Manufacturing Supervisor Resume Samples
4.8
(138 votes) for
Manufacturing Supervisor Resume Samples
The Guide To Resume Tailoring
Guide the recruiter to the conclusion that you are the best candidate for the manufacturing supervisor job. It’s actually very simple. Tailor your resume by picking relevant responsibilities from the examples below and then add your accomplishments. This way, you can position yourself in the best way to get hired.
Craft your perfect resume by picking job responsibilities written by professional recruiters
Pick from the thousands of curated job responsibilities used by the leading companies
Tailor your resume & cover letter with wording that best fits for each job you apply
Resume Builder
Create a Resume in Minutes with Professional Resume Templates
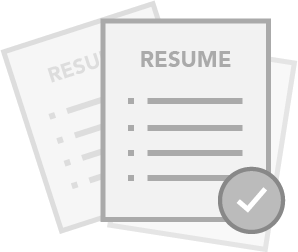
CHOOSE THE BEST TEMPLATE
- Choose from 15 Leading Templates. No need to think about design details.
USE PRE-WRITTEN BULLET POINTS
- Select from thousands of pre-written bullet points.
SAVE YOUR DOCUMENTS IN PDF FILES
- Instantly download in PDF format or share a custom link.
EF
E Feeney
Eveline
Feeney
470 Stefanie Islands
Boston
MA
+1 (555) 654 9540
470 Stefanie Islands
Boston
MA
Phone
p
+1 (555) 654 9540
Experience
Experience
Boston, MA
Manufacturing Supervisor
Boston, MA
Wiegand, Feeney and Wilkinson
Boston, MA
Manufacturing Supervisor
- Provide general people organization & management activities; Provide Product Quality Management; Provide Product Delivery Management
- Develop a high performance work team with high levels of worker morale, satisfaction, and performance
- Follow established safety, quality and production improvement goals. Monitor visual workplace 5S principles. Provide a safe workplace for all employees
- Work with other managers and operators to establish improved processes
- Executes and manage the Performance Management process for all direct report employees
- Lead, train and develop direct reports by providing challenging tasks and assignments; provide developmental feedback
- Effectively distributes work, evaluates performance, provides performance feedback, and assesses and selects candidates
Dallas, TX
Manufacturing Supervisor, nd Shift
Dallas, TX
Ledner, Brekke and Beer
Dallas, TX
Manufacturing Supervisor, nd Shift
- Perform daily crew assignments, supervise the job performance of milling operators and provide regular feedback and support
- Plan milling operations, establish priorities, sequences and prepare schedules for milling work
- By example, show a commitment to employee involvement, participative management and continuous improvement
- Provide operational input and guidance to technical staff for new product development
- Manage the performance of 20 or more non-exempt team members to include
- Perform quality control testing on in-process materials to determine performance to standards
- Manage resources within given area of responsibility to ensure staffing and equipment readiness levels match business activity levels
present
Boston, MA
Senior Manufacturing Supervisor
Boston, MA
Weimann, Raynor and Hodkiewicz
present
Boston, MA
Senior Manufacturing Supervisor
present
- Select, train, develop, retain, recognize, and manage associates in group in line with Ecolab standards
- Create an environment in which employees can work safely. Implements Safety Management System
- Provides formal and informal reporting on plant performance and issues
- Generates and implements ideas that improve performance indicators, in line with safety, cost, investment and service goals. Implements Lean concepts and practices
- Assists with setting the annual budget with focus on reduction of year over year costs
- Manages the daily manufacturing operations of the plant to ensure that the manufacturing plan is executed in a manner that meets or exceeds safety, quality and cost objectives
- Ensures that Quality system is followed. Ensures that products produced meet specifications
Education
Education
Bachelor’s Degree in Engineering
Bachelor’s Degree in Engineering
Carnegie Mellon University
Bachelor’s Degree in Engineering
Skills
Skills
- Basic knowledge of Lean manufacturing, Quality Control and Production Control
- Basic knowledge of Lean Manufacturing, Quality Control and Production Control
- Self-starter with strong work ethic and the ability to exercise good judgment
- Ability to work in an unstructured environment with the ability to make tradeoff decisions quickly
- Proficient and knowledgeable in the operation and complex troubleshooting of multiple manufacturing area’s
- Knowledge of basic manufacturing, quality and safety practices
- Proficient and knowledgeable in the operation and complex troubleshooting of multiple manufacturing areas
- Highly organized with good communication skills (verbal and written) and able to efficiently organize and complete daily activities
- Basic mathematical understanding and ability (add, subtract, divide units of measurement)
- Highly motivated self-starter, capable of self-management with little to no oversight
15 Manufacturing Supervisor resume templates
Read our complete resume writing guides
1
Manufacturing Supervisor Resume Examples & Samples
- Balance staff in accordance to production schedule each day to meet production volume goals
- Ensure QC standards are acheived
- Verify methods are accurate and followed
- Verify production meets manufacturing specs
- Assist in any other manufacturing department where needed to meet goals
2
Manufacturing Supervisor Resume Examples & Samples
- Minimum 1 year of manufacturing supervisory experience, good to have project management experience
- Possess Diploma qualification
- Have intermediate knowledge of Microsoft office
- Strong knowledge of factory floor, material or warehouse management systems and Microsoft Office suite
- Strong communication skills (e.g. written, verbal, presentation); mastery in English and local language
- Knowledgeable of country specific legislative and regulatory compliance (e.g., import and export regulations; trade restrictions, EH&S). Utilizes the expertise of others as necessary
- Good qualitative and quantitative analytics and data modelling skills
- Good people management skills
- Partnering skills (e.g. improving the day-to-day performance of internal and/or 3rd party partners)
- Familiarity with Lean Sigma or Quality Improvement methodologies
3
Manufacturing Supervisor Resume Examples & Samples
- Reviews production schedules to ascertain product quantities, specifications and scheduled delivery dates in order to plan department operations; Summarizes data for daily, weekly and/or monthly reports
- Coordinates with Production Control to ensure parts/raw material availability matches production schedules
- Reviews production and operating reports and resolves operational, processing, manufacturing and maintenance problems
- Reviews all production documentation for accuracy and completeness
- Ensures preventive maintenance occurs on machines/equipment to ensure specific operational performance and optimum utilization; Reports machine and equipment malfunctions to maintenance, calibration and/or engineering personnel
- Reviews, edits and approves Kronos time-keeping reports on a daily and weekly basis
- Coordinates process (line flow) changes and daily modifications needed to meet specified production levels and continuously improve efficiency rates
- Routes vendor quality issues to proper representatives. Interacts with QC and/or QA Reliability on defects and/or countermeasures
- Works with QC staff on part changes, part problems, deletions and additions
- Coordinates meetings with subordinates and attends required meetings and conferences
- Keeps management informed on any changes, such as part problems, inspection criterion or improvements to processes
- Evaluates current procedures and practices for accomplishing the activities and functions of the department in order to develop and implement alternate methods designed for the improvement of work. Seeks out, generates and recommends/implements profit-making and/or cost-saving ideas
- Assigns or delegates responsibility for specific projects, tasks or assignments; Gives work directions, resolves problems, prepares work schedules, establishes objectives and sets deadlines to ensure completion of operational functions
- Coordinates activities of department with interrelated activities of other departments
- Counsels and advises subordinates concerning performance. Coordinates or conducts training of members to improve performance and acquaint members with company policies and procedures. Maintains training records
- Initiates and/or recommends personnel actions such as hires, promotions, transfers, discharges and corrective or disciplinary measures; Interacts with HR/ER Department to report personnel problems and project manpower needs
- Using Manager’s goals, establishes team/cell operation visual display boards and uses to track progress
- Coordinates Production Innovation related activities of subordinates, including training, encouraging SPEED projects and motivating employees to participate in Production Innovation activities
- Ensures compliance with all safety regulations and ISO standards; Develops or revises standard operational and working practices and observes workers to ensure compliance with standards
- Any combination of education and experience equivalent to an Associates degree and 4-6 years manufacturing experience with 1-3 years experience in a lead or supervisory position
- Strong interpersonal and communication (written and verbal) skills
- Strong mechanical aptitude desired
- Good leadership and project management skills
- May have to work overtime and may be assigned to other shifts based on company needs
4
Manufacturing Supervisor Resume Examples & Samples
- Experience in a production plant supervisory position in the Chemical Industry
- Experience in implementing & using continuous improvement tools and techniques
- Experience supervising plant preventive maintenance programmes & implementing SHE policies & procedures
- Good Communication, Reporting, Presentation and analytical skills
- This includes attendance, performance appraisal & role function management. Developing training plans for the manufacturing personnel. Recruitment & probation management. Supervise & support the day to day tasks of the manufacturing department
- Achievement of Production plan set out in the Master Production Scheduling planning systems
- Establish key performance indicators. Provide feedback & reports to the manufacturing department & other key personnel. Use continuous improvement tools to instigate actions for improvements. This includes feedback from Quality, Customer Service, Environmental & H&S audits
- Drive process improvements to impact costs and improve competitive advantage, using key tools and techniques to enable success
- Implement a Total Productive Maintenance program to improve plant and tool availability and support H&S improvement targets
- Supervise the accurate storage, usage and clear down of raw materials and packaging used in the production process. Maintains inventory accuracy by conducting organized cycle counts as required
- Introduce a Clear down procedure & Analysis of Production Route cards & Reports, introducing improvement projects from findings
- Actively manage the requirements of the Health & Safety & environmental policy within the manufacturing department
- Develop, integrate & use all of our IT structures to strengthen our business intelligence & communication
- Ensure within the manufacturing department that the essence, integrity & growth of our brand is delivered in line with the brand strategy
- Work in a multi-disciplinary team of people to manage the process of integrating new products or procedures arising from the acquisition of new business
5
Manufacturing Supervisor, Aerostructures Resume Examples & Samples
- Responsible for transition of work requirements between shifts
- Manage and approve employee(s) timekeeping in SAP
- Participate in meeting throughout the day, occassionally working outside of the typical house to help ensure goals are met
- Responsible for continuous improvement initiatives while ensuring standard work and environment, health and safety (EH&S) requirements are met
- Comply with all company ethics policies, principles, and practices
- Quality
6
Manufacturing Supervisor Resume Examples & Samples
- Achieve daily attainment requirements
- Maintain and update training matrices
- Record downtime, scraps, and determine team efficiency
- Understand and administer HR policies
- Coach and counsel employees with performance concerns
- Independently administer corrective actions through the written level
- Approve all vacation and appointment time requests
- Document and deliver employee performance appraisals as issued
- Determine allocation of overtime, submit requests for OT approval
- Assign employees to work cells/machines daily
- Ensure cross training for your area of responsibility
- Maintain 5S checklist and ensure 5S performance
- Perform LPA’s
- Maintain Kanban cards, make replacements, and enforce their use
- Perform pre-shift meetings
- Complete their portion of incident/accident reports
- Understand your responsibility to the environmental programs, including ISO14001. Understand the importance of conformance with all environmental procedures of the environmental management system, including emergency response. Understand the EMS consequences, actual or potential, of their work activities and/or their behaviors from specified work instructions
- Associate's degree (A. A.) or equivalent from two-year college or technical school, preferred
- 3-5 years supervisory experience in high volume production, preferably assembly, is recommended
- Must have the ability and willingness to continue personal development activities/assignments
- Must demonstrate mechanical aptitude by performing minor machine adjustment and setup
- Capable of learning and performing all team jobs
- Must support safety policies and practices that apply to assigned areas
- Strong interpersonal skills and ability to effectively interact with people
- Demonstrate the ability to lead and develop others to achieve daily goals
- Must be able to communicate effectively (written and verbal)
- Must be self-motivated and have the ability to interpret data for corrective actions
- Demonstrate positive performance record and strong dependability with a proven attendance record
- Ability to obtain lift truck license
- Demonstrate positive performance record-individuals in Corrective Action steps may be ineligible
- Successful completion of the Team Facilitator Promotion Training may be required after positions are filled
7
Manufacturing Supervisor, nd Shift MRO Resume Examples & Samples
- Develop and implement employee training plans within and across manufacturing team
- Utilize problem solving techniques, teamwork building strategies, process control, and continuous process improvement tools to meet or exceed the plant metrics
- Ensure team compliance to Quality Management System. Identify opportunities for improvement and create action items for gap closure
- Provide manufacturing information by compiling, initiating, sorting, and analyzing production performance records and data to meet On Time Delivery, Turn Around Time, Cost of Poor Quality, etc.; answering questions and responding to requests
- Support and follow all rules/guidelines/standards set by EHS, Quality, and CI functions as set by the leader and position
- All other duties assigned including working extended shifts/overtime as required by the business
8
Manufacturing Supervisor Resume Examples & Samples
- High school diploma plus 3-5 years of related supervisory experience. A college degree is preferred
- Experience in shoe-making processes or similar manufacturing processes
- Demonstrated ability to manage and motivate a team structured workforce
- Strong planning, prioritizing, and organizing skills necessary. Must be able to multitask and manage multiple projects at once
- Desire to learn and practice TPS principles
- Computer proficiency, especially Word and Excel
9
Manufacturing Supervisor Resume Examples & Samples
- Proactively review all safety and health potential issues in areas of responsibility. Maintain a
- Assist with the development of the capacity plan to meet the needs of the business. Effectively manage capacity and make recommendations on staffing needs to support the master production schedule in order to meet the daily delivery and financial goals
- Drive daily production results and respond to changes in demand. Address/resolve conflicts regarding scheduling, production and personnel. Accountable for meeting request dates per production plans
- Collaborate effectively and timely with NPD and Manufacturing engineering personnel to
- Associate or related technical degree and a minimum of years 3 years supervisory experience
- Strong verbal and written Communication skills
- Must be proficient in Microsoft Office
- Technically proficient to understand and interpret drawings
- Ability to work on Saturdays on a rotation schedule
- Must be able to manage multiple tasks and/or priorities and easily adapt to changing situations
- 3 + years experience with enterprise wide manufacturing systems
10
Manufacturing Supervisor Resume Examples & Samples
- Assist the Plant Manager, Operations Manager and Production Manager with the day-to-day management of the facility and other tasks as needed
- Train, supervise and direct staff. Manage productivity, attendance and performance for staff on assigned shift
- Responsible for hourly production goals and quotas
- Control ratios of polymer materials introduced to a batch blending process
- Provide mechanical support for blending, grinding and material-separation processes
- Activate and adjust extruding machines, synchronize speed of extrusion
- Locate defects on extruded products
- Receive product, palletize, load product. Operate forklift
- Must be mechanically inclined and knowledgeable with hand tools
- Resolve issues related to day-to-day operations and maintenance
- Develop an understanding of OSHA regulations and Triumvirate’s Health and Safety Practices
- 3 years of experience working in a manufacturing setting -experience in Plastic industry desirable
11
Manufacturing Supervisor nd Shift Resume Examples & Samples
- 5 Years minimum experience in a job-related manufacturing environment
- 3 Years minimum experience in a Supervisor role
- Excellent English skills; ability to communicate both orally and written
- Strong computer skills; MicroSoft package: Word, Excell, Outlook
- JDEwards experience
- Ability to work 3:00 pm to 1:00 am
- Ability to work Saturdays
12
wet Manufacturing Supervisor, Rotating Resume Examples & Samples
- Develop and deliver technical training on process equipment
- Accountable for delivery on established expectations in safety, quality, service, cost and partner moral
- Wet process manufacturing environment, preferably in food, dairy, chemical or pharmaceutical required (4 years)
- Supervisory experience (2 years)
- Lean 6-Sigma or equivalent continuous improvement experience (1 year)
- Ability to apply knowledge of multidisciplinary business principles and practices to achieve successful outcomes in cross-functional projects and activities
- Comprehend raw data and make real time decisions
- Be an advocate for safety and instill that in others
- Own and deliver training on process control parameters such as temperature, level, pressure and flow
- Familiarity with American Institute of Baking (AIB), Good Manufacturing Practices (GMP), and Hazard
13
Manufacturing Supervisor Resume Examples & Samples
- The daily supervision and organisation of staff to ensure all schedules and objectives are met
- Planning the manufacturing schedule to ensure the needs of both the New Products and Commercial departments are met
- Maintaining compliance with Quality Systems
- Assisting in the preparation of all preapproval and routine audits by Regulatory Bodies (FDA and HPRA) and all partner audits
- Implementing cGMP's in all commercial activities and to ensure that company SOP's are implemented and adhered to
- Ensuring SOPs and training plans are created and put in place in a timely manner for new processes and procedures
- Maintaining all training plans and SOP's for routine production
- Reviewing and approving batch files, both experimental and GMP
- Assisting in the recruitment & selection of department personnel and carrying out performance reviews
- Working with the Engineering Department to ensure optimal machine performance and assisting with the introduction of all new equipment to the area when necessary
- Assisting with the co-ordination of cleaning verification/validation activities with QA and QC Department and assisting QA and Tech Affairs on all aspects of process validation for new and existing products
- A 3rd level degree (Level 8 NFQ/Hons) in a Life science
- At least 8 years manufacturing experience working within an Oral Solid Dosage environment. (HPRA/FDA approved)
- Experience of preparing for regulatory audits
- Ability to supervise and motivate a team of manufacturing personnel
- Ability to troubleshoot and identify technical issues and follow up with corrective actions
- The ability to work well with all key contacts both internal and external to the organisation
- The candidate will need to display clear and effective communication skills and have a focus on the development of teams
14
Manufacturing Supervisor Resume Examples & Samples
- 60% Processing
- Responsible for daily operations on the production floor, including scheduling, staffing, training, material use and troubleshooting to ensure that all operations are in full compliance with applicable MBRs/FPs, SOPs, and safety guidelines
- Develop technical expertise in area of responsibility and provide technical instruction on new/improved processes to appropriate audiences, primarily
- Manufacturing personnel
- Will monitor and control labor (absence, vacation and OT) and other group expenses
- Responsible for interviewing and selecting candidates
- Provide effective leadership through
- Assess performance and make recommendations for annual programs such as Talent Review and Year End Compensation
- Individual goal setting/performance reviews
- Ensure appropriate staffing levels and skill sets are maintained
- Effectively manage employee performance issues and corrective actions
- Recognize and appreciate employee contributions and support workforce diversity
- Ensure that employees are working in a safe and compliant manner
- Bachelor’s of Science degree and 2-4 years related industry experience or an equivalent level of education and/or related experience is acceptable
- Experience as a Lead or Supervisor in a GMP Manufacturing facility required
- Experience in executing moderate to complex schedules preferred
15
Manufacturing Supervisor Resume Examples & Samples
- Performance monitoring and evaluation of all employees, to include corrective counseling, new hires and termination
- Effectively communicate with employees and other shift key personnel
- Oversee workflow based on weekly schedule and collaborate with the scheduler in determining both staffing requirements and the finite schedule
- Develop, implement and manage departmental goals and objectives
- Work internally and with other departments to ensure an ongoing Continuous Improvement Program
- Engage the workforce and implement/maintain lean tools (5S, SMED, Value Stream mapping, OEE, etc.) in support of the LEAN initiative
- Work closely with the Health and Safety Committee and GMP staff ensuring that all processes and work areas are compliant throughout the Production areas
- Work with Engineering to ensure set-ups and changeovers are completed in a timely manner
- Monitor and achieve departmental targets such as T.I.R, OEE, Quality, Labour and Material Variance, Cycle Time. Address shortfalls
- Maintain Inventory Accuracy and address discrepancies
- Increase productivity, labour variance and quality through Process Improvement based on current acceptable standards
- Work with and support New Product Initiatives to meet launch dates
- Provide a level of service to internal customers consistent with corporate objectives
- Orientation and training of new employees, development and monitoring of individual employee goals
- Complete performance reviews
- Organize work flow based on weekly schedule
- Resolve manufacturing issues resulting from human error, equipment failure, product/component quality, and schedule changes
- Coordinate cycle count process, including review of variance reports, development of corrective action plans
- Daily attendance, employee information forms, vacation planning, payroll exception reports, weekly production reports
- Ensure compliance with: personal protective equipment guidelines, appropriate lockout/tag out procedures, emergency response procedures, WHMIS requirements, and ergonomic programs
- Performs other related duties as assigned by Management
- Education: College Diploma (minimum), University Degree preferred area of study: Engineering
- Experience: Previous Supervisory experience preferred
- Competencies: Experience in cosmetics, pharmaceuticals or food industries
16
Manufacturing Supervisor Resume Examples & Samples
- Lead a team of people including setting direction, deploying resources, addressing concerns and removing obstacles
- Leadership responsibility includes but not limited to management of employee performance, hiring, corrective coaching, and resource planning
- Maintain a safe and clean work environment by educating and directing personnel on the use of all control points, equipment, and resources; maintaining compliance with established policies and procedures
- Position requires access (on-call) at all hours and all day and potential to work during company designated holidays
17
Manufacturing Supervisor / Cell Leader Resume Examples & Samples
- Continually search for opportunities to enhance the production processes and the product
- Identify and resolve process improvement opportunities to enhance quality, decrease process cycle time and reduce operational costs
- Implement root cause corrective actions in a timely manner to ensure quality standards are maintained
- Implement continuous improvement (ACE) and lean strategies to improve quality, reduce process time and reduce operational costs
- Demonstrate a personal and team commitment to the EH&S program by complying with all policies and procedures, completing all required training, and supporting all applicable committee activities
- Manage all aspects of assigned hourly workforce including time & attendance, time off, rewards, discipline process, training, communications
- Conduct performance management, skill review and employee development activities for assigned employees
- Administer Pratt & Whitney and Columbus Forge policies and procedures to ensure compliance and equitable treatment for all employees
18
Manufacturing Supervisor Resume Examples & Samples
- Ensures a safe working environment through formal inspections/audits, correcting unsafe behaviors, safety / crew meetings, and utilizing proper work methods, procedures and equipment
- Incident investigation, problem solving and root cause analysis (EHS and quality)
- Organizes and reviews changeovers with appropriate staff to minimize downtime. Addresses production issues such as scheduling, quality, run time, etc
- Lead/participate in Kaizen continuous improvement sessions, make process suggestions to improve quality and reduce costs, involved with managing tier 1, 2 processes
- Involved with Lean Management systems deployment,implements cost reduction programs to ensure the efficient utilization of labor, materials, and equipment
- Part of supervisor team for IATD focus factory – day, afternoon, or night shift, 4-crew or 3-crew supervisor coverage required
- Primary plant management representative during off shifts
- Willingness to be on-call (interest question)
- Minimum 3 years of manufacturing and/or supervisory experience
- Bachelor’s Degree in Engineering, Science or Business discipline from an accredited University
- Previous supervisory and/or management experience
- Excellent organization skills with the ability to prioritize and manage multiple assignments
- Experience participating in Green Belt projects and/or have a Green Belt certification
- Interest in a position that will require you to work rotating shifts
- Good people skills including the ability to work effectively in a team environment and communicate effectively
- Desire and experience in leading change
19
Manufacturing Supervisor Resume Examples & Samples
- Supervising the safety and activities of 15 person staff of manufacturing technicians in the Chandler, AZ Assembly Technology Development factory
- Assesses personnel and monitors the flow of work in process through the manufacturing facility
- Investigates quality issues and implements corrective actions
- Establishes plans to ensure production schedules are met within established safety, quality, and cost objectives
- Actively provides development opportunities to the team and searches out ways to improve their contributions
- Emotional intelligence
- Very strong math and problem solving skills
20
Manufacturing Supervisor, Finish Resume Examples & Samples
- Requires a Bachelor’s Degree, preferably in a Technical Engineering Field, MBA or related Master’s degree strongly preferred
- Minimum of 7 years of experience directly with tools and methods in a Quality, Lean, Continuous Improvement or other known improvement system in discreet or continuous manufacturing environments
- Proven ability to use systematic problem solving to solve technical challenges
- Proven ability to communicate across broad levels of business: from shop floor to executive leaders in methods that are effective
- Excellent team facilitation skills. Build teams in a collaborative work style; previous successful experience in team building and motivating others
- Proficiency in Microsoft Office suite: Word, Excel, PowerPoint, Visio (Access Preferred), SharePoint preferred
21
Manufacturing Supervisor Resume Examples & Samples
- Flexible - willingness to work off shifts and weekends; most Resource start on 2nd or 3rd shift
- Work a focused 10 hour work day
- Ability to give/receive constructive feedback
- Ability to lead a team based approach to decision making
- Strong leadership with the ability to get results through mentoring skills
22
Manufacturing Supervisor Resume Examples & Samples
- Responsible for people and team development, quality performance, cost, service and safety
- Develop individuals and the team to solve operational issues
- Motivate the team to achieve performance targets
- Organize and facilitate team meetings to achieve continuous improvement process
- Coach team members to use the process and facilitate problem solving on the floor
- Job level will vary based on experience and scope of role
- Degree preferably in Engineering, Business, Operations Management, or related major
- Highly motivated self-starter
- Ability to lead a team based approach to decision making Demonstrated ability to work in a results oriented, challenging environment
23
Bulk Manufacturing Supervisor Resume Examples & Samples
- Responsible for directly supervising assigned staff, ensuring that they are performing their duties cost effectively and safely
- Responsible for analyzing data and implementing corrective actions to promote continuous improvement in all areas of responsibility (Bulk Yields, Labor
- Efficiencies, Safety, GMP, Dump Batches)
- Responsible for training and developing of all associates so that they can operate efficiently
- Responsible for holding staff accountable for their actions
- Responsible for fostering a team environment through training and two way
- Communication in order to improve morale
- Responsible for understanding and becoming expert on all system transactions
- And how they affect inventory including rework
- Knowledge of operations management theories, principles, methods and practices
- Knowledge of Good Manufacturing Practices (GMP)
- General knowledge of mechanical equipment, chemical processing, and process flow
- General knowledge of filling and assembly equipment and processes
- Skill in talent management and development
- Ability to interpret and adhere to union contract
- Ability to communicate effectively orally and in writing, including preparing and presenting information
- 2-5 years: Progressively responsible experience in a manufacturing facility
24
Senior Manufacturing Supervisor Resume Examples & Samples
- 8, Leading break through projects
- 1, Good communication skills, Leadership and Ownership
- 2, Can and be willing to work udner pressure
- 3, 4 years university graduate or above
- 4, 8+ years in industrial/process/manufacturing engineering in global company(s)
- 5, Optical / Electrical/Mechnical engineering With manufacturing experience desired
- 6, Lean manufacturing and Six Sigma is prefer
25
Senior Manufacturing Supervisor Resume Examples & Samples
- Select, train, develop, retain, recognize, and manage associates in group in line with Ecolab standards
- Create an environment in which employees can work safely. Implements Safety Management System
- Provides formal and informal reporting on plant performance and issues
- Generates and implements ideas that improve performance indicators, in line with safety, cost, investment and service goals. Implements Lean concepts and practices
- Assists with setting the annual budget with focus on reduction of year over year costs
- Manages the daily manufacturing operations of the plant to ensure that the manufacturing plan is executed in a manner that meets or exceeds safety, quality and cost objectives
- Ensures that Quality system is followed. Ensures that products produced meet specifications
- Resolves safety, quality, service and cost issues
- University degree or equivalent in Industrial Engineering
- Minimum 3 years manufacturing experience with significant experience in a related industry (health and hygiene products)
- Experience must include detailed knowledge of at least 2 operations functional areas
26
Manufacturing Supervisor Resume Examples & Samples
- Ensures a safe work place is provided for all employees; frequently inspects department for safety compliance. Completes accident reports and schedules appropriate follow-up reviews; identifies accidents related to operator/machine error and initiates necessary training to prevent future accidents
- Supervises the activities of production associates to achieve objectives with regard to quality, cost and time. Evaluates the performance of associates and completes necessary reports. Recommends merit increases and training/development needs
- Inspects and monitors production quality and equipment. Ensures quality procedures/practices are applied to the process, tooling, and equipment to achieve expected quality improvements
- Supervises the utilization of materials to assure an appropriate amount of parts are available to maintain smooth production flow; identifies wasteful practices and methods; reports any problems/concerns with viable solutions to the Manager, Production; and, reports suggestions recommended by associates for procedure change, etc
- Promotes and supports the company's efforts in associate involvement concepts, and "open door" communications through the development and or implementation of various programs
- Promotes commitment to quality through attitude, behavior, communication, and development/implementation of programs and activities
- Communicates/updates shift management of daily problems and concerns, identifying areas needing attention to ensure the continuity of the operation
- Bachelor’s Degree required
- 3-5 years of supervisory experience in a manufacturing environment preferred
27
Manufacturing Supervisor Resume Examples & Samples
- B.S. Degree in Business Management with minimum 5 years of manufacturing experience in a diagnostic or related industry is preferred or equivalent work experience
- Demonstrated skills in developing subordinates to their best potential. Team building, coaching and mentoring skills. Conflict resolution
- Ability to communicate effectively and comfortably with all organizational levels. Must include written and verbal skills
- Ability to react appropriately to changing priorities and impending deadlines. Ability to prioritize tasks
- Knowledge of handling hazardous materials, OSHA safety compliance required
- Formulation, filling, labeling, and packaging knowledge of diagnostic manufacturing desired
- Knowledge of Microsoft Word, Excel and Access required
- Ability to use an MPS system such as SAP
- Troubleshooting and formal problem solving skills required
28
Manufacturing Supervisor Liquid Resume Examples & Samples
- Creates and manages to an operational budget for each department including total headcount of between 10 and 20 employees
- Manages conversion process improvements of a limited scope, utilizing 5S, Lean, and Six Sigma methodologies
- Identifies and provides developmental opportunities for high potential employees
- Has accountability for department operations when Senior Management is not on site
- Responsible for answering specific questions during customer and regulatory agency audits
- Work with numerous departments and levels of employees
- The job encounters work situations of diverse scope and moderate complexity. The Manufacturing Supervisor operates within generally defined procedures and practices under general direction and minimal supervision
- Bachelor’s degree in Business Management, or technical field, or the equivalent knowledge and experience
- Requires a minimum of 5 years manufacturing experience in a GMP manufacturing environment
- Formal technical education and training in biology, chemistry and/or manufacturing process or systems is preferred
- Proven ability to direct personnel to accomplish daily work as well as periodic special projects
- Requires intimate knowledge of manufacturing process and inter-departmental responsibilities. Must demonstrate ability to work with internal and external customers
- Experience assessing current processes and techniques and implementing procedural improvements a must
- Good problem solving skills necessary
- User level working knowledge of PC software required
- The successful candidate demonstrates a sense of urgency, contagious optimism and a “can do” attitude. They lead by example and hold themselves and others accountable, while maintaining productive and professional relationships within the team. They must be approachable, transparent and have the ability to maintain a consistent level of energy and enthusiasm. The candidate also needs to be strategic, astute and forward thinking and have the ability to inspire, motivate and collaborate with others
29
Manufacturing Supervisor Resume Examples & Samples
- Plan, organize and safely control the direct labor and indirect labor for assigned areas of production
- Manage complex, multi- functional projects
- Skilled in Microsoft Word, Excel, and PowerPoint
- Root Cause Analysis techniques and Six Sigma methodologies
- Knowledge and experience with Kanban systems
30
Manufacturing Supervisor Resume Examples & Samples
- Using employee participation creates work center performance goals and leads each work center and each individual towards achieving those goals. Performs full performance evaluations for all direct reports
- Regularly interacts with diverse internal functional groups to solve moderately complex problems
- Works with Research and Development and Process Development to facilitate the scale-up and introduction of new products
- Initiates investigations into process failures, product failures, and safety incidents, and identifies and implements appropriate corrective and preventive actions
- Interviews/hires manufacturing technicians
- Knowledge of manufacturing process and inter-departmental responsibilities. Must demonstrate ability to work with internal and external customers
- Excellent creative problem solving, data analysis and influence skills preferred
- Works in manufacturing environment, may occasionally work in an office environment. Must be flexible to work varying schedules and hours as needed. Occasional travel may be required
31
Manufacturing Supervisor nd Shift Resume Examples & Samples
- Identify, implement, and follow up on improvements for safety, effectiveness and cost
- Additional duties including material control, labor reporting, scrap control, training, budgets and housekeeping
- Lead continuous improvement activities including 5S and lean workshops
- Shift hours are: 3:30pm - 2:00am, Monday - Thursday
- BS Degree from an accredited university or equivalent
- 3+ years progressive experience in supervision
- Excellent verbal and written communication skills, strong interpersonal skills
- Working knowledge of lean manufacturing, six sigma and 5S
- Lead and direct teams and individuals to drive results
- Lean/5S Implementation skills to drive lean results
- MRP skills required; SAP skills preferred
32
Manufacturing Supervisor nd Shift Resume Examples & Samples
- Responsible for overall production results and employee relations within assigned manufacturing area in regards to scheduling, process improvement, quality, and efficiency
- Coordinates activities with other management personnel to ensure consistency
- Overall responsibilities for second shift to include the supervision of machine operators running manual and CNC machines, assembly technicians, repair technicians, and finishing operators
- Plan, organize and control work schedules for production department to ensure production schedules are met
- Provide leadership and guidance to production staff to resolve technical and operational problems
- Responsible for pro-active people management. Sets the standard for performance assessment and feedback, effective communication, promoting positive morale and supporting employee involvement programs
- Develop and deliver training on operating procedures and technical skills
- Ensure department complies with company policies and procedures, including those for quality and safety
- Develops and regularly reports on department metrics
- Support the maintenance of the operating supply inventory for each department
- Responsible for all employee performance management activities
- Manage staffing requirements
- Update processes and procedures as necessary
- Minimum of 3 years of direct supervisory experience to include performance management responsibilities
- Bachelor's degree or equivalent in a technical or business discipline is required
- Be able to work a 2nd Shift position, 3PM – 12PM, Monday - Friday
- Ability to read, comprehend and apply documentation such as safety, operating and maintenance instructions
- Ability to effectively communicate, both written and verbally
- Ability to carry out supervisory responsibilities in accordance with the organization's policies and applicable laws
- Management of the following departmental processes including, but not limited to: interviewing, hiring, and training employees; planning, assigning and directing work; appraising performance; rewarding and disciplining employees; addressing complaints and resolving problems
- Normal office and production environment physical demands
- Comfortable with occasionally working near moving mechanical parts and exposure to noise of machinery. (The noise level in the work environment is usually moderate.)
