Quality Supervisor Resume Samples
4.8
(123 votes) for
Quality Supervisor Resume Samples
The Guide To Resume Tailoring
Guide the recruiter to the conclusion that you are the best candidate for the quality supervisor job. It’s actually very simple. Tailor your resume by picking relevant responsibilities from the examples below and then add your accomplishments. This way, you can position yourself in the best way to get hired.
Craft your perfect resume by picking job responsibilities written by professional recruiters
Pick from the thousands of curated job responsibilities used by the leading companies
Tailor your resume & cover letter with wording that best fits for each job you apply
Resume Builder
Create a Resume in Minutes with Professional Resume Templates
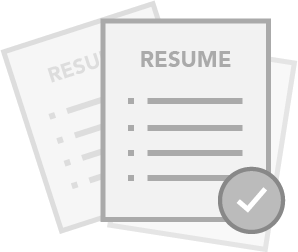
CHOOSE THE BEST TEMPLATE
- Choose from 15 Leading Templates. No need to think about design details.
USE PRE-WRITTEN BULLET POINTS
- Select from thousands of pre-written bullet points.
SAVE YOUR DOCUMENTS IN PDF FILES
- Instantly download in PDF format or share a custom link.
DE
D Ebert
Delpha
Ebert
2529 Garrison Oval
Detroit
MI
+1 (555) 409 9988
2529 Garrison Oval
Detroit
MI
Phone
p
+1 (555) 409 9988
Experience
Experience
New York, NY
Quality Supervisor
New York, NY
Stoltenberg-O'Reilly
New York, NY
Quality Supervisor
- Works with manufacturing operations to identify high scrap and rework areas and initiates investigations for establishing subsequent improvements
- Identifies and develops strategies, performance indicators and project improvement opportunities; manages documentation
- Works to identify high scrap and rework areas and initiates investigations for establishing subsequent improvements
- Manage and coach inspector; ensure the personal qualification establish and effective performance management system
- Set department goals/expectations, provide performance feedback to employees and manage performance on a daily basis
- Supervises, manages and develops quality staff and manages individual performance
- Create and manage quality gate inspection instructions per established guidelines to maintain operator awareness, without impacting velocity
Phoenix, AZ
Plant Quality Supervisor
Phoenix, AZ
Zulauf, Brown and Robel
Phoenix, AZ
Plant Quality Supervisor
- Be pro-active in identifying and performing tasks to maintain and improve safety, quality and environmental performance
- Manage quality systems to assure consistent process and product performance while maintaining maximum production and safe work habits
- Maintain and improve value stream maps, 5S+ processes and standard work
- Leads and develops plant QA staff of 2 to manage daily activities and deliver plant and Division quality goals
- Prepare, review and perform performance appraisals. Confidentiality of all personal data is strictly maintained
- Train, coach, and assist in the development of plant Quality Technicians
- Responsible for PES and QAR program administration. Also, responsible for continued development and continuous improvement of such programs
present
Detroit, MI
Senior Quality Supervisor
Detroit, MI
Lesch Group
present
Detroit, MI
Senior Quality Supervisor
present
- Establishing and maintaining metric capture programs, trending activities and implementing the QC plan
- Performing internal audits
- Providing strategic support at a branch location level
- Working knowledge of IPC-610 and its application to process control
- Communicating and interacting effectively with all levels of the organization and with external auditors/customers
- Performing corrective action investigations, determining root causes and defining corrective/preventive action measures
- Conducting and leading internal and external meetings and interfacing with customers
Education
Education
Bachelor’s Degree in Engineering
Bachelor’s Degree in Engineering
University of California, Los Angeles
Bachelor’s Degree in Engineering
Skills
Skills
- Dependable, detail-oriented, good problem-solving abilities, and strong commitment to teamwork
- Significant knowledge on quality systems (EQS, ISO/TS 16949), significant knowledge on quality tools as CEP, FMEA, 8D, PPAP, ELSS, APQP and engine valves
- Work with Quality Manager to establish goals for the Quality Assurance Unit. Design and utilize measures of productivity and quality for laboratory associates
- Ability to troubleshoot fly ash quality problems and understand long term quality trends
- Quality Auditor certification (ASQ CQA), Quality Engineer certification (ASQ CQE), or Manager of Quality/Organizational Excellence certification (ASQ CQMOE)
- Basic knowledge of Lean Manufacturing, Production Control, and overall Good Manufacturing Practices
- Train, support, and initiate Best Practice on Line Quality activities, leading to strong shop floor operator driven quality control
- Apply a working knowledge of quality principles and statistics to direct / coach quality technicians
- Responsible for site education of non-Quality Assurance personnel, responsible for professional development of the site Quality Assurance team
- Basic knowledge of probability and statistics
15 Quality Supervisor resume templates
Read our complete resume writing guides
1
Quality Supervisor Resume Examples & Samples
- Quality processes in a facility
- Products conformity within specifications
- Product defect reporting
- Setting priorities and establishing review schedules for product and equipment quality control
- Managing shop floor quality controllers
- Quality initiatives with the Caterpillar Production System
- Developing, implementing and monitoring of quality plans to meet standards and certification compliance
- Conducting and reporting internal quality audits
- Leading efforts to respond to customer feedback for quality improvements
- Acting as a Quality contact for internal and external customers
- Working with suppliers to improve the quality of products delivered to the facility
- Implementing and supporting Supplier Certification programs both internally and externally
- Providing support for corporate quality-related programs
- Leading and strengthening work teams relative to efficiency
- 4-year University degree in an Engineering or Manufacturing-related discipline
- Minimum of 6 years of work experience in progressively responsible quality / manufacturing roles
- Superior understanding of quality management practices
- General knowledge of shop operations and maintenance procedures
- Good interpersonal, communications, teamwork and collaboration skills
- Bilingual English - Spanish
- Ability to work with diverse teams of employees and customers
2
Quality Supervisor Resume Examples & Samples
- Ensure compliance to QS9000 internal certification requirements, accomplished by conducting and reporting internal audits
- Maintain and publish defect reports that are recorded and reported at all levels from start on line to OEM
- Quality contact for customers, contact for the day to day shop quality issues, including coordinating the holds due to quality and the rework needed
- Develops spec sheets for data analysis and process capability analysis
- Responsible for development and information collection for inspection reports
- Supervises or manages a work unit of employees where planning, scheduling, monitoring and reviewing work is required
- Responsible for all personnel issues and performance evaluation of team
- Responsible for verifying that quality is being maintained throughout the manufacturing process
- Work with Planning, Engineering, Operations and other functional areas in establishing audit procedures, audit frequencies and quality teams to insure customers are receiving a Caterpillar quality product
- Works with manufacturing operations to identify high scrap and rework areas and initiates investigations for establishing subsequent improvements
- Responsible for the design of the less complex tests for accuracy of in-house processes, and develops charts to monitor related results
- Bachelor's degree in Metallurgical Engineering or Material Science
- Requires a broad knowledge of manufacturing and foundry procedures (machining, heat treat, melting, casting and inspection) planning processes, work standards relative to manufacturing and inspection and a thorough background in statistical quality control data and gaging specifications
- Good interpersonal skills are essential to develop a cooperative working relationship with others, both inside and outside the organization
- Good analysis, diagnostic and judgment skills and good computer skills
- 2 - 5 years experience in Foundry operations
- At least 1 year of supervisory experience
- Good communication, interpersonal and collaboration skills
3
Quality Supervisor Resume Examples & Samples
- Perform all duties and promote themselves in a manner that reflects the P&F expectations, Cosma’s visions/values through Magna’s Employee Charter
- Follow and abide by all government, legal, Magna, Cosma and P&F rules and regulations
- Working Knowledge of Root Cause Analysis and ability to train department member
- Prevention of repeat issues
- Meeting project deadlines and follow up on outstanding concerns regularly
- Responsible for testing records, reporting monthly
- Responsible for calibration of Quality Measuring instruments
- Delivers and ensures on-going training of employees on QA standards such as QA alerts or other important information
- Adhere to procedures as prescribed by TS16949
- Maintains and drives TS16949 implementation and compliance
- Provides technical and process direction to manufacturing Quality Inspectors and all Supervisors
- Provides leadership, mentoring and supervision of manufacturing Quality Inspectors
- Trains employees in SOP’s and ensure training effectiveness in application of job skills
- Trains direct reports on safety topics, quality procedures and business updates for the month
- Directs and advises Quality personnel in special test procedures to analyze components and physical properties of product materials
- Communicate Quality issues to all appropriate departments
- Implement and oversee documentation process to cover all different shifts
- Respond to customer complaints and take appropriate measures to prevent reoccurrence and communicates directly with customer
- Full compliance with all administrative requirements/clerical duties within P&F Systems
- Develops and implements improvements to the operation procedures/plans and policies of the organization to manufacture a quality OEM product
- Keep organization informed of product quality and customer satisfaction
- Participate in engineering design review and product costing
- Responsible for production part sample approval
- Assist in the development and implementation of advance quality planning, process flow charts, FMEA and control plans
- Responsible for ensuring the organization meets and exceeds the needs of the customer related to quality
- Monitors QA final acceptance, Product Hold, Product Hold and Material review board performance and implements changes to improve operating efficiency
- Assist in developing, implementing and managing the Continuous Improvement Program
- Establishes or adjusts work procedures to meet testing schedules
- Develops and recommends test procedures for products and raw materials and maintains test equipment, including, but not limited to calibration of such
- Evaluate employees through performance reviews, ongoing coaching and feedback methods
- Continuously improve performance based on the key performance based on the key indicators
- Analyze and resolves, or assists operators and Quality Inspectors in solving production related problems
- Oversee the efficient implementation of quality standards, programs and processes to improve operational efficiencies and reduce/eliminate production waste, quarantine, and quality defects
- Maintain liaison between manufacturing, engineering and customer to resolve specific problems related to part/product and co-ordinate the implementation of preventive or corrective action
- Perform other assignments from time to time as management so directs
- Maintains a thorough knowledge of new developments, technology, and processes
- Grade 12 or GED (General Education Diploma)
- Post-Secondary Graduate with a technical degree/diploma in Quality Engineering
- Able to be flexible in hours of work in order to meet internal/external customer
- Ability to communicate effectively with all levels of management and plant personnel
- Computer proficiency in business applications
- Demonstrated ability to use precision measuring tools
- Basic knowledge of welding parameters and Cad and GD&T
- Basic understanding of Fixture Design and Datum structures
- Fluent English communication skills, both written and verbal
- Strong organizational skills, self-directed, strong problem solving and interpersonal skills
- Ability to work under pressure, and meet deadlines
- Physically able to perform the essential duties of the position
- Ability to travel within North America and overseas
- Full knowledge and experienced with TS16949
- Minimum 5 years related experience in a supervisory role in a manufacturing environment – preferably automotive Tier-1
- Excellent proven leadership skills
- Plans work and carries out tasks without detailed instructions
- Makes constructive suggestions
- Undertakes additional responsibilities
- Responds positively to instructions and procedures
- Able to work well with staff, co-workers, peers and managers, shares critical information with everyone involved in a project
- Maintains high standards despite pressing deadlines; does work right the first time
- Personally responsible; completes working a timely, consistent manner; works hours necessary to complete assigned work
- Is regularly present and punctual; arrives prepared for work
- Produces an appropriate quantity of work; able to manage multiple projects; organizes and scheduled people and tasks
- Is alert in a high-risk environment; follows detailed procedures and ensures accuracy in documentation and data; organized and maintains a system of records
4
Quality Supervisor Resume Examples & Samples
- Leads a team of 5 - 6 Quality Engineering professionals responsible for developing and executing quality processes for the facility
- Demonstrates the importance of quick and professional response to determine priorities and recommend solutions to problems to support production requirements
- Provides support for quality initiatives in facility operations, supplier quality, and materials technology
- Ensures conformity to global quality processes defined in the Caterpillar Quality Management System
- Ensures Quality professionals are trained and competent to perform their duties
- Accountable for conformity to global quality processes and management reporting
- Establishes review schedules for product and equipment quality control
- Leads and manages process execution and develops plans and tools in support of all quality systems and processes, in alignment with Caterpillar Production System principles
- Coordinates acceptance criteria used for conducting capability studies of new machine tools
- Defines method acceptance criteria priorities, alternative equipment and material certification and recertification
- Responsible for quality-related procedure conformance to improve quality and reduce cost
- Disposition non-conforming material through analysis of defects and root cause identification
- Supports facility certification efforts
- Manages and supports communications with external customers and suppliers related to quality expectations and metrics
- 4-year college or university degree in a manufacturing engineering-related discipline
- 5 – 8 years of work-related experience
- Excellent understanding of quality management, shop operations and maintenance procedures
- Good human relations, interpersonal and collaborative skills
- Good written and oral communication skills, including English language
- Good problem-solving skills
- Demonstrated history of process execution in the quality area
- Ability to read blueprints
- Prior supervisory experience in an engineering or quality role
5
Global IT Controls & Quality Supervisor Resume Examples & Samples
- Persistence & Courage - Able to motivate others through difficult circumstances or adversity to achieve desired outcome, Is not afraid to have difficult conversations or take negative action when necessary, Guides team through ambiguous situations. Willing to stand up and advocate for an idea or position, even if it is politically unpopular, Is looked to for direction in a crisis
- Previous experience defining and enforcing, standards, processes or controls
- Requires a relevant IT degree and/or 7-10 years of progressively complex IT experience generally gained through staff and supervisory assignments in Information Services and related areas
- Requires understanding of IT business operations and processes including but not limited to application development/support, infrastructure implementations, consolidations and support
- Requires previous technical and leader experience in Caterpillar applications or infrastructure with a broad background in systems hardware, system software, support and development methodologies, business planning, project management, and customer application needs
- Requires ability to work with diversified departments along with effective oral and written communications skills. Must have a strong customer focus and ability to work effectively across organizational boundaries
- A successful candidate must enjoy significant challenges, change management, and being held accountable to produce quantifiable results
- Ability to communicate effectively with senior leaders and strategic suppliers
- Diagnostic and analytical ability along with good interpersonal, teaming, delegation, and leadership and communications skills
- High level of business acumen and people skills
- Broad-based knowledge of Cat systems
6
Senior Quality Supervisor Resume Examples & Samples
- Developing and maintaining quality world class system while developing employee efficiencies,
- Direction for quality in all manufacturing areas
- Direction of the relevant quality engineers in areas of responsibility
- Direction of the relevant inspectors in areas of responsibility
- Playing a role in the plant annual objectives
- Ensure continued compliance with all Regulatory Standards including:ISO 13485, FDA QSR,ISO 14000
- Ensuring continued compliance with DMR
- Monitor production process for compliance to implemented process controls to ensure quality product is shipped to customer
- Support the RCA meetings to ensure that internal and customer concerns are handled and dealt with in an appropriate manner
- Review and ensure that for areas of responsibility (and those of direct reports) documents listed below are approved in an appropriate and timely manner
- Develop and maintain a program ensuring only correctly validated equipment is used in production process
- Supervision of quality engineers to ensure compliance for their areas of responsibility
- Project meeting attendance as required
- Attend and participate in daily cell meetings
- Ensuring information for PMR and Management Review meetings is maintained and available on time
- Manage and minute PMR KPI meetings
- Maintain training records for all reports
- Ensuring all quality reports are of required standard and issued on time
- Maintain Core records for all direct reports and raise issues concerning timekeeping should they occur
- Carry out a documented monthly evaluation with the quality engineers as well as an annual review
- Ensure open communication exists between the quality engineers and all other groups in order to facilitate the speedy dissemination of relevant changes and improvements to both products and processes
7
Quality Supervisor Resume Examples & Samples
- Supervise a section of 8-11 hourly inspectors
- Provide technical support for issues related to Geometric Dimensions & Tolerances (GD&T), prints, Caterpillar 1E Specifications, external specifications, etc
- Coordinate the daily activities regarding Quality Inspection
- Manpower planning and workload balancing (on-site and at contract processor)
- Prioritize inspection types to best service various customers
- Track progress against goals utilizing CPS
- Make economical decisions regarding refurbishment, rework, & scrap
- Utilize databases and available systems to make decisions and drive improvement
- Provide a high level of service to internal customers from Operations, Order Fulfillment, & Purchasing by being the primary inspection contact
- Improve velocity by analyzing material flow, layout, 5S, etc
- Utilize technical and industry knowledge to implement new inspection technology, and collaborate with other network Inspection Labs
- Participate in 6 Sigma projects & RIWs; possibly lead projects as greenbelt
- Develop technical expertise of inspectors to form the Best Team
- Bachelor degree in Engineering or Engineering Technology
- 1 to 2 years of supervisory experience
- Minimum of 3 years of quality experience in a manufacturing environment
- Highly organized with uncompromising standards of excellence
- Flexibility with location; Position will start in Franklin, NC for up to 12 months until transitioning to Mapleton, IL
- Willing to travel for the first year up to 50%, then travel will drop to 10-25% as needed
- CMM programming experience with PCDMIS
- Surface finish measurement experience
- Compression/Extension measurement experience, (Instron Bluehill)
8
Plant Quality Supervisor Resume Examples & Samples
- Lead quality team to achieve established goals and objectives
- Develop, recommend and implement growth and educational programs for department personnel
- Responsible to maintain open channel of communication/support with all internal departments
- Responsible to ensure company policies and procedures are followed
- Responsible to ensure all employees are treated fairly and consistently and that compensation and discipline is according to DORTEC policy and procedures
- Plan and monitor new program development and ensure flawless launches
- Develop succession plan and employee backups
- Responsible to review the scheduling, implementation and the monitoring of all departmental activities to ensure timely completion of projects
- Prepare, review and communicate performance appraisals. Confidentiality of all personal data is strictly maintained
- Must be capable of collecting and correlating relevant data that pertains to the overall efficiency and effectiveness of the department. Assessing trends through generated graphs and charts
- Maintain continuous improvement project tracking and report out status monthly
- Will be expected to display a positive approach to the continuous improvement of the department and keep current with new products, processes, materials and equipment technologies
- Responsible to manage own time to ensure effective completion of tasks/projects
- Responsible to maintain an organizational structure to meet company long term goals and procedures and to develops policies and procedures to control operations of the department
- Responsible for annual department budget preparation and monitoring to ensure budgets are achieved
- Determine strategic directions for the company information needs and implement
- Conduct Layered Process Audits and ensure corrective actions are implemented
- Establishes and maintains TS16949 internal audit program
- Plans, schedules and ensures performance of internal audits and Layered Process Audits
- Ensures adherence to TS16949 and ISO14001 standards through audits and corrective action follow-up
- Coordinates and leads TS16949 and ISO14001 third party certifications
- Acts as the company TS16949 champion providing answers to inquiries and directing related activities
- Completion of community college diploma/certificate
- Minimum competion of a post secondary education program in mechanical/quality engineering
- A.S.Q.C. Certification as a quality engineer preferred
- Min 3 years of work related experience in a supervisor role
- Related manufacturing / industry experience
- Communicates Effectively
- Multi-Tasks
- Troubleshoots problems
- Presentation Skills
- Analyses Data
- Interpersonal and Customer Service
9
Quality Supervisor Resume Examples & Samples
- Post-Secondary education or Engineering designation
- Minimum of 5 years’ experience as a Quality Engineer within a TIER 1 or TIER 2 QS 9000 company
- GD&T experience as well as 8D’s a must
- Able to be flexible in hours of work in order to meet internal/external customer requirements (scheduled and non-scheduled overtime, shifts, etc)
- Good leadership and problem solving skills
- Able to provide clear direction and training to employees
- Able to operate a computer and work with Microsoft Office
- Ability to promote, develop and work effectively with a team environment
10
Quality Supervisor Resume Examples & Samples
- Monitoring and enforcing the use of protective devices
- Responsible for following and reinforcing environmental and safety standards
- Monitoring shifts' beginning and end, as well as breaks, checking participants on continuous develpoment meetings
- Disciplinary authority, motivating employees
- Monitoring and updating employees' quarterly goals
- Responsible for quality and quantity of materials arriving to the area assigned
- Responsible for MQ and ISO measurements
- Supporting constant development with your team's ideas (T-card) and introducing and implementing them, especially safety precesses
- Takes part in RIW as well as CPS and 6 Sigma projects
- Managing documentations for headcount, holiday plans, sick leave records, daily measurement/control plan
- Responsible for PPM, DPM index and root cause analysis of any problem
- Passing on information amongst shifts and work areas
- Making sure everyone is concetrating on solving potential problems and keeping this attitude
- Operation of ISO9001
- Calibration of measuring equipments, replacement of them if needed
- Technical or Engineering Degree is required
- 3-5 years of quality job related experience
- Proficiency in Microsoft Office Suite
11
Quality Supervisor Resume Examples & Samples
- Maintain and monitor accurate performance trends for each direct report as overall team level performance
- Manage resources across the assigned vertical/portfolio (i.e. personnel schedules, technology by account needs)
- Evaluate and manage levels of staff effectiveness by partnering with operations to create improvement action plans
- Ensure facilitation and coordination of calibration process and sessions (both internal/external)
- Develop and maintain strong working relationships with internal operations personnel and clients
- Establish rapport and effective working relationships with client services and vertical/portfolio business owners in order to understand specific needs for their accounts
- Oversee and administer audits of key support processes within each account
- Conduct periodic audit of staff and departmental processes and recommends change
- Ensure consistent application of the quality process/system
- Attend and/Facilitate Client Calibration or monitoring sessions
- Facilitate Quality training and/or initiatives as needed
- Deliver client-facing presentations related to contact center quality
- Responsible for day-to-day functional supervision of non-exempt work group, including work assignment, performance and attendance oversight; administers Transaction Monitoring team coaching and development and all associated performance management responsibilities, drives input into selecting, training, developing, and completing performance appraisal of work group(s) in accordance with the organization’s policies and applicable legal requirements
- Diagnosis continuous improvement opportunities applicable to account, workgroup and department. Utilize common process methodology for process improvement
- Top Tier Call Center Quality Experience
- Program Level Experience preferred
- Some college experience or related work experience
- 1-2 Years of relevant supervisory experience
- Must have strong background and knowledge in Quality assurance areas
- Strong Business Process Improvement knowledge and/or Training Preferred
- COPC, APAQ, Transaction Monitoring, Six Sigma background/experience preferred
- Completed course in Transaction Monitoring/Call Center Quality Program, preferred
12
Quality Supervisor Resume Examples & Samples
- Oversee the daily activities of the functional quality organization engaged in inspection activities, both in the shop floor inspection activity as well as calibration of inspection equipment. Instruct staff in quality control and analytical procedures. Ensure that adequate resources are in place for compliance while maximizing the capacity of the quality staff. Work with production control to schedule work and establish priorities. Maintain applicable QC metrics
- Monitor the performance of quality control systems to ensure effectiveness and efficiency. Proactively lead in the development and effective implementation of robust processes to drive toward zero-defect quality performance. Facilitate initiation and closure of QN's for non-conforming material
- Communicate QMS matters to all relevant organizational departments, outside vendors, or contractors. Oversee the compliance of products and processes supporting business objectives while serving as a customer advocate to ensure that customer requirements are met
- Coordinate with relative functions to ensure understanding of customer requirements and expectations. Coordinate activities related to utilization of CMM inspection method, train inspectors on use, oversee development of programming and validate results
13
Quality Supervisor Resume Examples & Samples
- Plans, directs, and develops direct reports and supports the work efforts of indirect employees including overseeing the training of the Quality group (such as Inspectors, NDT, Quality Engineers, etc.) within their assigned area of responsibility in the application of inspection processes, customer requirements, etc. Provides leadership in the balancing of compliance practices with other business initiatives to allow all objectives of the business to be satisfied
- Performs the daily duties of assigned work such as Quality Engineer, MRB, MRO designee, etc
- Drives the development of robust processes that affect the quality of the product by planning, coordinating, and executing tactical department projects and corporate initiatives to meet established deadlines and policy deployment objectives
- Provides support for functional leadership by gathering and analyzing Quality information, programs, and initiatives. Responsible for monitoring and analyzing processes and/or product outputs, identifying systemic problems and opportunity areas, providing data and direction to the site(s), and work with team members to drive process improvements to work toward zero-defect quality performance
- Ensures that the site and suppliers' quality management systems consistently meet or exceed customers' and company requirements
- Maintains strong communication with customers, internal management team and suppliers to ensure quality level is meeting expectations
- Prepares, monitors, and responsible for budget, staffing, and business results of the assigned Quality team
- Lead and/or assist internal product and systems audits
- Support and follow all rules/guidelines/standards set by EHS, Quality, and CI functions as set by your leader and positions
14
Quality Supervisor Resume Examples & Samples
- Coordinate the Quality in Manufacturing Processes Gear
- Build and Implementation quality documentation for production processes
- Responsible documentation’ PPAP and APQP for the approval
- Leader Internal-External Audits (Client-Provider)
- Certify quality technicians for Gear manufacturing operations
- Coordinate the acquisition of calibrators and GR & R in manufacturing operations gear
- Mechanical Engineer, Electrical, Industry, Quality or related fields
- 10 years of experience in similar positions in the metalworking industry
- TS 16949 standard, ISO9000. With experience in internal audits - external (desirable is certified auditor.)
- PPAP, APQP, Core Tools,Control Plans, FMEA, FMEA
- Advanced level, Ishikawa, 8DS, Kaizen, GD & T
- Knowledge of Anova software, Minitab, SPC, SAP (or similar)
- Capacity and ability studies (Cp and Cpk), GR & R
- Poka yokes development, Fixture Gages
- Leadership and personnel management(Desirable working with gear manufacturing processes.)
- Establish and standardize processesand documents for quality control. (Alerts, Quality, visual aids, Inspection Instructions)
- Control Indicator (control charts, PPM's, Scrap)
- 5's methodology
15
Quality Supervisor Resume Examples & Samples
- Accountable to help define and effectively implement company quality systems, comply with customer quality requirements, and to continually improve the manufacturing process to achieve world-class quality and flawless launches
- Leads quality initiatives to achieve established goals and objectives
- Responsible to manage/support Online trainers assigned to shift
- Conduct Layered Process Audits and ensure corrective actions are implemented and sustained
- Initiation on Document Change Requests based on findings from auditing of the processes
- Initiation of Process Deviations as required and ensuring that all aspects including Customer Protection is adhered
- Responsible to ensure Company policies and procedures are followed
- Plan, monitor new program development
- Prepare, review and perform performance appraisals for Online trainers ensuring confidentiality is maintained
- Collect and correlate relevant data that pertains to the overall efficiency and effectiveness of the department
- Assess trends through generated graphs and charts. Maintain continuous improvement project tracking and report out status monthly
- Display a positive approach to the continuous improvement of the department and keep current with new products, processes, materials and equipment technologies
- Establish goals and objectives for the department
- Determine strategic directions for the Company information needs and implement
- Diploma or Degree in mechanical or quality engineering required
- ASQC Certification is considered an asset
- 2 - 4 years experience in a supervisory role an asset
- Highly motivated, self- directed, innovative and people oriented person
- Able to multi-task on several fronts to meet objectives
- Able to drive accountability down to direct reports through structured requirements, expectations and timelines
- Strong organizational and problem solving and prioritizing skills
- Self-starter with the ability to prioritize many different tasks
- Ability to gather and analyze information
- Ability to work independently and also as part of a team
- Strong computer skills, including Microsoft Word, Excel, Power Point
16
Quality Supervisor Resume Examples & Samples
- 4-year University degree in an Engineering, Manufacturing or Management-related discipline OR
- 2-year degree in a technical field with a minimum of 6 years working in Quality Engineering or Quality Management
- Minimum of 4 years of work experience in engineering, quality or manufacturing roles
- General knowledge of factory operations and mining/construction products
- Demonstrated product and quality process knowledge related to construction mining equipment
- Previous 6 sigma green or black belt experience
- Knowledge and experience in ISO and APQP
17
Quality Supervisor Resume Examples & Samples
- Sets priorities and recommends solutions to problems to support production requirements
- Ensures conformity to global quality processes defined in the Quality Management System
- Serves as the internal certification coordinator responsible for assisting and providing resources to internal certification teams
- Attends internal certification meetings at the corporate level interfacing with other facility and corporate coordinators and plant contacts for customer/corporate approval of certification
- 3 – 5 years of work-related experience
18
Quality Supervisor Resume Examples & Samples
- Ensure team compliance for quality assurance and customer provisions and criteria
- Serve as an issue resolution focal point that works with engineering, customer service support, to drive continuous improvement in products and processes
- Provide leadership with the proper disposition of nonconforming material when participating in the Material Review Board (MRB) activities
- Perform as an integrated team leader with engineering, customer service support, to investigate and correct various quality issues related to internal non-Conformances, product returns, supplier issues, customer complaints and corrective action requests with clear and concise reports to customers
- Participate on cross functional team projects to improve the overall organization and to develop a career path and leadership, with coaching and assistance by the Site Quality Manager
- ACE team lead for cell
- Establishes priorities for cell turnover
19
Quality Supervisor Resume Examples & Samples
- Responsible for verifying that quality is being maintained throughout the assembly and manufacturing process
- Work with assembly Planning, Engineering, Operations and other functional areas in establishing audit procedures, audit frequencies and quality teams to insure customers are receiving a Caterpillar quality product
- Bachelor's degree or equivalent experience of engineering
- Requires a broad knowledge of manufacturing and assembly procedures (machining, heat treat, assembly and inspection) planning processes, work standards relative to manufacturing and inspection and a thorough background in statistical quality control data and gaging specifications
20
Quality Supervisor Resume Examples & Samples
- Requires a broad knowledge of manufacturing (machining, heat treat, and inspection) planning processes, work standards relative to manufacturing and inspection
- Have Union experience either working in the shop or being a manager
- Requires at least two years in a supervision role
- To have knowledge of Seals and/or undercarriage business units
- Board knowledge of CQMS, ETQ, BIQ, and AQE systems
- Have knowledge in working in a foundry or forge shop
21
Quality Supervisor Resume Examples & Samples
- Display a positive approach to the continuous improvement of the department and keep current with new products , processes, materials and equipment technologies
- 2 - 4 years of experience in a supervisory role an asset
- Valid Driver's license and ability to travel between plants required
- Must be willing to work rotating shifts on quarterly basis
- Knowledge of SPC and Gaging required
- Strong computer skills, including Microsoft Word, Excel, Power Point,
22
Mortgage Banking Production Quality Supervisor Resume Examples & Samples
- Manage, coordinate and direct the daily operations of a unit of fifteen (15) or more non-exempt staff members to meet established productivity and quality targets
- Assign resources based on target deadline, set workflow priorities
- Introduce staff to new procedures and track their performance
- Recruit and develop effective Team Leaders and review staff, ensuring personnel continuity and backup
- Coach employees, motivate and develop staff to achieve mastery over multiple reviews
- Recommend human resources actions (hiring, salary actions, promotions, corrective action & termination)
- Coordinate with management to resolve problems and work on special projects
- Handle the exception items, resolve complex issues, review and recommend system modifications and monitor daily business and quality review of input
- Strong communication skills, with the ability to communicate with all levels of staff and management
- Demonstrated ability to handle employee and peer situations with professionalism and tact
- Successfully manage high volume processes with stringent time constraints
- Ability to learn detailed processes to train and manage non-exempt employees to high standards
- 3+ years of mortgage banking or financial experience, operations preferred
- 1+ years of managerial/ supervisory experience in a related field
- Quality Control/Audit related experience preferred
- Strong PC skills including (MS Outlook, MS Office including Word, Excel, Access and PowerPoint)
23
Quality Supervisor Resume Examples & Samples
- Leads and manages the Quality department colleagues on assigned shift, assuring an effective & strong audit function. Directs and manages all quality functions in accordance with the Quality Assurance department procedures, as well as the GMP
- Provides support/guidance for the QA labs & production areas to include training in food safety (GMP, HAACP, SQF, allergens, and other topics)
- Secondary site contact for all raw material and packaging suppliers
- Provides needed support of all internal and external audits
- Monitor quality and process improvement activities
- Responsible for relevant documentation for Quality processes
- Responsible for relevant tracking of KPI's associated with Quality
- Comprehend HACCP Principles and practices consistent with the Safe Quality Food Standards and report any problems with the food safety management system
- Strong leadership skillset
- Previous food or pharmaceutical manufacturing experience
- HACCP training certificate or related work experience
- GFSI experience
24
Quality Supervisor Resume Examples & Samples
- Developing, planning and implementing the Quality Plan / PPAP for Product launching
- Lead required Correlation, Capability, Gage R&R (Repeatability & Reproducibility) Studies
- Developing and execution of a plan for implementing the Quality System (In Process Control & Verification, Quality Standards, Quality System Management, Manufacturing Validation) for building products
- Manage “Customer Claims reports” and “Warranty Reports”
- Define and implement the Quality System Management tools (Quality Metrics, Quality Business, etc.)
