Contract Manufacturing Resume Samples
4.5
(103 votes) for
Contract Manufacturing Resume Samples
The Guide To Resume Tailoring
Guide the recruiter to the conclusion that you are the best candidate for the contract manufacturing job. It’s actually very simple. Tailor your resume by picking relevant responsibilities from the examples below and then add your accomplishments. This way, you can position yourself in the best way to get hired.
Craft your perfect resume by picking job responsibilities written by professional recruiters
Pick from the thousands of curated job responsibilities used by the leading companies
Tailor your resume & cover letter with wording that best fits for each job you apply
Resume Builder
Create a Resume in Minutes with Professional Resume Templates
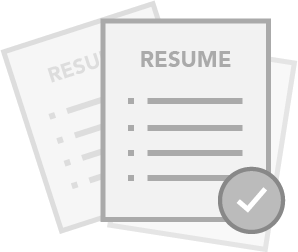
CHOOSE THE BEST TEMPLATE
- Choose from 15 Leading Templates. No need to think about design details.
USE PRE-WRITTEN BULLET POINTS
- Select from thousands of pre-written bullet points.
SAVE YOUR DOCUMENTS IN PDF FILES
- Instantly download in PDF format or share a custom link.
VG
V Gottlieb
Vincenza
Gottlieb
233 Wolff Knolls
Houston
TX
+1 (555) 557 0839
233 Wolff Knolls
Houston
TX
Phone
p
+1 (555) 557 0839
Experience
Experience
San Francisco, CA
Contract Manufacturing Planner
San Francisco, CA
Schmeler-Larkin
San Francisco, CA
Contract Manufacturing Planner
- Track and improve vendor performance with identified KPI’s
- Expedite purchase orders by working closely with vendors while identifying and resolving vendor or shipment problems
- Manage inventory levels with a key focus on reducing inventory days while improving service to our Representatives
- Drive to constantly look for areas for process improvements and eliminate non-value-added activities
- Communicate service outlook and develop strategies for all service shortfalls
- Work with PLC and Marketing on new product introduction, clearance and end of life runs and dispositions
- Review New Items and manage buy decisions for finished goods and back up materials at all buying stages: S&OP, Trend, Early Sell
Phoenix, AZ
Contract Manufacturing Manager
Phoenix, AZ
DuBuque, Zemlak and Krajcik
Phoenix, AZ
Contract Manufacturing Manager
- Lead supporting efforts to contract manufacturing partners in region in executing daily/weekly/monthly/quarterly plans
- Contract Management : You ensure the establishment of Complete Contract Manufacturing Agreements and the timely review of existing contracts
- Organize and lead day-to-day efforts and priorities of local and global engineering teams that may include, but not be limited to
- Support assigned innovation from signed PDR1 stage through start up and into ongoing production
- Develop yearly volume budgeting process for respective co-packers
- Evaluate product sourcing networks and vendors to ensure best service & quality at a competitive price. Establish annual service and cost targets
- Operations & Project Management
present
Chicago, IL
Manager, Contract Manufacturing
Chicago, IL
Mayer Inc
present
Chicago, IL
Manager, Contract Manufacturing
present
- Partner with Purchasing to co-create and manage the bidding process for new sourcing opportunities among our supplier network
- Develop and manage a visual metric/dashboard to provide an oversight of the production plan
- Develop and manage budgets for area of responsibility to ensure performance to business objectives
- Provide leadership to ensure continuous improvement throughout contract manufacturing network
- Lead and manage complex North America Contract Manufacturing network across multiple product categories
- Performance Analysis and Improvement
- Manage ERP aspects at BioMarin for production efforts at CMO & Monitor and manage inventory levels of drug substance at CMO site
Education
Education
Bachelor’s Degree in Business
Bachelor’s Degree in Business
Indiana University
Bachelor’s Degree in Business
Skills
Skills
- A team player; able to use strong communication, analytical and management skills to lead a diverse group forward
- Broad knowledge of regulatory compliance inclusive of cGMP, FDA regulations, familiarity with ICH guidelines and EU regulations
- Prior knowledge in Advanced Planning systems is desired
- Experience with documentation and quality systems
- Proficient in Excel, PowerPoint, Visio, Word, etc. in addition to experience working within shared work environments
- Able to provide clear direction to others in ambiguous situations and environments
- Strong interpersonal, written and oral communication skills
- Extensive knowledge and experience with full-scale drug product manufacturing from formulation through the final package
- Superior problem solving skills and the ability to think “outside the box”
- Overall operations/marketplace knowledge with experience in the relevant category
15 Contract Manufacturing resume templates
Read our complete resume writing guides
1
Contract Manufacturing Planner Resume Examples & Samples
- Review New Items and manage buy decisions for finished goods and back up materials at all buying stages: S&OP, Trend, Early Sell
- Partner with the Suppliers to develop and negotiate the best production and shipping schedule needed to support customer demand. Review supplier production schedule weekly. Partner with Logistics to ensure product is available on time at the distribution center
- Communicate service outlook and develop strategies for all service shortfalls
- Manage inventory levels with a key focus on reducing inventory days while improving service to our Representatives
- Work with PLC and Marketing on new product introduction, clearance and end of life runs and dispositions
- Must analyze sales and shipment data daily and react within constraints of basic inventory control. Examples are evaluation of airfreight expenditures, expedited production, express inspection, etc
- Judgement: Must consistently demonstrate strong judgement skills in all aspects of the position, including planning, expediting, and de-expediting
- Dollar: Direct responsibility for material and finished good inventories valued up to $20MM per year. Responsible for premium cost control (freight and direct and indirect overtime)
- Volume: Directly responsible for inventory control of 300-600 active individual finished stock codes depending on complexity
- Requires effective, frequent, independent judgement on complex, volatile situations. Stock substitutions, primarily resulting from significant changes in trend or estimates, field communications, "ROQ" revisions, and "Take off Sales" require higher level approval
- Contract Manufacturing Planner provides the critical role in inventory management. Major impact on facility KPIs in terms of cost, service, and capacity restraints. Any errors caused by the Finished Good Planner could directly affect customer service and the financial performance of the unit
- BA/BS with basic understanding of the fundamentals of Supply Chain Management, Finance, Engineering and Logistics
- One to three years experience with an ERP system and knowledge of MRP II concepts
- Proficiency in MS Excel is a requirement, MS Access a plus
- Knowledge of functional operations (production, material handling, purchasing, and finance)
- Experience analyzing, preparing and communicating reports to production and planning with projected impact to the goals and objectives
- Must have a thorough understanding of all policies and procedures relative to customer service and inventory control. APICS certification a plus
- Detail oriented, with the ability to work at a fast pace in a rapidly changing business environment
- Demonstrated experience in addressing issues to senior management
- Drive to constantly look for areas for process improvements and eliminate non-value-added activities
- Customer focused with a sense of urgency and the ability to effectively function within a diversified team which utilizes matrix management
2
Director, Procurement Contract Manufacturing Resume Examples & Samples
- Attract, develop, and retain a high performing team (1 Sr. Manager and 1 Specialist) through coaching and feedback
- Serve as the subject matter expert for contract manufacturing contracts and possess an in-depth knowledge of market capabilities, economic cost drivers, supplier financials, and market competition
- Negotiate, implement and manage long-term strategic contracts to ensure relationships are protected by legally binding contracts that are aligned with corporate mandates, support business requirements and protect Company interests, ensuring continuity of quality supply and lowest total delivered cost
- Drive senior level alignment and engagement with key Business partners for Procurement initiatives and programs (sourcing, implementation, compliance)
- Develop strategies for maximizing value across the end to end supply chain
- Prioritize and enable continuous improvement in area of responsibility
- Benchmark supply alternatives to competitively position optimal solutions
- Manage and continuously improve financial tools to forecast spend, highlight risk/opportunity and quantify productivity initiatives
- Assess supplier and platform risks and develop the appropriate contingency plans
- Utilize Supplier Relationship Management tools and provide Procurement Leadership for the identification and execution of Supplier Productivity and Sustainability initiatives for key suppliers
