Value Stream Manager Resume Samples
4.5
(118 votes) for
Value Stream Manager Resume Samples
The Guide To Resume Tailoring
Guide the recruiter to the conclusion that you are the best candidate for the value stream manager job. It’s actually very simple. Tailor your resume by picking relevant responsibilities from the examples below and then add your accomplishments. This way, you can position yourself in the best way to get hired.
Craft your perfect resume by picking job responsibilities written by professional recruiters
Pick from the thousands of curated job responsibilities used by the leading companies
Tailor your resume & cover letter with wording that best fits for each job you apply
Resume Builder
Create a Resume in Minutes with Professional Resume Templates
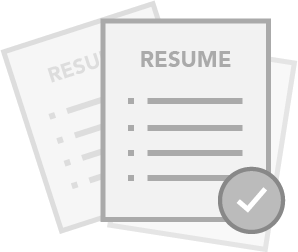
CHOOSE THE BEST TEMPLATE
- Choose from 15 Leading Templates. No need to think about design details.
USE PRE-WRITTEN BULLET POINTS
- Select from thousands of pre-written bullet points.
SAVE YOUR DOCUMENTS IN PDF FILES
- Instantly download in PDF format or share a custom link.
CB
C Bashirian
Chaya
Bashirian
743 Hackett Ford
Dallas
TX
+1 (555) 833 8345
743 Hackett Ford
Dallas
TX
Phone
p
+1 (555) 833 8345
Experience
Experience
Phoenix, AZ
Assistant Value Stream Manager
Phoenix, AZ
McKenzie-Abbott
Phoenix, AZ
Assistant Value Stream Manager
- Recommend changes, assist in continuous improvement initiatives for warehousing processes and implement new systems/processes
- Develop and mentor leaders
- Assist coaches in answering associate concerns/complaints. Identify and implement staffing levels for assignment completion
- Provide leadership to a range of initiatives across departmental lines
- Prioritization of workload to sustain on time shipment of customer emergencies
- Assume responsibility for operations in absence of manager
- Communicate and maintain a culture of open relationships with associates
San Francisco, CA
Value Stream Manager
San Francisco, CA
Rodriguez Inc
San Francisco, CA
Value Stream Manager
- Leading the day-to-day activities within the value stream to ensure that current commitments are achieved while improvements are being made
- Ensure team adheres to quality measures. When quality gaps are identified, collaborate with peers to propose risk mitigation plans to Value Stream Leader and Media Management leadership. Drive research and resolution of any issues, utilize Performance Excellence methodologies/tools to identify root cause; follow all SLAs on issue escalation and resolution
- Ensuring that a current state value stream map is created of the end-to-end value stream(s)
- Budgeting and Cost Management
- Routinely visits production operations to interact with employees, facilitate/assist in root cause determination for safety, quality, and productivity issues, monitor performance and schedule adherence, monitor product quality characteristics, and gather information and input from Supervisors, support staff, and operators to make decisions when. Coaches Supervisors and Team Manager(s) in these areas
- Preparing a future state map that uses kaizen/lean techniques to eliminate waste and improve process value in the short to mid-term
- Actively participates in the following environmental health and safety initiatives: MESH, ISO14001, and the safety / environmental programs established for the facility for a safe work environment. Follow all environmental health and safety procedures and practices to assure a safe work environment. Identify and report unsafe conditions or practices to your manager, EHS Manager, safety coordinator, or any member of the safety team
present
Boston, MA
Senior Value Stream Manager
Boston, MA
Satterfield, King and Ruecker
present
Boston, MA
Senior Value Stream Manager
present
- Leading section operations to consistently meet or exceed business objectives and targets
- Developing and maintaining successful relationship with site union leadership
- Developing relationships to improve performance with key customers
- Maintaining cost effectiveness through aggressive productivity and asset management
- Improving and developing organization capabilities through effective performance management and planning/utilization of human and capital resources
- Developing and maintaining effective area leadership teams
- Responsible for policy setting and defining procedures for the staff in accomplishing and documenting projects
Education
Education
Bachelor’s Degree in Engineering
Bachelor’s Degree in Engineering
Temple University
Bachelor’s Degree in Engineering
Skills
Skills
- Good attention to details, but able to see and manage the big picture and have a “make the numbers" mentality
- Strong planning and organizational skills with the ability to be flexible and adaptable to changing priorities and assignments
- Solid experience with Microsoft Office Excel, Word, and Outlook Solid use of PowerPoint and the ability to present to Sr. Leadership levels
- Excellent interpersonal and relationship management skills with the proven ability to work at all levels of an organization
- Good understanding of HR and Financial acumen is highly desired
- General knowledge and basic understanding of metal forming and welding and assembly
- Flexibility to respond quickly to changing business demands and the ability to assess priorities and act decisively on complex issues
- Excellent listening skills with the ability to size up situations in order to resolve conflict and solve problems with both people and processes
- Demonstrable capability and inclination to make decisions based on data and facts rather than opinion
- Solid use of PowerPoint and the ability to present to Sr. Leadership levels
15 Value Stream Manager resume templates
Read our complete resume writing guides
1
Graduate Value Stream Manager Resume Examples & Samples
- The customer experience and establish Barclays as the ‘GO-TO’ bank
- Mentor and coach the team delivering the Customer Experience initiative in Operational Excellence (LEAN/Six Sigma) and customer centric thinking
- Operational Excellence (LEAN, Kaizen, Six Sigma)
2
Value Stream Manager Resume Examples & Samples
- Lead the delivery of pan Barclays products and services which make a significant impact on
- As part of project delivery, train colleagues in LEAN Six Sigma, innovation, and customer-centric thinking
- Influence stakeholders from across Barclays to support the initiatives you are leading and the overall Group Design Office agenda
- Deliver the operational excellence training
- This role is delivering initiatives across Barclays, so their will be UK and international travel required
3
VP Value Stream Manager Resume Examples & Samples
- Lead the delivery of pan Barclays products and services which make a significant impact on the customer experience and establish Barclays as the ‘GO-TO’ bank, with a budget in excess of £5million
- Support the business clusters across Barclays to identify and prioritise improvement opportunities, which make a significant impact on the customer experience and establish Barclays as the ‘GO-TO’ bank
- Embed a culture of Operational Excellence through LEAN Six Sigma, and customer-centricity into the cultural fabric of Barclays
- Influence stakeholders from across Barclays to support the initiatives you are leading and the overall Design Office Strategy
4
Value Stream Manager Resume Examples & Samples
- Management of all warehouse day-to day activities
- Manpower, capital and expense budgets
- Monitor & manage key performance criteria ensuring key deliverable targets are achieved
- Develop & execute business strategic plans
- Safety & Environmental compliance
- Employee training, development, mentoring and coaching
- Implementation of the Caterpillar Production System
- Prior experience within a fast paced warehouse/operations environment
- Prior experience working in a Leadership position – mentoring and coaching staff
- Ability to develop & lead successful teams
- Experience in a Continuous Improvement environment/Lean manufacturing environment
- Exceptional communication and leadership skills, together with a high level of integrity & honesty
- MS Office Suite including MS excel, Project and Access
- Formal qualification in an engineering , logistics or supply chain related discipline
- SAP System knowledge (or similar operating platform)
5
Value Stream Manager Resume Examples & Samples
- Defining the product family by conducting product routing analysis and appropriate groupings
- Ensuring that a current state value stream map is created of the end-to-end value stream(s)
- Conducting fact-based analysis of the current state map(s)
- Preparing an ideal state map showing what the value stream could look like in the long term
- Preparing a future state map that uses kaizen/lean techniques to eliminate waste and improve process value in the short to mid-term
- Leading the day-to-day activities within the value stream to ensure that current commitments are achieved while improvements are being made
- Conduct Analysis and Provides meaningful insight to support business decisions
- Develop Business cases to help identify opportunities and support decision making process
- Develop and Implement new forecasting & planning methodologies
- Set-up and maintain all Production KPI’s from Planning, Production Control and Continuous Improvements
- Bachelor’s Degree in Engineering or equivalent subject
- Six Sigma Green Belt (Black Belt preferred) or Lean Leader/Facilitator Certification
- 5 to 10 years total professional experience in a manufacturing environment
- Minimum of 5 years’ experience and successful track record in roles focused on use of Continuous Improvement tools and methodologies such as Lean Enterprise, Six Sigma, TPS, or Theory of Constraints
- Minimum 5 years’ experience and successful track record in line roles such as Operations/Maintenance Management, Quality Management or Manufacturing Engineering
- Experience in food, beverage, pharmaceutical or CPG industry in a high-volume manufacturing environment is preferred
- Demonstrated history of successful change implementation and implementing of operational excellence improvements
- Formal training and work experience in managing mid-to-large scale projects
- Ability to work with teams across departments and external partners
- Facilitator Skills
- Willingness and desire to continuously learn
- Passionate about innovation and new ways of doing things
6
Value Stream Manager Resume Examples & Samples
- Plan for Every Part (PFEP) and Every Part, Every Interval (EPEI) implementation
- Build plan strategy for all products and planning to the Pacemaker by cell
- Design and creation of a Delivery Assurance Center in NBAS
- Integrated planning and material releases in alignment with the newly implemented Tugger route delivery system
- Inventory management, control and strategy
- Integration of Value Stream alignment
- Integration of procurement alignment in support of shop demand
- Demand and Supply Planning process alignment with Core Materials processes
7
Value Stream Manager Resume Examples & Samples
- Supervise the activities of a manufacturing team within assigned area(s)
- Achieve required safety, quality, delivery and performance levels
- Develop, coordinate, lead and execute daily production plans
- Foster a culture of continuous improvement utilizing the ACE tools
- Own customer satisfaction with everything under your direction
- Act as a single point of contact to manage competing priorities and resource demands to maximize customer satisfaction and cell performance
- Interface with internal and external organizations to prepare for, and successfully launch, modification programs or new program introductions within your assigned area
- Assist with shop processes as required (test, troubleshoot, etc.)
- Perform miscellaneous assignments as required / requested
8
Value Stream Manager Resume Examples & Samples
- Provide leadership and engage employees in the business through use of the ACE Operating System. This includes leading selected ACE elements that will guide / lead the Fasteners and Seals Team to ACE Gold
- Develop a delivery assurance plan aligned with 6 Pack, xRM, Supplier Delivery & Quality Clinics and Delivery Gated Review Process, which ensures the long term business delivery performance objectives are achieved
- Responsible for Supplier Relationship Management
- Develop and execute staffing plans to support the long term sourcing strategy
- Ensure Export Control Compliance
9
Value Stream Manager Resume Examples & Samples
- Provide leadership to assembly operations on production planning, staffing, and managing day-to-day manufacturing operations within the plant budget to ensure that current commitments and goals are achieved while improvements are being made
- Directly supervise, develop and set objectives for salaried employees within the group
- Develop and lead a team to achieve safety, operations and quality goals through training, coaching, performance management and effective communication
- Drives a continuous improvement culture by involving employees in problem solving and decision making as well as recognizing them for exceptional work
- Works as a change agent and drives out waste in the manufacturing operation through the deployment of Lean methodology
- Develops operational and financial plan and forecasts for the value stream and achieve financial objectives by preparing an annual budget, scheduling expenditures, analyzing variances, and initiating corrective actions
- Set goals, establish priorities, manage resources, and review project progress and results
- Champion employee engagement planning and activities to drive employee engagement across the facility
- Develop team members to address individual development goals, as well as succession planning needs for the business
- Participate on the EHS Management team to develop, implement or support plant and departmental objectives for safety, ergonomics, and environmental
- Lead assembly efforts for assistance in achieving quality goals such as FPY, escapes, leak reduction, COPQ and scrap reduction
- Lead periodic communication meetings with associates to promote alignment with departmental strategy and objectives
- Develop strategies to lead departments to ACE Gold
- Lead and facilitate department in meeting ISO requirements
- Assist assembly technicians in maximizing potential and contribution to plant objectives through effective coaching, mentoring, counseling and accountability
- Propose and implement changes to existing processes to streamline and improve overall performance while maintaining cost controls and creating cost effective use of resources
- Work with engineering, maintenance and materials groups to ensure production goals are met within budget and assembly lines issue are mitigated efficiently
- Ensure Corporate and plant programs are effectively maintained, the plant is in compliance with standards, and the appropriate training is effectively provided to all employees
- Partner with Human Resources and participate in teams, committees, events and training that improve the organization
- Participate in any other duties and responsibilities as may be assigned from time to time to grow and support the company’s success
- Model and promote adherence to environmental, health and safety policies and initiatives
- Monitor work order progress and drive quality and timeliness of completion
- Create and maintain departmental reports, timecards and overtime records for staff as required
10
Value Stream Manager Resume Examples & Samples
- Lead the day-to-day management of people and process using Agile Scrum approach; communicate and manage performance of the process and people through daily, weekly and monthly metrics; ensure compliance of process
- Lead teams of 10-15 individual contributors to deliver flawless media campaign implementation and management within specified deadlines
- Assess talent, recruit and hire new team members that both enhance the team overall as well as match the needs of Sales and clients. Make sure the team is properly trained on job responsibilities, process and Performance Excellence methodologies
- Ensure teams deliver superior customer service by providing coaching and development, identifying training needs and monitoring to ensure adherence to process and best practices
- Communicate job expectations to team to help ensure complete, timely and accurate media campaign execution
- Perform impactful bi-annual performance evaluations and conduct quarterly performance updates; leverage available data insights as part of overall performance evaluation
- Using daily management metrics and control charts, conduct fact-based analysis of current state. Analyze and derive insights on value stream metrics; take appropriate action as needed. Continuously improve the metrics captured
- Ensure team adheres to quality measures. When quality gaps are identified, collaborate with peers to propose risk mitigation plans to Value Stream Leader and Media Management leadership. Drive research and resolution of any issues, utilize Performance Excellence methodologies/tools to identify root cause; follow all SLAs on issue escalation and resolution
- Act as project manager in the development, execution and implementation of departmental and organizational strategies, process improvements, goals and projects. Track feedback received, collaborate with peers to develop and propose action plans; implement approved plans
- Be a change agent - lead and mobilize people inside and outside the value stream, including sales team and clients
- Collaborate with peers to develop recommendations for integration of key business initiatives into scalable and efficient media execution models, identify outliers, develop recommendations and drive efficiencies
- Build and maintain relationships across organizational boundaries. Ensure consistent communication between Media Planning and all internal and external clients
- Assist team in communicating and collaborating cross-departmentally in regards to troubleshooting issues, program budgets and other requests specific to campaign execution
- Ensure complete understanding of future state goals; propose ideas for plans to achieve future state to Value Stream Leader and Media Management leadership; drive implementation of plans to achieve future state
- Implement and champion system, product, process and organizational changes and drive these changes down to teams, providing coaching throughout the process
- Collaborate with and provide mentorship to other team members in the area of media planning
- Manage across departmental boundaries to ensure business needs are met in a collaborative and successful manner
- Minimum of five (5) years of marketing, marketing research, media planning and/or agency account management experience
- Prior management and/or team lead experience is highly preferred
- Lean Six Sigma Belt Certification, preferred but not required
- Good judgment skills
- Hard-working and dedicated
- Holistic value stream management, improvement and understanding of process and culture
- Knowledgeable of Lean methodologies and tools
- Strong leadership and individual/team development capabilities
- Commitment to the future state vision; not easily discouraged by challenges
- Able to influence change by
11
Value Stream Manager Resume Examples & Samples
- BS/BA in Engineering, Business or other relevant discipline
- 5 years experience in Supply Chain Operations
- 2 years direct management experience
- Leadership and integrity; manages by fact, achieves results, builds teams
- Bias for action, assertive, decisive
- Commitment to achieve key performance metrics and drive for continuous improvement
- Vision and purpose; creates and communicates compelling vision and direction, inspires, motivates
- Customer focus, meets expectations, internally and externally, forms partnerships
- Analytical problem solving ability, process oriented
- High level communication skills, written and verbal
- Proficient computer skills, e-mail, word processing, spreadsheet, presentation graphics
12
Value Stream Manager Resume Examples & Samples
- Assures all manufacturing processes and operations result in 100% quality, 100% schedule adherence, while meeting and continuously improving cost standards
- Continuously implement and improve application of Lean principles
- Establish the highest levels of job performance, ethical behavior, and positive work environment and work disciplines for yourself and direct reports in accordance with company policies, procedures and guidelines
- Maintain inventory control and accuracy, 5S standards and general appearance, cleanliness and organization in area(s) of responsibility
- Implements and monitors metrics (including forward-looking) that guide the operation to success. Establish the means and methods of tracking performance and operational status in the area, and report this status to upper Management and direct reports as appropriate
- Ensure all environmental, health and safety standards are maintained
- Maintain the highest ethical standards, even when challenged from above
- Responsible for first-line direction of nonexempt employees involved in production, assembly, and/or fabrication operations
- Reviews production schedules, material and manpower resources
- Assigns employees to maximize production objectives, maintain quality and attain output requirements
- Informs assigned employees of production and material problems and coordinates with support groups to resolve problems affecting schedules
- Participates in establishing and modifying operational methods and processes by recommending changes in materials, equipment and procedures
- Responsible for the hiring, training, employee motivation, counseling, and discipline of employees supervised
- Responsible for the upkeep and maintenance of production equipment
- Must possess excellent communication skills and have the ability to use those skills with direct reports, peers, cross-functional team members, customers, and upper management
- General knowledge of all manufacturing processes and specific knowledge in area of responsibility
- Knowledge of and the ability to implement Lean principles
- Self-sufficient in all areas of responsibility
- Ability to follow verbal and written instructions
- Work well with others as an equal team member
- Safety conscious behavior
- Ability to set and implement strategic vision for department, tying to corporate objectives
- BA or BS degree, technical or engineering discipline preferred
- This role requires a minimum of five years of experience in manufacturing and at least 2 years of production team supervisory/management experience
13
Value Stream Manager Resume Examples & Samples