- Develop, train and supervise the Quality team and their activities.Control of internal and external audits
25
Plant Quality Supervisor Resume Examples & Samples
- Direct, plan, and implement GMP compliance and training for the facility, working appropriately with any existing training roles in the organization
- Responsible for the oversight and administration of the “on hold” product program. This includes the status, release, and destruction of “on hold” product
- Responsible for PES and QAR program administration. Also, responsible for continued development and continuous improvement of such programs
- Accountable for the facilities eCOA program. Also, responsible for continued development and continuous improvement of such programs
- Responsible for quality accountability for all hours of operation
- Responsible for SOC/SOP compliance
- Additional responsibilities may include accountability for sanitation compliance and the execution of required food safety programs
- Responsible for vitamin analysis, moisture analysis, Aw analysis, ingredient analysis and water testing requirements
- Accountable for QAR/PES process
- Responsible for managing processes related to supplier non-conformances and consumer complaints
- Ensure adherence to all standard work processes including KWS Initiatives
- Responsible for compliance with all relevant regulations, FDA, PDA, CFIA, etc
- Responsible for compliance with SQF Food Safety Management System
- Ensure all department goals are met and/or exceeded
- Responsible for supporting the execution of relevant projects within assigned area
- Responsible for supporting talent management process for hourly employees. Ensure Diversity and Inclusion meets / exceeds corporate standards. Proactively engage in the development and training of hourly labor and support such plans developed by plant leadership
- Maintain understanding of processes and functional interdependencies. Recognize and escalate, as needed, those issues identified as risks to, or opportunities to improve, plant performance
- Drive K-Values
- Adhere to and administer company policies and procedures
26
Senior Quality Supervisor Resume Examples & Samples
- Certificar la ejecución de tareas específicas através de su revisión y firma
- Ensure procedures follow up set by the quality system of the company
- Ensure availability of forms and, materials necessary to perform inspection work
- Take preventive, corrective actions when required situations of non-compliance processes
- Review requirements and verify corrective actions when definitive solutions are implemented
- Supervise and assist quality inspectors in making decisions on the conformity of products
- Certify the execution of specific tasks through with review and signature
- Bachelor’s Degree in Industrial Engineering
- At least 5 year in previous experience in Quality Assurance areas
- English proficiency at an advanced level
- Domain of Microsoft Office to advanced level
- Mastery of ISO and FDA standards
- Ability to apply FMEA techniques
27
Quality Supervisor Guacara Resume Examples & Samples
- Works with Purchasing to qualify and rate local vendors of raw materials, packaging materials and finished goods
- Provides overall leadership for ISO 9001 compliance. Sets up and administers audit system for internal and external providers of products. Leads internal and external auditing. Works with regulatory agencies
- Ensures that Quality System is implemented and that raw materials, packaging materials, finished goods, and distribution activities meet specifications. Works cooperatively with Plants, Distribution, Engineering, R&D and Regional Quality to identify root causes of quality issues and implement processes to resolve and prevent issues. Regularly updates local Management Team and Regional Quality on quality initiatives and progress. Collects and reports on Customer Quality indicators. Drives complaints and other quality indicators results
- Provides technical guidance and works closely with Regional Quality, R&D, and local Manufacturing and Distribution on major new product introductions and acquisitions
- Generates and implements ideas that improve quality indicators, in line with cost, investment and service goals. Implements Lean concepts and practices
- A minimum of two years experience in a Quality, Manufacturing, R&D, or Engineering function
- Strong presentation and communication skills. English fluency
- The preferred candidate will have an advanced technical or business degree; experience in a Consumer Products industry; manufacturing management experience; regulated production Experience; strong IT background; and ISO auditing and implementation experience
28
Plant Quality Supervisor Resume Examples & Samples
- Directing, planning, and implementing GMP compliance and training for the facility, working appropriately with any existing training roles in the organization
- Overseeing the “on hold” product program, including the status, release, and destruction of “on hold” product
- Administering and continually improving established food quality programs
- Being responsible for food quality accountability for all hours of operation
- Being responsible for ingredient analysis, foreign material and metal detector program compliance
- Being accountable for the Quality Assurance Review (QAR) process
29
Quality Supervisor Resume Examples & Samples
- Responsible for providing technical expertise and leadership for daily Quality assurance operations and ensuring established metrics (Production, Scrap, Batch Conformance, and ATMPS) are met
- Provides specific technical expertise to support special projects, pilot operations, product and process improvements, and also provides input to develop capital expense forecast and FGQA equipment/spare parts budgets to support business needs and ensure timely inspection and batch release
- Supervises Quality Assurance personnel and collaborates with support functions to meet or exceed the goals and objectives of the Business Unit and alignment with those of the Plant and the Franchise
- Responsible for ensuring adherence to Environmental, Health and Safety policies and procedures; provides support to ongoing initiatives related to safety and ergonomics programs
- Ensures that manufacturing activities are performed in compliance with EES and International Quality System Regulations and drives efforts to enhance a culture of quality and compliance
- Manages the effective and efficient utilization of human, capital, and material resources to execute FGQA inspections and batch certification and release
- Supports rewards and recognition programs, participates in the development of employees, acts as mentor, and promotes talent
- Executes or supervises data entry on required systems, such as JDE, Kronos, AQR, and ETQ
- Partners with Franchise NPD teams to support process transfers and new product launches
- Collaborates with manufacturing partners to drive execution of validation protocols for Design and Manufacturing Process Changes
- Coordinates communication activities between Business Unit Personnel (production supervisors and associates, manufacturing engineers), Quality Personnel (Quality Technicians, Quality Engineers, MCQS technicians) and support functions (Kitting, warehouse, maintenance, open manufacturing, and facilities)
- Identifies and supports the resolutions of labor issues in coordination with the Human Resources department and Union leadership
- Generate, review, and approve QN and NCR’s
- Partner with manufacturing counterparts to ensure execution of OpCert activities and investigate, review and approve OpCert excursions
- Oversees response of Quality Assurance related audit finding observations
- Generate, review and approve of CAF’s for Plant Quality Procedure document changes
- Provides both direct support and mentoring to direct reports to support LEAN, PE, CIP, and Kaizen Projects
- Works with manufacturing partners and QS engineers to complete investigations and reports for Site and Franchise CAPA meetings
- Follow J&J and EES Records Management Policies for Convenience Information, Records Retention Schedules, Training and Education, Document Hold Notices, Records Cleanout,
- Inactive Records and Information Management, Vital Records and third party vendor if applicable
- Is responsible for coordinating and/or supporting the investigation and implementation of corrective and preventive actions to improve operating performance and to comply with requirements of the Quality system such as NCR, CAPA, audit observations and others
- Delivers year-over-year quality improvements (Batch conformance, scrap, process capability) and cost reductions associated with batch inspection and certification
- Plans, executes and documents training programs for associates and ensures on-time completion of training requirements
- Knowledge of EES Quality System Requirements and government and international regulations (FDA, ISO13485, etc)
- Knowledge of Failure investigations and robust documentation techniques, and Good Documentation Practices
- Basic knowledge of Lean Manufacturing, Production Control, and overall Good Manufacturing Practices
- Customer-focused decision-making skills
- Basic understanding of EHS regulations
- Basic knowledge of probability and statistics
- Supervision and development of Quality Technicians
- Basic knowledge of Process Excellence
30
Quality Supervisor Resume Examples & Samples
- Knowledge of the values and practices that align customer needs and satisfaction as primary considerations in all business decisions, and ability to leverage that information in creating customized customer solutions
- Knowledge of quality management methods, tools, and techniques used to create and support an environment that meets the needs of the organization
- Ability to measure the quality and quantity of work effort for the purpose of improvement
- Knowledge of techniques and tools that promote effective analysis and the ability to determine the root cause of organizational problems and create alternative solutions that resolve the problems in the best interest of the business
- Knowledge of and ability to create, implement, evaluate and enhance processes in internal controls
- Knowledge of the organization's customer support policies, standards and procedures and ability to guide customers on all company interactions
31
Quality Supervisor Resume Examples & Samples
- Maintains proficiency in the laboratory’s analytical procedures, including analytical techniques, data communication and testing protocols
- Facilitates communications of lab results, identifying and facilitating opportunities for improvement in reporting systems
- Supports the safety and loss control function as it relates to the Quality Department to ensure all plant, company and governmental requirements are satisfied
- Assists in providing budgetary planning information
- Direct, delegate and assign tasks to Quality Techs
- Train employees on duties
- 4 Year Degree in Quality or Food Science
- 3 to 5 years of relevant experience
32
Process Quality Supervisor Resume Examples & Samples
- All machining processes and the flow of material through the plant
- Blueprint reading including geometrical tolerancing
- All area of inspection such as techniques, principles, procedures, and know how
- Basic product engineering, process engineering and production control
- Statistical Process Control (SPC), root cause analysis, problem solving methods, QS-9000 criteria, and EQA criteria
- SIX SIGMA, LEAN
- EBE
- Measurement and Test Equipment
- Automotive experience
33
Quality Supervisor Resume Examples & Samples
- Ensure, with the Quality Manager supervision, that customer requirements are addressed. This includes to set quality objectives and related training, corrective and preventive actions to support production quality and to react quickly when a problem occurs and take the responsibility for problem solving analysis (i.e. 8D tool) in case of non-conformance
- Manage a group of people operating in metrological, gauges room and laboratory validating all the operations on production process flow
- Support all quality systems and functions, such as machine capabilities, control plans, measurement systems analysis plans (MSA), statistical process control (SPC), receiving inspection, tool inspection, PPAPs, corrective actions & PFMEA; Promote the Eaton Quality System and ISO /TS standard application
- Serve as support for TS 16949 plant certification processes and on-going TS16949 conformance
- Manage and coordinate PPAP documentations as per Customer specific requirements
- Provide technical training to plant employees on quality systems, statistical process control and other quality tools
- Manage the activities related new products development as per APQP requirements
- Promote and implement the continuous improvement programs applying Eaton Business System guidelines and lean tools such as standard work and 5S+
- Maintain relationship with all plant departments with the purpose to prevent / solve quality issues, improve the processes and answer to internal and external customer demands
- Degree preferred in Mechanical Engineering or equivalent
- 5 years of experience in Automotive Engineering or quality environment
- Thorough knowledge of ISO/TS 16949:2002 requirements and statistical process control techniques
- Knowledge of manufacturing processes and procedures including lean manufacturing tools
- ASQ Certified Quality Manager and/or ASQ Certified Quality Engineer is preferred
- Trained Six Sigma Black Belt or Green Belt is a plus
- Fluent in English and Italian
34
Quality Supervisor Resume Examples & Samples
- Be able to follow written/verbal procedures and instructions
- Possess good people and communication skills
- Experience with CMM and quality validation using a variety of tools
35
Quality Supervisor rd Shift Resume Examples & Samples
- Will initiate SOP revisions as needed to assure compliance, continuous improvement
- Perform review of quality related documents
- Bachelor’s Degree in Science or related field preferred not required
- Supervisory or team lead experience
- Minimum of 2-3 years’ experience in Quality, Operations, or related field in the healthcare industry. (Experience in FDA/DEA regulated environment a plus.)
- Aseptic experience a plus
- Demonstrated understanding of quality assurance in a regulated environment
- Must be able to communicate technical, scientific, and regulatory information, both written and verbally
- Must be a team player and enforce policies and standard operating procedures
36
Quality Supervisor Resume Examples & Samples
- Will provide direction, scheduling and training of the QA Technicians on new systems, procedures, and day to day activities
- Will participate in cross-functional teams to identify effective corrective and preventive actions to improve process quality
- Daily activities will include but not limited to: batch processing, label and packing, environmental monitoring, training of specific procedures
- Will provide reports from QA and data to support other business functions as needed for continuous improvements efforts within the facility
- Coordinate and schedule testing of all products for the on-going stability and on-going sterility monitoring programs with the appropriate contract labs (ensure product is produced and shipped to the appropriate lab in a timely manner)
- Will be responsible for tracking product lots from the generation of batch records through the final disposition. This will be done through the issuance of periodic reports to management that detail the status of all lots in progress
- Experience with LEAN Manufacturing, Six Sigma experience preferred
- Computer skills in word processing, spreadsheets and databases desirable
37
Quality Supervisor Resume Examples & Samples
- Planning and implementation of quality management personnel and any other work directly or indirectly affect the quality of products in terms of quality training; through a variety of ways to improve employee morale and work efficiency; in the company enhance strong customer orientation and quality consciousness. Responsible for the implementation of the Department staff appointment, training and assessment work. Assist HR to complete other related training work
- Bachelor degree or above, major in quality management or science and engineering, 5 years working experience in quality management
- Familiar with the company's production process, working principle, familiar with the company's products and production technology application of knowledge, system knowledge management knowledge
- Have received training in production operation management, management, quality management, product knowledge and so on
- Good command of office software; good communication skills both in English and chinese
- Strong verbal and written communication skills and business negotiation skills
38
Quality Supervisor Resume Examples & Samples
- BA/BS in Accounting, Finance, Business Administration or equivalent experience
- 4-7 years functional experience
- Strong knowledge of Accounting principles and general practices
- Strong knowledge of audit methodology and techniques
- Strong knowledge of Information Technology including PC, Network, Mainframe and E-commerce systems
- Strong knowledge of PC desktop applications
- Strong project management and organizational skills
- Strong knowledge of laws, regulations and business practices for industries in which Experian operates
39
Quality Supervisor Resume Examples & Samples
- Responsible for ensuring batch record documentation aligns with activities performed and is compliant against Catalent procedures
- Responsibility for releasing supplies for distribution
- Manage workload against the schedule for production priorities, working closely with the Scheduling and Production, including coordination of overtime
- Monitor distribution of work within the department, assigning tasks and making adjustments when necessary to meet commitments
- Publish daily review/release schedule and completed work report for previous day
- Coach QADC staff through day to day activities when needed and lead the daily communication meetings
- Takes initiative to make decisions for QADC collectively with the QADC team
- Ensure safe operations and engage employees in safety awareness
- Act as the Quality partner to support packaging operations, peer Quality Supervisors, and ensure projects are on-track
- Enforce Catalent policy & regulatory requirements
- Act as site subject matter expert for “Good Manufacturing Practices” and SOPs related to batch record documentation and release
- Act as lead investigator for all Problem Reports regarding batch record documentation and support Problem Reports led by Operations
- Interact with customers regarding questions, issues, metrics, batch records, etc
- Develop process excellence & efficiencies prior to the beginning of a project
- Track and report metrics and identify trends and predictive models
- Respond to and investigate customer complaints
- Support activities related to the TrackWise System
- Assist with customer and government audits, host and lead tours when required
- Review & revise SOPs, batch records, Change Orders and other related documentation
- Audit for compliance as pertains to Catalent SOPs, regulatory, & customer requirements
- Support Corporate and local Quality policies and initiatives
- Anticipates internal and or external business challenges and/or regulatory issues; recommends process, product or service improvements
- Leads project teams to achieve milestones and objectives
- Review of completed batch record for conformance with protocol and appropriate cGMP and ensure that any changes are performed according to procedures
- Confirm proper randomization schedule utilization for correct patient treatment group assignment
- Communicate with other functions to resolve inconsistencies with proper recording and completion of the batch record and associated documentation. Communications may include educating other functions to ensure compliance to regulations, procedures and client requirements
- Archive batch documents onto shared drive and within archive room
- Participates in meetings, projects as a representative of the Quality Manager, as appropriate
- Performs biennial SOP review related to QADC functions
- Complies with and ensures compliance with EH&S, and 5S requirements for QADC
- Other tasks or projects as assigned
- A Bachelor’s Degree is required
- Bachelor's Degree with a scientific focus is preferred
- Excellent communication skills both written and oral at all levels within the organization are required
- Project management, problem-solving and analytical skills, with a high level of attention to detail is required
- Computer literacy in Microsoft Office Suite including Microsoft Word, Excel and PowerPoint is required
- Supervisory experience is preferred
- At least one year of experience in Quality Assurance or Operations in the pharmaceutical/medical device industry is required
- At least three years’ experience in Quality Assurance or Operations in the pharmaceutical/medical device industry is preferred
- Experience in using an ERP tool such as SAP, JDE is preferred
- Strong knowledge of mathematical, mechanical aptitude and statistical analysis for quality control is preferred
- At least 1 year of experience working with Standard Operating Procedures and associated documentation within a regulated industry is preferred
- At least 1 year of experience working with and/or auditing batch records is preferred
- Good organizational/time management skills
- Exercises sound judgment and is analytical in thought
- Promotes a positive working environment
- Challenges status quo and initiates improvements
- Good math skills
- Solves unique and complex problems that have a broad impact on the business
- Contributes to the development of functional strategy
- Ability to provide routine off shift support
40
Quality Supervisor Aseptic Processing rd Shift Resume Examples & Samples
- Will coordinate with Pharmacist in Charge to ensure all Pharmacy Technicians are compliant and up to date with all training, certifications and qualifications required. Will ensure all documentation is current
- Ensure all Quality related documents generated at the Facility are received into the Documentation Center at the appropriate time per procedure
- Bachelor’s Degree in Science or related field desired
- Aseptic processing experience desired
- Minimum of 3-5 years’ experience in Quality, or related field in the healthcare or pharmaceutical industry
41
Quality Supervisor Resume Examples & Samples
- Develop and maintain quality systems that support the daily manufacturing operations to meet product and process quality metrics
- Act as an ambassador for World Class Manufacturing (WCM) by working closely with operations team members, team leaders, technical support specialists and business unit leaders to develop and enhance quality systems
- Manage Quality systems, including process documentation, Internal Quality Audit processes, and External ISO and Quality system audits
- Minimum 2 years of experience in Quality Systems management, in a production environment
- Ability to analyze and translate data into visual charts/graphs etc. for reporting purposes
- Bachelor's degree or higher in Engineering, Industrial Management, Operation, Quality, Manufacturing
- Powertrain manufacturing experience
- Supervisory experience/Working in a union environment
42
Quality Supervisor Resume Examples & Samples
- Positive Attitude, Ethics and International Values which support our company’s values, and a healthy, high performance culture
- Experience supervising employees in a represented manufacturing environment
- Knowledge of ISO Quality Operating Systems
- Working knowledge of basic Microsoft programs, such as Excel and Word
- Prior quality manufacturing experience preferred
- Ability to understand/interpret engineering prints and quality assurance standards
43
Quality Supervisor Resume Examples & Samples
- Conduct multiple projects simultaneously ranging from feasibility phase to post launch quality assessment and throughout production life
- Facilitate Failure Modes and Effects Analysis (FMEA) with Engineering in conjunction with advanced quality-planning activities and monitor the status throughout production life
- Develop, implement and maintain Statistical Process Control techniques
- Assure compliance of the documented quality system (QS 9000/TS16949) and promote consistency throughout the organization
- Conduct investigations to determine causes of defects, make recommendations for corrective action
- Maintain customer complaint log and facilitate and participated in the corrective action process
- Instruct and train personnel in techniques and use of audit and testing devices
- Monitor and revise quality documentation as required
- Visit customers and suppliers when necessary. Acts as a liaison to internal and external customers
- Review all production methods for compliance to quality standards and for improvement of product and quality standards
- Perform all responsibilities with QS9000/TS16949 system requirements
- Bachelors degree in Mechanical Engineering
- Minimum of two (2) years automotive experience
- Strong analytical and proven team oriented problem solving-skills required
- Strong customer satisfaction orientation
- In-depth knowledge of quality engineering techniques
- In-depth knowledge of Metrology
- Above average communication skills and interpersonal skills
- Bilingual (English required)
44
Quality Supervisor Resume Examples & Samples
- Oversee laboratory testing operations. Provide technical support to internal and external customers including Packaging Units, Processing and R&D. Ensure consistency in lab operations and drive continuous improvements in laboratory performance
- Work with Quality Manager to establish goals for the Quality Assurance Unit. Design and utilize measures of productivity and quality for laboratory associates
- Ensure that profit plan commitments are met by efficient use of resources and careful execution of laboratory testing requirements
- Facilitate the professional development of exempt associates. Ensure completion of staff performance reviews
- Participate in the development of laboratory procedures and the training and documentation processes to support ongoing compliance to regulatory requirements and GMPs. Communicate vulnerabilities and provide leadership in developing solutions
- Participate in the investigation of Out-of-Specification production. Initiate root cause/corrective actions and systems to ensure compliance to quality requirements
- Audit laboratory records to determine compliance with customer and GMP requirements. Coordinate the necessary resources to accomplish training goals
- Perform special projects and assignments in support of the unit or facility as defined by the Unit Leader
- Bachelor's degree required preferably in a technical field, plus 2-5 years' experience in a related technical field
- Demonstrated management skills and aptitude
- 2 or more years of Supervisory/Training/Coaching experience required
- 1-2 years of OTC Drug manufacturing experience
- Requires strong administrative and analytical skills
- Verbal and written communications skills are essential to deal with all levels of the company
- Willing and able to work weekends
45
Quality Supervisor Resume Examples & Samples
- Assist with the implementation of the QRMP (Quality Risk Management Process) system and operational standards as outlined in the plant accountability list in order to achieve targeted RCR
- Assist with communicating the factory Quality Management System expectations to all personnel and defined stakeholders, and provide training accordingly
- Provide technical support to Operations, Maintenance, Sanitation, Logistics, Procurement, and Sales / Marketing
- Assist with the factory Pre-Requisite Programs (PRPs), Operational Pre-Requisite Programs (OPRPs), and Critical Control Points (CCPs), as defined in the Food Safety Program
- Assist with facilitating and driving compliance to the Quality Risk Management Process (Q-RMP) via cross-functional work teams and leadership accountability
- Verify and validate manufacturing processes comply with regulatory requirements
- Assist with retaining and maintaining documentation and records associated with HNA and factory Quality Management Systems, Quality Risk Management Process, and Food Safety Systems Certification (FSSC 22000)
- Assist with training personnel in techniques and procedures for the Food Safety Program, Quality Assurance activities, Quality Control activities, Raw Materials and Finished Goods Inspections, and Sensory Taste Panels
- Assist with the administration, execution and maintenance of the internal audit program
- Review all Process Sheets and Specifications for acceptance or variance to capability
- Serve as the factory primary contact for all customers and third party audits, including management, preparation, and corrective actions
- Represent the factory in the New Product Development Process (NPD) to ensure factory capability for new products and line extensions
- Champion quality improvement initiatives and waste reduction projects to center line processes and reduce variation
- Manage and report on key issues, trends, customer / consumer complaints, and incident investigations to local and HQ Quality and Food Safety management
- Communicate and report on key quality performance metrics as defined by Corporate Quality and local management
- Assure that all non-conforming products are managed (including identification, segregation and timely final disposition) in accordance with current applicable policies
- Interface with contractors (pest control, cleaning chemicals, engineering, etc.) and raw material suppliers to ensure compliance with quality and food safety requirements
- Assist and partner with business leaders on implementation of process improvement (Six Sigma / Lean), including leading change initiatives, planning, and facilitation
- Assist with the supervision of Quality Assurance staff including but not limited to performance management and employee development, etc
- 1-5 years of manufacturing experience is required; preferably within an USDA and or FDA regulated environment
46
Quality Supervisor, Operations Resume Examples & Samples
- Carries out leading responsibilities in accordance with the organization’s policies and applicable laws including health and safety
- Ensures that the quality aspects for new processes, products and or upgrading of existing processes and products and subsequent PQ’s are met
- Supports/Initiates investigations for non-conformances
- Approves specification and process changes per applicable procedures
- Provides feedback to operations on problems related to quality and/or compliance
- Supports Operations in evaluation and implementation of actions plans to eliminate root causes of non-conformances
- Supports internal and external audit programs
- Promotes the use of Process Excellence tools to enhance analytical thinking and problem solving techniques
- Provides support to plant wide initiatives such as implementation of new initiatives safety, environmental and Quality related initiatives
- Supports and promotes the safety and industrial hygiene objectives of the plant
- Initiates and maintains interplant communications of quality issues
- Supports on-going continuing efforts and projects to improve our manufacturing Quality Systems, processes
- Supports and promotes cost savings opportunities that work toward global objectives in the organization
- Actively supports other plant functions in the implementation of company programs and projects
- Enforces, promotes and observes all safety, industrial hygiene rules and regulations established by the Company
- Is aware of, and complies with, Company policies on Safety
- Reports accidents, incidents, near misses, and hazardous situations in a timely manner and participates in the corrective action process
- Other related tasks as assigned
- University/Bachelor’s Degree or Equivalent in a Life Science, Engineering, or Physical Science area
- 6-8 of years related experience required as well as 3-5 years leadership experience
- Experience in the Medical Device environment with respective regulations knowledge will be highly regarded
- Process Excellence / Six Sigma Certification or equivalent preferred
- Good oral and written German and English language skills are required
47
Quality Supervisor Resume Examples & Samples
- Engineering Bachelors Degree (or similar) is required
- Advanced/ Fluent English
- CQE – Certified Quality Engineering is desirable
- GreenBelt certification is desirable
- Product and Manufacturing Knowledge is required
- Excellence Model Knowledge is desirable
- Strong leadership
- Capacity to work under pressure
- Communication ability to deal with customers
- Managerial courage and intellectual rigor
- Significant knowledge on quality systems (EQS, ISO/TS 16949)
- Significant knowledge on quality tools such as CEP, FMEA, 8D, PPAP, ELSS, APQP
48
Quality Supervisor Resume Examples & Samples
- Prepare report and presentation to monitor and improve the metrics that impact Quality indicators
- Propose and implement improvements processes to guarantee
- Participate in Internal ISO 9001 audits to assure compliance of the Quality System and follow up on the resulting corrective actions (CAR’s) or opportunities for improvement (OFI’s)
- Collect and maintain Historic data control (statistics of products) to support and determine quality issue and root cause
- Verify and Follow the final Audits results
- Analyse production quality issues (including metrics trends), customer and supplier Feedbacks, prepare corrective action plan, follow up and close any actions which are documented through WISPER; maintain the communication process between supplier, external and internal customers
- Lead the Quality process activities and implement quality action plan on any New Product Introductions and transfers
- Bachelor’s degree on industrial, electrical or electromechanical engineering, or other related science
49
Claims Quality Supervisor Resume Examples & Samples
- Works on issues of broad scope
- Requires considerable planning and direction setting
- Responsible for recommending changes in guidelines, procedures, and policies
- Minimum three (3) years of management in a claims processing environment preferred
50
Quality Supervisor Resume Examples & Samples
- Drive safety, compliance, engagement, and continuous improvement within Lexington sites
- Leads, supports and develops Quality department personnel
- Ensures personnel comply with all quality and laboratory requirements
- Coordinates and manages incoming, in-process, and finished product testing to support manufacturing operations, new product launches and customer requirements
- Ensure all records and data are maintained to meet government, corporate and customer requirements
- Generate and maintain work instructions, SOPs and other required documents
- Maintain compliance of all test equipment and recommend upgrades or acquisition of new equipment as needed
- Work with division leadership on new or revised product testing requirements
- Support customer and certification body audits
- Lead and/or support the integration of new product specifications or laboratory standards
- Minimum of five (5) years of Quality Assurance and/or Quality Control in a manufacturing environment
- Minimum of two (2) years of Supervisory experience
- Bachelor’s degree or higher in an Engineering or Science discipline from an accredited institution
- International Organization for Standardization (ISO: 9001) lead auditor and/or experience working within a regulated environment
- Demonstrated ability to lead teams and drive continuous improvement
- Excellent communications skills (verbal, written and presentation)
- Experience leading global cross functional teams
- Microsoft Office proficient, Minitab and DPQx a plus
51
Quality Supervisor Resume Examples & Samples
- Provides support of production rate increase, technical support and hands on training to shop floor quality personnel and manufacturing
- Achieve quality assurance operational objectives by contributing information and analysis to strategic plans and reviews; preparing and completing action plans; leads and directs operational unit; identifying and resolving problems; completing audits; determining system improvements and implementing change
- Supervise / administer hourly (Inspectors) and salaried quality engineers and provide necessary guidance to team and validate their work
- Validates quality processes by working to or establishing product specifications and quality attributes; measuring production; documenting evidence; determining operational and performance qualification; writing and updating quality assurance procedures
- Maintains and improves product quality by completing / participating in product, company, system, compliance, and surveillance audits; investigating customer complaints; collaborating with departments in the development of new products / engineering designs, manufacturing and training methods
- Prepares quality documentation and reports by collecting, analyzing and summarizing information and trends including failed processes, stability studies and corrective actions
- Updates job knowledge by studying trends in and developments in quality management; participating in educational opportunities; maintaining personal networks; participating in professional organizations
- Works extended hours in support of critical deliverables
- Minimum of 5 years’ experience managing and or working a certified quality management system
- Minimum of 2 years’ experience in preparing SPC material analysis
- Proven track record of driving continuous quality improvement in a manufacturing environment
- Experience in the Aerospace industry (preferably Nacelle components)
- Previous audit experience
- Demonstrated critical thinking and problem solving skills, using root cause analysis tools
- Must be able to apply a thorough knowledge of inspection practices, and procedures in the field of structural assemblies (preferably engine nacelle related)
- Must be able to demonstrate knowledge of quality policies, manufacturing processes and procedures, “blueprint / Model Base Definition” reading, continuous improvement techniques
- Must possess an advanced knowledge of technical data information systems, blueprints / Model Base Definition, material specifications, process specifications, regulations, as well as other pertinent information
- Must be able to work effectively across functional boundaries, and have demonstrated time management skills in order to handle multiple priorities
- Must possess the ability to define problems, collect data, establish facts, and draw valid conclusions in decision making
- Must possess excellent communication skills, both written and verbal
- Must possess excellent interpersonal skills and active listening
- Ability to work cooperatively with supervisors, co-workers, customers, and others in a team environment displaying mutual trust and respect
- Good understanding of Lean principles and/or ACE tools preferred. Ability to lead continuous improvement events preferred
52
Senior Quality Supervisor Resume Examples & Samples
- Provide advanced quality processes including statistically based variation reduction, control planning, mistake proofing, and Manufacturing Process Control
- Evaluate prospective supplier Quality Systems and conduct Gap Analysis where required
- Evaluate procedures for compliance to contractual and regulatory requirements (including international regulation coordination issues)
- Prepare progress reports, program reviews as needed, to assure the highest quality and cost effectiveness for HAS field quality support
- Train associates, suppliers, and contract personnel in Six Sigma techniques, Manufacturing Process Control, variation reduction, etc
- BA/BS degree in a technical discipline (i.e., engineering, computer science, quality assurance) with 8 years of Quality Assurance experience. In lieu of BA/BS, at least 12 years of relevant experience
- Demonstrated ability as a self-starting, self-directed individual
- Demonstrated technical knowledge, strong leadership and interpersonal skills
- Supervisory experience. Ability to counsel, coach, develop and motivate staffation skills
- Demonstrated written and oral communication skills at all levels of the organization
- Strong understanding of Quality engineering practices applicable to the manufacture of Aerospace products including customer and industry standards
- Must have experience with layout and precision inspection techniques and GD&T
- Must be, at a minimum, trained in Six Sigma techniques
- Must be proficient using common software (MS Word, Excel, Power Point, Project, etc.)