- 5+ years of procurement and negotiation experience
- CPG manufacturing experience is a plus
- Knowledge of current procurement policies, practices and procedures, as well as e-business, procurement systems and supply chain management processes to include
3
Manager, Contract Manufacturing Resume Examples & Samples
- Significant and diverse management experience (5+ years of plant operations, engineering, supply chain, distribution, and/or procurement experience preferred)
- A team player; able to use strong communication, analytical and management skills to lead a diverse group forward
- Strength in the following skill sets: Verbal, written, analytical, and problem-solving
- Organization and planning
- Group management
- Negotiation and Contract Manufacturing development
- Continuous Improvement skills
- Must be results-focused
- Flexible and customer/client service oriented
- Superior problem solving skills and the ability to think “outside the box”
- Desire to approach work as a continuous learning opportunity
- Travel required; can be significant at times
- Overall operations/marketplace knowledge with experience in the relevant category
- Superior project management capabilities
- Computer skills – Excel, Word, Power point, and Access
4
Contract Manufacturing Operations Manager VEB Innovation Resume Examples & Samples
- Develop and analyze performance data (consumer complaint, order fulfillment, budget variances, schedule attainment, etc) in order to identify business plan variances using established systems and ad-hoc problem solving
- Support Director in resolving Contract Manufacturer operational issues relating to conversion, quality and transportation
- Coordinate suppliers, concentrate plant, production, R&D and product commercialization using technology (e.g., e-mails, fax, teleconferences) and key business contacts in order to execute new product launches
- 5+ years of experience
- Capacity Planning and Management: Knowledge of multiple levels of the supply chain used to analyze contingency points, labor staffing and feedback on supplier capacities. Ability to predict suppliers' capabilities to deliver goods and services necessary based on KO system and industry trends. Ability to translate all supplier capabilities associated with commodities, products and/or services. Ability to align supplier capabilities with Company strategy. Ability to comprehend supply/demand market conditions
- Forecasting - Cost: Knowledge of cost forecasting processes and inputs to determine the impact to KO and/or bottlers. Knowledge of key elements such as raw material costs, economic principles, supplier/processing costs and market conditions
- Understanding / Familiarity with equipment & technology e.g. packaging machinery, fillers. labelers, palletizing etc
5
Contract Manufacturing Operations Manager Resume Examples & Samples
- Accountable to Director of Contract Manufacturing for achieving manufacturing goals and objectives across multiple third-party facilities. Primary focus will be to manage and lead Contract Packaging efforts supporting the Odwalla supply chain that includes Copack and DSD operations in Southern California
- Develop and analyze performance data (consumer complaint, order fulfillment, budget variances, schedule attainment, etc.) in order to identify business plan variances using established systems and ad-hoc problem solving
- Support Director and Program Managers on brand innovation project work and on-site implementation
- Identify supply chain metrics (e.g., forecast variance, total spending, cost savings) using data collection and survey reporting methods in order to monitor and coach for improved performance
- Responsible for production, quality, customer service and cost goals
- Sustain a consistent, long-term vision through continuous process improvement
- Adopt and share best ideas inside and outside of the company
- Demonstrate behaviors needed for effective implementation of change
- Ensure manufacturing processes are compliant with company specifications and meet customer expectations
- Satisfy the needs and service requirements of the internal and external customers
- Ensure compliance to company and regulatory policies
- Bachelor's Degree - Business or Technical. Masters Preferred
- At least 7 years of increasing levels of manager roles of people & processes
- Proficiency in the principles of manufacturing management
- Proficiency in specific supply chain capabilities, strategies and interdependencies
- Ability to collaborate cross-functionally and coordinate efforts around process improvement
- Proficiency in national regulatory requirements in the areas of safety, environment and emergency management
- Proficiency in basic elements of Good Manufacturing Practices in a Manufacturing environment
- Proficiency in key business drivers used to gauge the effectiveness and performance of an internal group or supplier
- Proficiency in MS Office Suite applications
- Contingency Planning: Knowledge of information used to establish contingency plans for supply chain processes (e.g., cost, risk level, manufacturing and third party capabilities). Ability to develop contingency plans that meet performance requirements
- Inventory Management: Optimize inventory levels using statistical models to design min/max/reorder levels. Knowledge of asset management procedures, policies and information used to optimize inventory levels and/or fill rates (e.g., balance inventory levels against inventory carrying costs)
- Beverage industry knowledge across multiple platforms, knowledge of contract manufacturing and packing networks
- Understanding / Familiarity with manufacturing processing technology (pasteurization, blending mixing, etc.)
- Understands IE workflow analysis, assembly, line and cell layout, manual packaging
- Negotiations – Experience in negotiating operating terms in agreements in addition to pricing
- Understanding / Familiarity with Lean Manufacturing principles
6
Contract Manufacturing Operations Manager Resume Examples & Samples
- Collaborate with Shared Services on Performance Letter investigations and explanations
- Participate in Director’s monthly Business Performance Reviews
- Monitor communication and distribution of confidential and restricted information involving confidential ingredients using standard procedures for handling of confidential documentation in order to protect Company trademarks
- Understanding / Familiarity Lean Manufacturing principles
7
Category Manager Contract Manufacturing Resume Examples & Samples
- 10+ years of exp in strategic sourcing
- Negotiation experience
- Exp in developing category/commodity strategies
- Bachelor's degree in Manufacturing, Engineering, Supply Chain, Finance, Management or related area of study
- LEAN certification is preferred
- Knowledge of Lean Concepts, Manufacturing, Process Improvement and Facilitation skills
- Experience in strategic sourcing of contract manufacturing services, preferably in a global technical product delivery organization, with a clear record of success and achievement dealing with complex supply chain/procurement issues
- Manufacturing, Engineering, Operations, Commodities or Supply chain management experience of a fast paced highly regulated environment strongly preferred
- Demonstrated knowledge of the latest supply chain management techniques, strategic sourcing, inventory management and contract management
- Experience with manufacturing, processes improvement methodologies and understanding of design and quality requirements
- Demonstrates prior experience in high performing teams in fast paced environment
- Advanced skills in Microsoft Office Word, Excel, PowerPoint, MS Project
- Demonstrated experiences providing data-driven analysis problem solving skills that address and balances cost with service level requirements (within a business unit and across multiple business units)
- Demonstrated understanding of project management methodologies that deliver cost savings to stakeholder satisfaction
- Proven success in leading vendor negotiating and facilitation
- Ability to develop complex contracts and work with legal counsel. Knowledge of contract law and trade compliance regulations
- Intimate knowledge of best-in-class procurement procedures and policies as well as best in class management of contract manufacturing or other 3rd party outsourcing partner
- Strong understanding of 7-Step Strategic Sourcing Model, e-tools, processes and systems (SAP a plus)
- Demonstrated ability to develop procurement category strategies
- Communications: Excellent interpersonal and presentation skills, ability to effectively communicate at all levels of the organization
- Organization/Time Management: Ability to prioritize and manage multiple tasks simultaneously to meet the deadlines & delegate tasks effectively
- Customer focus: Establishes and maintains effective customer relationships; uses first-hand information from customers to improve overall sourcing process; quickly gains trust and respect
8
Contract Manufacturing Director Resume Examples & Samples
- Minimum 10 years leadership experience in operations management, preferably in a multi-national environment. Proven experience in leading all facets of manufacturing (strategic planning, budget, production, global safety laws & regulations, etc.)
