Assistant Plant Manager Resume Samples
4.5
(139 votes) for
Assistant Plant Manager Resume Samples
The Guide To Resume Tailoring
Guide the recruiter to the conclusion that you are the best candidate for the assistant plant manager job. It’s actually very simple. Tailor your resume by picking relevant responsibilities from the examples below and then add your accomplishments. This way, you can position yourself in the best way to get hired.
Craft your perfect resume by picking job responsibilities written by professional recruiters
Pick from the thousands of curated job responsibilities used by the leading companies
Tailor your resume & cover letter with wording that best fits for each job you apply
Resume Builder
Create a Resume in Minutes with Professional Resume Templates
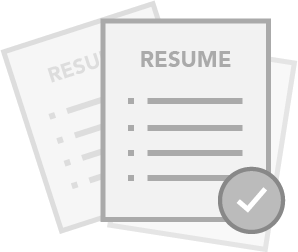
CHOOSE THE BEST TEMPLATE
- Choose from 15 Leading Templates. No need to think about design details.
USE PRE-WRITTEN BULLET POINTS
- Select from thousands of pre-written bullet points.
SAVE YOUR DOCUMENTS IN PDF FILES
- Instantly download in PDF format or share a custom link.
BT
B Treutel
Brionna
Treutel
759 Reichel Overpass
Houston
TX
+1 (555) 488 1523
759 Reichel Overpass
Houston
TX
Phone
p
+1 (555) 488 1523
Experience
Experience
Houston, TX
Assistant Plant Manager
Houston, TX
Pouros-Lind
Houston, TX
Assistant Plant Manager
- Analyzes and resolves work problems or assists workers in solving work problems
- Manage and lead to provide leadership as directed by Plant Manager and/or in Plant Manager’s absence
- Analyzes and resolves work problems, or assists workers in solving work problems
- Lead and develop employees to improve their capabilities and personal performance using Market-Based Management® Principles
- Assists in the development of plant goals and may work through subordinate employees to achieve same
- Works with plant managers to develop yearly budgets
- Assists the Operations Manager managing Manages profit and loss for the facility
Philadelphia, PA
Kemps Assistant Plant Manager
Philadelphia, PA
Leannon Inc
Philadelphia, PA
Kemps Assistant Plant Manager
- Leads and coordinates the activities of production/cooler supervisors, dispatchers/expediters, and other plant employees engaged in the production or load out of dairy products to ensure safety, quality, and customer standards are met. Responsible for overall plant operations in Plant Manager's absence
- Strong working knowledge of dairy industry production practices, processes, and equipment
- Initiates personnel actions such as promotions, transfers, discharges, and disciplinary measures. Reviews actions brought forth by production/cooler supervisors. Evaluates union employees on successful completion of probationary periods
- May be responsible for monitoring the intake procedures of raw dairy products, ensuring high quality standards are met and product shortages are avoided. May be responsible for ordering dairy products
- Strong working knowledge of general business concepts and practices, especially as they relate to the dairy business
- May be responsible for the identification of damaged and erroneously delivered orders. May work with supervisors and cooler employees to correct shortages or discrepancies in product stock levels
- May be responsible for supervising clean-up operations to obtain optimum production and utilization of manpower, machines, and equipment. May coordinate production activities with procurement, maintenance, and quality assurance
present
San Francisco, CA
Assistant Plant Manager Bacon Complex
San Francisco, CA
Daniel and Sons
present
San Francisco, CA
Assistant Plant Manager Bacon Complex
present
- Prepares and submits operating reports to management, makes recommendations to improve efficiency and effectiveness
- Provides managerial oversight on job assignments, scheduling and supervision
- Assist in establishing production and processing goals for plant
- Manages approximately 20 subordinate salaried exempt partners in a plant of approximately 300 hourly workers
- Directs production and ensures cost effectiveness and consistency with prescribed quality, accuracy and performance standards
- Selects, trains, develops and motivates manufacturing staff to maintain plant operation
- Confers with Plant Manager, Safety Manager, QA Manager, Shift Superintendents and Production Supervisors to analyze production schedules to plan and project cost effective production processes
Education
Education
Bachelor’s Degree in Business Administration
Bachelor’s Degree in Business Administration
Northwestern University
Bachelor’s Degree in Business Administration
Skills
Skills
- Proficient in quality methods and process performance (e.g., statistical problem solving and process capability analysis, FMEA, Control Plans)
- Strong written and verbal skills and the ability to complete detailed reports and make presentations
- Basic understanding of physical properties of various gases and chemicals and general knowledge of laws of Partial Pressure
- Ability to perform basic math functions
- Excellent problem-solving skills and strategic thinking ability
- Detail oriented with the ability to complete handwritten compliance documentation neatly and accurately
- Good analytical skills
- Develop Employees through coaching and Mentoring
- Thorough understating of production facilities, assembly and distribution operations
- Five or more years of Supervisory Experience
15 Assistant Plant Manager resume templates
Read our complete resume writing guides
1
Assistant Plant Manager Resume Examples & Samples
- Minimum 5+ years in Plant Operations management experience / Production / Maintenance related field
- Demonstrated capability to successfully partner with peers and senior business leaders
- Experienced in change management
- Bilingual (English and Bahasa Malaysia and/or other appropriate language)
- Skills (applied knowledge and technical skills directly related to this position)
2
Assistant Plant Manager Resume Examples & Samples
- Principal Accountabilities will include many of the below activities. Given that this is a newly acquired Cargill facility, additional responsibilities related to the integration will apply.)