- Must be able to interpret purchase orders, Aerospace engineering drawings, and industrial specifications and understand the correlation between each when appropriate
- Current ASQ CQA or CQE certification is highly desirable, as is an RAB auditor accreditation
- Experience using Honeywell specific software/management tools (ECATs, PDM, One Source, SAP, etc.) is a plus
- Understanding of basic international trade compliance and regulatory issues
- Familiarity with Quality Systems (e.g., AS9100, ISO 9001, etc.), Lean Manufacturing, Manufacturing Process Control, Six Sigma, and Root Cause Corrective Actions (RCCA) (8D)
53
Quality Supervisor Resume Examples & Samples
- Manufacturing and Quality Background
- Working knowledge of continuous improvement principles, i.e. Lean, ACE, QCPC, DIVE
- Bachelors in Engineering, Business or related field
54
Quality Supervisor Resume Examples & Samples
- Handle all company activities related to Schedule I-V Controlled Drug Substances, including record keeping, reporting, acquisition, storage, distribution, importing, and exporting
- Complete new and renewal registration requests
- Responsible for providing support to clients regarding regulatory inquiries
- Responsible for researching regulatory issues to develop appropriate action plans
- Supervise the coordination of customer shipments and receipt of controlled substances
- Supervise the coordination of destruction of controlled substances
- Manage reconciliation of clinical returns from sites
- Maintain precise inventory of controlled substances
- Submit Import/Export Declarations and Permit Applications to the DEA
- Perform Annual Inventory and Year-End Reports
- Reporting of Automation of Reports and Consolidated Order Systems (ARCOS) for Manufacturer and Distributor registrations to the DEA
- Audit vault and cage-related documentation and logbooks
- Ensure areas meet regulatory requirements
- Perform quota applications and increase requests
- Complete DEA 222 Forms for purchases and shipments of Schedule I and II materials
- Respond to and track client complaints
- Communicate with clients regarding received complaints
- Host internal, client, and government audits of the controlled substances areas
- Write and revise SOPs
- Assist in development and approve detailed and complicated Distribution and Returns Protocols requiring additional regulatory needs
- Successfully manage diverse teams to ensure that goals are completed
- Addressing CAPAs
- Communicating directly to regulatory agencies to handle complicated tasks
- Supervises the daily activities of business and technical support
- A High School diploma or GED is required
- A Bachelor’s Degree is preferred
- At least five years’ experience in pharmaceutical, biotech or chemical industry is required
- DEA experience is required since selected incumbent will handle all company activities related to Schedule I-V Controlled Drug Substances, including record keeping, reporting, acquisition, storage, distribution, importing, and exporting
- Knowledge of relevant cGMPs and Controlled Substance Regulations is required
- Knowledge of quality, regulatory and legal standards including USP, EP, JP, GMP, ICH, DEA and FDA is required
- At least five years’ experience working with Standard Operating Procedures and associated documentation within a regulated industry is required
- Strong knowledge of mathematical, mechanical aptitude and statistical analysis for quality control is required
- Ability to multi-task with high efficiency and work in a fast paced environment to meet deadlines is required
- Experience working with third-party contract manufacturing in the Pharmaceutical industry is preferred
- Appropriate communication skills allowing direct interaction with outside suppliers, internal managers and senior management are required
55
Quality Supervisor Resume Examples & Samples
- Manages all hourly quality personnel and Quality Laboratory
- Responsible for the management NCMR's from issuance to follow-up to corrective action of defects
- Responsible for the coordinating and conducting of plant self-assessments for
- All of the Quality and Food Safety Systems
- Responsible for assuring implementation to corrective action items for non-compliance items found from the self-assessments
- Responsible for leading activities for the Food Safety committee to meet AIB and regulatory requirements
- Responsible for implementation from problem solving activity based on monthly consumer contact analysis/feedback
- Responsible for assuring sustainment of training for current and new consumer response feedback systems for QA technicians and Micro technicians
- Responsible for sustainment and tracking of root cause effectiveness from implementation
- Actively participates in TPM for the Quality pillar
- Pillar board updates
- 7-Step tracking and reporting
- Provides support and coaching for shop floor teams for 5-S activity in all areas
- Involved in actively participating on a TPM team
- Responsible for the management of training program for all plant personnel
- Responsible for training, auditing & sustaining compliance to HACCP
- Responsible for training, auditing & sustainment to GMP's
- Responsible for training all employees and Food Safety Committee on current AIB and regulatory standards
- Responsible for training all employees on the current Quality Standards to reinforce compliance
- Responsible for self-assessment training for QA team
56
Senior Quality Supervisor Resume Examples & Samples
- Support the QRMP system and operational standards as outlined in the plant accountability list
- Perform follow-ups to non-conformances found and provide responses as appropriate. Review and approve minor change requests
- Insure proper construction procedures are followed to meet site/Kraft Food safety requirements. Takes appropriate steps to assure successful project startups
- Acts as Distribution Quality contact and work with Distribution on Quality concerns/initiatives. Also, assists with product disposition and security items
- Supports and follows proper plant safety policies and procedures
- Comply with all applicable Environmental, Health and Safety regulatory requirements and Kraft Heinz Global Operational Risk Management (ORM) policies/procedures
- Promote a performance-based culture that encourages continuous improvement and leverage Environmental, Health and Safety management excellence
- Advanced knowledge of quality systems, procedures, & policies helpful. Handle multiple assignments, develop work plans, & prioritize
- Planning and organizing skills
- Must be able to work shifts, weekends, and all required overtime. Prompt and regular attendance
57
Quality Supervisor Resume Examples & Samples
- Bachelor degree or above in Electrical Engineering or related field
- At least 5 years related experiences in power distribution service industry
- Demonstrated ability to take complex customer requirement into production
- Solid understanding of switchgear configuration and structure
- Technical oriented, Independent working ability and can work under pressure
- Effective Project management skills and demonstrated problem solving, willingness to work with team
- Written English is mandatory, good oral English is preferred
- Willing to travel 20% to 30% of working time
58
Quality Supervisor nd Shift Resume Examples & Samples
- Will be responsible for daily quality operations within the department. Ensures compliance to procedures and addresses non-compliance issues
- Will assist Quality Manager to assure timely closure of audit items
- Conduct root cause analysis for compounding errors and processing errors generated at the facility during all phases of the production process
- Minimum of 3-5 years’ experience in Quality, Operations, or related field in the healthcare industry. (Experience in FDA/DEA regulated environment a plus.)
- Knowledge of Management Inventory Systems desired
- Must be able to compile, analyze and present collected data in summary form
- Effective problem solving, supervisory and organizational skills
59
Quality Supervisor Resume Examples & Samples
- Develop the Quality strategy for the interior fabrication & installation of the new Global 7000/8000
- Define all the inspections requirements & quality plan for the completions manufacturing (internal or external)
- Creation of the quality team based on the operations needs
- Plan the Advanced Quality Planning (AQP) deployment & evaluate the risks (FMEAs) for internal or external manufacturing activities
- Define Quality KPIs & governance, ensure proper training and development of team members
- Ensure a strong & continuous alignment with your quality peers from Toronto (Global 7000/8000) and with the Global Completion Center (Global 5000 & 6000)
- Develop manufacturing processes and optimize internal and external processes
- Promote and act as a leader for Achieving Excellence System implementation
- You have a Bachelor's degree in Business, Management, Engineering, Operations and/or five (5) years of relevant experience
- You have a good knowledge of Advanced Quality Planning tools (FMEAs, process control plans,etc)
- You are recognized for your leadership, your communication and your coaching skills, for your ability to mobilize and engage a team
- (Could be required to travel from time to time)
60
Quality Supervisor Resume Examples & Samples
- Drive improvement through statistical analysis for trends, root cause determination and corrective actions
- Develop a strong Quality organization. Identify improvement options, including mentoring and training. Engage local and divisional resources to support this effort
- Primary contact for all Quality issues. Communicate issues within local and global organization. Requires the ability to communicate effectively in written and spoken English. Establish regular Quality reviews
- Improve customer focus and knowledge of the customer. Consider all decisions from a customer perspective
- Develop and improve total quality system to ensure that LLK operation meets applicable
61
Quality Supervisor Resume Examples & Samples
- Administer TYCO quality policies and procedures
- Maintain compliance with Commercial and MILQC Manuals, policies, procedures, and associated directives
- Maintain, develop as needed and train applicable inspection and work instructions
- Assist QC Manager in capital expenditure planning and spending
- Assist QC Manager in establishing an annual expense budget plan; control expenses within budget limitations
- Evaluate needs and provide tolls, equipment, and supplies for inspection
- Translate orders, contracts, specifications, and engineering drawings into inspection instructions; Determine characteristics to be inspected, frequency, sampling plan, and method of inspection
- Complete a contract review form for all Engineered Systems government contracts; translate requirements to an inspection plan and communicate to inspection
- Schedule final inspection and GSI submittal for government product
- Evaluate inspector performance and develop training as necessary with QC manager to maintain or enhance skill levels
- Schedule inspector work hours and work assignments
- Work with customers, customer representatives, and outside regulatory agency personnel during audits, source inspections, and product submittals
- Coordinate inspection and analysis of customer returned product
- Evaluate and maintain program compliance with military and customer specifications as required by contract
- Evaluate vendor compliance to government specification and contract requirements
- Conduct vendor audits as required
- Bachelors Degree with 3 years experience in pressure vessel welding related field
- Associates degree with 7 years experience in pressure vessel welding related field
- Experience Required: Minimum of High School diploma with 15 years experience
- Training Desired: Certified Quality Engineer with ASQ, Level III in x-ray, certified training in Six Sigma
62
Plant Quality Supervisor Resume Examples & Samples
- Develop and implement quality systems and corrective actions
- Create, maintain and periodically review and update quality assurance manual
- Train employees in quality systems
- Coordinate all customer inspections to ensure timely shipments of orders
- Manage direct report activities in order to ensure compliance to procedure and part specification
- Ensure that documented procedures are established
- Ensure that product quality plans are established
- Maintain and improve value stream maps, 5S+ processes and standard work
- Improve appropriate safety processes. Lead all 8D corrective action investigations for any safety issues (including near misses)
- Maintain & control Plant quality operating systems and EHS databases
- Coordinate with other department supervisors Maintain & Update EPM on the monthly basis
- Coordinate EHS with other department supervisors and responsibility for Safety Issues and reports on the daily & monthly basis
- Minimum two years’ experience in Manufacturing/Quality Assurance with ISO or TS Quality Standards
- Must be eligible to work in the US without company sponsorship
- No relocation is being offered. Candidates being considered must reside within a 50 miles of Eaton Williamsport site
- Master degree preferred
- Knowledge of quality techniques including statistical methods used to analyze and control process variations, capability studies and PFMEA
- Team-orientated problem solving skills and corrective action methodology
- Familiarity with Lean manufacturing and Six Sigma methodology
- Ability to read and interpret detailed engineering data including customer specifications, and ISO Standards
- Knowledgeable in the use of scales, calipers, micrometers and other quality control equipment
- Knowledgeable in Safety area
63
Quality Supervisor / Engineer Resume Examples & Samples
- Respond to day to day technical concerns/issues in manufacturing environment
- Partner with manufacturing engineering to design the quality process for inspection of the part
- Create/review FAI and/or PPAP packages per A9102 or equivalent
- Review process changes or conformity to requirements
- Coordinate and perform RRCA to solve manufacturing process issues
- Responsible for communicating quality requirements to our suppliers on parts assigned
- Facilitate and prepare for external audits
- Interface with customers regarding quality concerns
- Supervise employees on 2nd shift
- The incumbent is an independent worker with strong technical capabilities and strong product/quality knowledge, which contributes to the total understanding of how to manufacture products with quality built into the process
- The incumbent also understands the quality requirements of parts under his/her assignment
- A strong ability to work in a team problem-solving environment is required
- The candidate must have knowledge of SPC and process control technologies. In addition, the candidate must have a thorough understanding of ISO 9000, AS9100, NADCAP, and Pratt & Whitney Quality Systems (preferred requirements)
- Experience with dimensional inspection, blueprint interpretation, and/or GD&T
- The candidate must have prior supervisory experience
- This candidate must have strong interpersonal and communication skills and the ability to facilitate and motivate teams
- Experience with SAP and other IT Quality systems desired
64
Quality Supervisor Resume Examples & Samples
- Actively engaged support in planning, defining and directing the site auditing control program to ensure compliance to all procedures, and policies, GMP standards, Mondelez requirements, and regulatory, federal and local laws
- Trains, mentors and leads site QA and Production team to insure program goals are met. Strong support to site QCMS/ISO program owners. Monitors and maintains plant QCMS program by complying with current Mondelez and International Audit (FSSC/ISO) standards. Facilitate and co-lead site cross functional QCMS Team and participate with Mondelez corporate to insure successful certification for site
- Lead and train Trace/Recall ensuring SAP and written compliance with Mondelez Special Situations Management and audit requirements
- Supports annual verification of all HACCP plans or when required due to project changes
- Support all internal and external inspections/regulatory visits. Support audit preparation activities, accompany inspector, and complete necessary reports and postings
- Support QM Pillar functions and lead MSA/line certifications
- Manage Pathogen and Non-Pathogen Environmental testing program facilitating trending analysis ensuring compliance with Mondelez and FSMA requirements
- Insure proper construction procedures are followed to meet site/Mondelez Food safety requirements. Takes appropriate steps to assure successful project startups
- Support for Hold/Release documentation and dispositioning of products
- SAP Quality Data Steward role and maintaining compliance
- Responsible for maintaining/validation/continuous improvement of all laboratory testing and equipment
- Facilitate plant sanitation. Coach and audit production on santiation practices
- Manage and direct Environmental Healthy and Safety (EHS) crew to ensure facility cleaning is completed. Maintain facility cleaning database to ensure cleaning routines stay on track. Create plans to continuously drive improvement and to mitigate any gaps
- Support and/or lead Quality functions as directed by the Quality Manager and Compliance Manager
- Bachelor's Degree in Food Science or equivalent degree
- Strong leadership, technical, communication and organizational skills required along with attention to detail. Previous experience managing people. Experience within a union facility is a plus
- Effective communication skills (oral written and verbal)
- Successful candidates must posses a positive focus toward solutions with emphasis on preventative pro-active measures and team-building
65
Quality Supervisor Resume Examples & Samples
- In addition to fulfilling all requirements of a Quality Technician, the Quality Supervisor has responsibility for direct supervision of the Wylie and Terrell Plant quality lab and supports other CCW plants as needed
- Perform correct action investigations, determining root causes and definition corrective action measures
- Identify process and product deficiencies
- Provide process improvement know how, methods and conceptual expertise to teams
- Leadership responsibilities including: scheduling of lab manpower, including overtime, taking initial steps to address job performance issues with Quality Technicians, coordination of job activities, identification of training needs for lab personnel
- Ensure product, process quality, cost, safety, and customer delivery goals are met
- Serve on task forces consisting of cross-functional teams to improve efficiency and performance
66
Quality Supervisor Resume Examples & Samples
- This role is responsible for monitoring and maintaining the plants Quality systems to ensure compliance to regulatory, federal and local laws. Areas of focus will include the identification and achievement of facility Quality KPI's through appropriate corrective/preventive actions and continuous improvement initiatives. This role will actively participate in all internal and external auditing activities and follow-up. Further, this role will act as support for QCMS/ISO; QRMP and HACCP functions will lead the development of new quality systems/programs across the facility and will provide Quality support/resources for major commercialization projects
- Train site on proper inspection procedure practices. Assist in insuring facility is inspection ready at all times. Provide Quality/Sanitation support for project commercialization
- Responsible for Hold/Release documentation and dispositioning of products
- Support and/or lead Quality functions as directed by Technical Services Manager
- Bachelor's Degree in Food Science or equivalent degree, preferred
- Successful candidates must possess a positive focus toward solutions with emphasis on preventative pro-active measures and team-building
67
Quality Supervisor Resume Examples & Samples
- Monitor performance and efficiency through timely reporting of quality metrics / internal and external objectives
- Handling customer complaints, collect, analyze and report data on nonconformity provide actions and root cause
- Set activities to achieve the goals set by management
- Define quality improvement projects for cost savings
- Monitor and maintain the First Pass Yield and PPMs process according to the established goals
- Ensure that production is carried out according to the Quality System Plant, nonconformity report
- Generate (PFMEA, process control plans and flowcharts)
- Provide monthly updates metric area to plant management
- To assist the Quality Manager and Production Manager assigned area, as instructed
- Verify compliance testing, measuring and control charts correct filling
- Assist in reducing rejects and rework in the production area
- Implement corporate quality initiatives
- Monthly Performance Monitoring and annual performance evaluations subordinates
- Lead together in conjunction with other departments to resolve problems reported in the process
- Perform other work-related functions as assigned ratings
68
Quality Supervisor Resume Examples & Samples
- Develop a culture of compliance to ISO/TS 16949 requirements through development of an internal auditing team as well as administering Corrective Action Requests for root cause analysis and corrective action for quality system non-conformances
- Lead a team of technicians to enforce our requirements to ISO/TS 16949 as well as to serve the campus in the area of document control
- Work with customer quality manager to implement customer specific requirements on the campus
- Work with regional quality systems leadership to commonize our practices and procedures across the Americas region
- Provide guidance to the value streams for change control decisions relative to compliance and customer notification. Work as a leader on the campus in the PDMLink application
- Support digital factory initiatives on the campus as it relates to implementation of our quality system
- Bachelor’s Degree required in a related field to Quality in an automotive manufacturing environment along with at least 3-5 years of experience in the industry
- Excellent presentation skills in addition to written and verbal communication skills required
- ISO/TS 16949 lead auditor certification preferred
- Lean Six Sigma Green Belt or Shainin Red X Journeyman a plus
- Strong knowledge in APQP documentation integrity preferred
- Working knowledge of molding, stamping, plating and assembly processes a plus
- Good computer skills with a working knowledge of SAP, Word, Excel and PowerPoint
69
Plant Quality Supervisor Resume Examples & Samples
- Prepare, review and perform performance appraisals. Confidentiality of all personal data is strictly maintained
- Must be capable of collecting and correlating relevant data that pertains to the overall efficiency and effectiveness of the department. Assessing trends through generated graphs and charts. Maintain continuous improvement project tracking and report out status monthly
- Management and Customer service representative for Technical Specification (TS16949)
- Minimum completion of a post-secondary education program in mechanical/quality engineering and minimum of 5 years related experience in the quality field
- S.Q.C certification as a quality engineer preferred
70
Quality Supervisor Resume Examples & Samples
- Assist the Quality Assurance (QA) Manager and provide direct supervision for the coordination and maintenance of all company Quality and Food Safety standards
- Effectively lead, develop, train, and evaluate QA Technicians and Microbiologists to maintain or improve skill competency. Monitor and ensure the performance of Quality Staff to ensure operational and regulatory compliance. Build bench strength through active development of direct reports
- Responsible for continuous improvement activities
- Responsible for data analysis to include statistical analysis of laboratory and quality system data which include but not limited to market score reports, consumer complaints, nonconforming products, yield data, audit results, etc. Determine data trends and implement improvement to processes and/or procedures to improve KPI’s associated with Quality
- Provide direct supervision to ensure sound calibration and validation programs for all Quality Lab instrumentation
- Responsible for the development, maintenance and full implementation of new methodologies and procedures to support Chemical and Microbiological Lab operations
- Along with the Quality Manager, liaise with internal and external auditors during Quality, Food Safety and Regulatory audits
- Responsible for full implementation of all Quality initiatives to reduce wastes associated with sample process flow, batching procedures, sanitation procedures, etc
- Perform administrative functions such as scheduling Quality staff to ensure 100% support to operation, perform SAP transactions, and ordering of lab materials
- Provide technical support/guidance to shop floor for problem solving of raw & package, product, and process deviations. Assist in the writing of technical laboratory & best practice (SOP) and package test procedures
- Monitor the implementation and integration of relevant Quality Assurance programs into plant operations, which ensures compliance to company and regulatory standards specific to Food Safety, Quality, sanitation, and process control. Review and maintain daily HACCP, QA audit, and production records as part of the audit function
- Train, support, and initiate Best Practice on Line Quality activities, leading to strong shop floor operator driven quality control
- Perform investigations and troubleshooting activities with regard to Quality Holds, microbiological contamination issues and process deviation
- Develop and maintain in house microbiological testing protocols. Evaluate new technologies, and coordinate aseptic process audits and related microbiological activities, providing strong technical support of the aseptic process
- Able to handle stressful, fast-paced and rapidly-changing environment
- Prior exposure, training, or experience in Visual Workplace Management, 5S, LEAN Manufacturing, Six Sigma, GMP, GSFI, SPC, and Process Capability Studies
- Working knowledge of MS Outlook, Advanced Excel, Word, PowerPoint, SAP, InfinityQS, Minitab, Visio
- Must be able to multitask and have excellent time management and organizational skills
- Effective training capabilities as well as excellent oral and written communication skills
- Dependable, detail-oriented, good problem-solving abilities, and strong commitment to teamwork
- Bachelor’s degree in Chemistry, Biology, Food Science, or science-related field
- 5 years’ previous quality experience
- 2 years’ prior supervisory experience
- Knowledge in HACCP (Hazard Analysis Critical Control)
- Flexibility and willingness to work off-shifts and weekends as business needs dictate
71
Quality Supervisor Resume Examples & Samples
- Excellent written and verbal communication skills. Ability to successfully interface with employees, department managers, supervisors, engineering, and customer quality representatives
- Proven track record and/or ability to supervise skilled employees. Commitment to achieve group cohesiveness
- Support Quality department objectives, maintaining quality and improving processes
- Technical Support for ISO 9001:2008 certification and audits
- Quality lead in factory FMA activities
- Support TEOA initiatives
72
Quality Supervisor Resume Examples & Samples
- Provides technical guidance & works closely with Regional Quality, R&D, & local Manufacturing & Distribution on major new product introductions & acquisitions
- Represents plant to regulatory agencies
- Selects, trains, develops, retains & manages associates
- Works cooperatively with Plants, Distribution, Engineering, R&D & Regional Quality to identify root causes of quality issues & implement processes to resolve & prevent issues
- Generates & implements ideas that improve quality indicators, in line with cost, investment & service goals
- Implements Quality System & ensures raw materials, packaging materials, finished goods & distribution activities meet specifications
- Leads internal & external audits & provides training on auditing tools to associates
- Sets up & administers audit system for internal & external providers of products
- Bachelor’s degree Chemistry, Chemical Engineering or related scientific area
- Minimum 2 years of experience required, including experience working with or in a manufacturing/plant environment
- Immigration sponsorship not available for this opportunity
- 4+ years experience with 3 + years experience in consumer product industry, regulated production or similar manufacturing environment & related Supply Chain or R & D function
- Strong written & oral communication skills and experience with ERP and electronic specification systems
- Expertise in ISO 9001, GMP & in managing quality improvement projects
- Lean Six Sigma Green Belt certification
- TPM experience or knowledge
73
Site Quality Supervisor Resume Examples & Samples
- Supervise and develop site quality staff; including technicians, engineers and documentation control
- Oversee and provide guidance to key quality processes such as CAPA’s, supplier/internal audits, calibration system maintenance, quality engineering, and customer complaint handling
- Maintain quality systems to ensure compliance to FDA regulations and ISO requirements, as well as compliance with the TFX quality system
- Represent quality for new and existing product improvements; support protocol, procedure and specification development
- Work cross functionally with site and OEM counterparts to support the business while maintaining the integrity of the TFX Quality System
- Represent Quality for new and existing product improvement, manufacturing transfers, and quality plan initiatives. Support protocol, procedure and specification development
- Complete special assignments as assigned
- Bachelor’s Degree or equivalent combination of education and experience. Education preferably in an engineering or related technical field (industrial, mechanical, chemical, etc.)
- 5 years related experience in quality management systems
- Previous supervisory or team lead experience required
- ASQ CQA or CQE preferred
- Engineering experience in manufacturing operations including new product development, cost reduction, and quality engineering
- Knowledge in metal fabrication, plastics, extrusion, mechanical assembly and world class manufacturing desirable
- Ability to coach and supervise a team
- Knowledge of Regulatory, cGMP, and QSR
- Statistical knowledge (DOE, SPC, hypothesis testing, sample comparison)
- Proficient in Computer applications (i.e. data-base development, statistical software and analysis, word processing for report generation, etc.)
- Negotiation and problem solving skills
- Ability to operate and communicate effectively within a matrixed organization
- Ability to audit suppliers (i.e. ASQ-CQA, internal/external courses, seminars)
- Able to understand blue prints, tolerance analysis and related knowledge
- Reasoning ability, support and prioritize projects, adapt to shifting priorities, work with minimal supervision, able to resolve problems and conflicts
74
Quality Supervisor Resume Examples & Samples
- Manage and oversee project quality to ensure compliance to codes, standards, regulations, equipment specific specifications, and QMS requirements
- Advancing quality achievement and performance improvement throughout the organization
- Managing the development and implementation of the QMS for planning, fabrication, inspection, documentation, and operations activities including
- Minimum of 10 years of quality inspection experience on pressure equipment
- Petrochemical or oil refining plant owner / user organization work experience
- Certifications in API 510, 570, or AWS-CWI or ability to obtain
- Advance knowledge of qualifying ASME WPS and welder/welding operator qualifications, including local regulation requirements
75
Quality Supervisor Resume Examples & Samples
- Define standards for quality in close collaboration with all other departments of the plant (Management, Production, Technical, Health & Safety, Finance and IT)
- Establish the company's quality procedures, standards and specifications in collaboration with operating staff
- Design and maintain controls as well as documentation of quality procedures
- Monitor performance by gathering relevant data and producing statistical reports
- Assessing product specifications against defined parameters
- Accurately identify/review requirements and expectations of existing or potential customers while providing confidence that quality requirements will be fulfilled or exceeded
- Anticipate changes in customers’ expectations over time and determine action plan to meet these changing expectations
- Responsible for supporting the development and maintenance of a customer-focused culture
- Ensure compliance of manufacturing processes with international and national standards
- Propose suggestions for changes and improvements as well as provide guidance for implementation
- Champion, support or lead quality improvement initiatives while ensuring that all stakeholders develop and maintain their part of the quality management system based on agreed in-house standards
- Publish statistics regarding company performance against set measures to monitor performance
- Develop the quality goals and targets in the according to organization’s strategic plan
- Supervise planning and activities related to internal and external auditing (ISO certifications)
- Liaise with other managers and staff, particularly in areas such as design, production and purchasing
- Consider application of environmental and health and safety standards
- Ensure tests and procedures are properly understood, carried out and evaluated and that product modifications are investigated if necessary
- Prepare technical and management system reports
- Manage the Quality Steering Commitee
- 10 years of experience as technician in Quality and ideally working within Glass Quality Management
- Manufacturing background in a Glass Making industry
- Experience in managing external suppliers and partners
- ISO Certification
- Dynamic, high energy leadership skills and effective communication skills with a collaborative approach to problem solving
- Collaboration skills – Able to effectively collaborate with peers in other functions and with colleagues in other businesses or divisions
- French native speaker as well as perfectly fluent in English
76
Quality Supervisor Resume Examples & Samples
- Non conforming quality processes
- Quality initiatives with the Caterpillar Quality Management System (CQMS)
- Conducting and reporting internal quality audits for all CAV Core inspections processes
- Supports Supplier Certification programs both internally and externally
- Providing support for corporate quality related programs
- 4-year University degree in an Engineering or Manufacturing related discipline
- Experince with BIQ, APQP, and / or CQMS deployment
- Prior supervisory experience in a quality / manufacturing role
- Experience in a technical quality related role
77
Watson Bowman Acme-quality Supervisor Resume Examples & Samples
- Sample, measure and verify manufactured products meet pre-determined quality standards. These quality standards can include ISO
- Represent the "face of quality" and our representative to state agencies, consultants, and contractors
- Perform or oversee quality inspections and/or staff to complete physical inspections throughout the fabrication process
- Document and maintain all quality control files and records for AISC and ISO conformance
78
Quality Supervisor Resume Examples & Samples
- Supervises the inspection department ensuring product is inspected in a timely manner without sacrificing quality
- Manages production inspection and receiving inspection
- Develop and review quality instructions and methods for inspections and testing
- Manages inspection audits and follow-up with corrective action
- Ensure timely and effective responses to customer quality issues
- Associate Degree or equivalent from a two-year college or technical school and 3 or more years experience with inspecting parts. Experience in automotive manufacturing preferred
- Must have strong leadership ability (2 years previous experience supervising is desired) and excellent problem solving skills
- Experience working in a QS9000/TS16949 environment is required
- Ability to utilize inspection equipment such as SPC, calipers, micrometers, CMM, Vision Systems and other measuring devices
- Ability to organize and prioritize work
- Must be proficient in MSWord, Excel, PowerPoint. Some Access experience preferred
79
Field Quality Supervisor Resume Examples & Samples
- To manage all area pass certified government test
- To work with government and Field Supervisor to handle field area pass quality
- To make sure internal document and external document walk in procedure
- To ensure the quality standard are meet (Isolation; Detaselling; Rogueing; Male Cutting, Harvesting)
- Make and send weekly and monthly update report (planting up date, detaseling, rouging, male cutting harvest and reports)
- To coordinate all Field Inspector each area
- Achieve agreed quality in field levels
- Achieve field certification from government
- Good relationship with contact at field production and plant certification
- University degree of science in Agriculture
- Language (site or country) plus English
- 2 years experience production process in agriculture
- Build good relationships with grower, vendor and BPSB
80
Quality Supervisor Resume Examples & Samples
- Ensure processing, tolling and channel quality activities are controlled by quality manual, procedure and work instruction
- Implement QMS in accordance with APAC quality management guidelines
- Monitor quality data uploading in FOU, coordinate to fix system’s issue
- Document results of all QC inspections and communicate results to cross functional teams
- Track and maintain non conformity inventory by quality data
- Audit distributor’s returns to ensure items are fit for resale
- Maintain quality specification, fit for customer and legislation requirements
- Audit and assist third party to compliant with Syngenta quality standard
- Generate and report Quality KPI
- Capability to understand operational processes focused on integrated product offers (Seeds & CP)
- Certifications an advantage including Quality Auditor, Quality Engineer, Quality Improvement Associate, Six Sigma
- Experience in assessing a situation, identifying issues and developing solutions that result in efficiencies and/or process improvements
- Experience with implementation of corrective and preventive action programs
- Successfully demonstrated ability to coach others with a strong self-awareness (both strengths and opportunities) and ability to self-develop
- Ability to adapt to change and work flexibly to overcome boundaries
- Strong project management skills with the ability to work independently and within a team
- Ability to adjust work schedule based on business requirements
- Knowledge of relevant regulatory requirements
- Bachelor’s degree from a four-year College or university in specific or technical fields of Biological Science, Agriculture or other relevant fields
- Minimum of 2 years’ experience in quality control in seed processing or in consumer goods manufacturing
- Possess a broad understanding of Seed Quality Control processes and Quality Management System
- Basic principles of biology, biotechnology, agriculture, seed production and quality control, Principles of Quality Assurance, QMS/ISO 9000
81
Quality Supervisor Resume Examples & Samples
- This role is responsible for monitoring and maintaining the plants Quality systems to ensure compliance to regulatory, federal and local laws. Areas of focus will include the identification and achievement of facility Quality KPI's through appropriate corrective/preventive actions and continuous improvement initiatives. This role will actively participate in all internal and external auditing activities and follow-up. Further, this role will act as support for QCMS/ISO; QRMP and HACCP functions will lead the development of new quality systems/programs across the facility and will provide Quality support/resources for major commercialization projects
- Trains, mentors and leads site QA and Production team to insure program goals are met. Strong support to site QCMS/ISO Coordinator. Monitors and maintains plant QCMS/QRMP program by complying to current Kraft Heinz and International Audit (FSSC/ISO) standards.Facilitate and co-lead site cross functional QCMS/QRMP Team and participate with Kraft corporate to insure successful certification for site
- Supports and followsproper plant safety policies and procedures
- Effective communication skills(oral written and verbal)
- Must be able to work shifts, weekends, and all required overtime. Prompt and regular attendance
82
Quality Supervisor Resume Examples & Samples
- Responsible for the supervision and scheduling of Quality Assurance and Sanitation staff
- Responsible for implementation, review and verification (as directed) of the facilities food safety, quality and sanitation programs in support of current legal, Kerry and customer requirements
- Responsible for supporting BU Kerry Quality Projects
- Responsible for supporting plant QIP, SIP and CI initiatives
- Supervision of Quality Assurance and Sanitation staff. This includes scheduling (electronically and physically posting), approving time records, providing constructive periodic evaluation, goal setting, training, counselling, and performance documentation
- Responsible for conducting training with all plant staff
- Responsible for maintaining training matrix and sign off records (electronically and physically.)