- 5+ years’ experience in professional procurement/supplier mgmt/supplier quality position
- Available to travel domestically and internationally (40%-60%)
- Leadership of cross-functional commodity/process teams
- Contract management and negotiation
- Six Sigma and/or Lean Manufacturing experience and experience with manufacturing operating systems designed to gain efficiencies, lower costs, improve quality and service delivery
- Innovation design processes
- Skilled in supply management performance measurements
- Demonstrated leadership in forming and maintaining strategic alliances
- Experience in procurement, supplier development, and/or supplier quality assurance for a large, multi-divisional corporation
- Knowledge of procurement and/or ERP systems
- Strong negotiation experience with experience performing financial analysis and P&L understanding
- Strong oral and verbal communication skills
- Influence skills to achieve results across a matrixed organization
9
Associate Director, Contract Manufacturing Resume Examples & Samples
- Direct CMOs to ensure the supply of reference standards and other key materials used in the manufacture of drug substance and drug product
- Manage the transfer of manufacturing and testing procedures and specifications to CMOs
- Perform technical reviews and ensure CMOs compliance with manufacturing and testing procedures and specifications
- Work cross functionally, coordinating the necessary internal resources to ensure timelines can be achieved and flag issues for resolution
- Proactively solve potential supply chain issues
- At least 5 years of experience in managing CMOs
- Experience in supply chain management of clinical trial material/commercial products highly desirable
- Ability to work independently in a highly focused manner
- Impeccable organizational skills
- Ability to manage multiple projects with competing priorities
- Excellent computer skills (e.g. Excel, Visio, and Project)
10
Global Contract Manufacturing Distribution Planner Resume Examples & Samples
- Ensure accurate ERP signals to Distribution Centers and Contract Manufacturing Buyers
- Coordinate / negotiate supply commit dates that adequately satisfy distribution center requirements / stocking level requirements
- Support the Sales and Operations Planning process by analyzing the site capacities and developing production plans through rough cut capacity analysis
- Manage safety stock targets / inventory levels that meet company goals related to service and inventory levels
- Maintain and monitor customer program/consignment inventory as they relate to established MIN / MAX values and performance targets
- Facilitate Off-site program/consignment inventory reconciliation with Entegris SAP logical on hand quantities to demonstrate audit/process requirements
- Manage product shelf life with consideration to customer requirements and financial Excess & Obsolescence (E&O) targets
- Work closely with logistics operations and customer service including cross-functional teams to resolve planning/scheduling issues and expedites
- Manage Intercompany orders and inventory transactions (consignment receipts) while meeting SOX compliance
- Maintain item attributes, sourcing rules and transfer price in SAP
- Interface between Contract Manufacturers, Buyers, Regional planners, Customer Service and Sales team
- Bachelor’s Degree requested
- Experience in Supply Chain Planning
- Proven expertise and performance in a global supply chain distribution role (processes & systems)
- SAP and Advanced Excel skills a plus
- Effective people skills (Communicate, Influence and champion change)
- APICS certification a strong plus
11
Manager Contract Manufacturing Resume Examples & Samples
- Monitor clinical/commercial production efforts at contract manufacturers
- Coordinate production logistics, control documentation and metrics
- With the Process Development, Regulatory Affairs and Quality departments, lead technology transfer and the final stages of process development. Optimize the inclusion and contributions from the Contract Manufacturing Staff, Process Development, Quality and Contractor staffs
- Troubleshoot equipment and process failures. Follow-up on variance reports generated during production efforts
- Communicate with members of the manufacturing group, and with other departments, as needed to optimize the production schedule
- Write and review regulatory documentation as assigned
- Contribute to the selection contract manufacturers for audit; initiate and implement necessary control systems within budget and to reduce cost of goods
- With the Corporate Compliance and Quality departments, ensure that the physical contract facility is compliant with cGMPs
- Manage contract and confidentiality agreements with the contract manufacturers, ensuring consistency between sites
- Customarily and regularly exercises discretion and independent judgment in the
- Working knowledge of manufacturing processes
- Working knowledge of aseptic manufacturing
- Experience with medical device and/or combination product manufacturing desired
- Working knowledge of desktop computers
- Highly developed organizational and leadership skills
- Process development or technology transfer experience preferred
12
Head of Contract Manufacturing CoE Resume Examples & Samples
- Partners with Head of the Small Molecule Operating Unit to create alignment across Tech Ops around a proven set of outsourcing best practices through the creation and maintenance of a CoE and a community of practice for Tech Ops covering the Small Molecule, Plasma Products and Biologics Operating Units, Packaging and PD (20%)
- Drives the deployment of the outsourcing model across Tech Ops with as much standardization as serves the effectiveness and efficiency of Tech Ops (20%)
- Supports the deployment of the model to CDMO, CMO, CRO, and Contract Laboratory Partners (20%)
- Develops and Deploys a Governance Process for Outsourced Relationships that is both standardized in philosophy and fit for purpose in magnitude relative to the size and importance of the relationship (20%)
- Ownership of the Continuous Development and Improvement of the Best Practices in Outsourcing to maintain outsourcing as a sustainable competitive advantage for Shire. Builds B2B partnerships / relationships and ensures quality, cost, service performance and supply availability in assigned product categories. (10%)
- Leads and coaches teams (mentoring Supplier Relationships and Manufacturing Leads) (10%)
13
Manager, Contract Manufacturing Resume Examples & Samples
- Execute with the CMO the production plan to deliver an uninterrupted supply of clinical & commercial product
- Identify any supply constraints and negotiate/resolve with the CMO any issues to meet the supply plan
- Attend at CMO to monitor production campaigns and develop an in depth knowledge of the manufacturing process and systems at the CMO
- Manage ERP aspects for production efforts at CMO & Monitor and manage inventory levels of drug substance at CMO site
- Develop and manage a visual metric/dashboard to provide an oversight of the production plan
- Coordinate activities in the evaluation of process changes, change requests and deviations to ensure timely resolution without impacting on supply
- Act as the focus and conduit for communications between the CMO and with members of manufacturing group and other departments to meet the supply plan
- Lead and/or participate in technology transfers, new product launches, validation activities with the CMO and internal cross functional teams including Process Development, Regulatory Affairs and Quality departments
- Contribute to the development of formal systems and procedures for the selection of CMOs
- Initiate and implement necessary control systems within budget and to reduce cost of goods
- With the Corporate Compliance and Quality departments, ensure that the CMO is compliant with cGMPs
- Manage contracts and negotiations with CMO
- A minimum of 8 years experience in the pharmaceutical industry with a strong production management and/or supplier relationship management experience
- Working knowledge of solid oral dosage manufacturing and packaging processes to enable problem solving and identification of process improvements
- Working knowledge of pharmaceutical regulatory requirements appropriate to level and solid cGMP skills required
- Ability to start up and lead cross functional teams in the resolution of short term issues or sustained performance for longterm goals
- Demonstrated ability to project manage technology transfer and/or new product launches
- Use of Lean Six Sigma tools in continuous improvement projects
- Familiarity with an ERP system and Trackwise documentation systems are desirable
- Excellent organizational, written and verbal communication & negotiation skills
14
Manager, Contract Manufacturing Resume Examples & Samples
- Manage ERP aspects at BioMarin for production efforts at CMO & Monitor and manage inventory levels of drug substance at CMO site
- Coordinate BioMarin activities in the evaluation of process changes, change requests and deviations to ensure timely resolution without impacting on supply
- Act as the focus and conduit for communications between the CMO and with members of BioMarin manufacturing group and other departments to meet the supply plan
- A minimum of 8 - 10 years’ experience in the pharmaceutical industry with a strong production management and/or supplier relationship management experience
