Supervisor Production Resume Samples
4.6
(121 votes) for
Supervisor Production Resume Samples
The Guide To Resume Tailoring
Guide the recruiter to the conclusion that you are the best candidate for the supervisor production job. It’s actually very simple. Tailor your resume by picking relevant responsibilities from the examples below and then add your accomplishments. This way, you can position yourself in the best way to get hired.
Craft your perfect resume by picking job responsibilities written by professional recruiters
Pick from the thousands of curated job responsibilities used by the leading companies
Tailor your resume & cover letter with wording that best fits for each job you apply
Resume Builder
Create a Resume in Minutes with Professional Resume Templates
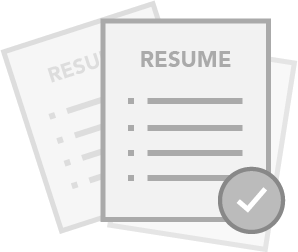
CHOOSE THE BEST TEMPLATE
- Choose from 15 Leading Templates. No need to think about design details.
USE PRE-WRITTEN BULLET POINTS
- Select from thousands of pre-written bullet points.
SAVE YOUR DOCUMENTS IN PDF FILES
- Instantly download in PDF format or share a custom link.
JH
J Heaney
Johnathon
Heaney
65774 Demarco Curve
San Francisco
CA
+1 (555) 221 4460
65774 Demarco Curve
San Francisco
CA
Phone
p
+1 (555) 221 4460
Experience
Experience
New York, NY
Supervisor Production
New York, NY
Murray-Raynor
New York, NY
Supervisor Production
- Responsible for providing performance feedback through the Performance Excellence system and growth/development planning
- Analyze and resolve work problems, or assist workers in solving work problems
- Will be facilitator to staff with regards to performance, quality, inventory management, process improvements and daily communications
- Provide continual leadership and guidance to team members for the purpose of increasing their effectiveness and establishing good working relationships
- Manage employee performance, providing positive and/or corrective feedback
- Manage production process and employee performance, providing positive and/or corrective feedback
- Technical Knowledge: Develop and continually improve technical knowledge of processes in order to continually improve and problem solve
Boston, MA
Supervisor, Production
Boston, MA
Grady Group
Boston, MA
Supervisor, Production
- Works with employees to maintain a safe work environment. Leads and supports subordinates to work in a safe manner and to seek improvements in work practices
- Identifies process problems and suggests process improvements and assists team with the development of improvements
- Develop direct reports by providing challenging tasks and assignments; provide developmental feedback
- Develop direct reports by effectively using the PMD (Performance Management Discussion) process and offer clear and constructive feedback
- Build and develop a disciplined workforce that adheres to all procedures and Work Instruction Documents
- Assist with development, evaluation and improvement of manufacturing/fabrication methodologies and techniques
- Prepares/delivers performance evaluations. Recommends compensation adjustments and promotion candidates to manager
present
Philadelphia, PA
Senior Supervisor, Production
Philadelphia, PA
O'Connell-Gibson
present
Philadelphia, PA
Senior Supervisor, Production
present
- Monitor workflow and control output through work order distribution
- Leads Root Cause Problem Solving (RCPS) sessions to drive continuous performance improvement
- Implements ownership culture and management routines to improve compliance, equipment efficiency and personnel efficiency
- Monitor work being produced to make sure it meets all specifications
- Schedule and manage resources, track and report results, troubleshoot issues, train employees, and implement process improvements
- Develops a plan, with staff, to achieve goals and tracks progress-to-plan using performance metrics
- Provides one-to-one feedback to area leads and direct reports regarding team/individual performance
Education
Education
Bachelor’s Degree in Physical
Bachelor’s Degree in Physical
Kean University
Bachelor’s Degree in Physical
Skills
Skills
- Proficient knowledge and use of Microsoft office programs
- Ability to make decisions quickly that are rational, logical, and fact driven
- Proficient knowledge of Microsoft Office applications (Outlook, Word, Excel, PowerPoint)
- Technical Knowledge: Develop and continually improve technical knowledge of processes in order to continually improve and problem solve
- Proficient knowledge of production processes, general line maintenance and staffing
- Ability to pay attention to the minute details of a project or task
- Proficient English language knowledge and skills (oral and written)
- High work capacity, dependable, results oriented and strong sense of urgency
- Maintain a strong working knowledge of the products manufactured, the tools utilized, & other assets in their departments
- Strong MS Office skills
15 Supervisor Production resume templates
Read our complete resume writing guides
1
Supervisor, Production Operations Resume Examples & Samples
- Assess the operation and project for headcount; originate both operating and capital requests and implement innovative training programs
- Make any recommendations regarding corrective measures and adjust the personnel and facility schedules to satisfy changing programming demands while maintaining maximum efficiency and flexibility
- Work with crews and staffing through late night shifts, weekends and holidays. The Supervisor is expected to perform a variety of special projects
- May be asked to supervise the recommendation, implementation, installation and integration of new equipment and work flows
- Proficient in business protocol and procurement techniques as well as in-depth research and development in specified areas of expertise
- Past budgetary experience, comprehensive understanding of supervising staffs or operations
2
Supervisor Production Resume Examples & Samples
- Monitor to ensure that all employees comply with safety regulations and the plant's safety program
- Perform other duties as assigned by the Section Manager
- Ability to meet deadlines and be accountable for quality / quantity
- One to three years of industrial supervisory or similar leadership experience preferred
- Able to work a flexible schedule, including weekday and weekend overtime
- Good computer skills, experience with Microsoft Office a must
3
Supervisor Production, Tool & Die Resume Examples & Samples
- Supervision of hourly Tool & Die Specialists. This is a hands-on working supervisor role
- Manpower management: day to day line support; PM and repair tasks; vacation scheduling; OT & weekend work scheduling
- Interaction with Production, Manufacturing Engineering and Design Engineering
- Standards development and creation of procedure and methods as well as maintaining updates as required