- Responsible for becoming site LIMS point of contact (Maintain files of test results and product dispositions. Supports QA Technicians and Analyst in resolving IT based errors with Corp. LIMS team)
- Provide technical support for resolution of quality problems with operations
- Maintain and update product specifications including customer specifications and raw material specifications to reflect any changes or product use requirements. Ensure finished product and raw materials are tested per Kerry specification. Monitor test results in relation to these specifications
- Development and adherence to Quality SOP’s
- Support the plant Food Safety & Quality System to produce safe quality food
- Functions as backup PCQI. SQF and HACCP Certified (or trainable)
- Order QA and Sanitation Supplies; support the purchase of supplies for other departments in absence of Supervision
- In conjunction with the Quality Manager, update and support food safety programs and food safety systems: FSMA, sanitation, and environmental monitoring program. Maintain the quality systems for the plant. Ensure work instructions, SSOPs, procedures and other pertinent documentation is up to date. Recommend revisions plant work instructions as needed
- Facilitate as directed: quality complaint investigations. Verify corrective action completion and continued conformance
- Conduct and participate in internal audits while ensuring compliance to internal quality policies and applicable local regulations through the audits, observations, process reviews, and development of corrective actions with site management
- Participate in external audits, with the eventual goal being to facilitate them in absence of QATM
- Support facility during inspections, customer audits, communications, commercialisations, and other interactions with regulatory agencies or customers
- Provide technical assistance to quality assurance and operations
- Enter Work Orders in MVP System
- Participate as a leader in facility safety programs
83
Quality Supervisor Resume Examples & Samples
- Responsible for supporting quality functions including food safety systems and programs along with compliance
- Leads and supervises quality staff. This includes scheduling, approving time records, periodic evaluation, counselling, and performance documentation. Responsible for conducting departmental and job specific training
- Conducts laboratory analyses and investigations
- Provides technical assistance to quality function and operations
84
Quality Supervisor, Rochester Resume Examples & Samples
- Coaches and mentors Quality team to strive for laboratory excellence. Ensures Quality team is appropriately challenged with meaningful and cross-functional project work to support QC and site objectives. Guides the development of strong communication and collaborative skills within the group
- Works with laboratory leads and QATM to identify and foster talent within the group and to position roles and responsibilities strategically. Ensures all group individuals are supported in their personal development plans
- Responsible for establishing working schedules, ensuring adequate laboratory coverage and approving timecards
- Maintains role as primary point of contact for communication to and from Quality laboratories
- Oversees performance, interpretation and evaluation of QC test results and makes recommendations
- Gives input and assists in the development of QC procedures, policies, and philosophy
- Ensures that products and QC practices are in compliance with Kerry policies and local, state, and federal regulations
- Ensures that a current, maintained, and documented system is in place and trained to all pertinent personnel for incoming raw material control, evaluation, COA & COC documentation, and release for use
- Ensures that a current, maintained, and documented system is in place and trained to all pertinent personnel for intermediate powder material control, evaluation, documentation, and release for use
- Ensures that a current, maintained, and documented system is in place and trained to all pertinent personnel for outgoing finished good material control, evaluation, COA, COC, other shipping documentation, and release for sale
- Provides input on relevant QC issues
- Promotes and works in a team environment. Is an active participant in all QC activities
- Enforces and supports GMP policies by leading other quality staff through full plant GMP periodic inspections. Ensures the plant inspection method is documented and communicated to proper personnel
- Maintains skills and knowledge base in QC methods. Maintains knowledge of relevant chemistry & microbiology methodologies
- Provides back up to Quality Manager functions
- Responsible for development, implementation, and enforcement of GLP practices to align with Kerry standards, Industry best practices, and continuous improvement goals
- EDUCATION: Bachelor's degree in Microbiology, Chemistry, Food Science, or related fields
- EXPERIENCE: 3+ years experience in a food Chemistry, Microbiology or Food QC lab setting
- SKILLS Knowledge in QC laboratory methodologies and quality systems is required. Knowledge of current GMP. HACCP Training. Allergen awareness. Must be computer literate. Incumbent must have excellent interpersonal skills, including both verbal and written communication and the ability to lead and work in interdepartmental teams. The work is self-directed and requires the ability to work without close, direct supervision utilizing good organizational techniques
85
Quality Supervisor Trainee Resume Examples & Samples
- Directs and advises personnel in the special test procedures to analyze components and physical properties of product materials
- Compiles and analyzes test information to determine operating efficiency of process or equipment and to diagnose malfunctions
- Tests and analyzes sample products, adjusting formulas and processes based on results
- Prepares test solutions, compounds, and reagents for use by laboratory personnel in conducting tests
- Investigates complaints on existing products and responds to vendor or customer
- Establishes or adjusts work procedures for products and raw materials and maintains test equipment
- Develops and recommends test procedures for products and raw materials and maintains test equipment
- Analyzes and resolves, or assists workers in solving work problems
- Maintains time and testing records, reporting monthly
- Trains lab group on safety topic, quality procedures and business updates for the month. Other duties may be assigned
- Participates in other plant teams and programs such as Aged Inventory Control Team, Self Inspectors Team, HACCP Team, and others assigned
- Knowledge of food safety principles and food process, eg. Exposure to HACCP, GMPs
- Presentation, communication skills and confidence, demonstrated by ability to ask meaningful questions and clearly articulate experience, good non-verbals, and experience interpreting and acting on info/data and/or leadership roles
- Strong science foundation demonstrated by time in lab (volunteering, research experience) and coursework in chemistry, biochemistry and/or microbiology
- Inquisitive nature that enjoys problem solving and identifying business improvements
- Demonstrated interest in being hands-on in a manufacturing environment, e.g. internship experience, seeking out opportunities to learn about manufacturing
- Ability to understand results or impact, make quick, accurate and sound decisions based on results
- Employees must have reliable means of transportation to and from work
86
Quality Supervisor Resume Examples & Samples
- Accountable for ensuring full quality and regulatory compliance while driving process effectiveness and efficiency at the site
- Ensures site audit readiness and host the Quality System audits and executes Quality Management System reviews
- Owns site compliance assessment and remediation, leads communication and training requirements for Quality matters
- Review standard operating procedures for company directives and compliance
- Responsible for site education of non-Quality Assurance personnel, responsible for professional development of the site Quality Assurance team
- Monitor, control, and analyzes product and process quality to meet internal and external customer requirements
- Determine through statistical data continuous improvements projects
- Partner with production in detecting root causes for defects during production phases
- Work with management staff in analyzing data for purpose of developing and implementing preventative measures to limit or eliminate quality defects
- Communicate quality goals and requirements by preparing and disseminating standards, metrics, standard operating procedures (SOP) management, and vendor document and production record guidelines
- Improve quality compliance by recommending and following-up on improvement plans, writing training courses, contributing information to cross-functional quality improvement teams
- Prepare quality assurance reports by collecting, analyzing, and summarizing data and trends
- Establish quality metrics for the operations that drive awareness, action, and continuous improvement in quality daily
- Facilitate Lean process improvement opportunities throughout the plant and be the plant ambassador for quality and process excellence
- Responsible for site RMA/RFC process to include evaluation, processing, and corrective actions and disposition
- Bachelor’s degreed preferred (or Associate Degree plus 4 years practical experience)
- Minimum of 4 years experience and understanding of a quality production environment
- Spanish preferred
- Supervisor or Manager experience in a work environment with proven quality processes
- Six Sigma or Lean GB certification highly desired or ability to attain within 1 year
- Certified Quality Manager (CQM) or Certified Quality Auditor certification from ASQ highly desired or ability to obtain within one year
- Strong presentation and facilitation skills
- Subject matter expert (SME) on all Quality Inspection & Audit process with defined CARS and remediation to drive performance optimization
- Excellent understanding of Quality Management Tools to include Six Sigma, Statistical Process Control, MS-Excel, Visio, DOE, DFR, etc
- Ability to multi-task & handle task with competing priorities
- Microsoft office programs including MS-Excel, MS Word, and MS Power-Point, MS Access or comparable programs
- Demonstrated ability to lead, acknowledge, develop people and implement a strategy under crisis situations to ensure compliance
87
Quality Supervisor Resume Examples & Samples
- Execute a multi-year quality improvement plan to climb the value chain from Quality Control to Quality Assurance to Excellence
- Set quality expectations of the organization to satisfy the requirements of our customers
- Direct policy and procedure for inspection and testing activities to ensure continuous control over materials, facilities, and products
- Oversee deployment of standard Generac quality tools (Generac Quality Management System), methodologies, standards, practices and processes
- Direct root cause investigations addressing internal failures and customer complaints; facilitates corrective actions
- Present quality metrics and analysis regularly to senior management team and external customers
- Facilitate communication and interaction between team members and other areas resolving differences and/or conflict situations effectively
- Define resource needs and work within budget and staffing parameters to accomplish objectives
- Support changes in procedures, process, technology, responsibility and assignments
- Coach and develop staff. Set clear expectations to inspire and motivate the team
- Manage performance-- recognizing achievement, providing feedback and administering progressive discipline
- Act as SAP Super User within functional area
- Bachelor’s Degree in Engineering, Business or Industrial Technology OR 8 years related experience in the Operations function within a similar working environment
- 3 years of Quality Management System experience
- Proven track record of successfully managing shifting deadlines and priorities in a fast paced environment
- Ability to evaluate situations objectively and demonstrate the ability to make decisions that are intended to have a positive impact on work performance or area and the total business
- Ability to organize and prioritize work assignments in order to complete them on time
- Demonstrated skills in problem solving, contract negotiation and project management
- Strong project management and analytical skills
- Advanced degree, MS and/or MBA
- Certified Manager of Quality, Certified Quality Engineer, and/or Six Sigma
- Certifications: CHMM, CSP, CIH, or PE
- Previous experience using SAP or equivalent ERP
88
Quality Supervisor Resume Examples & Samples
- Responsible for overseeing the quality function with specific responsibility for the corrective action and preventive action (CAPA) and risk management processes
- Coordinates workflow for quality projects assigned to the specialists
- Ensures the maintenance of quality records on product testing, nonconformance, project outcomes, and that stakeholder input is filed in an accurate and timely manner
- Reviews and audits change control documentation and tracks the approval process
- Contributes to the development of corrective action plans and monitors implementation
- Reports on closure of corrective and preventive actions
- Monitors and leads investigations, recognizes trends and presents reports for assigned quality processes
- Reviews reports on current quality systems and supports improvements in order to enhance quality and reduce cycle time
- Assures preparation for audits and inspections
- Monitors trends, identifies issues, recommends and implements appropriate actions
- 2 years+ experience in Quality Assurance within Pharmaceutical, Medical Devices or FMCG business
- Knowledge of GMP and GDP preferred
- It is preferred that the job holder is an experienced internal auditor or certifies lead auditor
- English on upper-intermediate level as a must
- Excellent interpersonal, collaboration, networking and communication skills
- Readiness for business tripsQuality (Generalist)
89
Quality Supervisor Resume Examples & Samples
- Provide audit and inspection coverage for all assigned departments on all shifts
- Establish and implement procedures and inspection /sampling methodologies
- Provide technical guidance and support to employees regarding inspection and measurement techniques
- Participate in internal, customer and agency audits
- Verify completeness and accuracy of inspection records and nonconforming material reports
- Responsible for investigation and closure of customer and field complaints
- Provide accurate technical information for engineering investigation and troubleshooting reports
- Conduct monthly department meetings and regulatory training as required
- Responsible for oversight of employee performance to maintain department standards in efficiency, productivity and accountability
- Provide recognition and constructive feedback through both formal and informal discussions
- Monitor and maintain operational integrity of instruments, gages and specialized measurement equipment
- Provide technical training and assistance to all assigned personnel
- Obey all safety rules and stop work if continuing will create an unsafe condition. Report all safety concerns immediately
- Perform other tasks as assigned by manager
90
Quality Supervisor Resume Examples & Samples
- Lead a team QA team members to achieve quality metrics in a manner consistent with our culture and values
- Partner cross functionally with the Planning, Production, and Warehouse teams to maximize results
- Facilitate the execution of changes and activities needed to support Nestle Continuous Excellence (NCE) and the pursuit of TPM
- Assist the QA Manager with leading all company Quality initiatives and Quality audits locally
- Track, analyze, and lead initiatives for all quality and customer complaint issues within the plant
- Ensure compliance and record keeping for all mandated quality checks, testing, sampling and sanitation activities
- Manage budgeting, purchasing and inventory of plant operating supplies such as filters, chemicals and lab supplies
- Use continuous improvement methodologies and projects to improve and streamline quality processes
- Ensure plant compliance to good hygiene practices, good manufacturing practices (GMP's) and HACCP
- Communicate new quality programs as needed and facilitate or support the training of plant personnel
- Offer expertise and assistance in managing the plant water sources and monitor over fill and water usage reporting
- Responsible for recording keeping requirements within the laboratory
- Bachelor's Degree in Chemistry or Biology or equivalent combination of education and/or experience
- Five or more years of experience in quality assurance within clean (food, bev, pharma) manufacturing and two or more years of experience in a supervisory capacity
- Prior experience in the consumer products industry or food and beverage with familiarity with quality and hygiene regulation necessary
- Understanding of quality testing and standards within the food and beverage industry to include analytical, microbiological and sensory
- Demonstrated application of Good Laboratory Practices (GLP's) and knowledge of GMP's
- Knowledge of Statistical Process Control, HACCP, sanitation, and hygienic design
- Familiarity with quality and hygiene regulations as it relates to CFIA and provincial requirements preferred
- Knowledge and exposure to Six Sigma, and various problem solving methodologies needed, TPM exposure preferred
- Strong computer skills, including Word, Excel, PowerPoint and business management software (SAP preferred)
- Ability to manage multiple projects and initiatives on tight deadlines and delegate accordingly
- Effective communication skills with the ability to influence change and encourage action
- Solid problem solving abilities with the ability to coach and mentor others in this capacity
- Demonstrated track record of developing employees
- Ability and willingness to respond to after hours calls for critical issues and provide weekend coverage as required
91
Quality Supervisor Resume Examples & Samples
- Maintain quality system policies and procedures and recommend improvements; interact with plant team members to achieve daily and long term goals; ensure plant policies are followed
- Assist in the development of control plans, inspection procedures, capability studies and sampling frequencies
- Develop quality initiatives to attain and maintain customer satisfaction and focus; may direct and support quality analysts in quality planning and auditing activities
- Provide technical expertise in quality techniques and services; develop, train and motivate team members to acquire maximum proficiency in quality fundamentals and manufacturing principles
- Support Quality Manager in customer issues: problem solving, root causes, corrective/preventive actions & verification
- Monitor communications and information systems to maintain awareness of new projects requiring planning, customer satisfaction and plant initiatives; utilize knowledge to proceed with proper responses and planning activities
- Perform full range of managerial responsibilities which may include but not be limited to: interviewing, hiring, coaching and developing employees; planning, assigning and directing work; EEO/AA; performance management; department budget
- Perform other duties and responsibilities as requested or required
- Thorough knowledge of quality practices and procedures including Quality Management System (QMS) and ISO/QS requirements along with track record of achieving and maintaining same
- Good knowledge of quality tools such as Statistical Process Control (SPC) with an ability to interpret and apply SPC information to plant processes as well as understanding of Design of Experiments, Failure Mode Effects Analysis, Advanced Product Quality Planning (APQP) tools including control plans, process FMEAs, etc
- Good interpersonal and written communication skills to communicate effectively with diverse groups of people; ability to solve practical problems and deal with a variety of personnel and quality issues/problems
- Basic knowledge of Geometric Dimensioning & Tolerances and blueprint reading
- Minimum of 3 years experience of related experience in engineering, purchasing or quality field; fundamental quality experience in machining or assembly type operations or equivalent experience preferred
- Enterprise wide reporting system experience preferred
92
Quality Supervisor Resume Examples & Samples
- 30%
- High School or GED with a minimum of 10 years general experience in manufacturing with 6 years specific experience in quality
- Or 2 year college (Associate Degree) with 6 year specific experience in quality
- Prior to a job offer being extended to a perspective applicant, the applicant will be required to pass a 3 step interview process, background check and a drug screen
- Good communication skills required (oral and written)
- Knowledge of equipment and production processes
- Ability to deal with personnel issues
- Experience to make good problem solving decisions
- Capability to interpret and evaluate information and apply judgment in setting priority , interpreting polices and establishing approaches
93
Quality Supervisor, Technical Services Resume Examples & Samples
- BS/BA degree in business or engineering (engineering preferred)
- Comprehensive understanding of quality managing system design and implementation, specifically ISO/TS16949
- Advanced knowledge of print requirement and metrology process linkage
- Demonstrated strong leadership and conflict resolution skills
- Effective verbal/written communication, human relations and organizational skills
- Use of computer technology for communication, organization and process management, specifically MS Office, MQ1, MS SharePoint, Minitab, SAP
- Superior problem solving skills
- Eight years experience in manufacturing processes, systems and tools
94
Quality Supervisor Resume Examples & Samples
- Identify, prioritize and initiate plans to achieve the operational goals of the laboratory
- Scale-up the cGMP laboratory to execute new test methods
- Actively participate in cross-functional teams and projects that have major importance to the site such as cycle-time reduction programs and new product introductions
- Manages costs within the QC laboratory department
- Leads QC Laboratory activities including technology transfer, continuous improvement and issues management
- Network with internal and external organizations in areas that relate to laboratory activities
- Train, counsel and guide peers and subordinates as required
- Bachelor's degree or higher in a Science, Technology, Engineering or Mathematics from an accredited institution
- Minimum of three (3) years of experience working in a medical device and/or pharmaceutical environment
- Bachelor’s degree or higher in Analytical Chemistry, Chemistry, Chemical Engineering or related discipline from an accredited institution
- Minimum of three (3) years laboratory experience in a cGMP environment
- Minimum of two (2) years supervisory experience
- Experience with LEAN Six Sigma methodology
- Statistical expertise
- Microsoft Office proficient, Minitab a plus
- Participated in/led Customer or Regulatory audits (GMP, ISO, etc.)
95
Quality Supervisor Resume Examples & Samples
- GreenBelt certified
- Significant knowledge on quality systems (EQS, ISO/TS 16949), significant knowledge on quality tools as CEP, FMEA, 8D, PPAP, ELSS, APQP and engine valves
- Competencies: Strong leadership, Capacity to work under pressure, Communication ability to deal with customers, Conflict resolution skills, Problem solving ability, Managerial courage and intellectual rigor
96
Quality Supervisor Resume Examples & Samples
- Bachelor’s degree from an accredited institution in an applicable field of study such as Food Science, Chemistry, Biochemistry, Microbiology, or similar Science/Engineering
- Knowledge of relevant GFSI standards such as SQF, BRC, IFS or FS 22000
- Knowledge and understanding of Food Safety regulations, FSMA, and industry and market trends
- Strong team leadership, communication, analytical and problem-solving skills
- Proven ability to demonstrate the following key competencies: Technical Expertise, Strategic Thinking & Influence, Process Optimization & Product Knowledge, and Leading & Managing Change
97
Quality Supervisor Resume Examples & Samples
- Facilitate/perform inspection of materials,processes, and products in accordance with quality standards and customerrequirements
- Monitor and report the status of plant andsupplier quality standards
- Assist in resolving manufacturing, supplier,and customer issues relating to satisfactory quality conformance
- Facilitate and assist in updating inspectioninstructions, procedures, gages, visual aids, test equipment, and customerdocuments
- Promote and facilitate “Best Practice” quality systems
- Facilitate the procurement, inspection, andcalibration of test equipment and gages
- Ensure proper verification and documentationcontrols are maintained and utilized
- Lead, motivate, and develop employees
- Promote and support a teamwork approach toachieving goals
- Ensure open and effective communications
- Maintain a work environment where third partyintervention is not required or desired
- Develops recommendations in standards, testequipment and gages to facilitate work and maintain quality
- Interacts with Operations to determine andresolve quality issues
- Identify and implement continuously improvedinspection methods in order to improve efficiency and effectiveness
- Develop and maintain the facility’s qualitymanual
- Coordinate the development and maintenance ofquality procedures and related documents
- Ensure uniform understanding and complianceby all personnel with the quality policy, procedures, and documentation
- Ensure effective documentation and controlsystems are developed, utilized, and maintained
- Identify non-conformance to qualityprocedures by leading internal audits or by coordinating customer or accreditedregistrar audits
- Ensure non-conformities are addressed in atimely manner by coordinating activities for assignment, containment,corrective action plans, and resolution and follow through
- Prepare and make presentations to customers,employees, and all levels of the management team
- Coordinate contract process for third partyregistrar
- Strong leadership abilities, including motivation and team building skills
- Thorough understanding of quality systems and standards (new quality techniques and technology)
- General understanding of Statistical Process Control (SPC)
- General understanding of Failure Mode and Effects Analysis (FMEA)
- General understanding of Production Part Approval Process (PPAP)
- Thorough understanding of manufacturing processes
- Strong blueprint reading skills
- Strong communication skills for both internal and external customers
- Strong problem-solving, organization and planning skills
- Good knowledge of health and safety systems and procedures
- Knowledge of the automotive industry and customers
- Good knowledge of related governmental laws and regulations Benchmarking
- Organization and planning skills
- Problem solving skills (DOE, Painters chart, Fish Bone)
98
Quality Supervisor Resume Examples & Samples
- Designing, developing, implementing, documenting and monitoring business management systems to ensure facility compliance with ISO9001. This includes providing vision, direction and planning for the "future state" (3-5 years ahead) of the facility Management system
- Advising Senior Facility Management on the business policies, processes and procedures required to support the quality management system
- Advising and supporting Health, safety and environmental Management system performance. This includes the coordination of internal audit processes for Occupational, Health, Safety Management System (OHSMS) and Environmental Management System (EMS)
- Managing and developing functional aspects of quality department to achieve best practice performance. These areas include MQ12005 and MQ13005 internal certification, contamination control requirements and incoming Quality Inspection
- Managing the auditing of planned methods, process outputs, report internal & external quality metrics relative to product defects or problems
- Acting as an advisor or consultant to senior management
- Serving as a companywide resource on a highly specialized area or serve multiple units in a broader functional area and assist senior management in interpreting and using information provided
- Engineering or manufacturing background
- Expert knowledge of a specific manufacturing process or engineering discipline, or maintenance process, as applicable
- Complete understanding of company policies and procedures related to manufacturing, engineering and/or maintenance
- License or certification: ISO Lead Auditor trained and qualified
- Five to ten years of job-related experience
- Good human relations skills are required to develop a cooperative work relationship with others inside and outside the department
99
Quality Supervisor Resume Examples & Samples
- Supervise Quality Inspectors at plant site
- Perform and/or assists with internal audits
- Support customer and 3rd-Party quality audits, visits and certifications
- Analyze audit findings and support site and corporate corrective action process
- Make recommendations or participate in problem solving teams to improve the efficiency or effectiveness of the Quality and Manufacturing Systems
- Support generation and analysis of process and product metrics
- Mentor and Lead site TCBA initiatives
- Bachelor’s Degree and 3-5 years experience within the Aerospace industry, or the equivalent in training, education and experience
- Working knowledge of Integrated information systems
- Knowledge of LMI processes and customer base
- Ability to effectively present information and respond to questions one-on-one from groups or individuals
- Ability to solve practical problems, utilizing standard operating procedures
- Ability to interpret information furnished in written, oral and/or diagram form, to determine the best course of action among various alternatives
100
Quality Supervisor Resume Examples & Samples
- Work out PQIP for new and transferred product
- Review production quality status of on-line daily
- Continuous improvement of process, include rework, sorting, product trace ability etc
- Feedback customer complaint and take a leadership for internal corrective action
- Monitor site performance to goal. Facilitate corrective actions as needed
- Facilitate disposition of non-conforming material
- To manage QC inspectors
- Oversee site QA functions
- Create new and maintain existing inspection visual inspection standards
- Provide engineering, quality system, metrology and TQM support to improve processes
- Internal quality systems auditor
- Obtain and implement new technology for improving the quality system
- Early involvement for the new project, finish the HUDDLE list items timely
- Take the leadership for the product group team of quality handling
- Bachelor’s degree in Engineering, Technical Field or Business, Masters Degree preferred
- Minimum of 3 years related experience in Quality and/or Manufacturing
- Two plus year’s Supervisory experience and working with Quality systems
101
Quality Supervisor Resume Examples & Samples
- Manage the auditing of planned methods, process outputs, report internal & external quality metrics relative to product defects or problems
- Support the BIQ process using root cause and data analysis
- Create and manage quality gate inspection instructions per established guidelines to maintain operator awareness, without impacting velocity
- Monitor IPV performance and coordinate containment and resolution activities to address problems
- Lead and support CPS continuous improvement activities
- Support investigation, resolution and prevention of Customer issues, and other quality concerns
- Engage Product Engineering group to identify and implement product design changes to improve quality
- Two year associate degree or a minimum of 2 years completed from a 4 year bachelor's degree
- Extensive knowledge of PLEX and Shop Floor Manufacturing Processes
- Experience working in a manufacturing environment using SPC and data analysis
- Understanding of blueprints, GD&T, and Measurement System Analysis (MSA)
- Broad knowledge of manufacturing and assembly procedures (machining, heat treat, assembly and inspection) planning processes, work standards relative to manufacturing and inspection and a thorough background in statistical quality control data and gaging specifications
- Good analysis, diagnostic and judgment skills
- Good computer skills
- Advanced proficiency in the Caterpillar Built in Quality (BIQ) Process
- Advanced proficiency on PFMEA
- Knowledgeable with facility product and manufacturing process
- Advanced proficiency in the use of Plex Quality Menu
- Advanced proficiency in using HVC and / or EPIX
- RCCA certification
- Six Sigma Green Belt certification
102
Quality Supervisor Resume Examples & Samples
- Develops systems and processes that adhere to Aerospace requirements such as AS9100, and customer requirements in a manner that ensure compliance with Four Gears Culture, Procedures and Ethics requirements
- Ensures quality through management of the assembly and spare orders flow lines through metrics of operations such as quality, QCPC, COPQ, on-time delivery and audits, developing plans for process development through continuous improvement tools and Corrective Actions
- Acts as a liaison between team members and other functional areas
- Typically requires management and training of inspection processes
- Adhering to budgetary constraints
- Manage through continuous improvement of systems, processes and policies using lean tools
- Travel required - 10%
- Bachelor’s Degree in Business, Engineering or related field preferred
- Minimum 2 years related work experience in a manufacturing environment
- Understanding of lean principles, six sigma and or statistical process control
- ASQ, AS, Black Belt or Lean Certification preferred
- Must be able to verify U.S. Person status as defined by International Traffic in Arms Regulations (ITAR)
103
Quality Supervisor Resume Examples & Samples
- Conduct Quality Control Training in Producers
- Check / Audit the processes of Quality Control to Field performed by the Producer and / or Production Area / Parent Seeds Syngenta
- Establish and guarantee the process of collecting samples and sending them to the analysis sites, and that is performed according to the procedures and within the established deadlines
- Assemble, align and guarantee the execution of the quality analysis plan with the Own and External Seed Analysis Laboratories (Network of Third Party Laboratories), checking and guaranteeing the accuracy of the information
- Conduct inspections / audits, with a focus on Quality, in the processes of processing Seeds, treatment and packing, and in the warehouses, and give the appropriate treatment in cases of deviations
- Guarantee the classification of lots in the control system of Syngenta
- Represent the Quality area in internal and external Meetings and Alignments as needed, and interact with the areas related to Syngenta seed processes
- To fulfill customer complaints, in the case of seeds not planted and that are linked to physiological quality or varietal purity
- Interaction with the other departments of Syngenta that are part of the production process, as well as making the necessary alignments
- Plan the contracting needs of third-party services, as well as monitor and ensure compliance with established processes and deadlines
- Comply with the HSES standards during the execution of the activities
- Ensure and comply with the Quality Management System's service, by complying with the ISO 9001, ISO 17025 and Syngenta Quality Practices Codes, guaranteeing the continuous improvement of the process
- Skills Negotiation, communication, teamwork, organization and planning
- Desirable knowledge in seed production, Official Standards and Seed Legislation
- Desirable 1 year experience with soybean seed quality
104
Quality Supervisor Resume Examples & Samples
- Providing leadership, coaching, and direction to quality professionals to drive quality improvements
- Identify and implement best practices in quality processes through the use of quality tools and methodologies
- Apply a working knowledge of quality principles and statistics to direct / coach quality technicians
- Develop and track metrics that support quality systems effectiveness
- Direct reports in the training, improvement, and documentation of test methods
- Effectively identify, troubleshoot, and resolve non-routine problems
- Direct reports in support of resolution owners for incoming customer complaints, including assisting in identifying root cause, and implementing effective corrective actions
- Support and coach the management of documentation, including Test Methods, Corrective Actions, Nonconforming Material, Management of Change, and other records as needed
- Minimum of three (3) years of combined experience working in a Quality, Product Engineering and/or Manufacturing / Technology environment
- Minimum of two (2) years of supervisory experience
- Quality Engineer (CQE) certification from the American Society for Quality (ASQ)
- Lean Six Sigma (LSS) trained
- Experience as a Quality Systems Auditor, Quality Engineer, and/or Product Engineer
- Experience and/or knowledge of Industry Quality Standards and Regulations (i.e. IPEC, cGMP, AS9100, ISO/TS16949)
- Strong verbal and written communication skills with the ability to influence across all levels
- Microsoft Office proficient, Minitab and/or another statistical tool a plus
- Excellent organization skills with ability to prioritize and manage multiple assignments
105
Quality Supervisor Resume Examples & Samples
- Manage the performance of a Performance Monitoring Analysts (PMA) team supporting several markets
- Evaluate team performance on an on-going basis and provide continuous coaching and feedback to their PMAs
- Collaborate with business partners’ functional leaders to improve procedural opportunities identified by team
- Work closely with Compliance and Regulatory & Business Assurance leads supporting Global Servicing Network to ensure team is aligned with regulatory requirements
- Analyses results, identifies and designs solutions, presents recommendations to management, and manages gap closure
- Regularly reviews processes and procedures for effective controls
- Facilitates brainstorming and call calibration sessions with different teams to identify compliance, policy, procedural, case actioning and system gaps
- Ongoing review of customer feedback results and drivers of customer dissatisfaction with linkages to current policies and procedures. Identifies opportunities for enhancements and challenges the status quo
- Participates in compliance reviews of business units
- Partner with local Market Compliance and Legal to ensure alignment with regulations and related tests
- Partner with Compliance and Process Owners to establish and follow through on Corrective Action Plans
- People leader experience of 2-5 years in a Premium call center environment a must
- At least 1 year experience as a Quality Monitoring Lead, preferred
- Experience in US Financial Operations in a call center environment, highly preferred
- Proven high performer in previous job roles
- Bachelor’s Degree preferred
- Should be proficient in Microsoft Office tools (PowerPoint, Excel and Word)
- Exceptional verbal and written communication skills in English
- Demonstrated ability to coach and lead employees
- Strong knowledge of Policy & Procedures in one of the following - consumer, corporate, merchant
- Ability to provide effective feedback to all levels of management
- Ability to perform in a fast-paced team environment
- Strong organizational / time management skills
- Demonstrated follow-up and conflict resolution skills
- Ability to identify opportunities and drive these to closure
- Strong relationship building skills, highly engaged and a really good team player
- Self-motivated with a demonstrated ability to drive results under tight timelines and handle multiple tasks concurrently
106
Itápolis Quality Supervisor Resume Examples & Samples
- Planning of Quality Activities (analysis of seedlings / inputs, quality audits, etc.)
- Quality report management in Excel spreadsheets and SAP (Syngenta Software)
- Critical analysis of the results of Quality analysis and communication with interested areas
- Participation in operational forums (presentation, preparation of data in Power Point, etc.)
