and cafeteria services, coordinating with external contractors/agencies where necessary
- Meets customer requirements by managing plant operations according to established company policy; directs and coordinates all activities within the plant: coordinates requirements with leadership, engineering, supply chain, production, shipping/receiving, maintenance, marketing, and quality functions
- Minimizes and resolves external business related complaints by working with Divisional Quality staff to investigate and resolve customer issues
- Strives for continuous improvement by using Lean Manufacturing techniques (Kaizen, 5S, etc.) to analyze new or alternative ways to improve operations; incorporates staff suggestions into analysis by responding to audit activities in a constructive manner and use findings to improve operations where possible
- Contributes in a team effort by performing according to the guidelines outlined in the Medline Code of Business Conduct, the GMP and other directives; supporting the directives and decisions of higher level management and accomplishing other duties as assigned
- Supports the Medline business imperatives of Growth, Operational Excellence, Leadership Excellence and Customer Focus, by acting with integrity, treating everyone with mutual respect, exhibiting a genuine commitment to the success of all employees, and delivering satisfaction to our customers through teamwork, innovation and continuous improvement: this will be accomplished while acting safely
- Bachelor's degree plus 10 years of Operations related experience, with the majority being in a plant (production/warehouse) environment
- 5 to 7 years management experience. Working knowledge of Lean Manufacturing principles. APICS Certification a plus
- Extremely high sense of urgency, and positive approach to help instill both in all employees. Capable of handling multiple priorities and extensive time demands. Must have a high level of personal integrity
- Strong work ethic, with hands-on approach and attention to detail
- Possess strong initiative, and ability to work independently under general guidelines and supervision
- Effective interpersonal skills as demonstrated through prior management experience
- Ability to influence people in their opinions, attitude or judgements; to generalize, evaluate and make decisions in stressful situations
- Ability to coach/mentor/develop employees at all levels
- Ability to effectively read, write and verbally communicate in English, Bilingual Spanish a plus
- Above average organizing, analyzing and computer skills (Microsoft Office)
- Ability to attend training and meetings in Nuevo Laredo, Mexico
- Ability to travel up to 15% of the time
241
Plant Manager Resume Examples & Samples
- Candidates must have clearly demonstrated strong leadership characteristics, planning and scheduling skills necessary to successfully manage a ~750,000 tpy sand and gravel operation
- Effectively and proactively administer Lehigh Hanson’s safety program ensuring compliance with MSHA rules and regulations, including but not limited to root cause analysis, develop and share best practices, train employees to identify and address potential hazards
- Manage direct reports under the guidelines of Lehigh Hanson HR Policies and Procedures
- Instill a culture of continuous improvement. Identify opportunities to improve operational efficiencies, track improvement progress and quantify financial impacts, encourage and reward behaviors that progress a culture of innovation and improvement
- Experience managing a P&L is a must. Detailed monthly financial progress updates, accuracy in budgeting cost forecasting and production by product forecasting are integral to our success
- Coordination with sales and quality control are critical. Inventory accounting accuracy and gradation analysis are expected on a continuous basis
- Oversee the production planning, staffing, and day-to-day manufacturing operations in a cost-effective manner, accurately track and record key performance indicators, troubleshoot and resolve operational, manufacturing, and maintenance problems to ensure minimum costs and prevent operational delays
- Establish key inventoried items needed for all MRO (maintenance, repair and operation) items for the plant, and effectively interact with governmental and regulatory agencies, customers, vendors, Lehigh Hanson management, and neighbors as required
- Bachelor's degree with mining-related discipline or the equivalent in relevant work experience
- At least 5 years of quarry management experience with prior P/L responsibility
- Proficient working knowledge of Microsoft Office products
- Solid understanding of government regulations and demonstrated ability to impact safe working practices
- Close vision (clear vision at 20 inches or less)
- Distance vision (clear vision at 20 feet or more)
- Color vision (ability to identify and distinguish colors)
- Peripheral vision (ability to observe an area that can be seen up and down or to the left and right while eyes are fixed on a given point)
- Depth perception (three-dimensional vision, ability to judge distances and spatial relationships)
- Ability to adjust focus (ability to adjust the eye to bring an object into sharp focus)
242
Plant Manager Resume Examples & Samples
- Establish a culture that supports safety and employee engagement in the business