- Working knowledge of pharmaceutical regulatory requirements appropriate to level and strong knowledge of the cGMP manufacturing process for aseptic drug product fill operations
- Ability to start up and lead cross functional teams in the resolution of short term issues or sustained performance for long-term goals
15
Contract Manufacturing Team Leader Resume Examples & Samples
- Provide day to day direction and guidance to team members for toll manufacturing activities. Coach and develop staff to meet ongoing and changing business dynamics. Create individual development plans for staff personal growth
- With the Tolling Supervisors manage the toll manufacturing operations including contract negotiation, execution, and maintenance/enforcement. Ensure compliance with applicable internal and external standards (EHS, Responsible Care, Regulatory, Procurement, Legal, Quality, and Cost) and provide timely follow up and closure of action items
- Monitor and control production activities at tollers, managing cost and volume variances and implementing corrective actions as needed
- Manage Process Technology & Contractual Ownership at Tollers, ensuring compliance with internal delegated procurement authorization
- Partner with Business Leadership, Operational Planning and/or Sales & Operational Planning teams to develop and implement strategies and plans to optimize business support
- Coordinate with Supply Chain and other functions to establish production schedules that meet customer needs. Provide oversight of Tolling Supervisor to monitor and control production activities at tollers; manage variances and implement corrective actions as needed
- Provide oversight of the materials management function for raw materials, packaging components, labels, and maintaining SAP bills of material
- Develops strategic tolling plans in conjunction with the Asset Strategy, maintains strategic long term relationships with existing contract manufacturing base and identifies and develops new contract manufacturing options as required to support the long term asset strategy
- Support ongoing continuous improvement initiatives for operational excellence, process efficiency, cost reduction, PLE Process, NCM investigation and closure, lessons learned documentation, etc
- BS/BA Degree
- 10+ years of experience in chemical manufacturing operations, sourcing and contracting, or procurement, including experience with startup of new operations
- Experience leading direct reports
- Experience negotiating complex contract manufacturing arrangements
- Strong computer capabilities (SAP, Excel, Outlook)
- Strong negotiation, critical and strategic thinking skills; Strong technical and interpersonal skills; Effective written and verbal communication skills
- BS within an Engineering or Scientific discipline
- Experience with agricultural formulation processes; including wet and dry milling and extrusion operations
- Experience with packaging operations and equipment (liquid and dry)
16
Contract Manufacturing Manager Resume Examples & Samples
- 3+ years in roles requiring knowledge of cGMP principles, FDA and other regulatory guidelines, and validation principles
- 2+ years of experience working with external parties and/or leading cross-functional teams for clinical and/or commercial products
- 2+ years of project management experience leading multi-functional and multi-location team
17
Director, OEM / Sub-contract Manufacturing Resume Examples & Samples
- A minimum of a Bachelor’s Degree in Engineering or related degree is required. Master’s Degree in Business / Engineering / Science preferred
- A comprehensive record of continuing education in LEAN, Continuous Improvement Methods, and Quality Best Practices
- A minimum of 10 years of experience as a Role Model Leader, including at least 5 years of experience as a senior functional leader in a manufacturing environment. Experience must include proven success in managing products and systems in a cross-functional and cross-cultural environment
- Comprehensive experience with a wide range of electro-mechanical products and manufacturing methods. Must understand the engineering on which products are based, and the manufacturing issues involved in achieving high-quality, low-cost product
- Broad knowledge of multi-functional, multi-site, global organizational processes and financial business methods
- Must have comprehensive working knowledge of ISO and similar standards and be familiar with common practices of Regulatory Agencies
- Ability to drive strategic thinking and continuous improvement in both non-operational and operational areas, including connecting the cross-functional resources to remove waste along the extended value streams
- Perform as a Role Model Leader, acting in compliance with the Thermo Fisher Code of Ethics and the 4-I Values (Integrity, Intensity, Involvement and Innovation)
- Proficiency in spoken and written English (German a strong plus)
- Broad knowledge of multi-functional, multi-site, global organizational processes and financial business methods (SIOP, Customer Care, Strategic Sourcing, etc.)
- Ability to create and present high level commodity presentations to upper management
- Ability to travel 60%, including international
- Excellent critical thinking, project management, analytical, communication, presentation skills
- High-energy self-starter with strong drive for results
- Progressive/dynamic business professional with a consultative and trusted business partner philosophy
- Proven record of partnering with cross-functional management to drive cost and productivity/efficiency improvements
- Strong business, financial and strategic acumen
- Strong interpersonal skills and the ability to connect with and positively influence leadership and all levels of the organization
- Strong process orientation, with the ability to create scalable numerical systems
18
NYX OMA Contract Manufacturing Planner Resume Examples & Samples
- Communicate and maintain all vendor agreements
- Prepare, maintain and issue a shipment schedule to include historical data, current shipment details and forthcoming shipments
- Track and improve vendor performance with identified KPI’s
- Expedite purchase orders by working closely with vendors while identifying and resolving vendor or shipment problems
- Review finance details and obligations in vendor payments
- Strong interpersonal skills, ability to develop relationships and communicate with all levels of management
- Proficient in computer operations, especially Microsoft Office including Outlook, Excel, Word, and PowerPoint
- Minimum Bachelor’s degree from an accredited university
19
Director, Contract Manufacturing Resume Examples & Samples
- Direct contract manufacturing organizations (CMOs) to ensure the supply of starting material manufactured according to ICH Q7A Good Manufacturing Practice Guidance for Active Pharmaceutical Ingredients and EudraLex Volume 4 GMP Part II Basic Requirements for Active Substances used as Starting Material
- Manage service agreement negotiations and collaborations with CMOs
- Author and review US and ROW CMC regulatory submissions, testing protocols, and technical reports relating to radiopharmaceutical drug substance and drug product development
- Author and review standard operating procedures, batch records, and specification documents relating to the manufacture and testing procedures of starting materials, reference standards, and key materials
- Resolve project issues from a technical and timing perspective and provide project management oversight (e.g. hold project review meetings as appropriate) to ensure timely deliverables to meet development program requirements
- Become fully conversant in radiopharmaceutical manufacturing and test procedures
- Ph.D. in chemistry
- Minimum of 10 years’ experience in managing commercial pharmaceutical development and/or manufacturing
- Thorough knowledge of cGMP drug substance/drug product manufacturing and quality control
- Superior written and verbal communication skills
- Excellent computer skills (e.g. Excel, Visio, and Project
20
Associate Director, Contract Manufacturing Resume Examples & Samples
- Manage supplier relationship management with suppliers and contract manufacturing partners. Lead cross-functional teams in the management of contract manufacturers and key material suppliers. Coordinate internal resources with external suppliers to achieve business goals. (25%)
- Oversee initiatives for the Contract Manufacturing Group (e.g. strategic, contractual, technical) Identify areas of supply risk. (10%)
- Project management within the SCO group for critical supply chain operations projects including product launches and major continuous improvement project implementations that cross product or departmental lines. (20%)
- Coordinate ERP system tools and requirements from a business and implementation perspective as they impact supply chain operations. (5%)
- Negotiate contracts with contract manufacturing partners for product supply. Coordinate with legal and other departments as required. (5%)
- Analyze business risk associated with existing supply and recommended supply strategies. Recommend mitigation strategies to management. (5%)
- Perform in-depth, complex analysis to evaluate supply chain initiatives. Evaluate current processes or tools and recommend improvements. Generate business case analysis for supply chain projects. (10%)