- Maintain a system that evaluates process improvement sheets and model reports for accuracy and changes in trends, and act on any adverse trends or lack of accuracy
- Understand plant audits and results and respond to deficiencies including HACCP
- Employees must be educated and trained to perform their jobs safely and to accept responsibility for their own safety performance
- Maintain physical condition and appearance that reflect the standards of quality and service of our business and the character of our people professionally represents the brand image
- Understand the plant flow and what restrictions or bottlenecks cost vs. the cost to remove those restrictions or bottlenecks
- Maintain a system that sets standards on quality and customer service
- Utilize a tool (activity schedule) to help manage and execute the numerous requirements you are accountable for
- Coordinating the logistics for the shipping and receiving of animal feed monthly
- Lead a group of highly engaged employee's in such an environment
- Participate in some production activities
- Daily paperwork review
- Lead and manage maintenance teams including using systems for planned maintenance
- Manage daily production scheduling, inventories and cost management
- 2+ years of experience working in a manufacturing environment
- 1+ years of experience in a supervisory role - preferably in a manufacturing environment
- Ability to lift up to 50 pounds
- 2 + years of maintenance experience in a manufacturing environment
- 3 + years in a high-speed manufacturing packaging environment
- 3 + in EH&S compliance
- 1 + year experience in Food Safety quality and regulatory compliance
3
Assistant Plant Manager Resume Examples & Samples
- 20% - Maintain a system that evaluates process improvement sheets and model reports for accuracy and changes in trends, and act on any adverse trends or lack of accuracy
- 20% - Understand plant audits and results and respond to deficiencies including FSQR
- 15% - Employees must be educated and trained to perform their jobs safely and to accept responsibility for their own safety performance
- 15% - Maintain physical condition and appearance that reflect the standards of quality and service of our business and the character of our people professionally represents the brand image
- 10% - Understand the plant flow and what restrictions or bottlenecks cost vs. the cost to remove those restrictions or bottlenecks
- 10% - Maintain a system that sets standards on quality and customer service
- 10% - Utilize a tool (activity schedule) to help manage and execute the numerous requirements you are accountable for
- Right to work in the U.S. that is not based solely on possession of a student visa or a visa sponsored by a third-party employer
4
Assistant Plant Manager Resume Examples & Samples
- Responsible for managing daily production on multiple shifts, ensuring compliance with company policy, quality assurance, regulations established by FDA, EPA, and OSHA and following GMPs
- Responsible for providing leadership, managing, hiring, training, coaching and developing production and maintenance personnel and Safety Coordinator
- Responsible for Safety—promoting safe behavior, implementing safety programs and oversight of training requirements
- Responsible for the execution of approved capital and maintenance projects
- Responsible for maintaining and updating production SOPs
- Responsible for managing all production related expenses (overtime, equipment repairs and maintenance, and supplies)
- Will develop an annual operation plan to include productivity and efficiency improvements, automation and quality advancements and employee development
5
Assistant Plant Manager Resume Examples & Samples
- Solid background of production and engineering management, Honest, Righteous, Diligent, Carefully, Studious
- Technical or finance Universities with English, MBA qualifications is an advantage
- 5-10 years’ Experience in manufacturing management, at big FDI manufacturing is an advantage
- Interpersonal skill to production people and other depts
- Hand-on experiences in production management and engineering skills
- Experiences in FDI manufacturing environment: Benchmarks, safety, performance management and interpersonal skills
6
Assistant Plant Manager Resume Examples & Samples
- Assists the Plant Manager with effective and efficient operations of assigned manufacturing plant(s), to include engineering, manufacturing, purchasing, materials, planning, production, quality, etc. Assists with plant performance to meet divisional goals and provides for the right skills mix and production processes to meet or exceed internal and external customer requirements and specifications
- Exercises direct supervision over departmental or general supervisors with respect to production volume, cost and quality of production, meeting production schedules and delivery dates
- Stimulate maximum efficiency and productivity of both supervisors and production workers. Encourage efficient utilization of equipment and facilities. Develops plans for efficient use of materials, machines and employees
- Assures the availability of material to meet manufacturing plans consistent with customer needs, inventory restraints and profit requirements by managing the materials function including imports, purchasing, inventory control and planning. Assists with logistics function from inbound freight, receiving, warehousing, line stock, project inventory, work in progress, stock in progress, work order management through outbound freight, etc for all functional areas
- Confers with Plant Manager in establishment of shift standards and working schedules for all departments connected with production. Maintains compliance to budgetary limitations and directing and coordinating activities to ensure goals and objectives are accomplished within prescribed time frame and funding parameters; managing all aspects of requirements, design, development, implementation and testing of assigned projects
- Proactively seeks ways to apply technology to business processes, researching and providing information on technical trends and competitors’ practices; stays abreast of industry trends, technology changes and “best practices”,proactively identifying opportunities to enhance production technology, process flows, operating and tactical plans to improve efficiency, product quality and manage cost
- Manages production functions for padding and cushion plant, which includes reviewing production orders and/or schedules to ensure that production requirements are optimal, and are completed according to established production schedules. Resolves operational, processing and maintenance problems to ensure minimum costs and production downtime
- Ensures the availability of material to meet manufacturing plans and manages all inventory requirements to support the plant and division goals. Actively participates on Division short- and long- term strategic planning meetings and projects
- Continuously improves all production methods while adhering to all safety procedures. Responsible for training and development of hourly employees, estimating personnel needs, assigning work, meeting completion dates, interpreting and ensuring consistent application of organizational policy
- Schedules personnel and assigns work to meet production requirements in an efficient and cost effective manner. Ensure adherence to established priorities for production workflow. Assists with planning, developing and administering departmental procedures, policies and standards, ensures organization policies and procedures are communicated and practiced. Develops appropriate measures or standards for performance and uses these to monitor, evaluate and continuously improve employees and production. Maintains shift reports and records. Verifies employee hours worked in KRONOS
- BS degree in a related discipline or an equivalent combination of education, training and experience that provides the required skills and knowledge to perform the essential function of the job. Five to eight years of progressively responsible job specific experience that includes
- Experience working in a manufacturing environment overseeing multiple production functions simultaneously
- 8 years in a leadership/management role in an environment of comparable size and diversity
- A working knowledge of Labor Law and related laws as set forth in National decree that regulates the industry
- Knowledge of Mohawk’s vision, mission organizational and functional operating structure, products, administrative procedures and policies
- Working knowledge and understanding of HR policies, practices and procedures as it relates to employee relations, hiring, terminations, benefit and compensation plans and administrative guidelines
- Demonstrated experience and understanding of product development life cycle, dynamics of manufacturing environments, operational and tactical plans, processes and techniques
7
Assistant Plant Manager Resume Examples & Samples
- Understands key drivers of operational excellence metrics for the business
- Continue to drive the safety performance of the facility to achieve safety excellence by empowering employees to understand and accept their roles to meet expectations
- Make working safely the top priority. Continue to improve safety performance through utilization of job hazard analysis, safe work permitting, and behavior based safety, root cause analysis, housekeeping and training
- Maintain and improve plant process safety information, support and participate in process hazard analysis
- Conduct & follow-up on incident investigations in our pursuit of an incident-free work environment
- Sets high standard for self and others for behavior in the workplace and refuses to allow inappropriate behavior in others – Code of Conduct, Compliance, Guiding Principles
- Lead and develop employees to improve their capabilities and personal performance using Market-Based Management® Principles
- Drives change through challenging the status quo and focusing on continual improvement
- Leverages the strengths of the management team, and seeks the input of others to improve decisions and results
- Effectively uses Root Cause Analysis to identify system failures and gaps
- Ensure a robust Management of Change (MOC) process