- Assign capacity and resource to fulfill the execution plan in line with that in SIOP
- Overall capacity planning, allocation of reserve capacity, identification of planned shutdowns and allocation of down-time for maintenance (value stream capacity)
- Execute the plan flawlessly – problem-solve and direct resources and activity
- Develop local production plan along with Planning and Purchasing
- Application of the Cobham SOF (Standard Operation Framework) such that all levels of opportunities for continuous improvement and waste elimination are identified and acted upon
- Ensure the deployment of Standard Work to all levels under their control, regularly checking compliance and taking corrective actions where necessary
- Ensure capacity and capability are continually planned in order to meet agreed customer requirements and work and information flow are documented and regularly reviewed to ensure smooth and rapid execution of Customer requirements
- Responsible for the communication of daily performance using visual management and maintaining the value stream board containing KPIs/scorecard, Root Cause problem identification and accountability/corrective actions and other pertinent information. Ensure that local KPIs are linked to higher level company objectives
- Identification of opportunities for cross training and capacity training in order to enhance capacity and responsiveness to know customer requirements
- Compliance with implemented QMS in line with BSI/CAA regulations
- Completed Bachelor’s Degree in an Engineering discipline is strongly preferred
- Experience in Aerospace operations and/or business management
- Experience with ISO9001 or AS9100 is preferred
- Ability to link financial outcomes with operational actions and business strategy
- Ability to think strategically and understand complex business/financial data, and develop operational plans and organizational structures to meet SIOP commitments
- Excellent organizational, communication, and leadership skills
- Demonstrated ability to lead and facilitate progressive change
- The ability to build, & lead but also to operate as part of high performing teams
- Possess relevant manufacturing and technical experience sufficient to support product groups within the Value Stream
- The ability to work within the wider context of a large organization in a matrix management structure
- Decision Making/Problem Solving – able to make decisions in complex/ambiguous situations and with incomplete data
- Ability to build excellent customer and internal relationships; strong communication skills
- Ability to provide role modeling to organization in line with Cobham core values and behaviors
- Demonstrated ability to performance manage both Operations & Quality KPIs
14
Value Stream Manager Resume Examples & Samples
- Develops and implements integrated departmental plans to ensure business, technical and customer requirements are achieved. Reviews plan execution, makes appropriate adjustments, and resolves issues
- Coaches, counsels, mentors and provides developmental opportunities and job assignments to enhance employee performance and expand capabilities of first-level supervisors and others within their department. Provides on-going developmental feedback. Promotes employee recognition and builds a departmental culture that improves employee satisfaction and retains a skilled and motivated workforce
- Establishes partnerships and relationships with internal and external customers, stakeholders, peers and direct reports. Builds strategic cross-functional and cross-organizational partnerships to resolve problems, improve processes or achieve goals
- Forecasts, obtains and manages personnel, facilities, services, equipment and tools to meet project and departmental requirements. Acquires, deploys and schedules personnel to meet departmental objectives
- Develops plans to ensure appropriate utilization of employee skills within an organization or functional area. Reviews, approves and implements facility, equipment and service plans to maximize productivity and ensure safety, security, environmental and regulatory compliance. Coordinates with providers to achieve timely delivery of resources
- Provides input on the development of departmental business and technical strategies, goals, objectives and related metrics to ensure alignment with Company vision/strategy. Measures performance to plan for multiple projects
- Conducts confirmations to ensure standard work processes are being followed. Identifies and addresses non-compliance and lowered productivity, looking for continuous improvement opportunities
- Communicates with others across the organization to gain information and support, escalate issues, receive feedback and suggestions and provide updates and information. Acts as liaison between downstream team and other departments
- Ensures that Safety, Health and Environmental compliance is included as part of everyday activities
- Bachelors in Operations Management or Business Administration
- 10+ years’ experience in a production/operations environment
- Aerospace and defense industry experience strongly preferred
- Ability to think strategically and develop operational plans
- Working knowledge of business finance and ability to link financial outcomes with operations actions and strategy
- Working knowledge of Lean and Continuous Improvement
- Proven ability to lead operational transformations
- Ability to Work across functions in a matrix organization
- Effective Presentation Skills – ability to present to large groups at all levels of the organization
- Strong planning and organizational skills with the ability to be flexible and adaptable to changing priorities and assignments
- Good working knowledge of PC applications including ERP/MRP and Microsoft Suite
15
Value Stream Manager Resume Examples & Samples
- Completed Bachelor’s Degree in an Engineering, Technical, or Business field
- Experience leading an operations organization and improving processes using Lean Six Sigma principles & methods
- Demonstrated ability to performance manage both Operations and Quality KPIs
16
Value Stream Manager Resume Examples & Samples
- Promotes the Plant Safety Process by leading the process and maintaining a high level awareness and operating discipline for all plant safety policies
- Guides and advises supervisors in interpretation of Plant and Company policies and Union contract. Helps resolve non-routine personnel problems. Assists Supervisors with first step of grievance
- Drives quality performance of the Value Stream operations through use of systems management and Lean principles, including layered auditing
- Drives customer awareness throughout the value stream and focus on delivering material that meets customer and regulatory requirements. (0)
- Routinely visits production operations to interact with employees, facilitate/assist in root cause determination for safety, quality, and productivity issues, monitor performance and schedule adherence, monitor product quality characteristics, and gather information and input from Supervisors, support staff, and operators to make decisions when. Coaches Supervisors and Team Manager(s) in these areas
- Assists in determining manpower requirements to meet production schedules
- Works to promote good employee relations by interacting with employees frequently and discussing and helping with problems or complaints. Encourages supervisors to establish and maintain similar relationships
- Promotes achievement of the plant’s goals and works closely with Value Stream Improvement Champion to drive focus, ownership, and engagement from Value Stream Steering Team, maintenance, and production employees. Participates in, sponsors, and supports the Lean process
- Promotes effective training of employees and works closely with Value Stream Specialist to drive continuous improvement of the content and execution of the training & certification process; Promotes continuous skill and process knowledge improvement; and drives effective crew skill management by Supervisors/Team Manager(s)
- Facilitates and promotes participative management and employee involvement through the Gemba process, employee meetings for communication and problem-solving, training, recognition, information sharing and interpretation, and delegation of authority and responsibility
- Promotes excellence in housekeeping; promotes processes, systems, and Lean events/tools to reduce effort and cost to maintain housekeeping
- Promotes regular communication between maintenance and production. Facilitates the on-going integration of maintenance and production activities
- Continually provides assessment and feedback of supervisor and support staff resource performance and behaviors
- Must demonstrate the ability to lead a large organization spread over a complex production operation
- Minimum of 3 years of demonstrated supervisory and/or operations management experience in an industrial production environment
- Demonstration of presentation, facilitation and meeting management skills
- Demonstration of basic project management skills
- Demonstration of process improvement skills. Ideally, candidate would have proven Lean and 6-sigma skills and be able to effectively apply methods and tools
- Basic understanding of maintenance systems including, PM, Pd/M technologies including and planning of work
- Demonstrate ability to use data from multiple sources to quickly solve complex operational problems
- Computer proficiency in, Excel, Word, and Power Point with basic skills in SAP and Minitab
- Effective writing and data organization skills
- 4 year Technical or Business Degree preferred
17
Senior Value Stream Manager Resume Examples & Samples
- Leading section operations to consistently meet or exceed business objectives and targets
- Developing and executing strategy for the section to increase sales, productivity, quality, customer satisfaction, and effectively introduce new products for growth
- Accountable for all Safety and Environmental concerns in areas of responsibility
- Championing use of Six Sigma/Lean tools in driving plant improvement to develop and implement strategic initiatives relative to inventory, capacity utilization, and growth opportunities
- Maintaining cost effectiveness through aggressive productivity and asset management
- Improving and developing organization capabilities through effective performance management and planning/utilization of human and capital resources
- Driving cultural change, accountability and continuous improvement mindset throughout the organization
- Developing and maintaining effective area leadership teams
- Developing relationships to improve performance with key customers
- Developing and maintaining successful relationship with site union leadership
- Championing programs to address employee satisfaction, employee training, communications, yield improvement, technology transfer, process improvement and departmental structure to support operating and strategic goals
- B.S. degree in Engineering, Chemistry, Business or a Technical Discipline
- Minimum 6 years chemical manufacturing experience in industries such as, Chemical, Pulp & Paper, Petro-Chemical, or Pharmaceutical, in direct support of chemical manufacturing facilities
- Minimum 6 years of experience with process improvement in areas of process safety, environmental systems, yield, energy and capacity
- Experience managing in a union facility
- BS in Chemical Engineering or Masters degree preferred
- 10 years of experience with process improvement in areas of process safety, environmental systems, yield, energy and capacity preferred
- 5 years of managerial experience preferred
- Ability to perform each essential duty satisfactorily
- Demonstrated ability to use influencing skills to accomplish goals and objectives
18
Senior Value Stream Manager Resume Examples & Samples
- Implement a comprehensive Value Stream Strategy including lean manufacturing processes based on the most progressive and advanced manufacturing techniques to include the Honeywell Operating System (HOS) and Lean/Kanban principles
- Manage directly or indirectly a group of approximately 100 employees
- Provide the necessary leadership to promote change throughout the organization and continue to develop and lead a world class manufacturing organization
- Work across all functions in a matrix environment to drive the deployment of the Honeywell Operating system to create a World Class Safety culture, strong Delivery improvements, On Time to Customer Request, TAT and inventory reductions, improved quality and year over year cost productivity
- Ability to develop, execute and achieve tactical and strategic initiatives through active leadership that positively impacts business plans, conversion cost, practices, policies and procedures
- Understanding of lean, integrated supply chain principles, and aerospace quality requirements
- Ability to effectively select, develop, coach, empower and motivate a staff to ensure growth in their scope of responsibility and accountability for operational excellence
- Ability to communicate clearly with an understanding of the audience and to present ideas and gain commitments that are crucial to the success of the business
- Widely trusted, direct, truthful and credible by showing consistency between words and actions
- Demonstrated ability to think innovatively and creatively to resolve problems
- Ability to develop multi-talented/functional teams
- Sound coaching, influencing, negotiating and mentoring skills
19
Value Stream Manager Resume Examples & Samples
- Proactively implements, promotes and maintains a safe working environment, through diligence in accident prevention, near miss reporting, 8D investigations, equipment maintenance, and safety principles enforcement
- Meets or exceeds product quality requirements using plant quality tools, including LPA, QAR, first piece approval, and audit processes. Deploys and reinforces quality expectations with Frontline Leaders and production associates, with a focus on accountability
- Selects, develops, and motivates product line personnel and resources to achieve established goals for productivity, quality/scrap, cost, engagement, and profit
- Monitors product line Staffing for best utilization of both direct and indirect labor
- Establishes product line priorities as they apply to current product, standards and processes
- Assists with capital project planning under the direction of the Operations Manager,
- Coordinates manufacture of product to meet customer requirements, including scheduling of product, or collaborating with Production Control for efficient scheduling of product throughout the facility
- Monitors and improves general plant activities such as safety, 5S, lean initiatives, and communication/information systems
- Works with Production Control to establish appropriate inventory levels, and adherence to the established inventory goals
- SIOP process co-owner in conjunction with Production Control, through the forecasting of production output for areas of responsibility
- Assists the Plant Manager in setting, communicating, and achieving department goals and objectives. Develops and maintains performance metrics as required to drive results, and analyze results as a tool for identifying and initiating process improvements
- Fully engages workforce and promotes personal accountability by identifying goals, empowering employees to drive decision making, fostering innovation and continuous learning, by providing ongoing feedback
- Drives continuous improvement programs and manufacturing process improvements by applying appropriate Eaton Business System processes and problem solving tools such as Eaton Lean System, Six Sigma, and 5S
- Drives the company's vision and mission by reinforcing ethics, values and quality policies throughout areas of responsibility
- Bachelor’s degree in business, quality, or engineering
- Minimum of 5 years prior work in manufacturing environment
- Minimum of 2 years prior management/supervisory experience
- Demonstrated ability to effectively communicate positive and constructive feedback to employees or co-workers
- Advanced knowledge of production planning, product flow, inventory control, and the product and its application
- Knowledge in Statistical Process Control and TS 16949
- Knowledge of supervisory techniques and proactive counseling methods
- Skills in teaching, training, motivation, and development of employees
- Demonstrated ability to lead and motivate employees
- Administrative skills to include planning, coordinating, team building, communication, organization, and time management
- Ability to direct the training, motivation and development of personnel in the product line group
- Proficiency in Microsoft Excel, Word, and PowerPoint
20
Value Stream Manager Resume Examples & Samples
- Actively connecting with the sub portfolio owners of the GEOS PPM ( Project Portfolio Management ) process - ensuring full comprehension of the location specific projects and relative value/priority in the portfolio
- Accountable for the front end loading phase of selected Customer Focused Innovation ( CFI ) and High Performance Innovation ( HPI ) projects (Project Delivery Process 1-a) - applying PPM/PDP principles - in cross-functional setting. In this temporary setting PDP projects 1-3 will be assessed by the overall (New Product & Service Solution - NPSS) Project Supervisor
- Accountable for leading the plant supervisory team in actually implementing sustainable change in the execution and start-up phase (PDP 4-5) - leading to noticeable and measurable bottom-line impact of
- 1) Significantly improve the ability and speed to capture value from CFI and HPI projects and initiatives at the fat refineries - by applying a structured project approach - fully in line with PPM/PDP principles demonstrate and report a noticeable and measurable bottom-line impact of > 100k USD per location per year (in contribution margin increase and/or cost reduction)
- 2) Advice on plant operations capability in fulfilling new product / service request - on local as well as central level ( eg. advise Commercial / Tech Service team on time line for completion new product /service
- 3) Need to work with a wide range of stakeholders
21
Value Stream Manager Resume Examples & Samples
- Champion a Safety Culture through using MESH tools, safety best practices, and empowering all employees to take
- Responsibility for their own safety as well as the safety of everyone they work with. Ensures that environmental health and safety issues are addressed considering local regulations, Eaton policy, and good corporate citizenship
- Responsible for daily operational performance indicators. Takes appropriate actions to ensure safety, quality, schedule, cost, and productivity goals are met. Manage the “Tier review” process to track and understand key operational metrics (leading and lagging) and develop strategies and action plans to improve operational performance
- Responsible for creating and executing the profit plan for assigned value stream, including labor and resource planning, managing material and support costs, and future forecast to deliver upon financial commitments
- Ensures required documentation and/or system transactions are executed to meet customer, manufacturing systems, and financial reporting requirements
- Minimum of 5 years of experience in Operations/Manufacturing
- Minimum of 3 years of leadership experience in a manager of people role
- This position requires use of information or access to hardware which is subject to the International Traffic in Arms Regulations (ITAR). All applicants must be U.S. persons within the meaning of ITAR. ITAR defines a U.S. person as aU.S. Citizen, U.S. Permanent Resident (i.e. 'Green Card Holder'), Political Asylee, or Refugee
- No relocation is being offered, all candidates must reside within 50 miles of Beltsville, MD
- MBA from an accredited institution
- Understanding of industrial safety and environmental regulations and practices
- Thorough understanding of production planning, scheduling, purchasing, and inventory control
- Knowledge of financial concepts and techniques utilized to establish value propositions for operational changes
- Strong leadership, process focus, and interpersonal skills
- Comfortable managing high levels of pressure while delivering results
22
Value Stream Manager Resume Examples & Samples
- To improve and sustain a healthy and safe work environment
- To deliver the desired quantity of instruments each day
- To improve the quality of the instruments in close collaboration with R&D
- To reduce stock levels by optimizing flow and the supplier setup
- To improve productivity by means of standard work and enhanced quality
- To increase the production capacity in order to support the high growth
- To set clear goals for today — and going forward
- To motivate and develop your team
23
Value Stream Manager Resume Examples & Samples
- Delight our customers through business unit leadership, department engagement, empowerment and execution of customer programs/initiatives
- Communicate order status internally and externally
- Maintain cross-functional relationships with internal departments including sales, marketing, supply chain, manufacturing operations and distribution channels
- Identifies and communicates critical issues, gaps and constraints to leadership and stakeholders
- Develops run strategies that decrease cycle times and increase average throughput
- Facilitates communication and action to resolve supply constraints and/or bottlenecks
- Periodic travel required: up to 15%
- Bachelor’s degree from accredited college or university in applicable field
- 2-3 years of experience in a supply chain planning, manufacturing, customer service role, or equivalent combination of education and experience
- Thorough understanding of continues improvement (Lean/six-sigma)
- Process-orientated and self-motivated with a passion for continuous improvement and customer service
- Proven organizational skills and multi-tasking abilities
- Confidence and poise to negotiate and manage a relationship with Director and Vice President level internal and external customers
- Proficient in use of Microsoft Office tools (Word, Excel, etc.) and other similar software
- Proficient in the navigation through and interpretation of data in the ERP system
24
Value Stream Manager Resume Examples & Samples
- Provide leadership and direction to supervisors, process engineers and associates within the manufacturing operations (exempt and non-exempt) and drive a root cause / corrective action culture
- Mentor direct reports to improve their skills and overall effectiveness
- Maintain positive employee relations through the use of proficient and open communication skills. Listens, supports, engages and encourages employee suggestions and input to achieve excellent results