- Oversee Sales & Operations Planning process to ensure coordinated efforts among groups participating in the S&OP process. Manage production planning and scheduling as required. (15%)
- Organize & execute regular, face-to-face business reviews with contract manufacturing partners. (5%)
21
Contract Manufacturing Manager Resume Examples & Samples
- Drive strategies to achieve year over year material cost reduction (PPV/MPV), material quality/delivery improvements and inventory reduction goals through the use of appropriate supply chain tools
- Supplier Development - Work with Engineering and Quality to develop new suppliers with systems to support quick development, new product development, best cost, and high Quality
- Negotiations - Act as the lead negotiator with assigned suppliers to deliver stated objectives
- Conduct Monthly / Quarterly Business Reviews with Supplier and 3D Systems Senior management
- Strategic Sourcing - Lead the strategic sourcing process including RFQ development, quotation reviews, supplier/contract negotiations and supplier development. Lead sourcing meetings with Engineering, Quality, Manufacturing etc. to reach consensus on sourcing
- VA/VE - Work closely with long term suppliers to manage this core supply base for productivity/cost down initiatives through the use of VA/VE tools
- Actively participate in Make vs. Buy decisions
- Own the supplier relationship for the major suppliers in the areas (contract manufacturers) of responsibility
- Maintain a working knowledge of the world-class supply chain process to ensure that existing processes are targeted to attain excellence versus industry benchmarks
- Model and promote 3D Systems Leadership standards to create an environment that mobilizes empowered people to achieve business goals
- Minimum of 7 years relevant work experience in global manufacturing companies with increasing responsibilities in a multi-site, multi-product, company
- International experience required
22
Production Lead, Contract Manufacturing Resume Examples & Samples
- Primary contact and relationship manager to specified Contract Manufacturing Organization(s) for a single product or for the entire relationship depending on the size and tier of the supplier. This includes managing site performance to BIIB expectations with specific KPIs, ensuring on time in full delivery of all products and projects. It is also expected to assist in implementing the External Manufacturing SRM concept at any site that is managed
- This position is a member of matrix teams, in some cases may lead matrix teams, to drive projects both internally and externally as it relates to the relevant API, DP, and FG operations. These projects can include activities like Technology Transfers, process optimizations, validation activities, packaging changes, and the associated change management and project management
- Monitoring and evaluation of CMO key deliveries and performance. Follow up on KPI’s (key Performance Indicators) and ensures the CMO (s) constantly meets standards and expectations for contract obligations, compliance, quality, and production performance and that performance is documented. Responsibilities include monitoring and follow up on Deviations, CAPA’s and Change Requests
- Responsible for aligning with the internal planning teams to ensure production schedules are maintained with the relevant CMO or supplier
- LI-EU3
- Minimum 5 - 7 years of experience in biotech/pharmaceutical cGMP manufacturing industry with supplier relationship experience
- Experience with both biologics and solids manufacturing including a mix of parenteral filling, API and solids manufacturing and, finished goods production
- Demonstrated project leadership skills and ability to develop effective working relationships with internal/external partners and cross-functional project teams
- Excellent communication skills both verbal and written. Ability to communicate at different levels of the organization
- Fluency in English is a must, any other European language is a plus
23
VP, Contract Manufacturing Resume Examples & Samples
- Develop and implement strategies to optimize the existing HCG co-packer network
- Develop/maintain database containing key information for all Co-Packers-including terms, conditions, sku's, & pricing (broken down into key components)
- Develop partnerships with co-pack suppliers to reduce cost and improve quality
- Strive to ensure lowest delivered cost whether turn-key vs. tolling arrangements
- Maintains (shared with production planners) for appropriate inventory levels (raw, package, and finished good), and satisfactory service levels
- Serve as a liaison in resolving issues between HCG Production Planning staff and Co-Packer
- Project management of initial production setup of both new co-packers and new products
- Negotiate/enforce contracts, determine pricing systems, analyze sourcing alternatives
- Support marketing and R&D with sourcing new and alternate production facilities for both new and existing products
- Develop and review standard cost of goods with Finance and Marketing
- Knowledge of financial budgeting processes with cost control and expense management acumen. Prepare annual budgets for assigned co-manufacturing facilities
- Assists with other projects, as needed
- 4 / 6 Contract Manufacturing Directors
- Engineering, Operations Management, Strategic Sourcing or other technical degree is required, MBA preferred
- Operations experience in a food / beverage or Consumer Products Manufacturing background
- Prepare and analyze standard cost of goods
- Ability to understand/relate to all other functional areas within company (R&D, Sales, Marketing, & Finance)
- Strong strategic planning and tactical decision making skills
- Excellent organizational skills, ability to prioritize tasks and meet constant deadline with strong attention to detail and quality control
- Strong interpersonal skills and ability to communicate (verbal/writing) effectively
- Self-motivated and strong analytical / problem solving skills
- Ability to collaborate at all levels of the organization and across other functional areas
- Preferred knowledge of the Consumer Product Goods Industry
- Work with minimal supervision execute for results in a fast paced environment.EEO/AA/M/F/Veteran/Disabled
24
Contract Manufacturing Manager Resume Examples & Samples
- BS in Engineering, Pharmaceutical Sciences or other technical or business field
- 5+ years in a similar position within the pharmaceutical industry
- Strong understanding of regulatory requirements for FDA-CVM, EPA, AAFCO, and NASC
- Knowledge of project management fundamentals and demonstrated experience in successful project exectuion
- Must be able to travel 50-75%
25
Contract Manufacturing Technician Resume Examples & Samples
- Maintain a running status for each contract manufacturing Order from the time it is issued until it is completed and the finished product is in stock and the costs correct on the order. This also means tracking all components required by the order, when they were issued and the quantity shipped as well as what was returned from the vendor
- Oversee the collection and preparation of all required components for each Contract manufacturing Order and where possible ship all components together in a complete contract manufacturing Order package
- For orders sent short (per buyer request), monitor component shortages and ship them to the vendor as soon as they are available
- Monitor status of orders holding for stock outages to coordinate pulling of order when components become available
- Monitor material completed by Production/Batching area needed for contract manufacturing Order shipments. Gather necessary information needed to request CofA’s from QA. Verify product is properly identified and tagged
- Ensure that all required paper work is complete and accurate thus documenting what has been done on each CM Order for traceability
- Double check each CM Order Package being shipped to the vendor for accuracy and completeness
- Ensure that all required system transactions related to CM Orders are performed correctly in a timely manner
- Coordinate with other departments relating to component shortages, product issues, BOM issues and so on
- Ensure that any BOM changes or component quantity changes are updated in Great Plains before issuing any components to the CM Order
- Coordinate CM Order requirements related to material movement and requirements, inventory usage, material lot numbers and system transactions with various departments, i.e., Planning, Production, Purchasing, Inventory, Shipping, Inventory and suppliers/vendors
- Monitor drop ship components and receive them into inventory as so as they are available and issue them to the appropriate CM Order
- Review receiving logs periodically throughout the day for any OS shipments that were received and get them received against the CM Order
- Before receiving any finished goods on an CM Order, review the status of components to ensure that all components have been properly issued in the correct quantities to the CM Order
- If CM Order has been received to within 10% of completion, email the buyer to see if CM order can be closed and remaining product reverse issued back into the system and transferred into vendor bin
- Schedule outside truck for local deliveries that would take more than one delivery in our truck
- Become an expert in using the Inventory / Manufacturing system so that you can effectively help manage the schedule of the CM Orders and the related components
