Manager Maintenance Resume Samples
4.5
(124 votes) for
Manager Maintenance Resume Samples
The Guide To Resume Tailoring
Guide the recruiter to the conclusion that you are the best candidate for the manager maintenance job. It’s actually very simple. Tailor your resume by picking relevant responsibilities from the examples below and then add your accomplishments. This way, you can position yourself in the best way to get hired.
Craft your perfect resume by picking job responsibilities written by professional recruiters
Pick from the thousands of curated job responsibilities used by the leading companies
Tailor your resume & cover letter with wording that best fits for each job you apply
Resume Builder
Create a Resume in Minutes with Professional Resume Templates
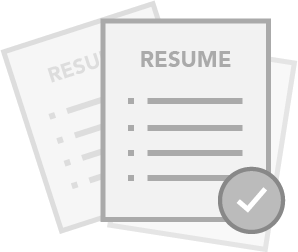
CHOOSE THE BEST TEMPLATE
- Choose from 15 Leading Templates. No need to think about design details.
USE PRE-WRITTEN BULLET POINTS
- Select from thousands of pre-written bullet points.
SAVE YOUR DOCUMENTS IN PDF FILES
- Instantly download in PDF format or share a custom link.
IK
I Koss
Irwin
Koss
718 Lakin Ridge
Boston
MA
+1 (555) 753 9832
718 Lakin Ridge
Boston
MA
Phone
p
+1 (555) 753 9832
Experience
Experience
Phoenix, AZ
Manager Maintenance
Phoenix, AZ
Fadel-Kiehn
Phoenix, AZ
Manager Maintenance
- Establish criteria for assessing the quality of work performed by employees and contractors
- Focus on continual improvement, efficiency and value driven performance management
- Manage project engineer to improve/develop maintenance processes
- Develop and execute capital projects to meet schedules and budgets
- Responsible for maintaining budget for repairs, tracking repairs and obtaining quotes for work to be performed
- Lead, manage and direct all activities for ConAgra Performance System Planned Maintenance Pillar
- Responsible for executing the capital plan to include all engineering design and project management, working with both internal and external resources
Detroit, MI
Manager, Maintenance
Detroit, MI
Blick and Sons
Detroit, MI
Manager, Maintenance
- Working closely with Operations peers to achieve production goals, provide support and expertise to the Distribution and Supply Chain Operations teams
- Providing cost justification and business case analysis to local and corporate business partners
- Budgeting and budget management
- Other duties as assigned
- Maintains master record of safety manuals, procedures, Hazmat, and MSDS sheets. Coordinates with safety vendors and facility audits with internal and external personnel. Prepares follow-up reports and enforces the recommendations of safety audits. Coordinates emergency response plans and safety training for the leadership team, safety committee personnel and all building associates. Enforces safety rules and procedures are strictly followed both at the companies policy level and through all Federal and State programs
- Ensure a positive working environment through continuous communication of policies and procedures that affect the Maintenance department staff. Conduct regularly scheduled meetings to inform, resolve issues and provide direction
- Facility Planning - Support campus construction projects by acting as local coordinator for general contractor and Divisional Engineering Project Manager. Identify facility design issues and present alternate solutions. Review project progress to recognize and resolve safety or quality issues. Provide business partners with project updates
present
Los Angeles, CA
Senior Manager Maintenance
Los Angeles, CA
Stehr-Kessler
present
Los Angeles, CA
Senior Manager Maintenance
present
- Guides and directs terminal and/or hangar management/supervision in the planning and execution of aircraft maintenance
- Working through subordinate managers/supervisors, plans, coordinates, and controls the daily operation of his/her operation
- Establishes current and long range goals, objectives, resource forecasts, plans and policies, subject to approval by the Managing Director
- Develops and maintains a strong working relationship with Union at all levels
- Requests feedback from Managing Director on his/her own performance at least once every 6 months
- Implements processes and works them through shift managers
- Meets with Managing Director and other Managers to ensure that operations are being executed in accordance with the organizations overall goals, strategies, policies and plans
Education
Education
Bachelor’s Degree in Engineering
Bachelor’s Degree in Engineering
University of Cincinnati
Bachelor’s Degree in Engineering
Skills
Skills
- Knowledge of Microsoft Office Suite of and the Internet. Well versed in the use of SAP
- Excellent written and verbal communication skills
- Strong critical thinking and problem solving skills
- Thorough knowledge of world-class maintenance management systems, work order processes, preventive/predictive maintenance, TPM, etc
- Possesses advanced technical skills in the mechanical / electrical fields (e.g. PLCs, instrumentation, mechanical engineering, etc.) and is able to lead resource planning efforts in a large manufacturing environment
- Responsibilities include interviewing, hiring, and training employees; planning, assigning, and directing work; appraising performance; rewarding and disciplining employees; addressing complaints and assisting in providing appropriate resolutions
- Carries out supervisory responsibilities in accordance with the organization's policies and applicable laws
- Ability to pass a safety sensitive medical
- Advanced Budget and Cost Control Knowledge
- Knowledge and experience in a maintenance management system
15 Manager Maintenance resume templates
Read our complete resume writing guides
1
Manager, Maintenance Resume Examples & Samples
- Develop People - Direct reporting responsibility for all campus Maintenance supervisors as well as Senior Mechanics with campus responsibilities. Establish clear performance objectives utilizing IDP and PPA tools. Insure expectations are consistent across campus, yet address specific facility needs. Provide training across campus to address individual development needs. Develop succession plan for Maintenance. Oversee application of Intern Development Program with Maintenance
- Facility Planning - Support campus construction projects by acting as local coordinator for general contractor and Divisional Engineering Project Manager. Identify facility design issues and present alternate solutions. Review project progress to recognize and resolve safety or quality issues. Provide business partners with project updates
- Equipment Maintenance - Leverage campus Maintenance personnel to address current needs of each facility. Oversee maintenance of campus equipment to maximize product warranties and uptime. Establish preventative maintenance programs to maximize reliability and to achieve or exceed life expectancies. Analyze and communicate performance results relative to key performance indicators. Benchmark performance of each facility to identify areas and establish methods of improvement
- Facilities Maintenance - Oversee grounds and facility maintenance for campus. Identify and coordinate necessary improvements, such as painting, landscaping, paving, etc. Define scope of janitorial work with business partners at each facility. Develop schedule and oversee quality of work
- Budgeting and Purchasing - Monitor spending to budget, and take corrective action. Manage the bid process for campus services and leverage the purchasing power across the campus to achieve economies of scale. Ensure parts purchases and services fall within budget guidelines. Oversee common CMMS for campus. Audit CMMS system and physical inventories to ensure proper accountability for parts expenses
- Project Management - Act as project manager for major material handling renovations and facility layout changes. Establish common procedures for processing project requests across the campus. Partner with business partners to prioritize projects and communicate status updates. Deploy campus resources within Maintenance to ensure timely completion of projects. Partner with Engineering to test and assess new technologies. Complete ROI justifications for proposed Capital expenditures relative to Maintenance
- BS Degree in technical or business field with 5 to 10 years minimum direct supervision
- Material handling, facilities maintenance
- Vision, Creativity, Versatility, Flexibility, Initiative, and Customer Focus
- Employee development, promoting teamwork, feedback, and coaching
- Contract negotiation and Project management
- PC Proficiency
- Safety regulations and codes
- Electrical, mechanical, pneumatics, PLC
- Material handling equipment
2
Assistant Manager, Maintenance Resume Examples & Samples
- Respond to assistance requests throughout facility
- Supervise/oversee operations conducted within department to ensure quality and service. This includes providing direction to staff as needed
- Consult with contractors
- Operate facility computerized facility management and control systems
- Develop and is accountable for department budget
- Provide prompt, strategic and cost effective solutions to facility maintenance issues
- Conduct inspection tours of building and grounds to ascertain that established standards of maintenance are being upheld
- May also perform basic and general maintenance within the following areas of the facility: Air Conditioning; Carpentry; Plumbing; Electrical
- Load/unload repair equipment, tools, supplies etc. as needed
- Utilize various lifts, to include but is not limited to forklifts and Genie lifts
- Utilize basic hand and power tools
- Maintain a safe work environment and adhere to all safety policies
- Performs other related duties as assigned and/or in the absence of Maintenance Manager
- A minimum of 5 years of relevant maintenance experience, preferably within a large facility such as a convention center, hotel, or hospital with at least 2 years within a supervisory capacity
- Experience utilizing lifts, hand and power tools
- Experience utilizing various methods, tools, materials and equipment within building operations and conversion operations
- A high school level education is required
- Vocational training within the area of general maintenance strongly preferred
- Must have the ability to lift 75 lbs., stand, sit, crouch and bend throughout the course of daily activities
- Be certified in various lifts (forklift, Genie, etc) or have the ability to become certified
- Requires the ability to interface with all levels of employees in all departments
- Ability to work a varied schedule including weekends and holidays, as required
- Ability to work long hours, while under pressure
- Ability to work in various climates based on the environment
3
Manager, Maintenance Iv-auburndale Resume Examples & Samples
- Manages and develops maintenance team leads/supervisor and maintenance technicians; Provides maintenance guidance and oversight for all plant associates; motivates, coaches and develops a diverse, high performing and engaged team to meet established goals and build organizational capability
- Supports plant facilities and equipment maintenance to produce quality products in an efficient and profitable manner; Supports the operation in ways to help reduce overall costs
- Continually reduces equipment downtime and increase availability through the establishment of a preventive/predictive maintenance program (including failure analysis) designed, directed, monitored and continually improved
- Manage plant level capital projects in conjunction with Project Managers
- Participates in, and supports, the Department safety training program. (I.E.: weekly safety meetings, shop safety inspections, enforcement of lock-out/tag-out program, enforcement of the confined space program, etc.)