- Proficiency with MS Office, Excel, and PowerPoint,
- Experience working with SAP is preferredProduction
33
Manufacturing Supervisor Resume Examples & Samples
- Responsible for providing technical expertise and leadership for daily manufacturing operations and ensuring established metrics (Production, Quality, Scrap and Cycle time) are met
- Provides specific technical expertise to support special projects, pilot operations, product and process improvements; and also provides input to develop capital expense forecast and equipment/spare part budgets to support business needs
- Supervises production personnel and collaborates with support functions to meet or exceed the goals and objectives of the Business Unit and in alignment with those of the Plant and the Franchise
- Responsible for ensuring adherence to Environmental, Health and Safety policies and procedures; provides support to ongoing initiatives related to safety and ergonomics programs
- Ensures that manufacturing activities are performed in compliance with the Quality System and drives efforts to enhance a culture of quality and compliance
- Manages the effective and efficient utilization of human, capital, and material resources to optimize performance
- Supports rewards and recognition programs, participates in the development of employees, acts as a mentor, and promotes talent
- Drives Lean Manufacturing efforts, including the maintenance of performance metrics, line balancing, continuous flow manufacturing, inventory reduction efforts, and good housekeeping practices
- Execute or supervises data entry on required systems, such as JDE, Kronos, and others
- Supports process transfers and the introduction of new products
- Execute validation activities
- Coordinates communication activities with manufacturing associates
- Identifies and supports the resolution of labor issues in coordination with the Human Resources department
- Develops and maintains a Credo-based culture
- Is responsible for coordinating and/or supporting the investigation and implementation of corrective and preventive actions to improve operating performance and to comply with requirements of the Quality system such as NCR, CAPA, audit observations and others
- Delivers year-over-year cost improvements, including productivity improvements and reductions of defects
- Plans, executes and documents training programs for associates and ensures on-time completion of training requirements
- Knowledge of Quality System requirements
- Basic knowledge of Lean manufacturing, Quality Control and Production Control
34
Manufacturing Supervisor Resume Examples & Samples
- Schedules work through the various manufacturing and/or test cell(s) and manages the floor space to assure adequate flow of production. For continuous flow cells, manages line balance ensuring the pacing process is adequately staffed to maintain desired output levels
- Perform regular daily audits of key processes to ensure optimum process performance
- Respond to test and production problems by personally investigating and resolving such problems with hourly and salaried personnel to assure a continuing flow of product. Utilize formal problem solving methodologies (8D, DMAIC, PDCA, etc) to discover and eliminate root cause
- Maintain department/cell metrics utilizing visual management techniques. Ensure all direct reports understand their cell metrics and how they impact/improve each metric. Prepare associates to lead the report-out of metrics weekly to management
- Support PFEP (Plan For Every Part) initiatives to ensure assurance of supply and minimize non-value-added activities
- Create and coach factory teams, assign and monitor hourly personnel in test and/or assembly areas to accomplish daily production and repair schedules to Rockwell Automation quality standards
- Develop, plan and implement continuous quality improvement through teams within the area of responsibility to attain World Class Quality
- Coach teams in maintaining accurate reporting of employee time and work performance within the area
- In conjunction with manufacturing teams and support personnel, develop and implement new or enhanced policies and procedures for test and/or assembly
- Develop and implement action plans to meet department goals in the areas of labor efficiency, labor utilization, housekeeping, on-time shipments and productivity improvements
- Promote an awareness of state-of-the-art manufacturing concepts and practices utilizing Rockwell Production System techniques
- Collaborate with production planners, customer service, and other management team members to set work priorities to satisfy customers
- Develop and adhere to leader standard work. Monitor/update/approve standard work for department/cell team leads and audit adherence to standard work for production associates
- Use personal computer and mainframe programs to obtain, organize, and analyze data and to prepare charts and reports. Software skills required in word processing, spreadsheet, and SAP
- Bachelor’s Degree required in Engineering, Supply Chain and/or Operations Management or equivalent
- Prior leadership position in a manufacturing environment
- Rockwell Automation will only employ those who are legally authorized to work in the United States for this opening. Any offer of employment is conditional upon the successful completion of a background investigation and drug screen
35
Manufacturing Supervisor Resume Examples & Samples
- Monitor/Assess performance of self, other individuals, or organizations to make improvements or take corrective action
- Use logic and reasoning to identify the strengths and weaknesses of alternative solutions, conclusions or approaches to problems
- Identify the developmental needs of others and coaching, mentoring, or otherwise helping others to improve their knowledge or skills
- Demonstrate acquired knowledge and general understanding of Microsoft Excel, Word, and PowerPoint
- Understand the production processes, quality control, costs and other techniques for maximizing the effective manufacture and distribution of goods
- Have general awareness of business and management principles involved in strategic planning, resource allocation, leadership, production methods, and coordination of people and resources
- Have working knowledge machines and tools, including their designs, uses, repair, and maintenance
- Ability to read, speak, and write fluently in English
36
Manufacturing Supervisor Resume Examples & Samples
- Manage the operations of the Precision Fabrication department, including production scheduling, quality assurance and executing continuous improvement initiatives
- Meet production demands by ensuring maximum throughput of parts through the department
- Maintain manufacturing documentation and records, establish and/or modify operational methods and procedures and maintain employee training records
- Responsible for effectively cross-training personnel and participation in corrective actions and process improvements
- Associate’s degree in a technical or business discipline is required; a Bachelor’s of Science degree in Engineering or Manufacturing discipline is strongly preferred
- Must have a minimum of three years experience in a manufacturing environment
- Prior manufacturing supervision is strongly preferred
- Strong people and exceptional organizational and communication skills (both written and verbal) are required
- Strong computer skills, utilizing Microsoft products, required
- Knowledge of Six Sigma and Lean Manufacturing concepts preferred
37
Manufacturing Supervisor Resume Examples & Samples
- Engineering or technical degree preferred
- Three (3) years supervisory experience in a high volume or labor intensive manufacturing work environment, preferably in the medical device industry
- Technical background in Project Management, cost accounting etc. considered a plus
- Lean trained required, Lean certified preferred
- Six-Sigma trained required, Six-Sigma certified preferred
38
Senior Manufacturing Supervisor Resume Examples & Samples
- 5+ years related manufacturing experience and/or training, or an equivalent combination of education and experience
- Ability to accept and work with constant change
- Must have the ability to manage conflict with good communication skills
- Familiar with FDA, GMP’s, ISO 13485 standards, OSHA, and other applicable state and federal laws
39
Manufacturing Supervisor Resume Examples & Samples
- Four or more years of experience in a leadership, supervisory or management role in manufacturing required
- Computer keyboard and understanding of computer system(s) currently being used
- Ability to communicate effectively with all levels of staff and clearly explain assembly processes
- Ability to organize time and schedule employee hours effectively
40
Senior Manufacturing Supervisor Resume Examples & Samples
- Previous experience working in an FDA regulated industry preferred
- Previous experience providing work direction to people preferred
- Ability to communicate and present information effectively to all employee levels in the organization
- Experience with ERP planning systems
- Understanding of lean sigma concepts preferred
- Experience in Microsoft Office, or equivalent software
- Demonstrated problem solving abilities
- The physical demands described within the Responsibilities section of this job description are representative of those that must be met by an employee to successfully perform the essential functions of this job. Reasonable accommodations may be made to enable individuals with disabilities to perform the essential functions
- While performing the duties of this job, the employee is regularly required to be independently mobile. The employee is also required to use a computer, and communicate with peers and co-workers
- During the course of regular assigned duties, the employee may be required to properly utilize personal protective equipment including but not limited to: safety shoes, safety glasses, goggles, hard hats, air purifying respirator or supplied air respiratory protection
- The employee must be able to lift 25 pounds per job requirement
- The noise level in the work environment is usually quiet to moderate
41
Manufacturing Supervisor Resume Examples & Samples
- Three or more years of experience in a leadership, supervisory or management role required
- Proficient in the use of MS Excel, Word and PowerPoint
- Experience in manufacturing preferred
- Experience in medical or other highly regulated industry strongly preferred
- Lean or Six Sigma training preferred
- Must be a change agent
- Ability to develop and coach others
- Ability prioritize and a fast-paced, changing environment
- Solid conflict resolution skills
- Ability to effectively interact with all levels of employees
42
Manufacturing Supervisor Resume Examples & Samples
- Production operations, work planning, scheduling
- Read drawings and Shop Orders
- ISO procedures
- Supervise and train production personnel
- Use of various tools, including microscopes, calipers
- Analyze operations, functions, finished products
- Recognize problems and take corrective measures
- Hazardous materials handling and emergency response procedures
- Basic reading and math
43
Manufacturing Supervisor Resume Examples & Samples
- Proven leadership and mentoring abilities, promoting constructive feedback , continuous learning opportunities within a manufacturing / production environment
- Efficient time management skills, well organized and accountable
- Planning and scheduling and managing performance expectations of direct reports
- Experience with change management cultures and lead sigma concepts a plus
- 5+ years of progressive Medical Device Manufacturing experience and 5+ years’ experience leading teams
- Experience in a medical manufacturing industry specifically with regulatory practices
- Proven ability to interface with an auditor
- Proven ability to work with minimal supervision and to flex between tasks and product lines, when needed
44
Manufacturing Supervisor Resume Examples & Samples
- Oversees and schedules production operations and personnel within cGMP guidelines
- Interacts and communicates with clients regarding production. Troubleshoots complex manufacturing process problems and issues
- Coordinates with multiple departments including sales and quality on production deliverables
- Trains employees in production methods, cGMP guidelines, and SOP’s
- Orders raw materials
- Writes batch records and writes/revises SOP’s pertaining to production processes
- Drafts, reviews, revises, and executes batch records, validation protocols, and reports
- Analyzes data and results and provides conclusions and proposals
- Researches and implements new methods and technologies to enhance operations
- Develops scalable processes with improved product yield and reduced costs for manufacturing systems
- Responsible for maintenance of production equipment
- Operates production equipment and may inspect, label, or package
45
Manufacturing Supervisor Resume Examples & Samples
- Oversees the chemical manufacturing and purification of oligonucleotide products according to customer specifications
- Ensures product documentation is in compliance with regulatory requirements, Good Manufacturing Practices, and Standard Operating Procedures
- Provides day-to-day work direction to the Manufacturing Chemists concerning oligonucleotide production activities
- Coordinates with Quality Control the submission, processing, and disposition of production samples
- Maintains analytical results for use throughout product campaigns
- Works with manufacturing management to determine the feasibility of new projects
- Assists manufacturing management with the transitioning of processes from R&D and other functions to Manufacturing
- Ensures the effective use of material, equipment and personnel in producing quality products
- Helps to formulate and makes recommendations with regards to manufacturing Standard Operating Procedures and GMP practices
- Ensures appropriate product and process change controls, deviations and corrective and preventive actions are implemented as required
- Troubleshoots manufacturing problems, develops and implements continuous quality improvements
- Initiates the development of new processes as required to resolve manufacturing issues
- Establishes operating procedures and specifications, improves upon existing methods and techniques, and provides guidance for quick resolution of technical issues
- Pursues activities for the ongoing streamlining and improvement of production processes, and associated support processes
- Sets-up, coordinates, and at times, conducts experimentation with new techniques and materials for evaluation of product and process improvement
- Coordinates with vendors to ensure the on-going consistency and suitability of their materials used in Agilent products
- 8 + years related experience and/or training; or equivalent combination of education and experience
- Knowledge of GMP manufacturing processes and methods for cost-reduction, mass balance calculations, quality improvements, yield improvements and manufacturing efficiency
- Knowledge in the fields of Science and Engineering; being able to apply these concepts to define problems, collect data, establish facts, deal with concrete and abstract variables, and draw valid conclusions
- Ability to manage multiple tasks and priorities, and establish short and long-term planning horizons to complete these duties
- Ability to work effectively as a team to accomplish deadlines and objectives, yet make independent decisions on various tasks
- Knowledge of HPLC, HPLC-MS, GC, and UV analysis desired along with familiarity in the manufacturing of oligonucleotides
- Knowledge of cGMP guidelines as well as international regulations pertaining to the production of APIs and drug products
- Technical knowledge of assays utilized for the testing of oligonucleotide APIs and raw materials
46
Manufacturing Supervisor, nd Shift Resume Examples & Samples
- Ensures team adherence to cGMPs and standard operating procedures
- The Supervisor may have multiple direct reports and will take an active role in developing staff
- Schedule and conduct regular one on one meetings and perform periodic and year end employee evaluations
- Primary point-of-contact for the area over assigned shift
- Manages daily coordination of work load among team members to accomplish the production schedule and provides shift handover working directly with other shift Supervisors
- Supports investigations and implementation of corrective/preventative actions
- Authors/reviews/improves manufacturing documents, technical reports, and qualification/validation documents as needed
- Executes all process automation systems (e.g., Wonderware, OSI/Pi, etc.) and business systems (e.g., Trackwise, SAP, Maximo etc.)
- Engages in and supports a culture of cooperation and continual improvement. Collaborates effectively with cross functional partners such as Quality Assurance, Quality Control, and Supply Chain
- Position is specific to 2nd shift; occasional work on nights, weekends, and holidays required
- Demonstrated ability to lead manufacturing operations teams to achieve objectives. Previous supervisory experience a plus
- Sound background in equipment qualification is desired (i.e. set-up and execution of installation/operational/performance protocols (IQ/OQ/PQ), qualification lead experience a plus
- Demonstrated success with internal process transfers and process scale-up is essential
- Ability to lift at least 25lbs
- 1603262
47
Student Manufacturing Supervisor Resume Examples & Samples
- Promotes and supports continuous improvement in the areas of manufacturing and inspection process methods and recommends improvements
- Interfaces effectively with NNSA, Quality Assurance, Manufacturing, Engineering and other support organizations
- Follows Honeywell policies, upholds professional standards, and performs all work in a manner respectful of others
- Directly supervises associates and performs other managerial responsibilities including interviewing, hiring, and training associates; planning, assigning, and directing work; appraising performance; rewarding and disciplining associates; addressing complaints and resolving problems
- Conducts activities in a safe and healthy manner and works in accordance with established ES&H requirements to ensure the protection of associates, the public, and the environment. Takes actions necessary to "stop" work when an unsafe condition or action is identified. Every associate has the right and responsibility to stop work when unsafe conditions or actions are identified
- Performs other responsibilities as needed
- Completion of the Sophmore years of college with a degree focus in Supply Chain Management, Operations, Business Administration or other related discipline
- U.S. citizenship and ability to obtain and maintain government security clearance
- Previous work experience in a manufacturing environment
48
Manufacturing Supervisor Resume Examples & Samples
- High School diploma/GED with 6-10 years of experience in a cGXP environment, or a Bachelor’s degree with 4-8 years of experience
- Must have prior experience in cGMP manufacturing operations
- Extended experience in large-scale chromatography
- Experienced facilitating meetings
- Experienced authoring and reviewing standard operating procedures, on the job-trainings, and other controlled
49
Manufacturing Supervisor Resume Examples & Samples
- High School Diploma with at least 10 years’ in CGMP manufacturing environment or Bachelor’s degree in a Science field (preferably Biology or Chemistry) plus at least five years’ experience in a cGMP manufacturing environment
- Bachelor’s Degree in Science (eg. Biology, Chemistry, Biochemistry, or Chemical Engineering) with at least 6 years’ GMP experience
- Extended experience in large-scale fermentation and/or chromatography
- Familiarity with Deviation Management Systems (eg. Trackwise)
50
Manufacturing Supervisor Resume Examples & Samples
- Oversee Manufacturing Associates to assure they are working in a cGMP compliant and safe manner. Ensures adherence to the (daily) manufacturing schedule
- Documents/Records cGMP data and information for processing steps and/or equipment activities, following standard operating procedures. Key documentation includes batch records, SLRs, and equipment logbooks
- Coordinate training and development of Manufacturing Associates
- Reviews Manufacturing documentation on a daily basis (BPR’s, .LB’s etc.)
- Coordinate Facilities, Metrology, Validation, Product Development and other non-routine activities with the manufacturing schedule
- Provide oversight of support groups when working with manufacturing systems
- Provide leadership support during trouble shooting of equipment, operation and processes
- Conduct annual performance reviews of direct reports
- Develop goals for direct reports on an annual basis and routinely monitor progress against those objectives
- Leads/ supports deviation initiation, investigations and closure. Participates in cross functional project teams, supports technical transfers with relevant teams/ individuals
- Excellent knowledge of current Good Manufacturing Practices (cGMP’s). Working knowledge of all relevant safety procedures within the company. Excellent understanding of most areas in Manufacturing and supporting functional groups
- Has an excellent understanding of cGMP Biotech or Pharmaceutical operations
- Possess excellent written and oral communication skills
- Possesses excellent knowledge of non-manufacturing functions such as QC, Regulatory, QA, and/or Materials Management
- Possesses an excellent understanding of the scientific theory of biologics manufacturing
- Has a excellent understanding of biotechnology processing - purpose of major unit operations and microbial control concepts
- Understand routine procedures upon which they have been trained, is able to revise and create new procedures/documents
- Possesses excellent equipment understanding, including understanding equipment function and application
- Proficient and knowledgeable in the operation and complex troubleshooting of multiple manufacturing area’s
- Lead/ supports deviation investigations. Participates in cross functional projects teams, supports technical transfers with relevant teams/individuals
- Analyze department performance and proactively identify and implement strategies to improve
- Must have the ability to work either Day or Night shift
51
Manufacturing Supervisor nd Shift Production Operations Resume Examples & Samples
- Monitor activities and initiate actions to eliminate problems, ensure that employees are properly trained, and that work is performed in accordance with health & safety requirements
- Maintain awareness of new developments and technologies
- Provide guidance / training and ensure fair & equitable treatment of staff
- Requires ability to communicate effectively with staff and technical groups
- Associate's degree and 4 years of professional experience in manufacturing and/or military environments
- Bachelor’s degree in Engineering and/or related technical fields
- Extensive training with “soft skills” (e.g. leadership, business communications, conflict resolution, etc.)
- Proven leadership expertise and business acumen, especially with previous supervisory experience
- Lean Manufacturing and/or Six Sigma expertise
52
Manufacturing Supervisor Resume Examples & Samples
- Manage staff by assigning and training employees
- Understand organization’s KPIs (Key Performance Indicators) and work to meet goals for On-Time Delivery, Throughput Time, Productivity, and Efficiency
- Track and enter hourly employees’ time into time keeping system
- Completes production plan by scheduling & assigning personnel, accomplishing work results, establishing priorities, monitoring progress, revising schedules, reducing backlog, communicate & push expedites, resolving problems, monitor & reduce rework, reporting results, etc
- Assures product quality, performance standards, and safety by establishing / enforcing organization standards
- Ensures continuous operation of equipment, and evaluate new equipment & techniques to improve productivity
- Provides manufacturing information by compiling, initiating, sorting, and analyzing production performance records / data, answering questions, and responding to requests
- Ensure safe & clean work environment by educating & directing personnel on the use of all equipment & resources, maintaining compliance with established policies & procedures
- Maintains working relationship with the union by following the terms of the collective bargaining agreement
- Resolves personnel problems by analyzing data, investigating issues, identifying solutions, and recommending action(s)
- Improve professional and technical knowledge by attending educational workshops, reviewing professional publications, establishing personal networks, benchmarking state-of-the-art practices, and participating in professional societies
- Uses excellent people skills, coaching skills, management skills, and communication skills to accomplish daily deliverables
- Provide clear direction to the work group: set priorities (as needed and in a proactive manner); escalate issues (when needed), and builds support for issue resolution
- Gain clear agreement & commitment from others through persuasion, convincing, & negotiation
- Manage conflicts in an effective manner
- Bachelor's Degree and 2 years’ manufacturing and/or maintenance experience; OR
- Associate’s degree and 4 years’ manufacturing and/or maintenance experience
- Bachelor’s degree in Business or Engineering
- Broad experience working in industrial manufacturing environments, especially with operations leadership responsibilities. Experience working in unionized environments is a plus
- Knowledge and experience with Lean Manufacturing implementation; Six Sigma training and certifications are preferred
- Proven leadership expertise, especially with previous supervisory experience
- The ability to work effectively with limited supervision
- Strong communication skills (verbal & written) are necessary to work effectively with all levels of the organization
53
Manufacturing Supervisor Resume Examples & Samples
- Organizes, supervises, leads and trains employees to complete projects within established guidelines and timeframe
- Implements and maintains safety and housekeeping standards as required by law and by company policy
- Coaches and provides technical expertise to resolve processing issues and ensures that corrective actions are implemented
- Creates a high morale workplace with the highest ethical standards
- Ensures that established processes (quality, safety…) are adhered to and not compromised
- Assigns, controls and monitors team members appropriately to achieve established schedules
- Utilizes problem solving techniques, teambuilding strategies, process controls, and continuous improvement tools to meet or exceed company productivity and quality key performance indicators
54
Manufacturing Supervisor Resume Examples & Samples
- Supervise the final assembly, electro-mechanical assembly, and test of assemblies to ensure product delivery and cost objectives are obtained while maintaining the highest level of quality while providing a safe, clean and orderly work environment
- Identify training needs and provide technical leadership to train employees. Develop employee knowledge of processes and products to assure the highest quality
- Control key manufacturing performance metrics - efficiency, quality, productivity, rework, capacity, defects, staffing and production output
- Develop production schedules, capacity and equipment to effectively meet required delivery schedules
- Maintain all associated equipment for final assembly
- Participate in Safety, 5s Lean and cost reduction programs to meet corporate objectives. Develop innovative work methods to improve output and reduce product costs
- Supervise material handling and stock keeping in the Assembly Department. Control transactions and inventory accuracy
- Actively participate in new product introduction and design reviews to ensure projected availability dates are met
55
Manufacturing Supervisor Resume Examples & Samples
- Supervises the performance of 2 or more non-exempt employees
- Evaluates the performance of 2 or more non-exempt employees based on pre-established performance parameters
- Manages and processes all payroll adjustments necessary for each employee. Coordinates and approves time off for all assigned associates
- Manages all disciplinary processes jointly with HR Business Partner
- Designs and ensures implementation of training plans to comply with job requirements, regulations and to develop associates
- Will coach and develop direct reports to ensure the operation has the right talent in place (succession planning)
- Promotes engagement of team members to meet or exceed production goals
- Leads Q12 impact planning process
- Continuously comply will all related regulatory requirements
- Responsible to stop further processing in the event of encountering non-conforming product condition
- Will develop, coordinate and/or implement production activities, schedules and methods to ensure goal attainment and ensure regulatory compliance in assigned production area
- Will prioritize production schedules based on product, equipment, material and manpower variables within the assigned area
- Will submit periodic reports, in writing and in person, to appropriate personnel
- Responsible of identifying manufacturing efficiencies within product processes and allocation of human resources
- Participates in Operational meetings, Unit Reviews, Staffing Reviews and any other presentation to management
- Liaison between management, support team and manufacturing associates
- Act as a Representative on key supervisory functions of the Stryker Brand of becoming the most admired medical device company
- Excellent interpersonal communication and supervisory skills
- Effective organizational skills
- 1-3 years related manufacturing or technical experience
- B. S. in Engineering (preferred)
- B.B.A. or B.S. in business or related curriculum
56
Upstream Manufacturing Supervisor Nights Resume Examples & Samples
- Manage daily communication to shift personnel and drives shift huddles and supports functional team meetings. Provides shift handover support in working with other shift supervisor/manager
- Manage to schedule and plan. Recognize impact for cross functional impact. Any variance to be captured and communicated to cross functional groups in real time
- Manage decisions– acquire feedback, input, and consult as require
- Extensive knowledge of SOPs and cGMPs and the know–how to work and manage within a regulatory environment
- Knowledge of pharmaceutical and biopharmaceutical manufacturing process with participation in pharmaceutical technology, technology transfer, process development, manufacturing support
- 1603833
57
Purification Manufacturing Supervisor Nights Resume Examples & Samples
- Takes active role in selecting and developing team. This includes leveraging relationships internal and external to the LSCC manufacturing team to build the best team possible
- Takes active role in developing less experienced Technical leads and leads selection and development of own team
- Act as an area/system owner – a point of contact for all work to be carried out for the area over assigned shift
- Provide critical communications upwards, downward and across as deemed fit
- Direct biologic manufacturing experience of 6+ years with a minimum of 2+ years of previous supervisory experience which demonstrates proficiency in selection of team and effectively managing personnel issues is highly desired
- Adaptable to a fast paced, complex and ever changing business environment
- 1603822
58
Purification Manufacturing Supervisor Days Resume Examples & Samples
- Leads the operation of all area specific production equipment (i.e. CIP systems, bioreactors, chromatography systems, media/buffer preparation equipment etc.), process automation systems (i.e. Delta V and Syncade Interactions, OSI/Pi Historian) and supporting business systems (i.e. SAP. Trackwise, Maximo etc.)
