Manager Plant Resume Samples
4.7
(157 votes) for
Manager Plant Resume Samples
The Guide To Resume Tailoring
Guide the recruiter to the conclusion that you are the best candidate for the manager plant job. It’s actually very simple. Tailor your resume by picking relevant responsibilities from the examples below and then add your accomplishments. This way, you can position yourself in the best way to get hired.
Craft your perfect resume by picking job responsibilities written by professional recruiters
Pick from the thousands of curated job responsibilities used by the leading companies
Tailor your resume & cover letter with wording that best fits for each job you apply
Resume Builder
Create a Resume in Minutes with Professional Resume Templates
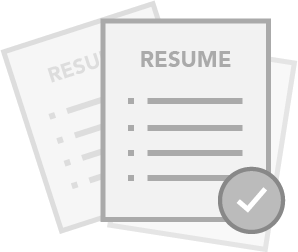
CHOOSE THE BEST TEMPLATE
- Choose from 15 Leading Templates. No need to think about design details.
USE PRE-WRITTEN BULLET POINTS
- Select from thousands of pre-written bullet points.
SAVE YOUR DOCUMENTS IN PDF FILES
- Instantly download in PDF format or share a custom link.
LP
L Pfeffer
Lurline
Pfeffer
616 Emely Bridge
Detroit
MI
+1 (555) 976 2835
616 Emely Bridge
Detroit
MI
Phone
p
+1 (555) 976 2835
Experience
Experience
San Francisco, CA
Plant Manager PAS
San Francisco, CA
Homenick-Cummerata
San Francisco, CA
Plant Manager PAS
- Internally work together with Regional Management Team incl. Engineering, Finance, HR, Lean, Quality & HSE, IS IT, Purchasing and other Plant Managers
- Manage, coach, develop the people in to support the Strategy
- Manage Plants to deliver the agreed business and operational plans
- Represent the company in living the values, practice and lead by example
- Foster a culture of continuous improvement and ensure the effective execution of CI plans
- Lead the development and implementation of common processes, systems, standards and tools in line with Divisional and Corporate standards
- Track financial status to ensure targets are achieved
Detroit, MI
Plant Manager, Thermal
Detroit, MI
Schroeder-Wintheiser
Detroit, MI
Plant Manager, Thermal
- Support the establishment and enforcement of safe working conditions and practice safe work habits in all activities
- Provide long range planning for maintenance, repair and capital improvement projects in conjunction with engineering
- Lead performance tests, equipment performance monitoring and trending
- Provide technical support of equipment commissioning and start-up
- Establish a rapport with local environmental regulatory officials impacting company operations
- Project lead on site level activities which includes generating, developing, and executing projects within the plants as well as within the Energy Center’s distribution system
- Basic knowledge of industrial water treatment (specialty chemicals and boiler pretreatment) and responsible for cost effective management of associated programs
present
Boston, MA
Manager, Plant Quality
Boston, MA
Becker-Hackett
present
Boston, MA
Manager, Plant Quality
present
- Work to reduce potential for foreign material contamination by identifying potential sources and developing corrective actions to prevent occurrence
- Provide leadership to the plant Performance System; Pillar ownership and Pillar support
- Initiating and leading continuous improvement projects around quality and food safety. Leads UPS process for quality related issues
- Work with our third party distribution warehouses with which we are paired in regard to problems with inbound shipments and other sanitation and GMP issues
- Monitors and maintains the “Hold, Rework and Return” programs
- Develop, implement, monitor and keep current quality assurance and food safety programs in coordination with Corporate Quality and Product Safety group
- Manages quality assurance technicians to maintain adequate support for production
Education
Education
Bachelor’s Degree in Business
Bachelor’s Degree in Business
North Carolina State University
Bachelor’s Degree in Business
Skills
Skills
- Strong computer application skills, network and PC business application software
- Background in statistical process control, basic financial skills and understanding
- Excellent communication, presentation, and negotiation skills
- 7-10 Years technical experience in the food industry
- 3-5 Years Supervisory/Management experience
- Key Leadership Competencies in addition to Ethics/Values and Integrity/Trust. (Action Oriented, Directing Others, Priority Setting, Decision Quality, Organizing, Process Management)
- SQF Practitioner certified; HARPC certified
15 Manager Plant resume templates
Read our complete resume writing guides
1
Solar Plant Manager Resume Examples & Samples
- 30% Leadership: coaching, performance management, engagement. Continue efforts to build high performing team; engage all employees; implementation of BU strategy; people development, champion recognition; collaborate effectively with experience teams and disciplines. Role Model and ensure compliance to laws, regulations and company policies
- 25% Operational Excellence: operations management including product quality; maintenance reliability & energy management; innovation, efficiencies & best practices
- 15% EHS Leadership: ensure compliance and commitment to policies, procedures, and regulations. Provide direction, coaching, support to BBS & Wellness. Environmentally sound adherence to all agency requirements
- 10% Customer Solutions & Innovation: Focus on continuous improvement and process management and cost efficiencies to support positive customer experiences
- 10% Project management, capital planning, P & L: business compliance; develop & meet budgets, develop capital spending requests & project management; aggressively & proactively manage operating expenses. Oversee and direct key projects and initiatives. Ensure capital projects are completed on time and within budget
- 5% Serve as the Cargill representative within the community
- 4 year college degree with 5 or more years Plant Manager experience of a process production facility OR in lieu of degree a minimum of 7 years operations related experience in a plant environment, including 5 of those years in a supervisory role
- Bending, Stooping, Walking, Lifting (50 pounds), Finger Dexterity, Grasping, Pushing, Pulling
- Using a computer and keyboard
- Project management utilizing PPM/PDP process
- Demonstrated ability to lead a diverse workforce
- Demonstrated excellent communication skills (listening, written, verbal, presentation)
- Original, independent thinker with solid analytical skills. Able to manage competing priorities
2
Plant Manager m Resume Examples & Samples
- Accountable for executing HTS objectives within the campus model at Lotte. Translate manufacturing strategy into operational objectives and goals to drive performance improvement on customer satisfaction, Cycle Time reduction, safety, quality, delivery, productivity, cost and working capital management
- Ensure deployment of the Honeywell Operating System for HTS in line with collaborative campus structure involving Honeywell Process Solutions, Smart Metering business and Environmental &Energy Solutions business. Maintain performance levels stated by Honeywell Operating System (lean manufacturing) maturity scorecard for HTS including visual management and the tiered meeting communication process
- Safety: establish safe work practice and company policies and continuously improve the HTS Lotte safety culture and meet / exceed all HSE lagging and leading targets
- Provide leadership for HTS Lotte of initiatives across global Integrated Supply chain in support of business and functional objectives
- Development and deployment of Honeywell core processes including succession planning and strategy deployment (MRR, SDP) for HTS. Lead the HTS Strategy Deployment Planning and execution process including metric alignment to individual employee goals
- Quality: Continuously improve customer quality performance and reduce Cost Of Poor Quality (COPQ)
- Delivery: Drive internal and external On Time To Request (OTTR) to achieve Annual operating plan (AOP) goals
- Productivity: Implement cost improvement strategy and deliver productivity improvements to AOP. Ensure that financial productivity and plant/product transition projects are successfully executed. Ensures process and yield improvement is embedded into the factory culture and actions
- Inventory: Develop and drive Cycle Time projects to reduce inventory and (write out meaning of IOS) IOS to AOP
- Costs: Develop and execute the HTS Lotte Annual Operating Plan. Direct responsibility for departmental spend and managing budget. Drive HTS to achieve/surpass financial commitments
- People and behavior: Actively coach, develop and provide performance feedback/actions to direct reports and support staff, including 12 desired Honeywell behaviors. Improve and develop organizational capabilities through effective performance management and planning/utilization of human and capital resources
- Develop and maintain an effective HTS leadership team. Model the HOS leadership expectations including use of, and adherence to, leadership standardized work. This requires spending considerable time walking the factory floor and auditing aspects of the operating system
- BS or BA degree in Engineering, Business or Supply Chain Management
- Master degree desired
- Six Sigma Green or Black belt certification preferred
- 10 years progressive managerial experience in Operations/Supply Chain capacities in high mix, low volume environment