4
Manager, Maintenance Resume Examples & Samples
- Champions and drives relentless reduction of breakdown losses through Breakdown Analysis and other appropriate Focused Improvement Tools
- Maintains good working relationships with other organizational units in the plant; ensures compliance to company and regulatory policies
- Bachelor’s degree required; Master’s degree highly desired; 7+ years of maintenance and 7 yrs. manufacturing experience
- TPM Certifications, ISO, Lean, Six Sigma, and/or continuous improvement strategy highly desired
- Strong experience in project management preferred; experience in Equipment Preventive Maintenance Management
5
Manager, Maintenance, American Canyon Resume Examples & Samples
- Develop and/or maintain an effective preventive maintenance program (including repair, modification and installation of equipment) in order to improve production efficiency and ensure optimum machine time availability
- Review plant production equipment environment (e.g., technology, systems, quality, cost, efficiencies, yield) in order to recommend process improvements
- Synthesize data and identify problems through operational and financial analysis in order to improve operational and financial performance
- Track maintenance schedules for trucks and/or equipment assets in order to ensure preventive maintenance is current
- Record and analyze plant equipment performance data using design and performance specifications in order to ensure optimum machine reliability
- Regularly inspect plant production support systems and equipment (e.g., HVAC, compressed air, refrigeration, production lines, process security, waste water treatment) in order to support effective plant operation
- Evaluate suppliers (e.g., spare parts, ingredients, materials) using KO guidelines (e.g., price, service, delivery capabilities, capacity) in order to select optimal supplier
- Measure the use of equipment spare parts by tracking spare parts transactions through use of a Maintenance Database Management tool in order to determine proper re-order points
- Develop strategies for implementing The Coca-Cola Quality System in order to ensure product quality and food safety as defined by Company requirements
- Maintain and lead Maintenance and Calibration portion of the Quality System
- Develop process improvement initiatives (e.g., supplier business processes and practices) in order to benefit the KO system and suppliers by directing supply chain activities, involving external suppliers, functional peers, account teams and/or cross-functional teams
- Provide direct reports with leadership, direction, and coaching to achieve work objectives and improve performance and skills
- Train and qualify Company associates to install or repair equipment according to Company guidelines in order to meet/exceed performance criteria and maximize business results
- Maintain tools, equipment (e.g., plant equipment), and Company assets in good condition in order to ensure effective response to mechanical or technical problems
- Provide technical assessment of equipment to determine what components should be repaired or replaced to maximize equipment performance
- Bachelor's Degree or equivalent work experience
- Drives Innovative Business Improvements: Develops new insights into solutions that result in organizational improvements; promotes a work environment that fosters creative thinking, innovation and rational risk-taking
- Imports and Exports Good Ideas: Relentlessly seeks, shares and adopts ideas and best practices in and outside the Company and embraces change introduced by others
- Develops and Inspires Others: Builds and maintains relationships that motivate, guide, and/or reinforce the performance of others toward goal accomplishments. Develops self and others to improve performance in current role and to prepare for future roles; seeks and provides feedback and coaching to enhance performance
- Lives the Values: Demonstrates the values of The Coca-Cola Company through words, actions, and by example; fosters an environment that reflects the values of the company
- Engineering Change Management: Knowledge of the principles of change management within an engineering system. Includes the ability to use engineering change documentation and approval to manage supply of parts, maintenance, installation, removal and refurbishment to a base of existing equipment to minimize life and ownership costs
- Equipment Evaluation: Ability to assess gaps in design and performance of equipment (e.g., fountain dispensers, manufacturing plant processing equipment), design corrective actions, and make basic corrections and repairs. Includes the ability to work in field-based environment to oversee trouble-shooting, commissioning, repair, removal and improvement of equipment
- Warehouse/Facility Layout Design: Knowledge of warehouse/manufacturing layout or design elements (e.g., product flow, storage requirements) necessary for effective manufacturing or warehousing
- Equipment Installation Requirements: Knowledge of equipment installation requirements (e.g., electrical power, water, drain, airflow, space requirements). Knowledge and application of dispensing equipment installation principles
- Engineering Analysis: Knowledge of analytical engineering tools including critical path problem solving and root cause analysis in order to determine design feasibility and identify variation from performance specifications
- · Plant Utilities: Knowledge of the non-manufacturing processes and systems that support the plant (e.g., electrical heat, HVAC, plumbing). Ability to diagnose problems with these systems and perform basic maintenance and repairs
6
Manager, Maintenance Resume Examples & Samples
- Good Manufacturing Practices
- Maintenance Troubleshooting
- Failure Analysis
7
Manager Maintenance Resume Examples & Samples
- Execute plant-specific vision and mission to assure continuous improvement and alignment with the corporate vision
- Ensure that all manufacturing / facility systems are properly resourced and that all resources are efficiently utilized
- Direct maintenance supervisors and hourly maintenance associates in their roles and responsibilities to meet plant objectives in safety, quality, cost, and customer service
- Provide technical support for efficient troubleshooting / problem solving activities and maintenance repair to maximize efficiencies and limit downtime
- Continuously apply sound mechanical and electrical solutions to resolve hindrances to plant efficiencies and to drive continuous improvement
- Provide leadership in implementing / maintaining preventive and predictive maintenance programs
- Manage maintenance department costs within budgetary guidelines
- Ensure that appropriate inventory levels for standard replacement parts are maintained
- Manage the buildings and grounds such that good manufacturing practices (GMP) are adhered to and a professional appearance is maintained
- Perform follow-up analysis to identify and resolve recurring downtime / inefficient operational issues
- Schedule mandatory inspections and coordinate certifications and appropriate authorities
- Ensure environmental compliance
- Drive employee engagement, training, and development to maximize manufacturing, quality, safety, and productivity goal attainment
- Effectively communicate results and action plans to appropriate employees and managers
- Collaborate directly with human resources to insure employee issues or concerns are correctly addressed and resolved
- Collaborate with finance to create and execute a maintenance and capital budget to insure that financial allocations and obligations are set, administered and met
- Initiate cost savings measures
- Ensure all plant maintenance operations are conducted in a safe and controlled environment
- Ensure all quality and regulatory standards, specifications and policies are met or exceeded
- 7-10 years maintenance experience in a manufacturing environment
- 3-5 years Supervisory / Management experience
- Bachelor's Degree in Engineering, Industrial Management, Manufacturing, Production Operations Management or equivalent field of study
- Excellent communication, presentation, and negotiation skills
- Strong computer application skills, network and PC business application software
- Basic mathematical and statistical skills
- Basic financial skills and understanding
- Food industry and experience in a union / union free environment preferred
- Key Leadership Competencies in addition to Ethics / Values and Integrity / Trust, (Action Oriented, Directing Others, Priority Setting, Decision Quality, Organizing, Process Management)
8
Manager Maintenance Resume Examples & Samples
- Work experience of managing diesel locomotive / rolling stock maintenance shed and should be technical proficient in understanding and maintaining locomotive system level and sub-systems level
- Ability to analyze locomotive performance data, records, reports including loco self-test data
- Should be capable to adopt and effectively implement IT systems related to monitoring & maintaining Locomotives
9
Manager, Maintenance Resume Examples & Samples
- Please note the Brampton Distribution Centre will be relocating to a brand new DC located in Bolton during the spring of 2017. The Bolton DC is a 1.45 Million square foot automated distribution centre which plays an integral role in Canadian Tire's supply chain network. This building will utilize many different integrated material handling equipment technologies such as Automated Guided Vehicles, Tire Gantry, Bose Conveyor system and Beaumier sorter, while using a CTR homegrown Warehouse Management System called DCCS
- 5-8 years of related management experience (warehouse equipment, mobile fleet, PLC knowledge and experience, and facility/grounds management)
- Post-secondary degree in business, operation or facilities management, engineering, technology diploma (Electrical, Mechanical, Industrial) or equivalent Skilled Trade or equivalent technical experience
- Experience with robotics, integrated conveyor and automated guided vehicles would be considered an asset
- Proven leadership of a technical based team that delivered strong results
- Passionate, influential leader that can build a credible roadmap, strive for the common good of all stakeholders and commits to and delivers results
- Proven experience managing a technical team within a large, complex, multi-shift, automated distribution centre
- Familiarity with and experience in
10
Manager, Maintenance Resume Examples & Samples
- Responsible for ensuring equipment reliability expectations are achieved in a 24/7, high-throughput, API production facility
- Provide strong leadership to the department in the coordination and execution of maintenance practices, department operations procedures, AbbVie Safety Policies and AbbVie quality policies are understood, communicated and followed by the department
- Provide and maintain tools and equipment necessary for the effective completion of work assignments including hand tools, communication devices, trucks and other heavy equipment, PC's and software appropriate to facilitate effective delivery of maintenance operations
- Supports the Plant Manager in developing Key Performance Indicators for the organization, tracks data related to KPI's, and drives improvement through the Maintenance Excellence Program (MEP) across the organization
- Serves as a project manager for department initiatives and capital projects. Leads members of the organization in the development of the budget, scope and schedule for major projects
- Ensure employee resource allotment and workload requirements are balanced to meet the needs of the business on a daily basis as well as when forecasting future work capacity
- Serves as the conduit for communication within the department to ensure the leadership messages, organizational changes, and initiatives are communicated to direct reports. Also serves as the conduit for communication from direct reports back up to the area management
- Continually evaluates and balances short term production support needs with long term strategic objectives of the department
- College degree or equivalent experience. Strong problem solving and analysis skills are required. A technical degree (Engineering or Science) is preferred
- Minimum 10 years of experience in chemical/pharmaceutical processing equipment maintenance, facilities maintenance, reliability engineering, or a combination thereof. Minimum 2-4 years previous supervisory/management experience
11
Manager, Maintenance Resume Examples & Samples
- Ensure maintenance activities full meet HSE and 5S requirements
- Monitor and control the maintenance cost under the budget
- Guide the contractor to make sure their activity properly
- Fully follow company related regulations and local mandatory requirement, ensure maintenance staff and contractor with high EHS awareness
- Monitor and guide maintenance work properly, keep the maintenance at high quality & safety
- Prepare maintenance yearly budget and monitoring the actual cost is in the budget
- Organize the cost saving analysis with engineers, improve spare parts warehouse management
- Organize engineers to fulfil the site maintenance work, make sure the external contractor works at site full comply with company regulations
12
Manager, Maintenance RW Oconus Resume Examples & Samples
- Serve as a point of contact for technical support issues relating to the assigned program
- Address any areas of concern or non-compliance as requested by the Director of Maintenance of Quality Director
- Act as liaison with Technical Services personnel relating to all maintenance/technical issues
- Work with other Managers to assist in the selection and training efforts to recruit and train personnel for new and existing programs as required
- Work closely with Maintenance Planning personnel to forecast scheduled maintenance events to minimize aircraft downtime
- Coordinate with Rotables personnel to insure all components sent for repair have the appropriate work scope applied
- Act as a liaison with various vendors when necessary to expedite the repairs process
- Federal Aviation Administration Airframe and Power Plant License
- Five (5) years experience on fleet types relevant to the assigned program (S-61)
- Proficient in MS Office (Word, Excel, Access, PowerPoint)
- Performance Management - Sets clear expectations & direction for staff; achieves team results consistently; coaches staff to improve; is a positive role model
13
Manager, Maintenance Resume Examples & Samples
- Keeping track of work order completion and performance metrics in a 24/7 manufacturing setting. Ensure maximum productivity and efficiency in a safe and compliant manner
- Ensure safety, compliance, efficiency, and speed is followed in all aspect of the jobs executed by the department. Strives for 100% plant equipment and operational reliability
- Ensure planning and scheduling of Work Orders to maximize equipment uptime and availability
- Manage, identify, hire, develop and recognize technical staff. Create and maintain employee development. Promotes an open and transparent working environment
- Adheres to applicable budgets for Maintenance for applicable cost centers
- Apply specialized knowledge in a creative way to a broad range of difficult problems. Implementing use of predictive technologies for Maintenance and troubleshooting
- Review and analyze staff proposals to determine if benefits derived and possible applications justify expenditures. Approve and submit proposal to Sr. Manager
- Responsible for enforcing policy and clarifying procedures for the staff in accomplishing and documenting projects
- Drive improvements in equipment performance metrics like OEE, MTBF, etc
- Provide support of Asset Management Excellence vision and implementation plan consistent with implementing Reliability Metrics, tracking and tools, Predictive Maintenance Program, World Class MRO and maintenance Management activities to maximize wrench time per technician
- Participate in an aggressive management developed plan to reduce exceptions across Plant Services departments utilizing data and appropriate Continuous Improvement Tools
