Maintenance & Reliability Manager Resume Samples
4.6
(135 votes) for
Maintenance & Reliability Manager Resume Samples
The Guide To Resume Tailoring
Guide the recruiter to the conclusion that you are the best candidate for the maintenance & reliability manager job. It’s actually very simple. Tailor your resume by picking relevant responsibilities from the examples below and then add your accomplishments. This way, you can position yourself in the best way to get hired.
Craft your perfect resume by picking job responsibilities written by professional recruiters
Pick from the thousands of curated job responsibilities used by the leading companies
Tailor your resume & cover letter with wording that best fits for each job you apply
Resume Builder
Create a Resume in Minutes with Professional Resume Templates
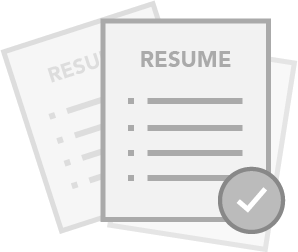
CHOOSE THE BEST TEMPLATE
- Choose from 15 Leading Templates. No need to think about design details.
USE PRE-WRITTEN BULLET POINTS
- Select from thousands of pre-written bullet points.
SAVE YOUR DOCUMENTS IN PDF FILES
- Instantly download in PDF format or share a custom link.
AH
A Harris
Alexander
Harris
77003 Lupe Pines
Chicago
IL
+1 (555) 150 9243
77003 Lupe Pines
Chicago
IL
Phone
p
+1 (555) 150 9243
Experience
Experience
Houston, TX
Maintenance Reliability Manager
Houston, TX
Beier and Sons
Houston, TX
Maintenance Reliability Manager
- Work order and asset management, refining PM schedules, technician cross-training
- Manages oil sampling & lubrication program for critical wash down & rotating equipment
- Collaborates with engineering group in developing Predictive & Preventive Maintenance programs & new equipment specifications and validations
- Initiated and leads maintenance department training program. Created SOPs, PM Tasks, PPT
- Administrates and refines Computerized Maintenance Management Software (DPSI / iMaint) through continuous improvement efforts and action items
- Responsible for maintaining inventory and management of MRO supplies including 2 direct reports that operate the plant stockroom. Also responsible for SOE costs for operational repairs and building support
- Drives continuous improvements within the Maintenance Department
Philadelphia, PA
Maintenance & Reliability Manager
Philadelphia, PA
McKenzie Group
Philadelphia, PA
Maintenance & Reliability Manager
- Initiate, implement, and manage the plant maintenance programs based on best practices in the chemical industry, with an emphasis on equipment condition inspections, planning/scheduling, high quality maintenance repairs, and safety, health & environmental policies and procedures
- Analyze operational data and equipment performance history to deliver improvements in critical maintenance related metrics including: unplanned downtime, PM compliance, schedule compliance, Mean-Time-Between-Failures, and maintenance related costs
- Coordinate with cross-functional departments (Engineering, R&D, Supply Chain, etc) to ensure operational effectiveness in new plants and expansions, and life cycle cost considerations in global equipment procurement activities
- Partner with worldwide operations group to coordinate maintenance activities in support of operational excellence
- Coordinate planned maintenance and connectivity with Maintenance Managers in plant positions. Regularly respond with advice to maintenance/equipment related questions, ensure access to up-to-date maintenance/operating procedures, and facilitate strong team communications activities
- Establish maintain, and leverage value from a computerized maintenance management system (CMMS) for tracking work orders, planned/predictive maintenance, spare parts inventory/sharing, MRO management, and maintenance history of plant equipment on a global basis
- Position can be based in Boston or at any of the Purification Solutions manufacturing sites globally (Marshall, TX; Pryor, OK; Zaandam, the Netherlands; Klazienaveen, the Netherlands; Glasgow, UK; Purton, UK; or Ravenna, Italy)
present
Philadelphia, PA
Maintenance & Reliability Manager
Philadelphia, PA
Turcotte-Sauer
present
Philadelphia, PA
Maintenance & Reliability Manager
present
- Process quality; Ensuring all work is performed according to the quality management systems and meets the specifications and standards
- Tenacity and energy in leading change toward a high performing work environment
- 5% Any other duties as assigned
- Develop and manage a work order system and preventative and predictive maintenance plan
- Monitor and analyze the performance of the equipment and improve the efficiency
- Ensure the quality of the spare parts and/or services purchased. Manage suppliers’/contractors’ performance and periodically carry out vendor assessment. Ensure that contractors comply with Cabot safety and all other site procedures
- Actively participate in maintenance and capital budget preparation and cost expenditure forecasts
Education
Education
Bachelor’s Degree in Engineering
Bachelor’s Degree in Engineering
Iowa State University
Bachelor’s Degree in Engineering
Skills
Skills
- Good computer skills with working knowledge of Google Apps, MS Word, MS Excel, MS Powerpoint and MS Project. General understanding of databases is desirable
- Process quality; Ensuring all work is performed according to the quality management systems and meets the specifications and standards
- Work with all site functions to ensure process and equipment reliability, availability and operational effectiveness
- 25% Maintenance & Reliability
- Working knowledge of common maintenance systems to include Meridium, SAP PM, Oracle eAM, IBM Maximo, Ivara, and NRX
- 6 - 8+ years of industry or consulting experience as a Reliability and Maintenance practitioner (including Oil and Gas Upstream)