- Extensive experience or knowledge of Honeywell Operation System, Toyota Production System or lean manufacturing excellence
- Successful leadership experience
- Experience in the following areas desired
- Ability to develop, execute and achieve tactical and strategic initiatives through active leadership that positively impact global business plans, operating profits, practices, policies and procedures
- Ability to effectively select, develop, coach, empower and motivate the HTS team to ensure growth in their scope of responsibility and accountability for operational excellence
- Ability to communicate clearly with an understanding of your audience and to present ideas and gain commitments that are crucial to the success of the Lotte site
- Strong knowledge and ability to develop and interpret operating plans, budgets, capital plans, cost components and financial statements
- Support and uphold HS&E policies
- Knowledge, skill, and ability to implement Lean manufacturing principles and process for material management improvement
- Ability to lead change and establish operational metrics/key indicators for process control, communication, and performance improvement
- Ability to manage multiple, complex projects and changing priorities; work extended hours when required, make sound decisions under pressure, and work effectively in a global environment
- A strong bias for action and results oriented strategic and tactical behavior
- Possess conflict management skills and understand self-directed work teams
- Ability to build strong teams with positive relations
3
Assistant Aggregates Plant Manager Resume Examples & Samples
- Follow and enforce Mine Safety and Health Administration rules and regulations, actively promulgate and support behavioral safety program though visible leadership
- Embrace full responsibility for Pennsuco aggregates P&L performance, specifically on fixed and variable cost management, manpower and productivity
- Through subordinates, direct and coordinate production activities of the limestone quarry operations to meet production goals for both the cement and aggregates plants. Review processing schedules and production orders to make decisions concerning inventory requirements, staffing requirements, work procedures, and duty assignments, considering budgetary limitations and time constraints
- Implement the Dragline reliability and efficiency plans (Marion 7820 & Page 732)
- Lead the development of short and medium-term mining plans. Utilize mining software to monitor mine planning and advance
- Implement process improvement and analysis by utilizing applied engineering techniques. Ensure safe and efficient mining and mineral processing methods, logistics, equipment management, manpower utilization, production maximization, and cost reduction
- Work with other functional leaders to ensure permitting, compliance and regulatory functions are completed as required and consistent with maximizing limestone reserves
- Develop a high performance culture fully aligned with the cement, aggregates, and sales personnel
- Promote a positive “can do” attitude in the work environment, emphasizing a “make change happen” approach while reinforcing group policies and providing feedback
- Maintain an open dialog with operations personnel to identify opportunities to improve performance
- Ensure the competence and development of department employees (hourly and salaried) by initiating training, coaching, counseling, mentoring and accountability to respond to items identified in the performance reviews while empowering them to perform
- Bachelor of Science degree in Mining or similar Engineering (Progressive responsible mining experience with dragline operations is recommended)
- Master of Science in Mining/Industrial Engineering or MBA is highly recommended
- Knowledge of budgeting, P&L, planning, permitting, compliance, regulatory negotiations and process improvement
- Knowledge of mineral processing, materials management (inventory and movement), slurry management, water management, and physical/chemical properties of limestone and limestone products
- Proficiency in MS Office, MS Project, MS Visio, MS Access, AGGFlow, AutoCAD, mine design/planning/scheduling software, ERP software (DataStream/SAP)
4
Manager, Plant Quality Resume Examples & Samples
- Manage all laboratory activities for the testing & evaluation of raw ingredients, processed batches and finished products to meet customer, consumer and corporate specifications
- Develop, implement, monitor and keep current quality assurance and food safety programs in coordination with Corporate Quality and Product Safety group
- Serve as Plant R & D liaison and coordinate plant involvement in corporate R&D projects and test runs
- Assure lab test results are timely, precise and accurate. Provide direct support and supervision to Lab Technicians. Schedule lab technicians to maintain adequate support for production
- Assure allergens are being managed appropriately
- Ensure all plant sanitation activities meet corporate and 3rd party standards
- Monitor, maintain, and oversee plant Hazard Analysis and Critical Control Point program and Safe Quality Foods (SQF Program)
- Ensure the plant insect and rodent control programs are effective
- Maintain the integrity and calibration of all lab test equipment
- Summarize technical data monthly to identify trends and appropriate corrective actions
- Train, support and motivate subordinates in the performance of their duties
- Respond to customer complaints involving technical or quality issues
- Ensure sanitation and GMP procedures for the plant are effective
- Conduct GMP and sanitation audits of operations and warehouse areas
- Represent the Quality department in department meetings and represent the facility in all regulatory activities
- Monitor and maintain the “Hold, Rework and Return” programs
- Responsible for disposition of all held product with input from the Plant Manager as needed
- Serve as liaison for all technical and quality control issues between operations and sales departments
- Work on special projects and assigned responsibilities outside of QA and Product Safety as needed
- Provide leadership to the plant Performance System; Pillar ownership and Pillar support
- Respond promptly, effectively and accurately to consumer or customer complaints and work with individuals at corporate to resolve as quickly as possible
- Work to reduce potential for foreign material contamination by identifying potential sources and developing corrective actions to prevent occurrence
- Conduct periodic plant GMP audits and inspections and communicate findings to appropriate individuals
- Recommend capital project relative to product quality, food safety and cost improvement
- Accompany regulatory, AIB, customer or rabbinical inspectors and report results as required to St. Louis headquarters
- Work with our third party distribution warehouses with which we are paired in regard to problems with inbound shipments and other sanitation and GMP issues
- Actively participates in association technical committees (American Association of Cereal Chemists) to keep plant current on issues impacting hot cereals and in particular oat based products
- Serve as the technical resource for production
- Interact as an integral team member with Plant Manager, all managers and group leaders. Works with all others in the administrative group and with bargaining unit Group Members
- Interacts with our oat product suppliers along with other suppliers, customers, government agencies, outside contractors, and our third party warehouses
- Provides back-up for Associate Quality Specialist
- 7-10 Years technical experience in the food industry
- 3-5 Years Supervisory/Management experience
- Bachelor’s Degree in Food Science, Manufacturing, Production Operations Management or equivalent field of study
- Excellent communication, presentation, and negotiation skills
- Strong computer application skills, network and PC business application software
- Background in statistical process control, basic financial skills and understanding
- Key Leadership Competencies in addition to Ethics/Values and Integrity/Trust. (Action Oriented, Directing Others, Priority Setting, Decision Quality, Organizing, Process Management)
- Training in cereal product sanitation and GMP required
- SQF Practitioner certified; HARPC certified
- Ability to communicate verbally and in writing with all levels of employees. Utmost honesty, integrity and dependability required
5
Recycle Plant Manager Resume Examples & Samples
- Minimum 5 years experience in processing / maintenance
- Experience in the management of employees
- Experience in the management of Safety, Health, and Environment
- Experience in concrete recycling is desirable but not required. (Aggregate production may be suitable substitute to concrete recycling)
- Strong communication skills and interpersonal skills including conflict resolution.
- Ability to plan and manage effectively.
- Must represent VMC in a professional manner to all customers, vendors, and internal personnel
6
Recycle Plant Manager Resume Examples & Samples
- Experience in the management of union employees
- Experience in concrete recycling and rail distribution is desirable but not required
- Knowledge of mining and production techniques and equipment, safety and environmental regulations (MSHA and OSHA), equipment application and operation, material specifications, and surveying.