- Must be well versed in Maintenance Management discipline with the ability to manage multiple teams simultaneously and manage multiple priorities in manufacturing plant setting
- Knowledge of GMPs, FDA guidelines, purchasing practices and process validation
- Knowledge of basic laboratory and pharmaceutical production equipment including but not limited to: Filling machines, process tanks, support equipment, analytical equipment, and CIP/SIP systems
- Must be able to read and follow detailed written instructions and have good verbal/written communication skills
- Good computer skills, knowledge of Microsoft Word, PowerPoint, Visio and Excel
- Ability to design and influence outside of immediate scope of responsibility
- Proven track record of management/leadership effectiveness
- Experience with Asset Management Initiatives, Reliability Programs, Equipment Performance Metrics
- Must have be results oriented with a high level of energy
- Must be able to challenge the status quo and lead organizational change
- Must be able to create and present project overviews and other departmental presentations without assistance
- Must demonstrate the ability to learn new material quickly and demonstrate high potential for continued professional growth within Engineering
- Must be proficient in all elements of talent development, recruiting, development, performance management, and succession planning
- Must be able to work in controlled environments requiring special gowning. Will be required to follow gowning requirements and wear protective clothing over the head, face, hands, feet and body
- May work in a cold, wet environment, be exposed to sunlight and heat and be exposed to dust, gases, and fumes
- The incumbent must work in a clean room environment wearing special garments. Additionally, personal protective equipment must be worn due to safety requirements
- May occasionally be working in a loud area that requires hearing protection and other protective equipment to be worn
- May work around chemicals such as alcohol, acids, buffers and celite that may require respiratory protection
- May be required to participate in the departments after hour on-call support
- Must be able to work more than 8 hours a day or 40 hours a workweek as required
- May be required to work shifts, after hour’s weekend and holiday works
- Will have interaction with other people
- Pace may be fast and job completion demands may be high
- May be required to travel for business reasons, e.g. training and meetings
14
Manager, Maintenance Resume Examples & Samples
- Performs preventative service and repairs of the conveyor systems, facility related building equipment, and forklift fleet
- Purchase and maintains adequate inventory of all spare parts and necessary supplies to support properly all preventative initiatives or critical repairs
- Performs all duties related to facility improvements and capital projects
- Providing cost justification and business case analysis to local and corporate business partners
- Oversee all local projects both on a capital level and towards continuous improvement initiatives
- Insure all projects are completed successfully and coordinated properly so that no negative effect is realized in our production environment
- Provide financial planning and support of all maintenance related expense categories such as: fork truck repairs, building services and expense, conveyor upkeep, and contractual Services
- Maintain annual budgets and related dollars so that no over-spending is realized while continuously seeking out ways to reduce cost
- Maintains master record of safety manuals, procedures, Hazmat, and MSDS sheets
- Coordinates with safety vendors and facility audits with internal and external personnel
- Prepares follow-up reports and enforces the recommendations of safety audits
- Coordinates emergency response plans and safety training for the leadership team, safety committee personnel and all building associates. Enforces safety rules and procedures are strictly followed both at the companies policy level and through all Federal and State programs
- Maintains a working knowledge of all building systems to include items such as: generators, fire alarms, sprinklers, electrical, plumbing, HVAC, Roofing systems, Outside Landscaping & Site Support, and lighting
- Maintains a working knowledge of all equipment to include: lift trucks, conveyors, conveyor control systems, weighing devices, and any other material handling equipment
- Support the appropriate scheduled testing of all emergency support systems that our part of the plants structure (Emergency Generators, Fire Pumps, Fire Detection & Alarms Systems & Emergency Lighting.)
- Oversees general clean-up and building maintenance including wall, door, cage repairs and storage handling
- Maintains documentation on the building and all electrical/mechanical devices associated with the facility
- Oversees service contract maintenance work to ensure proper performance relating to equipment, the building and grounds
- Reports on maintenance operational repairs and expenditures control, analyzing facility workflow to include productivity, and quality
- Directs and develops Maintenance and Housekeeping staff members while maintaining a leadership role in the facility
- Insure all members of the team remain productive and are provided daily directives so that all projects or daily responsibilities are carried out effectively and with positive support of the local team
- Routine communication and interactions with other LC Maintenance Managers to standardize purchases, procedures, technology, and to re apply best practices. Meets attendance and punctuality standards
- Able to assimilate research data from a variety of sources, analyze, and recommend appropriate courses of action to take
- Able to avoid win/loss situations and ensure productive resolutions of conflict
- Able to transport up to 50 lbs
- Able to express ideas clearly and convey necessary information
- Able to facilitate group interactions
- Able to interact effectively with all levels of management
- Able to respond to common inquiries from regulatory agencies or members of the business community
- Able to set high short/long-term goals/standards of performance for self, subordinates, and others
- Able to supervise, train, and evaluate the performance of subordinates
- Able to think strategically and tactically
- Knowledge of occupational hazards of the trade and necessary safety precautions
- Able to use relevant computer system applications (which may include spreadsheets, word processors, databases, etc) at an intermediate level
- Proficiency with Excel, Word, PowerPoint, Visio, AutoCAD preferred
- Mechanical, electrical, and motor controls & Logic; Conveyor systems and operations; HVAC, electrical, mechanical, and plumbing maintenance. Financial acumen to include ROI analyses necessary
- Project management skills critical
- Able to maintain confidentiality of senstitive information
15
Senior Manager Maintenance Resume Examples & Samples
- 3 + years direct supervisory experience or comparable team leadership experience
- 5+ years’ experience in engineering project management and process and / or machine validation
- 3+ years’ experience in Six Sigma and/or Lean Manufacturing as well as CAPA process management
16
Manager, Maintenance Changzhou Resume Examples & Samples
- Solid knowledge of industrial engineering and maintenance,
- Excellent Knowledge of industrial process (site & equipment),
- Specialized skills in methods applied to multiple areas: industry, maintenance organization and new technology, buildings, etc.),
- Applied knowledge of Lean manufacturing and process improvements
- TPM expert
- Analyze failures to suggest improvements
- Manage and track maintenance order and troubleshooting
- Educate and train staff in equipment maintenance and facilities
- Intervening in case of failure by weighting the consequences
- Ensuring the safety of operations
- Apply the technical requirements (standards and regulations)
- Have the concepts of ergonomics
- Self-adaptation to new technologies
- Comply strictly methodological processes
- Analyze and synthesize technical issues and/or relationships
- Develop functional links with the work environment
- Good communication with multiple department involved and demonstrated practice on project presentation
- Good reporting skills: he works with all departments and all positions
- Ability to work with international team /environment
- Cultural awareness for China
- Degree or equivalent in five areas of industrial engineering and maintenance or specific university training in industrial maintenance
- Experience of 10 years on an equivalent position; Knowledge of industrial process site (site & equipment), plus methods applied to industry/maintenance (organization and technology)
- Technical English required
17
Senior Manager Maintenance Resume Examples & Samples
- Guides and directs terminal and/or hangar management/supervision in the planning and execution of aircraft maintenance
- Prepare or directs the preparation of short-term and long-range plans and resource budgets based on the Managing Director’s station goals and strategic objectives
- Establishes current and long range goals, objectives, resource forecasts, plans and policies, subject to approval by the Managing Director
- Oversees managers/supervisors who direct terminal and/or hangar and related support activities that implement the organization's plans, processes, policies, and procedures
- Represents the Station/Base and his/her work groups, as appropriate, in its relationships with airport management, FAA, TSA, suppliers, competitors, other government agencies, professional organizations, and similar groups
- Works closely with other Station/Base Managers to coordinate the accomplishment of new directives and new objectives
- Dispenses advice, guidance, direction, and authorization to carry out long term plans, tactical plans, process improvements, and standards / procedures consistent with established goals, strategies, policies and Managing Director approval
- Meets with Managing Director and other Managers to ensure that operations are being executed in accordance with the organizations overall goals, strategies, policies and plans
- Implements programs that meet Station/Base, Line/Base maintenance, M&E, and corporate goals and objectives
- Reviews operating results of his/her operation, compares them to established objectives, and takes steps to ensure that appropriate measures are taken to correct unsatisfactory results. Evaluates the results of overall operations regularly and systematically and reports these results to the Managing Director
- Creates and continuously improves the structure and processes necessary to manage his/her operation’s current activities and its projected workload
- Operation achieves its stated objectives and the Managing Director credits the Level 6 Manager for his/her operation’s contributions with a good to excellent performance review
- Performance reports show satisfactory levels of safety, compliance, dependability, reliability, and financial performance
- Relationships with coordinates, interdepartmental partners and external agency personnel are harmonious and productive
- Periodic meetings among the Station/Base and Airport leadership teams reveal no significant problems in the area of his/her operations
- Managing Director and Vice President agree that the operation of cross-functional relationships, procedures, processes, and data/information flow are effective
- Airline and aircraft maintenance technical knowledge
- Apply airline and aircraft maintenance knowledge to operational improvement activities
- Understand and create plans utilizing a wide array of airline and aircraft maintenance technical and process measurement data
- Influence and persuade others to adopt maintenance practices, procedures, and processes that differ from the norm
- Work cross-departmentally to resolve issues and develop lasting effective relationships and solutions
- Build a culture of discipline and develops disciplined people who engage in disciplined thought and who then take disciplined action
- Plan and manage improvement projects
- Create and effectively implement operational and tactical plans
- Effectively utilize operational workload and financial analysis, forecasting, and other data to improve performance
- Effectively delegate duties
- Balance Operational Management & Business Administration duties
- Provide effective coaching, management development, and succession plans
- Prepare and present information in an informative, persuasive, and effective manner
- Plan and conduct effective meetings that achieve specific goals / objectives
- Write, create, and present plans and presentations that are intelligent, focused, persuasive
- Confront conflict and facilitate resolution
- Apply a high level of conceptual/abstract thinking to solve performance issues
- Manage resources and budgets to meet operational and financial objectives
- Raise professional operational management standards throughout an organization
- Recruit, train, develop, and retain talented people
- Implement and manage organizational change
- Create a positive work environment, engage people, and inspires esprit de corps
- Provide leadership, getting the best out of people
- Related technical undergraduate degree
- Business or related degree is a plus
- Four year degree required
- A&P is a plus but may be required for certain positions
- Has a successful Line and/or Base station production operations management track record and experience at a Level 5 manager level
- At least 5 -10 years in experience in related aircraft maintenance management positions
- Experience managing, supervising and/or directing mid to large size supervisor workgroups in a multi-shift environment
- A successful track record and experience with process improvement in maintenance and/or production environments
- Experience in positions requiring budget understanding, resource forecasting and management, and workload planning in maintenance environments
18
Manager, Maintenance Resume Examples & Samples
- Performs preventative service and repairs of the conveyor systems, facility related building equipment, and forklift fleet. Purchase and maintains adequate inventory of all spare parts and necessary supplies to support properly all preventative initiatives or critical repairs
- Performs all duties related to facility improvements and capital projects. Providing cost justification and business case analysis to local and corporate business partners. Oversee all local projects both on a capital level and towards continuous improvement initiatives. Insure all projects are completed successfully and coordinated properly so that no negative effect is realized in our production environment
- Provide financial planning and support of all maintenance related expense categories such as, Fork Truck Repairs, Building services and expense, Conveyor upkeep, and Contractual Services. Maintain annual budgets and related dollars so that no over-spending is realized while continuously seeking out ways to reduce cost
- Maintains master record of safety manuals, procedures, Hazmat, and MSDS sheets. Coordinates with safety vendors and facility audits with internal and external personnel. Prepares follow-up reports and enforces the recommendations of safety audits. Coordinates emergency response plans and safety training for the leadership team, safety committee personnel and all building associates. Enforces safety rules and procedures are strictly followed both at the companies policy level and through all Federal and State programs
- Maintains a working knowledge of all building systems to include items such as: generators, fire alarms, sprinklers, electrical, plumbing, HVAC, Roofing systems, Outside Landscaping & Site Support, and lighting. Maintains a working knowledge of all equipment to include: lift trucks, conveyors, conveyor control systems, weighing devices, and any other material handling equipment. Support the appropriate scheduled testing of all emergency support systems that our part of the plants structure (Emergency Generators, Fire Pumps, Fire Detection & Alarms Systems & Emergency Lighting.)
