Director, Manufacturing Resume Samples
4.9
(128 votes) for
Director, Manufacturing Resume Samples
The Guide To Resume Tailoring
Guide the recruiter to the conclusion that you are the best candidate for the director, manufacturing job. It’s actually very simple. Tailor your resume by picking relevant responsibilities from the examples below and then add your accomplishments. This way, you can position yourself in the best way to get hired.
Craft your perfect resume by picking job responsibilities written by professional recruiters
Pick from the thousands of curated job responsibilities used by the leading companies
Tailor your resume & cover letter with wording that best fits for each job you apply
Resume Builder
Create a Resume in Minutes with Professional Resume Templates
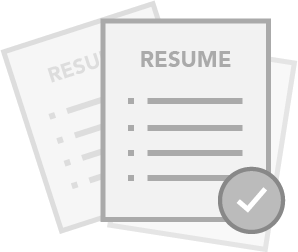
CHOOSE THE BEST TEMPLATE
- Choose from 15 Leading Templates. No need to think about design details.
USE PRE-WRITTEN BULLET POINTS
- Select from thousands of pre-written bullet points.
SAVE YOUR DOCUMENTS IN PDF FILES
- Instantly download in PDF format or share a custom link.
CU
C Ullrich
Chelsie
Ullrich
15513 Hazle Cove
Houston
TX
+1 (555) 414 4222
15513 Hazle Cove
Houston
TX
Phone
p
+1 (555) 414 4222
Experience
Experience
Boston, MA
Director, Manufacturing
Boston, MA
Hane, Pfannerstill and Bashirian
Boston, MA
Director, Manufacturing
- Develop and define critical performance metrics to control processes, measure performance, and guide corrective action
- Direct all personnel activities including staffing, employee relations, goal setting, personal development, performance reviews, discipline and terminations
- Contribute to the evaluation and development of operational strategy and performance goals and objectives in cooperation with executive team
- Manage budgets, schedules and key operating metrics
- Formulate, manage and control production operating budget and ensure that manufacturing costs are within budget
- Develop and deploy the following
- Establish mechanisms to ensure high levels of collaboration across sites and global functions
Boston, MA
Associate Director, Manufacturing
Boston, MA
Marvin, Legros and Abernathy
Boston, MA
Associate Director, Manufacturing
- Managing headcount and expenses in area of responsibility to meet approved spending plan while achieving all departmental commitments and project objectives
- Identifying and communicating risks in area of responsibility and across the site; creating strategies and plans to manage risk to the operations
- Providing technical leadership for aseptic manufacturing
- Manage and deliver assigned financial targets, to include the delivery of capital projects, trial activity and start-up expenses while leading resource & funding prioritization. Drive development of COGS, ensure alignment between category team and operations. Engage and support productivity agenda to deliver cost reduction targets
- Providing effective leadership including: developing and implementing objectives and business strategies; selecting key personnel and motivating members of the functional area; challenging employees to develop as leaders while serving as a role model and mentor; assisting with performance calibration/talent pool management/succession planning; individual goal setting/performance reviews; training and development; supporting workforce diversity, quality and safety and supporting supervisors/managers in the management of their employees/department which support achievement of individual/department/business objectives
- Focusing internally and externally; interacts internally with subordinates, peers, and senior management and interacts externally with regulators, customers, and suppliers
- Interacting closely with BU, relevant sites and functions to define production plans, yearly goals and budgets for reporting functions/operations as well as long range plans (LRP and LRCP)
present
Chicago, IL
Senior Director Manufacturing
Chicago, IL
Trantow-Kertzmann
present
Chicago, IL
Senior Director Manufacturing
present
- Lead multiple production teams in branch offices in managing the production process, quality, production planning and costing
- Set and influence tactical and operational direction for production and related supply chain (T2/T3) area. Own relationship to strategic suppliers of material and equipment
- Give major input to issuing directives in highly automated production and related area
- Manage tactical and operational relationship with the factory production top management across different supplier groups, influence different quality cultures and mindsets through process streamlining using CI techniques and quality tools
- Ensure with support from LO Innovation team, best practices, cohesive messages, projects are shared or implemented consistently across factories in the area of quality, production and MI/ME
- Exposure to leading and managing cross functional team (direct & in-direct) including developing, motivating and coaching team members. Managing team remotely
- Proven track record in innovation project management and implementation
Education
Education
Bachelor’s Degree in Business
Bachelor’s Degree in Business
Auburn University
Bachelor’s Degree in Business
Skills
Skills
- Ability to understand profit and loss calculations and basic business finance
- Strong SAP knowledge
- Ability to apply knowledge of advanced manufacturing and inventory management practices
- Thorough knowledge of Good Manufacturing Practices (GMP)
- Strong skills in developing and delivering effective presentations
- Strong skills in talent management and development
- Thorough knowledge of OSHA, EPA, DOT, FDA, DEA, SAP & ISO rules and regulations
- Ability to communicate effectively orally and in writing, including preparing and presenting information
- Ability to persuade, influence and impact others
- Extensive knowledge of operations management theories, principles, methods and practices
15 Director, Manufacturing resume templates
Read our complete resume writing guides
1
Director Manufacturing Excellence Resume Examples & Samples
- Drive cross functional collaboration with Brand Operations, Design, Marketing, Footwear Suppliers, Machine & Technology vendors to define and execute projects & programs that will lead to increase manufacturing efficiencies. (e.g. Automation, DFM, DFP, SMV)
- Facilitate cross functional events to identify short term, mid term and long term efficiency improvement opportunities
- Establish, refine and support tracking of KPI data for Automation and other efficiency improvement initiatives
- Build platform for knowledge transfer throughout the adidas-Group organization and supplier groups. (BPM, Training Material, News bulletin, etc.; supplier summits, exchange meetings, etc.)
- Communicate progress throughout the adidas-Group organization and assist building a platform for knowledge transfer. (BPM, Training Material, News bulletin, etc.)
- Liaise with Continuous Improvement Team and support driving direction for lean initiatives in footwear sourcing
- Liaise with Manufacturing Excellence Apparel team to identify synergies in Innovation, automation and other efficiency Kaizen for future cost mitigation opportunities
- Work closely together with Brand Operations, Business Solutions Sourcing and GIT to identify opportunities within product creation and sourcing to improve systems and processes. E.g. Supplier Collaboration
- Perform or support FACT criteria evaluations at all suppliers for FACT June and December milestones; collect and document Best Practice Kaizen, communicate throughout footwear division
- Innovative and challenges status quo
- University degree in Business, Industrial Engineering (IE) or a related field. Training/Certification in Lean Manufacturing and 6 Sigma tools
- Management experience in mul tinational companies
- Footwear and/or Apparel business expertise a plus
2
Director Manufacturing Resume Examples & Samples
- Direct all manufacturing operations. Manage utilization of equipment, facilities, and personnel to meet customer requirements and obtain maximum efficiency. Develop and manage Manufacturing budget
- Work with Brand Supply Chain to identify customer requirements and forecasted production. Develop and maintain production schedules. Determine work force, equipment, and space requirements to ensure efficient production and ongoing availability of scheduled product
- Manage monthly production planning and reporting process. Develop and maintain operational reports on performance with focus on achieving all KPI and metrics
- Develop and manage operations required to produce products; develop processes to ensure that cost, efficiency, and quality objectives are met. This applies to current products and to new product releases
- Drive continuous improvement in all aspects of cost performance: line efficiency, labor utilization, scheduling, intermediate inventory levels, line yields, etc
- Work with Product Engineering to improve cost, yield, manufacturability of existing and new products
- Develop and manage operations required for component warehousing, inventory control, material movement, packaging and shipping of product to/from distribution center. Manage component-level inventory to ensure ongoing supply of material to support production requirements
- Monitor production department’s conformance with QA standards and procedures
- Develop and manage strategic plans to ensure global expansion and improved efficiency necessary to support a global supply chain, increasing customer requirements, company cost and overall quality objectives
- Manage facilities and equipment maintenance. Maintain perfect safety record in the factory
- Bachelor’s degree required, engineering degree preferred, advanced degree preferred
- 10+ years related experience within fast-paced, high volume manufacturing (electro-mechanical device industry experience preferred)
- Strong data and analytics capability
- Ability to successfully lead and motivate employees
- Safety and quality focused with a demonstrated
- Excellent written and oral communication skills, with an emphasis on presenting data in a clear and concise manner
3
Director Manufacturing Footwear Resume Examples & Samples
- Set and influence tactical and operational direction for production and related supply chain (T2/T3) area
- Proven management experience including leading, developing and motivating and building effective team within a function/department. Managing team remotely
- Vietnamese local language an advantage
- 10+ years shoes making or quality experience in Footwear industry
- Experience on production and quality or product development/commercialization
4
Sourcing Director, Manufacturing Resume Examples & Samples
- Creating, influencing and implementing the Group's global sourcing strategies associated with their Manufacturing Indirect categories
- Maintain relationships with senior executive level internal stakeholders, as well as external supplier relationships with key suppliers
- Leading a team which will comprise of other Directors and Associate Directors of Sourcing
- International travel, at least one week in four
- Bachelor´s Degree in a related field, MBA an advantage
- Certified Purchasing Manager (CPM) or equivalent credentials is desirable
- Experience in the procurement of capital equipment or manufacturing products and services in Pharmaceutical or Biotechnology industry is essential
- 2 - 5 years of senior leadership experience from the Pharmaceutical industry is preferred
- Knowledge of ePurchasing tools (e.g. Ariba, SAP, JDE etc)