- Ability to work as a team member or independently at client sites
- Strong interpersonal skills
- Excellent communication skills, both written and verbal
- Demonstrated ability to work creatively and analytically in a problem-solving environment
15 Maintenance & Reliability Manager resume templates
Read our complete resume writing guides
1
Maintenance & Reliability Manager Resume Examples & Samples
- Leadership; providing leadership, knowledge, operations and maintenance experience to ensure the team deliver the maintenance services required by the plant to meet and short and long-term objectives. Motivating and coaching the team through regular feedback and effective performance management
- Food Safety, Environment and Health and Safety; ensuring all H&S procedures are championed and adhered to across maintenance and plant operations. This will involve employee training and meetings, workplace inspections, work permit sign off, conducting investigations and on-going evaluation of policies to ensure they are continuously improved
- Maintenance & Reliability; Using your technical skills and significant operations experience to manage process and equipment reliability, availability and operational effectiveness via predictive, planned and preventative maintenance techniques. You will continually look to improve reliability through effective work processes and operating efficiencies. You will also work with our team of European wide ‘best practice’ leads to embed processes and systems in to the plant
- Financial Control; full responsibility for the maintenance budget ensuring the effective management of costs through tracking expenditure and making adjustments as required
- Plant operations; Working with colleagues across the plant to ensure compliance with all on site policies and procedures e.g. H&S, housekeeping, HACCP etc. Oversee stores and parts inventory to ensure the team meets operational requirements and where possible make improvements to work processes and operating efficiencies. You will also be involved in plant projects to support the overall plant operations
- Process quality; Ensuring all work is performed according to the quality management systems and meets the specifications and standards
- Previous operations and maintenance experience gained within a heavy industrial environment (e.g. Petro chem, chemicals, coal, steel, heavy pharmaceuticals, oil and gas, refinery)
- Experience of working in a 24/7, 365 day per year continuous processing environment is a distinct advantage
- Excellent leadership experience, able to coach and develop a team of high-performing individuals
- Relevant degree/MSc (or equivalent qualification) e.g. Reliability & Maintenance, Chemical Engineering or qualified by extensive experience
- Strong communication skills, able to work cohesively within a matrix environment
- Working knowledge of continuous improvement methods e.g. Kaizen, 5S with the drive and determination to make significant changes to how we manage our Maintenance and Reliability function
2
Maintenance & Reliability Manager Resume Examples & Samples
- Organize, plan, lead, control and coordinate maintenance activities
- Support local alignment, deployment and execution of Business Unit reliability excellence vision, strategy and processes to change reliability culture
- Ensure optimum utilisation and development of the facility Asset Management System
- Ensure compliance with local/country/European regulations and all business unit/facility policies and procedures as related to safety, environment, HACCP, ISO 9002, GMO
- Ensure effective processes are in place for shutdown planning and procedures
- Review existing organisation, work methods to identify gaps and ensure alignment with Maintenance and Reliability Centre of Excellence practices
- Coach and counsel employees
- Improve work processes and operating efficiencies
- Master degree in mechanical, chemical or electrical engineering
- 5+ years’ experience in maintenance or operation at medium to large plant operations
- Demonstrated experience in leading M&R function in a complex facility
- Experience within a manufacturing/engineering environment; chemical/starchy industry is a plus
- Excellent verbal and written communication skills in English and German
- Personal drive and commitment for M&R processes and strategies
- Promoter of innovation, adaptable and focused on process improvements
3
Maintenance & Reliability Manager Resume Examples & Samples
- 30% Leadership: As a member of the plant leadership team, this position is responsible for providing strategic direction, leadership, and vision, ensuring the proper execution of the RE process throughout the location.. Specific leadership functions are as follows
- Create a high performing, efficient and engaged maintenance and operations team
- Develop and coach team members to improve efficiency to deliver results and achieve high performance
- Assure the Maintenance Staff are properly trained, exhibiting the knowledge and skills to effectively perform their tasks in compliance with Cargill Reliability Excellence model
- Continue to build and expand capabilities across the site in all work steams
- Support governance of CCE, and P&M streams
- Manage sustainment scorecard and sustainment audit process to utilize and understand culture gaps and focus areas
- Maintain, improve utility operation including waster water, chillers, heating system, air compressors, etc
- 25% Maintenance & Reliability
- Work with all site functions to ensure process and equipment reliability, availability and operational effectiveness
- Utilize technical skills and established RE “Process and Metrics” tools and activities while partnering with production and other plant functions to ensure plant reliability