- Oversees general clean-up and building maintenance including wall, door, cage repairs and storage handling. Maintains documentation on the building and all electrical/mechanical devices associated with the facility
- Directs and develops Maintenance and Housekeeping staff members while maintaining a leadership role in the facility. Insure all members of the team remain productive and are provided daily directives so that all projects or daily responsibilities are carried out effectively and with positive support of the local team
- Able to use relevant computer system applications (which may include spreadsheets, word processors, databases, etc) at an intermediate level. Proficiency with Excel, Word, PowerPoint, Visio, AutoCAD preferred
- Strong knowledge in the following areas: Mechanical, electrical, and motor controls & Logic; Conveyor systems and operations; HVAC, electrical, mechanical, and plumbing maintenance
- Financial acumen to include ROI analyses necessary. Project management skills critical
19
Senior Manager, Maintenance Resume Examples & Samples
- Manages major and minor model manufacturing plan development and execution, including launch and trials of new facility modifications, new color development, and process changes within Paint plant; confirms new, minor, and current model program requirements; ensures requirements for quality, delivery, cost, and safety are met; addresses production concerns related to equipment downtime to ensure countermeasures are made in a timely manner; coordinates preventative maintenance program to minimize downtime
- Supports manufacturing as required to meet quality, cost, and delivery goals with continuous improvements to process equipment development, installation, and maintenance; provides direction to manufacturing regarding manpower utilization and efficiency
- Provides resources and guidelines for assigned engineers to work with paint suppliers; monitors supplier performance to ensure corporate quality and delivery goals are met; supports suppliers in continuous improvement to reduce costs and defects of their commodities on our products; approves supplier parts for trials and launch
- Manages, confirms, and controls the budget of one engineering and three maintenance groups within Paint plant for current paint related programs and new model development; ensures department adherence to the approved budget. Manages a staff of engineers, Section Managers, and maintenance Area Managers; provides direction and responsibilities for employees within Paint plant; facilitates engineer development through the ECL program; reviews performance appraisals for employees to determine responsibilities and direction for continued engineering growth; manages contract maintenance service groups for Paint plant
- Ensures employee compliance with company approved safety guidelines; includes Lock Out-Tag Out standards, robot safety, and fire prevention; reviews employee injuries to ensure appropriate countermeasures are taken to eliminate future injuries. Management Accountabilities
- Has subordinate managers (not supervisors) and/or senior level individual contributors or contractors. Manages employees by establishing annual performance goals, allocating resources, assessing annual performance, and determining individual merit, incentive and/or promotional increases
- Supervises and provides leadership, coaching, guidance, training, career counseling and staff development, interviews and selects employees; recommends merit increases, transfers and promotions; counsels and disciplines employees as necessary; recommends termination when appropriate; and monitors attendance of subordinates. As necessary, performs other related duties of which the above are representative
- Excellent verbal and written communication, and motivational skills. Knowledge of Tennessee and Federal OSHA standards, ISO9002 quality guidelines, ISO14001 environmental guidelines
- Knowledge of Tennessee, Mississippi, and Federal environmental protection guidelines, robot safety guidelines, factory mutual insurance requirements, and product safety management rules
- Ten or more years of related experience at a professional level
20
Manager, Maintenance Resume Examples & Samples
- Reviews job orders to determine work priorities. Schedules repair, maintenance, and installation of machines, tools, and equipment to ensure continuous production operations
- Directs maintenance activities on utility systems to provide continuous supply of heat, electric power, gas, or air required for operations
- Develops preventive maintenance program in conjunction with engineering and maintenance staff
- Reviews production, quality control, and maintenance reports and statistics to plan and modify maintenance activities
- Confers with management, engineering, and quality control personnel to resolve maintenance problems and recommend measures to improve operations and conditions of machines and equipment
- Plans, develops, and implements new methods and procedures designed to improve operations, minimize operating costs, and effect greater utilization of labor and materials
- Directs training and indoctrination of workers to improve work performance and acquaint workers with company policies and procedures
- Prepares department budget and monitors expenditure of funds in budget
- 5 years progressive experience in Maintenance Management within heavy industrial manufacturing firm
21
Manager, Maintenance Resume Examples & Samples
- Assist in a Safe working environment within all SOWA maintenance shops
- Communicate with GM on costs of repairing and maintaining equipment
- Be involved with all decision making on purchases of parts (Market place)
- Create and back-up purchasing/create P.O.'s., includes Goods Receipting
- Provides current information on 2290 for proper tax and license
- Vehicle License and registrations, organizes emission testing
- Communicate costs vs. Monthly budget
- Ensure compliance with corporate policies, plant rules, environmental and safety procedures, and laws
- Coordinate with other departments to ensure completion of work orders, preventive maintenance, and proactive identification of equipment reliability issues
- Ensure all shop personnel are following CEMEX safety policies and procedures
- Assist in training of new mechanics
- Flag repairs with warranty potential and initiate warranty reimbursement
- Develops preventive maintenance program in conjunction with engineering and maintenance staff within AMG
- Manage the fleet of Heavy, Ready Mix and Aggregates Delivery equipment which includes timely completion of routine day to day maintenance, preventative maintenance which includes planning for and scheduling long term maintenance (engine, transmission, differential rebuilds) as well as a replacement schedule which supports each line of business, including disposal/selling of the types of equipment in the fleet
- Excellent communication and people interaction skills
- Ability to read and interpret documents and write routine reports
- Driver’s license required / Able to travel
- Ability to work all scheduled hours, including nights, weekends and overtime
- Knowledge of maintenance required and mechanical systems of Heavy Equipment used in Quarries/Pits including Loaders, Dozers, Haul Trucks, Excavators, Manlifts, Gradalls, Cranes and Service Vehicles and Pickups
- Knowledge of Equipment Market Values
- 1-5 years of progressive experience managing maintenance shop
22
Manager, Maintenance Resume Examples & Samples
- Performs preventative service and repairs of the conveyor systems, facility related building equipment, and forklift fleet. Purchase and maintains adequate inventory of all spare parts and necessary supplies to support properly all preventative initiatives or critical repairs
- Performs all duties related to facility improvements and capital projects. Providing cost justification and business case analysis to local and corporate business partners. Oversee all local projects both on a capital level and towards continuous improvement initiatives. Insure all projects are completed successfully and coordinated properly so that no negative effect is realized in our production environment
- Provide financial planning and support of all maintenance related expense categories such as, Fork Truck Repairs, Building services and expense, Conveyor upkeep, and Contractual Services. Maintain annual budgets and related dollars so that no over-spending is realized while continuously seeking out ways to reduce cost
- Maintains master record of safety manuals, procedures, Hazmat, and MSDS sheets. Coordinates with safety vendors and facility audits with internal and external personnel. Prepares follow-up reports and enforces the recommendations of safety audits. Coordinates emergency response plans and safety training for the leadership team, safety committee personnel and all building associates. Enforces safety rules and procedures are strictly followed both at the companies policy level and through all Federal and State programs
- Maintains a working knowledge of all building systems to include items such as: generators, fire alarms, sprinklers, electrical, plumbing, HVAC, Roofing systems, Outside Landscaping & Site Support, and lighting. Maintains a working knowledge of all equipment to include: lift trucks, conveyors, conveyor control systems, weighing devices, and any other material handling equipment. Support the appropriate scheduled testing of all emergency support systems that our part of the plants structure (Emergency Generators, Fire Pumps, Fire Detection & Alarms Systems & Emergency Lighting.)