- Works with staff, trains personnel, management and operational staff in production, maintenance and shipping procedures
- Implements and monitors procedures to maximize plant efficiency while controlling cost of production
- Coordinates necessary loading of trucks
- Manages critical spares and minimizes inventory cost
- Maintains a maintenance backlog and plan for preventive maintenance
- Ensures a safe and clean working environment in the operating facility
- Leads weekly tailgate safety and department meetings
- Audits production, maintenance and shipping processes to promote best practices
- Works with operations management to develop yearly budgets
- Creates and oversees a detailed maintenance plan
243
Plant Manager Resume Examples & Samples
- Delivery and Capacity Planning/On Time To Customer Request (OTTR),
- Developing short and long range 'Best In Class' / 'World Class' vision, mission, site value proposition and supporting plans to maximize the utilization of all site assets and assure availability of resources in accordance with the changing business environment
- Strong believer in personal learning and self development and has a strong sense of 'self knowledge'
- 10 years of progressive manufacturing management experience
- 5 years experience as a Plant Manager, with Manufacturing Site Leadership background, at a manufacturing facility with 400+ employees
- 5 years experience in Total Quality, Six Sigma or Lean
- BS in Engineering or operations management
- Demonstrated ability to manage multiple, complex projects and changing priorities, make sound decisions and work effectively in a technical environment
- Ability to develop in-depth understanding and application of Honeywell core processes - Strategic Planning (STRAP), Annual Operating Plan (AOP), Operating System (HOS) and Management Resources Review (MRR)
- Experience with the tasks and culture change associated with 'turn around' and / or start-up facilities
- Professional experience that includes exposure to multiple business models and / or varying company settings
244
Plant Manager Resume Examples & Samples
- Directs activities of production team, sets priorities for day to day equipment maintenance, and maintains appropriate production staffing as needed to meet company goals
- Responsible for shop production schedules and conducts production meetings including supervisors’ meetings working closely with the Customer Service Manager
- Ensures customers’ needs are appropriately met by shipping to schedule with minimum turnaround time and a high degree of quality, working closely with the Quality Manager
- Directs maintenance activities in regard to shop equipment, instrumentation, facilities and personnel
- Responsible for communicating and ensuring policy & procedures are adhered to by plant
- Responsible for enforcing company handbook and communicates on matters relating to discipline
- Responsible for maintaining an effective energy conservation program, maintaining controls over labor costs, directs industrial services and approves expenditures within established company guidelines under the guidance of the General Manager
- Responsible for ensuring the safe operation of equipment, safe work habits of the employees and administering the safety program within the guidelines established by the company and General Manager
- Responsible for purchasing and/or approving materials for shop, facilities, tooling, fixtures, etc., under the guidance of the General Manager
- Participates in staff meetings as a member of management
- Experience: Requires extensive knowledge of heat treating, operations management, metallurgy, inspection and customer needs through technical and advanced training, seminars, college, B.S.M.E. (metallurgy) and/or equivalent work experience
- Minimum five years practical experience in heat treatment of alloys, including aluminum, titanium and exotic metals or related and the ability to manage multi-level employees and functions with a minimum of five years’ experience in a supervisory role
- Language skills: Must be able to communicate effectively verbally and written, including reports as required, attend staff meetings and interface with other departments
- Requires basic knowledge of metals, furnaces and capabilities of all plant equipment
- Must be knowledgeable of tooling needs and costs
- Must be able to read and interpret blueprints and customer specifications
- Must be knowledgeable in customer needs, material handling procedures, and quality control
- Must possess knowledge and have experience in industrial safety programs, OSHA regulations, company rules and compliance to State and Federal labor laws relating to employment, discipline, etc
- Must possess ability to ensure compliance of company rules as established by Corporate and the General Manager
- Must be effective in promoting and maintaining positive employee relations, and have basic understanding of company rules, procedures, benefits and pay policies as related to production employees
245
Plant Manager Resume Examples & Samples
- Management of site Health & Safety Environmental performance in accordance contract and Regulatory requirements
- Manages the financial results and requirements of the plant's business and operations to ensure that revenue and expense goals are met (or exceeded) as established in the annual business plan
- Oversees the development of capital and operating budgets. Provides for business projections as required