- Oversight of all MRO and OEM procurement, purchasing and rentals. Lead and foster the RE Reliability Engineering function in an effort to early detect and eliminate defects as well as eliminate “bad actor” assets and repeat offenders
- Lead and manage all basic “maintenance management” plant functions
- 25% Financial
- Effectively manages expenses through effective cost optimization methods in accordance with RE
- Work with plant leadership team with developing and managing the maintenance budget. Contributes to and monitors annual plan for facility as well as balanced scorecard and standards and goals
- Tracks maintenance expenditures, makes adjustments as needed, and communicates progress to others
- Ensure “Total Cost of Ownership” is considered
- 10% Food Safety, Environmental, Health and Safety: Executes and champions Cargill environment, health and safety procedures in the maintenance department and plant operations
- 5% Capital Projects: Actively contributes to capital planning process (project identification & scheduling) and prepares capital commitments as needed
- 5% Other Duties: Develop and manage work plans, status reports, value tracking and miscellaneous job-related duties as assigned. Manage risk, issues and remove barriers to ensure completion of milestones on task and budget
- Minimum 5 years of proven experience leading and managing diverse teams within plant operations
- Managing complex projects in a cross-cultural environment
- Experience leading ‘rapid’ change management initiatives
- Experence creating and executing plans to drive organizational results
- Strong analytical capabilities
- Effective training and development skills
- Strong competencies in the areas of leadership, communication, teamwork, interpersonal effectiveness, initiative and process discipline
4
Maintenance Reliability Manager Resume Examples & Samples
- Build up and maintain clear communication and close co-operation with all relevant internal (plant staff, R&D and corporate engineering) and external (i.e. suppliers, local authorities) interfaces
- Utilize root cause analysis and conditional assessment to implement long term solutions to resolve issues
- Manage the Reliability Supervisors who in combination with the Reliability Manager will oversee maintenance, and alteration of equipment, machinery and building structures
- Review and implement procedures and preventive maintenance job plans to ensure effective use of manpower, maximize equipment uptime and life, and reduce operational and facility expenses
- Responsible for maintaining inventory and management of MRO supplies including 2 direct reports that operate the plant stockroom. Also responsible for SOE costs for operational repairs and building support
- Ensure that new equipment and facility functions operate as planned to avoid downtime and ensure products are available per Customer demand such that they meet or exceed safety, quality, productivity, and cost objectives
- Responsible for facility compliance to insurance requirements, building codes, and local municipality regulations
- Responsible for the safety programs that are related to reliability functions such as lockout/tag out, confined space operations, hot work programs, etc
- Bachelor’s degree in engineering or equivalent experience
- 3 + years of experience in a Lean Manufacturing Environment OR 5+ years engineering or manufacturing experience in a manufacturing environment
- 3+ years of experience with automated process and packaging systems
- Immigration Sponsorship not available for this role
- 3 years of experience designing or maintaining building, process, and packaging equipment
- 3 years of experience utilizing Root Cause Analysis processes
- 3 years of Total Productive Maintenance (TPM) experience
- 3 years of experience improving Process Reliability (PR %) and / or Overall Equipment Effectiveness (OEE %)
5
Maintenance & Reliability Manager Resume Examples & Samples
- Develop and maintain a program for site improvements, introduction of new technology, and manage the execution of a capital expenditure and maintenance plan to ensure work is completed to a high standard in accordance with customer and project objectives
- Develop and manage a work order system and preventative and predictive maintenance plan
- Monitor and analyze the performance of the equipment and improve the efficiency
- Ensure the quality of the spare parts and/or services purchased. Manage suppliers’/contractors’ performance and periodically carry out vendor assessment. Ensure that contractors comply with Cabot safety and all other site procedures
- Actively participate in maintenance and capital budget preparation and cost expenditure forecasts
- Review maintenance expenditure and forecasts on a regular basis to assure appropriate spending levels
- Ensure maximum plant availability through the implementation and use of established reliability principles and optimal asset management. Ensure that optimal manning levels are maintained
- Planning and organizational skills to organize resources, conflicting demands and deadlines
- Ability to communicate clearly both verbally and in writing and to provide consultation, advice and handle sensitive matters
- Ability to influence and lead others and interface with all levels of employees and external entities
6
Maintenance & Reliability Manager Resume Examples & Samples
- Develop and implement strategies that accelerate and improve current maintenance practices and processes to improve equipment performance, reliability and lower repair costs
- Initiate, implement, and manage the plant maintenance programs based on best practices in the chemical industry, with an emphasis on equipment condition inspections, planning/scheduling, high quality maintenance repairs, and safety, health & environmental policies and procedures