- Oversees general clean-up and building maintenance including wall, door, cage repairs and storage handling. Maintains documentation on the building and all electrical/mechanical devices associated with the facility
- Oversees service contract maintenance work to ensure proper performance relating to equipment, the building and grounds
- Reports on maintenance operational repairs and expenditures control, analyzing facility workflow to include productivity, and quality
- Directs and develops Maintenance and Housekeeping staff members while maintaining a leadership role in the facility. Insure all members of the team remain productive and are provided daily directives so that all projects or daily responsibilities are carried out effectively and with positive support of the local team
- Routine communication and interactions with other LC Maintenance Managers to standardize purchases, procedures, technology, and to re apply best practices. Meets attendance and punctuality standards.*Performs additional duties as assigned *Meets attendance and punctuality standards
- Able to coach others in the development of their skills. Able to avoid win/loss situations and ensure productive resolutions of conflict
- Able to transport up to 50 lbs. Able to express ideas clearly and convey necessary information
- Able to facilitate group interactions. Able to identify areas of risk/concern in area of responsibility
- Able to respond to common inquiries from regulatory agencies or members of the business community. Able to set high short/long-term goals/standards of performance for self, subordinates, and others
- Able to think strategically and tactically. Able to negotiate skillfully, promote/sell ideas persuasively, and close transactions with mutually beneficial results. Knowledge and/or expertise in related area of responsibility. Knowledge of occupational hazards of the trade and necessary safety precautions. Possesses strong leadership skills with a willingness to lead, create new ideas, and be assertive. Possesses strong organizational and time management skills, driving tasks to completion
- Able to use relevant computer system applications (which may include spreadsheets, word processors, databases, etc) at an intermediate level.* Proficiency with Excel, Word, PowerPoint, Visio, AutoCAD preferred. Strong knowledge in the following areas: Mechanical, electrical, and motor controls & Logic; Conveyor systems and operations; HVAC, electrical, mechanical, and plumbing maintenance
- Financial acumen to include ROI analyses necessary. Project management skills critical
- Able to maintain confidentiality of senstitive information
23
Manager Maintenance Resume Examples & Samples
- Supervises Technical Representative(s), and/or Line Maintenance Supervisor(s) as assigned
- Coordinates personnel schedules to provide adequate manpower coverage as needed to support of aircraft maintenance operations
- Ensures the safe and efficient maintenance of company aircraft within their station / geographic area, in accordance with company policies, procedures and regulatory requirements
- Responsible for managing, coordinating and providing oversight for contract line maintenance in their station / geographic area as assigned
- Ensures personnel under their supervision are trained and qualified in accordance with GMM policies and procedures
- Monitors the training, qualifications and level of proficiency for maintenance personnel at assigned station(s) / geographic area
- Monitors Flight Schedules and fleet status to ensure best use of resources, ground time and aircraft routing
- Coordinates line maintenance requirements with MCC, Workload Planning, Materials, Quality Control, and A/C Planning Departments
- Maintains surveillance of line maintenance activity at assigned station(s) / geographic area
- Provides resources and technical support as necessary in cases of major mechanical problems or AOG situations
- Improve efficiency and reliability by identifying recurring problems and recommending changes in procedures
- Responsible for coordinating the timely repair of deferred maintenance items on aircraft transiting assigned station(s) and/or geographic area
- Ensures shift turnover and work interruption procedures are followed to ensure incomplete maintenance work is completed before an aircraft is returned to service
- Responsible for ensuring timely return of correct and accurate aircraft maintenance log pages to HDQ
- Coordinates with MCC for maintenance and aircraft status information
- Monitors mechanical problems, Aircraft and Popwerplant performance. Repeat Item and Oil Watch Programs
- Formulates corrective action plans for mechanical problems and deferred maintenance items in coordination with MCC
- Maintains communication with Regional Manager to ensure cost effective application
- Ensures timely entry of log page discrepancies and parts changes in TRAX
- Ensures personnel in their assigned station(s) / geographic areas are versed in the use of the TRAX system
- Monitors line station spare engine status and engine change kits
- Maintains liaison with Ground Operations and Flight Operations to ensure safe and dependable operations
- Enforces safety procedures and practices outlined in company manuals and industry standards
- Performs duties and responsibilities at field locations away from home base as assigned
- Flies on company aircraft as assigned to support aircraft operations around the world
- Performs self-audits of station(s) / geographic area as needed
- Develops and manages station(s) / geographic area budget(s)
- Must hold a current and valid FAA Mechanic Certificate with Airframe and Powerplant ratings
- Must maintain Atlas Air qualification and authorization for Airworthiness Release
- Experience on 747/767 aircraft or equivalent wide body aircraft preferred
24
Manager, Maintenance & Systems Resume Examples & Samples
- Site voice & data networks
- Site meeting rooms and AV/VC equipment
- IT & HSSE responsibilities not already covered by IT&S
- Accountable for budgets assigned looking to make efficiency gains wherever possible
- Responsible for the assessment and approval of related risk assessments within the department
- Responsible for managing support to the Projects team
- Continuous improvement on all of the above
- Degree/HND or equivalent in a scientific/engineering or related discipline
- Excellent interpersonal skills are desired
- Strong negotiation/influencing skills are desired
- Motivated, flexible and enthusiastic person with a desire to meet or exceed customer expectations and requirements
- High level knowledge of IT skills
- Required to have relevant experience in maintenance, building services, engineering or related field
- You will have the presence and credibility to motivate your team to achieve safety, cost, quality and delivery targets
- Experience in the following areas would be beneficial
- Local planning and HSE rules and regulations
- Working in a technology environment
- HSSE Behaviour & Leadership: Basic Application
- Project Management: Skilful Application
- Quality Systems & Standards: Basic Application
25
Manager Maintenance Resume Examples & Samples
- Champion the Plant’s “High Performance maintenance Plan.”
- Develop and maintain a sustainable system for the training, evaluation, and development of technicians to meet the plant’s needs, to include providing regular performance feedback
- Develop and maintain a sustainable system (work flow) that identifies work, plans jobs, schedules jobs, executes, audits, and continuously improves the quality and performance of the work being completed
- Develop and maintain a sustainable system that prioritizes the plant’s Equipment, and develops and updates Failure Defense Plans
- Coordinate with production and others on new products and upgrades
- Support and drive Process Improvement, Employee Involvement, and Safety
- Supervise internal and external personnel to insure maintenance is performed correctly and in a timely manner
- Analyze maintenance problems and devise solutions to improve plant production, reduce downtime, prevent repeat failures and/or increase the time between scheduled preventative maintenance
- Complete administrative tasks such as budgeting and reporting
- Develop and implement Maintenance department procedures
- Oversee and manage maintenance teammates
- Inspect the plant’s electrical and hydraulic systems for functionality
- Plan and oversee all repair and installation activities
- Monitor equipment inventory and place orders as necessary
- Monitor and control the Maintenance budget
- Manage relationships with plant contractors
- Maintain Maintenance log
- Ensure Maintenance department compliance with health and safety regulations
- Allen Bradley Drives and PLC’s
- PLC Programming
- Control Loops
- Sensors (temperature, pressure, proximity, limit, laser)
- Wonderware SCADA Interface
- Electric Motors
- 480, Three Phase Power
- Wiring Diagrams
- Fluid Pumps and Pump Curves
- Bearings
- Welding
- Laser Alignment
- Vibration Analysis
- HVAC
- Chillers
- Natural Gas Burners
- Variable Frequency Drives
- Health and Safety Regulations including Arc Flash
- Reliability and PDM Practices
- Lubrication
26
Manager Maintenance Resume Examples & Samples
- Initiate, implement and manage the plant maintenance program based on best practices, with an emphasis on preventative / predictive maintenance
- Monitor the use and inventories of spare parts, maintenance supplies and equipment and initiate reordering when necessary
- Maintain and repair maintenance shop equipment, fuel pumps, filter system, meters and hoses, etc
- Responsible for repairs on mobile equipment, including dozers, loaders, locomotives and welders
- Responsible for maintaining cleanliness in the maintenance shop
- Responsible for coordinating repairs to be conducted in-house and/or coordinating outside vendors
- Responsible for maintaining budget for repairs, tracking repairs and obtaining quotes for work to be performed
- Maintain a computerized maintenance management system for tracking work orders, spare parts and maintenance history of plant equipment
- Oversee all contractor work on site to ensure contractors comply with facility standards and procedures
- Repond to unplanned operational and maintenance events
- Plan and budget maintenance activities to work within the O&M monthly budget
- Demonstrate continuous effort to improve operations, decrease turnaround times and streamline work process
- Diagnose operational problems and recommend corrective action
- Prepare reports, analyze data and make recommendations for improvement of equipment operations and solving maintenance-related problems
- Supervise maintenance personnel
- Ensure maintenance personnel are properly trained and equipped so that the maintenance program can be accomplished in a safe, timely and cost-effective manner
- Establish preventative maintenance service programs, procedures and record systems in order to audit he performance of the services
- Develop and maintain a program for efficient production
- Provide instructions and procedures to ensure the continued usefullness of equipment
- Provide cost advice pertaining to facility equipment related to the short and long range needs of the business
- Assure compliance with all Federal, State and Local ordinances, regulations and codes
- Coordinate and integrate with other plant function areas to ensure necessary support
- Recommend improvement in equipment or methods
- Review the operation of facility equipment constantly to minimize unplanned downtime, anticipate problems in a timely manner and identify opportunities for improvement
- Track, analyze and improve key maintenance parameters, such as asset utilization, maintenance cost PM complaince, schedule compliance, etc
- Direct, matinain and enforce the safety program for the maintenance department
- Communicate directly with Operations to coordinate maintenance and repair work
- Three years prior supervisory experience
- Knowledge of safety requirements
- Previous project management experience
- Must possess understanding of bulk handling operations / equipment
- Experience in diesel engine repair
- Experience performing maintenance on bull dozers, conveyors,excavators, front end loaders, cranes, skid steers, sweeper trucks, maintenance trucks, fork lifts, etc
- Must be able to understand the needs of the business unit for which development work is being performed
- Intermediate to advanced proficiency level in Microsoft Office applications including, but not limited to Outlook, Word, and Excel
- Exceptional verbal and written communication skills including, but not limited to, the ability to present ideas, proposals and results to business segment leaders
- Ability to organize and prioritize daily work, including tracking and managing small projects to see projects to completion while maintaining strict confidentiality as necessary
- Must be able to successfully and simultaneously manage multiple tasks and work with minimal direct supervision
- Must be able to work with a team, take directions from supervisors, prioritize work schedules, focus attention on details and follow work rules
27
Manager, Maintenance Resume Examples & Samples
- Develops programs, procedures and practices to encourage employees to work safety in an environmentally responsible manner to achieve quality results at acceptable cost levels. - Participates in safety, health, and environmental continuous improvement initiatives. - Prepares budgets and monitors expenses - Plans, coordinates and oversees annual plant shutdown activities. - Provides technical support for maintenance functions for central maintenance - Manages the Mechanical Integrity Program and the Preventive Maintenance Program pertaining to process safety and reliability. - Provides advisory support to the plant-engineering group. - Maintains plant engineering standards and compliance. - Drives the cultural changes necessary for the organization - Resolves personnel conflicts and ensures customer satisfaction. - Develops systems and uses applicable tools to improve understanding of maintenance costs and utility measures relative to overall goals of reliability - Oversees the daily operation of the utilities systems for the site. - Inspects and troubleshoots equipment as needed. - Manages engineering stores functions to properly support plant needs, including maintenance material and contracting needs, process material needs, raw material purchasing, and physical inventory