- Planning of quality analysts' training and management of internal and external human resources standards
- Laboratory housekeeping and management of quality area safety standards
- Make quality management of seedlings in nurseries ensuring the value proposition and ensuring low level of customer complaints
- Ensure that Ministry of Agriculture standards are followed and implement controls during the checking process
- Have good communication and good relationship with the areas of expertise
- HACCP Training (Hazard Analysis Control Critical Point)
- Preferably with knowledge of IN's 22 and 24 regularized in MAPA FOR Production of seedlings
- Work experiences in the area of sugarcane
- Experience in safety practices
- Experience with supervision or people coordination activities
107
Quality Supervisor Resume Examples & Samples
- Be responsibility for incoming inspection for all the direct material
- Stat. and analysis the information/data of incoming inspection, transfer right information in time
- Manage and coach inspector; ensure the personal qualification establish and effective performance management system
- Facilitate rapid solutions to non-conformity product from supplier and direct root cause analysis for the product quality issue and corrective actions taken with SQA and AQD
- Organize resources and do the efficient inspection to meet the incoming inspection lead time
- Assist SQA sending non-conformance report to supplier and provide data support
- Redact the new productions incoming inspection control plan and update existing products
- Other tasks assigned by supervisor
108
Plant Quality Supervisor Resume Examples & Samples
- Perform all work in accordance with safety rules and regulations and participate in facility health & safety activities as assigned
- Be pro-active in identifying and performing tasks to maintain and improve safety, quality and environmental performance
- Ensure SSOPs and JSAs exist and are updated for all quality tasks. Ensure required training for Quality Technicians is completed and documented according to policies
- Manage a large scope of work, volume of activity, and direct reports
- Manage scope of project work, analysis, or report writing
- Provide safety, quality, and environmental training for Quality Technicians
- Lead process and product tests/trials as assigned. Compile, analyze, and report trial test results as required
- Define and implement procedures to support quality initiatives. Establish and maintain a comprehensive program that will ensure consistent product quality under certifying agency guidelines
- Ensure plant compliance with all internal product specifications, and corporate quality policies
- Manage quality systems to assure consistent process and product performance while maintaining maximum production and safe work habits
- Manage plant calibration and verification schedules for process and lab instruments. Lead and deploy process optimization (cost reduction, new technology, etc.), statistical analysis, continuous process improvement, and experimental design
- Support and assist in troubleshooting sources of Special Cause variation
- Supervise work activities for plant Quality Technicians
- Train, coach, and assist in the development of plant Quality Technicians
- Manage quality records, databases, and controlled documents in accordance with corporate record retention policies
- Manage and maintain quality records and databases in compliance with business, corporate, and certifying agency requirements
- Generate routine quality reports for internal communication
- Assist in the plant quality self-assessment
- Assume responsibilities of Quality Manager in their absence
- Thorough knowledge of quality system
- Thorough knowledge of LP and quality policies & standards
- Knowledge of manufacturing processes, equipment and basic mechanical ability
- Knowledge of customer requirements, installation requirements, compliance regulations, quality processes and procedures
- Skill in leading, planning, coaching, training, and supervising. Ability to hold people accountable
- Skill in data analysis and troubleshooting
- Knowledge and understanding of statistical process controls
- Proven ability to design experiments to investigate product attributes or qualities/conditions
- Strong computer spreadsheet software and software skills
- Proven ability to operate job related equipment and tools
- Proven ability to operate a computer and supporting software
- Proven ability to communicate effectively in oral and written form
- Proven ability to work independently with minimum supervision
- Proven ability to document process changes and their effects
- 5+ years quality related experience
- Manufacturing experience desirable
109
Quality Supervisor Resume Examples & Samples
- Responsible for leadership, guidance, and professional support of 1-2 employees
- Performs annual reviews for direct reports in a timely manner
- Ability to manage all required quality systems with minimal supervision in accordance to AS9100
- Inspects all AS9100 required parts and performs first article inspection (about 15% of time)
- Inspection and testing of parts using GD&T
- Ensures that proper inspection procedures are in place and followed for each part
- Develops implements and tracks training of all Quality Assurance inspection personnel in procedures and equipment utilized by inspectors. These include, but are not limited to, metrology equipment and part specific Quality Work Instructions
- Oversees Material Review Board activities, assures timely and accurate disposition of product (i.e. in-coming raw material, WIP, and customer returns)
- Assist with Root Cause Analysis necessary to complete/close NCR/CAPA(s) in a timely manner
- Collaborates with sales and customer service teams to manage customer complaints and customer returns by acting as a facilitator for the Material Review Board. Generates a written response to customer’s request for corrective action
- Collaborates with purchasing and engineering teams to resolve vendor nonconformances by acting as a facilitator for the Material Review Board. Generates a request for corrective action and enters the vendor’s response into Stratasys’ corrective action tracking system
- Collaborates with the Production Supervisor, Project Coordination Supervisor, and the Manufacturing Engineer/Service Supervisor to implement process improvements through the use of Statistical Process Control and process monitoring
- Collaborates with Quality Systems team in maintaining ISO 9001 & AS 9100 registrations and regulatory conformance
- Assist as an internal auditor for current ISO and AS standards throughout all facilities
- Responsible for performing on-site quality audits when required
- Develops and updates customer/part specific Quality Work Instructions for receiving, in-process, and final inspections
- Assists with Quality Inspection and Finishing as demand requires
- Responsible for driving proper presentation and cleanliness of QC area at all times
- Maintains and analyzes all quality metrics on a daily, weekly, and monthly basis
- Recognize and react to trends and prepare quality metrics/reports to be shared company-wide
- Drives and implements systemic improvements (about 15% of time)
- Demonstrates commitment to Stratasys Core Values by leading, acting and behaving in a manner consistent with these values
- Follows all company safety policies and procedures and attend all safety trainings related to the job
- Perform other tasks on time and as required by Quality Director and/or senior management
- Must be a US Citizen or Lawful Permanent Resident
- B.S. Degree in Engineering or Quality Assurance with emphasis on reliability, test engineering, failure analysis or manufacturing preferred
- A minimum of 5 years of experience in a Quality role or manufacturing setting
- One to two years of experience in a leadership role, with the ability to work well with all levels of the organization
- ASQ-CQE and Lean Six Sigma training preferred
- Solid written and verbal communications skills
- Strong problem solving and troubleshooting abilities
- Comprehensive knowledge of statistical process control
- Thorough knowledge of blue print reading and geometric dimensioning & tolerancing
- Ability to use inspection equipment, such as micrometers, tool scopes, and coordinate measuring machines (CMMs), etc
- Basic knowledge of ISO 9001 and AS9100C
- Computer proficiency, using both networked personal computers and electronic hardware utilized to run inspection equipment
- Thorough understanding of CAPA process and methodology
- Leadership, guidance, and professional support of 1-2 inspectors
110
Quality Supervisor Resume Examples & Samples
- Supervises a team of Quality Analysts
- Evaluates performance of Quality Analysts
- Reviews and Manages disputes
- Develops and initiates standards and methods for quality
- Establishes program to evaluate precision and accuracy of audits in nesting and production
- Assists the Quality manager in calibration requirements
- Suggests and implements changes in monitoring conditions
- Analyzes and resolves work problems, or assists Quality Analysts in solving work problems
- Initiates or suggests plans to motivate Quality Analysts to achieve work goals
- Interfaces with other Departments and the internal Trainer to develop and implement training programs as required
- Conducts audit of output per Quality Analyst
- Attends the Weekly Business Review with Campaign TL/OM/Client
- Holds calibration sessions with the assigned team/campaign
- Conducts one on one session with Quality Analysts
- Performs coaching sessions with Quality Analysts and TL
- Submits weekly and monthly quality reports
- Identify any potential quality issues per defined process and escalate quality issues immediately to management
- Isolate and report defects; verify defect fixes
- Other duties as assigned – it is understood that this list of major duties and responsibilities is not an inclusive list and that other duties and responsibilities, which may include helping others in the same or different departments, may be assigned by supervision
111
Quality Supervisor Resume Examples & Samples
- Evaluate and develop processes and critical control points with manufacturing to assure compliance with specifications
- Develop, implement and maintain an effective HACCP program
- Work closely with manufacturing to assure continued improvement of quality through communication and review of product compliance to specification
- Train all plant personnel in GMP’s
- Document production compliance with GMP and Critical Control Points
- Monitor, upgrade and document food safety programs to comply with government, corporate, customer and industry requirements
- Work actively with manufacturing supervisors and plant manager to pro actively prevent problems during manufacturing
- Supervise the plant’s quality control function
- Support and maintain Product Vision
- Audit ingredient and packaging suppliers to assure compliance to Hain standards and to push continuous improvement throughout the supply chain
- Work closely with the R&D department during the commercialization of new products to assure adequate specification development
- Investigate consumer complaints and determine root cause and corrective actions
- Work closely with the Corporate Director, Quality Assurance and Safety
- Support other operations as needed within the Hain Celestial Group Supply Chain
- Bachelor’s Degree in food sciences, food process engineering or appropriate biological sciences
- 3 to 5 years work-related experience in quality assurance, quality control or food product development
- Experience with H.A.C.C.P. and other food safety system
- Experience with organic certification and ingredients a plus
- Knowledge in the area of FMSA, certification as a PCQI is a plus
- Experience with GFSI and SQF
- Experience with USDA and FDA requirement is a plus
- Ability to successfully manage multiple projects in a fast paced environment
- Exceptional communication, analytical and leadership skills
- Some travel is required
112
Quality Supervisor Resume Examples & Samples
- Must have excellent written and verbal communications skills,
- Must be experienced with using MS Office products, especially Excel
- Supervise lab technicians and fill in/ back up when needed,
- Responsible for quality assurance throughout entire plant – process control, defect management, supplier quality reporting, etc
- Manage ISO 9001 certification and quality management system. Proficient writing skills for work instructions, management review, etc.,
- Lead teams and process improvement projects,
- Lead RCCA (Root Cause & Corrective Action) process for all customer and internal issues,
- Work with suppliers to minimize supplier defects and evaluate supplier RCCA responses,
- Ensure lab reliability through process control, calibration schedule and MSA,
- This position is located in Cincinnati, OH
- 4 years minimum experience in a lubricants and/or chemical manufacturing laboratory setting plus 2 years supervisory experience preferred
- Must be skilled at using common test equipment used to test lubricants and/or chemicals
- Experience in SPC (Statistical Process Control), control charts, and statistical software (e.g. mini-tab) is a plus
- Experience with automotive standards APQP, PPAPs, FMEA, Control Plans a plus,
- Experience in Lean, six sigma a plus,
- Experience with SAP and LIMS a plus
- Must be authorized to work in the United States
113
Quality Supervisor Resume Examples & Samples
- Assist the Quality Manager and senior management with the implementation of the ISO9001 & NQA-1 quality management system to ensure compliance with requirements and performance excellence
- B.S. degree in Mechanical Engineering, Electrical Engineering or related field required
- ASQ certification preferred
- Must possess working knowledge of engines and engine mechanical systems
- Minimum of 2 years experience in a manufacturing environment required; experience working with weld inspection strongly preferred
- Strong leadership skills, team building, and or personnel/organizational development skills
- Outstanding communication skills (written and oral) with the ability to successfully interact at all levels of a matrix organization; ability to develop relationships with all levels of the organization
- Self-motivating individual, able to complete assigned tasks/commitments, supplier evaluations and inspections to meet customer requirements with minimal supervision
- Possess a high degree of problem-solving skills through application of basic quality tools
- Proven lean manufacturing experience a plus
- Must be proficient with Windows, Microsoft Office and Google business products
- Experience with Oracle or other ERP software preferred
- Due to access to restricted information, U.S. citizenship required
114
Quality Supervisor Resume Examples & Samples
- Minimum of two (2) years combined quality assurance and/or quality control experience in a manufacturing environment
- Minimum of three (3) years combined quality, product and/or manufacturing environment experience
- Minimum of two (2) years combined team lead and/or supervisory experience
115
Quality Supervisor Resume Examples & Samples
- Evaluate, certify and verify analytical / evaluation of data for both incoming raw and packaging materials. Responsibility specifically includes prevention of further reprocessing and / or delivery of non-conforming materials when a problem is identified. Reports to Operations and provides immediate disposition and recommendations (if applicable) for non-conforming materials
- Qualify alternative suppliers in coordination with the direct Manager and the respective Planner / MRO. Measure supplier’s quality performance and coordinates with Purchasing for supplier’s quality improvements. Conducts vendor audits of new and existing suppliers in accordance to global and local requirements such as MRC process
- Generates reports / data / procedures covering QA / QC related activities as specified in the Company’s Quality Systems Operating procedures and Quality manual. Assist on the development, implementation and maintenance of the overall Quality System and other regulatory requirements. Develop QA programs like GMP, HACCP, Food Safety, Pest Control and etc. Provide relevant training to personnel
- Transact QA relevant transactions in the network system such as blocked stocks maintenance (as applicable), and generate reports as necessary. Maintain records. Upgrade SAP, as maybe applicable, periodically or as necessary. Responsible for creating and maintaining the master data of each material in SAP
- Creates vendor notifications and coordinates with Purchasing / Planner for the corrective / preventive action implementations. Ensure the timely monitoring of notifications closure
- Responsible in conducting audits relevant to the GMP and AIB requirements. Prepares the audit findings and discussed with the Operations team. Provides recommendations for the closure of the findings
- Responsible to the compliance of the atypical, illegal dye testing and other global requirements for raw materials. Ensure that timely submissions of samples are done and provide disposition on the results in coordination with VQDI Team
- Perform other related tasks that maybe assigned from time to time
116
Quality Supervisor Resume Examples & Samples
- At least 6 years of industrial working experience and more than 3 years experience of team leading
- Skilled operation of Microsoft office
- Quality knowledge like of ISO9001/14001/18001, quality tools, basic statistics
- Basic knowledge of SAP or ERP
- Communication and basic management skills
- Advanced oral and written English
- Make sure that all inspectors including new comers are qualified for the job by proper training
- Training/coaching quality auditors to ensure that products and processes comply with the relevant requirements of the quality management system
- Care for the team members and help to improve their working skills and plan their careers
- Update SOP and let all inspectors be aware of the new requirements related
- Daily management work of the QA auditor including the necessary resources available, 5S etc
- Assure Line Audit is conducted in an accurate and timing manner
- Align the inspection standards among both individuals and shifts
- Summarize inspection results regularly. Analyze the non-conformity and support QE/Packing operation to find solutions in time
- Interface with M&E, Production, Warehouse and QE to secure timely, efficient and effective problem solving
- Keep good communication and co-operation with local and global departments. Effectively support production and help to improve the production staff’s quality sense
- Make sure the smooth and balanced running of shifts. Distribute the work load in an effective and fair way
- Always keep an eye on the weakness and carry out continuous improvement activities to enhance the quality management system, such as 5S, Kaizen, Lean methods, etc
- Be proactive. Open mind for new knowledge and positive changes
- Assist during internal IMS audits in his / her area, including closing out audit findings and determine proper corrective and preventive actions
- Follow up on the timely resolution of supplier failure, corrective actions and preventive actions by SQM team and Internal claims team
117
Quality Supervisor Resume Examples & Samples
- Assign and supervise completion of F9 projects using SpaceX processes and systems, in a fast-paced, constantly changing environment
- Effectively communicate to the team the assignment, project, problems to be solved, deadlines, and any issues for review
- Implement training as needed to advance employees in applicable expertise to maintain a highly skilled work force, and create a succession plan to ensure there are employees slated for leadership opportunities
- Keep abreast of emerging technologies in your area of expertise and introduce these to the shop as needed to remain competitive within the industry
- Schedule the work load and required labor hours to ensure that projects are delivered on time and with expected quality, and sign overtime as necessary to keep schedule and prevent excess overtime when work load is low
- Review employees regularly, per SpaceX requirements and document performance improvements and disciplinary issues with accuracy and professionalism
- Identify project issues and planning errors and work with project management to find a solution through risk identification and mitigation
- Work with Management to identify and implement fair measures of performance and quality for shop personnel
- Identify non-conformances, plan associated rework, and follow through the entire process until closed
- Implement corrective action plans related to systemic problems; initiating and fostering a spirit of cooperation within and between departments
- Bachelor’s degree in an engineering field or 5 years in a leadership position
- Minimum of 3 years in a manufacturing sector
- Experience with applying lean manufacturing principles, efficiency methods required
- SpaceX experience preferred
- Demonstrated experience and ability to read, interpret and follow
118
Quality Supervisor Resume Examples & Samples
- Strong Lean and Six Sigma knowledge, Green Belt certification,
- Experience in KPI/SLA reporting regarding timeliness, accuracy, volumes, etc.,
- Statistical knowledge: sampling, forecasting, etc.,
- Very good analytical skills,
- Advanced and practical knowledge of MS Excel and other Office applications,
- Knowledge of Quality methods and tools (Six Sigma, Lean, Kaizen) is a must,
- Demonstrate professionalism, competence and clarity of communication when dealing with the clients and leadership,
- Fluent English,
- Other European language is an asset
- Supervising quality team members,
- Being first point of contact in quality related topics for the team,
- Identifying gaps in the process, search and delivery of possible improvements,
- Taking active role in designing new KPIs,
- Active participation in the process optimization,
- Communicate and report quality data, issues, non-compliance, process gaps through measurements,
- Drive quality culture in operations,
- Responsibility for the projects documentation,
- Support CAPA and FMEA initiative,
- Participation and support projects aimed at the development and implementation of new reporting solutions,
- Share best practices,
- Identify opportunities to share/adopt process standardization across GSS centers
119
Quality Supervisor Resume Examples & Samples
- Manage daily staffing and resource allocation to ensure quality standards are upheld; meeting or exceeding client SLA while minimizing labor cost
- Maintain compliance with all internal and external quality standards and documentation requirements
- Engage and collaborate with all departments, clients and suppliers ensuring that issues impacting quality are resolved within SLA and communicated to all stakeholders
- Build, maintain and execute a plan to ensure that quality and training resources are synchronized with business activity forecasting
- Conduct regular periodic review of training, working instruction and compliance related documentation and materials
- Drive Continuous Improvement and total employee engagement with Lean methodologies
- Manage, develop and motivate direct reporting staff and contract labor
- High school diploma or equivalent required; some college coursework preferred
- 3+ years experience in a leadership role in the manufacturing, distribution or logistics industries preferred
- Experience working in an ISO certified organization, Strong proficiency in MS Office, Familiarity with ERP/WMS Systems, Quality Management Systems
- Strong interpersonal skills including effective written and oral communication skills
- Ability to determine root cause and recommend corrective action, understand complex interdepartmental projects
- Attention to detail, logical analysis and problem resolution
- Ability to work flexible hours and weekends as required
- Willingness to work in a climate controlled office environment with occasional exposure to production area with noise, dust and periods of prolonged standing
120
Quality Supervisor Aseptic Processing Resume Examples & Samples
- The Quality Supervisor will assist the Quality Manager in assuring that PharMEDium’s core values are continually emphasized and kept in the forefront of facility operations
- Will be responsible for all Quality Assurance aspects related to aseptic processing. Will ensure routine daily audit of processes to ensure compliance to PharMEDium policies and procedures. Will coordinate the investigations, corrective actions and preventative actions of all nonconformances. Ensure the disposition of potential nonconforming product is disposition in an efficient and timely manner
- The Quality Supervisor will set the tone for quality processes and services to deliver safe compounded preparations to hospital customers
- Participate in cross-functional teams to identify effective corrective and preventive actions to improve Lean process quality
- Working with Quality Manger will assure timely closure of audit items
- 2 years of supervisory experience required
- Demonstrated understanding of quality assurance in a regulated (FDA, DEA, ISO) environment
- Computer skills in word processing, spreadsheets and databases required
- Effective problem solving, supervisory, strong communication (written and verbal) and organizational skills
121
Quality Supervisor Resume Examples & Samples
- Responsible for ensuring adherence to quality system requirements compliance to internal policies and external regulations (ISO 13485, 21CFR 820, OSHA, etc.)
- Set department goals/expectations, provide performance feedback to employees and manage performance on a daily basis
- Plan resource requirements and scheduling personnel to meet production needs and make hiring decisions for new personnel
- Maintain and conduct training and certification activities as required
- Maintain inspection throughput performance and metrics as required
- Maintain calibrated assets within the department to ensure they are within calibration due dates prior to use and in proper working condition
- Interface with Manufacturing Operations and Quality Engineering team members regarding identification and resolution of raw material inspection problems
- Participates in or leads investigations related to process deviations, nonconformance’s and as participate in CAPA activities
- Support and participate in all audit activities internal or external
- Attention to detail and the ability to work in a fast paced constantly changing environment
- Sound understanding of dimensional and visual inspection methods
- Requires demonstration of investigation techniques and ability to conduct root cause investigations
- Must be willing to work 2nd shift hours: Monday thru Thursday 3:15pm-1:45am (4/10 shift)
122
Quality Supervisor Resume Examples & Samples
- Develops and executes an auditable set of Standards and Processes for the daily monitoring of all Plant’s adherence to the recipes through utilization of the Incuity, SAP Quality, and Vantage Point to ensure consistent product quality across the plant grid and transloads
- Develops and communicates to all parties the daily plant reports on the processing and downtime associated with recipes and disruptions
- Conducts weekly Quality meetings with the manufacturing team and appropriate managers
- Develops each product’s operating windows using the Six Sigma Tools to create a confidential operating procedure to train plant process operators and shift supervisors
- Establishes Best Practice Communication for the Plants with a Monthly Educational Communication to assist them in beneficial practices for recipes
- Collaborates and troubleshoots with manufacturing sites recipe/processing issues
- Recommends Recipe modifications, if applicable, to the Technology Manager
- Monitors COAs of Raw Material and provides monthly assessment on performance to specifications
- Owner of SAP QM system
- Conducts SAP QM training for all associates in quality related roles within OTG’s manufacturing and supply chain grid
- Responsible for the development of quality control tests on all newly developed products
- Determines the classification and recommends disposition of “off-spec” raw material and finished product and provides monthly information to finance to accrue inventory reserves
- Approves all finished products returned by customers for issuance of credit
- Relieves Technology Manager as required
- Primary contact and decision point for plant product quality deviations per quality trouble shooting SOP
- Responsible for finished product and raw material testing procedures and protocols at manufacturing and transload locations (testing requirements, round robins, etc.)
- Performs causal analysis involving Product Quality Issues
- Identify, develop, and execute RTAs to improve product quality and product manufacturing processes
- Experience in operations environments, preferably with batch and continuous chemical process experience
- Demonstrated ability to effectively present information and transfer knowledge, engage an audience, and foster an enthusiastic learning environment
- Demonstrated strong quantitative and analytical ability
- Highly effective relationship management skills required
- Demonstrated experience in successfully managing multiple quality/process improvement projects
- Strong analytical and problem solving skills; ability to recommend alternative solutions and translate complex concepts into simplified and understandable examples
- Ability to drive change throughout an organization
- Exhibit tact when interfacing with people and use good judgment when decisive action is required
- Six Sigma experience preferred
- Chemical industry experience a plus
123
Quality Supervisor Resume Examples & Samples
- Acts as role model (Quality ownership & Leadership) reinforcing quality culture plant wide
- Develops implements and reviews quality programs and procedures; validates new processes, products and methods; coordinates audits and ensures execution of appropriate corrective actions
- Identifies and develops strategies, performance indicators and project improvement opportunities; manages documentation
- Shares his expertise and assists in employee training
124
Quality Supervisor Resume Examples & Samples
- Supervises and leads the Quality Technicians in the facility to provide coverage to match production schedule and define daily activities for those positions in support of plant operations
- Responsible for supporting the facility’s Hazard Analysis Critical Control Point (HACCP) Program and all Food Safety Plans through verification activities conducted by QA Technicians
- Supports the Quality Manager and Plant Quality Specialist in leading the plant’s efforts to maintain SQF certification
- Maintain and update the plant product specification database
- Manage and maintain the QA lab, quality testing equipment, and lab supplies
- Assist with Consumer Complaint investigations and development of corrective actions
- Serve as the plant Subject Matter Expert (SME) in the use of Quality and Statistical Tools for Quality and Process Improvement projects
- Assist in development of plant specific food safety and quality training programs, provides training for production personnel as required and ensures employee understanding of training through verification of activities. Maintains log of annual employee training and recertification
- Manage the Foreign Material Identification and Notification program
- Assist with new equipment installation, start up, and validation
- Assist with corrective action development for Quality Incidents (QI’s)
- Participates in monthly Food Safety and Quality facility audits
- Assist in coordination of non-conforming product and equipment issues including identification, segregation, disposition and development of corrective actions
- Assist Quality Manager with Regulatory audits, 3rd part audits, and Customer visits as needed
- Represents the Food Safety and Quality group as needed on special projects and process improvement efforts
- Provides back up support in the absence of the Quality Manager
- Inform management of ANY Food Safety or Quality issues or of any process which becomes non-compliant with specified requirements
- Coaching employees that are not meeting their performance goals and rewarding employees for good performance
- Responsible for food safety, food defense, and food quality
- Completing employee vacation forms, status change forms, issuing discipline, time & attendance management and terminations in a timely manner
- Other duties as assigned as requested by supervisor/management
- Minimum of two years’ experience in Food Manufacturing, Food Safety, Quality, or Operations
- Direct experience with GFSI certification schemes (SQF, BRC, etc.) is required
- Must have the ability to coach and train on quality, food safety, and process improvement programs
- Efficient computer skills: intermediate to advanced knowledge of Microsoft Office, SharePoint, and Statistical Process control software is preferred
- Possess strong interpersonal skills, with supporting verbal and written communication skills
- ASQ certification a plus
125
Quality Supervisor Resume Examples & Samples
- Directs and advises personnel in 5 why procedures to analyze non conformances
- Maintains a thorough knowledge of new developments, technology and processes
- Monitors QA final acceptance of Root Cause Analyst and implements changes to improve overall efficiency
- Develops, justifies and implements K-BOSSS process improvements
- Build a robust corrective action system to answer CAR's effectively by
- 5 years quality experience required. 3 years leadership/management experience required. 2 years in contracting environment
126
Quality Supervisor Resume Examples & Samples
- Directly supervise the activities of the quality technicians and management of laboratory
- Maintain ISO 9001 or standard requirements for the testing lab
- Maintain testing methods to standard – ASTM – CRI
- Calibration, control and maintenance of lab equipment
- Maintain necessary SPC within the lab to ensure gauge accuracy
- Perform routine MSA gauge R & R studies
- Oversee routine testing and acceptance / rejection of raw materials
- Ensure the application of the visual standards
- Implementation and audit of process control plans
- Participate in production trials and in the development process
- Participate in and lead SMATS and QMATS
- Assist the Quality Manager with the WCM Quality pillar
- Assist Quality Engineers with routine projects
- Participate in project teams as quality support
- Maintain document control of quality documents
- Assist operations with Quick and Standard Kaizen events
- Maintain Non-conforming materials area
- Participate in Shop floor Tier meeting and lead RCA activities targeting sporadic issues
127
Quality Supervisor Resume Examples & Samples
- Provide Management and Supervision for the Quality Management System at Lelystad and Lissieu and work closely with all departments and functions to promote processes that ensure consistency, continuous improvement and compliance with quality and business requirements
- Provide Management and Supervision for the Quality Systems and maintain the appropriate level of customer service. Has the ability to write clear, coherent internal business communications / reports. Formally presents results of work
- Non Conformance Reports and monitoring reporting performance and trends
- Problem solves identification of root cause and implementation / follows up of corrective procedures and preventive actions to ensure timely resolution of such problems
- Ability to perform internal audits as required according to site and global plans
- Use auditing as a proactive tool for improvement as well as compliance and challenge existing practice where appropriate
- Timely completion and follow up through to closure of CAPA actions
- Measuring and monitoring of performance against agreed KPIs
- Collate and share information / data across the sites as appropriate through reports and follows up on identified improvement opportunities
- Actively contribute to the success of the overall QA team and the sites
- Actively participates in the GSD Quality organisation
- Actively participate and/or drives EU/Global QMS improvements as required
- Degree in a scientific discipline or equivalent experience in a relevant discipline
- Knowledge of ISO 9001 and USDA requirements
- Quality Assurance / Auditing experience in a chemical, pharma or manufacturing industry
- Experience in the following - training, validation, problem solving tools. Understanding of statistics based management & procedure is preferred
- Excellent MS Office skills in particular Excel (Trackwise and Statistical Software or comparable experience)
- Ability to perform routine duties with minimum supervision
- Ability to work on a variety of assignments at one time
- Ability to recognize deviation from requirements and standard practice and understanding associated risks is essential in role
- Good communication skills (spoken and written)
128
Quality Supervisor Resume Examples & Samples
- Direct quality personnel and prioritize quality functions in regard to quality issues elimination from the systemic and non-systemic point of view and keeping production requirements as a part of the resolution
- Review daily in-process metrics to determine team priorities
- Develop and implement corrective actions using 8D, 5 Why, A3 and lean tools to support initiatives around the reduction of internal & customer PPM, rework, scrap and FPY
- Direct cross-functional teams to eliminate roadblocks and communication barriers that may affect quality and customer requirements
- Understand and adhere to a quality system in conjunction with divisional procedures to ensure compliance with TS 16949, customer specific requirements, and all regulatory requirements
- Interact with divisional resources on the problem solving projects for product quality improvements
- Support new product development from a Quality stand point
- Motivates and coaches employees to maintain high levels of satisfaction, productivity and quality through effectively utilizing available rewards and recognition channels to encourage and promote desired behaviors and results
- Ensure the standardized Vehicle Group processes for the supplier quality management system are established, implemented, measured, and maintained within the plant
- Supplier WISPER system utilization and Eaton Supplier Excellence Manual guidance within the plant
- Supplier PPAP – coordinate part samples for dimensional review and assembly trials in Auburn and work with Pune PPAP team for overall PPAP approval and documentation
- Manage notification (DMRs), responsiveness, containment, root cause determination, corrective action, and closure of supplier quality issues. Control scorecard (supplier DPPM) and lead the Cost of Poor Quality process
- Identification of the most disruptive suppliers and notify divisional SQEs
- Bachelors’ Degree from an accredited institution is required
- 3 years of experience in manufacturing or operations is required
- A minimum of 3 years of direct quality experience
- CQE Certification
- Green Belt Certification
- TS 16949 Knowledge & Experience
- Experience driving continuous improvement activities
129
Quality Supervisor Resume Examples & Samples