- Work with the warehouse to setup staging locations for CM Orders
- Review emails throughout the day for vendors requesting more quantities or what quantities were sent for a certain order. Research this information and follow up with vendor. These emails come through fairly consistent throughout the day, every day
- Oversee the entry of vendor inventories if the information is provided to the Warehouse Material Coordinator or that we have checked with the vendor for a particular quantity showing in their bin that may be needed for an upcoming order
- Review all partially received CM orders to see if PO’s have been closed. If they have been closed the CM order can be closed once all of the material has been reverse issued. Make decision where remaining product in WIP needs to be transferred to or taken out of the system
- Research items that do not match what the system says to find out possible reason why it is off
- In coordination with Team Manager, implement Lean Principles into processes and services performed for and with CM suppliers and vendors
- Identify and execute activities internally and with CM suppliers and vendors that will result in improved service levels, reduced inventory levels and the reduction in total costs of services and inventory ownership
- Implement Kan Ban programs with CM suppliers and vendors
- Other tasks as required by supervisor
- Typing speed of 30-40 wpm
- Computer database experience
- Microsoft Word and Excel experience
- Strong integrity; capable of upholding policies of confidentiality concerning department, vendor information, and pricing
- Must be detail oriented, be self-motivated, anticipate work to be done, work with minimum supervision, and have strong follow-up skills
- Must have problem-solving capabilities and be able to contribute ideas to department
- Professional manner and dress
26
Contract Manufacturing Planner Resume Examples & Samples
- Ensure vendor’s understanding of NYX demand and planning over 12 month period
- PO placement to respective vendors and maintain PO delivery schedule
- Work closely with operations team to ensure prompt receiving of shipments
- Experience in working with manufacturers and basic understanding of production is a major PLUS
- Knowledge in importing process is a plus
- Highly organized and self-motivated with minimal supervision with ability to multi-task in a fast paced working environment and passion for beauty
27
Contract Manufacturing Senior Coordinator Resume Examples & Samples
- Manage daily relationship with ordering personnel, Distribution Centers, and Contract Mfg locations, and partner with PWL planning team and Logistics teams to resolve supply issues
- Facilitate communication with CoPack suppliers as it relates to planning and execution of business initiatives, and issue resolution
- Initiate and execute day to day supply chain activities for products including order entry and tracking, issue resolution, and inventory reporting
- Partner with Supply Chain Manager and Industry Manager to ensure execution of base line activities and productivity initiatives at producing locations; including execution of all Business Proposals for PWL and Direct to Customer shipments
- Create orders using SAP
- Track and report inventory as required. Other reporting as needed
- Maintain supply chain systems - SAP, Masterfiles, DRP
- Assist Production Planning team with scheduling inventory deployment from manufacturing locations to Distribution Centers
- Experience in SAP is a plus
- Demonstrated Analytical Skills with Intermediate to Advanced proficiency in Excel
- Ability to influence results through collaboration
- Ability to understand and prioritize multiple demands
- Demonstrated ability to effectively work without direct supervision
28
Contract Manufacturing Manager Resume Examples & Samples
- Ensure contract manufacturers comply with Ecolab quality and manufacturing requirements. Work with Quality, R&D, Divisions, and customers to avoid and resolve quality and service issues related to contract manufacturing
- Evaluate product sourcing networks and vendors to ensure best service & quality at a competitive price. Establish annual service and cost targets
- Develop vendor scorecards and manage vendor performance
- Provide basic financial analysis and cost estimates for new product introductions
- Provide management with ideas on how to maximize service performance and minimize inventory investment
- Develop yearly volume budgeting process for respective co-packers
- Establish high-level manufacturing plans for co-packers. Ensure plans are created with respect to internal and external network capacity and in a manner that optimizes divisional cost, service and quality
- Ensure products are available to meet or exceed service, quality and cost objectives. Respond to changing customer and business needs
- Resolve inventory, service and cost issues by working with Plants, Divisions and R&D. Adjust sourcing plans based on Division needs and plant manufacturing capabilities
- Optimize inventory levels and actively drives initiatives to reduce FG and RM DOH inventory. Actively manage and champion At-Risk inventory processes to reach year over year reductions
- 5+ years of work experience within functions of Procurement, Planning, Logistics, Manufacturing and/or Quality
- Previous experience successfully managing relationships with third-party suppliers
- Ability to travel roughly 20%
- No Immigration Sponsorship Available for this Opportunity
- Bachelor’s degree in Chemistry, Chemical Engineering, Logistics, Supply Chain Management or related field
- Advanced Technical degree
- Strong systems background, with experience in SAP, CAS, MRP/MPS, Microsoft Excel and Access
- Strong problem-solving, analytic, conceptual and critical thinking skills
- Demonstrated leadership, communication, analytical, tactical & strategic thinking skills
- Demonstrated ability to manage complexity/ambiguity and multiple initiatives
- Excellent communications skills both verbal and written, including executive level presentations
- Self-starter with detail orientation; persistence and ability to drive execution
- Ability to anticipate change and transition with agility and flexibility while still meeting customer and corporate needs in a fast paced environment
29
Manager, Contract Manufacturing Resume Examples & Samples
- Oversee safety and quality through CM input to ensure best in class performance
- Lead and manage complex North America Contract Manufacturing network across multiple product categories
- Steer daily operations and make key decisions on scheduling, inventory control, customer service, capital planning
- Provide leadership to ensure continuous improvement throughout contract manufacturing network
- Facilitate strategic initiatives while ensuring compliance and supply readiness
- Maintain relationships and drive best-in-class performance metrics to ensure delivery on time, at the right cost and quality
- Lead supplier continuous improvement programs and lean initiatives, including cost savings with tolling, raw materials etc
- Partner with Purchasing to co-create and manage the bidding process for new sourcing opportunities among our supplier network
- Analyze complex sets of cost and manufacturing variables and make recommendations
- Develop and manage budgets for area of responsibility to ensure performance to business objectives
- Negotiate and resolve conflicts that may arise with internal and external partners, including interfaces with global teams
- Voice of Manufacturing and Technical Readiness leader for new product innovation delivery – requiring strong multi-functional collaboration and personal initiative to identify opportunities and achieve business goals
- Education Bachelor’s Degree in a related field or the equivalent education and work experience
- Experience 6 - 9 years related experience - preferably in FMCG within Purchasing or Manufacturing environment
- Special skills Proven team leadership experience in integrated supply chain
- Experience in different functional areas of operations and supply chain management
- Exceptional communication skills, both written and oral
- Proficient in Microsoft tools and data analysis
- Leadership, sound judgment, and solid technical problem solving skills
- Excellent project management skills and decision making skills
- Performance Analysis and Improvement
- Risk & Opportunity Management
- Certifications Six-Sigma, PMP ideal, but not required
- Physical Requirements: 10% travel
30
Manager, Contract Manufacturing Resume Examples & Samples
- Serve as the primary Regeneron technical contact for DP contract manufacturing sites concerning day-to-day activities
- Coordinated all filling activities at contract and/or business partner manufacturing sites, including but not limited to: scheduling of all batches, supplying of requested materials, directing shipment of bulk and finished product at manufacturing sites, tracking of outputs and project step completion times, and providing any required associated reports
- Lead sub-team in continuous process improvements, system implementations and/or strategy development
- Ability to travel up to 50%
- Strong interpersonal, written and oral communication skills
- Experience with documentation and quality systems
- Prior knowledge in Advanced Planning systems is desired
- Provide regulatory filing support (IND, BLA, MAA, etc.)