- Drive accountability throughout the operation
- Develop, review, and present various work/management reports to accurately measure production processes and make recommendations for better business results
- Drive cost reduction initiatives and yield improvement
- Lead and/or support the LEAN initiatives including but not limited to Level I, II, and III Daily management, GEMBA walks, 5 “S”, Leader Standard Work, and KPI metrics
- Drive Practical Process Improvement Business Systems into operations
- Support implementation of lean tools throughout manufacturing
- Drive continuous improvement teams and actions to improve process and product flow
- Develop capacity plans
- Manage key operations metrics
- Manage and take action on customer feedback
- Manage projects and teams within set budgets
- Support, lead and participate with Quality, R&D and Engineering on new product introductions; lead pilot and production trial runs
- Demonstrates Thermo Fisher Scientific values - Integrity, Intensity, Innovation and Involvement
- Demonstrates Role Model Leader characteristics
- Other miscellaneous activities as assigned
- BA, or BS degree in Engineering, Manufacturing Technology, Manufacturing Operations or related field. Advanced degree preferred
- 5+ years of related work experience in manufacturing highly preferred, ideally in manufacturing processes involving cutting, cleaning and coating glass substrates
- 3+ years experience managing within a production environment
- Quality Systems Regulations/ISO experience required
- Continuous Improvement experience is preferred such as PPI
- Proven track record in leading and implementing lean tools such as; 5-S, Kanban, Standard Work, etc. to drive improvement
- Excellent communication and attention to detail
- Ability to work independently and as part of a team, self-motivation, adaptability and a positive attitude
- Must demonstrate strong organizational and leadership skills and be able to handle multiple assignments simultaneously
- ERP software experience, JD Edwards a plus
- BA, or BS degree in engineering, or related field
- Quality Systems Regulations/ISO experience
- 5+ years of related work experience in manufacturing
- Proficient in MS applications (Excel, Word, Outlook)
25
Value Stream Manager Resume Examples & Samples
- Bachelor degree in business, engineering or related field
- 5-7 years manufacturing experience
- 1-3 years experience in leadership role with a preference in manufacturing
- Demonstrated understanding of Lean Manufacturing concepts
- Experienced at operating computers with familiarity with Windows Word and Excel, SAP and Internet
- Effectively staffs the team
- Quickly and effectively resolves conflict
- Acts with integrity at all times
26
Value Stream Manager Resume Examples & Samples
- Provide leadership and work direction for the process team to ensure that resources needed are adequate to meet key requirements related to safety, service levels, cost, and productivity
- Participate in and / or lead cross-functional projects and kaizen events involving the expansion / continuous improvement of Cooling concepts
- Provide a working environment and leadership that demands and ensures
- Data-driven decisions and actions
- Stable, consistent documented processes
- Utilization of lean tools to provide continuous improvement of all key cost and service metrics
- Teamwork, both within Cooling and between Cooling and related Business Units
- High team morale
- Communication between manufacturing area and support groups
- Be a change agent and drive out waste throughout the manufacturing operation using Lean methodologies
- Drive a continuous improvement culture by involving employees in problem solving and decision making
- Assist with the development of current and future state value stream maps and continuous improvement plans, as well as the implementation of those plans
- Lead the day-to-day production activities within the value stream(s) to ensure current commitments are achieved while making improvements
- Plan and schedule the work of the organization to make effective utilization of employees, equipment and material within budgetary requirements, and cost and quality standards to meet customer’s expectations for quality and delivery
- Responsible for assuring strategic plans are in place for talent acquisition, employee development and performance management
- Develop open lines of communication to continually monitor employee attitudes and concerns, and implement appropriate actions with input from Human Resources
- Track daily performance; verify team leader counter measures and recovery plans are in place for missed targets. Ensure process center communication boards are being used on a daily basis
- Recommend and implement changes regarding production capability, tooling, machine replacement and staffing in support of production plans as well as cost-effective procedures, systems, tooling, equipment, etc., to continually improve manufacturing productivity
- Coordinate and facilitate activities that respond to customer and market needs through contact with Sales/Marketing and district sales offices
- Participate, monitor and maintain departmental budget -- both expense and capital
- Develop a One Pentair culture ensuring Pentair values are being deployed
- Workforce planning: requisitioning, contingent workforce, review FTE count, etc
- Performance Management: conduct employee reviews, promotions, disciplinary action, and all other performance management responsibilities
- Provide coaching and feedback to Supervisor and Leaders in Training to promote career growth and development
- Support new processes , product development and implementation
- Be highly visible to associates and create an environment for participation. Promote hands-on approach to problem solving
- 4 year degree in business-related field
- 5 years experience in manufacturing operations or distribution environment
- 3 years experience in a leadership position
- Prior experience in a Lean environment preferred
- Knowledge of process improvement concepts and methods along with the flexibility and adaptability to accept, support, and deploy new processes in a changing business environment
- Skill to create and implement plans aligned with the business unit’s strategic vision
- Skill in effective communications at both technical and leadership levels. Skills must include good interpersonal skills, as well as written and verbal communication skills, and ability to understand information and ideas as presented
- Skill in developing and delivering effective presentations
- Skill in conflict resolution including the ability to address difference of opinions or facts and use the most appropriate method to reach an effective solution
- Ability to build and maintain effective work relationships, both internal and external, and establish credibility with business partners
- Ability to plan, organize, and prioritize time/workload and delegate work in order to accomplish tasks and meet deadlines
- Ability to effectively coach and foster staff growth and development
- Ability to evaluate and motivate personnel
- Ability to drive results through influence
- Ability to adapt to rapidly changing business circumstances; must be able to thrive in a constantly changing business environment
27
Value Stream Manager Resume Examples & Samples
- Integrates plant safety systems into the boardmill value stream and ensures risks are identified and eliminated. Maintains a high level of awareness and operating discipline for all plant safety policies
- Manages the daily Gemba walk, and follow up, to ensure that standard work and MDI are driving the value stream to meet its goals in Safety, Quality, Delivery, and Cost
- Leads the weekly value stream team meetings to ensure that longer term plans and resources are aligned around the critical work and improvements for the value stream
- Collaborates with Prod VSM to ensure that the manufacturing team managers are executing standard work and MDI in pursuit of their SQDC goals. Maintains consistency in employee relations regardless of value stream
- Directly supervises the Value Stream Specialist in Boardmill and oversees the value stream work of the Sr. Value Stream Process Engineer and the Value Stream Mechanical Engineer for Boardmill related projects and improvements
- Ensures all project work is effectively integrated into the value stream
- Serves as a module facilitator
- Provides for and promotes regular communication between maintenance and production. Facilitates the on-going integration of maintenance and production activities
- Recommends and manages implementation of value stream Kaizen events related to SQDC
- Continually provides for assessment and feedback of team manager and technical resource performance
- Associate’s degree or related years of experience
- Minimum of 3 years of experience working in a manufacturing environment
- Minimum of 3 years of demonstrated leadership experience
- Practical working knowledge of Lean methodology and process improvement methods
- Facilitation skills including presenting to small groups, getting work completed through others and coordinating work of multiple employee populations
- Engineering or Technical degree
- Ability to use computer programs and processes (Excel, Word, SAP, Access, Clarity, etc.)
- Practical working knowledge of process improvement methods
- Five or more years working in a manufacturing environment that utilized process improvement methods
- Prior experience working in a matrixed reporting structure environment
28
Value Stream Manager Resume Examples & Samples
- Direct and manage all Value Stream operations with overall responsibilities for production, manufacturing engineering, material, quality and other production related activities
- Coordinate and lead Value Stream activities through planning with departmental support to insure manufacturing objectives are accomplished in a timely and cost effective manner while fully meeting customer requests
- Implement and manage cost effective systems for control of process improvements, capital and operating expenditures, manpower levels, scheduling and shipping
- Establish and monitor measurements of overall Value Steam performance for safety, quality, delivery and cost
- Effective and efficient use of Lean Manufacturing and associated tools in all areas of the organization
- Develop key employees. Participate in company dialogues regarding employee performance to assure that deserving employees are recognized and that underperforming employees are given the direction required to improve their performance
- Coordinate and lead plant activities through planning with departmental team leads to insure manufacturing objectives are accomplished in a timely and cost effective manner and fully meeting customer requests
- Provide leadership and training on Colfax Business System (CBS) tools to accomplish company goals and objectives. Fully support Manufacturing Excellence / Lean Conversion Roadmap resulting in revolutionizing the shop floor and creating an Operator-Led Process Control environment
- Communicate frequently and effectively to associates throughout the organization. Establish and maintain effective communication vehicles such as toolbox meetings, employee meetings, roundtables discussions, and one-on-one meetings
- Provides leadership and employee development through selection/talent acquisition, performance management, training/development, coaching/mentoring and motivation of management, supervisory and hourly employees in alignment with the business goals and objectives
- Minimum 7 years experience in a key Operations leadership role
- Bachelor’s degree required, Master’s degree a plus
- Ability to understand the business on an in-depth level such that the right structure and the right people have been deployed resulting in a track record of routinely delivering forecasted outcomes
- Demonstrated leadership effectiveness (EI). Must be an effective change leader who challenges the status quo and acts with a sense of urgency to drive results. Effectively balances consistency with flexibility and willing to change ideas in the face of new information
- Strong business acumen and strategic thinking with demonstrated accomplishments. Proven performance setting and exceeding customer service goals and profit targets
- Impeccable integrity; Superior interpersonal skills; able to communicate and engage personnel at all levels of the organization
- High energy
- Innovative thinker
- Disciplined and persistent work style
- Track record of continuous improvement
- Experience effectively functioning in a matrix organization
- Keen attention-to-detail
- Experience in Union environment desirable
29
Senior Value Stream Manager Resume Examples & Samples
- Must be a US Citizen due to contractual requirements
- Bachelor's degree in Engineering, Supply Chain Management or Business Management
- Minimum 10 years experience in manufacturing operations
- Minimum 5 years direct or indirect Leadership experience
- Experience in manufacturing operations, preferably Repair and Overhaul
- Leadership skills to include understanding of Honeywell Operating System
- Ability to work in matrix organization
- Ability to communicate at all levels of the organization
- Ability to identify root cause and develop systemic Resolutio
- SAP/Microsoft Excel desired
30
Value Stream Manager Resume Examples & Samples
- Ability to read, analyze, and interpret general business periodicals, professional journals, technical procedures, or governmental regulations. Ability to write reports, business correspondence, and procedure manuals. Ability to effectively present information and respond to questions from group of managers, clients, customers, and the general public
- Exceptional organizational skills and the ability to manage multiple priorities
- Ability to emulate Tenneco values to all internal and external customers
- Bachelor's degree in Production Management, Business Administration, or Mechanical Engineering (or equivalent management experience)
- Five to Seven years broad manufacturing experience (including experience as a front line supervisor) in a high volume manufacturing environment
- General knowledge and basic understanding of metal forming and welding and assembly
31
Value Stream Manager Resume Examples & Samples
- Provides guidance, direction and leadership to insure that products are manufactured with the highest level of quality in a safe and timely manner that will meet or exceed customer expectations
- Conducts fact-based analysis using Lean techniques to create value and manage to a future state Value Stream that eliminates waste and drives continuous process improvement related to safety, quality, delivery, inventory, and productivity
- Builds strong alliances across all functions and is strategic liaison to Product Management, Sales, Customer Service, Design Engineering, and Finance to meet Customer and Stock Holder commitments
- Maintains a safe work environment, a high level of safety awareness among associates, and implements 5S principles
- Mentors and develops direct reports and entire Value Stream Team. Listens, supports, engages and encourages employee suggestions and input to achieve excellent results
- Establishes goals, sets priorities and coordinates all related activities within the Value Stream to ensure drive and focus towards meeting or exceeding established common business objectives from the Site Goal Tree and Strategic A3
- Monitors, reviews, and improves manufacturing and quality related activities and drives corrective and preventative actions. Focuses team on using standardized work practices
- Oversees and manages Value Stream expenses to meet budgets and financial objectives and proactively seeks opportunities to drive improvement of the operating results
- Maintains proper staffing levels, scheduling and organizing work assignments within the company policies and procedures
- Provides leadership guidance during morning walks
- Leads Value Stream Key Performance Indicators (KPI) review each month. Identifies gaps and implements countermeasures
- Performs all job duties in a safe manner, consistent with the Code of Ethics and the 4-I Values, and follows all ISO standards
- Performs all job duties in a safe manner and obeys all safety policies and procedures
- Performs all job duties consistent with the Code of Ethics and the 4-I Values
- Performs all job duties within ISO standards, regulatory or statutory requirements
- Performs other duties and responsibilities, as needed
- Bachelor’s degree in business management or engineering strongly preferred. An advanced degree such as an MBA is a plus. High school education with equivalent applicable work experience may be substituted.10+ years working experience in a manufacturing environment with leadership experience
- Strong leadership and decision-making ability
- Knowledge, experience or training in Lean techniques and proficient in process auditing
- Possess technical engineering aptitude to understand advanced level of product line knowledge
- Possess a continuous process improvement mindset with the ability to effectively lead and manage change
- Strong project management, communication, and organizational skills
- Possess a solid working knowledge of other business functions such as Logistics, Finance, Sales, Engineering, and Human Resources in addition to Manufacturing and Quality
- Proficient in use of Microsoft Office Suite
- Ability to travel as required,
- Working conditions require the ability to sit, stand, walk, bend, climb stairs, and work at a computer station and on manufacturing shop floor
- Ability to frequently lift up to 20 lbs; occasionally lift 40 lbs
- 10+ years working experience in a manufacturing environment with leadership experience
32
Value Stream Manager Resume Examples & Samples
- Implements strategic programs that improve labor efficiency, on-time delivery, continuous quality improvement, safety work place, and exceed customer requirements
- Generates monthly reports to effectively communicate program contributions, lead-times, on-time delivery, continuous improvement efforts, and manufacturing issues and needs
- Drives a corporate culture that focuses on facts, tangible results and behaviors
- Provides input for selection of appropriate manufacturing equipment to ensure the most cost efficient solution is available within company budget guidelines
- Maintains manufacturing staff by recruiting, selecting, orienting, and training employees; maintaining a safe and secure work environment; developing personal growth opportunities
- Accomplishes staff results by communicating job goals and expectations; planning, monitoring, and appraising job results; coaching, counseling, and disciplining employees; initiating, coordinating, and enforcing systems, policies, and procedures
- Produces products by establishing production planning systems; maintaining good manufacturing practices, enforcing quality standards, improving products and processes
- Interfaces closely with Plant GM and Supply Chain Manager to effectively develop purchasing and logistical systems, inventory and production control requirements
- Achieves financial objectives by establishing objectives; developing budgets; controlling costs, maximizing use of available assets
- Provides leadership needed to ensure the product quality meets product specifications and criteria for all products shipped from the plant
- Ensures efficient utilization of plant personnel and equipment to meet productivity and cost effectiveness in meeting the plants business goals from stated AOP
- Leads a trained and motivated workforce capable of implementing and executing the business strategy
- Works with all functional departments to actively pursue manufacturing excellence programs along with fostering a “one Plant” partnership with peers to achieve aligned goals
- Develops and implements with Plant GM an annual operating plan including capital plan, cost down projects, production department budget, eliminating non-value, and defining Six Sigma & Kaizen profit improvement programs across the plant
- Behaves continuously and consistently with desired Masonite Mprove values, and characteristics
- Communicates and facilitates meetings effectively
- Identifies and resolves issues skillfully and in a timely manner
- Keeps abreast of emerging technology and industry practice
- Demonstrated ability to lead cross-functional teams
- Must be self-motivated with the ability to work independently and in a team environment
- Excellent organizational skills, leadership qualities, computer literacy
- Ability to supervise is essential for the candidate to perform successfully in this position
- Competent in the use of Microsoft Word, Excel, PowerPoint, Access & MS Project
- Works with integrity and respect displaying a high degree of tact and diplomacy
- Must be familiar with various measuring devices and analyzing information
- Good understanding of HR and Financial acumen is highly desired
- Bachelor’s Degree preferably in Mechanical Engineering or Operations
- Minimum of 5-7 years’ experience of related experience in Manufacturing Management preferred
- Experience, knowledge or trained in Six Sigma Lean Methodologies manufacturing
- Six Sigma Lean GB certification highly desired or ability to obtain within 12 months
33
Value Stream Manager Resume Examples & Samples
- Drive performance improvement: Improve Safety. Review SIOP, drive material for on-time delivery. Plan for production capacity and scheduling to ensure OTTR targets are met. Drive product quality improvements including RTY and Customer OBF DPPM. Reduce production cost and inventory
- Drive continuous improvement: Engage all employees in improvement activities; develop and drive a continuous improvement culture. Drive improvement to meet all key performance metrics such as RTY, Productivity, Scrap, OTTR, DPPM, Inventory, TCIR, etc
- Team development: Drive increased employee satisfaction and employee development activities and results. Provide coaching, training, and guidance for IDL and professional employees development
- Financial Responsibility: Position has indirect accountability for budget management. (Accountability is High $5-10 million)
- Managerial Scope: Position receives a moderate level of management direction. Position is directly accountable for results and influences cross-functional departments. The position is indirectly accountable for managing a staff of approximately 75 people or more. (Hire/discharge decisions, initiate/recommend salary action, work performance of the team, train, conduct performance appraisals, coach for career development.)