- Bachelor’s degree required. Equivalent amount of related work experience may be considered in lieu of degree
- 10years experience required in maintenance and utility management, including CMMS, craft supervision, budgeting and capital control, and utility management to include a minimum of 3-5 years of prior management/supervisory/lead experience in a manufacturing environment
- Demonstrated ability in planning, organizing, and leading a team
- Must possess a balance of technical, human relations and conceptual skills required to achieve results through subordinate supervision
- Requires prior knowledge of process safety and environmental compliance in a manufacturing environment
- Excellent communication, organizational, time management and interpersonal skills
- Ability to interact with personnel at all organizational levels
- Proven expertise in PLC troubleshooting, pneumatic, instrumentation and mechanical areas
- Competent PC (MS Office and Windows) computer skills
- Experience in computers, networking and IT systems highly preferred. *LI-CB1
28
Area Manager Maintenance Resume Examples & Samples
- 2 or more years Industrial Warehouse maintenance experience
- Both Bachelor's Degree in Business, Logistics, or related field; AND 2 years maintenance experience including 1 year maintenance related supervisory experience
- RETA Certified Industrial Refrigeration Operator (CIRO) certfication
29
Qr-manager Maintenance Resume Examples & Samples
- Expert minimum 8 years of job -related experience required
- Practical and technical knowledge of electrical or refrigeration systems
- Managerial skills- Ability to delegate work, set clear direction and manage workflow. Strong mentoring and coaching skills. Ability to train and develop subordinate's skills. Ability to foster teamwork among team members
30
Manager Maintenance, Northampton Resume Examples & Samples
- Accountable to Plant Manager for achieving manufacturing facility operatives as top manufacturing person
- Responsible for production, operational excellence and engineering
- Develop and execute 1yr and 3yr business plans supporting national/regional/local objectives Including the development & implementation of strategies, processes & programs
- Motivate, direct, coach and develop a diverse, high performing leadership team to meet established goals and build organizational capability
- Effectively translate plant goals and objectives to all levels of the organization ensuring alignment on relevant performance data
- Routinely review business results with plant personnel to maximize supply chain performance
- Foster an environment that supports an engaged safety culture
- Develop a culture that embraces the tenets of operational excellence
- Sustain a consistent, long-term vision through continuous process improvement
- Adopt and share best ideas inside and outside the company
- Demonstrate behaviors needed for effective implementation of change
- Ensure manufacturing processes are compliant with company specifications and meet customer expectations
- Satisfy the needs and service requirements of the internal and external customers
- Ensure compliance to company and regulatory policies
- Represent the company and its interests in the community while remaining environmentally responsible in all efforts
31
R&D Manager Maintenance & Expansion Hygiene Personal Resume Examples & Samples
- Lead and manage one R&D ME team, based in the same location, accountable for providing R&D support to the product categories of responsibility, enabling protection and growth of the existing business as well as delivery of cost saving programs to increase the profitability of existing products
- Identify and recommend key strategic opportunities within own area of responsibility and share with relevant R&D teams / functions
- Manage and supervise direct reports and temporary employees with responsibility for ensuring their development
- Educate local organizations (marketing, supply, etc.) on technology and product specifics
- Lead the delivery of local facility improvements, namely: offices and laboratories. Ensuring that a professional and compliant working environment is provided for the team
- Ensure that facilities and processes are operated with a prioritization to Health and Safety and also to the required standards of good manufacturing and laboratory practice. Ensure that all work performed is subject to the scrutiny of internal and external auditors
- Support planning and management of an assigned budget
32
Manager Maintenance, Northampton Resume Examples & Samples
- Develops and executes 1yr and 3 yr business plans supporting national/regional/local (TPM) Total Productive Manufacturing objectives including the development & implementation of strategies, processes & programs
- Oversees and assists in the establishment, analysis, and submission of yearly departmental budgets
- Creates and adheres to a work order planning and scheduling process; Ensure service calls and machinery repairs are completed in a timely manner
- Establishes and maintains a SOX-compliant stockroom operation that provides repair parts for critical process equipment as well as necessary consumables for the plant
- 10 yrs. of increasing levels of supervisory roles of people & processes required
- Demonstrated ability to support a long term maintenance plan showing year over year improvement in Reliability, Maintenance KPIs and maintenance Cost
- Demonstrated ability to collaborate cross-functionally and coordinate efforts around process improvement
- Working knowledge of national, state, and local regulatory requirements in the areas of food safety, safety, environment and emergency management
- Working knowledge of basic elements of Good Manufacturing Practices and manufacturing management
- Working knowledge of key business drivers used to gauge the effectiveness and performance of an internal group or supplier
- Strong experience and working knowledge of plant maintenance software, SAP preferred
33
Manager Maintenance Resume Examples & Samples
- Coordinate and align scheduled and unscheduled maintenance activities, develop daily maintenance schedules and forecasts and maintain detail knowledge of maintenance statuses
- Ensures all maintenance performed is in accordance with current Federal Aviation Administration guidelines, Federal Administration approved data, Company Policy and Procedures Manuals and Standard Operating Procedures (SOPs)
- Work with outside vendors, e.g. NBAA, NBAA Schedulers & Dispatchers Advisory, ARINC and now FOS to ensure CSX is compliant and using best practice
- Ensures safety practices are followed by personnel while engaging and coaching for professional development
- Oversees and audits aircraft records and record keeping procedures
- Miscellaneous activities and responsibilities as assigned by manager
- 3 or more years of supervisory experience in Mechanics or Business Aircraft
- Airframe and Power Plant Certificates (A&P)
- 5 or more years of supervisory experience in Mechanics or Business Aircraft
- NBAA Certified Aviation Manager (CAM)
- Inspection Authorization (IA) Certificate
- Strong Microsoft Office skills (Word, Excel, Powerpoint)
- Organizational and prioritization skills
- Knowledge of Title 14 of the Code of Federal Aviation Regulations
34
District Manager Maintenance Division Resume Examples & Samples
- Client Service and Support
- Basic knowledge of personnel policies including hiring, interviewing and terminating
- Customer service experience and/or strong customer service focus
- Ability to effectively present information to clients face to face
- Basic knowledge of Excel and Word
35
Manager, Maintenance Systems Resume Examples & Samples
- Position is dedicated to building and managing a team responsible for development, implementation and management of applications, information systems, business processes and the reporting tools for optimally efficient and compliant support of assets, maintenance processes and workflows
- Work collaboratively with Production Maintenance, Manufacturing Operations, Production Services, MSAT, Quality, SHE and other functions. The expectation is to improve product quality, compliance, safety and reliability through the development of maintenance management programs thereby reducing the cost of goods sold
- Excellent interpersonal skills with a demonstrated commitment to teamwork and collaboration as well as ability to identify, align and influence stakeholders at varying levels of seniority
- Ability to identify links and connections between global and site strategies and activities as well as ability to multi-task amidst often aligning the needs to multiple stakeholder
- Expert-level mastery of communications competencies, paired with strategic acumen and strong execution skills
- Create an engaging and challenging environment for peers and direct reports
- Responsible for maintenance planning, master data management, spare parts management, engineering documentation, and supporting reliability initiatives
- Understand and drive equipment and process reliability, data accuracy, adherence to schedule throughout the organization
- Implement a sustainable long term vision of maintenance systems integration into Facilities, Utilities and Equipment
- Provide expertise in RCA, FRACAS, DMAIC, problem elimination, Kaizen, reliability centered maintenance and process improvement
- Collaborate with internal, network and external partners and service providers to ensure a strong culture of improvement
- Establish and enhance effective maintenance programs to promote maximum equipment availability, capacity, productivity, and elimination of discrepancies
- Manage analysis of maintenance data to identify trends in equipment and organizational performance that adversely affect efficiency, cost, quality, plant capacity, and production throughput. Manage recommendations on actions that can be taken to reverse adverse trends
- Manage participation in system criticality assessments, RCAs and FMEAs on equipment failures that affect product quality, equipment uptime and plant capacity
- Provide expertise in cGMP and Quality Policies and procedures
- Participate actively in team activities and advocate LEAN concepts and business process management
- Ensure integrity of data by developing robust data input and data analysis processes
- Establish and maintain trending results, quality metrics and KPI for maintenance activities to support benchmarking
- Provide site expertise in MRO best practices, technology /applications, and systems implementation
- Actively maintain an internal and external network of peers to ensure efficient idea sharing, best practices
36
Manager Maintenance Resume Examples & Samples
- Provide direction and support to supervisors and employees engaged in maintenance and warehousing work in support of company facilities that may include processing: fractionation, storage, compression, pumping and/or pipelines
- Ensure completion of routine preventive, predictive, and compliance maintenance work including documentation
- Ensure programs are effective and that key risks are identified and addressed
- Ensure compliance with laws, regulations and industry standards are maintained
- Design, implement and improve maintenance metrics of assets, including, but not limited to
- Experience with design, construction, operations and maintenance of company facilities that may include: processing, fractionation, storage, compression, pumping and/or pipelines
- Working knowledge of applicable OSHA/PSM, Industry Standards, Governmental and Environmental regulations and documentation requirements
- Working knowledge and understanding of pumps, compressors, piping, towers, heaters, pressure relief devices, mechanical integrity programs, instrumentation, electrical, and process control equipment and systems
- Experience with material failure and structural analysis and thorough knowledge of industry standards and governmental regulations
- Experience identifying, researching, evaluating and prioritizing operational problems or specific situations and determining appropriate action/response
- Experience researching and preparing, contracts, agreements, budgets and various reports, forms and correspondence
- Demonstrated ability to read and understand governmental regulations, references, journals, construction plans, blueprints, contracts, manuals, reports, specifications and correspondence and the use of that knowledge to develop and complete projects
- Demonstrated people skills to interact, negotiate, advise and communicate effectively
- Experience examining, testing and evaluating new products, materials and techniques
- Demonstrated ability to supervise, direct and/or delegate work assignments. Knowledge of personnel policies and procedures
- Experience interacting, advising, negotiating and communicating effectively
- Demonstrated ability to read and write fluently in English
37
Manager Maintenance Resume Examples & Samples
- Bachelor's degree in Engineering preferably (Mechanical, Electrical, Industrial)
- 10-12 years of relevant experience in Manufacturing, Ground Handling, Auto Mobile, Industries including at least 5 years in positions of progressively increasing managerial responsibilities
- Knowledge and experience in a maintenance management system
- Advanced Budget and Cost Control Knowledge
- Advanced IT and Computer Literacy
- Advanced Management Skills
- Advanced Safety Awareness
- Advanced Communication Skills
- Advanced Negotiation Skills
38
Manager Maintenance Resume Examples & Samples
- Ensure that the factory operates at the highest possible efficiency at the lowest cost, by being a leader the sustainable cost advantage strategy, and proper selection, installation, maintenance, and modification of all equipment/machinery
- Direct maintenance of equipment and plant infrastructure to meet production requirements and minimize downtime
- Develop and execute capital projects to meet schedules and budgets
- Lead continuous technical improvement of the facility, equipment, and production systems
- Manage the maintenance supervisors and personnel; effectively delegate work assignments and develop the knowledge, skills, and abilities of team members
- Ensure adherence to safety, food safety, and environmental regulations and practices
- Proactively support internal and external customers (i.e., Operations, Quality, Safety, Human Resources, etc.)