7
Ready Mix Plant Manager Resume Examples & Samples
- Knowledge of all aspects of concrete production and the types of products produced
- Current knowledge of D.O.T., O.S.H.A., EPA, and other agencies regulations
- Ability to direct, teach, motivate, and coach
- Excellent interpersonal skills to facilitate positive working relationships with all levels of management and staff
- Ability to make decision is a timely manner, sometimes with incomplete data and under tight deadlines and pressure
- Exercise independent decision-making, prioritize conflicting demands, and communicate with multiple departments and employees
- Strong problem solving and analytical skills and the desire to seek solutions
- Must be able to read and write in the English language
- Possess a current driver’s license
8
Asphalt Plant Manager Resume Examples & Samples
- Over 2 years up to and including 4 years from post high school, work, military, institutional or vocational environment
- Minimum 3 years experience in product line
- Plant maintenance and operation
9
Plant Manager Tier Resume Examples & Samples
- Provide direct oversight for the operations management team including production, engineering, maintenance, planning, procurement, quality, safety and logistics along with a strong connection to both finance and human resources
- Provide leadership for assessing and enhancing plant capabilities
- Ensure all quality standards, specifications and policies are met or exceeded, drive continuous process / manufacturing improvements and collaborate with Research and Development in product development and implementation
- Develop a culture based on open / honest dialogue and involvement of all team members that demonstrates the value of their input / engagement in improving performance
- Provide leadership for diversity and positive community involvement / relations
- Drive a culture of high performance and accountability in employee and product safety as well as other aspects of the business
- Collaborate with Human Resources and other function leaders to create and execute effective employee relations processes and develop managers to do the same in order to maintain a positive working environment
- Drive collaboration with R&D and Marketing in new product development to ensure plant capabilities and production feasibility are understood and addressed
- Bachelor’s Degree required (i.e. Business, Industrial Management, Engineering, Food Science, Management, Operations)
- Minimum 5-8 years manufacturing experience required preferable with some level of High Performance Work System implementation
- Minimum 2-3 years in a significant leadership role in a plant required (i.e. Production Mgr or similar)
- Experience in multiple pillars of TPM (Leadership, Organization Capability, Focused Improvement, Progressive Maintenance, Autonomous Maintenance, Early Management, Supply Chain, Quality and Safety) required
- Manufacturing experience in a Food, Beverages, CPG, Chemical or related industry required
- Change Management skills required
- Experience with FDA a plus
- Key Leadership Competencies in addition to Ethics / Values and Integrity / Trust (Drive for Results, Managing Vision and Purpose, Decision Quality, Building Effective Teams, Action Oriented, Managerial Courage, Strategic Agility, Priority Setting) required
10
Capital Projects Plant Senior Manager Resume Examples & Samples
- Build and maintain effective networks and relationships with key industry contacts, clients and alliance partners including representing Accenture and/ or speaking at relevant industry forums and conferences – market relevance
- Work within delivery teams as a subject matter expert, a project/team lead or as a delivery team member supporting through different stages of a project lifecycle from initial assessments to solution go-live to achieve project commercial objectives and client outcomes – delivery outcome focused
- 10 - 15 years of industry (or consulting) experience as a practitioner across
- One or more key industries : Powergen, Refineries, Chemicals and Metals
- Activities relevant to Capital Projects ranging from Plant Lifecycle Management, Construction Worker Management and Safety, Capital Projects Portfolio Planning and Management through to solutions that exploit IT/OT/ED convergence
- Knowledge of key alliance partners including SAP, Intergraph, Bentley Systems, Oracle-Primavera
- Asset data management and analytics solutions
- Demonstrated ability to work creatively and analytically in a problem-solving environment
- Willing to travel to domestic and international locations
11
Plant Manager Saxonburg Resume Examples & Samples
- Plan, implement, improve, direct and coordinate manufacturing activities and processes in a designated Sterile Disposables Medical Device site to produce products of high quality medical devices at competitive costs by adherence to safety and other legal regulations
- Act as Deputy for Head of Sterile Disposables/Plant Manager and represent Site on SD Management team
- Accountable for ensuring the manufacturing environment and the site are conducive to product quality and employee health and safety by ensuring adherence to processes and plant emergency operations
- Direct cross functional teams of significant resources and manage by analyzing and reporting against business parameters and participating as a key member of the Sterile Disposables Management Team
- External and Internal regulatory compliance, incl. environmental aspects of the plant
- Personnel training and development: Develop, communicate and manage objectives for manufacturing team members across multiple functions
- Efficient and effective financial controls across multiple cost centers and resources required for safe and productive operation
- Management of projects and successful deployment of key improvement initiatives around the principles of operational excellence to significantly influence the economic success of the SD organization, e.g. cost saving, performance improvement, capital investments
- BS/BA Degree
- 10+ years of total experience
- 5-7 years of experience in multiple Product Supply disciplines, leadership or supervision
- Instills company visions, values and beliefs in others by setting example
- Coaches, councils, manages and directs in business unite relative to changing priorities, sense of urgency and utilization of multiple skill sets
- Excellent presentation, training, coaching and interpersonal skills
- Ability to influence other members of the organization to help achieve goals and increase performance
- Ability to build relationships and partnerships within the organization
- Ability to lead projects of high complexity with limited to no direction
- Demonstrated advanced problem solving skills
- Proficient with Microsoft office tools and SAP applications
- Masters Degree
12
Plant Manager PAS Resume Examples & Samples
- Lead, develop and motivate the plant management team to ensure operational excellence in all areas and targets (e.g. production, quality, profit, cost etc.) are met
- Communicate the vision of the business’ purpose and future to the plant and represent the plant to management
- Lead change for the Plant & ensure the business is appropriately represented at higher level change projects
- Represent the company in living the values, practice and lead by example
- Proactively communicate with appropriate internal departments
- Champion Diversity & Inclusion in line with the Company guidelines
- Establish & maintain appropriate monitoring systems, ensuring effective measures, controls and reporting mechanisms exist. Takes corrective action where performance deviates from plan to ensure delivery of strategic and operational goals
- In conjunction with regional management, develop and agree the operations plan for the plant, in line with defined objectives, to deliver business goals including Budget, Capex and Product launch
- Manage Plants to deliver the agreed business and operational plans
- Accountable for P&L performance of the plant
- Establish & maintain appropriate monitoring systems, ensuring effective measures, controls and reporting mechanisms exist
- Lead the development and implementation of common processes, systems, standards and tools in line with Divisional and Corporate standards
- Track financial status to ensure targets are achieved
- Prepare documentations for general reviews
- Develop and implement standard processes, systems, standards and tools in line with Regional, Divisional and Corporate standards
- Support regional sales and engineering teams in winning new business. Work with these teams to influence pricing and implement new business into production at agreed timescales, costs and quality
- Ensure customer requirements in terms of product / service delivery timescales and quality are met or exceeded. Manage escalated issues including quality concerns
- Deploy Sinter Metals division standards within the plant
- Foster a culture of continuous improvement and ensure the effective execution of CI plans
- Proactively develop, build and maintain working partnerships inside and outside GKN, including customers and suppliers, in order to further business performance
- Internally work together with Regional Management Team incl. Engineering, Finance, HR, Lean, Quality & HSE, IS IT, Purchasing and other Plant Managers
- Act as an “ambassador” for GKN in the community at all times
- Externally work together with customers, suppliers, Industry bodies, local government and communities
- Manage risk for the segment in line with corporate policies and goals, including: - Environment, Health & Safety, Quality, Financial risk and Operational risk
- Execute statutory responsibilities & ensure operations comply with relevant legislation, regulations and corporate policies etc
- Solve problems with analytical thoughts and good judgment skills
- Manage, coach, develop the people in to support the Strategy
- Deploy Group/Division/Regional standard HR policies and processes
- Lead, with HR support, people resourcing, engagement and management activity for the function, including
- 5 plus years of experience in operational position
- Understanding of global markets, technologies and products
- Thorough understanding of global PM organisation and business strategy
- Analytical skills
- Basic understanding of accounting
- High motivation and initiative to get problems addressed
- Builds teams and interacts effectively in at all levels of the organization
- Ability to listen, challenge and communicate
13
Plant Manager, Castrol Resume Examples & Samples
- Leading the plant by providing strategic direction, business context and short and long term objectives in keeping with the overall business direction
- Providing leadership and assurance to ensure that the units are operated safely, reliably, in line with environmental site objectives and that product quality specifications are met
- Developing the necessary operating culture and continuously improving the current suite of operating procedures, practices and systems
- Ensuring optimum operational capabilities onsite both present and future
- Working closely with the HR team to ensure a positive employee relations environment
- Working closely with Engineering and Maintenance personnel to ensure adequate plant integrity, availability and cost efficiency
- Strategically plan to reduce costs within operations
- Control cost effective purchase of plant consumables and services and ensure that they assist in the implementation of the long term strategic plan
- Minimise waste such as flushing, obsolete raw materials and finished product
- Manage inventory, customer service levels and performance controls
- Incorporate lean thinking and continuous improvement into plant processes such that you are constantly striving to improve all performance measures on site
14
Atkh-plant Operation Manager Resume Examples & Samples
- Bachelor or above, major in mechanical/electrical engineering or management
- At least 5-year experience in the field of management and plant engineering
- Well understanding of facility related system (A/C, Cleanroom, CDA..etc) with management skill
- Proactively and fully engage on Facility system improvement
15
Plant Depot Manager Resume Examples & Samples
- Experience managing a small depot team
- Ability to understand and work with P&L accounts and budgets
- Excellent communication and organisational skills
- Ability to prioritise work load and work under pressure to strict deadlines
- Excellent understanding and experience of managing Health and Safety practices at work
- Capability to take ownership and responsibility