- Ensures team adherence to Good Manufacturing Practices and standard operating procedures
- Ensures daily work coordination and distribution of work as demanded through VirtECS schedule – work assignment to team members to accomplish the production schedule
- Build partnership with assigned technical lead to ensure daily data review and trends accomplished
- Ensure shift notes communication – accuracy and completeness
- Provide coaching, mentoring and development of staff. Manage performance
- Develops operational schedule in conjunction with scheduling and planning team
- Drives increased scheduled adherence
- Accountable for the preparation of performance connections objectives and for the mid-year and EOY performance connection review process
- Demonstrated ability to lead manufacturing operations teams to achieve objectives. Acts to promote a productive and cooperative climate. Helps to promote team effectiveness by engaging in a trusting, supportive partnership with others. Encourages or facilitates a beneficial resolution of purpose. Resolve conflicts in a constructive manner that allows win/win solution
- Demonstrated aptitude for engineering principles and manufacturing automation systems
- 1603821
59
Test Manufacturing Supervisor Resume Examples & Samples
- Manage a production team to meet output and cycle time targets
- Lead and motivate a highly trained and skilled team of operators
- Set objectives and goals to improve quality and productivity
- Plan and nurture operator development
- Create a working environment that instills commitment and teamwork
60
Test Manufacturing Supervisor Resume Examples & Samples
- The equipment & operators are aligned to deliver the volume in order to meet production targets unless its beyond manufacturing control
- All the above done effectively & efficiently - balance between overall cost/product cycletime/workforce productivity/asset utilisation
- Good teamwork within your organisation as well as with engineering support & manufacturing groups upstream & downstream
- Operators are managed/developed to give their best performance
61
Manufacturing Supervisor Resume Examples & Samples
- Position responsible for activities and resources engaged in the production process, ensuring processes are operating effectively and efficiently in order to meet cost, quality, and delivery targets
- Coordinates pre-press activity with production needs; Ensures rush orders are handled and customer service goals are met; Resolves conflicting work order information
- Responsible for direct supervision of the direct labor on one shift; Responsible for managing routine tasks through team leaders on the production floor/warehouse
- Required to manage and develop processes and adherence to them
- Provide general people organization & management activities; Provide Product Quality Management; Provide Product Delivery Management
- Coach and develop team leaders in the lean manufacturing environment
- Management of day to day manning levels to attain production schedule
- Analytical and/or technical experience
- Good PC skills
- Certification to use work-area equipment
- Vocational training or certification
62
Manufacturing Supervisor Resume Examples & Samples
- Develop, coordinate, lead, and execute daily production plans in the achievement of company goals, including driving compliance to business requirements, such as reporting time and attendance, safety, audits, etc
- Collaborate with various Project Managers, Planning, Engineering and Quality Assurance personnel to ensure timely on-time shipments of multiple product lines to our valued customers
- Ability to adapt and succeed in a dynamic environment with ever-changing customer requirements
- Report performance and analyze data to identify potential problems and issues: Assume ownership of the problem solving process and develop sound plans and corrective actions to ensure adherence to quality standards, delivery schedules, cost performance, and safe working conditions
- Develop and implement sound process controls; confirm routine quality and Team Leader checks and ensure all processes and procedures are executed using controlled methods and in accordance with work instructions
- Ensure consistent and effective shift-to-shift coordination
- Provide leadership and coaching that foster high team morale and effectiveness
- Develop and cross-train team members to support operational plans; ensure training plans are effective and documented
- Participate in tactical planning process
- Lead and/or facilitate continuous improvement efforts and projects and incorporate continuous improvement into the daily operations
- Create and maintain an environment where team members recommend and implement changes in procedures to improve value-added activities and eliminate non-value added activities
- Maintain neat and clean work areas and ensure compliance with safety and 5S standards; Ensure a safe work environment for all employees
- Meet goals and metrics that include: Safety, Quality, Delivery, Cost, and Productivity
- Must be able to effectively flow down goals from Manager into measurable tasks to subordinate levels
- 2-5 years of leadership experience to include direct supervision of staff in a manufacturing environment
- 2 -5 years of progressively increasing experience in operations, manufacturing engineering, or production control
63
Senior Manufacturing Supervisor Resume Examples & Samples
- Maintain a safe work environment throughout the facility, instill a high level of safety awareness among team members and insure sustainment of 5S principles
- Lead and support HOS efforts by meeting the following expectations and modeling appropriate behaviors
- Conduct fact-based analysis using lean techniques to create value and manage to a future state Value Stream that eliminates waste and drives continuous process improvement related to safety, quality, inventory and costs
- Monitor, review and improve manufacturing and quality related activities and drive corrective and preventative actions
- Ensure procedures are in place and being followed for production efficiency, safety, and compliance with state/federal regulations and guidelines. Focus team on using standardized work practices
- Encourage continuous improvement activities and seek opportunities and initiate action for process improvement. Serve as resource for team members to drive improvement opportunities. Identify gaps and implement countermeasures
- Mentor and develop team on HON behaviors and metrics. Listen, support, engage and encourage employee suggestions and input to achieve excellent results
- Build strong alliances between all functions and is strategic liaison to Maintenance, Technical, Quality, Planning, HSE, Customer Care and Engineering in order to meet customer and shareholder commitments
- Maintain time and production records. Implement policies and procedures as they relate to employees
- Perform performance evaluations. Coach and support to ensure a high functioning team
- Perform duties in a safe manner, consistent with company policy and ISO procedures
- Other duties and cross training as assigned
- A minimum of 3 years of experience in a manufacturing or production environment
- A minimum of 1 year of direct leadership or supervisory experience in a manufacturing or production environment
- Bachelor’s degree in Business Management, Supply Chain or Engineering strongly preferred
- A minimum of 3 years of experience with production planning, shop floor processes, materials planning, or inventory management
- Three or more years of experience with Microsoft Office Suite (Word, Excel, PowerPoint, Outlook)
- Excellent organizational skills and the ability to interface with all support roles to accomplish objectives
- Experience with mentoring and coaching employees
- Possess the ability to work with peer supervisors on the same and different shifts in order to accomplish similar objectives collectively and collaboratively
- Possess the ability to be a change agent in a production environment
64
Manufacturing Supervisor Resume Examples & Samples
- Evaluate the current training program and set policy and priority strategies
- Implement maintenance and operating skills training
- Design and develop a skill-development system
- Foster an environment that encourages self-development
65
Manufacturing Supervisor Resume Examples & Samples
- During start-up, establishing and documenting necessary processes to support effective production including overseeing start-up crew in documentation of JSAs, LOTO, work instructions, training documentation and identify best practices from other departments
- Reviewing production schedules daily, and assign hourly workers as required; train new personnel as required
- Directing and coordinating product flow through the department in accordance with Standard Operating Procedures
- Examining daily production and downtime reports
- Partnering effectively with maintenance and engineering to optimize equipment performance and reliability
- Champion and driving an effective safety process, including Risk Assessments, Gemba safety walks, JSAs, and successful 5S housekeeping levels
- Utilizing and coaching production employees in the use of Lean Manufacturing techniques including MDI, participate in Kaizens, Visual Management, and effective root cause analysis and corrective action implementation
- Maintaining high level of customer awareness throughout the value stream and focus on delivering material that meets requirements
- Bachelor's or Associate's degree and or equivalent work experience in engineering, business or related field
- Strong management and leadership skills and demonstrated ability to effectively lead and motivate a diverse group of employees
- Ability to work rotating shifts in accordance to the schedule the production team works. Shifts are 11pm-7am, 7am-3pm, and 3pm-11pm M-F with the flexibility to work weekends when needed
- Excellent working knowledge of safety and environmental practices and regulations, including OSHA compliance
- Strong verbal and written communication skills and ability to communicate at multiple levels of the organization
- Knowledge of Six Sigma, lean principles, and other process improvement processes
- Solid mechanical knowledge, including machine operation, troubleshooting and preventive maintenance
- 3+ years of effective production management experience
- Experience in a union environment
66
Manufacturing Supervisor Resume Examples & Samples
- At least two years of supervisory experience within a manufacturing environment
- Experience working with Six Sigma, Lean tools is highly desirable
- Strong leadership, communication and self-motivational skills
- Strong computer skills (SAP, Autotime, Excel, Word, Power Point)
- Available to work on 3rd shift (10pm- 6:00am)
67
Manufacturing Supervisor Resume Examples & Samples
- On Shift Supervision of Device Asembly Packaging (DAP) Operations in Mylan Dublin Respiratory to ensure that manufactured products meet business Safety,Quality and Delivery requirements, and in accordance with all Health Authority guidelines
- Performing tasks in accoradance with Quality and Safey requirements. Ensuring compliance with training, Standard Operating Procedures (SOPs), EU and US Food and Drugs Administration (FDA) requirements and Good Manufacturing Practices (GMP)
- Execute Mylans High Performance Management process for your Shift Team
- Administer the Training System for all Manufacturing Technologists and Manufacturing Operator staff
- Maintain a high standard of 6S and Housekeeping in all Manufacturing areas
- Drive Key Performance Indicators for all Manufacturing processes
- Drive Improvements through use of Lean Manufacturing and OE Tools
- Participating in cross-functional teams to establish and develop systems and procedures throughout manufacturing
- Be flexible and provide support to all other areas
- 3rd Level Qualification in a Science/Technical Discipline required
- 3 Years people management experience as a Supervisor within the Pharmaceutical or Medical Device Industry
- Experience with High-Volume Automated Assembly and/or Packaging manufacturing processes; Inhaler Assy/Packaging Experience a distinct advantage
- Start-up experience and technical writing skills are a distinct advantage.Qualification 3
- Experience of developing and delivering Training Systems and Certification programs is required
68
Manufacturing Supervisor Co-op Resume Examples & Samples
- Must have applied knowledge of process improvement
- Must be familiar with lean and or six sigma methodologies
- Strong analytical ability to solve programs and ability to learn quickly
- Strong written & verbal communication skills to generate process instructions and reports
- Ability to follow a structured project management process including document meeting minutes, action items, and monitor progress
- Assignment starts June 2017, must be able to start within this timing
69
Manufacturing Supervisor, nd Shift Resume Examples & Samples
- Direct and supervise the activities of manufacturing team leaders, technicians and operators on the 2nd shift
- Minimum 5 years of experience in Manufacturing in a Supervisory role
- Experience in a Machine Shop environment strongly preferred
- Experience in the Fastener manufacturing industry
- Experience with, and knowledge of, Lean Manufacturing programs and principles
- Proficiency with Microsoft Office programs
70
Manufacturing Supervisor Resume Examples & Samples
- Review documentation (batch records, SOPs, Logbooks) for completeness, clarity, accuracy and submit edits to documents for revision as required
- Administrative tasks – leading shift exchange, meetings, sending/receiving emails, participating in projects
- High School Diploma or Equivalent minimum; AS/BS preferred
- Experience Level in Manufacturing: Advanced
- GMP setting preferred, and/or 12-24 months experience as an Associate Level III in bio-pharm industry
71
Manufacturing Supervisor Resume Examples & Samples
- Manufacturing of therapeutic proteins under GMP conditions
- Ensures GMP compliance and safety, including adherence to all training requirements
- Daily review of production schedule and priorities to determine shift assignments and critical actions
- Ensure all materials and batch records to support shift requirements and any off shift needs for the day
- Oversee all tasks on the floor as they are carried out and provide assistance and troubleshooting where needed
- Provide on the floor training to support formalized technical and GMP training
- Communicate end of shift status to the next shift supervisor and to the unit manager as required for smooth hand off on a daily basis
- Review batch documentation for errors and deviations, signing off responsibility to the next supervisor after this review
- Work with technology transfer associates to incorporate new cell lines and processes in the plant
- Oversee the generation and review of Batch records and SOP's
- Responsible to help forecast and meet indirect materials budgets and overtime budgets
- Work interdepartmentally to see that work orders, dispensing, preventative maintenance, QC, and documentation issues are resolved and enhance communications at all levels
- Interview and hire operators to provide responsible, experienced people to carry out procedures
- Carry out performance reviews and recommend advancements for operators where reasonable
- 5+ years (min) of experience in a Biotech or pharmaceutical manufacturing industry
72
Manufacturing Supervisor Ii Temporal aÑo Resume Examples & Samples
- From 2 to 4 years of experience as production supervisor
- Customer-focused decision-making skills
- Proven initiative, creativity and assertiveness
- Basic understanding of EHS regulations
73
Manufacturing Supervisor Resume Examples & Samples
- Bachelors degree, higher education preferred
- Typically 5-7 years related experience with operations management in a finite scheduling environment
- 3-5 years cGMP experience, biopharmaceutical experience preferred
74
Manufacturing Supervisor, Downstream Resume Examples & Samples
- Ensure adequate allocation of human and technical resources to achieve objectives
- Manage conflicts and communications within Process Unit and with other disciplines
- Support teamwork and motivation within and across teams
- Work with the teams to resolve tactical issues and take corrective actions
- Coordinate, monitor, and improve production processes across all shifts for the responsible team
- Manage assignment for deviations and CAPAs within PU
- Coordinates activities with other disciplines such as access to production equipment for PM and calibration
- Execute the production strategy and ensure operation tactics are aligned with strategy
- Translating the long range production planning into actionable tasks and overseen the execution
- Meet together with the production teams’ quality, compliance, GMP requirements and regulations
- Keep the production always audit ready and ensure compliance with safety, cleanliness and storage (housekeeping)
- Responsible for Performance Reviews for manufacturing associate from all shifts within the responsible team with support/input from the shift leads
75
Manufacturing Supervisor Resume Examples & Samples
- Plan, establish schedules and assign work, considering requirements and priorities. Ensure most effective utilization of staff and equipment in order to cost-effectively achieve objectives while concurrently implementing efforts to continuously improve performance
- Monitor activities, anticipate and respond effectively to problems, ensure that employees are properly trained and work is performed in accordance with health and safety requirements
- Maintain awareness of new developments and technologies. Review equipment capabilities, methods and processes, and determine feasibility of utilizing alternative approaches, consolidating functions, and modifying or replacing equipment to reduce costs and improve quality
- As assigned, devise and implement new approaches to recurring problems. Prepare or assist in preparing budgets and ensure adherence to approved budget plans
- Provide guidance and training, and ensure fair and equitable treatment of staff. Assist less experienced supervisors with the more complex aspects of their assignments. Manage and document employee performance and develop associated recommendations
- Will need to have flexibility with working various shifts during training
- Transformer manufacturing experience is a plus
- Previous Manufacturing Supervision experience is preferred
- Knowledge in MS Office, including PowerPoint
- Exposure to ERP and Workforce Management software applications (e.g. SAP, etc.)
- Excellent communication skills (written & verbal)
76
Manufacturing Supervisor Resume Examples & Samples
- Foarte bune abilitati de coordonare si organizare, capacitate de a lua decizii rapid, orientare spre rezultat, abilitati de relationare
- Foarte buna cunoastere a activitatii de gestionare productie
- Cunostinte de limba engleza
- Cunostinte de operare PC (Word, Excel)
77
Manufacturing Supervisor Resume Examples & Samples
- Lead areas of responsibility in the use of EBS practices, including MESH, Eaton Lean Six Sigma (ELSS), EQS, ProLaunch, and BOS/BSC, with focus on performance of the entire value stream. Keep focus on meeting customer needs, both internal and external (Customer Centric Focus / KBKC)
- Utilize the Tiered Meeting process to track and analyze key operational metrics and implement actions to improve operational performance
- Direct day-to-day activities, including manpower movement, job assignments, time/attendance/vacation data, etc
- Collaborate with the other Manufacturing Supervisors to schedule overtime, and execute to labor plan
- Train and develop hourly team members, engage support team members in problem solving efforts
- Clearly define and communicate expectations, providing positive reinforcement when met and providing coaching and counseling as necessary when not met
- Bachelor’s degree from an accredited institution required
- Minimum of two (2) years’ experience in an operations and/or a manufacturing environment
- This role does not offer relocation, only candidates that currently reside within the immediate geographic area (50 miles) of Jackson, MI will be considered
78
Manufacturing Supervisor Resume Examples & Samples
- Utilize the Tiered Meeting process to track and analyze key operational metrics and implement actions to improve operational performance. Direct day-to-day activities, including manpower movement, job assignments, time/attendance/vacation data, etc
- Relocation is being offered for this position within the continental United states
- Excellent communication, customer service, and interpersonal skills necessary to converse with diverse group of stakeholders including senior management, manufacturing production/operations, and Supply Chain Management personnel
- Expert knowledge in materials and production master scheduling, inventory control, transportation/logistics, purchasing, logistics, manufacturing control systems, (APICS), and customer JIT services
- 3-5 years of management/leadership experience
- Experience managing in a union environment
79
Manufacturing Supervisor Resume Examples & Samples
- Is responsible for supporting the investigation and implementation of corrective and preventive actions to improve operating performance and to comply with requirements of the Quality system such as NCR, CAPA, audit observations and others
- Executes and documents training programs for associates and ensures on-time completion of training requirements
- Working knowledge of computer software (Microsoft Office, ERP system)
80
Manufacturing Supervisor Resume Examples & Samples
- Daily review production schedule and priorities to determine shift assignments and critical actions
- Provide on the floor training to support formalized technical and GMP training. Check that operator training files match and support the processes they are required to carry out
- Monitor operator training files and work with compliance specialist to keep files up to date
- Use the day book approach to manage the days goals and responsibilities in line with the priorities
- Review, on a shift wide basis, the batch records for error and deviations, signing off responsibility to the next supervisor after this review
- Partcipate in CIP team
81
Manufacturing Supervisor Resume Examples & Samples
- Oversee production in Buffer and Media Manufacturing
- 4 - 6 years of supervisory or leadership experience in a manufacturing environment; equivalent experience in leading project or work teams may be substituted
- Experience in inventory control
- Excellent communication, interpersonal, and leadership skills
- Ability to implement and maintain a 6S organization
- Experience with GMP regulations as they pertain to clinical diagnostic products
- Lean MFG
- Experience with an ERP system, SAP preferred
82
Manufacturing Supervisor Resume Examples & Samples
- Implements a staffing plan by identifying resource requirements, writing justifications for additional personnel, obtaining approval for changes, and co-ordinating the selection process with Human Resources (HR)
- Monitors daily work operations and provides direction to predominantly non-exempt and entry level staff to achieve unit or departmental goals
- Interacts with internal and external customers, by meeting regularly, responding to requests and explaining procedures
- Interprets and executes policies that affect individuals within the assigned organisational unit or department
- Monitors compliance with company policies and procedures (for example (e.g.) compliance with Food and Drug Administration (FDA), British Standards Institution (BSI), Equal Employment Opportunities regulations etcetera (etc.))
- Develops direct reports by securing appropriate training, assigning progressively challenging tasks, applying progressive disciplinary action as appropriate and conducting formal written and verbal performance reviews
- Maintains personnel records (e.g., work schedules, vacation schedules/leaves and makes or directs modifications in the database to reflect actual changes
- (Experience/Education) National Framework of Qualifications (NFQ) level 7 qualification in a relevant discipline and 2+ years of related work experience, or an equivalent combination of education and work experience
- (Technical/Business Knowledge (Job Skills)) Monitors progress of non-exempt employees toward departmental goals; monitors costs of projects and human and material resources within a department or unit. Will perform this job in a quality system environment
- (Cognitive Skills) Develops and/or identifies new work processes and the improved utilisation of human and material resources within the assigned area or related departments; facilitates other’s participation in the continuous improvement programme; investigates and solves basic problems that impact work processes and personnel within a unit or department
- (Influence/Leadership) Promotes department goals by selecting, motivating, and training capable staff. Leads the activities of assigned staff by communicating and providing guidance towards achieving department objectives
- (Planning/Organisation) Schedules human and material resources within a department or section in conjunction with near-term plans to ensure their availability; carries out operations within an established budget
- (Decision Making/Impact) Assignments are expressed in the form of tasks; generally makes day-to-day decisions within established policies, procedures and guidelines in order to carry out the operations and processes selected at higher levels; consequences of erroneous decisions or recommendations might include delays in programme schedules and result in the allocation of more resources
- (Supervision Received) Works under general supervision. Receives limited supervision on standard issues, and detailed instructions on new assignments. Work is reviewed for soundness of judgement, overall adequacy and accuracy
- (Supervision Provided) Provides direction and guidance to predominantly non-exempt and entry level exempt personnel; evaluates performance of and assists in career development planning for subordinates; often responsible for a local functional or process activity
83
Manufacturing Supervisor Resume Examples & Samples
- Oversee production of Bulk Products (CIP, SIP, Cross Flow) and Fill Operations (Parts Prep, Vial Handling, Fill, Coding, Inspection) for both Product and Media batches
- Working with support departments to schedule detailed daily activity and resolve issues
- Providing oversight in adherence to and maintenance of standard operating procedures (SOPs)
- Overseeing and administering training (Read and Understand and OJT)
- Generation and Investigation of process/product deviations utilizing the TRACKWISE System
- Providing oversight of issue resolution in cooperation with the department Director
- Participating in all departmental medium qualification requirements
- Leading an operations staff and conducting performance reviews on an annual basis
- Hiring and termination of employees
- Auditing of internal systems for compliance and continued improvement
- Providing reports to the production manager to form corrective action plans
- Support Director during Batch Review and MFG Tours during regulatory audits
- Contributing to staff meetings by occasionally serving as a facilitator
- Forming and support of cross functional teams for continuous improvement
- Interacting with outside vendors
- Measuring departmental performance (for example, through key performance indicators and time studies)
- Supervise several staff from entry- to lead-level
- A bachelor’s degree in a technical discipline from an accredited college or university is required, however exceptions may be made based on relevant industry experience
- A minimum of 2 years of industry experience in a supervisory role is also required. Industry-relevant technical or managerial training is a plus
- Strong sense of cGMP’s
- Performance as a “hands on” supervisor with a strong manufacturing background
- Proficiency in calculations related to concentration and scale up
- Must work with little direct supervision in order to meet timelines
- Must have relevant industry experience in a supervisory capacity
- Must be able to multi-task priorities and effectively communicate to the rest of the team
- Must be able to foster a strong sense of teamwork in the technicians by example
- Must possess strong written and verbal English communication skills as well as sound presentation skills
- Must be able to assist in all aspects of department training
- Good time management skills are a must
- Strong conflict resolution skills are required
- Previous team building training is a plus
84
Upstream Manufacturing Supervisor Resume Examples & Samples
- Ensures oversight for critical operations through systematic walk down and checks prior to execution advance. Review critical attributes and drive decisions
- Provide critical update summary to the staff following shift exchange
- Develops operational schedule in conjunction with scheduling and planning team. Drives increased scheduled adherence
- Drives continuous improvements through staff engagement
- Knowledge of science generally attained through studies resulting in a B.S., in science, engineering, biochemistry or related discipline, or its equivalent is highly desired
- Direct biologic manufacturing experience of 6+ years with minimum of 2+ years of previous supervisory experience which demonstrates proficiency in selection of team and effectively managing personnel issues is highly desired
- 1604531
85
Manufacturing Supervisor Resume Examples & Samples
- Must be able to provide effective coaching and mentoring to develop a high performing work team
- Knowledge of ISO 9001 Quality Systems
- Must have strong problem solving and analytical skills
- Must have an innate desire to learn and continually improve
- Ability to obtain and maintain a security clearance
- Previous experience with vacuum technology and/or semiconductor processing desired
- Previous experience in a high volume/high quality test environment desired
- Prior experience in an electro-optical testing environment under low-light conditions desired
- Previous Aerospace/Defense industry experience desired
86
Manufacturing Supervisor Resume Examples & Samples
- Lead a team of hourly employees to support the business
- Ensure all safety policies and procedures are followed and that all personnel are properly trained
- Drive daily scheduled attainment to meet all internal and external customer commitments with top quality, reliability and at the lowest cost
- Work with Quality to ensure all quality standards are met; and to address and any deficiencies with appropriate corrective action
- Interfaces with customers manufacturing and electrical engineering teams
- Develop, coordinate, lead, and execute daily production plans
- Report daily production results, rework and downtime
- Work with Engineering to identify root causes to solve quality issues
- Report product defects ensuring these are resolved and report solutions are recorded appropriately
- Collaborate with/provide information to Engineering on new product development regarding manufacturing methods, design requirements, tooling, processes and specification requirements to ensure future manufacturability quality
- Maintain product knowledge as new products are released
- Assist with development and implementation of processes, policies and procedures
- Drive improvement in quality, service and safety
- Accomplish goals while maintain high team morale, employment involvement, safety and teamwork
- 2+ years’ experience in a manufacturing leadership position
- Experience with automated electronics assembly required
- L3/CE will only employ those who are legally authorized to work in the United States
- Ability to build and lead a team through change
- Six Sigma or equivalent quality training
- Strong oral and written communication skills
- Ability to work without direct supervision
- Prior experience in the defense/space industry
87
Manufacturing Supervisor Resume Examples & Samples
- Works under general supervision
- Follows established procedures
- Work is reviewed for soundness of technical judgment, overall adequacy and accuracy
- Supervises non-exempts and/or entry-level exempts of manufacturing unit in accordance with established policies and methods to meet production commitments.
- Maintains manufacturing staff by recruiting, selecting, orienting, and training employees; maintaining a safe and secure work environment; developing personal growth opportunities
- Becomes expert in Lean Conversion. Participates in Kaizens planning and execution. Use +QDIP boards to challenge and develop Group Leaders and associates. Uses PSP and other DBS tools to detect and solve problems
- Provides ongoing communication to management and engineering on all manufacturing issues within the production area
- Coordinates and manages material flow, accuracy and quality of work performed, and unplanned maintenance support requirements
- Improves schedule linearity, total product cycle time, inventory levels, manufacturing effectiveness and employee satisfaction
- Develops, implements, and maintains manufacturing strategies for production measurements and general business communication
- Ensures the development and implementation of training plans and monitor the maintenance of training certification records
- Ensures compliance to safety rules, work expectations, housekeeping standards and consistency of operating practices across shifts and work areas
- Conducts regular and ongoing informational and improvement team meetings
- Monitors productivity and ensure that staffing levels are appropriate to support the manufacturing plan
- Executes and manage the Performance Management process for all direct report employees
- Monitors product quality and drive continuous quality improvement activity to prevent quality issues. When quality incidents happen,.leads root cause / corrective action analysis with direct reports and coordinate corrective actions as necessary
- Actively participates in Kaizens and Lean Operation activities
- Contributes to team effort by accomplishing related results; keeping business information confidential; administering the system security; ensuring data accuracy and integrity; maintaining updated professional and technical knowledge; assuring systems compliance with laws, regulations, and corporate standards; ensuring a safe and healthy environment
- Complies with QRS, ISO and all applicable regulations and company procedures
- Ensures that all personnel in his/her area are aware of the importance of Environmental Policy and EMS (Environmental Management System) requirements, their roles and responsibilities and the potential impacts of their work
- Identifies opportunities and propose ideas to minimize or eliminate environmental problems and participates in the definition of environmental objectives and targets
- Bilingual (English and Spanish)
88
Manufacturing Supervisor Resume Examples & Samples
- Prepare work schedules and ensure appropriate coverage for assigned shift
- Supervise all work processes and ensure work is performed accurately and efficiently
- Ensure monthly product QC requirements are met and Ensure quality and quantity of manufacturing and distribution goals are met; including timelines
- May perform, review and approve quality control on products, reagents, equipment and various test kits
- Three years experience including one year supervisory experience required. MT (ASCP) certifications or equivalent certifications where required
- Must have effective communication and customer service skills. Knowledge of blood products, supplies, and the ability to interact with diverse customers (internal and external) is required
- Available to work overtime, other shifts, early mornings, evenings, holidays and weekends
- Requires standing, stretching, stooping and bending for extended time periods. Lift, pull, push and move objects of up to 50 pounds. May work in walk-in refrigerator/freezers for periods of time
- Must have computer experience (intermediate to advanced)
89
Manufacturing Supervisor Resume Examples & Samples
- Directing activities of a production crew ranging in size from 8 to 14 hourly associates
- Maintaining safe and efficient operations
- Coordinating repairs and maintenance activities with maintenance department to maximize uptime
- Leading and facilitating troubleshooting of down equipment and process problems
- Leading safety activities of production associates
- Conducting accident investigations
- Providing ongoing creative shift leadership to personnel to ensure safety, quality and delivery performance while improving operating efficiencies
- Providing counseling, leadership and direction to the hourly associates on production issues
- Providing direction on production schedules, unscheduled downtime and the efficient utilization of resources
- Enforcing plant rules, monitoring attendance and providing corrective action as necessary
- Preparing production reports and data for management
- Conducting regular pre- shift meetings
- Coordinating training of hourly associates and improvement activities with other departments
- Identifying improvement opportunities and facilitating action on their shift
- 2+ years of experience in a leadership role
- Shift flexibility in working a rotational type work schedule
- Strong communication, facilitation, teamwork and management skills
- Bachelor’s degree or equivalent experience
- Continuous process manufacturing experience
- Experience with cost reduction, production efficiency improvements or continuous improvement activities such as Six Sigma, 5S, TPM, SMED or Standard Work
90
Manufacturing Supervisor Resume Examples & Samples
- Supports compliance with OPKO quality system requirements and with in-vitro diagnostic regulatory compliance to FDA, European Union and other requirements
- Develops and maintains relevant QMS procedures to ensure that products meet customer specifications
- Leads and initiates actions to prevent the occurrence of any nonconformities relating to product, process and the QMS
- Ensures that the QMS is maintained through appropriate audits, tests, inspections and surveys
- Reviews organizational requirements and makes recommendations for changes
- Reports quality and nonconformance data and trends
- Associate’s degree in a science or engineering field
- Manufacturing experience in a precision medical device production environment (FDA/ISO regulated)
- Experience providing production oversight in a diverse cell-based manufacturing operation
- Direct experience with reagent production processes and/or automated manufacturing operations
- Excellent written, verbal, and technical communication competencies with strong analytical and problem-solving skills
- Proficiency in PC applications including Microsoft Windows, Outlook, Word and Excel
91
Manufacturing Supervisor Resume Examples & Samples
- Assume full responsibility for the plastic molding activities for your assigned shift including supervision of subordinates and equipment
- Direct and coordinate all process activities to ensure that molding production schedule priorities are maintained and being followed
- Assign shift work assignments to Process Technicians and Technical Assistants, documenting all services such as mold changes, mold cleaning and repairs performed during the shift
- Ensures safe work practices and a clean working environment are maintained and hazards corrected efficiently
- Maintain effective communication with team members in support of a union-free environment
- Take initiative in solving problems and offering suggestions for process improvement
- Take initiative in implementing and improving TPM and SMED initiatives in the technical department
- Manage OEE, Scrap, Cycles, MUV, and machine utilization
- Assist in the implementation and maintenance of process control
- Expedites production and ensures product quality while supporting lean manufacturing
- Ensure applicable reports are timely and accurate to the technical manager
- Lead crew safety meetings and support safety initiatives including STOP, and SEAL in the technical department
- Bachelor’s degree preferred. High School Diploma or equivalent Required
- 5+ years injection molding maintenance and mold setting within a manufacturing environment
- 2+ years team lead/supervisory leadership-injection molding
- Proven commitment to safety and ensuring solid housekeeping initiatives
- Proven ability to lead, direct, control and organize efforts in support of production
- Excellent written, verbal and interpersonal communication skills
- Must be able to work longer than 12 hour shifts
- Ability to become proficient on Microsoft software programs and others as necessary
- Must pass post offer physical, controlled substance screen and criminal/reference background
- Proven proficiency in the practical application of 5S, SMED, TPM, Visual Factory and Kaizen practices in a Manufacturing environment
92
Manufacturing Supervisor Resume Examples & Samples
- Drive production productivity / discipline on the manufacturing floor through day-to-day operations of the group to ensure a smooth workflow. Impact of decisions on business operations is direct but limited
- Effectively coordinate / follow up inter-departmentally with Fabrication, Warehouse, Purchasing, Engineering, Customer Service, Quality Control and Human Resources
- Ensures Performed work is in compliance with established policies, procedures and/or protocols
- Identifies resource needs and suggests justification. May evaluate and recommend changes in methods or procedures in own area of responsibility
- Perform various administrative functions as part of day to day Supervisor / Manager responsibility
- Oversee creation of shortage list (purchased and/or fabricated parts) as well as receipt and control of purchased materials
- Updates manufacturing progress for daily production meetings as well as maintain shift to shift production status pass down
- 2-5 years experience in manufacturing assembly concepts, practices, and procedures for managed group (s) and how it supports related operations
- Supervisory approaches for work direction, motivation, performance management, time and attendance and disciplinary action
- Experience using Lean principles
- Previous experience as an agent for change
- Highly proficient with MS Office suite programs
- Typically BS/BA in related discipline, or equivalent experience
- Zero Harm Culture (ZHC) participation required
- Typically manages non-exempt technical employees, and/or lower level exempt employees
- SAP experience (use of various additional SAP functions to support production / personnel needs)
- Previous experience managing multi cultural work groups
- Previous experience in a union environment
93
Manufacturing Supervisor Resume Examples & Samples
- Plan establish schedules and assign work, considering requirements and priorities. Utilize most effective equipment, considering skills of staff, to cost-effectively achieve objectives
- Communicate status updates regularly with project managers and mitigate production schedule impact risks
- Implement enhancements to continuously improve performance and processes through lean manufacturing techniques. Ensure product quality through inspections and analysis and reduction of recurring quality issues
- Monitor activities and initiate actions to eliminate problems, ensure that employees are properly trained and work is performed in accordance with health and safety requirements
- Resolve semi-complex technical or human resource issues, and work with operations managers and human resource representatives to resolve more complex issues
- Maintain awareness of new developments and technologies. Review equipment capabilities, methods and processes, and make recommendations regarding feasibility of utilizing alternative approaches, modifying or replacing equipment to reduce costs or improve quality
- Provide guidance and training and ensure fair and equitable treatment of staff. Manage and document employee performance and develop associated recommendations
- Candidate will learn the overall manufacturing process in order to fill in for other supervisor’s absence
- Candidate must be willing to work second shift as their home shift - 3pm to 11:30 pm. Flexibility for other shifts as needed**
94
Manufacturing Supervisor, Purification Resume Examples & Samples
- Strong understanding of GMPs and other regulatory guidelines applicable to commercial pharmaceutical manufacturing
- Ability to manage multiple priorities in a fast-paced manufacturing plant setting
- Strong writing skills and ability to prepare technical reports
- Strong problem assessment and troubleshooting skills
- Demonstrated ability to interact with all levels of personnel to analyze and solve problems related to manufacturing, Quality, documentation, and personnel issues
- Ability to analyze data and information to determine paths for process improvement and potential root cause/corrective actions in the case of exceptions
- Ability to respond to detailed inquiries, and present information to groups with varying levels of scientific knowledge and to senior management
- Good computer skills including Word, Excel and PowerPoint
- Flexibility with work schedule to ensure adequate oversight and support for direct reports also required
95
Manufacturing Supervisor Resume Examples & Samples
- 2 years’ experience in a high volume or labor intensive manufacturing work environment, preferably in the medical device industry
- Lean and Six Sigma training/certified preferred
- Customer Focus (C)
- Drive for Results (C)
- Priority Setting
- Command Skills
- Compassion
- Confronting Direct Reports (C)
- Timely Decision Making (C)
- Decision Quality (C)
- Fairness to Direct Reports (C)
- Managing Diversity
- Motivating Others (C)
96
Manufacturing Supervisor Resume Examples & Samples
- Provide front line supervision, leadership and work direction to production technicians, including time and attendance, performance management, training oversite, and development
- Operates in accordance with established policies and procedures to meet production commitments within Alcon’s standards (production, quality, cost, conduct, and safety)
- Troubleshot problems regarding product quality and equipment
- Provides direction, correction and discipline as needed in accordance with alcon policies
- Manages multiple priorities, and effectively holds others accountable for results
- Manages conflict and deals effectively with others in a diverse workforce
- Lead and implement continuous improvement processes within the manufacting area utilizing industry known lean manufacturing principles (Six Sigma, GEMBA, Kaizen, etc)
97
Manufacturing Supervisor Resume Examples & Samples
- Manage the performance of all employees in order to meet operational goals including cycle time reduction, productivity improvements, quality improvements, and cost reduction
- Monitor production orders and schedules to ensure product and scheduled delivery dates are achieved
- Prepare operational schedules and coordinate manufacturing activities to ensure that the production and quality of products meet specifications
- Plan production operations; establish priorities and sequences for manufacturing products
- Perform staffing coordination between production cells as needed
- Preview production/operating reports and resolve operational manufacturing and maintenance problems to ensure minimum costs and prevent delays
- Work with Engineering and Maintenance to oversee process controls in the area
- Ensure a safe workplace by supporting all EH&S initiatives and activities
- Enforce and adhere to company policies
- Keep team members engaged and motivated by fostering an inclusive and respectful workplace, keeping employees informed, and providing actionable and meaningful feedback
- Facilitate the resolution of employee relations issues within the work groups
- Foster an environment of continuous improvement
- Minimum five years supervisory experience in a manufacturing environment
- Exceptional interpersonal and communication skills
- Ability to make informed decisions and suggestions quickly
- Ability to build relationships by listening, persuading, and negotiating
- Strong communication skills with ability to interact within a cross functional team
- Ability to coach, motivate and lead hourly employees
- Sense of urgency and ownership
- Proficiency with Microsoft Office (Excel, Word)
- Willingness to work extra hours, including weekends, as necessary
98
Manufacturing Supervisor Resume Examples & Samples
- Coach and support your team including all aspects of performance management and employee development
- Ensure employees follow company policies, safety rules and support the 5S process
- Facilitate shift-to-shift communications and foster open communication among employees
- Listen, engage and encourage employee input and suggestions to develop a team environment that achieves daily production goals
- Process weekly payroll including managing PTO and scheduling
- Develop a shift production schedule ensuring that products are manufactured with the highest level of quality in a safe and timely manner that will meet or exceed customer expectations
- Participate in leading efforts to drive process continuous improvement as it relates to targeted metrics and lean manufacturing
- Monitor and ensure compliance with ISO, GMP, FDA and class 7 requirements
- Maintain quality system by following SOP’s and QWI’s
- Resolve escalations in a fair manner
- Complete containment and quickly restore flow
- Accurately oversee Lot File reconciliation
- Associate’s degree or equivalent experience. BS degree preferred
- A minimum of 3 years’ experience supervising employees in a manufacturing environment
- Experience working in a Lean Manufacturing environment
- Work experience under Good Manufacturing Practice (GMP), ISO standard and familiarization of FDA material regulations desired
- SMED experience supporting mold and process requirements preferred
- Demonstrated experience in project management and effective organization and planning
- Demonstrated ability to apply problem solving methodology to understand root cause and implement solutions
- Effective leader with team building skills
- Strong verbal and written communication
- Ability to travel domestically and internationally (less than 5%)
99
Manufacturing Supervisor Resume Examples & Samples
- Mentors direct reports to improve their skills and overall effectiveness
- Maintains positive employee relations through the use of proficient and open communication skills. Listens, supports, engages and encourages employee suggestions and input to achieve excellent results
- Drives accountability throughout the operation
- Support cost reduction initiatives and first pass yield improvement
- Support Practical Process Improvement Business Systems into operations
- Support implementation of lean tools throughout manufacturing
- Participate on continuous improvement teams and actions to improve process and product flow
- Manage key operations metrics
- Support and participate with Quality, R&D and Engineering on new product introductions
- Demonstrates Thermo Fisher Scientific values - Integrity, Intensity, Innovation and Involvement
- Demonstrates Role Model Leader Characteristics
- Other miscellaneous activities as assigned
- Plans and assigns work, implements policies and procedures, and recommends improvements in production methods, equipment, operating procedures and working conditions
- Participate in Tier I and Tier II Standup meetings
- Provide constant shop floor leadership presence (90% of time on floor)
- Ensure effective employee relations. Provide employee coaching and development. Makes employment decisions
- Maintain a culture of accountability and colleague development
- Effectively manage a meaningful Performance Management process for direct reports
- Balance safety, quality, productivity, cost, and morale to achieve positive results in all areas
- Perform accident investigations
- Track absenteeism and timekeeping. Manage disciplinary action process
- Drive housekeeping and 5S
- Work closely with Training Coordinator to ensure compliance
- Collaborate with Scheduling/Planning to maximize throughput and attainment
- BA or BS degree in applicable field preferred
- Quality Systems Regulations/ISO experience required
- Continuous Improvement experience is preferred, such as PPI
- Ability to work independently and as part of a team, self-motivation, adaptability, and a positive attitude
- Must demonstrate strong organizational skills and be able to handle multiple assignments simultaneously
- ERP software experience, JD Edwards a plus
- Proficient in MS applications (Excel, Word, Outlook)
- 5+ years of related work experience in a Manufacturing facility
100
Manufacturing Supervisor Resume Examples & Samples
- A minimum of a Bachelor degree is required
- A minimum of six (6) years of experience in manufacturing or related operations with two (2) years of leadership or direct Supervision experience is required
- Experience within a GMP and/or ISO regulated manufacturing environment is required, ISO9001 or ISO13485 is preferred
- Experience with NCR process, CAPA, root cause analysis and other quality system components are required
- Basic understanding and working knowledge of Lean Six Sigma/Process Excellence Tools is required. Lean Six/Sigma Training and/or Certification are preferred
- General knowledge regarding capacity planning including ERP and Manufacturing Processing Systems (MPS) is required
- Demonstrated experience with revising site documentation to improve operations (logbooks, process sheets, work instructions, training guides, etc.)