34
Voice EMS Value Stream Manager Resume Examples & Samples
- Primary responsibility for the overall performance of the EMS supply chain including delivery, quality, inventory and cost
- Develop, implement and drive the Supply SIOP processes with the EMS supplier
- Collaborate with the Logistics function to design and implement a high performing logistics network including trade compliance and DC operations as appropriate
- Collaborate with HON Sourcing and Commodity leaders to ensure supply base supports EMS supplier as if it were supporting directly to Honeywell
- Coordinate with WFSS Engineering to prepare for and execute ISC ramp up of NPI programs
- Collaborate with leaders to drive forecast accuracy improvements
- Develop and manage the EMS management operating system to ensure the supplier acts and operates according to our customer’s needs
- Lead the tier accountability process with the EMS supplier. Ensure escalations are managed quickly and effectively to eliminate customer impacts
- Drive process standardization through appropriate deployment of Honeywell Operating System tools and systems
- Collaborate with WFSS Engineering team to drive productivity and quality improvements to improve customer experience
- Regularly execute Gemba in the EMS supplier production area to identify and resolve risks and issues
- BS Degree in Manufacturing, Industrial or Operations Engineering, Supply Chain Management or similar
- 5 Years Operations or Supply Chain experience
- Six Sigma & Lean Manufacturing Knowledge and Experience
- Materials Management Experience
- Proficient in use of Microsoft Word, PowerPoint, Excel including build-out of spreadsheets, charts, tables
- Solid multi-tasking, organization, and communication skills
35
Value Stream Manager Resume Examples & Samples
- Supports the following people initiatives for the facility: Eaton Values and Philosophy, Ethics, Diversity, APEX, OCA, and E-Star
- Actively participates in the following environmental health and safety initiatives: MESH, ISO14001, and the safety / environmental programs established for the facility for a safe work environment. Follow all environmental health and safety procedures and practices to assure a safe work environment. Identify and report unsafe conditions or practices to your manager, EHS Manager, safety coordinator, or any member of the safety team
- Participates in the following quality initiatives / programs: Eaton Quality System (EQS), ISO-9001, and etc
- Fulfills the requirements of the Quality Policy and Quality Management System
- Collaborates in the development and execution of facility profit plan objectives and balanced scorecards
- Responsible for holding dotted line reports accountable through tier 2 meetings and daily accountability tracking
- Develops and controls work team budgets
- Supports continuous improvement of area processes
- Participates in the planning of Work Area SIOP, then monitors and controls plans
- Maintains and develops the staffing/personnel strategy for the department
- Proactively implement, promote and maintain a safe working environment, through diligence in accident prevention, investigation, equipment maintenance and rule enforcement
- Act as a business partner by planning, initiating, leading, measuring, monitoring and assessing continuous improvement programs and manufacturing process improvements by applying appropriate Eaton Business System (EBS) processes and problem solving tools such as ELS (Eaton Lean System) and 5S
- Engage workforce and promote personal accountability by identifying goals, empowering employees to drive decision making, foster innovation and continuously learn and by providing ongoing feedback on employee performance with formal evaluation provided at least annually
- Actively participate in setting, communicating and achieving department goals and objectives and develops and maintains performance metrics as required to monitor results and uses those results as a tool to identify and initiate process improvements within own work area
- Coordinate and/or participate in continuous improvement teams in own or other areas to enhance plant results
- Minimum of 3 years in a Manufacturing and/or Operations environment
- Minimum of 1 year of Supervisory Experience in a Manufacturing or Operations environment
- Candidates must be legally authorized to work in the United States without company sponsorship
- B.S./M.S Degree in Business, Manufacturing, or Engineering preferred
- 5 years of previous leadership/supervisory experience
- Certification in Lean Manufacturing
- Previous experience working in a Precision Machining environment
- Ability to motivate and build effective and productive teams
- Working knowledge of quality control techniques, 5S, Six Sigma, and Quality systems (e.g. QS 9000, ISO 14001, ISO-9001, AS9100) preferred
- Strong written and verbal communication skills, strong leadership and teaming skills, solid analytical and reasoning skills
- Previous manufacturing engineering experience is preferred
36
Value Stream Manager Resume Examples & Samples
- Development and implementation of effective production planning, policies, and procedures to support and compliment company-wide strategic objectives
- Work closely with operations, engineering and quality to maintain departmental operational excellence
- Provide visibility of production schedule to VP/GM
- Maintain financial reporting and work with VP/GM to prepare program budgets
- Evaluation and preparation of KPI's for the department
- Support lean initiatives and continuous/operational improvement plans
- Provide leadership, mentoring and to production and support staff through goal setting, delegation and effective communication
37
Electronics Value Stream Manager Resume Examples & Samples
- Drives customer focus through prompt issue and complaint resolution, corrective action and effective interaction with the business team, operations team, sales, and customers
- Leads sustainable supply chain performance through capacity management, cycle optimization, delivery performance, supplier management and appropriate inventory management
- Implements sustainable improvements in factory cost through the application of LSS, entitlement thinking, yield improvements and productivity improvements
- Determines and leads systemic changes in quality performance, through appropriate application of LSS and quality system improvements
- Supports operations team in EHS compliance and accountability through active and visible leadership and effective coaching to ensure employee engagement and success
- Ensures compliance to all applicable standards (ISO, OSHA, RC, etc.)
- Pro-active involvement with division personnel and business team to support long term strategic objectives
- Provides strong plant leadership through being an effective member of the plant leadership team (staff) and engagement of technical team and all support departments
- Ensures strong alignment with department goals, plant and division metrics, and 3M vision and strategies
- Lives 3M values through all interaction with the plant population and local community
- Minimum 5 years of experience in manufacturing environment
- Minimum 3 years of leadership / supervisory experience
- Degree in technical or engineering discipline
- Certified Lean Six Sigma Black Belt
- Experience with PHA covered processes
- Experience in lean manufacturing methodologies in driving value steam improvement
- Strong communication and change management skills
38
Value Stream Manager Resume Examples & Samples
- Work collaboratively with the team of Value Stream Managers
- Assist in implementing the business priorities and strategic objectives
- Develop, document and maintain the policies and procedures necessary to fulfill the products as defined in the master build plan and new projects as defined by the product and delivery managers
- Manage the projects utilizing the KPI’s necessary to evaluate and monitor the performance of the product build
- Oversee and manage conflict in resources and allocations
- Escalate resources conflict to Value Stream Director were appropriate
- Maintain knowledge of the product development and operational production responsibilities
- Bachelor's Degree in Business, Finance or Accounting
- Five years' experience in Program Management, Product Management and/or Production Management
- Experience with Microsoft office products, Google products and services as well as Database systems
- Must understand and be able to apply LEAN principles
- The deal candidates must foster teamwork and change management
- Must have strong negotiation skills
- Must have the ability to make decisions and lead positively
- Must have strong organizational and planning skills
- Must have a strong sense of creativity and innovation
- Must have a strong sense of problem-solving
- The ideal candidate must behave ethically
- PMP preferred but not required
39
Value Stream Manager Resume Examples & Samples
- 1\ Be responsible for the management of operation department
- 2\Be in charge of the improvements of production, facility, planning, logistics, lean and warehouse management
- 1\Min. 5yrs of value stream management experience in machine manufacturing industry
- 2\Bachelor degree or above, major in mechanical or relevant profession
- 3\Good English in listening,speaking, reading and writing
- 4\Excellent communication skill and can work under pressure
40
Value Stream Manager Resume Examples & Samples
- Accountable for all operational results (Quality, Cost, and Delivery) across the value stream defined from raw material reception through finished goods shipment
- Accountable for reporting and delivering to all KPI’s which drive the operation to continuously improve, ensuring the Production Supervisors maintain all key KPI data & visual management boards
- Define and deliver Continuous Improvement Plans for the value stream from future state maps
- Accountable for contact between the value stream and all external stakeholders in the production process (shared resource, sub contractors. etc) in terms of delivery performance, quality issues, and flow between the facilities
- Through the Production Supervisors, ensure that all employees are fully conversant and compliant with the Company’s Health and Safety policies.Ensure that all relevant Health and Safety legislation is effectively implemented and managed
- Support Operations Director in all business aspects
41
Value Stream Manager Resume Examples & Samples
- Lead and manage a manufacturing department(s). Establish goals with actions plans to achieve and utilize metrics to communicate progress and trends
- Manage department with a target of zero lost time injuries and recordables within Division targets
- Manage quality systems and be responsible for all out of box quality within these departments
- Maintain OTD objectives
- Manage productivity levels with the departments
- Continuously improve productivity, flow, change-overs, etc through the implementation of Lean principles
- Decrease scrap levels and identify all forms of waste for elimination
- Manage cost as a % of net sales. Manage within the forecasted budget
- Bachelor’s Degree required. MBA preferred
- Lean manufacturing concepts experience (layouts, material, performance to Takt, etc)
- Ability to lead and coordinate multi-functional team projects
- Experience working in an ERP system (SAP)
- Ability to develop leaders
- Injection Molding experience is a plus
- Welding and Fabrication experience is a plus
42
Value Stream Manager Resume Examples & Samples
- Maintaining the Value Stream’s production schedule relative to incoming sales orders, sales order changes, component availability changes and cancellations
- Directing the activities of all value stream personnel; to maintain a smooth flow of work; to achieve customer delivery dates; to support Company profitability
- Manages employee objectives, annual performance reviews, employee training needs and employee development plans
- Monitors discretionary and operational budget within specified guidelines
- Supports site cost reduction efforts through identification and implementation of improvement opportunities while working closely with Lean/Six Sigma Champion
- Liaises with Order Management, Inside Sales, Outside Sales, Quality, Manufacturing and External Customers to prioritize work activities and optimize efficiency
- Support Loss Prevention and Control programs by enforcing Health & Safety regulations in responsibility areas
- Work in accordance with Quality System (Quality Policy and Quality Procedure) to meet customer requirements and eliminate non-conforming products and services
- Other duties, as may be assigned, from time to time, by the Operations Manager
43
Value Stream Manager Resume Examples & Samples
- Supports deployment of manufacturing operations strategy, control systems, tools and metrics to accurately measure progress and drive continuous improvement
- Workforce planning and forecasting
- Employee hiring and training
- Area layout and flow management
- Capital identification and control of overhead expenses
- Ensuring the full compliance of company policies and procedures
- 10+ years of experience in manufacturing, operations, or engineering
- Prior Management experience
- Experience utilizing lean manufacturing concepts with a proven track record of lean or six sigma project implementation
- Broad understanding of component design, quality and production requirements and a demonstrated ability to continuously improve these processes
- Strong management skills including the ability to make decisions with minimal supervision, goal setting, delegation, coaching, and motivating
- Manufacturing or industrial engineering and supervisory experience in the aerospace/defense industry
- Core competency in the area of assembly/metal fabrication operations, labor standards – earned value management, and lean supply chain initiatives
- Excellent communication skills (written and verbal), presentation skill and influencing skills
- Flexible, open minded, and able to think outside the box to solve complex operational issues while maintaining open communications and a cooperative work environment
- High computer literacy and with confidence and skill working with Microsoft Office Tools (Excel, PowerPoint, Project) and familiarity with Raytheon systems (VM, PRISM, PDM)
- Metrics-driven
- EVMS Level 2 Certified
- BS/BA in Operations/Manufacturing, Business, Engineering or any major related to the above job description
44
Value Stream Manager Resume Examples & Samples
- Minimum of 8 years of experience in manufacturing, operations, engineering, or related field
- Core competency in the area of assembly operations, labor standards – earned value management, and lean supply chain initiatives
- Excellent communication skills (written and verbal), presentation and influencing skills
- Bias for Action, Doing, Speed, Results, Execution
- Metrics driven and success oriented
45
Value Stream Manager Resume Examples & Samples
- Accountable for all operational results (Safety, Quality, Cost, Delivery & Inventory) across the value stream defined from raw material reception through finished goods shipment
- Accountable for reporting and delivering to all KPI’s which drive the operation to continuously improve, ensuring the Value Stream team/support members maintain all key KPI data & visual management boards
- Define and deliver Continuous Improvement Plans for the value stream from future state maps. Prioritize and task manage value stream support team to perform against KPI’s and budget
- Accountable for contact between the value stream and all external stakeholders in the production process in terms of delivery performance, quality issues, and flow between the facilities
- Through the Team Leaders/Value Stream members, ensure that all employees are fully conversant and compliant with the Company’s Health and Safety policies. Ensure that all relevant Health and Safety legislation is effectively implemented and managed
- Key Performance Indicator: RADAR, Accident Frequency Rate (AFR) and Incidents
- Accountable for implementation and sustainment of the company’s Health and Safety procedures for all personnel in the Value Stream
- Accountable for all relevant Value Stream Health, Safety, and Environment (OHSAS) violations and closure of the subsequent Corrective Action Plans (CAP’s) by using the appropriate Practical Problem Solving (PPS) tools and techniques
- Ensure risk assessments are updated and maintained as required including process change, engineering change, new plant, etc
- Key Performance Indicator: Tags, Scrap, DPU & Escapes
- Fully accountable for all aspects of quality from raw material reception through to finished product shipment
- Create and champion improvement plans of all manufacturing processes to enable right first time performance
- Ensure effective problem resolution using relevant data as required
- Ensure customer protection is in place and that countermeasures are completed in a timely manner
- Accountable for demonstrating awareness and application of relevant company procedures including conformity to AS9100 C and any other relevant certification processes
- Accountable for RCCA closure within the agreed timescales
- Key Performance Indicators: On time Starts/Completions & Delivery to IOP
- Accountable for achieving on time delivery to all external and internal customers
- Accountable for overall capacity planning of people, machine and support functions within the value stream to ensure continuous flow through the value stream
- Accountable for defining and implementing flow systems, in line with the Future State Value Stream Map, to meet customers’ requirements. Work with suppliers, procurement, and shared resources as required
- Accountable for a business continuity plan for the value stream
- Key Performance Indicators: Cost Per Unit, Labor and related Operational costs
- Accountable for the Value Stream budget, possessing sufficient knowledge of local operations to understand changes in performance and implement immediate countermeasures
- Champion Operational Supplies, POU and related cost for value stream, escalate out of control conditions, and implement recovery plan as needed
- Coordinate and be active participant in Change Board process for their Value Stream(s) and assist PMO change activity
- Provide input to Finance and Head of Business for budget creation
- Meet required Cost Objectives and provide EAC performance into the PMO on a monthly or as needed basis
- Manage labor cost (budgeted hours planned vs. actual & unplanned,) efficiency of workforce within the values stream production line
- Key Performance Indicators: Total Value (WIP, FG, Raw Material), Stock Turns
- Accountable for the Value Stream inventory levels associated with the build plan provided by the PMO
- Coordinate implement counter measures on inventory levels above plan
- Work WIP on tag for both internal and external PN’s to support disposition business process
- Meet required monthly step down plan of inventory to support lean manufacturing principles
- Accountable for all communication with value stream team members, value stream support staff, and relevant operations personnel