- Influencing skills, stakeholder management skills and executive maturity
- Must be highly strategic but with the ability to understand how procurement operations work within the pharmaceutical industry
- Able to resolve problem, transition and transform sourcing activities
- Ability to work well with ambiguity in a fast paced environment where transformation is constant
5
Director, Manufacturing FW Resume Examples & Samples
- Lead multiple production teams of the designated groups of factories/Operations Centers in managing the production process, quality, production planning, Manufacturing Excellence, SEA and adidas Group standards implementation
- Make day to day and long term impactful decisions within the defined production, quality, availability and ME / SEA scope
- Manage tactical and operational relationship with the factory production top management across different supplier groups, influence different quality cultures and mindsets through process streamlining using CI techniques and quality tools
- With support from SOM, ensure best practices, cohesive messages, projects are shared or implemented consistently across factories in the area of quality, production and ME
- Proven management experience incl leading, developing and motivating and building effective team within a function/department. Managing team remotely
- Have proven depth and breadth of experience in production and quality area which can be called up on to co-lead or support regional or global projects related to his/her area of expertise
- 4-5 years combined experience in at least 2 functions/area: production, development/commercialization or general Operation Center Management
6
Associate Director Manufacturing Sciences & Technology Upstream Lead Resume Examples & Samples
- Provide significant support to CMC strategy development and provide efficient and effective technical support for internal and/or external manufacturing to enable robust supply of commercial products
- Leading continuous process improvements, aimed at improving process robustness, capacity, and productivity, as per Shire’s QbD paradigm
- Work with cross functional partners to lead and/or support the evaluation and development of manufacturing technologies and implementation strategies. Data-driven decision analysis will be part of this person’s role including but not limited to evaluation of internal vs external mfg., facility fit, cost of goods, conventional vs. single use technology
- Leading and mentoring junior staff as an in-line and matrix group leader
- Have excellent knowledge and experience with commercial process development for upstream processes including cell culture, perfusion, protein capture and recovery, etc. such that the candidate has an in-depth understanding of unit operations, critical aspects as it relates to scale up and process robustness, and the associated manufacturing systems (equipment, automation, instrumentation etc.) requirements
- Have experience in design-of-experiment (DoE) and the ability to analyze and interpret and present data
- Candidate should have experience in healthcare/biotech/pharmaceutical industry with a demonstrated understanding of the interdependencies of research, technical development, cGMP Manufacturing, Quality, Supply Chain, Preclinical, Clinical, Regulatory and Product Strategy functions. Demonstrated leadership and capability for strategic analysis and issue resolution, organizational and project management skills working in a matrix environment is also required
- Should possess strong problem solving and risk based decision making skills and a strong ability to influence or manage without direct authority. Highly developed interpersonal skills will be a substantial component of being successful in this demanding role
7
Associate Director, Manufacturing Resume Examples & Samples
- Lead commercialization effort for large scale projects, platform innovation programs or significant capital related initiatives. Ensure effective team engagement which may include establishing and managing team meetings. Review project timelines and cost regularly with the project team, facilitate creation of mitigation/contingency plans and manage communication
- Lead technical and supply chain readiness to support commercialization activity. The individuals will lead using tools that prepare the supply chain and manufacturing facilities for successful start- ups for both growth and cost out initiatives (including manufacturing asset optimization)
- Lead Value Stream network assessment and E2E loss analysis with business partners. Ensure appropriate capacity for new business initiatives and growth plans across product life cycle. Develop and recommend alternatives as needed. Provide updates to leadership, project sponsors and stakeholders as needed on key initiatives, including progress against deliverables, cost management, next steps and needs from sponsors to alleviate hurdles. Escalate concerns and issues, report project fact base, define options/trade-offs, and provide team recommendation
- Lead internal feasibility assessment and business case to support business team’s commercialization plans; define network capability (capacity/technology) and capital associated with developing such capability. Identify impact across the supply chain with regard to cost of goods sold e.g. route to market, capacity utilization, DIOH, manufacturing efficiency, quality, safety. Lead AR development
- Partner with External Manufacturing managers and EM procurement to deliver against commercialization activities outside of current Kraft Heinz capabilities as well as drive cost out of the external manufacturing networks
- Manage and deliver assigned financial targets, to include the delivery of capital projects, trial activity and start-up expenses while leading resource & funding prioritization. Drive development of COGS, ensure alignment between category team and operations. Engage and support productivity agenda to deliver cost reduction targets
- Provide indirect leadership for the PCM organization and Plant BD’s
- Support Business and Manufacturing Systems initiatives as required, and support the continuous improvement of the commercialization process through collaboration with key stakeholders and best practice sharing
- Lead and/or participation in various stakeholder governance forums (i.e. Stage gate/Leadership teams)
8
Director, Manufacturing Resume Examples & Samples
- Establish and improve mechanisms to ensure the manufacturing organization provides the required products in a timely, cost effective and quality manner to the Bioproduction and Biosciences Divisions
- Assess resource needs across the manufacturing organization by working with site and functional leaders to assign resources per established priorities
- Provide thought leadership to leaders to achieve goals and create a culture of accountability and continuous improvement
- Drive performance of the manufacturing organization to achieve and exceed financial targets through quality, cost efficiency and productivity
- Establish mechanisms to ensure high levels of collaboration across sites and global functions
- Develop a succession strategy and improve bench strength by facilitating and mentoring manufacturing organization leaders to be both exceptional players and coaches
- Coordinate the hiring, training, coaching and annual performance reviews of manufacturing leaders. Define and establish clear objectives and expectations, routinely provide direct feedback for performance management and development
- Identify projects and recommend appropriate course of action (e.g., discontinuation, outsource, process improvement) to maximize profitability and supply
- Execute robust Risk Management practices to maintain high probability of project success, i.e., satisfaction of scope, schedule and budget
- Ensure effective transfers of new products into production that meet all requirements for the classification
9
Senior Director Manufacturing Sci-analytical Transfer Resume Examples & Samples
- Directs the design and scale-up of products, processes, instruments and equipment from the laboratory through pilot plant and manufacturing scale to meet clinical and commercial requirements for clinical next generation sequencing products. Acts as liaison with research, development and/or Contract Manufacturing Organizations to ensure processes and designs are compatible
- Develops and delivers the annual operational plan for Mfg Sciences. Includes working with R&D to develop strategies and for the introduction of additional capabilities for development/ production of products, ensuring validation of new processes, parts and methodologies
- Develops and executes world-class standards for the flawless transfer of products and processes from R&D into Mfg and Operations, including capabilities for facilities, systems, people and equipment (interdependency with Operations Transformation organization)
- Lead all elements of CSD’s process development, technology transfer, product manufacturing
- Lead CSD’sefforts with external vendors for the planning, execution and evaluation of all product manufacturing activities and plans according to current domestic and international standards, e.g. GMP, ICH, FDA etc
- Direct the relationship with Contract Research (CROs) and Contract Manufacturing Organizations (CMOs)
- Ensure that CSD and its vendors have plans in place to support replacement of existing programs, vendors and all other resources in the event of failure(s) in any of the Technical Operations operating systems
- Directs and gives oversight to significant intra- and inter-site sustaining projects, deploying resources short- and long-term as applicable (interdependency with major site leads)
- Development, deployment, compliance and refinement of manufacturing policies. Monitor and analyze utility and applicability of manufacturing technologies (existing and emerging) to Manufacturing and Operations. Analysis and reporting of competitor activities in relation to manufacturing and operations
- Participates in personal development programs to further enhance skills and knowledge relevant to the position. Additionally, promotes and implements staff training, motivation and personal development
- First and/or Second Degree level in an appropriate science discipline and/or relevant industrial experience. Excellent R&D, commercial and financial awareness and a thorough understanding of Company operations. Excellent leadership and people-development skills. Experience of operations in a foreign country preferable. Practical knowledge of Lean Enterprise, 6-Sigma and Project Portfolio Management, and their implementation desirable
- Minimum of 10 years senior management experience, Director level and above preferable, in a high technology Operations role, which would preferably include experience in chemical manufacturing and/or molecular biology manufacturing. Ability to lead and develop a group of broadly based technical staff up to PhD level
- Minimum Qualifications (must have)
10
Director, Manufacturing Resume Examples & Samples
- Responsible for the outgoing quality, safety and efficacy of all finished product and ensure compliance with all applicable specifications, Standard Operating Procedures, FDA regulations (GMP’s)
- Develop and deploy the following
- Bachelors Degree required (Science or Engineering major preferred)
- Minimum 10 years experience in all aspects of the aseptic manufacturing process
- Minimum 5 years in a leadership role