- Participate in all applicable Operations Excellence efforts associated with the areas of production efficiencies, product yield, operating costs and product quality
- Bachelor's Degree or higher in a Technical or Business field – OR – an Associate’s degree in a Technical or Business field and two (2) or more years of gypsum products manufacturing experience
- A minimum of five (5) years of experience working in a manufacturing or industrial environment
- A minimum of five (5) years of supervisory experience
- Employee performance management experience, including expectation setting, and coaching, counseling and developing employees
- Experience with root cause analysis, process improvement/optimization, and project planning and execution
- Able and willing to work in a manufacturing plant environment, including extended periods of time in noisy, dusty, non-air conditioned or unheated areas
- This is a day shift position, however you must be able and willing to work nights, weekends, and holidays, when needed
- Knowledgeable of Occupational Safety & Health Administration (OSHA) regulations and policies
- Intermediate or higher level proficiency with Microsoft Word and Excel, and the ability to learn various PC-based operations and production applications
- Strong teambuilding skills and the ability to work within a diverse team
- Experience analyzing financial and production data, including department budgets, cost tracking, and forecasting
- Bachelor’s Degree or higher in a Technical field
- Gypsum Wallboard or Building Products manufacturing experience
- Six Sigma Green Belt certification or similar training
- Knowledgeable of Mining Safety & Health Administration (MSHA) regulations and policies
8
Assistant Plant Manager Resume Examples & Samples
- Develop and oversee employee safety programs
- Manage and oversee the daily activities of supervisors, coordinators, office and operations specialists, and contract employees in a multi-shift operation
- Manage manufacturing and shipping schedules to ensure on-time delivery of multiple, line-sequenced just-in-time product orders for the Peterbilt and Kenworth truck plants as well as aftermarket customers
- Partner with Human Resources to ensure appropriate hiring, orientation, training, performance reviews, counseling and disciplinary actions of employees
- Champion multiple Six Sigma projects
- Assist in the research, document preparation, coordination and direction of major plant projects involving cost reduction and new product manufacturing setup and implementation
- Ensure local compliance with Dynacraft quality programs and maintain quality standards per ISO and QS requirements
- Assist in planning and implementation of annual operating and capital budgets. Control monthly operating expenses and maintain necessary records and documentation
- Assist in devising, reviewing and implementing methods for improving productivity and efficiency
- Maintain effective communication with division office and serve, as needed, as liaison between departments to ensure maximum cost-savings and efficient manufacturing and distribution operations
- Assist in development of strategic direction for the MDC in support of Dynacraft’s vision establish specific goal in support of the direction
- Maintain effective communication with the Division office in Algona, WA and with lateral organizations
- Leadership Skills and Ability to Supervise Employees
- Develop Employees through coaching and Mentoring
- Thorough understating of production facilities, assembly and distribution operations
- Five or more years of Supervisory Experience
9
Assistant Plant Manager Resume Examples & Samples
- Manages the overall safety, quality, scheduling, production, shipping, maintenance and other administrative functions for the facility
- Leads the effort in maintaining a safe, clean and efficient operation working within all company guidelines and local/state/federal regulations
- Strives to improve the plant's safety accident record year over year in creating a positive safety culture for all employees. Conducts safety walks of the facility on a weekly basis
- Ensures that the facility provides the highest quality products produced in the most efficient manner within budgeted costs. Implements systems to effectively manage production schedules properly supporting the business
- Drives Plant performance and reviews KPIs regularly (Daily, Weekly and Monthly)
- Works with scheduling, sales and operations to establish production schedules and/or make changes as needed
- Conducts talent reviews. Trains, develops and motivates staff in an effort to optimize the workforce. Delivers performance reviews and any feedback to the team as needed
- Leads the effort and drives Lean Manufacturing tools and techniques fostering continuous improvement within the facility. Acts in a proactive fashion in regard to problem resolution
- Conducts weekly staff meetings which focus on key operative measurements
- Schedules and conducts plant communication meetings for all employees
- Works as necessary to establish positive community relationships
- Interfaces with customers and suppliers and visits both as necessary
- Assists the Operations Manager managing Manages profit and loss for the facility
- Leads the overall strategic planning efforts for the location which include cost reduction initiatives, capital planning and resources as well as in other areas
- Please email your resume, and salary, immediately to: kmarold@snifinancial.com
10
Assistant Plant Manager Resume Examples & Samples
- Initially work in conjunction with the Plant Manager to establish a Dynacraft Texas plant including planning and managing the facility start-up, staffing ramp-up, and start of production for product programs
- Assist in the research, document preparation, coordination and direction of major plant projects involving cost reduction, new product manufacturing setup, activities to move from the temporary to permanent plant
- Develop and oversee Best in Class employee safety programs
- Manage and oversee the daily activities of supervisors, team leaders, office and operations specialists, and contract employees in a multi-shift operation
- Manage logistics / returnable container deployment and administration
- Leadership skills and ability to supervise employees
- Five or more years of supervisory experience
- Proficient in quality methods and process performance (e.g., statistical problem solving and process capability analysis, FMEA, Control Plans)
- Bachelor’s degree in business administration, management, engineering or other appropriate field
- Master's degree desired
- Six Sigma training strongly desired
11
Assistant Plant Manager Resume Examples & Samples
- A four year college degree, preferred
- Minimum of 2 years production supervisory experience, preferred
- P&L and budget experience, preferred
12
Assistant Plant Manager Resume Examples & Samples
- Operate and safely maintain plant for pumping or repackaging gases into cylinders while ensuring compliance with all federal, state, local and company policies, procedures, regulations and laws
- Manage and lead to provide leadership as directed by Plant Manager and/or in Plant Manager’s absence
- Ensure all injuries and accidents are properly investigated and reported within 24 hours
- Resolve problems associated with plant operation
- Ensure all safety rules are strictly observed and safety training is regularly scheduled, conducted and documented
- May assist Plant Manager with providing coaching and corrective action promptly, to ensure that poor performers are identified, documented and improved to acceptable performance, or released
- May approve overtime when essential, while keeping overtime at acceptable levels
- Ensure associate complaints, grievances, etc. are effectively handled
- May assist Plant Manager with ensuring that pre-employment documentation and physical examinations are completed in a timely manner
- May fill in or assist associates in the loading, unloading, sorting, filling, analyzing, movement, maintenance, retesting, and storage of compressed and liquid gases into cylinders
- Additional duties as required: This job description should not be construed to imply that these requirements are the exclusive standards of this position. Incumbents are expected to follow any other reasonable instructions, and perform any other related duties, as may be required by their supervisor. Performance of this job in a safe manner and in keeping with established Airgas policies is a condition of employment
13
Assistant Plant Manager Resume Examples & Samples
- Coordinate activities to work within budgets, control expenses, and provide necessary reports and information for capital expenditure reports
- Coordinate the proper inventory levels of cylinders and products
- Monitor capital cash flow to assure that regional plans and budgets are controlled to agreed limits; and promote efficiencies
- Promote development and cross training of staff
- Operate and safely maintain the high pressure gas repackaging plant while ensuring compliance with all federal, state, and local and company policies, procedures, regulations, and laws
- Manage and lead subordinate supervisors to provide leadership 20 or more associates
- Conduct periodic checks of each operation unit for safe and efficient operation
- Ensure monthly safety meeting are conducted
- Maintain neat, clean and orderly plant appearance. Maintain compliance with Airgas housekeeping policies
- Provide coaching and corrective action promptly, to ensure that poor performers are identified, documented and improved to an acceptable performance level, or released
- Approve overtime when essential, while keeping overtime to acceptable levels
- Ensure employee complaints, grievances, etc. is effectively handled
- Ensure pre-employment documentation and physical examinations are completed in a timely manner
- Coordinate with other work groups within the region to determine priorities regarding allocation of operation resources to all capital investment projects
- Coordinate the procurement and organization of supplies and equipment for production to reduce downtime and promote efficiencies
- Coordinate the proper inventory levels of supplies and equipment
- Production levels