- Support value stream team in acting as a Key Communicator. Communicate consistently and effectively to all employee representatives, external suppliers, management team and customers as appropriate. Provide appropriate feedback on a regular and as-needed basis
- Actively resolve issues using standard model of leadership behavior: setting expectations, coaching, recognition, constructive feedback, and escalation where appropriate
- Leading and sponsoring improvement activities using lean methodology, tools, and techniques. Ensure that all team members have equal opportunity to contribute to improvement and identify training needs within the team
- Ensure and enhance a people focused environment
- Manage employee relations on a day-to-day basis, working within GKN procedures and ensure effective interfaces with employees’ representatives
- Support and monitor the development of all employees in value streams and support functions via Personal Development Plans (PDPs), reviews and feedback
- Ensure value stream team leaders review current skills against predictive requirements and support the development and maintenance of skills matrix accordingly
- Coach and manage the value stream team members and direct reports through their Personal Development Review (PDR) and Personal Development Plans (PDP) to improve Value Stream performance
- Promote and deliver Employee Involvement (EI) through behavioral leadership
- Promote and develop EI activities and ensure effective shift start up meetings around PVDs (Primary Visual Displays) and allocate time for EI Group Leader to lead weekly/monthly EI activities
- Support PMRs and Operations Reviews as required and provide input status to the KPI’s presented
- Accountable for the operational and organizational management of the team ensuring that all value stream KPI objectives are achieved
- Address performance issues in a timely and appropriate fashion. Where necessary, initiate corrective action
- Report weekly to PMO/Ops Core Leader performance against KPI’s and business improvement plans
- Develop systems in value stream to create and monitor flow, evoking standard reaction procedures when flow is disrupted
- Accountable for sufficient supervisory / essential skill set cover for all periods of operation including safety, Leader coverage , as well as operators’ skill sets
- Provide accountability through Team Leader for all overtime requests
- Identify gaps in skills through Professional Development Reviews (PDRs) to be closed by Functional Heads
- A minimum of five years of experience in leadership roles with manufacturing operations and/or program management is required
- SCIL or MCIL Program Graduate or In Process
- Demonstrated skills in written and verbal communication, problem analysis, potential problem analysis, decision analysis and planning
- Skilled in coaching, team-building, business measurement, continuous improvement and lean manufacturing techniques
- Computer skills necessary
46
Value Stream Manager Resume Examples & Samples
- Leads cross-functional team to direct the order fulfillment process for assigned product lines
- Establishes and maintains key performance measures throughout the manufacturing environment
- Evaluates in-house manufacturing vs. outsourcing, quality control and workforce balance
- Accountable for managing overall strategic production planning practices taking into consideration short term/long term production requirements
- Supervises all work performed in their area; offering coaching/mentoring or corrective action when appropriate
- Responsible for managing operational inventory to ensure adequate stocking levels for immediate production items and forecasting for future requirements
- Creates operations budgets, identifies resource needs, and works with other management teams in determining financial needs of the product line(s)
- Provides leadership in the areas of continuous improvement of customer focused metrics, quality and safety
- Maintains daily visual production boards for efficient production performance; provides prioritized production scheduling to all Lead Associates and team members
- Drives Lean initiatives; including facilitation, process mapping, spaghetti charting, identification and elimination of the 7 wastes, takt-time, balanced flow process, visual factory, empowered team meetings, total safety, standardized work and world class 5S standards
- Leads the effort in safety compliance, improvement and promoting awareness in accordance with company safety requirements and guidelines; drives 5S into production on a daily basis
- Provides technical manufacturing assistance. Maintains knowledge of plant's processes, techniques, tools, materials, machines and equipment
- Leads Lean transformation efforts throughout the organization
- Responds to line down issues and provide leadership to root cause analysis and corrective action plan execution
- Conducts regularly scheduled Lead Associate meetings
- Provides technical assistance to the Lead Associates and team members
- Ensures equipment is maintained in accordance with Company guidelines
- Reviews and updates ECO’s
- Approves weekly attendance records on E-Time for team members
- Ensures quality standards are met will all products
- Administers AERCO policies and procedures
- Additional projects as necessary
- Direct supervision of Value Stream’s Planner/Buyers, Manufacturing Engineer, and Production Supervisor
- Perform annual performance appraisals of Team on a timely basis
- Lead team to work in a safe manner at all times and comply with safety policies and standards
- Demonstrates ability to be a team player by actively participating in assigned teams as well as intercompany, cross-functional and/or special committees
- Demonstrated ability to manage/lead cross functional teams
- Sense of Urgency
- Knowledge and expertise in Lean Manufacturing
- Must possess a desire to excel and a “hands on” management style
- Ability to manage multiple priorities and projects simultaneously
- Strong management and leadership skills to include coaching and facilitating
- Well developed organizational skills
- Must excel in a team environment
- Must embrace change
- Minimum 7 years supervisory experience in a manufacturing environment
- While performing duties of the job, employee is required to sit; stand; walk; use hands to handle objects, tools, or controls; reach with hands and arms; talk and hear
- Employee will occasionally lift and/or move up to 40 pounds
- Specific vision abilities required by the job include close vision, distance vision, color vision, peripheral vision, depth perception, and the ability to adjust focus
- Office and shop floor working environment
- Noise level is constant with intervals of spikes
- Required to wear safety glasses and utilize other safety equipment as required while present on the shop floor
47
GSC Value Stream Manager Resume Examples & Samples
- Develop and execute Supplier Gold Strategy, which will ensure Gold spend is achieved and Underperforming Suppliers are addressed
- Develop the Product Process Organization (PPO) relationship to ensure source selection alignment to VSM strategy
- Lead the supplier accountability board process for the cognizant value stream
48
Value Stream Manager, Materials Management Resume Examples & Samples
- Working across Global Operations in the training, deployment and implementation of UTAS Standard Factory processes for Materials Management
- Stewardship of the processes, tools, and standard work for Materials Planning, Production Control, Logistics Management, and Delivery Assurance
- Mature team capability through coaching and mentoring site teams. Interact with the global organization on best practice sharing
- Work closely with site materials management leaders and SAP technical team to design and implement business process changes aligned with improved operational performance
- Develop Materials Management employees throughout the business unit to improve their ability to
- Minimum of 10 years of progressive experience in Operations, Lean, Supply Chain, or Materials Management with at least 3 years managing (either directly or indirectly) people and teams
- Strong interpersonal, facilitation, and conflict resolution skills. Proven ability to lead without positional authority across organizational boundaries
- Strong written and verbal communication skills across a variety of formats and audiences. Able to effectively interact with employees at all levels. Past success in presenting to executive leadership and influencing key decision makers
- Demonstrated experience in using a hierarchy of controls to mistake proof processes and creating visual controls for effective monitoring and real time problem resolution
- Demonstrated proficiency in ERP and/or MRP systems, SAP preferred
- Candidate must be a US Person. (US Citizen or Permanent Resident)
49
Value Stream Manager Resume Examples & Samples
- Work together with the Plant Manager and site support team to achieve optimum Safety, Quality and Delivery results and expectations
- Complete Leader Standard Work and all deliverables of value stream
- Accountable for “wall to wall” KPI performance for the value stream
- Lead change agent to ensure lean processes are deployed in measurable improvements
- Presenting current issues and requesting support of the Plant Manager, when applicable
- Schedule reviews of projects and progress with Plant Managers
- Coach and mentor Group Leaders
- Facilitate the identification, selection, and prioritization of projects with an emphasis on those that have breakthrough potential
- Train Group Leaders on the application of SPS tools and appropriate project planning tools to improve processes, eliminate waste, and reduce cycle time
- Ensure value stream results are aligned to methodology and strategies of Shiloh
- Audit the SPS system in the value stream on a regular basis
- Accountable for project executions from inception to completion, including communication of results and verification
50
Value Stream Manager Resume Examples & Samples
- Commitment to continuous improvement culture – stretch, fact based questioning, etc
- Setting and executing strategy in a business through a strategy deployment process (Hoshin Kanri, goal deployment, or similar)
- Driving daily visual management to the operator / associate level for both execution and counter measuring / adjusting
- Leading cost reduction, inventory reductions and supplier contract negotiations
- Setting and meeting commitments through creating a culture of accountability
- Directing and controlling assigned work force through the good communication
- Dynamic leadership resulting in improved operational performance through daily management, Gemba walks, providing feedback, mentoring next-level leadership
- Creating, deploying and enforcing lean principles in the plant and with suppliers
- Utilizing sound problem solving skill set and root cause analysis as method of metric driven performance improvements
- Commitment to candid feedback to team including deploying Performance Ownership or similar process
- Workforce management, contract or policy execution, good judgment on labor issues
- Leadership, management, and communication skills leading to sustained cultural change
- Ability to effectively communicate in small to medium groups of diverse backgrounds as well as effective communication with various levels of management
- Organizational insight and planning
51
Value Stream Manager Resume Examples & Samples
- Provide leadership and direction to Production Supervisors, Team Leads, Process Engineers and associates within the value stream and create a positive work ethic and culture
- Mentor direct reports and their subordinates to improve skills, efficiency and effectiveness
- Maintain positive employee relations through transparency and open communication skills
- Listen, support, engage and encourage employee suggestions and input
- Drive daily accountability and customer focus throughout the value stream
- Develop, review, and present various reports to accurately measure production processes and make improvements to drive improved results
- Drive PPI projects to improve efficiency, work environment and product and process quality
- Lead and support PPI initiatives and projects including/but not limited to Tier I, II, and III Daily management, GEMBA walks, 5 “S”, Leader Standard Work, and KPI metrics
- Develop and utilize capacity plans to accurately understand planning and headcount requirements
- Manage and take action on based on customer and other manager feedback
- Manage value stream within set budgets
- Participate with support functions on new product introductions; lead pilot and production trial runs
- Demonstrate Thermo Fisher Scientific values - Integrity, Intensity, Innovation and Involvement
- Manage disciplinary action process when required and warranted
- Track absenteeism and timekeeping
- Provide constant shop floor leadership (75% of time) and lead by example
- Manage in-bound and out-bound freight pacing aligned with capacity and customer requirements
- Oversee warehouse management including inventory accuracy and efficient utilization of footprint
- Assist with carrier selection and be contact for division and corporate freight management objectives
- BA, or BS degree in Engineering, Manufacturing Technology, Manufacturing Operations, Management or related field, or equivalent work experience Advanced degree preferred
- 7+ years of work experience in highly preferred, ideally in logistics and distribution
- Quality Systems Regulations/ISO experience required; ISO 9000, ISO13485, FDA experience preferred
- Proven track record in leading and implementing lean tools to drive improvement
- Must demonstrate strong organizational and leadership skills and to handle multiple tasks simultaneously
- High degree of accuracy and decision-making ability
- Flexibility in scheduling
- Strong math and data entry skills
- Possesses motivation for a continuous improvement & desire to improve all aspects of the Value Stream
- Knowledgeable in data collection, measuring, analysis, improvement and control
- Ability to conduct critical analysis and assessments to develop strategic action plans that ensure efficient, lean, and effective processes are in place to produce quality products
- Ability to deliver results in a team based manufacturing environment and make fact based decisions
- Demonstrate strong business acumen, organizational and analytical skills
- Effective employee management skills including dealing with difficult employee situations and providing constructive feedback. Ability to lead, coach, counsel and encourage subordinates
- Minimum of 5 years of demonstrated leadership skills in a manufacturing environment
- Read, write and understand English
52
Value Stream Manager Resume Examples & Samples
- Provide leadership and direction to Production Supervisors, Team Leads, Process Engineers and Associates within the value stream and drive a process improvement and RCCA culture
- Mentor direct reports and their subordinates to improve skills and overall efficiency and effectiveness
- Maintain positive employee relations through the use of transparency and open communication skills
- Develop, review, and present various work/management reports to accurately measure production processes and make improvements to produce improved results
- Lead and support LEAN initiatives including but not limited to Tier I, II, and III Daily management, GEMBA walks, 5 “S”, Leader Standard Work, and KPI metrics
- Develop and utilize capacity plans to accurately understand resource planning and headcount requirements
- Produce and manage key operational metrics
- Manage and take action based on customer and other manager feedback
- Participate with Quality, R&D and Engineering on new product introductions; lead pilot and production trial runs
- Manage disciplinary action process
- Provide constant shop floor leadership (90% of time)
- BA, or BS degree in Engineering, Manufacturing Technology, Manufacturing Operations, Management or related field, or equivalent work experience. Advanced degree preferred
- 7+ years of related work experience in manufacturing highly preferred, ideally in manufacturing processes involving cutting, cleaning and coating glass substrates
- Possesses motivation for a continuous improvement mindset and desire to improve all aspects of the Value Stream
- Ability to lead and deliver results in a team based manufacturing environment and make fact based decisions
53
Value Stream Manager Resume Examples & Samples
- Responsible for leading and managing the Value Stream and its overall day-to-day business operations to the successful achievement of its production output and financial goals as measured through the profit and loss statement (P&L)
- Partners with BU leadership and Product Line Management to develop and implement product line strategies around NPI, Quality, and Cost
- Partner with design engineering to ensure quality, manufacturability, and cost targets are met on new products introductions. Provide business case analysis on where we should invest sustaining engineering to drive cost out of current products
- Improve overall productivity and performance by implementing and executing Lean Principles in accordance with the API Business System (ABS). Develop a culture of Lean and associated methodology for sustained growth
- Drive continuous improvement by involving employees in the problem solving and decision making as well as recognizing them for exceptional work
- Provides direction in developing and integrating new technology
- Monitors, reviews, and directs operations by providing feedback and information regarding production standards and capabilities and how they relate to productivity and performance goals
- Set operational priorities and achieve key business measures and key performance indicators (KPIs) as established in the company’s Strategic Deployment (SD) process
- Bachelor’s degree in Engineering, Business, or related field, AND
- 6 years of experience as a Manufacturing Management Professional, OR
- Proven ability to learn and apply modern production and material methodologies that may include Six Sigma, SPC, Kanban, 5S, Value Stream mapping, Design of Experiments, process capability, gauge R&R, hypothesis tests, SPC and other means to improve and control processes
- Possesses understanding of quality system requirements
- Electronics, government and military high reliability experience preferred
- Financial and management systems experience preferred
- Ability to effectively communicate with personnel at all levels within the organization
- Ability to lead, direct, monitor, and maintain activities of organization
- Ability to coordinate plans and activities of the corporation with plans and activities of the division
- This is an office-based position
54
Value Stream Manager Resume Examples & Samples
- Direct and supervise the coordination of focused factory shifts to achieve production and quality requirements as specified
- Implement and monitor all safety procedures with appropriate follow-up and corrective actions for unsafe conditions
- Anticipate, analyze, diagnose production problems (tooling problems, equipment malfunctions, material or labor shortages, etc.)