- Lean Manufacturing experience required (i.e. value stream mapping, 6S, leading kaizen events to drive positive change on the floor, problem-solving methodology and teaching people to think)
11
Director, Manufacturing Excellence Resume Examples & Samples
- Co-Leadership within the Manufacturing Excellence program and projects
- Work with our supply partners to identify opportunities for waste reduction
- Work with our internal UA teams to identify waste in our processes and present solutions that are connected across of impacted functions
- Enable Lean solutions that affect – Lead Times, Quality, Output and Cost
- Create learning programs for both UA team members and supply partners
- Enable common metrics for supply partners
- Co-Develop and support the UA ME metrics
- Develop Current and Target Condition mapping that aligns to the business strategy for UA
- Assess new vendor opportunities based on Lean capabilities and opportunities
- Conduct quarterly reviews of projects both internal to UA and supply partners
- Enable continuous improvement programs that result in supply sharing programs of cost and manufacturing gains
- Promote the UA culture and ethical business practices
- This role will involve travel to the regions UA manufactures products
- The expectations for this role are to lead / drive improvements in direct relationship to the key metrics established and aligned with individual goals of this role
- Goals for the role and region are aligned to the Supply Chain deliverables
- 10 years related industry experience preferred
- Knowledge of TPS
- Position may be based in Baltimore or Panama
12
Executive Director Manufacturing Resume Examples & Samples
- Support the product requirements of all marketing and sales divisions to ensure that products are produced according to plan and do not go into backorder
- Maintain appropriate inventory levels
- Develop and obtain support for the strategic plan for departments under position’s control
- Manage production expenses and maintain or reduce COGS
- Responsible for maintaining quality standards to meet GMP requirements
- Participate in all FDA Audits of the manufacturing facilities and processes
- Work as a business partner with the Executive Director, Quality
- Ensure that the facilities meet the necessary strategic requirements
- Implement new manufacturing technology
- Ensure the safety of all employees
- Adheres to all applicable procedures, cGMP’s, company policies, and all other quality or regulatory requirements (OSHA, DEA, FDA, EMEA, ANVISA, HS&E, etc.). Ensures all work is performed in a safe, effective manner, and in compliance with the appropriate industry and regulatory (FDA, DEA, OSHA) standards, and Departmental, Plant, and Corporate quality and Behavioral Based Safety (BBS) goals
13
Director Manufacturing Resume Examples & Samples
- Working with the Performance Excellence team, implement continuous improvement for increased productivity and cost reduction initiatives to minimize plant and labor expenditures
- Lead small internal teams to ensure timely, impact driven execution of strategic manufacturing programs
- Lead innovation and evaluation of alternative strategies for meeting capacity, distribution and customer requirements including in-network alternatives, as well as both domestic and international manufacturing locations
- Connect and build relationships to analyze status quo, identify opportunities and risk, and liaise with business to drive improved outcome
- Drive and align necessary change management and learning support solutions across an organization through a broad understanding of innovation, people and business strategies
- Work closely with corporate and site leadership team members to ensure successful implementation of Site Master Plan (SMP) projects
- Champion change management efforts for system improvements, to reduce errors, minimize cost and maximize efficiency
- When assigned, lead integration activities in acquisitions
- Participate in employee development, through coaching, mentoring, and professional development
- Partner with quality leadership to ensure good quality and cGMP practices, etc., and their implementation across the Plant
- Drive initiatives to support Performance Excellence philosophy and practices throughout the Plant
- Regularly update knowledge of pharmaceutical industry practices and changes
- Act as a visible champion of improvement work, including participation in key meetings and site visits, as necessary
- Partner with plant leaders and collaborate to find the best possible solution and best practices
14
Associate Director Manufacturing Resume Examples & Samples
- Bachelor’s degree and 10-12 years in biopharmaceuticals or highly regulated industry OR Master’s degree and 8-10 years of experience in biopharmaceuticals or highly regulated industry
- 5 years in management/leadership positions
- Bachelor’s Degree in a science or technical field and/or Advanced Degree
- Experience leading cGMP manufacturing/operations teams
- Expertise in GMP facilities and equipment design/engineering concepts
- Experience leading cross-functional operations teams including Quality, Manufacturing Technical Support, Facilities and Engineering, and/or Validation
- Exceptional communication and negotiating skills; strong presentation and facilitation skills
- Ability to gown and navigate GMP manufacturing areas
15
Director Manufacturing Resume Examples & Samples
- Bachelor's degree or higher in Chemical or Mechanical Engineering, Biotechnology, Biology or related scientific or technical disciplines from an accredited technical university
- 10+ years of relevant work experience managing manufacturing operations in a vaccine, biologicals, or parenterals pharmaceutical manufacturing environment
- Working knowledge of current federal, local, and international regulations regarding the production of drug substances and drug products
- Good understanding of cGMPs, industry and regulatory standards and guidelines
- Good understanding of federal and local regulations regarding occupational safety and health within a manufacturing environment
- Excellent interpersonal skills and leadership potential
- Strong ethical foundation and a sound compliance understanding
- Experience directing teams
16
Associate Director, Manufacturing Resume Examples & Samples
- Ensuring the safety of work practices in accordance with the Sanofi Safety Programs
- Ensuring that all activities are in compliance with cGMPs
- Ensuring that staff are sufficiently trained to perform their job responsibilities
- Providing technical leadership for aseptic manufacturing
- Developing strategies that ensure achievement of objectives that are consistent with the site’s strategic direction
- Managing employees, either directly or indirectly, who are involved in the scheduling, implementation, execution and/or maintenance of manufacturing processes and operations
- Undertaking long and short-term planning and supervision of projects that require interaction with Manufacturing
- Overseeing, either directly or indirectly, Manufacturing investigations, process variances and deviations
- Participating in the development, revision and accuracy of production plans
- Responsible for the Manufacturing annual budget and quarterly forecasting processes including work order variances and maintaining bill of materials and routings
- Focusing internally and externally; interacts internally with subordinates, peers, and senior management and interacts externally with regulators, customers, and suppliers
- Maintaining an external network of expertise and represents the division and company in professional organizations
- Providing effective leadership including: developing and implementing objectives and business strategies; selecting key personnel and motivating members of the functional area; challenging employees to develop as leaders while serving as a role model and mentor; assisting with performance calibration/talent pool management/succession planning; individual goal setting/performance reviews; training and development; supporting workforce diversity, quality and safety and supporting supervisors/managers in the management of their employees/department which support achievement of individual/department/business objectives
- Ensuring compliance with all legal and business requirements and Sanofi policies and practices
- Establishing departmental and individual goals and objectives in alignment with site goals and priorities. Identifying performance improvement targets and metrics. Ensuring capabilities and capacity in place to effectively deliver on all departmental commitments and performance targets
- Strengthening overall leadership and organizational capabilities in area of responsibility. Building and sustaining high performance management team and ensuring strong alignment and coordination with other functional groups at the site
- Identifying the required resources and expertise, implementing the appropriate team/departmental structures and establishing the required processes and communications to enable department(s) to effectively deliver on all commitments while building a culture of Safety and Quality and continuous improvement
- Identifying and communicating risks in area of responsibility and across the site; creating strategies and plans to manage risk to the operations
- Participating in development of site long range in line with the corporate Long Range Planning
- Ensuring effective utilization of resources by ensuring robust employee development, performance management, succession planning, and rewards and recognitions practices in area of responsibility
- Managing headcount and expenses in area of responsibility to meet approved spending plan while achieving all departmental commitments and project objectives
- Motivating, retaining and developing key employees. Building and sustaining employee engagement by creating an environment within which individuals and teams can excel
- Interacting closely with BU, relevant sites and functions to define production plans, yearly goals and budgets for reporting functions/operations as well as long range plans (LRP and LRCP)
- Bachelor's Degree in a science or technical field and10 years of experience in biotech/pharmaceutical manufacturing or a related industry with 5 years in a manufacturing management position or an equivalent combination of education and experience
- Extensive experience in Aseptic Manufacturing
- Experienced leading manufacturing teams to maintain adherence to a demanding commercial production schedule
- Experienced working with cross-functional teams, including Quality, Manufacturing Technical Support, Facilities and Engineering and Validation
- Experienced with Deviation, CAPA, Change Control Systems (i.e. Trackwise)
- Experienced in troubleshooting, investigation, root cause and risk analysis in a cGMP environment
- Experience leading the implementation of improvements to technical and business processes
- Expertise and knowledge in GMP engineering facilities and equipment design concepts in order to review engineering projects for compliance impact
- Knowledgeable of requirements for post approval changes and of information typically found in the CMC sections of regulatory submissions
- Skilled in achieving results and managing others to achieve corporate, site, and departmental objectives. Excellent collaborator
- Excellent communication skills, good presentation and influencing skills and the ability to interact and gain the support of senior management
- Process Development and/or Manufacturing Technical Support experience