- Analyze operational data and equipment performance history to deliver improvements in critical maintenance related metrics including: unplanned downtime, PM compliance, schedule compliance, Mean-Time-Between-Failures, and maintenance related costs
- Coordinate with cross-functional departments (Engineering, R&D, Supply Chain, etc) to ensure operational effectiveness in new plants and expansions, and life cycle cost considerations in global equipment procurement activities
- Develop and deliver comprehensive maintenance and reliability tactical training to maintenance resources worldwide
- Leverage company subject matter experience/experts to advance current maintenance and reliability efforts through enhanced communication and best practice sharing by driving their application globally
- Partner with worldwide operations group to coordinate maintenance activities in support of operational excellence
- Coordinate planned maintenance and connectivity with Maintenance Managers in plant positions. Regularly respond with advice to maintenance/equipment related questions, ensure access to up-to-date maintenance/operating procedures, and facilitate strong team communications activities
- Establish maintain, and leverage value from a computerized maintenance management system (CMMS) for tracking work orders, planned/predictive maintenance, spare parts inventory/sharing, MRO management, and maintenance history of plant equipment on a global basis
- Identify required equipment and process upgrades and effectively manage associated projects
7
Maintenance & Reliability Manager Resume Examples & Samples
- Maintain general plant and operations facilities
- Manage maintenance and departmental costs
- Works collaboratively with the Operations Area Superintendents to achieve operations goals in terms of meeting production demands and minimizing operational cost
- Improve plant reliability
- Manage the utilities function for reliable, cost effective generation
- Manage the storeroom for optimum cost, proper stock levels and high quality items
- Supervise the maintenance supervisors and provide oversight for maintenance crews, both Solvay employees and outside contractors
- Supervise the Plant and Corporate Project Engineers (as appropriate), the Reliability/Maintenance Engineer and the Maintenance Planner/Scheduler, providing oversight for other contract technical resources and their activities
- Supervise the plant procurer
- Instill discipline and accountability in execution of site and departmental plant policies/procedures. Lead this effort by example
- Drive/Implement formal program of root cause identification/failure analysis and corrective actions for maintenance related failures
- Provide the leadership to perform work in an orderly and proactive manner based on principles of reliable design and preventive/predictive maintenance practices
- Develop, implement and continually improve maintenance management systems including mechanical integrity programs, work order system, maintenance standards and procedures
- Develop and implement personal development plans for self as well as direct and indirect reports
- Develops, reports, monitors and is responsible for (along with the Operations Area Superintendents) improvement of key performance indicators for maintenance such as maintenance expenses, the availability component of OEE, number of call-ins, effective planning rate and work ratios compared to total work (i.e. emergencies, PM work, and improvement work)
- Manage the capital spend at the site to insure cost effective installations, reliability in design and accomplished within the approved capital spend budget
- Excellent leadership and organizational skills to manage, motivate and develop personnel and to facilitate cooperation between departments
- Good computer skills with working knowledge of Google Apps, MS Word, MS Excel, MS Powerpoint and MS Project. General understanding of databases is desirable
- Familiarity with Industrial Hygiene concepts and Personal Protective Equipment
- LI-TC2
8
Maintenance & Reliability Manager Resume Examples & Samples
- Work order management (planning, scheduling, execution, budget vs. actual resource consumption)
- Optimise the configuration and use of our Computerised Maintenance Management System (Maximo Asset Management), in collaboration with our Maximo team
- Validate RCA analyses, track leading and lagging maintenance KPIs, and follow up on the execution of corrective actions
- Coordinate the training of our personnel and the implementation of a Reliability-Centred Maintenance (RCM) strategy
- Follow up on the correct planning, preparation, execution, and closing activities for annual shutdowns and other major maintenance repairs
- Follow up on the execution and effectivity of predictive maintenance activities and other specialized inspections
- Lead and review the annual preparation of Maintenance budgets, continuous follow up of actual costs and the evolution of inventories, and benchmark our costs across plants
- Prepare 5 years Maintenance CAPEX plans and high-level budgets
- Ensure the correct contractual set up and execution of subcontracted activities
- Project Management diploma/certificate from a recognised international organisation
- Lean Management diploma/certificate from a recognised international organisation
- Experience with the IBM Maximo Asset Management System
- Experience in the implementation of ISO 55000 Asset Management Standard
9
Maintenance Reliability Manager Resume Examples & Samples