- Develops an annual operating budget for the facility with input from Group Operations Director, finance, Chief Operating Engineer
- Sets goals and objectives for the plant for financial, environmental, health and safety, and personnel results
- Monitors activities of the utilities and other businesses in the region regarding developments, pricing and potential expansion
- Monitors wage levels on a regional industry basis
- Meets or beats budgeted annual operating and maintenance expenses as determined in the annual business plan
- Ensures all contract agreements with parties are properly complied with, to protect the long-term interests of the client and the company
- Oversees the implementation of personnel policies, plans and programs for the plant
- Ensures the morale of all plant staff members is maximized to the successful completion of facility goals
- Implements and assists in the development of all required corporate policies, practices and procedures
- Writing, reviewing and revising operating and related procedures. Ensures procedural compliance in the conduct of plant operations, maintenance and personnel administration. Investigates plant problems, incidents, accidents and unusual events and provides analysis, recommendations, reports and develops and administrates appropriate follow-up plans
- Plans, directs and supervises routine preventive and predictive maintenance on all systems and equipment; supports corrective maintenance efforts on selected equipment. Reviews maintenance backlog and provides priorities to Chief Operating Engineer. Plans, directs and performs housekeeping duties. Establish and maintain housekeeping standards. Ensures all in-plant switching and tagging of equipment in accordance with approved procedures and prudent operations and maintenance practices. Maintains complete and accurate reports of downtime, outages, repair requirements and production and performance indices
- Plans, directs and supervises outage and shutdown activities including coordination with client, regulators, contractors, specialist consultants etc
- Oversees testing of plant systems and components executed by on-site staff and/or by contractors. Review data based on established standards and/or sound power plant practices. Conducts routine tours of the plant to inspect equipment; provide direction, supervision and feedback to employees; and ensures that all safety rules and plant procedures are followed, and are in accordance with corporate standards. Review incident reports for equipment malfunctions/employee accidents, and provide safety and environmental leadership for site
- Communicates with other Company personnel on-site and at other locations. Represents the Company in dealing with the public, steam and power customers, vendors, contractors, regulators and other non-Company personnel
- Conceives, develops and evaluates on-the-job and classroom training in operations-related subjects. Prepares lesson plans, handouts, visual aids, examinations, qualification standards and other material related to employee training and development
- Recruiting, screening, and interviewing candidates for employment on-site or at other locations. Plans, directs and supervises operation of plant and ensures proper licensing and qualifications are met according to local and federal regulations
- Maintains logs, records and data sheets; prepares and reviews reports, trends, timesheets, material requisitions, work orders and other administrative documents related to power and steam production, as well as reports required by Client and by Regulation
- Contributes to business development efforts by visiting with potential clients, attending tradeshows and conferences, and preparing budgets for opportunities
- A candidate with a First Class Ontario Standardized Power Engineering Certification recognized in Ontario is preferred
- LM6000 Gas Turbines operation and maintenance
- Commissioning of power generation equipment
- OEM Long-Term service agreement management
- Ontario energy market (IESO / OEB) rules and regulations
- NERC standards
- Unionized environment
- Any or all of District Energy, Energy – From- Waste, Alternative Energy projects
- New plant operational setup
246
Plant Manager Resume Examples & Samples
- Maintaining a safe work environment and drives efforts to achieve an accident free workplace
- Leading the plant in achieving or exceeding production goals, throughput, yield, cost, and quality
- Overseeing hiring, employee relations, and employee development activities, ensuring an effective and productive workforce
- Promoting and ensuring an environmentally compliant work environment
- Leading continuous improvement initiatives using tools such as Lean manufacturing, Six Sigma, and other process improvement techniques
- Managing the plant against the established operational and capital budgets, ensuring financial goals are met or exceeded
- Directing maintenance and engineering initiatives to optimize the equipment performance, quality, customer satisfaction, and reliability
- Bachelor’s degree in engineering, business, or a related field
- 10+ years of production management experience in a multi-shift environment, with at least 3 years of experience working as a plant manager
- Past experience leading and managing a diverse group of functions, including operations/production, engineering, materials and distribution, maintenance and reliability, quality, human resources, environmental health and safety, and controller