- Experience with budgeting and long range planning
- Good knowledge of supply chain theory and practice
- Experience with SAP/Athena MRPII systems
17
Associate Director Manufacturing Resume Examples & Samples
- 10 years of experience in pharmaceuticals or a related industry with 5 years in management position or an equivalent combination of education and experience
- 5 years in management / leadership positions
- Bachelor’s Degree in a science or technical field and/or advanced degree
- Experienced leading cGMP manufacturing / operations teams
- Expertise in GMP facilities and equipment design / engineering concepts
- Experience leading cross-functional operations teams including Quality, Manufacturing Tech Support, Facilities and Engineering and / Validation
18
Senior Director, Manufacturing Resume Examples & Samples
- Manage manufacturing group leaders and hourly staff in proper operating techniques and procedures
- Supervise, coordinate and control production and operating activities to ensure optimum utilization of personnel, materials, and equipment
- Allocate resources to production areas based on schedule needs
- Recommend and implement value and process improvement programs
- Maintain a positive, can do attitude and engage reports and peers in an empowering and motivating manner to drive performance
- Provide positive feedback or course correcting behaviors to direct reports on a routine basis
- Remain flexible, energetic and enthusiastic to drive change and support growth
- Model a culture of safety and strive for 100% compliance with safety and training initiatives
- Partner with department planners and/or site leadership to establish short term schedules to meet monthly demand
- Monitor line performance against target standards and quality through put and make adjustments as necessary
- Perform routine inspections of production areas, paperwork and product quality to assure correct and timely completion of activities to maximize line availability
- Take necessary action to eliminate delays ensuring adherence to production and shipping schedules
- Work in a team environment with other department management to coordinate a production schedule to achieve required deadlines, objectives and budgets
- Maintain compliance with company policies, cGMPs, safety standards, and good housekeeping practices
- Bachelor’s degree required: Engineering, Chemistry, or Biology Degree preferred
- Minimum of ten (10) years supervisory experience, in the pharmaceutical or medical device industry. Knowledge of sterilization and aseptic processes preferred
- Ability to work in a cross-functional organization to manage the day-to-day business and deliver continuous improvement initiatives
- Proven communication and employee relations skills necessary
- Proven ability to communicate clearly and present key information objectively and collaborate effectively with management
19
Director Manufacturing Resume Examples & Samples
- Manage relationship with the factory team leaders to continually upgrade sports category competence, development innovation capability, technical expertise and communication skills of factory personnel
- Improve production processes constantly by integrating and enhancing automation of process steps. Be first point of contact for innovation teams in business and IT on implementing new technologies into production, make joint decisions with the Senior Director LO Innovation on when to activate new technologies based on status of agreed deliverables and provide input on newly implemented and running automated production process to innovation teams
- Give input to issuing directives in development, commercialization, SEA and related area
- Experience in footwear manufacturing and creation areas such as pattern engineering, mold making, grading, materials processing
- Good understanding of costing principles and process; ability to decipher cost breakdown related to products
- Proficiency with standard software applications (Word, Excel, Access, PowerPoint, MS Project)
- MES / ERP proficiency is an advantage
20
Senior Director Manufacturing Resume Examples & Samples
- Lead multiple production teams in branch offices in managing the production process, quality, production planning and costing
- Lead implementation of Manufacturing Innovation / Future developments, SEA and adidas Group standards. Define deliverables for new technologies before implementation into production and decide with input from Director Manufacturing on when to implement new technologies into production
- Make day to day and long term impactful decisions within the defined production, quality, availability and Innovation / SEA scope
- Set and influence tactical and operational direction for production and related supply chain (T2/T3) area. Own relationship to strategic suppliers of material and equipment
- Give major input to issuing directives in highly automated production and related area
- Work directly with the Factory GM in term of factory production personnel skills evaluation and through LO Innovation team provide facts/business cases to get the Factory GM/Owner to invest into various productions manufacturing machineries
- Ensure with support from LO Innovation team, best practices, cohesive messages, projects are shared or implemented consistently across factories in the area of quality, production and MI/ME
- University degree preferably on business, production management or similar and at least 10 years of experience in relevant area and footwear industry
- Exposure to leading and managing cross functional team (direct & in-direct) including developing, motivating and coaching team members. Managing team remotely
- Proven track record in innovation project management and implementation
- Ability to cope with constant change
- Experience in production process automation and digital production management
- Experience in footwear manufacturing and quality or creation areas
- Experience in coaching and mentoring people and succession management
- Strong interpersonal skills, including directing and motivating others without direct management responsibility
- Excellent written and verbal English communication skills
- German language knowledge an advantage
21
Director, Manufacturing Resume Examples & Samples
- 2) Ensures budgets, schedules, and performance requirements are met. Erroneous decisions will result in critical delay(s) in schedules and/or unit operations and may jeopardize overall business activities
- 3) Improve product quality and cost and reduce customer complaints through a proactive program that includes interaction with internal and external suppliers. Utilize collected data from customers to enhance perceived product quality
- 4) Adheres to all environmental, health and safety SOP's, equipment, policies and procedures, including any department specific requirements
- 5) Propose and devise strategies from the data gathered to support the Manufacturing Operating System
- 6) Responsible for resolving complex problems where analysis of situations or data requires an in-depth evaluation of multiple factors
- 7) Must execute judgment within broadly defined practices and policies in selecting methods, techniques and evaluation criteria for obtaining results
- 8) Regularly interacts with senior management or executive levels on matters concerning several functional areas, division, and/or customers
- 8 to 10 years of manufacturing experience required
22
Director Manufacturing Speed Factory Resume Examples & Samples
- Lead commercialization and manufacturing for all production across categories ensuring that products consistently exceed customer expectations in respect to fit, comfort, design integrity, performance, perceived value, manufacturability and quality
- Oversee the direct development process between Headquarter/Creation Center Project Management and Tier 1 factory. Manages the development of cohesive and customer focused cross functional teams (development, Tooling, Materials, and Costing) ensuring that product integrity and Create to Value in an automated environment is the paramount priority and focus
- Exhibit “product eyes” and sports competence-have a feel for styling, product cosmetics, product construction and manufacturing technologies in order to influence and drive the overall product direction of the specific category(s) he/she manages
- Make decisions within the defined development and commercialization scope for the categor(ies) being assigned
- Ensure compliance of suppliers with SEA standards and link to the respective HQ and regional SEA teams
- University degree preferably on shoe making, production management or business engineering and at least 7-10 years of experience in relevant area
- Have knowledge and expertise and can support/lead LO based projects within defined scope of production
- Innovation mindset enabling implementation of new production process and provide feedback to innovation teams on production specific needs
- Strong written and verbal English communication skills
- Passion and interest in athletic competition, sports or fitness related activities
23
Senior Director, Manufacturing Development Resume Examples & Samples
- Lead and direct a group of scientists and engineers responsible for Cerus medical devices (drug – device –biologics combination products), including new products and product life-cycle management projects and activities
- Managerial and technical functional areas of responsibility include: Chemistry, Manufacturing, and Controls (CMC) and single-use plastic medical devices
- Build relationships with existing external consultants and contract manufacturers. Lead negotiations and qualification of new suppliers
- Regular interactions with peers in Project Management, Product Management, Development, Regulatory, Quality, and Operations. Work with project managers to identify issues/risks and ensure appropriate actions are taken to accomplish specific goals, milestones, and budget(s)
- Participate in the authoring and review of regulatory submissions as required
- Assume overall responsibility and accountability for performance against department, project and corporate objectives. Motivates employees to fulfill their commitments
- Responsible for establishing and adhering to budgets and reporting requirements for Cerus projects and external contracts
- Responsible for building infrastructure required to support a growing commercial organization with a portfolio of commercial and pipeline portfolio products. Manage and participate in human resources, and other organizational development and infrastructure activities
- Ensure quality system compliance as it relates to areas of responsibility. Examples include design control/change control, design transfer to manufacturing, ISO/EP/USP standards, cGMP, and other relevant requirements
- B.S. degree (Master or Ph.D. preferred) in chemistry or chemical engineering with a minimum of 12 years related experience
- A minimum of 6-8 years of management experience
- Experience with medical device and drug development process; GLP and GMP; FDA, European, ISO, and ICH requirements; and regulatory submissions
- Demonstrated experience in developing and sustaining successful working relationships with contract manufacturers, contract laboratories, and partner organizations
- Flexible; ability to adapt to changing priorities
- Demonstrated ability to provide vision and accomplish goals while managing the scope, time and resource needs of multiple projects and programs