- Project management of repair, refurbishment and engineering change implementation projects
- Completion of a Tool & Die apprenticeship or equivalent OJT experience
- 5+ years experience in supervision and leadership
- 5+ years of extensive experience with maintaining and repairing automotive stamping dies, plastic injection molds and/or high pressure die cast molds - aluminum stamping or structural die casting experience is a plus
- Proficient in Microsoft Office suite of programs
- Ability to motivate in high pressure situations
- Ability to develop individualized development plans to improve weaknesses and leverage strengths
- Open minded, highly flexible, positive attitude
- Good overall people management skill
- Great communication skills, both verbal and written
4
Supervisor, Production Resume Examples & Samples
- Monitors the production process to meet customer expectations, quality standards and internal production schedules
- Meets all committed deliverables for internal and external customers
- Works with Operations, Technology and Development support groups to define, document and measure complex non-routine operations
- Assists manager in development of department schedules, reports and milestones according to operating plan
- Creates, fosters and maintains a team atmosphere through coaching team members. Counsels team in development and direction
- Works with internal and external customers to develop rapport with customers and relevant contacts, addressing problems, establishing/modifying schedules, etc
- Proactively resolves problems, taking responsibility and ownership of process through final resolution
- Identifies process problems and suggests process improvements and assists team with the development of improvements
- Monitors quality and production levels of each employee and provides ongoing feedback to employees regarding their performance, ensuring contractual quality standards are maintained
- Prepares/delivers performance evaluations. Recommends compensation adjustments and promotion candidates to manager
- Identifies training needs, recommends courses for candidates to ensure employees receive appropriate training
- Participates in the hiring process. Interviews and hires candidates when appropriate
- Supports and administers all Human Resources policies
- Reviews, updates and ensures that current ISO procedures are being followed in an ISO environment
- Performs other job related duties as required
- Associate’s degree in related field or equivalent experience, Bachelor’s degree preferred
- Three to five years related experience in an Editorial, Electronic Publishing, Production or Call Center environment
- Ability to perform supervisory functions, i.e., schedule work assignments, distribute work throughout department and monitor tasks, provide performance feedback
- Ability to organize and prioritize production schedules
- A high degree of ingenuity and the ability to work well with support departments
- Excellent Customer Service skills
- Ability to organize and manage multiple, complex tasks
- Detail and quality oriented
- Experience with Microsoft Office Suite software
- Ability to work flexible hours or extended hours
5
Supervisor, Production Readiness Lead Resume Examples & Samples
- Effectively communicate, elevate and mitigate risks identified through the PRR process to executive leadership and other key stakeholders
- Present Production Readiness status to external Airframer customers
- Provide industrial planning-structure, framework and timing on sourcing and manufacturing decisions
- Ensure accurate forecast schedules are provided to all internal and external customers for effective industrialization planning
- Drive alignment with the transitions team to ensure transitions are initiated and completed on time to support value stream capacity needs
- Leverage outsourced resources to increase the capacity of the assessment team
- Progress standard work of team to ensure efficiency within organization
- Allocate team resources to ensure team priorities are met
- Manage salary employees needs including expense reports, travel approvals, mentoring and PFTs
6
Supervisor, Production Maintenance Still Resume Examples & Samples
- Responsible for overseeing the day-to-day mechanical and electrical repairs and preventative maintenance on all production equipment/machinery
- Responsible for overseeing the day-to-day preventative maintenance and repairs in maintaining PLC based control systems
- Maintain contact with maintenance techs in order to ensure quality precision work and report progress
- Maintain compliance with all company policy and procedure guidelines
- Utilize proper waste disposal procedures
- Support and assist with expertise in electrical equipment
- Provide technical assessment of equipment to determine what components should be repaired or replaced to maximize equipment performance
- Develop and/or maintain an effective preventive maintenance program (including repair, modification and installation of equipment) in order to improve production efficiency, ensure optimum machine time availability and ensure compliance with food safety requirements
- Inspect facility (e.g., production, warehouse, service/installation) to assure adherence to safety and operating policies and Good Manufacturing Practices (GMP) using Company policies and procedures
- Maintain the plant's manufacturing equipment in sanitary condition (e.g., clean and sanitize tanks and pipe routings, maintain conveyor belts, clean according to Company GMP policies and procedures in order to assure the quality of the manufactured product
- Investigate and identify root causes of any facility safety or security incident or environmental regulation non-compliance in order to prevent reoccurrence of similar incident at same or other facilities
- Review plant production equipment environment (e.g., technology, systems, quality, cost, efficiencies, yield) in order to recommend process improvements
- Protect all intellectual property, information and technology surrounding confidential processes and products using established legal safeguards in order to prevent a breach of trademark security within the Company
- 5-10 years previous maintenance experience; 3-5 years in a supervisory capacity
- Ability to read and utilize schematics in equipment repair
- Previous experience with Allen Bradley programmable controllers
- Previous experience in troubleshooting and maintaining PLC and SLC
7
Supervisor, Production Maintenance Still Resume Examples & Samples
- Utilizes data to analyze equipment failure modes, mean time between failure (MTBF), etc. and suggests/implements improvement processes to reduce or eliminate equipment/process failures (I.E.:PM inspection improvements, predictive maintenance techniques, maintenance employee training, etc.)