- Cylinder control
- Wage and salary expense
- Equipment repair expense
- Supply and equipment expense
- Experience supervising, motivating and leading employees, preferably in a manufacturing environment
- Thorough understanding of CFR 49, Parts 100 to 177 and have the ability to apply these regulations to the specialty gases produced
- Computer skills, including working knowledge of Microsoft Office or similar software suite
- Ability to perform work during prolonged standing up to 8 hours; Frequent bending, stooping, crouching, reaching, grasping, feeling and repetitive motion also required
- Ability to perform work during occasional climbing, balancing, kneeling, pushing, pulling and finger activities
- Ability to read and comprehend Materiel Safety Data Sheets (MSDS)
- Ability to work flexible schedule to meet management requirements and customer expectations
- Ability to work with a wide variety of people with different personalities and backgrounds
- Ability to work outdoors in temperatures ranging from -10 to over 110 degrees
- Ability to operate in a drug-free workplace
- Must possess a High School Diploma or GED. Bachelor’s degree preferred
14
Assistant Plant Manager Resume Examples & Samples
- Understand the key drivers of the business, and seeks to align decision-making, work, and actions
- Understand the value of compliance with an emphasis on Environmental, Health and Safety excellence
- Continue to drive the safety performance of the facility to achieve safety excellence by empowering employees to understand and accept their roles to meet expectations. Improve safety performance through utilization of job hazard analysis, safe work permitting, behavior based safety, root cause analysis, housekeeping and training
- Set high standard for self and others for behavior in the workplace and refuses to allow inappropriate behavior in others – Code of Conduct, Compliance, Guiding Principles
- Drive change through challenging the status quo and focusing on continual improvement
- Leverage the strengths of the management team, and seeks the input of others to improve decisions and results
- Understand the manufacturing process
- Effectively uses Root Cause Analysis to identify system failures and gaps; develop and communicate plans to manage the gaps or risks
- Ensure that economic and critical thinking is applied to arrive at value adding results
- Bachelor's Degree or higher in a Technical or Business field
- A minimum of five (5) years of direct supervisory experience
- Strong leadership and motivational skills, including expectation setting, and coaching, and ensuring accountability
- Intermediate or higher level proficiency with Microsoft Word and Excel, and the ability to learn various computer based operations and production applications
- Processing Capability
- Bachelor’s Degree or higher in Engineering
- Building Products manufacturing experience
15
Assistant Plant Manager Resume Examples & Samples
- Productivity– To leads and manage the facilities and the people to produce the excellent products quality as efficiently as possible while meeting all other Corporate and Business objective. Living in the Model program and accountable in process improvement and reporting; actively use them to measure and improve performance, develop costs and budget. Maintaining the Logistics system or an up-to-date production scheduling to the best advantage to improve productivity in the areas of inventory control, production costs and services. Continuously improved the productivity by knowing the proper Production process and bottlenecks and controlling the shrink/rework
- Physical Facilities– Maintain physical condition and appearance which reflect the standards of quality and service of our business and the character of our people professionally represents the brand image; Preserve and improve our facilities to keep them competitive; Follow specifications that follow the guidelines for general repair and capital projects; Use the preventive maintenance audit system to improve maintenance and operational efficiency; and assure that the productivity increases or cost reductions are realized as planned; Develop and enforce a security program that protects Cargill assets and safeguards the corporation against third party liabilities; Know and effectively manage the equipment and parts that are critical and have spare parts or contingency plans to handle emergencies; Use the audits (Best Practice Audit, Appearance audit and all permits) to effectively identify improvement or opportunity areas
- Administration – The intention is to provide accurate and timely information to those responsible for accounting and to understand on the information reports generated. Understand and manage manufacturing P&L and balance sheet reports and takes immediate action on deviations; Make accurate monthly projections of costs; Complete all routine reports to improve operations on a timely and accurate basis; Develop production budgets and understand how production costs impact; Know what inventory turns are and what the inventory costs are in interest and insurance, and strive to control these costs; Know the basis of energy management, understand the energy reports and use that knowledge to implement energy saving ideas
- Improvement Processes - To develop and coach all employees, and consistently do precisely what we intended to do by conforming to requirements. Uses the audit system to improve all programs striving for 100% compliance; Constantly improve through modification of equipment, techniques and processes; Integrate coaching model, learning model and freedom scale effectively into plant operations
- Product Quality - To manufacture products which conform to the product formula and all other requirements of the product design, i.e., PDI, color, density, etc. Manages receipt of raw material to assure they meet specifications; Knows how operation's physical quality compares in detail to major competitors' quality; Understands and complies with Cargill Animal Nutrition Quality Control Program; Assures the formulas are reviewed before manufacturing for projected quality control and takes necessary steps to assure all formulas will meet Business Unit quality control needs; Participate actively in evaluation and effect of ingredients for their potential to impact on costs and quality
- Environmental, Health and Safety - Sincere concern for the health and safety of all its employees. Management is deeply committed to maintaining an organization environment where these principles are realized. Accidental injuries can be prevented (therefore eliminated) and health exposures can be reduced to extreme minimal levels through employee learning, safe behavior and the application of engineering principles to facilities, equipment and process design; Prevention and elimination of injuries and illness, both on and off the job, is essential from the standpoint of efficiency and economy ; Employees must be educated and trained to perform their jobs safely and to accept responsibility for their own safety performance and safe behavior; Provide the necessary time, tools and resources that foster employee ownership of the safety process; Actively assure that all incidents are investigated in depth and reported on time ; Get personally involved in all areas of safety management at meetings, inspections, investigations, and audits; Understand and comply with the laws that relate to safety in our business, i.e., OSHA, local ordinances; Communicate safety standards on a daily basis; Hold well planned, informative safety meetings with all plant and contract personnel at least monthly; Have an active near miss reporting program and effectively follow up on the corrective actions; Immediately address non-conformance to safety issues; Provide an environment where unsafe acts and conditions are identified and eliminated; Lead the operation with a solid safety culture to achieve zero accidents; comply with local, state and federal environmental laws and regulations and that our facilities are exemplifying good neighbors within the community; Complete annual environmental audit and insure compliance in all areas; Have a training program to insure that all employees are informed of hazardous materials, spill reporting and other pertinent environmental activities
- Housekeeping/Appearance- To assure that plants and offices are consistently representing our brand and meet all Cargill standards. Assure a trained employee performs a formal housekeeping inspection at least monthly. Post the results and take appropriate action; Utilize the audit concept to improve housekeeping to achieve "World Class" standard; Have a training program for housekeeping; Maintain a plant that can win hearts and minds of employees and customers
- Minimum 5+ years in Plant Operations management experience / Production / Maintenance related fields
- Advanced degree in Engineering (Mechanical, Electrical, Industrial Engineering) or Operations / related field or equivalent experience
- Billingual (English with other appropriate for the cluster/country)
16
Assistant Plant Manager Resume Examples & Samples
- 2 plus years manufacturing management experience
- Must have excellent analytical, problem solving and communication skills
- Must have intermediate to advanced MS Office skills
17
Assistant Plant Manager Resume Examples & Samples
- Complies with all safety policies, procedures and established safety practices and ensures that all plant employees do the same
- Conducts safety training, risk assessments, and internal safety inspections to ensure all safety policies are practiced and enforced
- Under the direction of the Plant Manager oversees and directs operations of an aggregates mining crew including personnel, equipment, and securing parts, materials, and supplies
- Supervises and directs crew to ensure proper and effective placement of resources
- Completes daily/weekly/monthly reporting to meet all company, state, and federal guidelines, regulations, and requirements
- Maintains proper job records such as schedules, progress, payroll, equipment, safety inspections, etc
- Maintains strong customer and supplier relationships
- Monitors the changing needs of labor requirements and coordinates requests through the Plant Manager