- Strong leadership, interpersonal, and influencing skills in cross-functional team environment
- Requires U.S. and International travel (up to 25%)
24
Director, Manufacturing Resume Examples & Samples
- Extensive knowledge of operations management theories, principles, methods and practices
- Thorough knowledge of OSHA, EPA, DOT, FDA, DEA, SAP & ISO rules and regulations
- Thorough knowledge of Good Manufacturing Practices (GMP)
- Strong SAP knowledge
- Strong skills in talent management and development
- Strong skills in developing and delivering effective presentations
- Advanced skills in financial and analytical management
- Advanced interpersonal skills in dealing with senior company executives
- Ability to apply knowledge of advanced manufacturing and inventory management practices
- Ability to direct, plan, organize, assign, review and evaluate the work of subordinates
- Ability to make effective and efficient use of financial resources to achieve objectives
- Ability to understand profit and loss calculations and basic business finance
- Ability to persuade, influence and impact others
25
Senior Director Manufacturing Resume Examples & Samples
- Actively managing day to day operations to support manufacturing projects and warranty services within SYNNEX
- Guide the internal development/implementation of new projects and services within the manufacturing operations group
- Provide support across multiple internal department groups (procurement, engineering, program management, manufacturing, warehouse and quality)
- Ensure visibility and structure to manufacturing services
- Review existing system tools and working with internal teams to develop enhancements
- Analyze costs and pricing methodology to ensure profitability of the various service programs
- Work, coordinate and drive actions across multiple organizations within SYNNEX related to the support of Manufacturing Operations, Engineering and Value Added Business Groups
- Develop systematic methods and procedures to be made uniform across all SYNNEX Manufacturing locations
- Participate with senior managers, directors and executives to establish strategic plans and objectives for Manufacturing Operations
- Regularly interact with executives and major customers (interactions frequently involve special skills, such as negotiating with customers or management or attempting to influence senior level leaders regarding matters of significance to the organization)
- Devise high level, cost efficient organizational action plans for meeting business targets and objectives
- Provide input on planning, staffing, budgeting, managing expense priorities and recommending and implementing changes to methods within Manufacturing Operations
- Work with operational managers to ensure the prioritization of production schedules based on product introduction, equipment efficiency and materials supply
- Assist and drive the planning of various procedures and budgets related to manufacturing operations
- Make budgetary recommendations regarding and, at higher levels, controls capital expenditures and direct/indirect labor
- Participate in internal audits to assigned operations and/or related departments in compliance quality management system
- Coordinate with appropriate departments the Corrective Action taken on External Audit Nonconformity Reports, ensure timely submission to the Registrar and oversee the overall quality of Manufacturing Operation
- Respond to non-conformities and other issues raised by internal/external customers, the internal audit team or external auditors
- Support operations in defining, documenting and implementing processes to ensure compliance with the SYNNEX Operational Standard
- Perform capacity planning with set priorities
- Assist in the management of manufacturing, warehouse and customer service readiness to support all services
- Provide the applicable operation teams with details on new project planning, budgeting and recommend/implement changes to methods for supporting service
- Participate in Internal Audits to assigned operations and/or related departments in compliance with the requirements of ISO 9002:1994 and 9001:2000 (QMS) Quality Management System
- Commitment to continuous improvement to comply with ISO 9001:2000 and any other regulatory standards
- Travel as needed, < 25%
26
Director, Manufacturing Quality Resume Examples & Samples
- Standardize Manufacturing Quality System and processes across the plant network
- Establish Manufacturing Quality fundamentals and strengthen organizational capabilities
- Align metrics across plant network and lead quarterly Manufacturing Quality Management Review (QMR) process
- Support corrective action/preventative action initiatives and short term containment of issues at and across plants
- Point person for major rework issues. Works cross functionally to address field issues
- Develop and ensure PFMEA and control plans are in place across plant network in accordance to plans and priorities
- Benchmark similar industries and implement best practices
- Drive standardization – CAPA, control plans, and PFMEA, QMR, part traceability, routings, etc
- Create a culture of Safety and Quality first
- Represent Manufacturing on the Polaris Product Development Safety Board
- BS degree in Engineering or Business required
- MS or MBA highly preferred. Minimum 15+ years Manufacturing and Quality management experienced required. Engineering experience a plus
- Experience operating in a robust quality management system and Lean environment
- Strong leadership competencies required
- M&A integration experience preferred
- Experience managing global teams. Periodic international travel required
27
Operational Excellence Director Manufacturing Excellence Resume Examples & Samples
- Define, develop and deploy the Delphi Operational Excellence transformation Model which is aimed at supporting corporate and divisional strategic improvement goals (declarations)
- Support leadership in developing improved performance management through problem solving and the Monitoring & Continuous Improvement (MCI) of Safety, People, Quality, Volume & Cost (SPQVC) Metrics and management routines in each location
- Improve the Enterprise Operating System processes by the implementation of Delphi Lean Principles, methodologies, tools & practices through:-
- 10+ years' experience within related field
- Bachelors' Degree Business or Engineering
- 10+ years' experience
- Worked as a Senior Lean Leader within major automotive or Aerospace Tier I, or Corporate Level manufacturing environment
- Must have worked extensively at a Global or as a minimum a regional level across a large organisation and in different cultures
- Proven experience developing people and delivering improvements within manufacturing organisation
- Proven experience developing people and delivering improvements using value stream deployment
- Significant Lean training and implementation experience in manufacturing evidenced by results and culture change
- Expert knowledge & practice of Lean Systems and how / when to implement tools & techniques such as:-
- Practical problem Solving / Value Steam Mapping/ Lean Management Systems /Material Handling/ Visual Flow/ Kanban Mixed Model Production /PDCA / FIFO Flow / Shared Resources / 8 lean Guidelines /Visual Management / Standard Work/ LTA / 5S / Autonomous Maintenance / Change Over / TPM /JIT/ Kamishibai / Tachinbo / A3 Management etc
- Facilitate Leading senior project teams in “eVSM” review and design
- Proven application of Core Soft Skills for Coaching , Constructive Feedback & Recognition
- Able to lead members Senior management to team members in Lean Improvement activities, training & concepts
- Experienced in developing effective change communications both internal and external to Delphi
- Externally network to support the enhancement of knowledge within Delphi
- Able to work exceptionally well in team environments and be adept at motivating co-workers
- Strong Project Management Skills
- Able to make proficient use of corporate desktop environment such as Microsoft Office suite or equivalent
28
Account Director Manufacturing Resume Examples & Samples
- 3 – 5 years’ experience services selling to high revenue clientele in the Translation / Localisation industry and/or in the Software Industry
- Proven track record of meeting personal sales targets
- Proven ability to secure on site presentation opportunities with high level (C level) clients
- Ability to define problems, collect data, establish facts, and draw valid conclusions in order to present and sell SDL Global Solutions
- Ability to command respect from clients
- Solid proficiency in Word, PowerPoint, Excel, Outlook
- Experience working with Salesforce.com and manage personal pipeline and opportunities
29
Director, Manufacturing Resume Examples & Samples
- Responsible for the outgoing quality, safety and efficacy of all finished product, compliance with all applicable specifications, Standard Operating Procedures, FDA regulations (GMP’s) and New Drug Applications
- Ensures budgets, schedules, capacity, and performance requirements are met
- Improve product quality and cost and reduce customer complaints through a proactive program that includes interaction with internal and external suppliers. Utilize collected data from customers to enhance perceived product quality
- Ensure reliable operations through life cycle management of equipment, facilities, and processes
- Adheres to all environmental, health and safety SOP’s, equipment, policies and procedures, including any department specific requirements
- Propose and devise strategies for improvements through coordination with global process alignment teams and from the data gathered in manufacturing operations
- Responsible for resolving complex problems where analysis of situations or data requires an in-depth evaluation of multiple factors
- Must execute judgment within broadly defined practices and policies in selecting methods, techniques and evaluation criteria for obtaining results
- Quest for Innovation. Must be able to operate with agility and a learning mindset so that we can accelerate breakthrough innovations
- Engaged with the World Around Us. Must be able to embrace change and seek diverse perspectives and partnerships to benefit patients and make a positive impact on the world
30
Director, Manufacturing Sciences Resume Examples & Samples
- Leads the technical transfer activities into Manufacturing for both internal and external processes
- Hires, trains, motivates, leads, develops and evaluates staff. Takes corrective action as necessary on a timely basis and in accordance with company policy. Ensures compliance with current federal, state and local regulations. Consults with Human Resources Department as appropriate
- Informs personnel of communications, decisions, policies and all matters that affect their performance, attitudes and results
- Supports the validation of processes and preparation for commercialization
- Manage steam responsible for facility fit activities; including process flow diagram generation, scale-up calculations, defining equipment and solution requirements, generation bill of materials (BOM) and new specifications while insuring safety and quality standards are maintained
- Works closely with manufacturing to provide on-the-floor technical oversight before and during GMP runs
- Prepares and reviews technical documents including batch records, formulation/solution/media records, item specifications, project reports, and engineering specifications