- 1). The ideal candidate will have a Bachelor Degree in Electrical Engineering (preferred discipline). A Bachelor Degree in Engineering or Business related field is secondary but acceptable depending upon related experience in a manufacturing environment
- 2). Minimum of 5 years of management experience, leading and mentoring supervisory level direct reports. 7 to 10 years management level experience preferred
- 3). Experience working in a fast pace 24/7/365 manufacturing environment preferred
- 4). PROVEN Transformational Leadership, preferably moving a maintenance organization away from a reactionary environment to a Reliability focus
- 5). Demonstrated experience in leading continuous improvement efforts
- 6). Excellent verbal and written communication skills
- 7). Ability to coordinate with other departments and managers and work as a team
- 8). Knowledgeable at maintaining accurate employee documentation and files
- 9). Proficiency using MS Office applications, including Word, Excel and PowerPoint
10
Maintenance & Reliability Manager Resume Examples & Samples
- 40% Reliability and Maintenance Leadership: Ensure effective and efficient maintenance of the facility with a culture of continuous improvement. Provide the necessary planning to ensure the reliability of the plant and associated systems by use of various predictive and preventative maintenance programs. Develop maintenance budgets and manage expenditures accordingly. Lead the development of the three year capital plan for the facility. Lead utilities management for the facility. Collaborate with other locations to ensure best practice sharing. Be a visible presence in the community by active involvement, building networks and understanding the needs and concerns of the community
- 30% Engaged Employees: Create an environment where all employees are expected to be active members of the team. Involve employees in the business and hold them accountable to expectations. Recognize and celebrate successes. Challenge people to be better than they thought possible. Create opportunities for growth and development. Nourish the culture of precision maintenance, ensuring that all craftspeople are equipped with the requisite skills to be certain of success for themselves and the facility.Ensure an inclusive environment that is representative of the local market
- 20% Process Safety Management and Employee Safety: Champion process safety management (PSM) activities at the site and provide resources to support the development of the appropriate programs. Support compliance with the appropriate occupational health and safety programs. Help hold employees accountable for keeping their co-workers safe. Actively work to prevent/eliminate hazards that cause injury or illness
- 10% Customer Relationships: Will have some direct customer contact primarily at the facility
- At least four years of experience in maintenance, operations, or engineering, including significant daily people supervision/coaching/developing/leadership experience
- Working knowledge of processing equipment, construction and utilities
- Experience in leading teams through significant change
- Demonstrated ability to organize and implement projects which improve the operational effectiveness of a processing facility
- Computer skills including use of spreadsheets, word processing tools and understanding of databases. Comfort learning new technologies
- Ability to work in a variety of business environments including and plant floor in both hot and cold settings. Significant amount of time spent standing, walking, bending, etc
- Computer/phone usage on regular basis
- Travel occasionally (ie less than 10%)
- Ability to work a variety of hours to cover multiple shifts. Occasional weekend work. Ability to be on call
- This position shall have the responsibility to report problems with the food safety management system to identified person(s). This position has the responsibility and authority to initiate and record actions
- Acquire and maintain knowledge of HACCP/OPRP/PRP (GMP) policies and requirements to complete all monitoring and/or verifications tasks as outlined in Food Safety Management System and ensure that corrections and corrective actions, if needed, are taken per the Food Safety Management System
11
Maintenance & Reliability Manager Resume Examples & Samples
- Utilize technical skills and experience to promote the identification and solution of workplace problems
- Manage the maintenance budget and effectively manage costs
- Track maintenance expenditures, make adjustments as needed, and communicate progress to others
- Maintain employee morale and a productive workforce
- Participate in the selection of employees and plan for future needs
- Utilize technical skills and experience to manage process and equipment reliability, availability and operational effectiveness
- Implement and oversee Maintenance & Reliability (M&R) process
- Facilitate predictive/preventive work and ensure maintenance supervisors analyse results of predictive data
- Review existing work methods and align methods in accordance to M&R Center of Excellence (COE) practices
- Contribute to and monitor annual plan for department as well as balanced scorecard and standards and goals
- Execute and champion Cargill environment, health and safety procedures in the maintenance department and plant operations
- Assure required functions are performed in a timely and accurate manner and according to policies and procedures
- Electromechanical Engineer or proven capable to work at this level
- Minimum 5 years of experience leading an M&R team, preferably in the food industry
- Excellent technical qualifications: mechanics, electrical engineering, technical and administrative software
- Knowledge of principles of reliability
- Experience in continuous improvement projects