- Establishes correct field calculations and communicates cost yields and accountabilities
- Collaborates and communicates regularly with Quality Control to ensure specification requirements are met
- Tracks and records fuel usage, hour meter readings, and mileage reporting for equipment
- Under the direction of the Plant Manager the Assistant Plant Manager will carry out supervisory responsibilities in accordance with the company policies, procedures, and applicable laws
- Planning, assigning, and directing work
- Willingness to develop subordinates’ technical and leadership skills and make recommendations for new job opportunities when appropriate
- Effective management of employee performance through coaching, feedback (written and verbal), rewards, and discipline when necessary
- Addressing complaints and resolving problems in a timely manner
- Ability to get work done through others using effective delegation, scheduling, and time management practices
18
Assistant Plant Manager Resume Examples & Samples
- Bachelor’s Degree or equivalent experience
- 5-10 years manufacturing experience
- Glass plant experience desired
- Proven experience managing and leading others to change and improve technical processes
19
Assistant Plant Manager Resume Examples & Samples
- Coordinate cylinder requirements with region branches
- Interviews applicants for hiring and recommends action
- Trains and develops assigned personnel. Responsible for conducting timely and quality performance appraisals of assigned personnel with Plant Manager or independently. Recommends disciplinary action up to and including termination of plant personnel
- Directs and coordinates plant activities to obtain optimum efficiency and economy of operations and maximize production
- Assists in analyses plant budget to identify areas in which efficiencies can be obtained and production costs reduced and then allocates operating budget
- Develops plant goals with agreement of Plant Manager and works with and through subordinate associates to achieve results
- Supervises cylinder re-testing and certification, if process is active at location
- Maintain all required computer and hand generated paperwork as assigned
- Reports any equipment or facility defects to Plant Manager
20
Assistant Plant Manager Resume Examples & Samples
- Responsible for production efficiency, appropriate inventory, labor and cost controls
- Executes production plan to ensure the correct items are being made to meet on time business demand
- Ensure availability of labor, raw materials, and other production inputs to meet the production plan
- Provides leadership to the production team, assessing performance, and directing all operational activities to ensure product quality and consistency
- Ensures completion of monthly HS&E tasks
- Assists Quality department, by maintaining a successful QC program
- Assists Plant Manager in identifying key capital investment projects to meet current and future facility needs
- Involved in daily production processes; 70% of work schedule responsibility solving problems on the production floor and 30% in the office assessing production metrics and planning activities
- Maintains a high level of awareness of surroundings and communicates issues or concerns that could potentially interfere with production or create an unsafe work environment
- Adheres to all established safety procedures and advise supervisor of any potential safety hazards or concerns
21
Assistant Plant Manager Resume Examples & Samples
- Assist the plant manager with daily and strategic management of plant functions and provide leadership in areas to include: financial, safety, environmental, and personnel
- Responsible for driving location expectations and metrics to include: company assets, budgeting, cost control/savings measures, environmental and personnel functions
- Champion the Martin Marietta safety culture. Ensure compliance with all local, federal, state and Martin Marietta policies
- Provide direction to meet plant safety, quality, production and employee development expectations
- Comply with, maintain and update all local State, Federal and Company environmental regulatory programs, policies and guidelines
- A Bachelor’s of Science Degree in Engineering or equivalent work experience required
- 3-5 years quarry management experience
- Minimum 1 year experience with plant and mobile equipment maintenance
- Knowledge of MSHA laws and commitment to safety
22
Assistant Plant Manager Resume Examples & Samples
- Assists in the management of plant operations for efficient and optimal production level, including scheduling of personnel and equipment
- Ensures all plant personnel are continuously trained in order to understand, promote, and follow Vulcan’s Safety, Health, and Environmental standards and meet the zero incident/zero loss goal and works with SHE staff and Company officials to promote a safe work environment that meets all State and Federal rules and regulations
- Provides direction and training to production personnel on efficient processing methods for maximum profit margin, while meeting safety, quality control, and regulatory standards
- Participates in the selection, hiring, training and change of status and separation of employees
- Provides mentoring and coaching to employees. Works with manager and HR to address personnel issues, including implementing steps in the progressive discipline policy. Helps manager with identifying and developing operations and management talents
- Helps schedule and monitor fixed and mobile equipment maintenance programs. Makes sure that plant personnel are properly trained on maintenance standards
- Identifies, assesses, prioritizes, and resolves production quality and employee related problems
- Assists in coordinating activities between Sales and Operations to ensure proper balance between production and inventory levels in order to serve the customers
- Assists in reviewing and monitoring daily and monthly production and financial reports for more cost effective operations
- Assists Plant Management in developing and tracking the operating and capital budgets. Assists in developing justification for unplanned items
- Participates in the development of short and long range business planning
- Leads the daily production meetings and weekly safety meetings
- Is an active participant in community relations and community outreach and educational programs in the plant area
- Minimum of 3-5 years experience in processing and maintenance in the construction materials industry
- Experience in quality control, plant safety, and environmental compliance is required
- Three (3) years of supervisory experience is preferred
- Knowledge in mining and production techniques and equipment, safety and environmental regulations (MSHA and OSHA), equipment application and operation, and material specifications
- Knowledge and understanding of a plant operation (aggregate, asphalt, ready mix, sales yard)
- Knowledge of drilling and blasting
- Knowledge of business and financial principles including accounting and budgeting procedures
- Proficient in Microsoft Office Suite, Google, Oracle Business Environment and other software packages relevant to the position
- Ability to plan and manage effectively. Flexible to handle irregular or long hours
- Must represent Vulcan in a professional manner to all customers, vendors, and internal personnel
- Knowledge of production operations, including the capability and proper utilization of machinery and equipment used in loading, unloading, transporting, crushing, conveying, screening, and stockpiling stone, sand, and gravel as well as asphalt and batch plant operations
- Knowledge of distribution operations, trucking operations and inventory management
- Knowledge and understanding of modern principles and practices of supervising production employees
- Able to understand, interpret, and apply policies and procedures
- Able to motivate and reward employees
23
Assistant Plant Manager Resume Examples & Samples
- Individual supervises activities of hourly production and maintenance employees
- Individual screens and hires hourly production and maintenance employees
- Schedules production requirements to support daily, weekly and monthly sales forecast to meet customer's needs
- Individual provides coaching and disciplinary counseling to employees under his or her area of responsibility (includes employee relations and administration of collective bargaining agreements)
- Ensures that employee receives proper training and instructions to perform job duties
- Schedule and assign employee's work based on production needs (manpower planning)
- Administers and enforces Company and Area policies and procedures
- Ensures that the plant meets all SHE policies and practices at the site location
- Works with SHE Department and Company officials to promote a safe work environment that meets all State and Federal rules and regulations
- Works closely with salespeople and customers to ensure that products meet customer needs and expectations (to include customer visits)
- Participates in Operations short and long range business planning; and
- Attends daily production meetings on the daily running and operations of the plant
- Education, Experience, Licenses, Certifications & Skills Required
- Experience
24
Assistant Plant Manager Resume Examples & Samples
- PRODUCTION LEVELS: ensure that production levels are at an optimum with a minimum of downtime. Coordinate by-size production with sales market demands and long range planning. Work closely with the quality control technician and the sales department to ensure that all production meets the customer’s needs
- MAINTENANCE PROGRAM: proper utilization and maintenance of all stationary and mobile support equipment so that equipment cost and downtime is minimized and the equipment is available when needed
- SAFETY, HEALTH, AND ENVIRONMENT: be proactive in the safety of all personnel and activities in the plant area. Inspect and maintain dust control systems to ensure a healthy work environment. Be knowledgeable of waste products, their impact on the environment and their proper disposal. Ensure that all safety procedures and company guidelines are adhered to