- Provide input to management to facilitate effective cost reduction, work simplification, scheduling, and other continuous improvement measures
- Monitor accuracy of production and quality reporting information with accountability for accuracy
- Review performance of focused factory shifts, coach for improvement, and set objectives specific to safety, quality, productivity, and utilization of labor
- Ensure consistent workflow to achieve quality and production requirements
- Administer company and government policies/laws in accordance with all employee actions (hiring, layoffs, terminations, transfers, disciplinary actions)
- Recommend personnel actions, changes of assignment, training, wages, etc. for focused factory
- Maintain an adequate and efficient work force in accordance with skill requirements, work levels, budgetary requirements
- Management of overall production and setup operations
- Developing and setting departmental performance standards
- Achieve quality objectives
- Working knowledge of LEAN
- Operate within department budget guidelines
- Maintain a motivational climate of continuous improvement
55
Value Stream Manager Resume Examples & Samples
- Bachelor’s degree in business management or engineering strongly preferred. An advanced degree such as an MBA is a plus. High school education with equivalent applicable work experience may be substituted with additional experience
- 10+ years working experience in a manufacturing environment with leadership experience, business and financial acumen
- Ability to travel as required, Working conditions require the ability to sit, stand, walk, bend, climb stairs, and work at a computer station and on manufacturing shop floor
56
Value Stream Manager Resume Examples & Samples
- Fully responsible for product quality, employee safety, regulatory compliance and consistently achieving production schedules to successfully meet market demand
- Directly manage the implementation projects for all value streams. Partner with appropriate management to ensure customer deliverables and expectations are being met
- Bachelor’s Degree or equivalent. Masters preferred
- 5 years of major professional accomplishments, including increasing responsibility and leadership of projects and teams of considerable size, scope, and complexity
- Background in accounting, PC skills, manufacturing, human resources management, inventory control and strategic planning
- Team-building skills in producing results by meeting organizational objectives. Capable of assessing and developing individual and team skills and capabilities
- Involved with or directing strategic change within an organization
- Involved with or manage a team in LEAN process improvements/implementation preferred
57
Value Stream Manager Resume Examples & Samples
- Must be capable of maintaining a broad perspective of the entire value stream
- Must be capable of system level thinking to avoid sub-optimizing and drive improvement over the entire systems of processes
- Demonstrable knowledge of Lean Six Sigma, and an innate ability to work closely with Operational Excellence Leaders to drive appropriate action, or have demonstrable ability and commitment to getting this knowledge
- Must have exemplary leadership skills and a proven ability to both influence and motivate at all levels of the organization as well as lead without authority, negotiate and manage by influence
- Demonstrable capability and inclination to make decisions based on data and facts rather than opinion
- Must be both open to ideas from employees and an active champion of improving employee engagement at every level of the business
- Must be capable of creating and managing the execution of plans and projects within the value stream
- Must be able to communicate appropriately with employees, customers, suppliers and senior executives to gain buy-in on major elements of the value stream plan
- Must be capable of negotiating at a very high level to ensure that win-win changes are made when they affect suppliers, customers and internal employees
- Strong people and time management skills are required
- Excellent verbal and written communication skills are required; must be able to communicate effectively and professionally with customers and across all organizational levels
- Experience in production control, project management or contracts management, are key talents
- Detail oriented, positive friendly customer service are key attributes
- Computer knowledge and skills, i.e. MS Office Suite – Word, Power Point and Excel is required
- BA/BS degree required or equivalent years of experience
- Certification in PMP and or CAPM preferred, Contracts Administration, Project Management a plus
- Three (3) plus years in an aerospace or manufacturing environment required
- Program(s) oversight of a minimum of $10 million is preferred
- Two (2) plus years of supervisory or Program Management experience preferred
- Three (3) plus years’ experience with MRP systems is required
58
Value Stream Manager Resume Examples & Samples
- Aircraft and manufacturing experience desirable
- Quality system awareness
- Awareness of HSE requirements
- Supervisory management skills
- Basic understanding of continuous improvement tools and techniques
- Comprehensive knowledge of finance/budgeting
- Understanding of a commercial business environment
- Export Control understanding and regulatory requirements
59
Value Stream Manager Resume Examples & Samples
- Production planning in a high mix, mid to high volume environment
- Leadership of skilled mechanical assembly process
- Lead hourly direct labor employees to meet desired results
- Understanding of inventory control/management
- Utilize team leads and continuous improvement tools to reduce waste/costs
- Effectively produce written documents such as production reports or procedures/ work instructions when necessary
- Lead Lean Daily Management Meeting
- Trend and track manufacturing performance
- Root Cause Analysis of missed targets, able to drive action plans to address the root cause
- Responsible for aiding in own self-development by being available and receptive to all training made available by the company
- Plans daily activities within the guidelines of company policy, job description, and supervisor’s instruction in such a way as to maximize personal output
- Responsible for 5S within the work area to ensure safety and productivity goals are exceeded
- Coach, develop and mentor team members
- BA/BS Degree in applicable field
- A minimum of 5 years experience in a manufacturing environment with progressive responsibilty or leadership position
- Knowledge of Continuous Improvement Methodologies (Lean, Six Sigma, TOC)
- Experience with ERP systems (JDE knowledge is a plus)
- Ability to multitask and delivery expected results
- Advanced computer skills (Excel, Access, ERP systems)
- Demonstrate responsibility, respect, dependability, patience, and productivity in order to create a positive work environment
- Influential leadership skills
- Demonstrated ability to develop a team which produces expected results
- Three (3) plus years of Leadership Experience
- Experience working with ISO 9001 or QMS systems
60
Value Stream Manager Resume Examples & Samples
- Effectively plan, direct and coordinate all activities of value stream manufacturing
- Ensure that all team personnel are adequately trained, supplied, resourced and managed to accomplish core objectives (Safety, Quality, Delivery, Cost, and Productivity)
- Develop subordinates to optimize their skills and performances in a team environment
- Develop plans and metrics for value stream (VS) transformation together with Site leader
- Utilizes Lean Manufacturing and Six Sigma tools to create flow and eliminate non-value added activities and defects, reduce process variation
- Lead or participate in Rapid Improvement Events and Six Sigma projects necessary for VS transformation
- Create standard work procedures and visual controls to manage VS’s
- Recommend and/or authorize improvements in machinery, equipment and manufacturing methods
- Responsible for long term production capacity, continuous improvement and strategic planning
- Develop and deploy key performance objectives to employees via Performance Ownership process and Daily Management. Set reasonable goals for the cells and motivate subordinates to meet or exceed these expectations
- Work closely with internal Quality Manager. Request 5-why root cause analysis from responsible parties and document countermeasures. Data mining and analysis relating to quality process improvements regarding the Value Stream metrics
- Ensure plant and Corporate Policies are consistently administered within the cells
- Maintains regular and reliable attendance
- Minimum 3-7 years experience of related work experience in a LEAN manufacturing operation
- Must have the ability to direct and control assigned work force through the use of good communication
- Attention to detail with the ability to multi-task in a fast paced environment
- Willingness to be a participant in a continuous improvement surrounding
- Understanding of SOPs, BOM, Work Instructions, Six Sigma, project management, leadership, and LEAN manufacturing highly desirable
- Able to conduct basic root cause analysis using structured problem solving method
- Working knowledge of basic facility infrastructure and mechanical equipment
- This job position requires compliance with ITAR Regulations. Therefore, all employees working in this capacity must meet citizenship status. The employee must be a U.S. Citizen or a U.S. Permanent Resident
- Bachelor’s Degree in Business or Engineering with at least five (5) years demonstrated success in manufacturing supervision
- Demonstrated experience in leading lean manufacturing, quality improvement initiatives
- Demonstrated leadership and team building skills
- Demonstrated computer literacy especially working with Microsoft Office and ERP systems
- Ability to understand and apply basic cost accounting concepts
- Demonstrated mechanical aptitude and knowledge of manufacturing processes
- Well-developed inter-personal skills to help focus and motivate employees in a positive and constructive fashion
- Ability to appraise a situation through data analysis and facilitate team members accordingly
61
Senior Value Stream Manager Resume Examples & Samples
- Manage a variety of complex issues in associated projects, plans and schedules project implementation
- Responsible for defining scope of work for Value Stream
- Manage, identify, hire, and develop staff
- Provide technical direction
- Review and analyze proposals to determine if benefits derived and possible applications justify expenditures
- Responsible for policy setting and defining procedures for the staff in accomplishing and documenting projects
- Approve protocols and support documentation (engineering change requests, system change forms, etc.)
- Ensure products are provided to customers on time so that product quality, yield, operating costs and process efficiencies are met
- Identify/prioritize/provide resources
- Emphasize training and implement control systems
- Commit to employee feedback and developmental processes
- Provide a positive and equitable working environment emphasizing the Baxter Shared Values
- Help prepare budgets for areas of responsibility
- Responsible for assuring compliances to all regulatory requirements – FDA, OSHA, OFCCP, EPA, etc
- Adheres to all environmental, health and safety SOPs, equipment, policies and procedures, including any department specific requirements
- Make staffing decisions
- Investigate and resolve disciplinary issues
- Support plant-wide strategic plan programs and activities
- Drive continuous improvement activities in support of cost reductions to meet VIP program objectives
- Understanding of engineering disciplines
- Must be self-motivated, have good interpersonal skills, capable of analyzing and solving complex problems through innovative thought and experience
- Ability to design and implement in own area of expertise
- Has demonstrated effective supervisory skills
- Knowledge of World Class manufacturing methods (QLP, Lean, Six Sigma)
- B.S. degree in a relevant engineering discipline. Master's degree preferred
- 10 – 12 years of engineering experience
- 5-7 years’ experience in all aspects of the manufacturing process
- Black Belt or Master Black Belt certification preferred
62
Value Stream Manager Resume Examples & Samples
- Assisting in setting aggressive performance targets and challenging associates to consistently meet or exceed such goals. The diversity of operations requires all departments to work closely together and interact with sales, technical functions, customers and suppliers in order to meet established goals and financial objectives
- Managing and directing the activities of Production Supervisors, Engineers, and hourly employees
- Providing appropriate training, work direction and guidance to ensure that specific performance standards are consistently met
- Creating a cohesive team environment through enthusiastic leadership, coaching and performance management is critical to successful supervisory performance
- Identification, participation, and leadership of projects to address the needs of the department, the company and customers
- An understanding of glass fabricating technology is an asset
- Previous manager level experience with Tier 1 Automotive manufacturing practices
- Experience using Lean Six Sigma to improve and control processes with documented favorable results (Yellow, Green or Black)
- Knowledge and use of standard work
- Experience performing in a 24/7 manufacturing operation with significant accountabilities * History of personally making improvements in Key Process Indicators
- Strong interpersonal skills in problem-solving, leadership, team-building and written and verbal communications
- Flexibility to respond quickly to changing business demands and the ability to assess priorities and act decisively on complex issues
- Ability to act with long-term perspective, accept responsibility, mobilize resources, plan and organize and share information
- Excellent listening skills with the ability to size up situations in order to resolve conflict and solve problems with both people and processes
- Solid experience with Microsoft Office Excel, Word, and Outlook * Solid use of PowerPoint and the ability to present to Sr. Leadership levels
63
Value Stream Manager Resume Examples & Samples
- Supervise all production operations such as machining, processing and heavy assembly
- Plan, schedule, and coordinate departmental activities to fulfill sales orders, meet inventory requirements, and deliver manufactured products in a timely fashion
- Supervise all value stream associates on 2 shifts
- Daily Standard Work which includes
64
Value Stream Manager Resume Examples & Samples
- Must be organized and able to work with multiple jobs at one time while meeting necessary deadlines
- Previous experience managing to metrics, driving projects from creation to implementation, leading cross functional teams
- Prior experience driving action plans or owning counter measures is highly preferred
- Ability to manage a department and lead cross functional teams
- Ability to make decisions and drive them to results in a high paced business environment
- Ability to hit deadlines is a must
- Measurable continuous improvement experience desirable
- Excellent communication skills, including written, listening, and verbal skills
- Self motivated individual, able to muti-task and drive team cohesiveness effectively
- Leadership abilities with coaching and team development experience a plus
- Previous experience with piercing, machining and welding processes a plus
- Experience automating and upgrading manufacturing processes desirable
- Union experience a plus
65
Value Stream Manager Resume Examples & Samples
- Accountable for all operational results (Cash, Quality, Cost, Delivery) across the value stream defined from raw material reception through finished goods shipment
- Accountable for reporting and delivering to all KPI’s which drive the operation to continuously improve
- Define and deliver Continuous Improvement Plans for the value stream from future state maps. Prioritize and manage value stream support team to perform against KPI’s and budget
- Accountable for contact and coordination between the value stream, the GKN support organizations, and all external stakeholders in the value stream process (Including Customers, the Commercial Teams, Product Engineering, site shared resources, Suppliers, etc.) in terms of delivery performance, quality issues, and flow between the facilities
- Accountable to ensure that all employees are fully conversant and compliant with the Company’s Health and Safety policies. Ensure that all relevant Health and Safety legislation is effectively implemented and managed
- Support Plant Operations Manager in business planning, budgeting, and all business aspects
66
Value Stream Manager Resume Examples & Samples
- Ensure that the health and safety of all employees remains the number one goal
- To communicate the business objectives, plans, budgets, and performance to all employees within the value stream in order to maximize individual and collective contributions and commitment to continuously improve the performance of the business
- To direct business operations for the value stream, including the current state value stream map, future state value stream map, action plans to achieve the desired future state including accountability to the desired business metrics
- Ensure that all business objectives are met; understand key constraints, critical process flow, staffing, and scheduling
- To provide hands on leadership and management while utilizing standardization, continuous improvement, and the sharing of best practices to deliver best in class operational performance
- To build a high performing team culture that recognizes and rewards excellence and encourages individuals to strive for performance improvement within the business
- Responsible for developing and implementing a cross training plan that supports production needs
- Partner with all functional areas to positively impact culture and clearly communicate the business objectives
- Proactively manage new product introductions to ensure they are successfully implemented within the value stream
- Strong background in lean manufacturing, continuous improvement, and other production related models. Experience in planning and execution. Ability to develop operational plans and manage resources. Ability to analyze and interpret financial data. Knowledge of human resource principles and practices. Knowledge of communication techniques and ability to act as a coach and mentor to help employees reach their full potential. Ability to develop and deliver presentations
- Strong written, verbal, and interpersonal skills required. Ability to convey information and ideas through a variety of media to individuals and groups. Ability to engage others and instill trust both inside and outside of the value stream. Must be able to interact with a diverse group of people to create an environment that is equitable, inclusive, and cooperative
- Ability to make time bounded decisions characterized by logic and reasoning while keeping the organization's vision and values at the forefront. Ability to facilitate and lead using innovative approaches, addressing of problems and opportunities, and implementation and acceptance of change within the workplace
67
Value Stream Manager Resume Examples & Samples
- Minimum of 3+ years of experience as a manager or supervisor in a manufacturing environment
- Experience using Lean Six Sigma to improve and control processes with documented favorable results (Yellow, Green or Black) * Knowledge and use of standard work
- Experience performing in a 24/7 manufacturing operation with significant accountabilities
- History of personally making improvements in Key Process Indicators
- Solid experience with Microsoft Office Excel, Word, and Outlook
- Solid use of PowerPoint and the ability to present to Sr. Leadership levels
68
Value Stream Manager Resume Examples & Samples
- Creates, implements and drives key safety initiatives through our talented associates, assuring resources are sufficient to create an accident free culture. Ensures safety commitment and engagement from EVERY associate, while creating an atmosphere of open and honest dialog and feedback
- To exceed the product quality expectations of the customer while ensuring orders are manufactured on time, without compromising processes or design specifications
- Responsible for total production of the unit and cell metrics including safety, production quantity, customer service, defect levels, waste, work order attainment, etc. Creates an atmosphere of team ownership of daily process and results, ensuring fully engaged associates
- Selects, mentors and coaches’ cell coordinators and star points along with direct and indirect associates that help lead the manufacturing effort. Ensuring the correct skill sets and styles are evident and practiced in all cell coordinators
- Ensure resources are available and fully utilized, with a focus on continuous development of hourly associates
- Utilizes effective leadership skills in a manner to achieve proper motivation, performance, reward, respect and accountability for all operational resources
- Coordinate the maintenance of manufacturing data systems necessary to support the manufacturing process, and provide information for budgeting, capacity and planning processes. Ensures the use of data-driven improvements within the facility
- Effectively manages cross functional relationships with other departments to support effective use of manpower, materials, and equipment, as well as productivity and quality improvement initiatives
- Promotes “on-the-spot" problem solving activity, supporting associates in cells with decisions and needs, ensuring progress toward operator led decision making and control
- Utilizes Lean-Sigma tools to continuously improve the business every day
- Executes the financial plans associated with the operational team
- A visible and vocal presence as the shop floor leader. Has a passion for mentoring associates expanding their ability to self-manage (best in class process, culture, involvement and results) Observes cell/team meetings and make recommendations for improvement to team processes
- Engages in daily two-way pro-active communication with team