- Must have PC knowledge with experience using Windows and Microsoft Office software, advanced proficiency in Excel is required
- Excellent written and verbal communication skills are required
- Experience with clean room environment
- Prior experience working in a union-manufacturing environment may be preferred based on site
- Demonstrated strong project management skills are required; the ability to lead and facilitate project improvements
- Based in Irving, TX with minimal travel up to 10% domesticProduction
101
Manufacturing Supervisor Resume Examples & Samples
- Incumbent will possess a Bachelors Degree (BS/BA) 3+ years of direct supervisory experience and Two plus years of manufacturing experience involving welding fabrication and machining
- Experience in Lean Manufacturing, Six Sigma, and or 5S
- Working knowledge of MRP and Quality Control systems
- Excellent, demonstrated experience with computers and Microsoft Office software
- Conflict resolution experience with an hourly workforce is preferred
102
Manufacturing Supervisor Resume Examples & Samples
- Achieving daily attainment requirements
- Maintaining and updating training matrices
- Recording downtime, scrap, and determining team efficiency
- Understanding and administration of HR policies
- Coach and counsel employees through performance concerns
- Independently administer corrective action through written level
- Ensures cross training is occurring in their area of responsibility
- Maintain kanban cards, make replacements, and enforce their use
- Understand your responsibility for the environmental, health & safety programs, including ISO14001. Understand the importance of conformance with all safety and environmental procedures of the environmental and safety management systems, including emergency response. Understand the EMS consequences, actual or potential, of their work activities and/or their behaviors from specified work instructions
- Ability to use measuring and gauging devices with an understanding of SPC
- Must have demonstrated mechanical aptitude with the ability to perform minor machine adjustment and setup
- Demonstrated ability to lead and develop others to achieve daily goals
- Demonstrated positive performance record, strong dependability with a proven attendance record
- Demonstrated positive performance record. Individuals in Corrective Action steps may be ineligible
- Associate's degree (A. A.) or equivalent from two-year college or technical school preferred
103
Manufacturing Supervisor Resume Examples & Samples
- Utilize process improvement by simplifying complex processes
- Lead, train and develop direct reports by providing challenging tasks and assignments; provide developmental feedback
- Direct others through establishing direction; distribute workload; clear communication
- Manage & Measure work by tracking and assigning responsibilities for tasks; set clear objectives and provide feedback
- Supervise the production process and ensure compliance to all safety and other regulatory requirements
- Develop direct reports by effectively using the PMD (Performance Management Discussion) process and offer clear and constructive feedback
- Communicates vision and supplies leadership and management to their Production departments in order to attain corporate goals in quality, manufacturing cycle time, and total cost
- Establishes and implements performance standards for department members and performs ongoing evaluation for each department member
- Assists in the recruitment and selection of Production department members
- Manages vacations and work hours
- Counsels members in accordance with company policies with issues relating to conduct and performance issues. Assists with recommendation and implementation of disciplinary actions
- Review performance of personnel as required and documents required performance enhancement plan as needed or any other disciplinary actions that may be required
- Serve as a manufacturing technical expert for identified manufacturing processes. Continually review process and results, anticipate problems, and trouble-shoot processes and equipment with the assistance of other support groups
- Ensure that all quality and regulatory guidelines are followed and that proper records exist and are properly maintained
- Understand validations of processes and machinery following ISO 13485 guidelines. Responsible for maintaining financial budgets for areas of responsibility. Provides recommendations to develop both capital and expense budgets
- Supports the Affirmative Action program (AAP) goals of the company in all personnel interactions
- Demonstrates Thermo Fisher Scientific values – Integrity, Intensity, Innovation, and Involvement
- Bachelor’s degree from accredited college or university or equivalent experience within operations production management
- Leadership capability through proven work or official management experience
- 2-5 years of experience or equivalent combination of education and experience
- Related experience within a manufacturing/ regulated industry
- Exposure to quality systems (ISO 9001, 13485 standards) or FDA
- Thorough understanding of manufacturing processes
- Proficient in use of Microsoft Office tools (Word, Excel, etc.) and other similar software
- Ability to problem solve and work efficiently under pressure
- Lean Six Sigma experience preferred
104
Manufacturing Supervisor, st Shift Resume Examples & Samples
- Plan milling operations, establish priorities, sequences and prepare schedules for milling work
- Perform quality control testing on in-process materials to determine performance to standards
- Inform maintenance of all necessary repairs and equipment malfunctions
- Utilize data-based computer programs to perform cycle count, milling transactions, and test scheduling
- Utilize computers control systems including operational automations and SAP systems and train operators on the use of these systems
105
Manufacturing Supervisor Resume Examples & Samples
- Lead and direct activities and technicians in carrying out manufacturing activities
- Develops technicians to improve on individual and overall manufacturing and development activities
- Facilitates in-house training for process technicians on existing process equipment and manufacturing operations
- Makes recommendations to revise/enhance training curriculum
- Develops training materials and communicates observations during training sessions
- Resolve minor manufacturing issues and bring to the attention of engineering and QA staff as appropriate
- Work with project team to schedule activities and technicians for manufacturing operations
- Issue production forms and request batch records required for unit operations
- Perform daily review of production documentation for accuracy and completeness
- Process equipment cleaning, set-up, and operation, as well as component assembly and aseptic operations
- Follow written procedures, document all work in writing, and maintain safe work environment
- Perform additional activities to support cleanroom operations, such as stocking supplies, water sampling, and environmental monitoring. Work requires high level of interaction with team members, including technicians, supervisors, engineers, and QA personnel
- Bachelor’s degree in life sciences, biotech, pharmaceutical preferred
- Must be able to work evening or night shifts
- Willing to work overtime or different shift schedules
- Able to sit or stand for two to three hours at a time
- Must be able to lift up to 50 lbs and push/pull up to 70lbs
- Basic computer skills a minimum; knowledge of MS Word, Excel, Outlook preferred
- Must be able to speak and write in English
- At least 6 years supervisory experience is required. GMP experience in pharmaceutical manufacturing or related industry is preferred; aseptic manufacturing a plus
- Knowledge of cGMPs
- Experience in training manufacturing technicians, coaching, and providing feedback
- Attention to detail, keen observational skills and good listening skills are necessary
- Must be self-motivated, resourceful, flexible, and responsible with follow-through and conflict-resolution skills
- Must have good verbal communication skills and be able to read and follow detailed written instructions and document activities in writing
106
Manufacturing Supervisor Resume Examples & Samples
- Ensures partner development and satisfaction. Provides partners with timely performance feedback
- Serves as a technical expert and coach for team members. Supports partners in presenting ideas for improving the efficiency and productivity of operations
- Reports all incidents immediately and will not move the scene of an incident
- Wears all required Personal Protective Equipment (PPE)
- Obeys all facility traffic control devices
- Does not alter or bypass any safety device
- Does not use or work on equipment unless I am authorized
- Follows lock out-tag out (LOTO) procedures
- Follows dock lock procedures
- Manufacturing or related functions (1 year)
- Knowledge of business requirements management- Familiarity with British Retail Consortium (BRC), Good Manufacturing Practices (GMP), and Hazard Analysis and Critical
- Control Points (HACCP) standards
107
Manufacturing Supervisor Resume Examples & Samples
- 1) Provide mentoring and training to team members
- 2) Maintain compliance with and support of all safety, health & environmental rules/regulations in order to ensure a safe working environment
- 3) Ensure schedule and production commitments are maintained
- 4) Maintain production line efficiency, quality, cleanliness, and safety
- 5) Support a culture of continuous improvement and embrace change and standard methodologies outlined in the Schneider Production System guidelines
- 1) Bachelor’s degree in the field of Engineering, Business or related field
- 2) Knowledge of lean manufacturing/ Six Sigma concepts
- 3) Ability to lead, effectively communicate, problem solve
- 4) Ability to implement process improvements and rally the team to achieve set goals
- 5) Flexibility to respond to shifting priorities and ability to prioritize work with minimal supervision
- 6) Positive, enthusiastic, team player and champion of the business and customers
108
Manufacturing Supervisor Resume Examples & Samples
- Manages scheduling of operator’s workload
- Follows established company procedures and policy
- Exhibits strong leadership skills mentoring staff, evaluating employee performance, dealing with performance & behavioral issues, and hiring safety
- Maintains compliance with and support of all safety, Health & Environmental rules/regulations in order to ensure a safe working environment
- Conducts team safety meetings
- Ensures Quality-Product and Service
- Maintains strict adherence to documented processes and eliminating process variability
- Ensuring schedule & production commitments are maintained (On Time Delivery)
- Responsible for supporting the Schneider Production System
- Supports a culture of continuous improvement and embraces change and best practices outlined in the SPS guidelines
- Monitor all appropriate KPI and reporting
- Maintains production line efficiency (DVC), quality, cleanliness, and safety
- Strong Customer Focus
- Counsels employees and administers reward or disciplinary action depending on situation
- Assists in proper coordination of company policies and procedures regarding compliance with such legal activities as the OSHA, Equal Employment Opportunity, Affirmative Action Program and all aspects of Discrimination and Sexual Harassment
- Other duties as required due to the needs of the business
- A four-year degree preferred in Engineering, Business or other related field
- Minimum 5 years’ experience in a leadership assembly/production position preferred
- Must have prior experience in an electrical environment and be familiar with electrical principals
- Solid knowledge of lean manufacturing concepts (six sigma certification a plus)
- Strong knowledge of Schneider products, solutions and business a plus
- Competent level computer skills to include Microsoft Office: Excel, Word, Power Point, Lotus Notes, Access
- Must be willing to grow quickly within the organization
- Proven ability to take personal ownership of issues and drive results
- Excellent organizational, problem solving, time management, communication, decision-making and relationship management skills. Demonstrated leadership abilities
- Flexibility to respond to shifting priorities and ability to prioritize work with minimal supervision
- Very strong interpersonal skills – including strong conflict resolutions skills
- Ability to envision team improvements and rally the team to achieve them
- Positive, enthusiastic, team player, champion for the business and our customers
109
Manufacturing Supervisor Resume Examples & Samples
- Bachelor’s degree
- 3-5 years supervisory experience in a manufacturing environment
- Must be able to communicate effectively, both oral and written form, among different levels of the organization and have the ability to communicate with employees who use English as a second language
- Must be a team player and be committed to company goals, policies, and procedures
- Knowledge of Microsoft Office Suite, especially Excel and Outlook
- Must be detail oriented, a self-starter and have the ability to follow initiatives through to resolution
- Well organized with a demonstrated ability to handle multiple tasks simultaneously
- Knowledge of OSHA and safety requirements a plus
- Lean 6σ experience preferred
- Must be able to stand and/or walk for much of a 12 hour shift
- Supervisors are regularly exposed to heavy machinery, noise and cutting fluids
- Occasional lifting of up to 50 pound may be necessary
- Must be able to climb a ladder or stairs, kneel and/or crawl occasionally
- Supervisors are required to use a computer throughout the day
110
Manufacturing Supervisor Resume Examples & Samples
- May assign work to meet daily manufacturing requirements
- May audit Standard Work Practices for each area and regularly reviews them for effectiveness through team meetings and practice
- Daily preparation of shift reports
- May control labor and material usage to meet or improve standard costs
- May coordinate workflow with Production Control
- Minimum one year supervisory experience in manufacturing environment
- Must be able to work a PM or overnight shift
- Must be able to work 12 hours shifts (night or day shift), overtime is required to meet internal and external customer requirements
111
Manufacturing Supervisor Resume Examples & Samples
- 3 + years experience in a supervisory role
- 2 + years developing process improvements to the production process
- Have the ability to work 2nd shift
- Ability to motivate and team build
- ISO experience
- Production assembly experience
- Six Sigma/Lean manufacturing experience
- Electrical distribution product experience
112
Manufacturing Supervisor Production Operations Resume Examples & Samples
- Plan / establish schedules, and assign work while considering requirements and priorities
- Coordinate the most effective utilization of staff and equipment in order to cost-effectively achieve objectives while concurrently implementing efforts to continuously improve performance
- Resolve semi-complex technical problems and/or human resources issues, and work with Senior Supervisors and/or Human Resource Representatives to resolve more complex issues
- Review equipment capabilities, methods, & processes; make recommendations regarding feasibility of utilizing alternative approaches, which may include modifying or replacing equipment to reduce costs and/or improve quality
- Manage & document employee performance, and develop associated recommendations
- Requires thorough knowledge of skilled trades and related functions, and ability to resolve problems
- Errors typically result in delays and inefficient use of resources
- Complex or controversial issues are subject to review before implementation
- Bachelor’s degree and 2 years of professional experience in manufacturing and/or military environments; OR
- Exposure to ERP and Workforce Management software applications (e.g. SAP, Kronos, etc.)
- Flexibility with shift assignment
113
Manufacturing Supervisor Resume Examples & Samples
- A minimum of six (6) years of supply chain related experience is required
- A minimum of two (2) years of manufacturing experience is preferred
- Demonstrated experience as a lead or supervisor is preferred
- Knowledge of FDA regulations and JIT practices is preferred
- Must be computer literate in E-Mail, word processing and spread sheets is required
- Must be detailed oriented and have the ability to develop and meet deadlines, and be able to delegate and follow-up
- Strong verbal and written communication skills required as well as skills in the following areas: Conflict Resolution, Managing for Performance/Accountability and documenting issues, as well as developing leadership and ownership in individualsAdministration
114
Manufacturing Supervisor Resume Examples & Samples
- Production experience in 3M Film manufacturing processes
- Any leadership experience such as supervisor or lead person assignments
- Position requires advanced knowledge of process equipment such as coaters, slitters, reactors, reactor systems, dryers, instrumentation/controls, etc
115
Manufacturing Supervisor Resume Examples & Samples
- Minimum 5 years manufacturing plant experience
- Good interpersonal, communication, prioritization, organizational skills, and computer skills
- Self-directed and detail oriented
- Ability to identify and resolve process and product issues
- Ability to communicate clearly and concisely and influence changes with operators as well as other plant employees and management team members
- Ability to produce results through continuous improvement methodologies (e.g. lean six sigma) and provide impact through cost reduction programs, quality improvements, and safety of work environment
- Bachelor’s degree, BS in engineering preferred
116
Manufacturing Supervisor Resume Examples & Samples
- Direct supervision of 40 to 60 employees across multiple work shifts
- Maintain and enforce safe work practices
- Perform resource planning requirements and scheduling of work hours and time off requests
- Receive predetermined assignments subject to a moderate level of control and review
- Plan and coordinate production order transitions between shifts and between manufacturing departments
- Lead continuous improvement projects, i.e. Kaizen events
- Understand and maintain complex manufacturing order management systems
- Facilitate manufacturing teams toward the achievement of business and customer objectives
- Coach and train teams in the philosophy of continuous improvement and waste reduction concepts
- Foster an environment that instills pride and ownership by all employees
- Evaluate employee performance on a continual basis and provide continuous performance feedback
- Develop a motivated employee base through rewards and recognition linked to accomplishments
- Provide leadership in the support of best practices and compliance to procedures and specifications
- LEAN Six Sigma Green Belt certification
117
Manufacturing Supervisor Resume Examples & Samples
- Ensuring that the production lines operate efficiently, safely, and manufacture a high quality product
- Training – Supervisors are responsible for the delivery of both technical and additional training programs
- Employee Relations– the Supervisor plays a role in the engagement of manufacturing personnel in terms of leading, coaching, and promoting the values of the business. All Supervisors must be mindful of what a workplace culture is and how to maintain it in a positive manner
- Ensure that the Unilever’s policies (handbook) and procedures are communicated and understood. Disciplinary actions, when necessary, should be administered in a way that is consistent with the coaching approach of the business. The Front Line Manager (“FLM”) is a management professional with a good technical understanding of manufacturing, general or chemical engineering or food technology. FLMs have proficient mechanical skills and display excellent personal qualities
- Provides the governance function for a cluster of semi-autonomous teams, delivering management and leadership support for performance monitoring, overtime allocation, working patterns and dispute resolution. The FLM retains responsibility for the Technical and Basic Operators within the semi-autonomous team, but is not involved in the day to day team management beyond the monitoring and performance management role
- Leading improvement projects for operational processes, FLMs have a strong understanding of the end to end manufacturing process. This includes the chemical and electro-mechanical processes and controls. She/he is able to interpret technical diagnostics, identify key issues and process risks. FLMs possess the leadership skills to act with speed and rigor
- Understanding the factory’s financial situation and uses their training in WCM methodologies and IP processes to drive the semi-autonomous team’s work to counter losses and eradicate waste. They lead project work to support factory initiatives. Skills for problem solving, coaching and innovating are central to the role
- Provide a common standard of communication and engagement across the factory. They liaise closely with the core factory functions, including Manufacturing, HR, Quality and Safety to achieve this
118
Manufacturing Supervisor Resume Examples & Samples
- Develop, coordinate and execute daily Production plans to achieve all internal and external customer commitments
- Direct and supervise non-exempt employees to ensure correct, accurate and timely completion of production and delivery schedules
- Drive Continuous Improvement in areas including safety, quality, lead time, and in-process inventory
- Select, train, and ensure optimum performance of direct reports and support these efforts with production floor employees
- Complete meaningful and timely APEX performance reviews and performance feedback to include positive and corrective actions
- Plan for and monitor the development of staff and self
- Recommend and implement measures to improve production methods, equipment performance, and quality of product by participating in Kaizen activities
- Identify opportunities for Continuous Improvement, ensure that continuous improvement activities are planned, implemented, measured, reported and reviewed in the respective area of responsibility
- Correct and improve actions in the respective area with regard to employee satisfaction
- Manage & approve time of subordinates utilizing timekeeping system, including managing overtime
- Supervise assembly, warehouse, packaging and/or international/OEM shipping personnel
- Lead recruitment, on-boarding, training and development and performance management efforts for all direct reports
- Ensure staff is trained and implements all regulatory compliance and all technical competency requirements
- Support the day to day management of staff by team leads to complete assigned tasks
- Analyzes and adjusts work procedures for maximum efficiency
- Bachelor’s Degree preferred with demonstrated success in a supervisory or leadership position
- 3 - 5 years of experience planning and executing the activities of a manufacturing organization
- High energy and drive to make improvements in a manufacturing environment
- Excellent organizational and computer skills
- Ability to motivate people and determine best placement of personnel to accomplish department goals
- Ability to understand and implement production and inventory control techniques
- Ability to work successfully in a team environment
- Excellent Oral and Written communication skills
- Proficiency using general business computer applications such as Microsoft Office, and ERP systems
- Strong production scheduling/planning experience in make to stock and make to order environments
119
Machineshop Manufacturing Supervisor Resume Examples & Samples
- Manage production efficiently and to schedule in accordance with plan
- Support costs and headcount in line with company business plan
- Ensure coordination with planners to execute Production Plan on a daily, weekly and monthly basis advising most effective route to OTD
- Identify and communicate technical production challenges which may impact OTD, make recommendations on corrective actions and implement preventative measures
- Compile daily productivity reports, identify discrepancies between planned versus actual and communicate with recommendations to Workshop Operations Manager
- Implement and deliver relevant KPI's in Safety, Quality, Cost, Delivery and Workforce engagement
- Drive improvements in production processes using defined lean and continuous improvement methods and standardised processes and procedures
- Identify constraints and bottlenecks in workflow/planning processes that adversely impact on customer delivery deadlines
- Ensure departmental compliance with all controlled documentation
- Development of training and coaching plans for direct reports promoting cross functional skills
- Supervise and motivate your team and review performance
- Ensure all company policies / procedures are adhered to and enforced by department supervisors
- Travel as and when required
- Support other departments and carry out other duties as and when business requirements dictate as may be reasonably expected by line manager
- Time served engineer and/or HNC equivalent in an engineering discipline
- Degree in Production Manufacturing
- Good working knowledge within engineering/manufacturing environment
- Good working knowledge of leading engineering production teams
- Working knowledge within a continuous improvement and process led environment
- Working knowledge of implementing and tracking individual and team metrics
- Good working knowledge within oil and gas manufacturing environment
- Computer literacy (including good command of Microsoft Office Excel, Word and Outlook)
- Working knowledge and technical understanding of ISO CNC machine code
- Proven technical understanding of Horizontal Turning with the use of steadies
- Proven technical understanding of Vertical Turning
- Proven technical understanding of milling applications
- Proven technical understanding of Horizontal Boring applications including contouring heads and internal profiling bars
- ERP knowledge such as Oracle, Emax
- Continuous Improvement Techniques including Kaizen, Lean, Kanban
- 5 Whys
- Working knowledge of weld clad processes
- Working knowledge of EdgeCAM CAD/CAM software
120
Manufacturing Supervisor Resume Examples & Samples
- Responsible for the effective use of personnel, material, and equipment
- Meets production schedule, cost goals and quality requirements
- Understands and consistently administers National and Local Agreements; participates in local labor relations activities
- Implements divisional and corporate policies
- Ensures employees perform job responsibilities and empowers them to continuously improve their work by managing and eliminating constraints
- Reduces waste by identifying and improving value-added tasks and eliminating non-value added tasks
- Builds and maintains good working relationships with employees, union and management
- Keeps management informed of developments as they occur
- Maintains corporate and unit management control systems
- Maintains department records
- Knowledge of scheduling and other management systems
- High level interpersonal skills to work effectively with all levels of the organization, motivate employees and elicit work output
121
Manufacturing Supervisor Resume Examples & Samples
- Bachelor Degree in Engineering
- Minimum of 3 years of manufacturing experience at Technician/Engineer level
- Good knowledge in inter personal communication
- Able to lead and motivate subordinates to achieve organizational goals
- Effective team building
- Posses effective analytical and decision making skills
122
Senior Manufacturing Supervisor Resume Examples & Samples
- Bachelors degree in engineering or related field required
- Minimum 5 years experience in a manufacturing environment or similar position is required
- Experience with machining including milling and turning of both metals and plastics strongly preferred
123
Manufacturing Supervisor Resume Examples & Samples
- Supervise Manufacturing Operations to ensure that the products are produced in a safe and timely manner which meet or exceed all specifications, quality standards, HPRA & FDA regulations and other Health Authority guidelines
- Maintain Documentation pertaining to the Manufacturing operation to the required GMP Standard
- Maintain Health, Safety and Environmental requirements to Company and Legislative Standards
- Participating in cross-functional teams to improve systems and procedures throughout the plant
- Be flexible and provide support to all other areas i.e. Assembly and Pack
- Any other duties as assigned by Manufacturing Manager/Director
- At least 3 years people management experience in as a Team Leader/ Supervisor within the Pharmaceutical Industry
- Experience with Dry Powder Inhalation processes is desirable
- Experience of Dispensing, Blending and Filling of Dry Powder a distinct advantage
- Experience or exposure to LEAN Manufacturing tools and techniques a distinct advantage
- Strong Leadership, Team working, communication and analytical skills
- Strong PC Skills including MS Word, Excel , Powerpoint etc
- Proven track record in using methodical approaches to problem solving and able to identify and implement improvements
124
Manufacturing Supervisor Iii Temporal aÑo Resume Examples & Samples
- Engineering degree or equivalent minimum required
- From 4 to 6 years of experience as production supervisor, 3 years in medical industry is preferred
- Basic knowledge of Lean Manufacturing, Quality Control and Production Control
- Working knowledge of computer software (Microsoft Office, **JDE system)
- Good leadership and team working skills
- Basic knowledge of Mexican labor regulations
- Bilingual in English and Spanish preferred
125
Manufacturing Supervisor Resume Examples & Samples
- Provide manufacturing, process, and team support, direction, expertise and effort in specific manufacturing areas. Focus is on meeting plant and team objectives in safety, quality, productivity, delivery and cost
- Strive to reach fill rate and productivity goals using an operational excellence approach and lean methods
- Plan, initiate, determine, and schedule manpower to meet production requirements of customers, provide quality product, and assure schedules are met
- Coordinate with engineering, maintenance, and others in solving problems that occur to assure a quality product is produced in a timely manner
- Coach and develop employees to problem solve and utilize the available tools to continuously improve
- Conduct meetings to maintain employee / employer relations, encourage employee engagement, and promote improved communication
- Assure employees are trained on assigned jobs, use tools and equipment in a safe and proper manner, and maintain a clean working environment
- Complete and maintain necessary records
- 3-5 years of managing teams in a machine manufacturing environment
- Bachelor’s degree in related field preferred or equivalent experience
- Proficient in the Microsoft Suite (Outlook, Excel, Word, and Power point)
- Proficient in reading blueprints
- Must be able to manage effectively and exhibit strong technical aptitude
- Must enjoy working in a fast-paced, multi-faceted work environment
- Oracle software experience preferred
- Experience supervising a union work force would be beneficial
- Distribution warehouse experience would be beneficial
126
Manufacturing Supervisor Resume Examples & Samples
- Maintain department/cell metrics utilizing visual management techniques. Ensure all direct reports understand their cell metrics and how they impact/improve each metric. Prepare associates to lead the report-out of metrics weekly to management
- Develop and adhere to leader standard work. Monitor/update/approve standard work for department/cell team leads and audit adherence to standard work for production associates
- Use personal computer and mainframe programs to obtain, organize, and analyze data and to prepare charts and reports. Software skills required in word processing, spreadsheet, and SAP
- Willing and able to work 2nd shift
- Legal authorization to work in the U.S. is required. We will not sponsor individuals for employment visas for this job opening
- Any offer of employment is conditional upon the successful completion of a background investigation and drug screen
- At least 2 years as a manufacturing supervisor preferred
- Previous experience in Printed Circuit Board Assembly a plus
127
Manufacturing Supervisor nd Shift Resume Examples & Samples
- Maintain Costs Associated With Manpower, Supplies, & Scrap
- Achieve Attainment and Efficiency Through Managing Manpower
- Team With Materials, Assembly, & Other Shift Supervisors To Beat On
- Time Delivery Goals
- Ability To Manage Multiple Tasks / Assignments
128
Manufacturing Supervisor Resume Examples & Samples
- Actively lead, train, and develop hourly personnel in operations
- Meet and or exceed plant business goals/objectives
- Plan and manage resources to meet period business goals
- Manage Lean System Team training/facilitation and leadership
- Ensure proper training for new hires & current employees
- Manage daily work activity conformance to quality and GMP standards
- Maintain staffing schedules
- Ensure company policies, procedures, and work rules are being followed
- Actively attract, train, develop & retain effective personnel to ensure an efficient, motivated, and muti-skilled workforce
- Manage cross-functional team capability and capacity
- Ensure a safe working environment. Encourage personnel to work safely, preventing injuries and lost time
- Facilitate cross -functional team meetings within an environment of trust and high involvement
129
Manufacturing Supervisor Resume Examples & Samples
- Lead, develop and mentor the QA team to achieve a high performance team oriented environment
- Meet or exceed QA goals objectives
- Ensure superior customer service & foster a customer service environment
- Foster an atmosphere where safety is a priority with an emphasis on protecting company assets and preventing injuries
- Ensure proper distribution through proper frequencies & proper package and brand management
- Ensure proper training of new hires and ongoing training of current employees
- Maintain CCBCC quality standards
- Foster and build positive employee morale
- Should have knowledge of Quality Assurance in a manufacturing environment
- Should have lab experience and understanding of a laboratory environment. Should have experience dealing with equipment used in the lab
- Should have 1 to 2 years experience in management or leadership role
- Ability to work a flexible schedule (includes some weekend/holiday responsibilities)
- Must have good PC skills. Proficiency in Microsoft Word & Excel is strongly preferred. Experience and Proficiency with SAP is a plus
- Should understand/troubleshoot water treatment systems
- Excellent prioritizing, organizing & decision making skills required
- Dynamic communication skills with the ability to communicate with all levels of management & personnel
- College Degree is strongly preferred. Emphasis in Biology, chemistry, food science or Quality Assurance is preferred
- An excellent safety record
- Must have an excellent quality record & experience in managing quality control
- Must be self-motivated, positive, have a high degree of integrity, dependability & participate as a team member to achieve common goals with sense of urgency
- Should have strong math and problem solving skills
- Previous experience in a sanitation procedures
- Should have general knowledge in basic Chemistry and Biology with emphasis of experience with alkaline and acidic chemicals
130
Manufacturing Supervisor Resume Examples & Samples
- 5-10 years manufacturing operations management experience in a LEAN environment required
- LEAN certification preferred (Green Belt, Black Belt)
- A passion for employee development and improvement
- Excellent Team Building Skills for diverse groups
- Excellent written and verbal communications skills and ability to communicate with those at all levels
- Strategic Planning experience preferred
- Moderate to heavy physical effort moves/lifts heavy equipment/supplies
- Prolonged extensive, or considerable standing/walking
- Lifts supplies equipment up to 35 pounds
- Pushes/pulls or moves/lifts heavy equipment and supplies
- Manual dexterity and mobility
- Considerable reaching, stooping, bending, kneeling, crouching
- Moderate exposure to warm temperature and humidity variations throughout the year
131
Manufacturing Supervisor Resume Examples & Samples
- Prior experience in a Manufacturing or Logistics environment
- Ability to multitask, work in a fast paced environment and think quickly on your feet
- Must be able to work 9 hour shifts (night or day shift), to include overnight shifts
- Ability to perform other duties as assigned
- Bachelor’s Degree in Engineering, Business, Operations or other related fields
- Experience with a Computer Inventory System
- Supervisory experience in manufacturing environment
- Experience working in a transportation or logistics role
- Previous experience in a heavy industrial environment
132
Manufacturing Supervisor Resume Examples & Samples
- BS – Industrial. Electrical, Mechanical Eng. or any Management related subject
- Bilingual, speak and write Spanish and English
- Minimum 3 years supervisory experience in a manufacturing environment preferably with molding knowledge
- Technical knowledge: human relations skills, electronic / mechanical experience, knowledge of precise measure equipment. Ability to show leadership, sell ideas and make changes. Good at problem solving and decision-making. Good manufacturing practices. Computer knowledge
133
Manufacturing Supervisor Resume Examples & Samples
- Be able to follow engineering prints and specifications
- Know proper use and care of manufacturing equipment
- Basic knowledge of Lean Mfg., any certification is a plus
- Be able to use computer as necessary to obtain specifications and prints
- Understands and can work within
- High School diploma, minimum requirement
- 2 years’ experience in a similar role
134
Manufacturing Supervisor Resume Examples & Samples
- Direct supervision of Manufacturing Associates, including Test, Conformal Coat and SMT groups
- Conduct performance reviews of Manufacturing Associates
- Discipline of manufacturing associates
- Structure workflow (prioritization)
- Manage product schedules
- Ensure productivity and quality standards are met
- Identify and submit changes for process improvements
- Structure workflow
- Assist other supervisors/managers in their duties ensuring company goals and objectives are met
- Maintain safe and respected work environment
135
Manufacturing Supervisor Resume Examples & Samples
- Direct supervisor of hourly employees on assigned shift
- Maintains production records for production counts and standard hours
- Completes GEMBA board daily for assigned department
- Monitors productivity indicators and initiates improvement efforts to avoid unfavorable variances
- Responsible for production runs, proper die setting procedures, quality of product and maximizing the department’s full potential
- Recommends disciplinary action for all hourly employees as needed
- Completes Corrective Action plans on all external and internal rejections for quality
- Ensures housekeeping and 6S initiatives are completed and met for department
- Complies with and enforces all safety rules, regulations and policies for employees
- Completes accident investigation forms timely, participates in investigations and is a part of solutions for improved safety for all near miss, recordable or lost time incidents
- Proactive with continuous improvement projects, processes and systems for department
- Communicates timely with Production Manager and management team any difficulties or issues that arise due to condition of machines, employee actions, quality problems
- Provides back up to other manufacturing supervisors
- Participates in employee involvement actives
- Provides training as needed/required to employees
- Able to work weekends as needed
- Bachelor’s degree in manufacturing, management or engineering preferred
- Supervisory experience 3+ years, manufacturing experience preferred
- Experience in metal stamping or forging environment preferred
- Computer skills in Microsoft office, particularly Word and Excel
- Knowledge of basic manufacturing, quality and safety practices
- Basic mathematical understanding and ability (add, subtract, divide units of measurement)
- Good communication skills, verbal and written
- Good computer knowledge
- Ability to stay focused on work and manage multiple projects timely
136
Manufacturing Supervisor Resume Examples & Samples
- Operation knowledge of Grand Format digital printing
- Create die files, proofs, and plates. Import, trap, bleed, and color separate production files for proofing & printing. Scan, create art and typeset artwork as needed
- Operate and maintain Mac, Mac file server, proofers, printers, RIP
- Perform color correction to process color files for offset and Digital presses
- Work closely with customer service reps, press operators, and occasionally with sales and/or customers
- Follow ISO, Safety, Standard Operating procedures and general housekeeping requirements
- Record time and materials accurately
- Work in a neat, orderly manner, maintain supply levels, and request repair of equipment as necessary
- Maintain equipment -general minor maintenance
- Effectively present information in one-on-one and small group situations to customers, clients, and other employees of the organization