- SUPERVISION: provide an example of good leadership. Keep open effective lines of communication with staff and operation level personnel
- INVENTORY CONTROL: maintain proper levels of inventories to support local sales activities and long range market demands
- QUALITY CONTROL: Ensure that Vulcan remains the market leader in quality of product and service to the customer. Work closely with the onsite Quality Control Technician and the Division’s Technical Services staff to ensure consistency
- COMMUNITY RELATIONS: Ensure that Vulcan remains proactive and transparent with community partner. Continue to assist with utilizing our resources as opportunities to enhance classroom curriculum
- Minimum of 3-5 years experience in processing and maintenance. One (1) year of supervisory experience is preferred. Construction materials industry experience preferred
25
Assistant Plant Manager Resume Examples & Samples
- Operate and safely maintain production at dry ice manufacturing plant
- Manage and provide leadership to plant production personnel
- Audit routinely to make sure all Airgas policies are being followed
- Assign job tasks to plant operators according to customer needs
- Analyze production schedules to run efficiently as possible
- Ensure quality of products is maintained at a high level and in accordance to company policy and regulations
- Adjust resources to meet production schedules through capacity planning and machine utilization
- Implement measures to improve production methods
- Ensure all injuries and accidents are properly investigated and reported immediately
- Train new workers and cross train employees
- Five (5) years experience in a supervisory role of more than 10 production personnel in an industrial environment
- 2 years experience with hydraulic maintenance
- Self starter with strong leadership and team building skills
- Authoritative presence to discipline associates in a fair and professional manner
- Strong written and verbal skills and the ability to complete detailed reports and make presentations
- Understanding of financial reports
- High level math skills to create formulas and spreadsheets for budgets, cost control, and inventory
- Proficient with computer systems and software packages such as Microsoft Word, Excel, PowerPoint, and e-mail
26
Assistant Plant Manager Resume Examples & Samples
- 5 years experience operating and maintaining double-acting, dual-service reciprocating compressor (with CO2 and NH3)
- 5 years experience in operating and maintaining an NH3 refrigeration system
- Proficiency in proprietary CU and CMS systems
- Experience in hydraulics and pneumatics equipment and systems
- Willingness to work any shift as required
27
Assistant Plant Manager Resume Examples & Samples
- High School Diploma/GED required, Bachelor Degree preferred
- 3+ years experience in an industrial plant environment required
- 2+ years managing and developing employees required
- Experience working and/or managing in a union environment preferred
28
Assistant Plant Manager Resume Examples & Samples
- 25% -Provide support for the entire area of the facility through consistent guidance and direction, ensuring awareness of company policies and procedures while demonstrating an effective means to achieve them. Provide leadership and coaching to the operations managers and effectively collaborate with all others functional managers to help achieve our plant goals
- 10% -Assist in establishing product quality standards and following up with supervisors to ensure any corrections to processes that are made result in improved quality. Ensure quick resolution of any quality complaints in conjunction with monitoring compliance to Sanitation and Hygiene policies and legislated requirements
- 20% -Optimize overall plant performance. Using KPI’s identify trends and data to identify areas for improvement and deliver on the Plant to Win savings commitments
- 15% -Investigate employee or labour relations matters to bring them to a close. Work with operations managers and supervisor to resolve grievances
- 10% -Review and follow up on all accident or incident reports, maintaining compliance with the Occupational Health and Safety Act and company Health and Safety policies. Act as a champion for safety within the facility through observations and behaviours. Promote safety every day, and ensure stakeholders are working safely
- 10% - Ensure compliance with the department budget and document and review departmental issues, explaining production variances and identifying opportunities to improve. Other various projects and responsibilities
- 10% -Ensure efficient deployment of CAPEX and successful implementation of project goals
- Bachelor's Degree in Agricultural Sciences, Business, Engineering or other relevant fields
- Minimum 5 years of progressive food industry experience
- Minimum 2 years of experience in a management position
- Strong problem solving and decision making skills
- Ability to drive team work and collaboration
- Demonstrated leadership amongst a team
- General understanding of HACCP and GMP’s
- Ability to work in a cold, damp environment
- Ability to work around animals, dust, dander, feathers and chemicals
- Ability to work flexible work hours to provide occasional leadership on all three shifts; may require some weekends
29
Assistant Plant Manager Resume Examples & Samples
- Manage and lead 15 or more plant technicians
- Conduct periodic checks of plant for safe and efficient operation
- Helps manage open order book and production schedule to achieve goals set by ASG management
- Insure compliance to all applicable quality standards (ISO, 17025 and 9001)
- Provide input as it relates to employee performance
- Approve overtime when essential, while keeping overtime at acceptable levels
- Issue disciplinary action if required
- Trains new workers and cross trains employees to continue production during personnel shortages
- Supports efforts to meet facility on time, safety, quality and financial goals
- Bachelor Degree in Engineering, Chemistry, Industrial Technology, or related field, or equivalent experience in gases and welding supply industry
- Basic knowledge of analytical instrumentation such as gas chromatography, nondispersive infrared and component-specific analyzers for analysis of gaseous samples
- Basic understanding of physical properties of various gases and chemicals and general knowledge of laws of Partial Pressure
- Must be Hazmat Certified
- Regularly required to use hands and fingers to handle, feel or operate objects, tools or controls, and reach with hands and arms
- Must be able to talk to and hear customers/co-workers as well as smell/hear leaking gas from cylinders
- The noise level in the work environment is usually moderate and the work environment is an office and industrial production setting
30
Assistant Plant Manager Resume Examples & Samples
- High school diploma / equivalent
- Must have related work experience, at least 1 year is preferred
- Ability to read / write and comprehend simple instructions, short correspondence and memos
- Ability to perform basic math functions
- Strong interpersonal and organizations skills
31
Assistant Plant Manager Resume Examples & Samples
- Responsible for the daily operations of the plant with a primary emphasis on Safety, Health and Environmental compliance
- Financial and production performance
- Training and development of employees
- BS in Wood Science, Industrial Engineering or Business or equivalent work experience
- At least 5 years of supervisory experience in a manufacturing environment required; 5 years of supervisory experience in a wood treating facility preferred
- SH&E awareness
- Strong leadership, organizational and communication skills
- Prior experience in a union environment preferred
- Must be a team player with the ability to set priorities, analyze problems, work independently and manage time effectively
- Proficiency with Microsoft Word, Outlook and Excel
32
Assistant Plant Manager Resume Examples & Samples
- Develop plant short and long-range strategic operating objectives. Oversee plant operations including production, warehouse, shipping and receiving, maintenance and office management; ensures compliance with federal and state regulations; monitors and enforces quality control standards; executes production schedules; develops and/or approves all plant operating policies
- Direct, manage, and develop Plant Leadership to ensure the safe and efficient operation of the plant
- Establish, communicate, and implement safety, associate engagement, and operations excellence initiatives
- Establish and monitor plant operating budget; prepares and analyzes profit and loss statements; identifies and implements improvements to positively affect profitability
- Communicate with other plant managers to share ideas and resources. Works under the direction of the Director of Liquid Operations and alongside salespeople and corporate support personnel to ensure the success of the plant and associates
33
Assistant Plant Manager Resume Examples & Samples
- Supervises the activities of all plant, quality assurance lab, and drivers
- Coordinates and partners with other Plant Supervisors to ensure smooth day-to-day operations
- Promotes a strong safety and compliance culture correcting unsafe acts or conditions without delay
- Assigns task to workers according to customers’ needs, current stock levels, and worker’s expertise
- Studies production schedules and estimates worker-hour requirements for completion of job assignments. Maintains time and production records
- Interprets company policies to workers and enforces safety regulations
- Implements measures to improve production methods, equipment performance, quality of product, and changes working conditions and use of equipment to increase efficiency of work crew. Initiates or suggests plans to motivate workers to achieve work goals
- Analyzes and resolves work problems or assists workers in solving work problems
- Recommends or initiates associate actions, such as new hires, promotions, transfers, discharges, performance improvement and disciplinary measures
- Provides assistance to the Plant Manager with regard to planning and managing capital investments
- Coordinates the proper inventory levels of supplies and equipment