- Comprehensive knowledge of Six Sigma, Lean, optimization, and other process improvement processes
- Strong management and leadership skills and demonstrated ability to effectively manage a diverse group of employees and build a team culture
- Experience managing operating costs and capital and maintenance budgets
- Strong interpersonal and communications skills
- Experience in flooring, paper, plastics, or similar manufacturing industry
- Union experience
247
Plant Manager Resume Examples & Samples
- Bachelor degree or equivalent experience is preferred
- Six Sigma experience is preferred
- 5+ years operations/maintenance experience
- 2+ years management experience
- Military experience in these areas will be considered
- Sound knowledge of process management, asset management and product knowledge
- Sharp mechanical aptitude
- Working knowledge of cryogenics and their characteristics
- Strong knowledge of California EPA requirements
- Demonstrated excellent people leadership skills
- Good and effective communications skills - written and verbal
- Quality control proficiency
- Good understanding of intra-departmental relationships
- Technical knowledge of hydraulics, piping, compressors, PLC's, tanks and other related equipment
- Desire to get "Hands On" to troubleshoot issues in the plant with the process systems
- Ability to read and understand P&IDs and electrical schematics is required. Experience in troubleshooting PLCs and basic electrical circuits and control systems is a significant plus
- Understanding and knowledge of applicable government regulations and ability to rigorously comply to the requirements
- Demonstrated success using Six Sigma or other process improvement initiative is a significant advantage
248
Plant Manager Resume Examples & Samples
- All aspects of costing process
- Develop of new product costs
- Analyzing actual manufacturing costs, compare standard costs to actual production costs
- Absorption and PPV reports for all manufacturing facilities
- Weekly and Monthly inventory analytical reports
- Coordinate physical inventory counts for each site
- Guarantee all transactions relating to all aspects of the plant and inventories are following the proper protocols
- Provide financial analysis for strategic decisions involving acquisitions
- Drive cost savings by identifying and analyzing operations cost drivers
- Report on performance versus the annual budget
- Rolling quarterly forecast with variance analysis
- Work with management on the development of the Annual Capital Plan
- Assist to develop a currency management program
- B.S. in Accounting or Finance required
- MBA or CPA preferred
- 8+ years in manufacturing or cpg environment with plant experience
- Experience with Inventory Management
- FP&A experience surrounding the manufacturing process
249
Plant Manager Resume Examples & Samples
- 15% Production safety; create a culture for safety at the site – with emphasize on housekeeping and good maintenance practizes. Further description
- Lead employee and food/feed safety program standards and goals for the plant. Accountable for all internal/external operating/regulatory procedures on employee safety and food/feed safety including strategic and tactical execution in alignment with Corporate Environment, Health and Safety (EHS) and Food Safety, Quality and Regulatory (FSQR) Functions as well as government regulations
- Collaborate with EHS/FSQR experts to ensure the most effective risk mitigation plans and regulatory compliance strategies are in place
- Masters degree or commensurate experience
- 10+ years relevant experience within operations – with focus on manufacturing
- Knowledge and experience within people management (expectations & coaching, safety, quality, productivity, planning processes and inventory control etc.)
- Adequate knowledge of business and management principles (budgeting, strategic planning, resource allocation and human resources)
- Strong written and verbal communication skills in English and Norwegian
- Demonstrated strong leadership skills
- Prior supervisor experience and experience in developing talents – and specifically develop successors in all vital roles
- Interpersonal skills: able to speak and build relationship with employees, other department managers and senior management
- Leadership skills: able to motivate employees to keep operations running smoothly. Ability to create accountability and to lead by example. Strong team building, decision-making and people management skills. Able to develop and stretch the skills of your team members. Demonstrated ability to build a functional leadership team for the site
- Problem solving skills: able to quickly asess a situation and effectively solving it
- Prior experience in managing multiple projects
- Proven work experience as plant manager
- Proven managariel experience
- Preferably some knowledge about industry standard equipment and technical expertise
250
Plant Manager Resume Examples & Samples
- Bachelor’s degree in engineering or equivalent technical discipline is required; MBA
- Minimum of 10 to 15 years experience in manufacturing operations required and a minimum of 5 years in a manufacturing/plant operations leadership role, preferably as Plant Manager of a medium to small sized non-union manufacturing plant
- Preferably Six Sigma greenbelt certified