- Ability to resolve and solve problems with minimum supervision
- Must be able to communicate in basic English; read, write and understand
- Read and comprehend complex instructions, short correspondence and memos
- Advanced PC Skills
- Lead/Supervisory experience
- 5-7 years Mac experience required in a manufacturing environment
- 3-5 years operating and supervising employees in a Digital Print environment, Grand Format experience preferred
- Advanced process color experience is required. Color correction and proofing experience a plus
- Process color and reproduction experience is a must. Color management experience a plus
- Resolve daily safety, quality, and production concerns
- Administer quality corrective and prevention action program for hourly shift employees
- Administer attendance program for hourly shift employees
- Participate in plant focus groups: safety, quality, and productivity
- Perform annual performance reviews for hourly shift employees
- Conduct department shift meetings, as needed
- Respond to production issues (in-house) telephone, email
- Interact with other departments for service, quality, and staffing
- Adheres to and promotes all safety policies and procedures including, but not limited to the proper handling of hazardous waste, lock out- tag out rules and hearing and eye protection policies
- Performs other productivity improvement projects, related duties, and participates in special projects as assigned by manager
- It is the responsibility of all employees to follow the requirements of their documented process as defined in the ISO Quality Manual
137
Manufacturing Supervisor Resume Examples & Samples
- Management of approximately 30-35 direct labor employees
- Responsible for meeting internal and external customer delivery and quality targets
- Ensure the smooth running of the production processes
- Ensure that safety policies are adhered to
- Work closely with Engineering, Purchasing, and Quality to resolve issues that may impact the customer
138
Manufacturing Supervisor Resume Examples & Samples
- Provides immediate supervision to a unit or group of employees, assigning tasks, checking work at frequent intervals, and maintaining schedules
- Initiate Facility Work Orders when equipment requires repair
- Maintain current knowledge of regulatory and industry standards
- Generate thorough written reports, when required, that summarize investigations performed for out-of-specification results or out-of-procedure events
- Provide a leadership role ensuring employee health and safety
- Involved in interviewing/selection process of hiring or promoting department personnel
- Associate’s degree required. Bachelor's degree preferred. Emphasis in Biology, Chemistry, Chemical Engineering or closely related scientific / technical discipline is preferred
- Minimum of 2 years of related experience in a pharmaceutical, GMP, or FDA regulated environment is required
- Equivalency: In lieu of an Associate's degree, candidate must have a High school diploma or GED, and a minimum of 4 years of related experience in a pharmaceutical, GMP, or FDA regulated environment
- Prior supervisory or leadership experience is highly preferred
- Comprehensive knowledge and understanding of cGMPSs, FDA regulations, and industry guidelines
- Ability to effectively prioritize and manage multiple tasks to meet targeted deadlines
- Must be flexible with working hours / shifts in order to accommodate the 24 hour, 7 day plant operation
- Ability to stand for extended periods - up to four (4) hours at a time
- Manual dexterity to perform all job functions
- Exposure to toxic/caustic chemicals and biological hazards
139
Manufacturing Supervisor Resume Examples & Samples
- Manage time between the office and shop floor operations
- Provide guidance and leadership to employees and serve as a mentor for their day-to-day activities
- Identify reasons for variation in individual performance and take appropriate action that will result in improved performance
- Analyze data to guarantee key performance measures are met, while aiding in the removal of waste
- Maintain proactive communication with support teams to ensure efficient, accurate and timely responses to internal/external customer needs
- Responsible for sustaining and enhancing processes and procedures utilizing core lean tools
- Responsible for observing processes and Ensuring all employees are following Standard operating procedures and standardized work
- Work with other managers and operators to establish improved processes
- Responsible for coaching and enforcing Standards and ploicies of current and future best practices
- Monitors quality and production and holds employees accountable for meeting and exceeding expectations
- Must be willing to work any shift
- Must have excellent people skills
- Must be skilled in public speaking, interpersonal, and written communications
- Must be able to have constant interaction with direct reports
- Must be self-motivated
- Must possess leadership skills, and be willing to drive innovation and change
- Must be detail oriented while working in a fast–paced environment
- Must have an aggressive approach to improvements
- Must be willing to work as part of a team
- Must have good computer and writing skills
- Two (2) year technical degree. (Required)
- Must have five (5+) years of proven leadership and or supervisor experience in any field
140
Manufacturing Supervisor Resume Examples & Samples
- Oversees all work activities and personnel of the assigned area
- Establishes work schedule and develops cost effective plan to meet store goals
- Maintains equipment and machinery
- Supervises personnel and ensures adherence to company and department policies and procedures; performs personnel management duties including hiring, training, completing disciplinarian, etc
- Monitors all costs and inventory levels
- Ensures excellent customer relations and satisfactory services are provided
- Completes various reports and maintains records as needed
- Performs other related duties as necessary
- Minimum education required—High School Diploma with 2 years of additional advanced training in building materials component production and assembly
- Special skills required—Proficient comprehension of measurements and basic math principles. Understanding of the operation, troubleshooting and repair of related machinery and equipment. Should possess excellent oral communication and interpersonal/ customer service skills. Knowledge of inventory control, negotiations and purchases. Must be computer literate
- Other—Ability to perform all physical aspects including repetitive lifting up to 100 lbs, stooping, twisting and bending. Performing various duties throughout manufacturing process for training and relief purposes
- Minimum experience required—2 years of supervisory experience in the building materials industry with an emphasis in component production and assembly. Managing a workforce of up to 15 subordinates
141
Manufacturing Supervisor Resume Examples & Samples
- Assign employees to work stations, making adjustments at the start of and during each shift in accordance with production schedule, customer priorities, company policies and current production requirements
- Interpret Company policies and production procedures to shift personnel and assure they are followed
- Solve problems as they arise on shift and make decisions based on Company policy
- Direct and oversee proper production and quality records
- Review production reports to take corrective action or advise management of necessary steps to maintain proper quality and quantity
- Conduct department interviews, present department orientation and oversee training of all new shift employees
- Recommend and implement disciplinary action on shift employees according to Company policies after reviewing all the circumstances
- Implement Company safety policies and procedures and promote 5S and good housekeeping practices for department facilities
- Promote continuous performance and quality improvement efforts, monitoring and reporting processes
- Promote Company philosophy and be available and approachable to all department employees
- Participate in and facilitate monthly safety and communication meetings with department personnel
- Coordinate and cooperate with other departments to help meet Company goals and objectives
- Keep the Manager informed, on a timely basis, of department activities and any problem situations
- Perform any other task necessary for the smooth operation of the department as a whole
- Ability to read, write and do basic math. Some post-secondary training or education desired
- Seven to ten years manufacturing or production experience with at least three of those years in a supervisory role to include distribution of work, scheduling, training, answering of questions related to work, assistance in problem solving, performance management and discipline
- Intermediate level proficiency with MS Excel, MSWord, AS400 data retrieval and entry and ERP (JD Edwards preferred)
- Strong mechanical aptitude and problem solving skills highly desired
- Continuous improvement certification or training a major plus
142
Manufacturing Supervisor, Cast Components Resume Examples & Samples
- Requires a bachelor’s degree, preferably in a Technical Engineering Field, MBA or related Master’s degree strongly preferred
- Ability to teach, mentor, and coach across multiple levels of an operation (shop floor to plant manager) so that the customer can maintain and improve standard developed through kaizen events
- Strong Leadership and Change Agent skills. Able to overcome obstacles using positive facilitation, teamwork, and influence through building and maintaining relationships
- Proficiency in Microsoft Office suite: Word, Excel, PowerPoint, Viso (Access Preferred), SharePoint preferred
143
Manufacturing Supervisor Resume Examples & Samples
- Coordinate daily production activities to meet safety, quality, productivity, on-time delivery targets and revenue
- Identify material/capacity constraints and resolve issues, including material shortages, prioritizing support functions (receiving, inspection, mfg. engineering, etc.) and escalating issues
- Ensure that safe work practices are in use at all times including teams adherence to Personal Protective Equipment (PPE) requirements of the job function (i.e. safety glasses, ESD protection)
- Responsible for ensuring accurate material transactions from the team in Intuitive
- Manage daily cycle count activities and participate in reconciliation efforts
- Ensure production activities are completed in accordance with design and process documentation
- Lead daily production meetings and assist with creating and publishing daily/weekly/monthly tracking metrics
- Assist with training and coaching of the production workforce (through documentation), and with completion of PMD’s for production personnel
- Complete annual Performance Review’s for direct reports
- Participate and lead improvement events (such as Kaizen, 5S, Practical Process Improvement); coach and mentor direct reports to drive PPI as part of standard work
- Work with peer supervisors to consolidate orders and flex resources
- Coordinate, report and manage direct reports paid time off schedules and timecards
- High school diploma or equivalent (college degree or equivalent experience preferred)
- 5+ years experience in a manufacturing environment
- 3+ years experience supervising a group preferred
- Working knowledge of Microsoft Word, Excel, PowerPoint, Outlook and Intuitive
- Experience in lean practices and continuous improvements tools
- Demonstrates problem solving skills and teamwork
- Demonstrated ability to lead by example and to provide guidance and mentoring to peers
144
Manufacturing Supervisor Resume Examples & Samples
- Minimum three years of experience in an FDA regulated medical device manufacturing plant required
- Leadership experience required with strong coaching and development skills that lead to building relationships with employees and other departments
- Ability to express ideas clearly both in written and oral communications
- Ability to supervise diverse groups of people
- Lean Manufacturing experience preferred
- Accountability for your team, foresight to identify and troubleshoot various issues, versatility to be attentive to safety, quality, production and goals, focus on continuous improvement, and empower your team
145
Manufacturing Supervisor Resume Examples & Samples
- Develop and execute a demand-based manufacturing strategy which supports high customer satisfaction while balancing raw material and finished goods inventory levels
- Coordinate activities of QC Technicians, Buyers, Product Engineers, and Process Engineers as their functions impact the team’s area of responsibility
- Direct multi-departmental resources for projects which may include cost reductions, manufacturing process improvements, and corrective action investigations/ implementations
- Identify, develop and implement operational and technical strategies to continuously improve the effectiveness of the manufacturing process to achieve benchmark-class standards
- Be responsible for developing, implementing, and trending process metrics to continuously monitor and improve the manufacturing process
- Be responsible for leading and personal development of the production team including direct labor, production specialists with respect to training, performance management, salary administration, overtime authorization, hiring, firing, administering disciplinary action, and application of organizational policies
- Make staffing recommendations and implementing staffing plans along with providing input to and operating within the departmental budget
- Ensure regulatory compliance while promoting safe working methods and a safe environment
- Contribute to and execute upon capacity studies to ensure high levels of product availability
- Market foresight, learning agility and teaming (RI key competencies)
- Leadership and staff development skills
- Conflict management skills
- Customer relations and teamwork skills
- Interpersonal and influencing skills (across organizational levels)
- Innovation and change mindset
- Planning and organization skills
- Strategic thinking skills
146
Manufacturing Supervisor Resume Examples & Samples
- Good computer skills (MS Word, Excel, PowerPoint, email, and production reporting experience)
- Must be able to read and understand job tickets
- Must have good mechanical aptitude and analytical skills
- Must be able to work in a fast-paced team environment
- Good communication and people skills, both written and verbal
- Must be able to communicate well with both supervisors and employees regarding problem areas and quality concerns
- Must be able to communicate regarding customer and sales requirements
- Must be adept with fractions, decimals, and multiple units of measurements
- Must be able to recognize safety issues and immediately formulate appropriate corrective action
- Must be able to decide and/or recommend whether product should be sent to customer
- Continuously make judgments regarding quality of products
- Must be able to lift, pull, and push 60 pounds
- Required to stand constantly
- Minimum of high school diploma or equivalent, some college or trade school preferred, and/ or five to seven years of supervisory experience in a manufacturing environment
- Demonstrated ability to lead or supervise others
- Previous experience in the operation of a printing press or work in a printing environment preferred
147
MSB Module Manufacturing Supervisor Resume Examples & Samples
- Manage and supervise a production team consisting of skilled operators to meet the department's output, quality and cycle time targets
- Communicate handing/taking over duties/issues between shifts
- Nurture operators' career development through coaching and on-the-job training
- Create and maintain a harmonious and safe working environment that instills teamwork, commitment and ownership in the team
- Work to create a culture of learning and sharing of Best Known Methods to simplify procedures and process flows
148
Manufacturing Supervisor Resume Examples & Samples
- Four year degree or equivalent experience in an industrial environment or equivalent experience
- 4 years supervisory experienceDemonstrated leadership abilities
- Demonstrated ability to develop and deliver concise written and verbal instructions
- PC and PC applications experience
- Experience in product/component design is desired, preferably in the aerospace machining industry
- Proven record of accomplishment regarding ability to facilitate and lead a team(s)
- Supervisory experience in a manufacturing environment, investment casting or other foundry experience preferred
149
Manufacturing Supervisor Resume Examples & Samples
- Monitors product quality and drive continuous quality improvement activity to prevent quality issues. When quality incidents happen. leads root cause / corrective action analysis with direct reports and coordinate corrective actions as necessary
- Ensures that all personnel in his/her area are aware of the importance of Environmental Policy and EMS (Environmental Management System) requirements, their roles, responsibilities, and the potential influences of their work
- Identifies opportunities, propose ideas to minimize or eliminate environmental problems, and participates in the definition of environmental objectives and targets
- Bilingual – English/Spanish
- Bachelor degree in Administration, Engineering or related area
- 2+ years of experience in supervision in a medical device or pharmaceutical environment
- 2+ years supervisory experience
150
Manufacturing Supervisor Resume Examples & Samples
- Must be able to work 9 hour shifts (night or day shift), to include overnight and
- Prior experience in a Manufacturing or Heavy Industrial environment
- Previous experience working in a Union environment
151
Manufacturing Supervisor Resume Examples & Samples
- Supports continuous improvement philosophy driving lean manufacturing principles
- Day to day manufacturing process support of production teams
- Works closely with manufacturing engineers as well as other support groups and direct labor personnel to resolve issues that arise as related to safety, quality, delivery, and cost
- Works closely with HR and management to maintain consistency and fairness in administration of company policy and code of conduct
- Provides necessary talent and resources to the manufacturing process to meet objective goals
- Management of departmental budgets within assigned area
152
Manufacturing Supervisor Resume Examples & Samples
- Bachelor Degree in Engineering Minimum of 1 year of manufacturing experience at Technician/Engineer level
- Able to plan and execute plans effectively. Possesses sound knowledge on relevant company policies and regulations
- Effective team building. Posses effective analytical and decision making skills
153
Cgmp Manufacturing Supervisor Resume Examples & Samples
- Supervise cGMP Biomanufacturing production activities
- Author and revise Standard Operating Procedures (SOP), Batch Production Records (BPR) and Job Aid (JA)
- Maintain effectiveness of Quality system
- Performs Daily review and final sign-off of executed cGMP documentation (BPRs, forms)
- Supervise general cleanroom housekeeping, including room and equipment cleaning(s), disposal of trash and recyclables, and adherence to 5S standards
- Proven leadership abilities; ability to oversee junior staff involvement with deviations and ability to mentor direct reports regarding regulatory requirements
- Ability to transfer knowledge to others via training or mentoring of direct reports; ability to guide others through communication and learning
- Ability to interpret and apply Technology Transfer into BioManufacturing
- Train, monitor and mentor direct reports on Biomanufacturing activities
- Act as Subject Matter Expert (SME) on Biomanufacturing activities
- Supervise continuous process improvement initiatives
- Lead team meetings and/or training sessions
- Coordinate with Manager/Director to prioritize and schedule activities to meet deadlines
- Perform aseptic techniques within in a clean room environment
- Supervise, execute and document cGMP Biomanufacturing activities
- Supervise operation of cGMP Biomanufacturing equipment such as pH/conductivity meters, mixing tanks (SUMs), tubing fusers/sealers, filter integrity testers, peristaltic pumps, balances and BioSafety Cabinets (BSC) or Laminar Flow Hoods (LFH)
- Supervise/Stage raw materials/components for use within cGMP Biomanufacturing
- Supervise completion of routine and preventive maintenance on Biomanufacturing equipment
- Supervise/lead deviation investigations and change control/protocol execution in a time sensitive fashion
- Supervise/execute equipment qualification/validation protocols, as required
- Supervise Media/Solution Preparation, as required
- Ability to work scheduled shift and other off-shift coverage as required
154
Manufacturing Supervisor Resume Examples & Samples
- Select and develop personnel to ensure the efficient operation of the production function
- Develop schedules and manpower requirements for assigned areas
- Receive predetermined work assignments with specific instructions
- Erroneous decisions or failure to achieve results may cause delays in schedules
- Interact daily with subordinates and/or functional peer groups. Interaction normally involves exchange or presentation of factual information
- Provide immediate supervision to a unit or group of employees, assigning tasks and checking work at frequent intervals
155
Manufacturing Supervisor Resume Examples & Samples
- Effective problem identification and solution skills
- Strong interpersonal and leadership skills, including the ability to influence others and lead small teams
- Must have the ability to obtain a security clearance
156
Manufacturing Supervisor, Blood Components Resume Examples & Samples
- Responsible for the daily operations of Manufacturing
- Hire and supervise staff
- Participate in education and training activities
- Ensure compliance with federal, state, Red Cross Blood Services directives and regional policy and procedures and regulations; assure compliance with safety policies and procedures in the work area and use of applicable protective equipment at all times to prevent exposure to potentially infectious blood and body fluids
- Bachelor's degree in science, or equivalent related experience; CLS (or CLS eligible) preferred. Must meet state and CLIA requirements Competencies
- Three year's related experience including at least one year supervisory experience. Related experience includes laboratory experience with MT (ASCP) certifications or equivalent certifications where required. Pharmaceutical manufacturing experience preferred
- Post-training schedule will be 2nd shift Monday thru Friday 3pm-11:30pm. Additional flexibility required to meet changing department needs
- Good communication and computer skills required
- Knowledge of blood products and supplies and the ability to interact with diverse customers is required
157
Manufacturing Supervisor Resume Examples & Samples
- 1 year experience with deviation or investigation management systems
- Bachelor’s Degree in life sciences
- Previous departmental experience in Media and/or Buffer Preparation
- Experienced leading manufacturing teams and adhering to a demanding production schedule
- Experienced authoring and reviewing standard operating procedures, on-the-job-trainings, and
158
Manufacturing Supervisor Resume Examples & Samples
- Able to multi-task and/or willing to take on additional assignments
- Adapts to changes (work plan, priority and management decision) in the work environment
- Supports improvement initiatives and participates actively to improve work environment (example 5S)
- Competent in required job knowledge and skills to perform assigned tasks
- Able to apply new work requirements with minimal supervision
- Able to learn/develop new job knowledge or requirements quickly and to contribute at an effective level
- Consistently completes assignments or work requirements on time without compromising on quality
- Uses time effectively to manage workload/tasks
- Looks for opportunities to improve work productivity and efficiency
- Understands and follows Plexus quality policy guidelines, customer specifications and adheres to regulatory compliance
- Monitors own work to ensure quality standard is met
- Looks for opportunities to improve quality and eliminate waste at work
- Able to work cooperatively in a team & cross functional team(s) as needed
- Able to maintain a level temperament in a stressful environment
- Openly and proactively shares information, knowledge & experience with co-workers
- Responsible for directing the activities of production operators in high volume, quality manufacturing
- Develop and implement action items to meet production schedules, goals and objectives
- Has authority for solving problems encountered during the production process
- This includes quality, output, materials, equipment and personnel issues
- Communicate pertinent information regarding production, quality, or personnel issues to the appropriate team members
- Participate actively in the Direct Labor retention program
- Experience in SMT will be an added advantage
159
Plant Manufacturing Supervisor Resume Examples & Samples
- Works with Plant Management and other Supervisory Staff to assign, direct, review and monitor work of supervised staff to maximize productivity in the plant
- Ensures proper procedures are in place and being followed for, production efficiency, quality of product, employee safety, state and federal guidelines
- Inspects products to verify conformance to specifications and directs setup and adjustments to machines
- Coordinates production schedules and estimates worker hour requirements for completion of job assignments
- Evaluates needs in production for daily assignment of duties; establishes or adjusts work procedures to meet production schedules
- Recommends improvements to production methods, equipment performance and quality of product
- Analyzes and resolves work problems, or assists workers in solving work problems
- Maintains time and production records as required
- Collaborates with other supervisors to coordinate activities of individual departments
- Provide for the supervision of assigned employees in scheduling and daily activities, ensuring effective selection, retention, feedback, disciplinary action and performance management. If a collective bargaining agreement exists, may participate grievances or other contract related activities and discussions
- Trains and instructs employees in regard to production and equipment standards and processes. Oversees instruction, implementation and enforcement of policies as they relate to employees
- Leads by example with the Dean Foods Code of Ethics. This includes following company policies, standards and specifications
- Engages in the typical responsibilities of a manager requiring planning, evaluating, organizing, integrating, and delegating
- Bachelor’s degree preferred, or a minimum of 2 years plant experience
- Familiarity with Good Manufacturing Practices
- Experience leading and following Safety/Security Policies and Procedures
- Experience using Microsoft Office and other computer based applications
- Ability to follow all Sanitation and Quality Policies and Procedures, and report and follow through on any deficiencies
- Proficient in Microsoft Office Suite and computer based applications
- Excellent verbal/written communication skills
- Ability to adapt to changing organizational and operational needs; ability to lead others through change
- Ability to handle multiple tasks simultaneously
- Skill in organization, prioritization, and attention to detail
- Strong team player and leader with the ability to work across multiple functions and disciplines
- Ability to select, coach, develop, engage, and retain a team of employees
160
Manufacturing Supervisor Resume Examples & Samples
- Adheres to all safety policies and procedures
- Ensures all functions of the jobs are performed safely
- Oversees and ensures the safety of all employees
- Follows and leads all Safe Quality Food and General Manufacturing Procedures
- Coordinates and supervises activities of equipment and personnel and assists throughout the facility with a focus on optimizing Safety, Quality, Productivity and Spoilage
- May change shifts and plant departments to cover absences or provide additional support
- Applies knowledge of various processes, production methods and processes
- Oversees quality and recommends modifications of existing quality or production standards to achieve optimal performance within the equipment limits
- Communicates all pertinent information between departments and between shifts on changes to shipping schedules, production schedules, or any other related information
- Works with employees on identifying, discussing solutions and implementing best practices
- Perform and facilitate “on the job training” and/or coaching of all employees as needed or required
- Complete and/or administer necessary documentation such as production sheets, pallet ticketing, job progressions, disciplinary actions, SAFE cards, time and attendance, incident reports and process control sheets
- Communicates with customers, internal and external, corporate, and coworkers in a professional manner both written and verbally
161
Manufacturing Supervisor Resume Examples & Samples
- Coordinates and supervises activities of equipment and personnel throughout the facility with a focus on optimizing Safety, Quality, Productivity and Spoilage
- Manages machinery set-up and adjustment and inspects products to ensure compliance to standards
- Communicates all pertinent information between departments and between shifts on changes to equipment, production schedules, production problems or any other related information
- Works with employees on identifying, discussing solutions and implementing "fixes" on machinery and equipment problems
- Perform and facilitate "on the job training" and/or coaching of all employees as needed or required
- Complete and/or administer necessary documentation such as production sheets, pallet ticketing, job progressions, disciplinary actions, monthly SAFE cards, time and attendance, accident report
162
Manufacturing Supervisor Resume Examples & Samples
- Prepare documentation, maintain records and coordinate logistics for product shipments
- Provide guidance to others within the shipping/receiving area
- Issue oral and written instructions
- Coordinate the shipping of freight by contacting the appropriate freight carriers using computer based software
- Prepare work schedules and expedite workflow
- Receive and document incoming products and materials
- Keep up inventory tracking system and use FIFO for shipments
- Effectively communicate shipping issues with customer service and manufacturing as needed
- Assist in loading/unloading product with forklift as needed
- Ensure warehouse is kept clean and organized
- Manage maintenance of shipping docks and forklifts
- Annual training and certification/evaluation of forklift drivers and new forklift drivers
- Dangerous materials and goods shipment training
- Perform hazardous waste shipments with EHS coordinator
- Ability to balance onsite finished goods inventory levels and coordinate outside warehouse shipments on a daily basis
163
Manufacturing Supervisor Resume Examples & Samples
- 3 - 5 years’ experience in supervisor capacity
- Supervision experience in a team based environment
- Lean Manufacturing Experience
164
Manufacturing Supervisor Resume Examples & Samples
- Utilizes metrics and visual factory tools to facilitate two-way conversations relative to expectations and performance
- Links day to day work and business needs providing regular team feedback relative to goals
- Handles reluctant team members effectively with an ability to communicate to associates the need for engagement
- Teaches others to lead cell/team meetings
- A relationship builder that builds trust through listening and responding with empathy
- Crafts and celebrates wins with the team
- Teaches teams how to keep metrics, develops ownership for the metrics and desire to positively impact them
- Uses known problem solving techniques to reach quick and effective solutions
- Teaches associates how to use continuous improvement and lean tools
- Understands change management
165
Manufacturing Supervisor Resume Examples & Samples
- Responsible for directing and managing assigned team members; provides the necessary tools, knowledge, and support to ensure success in their job
- Performs personnel functions such as; interviewing, hiring, training, coaching and development, timekeeping, performance evaluations, compensation recommendations, and disciplinary/corrective action
- Develops and analyzes statistical data and product specifications to determine present standards and established proposed quality and reliability expectancy of finished product
- Maintains current process specifications relating to Tool & Progressive Dies. Develops new process specifications as new requirements emerge
- Responsible for purchasing parts and materials required for maintaining equipment and tooling in all assigned departments
- Ensures that assignments, tasks assigned, quality concerns affecting the “quality of the product”, and established agreed upon objectives are completed on time or in those cases they can not, notifying supervision
- Investigates and resolves internal/external customer issues in a timely and efficient manner
- Continually exemplifies and is an advocate of LISI Aerospace’s Vision, Mission, and Guiding Principles as stated in LISI Aerospace’s Team Member Handbook
- Ensure all people placed under their assigned area of responsibility, or all persons who may be affected by equipment or processes placed under their responsibility are complying with the rules and regulations set forth by Federal, Local and State government, and LISI Aerospace policies, procedures and plans
- Bachelor’s Degree in Manufacturing or Mechanical Engineering with minimum 5 years working experience in a Tool and Progressive Die and/or Manufacturing environment required; or equivalent combination of education and experience
- Proven ability to lead others effectively in a diverse environment
- Strong working knowledge of manufacturing methods and processes
166
Manufacturing Supervisor Resume Examples & Samples
- Supervise plant production line workers with an emphasis on teamwork, continuous improvement and accomplishment of Safety, Quality, Delivery & Cost goals
- Lead and monitor production line tasks
- Work with planning and scheduling to ensure compliance with production schedules
- Ensure tasks are performed according to regulations
- Partner with Safety and/or HR to investigate, resolve and provide corrective measures for accidents, injuries, production and personnel issues
- Ensure production and quality details are properly recorded
- Schedule/assign subordinate staff tasks to meet production goals and objectives
- Maintain a department that meets company housekeeping standards
- Maintain consistent and fair labor relations with union employees
- Ensure compliance with all company goals, policies, rules and procedures
167
Manufacturing Supervisor Resume Examples & Samples
- Technical AS Degree, BS degree or equivalent preferred
- 3 years high technology manufacturing experience, supervision experience preferred
- Supervisory, coaching and people development skills
- Ability to facilitate and influence cross functional problem solving and process improvement
- Ability to create, communicate, and hold subordinates accountable to expectations
- Effective written, verbal and presentation communication skills
- Microsoft Office Application skills suitable for data analysis and reporting
- Understanding of basic Lean Manufacturing concepts such as One Piece Flow, 5S, TAKT
- Fact based problem solving, able to separate opinion from data
- Direct experience with Oracle ERP or equivalent preferred
- Direct the development and implementation of activities in production areas to meet production goals, quality, and cost objectives
- Prioritize production schedules based on product build plan, equipment efficiency, and materials supply
- Administer procedures and trainings
- Make budgetary recommendations on capital expenditures and direct labor
- Select, evaluate and develop personnel, to ensure efficient and flexible production
- Lead subordinates to complete assignments using established guidelines, procedures, and policies
- Follow established practices and procedures in analyzing situations or data from which answers can be readily obtained
- Monitor and manage daily operations of multiple work areas
- Ability to evaluate individual performance and provide feedback necessary to improve performance, teamwork and accountability
- Successful experience selecting, hiring, and developing subordinates
- Demonstrated experience with performance management, providing real examples of positive performance feedback as well as constructive feedback
- Experience and skill providing formal performance review feedback to subordinates
- Successful experience facilitating team stand up meetings within a production environment
- Experience attending, contributing to, and facilitating peer level and above status meetings
- Effective business communication skills. Able to obtain complex data and summarize it into easy to understand, presentable information
- Effective identifying and implementing process changes as necessary to achieve targeted business objectives
- A constant learner that has a track record of expanding skills
- Fundamental understanding of Lean Manufacturing and 5S concepts
- Able to lead improvement in manufacturing areas. Knowledge of and experience with lean tools including one piece flow, value stream maps, red tag, visual pull kanban
- A person that is generally likable and has a high probability of success in the Coherent culture
168
Manufacturing Supervisor Resume Examples & Samples
- Previous supervisory experience is needed
- Demonstrated leadership skills are necessary
- Must be able to interpret detailed engineering drawings and associated assembly instructions
- Effective verbal and written communication skills are required
- Ability to create documents, spreadsheets, and presentations utilizing Microsoft Word, Excel and PowerPoint
- Previous experience working in a clean room environment is helpful
- Working knowledge of or experience with Lean Manufacturing principles is a plus
- Experience in a union environment is beneficial
- A relevant bachelor’s degree is preferred
169
Manufacturing Supervisor Resume Examples & Samples
- Supervises all personnel and operations monitoring production to assure control, adherence to safety, quality, and schedule requirements
- Assures adequate employee training and compliance to Regulatory and Company requirements and polices
- Maintains direct contact with support departments to resolve issues on a day to day basis
- Keeps records and issues reports as required to document the performance of the area supervised and to keep management informed of overall performance
- Participates actively in various Company programs (Lean Thinking, CIP’s, etc) geared to optimize performance, reduce costs and meet regulatory requirements
- Evaluates EE’s performance, administers the disciplinary procedure where applicable
- Assures for the training and certification of employees in all manufacturing procedures in which employees will participate
- Ensures monthly schedule goals are met and well planned (this is your responsibility, you are the owner an the one accountable to make it happen)
- Updates and corrects procedures for the operation of new or existing equipment
- Supports the incorporation of new technology for Company applications where feasible and practical
- Supports and coordinates the implementation of Lean Manufacturing strategies
- Identifies new opportunities for Process Improvement and assists in implementation
- Assists identifying and elimination of Non Value Added Activities
- Reviews Manufacturing lines start up, operation, labeling, package, release, and shipping logistic for appropriate process flow and documentation
- Assists in development and implementation of process improvements and optimization
- Updates, in coordination with the ME, Mfg. procedures, specifications, bill of materials, drawing, operating procedures and any other documentation needed to manufacture, test or purchase products
- Provides, in coordination with the Facilities Supervisor, all facilities and resources during the first production steps to assure on time start-up of new production items. Investigates availability of adequate machines accessories, tooling supplies, safety feature, inspections gauges and training
- Assists in establishing annual tooling and capital investment budget
- Analyzes value of product and methods with emphasis on cost reduction of labor, material, and auxiliary expenditures
- Performs monthly audits of area supervised for the compliance to Company goals and Regulatory requirements including but not limited to cGMP's, FDA, ISO 9002 and OSHA. (Written reports must be provided to immediate supervisor, and audit procedure must be followed)
- Complies with the cGMP's, Quality Standards and established policies and/or procedures
- Executes other duties assigned by Supervisor
- Must be bilingual (English/Spanish) and must have good communications skills both oral and written
- Basic knowledge of mathematics and statistics
- Must have knowledge of cGMP's, OSHA, and ISO 9000 requirements
- Bachelors Degree preferably in Engineering
- 3-5 years experience within a manufacturing environment, preferable in the Medical Device Industry
- 2b. Repetitive hand movements? _____Yes ___X__No
- 2c. Simple Grasping?