- Provides meaningful management reports to enhance control of maintenance operations
- Maintains the work backlog within prescribed limits by providing for forested resource requirements
- Creates and adheres to a work order scheduling process
- Continually reduce equipment downtime and increase availability through the establishment of a preventive/predictive maintenance program (including failure analysis) designed, directed, monitored and continually improved
- Keeps the operations managers properly informed on all abnormal or critical situations
- Assesses the skills and abilities of assigned personnel and develops training opportunities to close the skills gap
- Seeks and schedules training courses and/or seminars to close worker skills gaps
- Participates in, and supports, the Department safety training program. (I.E.: weekly safety meetings, shop safety inspections, enforcement of lock-out/tag-out program, enforcement of the confined space program, etc.)
- Conducts accident investigation of all injuries requiring medical attention (or as requested by Plant management)
8
Supervisor Production Operations Resume Examples & Samples
- Supervise personnel, projects and workflow. Develop peak efficiencies in personnel development, facilities and staffing requirements of specific operations areas. Provide administrative support and enforcement of all departmental and company policies and initiatives
- Interface with applicable Programming and/or Production representatives in the advance planning stages to ensure the efficient provision of facilities and personnel to achieve desired results
- Direct and evaluate the performance of all assigned employees including the implementation of departmental and company goals and the resolution of employee conflict situations
- Assist the Management Team in implementing training programs to improve efficiency and competency of the operating staff. In this regard, Supervisors suggest methods of improving the quality of work performed by staff and maintain awareness of industry developments
- Evaluate the staff capabilities and performance, make recommendations to scheduling partners with respect to shift and crew assignments, administer the annual reviews for assigned staff members and develop and administer Standard Operating Procedures
- A minimum of 10 years of production operations or related experience
- Ability to perform tasks under tight deadlines is critical
- Candidates must have good computer background (Outlook, Word, Excel, etc...)
- Ability to work nights, weekends, and holidays
- Flexibility to alter shifts/days off to accommodate projects and departmental objectives
- Has in-depth understanding/background in Production Operations job roles in Studio, PCR, Network Control, and Editing
- Bi-lingual (English/Spanish)
9
Supervisor Production Resume Examples & Samples
- 1st Shift - 5:00 am to 3:00 pm 5 days with every other weekend possible
- Coach team on HON behaviors and metrics
- Encourage/provide development opportunities
- Provide supervision in scheduling, ensuring effective selection, retention, feedback, disciplinary action and performance management
- Coordinate with Leads to ensure proper orientation, assimilation and training of new team members
- Implement policies and procedures as they relate to employees
- Must have working knowledge of job functions within accountability
- Ensures all HSE and HOS systems are continuously sustained and improved, such as
- 5S Tiered Accountability Meetings
- Leadership Standardized Work TPM
- Ensure safety policies and procedures are being adhered to
- Bachelor's degree in Engineering preferred
- 2 Years of leadership experience in a manufacturing environment
- Maintain customer focus, internal and external
- High level communication skills, written and verbal
- Ability to coach and motivate
- Proficient computer skills, including e-mail, word processing, spreadsheet and presentation software
- Strong presence on production floor continuously driving improvement and Five S
- Steel toed shoes, safety glasses, and other PPE as may be necessary
- Experience working in a functional organizational structure preferable
10
Supervisor Production Maintenance Resume Examples & Samples
- Monitors and/or manages the entry of correct documentation and scheduled maintenance via Maximo/SAP
- Manages reactive/corrective maintenance as it is reported and distributes to available technicians
- Leads safety program for the worksite and maintains reporting associated with safety activities
- Audits work performance for safety actions and quality of work, and provides coaching as needed
- Reviews new job requests to differentiate between in-scope and non-scope work, and addresses accordingly
- Maintains effective performance of individual employees and the worksite team
- Reviews and approves time reporting
- Compiles, maintains and presents various reports to AECOM management and client teams
- Four years of experience in a Lead or Supervisory role
- Bachelor’s Degree or equivalent trade school credentials preferred
- Proficiency in Microsoft Office Suites with emphasis on the ability to navigate and formulate within Excel and Access
- Experience in a supervisory or subcontract management capacity within a technical industrial or manufacturing environment
- Experience in a leadership position demonstrating the ability to analyze Process Maintenance related problems (i.e. Electrical, Mechanical, Machine Tools, Heat Treat, etc.); then recognize and determine solutions (engineered or otherwise) for resolution. This includes but is not limited to; opportunities for improved asset reliability, improved quality results, safer work conditions, and lower maintenance cost, improved work plans to increase efficiency
- Experience creating Power Point presentation and giving presentation in front of large audiences
- Experience with the development and training of a multi-skilled technical workforce
- Experience creating metrics and data mining for driving performance results
- Experience utilizing Continuous Improvement disciplines such as Six Sigma, Kaizen, Lean Manufacturing, 5S, 4 M’s, etc
11
Supervisor, Production Resume Examples & Samples
- Process Management by simplifying complex processes; getting more out of fewer resources; understand how to separate and combine tasks into efficient workflow