- Ability to adapt to individual and operational change in a diverse and fast-paced organisation
- Local area knowledge of the market and sectors
- Knowledge of plant equipment
- Mechanical knowledge
- Previous hire experience
- IOSH qualified
16
Plant Manager Tier Resume Examples & Samples
- Assist in the development of operational and capital budgets, policies and procedures, and the execution of same
- Utilize available data including OEE, line speed target, and efficiency and process data to continuously improve productivity, uptime and reliability
- Continually coach, direct and train employees utilizing Lean principles. Monitor employees' work performance and attitude and perform formal reviews as required by policy. Coach and counsel employees about work-related issues and assist employees to correct job skill deficiencies
- Ensure all plant personnel are operating in compliance with plant and corporate procedures as well as in compliance with all customer and governmental regulations
- Lead the continuous improvement program to deliver opportunities in cost, quality, food safety and service
- Coordinates manufacturing activities with all other functions of the organization and suppliers to obtain optimum production and utilization of human resources, machines and equipment
- Conduct regular meetings with plant personnel to ensure operational issues are being communicated and addresses expediently with a common understanding of goals
- Processing or Packaging industry
- Results-driven with a strong desire to grow and learn in a fast paced environment
- Demonstrated track record of meeting or exceeding targets goals
17
Production Manager / Plant Manager Resume Examples & Samples
- Responsible for implementation of all manufacturing operations including the safety, production efficiencies, quality of the plant
- Supports continuous improvement processes to ensure safety, quality, cost, and customer service goals are met
- Maintains an engaged and team-oriented workforce to meet business demands
- Responsible for hiring, performance reviews, training and career development of employees
- Working on new product trials
- Implementing Continuous Improvement projects and initiatives
- Union meetings/topics
- Managing department budget and large capital projects
- Developing and maintaining department KPI's
- Minimum 7 years of experience in the Food industry in a manufacturing environment at the Management level
- Demonstrated success as a change agent & developing/implementing continuous improvement initiatives and accountability programs
- Demonstrated success assessing, developing and retaining top talent
- Proven ability to drive process improvements, adhere to budgets, and maintain regulatory compliance
- Proven ability to lead with the following key competencies: Managing Change, Critical Thinking, Continuous Cost Focus, Technical Expertise, Influence and Delivery of Sustainable Result
- Must be able to troubleshoot problem(s) to develop corrective solutions
- Must have a flexible schedule and be able to work weekends
- Must be computer literate (Microsoft Office); Excel; Mapix; PowerPoint & MS Project
- Experience with Lean Six Sigma is required
- Experience with SQF and ISO 14001 is perferred
- Dryer experience is preferred
- Milk/yogurt food industry experience is preferred
18
Manager, Plant Continuous Improvement Resume Examples & Samples
- Leads the Continuous Improvement process (e.g. behaviors, attitude and culture), working with staff and operations to develop, implement and sustain a continuous improvement program based upon lean principles that support meeting plant goals and targets
- Leads, identifies and defines scope of continuous improvement planning and activities
- Primary owner in leading and/or coordinating continuous improvement activities
- Identifies opportunities and works closely with technical resources to help drive efficiencies and best practices
- Teaches and models root cause analysis and problem solving to prevent recurrence, standard work and follow-up. Viewed as an expert in these areas
- Develops lean change agents (Lean Coordinators) to foster continued growth. Plans for training/seminars to keep the team energized and focused; including budget planning for such activities
- Works with the Lean Coordinator in charge of Standard Work to ensure processes and work instructions are kept up to date and documented
- Works with the Lean Coordinator in charge of 5S to ensure the site is sustaining and improving the 5S program
- Is a change agent who challenges existing processes that create waste and non-value added work
- Coaches, guides and/or leads cross-functional teams to achieve resolution of assigned projects
- Leads focused efforts aimed at breakthrough and incremental improvements in process, department and/or line-specific opportunities that meet and exceed plant operational performance metrics
- Monitors data and metrics to identify areas of waste and prioritize the development an implementation of solutions
- Teaches and models tools and concepts of Lean Thinking and Six Sigma; facilitates kaizen events
- Provides appropriate documentation and project update communications to Operations leadership. Collaborates with all departments and individuals affected by CI projects
- Shares best practices and builds relationships with CI Consortium Members and other TreeHouse plants
- Deep understanding of Lean Manufacturing/Continuous Improvement methodologies and ability to teach and model them
- Demonstrates a passion for safety. Able to develop and maintain a respectful and safe work environment
- Must have strong analytical and business judgment including demonstrated problem-solving and trouble-shooting skills
- Ability to influence, mentor and coach to get results through others
- Results driven; supports company growth strategies
- Conveys a high level of optimism while setting aggressive targets and supporting the team in achieving those targets
- Communicates a compelling vision and inspired sense of purpose. Talks about the possibilities and is optimistic. Creates strong morale and spirit within team
- Solves highly complex problems and prioritizes actions in a timely manner. Probes all sources for answers and can quickly sense what will help resolve issues
- Establishes clear directions, sets stretch objectives. Lays out work in a well-planned and organized manner and brings out the best in people through leveraging their strengths
- Speaks candidly and provides constructive feedback in a professional manner
- Organizes and manages projects; interacts, supports, facilitates and leads multi-functional work teams; leads teams to consensus; maintains strong negotiation skills
- Able to build strong relationships across the business unit to support and foster change
- Must be mobile and able to take on broader assignments for additional development opportunities within Meals Division and across Treehouse Foods as a whole
19
Plant Manager Ntrm Resume Examples & Samples
- Conducts/oversees monthly and quarterly safety meetings, maintaining a consistent focus on safe behavior
- Enforces the wearing of appropriate safety equipment in the plant at all times
- Coordinates monthly plant and truck inspections with the Director of Operations and Fleet Manager
- Responsible for consistent batching sequence and monitoring scale and gate accuracy
- Supervise employees at the plant in daily activities including hiring, evaluation, progressive discipline, etc
- Accountable for the integrity of Mixer Operators and yard personnel loads and payroll hours. The time entry system should be audited daily for accuracy
- Monitors loading and tempering time; working with the Mixer Operators to arrive on each jobsite in a timely fashion
- Reviews, daily, a pre-shift inspection checklist to ensure equipment is functioning properly
- Responsible for performing preventive maintenance procedures. Periodic inspections are performed to inspect bin integrity, dust collection system, admixture dispensers, gate and rams, and aerator functionality
- Responsible for overall housekeeping including the plant, batch office, and driver and equipment appearance
- High School diploma or GED, Bachelor’s Degree Preferred
- 3 years’ experience with concrete and related products
- 1 year maintenance and supervisory experience preferred
- Self-starter with desire to excel
- Ability to direct, motivate, and coach the activities of others
- Ability to formulate decisions, make and support recommendations, prioritize work, communicate with multiple parties and handle multiple tasks
20
Plant Unit Manager Resume Examples & Samples
- The Plant Unit Manager will provide the organizational leadership and hands on management required to achieve all operational and strategic objectives of the two operations
- Direct and strategic leadership responsibility for the manufacturing activities of both operations
- Maintains highest Environmental Health and Safety standards in the operation
- Ensures 100% on time shipment rate through the most efficient use of the human and material resources at his/her disposal
- Builds/maintains processes that ensure collaboration at all levels of organization / functions to achieve EMEA strategic growth objectives
- Drives the implementation of LEAN techniques, constantly looks for opportunities to eliminate waste
- Builds and executes a cost out project deck in close cooperation with the AME & Cost Out Leader
- Planning, control and execution of plant variable cost targets
- Manages regular cost estimate cycles, and executes to goals set there
- Responsible for all maintenance and repair of machinery, equipment, the evaluation and justification of capacity and productivity investments
- Supports product localization effort and new product launches by delivering products at target cost on time
- Maintains an effective and motivated workforce, promotes a culture of positive employee relations, respect and trust at all levels of the organization
- Champion of compliance and a promoter of GE Beliefs
- Continuous improvement of cost, capacity, capability both for human and fixed assett
- Engineering and/or Operations Management degree
- Strong manufacturing experience in running complex operations
- Passionate, proficient, practical LEAN leader
- Quality system management and project management experience
- Demonstrated problem solving skills, self-starter attitude
- Excellent communication and interpersonal skills working with all levels of the organization, demonstrated ability to motivate & inspire others
- Experience in metal/plastic parts fabrication, Six Sigma knowledge, and experience with SAP are advantages
21
Feeds Plant Manager Resume Examples & Samples
- Promote and support a safe environment for all employees
- Operational excellence in the manufacturing process
- Promote and support outstanding customer service
- Manage the P & L for the production and freight operations
- Bachelors Degree in Ag-Related field preferred
- Minimum 5 years experience in the Feed Mill industry
- Supervisory and Employee Management experience
- Excellent understanding of Safety Regulations and Compliance
- Attention to detail is critical in this retail, bagged feed environment
- Financial and P&L experience
- Strong computer skills to operate production systems as well as accounting and Microsoft products
22
Feed Ingredients Plant Manager Resume Examples & Samples
- Ag-Related Bachelors or 4-year degree preferred
- 2+ years of Operations Management with FeedMill experience
- Knowledge of Animal Nutrition
- Knowledge of Animal Proteins for Formulations
- Positive attitude and friendly personality
- Demonstrated knowledge of Government Regulations and Standards
- Proven leadership experience with the ability to manage a team
- Not afraid to work long hours
23
Plant FES & Productivity Manager Resume Examples & Samples
- At Plant level, provide FES expertise and coaching (HSE, Quality, EE, PC&L and Production system) based on 11 lean manufacturing principles to contribute to achieve operational business targets
- Contribute to the definition of the Plant Improvement Plan to achieve the budget
- Lead construction and follow up of the FES deployment plan, to support the Plant Improvement Plan (PIP) execution
- Ensure understanding at plant level of 18 FES KPIs and the link with P&L results to properly prioritize the FES plan
- Provide, according to the needs, FES knowledge and skills to the plant team through training and coaching
- Contribute to the application and /respect of FES Principles in Programs from design stage (lean process design, MIFD, validation of Equipment design, cardboard workshop activities, Standardized Work ,OHP, process layout, packaging, etc..)