- Associate Manager requires a minimum of a BA/BS in any physical or Biological Science with 6+ years industry related experience 3+ years of relevant and progressive parenteral manufacturing experience
31
Contract Manufacturing Manager Resume Examples & Samples
- Sourcing Management : You identify and validate potential Contract Manufacturers (new or existing) for a particular product, and you ensure selection of the best option
- Contract Management : You ensure the establishment of Complete Contract Manufacturing Agreements and the timely review of existing contracts
- Strategic Management : You ensure that Operational & Strategic Meetings are conducted with external & internal stakeholders to ensure alignment of Contract Manufacturing with Business strategies
- Quality management: You ensure that all procedures are in line with our quality standards
- Operations & Project Management
32
Contract Manufacturing Assoc Productivity Manager Resume Examples & Samples
- Identify potential projects; develop financial impact, scope of work, performance metrics, cost, and timing for projects that delivers productivity with Frito-Lay's contract manufacturers
- Responsible for preparing funding documents within Frito-Lay as well as negotiating contracts governing equipment ownership, exclusivity, performance, and liability with the associated contract manufacturing company
- Work experience in a high speed manufacturing environment, preferably consumer packaged goods
- Strong project management and team leadership skills
- Excellent communication and presentation skills
- Demonstrated ability to manage multiple priorities
- Productivity Process Experience (Starfleet, Six Sigma, Lean Mfg., Continuous Improvement, etc.)
- Demonstrated Change Management skills
- Demonstrated computer proficiency: Microsoft Suite
33
Manager, Contract Manufacturing Resume Examples & Samples
- Responsible for developing external manufacturing solutions to meet Campbell innovation and new business initiatives. This includes developing a broad understanding of manufacturing capabilities, identifying potential partners, and partnering with cross function teams (quality, finance, R&D, marketing) to develop comparative analysis to determine best fit solutions
- Partner with innovation teams to understand innovation project funnel and objectives. Proactively explore and develop network of potential partners
- Translate innovation and new business projects into manufacturing strategies. Collaborating with the broader Contract Manufacturing organization to develop strategic and existing partners
- Working closely with Campbell legal team, negotiate legal contracts and agreements, including supply agreements, product development agreements, and non-disclosures
- Utilize strategic sourcing techniques and negotiation skills to insure best costs, including RFP’s, competitive bidding, cost models, spend analytics etc
- Manage 1 – 3 Contract Manufacturing Managers
34
Senior Director Contract Manufacturing Resume Examples & Samples
- Relationship development with Division, Business unit and Site Operations Leadership
- Works closely with suppliers, Division Operations, Category and Procurement Managers to identify opportunities, analyze data, recommend go/no-go, create a project plan and lead implementation
- Develop tools, processes and teams required to create and execute project funnel and coordinate support with the PMO
- Drive productivity and ensure goals are met or exceed Company requirements
- Coordinate with Technical Sourcing team to align with Business and Category Management
- Manages daily procurement, planning supply/demand/distribution, and first level problem resolution
- Bachelor's degree in Engineering or a Supply Chain discipline is preferred
- 7+ years sourcing experience required
- 7+ years OEM or contract manufacturing experience required
- 5+ years Supply Chain practical experience is preferred
- Experience with taking component build and developing sub-assemblies required
- Demonstrated strong project management skills
- PPI or similar experience required
- Extensive experience with Make/Buy analysis, tools and application
- Demonstrated experience leading and managing teams
- Strong written and oral communication skills
- Ability to influence without authority
- General knowledge of basic Project Management Tools – project plans, timelines, risk assessments, etc
35
Associate Director, Contract Manufacturing Resume Examples & Samples
- Education: Bachelor Degree in relevant field, ideally supply chain management or engineering, or equivalent experience preferred
- Experience: 10+ years' relevant work experience preferred. 5+ years' experience in contract manufacturing or related field required. This position requires that candidates have food manufacturing experience
- Computer Skills: Proficient with MS Office. SAP experience preferred
- Communications Skills: Excellent communicator, politically persuasive and demonstrates skills in collaboration
- Travel: Job requires a minimum of 25% travel
- Supervisory Skills: Demonstrates leadership experience in one or more of the following areas: Procurement, supply chain, operations, engineering, finance or R&D
- Special skills: CPG experience in finance analysis with significant cross function project management, ability to thrive in a fast paced environment & communicate at a high level across function and must be a quick study, proven ability to manage change, ability to work in a matrix environment and strong decision maker
36
Category Manager, Contract Manufacturing Resume Examples & Samples
- 7+ years of exp in strategic sourcing
- Supply chain management experience
- Exp in executing category/commodity strategies
- Master's in Business Administration (MBA) is preferred
- Six Sigma Green Belt & preferred
- Certification from the Institute of Supply Management (C.P.M., C.P.S.M.) preferred
- Ability to manage multiple projects
37
Director, External Contract Manufacturing Resume Examples & Samples
- Participate in searching for ECM suppliers and developing manufacturing agreements
- Participate in meetings with internal and external customers as needed to support the business relationships
- Support a culture of Continuous Improvement and Innovation
- Facilitate an environment of cooperation and collaboration between the various departments in DFA to support ECM
- Participate in the development of ECM strategy
- Participate in development of Operating and Capital Budgets as required
- Facilitate communication between various departments within DFA to support ECM
- Interact and communicate effectively with all employees, DFA business partners, and customers at various levels
- Provide leadership for the Manager of ECM
- Complete special assignments as required by the VPGM
38
Contract Manufacturing Resume Examples & Samples
- Manage the commercial terms and business relationships with select Contract Manufacturers
- Engage suppliers on pricing and supply related issues for new product quotes, volume transfers and/or cost savings projects
- Support new project initiatives from the business - attend team functions and provide input, engage suppliers to help team understand potential costs and design/cost implication, engage larger Supply Chain functions when necessary, execute startups
- Cost savings initiatives - generate new ideas and execute on those ideas to deliver cost reductions around 1 to 2% of spend under management
- Manage intermittent supply issues and support planning organization to ensure supplier performance and compliance
- Oversee regular supplier audits and measure supplier performance
- Develop appropriate communications to advise business of supplier performance and supply issues
- Bachelor degree
- Minimum of 3 years of work experience in Supply Chain, engineering, sourcing or purchasing
- Degree in Engineering, business, or other applicable technical field of study is preferred
- Strong manufacturing experience, ideally within the industry
- Candidate must have a strong understanding of the manufacturing environment and cleaning product chemistries
- Must have strong business and analytical skills with specific knowledge of small to medium size business operations
- Must have strong negotiations and sourcing skills
- Must have knowledge of small to medium size business operations
- Certified Purchasing Manager a plus
- MBA a plus
39
Regional Category Manager Contract Manufacturing Resume Examples & Samples
- Manage a complex portfolio of CMOs in the region across multiple technologies and modalities. Partner with stakeholders & associated functions to drive consolidation initiatives aimed at simplifying the supply-base and developing preferred suppliers
- Collate supplier, market, category and internal business data and information for the region, and provide regional input and validation to the global Category Strategy, including facilitating involvement of relevant stakeholders. Using this as a basis, develop regional-specific category strategies and communicate and distribute to relevant stakeholders in the procurement and business community. Strategies developed will be scalable and aligned appropriately across Takeda Operating Companies and functions
- Provide regional category input to inform the top-down target setting process and take responsibility for the delivery of regional savings targets following engagement in the target setting process
- Develop a pipeline of regional category initiatives and opportunities
- Ensure a robust approach to Suppler Relationship Management (SRM) & Supplier Performance and Innovation (SP&I), supported by members of the CSPI team
- Degree level educated
- 5+ years in-depth strategic and operational procurement experience with a solid working knowledge of category management
- 5+ years overall business experience, including working within a regulated industry
- Capable of managing cross functional project teams to generate material value across multiple categories
- Direct experience in managing category management projects and development of sourcing strategies
- Proven Financial and Business Acumen (e.g. TCO, Cost Modeling NPV)
- Proven capability in negotiation, conflict resolution and stakeholder management
- Ability to deal with ambiguity and complexity
- Change management and process improvement skills
- Strategic thinker with solid facilitation ability supported by excellent interpersonal competencies (communication, leadership, influencing)
- Ability to manage effectively in a global, fluid, interactive, matrix environment
- Expert proficiency in basic MS Office© software and other business systems (Ariba, Emptoris Mpower, SAP etc.)