- Develop direct reports by providing challenging tasks and assignments; provide developmental feedback
- Direct others through establishing direction; distribute workload; clear communication
- Managing & Measuring work by tracking and assigning responsibilities for tasks; set clear objectives and provide feedback
- Supervise the production process and ensure compliance to all safety, GMP, and other regulatory requirements
- Develop direct reports by effectively using the PMD (Performance Management Discussion) process and offer clear and constructive feedback
- Direct the daily work load to ensure schedule completion while managing utilization and efficiency
- Build and develop a disciplined workforce that adheres to all procedures and Work Instruction Documents
- Improve the production processes by utilizing the tools outline in PPI (Particle Process Improvement)
- Working knowledge, Microsoft Office (Word, PP, Excel)
- Advanced communication skills
- Advanced problem solving
- Ability to mentor, train, motivate and coach
- Analytical capability
- Ability to identify waste and improve processes
- Ability to challenge the status quo
- Ability to delegate
- Previous experience working with internal customers
- Continuous Improvement Certification a plus (i.e. Six Sigma)
- 10% travel time
- 2 year post high school education or applicable industry experience required
- 1 year experience leading a team in a professional work environment
- IND-LSG
12
Supervisor, Production Resume Examples & Samples
- Coordinate daily production activities to meet safety, quality, output and on-time delivery targets and revenue
- Identify material/capacity constraints and resolve issues, including resolving material shortages, prioritizing support functions (receiving, inspection, mfg. engineering, etc.) and escalating issues
- Ensure that safe work practices are in use at all times including teams adherence to Personal Protective Equipment (PPE) requirements of the job function (i.e. safety glasses, ESD protection)
- Manage daily cycle count activities and lead reconciliation efforts
- Maintain accurate material transactions and backflushing
- Ensure production activities are completed in accordance with design and process documentation
- Lead daily production meetings and assist with creating and publishing daily/weekly/monthly metrics
- Assist with 3rd party audits, including ISO 9000
- Lead training and coaching of direct reports
- Complete annual Performance Review’s for direct reports
- Participate and lead improvement events (such as Kaizen, 5S, Practical Process Improvement); coach and mentor direct reports to drive PPI as a way of life
- Work with peer supervisors to consolidate orders and flex resources
- Coordinate, report and manage direct reports paid time off schedules and timecards
13
Supervisor Production Night Shift Resume Examples & Samples
- Direct, supervise and monitor activities of leads and team members to maximize productivity in the plant
- Responsible for safety throughout Lineman Unit. Instill “safety first” mindset within group. Lead HSE initiatives
- Ensure procedures are in place and being followed for production efficiency, quality, safety, and state/federal regulations and guidelines
- Prepare/coordinate production schedules and ensure shifts are adequately staffed. Evaluate production needs for daily assignment of duties, adjustment as required
- Encourage continuous improvement activities and seek opportunities and initiate action for process improvement. Serve as resource for Leads and team members to drive improvement opportunities
- Analyze and resolve work problems, or assist workers in solving work problems. Represents site management during off shifts
- Coach team on HON behaviors and metrics. Encourage/provide development opportunities
- Provide supervision in scheduling, ensuring effective selection, retention, feedback, disciplinary action and performance management. Coordinate with Leads to ensure proper orientation, assimilation and training of new team members
- Maintain time and production records. Implement policies and procedures as they relate to employees
- Shift 6:00 pm to 6:00 am
- Bachelor’s degree and a minimum of 2 years leadership experience in a manufacturing environment; OR HS Diploma and a minimum of 5 years leadership experience in a manufacturing environment
- Experience in advanced manufacturing concepts, (i.e. Lean, Six Sigma, TQM) and ERP systems (AS-400)
- Previous experience working in a functional organization preferable
14
Supervisor, Production Resume Examples & Samples
- Directs staff through subordinate 'lead' employees
- Participates in establishing and modifying operational methods and processes by recommending changes in materials, equipment, and procedures
- Performs advanced production tasks as needed
- Reviews and compiles operations records, such as floor inspection reports and tool, equipment and supply usage, and safety reports
- 5-8 years of related experience in mechanical production, assembly or construction
15
Supervisor, Production Resume Examples & Samples
- Provide technical expertise and recommendations in assessing new IT software projects and initiatives to support and enhance our existing Microsoft based systems
- Identify opportunities that can improve efficiency of business processes
- Investigate and resolve application functionality related issues and provide first level support
- Manage application development for multiple projects
- Assist in application installation and testing
- Troubleshoot technical issues and identify modifications needed in existing applications to meet changing user
- Diploma/Degree in Computer Science or related discipline
- Passion in software development and keen in writing or debugging software codes
- Willing to learn and adopt coding practice to ensure system sustainability
- Have done coding with .Net Framework using C#, would be desirable
- Understand database schemas and design, ability to write queries or stored procedures, preferably with MS SQL
- Experience in developing mobile apps for mobile devices would be advantageous
- Excellent communication skills possess logical and analytical skills with attention to detail