- Languages: native French speaker + good knowledge of English. Dutch is a plus
- Experience with CMMS ( SAP PPM or Maximo or similar)
- A firm and solution-oriented attitude, with continued focus on efficiency and cost control is essential
- Good leadership skills, good management experience of technical team
- Team player, good communicator
- Structured, strong skills in planning and organizing
- Capable of making good decisions even under stressful circumstances
- Knowledge of automation is a plus
12
Maintenance & Reliability Manager Resume Examples & Samples
- Minimum of 3 years experience in maintenance management or as part of a consulting practice focused on maintenance, reliability and operational excellence
- Minimum of 3 years experience in Resources industry
- Deep expertise in Preventive Maintenance, Predictive Maintenance, RCM, FMEA, Key Performance Indicators (KPI), Inventory and Warehouse Management, CMMS and/or EAM
- Background in Maintenance Management, MRO Inventory Management and/or Reliability Engineering
- Experience in M&R best practices, root cause analysis, criticality analysis and lifecycle management
- Certified Maintenance and Reliability Professional (CMRP) preferred
- Working knowledge of common maintenance systems to include SAP PM, Oracle eAM, and IBMm Maximo
- Direct experience in Resources industry segments is essential
- Proven ability to deliver management consulting projects with a focus on maintenance effectiveness
- Ability to support business development efforts with specific emphasis on value proposition development and solution architecture
- Demonstrated ability to work creatively and analytically in a problem-solving environment
- Program management and service delivery expertise to include resource planning, staffing, and status reporting
- Ability to work as a team member or independently at client sites
- Willing to travel to domestic and international locations
13
Maintenance Reliability Manager Resume Examples & Samples
- Bachelor’s degree in Industrial or Mechanical Engineering, Supply Chain/Operations, or a related field
- Minimum 3 years of professional experience in manufacturing and/or maintenance related process improvement initiatives
- Demonstrated knowledge and experience implementing reliability centered systems and procedures in a complex manufacturing environment
- Demonstrated strong Knowledge and experience implementing Predictive technologies systems, routines, vibration analysis, Infrared thermography, Oil analysis
- PMO- Preventive Maintenance Optimization & RCFA strong knowledge and ability to lead those strategies
- Significant knowledge of the Corn Wet Milling or similar type processes desired
- Certified maintenance and reliability professional preferred
- Demonstrated leadership experience and the ability to concisely communicate objectives and results to reach targeted goals
- Ability to work as part of a team with strong leadership, analytical, problem solving, interpersonal and communication skills
- Demonstrated ability to influence others without direct line of authority
14
Maintenance & Reliability Manager Resume Examples & Samples
- 50% Development and supervision of direct and indirect reports (coaching, Performance Management Plans (ePM's)). Work with peers at location in establishing consistent personnel policies. Lead department/area in a manner that leads to an engaged and safe environment. Food Safety Responsibilities. Responsible for working with site contractors to ensure a safe work environment with a basis in behavioral based principles
- 20% Develop strategies to include technical optimization of processes as well ensure continuous improvement to optimize the company’s physical assets, processes, and strategies. Collaborate with the operations team and peers at other facilities to establish plant policies. This involves partnering with BU Process Development Group (PDG) and Center of Expertise (COE)
- 15% Utilizes leadership and expertise in the principles of Root Cause Analysis and Reliability Centered Maintenance to create an environment of continuous, aggressive defect elimination program that drives asset reliability improvement
- 10% Establish, implement, and maintain facility maintenance budget and ensure reliability principles to improve the facility costs and productivity. Oversee product quality to ensure total customer satisfaction. Interface with customers on plant visits and audits
- 5% Any other duties as assigned
- OR High School diploma or GED and a minimum 10 years technical experience in lieu of degree
- Minimum 5 years of operations management
- Minimum 5 years of reliability project management
- Minimum 3 years of demonstrated supervisory experience
- Strong technical experience and or knowledge
- Supervision, including employee hiring and retention, performance review and discipline
- Demonstrated team building, leadership and conflict resolution skills
- Working knowledge of Food Safety, Occupational Safety and Health Administration (OSHA) and Environmental regulations
- Knowledgeable of basic HR practices, Equal Employment Opportunity (EEO), Guiding Principles, etc
- Ability to communicate effectively both verbal and written within multiple levels of the organization
- Demonstrated ability to build and maintain effective working relationships both internally and externally
- Leadership: A demonstrated ability to lead people and get results through others
- Demonstrated effective systematic approach to problem solving
- Microsoft Office Suite experience
- Ability to organize, coordinate and accomplish multiple tasks
15
Maintenance & Reliability Manager Resume Examples & Samples
- High school diploma or equivalent degree