170
Manufacturing Supervisor Resume Examples & Samples
- 3 – 4 years supervision experience
- Proficient utilization of Lean tools such as 5-S, Process Flow, Kanban, etc
- Practical experience with driving safety and an operator lead work environment in a production environment
171
Manufacturing Supervisor Resume Examples & Samples
- 1) Conduct pre shift start up meetings covering safety and production
- 2) Manage scheduling of Setup, Material Handler and Operator workload
- 3) Use the SIM (Short Interval Management) process to drive safety, quality, customer service and 5S
- 4) Manage time and attendance in Autotime for employees
- 5) Mentor and council employees concerning any issues with attendance or job performance
- 6) Responsible for supporting the Schneider Production System
- 7) Other duties as required due to the needs of the business
- 1) Bachelor’s degree or equivalent experience
- 2) Ability to lead, effectively communicate, problem solve
- 3) Ability to implement process improvements and rally the team to achieve set goals
- 4) Flexibility to respond to shifting priorities and ability to prioritize work with minimal supervision
- 5) Positive, enthusiastic, team player and champion of the business and customers
172
Manufacturing Supervisor Resume Examples & Samples
- Managing all aspects of Manufacturing/Production team’s daily operations
- Supporting the manufacturing engineers as well as other groups to generate smooth and successful processes
- Working closely with HR and direct manager to maintain consistency and fairness in administration of company policy and code of conduct
- Supporting team of direct labor operations – Including resolving any issues that arise as related to safety, quality, delivery, and cost
- Assist with training/talent development, goal attainment, and continuous improvement within these areas
- Should be cognitive of improvement philosophy & driving lean manufacturing principles
- Associate of Science (AS) Degree in Engineering or Business, Mechanical/Manufacturing or Technology required. Bachelor’s degree preferred
- 3-5 years’ of progressively responsible experience in a similar role with management background
- Solid understanding of welding/assembly process with a keen attention to detail
- Strong go-getter attitude with a willingness to accept responsibility
- Comfortable communicating with all levels of the organization in a variety of formats
- Comfortable using Microsoft Office and general computer skills preferred
173
Manufacturing Supervisor, Split Shift HVT Resume Examples & Samples
- Supervise employees and manufacturing activities pertaining to the production of products and/or manufacturing processes of 2 or more production areas, depending on the complexity of the areas
- Lead improvement projects, partner with engineering on investigations and/or corrective actions, perform non-conformance investigations for review with engineering, assure documentation content is valid
- Oversee the scheduling of work orders and team performance metrics
- Ensure staff is appropriately trained to perform assigned work
- Document owner for assigned product line assembly procedures
- Monitor raw material usage and availability required in daily production
- Monitor material and labor variances to meet established standards
- A Bachelors' degree is required. An Engineering Degree is preferred
- A minimum of 2 years of supervisory experience or manufacturing engineering experience leading project teams, within a regulated manufacturing environment is required
- Experience working in a FDA regulated industry is highly preferred
- Experience working with new product development teams and/or ramping up new product production is highly preferred
- Proven expertise in Microsoft Office Suite with working knowledge of Enterprise Resource Planning (ERP) system, preferably JDE
174
Manufacturing Supervisor Resume Examples & Samples
- Co-operate in the establishment of organizational arrangements, human resource policies and management development plans that will create a high quality product team and ensure amenable workplace relations to enable the business unit to meet its current and future objectives
- Comply with government regulations and the company’s Equal Employment Opportunity and Affirmative Action policies
- Regularly assess and provide feedback regarding performance to employees
- Maintain a safe workplace
- Developing and/or maintaining plans that meet internal and external customer requirements
- Representing the team at meetings with customers, vendors or company management
- Developing innovative problem resolution processes and encouraging new ideas and methods
- Coordinating with logistics for the shipment of completed product including supplies and inventory
- Planning with information from the team, operations management, production planning, purchasing, QA, engineering and finance the daily, weekly and monthly activities and priorities
- Develop and maintain for the team a set of clearly defined performance objectives that involve individual and team accountability in work place safety, quality, attendance, cleanliness, and performance measurement
- Develop competencies within the department or product line that focus on
- Technical skills and continuous manufacturing process improvement
- Developing an understanding of our overall business and financial (cost and asset) management objectives
- O Team participation, communication and problem solving techniques
175
Manufacturing Supervisor Resume Examples & Samples
- 1) Adhere to Human Resources Accountabilities
- 2) Provide supervision, leadership and coordination of employee activities associated with an assigned product line or department by
- 3) Develop and maintain for the team a set of clearly defined performance objectives that involve individual and team accountability in work place safety, quality, attendance, cleanliness, and HAZMAT handling & disposal, housekeeping, performance measurement
- 4) Develop competencies within the department or product line that focus on
- Team participation, communication and problem solving techniques
- Team flexibility, cross training and personal motivation to achieve world class quality, financial, and schedule performance
- 5) Work to ensure continually improving manufacturing processes and procedures, with technical assistance from tooling, engineering, finance, and materials
- 6) Responsible for the completion of key job requirements and other tasks related to this position as assigned by cognizant management
- 1) A minimum of a 2-Year Associates Degree is required. A 4-year Bachelor’s Degree is preferred
- 2) A minimum of Five years of experience in leadership positions in a manufacturing environment
- 3) Demonstrated skills in written and verbal communication, problem analysis and solving, potential problem analysis, decision analysis and planning
- 4) Must be skilled in coaching, team-building, business measurement, continuous improvement and lean manufacturing techniques
- 5) Multi-task oriented, strong interpersonal skills, computer literate required
176
Manufacturing Supervisor Resume Examples & Samples
- Results orientation, accountability, and project ownership are essential
- Requires excellent communication skills (written and spoken), and possess strong capabilities in managing, coaching and training talent
- Ability to adapt to changing requirements is essential
- Must be able to work Monday through Thursday 4pm – 2:30am
177
Manufacturing Supervisor Resume Examples & Samples
- Promote all plant activities related to safety, and the providing of a safe work environment. As part of this, ensuring that all equipment is functioning in a safe manner; helping to indentify & eliminate workplace hazards; ensuring performance standards include safe work practices; enforcing all safety rules; conducting weekly departmental safety audits, monthly safety meetings, and monthly safety inspections; responding to injuries promptly; investigating all accidents in a timely matter, and following up to ensure corrective action is taken
- Lead the development, training, and operation of production associates, working on the plant floor to implement lean manufacturing techniques, including 5S
- Responsible for the implementation of the plant quality plan as it relates to the department, including making the audit checks specified, and insuring customer standards are achieved
- Develops qualified personnel primarily through implementation of the plant's training program. Training of all employees new to the plant or the job. Retraining of experienced employees to be completed on an annual basis. Employee performance is to be developed through a merit review process, one on one feedback, and as a last resort the plant discipline system
- Works with the Operations Manager and production control planner to schedule product to achieve timely customer delivery. Gives Operations Manager requests for staffing level changes
- Responsible for the effective maintenance of department's machines through work order requests. Gives input to the Operations Manager on new machine requirements when developing the plant capital plan
- Works with Operations Manager and through department personnel to maintain actual expenses at or below levels specified in current department budget. Expense areas to be controlled include labor variances, scrap, machine repair expenses, raw material usage, absentee rates, and general expense items
- Develops and maintains good employee relations by the fair and consistent administration of plant polices, open individual communications, and regular departmental meetings
- Ensuring that Good Housekeeping practices are followed by all employees
- 4-year degree or equivalent combination of technical training and /or 2 years prior supervisory experience in a high-volume manufacturing environment
178
Manufacturing Supervisor Resume Examples & Samples
- Works with employees on identifying, discussing solutions and implementing “fixes” on machinery and equipment problems
- Complete and/or administer necessary documentation such as production sheets, pallet ticketing, job progressions, disciplinary actions, monthly STOP cards, time and attendance, accident reports and process control sheets
- Bachelors level new graduate in engineering or related discipline with two or more related co-op or internship work assignments in a manufacturing setting would be an alternate for the 5-7 years of work experience listed above
- Strong problem solving skills and the ability to effectively solve problems both on an individual and collaborative approach
- Knowledge of Lean Manufacturing and Six Sigma principles is a plus
- Ability to look at new solutions and “think outside the box.”
- Proven ability to communicate effectively with employees and deal with and relate to an assortment of personalities
- Strong PC skills and working knowledge of various Windows programs (Excel, Access, etc.)
- Effective leadership skills such as conflict resolution, communication, decision making, etc
- Career path of plant management or corporate engineering
- Proven ability to prioritize effectively and excellent time management skills
- Strong understanding of machinery and equipment, but with the ability to know when to assume the responsibility and when to delegate
- Strong commitment to quality and safety
- Desire and ability to travel and relocate if career opportunities arise
- Ability to work on various shifts
- Commitment to ongoing personal training and development
179
Truss Manufacturing Supervisor Resume Examples & Samples
- Supervises personnel and ensures adherence to company and department policies and procedures; performs personnel management duties including hiring, training, completing disciplinaries, etc
- Oversees delivery operation including truck repair and maintenance and drivers
- Compiles data and prepares various reports
- Assists with inventory and purchasing functions as required
180
Manufacturing Supervisor Resume Examples & Samples
- BS/BA or Associates Degree or college courses with 5 or more years of directly related experience. Degree in other discipline if sufficient technical depth has been achieved from professional experience. Technical field or equivalent e.g. Biology, Chemistry
- Minimum of 5 years of directly related manufacturing (or related) experience (preferably with leadership role)
- Preferred Level of Education: BS or Associate degree. Technical field or equivalent eg Biology, Chemistry
- Strong quality/compliance orientation and track record
- Excellent interpersonal and leadership skills
- Strong influence and relationship building skills with an emphasis on teamwork
- Comprehensive understanding of Lean/Six Sigma (OE) principles and their application
- Verbal and written communication skills which emphasize teamwork and a strong quality orientation
- Team player with demonstrated ability to lead and motivate a diverse team
- Demonstrated ability to solve complex technical problems
- Understanding of the control systems used to run processes in modern large scale Biopharmaceutical plants
- Provides first-line supervision on day, swing or night shift, to a staff of Manufacturing Associates who conduct: the glass wash, autoclaving, and assembly preparation for manufacturing operations. Additionally should be able to order materials through Production Planning to ensure on time delivery of required buffers and medias is maintained. Production Supervisors are expected to have the capability to perform above activities alongside Manufacturing Associates
- Perform duties in a compliant manner and behave in accordance with site SOP’s, GSK EHS standards and guidelines and relevant legal requirements and ensure that their team do the same
- Assures that the cleaning and sterilizing operations, and preparation of assemblies meets all quality standards for cGMP, GSK and any other applicable regulatory agency
- Supports successful implementation of new products and processes into the facility, including all appropriate equipment and area changeover activities
- Accountable for Manufacturing Associate development and/or performance management though activities such as assignments and associated technical training programs
181
Manufacturing Supervisor, Slide Manufacturing Resume Examples & Samples
- Take full responsibility of the shift in terms of management of staff, management of production and quality targets and to ensure the smooth running of the production processes
- Take full responsibility of the quality and product that is produced within the shift, in line with company’s quality systems, processes, and procedures
- Manage, develop, and motivate direct reporting staff. Utilize techniques to foster a fully engaged work force that is motivated to grow and develop new skills
- Comply with all company policies and procedures, including safety, PPE requirements, SOP’s, Manufacturing Procedures, Quality System Regulations, and Good Manufacturing Practices
- Monitor, measure, and report on production related process performance and general issues
- Ensure good communication is given either verbally or written to all members of the team
- Problem solving and troubleshooting skills are used to ensure that team members can identify root causes and take effective action to resolve matters
- Work closely with colleagues to ensure production turnovers are effective
- Ensure training skills are met for the demands of the shift
- Take an active role in the company’s continuous improvement, Lean, and cost reduction goals
- Maintain and enforce high housekeeping standards to ensure a clean and safe workplace
- Be able to make appropriate decisions while following the company’s organizational structure
- Core skills include familiarity with Microsoft Office products and ability to learn Oracle and Agile
- Maintain high level of timekeeping
- Experience supervising all aspects of a semi/fully-automated, high volume, manufacturing process
- Demonstrated ability in training and monitoring employee performance, tracking and reporting on key manufacturing metrics, and managing employee work assignments
- Ability to work First Shift hours
- Minimum 5 years’ experience in related field or an equivalent combination of education and experience
- Prior military candidates are encouraged to apply
182
Manufacturing Supervisor, Blow Fill Seal Resume Examples & Samples
- Supervise the day to day activities of production associates
- Supervise production activities including Formulation, Filling, Inspection, Packaging, Labeling and Sanitization
- Schedule production activities and coordinate activities of support groups
- Communicate production priorities and progress to team on a continuing basis
- Maintain records and a clean environment to comply with regulatory requirements
- Read, understand, and comply with Good Manufacturing Practices and Standard Operating Procedures
- Review completed production documentation (Batch Records, Protocols, etc.) for quality and cGMP compliance
- Review/Update current SOPs/batch records as well as write new SOPs/batch records, and protocols
- Assist associates with in-process testing to assure batches meet specifications
- Ensure weights, measures and raw materials are managed appropriately to assure batches manufactured contain proper ingredients and quantities
- Manage the performance of Production Associates and Leads
- Assist with the operation and maintenance of production equipment
- Perform line clearances, cleaning/sanitization, CIP and SIP process equipment, filter testing, operation of Blow Fill Seal process equipment
- Lead troubleshooting and process improvement activities including corresponding documentation activities
- Initiate appropriate action when process deviations occur
- Execute validation protocols for processes and equipment
- Proficient in Microsoft Office (Word, Excel, PowerPoint, Outlook)
- Applied knowledge of pharmaceutical GMPs, FDA guidelines, and industry standards. Ability to apply GMP to company specific processes and products
- Excellent professional documentation skills. Ability to objectively, accurately, and thoroughly convey complex issues in writing. Ability to produce a large volume of written materials independently
- Ability to interact with other departments effectively. Ability to review work performed by other personnel, communicate problems and deficiencies, elicit corrections, and enforce company policy and procedures as they relate to manufacturing requirements
- Ability to handle confidential company data, projects, information, etc
- Must possess excellent written and oral communication skills
183
Manufacturing Supervisor Production Resume Examples & Samples
- Execute their assigned maintenance work order schedule
- Evaluate equipment and understand situation
- Collect and use equipment failure data
- Support the development of and implement the periodic maintenance system as developed by the PM Pillar Lead
- Evaluate and implement reliability improvement: number of minor stops, process stops, breakdowns, MTBF, etc
- Evaluate and implement maintainability improvements: reduce maintenance frequency rates, increase predictive maintenance effort and improve MTTR
- Develop, implement and audit Productivity Improvement initiatives
- Support manufacturing supervision, as required
- BS – Engineering
184
Manufacturing Supervisor Resume Examples & Samples
- Bachelor of Science or BA or Associates Degree or equivalent combination of experience and post-secondary education, preferably in a technical background
- 3-5 years previous supervisory experience
- Verbal and written communication skills. Should possess problem solving skills and facilitate group meetings
- Knowledge of manufacturing organization, controls and procedures
- Knowledge of fundamental Safety principles for an industrial work environment
- Must have experience with team building, process improvement, conflict resolution, and motivating people
- Lean manufacturing knowledge & implementation
- Knowledge of ISO 14001/9001 required
- Strong skills in the following areas
185
Manufacturing Supervisor Resume Examples & Samples
- Understand and follow current Good Manufacturing Practices
- Provide guidance, support, direction and leadership through positive interactions with all personnel during daily operations
- Interview, hire, coach, and develops staff. Conduct annual performance reviews for all direct reports. Assists in setting performance objectives and development plans
- Supervise the day-to-day production, scheduling, staffing, material management, compliance, training and auditing activities – to meet customer requirements including deadlines and quality standards
- Review, approve, and manage documentation for batch and system records. Assist in release of product for distribution. Assist in meeting product release time goals
- Implement and support training programs designed to enable staff to consistently execute all manufacturing processes with strict compliance to cGMPs and EHS regulations
- Develop and implement performance measurement and internal auditing programs in order to routinely evaluate operation efficiency and quality. Implement changes as needed based on assessments
- Resolve technical, material and cGMP problems that may impact project deadlines
- Provide guidance and troubleshooting assistance as needed during a deviation in the process
- Represent the company during audits and inspections
- Minimum 2 years of manufacturing experience required
- Minimum 1 year leadership experience required
186
Manufacturing Supervisor Resume Examples & Samples
- Posses of a bachelors degree in engineering. Masters degree strongly preferred
- 5+ years of experience working a manufacturing environment
- Demonstrated results in a leadership role
- Must be able to deliver results in an ambiguous and fast paced environment
- Ability to apply appropriate problem solving techniques FMEA, 5 Whys, etc
- Database proficiency a plus
187
Manufacturing Supervisor Resume Examples & Samples
- Demonstrated proficiency with manufacturing computer systems
- Demonstrated professional written and verbal communications
- Ability to be effective in an environment that changes quickly
- Ability to be effective working independently and responsible for the work of others
- 5-7 years combined experience manufacturing operations preferred
- Previous front line supervisor leadership experience
- Experience with Lean Tools (Kaizen, KanBan, Value Stream, 5S )
- Previous experience analyzing information to make directional decisions
188
Manufacturing Supervisor Resume Examples & Samples
- Supervisor fully supports, maintains and fosters a safe working environment by being a champion for Safety. Instills a culture where safety is the number one priority. Performs safety training lectures at regularly scheduled meetings so that team members understand the importance of following established training procedures and practices and utilize proper PPE. Conducts regular safety walk throughs within the work center and company, identifies and helps to correct safety hazards, Near Misses or potential issues
- Lead Tier 1 meetings. Supervisor is expected to provide guidance, support, direction and leadership through positive interactions with all personnel during daily operations. Participate and help lead Tier 2 meetings. When needed represent Manufacturing Department at Tier 3 meetings
- Performs regular GEMBA walks. Determine short/midrange and long term head count requirements based on budgeted and long term forecasts to support budget process and ensure adequate resources to meet production schedules
- Interview, hire, coach, motivate, develop and discipline staff. Conduct annual performance reviews for all direct reports. Assist in setting performance objectives and development plans. Monitor progress. Develop, train and challenge Leads and technicians for growth and advancement to the next levels
- Review, approve, and manage documentation for batch and system records. Assist in release of product for distribution. Assist in meeting product release time goals. Conduct regular reviews of standard procedures and batch record documentation and identify areas for improvement and implement process improvements
- Emphasize training programs designed to enable staff to consistently execute all manufacturing processes with strict compliance to cGMPs and EHS regulations. Develop and implement programs to track GMP errors, identify opportunities for improvement and implement activities to reduce errors
- Develop and implement work center performance measurement metrics and internal auditing programs in order to routinely evaluate work center performance, operation efficiency and quality. At a minimum, metrics should include Cycle Time, Efficiency, Schedule Adherence, Yields and Absorption. Identify processes to determine efficiencies in both work order closures and headcount. Identify root causes for inefficiency and implement changes as needed based on assessments
- Resolves technical, material and cGMP problems that may impact project deadlines. Provide guidance and help to lead troubleshooting efforts as needed during a deviation in the process. Initiate, own and properly manage work center NCR's and CAPA's
- Leads the team, supports and fosters a positive and equitable working environment emphasizing Baxter 2020, Baxter Shared Values: Respect /Responsiveness / Result
- Demonstrated interpersonal and leadership skills with ability to interface well with other departments, and lead effectively and efficiently in a team environment
- Strong Lean experience. World Class Medical Device manufacturing experience and Black Belt certification preferred
- Ability to analyze and interpret scientific and statistical data
- Strong assessment, analytical and troubleshooting skills
- BS degree in a scientific or engineering discipline with 3-5 years of manufacturing experience plus 4-6 years supervisory related experience required
189
Manufacturing Supervisor Resume Examples & Samples
- Direct supervision of production personnel
- Providing leadership that promotes a culture of EHS ownership by all employees
- Championing Lean Manufacturing continuous improvement by showing active support and coaching of others
- Developing the leadership behaviors of Production Team Leads to insure daily manufacturing targets for productivity, service, quality and cost are attained
- Training of production personnel regarding their assigned job duties
- Providing coaching to production operators to develop them as engaged problem solvers
- High School Diploma/GED or higher from an accredited institution
- Minimum (5) years of manufacturing experience
- Abrasive manufacturing experience
- Previous Production Supervision experience
190
Manufacturing Supervisor Resume Examples & Samples
- Abides by Steris-IMS health, safety, & environmental requirements
- Abides by Steris-IMS quality requirements including ISO standards
- Responsible for assessing team skills, and directs team training efforts to ensure direct reports are adequately trained
- Responsible for interviewing potential new hires, administering reviews, communicating corrective actions, and termination process
- Collaborates with and provides information to Customer Care, and sales representatives to address any concerns that arise within an account
- Supports and actively participates in company’s lean philosophy of continuous improvement
- Leadership Skills – The ability to make things happen by encouraging and channeling the contributions of others, taking a stand on and addressing important issues, and acting as a catalyst for change and continuous improvement
- Fostering Teamwork – The synergy that comes from putting employees together to form teams to solve problems, make decisions, and take action for greater department success
- Coach & Develop Others – The ability to lead, coach and develop the department’s human capital by establishing an environment conducive to feedback, giving positive and constructive feedback, addressing performance problems and grooming employees for advancement
- Displays Positive Attitude and Confidence
- Communication Skills – Builds trust and solid working relationships with employees and others in the organization. Shares information with others and goes beyond communicating only what is necessary
- Copes well with stress – Effectively deals with the concerns of the organization and the people in it and provides appropriate attention
- Computer Skills- Must be proficient with all Microsoft Office applications, previous experience using Oracle preferred
- Business Acumen – ability to understand company financials, department cost structures, budgets, and operating costs
191
Manufacturing Supervisor Resume Examples & Samples
- Supervises production activities to meet production schedules and to maintain all required quality specifications through the use of manual/semi-automatic equipment
- Maintains a safe working environment by fully implementing the World Class Safety initiatives and culture of STERIS Corporation, instructing employees in established safety practices, and enforcing them at all times. Responsible for keeping safety equipment in good working order
- Monitors production quality and assures that company standards are met. Monitors and follows all production SOP’s including all company, FDA, ISO and cGMP requirements
- Responsible for the timely requisitioning of required supplies from appropriate sources in order to meet production schedules relative to the current Kanban and J.I.T objectives
- Responsible for meeting production cost standards of both labor and product yield and for reporting all such data
- Supervises and checks lines and utilization of operators. Participates in the daily Gemba walks and maintains the Production Control Boards and Communication and Assignment Boards in area of responsibility
- Ensures proper operation of equipment including instruction of operators on equipment use and procedures to use to request needed maintenance support. Ensures equipment is maintained in a clean, safe working condition (TPM)
- Supervises general housekeeping in the work area and ensures area of responsibility is kept in good status, keeping aisles clear, pallets properly stacked, and trash removed. Ensures finished product is current and emergency equipment and electrical panels are not blocked
- Establishes and maintains good relations and open communications with plant employees, while maintaining productivity, attendance and general order required for an efficient production operation
- Responsible for 5S objectives in area of responsibility
- Supports all established Lean objectives and participates in Lean activities as necessary to support the business goals
192
Manufacturing Supervisor Resume Examples & Samples
- Coordinate the daily manufacturing activities to execute production plans
- Manufacture a quality product on time
- Promote and ensure a high level of direct report performance to standards
- Maintain a safe working environment for all employees
- Provide security support as needed to protect company assets
- Maintain time and attendance records
193
Manufacturing Supervisor Resume Examples & Samples
- Technical degree, Associates or higher
- 3 to 5 years experience in calibration of instruments, preferably flow instruments
- Knowledge of basic gas physics, flow unit conversions and tubing connections
- Experience working in an ISO:9001 certified lab (ISO:17025 preferred)
- Must be able to handle air lines/bottles
- Must be familiar with gas fittings, regulators and pressure gauges
- Must be able to read and understand schematics of basic electronic circuits
- Must be able to read and follow drawings and procedures
- Basic math skills and Algebraic understanding is necessary
- Must be able to follow signal flow and deduce failure points
- 2 to 3 years of exeprience in a supervisor role
- Must have general computer skills, with a proficiency in Excel and familiarity with LabView
- Sitting, standing, walking for long periods of time
- Use of hands and fingers to feel and for keyboarding
- Must be able to use hand/eye coordination to solder and probe electronic circuits
- Must be able to lift up to 35lbs
194
Manufacturing Supervisor Resume Examples & Samples
- Knowledge of plastic material properties/processes, and statistical methods
- Associates degree is required
- Specialized training in foreman and management courses
- Formal RJG training preferred
- Minimum of three (3) years of experience in plastic injection molding plant and related fields, with a background in supervision
- Must have experience in mold set-up, troubleshooting, exposure to maintenance problems, and familiarity with state-of-the-art controls and engineering resins
195
Manufacturing Supervisor Resume Examples & Samples