- Leads the compilation of process data, including communicating project status, and delivering internal / client presentations
- Acts as the lead for technical support deviations, change controls, and CAPAs including determination of event impact, root-cause analysis and corrective action identification
- Evaluates existing processes and identifying process and/or equipment improvements to improve efficiency, consistency and competitiveness. This includes development of project requirements, scope of work, technical design, and cost justification for management evaluation
- Oversees the alignment and direct technical transfer across departments (PD, manufacturing, Quality) in an effort to launch and support new products
- Experience with Upstream and/or Downstream processes at the small to intermediate scale of cGMP biologics production
- Prior experience in process scaling and technology transfer
- Experience in report and documentation skills
- Experience in investigating and closing out deviations, OOS and CAPAs
- Experience writing and revising standard operating procedures and batch production records
- Experience with operating and troubleshooting process equipment
- Experience working on late phase and commercial programs is a plus
31
Director, Manufacturing Resume Examples & Samples
- Directly impacts the direction of the business, i.e. product design and development, process development and manufacturing of the product, materials and product cost, capital expenditures and long-range planning
- Assures the existence of a positive employee relations’ environment within the Business Units
- Continuously seeks process improvements, meets or exceeds cost reduction goals and develops programs for implementation
- Responsible for establishing the manufacturing quality standards
- Leads achievement of objectives of quality, timely delivery, planned cost and profit and personnel relationships and development
- Ensure compliance with Company and Regulatory Agency policies and regulations
- Plans capital for the Business Unit
- Anticipates and reacts to equipment and materials problems impacting production goals
- Reviews and approves major personnel changes for the Operations Unit
- Responsible for the direct supervision and guidance of the Business Unit Managers and clerical staff
- Maintain all manufacturing facilities to ensure regulatory compliance
- Assure compliance of manufacturing through analyzing industry and governmental trends. Implement proactive measures to prevent any disruption of manufacturing due to non-compliance
- Utilizes Six-sigma/Lean Manufacturing to continually improve quality and customer service
- Bachelor’s Degree is required: Pharmacy, Chemisty, Engineering; MBA is preferred
- Previous experience as Supervisor, Production Manager, Engineering Manager, preferably in Pharmaceuticals
- Minimum 5 years Pharmaceutical management experience
- Minimum 2 years as an Engineering Manager / Supervisor, in a Pharmaceutical or related field
- Minimum 3 years Production Supervisor, in a Pharmaceutical or related field
- Minimum 10 years Manufacturing Experience – related field
32
Director Manufacturing Resume Examples & Samples
- Champion a disciplined manufacturing culture that promotes patient focused quality, customer satisfaction, and innovation as a way of life
- Ensure understanding and achievement of all necessary regulatory and compliance requirements
- Promote a quality compliant culture and adherence to the Quality Management System requirements at all times
- Manage all manufacturing resources and operations in collaboration with other functional managers
- Establish continuous improvement performance targets, measure actual performance and take appropriate and timely corrective action if negative trends emerge for; product quality, customer service, capacity, lead time, labor efficiency, space utilization, yield, department spending, and business processes effectiveness
- Provide leadership direction to team on manufacturing process improvements to meet new product introduction quality, service, and time to market objectives
- Collaborate with Business and Product Development teams to ensure that all new products and processes are introduced into FDA compliance, on time, on budget to ensure operational success
- Maintain and improve health & safety systems; oversees the development of appropriate training materials and programs that will foster a safe working environment and a culture of continuous SEHS improvement. Utilizes existing resources where available and develops new materials as required
- Directs all facilities and maintenance activity for the Denver site
- Proven track record and genuine interest in successfully creating and managing a highly talented, engaged and performing team
- Demonstrated knowledge and application of FDA regulatory requirements, housekeeping, health and safety
- Demonstrated problem solving and process improvement skills
- Demonstrated ability to create and sustain a culture of continuous process improvement and waste elimination that yields improvements to quality, delivery, cost and time-to-market using recognized industry Lean practices
- Ability to handle multiple tasks in a fast-paced and results-oriented environment
- Demonstrated flexible management style, utilizing the appropriate style for the given situation
- Preferred experience in various 3D printing platforms, materials and necessary post processing
- Ability to travel 15% of the time both domestic and international
33
Associate Director, Manufacturing Resume Examples & Samples
- Ensure plans and resources (people, facilities, supplies etc.) are efficiently utilized to deliver uninterrupted supply of clinical drugs
- Oversee the hiring, development, retention and performance of staff for the leadership and execution of manufacturing operations
- Develop comprehensive operating plans and monitors achievement of business and financial goals
- Development of effective working relationships with both internal and external partners
- Requires a BS in the sciences and a minimum of 8+ years of experience in cGMP pharmaceutical or biotechnology manufacturing environment
- Previous management or project experience is required
- Master’s degree in Biology, Biochemistry, Molecular Biology, Chemistry or Chemical Engineering
- 10 years of professional/industrial cGMP experience in a biotech, diagnostic, therapeutic or pharma company
- Subject Matter Expert on chromatography and TFF
- 5 years’ supervisory experience in manufacturing or operations
34
Director, Manufacturing Resume Examples & Samples
- Resource planning, manufacturing execution and deployment or all Optical Communications and Commercial Lasers product lines
- Alignment/Coordination with engineering and demand planning functions to ensure order fulfillment expectations are met or exceeded along with operations efficiencies indicators
- Deploy strong leadership skills . Build and retain a high-functioning team with a focus on direct labor training and engagement
- Instill a Quality First culture, employing lean initiatives
35
Senior Director, Manufacturing Resume Examples & Samples
- Development of manufacturing plan and establishment of procedures to ensure high standards of quality, safety, efficiency and schedule compliance
- Formulates and recommends manufacturing policies and programs that guide the organization in maintaining and improving its competitive position and profitability
- Directs and monitors department managers to accomplish goals of the manufacturing plan, consistent with established manufacturing and safety procedures
- Acts as liaison between department management/subordinate levels, as well as executive/department manager levels to inform personnel of communications, decisions, policies and all matters that affect their performance, attitudes and results
- Hires, trains, develops and evaluates staff. Holds direct reports accountable for performance. Takes corrective action as necessary and develops top talent to grow within the organization
- Develop and manage the budget within the functional area of responsibility
- Partners with Quality and Safety directors to ensure compliance with quality and safety best practices
- Leads manufacturing Lean and Continuous Improvement efforts resulting in significant year over year savings
- Incumbent will challenge and improve upon existing operating standards to include a proactive, continuous improvement focus on metrics associated with throughput, efficiency and quality
- Hologic, Inc. is proud to be an Equal Opportunity Employer & VEVRAA Federal Contractor
36
Director, Manufacturing & Packaging Resume Examples & Samples
- A minimum Bachelor’s Degree is required. A Master Degree and/or a degree focused in Health Sciences, or Technical Engineering preferred
- A minimum of ten (10) years of overall business experience is required
- A minimum of five (5) years of pharmaceutical industry experience is required
- A minimum of five (5) years of experience leading other leaders is required
- Experience in multiple functions such as Operations, Engineering, Maintenance, Materials Management, supply chain/logistics, Quality, and/or other related operations functions are highly preferred
- Experience in remediation of a consent decree or warning letter is preferred
- Knowledgeable in cGMPs and pharmaceutical industry applicable regulations
- Process Excellence/Six Sigma certifications are preferred
- Ability effectively manage performance and engage employees
- This position is based in Lancaster, PA and may require up to 5% of domestic and international travel.4863170315
37
Director, Manufacturing Optimization Resume Examples & Samples
- Strategically focus on process modifications to increase efficiencies on manufacturing processes used to fabricate tubs and shower bases (thermoforming, fiber and resin application, trimming, assembly and pack)
- Optimize the processes within New Product Introduction (Stage/Gate) and Production Part Approval
- Develop the strategy for tool design, deploying best practices from outside the industry
- Determine the correct locations for New Product Introductions working closely with Product Development
- Strategically develop improvements to the implementation of changes through the ECN and 4M processes
- Developing and deploying Training (6s, 5s, Kaizen, Lean),
- Value Stream Mapping (current & future state) of primary and secondary manufacturing sites
- Line Balancing with the goal of one piece flow
- Develop the strategy and best practices for Routings & BOMs for NPD and current products
- Tool and Fixture Design for NPD and ongoing production
- Bachelor’s degree in Mechanical Engineering or equivalent
- Master’s degree in Business Administration or Mechanical Engineering is a plus
- Certifications: Professional Engineer, Six Sigma Black Belt is a plus
- At least 10 years in Engineering, Sourcing, or Quality related roles as a manager in a discrete manufacturing environment (Fortune 500 Company is a plus)
- Excellent Communication and Presentation Skills
38
Director, Manufacturing, Global Resume Examples & Samples
- Provide strategic operational leadership and management direction in a multi-disciplined manufacturing operation to ensure timely delivery of quality products to the customer while meeting profitability objectives
- Develop and implement the strategic and operating plans which support the company's business and operational objectives aligned with the Balanced Scorecard and Operating goals, while leading and driving the implementation of Lean manufacturing practices