- Be an active change agent within his site, by cultivating an FES mind-set / Lean Manufacturing Concept
- Minimum 3 years of managerial experience (UAP / PC&L / Quality Manager…)
- Recommended 3 years of working experience within a production environment (e.g. Engineer, Supervisor, Manager level or equivalent)
- Recognized experience and ability to improve processes and KPI's within a plant using FES principles
- Previous plant launch experience and previous management experience is a plus
- Network animation, coaching and influencing/persuasion skills
- Ability to train and coach within all levels of the plant
- Continuous improvement mind set
- Ability to master change
- Understand basic P&L and operational levers
- Fluent English language knowledge: written and spoken
- Problem Diagnosis and analytic skills to understand contexts and define/support the definition of action plans
24
Retread Plant Manager Resume Examples & Samples
- Creating and maintaining a positive work attitude in plant operations towards all customers (internal/external) and employees
- Maintains good working relationships with all employees and ensures they are aware of their job duties and responsibilities
- Utilizes Material flow processes for overall efficiencies in plant operations
- Responsible for maintaining plant compliance on operations defined by the Operational Compliance Review process
- Responsible for inventory management and controlling expenses
- Maintain spreadsheets to monitor beginning inventory levels, receipts, monthly levels of inventory to be used in determining rubber usage and compare to Tire Pro and BASys
- Responsible for maximizing and leveraging the use of and data from BASsy Manufacturing
- Evaluate and identify rubber inventories and make adjustments as necessary, i.e. - transfer rubber that is not turning to other GCR TIRES & SERVICE locations, return rubber to Bandag, identify obsolete rubber and transfer accordingly, and identify excessive inventories
- Hires, trains, and motivates retread technicians, and administrative support personnel and maintains the proper workforce suitable to the workload of present business
- Works closely with the Store Managers regarding sales personnel and customers
- Maintaining a proper work schedule of employees to achieve maximum productivity and minimal overtime
- Ensure that scheduled equipment maintenance transpires and is logged as required by Bandag equipment specs
- Resolving issues relating to the satisfaction of the customers
- Promote cooperation between all departments in the plant
- Promote and share plant or BASsy best practices with other GCR TIRES & SERVICE Plant Managers
- Establish and maintain ISO certification processes and follow the guidelines for the Bandag MEP system
- Make sure all company policies and safety regulations are understood and obeyed by all store personnel by holding monthly safety meetings
- Monitor and control all plant expenses keeping within Financial Model guidelines and parameters by regular review of the Plant’s P&L, general ledger and accurate productivity reports
- Overall profitability of the plant operations
25
Plant Operation Manager, Parent Seeds Resume Examples & Samples
- Provide clear process for parent seed processing at Toller and implement
- Ensure delivery of good quality parent seed
- Monitor field crops parent seed treating & packing at Lop buri site and implement
- End to End inventory management starting from monitoring seed storage, seed movement, provisioning, physical write off and Cycle counts etc
- Provide Monthly report covering the summary of operations, parent seed quality ,usable ,un usable
- Strong collaboration and engagement with commercial site stakeholders to ensure safety of site and following compliance in sites
- Collaborate with Thailand and APAC Parent seed team
- Experience in FPP work ,such as seed processing ,seed quality ,seed planning ,seed inventory management
- Knowledge in seed processing, warehouse management and seed quality analysis
- Bachelor’s degree in field crop production ,seed technology ,agriculture engineering is preferable
- Fair to Good command in English
- Strong planning and time management skill, negotiation skill
- Result-oriented
- Health, safety , Environment .security mind set
- Strong leadership, coaching and consultancy skills with ability to manage and motivate people to improve diary work and quality
- Analytical skill and able to work independently in managing manufacturing activities in the responsible area
26
Cssi-plant Manager Resume Examples & Samples
- Minimum Bachelor’s Degree in Engineering or equivalent discipline
- Working knowledges of food safety, safety and environment
- Strategic thinking, business acumen, good at technical as well as commercial knowledges
- Demonstrated leadership & conflict resolution, drive for performance and high courage
- English skill is a must
- Effective communicator both verbal, written and presentation skill for multiple level
- Mobile and willingness to travel as necessary or as business requires
- Good at people management including coaching, and experienced in leading minimum 150 employees
- Minimum 5 years in managerial experience in manufacturing and operations preferably in Food or beverages manufacturing
27
Administration Assistant to Plant Manager Resume Examples & Samples
- Maintaining calendar(s) and arranging meetings as required with internal and external stakeholders
- Provides senior leadership team with reminders of upcoming events and projected related deadlines
- Coordinates, prepares and edits reports and presentations
- Organizes files, assembles relevant data, compiles statistics or information as directed for use by others
- Makes travel arrangements, prepares expense reports and process invoices, maintains financial and expense records
- Handles business confidential matters requiring discretion and judgment. Takes initiative to follow up on relevant issues and informs manager of status as well
- Requires minimum of 4 - 6 years related administration experience supporting senior management roles
- Excellent PC skills and proficient in desktop tools essential
- Knowledge and experience of administering and managing global travel and hospitality matters
- Individual should be a strong communicator with excellent interpersonal skills1700157914W
28
Maintenance Plant Manager Resume Examples & Samples
- Follow company policies and procedures for proper routine and preventative maintenance of all manufacturing equipment and other mechanical equipment within a specific location
- Analyze and resolve work problems, or assist employees in solving equipment related problems
- Set schedules for maintenance staff for equipment maintenance at manufacturing location(s)
- Maintain accurate records for management of cost for repairs and maintenance for all manufacturing equipment in a location (s)
- Work with vendors for timely delivery of spare parts for repairs and maintains spare parts inventories for manufacturing location (s)
- Preventative maintenance, installation, upkeep, and repair of machinery and equipment in all facilities
- This position will identify, justify, and implement any cost reductions where applicable without sacrificing the integrity of our plant, or the finished goods we produce
- You will serve as support to all manufacturing areas, and help to minimize our cost through lean initiatives to provide BMC a competitive advantage
- The position will reinforce teamwork and a positive working environment as well as participate in the establishment of goals for our Maintenance team
- Work with management to insure the proper maintenance of all location equipment within a manufacturing location(s)
- Minimum education required: High School Diploma or GED. 2 Year Trade School training in machine maintenance. Experience may be substituted for education
- Special skills/knowledge required: Knowledge of computer driven manufacturing equipment. Component or Millwork equipment maintenance knowledge helpful
- Electrical experience required, single-phase and three-phase exp., PLC logic, computer skills needed
- Diagnostic , pneumatic, and hydraulic knowledge required
- Minimum experience required: 3-5 year’s previous maintenance experience in a similar manufacturing industry
29
Plant Manager New Creek Resume Examples & Samples
- Management of the safe and reliable operations of the New Creek (NC) wind generation assets
- Ensure compliance with all provincial and federal regulations, liaise with applicable ministries and government agencies (i.e. WV DNR)
- Produce regular O&M reports, including production, downtime and budget forecast and variance reports
- Scheduling, execution and reporting of activities related to maintaining NERC Compliance
- Daily interaction with Market Operations Center (Tenaska) on daily activities and scheduling
- Scheduling and execution of all Balance of Plant related activities
- Assist in the preparation of the budgets for the New Creek Windfarm
- Review and approve capital and operating expenses associated with works and contractors
- Review and ensure onsite safety, security and environmental practices comply with government regulations and standards as well as Green Energy Operations policies
- Working with the Mechanical Supervisor, liaise with OEM turbine manufacturer Gamesa for the operations and maintenance of the 49 Gamesa turbines at New Creek. Also ensure compliance with Service and Maintenance Agreement
- Liaise with Landowners, Residents, Municipal officials, Government agencies and officials
- Record and Update complaints and actions taken regarding landowner or resident complaints. Ensure actions required are performed and that reporting and notifications related to complaints or actions are completed
- On-call 24/7 for emergency response and urgent operational issues, also liaison with local First Responders and responsible for the development and execution of annual mock emergencies
- Provide technical expertise and engineering assistance to various field groups, including Maintenance and Operations, and act as a Green Energy Operations liaison for Engineering sponsored projects
- Coordinate preparation of the Annual Capital Budget by submitting projects and assisting in the development of field submissions
- Prepare technical reports on special projects and assignments
- Provide project management for approved Capital Budget items, including design, development of specifications, obtaining quotations, purchase of materials, contract preparation and administration, cost and schedule tracking and control, and inspection as required
- Manage specific projects and programs as they relate to renewable energy operating and maintenance issues
- Assist in the implementation of the Company's Safety and Environment programs
- Electrical Engineering degree with minimum 7 years of related Operations experience OR 10 Years of related Operations experience
- Project management experience an asset
- Prior Windfarm experience is preferred
- Valid driver’s license and passport
- Effective verbal and written skills, computer skills, problem solving, project management and decision making skills are required
30
Plant Pathology Manager Resume Examples & Samples
- Execute quarantine and seed movement activities timely, accurate and within applicable legislation
- Perform workflow forecast to resource Quarantine operations properly
- Coordinate and oversee operations and equipment necessary for successful operations
- Elaborate long range plans for people, equipment and budget considering strategic objectives of the company
- Collaborate with multi location people to share new technologies and results of plant pathology