- Big Pharma, FMCG or F&B experience
- Analytical experience in positions of increasing analytical complexity, autonomy and responsibility. Demonstrated ability in organizing, analyzing and reporting complex financial data with solid grounding in basic procurement and financial processes and systems
- International strategic sourcing / category management experience
- LI-RL1-EUR
40
Global Contract Manufacturing Leader Resume Examples & Samples
- This person is responsible for managing the Global Contract Manufacturing process and costs for all Momentive Contract Manufacturers. Momentive works today with approximately 100 Contract Manufacturers, which represents a “spend” of approximately $50 MM
- Ensure that appropriate contracts are established
- Work closely with Operations and Business Unit Resources to identify and secure new Contract Manufacturers to drive growth and surety of supply
- Work closely with team and directly with Contract Manufacturers to expand capacity/capability where needed
- Improve productivity performance by identifying opportunities to bring production in-house and/or to identify acquisition targets
- Evaluate Contract Manufacturing production productivity opportunities at their locations
- Conduct EHS, Quality and Business Strength audits for all key Contract Manufacturers
- Develop a multi-year strategic plan that addresses growth and productivity needs for the Buiness Units
- Ensure Legal and EHS Compliance
41
Buyer, Contract Manufacturing Procurement Resume Examples & Samples
- Create a partnership with Marketing/PD and suppliers
- Work with suppliers to create the partnership that helps to bring new innovation to Shiseido
- Work on new innovations (end to end) in their category to make sure we are paying the lowest possible cost, and it meets the timeline
- Create and execute strategies for their brand
- Work with NPD group to make sure new launches time line, competitive cost vs. benchmark and delivery as per the calendar are met
- Participate in weekly launch meeting and provide project update as needed
- Participate in supplier business reviews and lead future strategies with suppliers x brand
- With direction from the Procurement Managers, manage Item Master Setup process for Price Entries in JDE/Mapics Systems
- Responsible for New Vendor Information & System Setup, Contract Price List Management and System Validation
- Develop annual budget, cost savings, cash glide paths and action plans to deliver the corporate objectives for continuous improvement in cost and cash
- Participate in defining aligned and documenting processes that support the Procurement best practices
- Adhere to KPI’s to measure and improve the effectiveness of the key elements of the procurement organization
- Work with internal and external stakeholders to develop and use harmonize processes and tools
- 4 year academic degree, MBA a plus
- Prefer procurement certificates
- Minimum of 2-5 years’ experience operating in contract manufacturing procurement role, including experience working within a procurement tool (SAP, Ariba, JDE etc) environment at an advanced level
- Competent user of computerized IT systems – Word, PowerPoint, Excel and other associated scheduling, forecasting software packages
- Beauty Industry Background a must
- End to End Supply Chain Functions and Linkage
- Understanding of payment terms, total cost of ownership etc
- Understanding of financial health and social audit requirements to assess suppliers
- Thorough working knowledge of procurement management
- Understanding of Supplier Management concepts
- Working in fast pace Team environment
- Achieves results
- Customer and consumer focus
- Attention to detail while being able to see the “big picture”
- Ability to lead others through example, setting standards for performance, and creating accountability
42
Contract Manufacturing Category Leader Resume Examples & Samples
- Structure and recommend make-or-buy options in the manufacturing area, build business cases and raise risks & opportunities
- Core sourcing responsibilities: manufacturing services vendor selection, contract management, vendor performance evaluation and monitoring
- Share and align with Global Direct Souring Directors on new contract manufacturing programs
- Own the contract manufacturing vendor steering
- Opportunity to work in highly innovative environment focused on values such as Integrity, Excellence, Team Work and Accountability
- Direct influence and impact on enterprise contract manufacturing strategy
- Participation in shaping future of high-tech mobility solutions
43
Contract Manufacturing Manager Resume Examples & Samples
- As a Manager, assist the Director to develop and drive comprehensive strategy for the assigned food platforms and associated Coman locations
- Develop and maintain annual COP (cost of production) Budget for assigned locations
- Support assigned innovation from signed PDR1 stage through start up and into ongoing production
- Drive Operational Performance to ensure delivery of service, cost, quality and CI
- As the Relationship Manager, this role serves as the single point of contact to develop the relationship and is the escalation point for issue resolution
- Perform periodic Risk Assessment of assigned platforms and associated locations
- Ensure work streams follow standardized best practices and comply with legal and internal audit expectations
- Where assigned platform/locations are considered part of a larger global platform, provide visibility, support, and assist in development/implementation of the Global Strategy as it exists within your region
- Apply SRM system to assigned locations twice per year
- Where appropriate support Kellogg Supplier Diversity Goals for both tier I & II spend
- Master Degree or Bachelor’s Degree (i.e. Business, Engineering, Food Science, Manufacturing, or Supply Chain) plus significant experience in Supply Chain or related areas
- Requires strong leadership, planning skills
- Demonstrated strong communications with some negotiation skills are required
- Must have a developing track record and ability to work with all levels of management within Kellogg’s and with external manufacturing companies
44
Contract Manufacturing Computer Technician st Shift Resume Examples & Samples
- High School Diploma required. 2 years of college or technical school preferred
- A+ Certification required. Network + certification preferred or equivalent experience
- Strong math and problem solving skills
- Excellent communication skills. Bilingual in Creole, Hindi, or Spanish preferred
- Highly motivated, goal oriented and able to work independently as well as part of a team
- Prior manufacturing environment experience preferred
- Experience using MS Office 2010 in a professional environment
- Experience working with MS Visual Studio strongly preferred
- Experience working with database environments (MS Access, SQL or MySQL) preferred
45
European Technical Contract Manufacturing Specialist Resume Examples & Samples
- Bachelor's degree in business administration, engineering, or supply chain
- Minimum of 10 years manufacturing / supply chain experience as well as previous outsourcing and Contract Manufacturing experience
- Proven ability to work independently, with excellent negotiation, technical problem solving, decision making, communication and project management skills
- Skilled in the implementation of functional excellence strategies and tactics in a global, cross-cultural environment, as well as the ability to grasp the concepts of PSM and SET/ET to drive a regional understanding
- Knowledge of supplier evaluation and selection criteria and current state of the art Contract Manufacturing practices as well as understanding of contractual and legal issues and proprietary/confidential information requirements
- Strong technical problem solving skills and able to read and understand technical drawings and specifications
- Willing to undertake 15-20% travel
- Fluent German and English