- Minimum of five (5) years of experience managing a maintenance group in a manufacturing, industrial or military environment
- Minimum of five (5) years of maintenance and reliability experience with industrial equipment and/or manufacturing systems
- Must have experience in leading improvement efforts in Maintenance, Reliability, and Predictive and Preventive Maintenance
- Working knowledge and experience in maintenance planning, scheduling, and coordination
- Experience routinely utilizing Root Cause Analysis (RCA) or other similar problem solving tools
- Working knowledge and experience with computerized maintenance management systems (CMMS)
- Must be able and willing to work in a manufacturing plant environment, including extended periods of time in noisy, non-air conditioned or unheated areas
- Bachelor's degree or higher in Industrial, Mechanical, Electrical, or Chemical Engineering
- Certification as a Maintenance Reliability Professional
- Wood products manufacturing experience
- Experience with MP2
16
Maintenance & Reliability Manager Resume Examples & Samples
- 6 - 8+ years of industry or consulting experience as a Reliability and Maintenance practitioner (including Oil and Gas Upstream)
- Consulting experience in Maintenance and Reliability domain preferred
- Working knowledge of common maintenance systems to include Meridium, SAP PM, Oracle eAM, IBM Maximo, Ivara, and NRX
17
Maintenance & Reliability Manager Resume Examples & Samples
- Manage the assets, teams and processes to deliver World Class SHE performance in line with the site strategy. Lead the organization to create and maintain a safe work environment / mindset for their employees, contractors, and visitors achieving the site’s goal of zero safety and environmental incidents
- Support site and department manager in establishing and managing the site’s asset reliability program in an effort to achieve World Class reliability and maintenance effectiveness through the implementation of accepted industry best practices in the following areas
- In depth knowledge of accepted Maintenance best practices and a sound understanding of reliability practices. Certification as a Maintenance and Reliability Professional is desired but not required
18
Maintenance Reliability Manager Resume Examples & Samples
- Drives continuous improvements within the Maintenance Department
- Work order and asset management, refining PM schedules, technician cross-training
- Manages maintenance team comprised of Maintenance Planner, Lead Technician, Facilities and Production Technicians, Maintenance Planner and MRO Buyer
- Administrates and refines Computerized Maintenance Management Software (DPSI / iMaint) through continuous improvement efforts and action items
- Responsible for the site utility infrastructure
- Drives Preventive and Predictive maintenance practices and technologies to increase equipment reliability
- Maintains departmental Dashboard, KPI’s & Metrics, ISO point person & maintains all documentation related to the Maintenance Dept. regarding ISO 9001 and FSSC 22000
- Maintains all calibration records for calibrated and certified instruments / provides traceability for certified equipment and instrumentation
- Participates -and presents documentation for all internal and external customer audits. ( ISO, AIB, GMP)
- Establish maintenance parts inventory / MRO purchase order system / maintains Vendor Managed Inventory relationships
- Collaborates with engineering group in developing Predictive & Preventive Maintenance programs & new equipment specifications and validations
- Manages Contractors and Vendors on a daily basis as required
- Manages oil sampling & lubrication program for critical wash down & rotating equipment
- Develop Preventive & Predictive Maintenance procedures for outside contract services
- Initiated and leads maintenance department training program. Created SOPs, PM Tasks, PPT
19
Maintenance & Reliability Manager Resume Examples & Samples
- Supervising and evaluating employees
- Overseeing various maintenance and operational functions and departments
- Leading multiple teams who meet operational goals and objectives
- Developing and implementing various maintenance and operations programs
- Applying broad maintenance and operations management principles and practices
- Interpreting and applying department policies and procedures and applicable laws, rules, and regulations
- Developing and analyzing applicable maintenance reports
- Coordinating activities across multiple groups
- Investigating and resolving maintenance and operational problems
- PC skills; Microsoft Office applications (Word, Excel, PowerPoint, Outlook); and other applicable applications
20
Maintenance & Reliability Manager Resume Examples & Samples
- Organizes the designs, specifications and estimated costs for internal or contracted renovations, modifications, expansions or installation of plant facilities and utilities
- Establishes contracted maintenance and service programs, procedures and record systems in order to manage and measure the performance level of these services
- Provides maintenance, engineering and cost advice about plant equipment and facilities related to the short and long term needs of the business
- Assures compliance with national, regional and local insurance ordinances, regulations and codes
- Analyzes and controls unit or plant wide startup/shutdown of plant facilities in areas of responsibility including maintenance and repair, planning, execution, follow-up and
- Provides guidance in supervising the planning, scheduling and execution of daily department activities while establishing priorities, assigning work and ensuring that work is accomplished in a timely, safe and cost effective manner