- Lead effort aiming maintenance of Lab and Greenhouse operations
- Train and develop research Associates, Assistants, Fieldmen and temporary personnel
- Meet site safety requirements as well as foster a safety working environment
- Agronomist with valid CREA and Doctorate degree on Plant pathology areas
- Excellent organizational and and record keeping skills
- Strong operational familiarity with different procedures of plant pathology, preferably seed pathology
- Experience on working in team of teams from different backgrounds, different cultures, preferably with international cross cultural experience
- Successful experience on collaborating across interdisciplinary teams
- Experience in conduction quarantine related assays
- Results oriented leadership approach
- Ability to make decisions and solve problems while exhibiting situational judgement
- English fluency is required
31
Manager, Plant Quality Resume Examples & Samples
- Responsible for maintaining food safety, quality and employee safety
- Assures allergens are being managed appropriately
- Manages all plant sanitation activities to meet ConAgra standards
- Manages quality assurance technicians to maintain adequate support for production
- Summarize technical data monthly to identify defect trends and corrective actions
- Initiating and leading continuous improvement projects around quality and food safety. Leads UPS process for quality related issues
- Conducts GMP and sanitation audits of operations and warehouse areas
- Monitors and maintains the “Hold, Rework and Return” programs
- Acts as liaison for all technical and quality control issues between operations and sales departments
- Represents the facility in all regulatory activities
- Monitor and maintain the plant insect and rodent control programs
- Monitor and maintain the food safety program
- Plant SQF Practitioner
32
Plant Manager Golden Peanut & Tree Nuts Resume Examples & Samples
- Bachelor’s degree in Engineering, Food Science (or equivalent experience/background) supplemented with a minimum of ten (10) years relevant work experience in tree nut manufacturing or similar work experience
- Demonstrated capacity to excel within high risk, fast-paced work environment and results driven to provide support and achieve goals established by the division
- Fluency in both English and Spanish considered an asset
33
General Manager DPS Tianjin Plant Resume Examples & Samples
- 10-15 years in Manufacturing Operations, at least 5 years supervisory experience
- Multi-functional experience is preferred
- Knowledge
- Strong knowledge of manufacturing processes and machinery
- Familiar with health and safety regulations
- Familiar with Value Based Management, Six Sigma, and Lean Manufacturing concepts
- Proficiency in spoken and written English language is mandatory
- Strong organization skill and planning skill
- Strategic thinking; Networking building skills
- Analytical and creative
- Presentation skills
- Strong interpersonal and conflict management skills, ability to build cross-functional teams and manage complex activities
34
Volvo Production System Manager Borås Plant Resume Examples & Samples
- Being accountable for our overall factory objectives, with a special focus on the VPS implementation
- Together with the plant management team lead and follow up the VPS work
- Coach leaders to become true lean leaders
- Support the knowledge and understanding of the VPS principles and tools in the organization
- Perform VPS activities and trainings
- Support managers’ improvement activities (gap analysis, roadmap, kaizen plans, OMS) linked with area KPI:s
- Coach/Support in shop floor activities (kaizen event, QRQC, std. work, 5S…)
- Promote sharing of best practices / benchmarking between plants / areas (Peer to Peer concept)
- Coordination and development responsible for the industrial school
- Be an active contributor to the plant management team
- Bachelor / master in science or similar
- At least five years as line manager
- Have deep experience in Lean/ VPS principles and tools
- Excellent and proven skills in communication, problem solving and change management
- Proactive coaching and Change Management skills with a strong drive to improve
- Genba skills (observation, coaching, communication…)
- Have confidence and curiosity in own ability and be prepared to question and challenge managers and employees
- Business oriented team player with great ability to work cross functionally
- Fluent in written and spoken Swedish and English
35
Plant Manager Nsee Resume Examples & Samples
- Identifies and develops a plant operating plan that is consistent with and supports the business plan
- Determines what resources are required to successfully execute the plan
- Ensures standards for product quality, equipment and operator performance are maintained and that cost-effective technology is used to maximize production
- Develops, monitors, and reports on operating cost within functional areas
- Develops and initiates the direction and necessary resources to establish leading edge safety and environmental performance objectives
- Leads and directs the development and deployment of key operational initiatives for Lean Six Sigma (factory utilization improvement, process capability enhancement, customer satisfaction, employee involvement, etc.) in support of Supply Chain, vision and values
- Sets the standards, communicates and achieves clear and measurable expectations of performance for the operation as well as direct reports
- Takes the lead as agent for positive change, including raising the bar on objectives to attain and sustain Lean Six Sigma status
- Develops a culture that leverages customer relationships/satisfaction, encourages active communication, employee engagement, and talent development
- Works with sales/marketing, engineering and customers to understand and meet their needs
- The Plant Manager will demonstrate commitment to excellence inspiring, supporting, facilitating and communicating to others the drive toward zero injuries, zero waste, growth with customer, and financial achievement through leading edge operational practice
- BS/BA degree required
- Must have minimum 10 years industry related experience
- 8 years in management role is desired
- Excellent communication, organization and presentation skills
- Manufacturing operations and factory management experience
- Ability to develop, monitor, and report key performance metrics and recommend corrective action as appropriate
- Must excel in planning and establishing priorities while demonstrating flexibility and the ability to multi-task
- Must be adept at all phases of manufacturing processes: Concept Refinement, Technology, Systems Development, Production and Deployment, Operations and Support
- Experience with leading and managing a diverse workforce
36
Plant Manager, Performance Tapes Resume Examples & Samples
- Analyze and draw information for long-term strategic change and improvement for the site
- Lead significant multi-functional or multi-business project initiatives, scheduling and planning
- Focus on improving more complex performance of the site: develop site organizational culture that fosters continuous improvement
- Successfully implement annual and long-term financial and business plans (financial, safety, service, organization, inventory)
- Drive for results and effectiveness in: quality, service, safety, employee relations climate, inventory and organizational development. Ensure good operational practices are in place; anticipate and manage through adversity, effectively incorporate improvement programs into the culture of the Operations function
- Practice all health and safety procedures and make safety a top priority
- Lead the safe operation of a facility and comply with legal, legislative and corporate safety requirements
- Create a vision and operating strategy/plan for the plant; steer the plant toward that vision
- Drive continuous cost reduction and operating effectiveness improvement
- Ensure accuracy and completion of capital planning and budgeting
- Understand and implement ISO 9000 and ISO TS 16949 procedures that relate to the role and responsibilities of the Plant Manager position
- Achieve maximum levels of productivity, ensuring that the business benefits from the lowest possible cost and best value
- Responsible for delivery of short-term and-long term results in order to develop and maintain the organization’s credibility with the business and creating opportunities for the function to add greater value to the business
- Translate market trends and customer needs into actionable goals that create competitive advantage
- Develop, analyze and manage Operational expenses
- Develop Objectives, Goals, Strategies and Measures (OGSM) for assigned area and confirm linkage to global business strategies
- Lead benchmarking of Operations-related topics in support of divisional goals
- Perform general management duties, exercising usual authority concerning staff, performance appraisals, promotions and terminations. - - Responsible for training and development of subordinate staff, estimating personnel needs, assigning work, meeting completion dates, interpreting and ensuring consistent application of organizational policies
- Act as a team role model and change-agent
- Positively lead and influence team members to partner together to achieve individual and business goals
- Coordinate team efforts, create and manage a regional strategy and team operating plan
- Bachelor’s Degree in Business, Engineering or related field required
- 8+ year’s successful multi-functional Operations experience including management and employee development
- Working knowledge of modern manufacturing, material flow and improvement strategies (e.g. six sigma, continuous flow, cellular etc.) and the ability to integrate those into the operation
- Skilled in analyzing and drawing information for long-term strategic change and improvement for the site
- Skilled in leading significant multi-site, multi-functional or business project initiatives, scheduling and planning
- Demonstrated understanding of financial systems and the key drivers within the manufacturing environment
- Strong organizational skills in strategy, communication at all levels and execution
- Demonstrated experience in leading and managing individuals and teams
- Operational knowledge of the applicable systems
- Strong financial and business acumen
- Excellent written, verbal communication and presentation skills, in Mandarin as well as English
- Excellent teamwork, leadership, relationship building, mentoring, training and project management experience and skills
37
Water Treatment Plant Manager Resume Examples & Samples
- Responsible for operation of surface water plant in accordance with GA DNR EPD regulations
- Responsible for decisive and timely action in response to production, utilities and environmental upsets
- Manages all plant operations, plant maintenance, laboratory analysis and reporting requirements
- Responsible for planning and directing operations and maintenance as well as plant operators and plant maintenance staff
- Budgetary responsibility for all plant operations and maintenance as approved by the Program Manager
- The Plant Manager has primary contact with the client on plant operations and maintenance
- Ability to effectively communicate with the sites integrated areas
- Manages operators and maintenance staff, reviewing their performance, allocating work, determining workforce needs and recruiting new employees, as well as disciplinary actions
- All managerial duties are subject to approval by the Program Manager