- Developing, implementing and improving the Quality Management System (QMS) in support of a “Zero Defect” business objective and internal and external customer needs. Ensure QMS meets required standards (ISO 9001:2015, 10CFR50 Appendix B, 10CFR21, other standards/regulations required by internal/external customers). Act as ISO 9001 Management Representative
- Promoting Quality Management strategic vision, quality policy, quality objectives and quality improvement initiatives across all departments and levels of organization
- Participating in, and promoting Quality at daily, weekly and monthly performance review meetings. Develop and oversee metrics tracking to ensure improvement activities address and correct identified deficiencies and non-conformances
- Developing, implementing and improve QMS Systems, including M&TE and Calibration, Supplier Management, Internal and External Audits, Product /Process Non-Conformance Management, Problem Solving Tools, Management of Change, Laboratory Quality Management etc., in support of the “Zero Defect” business objective. Act as Lead Auditor
- Manage Quality and Analytical Laboratory personnel and company assets
- Ensure a safe work environment through development and maintenance of safe work practices, and implementation of and participation in training, observation and corrective action programs. Champion and provides leadership in corporate and site specific EHS and regulatory compliance projects and programs
- Support 5S, Kaizen and Lean Six Sigma teams in implementing programs to improve workplace housekeeping and efficiency
- Bachelor’s degree or higher in a science or engineering discipline from an accredited institution
- Minimum of five (5) years of combined experience in a quality and/or laboratory role
- Master’s Degree in Chemistry or Quality from an accredited institution
- Minimum of 5 years of experience in a manufacturing environment
- Minimum of 3 years of experience in a supervisory experience
- Understanding of analytical instrumentation, data acquisition systems and statistical analysis
- Proven knowledge of ISO 9000 Quality standards
- 10CFR50 Appendix B
- 10CFR21
- Working knowledge of SPC applications
- Working knowledge of gauge R&R
130
Quality Supervisor Caterpillar Production System Supervisor Resume Examples & Samples
- Collaborating with internal and external suppliers early in the new product introduction process ensuring that Caterpillar delivers world class products and services
- Creating a Built In Quality Culture through continuous improvement of robust, lean processes
- Partnering with customers to truly understand their needs and responding quickly to customer issues
- Understanding and managing quality as a key activity to deliver long term strategic goals and superior results
- Driving quality competencies and individual accountability that is aligned to customer expectations
- Leads a team of quality technicians and CPS black belts to provide quality measurement reports and make continuous improvements to products and processes
- Facilitates quality investigations to determine root cause and then develops and implements corrective action plans
- Responsible for the resolution of day to day shop quality issues, including the coordination of stop to fix issues and rework programs
- Works with global purchasing to improve the quality of products delivered to the facility
- Receives customer feedback and acts as the operations quality contact for product support
- Provides support and resource for the NPI process, CPI process and value stream certification program
- The incumbent will be expected to resolve issues by following departmental procedures, using past experience and 6 Sigma methodology to develop robust interim and permanent corrective actions
- Bachelor's degree in Management, Manufacturing or an Engineering based subject OR, equivalent relevant experience will be considered
- Previous 6 Sigma experience should have been in the required qualifications i.e. the candidate should have at least been through yellow belt/green belt training and be aware of the DMAIC & DMEDI framework for problem solving
- Strong operational experience
- Proven leadership capabilities and comfortable developing a team
- Excellent interpersonal and communication skills, as he/she will facilitate the quality link between operations, product group and supply chain
- Self-starter and team player with experience resolving issues following procedures
- Proven problem solving skills and able to manage the completion of work and assignments independently
- 6 Sigma/CPI/CPS Black Belt Certification
- Experience of leading and supervising hourly and salaried positions
- Experience in lean deployment and built in quality (BIQ)
- Working knowledge of CPS /Lean Manufacturing
- Experience of facilitating rapid improvement workshops
131
Quality Supervisor Night Shift Resume Examples & Samples
- Will be responsible for all Quality Assurance aspects of all classified areas in the Facility. This will include coordination with Facilities Maintenance on all certification / recertification, maintenance / preventative maintenance (PM), Monitoring, and audits of the sanitization process. Will investigate any nonconformances and out of compliance issues related to these areas. Will review all documentation related to the classified areas
- Ensures compliance to procedures, governing regulations and address non-compliance issues
- Will conduct internal audits of processes, systems and procedures
- Will initiate SOP revisions as needed to assure compliance, continuous improvement of overall operation
- Bachelor’s Degree in Science or related field required
- Aseptic processing experience desired not required
- A must:Minimum of 2 years experience in Quality, or related field in the healthcare or pharmaceutical or medical device industry. (Cosmetics and food are acceptable industries)
- Team lead or supervisory experience required
- Demonstrated understanding of quality assurance in a regulated (FDA, DEA, ISO) environment a plus
- Thorough understanding of the Governmental requirements in a sterile processing environment
132
Quality Supervisor Resume Examples & Samples
- Maintains all quality records
- Establishes and maintains procedures for laboratory safety management
- Provides technical support to plant operating staff
- Represents plant to regulatory agencies when needed
- Selects, trains, develops, retains & manages lab technicians
- Resolves daily batch issues adjusts batches, decide whether products need rework or adjustments
- Maintain the production specification implementation process. Maintain the use up and changeover process for raw material / package component/label changes – communicate the change, coordinate the bill of material change to match real time change. Audit the change process and the bills of material to be sure all changes have been implemented
- Conduct the inspection and testing of finished goods inventory on plant produced items and non-plant produced items as needed due to product complaints or other identified quality issues
- Establish and maintain the laboratory equipment, methods and reagents using the method assurance procedures, calibration procedures and standardization procedures as required by the Global QC Manual. Resolve issues that arise on the accuracy/correctness of methods or reagents or equipment
- Establish and monitor on an ongoing basis that chemical raw materials are tested against the Ecolab specification C of A’s are received as proof of meeting the Ecolab specification for chemical raw materials that require testing. Coordinate the review of the chemical raw materials that should be tested. Resolve a problem chemical raw material by interfacing with Corporate or Local Research, Development & Engineering or suppliers or other plants, as needed
- Evaluate customer returns as needed to resolve complaint issues by identifying the root cause and participating in identifying the action needed to eliminate the root cause
- Serve as communication liaison with the in-line product maintenance persons from each R&D division to resolve day-to-day questions that arise on products, product specs, rework, complaints, plant QC procedures, FDA/EPA requirements, etc
- Maintain the procedures for the FDA products GMP requirements including production record reviews, incoming raw material lot approval, product testing, label control, retainer maintenance, GMP procedure maintenance
- Support the complaint handling process to assure timely and accurate feedback. Participate in an in depth, detailed investigation. Provide follow-up on the outcome of the complaint process to eliminate root cause that have been identified
- Maintain the retainer review process. Provide a mechanism to document variations identified and report them to the appropriate R&D division. Verify that all required retainers are being taken and retention requirements are being met
- Establish and maintain the daily execution of production specification QC requirements including: finished product testing, data recording accuracy, maintaining retainers and analytical testing
- Maintain safety procedures in the laboratory. Audit that safety requirements are being met or followed
- Recommend continuous improvement projects related to manufacturing and distribution procedures
- Bachelor’s degree in Chemistry, Chemical Engineering or related scientific area
- Minimum 3 years of experience required, including experience working with or in a manufacturing/plant environment
- 4+ years’ experience with 3 + years’ experience in consumer product industry, regulated production or similar manufacturing environment & related Supply Chain or R & D function
- 3 years supervisory experience
- 1 year supervising a team
133
Quality Supervisor Resume Examples & Samples
- More than 5 years quality assurance experiences in sheet metal company(Mandatory). Must be familiar with punching, bending, welding and painting processes and related technical
- Very strong problem solving skills (Mandatory), be familiar with 8D, 5 why analysis
- Have knowledge with ISO9001 & ISO14001 standard with practice experience
- Six Sigma GB is plus
- Good communication skill and coordinate ability
- Basic reading and writing in English
- Mechanical major, bachelor degree is preferred
134
Quality Supervisor Resume Examples & Samples
- Responsible for incoming, in-line, and final quality control testing and processes
- Quality auditing
- Quality training
- Supervise quality staff and train/assist employees in department procedures and performance expectations
- Assuring products and processes meet required customer and internal quality standards and requirements for our growing facilities
- Ability to prepare quality control reports (including data analysis)
- Ability to identify and institute corrective action when necessary
- Interact effectively with customers and all levels of CTDI management
- Strong analytical, problem solving, and decision making skills
- Excellent communication and interpersonal skills with the ability to lead and motivate others
- Must be an organized, self-motivated individual
- Have the ability to work independently and as part of a team
135
Quality Supervisor Resume Examples & Samples
- QUALITY CONTROL LABORATORY
- Oversees all testing and inspection staff and their activities for all assigned applications
- Ensures all testing standards (ASTM, AWWA, AWS, ASME, etc) are being met
- Provides weekly status report that includes testing metrics
- Ensure all testing and inspection are in compliance with the project specification
- Provide appropriate test data to inspecting agency personnel
- Maintain and interpret test data, monitoring trends
- Train subordinates for higher levels of responsibility
- Bachelor Degree in Engineering , College or High School Diploma
- Minimum five years of experience in manufacturing of welded steel pipe
- Certified Welding Inspector
- ASNT LEVEL II in PT, MT, RT or UT
- Nace Level II or III
136
Quality Supervisor Resume Examples & Samples
- Actively engaged in planning, defining, and directing the site auditing control program to ensure compliance to all procedures and policies, GMP standards, Mondelez requirements, and regulatory, federal, and local laws
- Trains, mentors, and leads site QA and Production team to insure program goals are met. Strong support to site QCMS/ISO program owners. Monitors and maintains plant QCMS program by complying with current Mondelez and International Audit (FSSC/ISO) standards
- Support Hold/Release documentation and dispositioning of products
- Acts as SAP Quality Data Steward role and maintaining compliance
- Responsible for maintaining, validation, and continuous improvement of all laboratory testing and equipment
- Facilitate plant sanitation. Coach and audit production leaders and employees on sanitation practices
- Manage and direct Environmental Health and Safety (EHS) crew to ensure facility is cleaning completed and crew works safely. Maintain facility cleaning database to ensure cleaning routes stay on track. Create plans to continously drive improvement improvement and mitigate any gaps. Actively supervise crew to coach their learning, grow their capabilities, and hold them accountable. Ensure their schedules, attendance, and paychecks are accurate in appropriate systems
- Support and/or lead Quality functions as directed by the Quality Manager and Sanitation/Compliance Manager
- Facilitate and co-lead cross-functional QCMS team and participate in Mondelez corporate to ensure successful certification for site
- Ensure all specifications/KPI/QCMS/FSSC/ISO plans are maintained and updated/approved as required. Co-lead plant bi-annual validations
- Support all internal and external inspections and regulatory visits. Support audit preparation activities, accompany inspector, and complete necessary reports and postings
- Support QM pillar functions, lead MSA/line certifications, and engage actively on facility IL6S journey, including engaging on other pillars and/or supporting work processes as identified
- Minimum 2 years of experience in a quality and/or technical leadership role or minimum 2 years of experience in operations/quality/technical (R&D) role
- Experience with Quality Systems, procedures, and policies, including HACCP, Pre-Operational Inspections, Sanitation, Product Specifications and Product Testing (eg KPOGS)
- SAP usage for vendor complaints, ingredient COA
- KWIC usage for tracking materials that are on hold
137
Industrial Quality Supervisor Resume Examples & Samples
- · Prepare and manage technical dossier for contract manufacturers production
- · Prepare and manage the quality agreement between L’Oreal and contract manufacturers
- · Secure all formula information per L’Oréal’s procedures
- · Manage Quality Master - running reports and maintaining SAP fields
- · Control and release finished goods and packaging components
- · Initiate the corrective action process for finished goods, packaging components
- · Develop training and train quality personnel on the use of new test methods
- · Participate in subcontractor’s certification program (test delegation, control and process validation)
- · Lead the approach of continuous improvement of quality: monitoring performance, analyze quality reports, monitor the change management
- · Bachelor's degree in Engineering or Science
- · Experience in the cosmetic, pharmaceutical, medical device nutraceutical or fast moving consumer goods industry
- · Ability to influence
- · Knowledge of GMP standards
- · Proficient in SAP
- · Strong Microsoft Office skills especially with Excel
- · Strong attention to detail and desire to follow procedures
138
Quality Supervisor Resume Examples & Samples
- Develop and implement a OpEx organizational structure capable of supporting the strategic initiatives of the local Plant and lead the efforts to integrate quality needs into the development of short and long-term improvement plans. This includes leading/supporting the operation in the implementation and improvement of the local Quality Management System and Lean/Six Sigma initiatives
- Provide Quality interface and expertise between the operation and its customers to proactively identify or anticipate their needs and expectations and ensure they are understood and satisfied. This includes the complaint management system and the corrective/preventive action process related to customer issues – with feedback (Customer and Division) – and the coordination of customer visits and audits
- Develop a thorough understanding of the Eaton Business System (EBS) with expertise in the tools related to OpEx (e.g. – EQS, OpA, EBEA, EPM, Ethics, Vision, Mission, Values, Philosophy, Organizational Capability Assessment, and Corporate Accounts). Appropriate levels of this knowledge must be transferred to all subordinates as part of their personal development
- Lead the deployment and integration of the Eaton Quality System (EQS) into the local Quality Management System
- Analyze key organizational quality and continuous improvement metrics related to EPM (e.g. – Customer Returns DPPM, Internal Quality, Scrap, Warranty, Cost of Nonconformance, and Supplier Quality) and perform periodic reviews to evaluate results and establish action plans to close the gaps at an operational level
- Actively participate as a member of the leadership team in the deployment of the Eaton Business System (EBS) tools process to integrate initiatives into an overall comprehensive site strategy
- Provide support to the Supply Chain Management organization relative to Supplier Quality activities of the operation as well as provide Quality interface, expertise and support to the organization’s suppliers and partners. This includes the feedback of supplier performance to suppliers and the Division
- Lead the internal Quality System Audit program for the organization and manage the corrective action system in conjunction with the management review process
- Provide expertise in Quality Assurance and process improvement tools/methods to the other functions of the organization to support them in their continuous improvement activities
- Recommend new or leading-edge technologies, methods, tools and procedures on the fields of quality assurance and continuous improvement to proactively address changes in the business environment
- Develop and analyze statistical data and product/process specifications to determine standards and establish proposed quality and reliability requirements for the finished product
- Manage the performance and provide career development opportunities to all the employees within the OpEx function of the organization. This includes the development and implementation of training programs to build “bench strength” in the organization
- Manage the budget of the OpEx organization
- Lead the development and implementation of the site Lean and Six Sigma strategy, actions, and cross-functional activities to eliminate waste, drive customer satisfaction, reduce cost, and improve working capital performance
- Provide Lean and Six Sigma support across the organization to drive short-term and long term business improvements by identifying performance gaps in assessments such as OpA, EBS Pull, EBEA, etc. and work with the leadership team to prioritize improvement activities and close gaps
- Promote plant wide culture of continuous improvement and learning and facilitate cross-functional continuous improvement teams and other project teams to accomplish improvements throughout the facility
- Bachelor’s degree in Engineering or Business from an accredited institution required
- Minimum of 3 years of experience in manufacturing engineering, product engineering, or quality assurance
- 1-2 years of manager of people experience
- Lean/Six Sigma training or certifications
- Previous role in Quality Assurance
- Quality Management System experience
139
Quality Supervisor Resume Examples & Samples
- Provides direct supervision, resolves personnel issues, conducts performance evaluations and performs supervisory discipline as necessary
- Ensures compliance with quality system documents, cGMPs, ISO standards and FDA regulations
- Schedule and prioritize quality inspection, testing, and documentation review to support Operations and release of product
- Identifies and develops opportunities to improve existing processes and procedures
- Assist in and manage the verbal communications and visual checks of work activity to ensure quality requirements are met. Ensure proper corrective actions, discrepancy reports and follow up activities are accomplished. Advise on equipment condition, test method, etc. to aid in the course of action when components do not meet specifications. Responsible for quality inspection and verification
- Reviews documentation and records for accuracy. Determines if product is impacted, can be released, or if Non‐Conformance Report (NCR) is required
- Assist in developing documentation and procedures during the qualification of new equipment/inspection methods
- Performs other duties as assigned based on business needs
- Education or Equivalent Experience: Associate’s Degree in Technical or Engineering
- Experience: 5-8 years of experience
- Supervisor experience 3+ years or equivalent experience
- Coordinate Measuring Machine (CMM) experience
- Experience working in ISO 13485 or FDA-regulated industry
140
Quality Supervisor Resume Examples & Samples
- Prepares Statistical Process Control Charts
- Analyzes data and puts corrective actions into place
- Performs ESD and ISO audits
141
Enjoy Life Foods Quality Supervisor Resume Examples & Samples
- Design, develop and provide quality systems training and education programs for employees
- Assist in facilitating site document and record control, and corrective & preventative action programs
- Facilitate and document site based hold management systems, requirements and procedures including product disposition and destruction in accordance with ELF Quality and Food Safety Standards
- Food Safety Representative for site HACCP Team
- Directly manage 5 Quality Technicians
- Facilitate site based quality systems to assess compliance to published product and process specifications
- Oversee allergen testing program including data analysis, trending, reporting and recommendations
- Knowledge of the Windows working environment including Word, Excel, and PowerPoint
- Strong background in math and computers; working knowledge of descriptive statistics
- Proven application of engineering principles, laboratory methodologies, food science, statistics, and quality tools
- Strong oral, listening, and written communication skills in order to communicate with all levels of the organization
- Strong project management and planning skills with proven ability to manage numerous projects simultaneously
- Strong interpersonal communication and leadership skills, and the ability to effectively negotiate, influence, and persuade
- Excellent analytical and troubleshooting skills
- Excellent interpersonal skills, with the ability to influence, motivate, and lead a team
- Building and sustaining relationships to ensure a strong team environment
- Strong decision making skills and prioritization skills
- Ability to work independently without supervision as well as within a team setting
- Attention to detail required when working with scientific data and analysis
- Ability to work different schedules as needed for testing and projects
- Physical requirements: Sufficient mobility, strength, flexibility, hearing, and sight to access all job relevant areas of warehouse in a high forklift traffic environment and perform routine activities as necessary to deliver required results. Some pushing/pulling, bending/stooping, and lifting (up to 50 lbs.) necessary
- ·4 Year Degree in Quality or Food Science (preferable, but not required)
- 3 to 5 years of relevant experience (change to at least two years)
- 1+ year managing people (change to at least two years)
- Experienced in GFSI Quality Systems such as SQF, BRC, FSSC 22000 or ISO 9000 preferable
- Ability and aptitude to work in an R&D, Manufacturing, and/or Distribution environment
- General understanding of Good Manufacturing Practices (GMP's), Good Laboratory Practices (GLP's), Hazard Analysis Critical Control Point Systems (HACCP), ISO, Regulatory Guidelines, Sensory, and/or Microbiology
142
Senior Quality Supervisor Resume Examples & Samples
- Performing corrective action investigations, determining root causes and defining corrective/preventive action measures
- Performing internal audits
- Establishing and maintaining metric capture programs, trending activities and implementing the QC plan
- Conducting and leading internal and external meetings and interfacing with customers
- Implementing and maintaining a Quality System meeting customer and registration system requirements
- Providing strategic support at a branch location level
- Communicating and interacting effectively with all levels of the organization and with external auditors/customers
- Performing training and supervising of the inspection workforce
- Act as lead auditor with strong emphasis on ISO/TL9000 registration requirements
- Evaluate and update current inspection and system procedures
- Identify process and product deficiencies and research improvements
- Perform Qualification tests on work benches
- Set up and participate in QAT''s and meetings
- Manage the Quality Information Systems (QIS)
- Conduct customer on-site visits
- Train new and current employees
- Initiate and manage new projects
- Provide strategic direction to take CTDI Quality to the next level
- Strong understanding and experience of TL9000 and/or ISO 9001 Quality standards
- Expertise involving electronic equipment, diagnostics, and/or electronics repair
- Working knowledge of IPC-610 and its application to process control
- Strong documentation keeping best practices
- Excellent analytical skills, organizational skills, and follow-up skills
- Ability to create and deliver presentations
- Proficiency in Excel, Word, and Power Point - will need to be able to chart and graph trends, create metrics, and track and monitor data
- Must be able to communicate with all levels of management
- Must be detail oriented and a team player
- Ability to read electronic and electrical schematics and machine shop drawings
- Ability to motivate production/quality performances
- Must be flexible in work duties and schedule
- Knowledge and understanding of Total Quality Systems and/or ISO/TL 9000 registered system
- Strong root cause and trend analysis reporting skills
143
Quality Supervisor Resume Examples & Samples
- Hire and train Quality A Technicians and Auditors, schedule working hours, including over/under and weekend overtime for Quality Technicians and Auditors
- Interact with customers/ suppliers to resolve quality issues
- Problem resolution at the plant level
- Monitor supplier systems to gauge quality performance
- Support AQP activities with suppliers
- Define and improve plant standardized quality systems
- Complete special projects in the areas of quality system improvement and corrective action
- Complete quality system training of plant
- Facilitate implementation of new quality system requirements
- Thorough knowledge of manufacturing operations
- Customer and supplier written and verbal interaction
- Systematic problem solving skills
- Experience in conducting or preparing for QS/ISO quality system audits
- Eight Discipline Problem Solving training or experience
- 2 or more years of related experience and/or training; or equivalent combination of education and experience
- Minimum five years in a manufacturing environment
- Minimum three years in supervisor capacity preferred
144
Quality Supervisor Resume Examples & Samples
- Be a driving force in ensuring a strong and committed culture of quality throughout the organization
- Develop and implement a Quality organizational structure (utilizing the OCA) capable of supporting the strategic initiatives of the region and lead the efforts to integrate quality needs into the development of short and long range strategic business plans for the operation
- Provide Quality interface and expertise between the operation and its customers to proactively identify or anticipate their needs and expectations and ensure they are understood and satisfied. This includes the complaint management system and the corrective / preventive action process related to customer issues – with feedback to the region – and the coordination of customer visits and audits
- Partner with the Supply Chain Management organization relative to the Supplier Quality Assurance activities of the operation as well as provide Quality interface, expertise and support to the organization’s suppliers and partners. This includes the feedback of supplier performance to suppliers and the division
- Provide expertise in Quality Assurance and process improvement tools and methods to support the continuous improvement activities to insure compliance with the policies of the Eaton Quality System and TS 16949
- Participate as an equal member of the leadership team, all of whom are responsible for the advancement of the quality goals and objectives of the organization to insure the quality and effectiveness of the product and processes utilized in the plant. The end goal is complete customer satisfaction with product quality, delivery and responsiveness to issues with the objective of being proactive and preemptive
- Support the initiatives of the operation in the development, implementation and improvement of the appropriate Quality Management Systems throughout the organization, with all the documentation required. This includes providing advanced quality planning support in the development and launch of new products, processes and services
- Support the internal Quality System Audit program for the organization and lead the corrective action system in HB in conjunction with the management review process
- Drive the deployment of the Eaton Quality System process for HB including identification of improvement actions that result from the EQS assessment process
- Gather and analyze key organizational quality metrics related to the Balanced Scorecard and perform periodical reviews to evaluate trends and results and establish action plans to provide the necessary improvement at an operational level
- Develop and analyze statistical data and product / process specifications to determine present standards and establish proposed quality and reliability requirements for the finished product
- Manage the performance and provide career development opportunities to direct reports through the utilization of the OCA and APEX. This includes on- going coaching and feedback to ensure organizational goals are met
- Identify, design and/or implement quality assurance training programs for key personnel in conjunction with the Eaton Quality System to satisfy the needs of the organization
- Participates on the Material Review Board as well as authority for Special Process MRR
- Is a customer representative
- Bachelor’s degree from an accredited institution in Engineering or Chemistry
- Minimum of five 5 years’ experience in quality, manufacturing or engineering
- Minimum of two 2 years’ experience developing and leading strategic quality, manufacturing or engineering projects
- Legally authorized to work in the United States without company sponsorship
- A demonstrated knowledge of quality assurance and continuous improvement methods, approaches and tools, including strategic planning and project management
- Proven track record of leading and managing quality initiatives that have resulted in improved productivity and reducing cost of non-conformance in a manufacturing setting
- Expertise with Six Sigma, Lean Manufacturing, Eaton Business Excellence Criteria, Project Management, Organizational change management, Quality Management System standards (i.e. ISO/TS 16949:2002, etc.)
- Interpersonal communication skills and leadership development ability
- Experience in managing a quality function and building organizational capability in that function
- Prefer Six Sigma Blackbelt or Greenbelt certification
- ASQ Certified Quality Manager (CQM), ASQ Certified Quality Auditor (CQA)and/or ASQ Certified Quality Engineer (CQE)
- Advanced technical knowledge in product design functions, manufacturing processes, inspection, metrology, metallurgy, statistical methods, and quality auditing
- Master’s degree in engineering, industrial management, quality, or business from an accredited institution as a plus
145
Quality Supervisor Resume Examples & Samples
- Monitor the production operations through coordination production audits, completion of product testing, and maintenance/review of documentation
- Create regular reports on operational performance and investigational reports as required
- Interface with Manufacturing Operations and Engineering team members regarding identification and resolution of production floor and/or product problems
- Participates in or leads investigations related to process deviations, nonconformances and customer complaints, as well as participating in CAPA activities
146
Quality Supervisor Resume Examples & Samples
- Create and develop an executable plan for their team to support the validation of S045 engines and power generators in the factory
- Monitor the validation process to ensure adherence to standards and criteria
- Develop and set the validation criteria for engineering change requests
- Responsible for the SORT meeting where defects found during S045 follow are assigned to the offending process
- Responsible for providing direction to the BIQ coordinator who will monitor walk backs and request RCCA for systematic issues
- Responsible for managing and monitor the robustness of the S045 Validation process and the new NPI Validation process
- Set priorities and establish a work plan for themselves and their team in order to complete broadly defined assignments and achieve desired results
- Lead & support continuous improvement activities impacting assembly. Gateway metrics, Audit Validation, ISO audit for Issue Recording
- Ability to lead team member on career developmental opportunities & following departmental guidelines
- A Bachelor’s degree with 1 year of experience with NPI Plant Readiness/NPI Programs OR minimum 3 years of experience with NPI Plant Readiness/NPI Programs
- Experience with APQP, PPAP, TFC, Prove Design, VDRA/VB, Ship Loose, and Change Control Board
- Knowledge on systems like EDS, MCS, and JRS
- Experience in validation of new products, Issue capture and resolution (S045 & S095 process)
- Experience with Design & Manufacturing Review & Machine shop Processes
- Familiarity with Plex, ECR workflow, Effectivity, Pset, CIAs, BIQ, DFMEA/ PFMEA, and Quality check sheets
- Basic knowledge on Diesel Engines & Power Generators
- Knowledge on Assembly Planning, Time Standards, Visuals & some Tooling
- Experience in Schooner, Creo, and Teamcenter
147
Quality Supervisor Resume Examples & Samples
- Must be able to effectively work with external customers and internal employees
- Review and assist the Quality Manager in making disposition of any non-conforming materials or products
- Initiate and maintain “Quality Hold Areas” within the facility
- Assure timely disposition and movement of any on hold material throughout facility. This requires involvement of departmental leaders
- Supervise Inmates in all three P.I.’s that are performing quality functions. ( approx. 30 inmates)
- Supervise incoming inspections of critical raw materials
- Assist Quality Manager on any internal trials (i.e. new products)
- Responsible for publishing quality reports as they relate to inspections and production
- To assist the Quality Manager in designing, implementing and maintaining the plants HQMS
- To maintain inventory control of all color standards
- Coordinate and Schedule color signing meetings
- To collect and send out GreenGuard samples
- Must be able to perform all Quality Lab Tests
- To handle the procurement and monitoring of all necessary quality items (i.e. tools, measuring equipment, etc.)
- Assist in the design, implementation and maintenance of the SAFE & TPM modules required for Shaw employees in HQMS
- Supervise all Corrective Action System, Document Control, and Quality Alert System for HQMS
- Assist the Quality Manager with maintaining MOC (Management of Change) within HQMS
- Ensure production set-ups are in accordance with the developed criteria for the respective product
- Assist and be an active participant in any of the facilities trials (XR’s, HMTR’s, etc.)
- Assist the Quality Manager in tracking and monitoring the facility claims
- To act in the capacity of a general Supervisor, filling in for Supervisors when on leave, vacation, and vacancies
- Maintain and update the facilities goals & objectives as they relate to quality
- Work normally scheduled days adhering to starting and stopping times and overtime as required
- Communicate any problem or concerns to the Quality Manager in a timely fashion
- Other duties as assigned by the Quality Manager
- Must be willing to travel to job sites to address any quality related issues
- Must be able to perform standard quality field tests – gloss, moisture, etc
- Building Relationships
- Adapt and change
- Continual Learning
148
Quality Supervisor Resume Examples & Samples
- Coordinates with production the monitoring of processes and procedures to ensure effectiveness and continuous improvement
- Uses Defect Root Cause Analysis for the investigation of consumer and customer complaints and quality related losses. Develops corrective actions and monitors for effectiveness. Troubleshoots using product tests and product specification measurements
- Ensures an active internal quality audit program in compliance with FSSC 22000 and the Nestlé Quality Management System
- Ensure update HACCP, NQMS and SOPs as needed and ensures training of associates at all levels on quality programs
- Manages relationships with internal and external customers, suppliers, colleagues, and support services to ensure achievement of targets
- Manages quality assurance production floor support team by scheduling and assigning work, providing training and managing budgets
- Responsible for ensuring compliance for FSSC 22000 while driving continuous improvement for Quality metrics and KPIs in the factory
- Actively participates in the change control process. Maintains and updates Rework and Allergen matrices for the factory
- Maintain Quality Pyramid. Summarizes the information and reports for operational reviews
- Communicates Quality and Food Safety briefs to the factory
- Summarizes data, and prepares and interprets reports for use by management
- Acts as a communication liaison between management and quality staff to support corporate and plant-driven initiatives
- Supports factory traceability exercises
- Manages factory laboratories for chemistry, incoming goods, microbiology and / or sensory by scheduling and assigning work, providing training and managing budgets
- Ensures daily routine sample analyses using lab techniques and other instrumentation following Good Laboratory Practices and Internal Control Plans (ICP)
- Oversees lab operational activities – daily equipment maintenance, ordering, stock control, stock record entry, reporting, document control, etc
- Ensures lab compliance for FSSC 22000 and NQMS while driving continuous improvement for Quality metrics and KPIs in the lab
- Ensures the completion of internal lab audits in compliance with the NQAC program
- Updates NQMS, ICPs and SOPs as needed and ensures training of laboratory associates. Assists, advises and trains factory employees in attaining NQAC requirements (MI, LI, P-test, etc.)