- Plan, direct, and coordinate all Production activities through subordinate Production Managers ensuring the division's objectives for producing and shipping the quality and quantity of aircraft within the cost parameters established
- Coordinate with the support groups as necessary to create focus, attention, and accountability to Production requirements
- Identify Key Performance Indicators (KPIs) and ensure feedback at a business unit level
- In coordination with Methods and Facilities, assures the development and implementation of the capital plan to support Production requirements, product improvements and enhancements of Production facilities in keeping with the division product, productivity, and growth goals
- Coordinate the development and implementation of operating and Production standards and goals in support of the division business plan
- Review and evaluate cost effectiveness, consistency, quality, accuracy, and performance to standards and takes actions as necessary to correct discrepancies
- Approves operational budget and manpower requirements
- Actively lead and drive execution of the Achieving Excellence System within area of responsibility (i.e. SQPEC, Visible Leadership, etc) in line with Bombardier's strategic vision
- Assure effective customer service and relations by implementing processes to deliver quality products on time
- Promote continuous performance improvements throughout the area using AES tools and methodology
- Build, develop, and lead a competent and motivated Production management team that positively contributes to Safety, Quality, Productivity, Employee and Cost commitments
- Promotes the maintenance of harmonious industrial relations within the Production environment by promoting and developing good working relationships with team members and open communication
- Facilitate communication & collaboration with other functions and senior leadership
- Coach, develop and mentor Operations Unit Managers and Line Managers, and jointly establish performance measures
- Ensure financial performance objectives (manufacturing costs and operating budget) are met through efficient governance, continuous performance evaluation & control and deployment of key indicators at all levels
- Identify and mitigate potential risks pertaining to delivery, manufacturing costs, product conformity and compliance to regulations (Environment, Health & Safety)
- Be required to travel occasionally
- You hold a University Degree in Business Management, Engineering, Operations Management, or equivalent
- You have minimum of 10 to 15 years of progressive management experience in an aerospace manufacturing environment
- You have a minimum of 7 years management experience in implementing lean manufacturing principles and concepts or Six Sigma/performance improvements within the aerospace industry
- You have a minimum of 5 years experience managing complex organizational change initiatives
- You have demonstrated of strong leadership and team building skills, coupled with strong analytical skills
- You have excellent written and verbal communication skills
- You have the credibility, presence and maturity to quickly gain the confidence and respect of Bombardier Business Aircraft senior management
- You are self-motivated and can efficiently organize and prioritize objectives and projects
- You have a firm understanding of aircraft Customer Options and option management
- You have interpersonal skills necessary to establish and maintain effective working relationships with co-workers, employees, management, and contractors
- You possess presentation skills necessary to effectively communicate, update, persuade, and/or facilitate discussions with all levels of management, customers, and potential customers
- Have computer skills necessary to learn and/or operate word processing, spreadsheet, database, email, and web-based applications
- You are a results-driven leader who is outgoing and persuasive, is accustomed to working with senior management and yet is able to effectively relate to shop floor issues
- You have experience developing teams, including individual development and improving teamwork across an organization
- Have the credibility, presence and maturity to quickly gain the confidence and respect of senior
39
Director, Manufacturing Resume Examples & Samples
- Bachelors Degree in a manufacturing-related curriculum. MBA degree is desired
- Minimum of 10 years of career progression in a manufacturing environment preferred. Experience in fabrication, assembly, and testing of electro mechanical products preferred. Experience in a manufacturing organization of at least 300 employees, and experience with multi-national business also preferred
- Record of success in driving continuous improvement and rapid customer response through closed-loop feedback systems required
- Proficiency in spoken and written English is required
- Superior leadership skills with demonstrated ability to effectively manage and develop a diverse team of people, and facilitate effective cross-cultural business interaction
- Electro-mechanical comprehension sufficient to understand the operation of production equipment and facility systems and to engage in problem-solving discussions on products
- Financial literacy sufficient to understand Financial Statements and Budgets
- Microsoft suite of software and understanding of ERP systems
- Self-motivated, with a bias for action
- Travel occasionally in the US and internationally
40
Director, Manufacturing Resume Examples & Samples
- Ability to read, analyzes, and interprets the most complex documents in Technical English. Respond effectively to the most sensitive inquiries or complaints. Multilingual proficiency is a plus (English, Spanish, Dutch & Papiamentu)
- Ability to utilize Microsoft Office Professional Software package, to include MS Word, MS Excel, MS PowerPoint, and MS Project Management. The Employee must have practical knowledge of Microsoft Outlook and related Smith & Nephew software
- Comprehends and applies principles of advanced calculus, modern algebra, and advanced statistical theory
41
Senior Director Manufacturing Resume Examples & Samples
- Deliver on the successful implementation of key strategic Manufacturing programs to deliver $300M in value over the next 5-7 years
- Develop capabilities and motivate talent across the globe to become top performing change agents that drive the supply chain transformation programs
- Participate in the development and implementation of manufacturing strategies and tactical execution in support of business objectives
- Collaborate with Global Business and Regional Supply Chain leaders to develop robust strategies and work plans to deliver forecasted value expectations
- Provide strategic leadership and oversight for the IT migration of the Manufacturing systems across all 92 global mills
- Benchmark with external companies and industry experts to identify transformational Manufacturing thinking and processes in order to develop a robust pipeline of future programs
- Drive integration across all KC Supply Chain functions (Safety, Sustainability, Quality, Procurement, & Logistics) to develop and strengthen source to shelf connection and eliminate waste
- Ensure complete integration of standard OPEX process & Reliability programs across all global regions and business units
- Ensure capability is being built internally to the Global Manufacturing Team and externally to business resources to sustain the long term objectives through program deployment as well as building long term capability through the Supply Chain University. This includes the ongoing development of our global mill managers
- Work with KC global business units to gain leader alignment at all levels of the organization, identify capable resources to train and deploy standard and sustainable Manufacturing Programs with a strong focus on Management Systems and Cultural Enablers
- Execute all Human Resources processes for team including Performance & Development, Talent Review, and Succession Planning
- Provide coordination of processes and standards across KC Manufacturing programs
- Advanced degree from an accredited college/university; MBA desired
- Must have 10 year’s direct or indirect manufacturing/operations or supply chain experience, preferably in a consumer goods company
- Project management certification
- Six Sigma Green and/or Black belt certification and working knowledge of Lean End to End thinking & tools
- Thorough knowledge of Manufacturing programs, OPEX/Six Sigma, Reliability and Design to Value
- Experience leading large initiatives in the context of a large, complex, global organization where working across boundaries and leading through influence are keys to success
- Demonstrated ability to be an accountable change agent
- Proven experience of leading and driving high quality results on large global, multi-functional programs
- Executive presence – is viewed as promotable to key functional role
- Global perspective, including cross cultural acumen and international experience
- Demonstrated ability to lead large projects using project management standards & practices
42
Director, Manufacturing Excellence BDS Resume Examples & Samples
- Security clearance will be required
- Experience in leading Operations changes across multi-site operations groups
- Experience with complex fabrication and assembly operations
- Familiarity with automobile manufacturing control processes is desirable
- Familiarity with aerospace products and/or US government customers is desirable
43
Associate Director, Manufacturing Technical Resume Examples & Samples
- Oversee all manufacturing technical functions and collaborate with partners and customers, such as MT and MST, to achieve MFG deliverables including continuous improvement projects (yield increases), COGs reduction, lean manufacturing, schedule adherence, and facility upgrades and enhancements
- Through the use of advanced scheduling systems and tools, maximize schedule adherence, build standard process models, optimize real time scheduling, and implement CAPA action plans as needed
- Interact regularly and collaboratively with both internal and external customers to effectively resolve MFG issues
- Oversee the investigation and execution of low risk Quality Events to support manufacturing operations and provide support for medium and high investigations where required
- Facilitate the authoring of minor equipment and facility change controls, MBR revisions, and CAPA Action Plans
- Lead and manage project plans, spending, personnel, and schedules of MFG specific projects according to deliverables and overall priorities
- Drive strong collaboration and communication across MFG, Quality, MS&T/MT, Analytical, and Product teams to ensure projects meet all objectives and timelines
- Identify process improvement opportunities and implement process changes and improvements through quality systems
- Proven leadership skills and track record of success in managing technical groups (direct reports) and teams (matrix environment)
- Excellent project team management and matrix system skills
- Excellent verbal communication, documentation and technical writing skills
- Demonstrated experience in cell culture, purification and analytical sciences for producing clinical and commercial biopharmaceuticals
- Proven records and ability in productivity improvements and cGMP biologics manufacturing
- Familiarity of regulatory issues pertaining to the manufacture of biologics, large scale biopharmaceutical unit operations and process validation