- Bachelor's degree required, food science, entomology, or business preferred
- 2-4 years experience managing hourly employees using a team based approach
- Prefer experience in a manufacturing environment
- Effective coaching facilitation, presentation, team building and communication skills
- Demonstrated people and leadership skills including conflict resolution, problem solving and performance management
- Must be willing and able to travel 5-10% of the time
196
Manufacturing Supervisor Resume Examples & Samples
- Supervise team members in assigned departments, hire new team members, conduct performance reviews, recommend increases, monitor attendance and responsible for early stages of conflict resolution
- Provide feedback, coaching, counseling, and documenting team member performance
- Research, identify, and correct issues that cause inefficiencies in productivity and accuracy
- Review of nonconforming items as required by customer and Management
- Provide customer assurance on all cases that are delayed or require additional work, ensure ship dates are met and alert customers of issues pertaining to Rx information
- Enforce compliance with laboratory safety rules and regulations
- Maintain a complete understanding of all assigned functions, computer software, and any required reporting
- Communicate with other departments regarding issues, and respond to all questions
- Define production flow and scheduling in assigned departments, utilizing team members for overflow in other departments when necessary
- Promote teamwork and look for opportunities for cross training of team members
- Maintain awareness and understanding of how each department impacts customers, both internal and external, and the department's overall impact on the operation
- Set quality standards for final product delivered from assigned departments and assure that they are followed
- Communicate with team by conducting documented meetings on a regular basis
- Ensures operation of equipment by calling for repairs; conducting preventive maintenance and evaluating new equipment and techniques
- Meeting company standards pertaining to quantity and quality of work performed on an ongoing basis, performing all work related tasks in a manner that is in compliance with all Company policies and procedures including Worldwide Business Standards
- A minimum of 5 to 10 years formal training/experience in Mechanical Engineering Technology including
- Experience with CAM software
- CNC Programing and Machinery
- Experience working in ceramics, metals and metal forming
- Rapid prototyping and 4-5 axis milling machines
- Good Problem Solving Skills
- Excellent written and good verbal English communication skills
- Must be able to read Rx requirements and communicate effectively with staff and customers the provisions required on any and all scripts provided to the department
- Two years of experience in a lead or supervisory role, preferably in a dental lab environment. Minimum1 year of experience utilizing case management software
197
Manufacturing Supervisor Resume Examples & Samples
- Apply quality criteria
- Comply with safety requirements
- Apply Lean Mfg concepts to manufacturing process
- Administer personnel
- Able to work in different manufacturing shifts and schedules
- MES system
- Manufacturing process decision making
- Comply with GMPs
198
Manufacturing Supervisor Resume Examples & Samples
- Demonstrated ability in coaching, counseling, motivating, training, recognizing and communicating objectives
- Basic understanding of Lean Manufacturing
- Basic understanding of quality systems is a plus
- Good communication and interpersonal skills are a must
- Analytical and problem solving abilities are required. Must have flexibility to re-prioritize tasks as needs change
- Bachelor’s degree in business or engineering discipline or equivalent field preferred
- 3 to 5 years supervising direct labor in a manufacturing environment and maintaining positive employee relations. Experience in related manufacturing process knowledge, including machining, polishing, and/or clean room packaging is preferred
199
Manufacturing Supervisor Resume Examples & Samples
- Performs/assists with Processing Steps and/or Manufacturing Support activities, monitoring process against the batch record, SLR and control system
- Reviews Manufacturing documentation on a daily basis
- Excellent understanding of cGMP Biotech or Pharmaceutical operations
- Understands cGMP requirements and follows those requirements, including requirements for good documentation practices
- Possesses an excellent understanding of the scientific theory of biologics manufacturing: Has a excellent understanding of biotechnology processing - purpose of major unit operations and microbial control concepts
- Proficient and knowledgeable in the operation and complex troubleshooting of multiple manufacturing areas
- Lead/ supports deviation investigations. Participates in cross functional project teams, supports technical transfers with relevant teams/individuals
200
Manufacturing Supervisor Resume Examples & Samples
- Effectively schedules all work according to overall production needs and ensures all employees have the proper tools, equipment, supplies, and instruction to perform the assigned work
- Maintains and ensures effective communications regarding performance and departmental and/or company goals
- Trains and develops new and existing employees in areas such as safety, quality, and equipment operating procedures
- Develops and conducts effective performance appraisals
- Ensures consistent compliance to all company and departmental policies and procedures
- Participates in development of departmental budget
- Participates in recruitment of new employees
- Participates in new production introduction as required
- Works with Site Manager to implement improved processes to improve; cost, quality, delivery and safety
- Monitors and manages department and individual productivity to ensure cost effective schedule attainment
- Effectively manages department resources such as supplies and equipment to control costs and meet production demands
- Keeps Manager and Human Resources informed of any employee relations issues (such as union activity) that are significant
- Provides positive image and plays a supportive role, in the implementation and execution of change
- Shares ideas with and provides support to fellow supervisors
- Provides routine maintenance on all equipment utilized by the department
- Ability to troubleshoot equipment failures and implement repairs
- Understanding of tool and die functionality and the ability to recommend order and implement repairs and/or install new components
- Perform time studies on manufactured product and compile reports necessary to establish standard costs
- Engineer, input and maintain bill of materials in the FACTS System
- Ensure that all required training is identified for and completed by all direct reports
- Evaluate staffing needs and costs; identifies, hires and promotes individuals with the right skills and competencies necessary to achieve superior results
- Develop a team environment that values diversity and uses various individual’s strengths to the benefit of the team
- Effectively manage and drive 5S programs in production areas to ensure operational excellence and a clean/safe work environment
- Ensure required annual department specific safety training is conducted and documented
- Maintain employee time/attendance records
- Additional responsibilities as requested or required
- Bachelor’s Degree or equivalent in experience
- One (1) to two (2) years experience in a non-union environment
- Practical experience in Lean Manufacturing and cellular manufacturing a plus
- Experience in assembly, fabrication, or production control (multiple experience preferred)
- One (1) to two (2) years supervisory experience
- Effective administrative computer skills (MS Work, Excel, Email, Oracle, AMAPS)
201
Manufacturing Supervisor, Second Shift Resume Examples & Samples
- Management of subcontracts post contract award through the full development life cycle (design, manufacture, test, acceptance) ensuring subcontractors deliver to agreed requirements and schedule
- Knowledge of contract law
- A strategic individual with good judgment and strong professional and ethical standards
202
Manufacturing Supervisor Resume Examples & Samples
- Minimum 5+ years of supervisory experience in a manufacturing environment
- Have a critical eye for improvements in all areas of responsibility
- Must be willing to work first or second shift as well as required overtime
203
Manufacturing Supervisor Resume Examples & Samples
- Previous supervisory experience in manufacturing environment
- Proven ability to lead functional groups and operational units
- Experience in development and management of budget, staffing, and business operations results
- Ability to work effectively with internal and external customers
- Experience documenting employee related issues, monitoring employee attendance and administering disciplinary actions
- Ability to communicate effectively verbally and in writing in both English and Spanish
- Knowledge in Six Sigma, Lean Manufacturing, ACE and Project Management skills
- Good attendance and disciplinary record
- Available to work 2nd shift and extended hours
- Due to iTAR regulations candidates must be an US Citizen
204
Manufacturing Supervisor Resume Examples & Samples
- Successful completion of four-years of high school, or equivalent, plus completion of two years of college or graduation from a two-year technical college with an associate’s degree (bachelor’s degree preferred) with a concentration in either manufacturing, operations, engineering or business manufacturing
- Five to seven years of experience, or any combination of education and experience that provides equivalent knowledge, skills and abilities
- Lean Manufacturing Green Belt Certification required
- Lean Manufacturing Black Belt Certification preferred
- Experience with case study, data acquisition and mathematical analysis and conclusion
- Able to effectively make presentations in both large and small group settings
- Experience Supervising personnel in a manufacturing setting to include distribution of work, scheduling, training, answering of questions related to work, problem solving, performance management and discipline
205
Multi Functional Manufacturing Supervisor Resume Examples & Samples
- Demonstrated understanding of manufacturing/productions methodologies
- Experience using tools, machines, and systems typically used in a production/manufacturing environment
- Experience with Microsoft Office programs (i.e. Word, Excel)
- Greenbelt Certified
- Previous development experience
- Working Knowledge of Crew Plans
- Forecasting manpower
206
Manufacturing Supervisor, nd Shift Resume Examples & Samples
- Maintains work flow by monitoring steps of the process; setting processing variables; monitoring personnel and resources; studying methods; implementing cost reductions; facilitating corrections to malfunctions
- Initiating and fostering a spirit of cooperation within and between departments
- Completes production plan by scheduling and assigning personnel; accomplishing work results; establishing priorities; monitoring progress; revising schedules; resolving problems; reporting results of the processing flow on shift production summaries
- Ensures operation of equipment by calling for repairs; interfaces with Maintenance
- Applies discipline as necessary and resolves conflicts between employees and departments
- Maintains EHS standards by observing, educating and directing personnel on the use of safe work practices
- Drives 5S activities and AM activities in support of plant objectives
- Manage resources within given area of responsibility to ensure staffing and equipment readiness levels match business activity levels
- Coach and motivate employees. Evaluate employee performance and provide disciplinary action as required
- Promotes, maintains, and enforces safe and healthy working conditions for all employees in accordance with regulatory requirements and Company standards
- Provide operational input and guidance to technical staff for new product development
- Maintain a high standard of product quality in accordance with ISO and the company Quality Manual
- Identify and execute cost savings initiatives to impact business and operations goals positively
- Assign work according to designated priorities in order to maintain scheduled completion dates
- Orient, train and instruct all employees in the safe and efficient performance of their duties
- Drive continuous improvement through TPM and 5S with an open dialogue and a bias for action
- Other duties as assigned by the Plant Manager
- Directly supervises 30 – 35+ employees on the Swing Shift (3 PM – 12 AM). Carries out supervisory responsibilities in accordance with the organization's policies and applicable laws. Responsibilities include interviewing, hiring, and training employees; planning, assigning, and directing work; appraising performance; rewarding and disciplining employees; addressing complaints and resolving problems
- High School Diploma or GED from an accredited Institution
- Minimum 3 years of supervisory experience in a production environment
- Prefer 5+ years of supervisory experience in manufacturing
- Experience supervising swing shift or night shift
- Experience with Lean Manufacturing and Continuous Improvement concepts and programs
- Exposure to Theory of Constraints (TOC), throughput and inventory management
- Experience with Environmental, Health and Safety programs
207
Manufacturing Supervisor Resume Examples & Samples
- Creates plans for and oversees mid to long term direction of the organization
- Environmental, Safety, Housekeeping, Quality and Health performance
- Production Planning and execution
- Maintenance work identification, scheduling and execution
- Implementing the tactical plans for areas of influence
- Budgeting, forecasting and managing cost to meet financial commitments
- Optimizes people performance and development through
- Mentoring, coaching, and training employees,
- Create and execute career development and progression plans for employees
- Effective utilization of the DPR process
- Formal and informal recognition of employees to reinforce desired results
- Provide redirecting feedback. Document issues and follow discipline process as needed
- Embraces change initiatives while leading the organization through change by modeling effective leadership
- Leverages both internal and external resources to effectively and expediently solve problems
- Exercises influence both within and across traditional boundaries to deliver outstanding business results for their team,
- B.S. Degree in Engineering or others degrees
- Demonstrated skills and experiences in manufacturing facilities
- Understands and collaborates with other departments to drive cost management, reliability, performance and on-stream
- Strong technical background as Engineer or Technician
- Lean/Six Sigma methodology
- Advanced Production System
- Chemical production processes
- Management of Change
- People Management
208
Manufacturing Supervisor Resume Examples & Samples
- Establishes a culture of respect, hard work, consistency and effective communication in the production facility and when interfacing with contacts external to the organization
- Maintains food production yields and quality assurance and control methods in a high speed food manufacturing operation focused on continuous improvement
- Utilizes company production planning tools and resources to maximize facility throughput and workflow
- Adheres to the Federal, State, and District rules and regulations pertaining to food manufacturing operations including both Food Safety and Employee Safety
- Maintains the company’s high standards of food safety, sanitation and cleanliness in all manufacturing facility areas
- Manages the health, sanitation, and safety regulations pertaining to the handling and storage of foods and the operation of food processing facilities and equipment
- Develops and maintains accurate records, makes mathematical computations, and prepares production reports
- Reviews and analyzes production work processes and implements corrective action for operational improvements
- Establishes and maintains effective working relationships with Peers, Vendors and Manufacturing Employees to ensure costs are aligned with the operating budget
- Participates in hiring, staff training and development, and the supervision of the production staff
- Conducts performance reviews and coaching for hourly manufacturing employees
- Flexible work schedule as dictated by the needs of the business
- Performs other duties, as assigned, and follows through on requests in a timely manner
- High School Diploma required, College Degree preferred
- 2 years minimum experience in a high volume food manufacturing facility
209
Cable Manufacturing Supervisor Resume Examples & Samples
- Demonstrate hands-on approach to supervising the build of product, frequently checking quality and adherence to process steps
- Resolves personnel problems by analyzing data; investigating issues; identifying solutions; recommending action
- Technical ability to know, understand and communicate the various processes of their department
- Ability to identify production bottlenecks or constraints and work with others to improve product flow
- Demonstrate equipment operations and work and safety procedures to new employees, or assign employees to experienced workers for training
- Responsible for schedule adherence while still maintaining high quality standards
- Demonstrates knowledge of labor standards and ability to compare actual labor hours to standard
- Look for and provide feedback on efficiencies, continuous improvement, cost improvements, and innovation
- Ensure cross training and job rotation of personnel; effectively and efficiently resource plan and schedule to meet commitments
- Ensure that employees are trained to the procedures, material and equipment prior to commencing work
- Conduct performance reviews, provide areas of development and recognize achievements
- Confer with management or subordinates to resolve workplace issues
- Ensure adherence to safety procedures, regulations and commitment to creating a safe working environment
- Shift work may be required. Overtime as needed to support department
- 5 years' minimum experience in a manufacturing environment, previous experience in a supervisory or lead position preferred
- Previous experience of quality systems and manufacturing processes required
- Proven ability to lead/drive change using lean manufacturing techniques required
- Ability to communicate effectively - verbal and written
- Must possess strong mechanical troubleshooting skills and be able to train associates in the team
- Strong understanding of Microsoft Office Programs such as Outlook, Excel and Word
- High School diploma or GED required, Bachelor's Degree preferred
- Climb up and down from equipment
- Regularly lift and/or move 10 pounds, frequently lift and/or move 25 pounds and occasionally lift and/or move 40 pounds
- Climb up and down a ladder
- Able to manipulate small hand tools
- Ability to reach with hands and arms and use hands to finger, or handle objects, tools and controls
- Ability to stand, walk and climb stairs regularly
- Ability to bend, squat, stoop, kneel, crouch or crawl frequently
- Ability to talk and/or hear frequently
- Specific vision abilities required by this job include close vision, peripheral vision, depth perception, and the ability to adjust focus
210
Manufacturing Supervisor Resume Examples & Samples
- Verbal and written communication skills. Should possess problem solving skills and ability to facilitate group meetings
- Experience with team building, process improvement, conflict resolution, and motivating people
- Ability to learn the use of ERP systems, Dayforce, Microsoft Project and Microsoft Office (Word, Excel, PowerPoint)
211
Manufacturing Supervisor Resume Examples & Samples
- High school diploma or its equivalent is required. Bachelor's degree in Engineering, Science, or Business is preferred
- A minimum of 8 years of experience or 4 years of experience with a Bachelor’s degree working in a regulated manufacturing environment is required
- Proven experience in leading a team in a manufacturing environment is preferred
- Knowledge of FDA, EMA, and cGMP regulations is preferred
- Proven ability to interact, motivate, and lead individuals in a manufacturing environment is required
- Must be able to meet the physical demand of that this position including continuous lifting and/or moving from 5 to 25 pounds weight material
- Must have the ability to work 1st, 2nd and 3rd shift.Production
212
Manufacturing Supervisor Resume Examples & Samples
- Responsible for manufacturing and remanufacturing activities for multiple product lines, ensuring that performance (inventory, cost, etc.) meets regional business requirements
- Manages a team of non-exempt individual contributors; leads and coordinates daily activities
- Ensures the delivery of products and services that meet the performance metrics defined by next level management
- Prepares monthly performance reports
- Engineering Diploma may be required in some countries
- Typically 2+ years of experience in an operations function
- Typically 0-2 years of project management experience
- Knowledgeable of country specific legislative and regulatory compliance (e.g., import and export regulations; trade restrictions, EH&S)
- Utilizes the expertise of others as necessary
213
Manufacturing Supervisor Resume Examples & Samples
- It is responsible for the safety of personnel, to ensure that the safety, hygiene and environmental standards are fulfilled through monitoring
- Coordinate the activities and resources necessary to ensure timely delivery to customers
- Make timely decisions to maintain production and be able to quickly analyze situations to direct staff
- Actively participate to maximize the utilization of space designated for the specific operations area using continuous improvement tools
- Develop and recommend improvements to facilities, equipment or procedures to improve safety, quality and efficiency
- Elaborate and analyze reports of the area and other areas with the collaboration of the SIM equipment
- Maintain a safe and clean workplace by training and directing personnel to comply with established policies and procedures, as well as the requirements of 5's
- Track the production process and the hourly time and reports results by turn delivery
- Ensure that updated SIM chalkboards are maintained by daily monitoring
- Interact with all support departments (Quality, Engineering, Materials, Maintenance, HR, etc.) to ensure team goals
- Apply disciplinary measures, corrective actions and improvement plans, according to the internal regulations of work
- Evaluate the development of staff, leaders and lower level supervisors while providing timely feedback
- Create employee development plans, promote cross training and contingency plans in critical operations including supervisors
- Communicate production goals and objectives and work expectations to operational staff
- Supervise employee training and ensures that it is put into practice
- Ensure that all staff are trained in their work and their workouts are properly documented and valid both in the records and their training shade
- Oversee payroll of the employees in charge through the use of the TRESS system
214
Manufacturing Supervisor Resume Examples & Samples
- Manage the manufacturing of products to meet deadlines and production goals
- Manages production to meet EBIT goals and monthly budgets
- Responsible for preventive maintenance and machine uptime
- Supports the Departmental Action Plans to achieve the Company's and Department’s long-term goals and objectives
- Assigns and schedules work to production employees, including supervisors and manufacturing engineering
- Inspects products to verify conformance to specifications and directs setup and adjustments of machines
- Recommends overtime when necessary to achieve production goals
- Observes equipment usage and employee quality of work and takes corrective action when necessary
- Manages and reports capital equipment including preventive maintenance, and procurement selection
- Monitors tools, material, quality, and production
- Interprets specifications, blueprints, job orders to workers and assigns duties
- Ensures that all manufacturing problems in the assigned shift are resolved
- Determines corrective actions and confirms full cycle of problem solving and prevention
- Organize and maintain high standards of performance, quality and customer service within all departments
- Responsible for adhering and implementing company policies and guidelines as prescribed by management
- Utilizes SPC, Real Time, and other tools within the system to manage the factory quality
- Implement and maintains continuous training for job related functions
- Interviewing, evaluating, hiring, training, motivating, supervising, and disciplining all personnel under direct supervision
- Responsible for the supporting and implementing company safety programs in the assigned shift
- Performs personnel functions; Coaches for improved performance, identifies/ develops high potential employees, conducts performance evaluations, disciplinary action and recommends compensation increases within company guidelines
- Maintaining a working knowledge of ISO policies, procedures, and directives
- Works with a certain degree of creativity and latitude as required
- Implements and suggests waste elimination initiatives specifically related to the function and department such as EMS and recycling opportunities to elimination of production waste
- B.S. Degree preference in Mechanical or Manufacturing Engineering
- Minimum 5 years working experience in manufacturing environment preferred
- Minimum of 5 years equivalent combination of education and experience in manufacturing environment preferred
215
Manufacturing Supervisor Resume Examples & Samples
- Champion for Safety
- Using thorough up-to-date knowledge of the process and equipment for which they are responsible, plans work and production for the shift
- Insure associates have the needed raw materials, instructions, machine availability, and training to meet production requirements
- Observe associates for effectiveness, efficiency, performance safety practices, following instructions and procedures to reduce scrap usage and waste. Evaluate process, work performance on each associate, and make recommendations
- Keep records during each shift on attendance, absence, call ins, and over time schedule
- Assures that all the manpower, raw materials, and equipment is on hand and running in order to produce the highest quality product, in the mast efficient, and timely manner
- Perform other tasks that are reasonable to the job as requested by Direct Management
- Perform routine and on-going monitoring of machinery/equipment use within area of responsibility to ensure that machine safeguards/controls are effectively in place whenever machines are operating in a production mode
- Proven experience in manufacturing management
- Must have good attention to details, but be able to manage the big picture and have a “make the numbers" mentality
- Must be able to manage multiple, complex tasks and deal easily with pressure on a day in and day out basis
- Must be able to motivate, communicate and drive continuous improvement
- Critical thinker, with excellent analytical abilities
- Good written and oral communication skills
- Solid planning, leadership, and administrative skills
- Good understanding of business principles and practices; can effectively manage the manufacturing function with a bottom line result
- Champion for safety and injury prevention
- At least two years of experience in manufacturing supervision (OLPC)
- Strong manufacturing background; able to understand and develop appropriate product specifications
216
Manufacturing Supervisor Resume Examples & Samples
- Establishes and maintains an environment conducive to continuous improvement manufacturing; recommends alternatives for improving production methods, equipment, operating procedures, and working conditions
- Participates in and directs problem-solving meetings and activities (i.e. accident investigations, quality concerns, etc.)
- Drive activities to reduce past due, scrap, rework and overtime cost while meeting safety and quality objectives
- Drive activities to improve on-time delivery, labor utilization and productivity
- Train evaluate, coach and develop subordinates utilizing the Eaton performance management system to help them meet established objectives and improve their overall performance and competencies
- Maintain and consistently administer local policies to meet day to day operating requirements. Ensures that all regulatory standards and company policies are understood, supported, and followed on the production floor
- Proactively manages the performance of all subordinates through daily coaching and periodic written evaluations and rewards and recognizes positive efforts of employees; implements corrective actions as appropriate
- Six Sigma Knowledge/Lean Experience; Greenbelt/Blackbelt certification preferred
- Ability to manage multiple projects and relationships simultaneously and the ability to work among competing priorities
217
Manufacturing Supervisor Resume Examples & Samples
- Identify and implement ways to reduce cost on jobs
- Demonstrate safe behaviors and hold people accountable to follow the programs set forth by management. Make recommendations for program changes or additional safety programs
- Working with the quality staff to help guide the staff through the quality expectations which are set by our customers. Interpret the nuances of acceptable from unacceptable with the assistance of peers
- Sets the expectations and provides the benchmark for standards in both work processes and production. When employees are not meeting the expectations of the area, there is a responsibility to address poor performance so employees can change
- Responsible for independently performing or recommending the following: hiring, performance ratings, merit and/or promotional increases, resolving grievances or complaints, addressing performance issues, staffing levels, training, and personnel actions. Directs day-to-day activities so that unit meets production quotas and deadlines. Receives assignments in the form of objectives with goals and the process by which to meet goals. Provides direction to employees according to established policies and management guidance. Administers company policies that directly affect subordinate employees. Management reviews work to measure meeting of objectives
- Full knowledge of job related policies and procedures as well as corporate policies and procedures that may impact role functioning, particularly regarding Human Resources
- Effectively distributes work, evaluates performance, provides performance feedback, and assesses and selects candidates
- Executes against plans developed by higher levels of management
- First true level of supervision. Responsible for recommending staff levels, personnel actions, and for directing day to day activities
- Associates degree required, 4-year degree in a technical field or management preferred
- 5 + years experience including minimum 1 year as team lead / supervisor
- Proficiency with Microsoft Office applications
- Experience in printing / label industry preferred
218
Senior Manufacturing Supervisor Resume Examples & Samples
- Ensure that area spending is within budgeted amounts
- Lead daily production line meetings with support staff (engineers, planning, and quality); prioritize projects; organize the efforts of the support team; facilitate resolution of issues
- A minimum of four years’ experience supervising in a highly regulated manufacturing environment is required. Medical device manufacturing experience is highly preferred
- Attention to detail and the ability to work in a fast-paced changing environment is key
- Requires excellent communication skills, direct and to-the-point (written and spoken), and possess strong capabilities in managing, coaching and training talent
- Ability to adapt to changing requirements
219
Area Manufacturing Supervisor Resume Examples & Samples
- Support your team with any resources they need for success – tools, manpower and materials
- Enforce internal rules as outlined in the Standard of Conduct and non-negotiables
- Fill out incident reports immediately and prior to leaving the shift
- Place all orders in CEOS (supplies, tools etc.)