- Ensures that a high quality of products, services, housekeeping, and hygiene standards are maintained and improved in designated and specifically Lab areas
- Acts as a communication liaison between management and laboratory staff to support corporate and plant-driven initiatives
- Is the key factory contact person with NQAC
- 3-5 years manufacturing and/or laboratory experience required, food industry preferred
- One – three years of supervisory experience in QA/QC preferred
- Must have excellent verbal and written communication skills, proven planning and organizing skills, leadership, teamwork, and influencing or collaboration skills
- Strong mathematical and statistical skills required
- Must be able to manage multiple assignments
- Must be able to perform in a demanding, fast-paced environment
- Must have strong problem-solving and analytical skills
- Must be proficient with computer systems, personal computers, and spreadsheet software (Microsoft Office, etc.) and mainframe system with custom applications
- Proficiency in SAP/GLOBE systems is preferred
149
Quality Supervisor Resume Examples & Samples
- Extensive knowledge of AWS D 1.1
- Current CWI license
- 3 years of progressive work experience performing professional level quality management duties; preferably in metal fabrication industry
- Ability to interact with customers
- Knowledge and experience in ISO 9001 quality standards and models
- Strategic, methodical, logical, and detail oriented
- Excellent verbal and written communicator
- Advanced in data analytics and problem solving
- Proficient interpretation skills for figures, statistics, regulations, and policies
- Reviewing and formulating/revising operations policies and procedures; ability to exercise controls over the implementation of policies and procedures
- Proficient in Microsoft Word, PowerPoint, Excel, Visio
150
Quality Supervisor Resume Examples & Samples
- Knowledge and experience with SAP
- Maintain harmonious working relations with employees from all departments
- Maintain harmonious working relations with management from all levels
- Communicate effectively with all employees and management
- Communicate in English to give and acknowledge instructions and problems
- Ability to apply concepts such as fractions, percentages, ratios and proportions to practical situations
- Ability to interpret a variety of instructions furnished in written, oral, diagram and schedule form
- Two-year college degree in business or related field required; Four-year college degree preferred
- Three (3) -- five (5) years of Food Safety / Quality Assurance experience in a manufacturing environment; Bakery experience a plus
- Experience with the administration of various training topics for new hires and annual regulatory compliance in groups of (2) two -- (25) twenty-five participants; Experience with tracking training events a plus
- Bilingual in English/Spanish preferred
- Proficient in MS Office applications such as Excel, PowerPoint and Word
- Excellent communication, decision-making and organizational skills
- Strong self-confidence and leadership skills
151
Quality Supervisor Resume Examples & Samples
- Ensure compliance to the organizations Quality Management Systems Certification’s and requirements
- Conducting and complete report’s on internal, line and process audits
- Maintain and publish defect reports and analysis at all levels of the value stream
- Quality voice for customer in the plant, driving resolution on the day to day shop quality issues, including coordinating the containment, corrective and preventative actions needed to protect the customer
- Develops and monitors daily data analysis and process capability analysis
- Responsible for the In Process Validations of product for verification, effectiveness, accuracy and develops charts to monitor related results
- Identify and eliminate any behaviors and processes that put safety and/or quality at risk
- 2 years of experience in manufacturing or assembly procedures
- Minimum of 1 year of team lead or supervisory experience
- Extensive knowledge of PLEX or Shop Floor Manufacturing Processes
- Understanding of blueprints, GD&T, Tolerances and Measurement System Analysis
- College or University Diploma
- 2+ years of quality assurance related experience in a manufacturing/assembly environment
- Yellow Belt, Green Belt or Black Belt Six Sigma Certification
- ASQ or similar Quality Certifications
- Experience with Six Sigma, Shainin, 8D, FMEA and problem solving techniques
- Diesel Engine repair and troubleshooting experience
- 2+ years of experience in engine assembly operations
- Advanced computer skills in office and shop floor control software
152
Quality Supervisor Resume Examples & Samples
- Supports implementation of UL QMS in the site to assure consumer safety and overall quality of final product being manufactured
- Supports efforts to verify compliance of site operations to UL QMS through program of internal quality audits
- Supports preparation of local procedure and work instructions that ensure UL and other applicable standards are accurately represented in local procedures and work instructions
- Leads efforts to complete and maintain external audits and certifications
- Lead, manage and coordinate all the activities associated with Food safety plan as well as company GMP program
- Leads efforts to verify and document compliance to regulatory requirements applicable to quality and consumer safety, and to ethnic / religious requirements
- Leads site implementation and on-going verification of HACCP plan and pre-requisite programs such as pest controls, allergen management, hygienic controls, etc
- Oversee the communication and resolution of pest control related trends between pest control technicians and the plant
- Supports efforts to verify and document the traceability of materials, packaging and products e.g. includes annual dummy or mock recall exercises
- Utilizes SAP QM and Unilever specifications including Interspec system and supports verification of use for quality purposes
- Supports site required actions necessary to manage product incidents e.g. data and information requested by MCO Quality
- Supports the implementation and verification of procedures to control non-conforming materials and products
- Supports implementation and on-going verification of category / technology GMP as applicable to the site
- Supports implementing and assessing of on-going compliance to in-take control program for received materials and packaging
- Supports implementing and verifying site calibration and maintenance program for inspection, measuring and testing equipment
- Supports the implementation and maintenance of system where key quality data and information are recorded and preserved
- Supports data collection, analysis and assignment to standard Quality loss trees in support of operational KPIs reporting
- Supports / participates in Quality Pillar activities in WCM
- Supports / participates in structured quality improvement activities related to customer, consumer issues and CRQS gaps
- Trains employees on food safety, quality assurance concepts, policies and procedures
153
Quality Supervisor Resume Examples & Samples
- Manages and coordinates the activities of staff including training, employee development performance evaluation, hiring decisions, and the establishing of goals and performance objectives for assigned department
- Provide Continual evaluation of department processes, methods, and activities to assure the most effective use of resources and equipment
- Manage budget and expenditures
- Responsible for all quality related processes at the facility
- Provide support manufacturing, engineering, sales and marketing
- Effectively utilize the authority to acquire corrective action through management
- Monitor, review and approve quality audits
- Acquire working relationships with technical staffs or operators, contractors, agents and facility personnel
- Attend industry seminars and trade shows, as available and ad specified
- Comply with all NOV Company and HSE procedures and policies
- Bachelors degree in related field or equivalent combination of education and experience
- 5 + years experience
154
Laboratory Quality Supervisor Resume Examples & Samples
- 2 years of experience in a laboratory leadership role
- Bachelor of Science Degree
- Basic knowledge of performance improvement concepts
- Demonstrated experience in laboratory quality management and/or laboratory activity
- New York State Clinical Laboratory Technologist License
155
Quality Supervisor Resume Examples & Samples
- Training and Developing: Assist in leading and organizing formal/informal problem solving in areas of scrap, process capability warranty, etc. Provide training in quality systems and related areas such as APQP, BOS, Problem Solving, Statistical Process Control, Gage R&R and DOE
- Customer Support: Support compliance with external customer requirements, including customer visits. Interface with design/process engineering, purchasing, manufacturing plants and customer on new product/process launches
- System Support: Conduct system and product audits. Assist in maintenance of TS-16949 and ISO 9001 certification. Coordinate/facilitate continuous improvement in system compliance, product quality, customer satisfaction, cost of quality, etc
- Communication/Reporting: Provide risk assessment to Plant Manager, Business Unit and Director of Quality on customer design/quality issues. Submit monthly plant PPM performance to Direct of Quality. Coordinate corrective action responses to the customer
- Employee must perform his/her job within acceptable safety, environmental, quality, productivity and performance standards as outlined in plant policies, handbooks and applicable work instructions
156
Quality Supervisor Resume Examples & Samples
- Performs and reports internal and 3rd party audit results
- Acts as primary resource for the local office on quality issues, training and implementation of quality program
- Maintains and updates local quality policies and procedures
- Proves metrics data on required bases
- Supports complaint analysis and corrective action reporting
- Unpacks, identifies, logs and marks client’s samples and packages using standard procedures
- Performs clerical duties in accordance with standard procedures
- May assist with other administrative tasks when needed
- May provide temporary phone support
- Maintains a clean, organized and safe work environment
- Performs other work as required
- High School Diploma or equivalent; Bachelor Degree in related field or the equivalent preferred
- 2+ years related quality or operations experience
- Excellent communication skills in both verbal and written format
- Excellent prioritization, organization and time management skills
- Ability to work independently in a fast-paced, multi-tasking environment with shifting priorities
- Microsoft Office software proficiency
- Ability to lift up to 49 pounds
157
Weekend Quality Supervisor Resume Examples & Samples
- Ensure staff is appropriately trained to perform assigned work. Develop, maintain and implement training requirements for all personnel. Conduct training and certification activities as required
- Develop in-depth understanding of inspection methods in mixed-model operations environment
- Full understanding of quality procedures related to all stages of own area of responsibility
- Monitor the production operations through coordination of production audits and maintenance/review of documentation
- Participate in or lead investigations related to process deviations, and non-conformances, as well as participate in CAPA activities
- Initiate Engineering Change Requests (ECR)
- Lead improvement projects including new equipment and fixture design
- Identify and escalate complex problems for resolution, including partnering with technical staff to develop and propose solutions to operating issues
- Accountable for the performance and results of a team within own discipline or function
- Document owner for assigned product line inspection procedures
- May represent the organization to outside contacts, e.g., vendors, suppliers, contractors, staffing agencies
- Conduct performance reviews, including resolving performance issues
- Participate on cross-functional teams Engineering, management, Regulatory, Manufacturing, HR, Planning for the development of cohesive production operations
- Bachelor's degree in engineering, science or related field, with a minimum of four years’ experience in a Medical Device or Pharmaceutical Manufacturing environment. Alternately, a combination of education, certification (ASQ certification as a CQE, CQA, CQM, SSGB or SSBB), and 10 yrs. supervisor and quality experience in related fields may be considered a substitute for a bachelor’s degree
- Sound analytical/statistical skills and technical writing capability
- Good understanding and experience in compliance to ISO13485 and FDA 21CFR820 regulations
- Demonstrated ability to supervise teams and provide coaching and feedback, including responsibility for all employee actions including hire/fire authority and partnering with HR on all aspects of employee relations
- Ability to analyze and adjust line/operation layouts to improve efficiency / effectiveness
- Working knowledge of Enterprise Resource Planning (ERP) system, preferably JDE
- Experience working in a medical device industry, preferred
- Excellent communication and interpersonal relationship skills; possessing strong collaboration skills in partnering with cross functional stakeholders in order to achieve objectives, as well as mediating differences to achieve consensus
158
Quality Supervisor Resume Examples & Samples
- Implement and maintain Quality Management Systems to guarantee that we produce safe and legal products to the correct specification
- Achieve the daily BRC standards for food safety
- Meet customer codes of practice and technical standards
- Meet KPI for quality daily and weekly dashboard are met
- Implement any corrective actions are implemented as directed and agreed
- Be actively involved in the operational excellence and process optimisation agendas
- Work with the Technical and Quality teams ensuring that product development trials and activities are introduced in a controlled fashion
159
Quality Supervisor Resume Examples & Samples
- Assure timely inspections that support materials releases and engineering requests
- Maintain staff and equipment to assure appropriate technical capabilities
- Monitor inspection procedures for effectiveness
- Monitor compliance to appropriate regulatory standards
- Effectively communicate with and provide support to other departments as necessary
- Maintain a department culture of continuous improvement
- 3 – 10 years quality supervisory experience in medical industry
- Associates Degree/Bachelors degree or related experience
- ASQ certification in quality, six sigma, and/or lean manufacturing is desired
- Ability to work within a team and as an individual contributor in a fast-paced, changing environment
- Ability to leverage and/or engage others to accomplish projects
- Multitasks, prioritizes and meets deadlines in timely manner
- Strong organizational and follow-up skills, as well as attention to detail
- Ability to maintain regular and predictable attendance
- Experience working with inspection tools and instrumentation preferred
160
Quality Supervisor Resume Examples & Samples
- Supervises the Quality Technicians and Inspection personnel ensuring product is tested and inspected in a timely manner without sacrificing quality
- Manages production testing, inspection and receiving inspection
- Ensures the completion of gauge qualification and gauge R&R requirements
- Ensures compliance to gauge calibration and control requirements
- Ensures compliance to the customer and internal requirements to test and inspection record requirements
- Must understand and be able to apply basic inspection and testing techniques, including various types of sampling plans; must be able to read and interpret blueprints (drawings), including geometric dimensioning and tolerancing (GD&T)
- Reviews, monitors and reports on trends in quality and testing data and makes recommendations as to adjustment, correction and monitoring
- Develops, reviews and trains quality instructions (SWI) and methods for inspections and testing
- Supports timely and effective responses to customer quality issues
- Supports and supervises effective employee relations. Provides employee coaching and development. Assists in resolving employee issues through problem resolution
- Supports and ensure that teams and team members have the necessary resources and training to accomplish department and facility goals
- Supports and conducts individual and team coaching sessions to improve performance. Recognizes team accomplishments
- Supports and manages department priorities
- Assists Quality Manager in development of new quality processes administration, training, and auditing of processes
- Conducts Safety audits and assessments within the Quality Department and ensures a safe work environment and continued awareness of Safety
- Supports and assists in the achievement of goals and objectives of the Quality Manager, Engineers and Technicians
- Ensures completion of Dock Audits
- Ensures completion of Layered Process Audits
- Ensures compliance to all areas of the Quality Management System and MAFACT within the Quality Department
- Minimum of 5 years previous experience in a Quality Supervision role
- ASQ quality certification preferred
- Strong communication and team building skills
- Previous experience in production reporting (scrap, rework, labeling, etc.) within computerized operating system
- Previous experience in problem solving in a team based atmosphere
- Working knowledge of O.E.M. customer requirements & expectations
- Working knowledge of basic automotive requirements as it relates to quality
- Working knowledge of basic quality functions, inspection equipment and techniques
- Ability to read and interpret GD&T and CMM layout data (PC DMIS software prepared)
161
Senior Quality Supervisor Resume Examples & Samples
- Assist in preparations of policies and procedures to comply with regulatory requirements
- Work with engineering and manufacturing personnel and in conjunction with them resolve problems of product design, specifications, materials, tooling, and production operations affecting quality
- Participate in customer and supplier visits as required to confer on specific quality problems
- Control inspection, rework, and reprocessing of customer returns (where applicable)
- Participate in audit of the plant for conformance with FDA Good Manufacturing Practices and ISO 13485 requirements
- Assist in the direction of Documentation, Incoming, Calibration, Inspection, Release and Quality Systems Departments to ensure the maintenance and development of new and existing products to the Everett facility
- Help to develop and maintain an effective organization through selection, training, compensation, and motivation of all assigned personnel
- 1+ years’ supervisory experience
- Medical device experience required
- Experience with sterile disposable medical devices in an environmentally controlled room
162
Quality Supervisor Resume Examples & Samples
- Monitor, supervision and responsibility for quality indicators
- Build, improve and promote quality awareness within organization, conduct trainings
- Provides regular statistical report for quality improvement by systematically collecting and analyzing information and taking the initiatives to ensure corrective actions are taken
- Draft quality control plan according criteria and customer requirement
- Evaluate and analyze customer complain issues, lead the root cause investigation and follow up & evaluate the actions
- Perform system, process and product audits
- Implement actions and corrective actions in order to improve quality in different production areas
- Driving continuous improvement project or Kaizen
163
Quality Supervisor Resume Examples & Samples
- Manage a team ofQuality Inspectors and Technicians
- Work closely with Production to address issues
- Investigate causes of non-conformities
- Participate in 8D customer responses and coordination of
- Experience in Quality within a manufacturing environment
- Bachelor's Degree in Engineering or related technical field or a minimum of two years of lead role in the injection mold industry
- Knowledge and experience implementing Six Sigma, Statistical Process Controls, FMEA, process audits and other proactive quality management practices is preferred
- Ability to collaborate with cross functional departments with results oriented is a must
- Effective communication skills both verbal and written
164
Quality Supervisor Resume Examples & Samples
- 4-year technical degree with emphasis in science and/or math preferred
- 5 years Industry experience preferred
- Knowledge of ISO 9001 and ISO 17025 quality management systems, Good Manufacturing Practices (GMPs) and FDA regulations
- Proficient computer skills, including Microsoft applications and Lotus Notes
- Demonstrated ability to work independently and be self-motivated
165
Quality Supervisor Resume Examples & Samples
- Bachelor degree and above with major in Mechanical Engineering or related majors
- At least 5 years experience in Mechanical Part Manufacturing Industry or related industry in JV or foreign company
- Familiar with quality system
- Knowledge in 6 Sigma and Lean as an advantage
166
Quality Supervisor Resume Examples & Samples
- Maintains full quality and regulatory compliance while driving process effectiveness and efficiency at the site
- Reviews standard operating procedures for company directives and compliance
- Conducts site education of non-Quality Assurance personnel, responsible for professional development of the site Quality Assurance team
- Monitors, controls, and analyzes product and process quality to meet internal and external customer requirements
- Determines through statistical data continuous improvements projects
- Performs accident investigation and coordinates appropriate corrective actions
- Develops safe operating procedures
- Performs safety training for all levels of the organization Administers Worker’s Compensation claims
- Implements and manages safety policies, procedures, and practices. Including but not limited to; Lockout, Confined Space, PPE, Hearing Conservation, Respiratory, Guarding, Forklift, Fall Protection, Forklift, GHS, & Impact Review, and Emergency Response
- Leads the safety improvement process and implements safety practices throughout the organization
- Conducts safety and environmental audits/inspections and advises employees on safe work practices and potential hazards
- Trains production leadership on safety-related topics and coaches employees on accident prevention and safe work practices
- Proven leadership skills (experience successfully managing people/projects/processes/issues)
- Change agent with energy, passion and enthusiasm
- Bachelor’s Degree in Occupational Safety and/or Quality disciplines a plus
- At least 3 years of quality experience
- Lean experience highly desired
167
Direct Hire Quality Supervisor Resume Examples & Samples
- Desire candidates with experience in the automotive industry but this is not necessarily required
- Degree in business related field or Engineering; or minimum 3 years related experience and/or training in manufacturing environment; or equivalent combination of education and experience
- Strong written and verbal communication skills, work well with diverse groups of people and be able to function independently of direct supervision
- Must be able to prepare documentation and present to Senior and Executive Management both internally and externally
- Understanding of project management
- Knowledge of various quality system methodologies, 8D, 5 Why's, DFMEA, PFMEA, Control Plans, AIAG-PPAP, APQP, and etc
- Working knowledge of TS/IATF 16949, ISO 9001, and ISO 14001
168
Quality Supervisor Resume Examples & Samples
- Takes a hands-on supervisory approach to all Quality Control Technicians
- Is responsible for resolving maintenance and quality control issues
- Directly supervises, trains, and evaluates employees
- Communicates and coordinates activities with other shift supervisory staff and Operations Manager ensuring smooth production work transitions
- Actively monitors, documents and works to improve quality issues facility wide
- Assists with audits as needed
- Makes proactive recommendations and offers solutions to the quality systems manager to improve quality and efficiencies
- Is responsible for manufacturing, distributing and consistently maintaining safe and quality food by following good manufacturing practices, allergen controls, food defense, HACCP and SQF requirements
- Is responsible for immediately reporting all food safety and quality issues to your manager
- Is responsible for partnering with others; Sharing knowledge, skills and information within your team and across functional areas
- Bachelor Arts/Science in chemistry, biology or related field preferred
- Five plus years experience supervising quality personnel in a good manufacturing or GMP regulated environment
- Bilingual skills (Spanish/English) preferred
169
Quality Supervisor Resume Examples & Samples
- Demonstrates expert functional, technical and people and/or process management skills as well as customer (external and internal) relationship skills
- Understands the strategic impact of the function across sites
- Must be able lead and direct projects and business initiatives
- Financial, analytical and statistical skills to resolve complex and conflicting objectives
- Knowledge with databases
- Understand metrics and department metrics
170
Quality Supervisor, Evening Shift Resume Examples & Samples
- Ensure the compliance with the Manufacturing Strategy and the achievement of the highest quality standards
- Respect schedules and business plans associated to the various phases of a program launch
- Act as a leader in analyzing the root causes of quality issues in your sector
- You have experience in Quality
- You have a strong knowledge of our products
- You have an excellent bilingualism written and spoken (english and french)
- You have the capacity to work with concepts and translate them into solid execution plans, good project management skills
171
Quality Supervisor Resume Examples & Samples
- Assure compliance to quality standards through effective supervision of Quality Lab personnel
- Understand and interpret product specs for quality attributes
- Understand, interpret, and develop Quality standard operating policies/procedures
- Maintain compliance to customer requirements and research customer complaints
- Provide leadership to Quality personnel while promoting cooperation between other departments
- Assist employees in resolving work related problems/concerns
- Responsible for ongoing training of staff, planning, assigning and directing work
- Conduct employee performance appraisals and performance improvement process
- Maintain department expenses within established budget
- Maintain inventory supply and order as needed
- Participate in third party and internal audits
- Attend weekly production boardwalks, weekly performance meetings, daily scheduling meeting
- Participate in R&D meetings
- Conduct Held Product Rework meetings
- Train in Annual Sensory and Annual Quality Calibration
- Conduct Weekly Department Meetings with Quality Leads
- Participate in Sensory and Product Cuttings
- Maintain Micro and Incoming Sampling matrix
- Actively participate on the plant Food Safety and HACCP teams
- Assist with Raw Material complaint notification decisions
- 3 years supervisory responsibility, preferable in a food manufacturing environment
172
Plant Quality Supervisor Resume Examples & Samples
- Ensure that any non-conforming material is monitored and disposed of in accordance to NC material process utilizing quality gate issue identification and detection
- Work with Quality Inspectors, Side Line support, Liaison, Quality Coordinator and external sorters to maintain scrap log on a daily basis and work with the suppliers on NC material disposition
- Ensure process conformance & product quality audits are conducted through standardized work
- Ensure all hourly personnel is updated and trained according to latest issues reported internally and by the customer
- Ensure that CSS inspectors are measured utilizing monthly performance reviews and scorecards
- TS16949 Element champion as required
- Prepare management quality reviews
- Coordinate & establish quality gates/containment (FL1, FL2, VW Side line support, etc.) when required and ensure data analysis for closure
- Coordinate and ensure inspector communication between shifts for activity and issue follow up
- Responsible for activities defined on standardized work list
- Graduate of accredited university/college in engineering, technical or business, preferred
- Experience in quality and PPAP/PSW submissions to automotive customers, TS16949 and VDA 6.3 requirement knowledge
- Five years relative experience in an automotive assembly or manufacturing environment
- Three years of supervisory experience in a manufacturing environment
- Experience in inspection with strong skills in Quality and Root Cause Analysis
- Experience with computers and good math skills
173
Quality Supervisor Resume Examples & Samples
- Serving as a company wide resource on a highly specialized area or serve multiple units in a broader functional area and assist senior management in interpreting and using information provided
- College or university degree or 2 years quality experience and prior leadership experience
- 5+ years of experience in manufacturing, engineering, and/or quality
- Previous experience working with company policies and procedures related to manufacturing, engineering, and/or quality
- SAP and Infinity experience is preferred, but not an expectation of the position
- Expert knowledge of a specific manufacturing process or engineering discipline
- Good human relations skills are needed to develop a cooperative work relationship with others inside and outside the department
- ASQ quality certification
174
Quality Supervisor Resume Examples & Samples
- Oversee the development, implementation, review and maintenance of the current GFSI program
- Take appropriate action to maintain the integrity of the current GFSI system
- Responsible for verifying and validating changes to food safety and food quality plans that have an impact on the acceptability of food prior to release
- Maintains SQF Documentation – Policies, Procedures, Work Instructions, Forms, Training, etc
- Participate in 3rd party audits
- Participate in daily sensory panel
- Responsible for managing training needs of departments
- Complete/Track CAPA items
- Issue Internal Quality Audits
- Review completed Internal Quality Audits and follow through with corrective/preventive actions when necessary
175
Quality Supervisor Resume Examples & Samples
- Must understand and demonstrate safe work practices at all times to ensure a safe work environment and comply with all company policies and procedures
- Create and maintain a positive and respectful environment for all employees that is free from intimidation and harassment
- Contribute to the accomplishment of Key Performance Indicators including safety, quality, production, cost and lean implementation
- Monitor and manage the facility’s food safety program as the facility’s SQF practitioner
- Responsible for coaching, mentoring, selection, and training of QA technicians and QI inspectors
- Responsible for creating/editing of quality policies, work instructions, inspection plans, and procedures
- Responsible for planning, assigning, and directing work; appraising employee performance; rewarding and disciplining employees; addressing complaints and resolving problems and disputes
- Evaluate production schedules to ensure the appropriate staffing levels meet production demands and monitor work hours to balance overtime
- Develop, analyze, and present Key Performance Indicators as they relate to EDW quality
- Lead and support root cause investigations and analysis on quality related issues
- Facilitate and promote use of appropriate problem solving techniques such as 5 Why’s for effective root cause analysis and successful corrective action
- Effectively communicate with other Supervisors to ensure internal and external investigations such as CAPA and complaint forms are effectively communicated and completed in a time manner
- Create or revise SOP standard operating procedures, work instructions, test protocols to ensure quality of product
- Approval and issuance of product masters, BOM’s, and QC in process documentation
- Bachelor’s or Associate's degree preferred and one to three years of relevant experience in manufacturing, or an equivalent combination of education and experience
- Previous supervisory and or team building experience is required
- Working knowledge and understanding of incoming material and component
- Ability to comprehend and follow the Quality policies, SOP’s, work instructions, and inspection procedures
- Ability to communicate effectively before groups of customers or employees
176
Field Quality Supervisor Resume Examples & Samples
- Provide regular supervision, oversight, auditing, and monitoring of field-based Technical Specialists on both an announced and un-announced basis, to ensure quality and integrity of services
- Oversee field-based Technical Specialists for select pre-inspection meetings (PIM’s), inspections, or critical testing as directed by the Technical Manager
- Lead the technical support required by the sales and business development teams, with regional field perspective on technical information for large or important bids and tenders
- Execute internal or external quality investigations and provide corrective action training to Technical Specialists as required
- Engage with clients in the region to promote Intertek capabilities and provide them with technical support and insight on quality related items
- Lead the rollout and implementation of new or strategic initiatives, such as eReporting, in region
- Conduct technical interviews with potential candidates to determine whether they possess the skills and technical knowledge necessary to work as a Technical Specialist for Intertek
- Identify and monitor the disciplines and competencies of Technical Specialists to ensure Intertek and client expectations are met and exceeded
- Mentor less senior technical staff and perform other work as required
- Complete billable work for clients as required
- Bachelor’s Degree in Engineering or equivalent work experience
- 10+ years of direct field-based quality experience, preferably providing shop inspection services to the oil and gas industry
- Should possess recognized professional certifications relevant to the business (AWS/CWI, ASNT, API, ASME, NACE, etc.)
- Advanced knowledge and experience with vendor surveillance/shop inspection
- Superior knowledge of oil and gas equipment used for control, processing, and movement of petroleum products; i.e. valves, pressure vessels, pumps, turbines, compressors, diesel/gas engines, etc
- Clear understanding of basic procurement and fabrication processes with knowledge of relevant codes and specifications for the oil and gas industry
- Ability to make technical decisions and engineering judgments independently where limited standardization exists
- Must be self-motivated with organizational and time management skills
- High degree of personal integrity and the ability to collaborate with others in a team based environment
- Excellent interpersonal and demonstrated communication skills, both verbally and written
- Excellent leadership and management, mentoring, and coaching skills
- Ability to promote an effective working relationship at all levels and create a positive work environment
- Ability to travel frequently throughout the continental US (up to 80% of the time) with occasional overseas travel
- Proficient in MS Office programs and Outlook
177
Quality Supervisor Resume Examples & Samples
- Incumbent must perform his/her job within acceptable safety, environmental, quality, productivity and performance standards as outlined in plant policies, handbooks and applicable work instructions
- Bachelors degree in engineering, statistics, or related field, or equivalent experience
- 3-5 years experience in automotive quality, preferably manufacturing related
- PPAP Experience
- Knowledge of customer requirements for FCA and FORD
- Strong written and verbal/interpersonal communication skills
- Knowledge of automotive OE quality systems/requirements preferred
- ASQ certified quality engineer, certified quality auditor preferred
- Experience with TS 16949 (PPAP, APQP, FMEA, etc.)
- Knowledge of SPC, DOE, and GD&T
- Strong training skills
- Excellent problem solver – understanding of 8-D methodology
178
Production & Quality Supervisor Resume Examples & Samples
- Safety management
- Follow Air Products safety procedure
- Lead and implement supervisor level safety activities, be responsible for the quality team safety
- Join safety incident survey, develop and carry out the prevention actions
- Check and eliminate safety issues proactively
- Develop production site house-keeping plan and make the responsible area in order
- Quality management
- Establish the quality assurance system and make the system in effective
- Collect national and local quality codes and get the codes implemented
- Decide and explain the products inspection criteria
- Develop the quality target, implementing plan and evaluating plan
- Execute quality data collection and analysis, draft the improvement plan
- Survey and analyze any quality issues and follow up till all correction/prevention measures implemented
- Organize monthly quality meeting
- Monitor the production process, prevent and correct any improper operation
- Track the production record, ensure its conformity and validation
- Decide if the quality of raw material, cylinder, semi-finished products and products are up to standard or not. If not, raise the disposing comment
- Organize internal source to handle the audit by customers, certification bodies and internal management
- Quality control on outsourced gases and maintain the quality stable
- Provide quality training for operation team, improve team’s quality awareness
- Manage the inspection and measuring tools
- Complete the tasks in management system relating quality
- Job incumbent is expected to have 3+ years work experience
- Good in communication skill
179
Quality Supervisor Resume Examples & Samples
- Be in charge of controlling the production flow, planning, organizing, motivating and coordinating the Dorval plant
- Identify, document and standardize key processes leading to the achievement of objectives and optimize the sharing of knowledge and best practices throughout the organization
- Exert your leadership while respecting the vision and values of Bombardier Aerospace
- You must have strong management skills and an extensive aerospace experience, plus a college degree diploma or equivalent experience
- You must have values and a vision wich conforms with the company's philosophy
- You are bilingual (french and english), and have good communication skills and the required flexibility to work with different teams
180
Quality Supervisor Resume Examples & Samples
- Knowledge of equipment related to individual specialty codes
- Knowledge of safety and operating procedures for aircraft
- Knowledge of applicable publications, drawings, diagrams and schematics
- Knowledge of customer and/or company forms required by work requirements
- Ability and experience writing with clarity and technical accuracy
- Excellent communication, effective leadership and interpersonal skills
- Additional knowledge/skills may be required by contract or assignment
- Ten (10) years aviation experience, with 2 of those years in a supervisory capacity
- Prior experience as an Aviation Inspector
- Prior aircraft experience with quality systems that meet FAA requirements
- Experience working with and interpreting, precision measurement instruments
- FAA Airframes and Power Plants License (A&P) preferred or documented aircraft hands-on senior supervisory experience in the military, or commercial aviation operation
- Formal or Specialized Training or Equivalent FOD and TCP Awareness
- AS9100C Program Awareness Security Clearance Awareness
- Operational Risk Management, Anti-Terrorism, and Security/Safety Training
- Extensive working knowledge of MDR, MS, SCIR, and NAVFLIR as referenced in CNAFINST 4790.2 series as well as OPNAVINST 3710.7 series and OPNAVINST 3750.6 series
- Must have in-depth operational knowledge of the Naval Aviation VIDS/MAF operating procedures
- Must be able to meet any Government / Company licensing / qualification requirements for the position
- Additional experience/education may be required by contract or assignment
181
Mfg Quality Supervisor Resume Examples & Samples
- Manages and develops Finished Goods Auditors, Process Auditors, and Inline Inspectors on assembly line and in sub-assemblies and kitting. Supports a Risk-based auditing approach
- Ensure audit schedule and percentages are adhered to
- Monitors audit fails to look for opportunities to improve operator standard work (process steps, visual aids). Provides input to VWI team
- Creates and prepares Auditing Reports and other quality reports
- Attends daily Production Meeting and adjusts auditor assignments as required
- Must interact well with operators, Group Leads, Supervisors and QE team members to assist in mentoring and adherence to standard work
- Holds meetings with Operation’s Team to drive resolution to Process or Systems Audit failures
- Participates in Q-Team meetings for Finished Goods Audit fails
- Front line liaison to line QE’s, production supervisor(s) and staff in executing troubleshooting, root cause analysis and implementing corrective action on issues affecting production
- Manages the gauge calibration process and gauge calibration technician
- Maintains the tablet inspection system to include operating system and inspection elements in coordination with QE’s, ME’s and Operations supervision
- Responsible for coordination of quality aspects for new product development and start-ups in conjunction with Line QE’s
- Assists in ensuring product quality standards are met and adherence to standard work is maintained
- Assists the assembly teams in specifying inspection and testing mechanisms and equipment
- Develops and maintains in-line inspection criteria for critical assembly attributes as well as informational feedback systems from rolling road/finished goods test station
- Assists in the formulation of quality control policies and procedures
- Schedules work to meet completion dates and technical specifications
- Prepares evaluations and develop plans for direct reports
- Evaluates progress and results, recommends changes in procedures or objectives
- Develops and delivers quality control training programs as required
- Controls departmental overtime and operates within approved budget
- Ensure that self and direct reports work in a safe and healthy manner, following all safety rules and regulations
- Maintain a neat, clean, and orderly work area
- Performs other miscellaneous duties as assigned
- B.S. Degree in engineering or equivalent manufacturing or quality experience required
- 3 years previous quality control experience preferred
- Strong aptitude towards and interest in computer programming to manage the Tablet Inspection process is required
- Any VBA, VBScript, VB.Net, ASP.Net, SQL experience is preferred
- Strong problem-solving and communication skills required
182
Quality Supervisor Resume Examples & Samples
- Implement / Maintain The Company Safety Management System
- Head site Safety Committee and related programs
- All other duties and projects as assigned
- Completes routine tasks with minimal supervision
- Demonstrates advanced knowledge of FDA standards and quality systems
- Demonstrates advanced knowledge of Good Manufacturing Practices (GMPs). Provide support as a subject matter expert or as needed in organization
- Ability to communicate and collaborate cross functionally. Builds and leverages relationships and provides support internally within function and with cross-functional teams across the site
- Works independently and adapts quickly and resourcefully to changing situations and business needs while managing multiple projects meeting specific goals and deadlines
- Ability to prepare written communications and communicate problems to management with clarity and accuracy
- Must have the ability to define problems, collect data, establish facts, draw valid conclusions, and identify possible solutions
- Ability to make sound and timely decisions without compromising quality
- Must have the ability to lead others, motivate, coach, and identify development opportunities
- Excellent working knowledge of Computers and Microsoft Office, including Word, PowerPoint, Excel, Visio, and Access
- Ability to interpret a variety of instructions furnished in written, oral, diagram or schedule form
- Validation experience (IQ/OQ/PQ)
- Six Sigma Green Belt Certification is a plus
- Certified Auditor or external supplier auditing experience is a plus
- Ability to read, write and interpret information
- Ability to add, subtract, multiply and divide
- Ability to use hands to finger, handle, or feel
- Ability to sit/walk/stand for up to 10 hours per day
- Ability to intermittently crawl, squat, climb, twist, bend, stoop, push or pull
- Must possess visual acuity, i.e., close, distance, and color vision, depth perception and the ability to adjust focus
- Ability to lift/carry items less than 20 pounds
183
Customer Data & Quality Supervisor Resume Examples & Samples
- Manage the Customer Data Management Team
- Recruit, hire, train, and develop team members on systems, processes, and company policies
- Create employee development plans and conduct annual performance reviews which include setting expectations and direction through defined specific goals
- Monitor processes, and ensure adherence to policies, field requests, and otherwise respond to issues
- Manage the definition and implementation of processes and policy to support requests for new supplier entry or changes to existing supplier data, new/changes to items
- Identify opportunities for improvement, support technology, and define and implement projects to deliver on those opportunities in partnership with other GBO and PTC departments (Sales Operations, Marketing, Renewal sales, Sales, FP&A .)