- Facilitates relationship building between associates
- Creates and maintains a culture of teamwork, providing support without removing responsibility
- Coaches’ associates to use resources and lean tools, helping teams improve their ability to solve problems together
- Utilizes “critical few" metrics thinking to focus the team and achieve superior results
- Navigates and negotiates change with the team and the organization
- Proactively predicts and plans for team responses to challenges
- Advocates for the team ensuring the resources and opportunities provided are appropriate to develop the team’s capabilities
- Leadership, communication, relationship building, problem solving and enhancement of skills for self and with team
- Results driven individual who has demonstrated ability to manage in a high performance manufacturing environment
- Good attention to details, but able to see and manage the big picture and have a “make the numbers" mentality
- Able to manage and execute multiple, complex tasks and deal easily with pressure on a daily basis
- Able to motivate, communicate, and drive continuous improvement
- Solid planning, leadership, and administrative skills
- Good understanding of business principles and practices; can effectively manage the manufacturing function with a bottom line result
- Ability to run a focused agenda
- Utilizes great leadership attributes to interpret the toughest situations in a constructive and empowering way
- Individual familiar with and practicing Lean-Sigma techniques and quality improvement tools that drive continuous improvement
- A creative thinker who values engagement, ownership and contribution of all associates through empowerment and Operator Led initiatives
- A results driven individual who has demonstrated ability in creating a high performance manufacturing environment
- Able to understand, communicate and inspire associates to improve key performance metrics
- Is able to see the “big picture," communicate this to others, and help them grow their goal attainment
- 5-7 years experience in manufacturing management with team based environment
- 2-3 years experience as a manufacturing leader
- Strong database background, comfortable with a variety of software systems, including spreadsheets
- Strong manufacturing background; able to understand appropriate product and process specifications
69
Value Stream Manager Resume Examples & Samples
- Strong leadership skills, including the ability to inspire, impact and innovate
- Ability to manage changing situations, tasks and priorities
- Ability to work effectively with employees at all levels fostering a strong team environment
- Strong quantitative, analytical and process thinking capability
- Relationship and conflict management; communicates clearly and effectively with people inside and outside the organization to drive a culture of transparency and trust
- Bachelor's degree from four-year college or university, preferably in Engineering, Technical or Business discipline, is required
- 2-4 years of value stream operations management experience with track record of building, developing and evaluating teams
- 5 years’ experience in a Lean focused process improvement role with advanced training in Lean Manufacturing, Six Sigma, 6s, SMED, and other continuous improvement methodologies
- 5-10 years of aerospace manufacturing experience preferred, or progressive related manufacturing experience
- Lean / Six Sigma Certification a plus
- Proficiency in Microsoft Office applications required
- 3333 Main Street
70
Value Stream Manager Resume Examples & Samples
- Drives continuous improvement efforts in every activity of the value stream
- Demonstrates a high level of commitment to the business and team excellence
- Provides leadership, direction, and development to the value stream personnel
- Create and manage a value stream plan – centered around a living current and future state map
- Stay close to their customers to understand market needs and to get feedback on performance
- Utilize Lean techniques to reduce waste, improve work flow, and to grow the business
- Demonstrate strong leadership skills; motivation, planning, delegation, and communications
- Develop people through training, experience, and providing challenging growth opportunities and providing performance feedback to associates in a timely manner
- Develop long term growth strategies
- Conduct weekly value stream meetings to keep the assigned associates informed and engaged
- Utilize fact based decision making
- Ability to communicate effectively with all levels of an organization as well as with customers
- Provide timely value stream performance measurements to ECB management
- Visual management tools are widely used, are current, and meaningful
- Participation in ECB efforts to develop the annual business plan and 3-year strategic plan
- 5 years’ experience required in a manufacturing organization including demonstrated success in implementing Lean/TPS/CIP initiatives
- Experience in designing and developing continuous improvement programs (CIP)
- Broad knowledge of lean/TPS/CIP principles and tools
- Demonstrated ability to successfully implement lean/TPS/CIP principles within manufacturing environments and/or in office processes
- Ability to effectively train and mentor others on lean/TPS/CIP principles
- Strong strategic planning skills and the ability to convert to an action plan
- Effective and collaborative problem-solving skills
- Demonstrated ability to collaborate and develop effective relationships at all levels and functions within the organization
- Self-motivation, drive, energy, and resilience
- Strong business acumen and financial analysis skills
71
Value Stream Manager Resume Examples & Samples
- O Responsible for your Value Stream performance (Safety, quality, delivery and continuous improvement)
- O Development of people in terms of competence, polyvalence and leadership
- O Ensure proper execution of the production plan
- O Lean Implementation
- O Continuous improvements
- O Budget responsibility
- O HSE responsibility – ensure people are following the safety regulations
- O Competence & flexibility within area
72
Value Stream Manager Resume Examples & Samples
- Direct the business unit team in the preparation and implementation of operating plans and strategies consistent with agreed to business plan
- Plan the use of facilities, equipment, and personnel to meet current and future manufacturing requirements including department budgets and guidelines, plant layout and improvement, and capital and expenditure programs
- Drive Safety through the proper use of machines, tools and equipment, appraise technological developments, investigative, feasibility of new equipment and techniques, and prepare dependable cost estimates for changes in manufacturing methods
- Provide, implement, and administer quality assurance and engineering control functions to ensure product reliability and conformance to customer and federal specifications in the most effective and economical manner possible
- Bachelor's degree in Production Management, Business Administration, or Mechanical Engineering (or equivalent management experience
- Seven to ten years broad manufacturing experience
- Metal forming, welding and assembly experience
73
Value Stream Manager Resume Examples & Samples
- Co-ordinate and liaise with Quality Assurance, PPIC and Warehouse on material availability in order to minimize production disruption to meet ASP dates
- Co-ordinate and liaise with Engineering to ensure machine uptime is maximizing to meet agreed ASP dates
- To prepare the monthly production schedule and manpower requirement for the designated section. This is to be done in collaboration with Planners and Production Supervisors
- To monitor daily production output to ensure schedule adherence of 98%
- To be proactive in planning of production work when problems of not meeting the schedule arises
- Understand and prepare procedure relating to GQP for production
- Prepare implementation program based on QMS
- Put in place the measurement system to ensure compliance to GQP/GQG
- Prepare yearly self-assessment schedule to ensure compliance
- SOPs/MPCR Revision and daily checking of MPCR and other daily production records. To ensure 100% accuracy and documents are submitted on time
- To ensure that all safety policies and procedures are followed in the production department
- Assist in the Financial Planning Process I.e. Preparing 3/1 Plan and Annual Operating Budget
- Minimum tertiary education, B. Science, B. Management, B. Eng or any other related qualification
- Degree and Master Level in Manufacturing Management and equivalent will be an added advantage
- 3-4 years’ experience in production management/ production planning, manufacturing and people management
- Good GMP, SAP knowledge
- High standard of communication and writing skills
- Good leadership skills and drives in term of production, manufacturing and people development and management
- Possess good interpersonal, motivational and communication skills to allow effective liaison with internal and external parties
74
Value Stream Manager Resume Examples & Samples
- Deliver agreed to value stream results in the areas of safety, quality, customer service, costs and associate satisfaction/development
- Define and communicate performance targets for safety, quality, customer service, costs and associate satisfaction/development with Value Stream team. Hold team accountable to those targets
- Develop and implement plans to provide process improvement in key area defined above. Value stream improvement initiatives will be aligned with Lean Manufacturing principles and the manufacturing strategic plan
- Establish an environment conducive to high levels of morale, associates satisfaction, and performance
- Deliver performance to budget. Use participative approach in budgeting process
- Ensure alignment of activities and resources within the value stream, and ensure cross-organization collaboration and associate involvement where appropriate
- Acquire the appropriate people, technology, equipment and financial resources necessary to meet customer expectations and implement the business improvement plans
- Provide coaching, information, ideas, feedback and encouragement to associates and managers to promote the growth and development of the value stream team
- Support new process and product development and implementation
- Participate in negotiations with suppliers regarding issues that impact the value stream: prices, quality, customer service, etc
- Be highly visible to associates and create a safe environment for participation. Promote going to Gemba to solve problems and also promote hands-on, high involvement approaches to problem solving
- Four year degree or equivalent
- 3 - 5 years of supervisory or leadership experience
- Demonstrated knowledge of world-class (Lean, Safety, Quality, Manufacturing)
75
Value Stream Manager Resume Examples & Samples
- Leads departmental goal development and continuous improvement
- Executes human resource strategies by determining accountabilities; communicating and enforcing values, policies, and procedures; implementing recruitment, selection, orientation, training, coaching, counseling, disciplinary, and communication programs; planning, monitoring, appraising, and reviewing job contributions; reviewing compensation strategies
- Maximizes production by developing production schedules, organizing change-overs, and developing and scheduling preventive maintenance
- Keeps materials available by scheduling, monitoring, and adjusting deliveries and insures inventory transactions and accuracy are maintained
- Delivers customer-acceptable products by enforcing quality standards and maintaining good manufacturing practices (GMP)
- Improves quality production results by studying, evaluating, and re-designing processes, and implementing changes
- Prepares plant information and reports by collecting, analyzing, and summarizing data and trends
76
Value Stream Manager Resume Examples & Samples
- Manage the manufacturing departments with the appropriate communication or goals, performance feedback, corrective action, and rewards and recognition to provide optimum employee relations
- Identify and record any problems relating to product, process and quality systems. Initiate, recommend or provide solutions through designated channels
- Verify the implementation of solutions for all abnormalities using the TMS philosophy
- Control further processing, delivery or installation of nonconforming product until the deficiency or unsatisfactory condition has been corrected
- Define, document, maintain and continuously improve, if required, the plant’s quality policy relevant to the plant’s goals and expectations and the needs of its customers
- Be responsible for preparation, publication, distribution, and maintenance of the quality management system
- Be responsible for coordinating the requirements of the quality management system with the customers’ quality requirements
- Be responsible for implementing and maintaining a system, which identifies and records any problems relating to Safety, the Product, Process or Quality Management System
- Have the authority and responsibility to ensure that processes / machinery utilized in the manufacturing process and the verification process are capable of meeting both customer and quality plan expectations as well as Safety lockout/Tagout (LOTO) requirements
- Have the authority and responsibility to ensure customer product requirements are maintained as scheduled
- Have the responsibility to ensure environmental polices and procedures shall be followed
- Bachelor's Degree required in management or engineering
- Minimum 5 years experience leading salaried individuals and 100+ team members
- Commitment to EH&S and Quality with working knowledge of creating a culture and improving performance in these areas
- General understanding of all responsible areas, functions and their duties
- Automotive experience building exhaust systems for OEM
- Knowledge of metal forming, welding, and assembly
77
Value Stream Manager Resume Examples & Samples
- Formulates Value Stream business plans, goals, and objectives. Ensures that organization standards are met. Develops refinements to plan on a continuing basis to meet strategic objectives
- Supervises the Value Stream to ensure high level of productivity and quality. Ensures that staff works as a team. Leads by example, communicates information and provides training on new procedures. Determines performance expectations, evaluates performance and provides coaching and training opportunities. Handles employee issues in a timely way. Directs work of Team Leaders
- Prioritizes work. Maintains appropriate staffing level. Maintains workflow and balance, tracks and monitors work. Ensures that productivity and quality standards and measures are met for product line. Communicates information to appropriate departments and individuals. Provides reports. Manages expenses
- Implements Lean manufacturing processes to achieve company goals in cost, product flow, throughput, productivity, quality and delivery. Responsible for Value Stream performance, measurements, capacity planning and performance matrices
- Works with all Kamatics departments to meet strategic goals and objectives. Resolves Value Stream problems and performance issues
- Ensures that work environment is clean, safe and that safety, health and environmental procedures and regulations are followed
- Provides a high level of service to all internal and external customers. Contributes to positive teamwork environment
- Performs other duties as assigned. Accomplishes related results as needed
- Initaitive
- Organization
- Results Oritented
- Team Orientted
- Blueprint reading
78
Assistant Value Stream Manager Resume Examples & Samples
- Develop and mentor leaders
- Prioritization of workload to sustain on time shipment of customer emergencies
- Recommend changes, assist in continuous improvement initiatives for warehousing processes and implement new systems/processes
- Communicate and maintain a culture of open relationships with associates
- Assist coaches in answering associate concerns/complaints. Identify and implement staffing levels for assignment completion
- Participate in recruiting and screening applicants
- Ensure employees are thoroughly trained in processes and business practices/policies
- Support purchases of indirect material suppliers and capital items required for daily operations
- Assume responsibility for operations in absence of manager
- Provide leadership to a range of initiatives across departmental lines
- Operational updates, written and oral reports and operations summaries
- 4 year college degree completed or in progress
- Previous experience in all aspects of warehouse operations
- Previous staff and supervisory experience
- Previous experience with SAP/EWM
- Completed 4 year college degree
- Communication and analytical skills
- Demonstrated ability to modify style to support empowered associate teams
79
Value Stream Manager Resume Examples & Samples
- Drive rapid, significant and sustainable improvement in on-time delivery and lead-time
- Develop and execute a manufacturing strategy that supports the division’s overall market-driven business strategy. Specifically, lead expansion of highly successful point of impact manufacturing and delivery models
- Lead regular strategy deployment & KPI reviews for the manufacturing team ensuring attainment of results and a sense of urgency with respect to the strategic implementation priorities
- Passionately drive continuous improvement culture while implementing the strategic Roadmap to achieve breakthrough performance in working capital, quality, delivery, cost, and growth
- Build an outstanding team and evolve the organizational structure, as needed, in order to meet and exceed objectives
- Ensure key manufacturing metrics and key performance indicator systems are consistently tracking the appropriate measures and driving appropriate response behaviors
- Periodically present plans and actual results, as well as strategy deployment and KPI progress. Take aggressive action to drive financial performance in the areas of direct and indirect labor, manufacturing overhead cost, and inventory levels
- Partner with Director of Operations to coordinate manufacturing functions with sales, marketing, design engineering, and other departments
- Ensure effective allocation of resources across all areas of the operation to accomplish customer-driven priorities
- Partner with Management to ensure the best possible product and customer satisfaction
- Play an active and significant role in the S&OP process
- Continually benchmark best practices and implement as appropriate
- Bachelor’s degree in Business, Engineering or related field required. Master’s degree preferred
- 5–10 years operations leadership experience with a demonstrated track record of significant performance improvement required
- Experience in lean culture development and lean tool implementation required
- Manufacturing experience in metal fabrication, finishing/machining, and assembly preferred
- Highly customer responsive
- Resourceful, combining strong manufacturing and technical abilities with overall management acumen
- Ability to effectively deploy resources to key priorities
- Sets high expectations (driven by metrics and countermeasures) for self and the organization
- Ability and passion to rapidly learn and utilize the business system and achieve objectives
- Strong communication skills, both verbal and written, and the ability to effectively communicate throughout all levels of the organization
- Autonomous and self-directed
80
Value Stream Manager Aftermarket Resume Examples & Samples
- Maintaining the Value Stream's production schedule relative to incoming sales orders, sales order changes, component availability changes and cancellations
- Directing the activity of all Value Stream personnel; to maintain a smooth flow of work; to achieve customer delivery dates; to support Company profitability
- Monitors discretionary and operation budget with specified guidelines
- Works in accordance with Quality System (Quality Policy and Quality Procedure) to meet customer requirements and eliminate non-conforming products and services
81
Value Stream Manager Resume Examples & Samples
- Lead DMAIC Projects from identification through control phase
- Mentor DMAIC Projects led by others with less experience managing projects and/or less experience with lean and six sigma tools and thought processes
- Facilitate project identification and prioritization efforts with different departments and across the entire site
- Efficiently and accurately analyze all types of data (There are two MBBs within the organization that will support in this need)
- Efficiently and accurately summarize and communicate all types of data to all levels of the organization, including recommendations of the path forward
- Coordinate and/or lead a select few projects across all three US sites
- Actively participate and coach managers during weekly site metrics meetings
- Build strong, positive working relationships with all functional areas
- Perform follow-up, ensuring proper progress and shared ownership of delivered results
- BA/BS in engineering or related experience with 5-10 years’ experience, including one year managing projects
- Lean Six Sigma experience required
- Black Belt Certification from a reputable organization, achieved through multiple project successes a plus
- Excellent written and verbal communication skills, including the ability to interface with clients, corporate staff and other contacts
- Ability to formally present complex rationales, strategies or processes in a simple and succinct manner at all levels of the organization
- Able to analyze and interpret data to guide teams to solid technical solutions, including corrective actions to quality audit findings
- Experience with working cooperatively in teams
- Skills in change management, scheduling, and communicating time sensitive tasks
- Experience and competency in electronic data management systems
- Ability to accomplish daily tasks through the use of appropriate computer equipment and software, including proficiency in Minitab, Microsoft Excel, Word and Power Point
- Experience managing small, medium, and large projects
- Experience at multiple facilities or business types a plus
- Experience teaching project management or other materials to professionals a plus