- Fresh grads are welcome to apply
16
Supervisor, Production Resume Examples & Samples
- Oversee production in one or more of the following areas: reagent manufacturing, array, flowcell, manifolds production
- Coordinate with Quality, Engineering, Shipping, and Planning groups to deliver results
- Writing and revising work instructions, and training of technicians on the proper use of these documents
- Responsible for efficient processing of work orders, reviewing batch records, maintaining training records, facilitating efficient shift changeovers, revision of work instructions, production scheduling and reviewing timesheets
- Talent Acquisition activities which include identifying needs of the department, justification for budget to fill positions, coordinating with HR to market the position, review resumes, conduct interviews and identify and recommend a candidate as the potential hire, and employee orientation to the department and company
- Job Role Definition ensures that job descriptions accurately record the primary responsibilities, qualifications and terms for each job role in their group
- At higher levels of management, establishing and distributing budgets among departments is required
- Ensure employees follow all applicable company policies and procedures
17
Supervisor, Production, Injection Molding Resume Examples & Samples
- Effectively carry out production operations and meet production schedules while maintaining product quality across an entire shift
- Must be able to lead / drive change using Lean Manufacturing techniques and TEOA tools and initiatives
- Engage teams creating a Lean culture and demonstrate the effectiveness of sustaining Lean initiatives
- Engage in continual process improvement and cost reduction projects
- Provides career counselling and training plans
- Direct proper maintenance of production equipment and machinery
- Ensures that safety standards are followed and safety remains top priority in all we do
- Minimum of 10 years manufacturing experience
- Minimum 3-5 years prior Supervisory experience
- Prior Injection Molding Experience strongly preferred
- Ability to gain a working knowledge of Lickdale's Quality systems and manufacturing processes preferred
- Ability to communicate effectively - verbally, written, and email
- Strong understanding of Microsoft Office Programs such as Outlook, Excel and Word
18
Supervisor, Production Resume Examples & Samples
- Lead the Client Mail (Insertion/Manual) teams in Secaucus to exceed Broadridge's client expectations and SLAs
- Improve PEQ by working with all internal clients and external vendors; this includes but is not limited to Account Management, Quality Control, Print, Randstad, TMG, Logistics and Technical Support
- Ensure all equipment problems are addressed with the appropriate vendor (i.e. Gunther, Pitney Bowes, and Tech Support)
- Ensure downtime is documented correctly for each instance
- Monitor and address all inventory concerns with Account Management and Procurement as needed
- Ensure all testing is completed effectively with accurate documentation
- Design and implement daily production reports that monitor productivity, quality, unit costs and backlogs
- Provide technical assistance to operators with respect to resolving file problems, troubleshooting issues on the inserters, DFWorks, etc
- Recommend and implement cost containment initiatives to reduce expenses where possible
- Responsible for improving Client Mail equipment utilization by keeping machines running and prioritizing work appropriately
- Ensure that multiple backups are available to support each function with Client Mail Insertion and Manual Distribution
- Work with third-party agencies to recruit temporary workers as needed, develop staff schedules, cross-train and evaluate staff performance
- 2-3 years of experience leading a team in an energized environment, as well as 1-2 years of relevant print/mail, production or manufacturing experience
- Solid knowledge of all Client Mail equipment and USPS regulations
- Strong trouble-shooting skills and ability to work effectively with all partners to resolve problems
- Deep understanding of Microsoft Office (Word, Outlook, and Excel)
- Strong oral and written communication with staff and management at multiple levels
- Solid organizational skills, effective multi-tasking, lead multiple priorities and work under tight deadlines
- Detail-oriented when reviewing jobs before and after they are inserted to confirm quality standards are met
- Associate's or Bachelor's Degree a plus
- This position is the overnight shift and requires work Tuesday-Saturday from 12 am-8 am
- Flexible to work various shifts and overtime, including weekends & holidays, as needed
19
Supervisor Production Resume Examples & Samples
- High School Diploma or G.E.D. required; A.A. degree is preferred
- Must have a minimum two (2) years recent supervisory experience in military production programs, including electro-mechanical assembly experience with demonstrated strong leadership skills
- Must have the ability to enforce company’s rules and regulations effectively and professionally
- Must possess strong people skills and job knowledge with the ability to motivate his or her subordinates
- Must have background and experience with the supervision of personnel assembling and soldering products to the high quality commercial requirements includes ANSI/J-STD-001, IPC-A-610, IPC/WHMA-A-620
- Must be proficient in the reading and interpretation of assembly and wiring drawings
- Must be proficient in the use of personal computers with the ability to use MS Word, Excel, PowerPoint and Outlook
20
Supervisor, Production Resume Examples & Samples
- Direct the Production Leads and Team Members to ensure that day-to-day production needs are met
- Identify resource needs, as well as ensure that the production schedule is met
- Ensure a work environment exists for employees that provides effective communication between all shift team members in order to effectively communicate concerns regarding production
- Set the direction relative to manufacturing goals in order to meet production needs and expectations
- Identify and communicate information to correct Production disciplines relative to product quality and defect prevention, product disposition, as well as rework and/or repair activity