- Partner with Global Business Organization Management to define and implement internal controls and procedures
- Ensure data integrity and accuracy of supplier data elements through generation of reports and metrics
- Bachelor's degree or equivalent experience
- 3-5 years professional experience; previous Customer Service/Customer Data Management experience preferred; prefer supervisory / coach experience
- Proficiency in CRM software (SalesForce) and ERP (Oracle) and ISO
- Strong analytical and problem solving skills; ability to gather, synthesize and summarize data, also experience with BI tools
- Proficiency in leading projects, providing resolutions to a diverse range of complex problems And using judgments within defined policies and practices
- Detail oriented, accountable, and possesses a high degree of integrity
- Strong interpersonal, oral, and written skill
- Ability to collaborate in a cross functional and global team environment
184
Quality Supervisor Resume Examples & Samples
- Performs audits to monitor compliance with all GMP standards, Food Safety Standards, Food Safety issues, Case and Label procedures and Safety programs
- Supervise employees on the assigned shift
- Review and organize plant processing records for conformance with regulations and Company policy prior to review by the Quality Control Manager
- Provide employee training for Fill Control, Sanitation, Can Seams, Grading and Statistical Process Control
- Perform audits to monitor the sanitary conditions within the manufacturing facility
- Administer the Company Safety program
- Perform investigations of causes for any spoilage issues
- Participate in Food Safety audits as required
- Bachelor's degree in Food Science or a related field preferred
- One to two years of supervisory experience would be beneficial
- Certified or able to become certified in Better Process Control School, Thermal Processing and Container Closure
185
Quality Supervisor Resume Examples & Samples
- A member of materials review board (MRB) & concession, ECN whom able to decide and make disposition
- Liaison with customer on product quality standards, requirements and complaints
- Conduct a thorough investigation on the customer complaints and prepare the appropriate report
- Close follow up corrective action by relevant person / department to ensure and prevent
- Ensure the effectiveness in the implementation of internal and external corrective and preventive actions
- To monitor, follow up and ensure the IPQC & Out going QA to achieve quality goals and objective of the company
- Min certificate in Engineering and 5 years’ experience in manufacturing industry
- Proficient in English language both written and spoken
- Experience of working in a global multinational company
- Proficient in MS Office applications and presentation skills
- Knowledge in electronic components business and applications
- Knowledge in TS16949 automotive requirements such as SPC, APQP and PPAP
- Knowledge in ISO13485 medical standard requirements
186
Quality Supervisor Resume Examples & Samples
- Guide activities and personnel in the gas and physical testing laboratory to provide efficient and accurate test results in accordance with ISO 9001 standard, and other applicable standards and regulations (NIOSH, CE Mark, etc)
- Participate in and promote Quality at daily, weekly and monthly performance review meetings
- Develop, compile and report metrics for testing and calibration systems
- Train employees on all aspects of the testing process
- Ensure a safe work environment through development and maintenance of safe work practices, and implementation of and participation in training, observation and corrective action programs
- Champion and provide leadership in corporate and site specific EHS and regulatory compliance projects and programs
- Manage non-conforming material and monthly material review and dispositioning
- Develop, implement and improve Quality Management systems (Certificates of Analysis, Laboratory Data Handling, etc)
- Bachelor’s degree in science or engineering
- 2 years of combined experience in a quality or engineering role
- Ability to successfully obtain security clearance under the Canadian Controlled Goods Registration program is a mandatory requirement for this position
- Bachelor’s Degree in Chemistry, Biology or Chemical Engineering
- 5 years of experience in a manufacturing environment
- Solid understanding of analytical instrumentation, data acquisition systems and statistical analysis
- Proven knowledge of ISO 9000 Quality Standards
- Knowledge of SPC applications (ie: Minitab)
- Exposure to Measurement System Analysis techniques such as Gage R&R
- Software
- Experience with laboratory testing operations would be an asset
- 3M Canada welcomes and encourages applications from people with disabilities. Accommodations are available on request for candidates taking part in all aspects of the selection process
187
Quality Supervisor Resume Examples & Samples
- Bachelor degree in any engineering field
- Above 5 years experienced in quality or production function of manufacturing environment
- Strong in supervisory skills and problem solving skills
- Knowledge in quality system and ISO 9001
- Define problems, collect data, establish facts and draw conclusion
- Able to communicate in English
188
Quality Supervisor Resume Examples & Samples
- Performs Quality Assurance for a business division by performing product test procedures, validating product specifications, performing audits, and leading product reliability improvements via Caterpillar’s New Product Introduction program and Continuous Product Improvement programs
- Develops plans and tools to support quality systems and related processes for a business division. The incumbent provides support for quality programs and certifications, as well as Lean Manufacturing and systems implementations
- Supports business division employees tracking continuous quality improvement projects and a quality scorecard, leading internal quality programs, developing related training programs, conducting internal quality audits and facilitating management reviews
- Support launch of new generator assembly line to include: set up of initial quality system, Built in Quality (BIQ) system, collect initial quality data and develop line and team quality metrics
- 4-year Bachelor's degree
- Minimum of 3 years of relevant work experience in generator manufacturing
- Thorough knowledge of relevant quality concepts, certifications, processes and tools
- Strong communications, collaboration and influencing skills
- Prior experience working in a manufacturing environment and/or in the quality field
- Generator assembly & trouble shooting / quality experience
- Ability to effectively train / coach diverse groups about quality concepts, certifications, processes and tools
189
Quality Supervisor Resume Examples & Samples
- Bachelor’s degree from an accredited institution in an applicable field of study such as Food Science, Chemistry, Biochemistry, Microbiology, or similar Science/Engineering and/or 5+ years direct relevant food industry experience
- Root Cause Analysis experience
- HACCP certification required
- In depth knowledge of SQF or demonstrated internal auditing experience (SQF Practitioner Desired)
- Understanding of Food Safety regulations, FSMA, and industry and market trends, including PCQI? Are you PCQI Certified
- Demonstrate communication, organization and listening skills
- Excellent attention to detail and follow through
190
Shift Quality Supervisor Resume Examples & Samples
- Working knowledge of continuous improvement principles, i.e. Lean, ACE, QCPC, DIVE
- Supervisory experience with hourly bargaining unit employees
- Knowledge or ability to utilize PC Based information systems a must
- US Citizenship is required for this position
- Bachelors in Engineering, Business or related field
- Ability to work with all levels of Management
- Established background in Quality functions, processes, and procedures, AS9100 and Regulatory Agency Requirements
- Supervisory experience with a Collective Bargaining Unit preferred
- Demonstrated ability to motivate teams using ACE Tools to obtain high levels of performance to accomplish goals
191
Quality Supervisor Resume Examples & Samples
- Primary responsibility of this position is to drive cross-organizational initiatives to leverage improvement opportunities across NCR Business Units
- Responsible for preventing our customers from experiencing quality issues by promoting process adherence, rigor and improvement
- Required to ensure that Manufacturing has the appropriate processes and documentation to consistently produce high quality Products
- Proactively prevent problems and improve Product Quality; Resolve Quality issues and ensure that the correct Closed Loop Corrective Action is implemented
- Provide technical assistance to Manufacturing, SLM and Operation on procured items and modules
- Ensure those that impact our ability to meet customer performance (Deliver, Installation, and Support) and problem resolution (customer questions, problem reports and complaints) requirements in an effective, complete and efficient manner
- Participates on action teams to implement Quality Management Systems, ensure that an adequate Quality Management system is maintained and audited (e.g., ISO90000, ISO14001)
- Consults, defines and presents quality metrics for specific Initiatives/ projects
- Promotes the use and appropriate defect preventions practices to ensure NCR solutions improvement
- Plan and execute Acceptance tests for new product and material localization, coordinates results with development organization
- Provides Technical support, compiling information from various sources to aid the identification and resolution of quality problems and initiatives
- Experience and understanding of quality
- Great communication skills
- Engineering or technical degree - preferred
192
Area Quality Supervisor Resume Examples & Samples
- Direct the Production Zone team to deliver the quality management system aspects within the zone, including the completion of all QC tasks in order to ensure compliance with customer, manufacturing unit, legislative, divisional and strategic requirements
- To lead the transfer and handover of all QC tasks to the Production Zone team to enable the transfer from QC to QA
- Provide information and demonstrate operational practice in support of external audits to enable compliance with customer requirements
- Continue to develop the capability of the Production Zone team through the Technical Strategy
- Monitor Production Zone Technical KPI’s adjusting team activity to ensure targets are achieved
- Assist the Production Zone Manager in the planning and maintenance of resource utilisation in order to complete the required QA tasks
- Lead and deliver a project(s) to create business effectiveness and cost efficiency
- Building production capability and understanding to achieve relevant technical requirements
- Ensure that a safe working environment exists for all employees and that as a minimum the Production Zone meets the standards set out in the SHE Policy/Actively contribute to both customer and technical process development reviews to promote improvement to quality and consistency of production
- Food degree or equivalent qualification or relevant experience
- Internal audit experience
- Intermediate Food Hygiene certificate level 3 / Level 3 Health & Safety
- Relevant food manufacturing experience
- Ability to use computer programmes including word, excel and related technical IT packages
- HACCP principles and practice
- Allergen awareness-implications / related to labelling
- Shelf life determination and awareness
- Hygiene & disinfection principles/Basic microbiology awareness
- Principles of risk assessment
- Legal labelling –basic requirements & Nutritional Awareness
- Basic knowledge of Weight legislation
- Knowledge of technical KPIs
193
CS Quality Supervisor Resume Examples & Samples
- Supervisory experience in supervising QA Specialist, preferably in a call center center environment (2 Years)
- Experience in leading teams, project management methodology, process improvement methodology, and call center industry (4 years)
- Experience managing cross-functional relationship to drive business initiatives (1 Year)
- Demonstrated ability to interact with peers, senior management, and other departments in a professional manner in effort to reach business goals, and demonstrates the ability to influence those individuals/groups to produce results
- Strong organizational, leadership, and interpersonal management skills to allow collaboration across multiple business units
- Demonstrated communication skills, both written and verbal
- Experience with Microsoft Windows suite (e.g., Word, Excel, PowerPoint, Outlook)
- Self-driven, eager to learn and goal-oriented with strong time management skills
194
Quality Supervisor Resume Examples & Samples
- Ability to work on complex tasks, and interpret technical documentation including schematics, drawings, SCDs
- Demonstrate writing skills and ability to communicate effectively
- Ability to effectively utilize problem solving skills and Statistical Process Control
- Have, or develop, knowledge of all internal manufacturing processes and product requirements
- Must develop and maintain good team member and interdepartmental relations
- Must have people motivation skills
195
Quality Supervisor Resume Examples & Samples
- Manage, train, evaluate performance, and assign duties of direct reports (Quality Inspectors and/or Quality Auditors) to ensure productivity, efficiency, and effectiveness
- Implement quality control plans for new products
- Introduce and manage the quality assurance processes of current products
- Lead team responsible for analyzing defect data and implement improvement initiatives to ensure continuous product quality while reducing costs
- Supervise activities associated with development and implementation of
- Bachelor's degree in engineering, business or related field plus 3 years’ experience; or 8 years’ experience as a Quality Auditor, Quality Inspector, or in a related manufacturing role
- Experience in or knowledge of quality systems
- Demonstrated successful ability to collaborate on cross-functional teams
- Demonstrated successful ability to prioritize and multi-task various and conflicting responsibilities
- Master’s degree in Business or related field
- Exposure to Six Sigma and other continuous improvement tools
- Lean Process experience (Green or Orange Belt, Kaizen, Value Stream Mapping)
- Experience with Advanced Product Quality Planning (APQP) processes and/or Statistical Process Control (SPC)
- Quality Auditor certification (ASQ CQA), Quality Engineer certification (ASQ CQE), or Manager of Quality/Organizational Excellence certification (ASQ CQMOE)
196
Quality Supervisor Resume Examples & Samples
- Leads / Oversees activities of Quality Engineers and Technicians
- Provides guidance on 8D’s / White Boards completion
- Coaches / Brings On-board New Quality Engineers
- Prepares Value Stream for Customers visits and Prepares Executive Reports upon completion
- Maintains professional and technical knowledge by attending educational workshops; reviewing professional publications; establishing personal networks; benchmarking state-of-the-art practices; participating in professional societies
- Contributes to team effort by accomplishing set Quality Metrics by Operations Top Management
- Analyzing Information
- Reporting Research Results
- Technical Understanding
- Promoting Process Improvement
- Developing Standards
- Manufacturing Methods and Procedures
- Supports Innovation
- Operations Research
197
Quality Supervisor Resume Examples & Samples
- Knowledge of relevant cGMPs and Controlled Substance Regulations
- Excellent communication, organizational and writing skills
- Working knowledge in MS Word, Excel and other MS Office components
- Ability to coordinate, facilitate and organize resources
- Ability to work under pressure with multiple tasks and deadlines
- Superior customer service orientation with strong follow-up skills and attention to detail
- Ability to appropriately manage highly confidential material
- Must be a self-starter, be able to work independently and have the ability to multi-task under strict deadlines
- Prior experience working in Quality Assurance/Regulatory Compliance
- Knowledge of clinical requirements is preferred
- Experience in working with a high-paced distribution facility is preferred
198
Quality Supervisor Resume Examples & Samples
- Develop, implement and monitor performance against short and long-range plans to achieve quality control and objectives
- Implement short and long-range plans relative to quality assurance
- Identify needs, and develop the quality control department
- Develop or modify quality procedures, metrics and processes to achieve quality and on time delivery goals
- Provide direction to ensure compliance with all applicable customer requirements and government regulations involving product quality
- Select and develop competent inspectors and auditors to ensure quality goals are achieved
- Provide reports as required and drive corrective action and preventive action for timely and effective completion
- Assist as required in all qualify assurance functions as necessary
- Assure effective communication and reporting to customers
- Assure compliance with control phase of quality systems and initiatives such as internal auditing, statistical process control and testing
- Support the development and utilization of quality feedback tools to maintain and implement "lessons learned"
- Support the achievement of Business Operating System Quality Goals and Objectives, as identified by the Quality Leadership
- Minimum of 3 years Quality Engineering experience working with quality systems
- This position requires use of information which is subject to the International Traffic in Arms Regulations (ITAR). All accepted applications must be U.S. Persons as defined by ITAR (U.S. citizen, Green Card Holder,U.S. Permanent Resident, Political Asylee, or Refugee)
- Must live within 50 miles of Los Angeles, CA
- Experience with hydraulics and electro-mechanical application
- ASQ CQE, CQM, CQA
- Six Sigma Green Belt/ Black belt
- Working knowledge of Practical Inspection techniques
- Knowledge of FAA Standards and Reporting is a plus
- Experience with AS9100, AS9102
- Experience with Material Review Board and Corrective Action Board functions
- Experience working with continuous improvement and problem solving tools including root cause corrective action, failure analysis, 8D charts and process flow diagrams
199
Quality Supervisor Resume Examples & Samples
- Assigns employees to maximize quality control objectives
- Prepares Statistical Process Control Charts
- Performs ESD and ISO audits
- Ensures procedures are followed and may develop procedures for the quality assurance inspection operation
- Frequently interacts with outside customers, vendors and functional peer groups at various management levels and serves as a liaison between customer and the division regarding quality issues
- Directs daily department activities
200
Quality Supervisor Resume Examples & Samples
- Bachelor’s degree in engineering, statistics or related field and previous manufacturing experience required
- 3+ years of minimum experience in Quality in a manufacturing environment
- Previous Quality experience in ISO/TS-16949 environment highly preferred
- Competent in use of core quality tools including; MSA, PPAP, APQP, FMEA, Control plans
- Certified as Internal TS Auditor is a plus
- CQE or CQA certificates preferred
- Strong working knowledge of Excel and Access required. Able to use and develop Access databases preferred
201
Quality Supervisor Resume Examples & Samples
- The Quality Supervisor reports to the Quality Manager and is responsible for the maintenance and continuous improvement of the facility’s quality management systems and performs other quality assurance tasks as necessary to meet the applicable federal, state, and local regulatory requirements
- The position directs quality assurance personnel while maintaining a close rapport with production and the Quality staff to identify and ultimately prevent problems affecting quality
- The QA Supervisor will work with other members of the QA team to investigate product nonconformance’s, customer complaints, operational issues, conduct root cause analysis and implement corrective actions with verification follow-up
- Position is also responsible for the development, training and coordination of schedules for the QA technicians
- Plans and supports all activities related to BRC certification
- Works closely with all staff to ensure all aspects of the quality management system are understood, implemented and maintained. Position is responsible for management of the facility’s document control program and plays a key supporting role in both the internal and external audit programs
- Bachelor's degree in Food Science, Micro Biology, Chemistry or Biology required
- Two years' supervisory experience in a Quality department is a plus
- Two years' experience in a food or beverage manufacturing environment with previous quality systems experience preferred
- Strong committment to quality and process improvement
- Proficient with Microsoft Office Suite
- Knowledge of ERP systems a plus (SAP, MAPICS etc)
202
Quality Supervisor Resume Examples & Samples
- Oversees the testing and release of incoming raw materials and finished goods, and that it occurs in a timely manner
- Insures that proper coverage exists as required by Lyndhurst Operations. This includes scheduling of overtime
- Communicates quality problems and concerning quality trends to Production and Planning at the daily Operations meeting. Investigates, as directed by Management, issues in production
- Determines, with input from QA Manager, R&D and/or Technical Service, when materials that are not within the specifications can be released for consumption or sale
- Manages customer complaints – in particular the containment and swift initial response. Investigative responsibility will depend on nature of complaint
- Works with Lyndhurst Operations to resolve blocked and restricted inventory related to quality
- Enters and maintains inspection plans in SAP
- Manages lab spending according to budget
- Manages the calibration and preventive maintenance programs for equipment and instrumentation in the lab. Also their troubleshooting efforts as needed
- Monitors and communicates lab performance KPIs
- Monitors and insures training of the QC Technicians is executed correctly and that proper records of the training are maintained
- Insures that procedures and processes are followed within the QC Lab, and supports the processes necessary for ISO9001 / IATF 16949 certification
203
Quality Supervisor Resume Examples & Samples
- Key member of Plant Leadership Team contributing to the plant’s safety, quality, service, cost, and engagement objectives. This includes coordinating the plant management reviews
- Direct supervision of quality systems and quality control salaried & hourly employees
- Responsible for setting, monitoring and achieving plant quality objectives in alignment with business and divisional quality objectives
- Ensure ongoing compliance to all of the site’s certifications and registrations
- Host site notified body and customer audits and regulatory inspections
- Coordinate and maintain the plant internal audit program
- Work with suppliers to ensure that they can meet the product, process, and documentation requirements
- Provide training for the plant in quality management systems and tools
- Working with sourcing and customers on supplier surveys, inquiries and customer visits
- Oversight of the Material Review Board to disposition non-conforming materials compliant to quality procedures with proper documentation
- Oversight of incoming, in-process, and finished product testing to support manufacturing operations, new product launches and customer requirements
- Work with tier/lean process to respond to deficiencies and drive continuous improvement of quality systems and quality control processes and output
- Measure quality control effectiveness and efficiency
- Three (3) or more years of combined experience working in a manufacturing and/or quality role
- Experience working in a regulated healthcare environment
- Bachelor’s degree or higher in a science or engineering discipline from an accredited university
- Certification(s) or willingness to obtain one or more of the following
- Lean Six Sigma Black Belt
- American Society for Quality (ASQ™): Quality Engineer (CQE) and/or Manager of Quality/Organizational Excellence (CMQ/OE)
- Ability to lead and influence an organization to achieve performance excellence
- Ability to lead and execute regulatory/customer site inspections
- Internal auditing experience
- Strong communication skills (oral, written and presentation)
- Microsoft Office proficient
204
Quality Supervisor Resume Examples & Samples
- Bachelor’s degree in Engineering or related technical field with 3 years experience in quality assurance
- Knowledge of quality techniques including statistical methods used to analyze and control process variations, capability studies, Gage R&R’s, Control Planning and PFMEA
- Prior first hand experience (2 yrs. Minimum) dealing with customers on quality issues
- Proficient knowledge of AQP and ISO9000 / TS 16949
- Prior experience with ERP – Mfg Pro strongly preferred
- Team-oriented problem solving skills using quality tools and structured methodologies
- Knowledge in Six Sigma methodology (Green/Black belt preferred)
- Knowledgeable in the application of Product/Process and Quality System standards of the International Certification bodies, and Customer Quality Requirements
- Negotiation and conflict resolution skills
205
Quality Supervisor Resume Examples & Samples
- Ensure compliance to CQMS certification requirements, accomplished by conducting and reporting monthly metrics
- Maintain and publish defect reports that are recorded and reported at all levels of the organization
- Quality contact for customers, contact for the day to day quality activities, including coordinating the holds due to quality and the rework needed
- Develops spec sheets for data analysis and review with management
- Responsible for development and information collection for inspection reports used for material review and non conformance reports
- Work with Third Party Provider (3PL), Operations and other functional areas in establishing audit procedures, audit frequencies and quality teams to insure customers are receiving a Caterpillar quality product
- Works to identify high scrap and rework areas and initiates investigations for establishing subsequent improvements
- Bachelor's degree or 4+ years of progressively responsible experience in Supply Chain, Manufacturing, or Logistics
- Previous experience in creating, reviewing, and auditing standard work instructions
- Previous experience in quality inspection, statistical quality control data, and gaging specifications
- Previous experience with Microsoft office suite
- Working knowledge of PPAP, CQMS and CPS requirements
- Working knowledge of ETQ modules (Supplier NCM, CAR, PPAP, and Deviation)
206
Quality Supervisor Resume Examples & Samples
- Selects, trains, develops, retains and manages associates in group in line with Ecolab standards. May conduct laboratory analyses per specifications. Ensures that documentation is kept per Ecolab standards
- For Chemical Plants, University Degree in Chemistry, Engineering, Food Science, or related field with strong Chemistry component. For Equipment Plants, University Degree in Mechanical Engineering or related technical field
- Experience in ISO 9001 and in managing quality improvement projects
207
Quality Supervisor Resume Examples & Samples
- Coordinate the training and performance management of team members in the performance of lab analysis and line functions
- Responsible for the continual monitoring of all products during manufacture to assure conformance to established product specifications
- Provide the necessary technical support to the plant in the areas of processing, packaging and ingredient evaluation
- Participate in the planning, organization and implementation of special projects
- Must have effective communication and leadership skills as well as developed analytical, problem solving and decision making skills
- Prior supervisory or management experience
- Prior quality experience in a production manufacturing environment
- 2 years of experience with the Microsoft Office Suite, including Word and Excel
208
Quality Supervisor Resume Examples & Samples
- Manage quality systems including process documentation, internal quality audit processes, external ISO and quality system audits
- Minimum 2 years of experience in quality systems management in a production environment
- Ability to analyze and translate data into visual charts/graphs for reporting purposes
- Supervisory experience working in a union environment
209
Quality Supervisor Resume Examples & Samples
- Supervise, coordinate, facilitate, and provide leadership to employees directly or through group leaders
- Outline work procedures and assign duties to meet departmental and company requirements
- Provide daily leadership and direction to employees
- Train, advise, and counsel employees on work processes and procedures as well as company policies
- Regulate work flow to ensure maximum use of capacity and efficiency within department
- Ensure project and assignments remain consistent with company practices, policies, and regulations (for example: SOX, OSHA, Management System Standards)
- Interact and support all internal and external customers and set standards that promote good relations and communication
- Research and troubleshoot problems and corrective actions to allow continuous improvement
- Promote the concept of individual responsibility for quality work and workmanship standards
- Track and monitor departmental performance objectives
- Participate in periodic audits to ensure compliance to company standards
- Participate in recruiting, selection, and development of all operations personnel through maintaining discipline and personnel relations, interviewing screened applicants
- Provide input for hiring, terminations, transfers, salary adjustments and promotions
- Adhere to the General Requirements of Team Members
- Perform other assignments as required
- Supervisory Requirements: Multiple exempt and/or nonexempt reports
- Able to work with a high level of accuracy and attention to details
- Able to handle multiple tasks, have good organizational skills and a high level of energy
- Demonstrated ability to communicate with customers and project company image to attract business
- Computer skills-intermediate knowledge of e-mail, Microsoft Word, Excel, Access, Internet Explorer
- Professional attitude and demeanor; problem-solving and prioritization skills
- Abilities listed in the General Requirements of Team Members
- 2222 East Pensar Drive
210
Quality Supervisor Resume Examples & Samples
- Develop and conduct necessary training sessions on preventive quality action for all exempt and nonexempt employees within the division
- Create, define and implement specifications for all raw materials used in the division to ensure product quality and prevent production delays
- Assist the sales, customer service and production staff to achieve a high level of customer satisfaction related to quality problems through immediate, objective, and thorough processing of customer complaints and defective product claims
- Maintain, update and inform all concerned managers of statistical quality improvements
- Assist sales on troubleshooting calls to customers
- Perform other special projects as assigned. ISO 9000 requirements, customers’ needs, and manufacturing capabilities to ensure a quality product and customer satisfaction. Develop, write and implement procedures and maintain the division’s manual with documentation for ISO 9000
- Authorize rejection or reruns of all products that do not conform to requirements and take corrective action in all areas within the division to maximize quality and minimize cost
- Provide leadership and direction through meetings and planning sessions as needed with appropriate supervisors and managers to discuss quality related information and develops corrective actions
- Direct responsibility for all quality issues and successful maintenance of ISO 9000 certification, incoming raw materials, and spoilage
- Perform related projects and duties as assigned
- 5 years technical experience including management/supervisory responsibilities
- High school degree plus 2 years vocational/technical college or equivalent work experience, B.A. or B.S. preferred
- Demonstrated oral and written communication skills
- Label product industry understanding
- Analytical skills (including statistical analysis)
- C. skills
- Ability to design and present training programs
- Ability to effectively manage and develop employees
- Planning/organizational skills
- Ability to interface with various departments
- Knowlege of SPC tools, such as pareto analysis, gathering data, analyzing data, and graphing data
211
Plant Quality Supervisor Resume Examples & Samples
- Leads and develops plant QA staff of 2 to manage daily activities and deliver plant and Division quality goals
- Provides technical leadership and support on critical quality initiatives and product issues
- Develops and prioritizes plant quality improvement efforts and aligns with Division initiatives to deliver maximum business results
- Ensures monthly reports are delivered in a timely manner and action plans are developed on non-complaint metrics; and communicate to Corporate Quality and the plant
- Ensure plant process capability of all Regulatory and Consumer perceptible product characteristics meets or exceeds accepted levels
- Manage consumer complaints data, with action plans to address gaps
- Lead internal assessments and audits as required
- Issue Quality Notifications and administer product holds/releases
- Communicate status of quality through regular attendance at daily production meeting -- address urgent issues raised there and/or initiate longer term improvement plans to resolve quality issues
- Manage lab equipment needs; calibration program, maintenance and training
- Communicate directly with vendors on quality issues; issue corrective action requests and drive compliance to stated responses and timetables
- Be a Leader in the WCO initiative in the plant. Apply continuous improvement methods to enhance manufacturing quality, reliability, or cost-effectiveness
212
Quality Supervisor Resume Examples & Samples
- Key member of the Plant Leadership Team contributing to the plant’s safety, quality, service, cost, and engagement objectives
- Direct supervision of quality systems and quality control salaried employees
- Responsible for setting, monitoring and achieving plant quality objects in alignment with business and divisional quality objectives
- Ensure ongoing compliance of all plant’s certifications and registrations
- Oversee and coordinate creation and release of raw material and product specifications, and when necessary, new test methods
- Lead resolution of customer quality concerns, provide Voice of the Customer to all operations and translate Customers’ feedback into innovative solutions, thus maintaining and improving Customer relationships
- Oversight of the Material Review Board to disposition non-conforming materials complaint to quality procedure with proper documentation
- Oversight of incoming, in-process, and finished product testing to supporting manufacturing operations, new product launches and customer requirements
- Bachelor's degree or higher in an engineering or science discipline from an accredited university
- Minimum of five (5) years of experience working in a manufacturing environment
- Minimum of two (2) years of experience working in a quality role
- Bachelor’s degree or higher in Mechanical Engineering, Chemical Engineering, Materials Science or related discipline from an accredited university
- Minimum of two (2) years of ISO experience
- Experience with statistical tools such as: data analysis, basic statistics, Gage Repeatability and Reproducibility (R&R), Failure odes and Effects Analysis, Statistical Process Control and Capability
- Experience leading a cross functional team
213
Quality Supervisor Resume Examples & Samples
- Setting, in concurrence with the department manager, the daily quality goals and ensures that these goals are achieved for the assigned areas
- Direct the quality teams in evaluating quality of products to meet the customer’s quality and on-time delivery requirements
- Supervise work teams and individuals in the areas of personnel actions in compliance with company policies
- Establish and oversee the performance of appropriate physical and/or chemical tests, inspection and calibration procedures
- Assist in the preparation of written instructions and technical directives for test and inspection activities
- Participate in the development and execution of quality-related procedures and documentation based on Company, Government and/or chemical tests and inspection and calibration procedures
- Verify discrepancies and investigate its root causes
- Develop and implement quality control methods for all manufactured products. Conduct investigation to establish inspection and calibration procedures and performance of these tasks
- Review Engineering packages to ensure appropriate inspection methodology
- Investigate customer returned materials or complaints to determine cause: prepare analysis of problem and recommend corrective action
- Assure that inspection and calibration activities are conducted in the proper manner and insure the accuracy of inspection and calibration reports
- Schedule/ approve overtime, vacations and other personnel administrative requests
- Occasionally attend daily Production Review Meeting
- Completes timekeeping requirements for assigned hourly employees
- Bachelor’s Degree from an accredited Institution
- Minimum 3 years’ experience in the Aerospace industry in Manufacturing or in Quality
- Certificate from Quality Institution preferred, such as CQE, CQA
- Experience in the Fastener industry
- Experience with Nadcap requirements
214
Quality Supervisor Resume Examples & Samples
- Establish and oversee the performance of appropriate Inspection and Quality activities
- Assist in the preparation of written instructions and technical directives for Inspection and Quality activities
- Participate in the development and execution of quality-related procedures and documentation based on Company, Government and Customer procedures
- Develop and implement quality control methods. Conduct investigation to establish inspection and Quality procedures and performance of these tasks
- Assure that inspection activities are conducted in the proper manner and insure the accuracy of inspection reports
- Minimum 3 years of Quality experience in Manufacturing
- Quality experience in the aerospace industry strongly preferred
- ASQ Certification such as CMQ-OE, CQE, CQA
- Experience supervising a team of Quality Inspectors or other Quality personnel
215
Quality Supervisor Resume Examples & Samples
- Ensures that process conditions are monitored and controlled for product consistency and according to the specified conditions
- Ensures that products and process changes are made only according to the sequence of activities specified in the MSA/CSA process
- Ensures that a sound quality management system is implemented and maintained
- Ensures that all testing is carried out in accordance with PolyOne Lab Performance Policy and that all product grading is accomplished in a timely and accurate manner
- Represents the plant and PolyOne in all aspects of professional dealings with customers, the technology community and the commercial group
- Coordinates investigation and corrective action on all plant-related customer complaints
- Assesses training needs and provides training to production employees
- Provides technical support to plant personnel regarding OSHA regulations, state environmental regulations, and federal DOT regulations
- Follows up on corrective actions base on HSE audits
- Obtains and maintains applicable regulatory permits
- Reviews/prepares all applicable regulatory reports and maintains supporting documentation
- Responsible for Industrial Hygiene Monitoring Program for plant
- Participates in the development of and conducts in-house EH&S audits. Maintains documentation
- Responsible for Fire Protection Management for plant
216
Quality Supervisor Resume Examples & Samples
- Promote and actively pursue Safety First mentality and provide feedback on process and safety improvements
- Perform quality control testing by weighing and analyzing ash for carbon content, particle fineness, and air entraining qualities
- Assisting load out personnel as needed
- Ensure attention to detail, accurate data entry and customer service
- Develop an understanding of utility operations and its effects on fly ash quality
- Intermediate computer experience is required (Outlook, Microsoft Word and Microsoft Excel)
- Ability to troubleshoot fly ash quality problems and understand long term quality trends
- Mechanical understanding of large industrial equipment
- Proven attention to detail
- Physical job requirements include working outdoors with exposure to heat and cold, constant standing and walking, climbing, working from heights as well as lifting up to 25 pounds
217
Quality Supervisor Resume Examples & Samples
- Assist with the development of new processes, products, and/or services provided to insure appropriate quality and/or in-process controls are implemented
- Work with teams to solve customer/supplier/product issues
- Investigate issues and customer complaints to obtain root cause and correction action
- Establish or adjust related work procedures to meet business needs
- Provide technical and process direction to quality assurance staff
- Provide leadership, mentoring and supervision for quality assurance staff
- Establish samples plans and inspection procedures
- Evaluate employees through performance reviews, on-going coaching and feedback
- Analyze and resolve, or assists workers in solving work problems
- Oversee the efficient implementation of quality standards, programs and processes to improve operational efficiencies and reduce/eliminate waste and nonconformance
- Train employees in appropriate work instruction processes and ensure training effectiveness in application of job skills
- Review, approve and maintain time and attendance records
- Monitor QA inspection results and nonconformance performance and implement changes to improve operating efficiency
- Develop and implement QA process improvements
- Collect, trend and analyze internal performance metrics
- Train staff in quality concepts, tools, and processes, specifically the Customer Care Center (CCC Tool)
- Participate in and drive project and improvement efforts
- Assist in internal audits, as assigned
- Administer the Continual Improvement Process (CIP) program
- Complete special projects, as assigned
- Minimum 3-5 year general business experience; quality, supply chain or logistics preferred
- Minimum 1 year of experience in the support with Quality Management Systems; ISO:9001 and/or TL 9000 certification preferred
- Bachelor’s Degree or Associate Degree with 1 year of experience supporting a mature QMS or equivalent experience
- Ability to identify problems, and initiate corrective actions and preventive actions
- Perceptual and analytical problem solving
- Ability to set priorities and manage time effectively
- Ability to use Quality Tools such as survey, gap analysis, pareto analysis, fish-bone diagrams, 5-Why and process mapping for fact-based decision making
- Excellent verbal/communication skills
- Personally committed to WWT’s core values (displayed at http://www2.wwt.com/career/careers)
- Independent, professional, and self-motivated
- Able to work with and lead others
- Proficient in Visio, Microsoft Word, Excel and Power Point
- Minimal potential to travel
218
Quality Supervisor Resume Examples & Samples
- Operation of ISO9001 and CQMS
- 4-year degree in an engineering or manufacturing-related discipline (or equivalent)
- Minimum of 3 years of relevant work experience also supervisor experience
- Through knowledge of relevant quality concepts, certifications, processes and tools
219
Quality Supervisor Resume Examples & Samples
- Support QM Pillar functions
- Support and/or lead Quality functions and process improvement projects as directed by the Quality Manager and Compliance Manager
- Prior experience in Quality Control desired
220
Quality Supervisor Resume Examples & Samples
- Bachelor’s Degree in Chemichal, Industrial Engineering or related
- 5+ years of quality experience handling either adhesives, silicone or films preferred
- People-leading skills is a must
- Demonstrated understanding and skills in project and program management, including 3 rd parties
- Lean manufacturing, Six Sigma, ISO or related experience preferred
- Strong math and analytical skills. Strong organization and attention to detail. Strong scientific and engineering knowledge
- Strong written and oral communication skills with ability to be an advisor to clients and build strong and sustainable relationships
- Skilled in team building and experience in effectively working with cross functional teams
- Willing to travel
221
Quality Supervisor Resume Examples & Samples
- Coordinates activities within the organization in support of ISO 9000 requirements
- Conducts internal audits & process audits
- Coordinates the corrective action system, driving internal and external issue resolution
- Coordinates the customer satisfaction program; SCARS analysis and corrective actions
- Serves as customer liaison for the quality function
- Prepares analysis of and reports on audit results
- Demonstrates detailed expertise in very complex functional/technical area or broad breadth of knowledge in multiple areas
- Ability to read, analyze, and interpret the most complex documents
- Ability to respond effectively to the most sensitive inquiries or complaints
- Ability to write speeches and articles using original or innovative techniques or style
- Ability to make effective and persuasive speeches and presentations on controversial or complex topics to top management, public groups, and/or boards of directors
- Ability to define problems collects data, establish facts and draw valid conclusions
- Ability to interpret and extensive variety of technical instructions in mathematical or diagram form and deal with several abstract and concrete variables
222
Quality Supervisor Resume Examples & Samples
- Relevant experience as a Supervisor in a manufacturing environment
- Experience in a manufacturing machine shop environment preferred
- Direct hands on experience working in a quality / inspection function
- Results oriented, with sound judgment
- Excellent demonstrated verbal and written communication skills
- Excellent demonstrated analytical, critical thinking, and strategic skills
- Superior interpersonal skills
- Ability to perform multi-faceted projects in rapidly changing environment
- Resourceful and well organized
- Hands on familiarity of inspection tools and gauging (calipers, micrometers, ring and plug gauges, bore micrometers, height gauges, etc.)
- Must have strong knowledge of GD&T and understanding drawing requirements
- Experience running a CMM a plus
- Must have an understanding of how an ERP system functions
- Must have strong computer skills and knowledge of Microsoft Office
223
Quality Supervisor Resume Examples & Samples
- Oversee QC inspection/auditing across all Operations departments at the Oconee site. Includes “Finished Goods” auditors, Roving Auditors and Incoming Auditors
- Work with Quality Engineers to develop and implement test plans for receiving inspection and see that they are adhered to
- Establish and maintain skip-lot criteria and status of all suppliers and parts
- Assist with supplier audits as needed
- Maintain contact with suppliers on performance and quality issues to successfully close Supplier PDCAs
- Operate the department within variable expense budgets
- Work to minimize operating expenses
- Work with Design Engineering on new product activities
- Review and assist with first article approvals for all upgrades and modification to existing tooling and parts
- Support Internal First Articles and Customer First Articles for new products and significant changes to existing products
224
Quality Supervisor Resume Examples & Samples
- Will participate in evaluation of complaints for adverse event reporting on a global basis and is responsible for submitting necessary reports for North America according to policies and procedures
- Will develop and maintain company Standard Operating Procedures (SOPs) intended to assure compliance with applicable global regulatory requirements and standards
- Will assist or lead in identification, creation, implementation, and maintenance of training for QMS policies and procedures
- Will prepare and deliver presentations to management team
- Will direct supervision of professional and quality support staff including the review, evaluation, and development of reporting associates
- Working knowledge and experience with Quality Regulatory
- Able to orchestrate multiple activities at once under limited direction
- Experience in process mapping
- Strong knowledge of FDA and ISO regulations preferred
- Ability to communicate effectively both verbally and in writing on a global basis
- Working knowledge of manufacturing protocols, statistical tools and methodology, and continuous improvement techniques
- Demonstrated strong problem solving skills
- Proven project leadership and project management skills
- Proficiency in technical writing
- Knowledge and use of relevant PC software applications and skills to use them effectively