- Conduct all inventory counts
- Maintain your area is in order. Material flow is happening. FIFO is followed
- Enter maintenance work orders in SAP
- Keep product moving in the plant
- Maintain safety and housekeeping
- Ensure all hourly employees are qualified to perform duties in a timely manner
- Maintain efficiency levels to assure availability of components to meet required schedules
- Assist in identifying potential machine or quality problems within department of responsibility
- Participate and prepare for all internal and external QA / Customer audits, close all findings in a timely manner
- Management of confidential information
- Follow all processes for containment and repair of material
- Change over check list completion
- Timely response and effective resolution for departmental misproductions
- Ensure that all sequenced production orders for the shift are executed and completed and communicate the “whys” if not met, reason code must be entered in SFI every day
- Insures departmental technical compliance to all mandatory requirements including Safety, Environmental, ISO, Quality, Plant policy, Corporate policy, etc
- Assist with the development of instructional programs, process control plans and PFEMA of equipment. Identify/ incorporate best practices and lessons learned into program plans
- Train/present course material. Insures maintenance of instructional programs, departmental work instructions, quality records, training records
- Coordinate, participate and track departmental improvement initiatives including Kaizen, TQM, TPM, 5S and Six Sigma initiatives
- Work with process engineers on improvement projects
- Perform other miscellaneous duties as assigned. Maintain all departmental records, including overtime and vacation scheduling
- Other duties as assigned by Manager
- 3+ years manufacturing supervisory experience or relevant military supervisory experience
220
Manufacturing Supervisor Resume Examples & Samples
- Directly supervises a shift of production operatives with the goal of meeting/exceeding requirements for OTDP, WO accuracy, attainment to standard, quality and cost
- Directs work of Leads in driving actions and results, and develops capabilities of Leads through mentorship
- Develops and manages a high-performing, flexible team that is able to shift rapidly to respond to the needs of customers
- Maintains a safe working environment for their employees and enforces safety policies
- Drives employee engagement and IDEX values into the culture of the Denver Factory
- Coordinates cross shift activities to ensure that all jobs can be completed in the most efficient manner
- Ensures that all company policies and procedures are adhered to where applicable
- Drives continuous improvement activities, increases productivity, and reduces the cost of poor quality (COPQ)
- Carries out supervisory responsibilities in accordance with the organization’s policies and applicable laws
- Collaborates with all Lean initiatives and ensures employee participation
- For Transportation business line, it is helpful to understand TS certification requirements and Automotive-specific quality standards
- Ability to problem solve and improve processes
- Strong personal computer skills and spreadsheet experience (Excel preferred)
- Problem Solving:The individual participates in the continuous improvement process by attending meetings and presenting problems and possible solutions to the appropriate personnel
- Interpersonal Skills:The individual remains open to others’ ideas and exhibits willingness to try new things
- Relationships with Others: The individual works effectively and relates well with others, including superiors and colleagues. The employee exhibits a professional manner in dealing with others and works, to maintain constructive working relationships
- Operational Excellence:The individual is dedicated to providing organization systems for measuring work. The individual seeks to reduce variances in organizational processes
- Communication and Contact: The individual communicates effectively both verbally and in writing with superiors, colleagues, and individuals inside and outside the Company
- Planning/Organizing:The individual prioritizes and plans work activities, uses time efficiently and develops realistic action plans
- Quality Control:The individual demonstrates accuracy and thoroughness and monitors own work to ensure quality. The individual delivers the highest quality products which meet the requirements of internal and external customers
- Adaptability:The individual adapts to changes in the work environment, manages competing demands and is able to deal with frequent change, delays or unexpected events
- Dependability: The individual is consistently at work and on time, follows instructions, responds to management direction and solicits feedback to improve performance. The individual completes all duties as assigned, trains as required, and rotates into other departments as required
- Safety and Security: The individual actively promotes and personally observes safety all safety procedures. The individual compiles with Environmental, Safety, and Hazardous Communications requirements
221
Manufacturing Supervisor Resume Examples & Samples
- Bachelor's degree (or in process of attaining)
- Proven supervision experience
- Strong Leadership skills
- 8D Problem solving experiences
- Lean Manufacturing based principle experiences (ie. 5S, material flow methodologies, workstation / line / cell layout and architecture, Standardized work instructions, cross-training)
222
Manufacturing Supervisor Resume Examples & Samples
- High energy level, assertive personality and comfortable performing multiple projects in conjunction with normal activities
- Demonstrated ability to influence others to achieve required results
- Highly organized with good communication skills (verbal and written) and able to efficiently organize and complete daily activities
- Good interpersonal skills. Ability to get along well with others, tactful, mature flexible
- Ability to establish credibility and be decisive – but able to recognize and support the organization’s preferences and priorities
- Results oriented with focus on project completions
- Minimum of a Bachelor’s Degree – Engineering or related technical degree required, or eqiuvalent years of experience
- 5 – 7 years’ experience with a solid manufacturing background
- Repair Station experience
- Utilize appropriate methodologies to manage all projects
- Partner with the Master Scheduler and Planners to ensure accuracy and adherence to production schedules
- Experience in troubleshooting, investigation, root cause, 5 why's and risk analysis
- Strong process orientation, analytical and planning ability
- Strong interpersonal & communication skills to collaborate effectively build team consensus and influence others through leading mentoring & facilitating
- Excellent analytical, problem solving, project management and facilitation skills
- Self-starter, able to work with or lead cross-functional teams
- Strong financial acumen
- Previous experience with or training in lean tools (5S, Kaizen, Visual Management, Value Stream Mapping) desired
- Implementation experience with basic concepts of lean manufacturing
223
Manufacturing Supervisor Resume Examples & Samples
- Minimum of 1 (one) year of Supervisory experience directly managing people
- Familiarity with process improvement methodologies and project management skills and applications
- WIP process management
- Line balancing/load leveling experience
- Someone with experience with continuous flow
224
Manufacturing Supervisor Resume Examples & Samples
- To manage the arrangement of production operator to follow up production planning (monthly, weekly, daily) to achieve good OTDM and productivity (in term of hour and production cost)
- To follow up production order and run it based on priority to achieve good
- To improve the productivity of Line Structure (Line leader, feeder, Line Inspector) by organizing, training, motivating
- To control the WIP inventory at optimum level, with a good flow (including: sub-assy and debug), and maintain high accuracy in SAP
225
Manufacturing Supervisor Resume Examples & Samples
- Bachelor’s degree with 5 years experience; additional years of experience will be considered in-lieu of degree
- Strong experience with employee development
- Must have ability to work 2nd shift
- Experience with F-35 CNI Hardware products a plus
226
Manufacturing Supervisor Resume Examples & Samples
- Prioritize production schedules based on product introduction, equipment efficiency and materials supply for various departments, workflow and workstations
- Plan and administer procedures, select & develop employees to ensure an efficient operation of the production function – provide training, keep track of employee time & attendance
- Develops schedules and manpower requirements for assigned departments
- Maintain specifications to make sure they are accurate and up to date
- Assist in new product development, product improvement
- Bachelor's degree in Management, Engineering, Science or equivalent experience required
- 5 years of direct leadership experience, in addition to manufacturing and assembly supervision required
- Must be able to learn and communicate with all levels of personnel (technicians, engineers, assemblers, mgmt) and be highly organized with administrative documentation
- Must possess effective problem solving and solid reasoning skills
- Strong knowledge of electro-mechanical assembly processes and procedures such as relay adjust and final assembly tasks
- Must be able to handle and prioritize, work well with minimal direction, and effectively utilize time and resources
- Knowledge of supply chain management
- Familiarity & practical use of MS Excel/MS Word/MS Outlook, MRP System, Microscope, shims, gauges and small hand tool preferred
- PHYSICAL DEMANDS: Will be required to occasionally stand/walk/sit/reach with hands and arms/climb or balance/stoop, kneel, crouch/taste or smell/lift up to 25lbs; Will frequently use hands to finger, handle or feel/ lift up to 10 lbs; Will continuously need to talk or hear
- VISION requirements: must be able to see clearly at 20 feet or more, be able to distinguish and identify colors, be able to have depth perception (3D vision) with the ability to judge distance and spatial relationships, also the ability to adjust focus as needed
- WORK ENVIRONMENT: Clean room environment (smock and hair cap provided, no make-up, closed toe shoes required); occasionally able to work in wet or humid conditions (non-weather related), be exposed to vapors, airborne particles, possible chemicals or radiation (safely below occupational exposure levels). Frequently working near moving mechanical parts. Noise level is moderate (light traffic)
- Candidate must be a US Person
227
Manufacturing Supervisor Resume Examples & Samples
- Acts as a primary resource for the production team to help drive continuous improvement and organization driven results in the areas of Safety, Quality, Cost, Productivity, Service, and Employee Engagement
- Maintain housekeeping standards and ensures safe and healthy working conditions and an organized work environment
- Plans, Coordinates and executes established daily activities of department to ensure that goals are met
228
Manufacturing Supervisor, Coinstar Resume Examples & Samples
- Lead and direct the daily manufacturing operations to meet production goals, quality, and cost objectives
- Oversees the implementation of manufacturing schedules, personnel requirements, quality control, production standards, and safety programs
- Develops and administers procedures for manufacturing operations
- Oversee the flow of hardware and machines through depot repair and manufacturing
- Hire, train, educate and coach a staff of technical employees on the best industry practices within a manufacturing environment
- Develops schedules and staffing requirements for assigned areas
- High School Degree or GED required; Bachelor's degree strongly preferred
- 5 years’ experience in a medium to large manufacturing facility
- 2+ years of supervisory experience
- Must have working knowledge of ISO, Six Sigma, and GMP
- MRP systems, GMP, ISO requirements, Six Sigma and or equivalent quality systems
- Must have proven track record of leading, hiring, and managing a technical work-force in a successful company
- Must have clear understanding of the benefits of a strong team and the essential need for building a team environment
- Clear understanding of quality systems, Electro/Mechanical Engineering and a commitment to lifelong learning
- Exceptional organizational skills and capability of handling multiple tasks and assignments in a fast paced demanding environment
- Proficiency in Microsoft products including Word, Excel, Access, and PowerPoint
229
Manufacturing Supervisor Resume Examples & Samples
- Supervise safety in manufacturing environment and be responsible for employee training
- Direct and coordinate the development and implementation of activities in production area(s) to meet production goals, quality, and cost objectives
- Prioritize production schedules based on product introduction, equipment efficiency and materials supply
- Develop and evaluate personnel to ensure the efficient operation of the production function
- Organize and manage daily activity of product line
- Shorten operation cycle time and reduce cost
- Lead projects & achieve goals
- Provide technical, strategic and tactical direction for the area/shift NXP Fab Team
- Area sustaining shift coverage for all three: process, equipment and manufacturing
- Owns availability performance and escalations on shift and tool utilization
- Owns execution to all quality components including inspections, tool qualifications, tool PMs etc
- Reports: all direct labor on shift (process technicians, maintenance technicians, MSTs & associates)
- Reports to Operations Section Manager, works compressed schedule
230
Manufacturing Supervisor Resume Examples & Samples
- Supervise the production process. Monitor adherence to policies and procedures
- Lead and coach a team of operators to meet production schedules, quality standards, and to resolve production issues,
- Coordinate with manufacturing leads, Manufacturing management, and with support groups to assure production activities occur on schedule and to specifications
- Audit internal systems and procedures for compliance to GMP and EH&S. Look for opportunities for continued improvement
- Assist area management with developing capital and resource requirements plans
- Facilitate, manage, and execute manufacturing activities required for validation studies, process characterization, technology transfer, and commercial or clinical operations
- Assisting in regulatory inspection preparation and inspections
- Create cooperative processes and systems with support departments to schedule activities and/or resolve issues
- Participate in all departmental media qualification requirements; become fully qualified and proficient in all aspects of manufacturing
- Review GMP documentation such as batch records, forms, charts, logs. Review and approve incident reports and investigations in Track Wise
- Form and support internal and/or cross functional teams for continuous improvement
- Serving as the central point of contact for operational issues
- Develop, oversee and administer training for new employees, maintain skills of current employees, and advance skills of current employees as part of career development
- Work with department management to develop area metrics and goals
- Provide area oversight for EH&S policies and procedures. Liaise with the departmental safety committee member to coordinate audits and committee initiatives
- Maintain proficiency in cleanroom gowning and procedures
- (insert people management skills/requirements)
- 3 years of leadership experience and a bachelor’s degree in a technical discipline from an accredited college or university is required OR
- 7 years leadership experience in a regulated environment
- A minimum of 5 years of industry experience in a supervisory role is also required
- Demonstrated experience in a GMP manufacturing environment, understanding of GMP, and quality leadership on the manufacturing floor
- Performance as a “hands on” supervisor with a strong pharmaceutical/biopharmaceutical manufacturing background
- A good team player; able to develop and coach teams; experienced with conflict resolution; possess good interpersonal skills
- Ability to grasp complex concepts and systems and the documentation that accompanies them
- Self directed, logical, organized and able to work with little direct supervision in a team environment in order to meet the production schedule
- Flexible, decisive, and able to manage changing and multiple priorities
- Must possess strong written and verbal English communication skills: able to effectively communicate to the rest of the team; author memos, reports, SOP’s
- Experienced in training operators
231
Manufacturing Supervisor Resume Examples & Samples
- Three to five years of manufacturing supervisory experience preferred
- Journeyman Tool and Die certification preferred
- Assign work to and instruct, assist or direct die makers, tool room machinists and production operators
- Oversee and perform machining operations to build, test, install, modify and maintain permanent and temporary tooling, dies, fixtures, jigs, gauges, etc., using company designs, specifications or concepts
- Develop and use maintenance and operation guides for temporary and permanent production tooling, dies, gauges, etc
- Instruct production employees on the use, maintenance and operation of temporary and permanent production tooling, dies, gauges, etc
- Assume responsibility for the quality of workmanship, dimensional accuracy and efficient mechanical operations of assigned work areas
- Should possess problem solving skills and facilitate group meetings
- Skilled in the use of ERP systems, Kronos, Microsoft Project and Microsoft Office (Word, Excel, PowerPoint)
- Maintain and enforce a Safe work environment
- Make decisions and take action
- Analyze and make recommendations
- Maintain relationships with other departments and people
- Champion Lean Manufacturing Principles
- Assist in program launches
- Assure integrity of manufacturing processes
- Participate as a member of the Manufacturing Team
- Perform other duties as necessary in support of business objectives
232
Manufacturing Supervisor Resume Examples & Samples
- Reviews daily and weekly shipping schedules and production capabilities to assure all deadlines are met. Checks running orders/query dispatch lists to determine schedule priorities. Coordinates and expedites hot parts and assigns rework
- Maintains close contact with the M.E.Group to develop and maintain gauges, fixtures and SOEs
- Works with D.E. Group to incorporate new product development and improvements. Investigates the Root Cause of defects and scrap, implementing corrective action
- Work requires periodic stooping/bending and frequent walking/standing throughout day
- Requires occasional lifting of objects less than 25 pounds as well as occasional lifting of objects 25 to 50 pounds
- May on occasion require lifting, with assistance, of objects weighing 50 to 75 pounds
- Work involves activities that require special safety precautions, e.g., working around moving parts, machines, welders or vehicles
- Requires use of protective clothing
233
Manufacturing Supervisor Resume Examples & Samples
- Supervise all employees
- Drive the TOC’s so all goals and costs targets are achieved
- Participate in all Safety activities and observe and record employees
- Discipline floor workers within the rules of the Union Local 40 contract
- Fill in daily tracking logs
- Maintain employee’s time and absences
- Prep and track workers schedules
- Includes shift and weekend work, along with a rotating schedule
- Implement and maintain 5S
234
Manufacturing Supervisor, RPM nd Shift Resume Examples & Samples
- Develops and mentors students through delegation of duties, coaching, and mentorship.Counsels students on work related questions and problems.
- Motivates students to improve their knowledge and performance through study and educational participation
- Supervises daily operations, checking on workmanship, efficiencies, safe working conditions and methods and compliance with specifications. Reports daily, weekly and monthly performance against established goals and metrics.
- Identifies training gaps and works to develop skills/training needs
- Possesses a general understanding of company policies and goals
- Assures adequate supply of tools, equipment and materials for efficient department operations
- Checks and reports on status of production and takes action to eliminate delays and parts shortages
- Confers with Quality Control on the disposition of questionable inspections "squawks" and the control of recurring quality defects
- 1-3 years working with students and/or at risk youth (volunteer or paid)
- Demonstrated leadership, communication, interpersonal and team building skills
- Experience in Lean Manufacturing and Six Sigma
- Demonstrated ability to understand and improve manufacturing operations, business processes or systems
- Ability to plan and execute multiple projects/activities
- Microsoft software experience required (Outlook Excel, Word, PowerPoint etc)
- Effective written and oral communication and presentation skills.
235
Manufacturing Supervisor, nd Shift Resume Examples & Samples
- Provide guidance, training, feedback and annual performance reviews for milling department personnel. 3. Instruct and ensure compliance of all Milling Operators in standard milling procedures, required safety and environmental practices and housekeeping responsibilities
- Perform daily crew assignments, supervise the job performance of milling operators and provide regular feedback and support
- Visually inspect raw materials to verify quality and report discrepancies to Quality Control
- Monitor raw material supplies to insure adequate inventories for the production schedule
236
Container Manufacturing Supervisor Resume Examples & Samples
- Ensure department KPI’s (blow molder availability, air and electric usage, defect rate, asset intensity, machine availability, product quality) are met or exceeded by removing team barriers to success
- Coach, mentor and develop team members (which include all blowmold & injection operators and mechanics) to meet current and future business requirements
- Accountable for TPM implementation in the department and successful delivery of AM and PM drivers such as Index of minor stops, MTBF, Red tag closure, BDA closure and improved technical competency for team members
- Accountable for analyzing minor stops, process failures and breakdowns in the Container department in order to develop countermeasures to prevent re-occurrence using the tools of NCE
- Ensure complete compliance to prescribed Safety, Quality and HR policies, including GMPs, FSMS requirement and 5S processes and applies them fairly and consistently
- Maintain, review and report KPIs, plans and variances to daily review meetings, weekly BM / Injection reviews and monthly updates on improvements and opportunities
- Daily review of autonomous and planned maintenance effectiveness, process controls (SPC), bottle quality with production, quality and maintenance teams
- Investigate, develop and implement action plans to address failure root causes, eliminating waste and opportunities for continuous improvement
- Utilize the QS Infinity, SAM, Sidel Information and EIT systems to identify waste and opportunities for continuous improvement. Develop and implement these plans
- Enhance the use of SPC to continuously improve pre-form and bottle forming
- Understand and represent all regulations, and NWNA policies, procedures and work instructions; apply fairly and consistently
- Provide flexibility and availability to meet and support business objectives
- Post-secondary education is required. A degree in a technical field is preferred
- Demonstrated supervisory, organizational and problem solving skills
- Experience and knowledge of plastics, including injection molding and blow molding processes. Experience with Sidel and Husky equipment preferred
- Ability to work in a fast paced and rapidly changing environment
- Ability to work additional hours as required
- Good coordination and monitoring skills
237
Manufacturing Supervisor Specialists Resume Examples & Samples
- Practices and ensures safety of manufacturing areas and work practices in accordance with site Health, Safety and Environmental program
- Manages cross functional teams to drive complex investigation close outs, determine root cause and implement appropriate corrective and preventative actions
- Utilizes manufacturing process knowledge and investigation sill sets to identify and resolve manufacturing issues, improve process operations and affect positive change
- Conducts complex document revisions and/or document management including batch production records, manufacturing procedures and cross functional procedures
- Works with manufacturing managers and supervisors to develop and maintain training materials and curricula on process operations, theory and compliance
- Performs training with staff on the floor as needed
- Leads cross-functional continuous improvement teams with Engineering, Validation, Quality Assurance, Quality Control, Facilities, Metrology and Manufacturing Technical Services
- Works independently with minimal supervisor and direction
- Performs work that consistently requires independent decisions making and the exercise of independent judgment and discretion
- Creates and presents trending and metric reports
- Provides direction to the Manufacturing Specialist in the absence of the operations manager
- Selects, develops and motivates qualified staff to effectively carry out department functions and provide for the continuity of managerial and specialized skills
- Provides leadership, guidance and direction to staff consistent with cGMP and company corporate quality governance
- Coaches and mentors staff in all aspect of their job performance and career development including training, feedback, reward and disciplinary action
- Develops work plans, assign tasks and supervise team(s)
- Ensures staff has appropriate knowledge of department processes and procedures
- High school diploma/GED or biotech Certification with 7-10 years of experience in cGXP manufacturing environment or Bachelor’s Degree with 5-8 years of experience
- 1 year in a lead or supervisor role
- Subject matter expertise in biologics manufacturing
- Minimum of 2 years of experience with deviation or investigation management systems
- Bachelor’s degree in Biology, Chemistry, Biochemistry or Chemical Engineering
- Ability to influence in a cross functional environment
- Experience authoring and reviewing standard operating procedures, on-the-job-trainings and other controlled documents
- Familiarity with Deviation Management System (i.e. Trackwise)
- Experience in troubleshooting, investigation and root cause analysis in a GXP environment
238
Assembly Manufacturing Supervisor Resume Examples & Samples
- Supervision, including retention, performance review, discipline, and assisting in the hiring process
- Employee training and development
- Ability to balance and achieve positive results in the areas of safety, quality, productivity, cost and employee relations
- Systems and continuous improvement orientation
- Inventory management
- Product and process knowledge
- Completes other assignments and special projects as requested
- 3+ years in Assembly Supervision
- Ability to lead people and get results
- Experience with manual labor supervision
- Motivate people
- Bilingual preferred
- Experience with power tools
239
Container Manufacturing Supervisor Resume Examples & Samples
- Provide the planned production cases to support customers through the production plan
- Ensure planned KPI’s of Efficiency and Performance are met or exceeded
- Develop and track improvement in reduction of planned and unplanned downtime hours
- Manage the adherence to prescribed procedures to ensure the first time quality meets or exceeds planned goals
- Ensure QMS standards for all aspects of production are enforced
- Ensure prescribed department preventive maintenance activities are completed timely
- Ensure complete compliance to prescribed GMP’s and 5S processes
- Track competencies of direct reports and provide leadership and development
- Provide leadership in TPM process and activities
- Bachelor’s degree in Engineering Preferred or equivalent work experience
- Commitment to NWNA’s Aspirations and Beliefs
- Exceptional work ethic / dependability
- Strong oral / written / interpersonal communication skills
- Excellent organizational and analytical skills
- Tactful interaction with peers, subordinates, vendors and customers
- Ability to lead, train, motivate, coach and develop individuals and teams
- Problem solve creatively to lead team through improvements
- Ability to remove team barriers to ensure achievement of all Key Performance Indicators
- Proficient computer skills, SAP, Microsoft Office (Excel, Word, Outlook, Access, Power Point), Microsoft Live Meeting
- Experience and knowledge of plastics including injection molding processes and blow molding processes
- Experience with Sidel and Husky equipment preferred
- Experience and knowledge of mechanical piping systems including compressed air and cooling water
- Experience in continuous improvement programs such Nestle Continuous Excellence, TPM, or Lean Manufacturing
240
Operations / Manufacturing Supervisor Resume Examples & Samples
- Provide Operations Leadership which promotes, maintains, and enforces safe and healthy working conditions for all employees in accordance with regulatory requirements and company standards
- Coordinate the flow of product in the forge shop
- Assure conformity of product and processes to established specifications. Maintain a high standard of product quality in accordance with ISO, AS9100, and the Company’s Quality Manual, stopping jobs if process and instructions are either substandard or unclear
- Manage throughput performance of several manufacturing departments
- Motivate, coach, manage and evaluate labor and workforce performance; provide disciplinary action, if required
- Manage the training and development plans of new and incumbent employees
- Improve velocity of manufacturing operations and turnover of WIP inventory
- Participate in daily efforts to improve equipment uptime and 5S performance
- Promote completeness and correctness of information pertaining to operations
- Daily involvement in meeting TOC lines and inventory by department
- Take on SPA (Single Person of Accountability) roles in Environmental, Health and Safety (EHS) initiatives
- Manage financial expectations
- Manage resources within given area of responsibility to ensure that staffing and equipment readiness levels match business activity levels
- Identify and execute cost savings initiatives to positively impact the business’ and Operation’s goals regarding Variable Cost/Earned Standard Hours
- Read and interpret drawings, specifications, processes to complete the appropriate paperwork to meet quality process documentation requirements
- Maintain good working relationships with fellow supervisors, quality control and inspection personnel, in order to ensure a continuous flow of required productivity throughout the plant
- Work with the Forge Shop Team to drive continuous improvement through ABS, TPM and 5S
- Other tasks as assigned
- Strong interpersonal and leadership skills; able to interact with all levels of the plant
- Ability to write routine reports and correspondence; ability to read and interpret documents such as safety rules, operating and maintenance instructions, and procedure manuals
- Ability to effectively manage multiple priorities in a fast-paced environment
- Bachelor’s Degree from an accredited Institution
- Minimum 2 months of experience in Manufacturing
- This position is subject to the International Traffic in Arms Regulations (ITAR) which requires U.S. person status. ITAR defines U.S. person as an U.S. Citizen, U.S. Permanent Resident (i.e. 'Green Card Holder'), Political Asylee, or Refugee
- Prefer the Bachelor’s Degree is in Business, Mechanical Engineering, Metallurgical Engineering, or Materials Engineering
- Familiarity with Lean Manufacturing principles and programs
- Familiarity wtih ERP systems
- Proficient with MS Office
- Experience with data analytics; use of Microsoft Excel to create charts and graphs
241
Manufacturing Supervisor Resume Examples & Samples
- Responsible for the direct supervision/management of the staff
- Responsible for providing objective-oriented direction to subordinates utilizing management guidelines & general policies
- Experience working in a DoD manufacturing environment
- Previous Project or Program Management experience
- First Line Manager experience managing assemblers and test technicians
- Prior experience with Line Scheduling
- Prior experience with Environmental Health and Safety (EHS)
- Prior experience utilizing Kaizen Techniques
- Must be able to obtain a Secret Clearance with Special Access Permission
- Must be able to work a 3 (day) 12 Hour Shift
- Experience with Monthly Preventative Maintenance on Production and Environmental Test equipment. To Include but not limited to, Stencil Cleaner, Vibration systems, Temp Chambers, Pad Cooling Systems and Fume Extractors
- Experience with SAP and shop floor control systems
- Experience with calibration of test equipment
- Understanding development of overhead budgets for supplies and expenditures
- Proficient in ESD Training and Certifications
- Proficient in electronics equipment programming and maintenance
- Ability to track PO Funding and Period of Performance for all Production equipment requiring repair and update as required
- Ability to ensure that all chemical supplies requiring shelf life are current and not expired
- Experience with purchasing supplies, chemicals, spare parts and tools for production labs
242
Manufacturing Supervisor Resume Examples & Samples
- Supervise a group (or groups) engaged in various activities in the Operations organization
- Direct the resolution of technical and logistical problems, as well as the introduction of measures to improve operations and customer relations
- Plan and establish schedules and assign work while considering requirements and priorities
- Ensure most effective utilization of staff and equipment in order to cost-effectively achieve objectives while concurrently implementing efforts to continuously improve performance
- Monitor activities, as well as anticipate and respond effectively to problems to ensure that employees are properly trained and that work is performed in accordance with health and safety requirements
- Manage the resolution of complex technical problems and human resources issues, in concert with senior managers and human resource representatives
- Maintain awareness of new developments and technologies: review equipment capabilities, methods, and processes, then determine feasibility of utilizing alternative approaches, consolidating functions, and modifying or replacing equipment to reduce costs and improve quality
- Devise and implement new approaches to recurring problems
- Provide guidance and training, and ensure fair and equitable treatment of staff
- Assist less experienced supervisors with the more complex aspects of their assignments
- Manage and document employee performance, and develop associated recommendations
- Develop a thorough knowledge of the organization's activities and independently resolve complex problems
- Communicate effectively, represent the group, and influence decisions
- Anticipate problems and recognize opportunities for cost-effectively improving operations
- Bachelor’s degree and 5 years of experience in manufacturing and/or military environments; OR
- Associate's degree and 7 years of experience in manufacturing and/or military environments; OR
- High School Diploma (or GED) and 9 years of experience in manufacturing and/or military environments
- High school diploma or GED and twelve (12) years of experience in manufacturing and/or military environments; OR
- Associates degree and ten (10) years of experience in manufacturing and/or military environments; OR
- Bachelor’s degree and eight (8) years of experience in manufacturing and/or military environments; OR
- Master’s degree (MS) and six (6) years of experience in manufacturing and/or military environments
- Bachelor’s degree in Engineering, Business Management, and/or other related fields
- Lean Manufacturing and/or Six Sigma certification (Green Belt or Black Belt)
- Proven leadership expertise with supervisory experience
- Experience working with electrical manufacturing, power electronics, and/or transformer systems
- Excellent communication skills (written & verbal) and a high level of integrity
243
Manufacturing Supervisor Resume Examples & Samples
- A results driven individual who has demonstrated ability working in a high performance manufacturing environment
- Able to understand, communicate and improve key performance metrics
- Must have good attention to details, but be able to manage the plant expectations
- Critical thinker, with strong analytical abilities
- High energy, demonstrates urgency in a fast pace environment
- Good understanding of business principles and practices; can manage the manufacturing function to a bottom line result
244
Manufacturing Supervisor Resume Examples & Samples
- Manage day-to-day manufacturing operations including activities of quality management and production scheduling, people management
- Ensure the total manufacturing objectives including output, quality requirements and OTD are accomplished in a timely and cost effective manner
- Drive continuous improvement in quality, productivity, material usage reduction. Drive cost reduction projects
- Apply lean manufacturing practices, control work-in-progress inventory and drive cycle time reduction
- Implements and ensures conformance to all safety practices
- Coordinate with other functions to ensure production activities go smoothly
- Train, develop, coach and follow-up on teaming programs like SMWT / TPM / 5S activities, Lean manufacturing, VSM, and OEE
- Support Manufacturing Manager in staffing model including hiring, training and multi-skill development
245
Manufacturing Supervisor Resume Examples & Samples
- Ensures production is maintained in accordance with time schedules, engineering specifications, quality standards, expense budgets, employee safety and cost goals
- Prioritizes production schedules based on product introduction, equipment efficiency and materials supply
- Drives process improvements throughout the group utilizing lean concepts, six sigma methodology, kaizen methodology
- Leads and participates in cross functional teams in order to achieve company goals
- Identify needed operator training (multi-skill) and flexibility to improve productivity and efficiency
- Handle and coordinate quality problems occurring on production line
- Complete required production reports, quality records and operator evaluations
- Analyzes, suggests and implements activities to eliminate waste, redundant operations and improve material and product flow
- Maintains close liaison with quality and other productive groups, keeping them informed of any product difficulties or quality problems
- Bachelor's degree in Business, Engineering or related field with 1-3 years of related experience
- Applied knowledge in lean manufacturing, six sigma principles, ISO 9000, ISO 14001, and proven ability to lead successful and engaged teams
246
Manufacturing Supervisor Resume Examples & Samples
- Supervises manufacturing personnel in the weld and assembly areas
- Hires, trains and develops staff members
- Maintains a clean and safe work area to Clean room standards
- Effectively manages individuals and teams including performance management, conflict resolution, work scheduling, training, and successful accomplishment of delivery and quality objectives
- Strong management, leadership and organizational skills
- Ability to work effectively with operations and other groups to ensure that site delivery and quality issues are met
- Working knowledge of MRP/ERP applications; Visual preferred
- 3+ years supervisory experience in high-technology manufacturing required, experience in semiconductor capital equipment or related industry highly preferred
- Working knowledge of quick-turn, engineer-to-order environment desired
- Prior experience in cycle time, yield or cost improvement projects desired
247
Manufacturing Supervisor Resume Examples & Samples
- Plan, organize and safely control the direct labor and indirect labor for assigned areas of production, working knowledge of SAP a plus. Identify material shortages, scrap, rework key
- Identify, implement, and follow up on improvements for safety, effectiveness and cost. Develop production schedules
- Project management experience preffered
- Excel skills preffered
- Highly organized, manage multi-tasks
- Welding background or knowledge preferred
- QA background a plus
- Planning background a plus
248
Manufacturing Supervisor Bars Area Resume Examples & Samples
- Provide daily "shop floor" leadership with respect to EHS, Quality, Delivery, Cost, Productivity to assigned teams
- Champion an open reporting culture with assigned teams
- Provide leadership in scheduling resources, technical leadership and facilitating the flow of hardware to meet customer requirements
- Perform administrative duties including time & attendance, self-audits, disciplinary procedures etc
- Collaborate with other stakeholders to ensure requirements are met (including quality, cost, scope & cycle)
- Coach and develop employees to support their performance Development
- Support initiatives to achieve goals in asset utilization and process improvement
- Contribute to the provision of new equipment and tooling in his places of responsibility, following the purchase order processing
- Support customer meetings when required
- Assist Cell Leader/SCM with making smart resource-allocation decisions
- Solve problems, set direction, eliminate waste, own visual management
- Motivate team through a reward & recognition program designed to drive engagement & accountability
- Analyze and diagnose P&E issues and support CAPA measures in collaboration with others
- Performs other tasks as directed by his direct superior or superiors that relate to the company's activity
- Work sincerely and effectively with department's colleagues, foremen or supervisors in production workshop
- Collaborate, support and communicate with Product Management, R&D, Purchasing in order to improve existing process
- Engineering or Business Administration bachelors Degree or suitable practical experience
- Inclusive leadership & communication skills
- Demonstrated ability to self-direct within defined responsibilities
- Knowledge of Lean and/or alternative continuous improvement methods
- Must be a team player willing to sacrifice individual goals when needed
- Good knowledge of English language
- Project management experience/qualifications
- Experience dealing with customers and commercial activity
- Experience with forecasting, budgeting and planning
- Foreign language skills: English or French is a a plus
249
Manufacturing Supervisor, rd Shift Resume Examples & Samples
- Facilitate and advise employees within the assigned department to meet value stream goals, departmental goals, and balanced scorecard objectives
- Ensures that Eaton values and philosophies are integrated into the culture
- Provides proactive communication within the designated shift and across other shifts to ensure effective coordination of resources
- Responsible for creating and fostering a high-performance, business-driven team culture and environment
- Establishes trust with employees with un-biased decisions and direct and professional communications
- Bachelor’s Degree from an accredited institution required
- Minimum of 1 (one) year of Supervisory experience
- Demonstrated competency in: leading, motivating, counseling, training, and evaluating employees; production scheduling; problem solving; change management; presentation and facilitation skills
- Prior experience with Continuous Flow operations
- Knowledge of lean manufacturing, industrial safety, SPC, continuous improvement, and quality assurance concepts
- Familiar with Data Analytics for data driven decision making
- Line Leveling/Load Balancing experience
- Strong interpersonal skills; excellent oral and written communication skills
250
Manufacturing Supervisor Resume Examples & Samples
- Managing manufacturing activities during the designated shift by leading and motivating shift employees in all areas including safety, efficiency, loss management, quality, and continuous improvement (TPM)
- Driving UL SHEQ culture by protecting employee’s health and safety, ensuring compliance of all regulatory and plant safety rules, meeting legislative requirements, providing instruction in regard to safety procedures and supporting plant SHEQ initiatives as required (DuPont Program, GMP, Hygiene, 5S,etc..)
- Accountable for the productivity of the site during off-shifts. This requires contacting appropriate resources for issue resolution, providing alternative duties in the event of breakdown or material shortage, monitoring general performance and behavior of employees, and adjusting crewing or call in replacements as necessary. This requires interfacing with Facilities Support, Material Planning, Quality Support, Warehouse and other department supervisors to ensure efficient operation to meet plant goals
- Facilitating required training programs to employees. (SHE, TPM, QA, etc.)
- Utilizing Kronos Timekeeping System to maintain weekly record of hours worked, along with explanation of overtime hours worked and ensures hours worked, vacation, personal hours, absences, etc. are correctly documented so employees are paid accurately
- Regularly cascading/communicating site targets and goals from the Leadership Team to shift crews, consistently and accurately
- Participating in the development of the annual site manufacturing budget and controlling fixed and variable cost expenditures
- Fostering positive employee relations, including properly interpreting and managing the CBA, if applicable
- Promoting and maintaining a safety oriented culture