- Communicate and assist in the resolution of part shortages or the expedition of product
- Evaluate, monitor, and react to personnel allocation in the Factory, including the use of overtime in conjunction with production needs
- Monitor and prioritize aging material orders
- Work with the Planners and Manager to load all processes and shifts
- Coordinate and approve overtime and vacation days of Production Leads
- Monitor day-to-day staffing assignments
- Provide coaching, feedback and career growth guidance
- Responsible for understanding and providing input to capacity planning as customer's production demands fluctuates
- Determine and communicate the direction relative to housekeeping and safety practices
- Support of Company goals and metrics
- Additional duties as assigned by management
- Act as a role model to Production personnel and be recognized as a leader within the manufacturing site
21
Supervisor, Production Resume Examples & Samples
- Oversee production in Reagent Packaging
- Assist line personnel in resolving job related problems
- Monitor workflow and control output through work order distribution
- Ensure production goals are met; Communicate progress against these goals on a regular basis
- Coordinate with Planning, Quality, Engineering, Shipping, and Manufacturing groups to deliver results
- Manage the training program for direct reports
- Perform duties of Production Technician when no emergency backup can be identified
22
Supervisor, Production, Reagent Formulation Resume Examples & Samples
- Oversee production in Formulation
- Distribute work assignments effectively to meet schedule
- Assist formulators on process troubleshooting
- Ensure compliance requirements are met
- Schedule and manage resources, track and report results, troubleshoot issues, train employees, and implement process improvements
- Coordinate with Planning, Quality, Engineering, and Manufacturing groups to deliver results
- Train formulators on the proper use of work instructions
- Responsible for reviewing batch records, maintaining training records, facilitating efficient shift changeovers, production scheduling and reviewing timesheets
- Some overtime and may be required
23
Supervisor Production Resume Examples & Samples
- Prepare and lead line start-up and assign production line tasks
- Evaluating performance of employees, make recommendations for improvement, and utilize the corrective action process
- Facilitate team meetings and forums to share information
- Understand, monitor, and insure compliance to Good Manufacturing Practices (GMP) and adherence to defined procedures
- Assign line tasks per productivity guidelines and communicate all quality instructions
24
Associate Supervisor, Production Operations Resume Examples & Samples
- Expertise in the operation of various media applications, including but not limited to: server based record/playback devices and related software apps., etc
- Expertise and highest standard of Master Control functions, (e.g. setting up, controlling and monitoring TV Production equipment to transmit live and taped programming, commercials and network branding graphics)
- Comprehensive experience with integrated automation systems including, but not limited to; managing files, troubleshooting error messages and delivering content
- Providing expert levels and highest standard of audio engineering (“A1”) functions, e.g., operating various audio consoles; creating audio equipment and layout specifications for audio systems; “patching” audio effects racks, amplifier racks and mixing consoles; programming/operating intercom systems; QC and adjusting signals from remote venues including audio and telephony
- Providing expert levels and highest standard of Technical Directing functions, e.g. operating video switchers, implementing sources, creating displays, interfacing with external devices, creating user and suite preferences
- Comprehensive experience of TV Production measurement, formats, and language and full oversight of quality control of audio and/or video inputs and signals prior to and on air
- Works closely with Manager –Production Operations in the professional development of Production Operations Technicians; trains and mentors less experienced Technicians in the performance of complex assigned tasks, provides feedback to management
- Follows up on deviation reports to identify and isolate special and/or systemic problems; participates in post-production evaluations and recommends corrective actions
- Leads special projects and/or operations teams in complex productions
- Coordinates personnel conducting assigned tasks for ESPN’s networks or operations groups
- Coordinates and implements changes and improvements to policies and standard operating procedures; regularly suggests modifications to equipment and related technologies
- Recommend the implementation, installation and integration of technical systems, equipment and work flow. Communication priority is to execute all requirements around staff deployment and integration
- Leads or participates in the development of Production Operations standard operating procedures (SOPs) or assigned productions and for the implementation of new Operations equipment and/or workflows
- Knowledge in business protocol and procurement techniques as well as in-depth research and development in specified areas of expertise
- Has in-depth production operations skills related to studio, editing, master control and/or production control rooms
- A minimum of 8 years of production operations or related experience
- Advanced proficiency in specific aspects of Production Operations, including, but not limited to: work flow, SOPs, systems, support and the business requirements
- Master Control functions, (e.g. setting up, controlling and monitoring TV Production equipment to transmit live and taped programming, commercials and network branding graphics)
- Audio engineering (“A1”) functions, e.g., operating various audio consoles; creating audio equipment and layout specifications for audio systems; “patching” audio effects racks, amplifier racks and mixing consoles; programming/operating intercom systems; QC and adjusting signals from remote venues including audio and telephony