- Bachelor’s degree in a Science, Business or related degree field required. In lieu of degree, consideration for up to 4 years of additional related experience may be accepted
- A minimum of 2 years of demonstrated experience working in a leadership role within a manufacturing or distribution environment. Prefer prior technical experience with compressed gases, gas analysis and gas lab equipment
- Prior experience utilizing SAP preferred
- Intermediate knowledge of Microsoft Office applications (Word, Excel, and Outlook)
- Strong analytical skills and a thorough understanding of how to leverage metrics and related tools to improve production efficiency and effectiveness
- Excellent oral and written communication skills. Communication skills that ensure a smooth flow of information between self and others through clear speaking and writing, encouragement of open expression of ideas, and effective listening
- Demonstrated knowledge of addition, subtraction, multiplication, and division in all units of measure using whole numbers, fractions and decimals. Ability to compute rate, ratios, and percent
- Self-starter; self-motivated; well organized; ability to work independently and as part of a team
- Occasionally required to walk; use hands to finger, handle, feel or use a calculator or computer; and reach with hands and arms
- Regularly lift and/or move up to 60 pounds and move up to 125 pounds with the aid of material handling equipment
34
Assistant Plant Manager Resume Examples & Samples
- Bachelor’s degree (B.A.) from four-year college or university in Agriculture, Animal Science, Business or related field and 8+ years’ experience in plant management
- Manufacturing knowledge and understanding of yields, plant efficiencies, and operations procedures
- Knowledge of different pork products and the Meat Industry, preferred
- Bi-Lingual, preferred
35
Assistant Plant Manager Resume Examples & Samples
- Supervises four associates involved in activities related to the plant, quality assurance lab, and/or drivers
- Employee may occasionally be required to transverse through office and/or manufacturing locations
- Employee will frequently be required to actively listen and exchange information
- Employee will be required to observe and assess information received via computer
- Requires frequent use of computer and telephone
- Occasionally be able to move up to 60 pounds and move more than 125 pounds with the aid of material handling equipment
36
Assistant Plant Manager Resume Examples & Samples
- Bachelor's of Science degree in a technical field
- Minimum of three (3) years of manufacturing experience
- Minimum of two (2) years previous leadership experience with a focus on team building with a diverse team
- Experience using Microsoft Office software such as Word, Excel, Outlook, and Project
- Minimum of two years’ experience working with OSHA, EPA, and State Regulations
- Bachelor degree or higher in Chemical or Mechanical Engineering
- Five (5) or more years of experience in leadership
- Seven (7) or more years of experience managing in an industrial/chemical/refinery manufacturing setting
- Experience in a Process Safety Management covered facility
- Supervisory experience in chemical or refinery
- Batch and continuous chemical processing knowledge
- Experience working in a union environment
37
Assistant Plant Manager Resume Examples & Samples
- Confers with supervisors of other departments and/or branches to coordinate flow of materials or products
- Verifies and/or prepares records such as routing slips, material requisitions, and job orders
- Studies delivery schedules and estimates worker hour requirements for completion of job assignment
- Interprets company policies to distribution personnel and enforces safety regulations
- Interprets job orders to distribution personnel and assigns duties
- Recommends measures to improve production methods, equipment performance, and quality of product
- Suggests changes in working conditions and use of equipment to increase efficiency of plant distribution
- Analyzes and resolves work problems, or assists distribution personnel in solving work problems
- Initiates or suggests plans to motivate distribution personnel to achieve work goals
- Provide the necessary training and equipment to all employees to safely, properly and efficiently perform their jobs
- Manage the safety and health of their employees by complying with all internal policies and procedures and applicable government regulations
- Promote a collective and positive safety attitude by providing leadership by example
- Assists with directing and coordinating plant activities to obtain optimum efficiency and economy of operations and maximize production
- Assists in directing plant policies and procedures
- Assists in the development of plant goals and may work through subordinate employees to achieve same
- Directly supervises employees and subordinate supervisors in assigned production facility
- Responsibilities include interviewing and training employees; planning, assigning, and directing work; appraising performance; rewarding and disciplining employees; addressing complaints and resolving problems
- Associate's degree (A.A.or A.S.) or equivalent from two-year college or technical school; or minimum of three years related experience and/or training; or equivalent combination of education and experience
38
Assistant Plant Manager Resume Examples & Samples
- Works with staff, trades personnel, managements and operational staff on necessary plant and mobile equipment repairs
- Follows all company policies and safety procedures
- Coordinates with Plant Maintenance & Mobile Maintenance Managers necessary day to day repairs of equipment
- Assists in managing critical spares and minimizes inventory cost
- Ensures plant and mobile equipment is kept in good and safe working condition to maximize asset throughput
- Helps schedule preventive/predictive maintenance on the plant equipment to optimize performance
- Works with CCM Group and local site supervision to manage the successful completion of Capital Projects and other “in house” projects
- Attends weekly tailgate safety and department meetings
- Audits production, maintenance processes and promotes best practices
- Works with plant managers to develop yearly budgets
- Develops budgets and repair/replacement cost
- Works closely with plant manager to determine optimal times for repairs on production equipment
- Works with the Plant Maintenance Manager to create a detailed Maintenance plan quarterly with monthly updates
- Manages up to 6 direct reports
- Manages all related production/shipping processes
- Oversee multiple departments totaling 50+ hourly employees
39
Kemps Assistant Plant Manager Resume Examples & Samples
- Leads and coordinates the activities of production/cooler supervisors, dispatchers/expediters, and other plant employees engaged in the production or load out of dairy products to ensure safety, quality, and customer standards are met. Responsible for overall plant operations in Plant Manager's absence
- Ensures that production/cooler supervisors work effectively with unionized employees to promote positive and productive working relationships. Assists supervisors in effectively applying work rules, union contract provisions, and employment policies. Ensures that discipline is administered consistently and fairly. Coaches others in conflict resolution to avoid grievances. Works with Human Resources and Plant Manager to resolve employee grievances when filed
- Initiates personnel actions such as promotions, transfers, discharges, and disciplinary measures. Reviews actions brought forth by production/cooler supervisors. Evaluates union employees on successful completion of probationary periods
- Coaches and partners with non-union direct reports to effectively manage performance. Communicates company and cascading goals and assists performers in establishing goals that align with department and company goals. Provides on-going performance feedback and conducts performance conversations per Kemps' Performance Management process. Holds direct reports accountable for results and works with them to cultivate capabilities and utilize strengths
- Oversees and coordinates the development and maintenance of work practices and standard operating procedures. Accountable for plant compliance with same. Personally develops complex or non-routine procedures for work process changes, new products, and new equipment
- Understands and fulfills the requirements of SQF 2000 Level 3 code of regulation for food safety and quality. Manages policies, procedures and programs related to operations. Fosters continuous improvement to maintain the SQF 2000 Level 3 certification
- Actively promotes safe work behaviors and holds self and direct reports accountable for following safety rules and regulations. Conducts accident/injury investigations and sends reports of injury to HR in a timely manner to meet rapid reporting standards. May coordinate and/or facilitate plant safety meetings, training, and incentive programs
- May be responsible for monitoring the intake procedures of raw dairy products, ensuring high quality standards are met and product shortages are avoided. May be responsible for ordering dairy products
- May be responsible for supervising clean-up operations to obtain optimum production and utilization of manpower, machines, and equipment. May coordinate production activities with procurement, maintenance, and quality assurance
- May be responsible for the identification of damaged and erroneously delivered orders. May work with supervisors and cooler employees to correct shortages or discrepancies in product stock levels
- Performs other responsibilities as determined by business needs
40
Assistant Plant Manager Resume Examples & Samples
- Supervises the activities of the plant personnel to accomplish job duties
- Assigns task to workers according to customers’ needs, current stock levels and worker’s expertise
- A minimum of 2 years of demonstrated experience working in a leadership role within a distribution environment
- Prefer prior technical experience with medical and food grade compressed gases, gas analysis and gas lab equipment
- Self-starter; self-motivated; operates with a sense of urgency; ability to work independently and under pressure to meet deadlines