- Demonstrated creative problem-solving skills under resource constraints and time pressure
- Strong technical problem-solving abilities, written and verbal communication skills
- Demonstrated leadership skills in coaching, managing and mentoring new staff members
- Demonstrated success of leading effectively in a complex matrix project team environment
- Knowledge of science generally attained through studies resulting in a M.S. in science, engineering, biochemistry or related discipline, or its equivalent is highly desired
- Direct biologic manufacturing experience of 10+ years with minimum of 5+ years of previous supervisory experience which demonstrates proficiency in selection of team and effectively managing personnel issues is required
- Strong knowledge of biopharmaceutical manufacturing processes with a proven record in biopharmaceutical technology
44
Director Manufacturing FW Resume Examples & Samples
- Give major input to issuing directives in production and related area
- Works directly with the Factory GM in term of factory production personnel skills evaluation and through SOM provide facts/business cases to get the Factory GM/Owner to invest into various productions mfg machineries
- Act as LO Shoes Master responsible for coaching, training/teaching and continuously upgrading technical, shoes manufacturing expertise and decision making capability of the Production personnel of the designated groups of factories/Operations Centers
- Can independently lead LO based projects within defined scope of production
- Excellent written and verbal English communication
- Chinese, Indonesia or Vietnamese local language an advantage
- University degree preferably on shoe making or engineering
- Proven manufacturing expert / shoes master
45
Director, Manufacturing Execution System Resume Examples & Samples
- Responsible for implementation and sustainment of the global integrated standard Manufacturing Execution Systems strategy within manufacturing
- Serves as the Business Owner in the life cycle activities for virtual and control aspects of defined global MES manufacturing processes within manufacturing
- Contributes to system configuration and business process alternatives utilizing a working knowledge of the software and business processes
- Coordinates all deployments, including budget and schedule adherence, within the assigned areas and communication of status/issues to key stakeholders and leadership
- Serves as a champion for utilization of Lean Six Sigma techniques to improve all aspects of manufacturing processes
- Partners with IT Risk Management and Compliance in support of site GMP inspection readiness for business processes and systems under business ownership responsibility
- Participates in the creation/approval of business cases and the follow on benefit tracking for MES projects within manufacturing
- Participates in the annual budget preparation and project prioritization process for global MES programs
- Partners with appropriate departments to ensure regulatory compliance of global processes and systems within the defined span of control
- Experience in developing and/or deploying MES solutions in the pharmaceutical industry required
- Experience in GMP or GLP regulations required
- Experience in design and implementation of global manufacturing business processes and standard integrated systems required
46
Director, Manufacturing Egineering Resume Examples & Samples
- A minimum of a Bachelor’s degree is required in an Engineering or Science discipline
- An advanced degree, such as an MS or an MBA is preferred
- A minimum of 10 overall business experience is required
- Cross-Sector exposure/experience desired
- Ability to translate engineering goals and objectives into successful strategies that lead to tactical plans is required
- Ability to develop people, manage technology, embrace financial goals and utilize customer-focused decision making are required
- Change management, project management, the ability to work effectively and drive alignment in a global environment through strong communication and empowerment is required
- Demonstrated knowledge and expertise in bridging technical and business disciplines, evaluating and determining appropriate risks is preferred
- Multi-plant experience with a focus on global markets is preferred
- Deep knowledge continuous improvement tools, lean manufacturing and six-sigma is preferred
- Has A Track Record Of Tangible Improvements is preferred
- Strong Leadership: Bias for Action
- Assertive Influencing & Collaboration/Teaming Skills
- This position may require up to 60% travel both domestic and international.2731170605
47
Director Manufacturing Solutions Resume Examples & Samples
- Manage a team of 2-3 direct reports
- Engage with key stakeholders in BUs to define vision and strategy of Digital Factory aligned with BU strategy and priorities
- Define specific applications roadmaps for manufacturing systems per BU
- Drive the decision-making process from demand to implementation of manufacturing systems in close alignment of Business and IT
- Initiate and oversee the projects that fit the strategic roadmap
- Create mechanisms to ensure successful implementation and adoption of new technologies on the shop floor, including achievement of planned benefits
- Relationship building with key stakeholders within BUs, such as Digital Factory leads and Operations leaders and with the Segment IT function and TEIS delivery organizations
- Establish continuous improvement mindset within the team. Perform frequent benchmarks to check effectiveness of the implemented solutions
- Identify and provide recommendations on industry best practices and new solutions in the area of Digital Factory, Industry 4.0, IoT
- Performance driven nature
- Demonstrates strong business minded consultative approach with focus on profitability and margin
- Thorough and solid understanding of IT Strategy and IT Management
- Strong knowledge of operations, manufacturing systems and related technologies
- At least eight years of experience in the IT in high-tech industry
- Wide experience in developing customer-centric IT solutions
- Proven experience as IT director or similar role
- Experience in analysis, implementation and evaluation of IT systems and their specifications
- Experience in controlling information technology budget
- Excellent organizational and leadership skills
- Outstanding communication abilities
- Ability to build strategic partnerships across organizational lines
48
Director, Manufacturing Excellence Resume Examples & Samples
- Oversee a team of 40 plus engineers, continuous improvement professionals and process experts
- Develop and maximize team member capabilities by fostering an environment that identifies talent, provides ongoing coaching and feedback and creates opportunities for growth and development
- Responsible for taking on a visible, active role in safety programs and plans to ensure the safety of employees
- Provide oversight to BNA’s continuous improvement activities and coordinate with other Bunge opco’s Operating Companies (OpCo’s) as needed
- Ensure the BNA reliability excellence program is meeting overall objectives and expected cost savings
- Monitor and report out on the status of continuous improvement projects, capital projects and reliability excellence metrics
- Build, develop and grow initiatives and coordination amongst functions vital to the success of projects and achievement of objectives
- Work closely with segment operations leaders to foster a cohesive and aligned management and support team to drive results
- Work directly with the business units to evaluate, plan and develop larger capital expenditure projects
- Ensure capital and expense projects are aligned with business unit objectives and completed within scope, schedule and budget
- Manage project submission process to include evaluation of projects, review of proposals and advise on project feasibility
- Assign engineering team, process experts, reliability leaders and process control resources to projects to optimize resources and ensure required expertise
- Provide assistance to plant locations in identifying and developing projects resulting in added profit or cost savings
- Model and cascade behaviors supporting BNA capabilities (Operational Excellence, People Management, Business Intelligence, Customer Satisfaction, Value Chain Integration and Risk Management)
- Communicate and model good business practices that support the company’s core values
49
Director, Manufacturing Engineer Resume Examples & Samples
- Serves as primary functional contact and technical expert on the senior leadership team to set the strategic direction for the organization as well as to ensure the tactical execution of commitments for area of responsibility
- Provides leadership, direction and strategy development and makes final administrative or operational decisions within level of authority
- Plans, directs and is accountable for all activities and results of organizational goals and AOP objectives. Provides leadership to team members to achieve goals
- Establishes organizational procedures and plans, consistent with corporate policy. Executes, and recommends modifications to corporate policy
- Partner closely with Operations leaders to ensure the smooth transition of products to volume manufacturing by providing requisite component, subassembly or system level test fixtures, training and procedures
- Develop and coach the Engineering leadership team to provide project management of cross-functional product development teams to deliver projects: on time, within budget, with quality and within profit margins
- Ensure that the groups activities provide the role model for safe behavior, including proper protocols and procedures, to include core values
- Demonstrates broad and comprehensive understanding of different systems, theories and practices
- Negotiates and influences the opinions of others at the senior executive level and in external organizations; exercises sensitivity to the audience
50
Director Manufacturing Plant Resume Examples & Samples
- Develop and implement Stock Yards strategy to drive continuous improvement
- Lead efforts with plant leaders to standardize and drive operational efficiencies focused on continuous improvement strategy
- Lead and develop standardize productivity metrics, set goals, drive productivity
- Work with weak/underperforming divisions in a mentoring role
- Develop strategy to standardize production/packaging equipment, set standards for company
- Collaborate with procurement manager to develop plan to standardize raw material usage
- For facilities with fleet, lead and develop metrics for measuring productivity
- Commercial oversight for outsourced partners including pricing (formulas based) specifications, communicating items authorized and collaborating with FSQA and area leadership to drive penetration in COP
- *EOE Race/Color/Religion/Sex/Sexual Orientation/Gender Identity/National Origin/Protected Veteran/Disability Status***
- Minimum 5 years management level experience working in production/operations facility
- Broad knowledge of production experience (food preferred)
- Advanced knowledge of Microsoft Excel, Word & Power Point
- Highly analytical, ability to conduct advanced analyses independently
- Independent, self-motivated, proactive team player with strong work ethic
- Daily interaction with Production/Operations/Replenishment teams. This would include interaction with senior manmagement
- Lead Six Sigma accreditation