- Technical Directing functions, e.g. operating video switchers, implementing sources, creating displays, interfacing with external devices, creating user and suite preferences
- Candidates must have solid computer background (Outlook, Word, Excel, etc...) and excellent communication skills
25
Supervisor, Production Resume Examples & Samples
- Performs production duties in area/line
- Implements and maintains lean, zero loss, and ownership culture to improve equipment and personnel efficiency
- Develops and maintains shift and department metrics, i.e. performance boards
- Creates, implements and executes a quarterly plan for area/line
- Assists with quality investigations and CAPAs (Corrective and Preventative Actions)
- Performs reviews and approvals of completed batch records
- Creates, revises, reviews and approves Standard Operating Procedures (SOPs)
- Completes all training requirements and maintains 100% team compliance with all assignments
- Provides routine One-on-One feedback with direct reports
- Responsible for coaching and developing reports
- Responsible for assisting with shop floor schedule planning and adherence
- Performs additional related duties as assigned
- Prefer associates or technical degree
- Prefer previous experience in a leadership role
- Motivate and lead others
- Self-directed with ability to organize and prioritize work
- Communicate effectively with written and oral communication skills
26
Supervisor Production Resume Examples & Samples
- Provides guidance, leadership and motivation to ensure productivity goals are achieved; develops and implements training programs to meet current and future quality and productivity goals. Promotes a teamwork environment and builds positive employee relations. Promotes pro company atmosphere
- Resolves production issues relating to quality concerns in assigned areas; reviews quality check logs, final line/PDI, water leak and VES-E sheets to identify and provide countermeasures to quality issues and concerns within assigned areas
- Develops and adjusts manpower and equipment requirements and job layouts due to changes in line speed and production requirements; maintains and updates all documentation such as standard operation sheets and process sheets and employee training records
- Investigates all safety and ergonomic issues that occur in assigned areas; verifies implementation of all countermeasures. Ensures and maintains ISO9000 and ISO14000 compliance for assigned areas. Ensures assembly line efficiency and neatness, and minimizes downtime
- Controls operating supply usage for assigned areas to maintain adherence to budget; ensures targets to reduce scrap costs are met; maintains scrap budget within cost per unit
- Communicates with coordinating Supervisors to exchange information relating to production, quality, and safety issues and concerns; facilitates problem resolution
- As necessary, performs other related duties of which the above are representative
- Job Knowledge and Skill: Excellent communication, interpersonal and motivational skills. Basic understanding of automotive vehicle assembly and function. Knowledge of ISO9000 international manufacturing quality standards and ISO14001 environmental standards
- Experience: Three to five years of directly related professional experience
- Supervisory Experience: Two or more years in a work leader role coordinating the work of other employees or contractors
- Education: Bachelor’s degree OR a high school diploma/G.E.D and a minimum of eight years of increasingly responsible administrative experience preferred
27
Supervisor Production Resume Examples & Samples
- Manages a workgroup of production technicians; provides guidance, leadership and motivation to ensure productivity goals are achieved; develops and implements training programs to meet current and future quality and productivity goals. Promotes a teamwork environment and builds positive employee relations. Promotes pro company atmosphere
- Resolves production issues relating to quality concerns in assigned zone; reviews quality check logs, final line/PDI, water leak and VES-E sheets to identify and provide countermeasures to quality issues and concerns within assigned zone
- Develops and adjusts manpower and equipment requirements and job layouts due to changes in line speed and production requirements; maintains and updates all documentation such as standard operation sheets and process sheets, ILU charts
- Investigates all safety and ergonomic issues that occur in assigned zone; verifies implementation of all countermeasures. Ensures and maintains ISO9000 and ISO14000 compliance for assigned zone
- Communicates with opposing shift area manager to exchange information relating to previous shift production, quality, and safety issues and concerns; facilitates problem resolution
- Management Accountabilities
- Job Knowledge and Skill
28
Senior Supervisor, Production Resume Examples & Samples
- Accountable for the maximisation of resources available to deliver outstanding results on all key performance metrics on particular line(s)
- Provide strong, capable leadership and clear direction to all team members, including all support functions
- Promote quality and customer satisfaction as a way of life in all activities
- Ensure the site is compliant to all direct training requirements
- Continue to improve and enhance the ‘Training Methodology’ program for direct employees in Cork
- Liaise with corporate direct training on specific training projects and initiatives
- Represent the site on corporate projects related to direct training, Stryker Learning Management System (SLMS) etc
- Manage and develop direct reports to achieve business goals and objectives
- Champion effective communications with the relevant Management Team members
- Demonstrates a flexible management style and is adept at utilising the appropriate style for the given situation
- Identify and drive continuous improvement initiatives within the department
- Drive adherence to regulatory and GMP requirements
- Champion the deployment and on-going use of Lean tools and techniques in his/ her area to identify and drive continuous improvement in order to meet all key performance metrics