- Work in both hot and cold environments, inside and outdoors
- Ability to move throughout the entire plant site & operating areas including climbing ladders and stairs, to access elevated sources for inspection and operational purposes
- Assist with job safety analysis / safe work permitting and bench top analysis as needed
- Ability to work effectively within a team environment with internal and external personnel & regulatory agencies
- Responsible for parts and inventory control
- 8-10+ yrs; high school diploma or GED
- Highest level state approved Water / Waste Water Operator Certificate
- Experienced with SCADA system to monitor and control plant operation and distribution
- Computer experience in Excel, Word & other software
- Valid GA Driver’s License
38
Plant Manager, Thermal Resume Examples & Samples
- Responsible for Safe overall operation of plants included in the assigned Energy Center including effective management of staff required to operate the plants as needed on a 24/7/365 basis to provide steam, hot and chilled water,
- Communicate effectively with customers, vendors and other NRG personnel to properly communicate plant status or operational updates, carry out the coordination and completion of projects safely, timely and effectively, and provide other ancillary services to customers to provide additional value related to customers’ operation of the their building environment. This includes ensuring reliability and redundancy of the system to provide energy services greater than 99.999% up time at a reasonable cost to the customer
- Project lead on site level activities which includes generating, developing, and executing projects within the plants as well as within the Energy Center’s distribution system
- Perform as a Project Manager, if necessary, for capital projects by providing input to engineering regarding quality review of project assumptions and operational feasibility of projects, preparing all necessary documents and system input of approved projects necessary to allow completion, work with procurement department for bid preparation documents, prepares project schedule with input from construction, supports construction on the installation and testing of the project and writes a project completion report addressing cost variances
- Coordinate engineering analysis, inspections and support to operations to keep existing equipment running at their maximum reliability and performance levels while maintaining personnel safety, asset safety and environmental compliance. Work with engineering to develop and manage appropriate capital expenditure budgets
- Review and analyze predictive and preventive maintenance data to determine appropriate major maintenance and normal maintenance projects. Work with engineering to develop and manage appropriate maintenance budgets
- Monitor plant efficiency. Identify and troubleshoot deviations from expected values that would improve plant asset performance
- Make recommendations on reducing operational and maintenance expenses either by improving system design, modifying system practices, recommending alternate equipment designs, etc
- Review fuel consumption and energy production to ensure in compliance with or better than budget
- Provide long range planning for maintenance, repair and capital improvement projects in conjunction with engineering
- Ensure appropriate operating permits are maintained
- Stay abreast of developments in the district energy industry and recommend modifications or practices that could improve safety, performance, availability and reliability
- Provide a technical leadership role
- Provide technical support of equipment commissioning and start-up
- Lead performance tests, equipment performance monitoring and trending
- Compile and analyze operating data and help develop operational plans and equipment recommendations to optimize facility performance and profitability
- Assist in the development of various operations and data reports for internal and external distribution
- Direct maintenance staff regarding mechanical/maintenance issues, ensuring compliance for piping and valves, pumps and exchangers, etc
- Support the development and review of operating procedures
- Supervise the O&M staff and promote and support the development of technical, leadership, and business skills of employees to carry out responsibilities safely in a competitive personnel recruiting environment
- Ensures regular feedback is provided to employees on their performance to allow them to capitalize on their strengths and focus on opportunities for improvement
- Assigns work and holds employees accountable for their performance
- Manage contractors and maintain complete equipment and systems maintenance, test history, and design configuration databases
- Recruit and retain appropriately certified and qualified personnel in all assigned positions. Assist with creation of recruiting programs as needed and possible to attract top talent to the company
- Support the establishment and enforcement of safe working conditions and practice safe work habits in all activities
- Responsible for customer metering activities and customer technical support
- Basic knowledge of industrial water treatment (specialty chemicals and boiler pretreatment) and responsible for cost effective management of associated programs
- Head of Safety Committee
- Establish a rapport with local environmental regulatory officials impacting company operations
- Maintain close relationship with local utility supply personnel
- Coordination and/or Management of necessary consultants needed to accomplish engineering and regulatory tasks
- Manage LOTO, Fall protection, Confined space and electrical safety programs
- 7 – 10 years of experience in District Energy preferred or leadership experience within Power, or Industrial facilities such as a Navy powerplant leadership experience
- Demonstrated effective leadership and personnel management skills – 3-5 years experience
- Excellent quantitative skills
- Ability to learn quickly and work under pressure and multitask
- Strong computer skills to include spreadsheets, project management, databases, and word processing
- Superior interpersonal skills
- Proven planning and organizational skills
- High tolerance for stress; ability to adapt to changing requirements and quickly bring assignments to completion
- Demonstrated ability to exercise sound judgment and to identify problems and solutions without constant guidance
- Uses discretion concerning confidential and sensitive company information
- Displays good judgment, willingness to take responsibility and initiative to make decisions within scope of responsibility
- Team player able to work with all levels of the organization
- Demonstrated ability to effectively communicate (written and verbal) at all levels of the organization
39
Plant Manager, / Plant Director Resume Examples & Samples
- Leading a non-union manufacturing facility of approximately 278,000 sq. ft. that makes veggie products (burgers, nuggets, links, bacon, etc.)
- Overseeing a facility that consists of 322 employees with sales of $300 million and volume of 48 million pounds
- Providing strategic direction to 9 senior leadership team members across Finance, Human Resources, Quality Food Safety, Logistics, Manufacturing & Reliability, Maintenance, Facilities, Operations and Environmental Health and Safety
- Responsibility for the following
- Significant of years of related work experience
- Substantial years of experience as a Plant Manager/Director overseeing a medium to large facility
- Interpersonal skills
- Strategic Planning skills
- Financial and business management skills
- Ability to deal with multiple, high-priority issues and excel under stressful conditions
- Leadership skills including – Creates Direction, Drives Alignment, Inspires and Energizes People, Delivers Quarterly Results, Invests in People and Organizes to Win
- Effective Communication skills (verbal and written)
40
Cement Plant Manager Resume Examples & Samples
- Manage the operations and maintenance staff to ensure timely production and distribution of products within quality standards, high uniformity, and optimum production costs
- Responsible for the development and execution of annual operating plans
- Oversees the development and supervises the execution of Capital Expenditure plans
- Reviews cost reports to locate excessive expenses and takes necessary corrective action
- Prepare short and long range development plans
- Establish goals that reflect continuous improvement in plant operations
- Assure environmental compliance and clean plant operations
- Train and develop supervisors to provide management depth; provide motivation and career enhancement for all employees
- Review requests and make decisions regarding the purchase of new equipment and supplies
- Participate directly in labor relations, including grievance handling; member of the contract negotiating team
- Proactively manage safety and health of employees to continuously improve the company’s safety and health performance
- Bachelors’ degree in Engineering preferred
- Prior experience with increasingly responsible positions within the cement industry; minimum of 10 years’ experience required
- Complete understanding of the cement manufacturing process and experience with cement production technology
- Strong knowledge of modern maintenance technology and methods
- Demonstrated ability to optimize production costs
- Strong analytical and decision making skills
- Solid interpersonal skills and demonstrated ability to lead others
- Knowledge of union contracts and/or prior experience working in a union environment strongly preferred
- Good understanding of safety and environmental regulations
41
Plant Cluster Manager Resume Examples & Samples
- Exemplify the Sealed Air Safety behaviors you are expecting from your team
- Establish and communicate clear goals and deliverables. Support and foster a high performance work team that encourages collaboration and continuous improvement
- Site Safety Champion responsible for the deployment of the Sealed Air EH&S program
- Site Quality Champion responsible for the deployment of the Sealed Air QA program
- Ensure all Federal, Provincial, and Local permitting / compliance requirements are complete and on-time
- Responsible for ensuring the Canadian manufacturing operation achieves all strategic service targets
- Responsible for development and delivery of the annual operating plan (AOP) and the delivery of the plant capital budget
- Site continuous improvement champion responsible for effectively deploying the Sealed Air Production Management System to increase capacity and achieve strategic cost savings goals
- Ensure an effective employee engagement team is established and is focused on developing meaningful targets and delivering measurable results
- Handle employee relations issues focused on creating a positive “work team” based environment. Ensures the administrative HR requirements are met
- Maintain ISO 9001 & 14001 certifications and deliver plant quality KPI’s through SOP adherence, training and continuous improvement
- Bachelor's Degree in Engineering, Supply Chain or Business required, MBA preferred
- Minimum of 10 years of management experience, with 3+ years at a senior management level in manufacturing operations in a Plant Manager capacity required
- Seasoned experience in all facets of manufacturing operations including: Bulk Processing, Filling/Assembly, Warehousing, Continuous Improvement
- Broad knowledge of supply chain process and procedures (manufacturing, distribution, supply planning, engineering, etc.)