- Monitors and controls area costs and spending; minimizes employee overtime, supplies and maintenance cost; assumes ownership for maintenance related spending and accounts through accurate budgeting, estimating and cost control
- Assists engineering in reviews of new or proposed installations for proper operation, equipment design, materials of construction, maintenance cost, safety, ease of maintainability and operation procedures
- Develops and maintains key department performance indicators in the areas of equipment and process reliability and maintenance, spending and work system and workforce effectiveness
- Promotes and maintains Process Safety Management and ISO Standards
- Monitors established plant performance indicators, including variance reports, production reports, quality reports and injury reports
- Prepared reports in accordance with the company policies and submits by required deadline
- Participated in plant and Division audits, interfaces with internal and external auditors and regulatory and government agency personnel
- Guides supervisors on union contract interpretation, compliance with organization policies and adherence to quality control standards
- Participates on plant leadership team and in various weekly conference calls and meetings
- Reviews and approves requisitions, MOCS, projects, etc
- Works closely with plant engineering and Division resources on capital project design and implementation. Provides input and review to improve reliability and maintainability. Provides leadership in capital project implementation at the plant
- Manages related employee actions, including final job selection, training, performance appraisal, discipline, safety, time approval and grievance procedures
- Manages and motivates direct reports; reviews, assesses and provides direct and immediate performance feedback as needed; develops and builds employee skills, supports their professional development and enables employees to optimize their contribution to the department
- Facilitates positive change in the Maintained and Reliability organization by proactively driving department initiatives such as craftsman skills improvements, SAP and asset management system utilization, planning and scheduling improvement initiatives, maintenance cost reduction, warehouse cost and plant downtime reduction projects, etc
- Investigates all applicable EHS incidents, employee safety concerns, customer complaints and raw material/final product quality issues
- Leads or assists in developments and implementations of equipment reliability related incident corrective actions and ensures an adequate and effective Root Cause Failure Analysis (RCFA) has been completed
- Drives continuous improvement
21
Maintenance Reliability Manager Resume Examples & Samples
- Role model all safety standards/processes and on-the-job behavior by living our core principles, creating a positive and inclusive work environment
- Working with all disciplines of production, mechanical, electrical and mobile equipment maintenance to improve reliability
- Ensures all activities reflect safety values while working with all disciplines
- Builds positive relationships with operations and maintenance personnel to continuously improve mill operations
- Leads the organization to improve reliability through established processes and plans
- Continuously improve our preventative and predictive maintenance program following "best maintenance practices" and utilizing SAP
- Practice responsible financial management in the execution of maintenance reliability functions
- Facilitates fact-based meetings with maintenance, production, leadership to identify priorities and plans to improve
- Responsible for the development of maintenance leaders and associates through clear expectations, performance reviews, coaching and other professional approaches
- Ensure compliance with health and safety and other legislation
- Contribute toward strategic planning process to include providing input, direction and solutions to issues based on analytical data
- Assures purchasing functions follow established policies and procedures
- Serve as an alternate member of the joint labor-management committee and health and safety committee as necessary
- Remain current and up to date on changing technical, reliability and maintenance management improvements in the industry
- As necessary, own or contribute to other mill functions, such as health and safety or environmental initiatives
- Bachelor’s Degree in an industry-related field: Mechanical, Electrical or Industrial Engineering
- Reliability professional certification, such as CMRP, CRL, etc
- Minimum of three (3) years’ experience in a maintenance reliability role in an industrial or manufacturing environment with a demonstrated ability in safely delivering operational excellence
- Ability to establish positive relationships with mill leadership, business leaders and associates, effectively lead people, and promote healthy teamwork
- Good working knowledge of electrical, mechanical and PLC programming and/or troubleshooting
- Excellent planning, problem solving, communication and organizational skills
- Demonstrated experience in effective root cause analysis
- Experience working with SAP or other CMMS systems, along with strong computer skills with proficiency in Microsoft Word, Excel and Outlook
- Expertise in preventive and predictive maintenance methods
- Initiative to get things done with minimal supervision
- Ability to develop and lead training activities
- Proven application of safety practices in a manufacturing environment
- Willingness to travel occasionally to other units to review opportunities to exchange technology, innovations and best practices
- Experience managing in a unionized environment is an asset