- Occasionally lift and/or move up to 60 pounds and move more than 125 pounds with the aid of material handling equipment
- Work environment may contain loud noises
41
Assistant Plant Manager Resume Examples & Samples
- Manage the work of all production employees – oversees production and shipping schedules based on availability of raw and finished goods
- Provide hands-on leadership as a working manager, responsible for mentoring and coaching all employees and managing employee relations issues
- Support plant administration to ensure compliance to established policies
- Directly responsible for all employment decisions at the facility
- Responsible in consult with Plant Manager for the cost and yield performance of the Plant in partnership with the overall P&L of the Plant
- Support and implement cost control initiatives and process control within the Plant
- Continually review operations activities, including local transportation activities to maintain compliance with all Federal, State and local laws (OSHA, DOL, DOJ, EPA, FD)
- Drive Safety improvements (Zero Harm) across the Plant
- Ensure the consistent execution of all SOPs throughout the Plant and in accordance with the PMS Commercial Organization, Global Supply Chain
- Deliver best operational practices and cost efficiencies across the Plant while maintaining critical quality and raw material utilization standards that are necessary to maintain customer satisfaction and Plant profitability
- Ensure compliance through teamwork for all Standard Operating Procedures within the Plant
- Implement and manage Lean opportunities to effectively eliminate waste
- In partnership with Plant Manager, provide leadership to Plant staff to effectively recruit, train, develop, evaluate, motivate, delegate and monitor their activities
- Drive efficiencies in asset utilization through proper transportation scheduling, dispatch, & driver management while meeting customer expectations
- Bachelors in Operations/Supply Chain or related field like Operations/Manufacturing; also will consider 8-10 years of related experience
- Six Sigma/Lean certification preferred
- 3+ years in a plant supervisory role in an engineering or manufacturing environment
- Familiarity with private fleet management/transportation is helpful
- Strong customer focus orientation
- Expert people management capability including non-exempt production workforce
- Demonstrated success in delivering strong employee relations
- Demonstrated ability to work cross-functionally
- Experience managing safety performance and programs
- Understanding of supply chain practices and metrics
- Superior ability to manage people and motivate a team
- Excellent problem-solving skills and strategic thinking ability
42
Assistant Plant Manager Resume Examples & Samples
- Continuous improvement through meeting the safety targets of recordable incident rate and severity
- Continuous improvement towards meeting the quality goals through the coordination of AQP, Six Sigma and other programs
- Coordinate the Implementation of Best Practices and Poke Yokes throughout all the plant and keep Plant progress up to date in Divisional Data Base
- Daily coordination of production activities to support customer delivery and RIP targets
- Improvement in equipment uptime through the coordination of Preventive Maintenance and MTBF / MTTR programs
- Development of Subordinates through Organizational Review, Color Me Charts and Quarterly Performance Reviews
- Preparation of Capital Acquisition Requests and Implementation of Capital projects as stated in Financial Review
- Implementation of Scrap reduction programs to meet plant target
- Headcount control to meet production requirements and productivity targets
- Weekly report of Highlights to Plant Manager
- Attend monthly skip level meeting with production, engineering and maintenance to communicate department status and actions to meet objectives
- Identification and Implementation of Cost Reduction programs to meet Financial Review Targets
- Presentations to Staff and Divisional Management teams as per schedule. · Coordinate Improvement to production floor and all areas under his/her responsibility through effective 5S programs
43
Assistant Plant Manager Bacon Complex Resume Examples & Samples
- Directs production and ensures cost effectiveness and consistency with prescribed quality, accuracy and performance standards
- Manages approximately 20 subordinate salaried exempt partners in a plant of approximately 300 hourly workers
- Prepares and submits operating reports to management, makes recommendations to improve efficiency and effectiveness
- Provides managerial oversight on job assignments, scheduling and supervision
- Assures effective customer service and relations through timely delivery of quality product
- Selects, trains, develops and motivates manufacturing staff to maintain plant operation
- Assures compliance of all plant operation with company policy and Federal, state, and local regulations
- Has the authority to make decisions and must be capable of working with or without direct supervision
- Assist in establishing production and processing goals for plant
- Confers with Plant Manager, Safety Manager, QA Manager, Shift Superintendents and Production Supervisors to analyze production schedules to plan and project cost effective production processes
- Assures strict enforcement all safety, OSHA, FSIS, USDA, and HCAPP regulations
- In case of absence responsibilities would be filled by Superintendent, Scheduler, and product manager
- Must work in a respectful and cooperative manner with other workers, managers and supervisors
- Must possess the ability to apply commonsense understanding to guidelines furnished in written, oral, or diagram form
- Must understand the budgeting process and work closely with accounting to operate a cost effective plant
- Typically requires minimum of 1 year of directly related experience in a further processing/ slicing plant to successfully perform the duties of this jobs, experience in further processed and prepared foods is preferred
- Must understand HCAPP, USDA, OSHA/SAFETY regulations, and other federal and state requirements for a poultry processing environment
44
Assistant Plant Manager Resume Examples & Samples
- 20% Maintain physical condition and appearance that reflect the standards of quality and service of our business. Ensure that the character of our people professionally represents the brand image
- 10%Maintain a system that sets standards on each delivery
- 10% Utilize a tool (activity schedule) to help manage and execute the numerous requirements for which you are accountable
- Coordinating the logistics for the shipping and receiving of 7,000 tons of animal feed monthly
- Lead a group of highly engaged employees in this environment to return safely every day to their loved ones
- Oversee entire production of that shift from receiving to loadout
- Truck load order review
- Minimum 5 years supervisory/management experience in a fast paced production/industrial environment
- Ability to adjust working hours as needed by the business
- Ability to create an environment conducive to teamwork; strong interpersonal skills
- Customer Solutions Approach. Holds self and others accountable
- Strong listening skills; written and verbal communication skills
- Adaptable, nimble
- Demonstrated success in EHS
- Strong computer skills: Microsoft Office, Warehouse/Distribution Management Software, or SAP preferred
- Strong mechanical aptitude in automated packaging equipment
45
Assistant Plant Manager Resume Examples & Samples
- 5+ years of supervisory experience
- Industrial gas, industry production or equivalent manufacturing experience preferred
- Strong organization and project management skills
- Functions independently and make logical, sound decisions in a wide variety of situations
- Communicates effectively with customers, employees, and management
- Possess strong written and verbal skills
- Computer savvy and proficient in MS Office
- Regulatory agency knowledge including, but not limited to: DOT, OSHA, and EPA
- Positive and professional attitude
46
Assistant Plant Manager Resume Examples & Samples
- Negotiating cost with raw material suppliers and scheduling raw materials delivery to meet business and production build schedules
- Responsible for inventory management, labor and cost controls
- 2 or 4 year degree, and/or equivalent combination(s) of education, industry experience and training
47
Assistant Plant Manager Resume Examples & Samples
- Coordinate production activities for respective area insuring that obstacles are identified and resolved
- Assist with minimizing labor overtime, maintaining production schedules and quality standards
- Recognize and help solve problems affecting production, quality, safety and productivity
- Apply the tools of Lean Manufacturing that include, but not limited to: 5’s, Value Stream Mapping, Poke Yoke, VA/VE
- Apply the tools of Industrial Engineering that include, but limited to: Work Element Measurement, Process Flow
- Minimize attrition through effective coaching practices and effective employee relations
- Foster a culture of empowerment so that all levels of employees are engaged in continuous improvement activities
- Help implement and maintain preventative maintenance programs. Make recommendations to Plant Manager for facilities and equipment when necessary
- Incorporate shop floor organization and plant cleanliness among plant personnel
- Provide effective communication to support the needs of the employees as well as the goals of the organization
- Actively engage in all Safety initiatives to meet or exceed EH&S goals and plans
- Minimum 5 years in manufacturing experience, with operational knowledge of processes, equipment and facilities
- Training in Lean Manufacturing, TPS, and Demand Flow
- Background with manufacturing methods, process improvement programs and procedures required
- Exceptional communication and proven leadership skills
- Competent in Microsoft Office including Word, Excel and Outlook
- Manufacturing: 5 years
- Assistant Plant Manager: 1 year
- Are you in Greenville, TN ?
- How many years of manufacturing experience do you have?
- How many years of Assistant Plant Manager experience do you have?