- Attend required plant training programs per the training schedule. Ensure personnel are properly trained. Develop and deliver selected training programs as required
- Manage maintenance supervisors, who in turn supervise maintenance employees
- Responsible for the overall direction, coordination, and evaluation of the department
- Carry out management responsibilities in accordance with the organization’s policies and applicable laws. Responsibilities include interviewing, hiring, and training; planning, assigning, and directing work; appraising performance; coaching, recognizing, and disciplining employees; and addressing complaints and resolving problems
- Maintain and coordinate an ongoing development program for the maintenance personnel to enhance their skills, performance, and succession opportunities
- 5 to 10 years of engineering and / or maintenance in frozen food manufacturing
- 5 years of supervising people
- Experience managing projects, budgets, and a CMMS program
39
Manager Maintenance Resume Examples & Samples
- Responsible for plant maintenance including facilities, utilities and operations to reduce downtime and assure peak plant efficiencies. Will direct capital engineering design and projects to completion and work with appropriate vendors. This position will also have direct responsibility for the Maintenance team and their performance inconjunction with the Plant Business Unit Managers
- Promote safety throughout the entire maintenance organization
- Responsible for all maintenance department metrics
- Lead, manage and direct all activities for ConAgra Performance System Planned Maintenance Pillar
- Prepare and operate within established maintenance operating budget and monitor departmental expenditures
- Assists with planning and cost estimates for annual and longer term capital budgets
- Responsible for executing the capital plan to include all engineering design and project management, working with both internal and external resources
- Be acquainted with local/state/federal environmental regulations and ensure compliance with all operational permits. Directs all aspects of building operations including maintenance, repairs, and renovations
- Establish criteria for assessing the quality of work performed by employees and contractors
- Supervise the completion of work through review of reports, frequent site inspections and conferences with operations and vendors regarding electrical & plumbing equipment, HVAC systems, electric motors, ventilating fans, air conditioning and electrical control units
- Investigate the condition of buildings, equipment and grounds, and recommends improvements in the facilities to ensure that needs are met
- Bachelor’s degree in Industrial Engineering or related technical field preferred
- Minimum five years’ experience in food plant maintenance
- Must be computer literate; experienced in using computer software applications such as CAD, Microsoft Excel, Word, PowerPoint, MS Project Management, etc
- Must have complete understanding of PLC and logic controls for high speed operating equipment
- Prior experience using production environment SAP preferred
- Basic accounting knowledge preferred
- Broad knowledge & experience in project management & facilities administration with demonstrated ability to manage projects and personnel
- Excellent written and verbal communication skills along with superb time management and project scheduling skills
- Must have a proven track record of successfully managing the construction of
- Large, complex projects
- Comprehensive information on construction processes, trade practices, standards, building codes & regulations
- Excellent administrative and follow up skills to achieve successful maintenance and repair programs
- Ability to lead teams and achieve results through resources
40
Manager Maintenance Resume Examples & Samples
- Bachelor's degree in Engineering or related field and 5 years’ experience in a manufacturing environment; or equivalent combination of education and experience
- Possesses advanced technical skills in the mechanical / electrical fields (e.g. PLCs, instrumentation, mechanical engineering, etc.) and is able to lead resource planning efforts in a large manufacturing environment
- Thorough knowledge of world-class maintenance management systems, work order processes, preventive/predictive maintenance, TPM, etc
- High level of organizational planning, teamwork, analytical reasoning skills
- Knowledge of Microsoft Office Suite of and the Internet. Well versed in the use of SAP
- Strong interpersonal and technical skills required; presentation skills preferred
- May be required to work long hours and weekends
- Occasionally lift and/or move up to 50 pounds
- Specific vision abilities required include close vision, distance vision and ability to adjust focus
- Frequently required to stand; walk; use hands to handle, or feel; reach with hands and arms; stoop, kneel, crouch, or crawl and talk or hear
- The plant environment will include wet or humid conditions (non-weather related), extreme cold and heat (non-weather related), working near moving mechanical parts, exposure to fumes or airborne particles, and chemicals
- Noise level in the work environment is usually moderate but can be loud when in the production area
41
Manager, Maintenance & Reliability Resume Examples & Samples
- Monitor and assure compliance to Good Manufacturing Practices (GMP) and adherence to defined procedures
- 0 to 5% travel
- Must possess excellent interpersonal, communication and problem solving skills
- Must demonstrate a desire and ability to lead other people
- Must be familiar with TPM Techniques within day to day operations in order to reduce downtime
- Must possess a strong use of continuous Improvement methodologies, to align reliability efforts with, and support existing programs to meet or exceed our Quality, Delivery and Cost performance expectation
- Must be able to apply root cause analysis for problem solving
- Well versed in equipment automation, PLC Logic Control, Robotics, Servo Drive Systems, CMMS, MRO Storeroom Management and Automated Packaging Designs
42
Manager, Maintenance Resume Examples & Samples
- Collaborates directly with Manufacturing and Quality to ensure sustainable operations
- Contribute to the development of manufacturing priorities, long term strategies and goals
- Establish department goals in support of manufacturing and site priorities
- Ensure compliance with FDA, OSHA, and other regulatory agencies as appropriate
- In collaboration with Human Resources, oversees and directs all performance management, training, development, job descriptions, and safety procedures for all Maintenance personnel
- Support site activities and provide technical expertise and guidance
- Supervise and direct contract personnel and outside vendors in the performance of contracted services
- Develops and oversees the preventative maintenance program for the manufacturing equipment. Reviews the program and implements changes for improving the efficiencies of the maintenance department
- Coordinates and supports plant shutdowns activities to include preventative maintenance and equipment modifications
- Sets goals for the unit in achieving higher service level and optimum efficiency of the manufacturing equipment
- Monitors maintenance processes for compliance with the Company, FDA, OSHA, and GMP regulations
- Sets priorities for the maintenance department in accordance with the plant priorities
- Examines monthly expenses and approves monthly cost forecasts. Prepares annual expense budget for maintenance
- Collaborates with other groups (Production, Engineering, Quality, Supply Chain, and Controlling) in process, quality, and cost improvement projects as well as in the resolution of major issues
- Approves maintenance projects and ensures the availability of resources for timely completion
- Interfaces with outside vendors for equipment purchases. Reviews technical data on equipment to be used for modification or replacement
- Develops downtime tracking programs and approves changes to maintenance methods and/or projects to reduce equipment downtime
- Ensures that all areas and equipment are maintained in good housekeeping condition
- Knowledge of GMPs both basic and unique to the department’s specialty(s) area
- Software packages such as MS Office
- Motivation and team building skills
- Ability to supervise all levels of personnel
- Budgeting and budget management
- Project prioritization
- Communication skills, both verbal and written, commensurable with dealing with senior level management
- Ability to evaluate competence of personnel to perform work within the individual’s specialty(s) area
- Preparation of RCIs, and RSEs
- BS degree in an Engineering discipline with 5 - 8 years experience in Maintenance or Engineering position with at least 3 years demonstrated successful performance/experience in an applicable Maintenance management position
43
Manager Maintenance Resume Examples & Samples
- Deliver superior health, safety and environmental outcomes through the promotion, utilisation and continual improvement of business and site based systems and processes
- Realise budgeted equipment performance commitments in a safe and cost efficient manner
- Focus on continual improvement, efficiency and value driven performance management
- Promote our diverse work environment where our employees are engaged and empowered in contributing to the success of our operation and business
- Identify, build and develop the Maintenance talent pipeline, with robust succession plans in place for key roles
- Continue to leverage of the established and highly effective cross-departmental relationships within our operation
44
Manager, Maintenance Resume Examples & Samples
- Supervise and manage hourly Production maintenance mechanics to accomplish daily requirements
- Perform set-ups or product change-overs of equipment when necessary to support the daily Production schedule
- Troubleshoot and repair Production packaging lines in an efficient and safe manner as needed to minimize downtime
- Maintain an equipment preventative and predictive maintenance program for both Production filling and packaging equipment and Bulk Manufacturing batching equipment. Complete necessary documentation to ensure regulatory compliance
- Oversee the ordering and stocking of basic replacement parts and tooling and maintain proper inventory levels for critical and spare parts
- Actively contribute to the success and execution of a total productive maintenance (TPM) program
- Support efforts to measure and improve OEE (Overall Equipment Effectiveness) for all equipment
- Provide effective communication with peers and management, ensure company goals and objectives are supported
- Assist in improving equipment change-over and set-up sheet instructions for all unique products and filling equipment
- Manage department budget and endeavor to reduce costs through improved methods or procedures
- Provide and implement improvements in efficiency for both personnel and equipment
- Provide coaching to mechanics to improve their efficiencies and communication skills. Resolve and negotiate conflicts when necessary
- Perform skills assessments of mechanical workforce and determine where gaps or opportunities for improvement exist, and develop and implement plan to close those gaps
- Maintain a clean and orderly work environment as part of company 6S program at all times
- Facilitate and support a safe working environment and maintain all safety certifications and training requirements
- High School diploma with trade school, vocational school, or apprentice program training required
- Bachelor’s degree in engineering from a four-year college or university preferred
- 10+ years in a cosmetic, personal care, pharmaceutical, food industry, or related field required
- A minimum of 5 years of supervisory experience is required; experience at the Manager level is preferred
- Experience with an MMS required
- Must have strong mechanical background for mechanical repair, with advanced knowledge of mechanical, pneumatic, or hydraulic systems and equipment
- Working knowledge for electrical systems troubleshooting required
- Working knowledge for PLC programming and troubleshooting preferred
- Working knowledge of basic machine shop equipment required
- Ability to read and interpret basic engineering drawings and schematics required
- Proficiency with standard MS Windows software (Word, Excel)
- Excellent verbal, written, and interpersonal skills required
45
Manager Maintenance Excellence Resume Examples & Samples
- Industrial or civil engineer
- 5 years experience in pharmaceutical industries and in GMP environment
- Strong leadership of technical team. Able to motivate people. Good communicator. Able to delegate
- Expertise in maintenance and improvement of pharmaceutical facilities (HVAC, clean fluids, electricity, automation)
- Knowledge of the regulatory environment (international norms)
- English is required, French is a must
- Analyze reliability of equipment and improve through adjustments with maintenance team or define project requirement and follow project implementation with project team
- Define reliability objectives in line with EHS, Quality standards, production plans and cost effectiveness
- Participates to external audits by answering to questions
- Brings and pilots corrective actions for problems “de retard et d’en cours”
- Resolves audit actions and makes sure of the application in all teams
- Ensures consistency between procedures, training programs, validation methods, calibration equipment’s and requalification files
- Maintains good maintenance practices by updating our procedures and the check-lists associated to them. Ensures redaction, training and follow-up of the procedures
- Makes sure of the qualitative reliability of the qualification files
- Transfers to the requalification teams the knowledge acquired during the project
- Pilots improvement projects in Technical Services
- Brings an organizational and technical support to internal customers
46
Manager, Maintenance & Metrology Resume Examples & Samples
- Supervises, plans and schedules cGMP Building Maintenance, Process equipment maintenance, Metrology, Housekeeping, landscaping, and Pest control services at three sites around the Millsboro area
- Understands customer (Internal & External) needs to effectively tailor maintenance solutions to required service level
- Supports and maintains maintenance and metrology records to ensure strategic improvement decisions are considered
- Relays best practices to various corporate and site groups ensure equipment performance and reliability