- Experience in a regulated industry a plus
82
Value Stream Manager Resume Examples & Samples
- Build a strong team with focus on performance within the Portable Gas (RAE) portfolio in the El Paso and Sunnyvale locations. The VSM role will drive conformance and improvement for the ISC and business KPI’s with the SPS/HBT team in El Paso and the SPS team in Sunnyvale
- Develop strong liaison with cross-functional groups within a matrix organization: Sourcing, Materials Planning, SIOP, Distribution, Health, Safety and Environment (HSE), Human Resources, HBT, and Finance
- Drive Honeywell Operating System within the VSM to align to the HBT site and HIS Gas business expectations and timing. Formulate and implement process improvements using lean practices and Six Sigma tools
- Establish and improve robust manufacturing processes for all products to ensure repeatability and built-in-quality (BIQ)
- Demonstrate leadership behaviors core to HOS
- Participate in the Annual Operating Plan (AOP) process, metrics improvement, and STRAP planning
- Responsible to identify and drive Factory Productivity projects and other cost-out initiatives
- Ensure appropriate communications within the value stream to understand strategy, goals and actions necessary to achieve them
- Define and communicate roles and responsibilities as required to respond to customer needs
- Make staffing recommendations in order to support profitable growth
- Responsible for coordinating and initiating development activities (NPI) in response to emerging business needs
- Work directly with program managers to ensure that development schedules are appropriate to requirements on timing and budget
- Provide for the personal and professional development within the VSM to meet the current and future challenges of the business
- This position will require a maximum of 10-20% travel
- Direct reports will include Manufacturing Engineers, Quality Engineer, and Material Planner all located in El Paso and a Supervisor in Sunnyvale CA
- Bachelor Degree in Engineering, Operations Management or other technically related field
- 10 years of progressive management experience
- Manufacturing or VSM leadership experience is a plus
- Broad knowledge of lean manufacturing and six sigma principles, along with sound manufacturing and operations experiences
- SAP experience and preference for a Super User
- Extensive experience in application of Design for Six Sigma (DFSS) and Lean Enterprise methodologies
- Ability to lead change and establish operational metrics/key indicators for process control, communication and performance improvement
- Ability to manage multiple, complex projects and changing priorities, make sound decisions and work effectively in a highly technical, team environment
- Cross-functional experience in operations and at least one other functional area
- Ability and experience working in the Electronics industry
83
Value Stream Manager Resume Examples & Samples
- Train and facilitate kaizens in all areas to support safety, Quality, Delivery, and Coast growth objectives
- Champion FBS (lean) continuous improvement initiatives involving all associates in FBS
- Lead lean manufacturing efforts focusing on standard work efficiency and improving internal and external quality
- Support management in creating strategic breakthrough objectives and action plans
- Lead team to develop strong Root Cause Counter Measure plans and leverage FBS (lean) tool kit to solve problems
- Provide leadership to insure cells are level loaded and results are sustained
- Improve standard work efficiency. Champion direct and Indirect labor productivity goals
- Implement the strategy to obtain the established company goals
- Manage all aspects of operations-quality, productivity, safety, budget, training, personnel (safety, attendance, discipline, vacation, performance reviews), maintenance (repairs and preventive maintenance)
- Provide leadership for cell leaders and manufacturing associates in business unit
- Coordinate with sister companies and with company personnel internally on OTD and pull in’s to meet monthly shipment goals
- Bachelor's Degree preferably in Engineering, Supply Chain or related
- Five + years of related experience in manufacturing, operations, continuous improvement, or other related experience
- Creative and progressive thinker with excellent interpersonal skills able to communicate with others at all levels in written or verbal form
- Ability to analyze problems, propose solutions, test theories, research alternatives and reach conclusions
- Organized with the ability to prioritize activities to achieve short and long term goals and objectives
- Flexible and adaptive approach to change
- Team player who is able to build partnerships while leading cross functional teams
84
Value Stream Manager Resume Examples & Samples
- Lead one of 2 Value Steams with direct Supervisory and Production employee reports, and indirectly influence cross-functional team members to achieve shared business goals
- Manage a team of Supervisors and guide them through Eaton’s coaching and Front Line Leader behavioral model
- Facilitate assembly and component manufacture schedules in a Department (sub-value Stream) by leading a production team comprised of skilled Leads, Technicians, Machinists and Assemblers
- Coordinate Value Stream budgeting, forecasting, staffing, and overtime levels to achieve productivity and financial results
- Act as plant champion for Eaton Lean management competencies/systems including support for key supervisory influenced elements (Standard Work or 5S)
- Follow Supervisor’s Standard Work process and ensure all reports are following their Standardized Work processes. These actions will encompass approximately 50% of the workday
- Maintain a high level of morale through positive employee relations, and drive for a culture of continuous improvement. Lead by example
- Establish and monitor goals, provide performance feedback, establish development plans and provide coaching to direct reports or cross functional support members
- Maintain effective communication with other shifts, departments and management. Ensure cross functional sharing of resources to meet plant goals
- Leverage the Eaton Business Systems (EBS) values, tools and practices in order to drive performance excellence. Work with Operations Excellence partners (Lean, Quality, and Safety) to achieve continuous improvement results and foster a continuous improvement culture
- Review safety procedures and ensure safe working conditions to minimize employee risk to injury. Drive towards a zero incident safety culture
- Maintain accurate inventory levels and keep the transaction accuracy within compliance to accounting policy
- Minimum of 3 years of experience in a manufacturing/operations environment
- Minimum of 1 year of supervisory experience
- Master’s degree in Business or Engineering
- Prior experience in manufacturing assembly and test, machining, and CNC equipment
- Prior experience communicating with the manufacturing employees, Engineering, Quality, and Schedulers to ensure production commitments are met
- Prior experience working directly with operations metrics in a manufacturing environment and resolving customer problems
- 4+ years of supervisory experience
- Experience with leading Lean improvements
- Lean/Six Sigma Certification
85
Ducting Value Stream Manager Resume Examples & Samples
- Responsible for ensuring overall responsibility for leading a manufacturing team in achieving quality, cost, delivery and employee safety goals
- Deployment of MESH to support a Zero Incident Culture
- Plan and monitor key metrics to ensure quality, cost, delivery and safety requirements are met
- Ensure required documentation and/or system transactions are executed to meet customer, manufacturing system and financial reporting requirements
- Co-ordinate manufacturing schedules and priorities within the production plan to satisfy customer requirements
- Control in-process inventory to achieve production requirements with minimum impact on inventory levels. Direct application of capital and people resources to maximize operating efficiency
- Facilitate problem-solving and corrective action for production issues
- Provide leadership to employees to ensure customer requirements are satisfied
- Champion a Safety Culture through using MESH tools, safety best practices, and empowering all employees to take responsibility for their own safety as well as the safety of everyone they work with. Ensures that environmental health and safety issues are addressed considering local regulations, Eaton policy, and good corporate citizenship
- Provide leadership in commitment in strategic use of Eaton Business System practices, personally leading the use and documentation of MESH,CIF, EQS, ProLaunch, and Tier/BSC processes with focus on performance of the entire value stream. Keep focus on meeting customer needs, both internal and external (Customer Centric Focus / KBKC) through leading and lagging measures
- Responsible for analysis and presentation of operational performance metrics and action plans to both Eaton senior leadership and customers
- Responsible for building the organizational capability of the High Performance Work Teams through coaching, mentoring, and training of the Team Leads and Team Members. Utilizes the APEX process to manage performance of the High Performance Work Teams
- Coordinates and assists with business initiatives to drive best practices across the enterprise. Champions process design and compliance to AS9100, NADCAP, EBS, and Customer Quality Systems requirements
- Minimum 5 years of experience in Operations/Manufacturing
- Minimum 3 years of leadership experience in a manager of people role
- Candidate must be legally authorized to work in United States without company sponsorship
- Master’s Degree in Business Administration from an accredited institution
- Understanding of Quality Management Systems
- Demonstrated experience in the application of Lean Management Systems/Tools and Continuous Improvement Framework (CIF) and methodologies, including structured problem solving concepts/tools
- Knowledge of ERP systems, including MRP logic and transactions
- Ability to lead and direct cross-functional teams
- Thorough understanding of manufacturing technologies and processes
86
Value Stream Manager Resume Examples & Samples
- Provide leadership to ensure sustainment continuous improvement initiatives in production processes
- Drive safety and environmental compliance initiatives throughout the facility
- Lead lean manufacturing efforts as a Subject Matter Expert, focusing on standard work efficiency and improving internal and external quality through audits and kaizen; drive overall process improvements
- Work closely with Sales and Customer Service for production planning to ensure customer satisfaction
- Lead teams in meeting production line objectives through the use of the Danaher Business System (DBS) tools, such as driving the use of Root Cause Counter Measures (RCCM) to hit key performance metrics– Safety, Quality, Delivery, Inventory, Productivity (SQDIP)
- Monitor weekly and daily build plans to maintain >95% fill rate to customer request
- Work with the Wood Dale Materials team to maximize the effectiveness of Kanban systems and improve inventory turns year over year
- Support and sustain Quality systems while engaging the Quality/Manufacturing engineering team for support
- Aid in developing and monitoring monthly operating budgets
- Ensure area associates are cross-trained to maximize operation flexibility
- Drive talent management initiatives throughout the facility: evaluate associate performance and conduct performance review; recommend hiring and termination decisions; coach, train, and counsel associates to improve performance
- Execute on yearly plan to increase associate engagement
87
Value Stream Manager Resume Examples & Samples
- Accountable for all operational results (Safety, Inventory, Quality, Cost, and Delivery) across the value stream defined from raw material reception through finished goods shipment
- Accountable for reporting and delivering to all KPI’s which drive the operation to continuously improve, ensuring the Team Leaders (TL) maintain all key KPI data & visual management boards
- Define and deliver Continuous Improvement Plans for the value stream from future state maps. Prioritise and task manage value stream support team to perform against KPI’s and budget
- Accountable for contact between the value stream and all external stakeholders in the production process (shared resource manager, sub-contractors, external logistics personnel) in terms of delivery performance, quality issues, and flow between the facilities
- Through the TLs, ensure that all employees are fully conversant and compliant with the Company’s Health and Safety policies. Ensure that all relevant Health and Safety legislation is effectively implemented and managed
- Support Operations Manager and General Manager in all business aspects
- Manage inventory in line with budget and WIP targets
- Champion capital expenditures for value stream, escalate out of control conditions, and implement recovery plan as needed
- Accountable for all communication with Team Leaders, Value Stream support staff, and relevant operations personnel
- Accountable for the operational and organisational management of the team ensuring that all Value Stream KPI objectives are achieved
88
Value Stream Manager Resume Examples & Samples
- Hires, develops, maintains and supervises heat treat personnel, including
- Interviews and selects individuals to fill existing position requirements
- Organizes, assigns and coordinates daily workload to priorities set by Production Control to meet production schedules. Coordinates with production control on incoming parts and completion times required
- Verifies employee hours worked daily maintaining attendance records
- Provides technical knowledge and expertise to resolve problems in work areas. Interfaces with Engineering, other supervisors, support groups, and employees, assuring smooth product flow. Typically serves as primary facilitator for root cause determination and cause & corrective actions
- Supports company inventory management goals
- Requests order of new tools and necessary hardware to support job requirements
- Prepares capital expenditure requests complete with justification and financial payback analysis
- Prepares work areas for company and/or customer on-site audits
- Reviews planning changes with Manufacturing Engineers, as required, and evaluate and trains employees on changes
- Responsible for material flow in their areas. Sets shift job priorities
89
Value Stream Manager Resume Examples & Samples
- Manage manufacturing functions for assigned departments to achieve safety, quality, delivery, cost and inventory goals
- Implement and support Zero Incident Safety Culture efforts
- Communicate company policies, procedures, and guidelines and ensure they are consistently practiced
- Champion use of Eaton Business Systems and tools to ensure appropriate execution within assigned areas. Engage direct reports in manufacturing LEAN initiatives including but not limited to operator standard work, 5S, pull systems, and structured problem solving. Foster an environment that promotes Eaton’s goals, philosophies, and encourages continuous improvement
- Measure and monitor departments’ safety, quality, on-time delivery and productivity; facilitate corrective actions as appropriate
- Determine and control staffing and expense levels necessary to support production requirements at or better than Profit Plan productivity and customer service goals
- Ensure maintenance of manufacturing skills and manufacturing methods required for continued production of quality products
- Identify new capital requirements to achieve Profit Plan goals
- Assist the Operations Manager in annual budgeting process
- Assist the Operations Manager in developing one and five year operating plans
- Ensure raw materials and indirect materials are available and of quality adherent to Eaton Crouse-Hinds standards
- Maintain, in accordance with Eaton Crouse-Hinds policy, records and data on materials, processes and products to provide meaningful information on quality results and product liability
- Maintain and verify accurate physical inventories
- Minimum 4 years of experience in Manufacturing Operations or Engineering in a manufacturing environment
- Must be legally authorized to work in the United States without company sponsorship now and in the future
- No relocation provided. Only candidates residing within the immediate area (50 miles radius) will be considered for this position
- Minimum 1 year of direct supervisory experience in a manufacturing environment
- Minimum 4 years of direct supervisory experience in a manufacturing environment
- Experience with Enterprise Resource Planning (ERP) and Material Resource Planning (MRP) systems; SAP preferred
- Six Sigma/LEAN experience or certification
- Experience working in a union environment
- Working knowledge and experience with computers, specifically Microsoft Office
- Ability to walk frequently
- Ability to successfully interface with all organizational levels & departments
- Must apply knowledge of manufacturing processes and systems and engineering processes
- Good understanding and positive support of standard personnel and administrative policies, practices and legal requirements pertaining to business operations
- Demonstrated ability to build trust and credibility, provide ongoing coaching and feedback, manage through conflict, and strive for continuous improvement
- Willingness and availability to work weekends as needed
90
Value Stream Manager Resume Examples & Samples
- Prior management and/or team lead experience
- Must consistently leverage exceptional organizational abilities, superior follow-through and detail orientation to deliver results
- Natural strength and passion for turning analytic insights into high-impact actionable strategies with proven results
- Maintain big picture perspective - understand where the company is headed and anticipate future demands
- Communicate effectively to build and maintain strong, collaborative working relationships and influence across organizational boundaries to create mutually beneficial wins for Catalina and our clients
- Results oriented and able to execute with agility
- Capable of managing multiple projects and deadlines
- Experience with applying Lean-Six Sigma methodologies and/or LSS certification
91
Value Stream Manager Resume Examples & Samples
- 10+ years’ of experience in operations, supply chain or program management required
- Strong ability in decision making, business judgment and delivering results required
- Experience in a procurement and/or manufacturing environment required
- Demonstrated strong communication, interpersonal, and organizational skills required
- Leadership and/or supervisory experience preferred
92
Value Stream Manager Resume Examples & Samples
- Responsible for manufacturing of acrylic, glass and/or composite transparencies that conform to contractual and operating unit requirements
- Reviews and maintains overall budgets, schedules and performance standards
- Responsible for the analysis, evaluation and solution to production problems encountered in the application of manufacturing methods, facilities, processes, material and tooling incident to the fabrication and assembly of products
- Ensures implementation and maintenance of a cost effective work measurement program
- Promotes and supports continuous improvement efforts in both manufacturing and transactional processes
- Ensures full compliance with all safety and environmental regulations and policies
- BS degree in engineering/manufacturing technology
- 7-10 years experience in aerospace manufacturing
- Demonstrated managerial level leadership to include team building
- Lean/Continuous Improvement knowledge with industry application
- Understanding of MRP systems and production and capacity planning
- Computer literate: Word, Excel, Project
- Interpersonal skills to communicate effectively with all levels of management and individual contributors
- U.S. Citizenship
93
Value Stream Manager Resume Examples & Samples
- Ensures that the value stream organization, (staffing, tooling, and machinery) is able to meet customer demand
- Works as a change agent to drive out waste in the manufacturing and supply chain organizations through the deployment of Lean methodology
- Creates a culture of continuous improvement by involving employees in waste identification and problem solving, as well as recognizing them for exceptional work
- Develops operational and financial plan and forecasts for the value stream
- Ensures that inventory levels are right-sized to meet customer demand
- Leads the day-to-day production activities within the value stream(s) to ensure that current commitments and goals are achieved while improvements are being made
- Tracks daily performance. Verifies lead counter measures and recovery plans are in place for missed targets. Ensures process center communication boards and visual management techniques are being used on a daily basis
- Ensures the highest quality standards are maintained. Provides coaching, information, ideas, feedback and encouragement to personnel
- Assures a clean and safe working environment for all employees, maintaining 5S standards and emphasizing prevention of potential hazardous conditions. Addresses unsafe acts and unsafe conditions. Conducts safety training for employees. Reports incidents in a timely manner and participates in incident investigations as required
- Performance evaluations, A-3’s, interactions and disciplinary process, staffing and scheduling
- 3-5 years of experience in operations environment (supply chain management, production, distribution management, production/distribution flow design and optimization, Lean projects)
- Lean experience/certification
94
Value Stream Manager Resume Examples & Samples
- Minimum of 3 years in a Manufacturing or Operations environment
- Minimum of 1 year of supervisory experience in a Manufacturing or Operations environment
- B.S. Degree in Business, Manufacturing, Engineering is preferred
- Working knowledge of production processes, lean manufacturing and quality control techniques, 5S, Six Sigma, and Quality systems (e.g. QS 9000, ISO 14001, ISO-9001, AS9100) preferred
- Prior Machining experience is a plus
- Ability to hold a team accountable to goals and KPIs