- Experience in high volume/high mix, multi-shift manufacturing environment
- Solid finance and cost accounting acumen
- Strong leadership & managerial skills, and ability to motivate others
- Collaboration, and creative problem solving skills
- Experience with SAP (Production & Inventory control), Strong with Word, Excel, PowerPoint, etc
42
Plant Manager, Secure Shredding Resume Examples & Samples
- Degreed college education
- Manufacturing experience and maintenance experience
- Someone with 5+ years of experience
- Local applicant preferred (LA and Orange County..)
- Definitely looking for someone who has upward potential
- Some experience in recycling would be a plus
- Military experience a plus
- Six Sigma/lean processes a plus
43
Plant Manager Cscm Resume Examples & Samples
- Manages the day-to-day operational and financial operations of a Healthcare/CSCM plant
- Responsible for plant P/L
- Plans, directs, and coordinates production, filling, maintenance, and distribution activities to meet customer needs at minimum investment required
- Ensures all safety, quality, regulatory, accreditation procedures and policies are implemented and staff appropriately trained
- Forecasts future trends, needs and develops action plans which will enable the plant to meet the predicted situation
- Develops operating strategies and plan to pro-actively prepare for future demands based on analysis of current and past results
- Maintains strong customer service focus for all Plant employees; develops and monitors distribution schedules to ensure customers are served in a timely manner
- Responsible for representing company by ensuring employees and plant meet standards established by organization and cleanliness
- Develops profit plan for plant using strong P&L knowledge including actions required to meet cost and efficiency targets
- Facilitates communication within the plant by communicating with staff members keeping them informed of initiatives, strategies, and operational change
- Maintains professional growth by participating on teams and in educational programs and activities to maintain knowledge of national trends and to promote leading-edge expertise within the plant
- Motivates and encourages employees to participate in team building activities
- Manage and maintain local HQAA policies, procedures and compliance
- Ensures specific federal, state and local employment qualifications are met
- Ensures customer complaints are reported, cause is investigated and corrective actions are implemented
- Ensures local, state and federal regulatory requirements (FDA, DOH, DOT, OSHA etc) are met
- Represents the site during external regulatory inspections including, but not limited to US FDA, OSHA, and State Boards of Pharmacy
44
Mce Plant Manager Resume Examples & Samples
- Knowledge of all aspect of apparel manufacturing and production methods, production planning, quality and inventory control
- Background in fabric handling, purchasing and stock control is a plus
- Experience in scheduling expenditures; analyzing variances; initiating corrective actions in reconciling inventory of both Raw Materials and Finished Goods
- Experience determining product handling and storage requirements; developing, implementing, enforcing and evaluating policies and procedures; developing processes for receiving product; determining equipment utilization; inventory management and shipping of Finished Goods; inventory management of Capital Equipment/fixed Assets
- Knowledge of industrial equipment relevant to Textiles (Pattern-Making and Cutting Room equipment, sewing, machines, garment pressers and embroidery machines) is preferred
- Experience troubleshooting mechanical problems that hinder the flow of production is not required, but is a plus
- Must be computer literate, including intermediate knowledge of Microsoft Word, Excel and MS Office Suite
45
Feed Plant Manager Resume Examples & Samples
- Bachelor’s degree (additional years of experience may offset education requirement)
- 5 years of feed operations & manufacturing experience
- 3 years of supervising experience
- Working knowledge and experience with government regulations
- Knowledge of Safe Feed / Safe Food programs
46
Plant Manager Melle Resume Examples & Samples
- Safety, Health, Environmental, Food Quality and Safety & Core Values
- Leads identification and prioritization of risk reduction opportunities, establishes clear priorities and supports effective resourcing to drive improvement at the site. (SHE/PSM, Site security)
- Leads relationship with local authorities including safety, food safety, health regulatory agency, customs, police
- Maintains positive community relations through active participation in local organizations
- Accountable for leading and managing the site’s Environmental, Occupational Health and Safety, Quality and Food Safety Management Systems (ISO14001; OHSAS 18001, ISO9001, BRC, pharma agreements et FDA requirements
- Encourages employee’s engagement and fosters empowerment and ownership through leader standard work practices
- Establishes and ensures the effectiveness of two-way communication processes across the site
- Manages staffing strategy (core/ variable, overtime management and labor planning)
- Strategically guides employee and labor relations including working with site’s third party representation
47
Plant Manager Tier Resume Examples & Samples
- Must have requisite leadership skills and experience to thoroughly develop/challenge the organization to achieve high performance
- Must be a self-starter who can accomplish results in an ambiguous environment with little or no direction
- Diplomacy
48
Manager, Inside Plant Resume Examples & Samples
- 8+ years of Head End Technician, Cable Technician or Electronics work experience
- 2+ years of Engineering experience
- 4+ years of Management experience
- 2+ years of Project Management experience
49
Assistant Manager Plant Quality Resume Examples & Samples
- Maintain production processes and products quality
- 6 – 8 years’ experience in manufacturing and quality function environment (Preferably Gear/Transmissions Manufacturing Industry)
- Knowledge of machining, assembly operations, gauging, process capability, SPC, APQP, and quality assurance systems (ISO/TS 16949)
- Extensive knowledge and experience with AIAG Core Tools (SPC, PFMEA, PPAP, APQP & MSA). preferred
- Six Sigma, Project management, Interpersonal Communications and Leadership Skills Development
- Problem solving thru 8-D using Fishbone, FTA (Fault Tree Analysis) & Why-Why analysis, knowledge of Six Sigma preferred
50
Feed Plant Manager Resume Examples & Samples
- Manages product quality control of all finished feeds and various inbound products from rail and road
- Supervises all full and part time employees
- Manage all safety processes – Monthly safety training, hazard identification, corrective actions and be an overall safety leader
- Observe OSHA, State, and Federal Regulations
- Maintain equipment and facilities regularly, follow housekeeping standards
- Improve and adjust procedures to maintain highest standard of quality
- Train new employees and observe performance
- Over see facility projects and repairs
- *Employer provides Competitive Salary and Excellent Benefits!***
- BA/BS in AgBusiness or Ag-Related degree preferred
- 3+ years experience in Feed Mill Operations
- Experience with batch feed manufacturing, pelleting, flaking, or grinding
- Understanding of Inventory Control and Inventory Procedures
- Proven Supervisory and Management experience required
- Ability to read and analyze technical procedures, or governmental regulations
- Ability to write reports, business correspondence, and procedure manuals
- Strong Analytical / Problem Solving Skills a must
- Solid Computer Skills with spreadsheet and word processing software
51
Materials Manager Plant Resume Examples & Samples
- Customer Service Levels – delivery in full and on time (DIFOT)
- Total Inventory (raw and in-process, finished goods)
- Identification and implementation of lead time reduction programs (consignment, vendor managed inventory, localization, MOQ’s, etc)
- Maintain relationships with key vendors, influencing how Ecolab leverages Just-In-Time and vendor managed inventories
- Utilize timely and effective communication of delays in production that may result in late orders
- Generate and implement new ideas to reduce costs and increase product availability
- Exhibit safe work habits to ensure a safe working environment and comply with company safety regulations and guidelines
- Master Data Maintenance (A/B/C part classification, forecasts, safety stocks, etc.)
- Effectively manage your team, building their talent through your leadership, communication, and engagement
- Bachelor’s degree in Business, Finance, Supply Chain, Engineering, Science, or a related field
- 5+ years of experience in supply chain, planning, and/or procurement
- 2+ years of supervisory experience (goal-setting, team building, onboarding, coaching, etc.)
- Solid understand of Planning and Purchasing methodologies (forecasts, safety stocks, replenishment strategies, inventory optimization, lead time reduction, Kanban, etc.)
- Proficiency with data analytics (databases, MS Excel, and presentations)
- Demonstrated experience in operational excellence (lean six sigma, TPM, loss analysis, root cause, permanent corrective actions, etc.)
- SAP experience is a plus