- Oversees Maintenance COE (Center of Excellence) action plans and routinely evaluates status and makes adjustments as needed
- Ensures maintenance and metrology processes and controls meet quality and regulatory requirements
- Ensure top talent and potential successors are appropriately challenged and developed
- Coach maintenance teams on best practices, MPS principles and Merck leadership behaviors
- Provide training to personnel to stay current with all regulatory agencies and corporate policies
- Ensure proper safety procedures, standard operation procedures and maintenance techniques are followed
- A minimum of 8 years’ industry experience as a project engineer, operations supervisor, or technical lead in a Pharmaceutical and/or Biologic Production setting
- 3 year’s management and or lead role experience (people/budget/organization/results)
- Working knowledge and experience with use and management of SAP Plant Maintenance Computerized Maintenance Management System
- Proficiency in computer systems and applications including but not limited to: AutoCad, Microsoft Project, Microsoft Office (Word, Excel and Outlook), SAP Procurement
- Must be able to lead in a team-based empowered culture
- Ability to work independently and effectively with peers; display strong interpersonal and organizational skills
- Schedule, organize and supervise facility shutdowns
47
Manager Maintenance Excellence Resume Examples & Samples
- Create a motivating environment and organisational structure for Installation Changes, Maintenance Planning and Competence Management, integrated with the entire Maintenance & Reliability department and linked with the right partners in Operations and Project Engineering. Improve the processes for Installation Changes, Maintenance Planning and Competence Management and the key Maintenance processes for them to be lean and effective, for them to incorporate the next steps in safety and to stimulate a pro-active mindset
- Define and implement a long term vision for all electrical installations and automation and lay the foundation for similar exercises on existing, critical installations
- Make sure Umicore standards meet maintenance needs and safeguard their use in- and outside the Maintenance & Reliability department
- Drive the Maintenance & Reliability department, as a member of the management team, to contribute to the CSM Olen vision of operational excellence, EHS compliant, lean and smart, new and reinforcing current business
- Manages the department
- Determines the department vision and translates them in clear objectives, in line with the vision and objectives of the Maintenance & Reliability Department and CSM Olen
- Create, monitors and acts on the budgets
- Drives operational excellence within the Maintenance & Reliability department by analysing, optimizing and improving all key processes taking into account CSM Olen objectives, lean principles and people aspects. Implements these improvements by acting as a strong change manager to persuade employees, peers and management to take over the new way of working
- Takes care of his employees
- Makes sure the standards meet the maintenance needs
- Takes final decisions in discussions, together with his counterpart in Engineering
- Rolls out all standards within Maintenance & Reliability
- Safeguards the use of the standards throughout CSM Olen
- Allows exceptions to the standard, together with his counterpart in Engineering
- Represents Maintenance & Reliability in projects outside the department (HR, P&T, …)
48
Manager Maintenance Resume Examples & Samples
- Manage project engineer to improve/develop maintenance processes
- Manages personnel involved with maintenance, repair and servicing of plant facility, equipment, and grounds
- Monitors and tracks all maintenance costs including, but not limited to, spares use by functional area, utilities, down time, waste, fuel and emissions
- Ensures appropriate level of spare parts inventory in conjunction with Purchasing Manager. Manages weekly reporting on spares cost by plant functional area, number of zero item spares, as well as the spares cost of planned vs. reactive maintenance
- Manages maintenance MRO stores, ensures four full inventory cycle counts per annum
- Ensures calibration of all equipment
- Develops and directs preventative maintenance programs for all plant and ancillary equipment and researches ways to run equipment more efficiently and reduce equipment downtime
- Develops weekly maintenance management reports including but not limited to, percentage of actual maintenance activities completed vs. planned, total number of reactive maintenance activities. Total equipment breakdown downtime hours
- Ensures training as required to maintain necessary technical and mechanical skills
- Ensures safe and healthful working conditions and an organized work environment and conducts regular safety meetings
- Requires a high school diploma or equivalent with a bachelor’s degree preferred. Knowledge of industrial maintenance procedures and construction preferred
- At least 5 - 8 years of experience in electrical, mechanical, pneumatic, hydraulic and/or electronic equipment and systems
- At least 3 years of supervisory/management experience
49
Manager.maintenance Resume Examples & Samples
- Lead a team of approximately 50 skilled craft and technical personnel in a unionize environment
- Lead the maintenance team to zero injuries and zero major incidents
- Observe employee work practices and equipment, see that safety policies are followed at all times
- Remedy unsafe conditions and conduct safety meetings each day with department personnel
- Responsible for the proper maintenance of plant and facilities, including janitorial, Stores, DCS, building maintenance, etc
- Oversee and continuously improve the plant mechanical integrity program
- Oversee maintenance personnel in the performance of their duties
- Work closely with production personnel so that proper scheduling of maintenance work meets the demands of maintaining an efficient operation
- Train and develop maintenance personnel in the safest and most economical methods of doing their work and to continuously improve their skills
- Define maintenance objectives and develop departmental budget to attain objectives
- Measure, monitor, track and report Key Performance Indicators (KPIs) to ensure attainment of maintenance objectives. Use KPI’s to set and achieve Improvement objectives
- Remedy conduct that may impair production, efficiency, morale or safety performance
- Work with senior leads to schedule work and assign personnel as required
- Implement preventative / predictive maintenance through maintenance software for the issuance and carrying out of work orders
- Maintain equipment repair records, as well as preventative maintenance records
- Oversee the maintenance of all Policies and Procedures pertaining to the Maintenance Department
- Leadership. Must be self-motivated, organized, trustworthy, empathetic, and optimistic. Required leadership skills include setting goals, establishing priorities, and assessing performance. Critical to success is the ability to inspire and empower the maintenance team, effectively assign work duties, and provide the necessary resources to the team
- Interpersonal Relationships. An essential skill is the ability to communicate clearly and concisely to all stakeholders. Good interpersonal skills require active listening, honest and frequent feedback, and a positive attitude
- Problem Solving. Strong technical and problem solving skill for mechanical design, root cause failure analysis, and maintenance. Success requires critical thinking skills including the ability to make clear and reasoned judgements, the ability to process a large amount of information quickly, and making timely, effective decisions
- People Development. The successful maintenance manager will work with team members to identify areas for improvement and will provide the requisite training and development. Team success will depend on the manager’s ability to share information, ideas and experiences to build a strong knowledge base
- Time Management. An essential skill is the ability to manage activities to efficiently accomplishing results rather than just getting stuff done. This skill requires the ability to plan daily activities, manage priorities, and eliminate non-value added activities
- Teamwork. Good motivational skills; ability to influence and manage change; ability to work well with Operations in a team environment. Must be able to recognize the different strengths in individual team members and foster a working environment that encourages collaborative team efforts
- Adaptability. The maintenance manager will be expected to drive positive change and must be open to new ideas, new ways of working and new technologies. Success will depend on the manager’s ability to learn new skills, adopt new technologies, and implement innovative solutions
50
Manager Maintenance Carpenterus Resume Examples & Samples
- Will be responsible for supervising daily staff activities and work assignments to ensure timely and satisfactory completion of work assignments and will liaise with other departments to resolve miscellaneous facility issues
- Will respond immediately to all facility emergencies and will provide direction and resources to engineering staff for timely resolution. Will provide communication with other departments and property executives as required during and after such events
- Will enforce all company and department policies with maintenance staff members including issuing discipline, and commendations when appropriate. Will provide assistance to all trades and crafts with routine work assignments as needed
- Responsible for other miscellaneous duties that may be assigned by senior management
- Will provide daily verbal and written shift & log reports to senior management
51
Manager, Maintenance Control Resume Examples & Samples
- Perform managerial responsibilities, such as hire/fire, disciplinary actions, performance management process, training and work assignments
- Responsible for the Customer Response Team, Maintenance Control Center (CRT MCC) in Hartford, CT, and the Mobile Trucks and all employees across the USA
- Working with the Customer Response Center, will be responsible for supporting AOGs activities in North America by having complete control and oversight of the truck operations
- Responsible for the department’s budget
- Implement/support initiatives to continuously raise the employees’ engagement by looking into best practices (work schedules, pay equity, tools etc.)
- Implement/support initiatives to continuously capture the support for AOGs from the Mobile Response Team to raise our revenues
- Coordinate with other functions that may have an impact on support AOGs (BAS, Engineering, Part Services, etc.)
- Conduct investigations on areas of concern related to the support & operations and implement corrective actions
- Prepares and monitors annual operating budgets to include operating expenses, facilities, supplies, outside services, personnel, training, capital expenses and reserves. Reports deviations from estimated expenditures and actual costs to management with explanations in accordance with company procedure
- You have Bachelor’s degree or equivalent in related field
- You have at least 12 years of experience in business or commercial aviation maintenance
- You have the ability to work outside of normal business hours depending on business needs
- You have the flexibility for regular travel, including internationally
- You hold an A&P License
- You have previous management experience - preferred
- You have Project Management experience - preferred
- You have prior experience with maintenance and operational control of Bombardier Products (Learjet, Challenger &/or Global) - preferred
- You have experience in liaising with local regulatory authorities & any other internal or external entities - preferred
52
Manager, Maintenance Services Resume Examples & Samples
- Provide daily supervision of maintenance staff. Lead or assist in interviewing and selection of maintenance staff. Monitor and encourage staff development through on-the-job and formal training and conduct annual performance evaluations. . Establish annual department goals. Assist maintenance staff on specific jobs to facilitate completion of the job and training of the employee
- Review, prioritize and assign projects and work requests and preventive maintenance tasks. Conduct regular inspections of facilities and equipment. Direct, maintain and enforce safety programs and ensure compliance with applicable regulations, requirements and buildings codes. Complete work orders and resolve maintenance related issues with little or no direction. Respond to campus emergencies
- Assist in the preparation of the annual capital budget. Prepare, justify and recommend annual operating budget for area of responsibility. Responsible for monitoring expenditures of the maintenance operating budget. Check invoices in accordance with established policy and procedure
53
Manager, Maintenance Management Resume Examples & Samples
- Manage a team of Maintenance Experts to ensure that fleets adhere to GATX’s maintenance profiles and inspections and repairs are performed consistently across the GATX North American maintenance network. This role will make sure their team monitors the progress of repairs to confirm the following
- High level of railcar technical and maintenance knowledge
- FRA, AAR and Billing Repair Card knowledge
- Excellent Computer skills (Word, Excel, Data Querying) required
54
Manager Maintenance Resume Examples & Samples
- Provide direction and support to supervisors and employees engaged in maintenance and warehousing work in support of company facilities that may include processing, fractionation, storage, compression, pumping and/or pipelines
- Ensure completion of routine preventive, predictive, and compliance maintenance work including documentation. Ensure the Maintenance group is engaged in driving Environmental, Health and Safety excellence. Ensure compliance with laws, regulations and industry standards. Ensure programs are effective and that key risks are identified and addressed
- Improve Maintenance metrics of assets, including
- Experience with design, construction, operations and maintenance of company facilities that may include: hydrocarbon processing, fractionation, storage, compression, pumping and/or pipelines
- Working knowledge and understanding of pumps, compressors, piping, pressure vessels, fired heaters, pressure relief devices, mechanical integrity programs, instrumentation, electrical, and process control equipment and systems
- Experience developing information and making presentations to groups an individuals