- Demonstrates through his / her management style respect for the core values of Stryker and a commitment to teamwork
- Develop and report on metrics for his / her area to meet overall operational goals & objectives
- Project planning, in detail, in support of major projects, product/process transfer etc
29
Supervisor, Production Resume Examples & Samples
- Responsible for the management and development of direct reports
- Responsible for presenting and defending policies and procedures to both internal and external management and auditors
- Need to proactively investigate, evaluate, and potentially implement the latest industry trends
- Understanding of pharmaceutical manufacturing is required
- Experience writing and updating standardized working procedures is preferred
- ERP systems experience is preferred
- At least intermediate level skills in Microsoft Word are required
- Ability to organize daily work plans is required
- Incumbents must be willing and able to work core hours which are 2PM-10:30PM
30
Supervisor Production Iii Hour Night Shift Resume Examples & Samples
- Supervises needlepunch department across one or more shifts, which includes reviewing production orders and/or schedules to ensure that production requirements within the department are completed according to established production schedules. Resolves operational, processing, and maintenance problems to ensure minimum costs and production downtime
- Continuously improves all production methods while adhering to all safety procedures. Responsible for training and development of hourly employees, estimating personnel needs, assigning work, meeting completion dates, interpreting and ensuring consistent application of organizational polices
- Schedules personnel and assigns work to meet production requirements in an efficient and cost effective manner. Ensure adherence to established priorities for production workflow. Assists with planning, developing and administering departmental procedures, policies and standards, ensures organization policies and procedures are communicated and practiced. Develops appropriate measures or standards for performance and uses these to monitor, evaluate and continuously improve employees and production. Maintains shift reports and records. Verifies employee hours worked in KRONOS
- Provides consistent and constructive feedback to employees; trains, develops or identifies employee’s training and resource needs, establishes priorities, monitors the quality and quantity of work performed by the department and the individuals within the department. This includes ensuring quality requirements and procedures for the department and plant are communicated, understood and practiced
- Maintains control of resources to ensure on-going operation of the department within the established budget, productivity and efficiency standards; develops and maintains effective working relationships with other departments to proactively address issues that may potentially impact the quality of the production process or product
- Works with safety committee by attending safety meetings, working on safety projects, completing safety surveys, performing safety training and ensuring a safe work environment and appropriate employee behavior
- Involved in the hiring process for assigned employee work group. Responsible for employee counseling and disciplinary actions, including recommendations for termination. Involves Human Resources for assistance in the resolution of employee relation issues through effective remediation techniques
- College degree preferred or an equivalent combination of education, training, and experience that provides the required skills and knowledge to perform the essential function of the job
- 6-8 years of job specific experience in within the functional area. Experience must include a minimum of 2 years in a lead or senior capacity
- Proficient using a PC and other department specific databases, systems, and other hardware and software
- Proficient using all assigned department machinery and other related equipment and the knowledge and skills required to perform troubleshooting, preventative maintenance, and resolve other basic operating problems
- Knowledge of Mohawk’s organizational and functional operating structure, products, administrative procedures, and policies
- Basic knowledge and understanding of HR policies, practices, and procedures as it relates to employee relations, hiring, terminations, benefits and compensations plans and administration guidelines
- Ability to use and apply basic mathematical principles and to calculate figures and amounts such as proportions and percentages
- Excellent verbal, written and interpersonal communication skills in order to effectively interact with management, staff, and other internal customers
- Ability to communicate with others in an antagonistic situation using appropriate interpersonal styles and methods to reduce tension or conflict and maintain professionalism in accordance with corporate standards
- Ability and willingness to challenge established practices and draw relevant conclusions; ability to persuade, market and sell new ideas; ability to work in a high-pressure environment and exercise good judgment to resolve problems in the absence of formalized guidelines and procedures
- Excellent human resource management skills to effectively lead and direct a diverse work group; to achieve results through team efforts, and the desire and ability to motivate, persuade and direct the activities of others
31
Supervisor, Production Controlling Resume Examples & Samples
- Coordinate operational planning process, cost budget and production planning with plant and BU and global production network
- Definition, target setting and monitoring of KPIs in the plant organization
- Monitor business performance with regular business reporting and financial analysis to support business steering activities and coordinate the financial reporting compliance
- Analyze and identify reasons for variance against defined business operational objectives and alert management timely and suggest area of improvement
- Monthly report fixed cost, variable cost and cost of sales comparison BGT/ACT/FC and information to plant management, regional controlling and global production controlling
- Monthly inventory report to plant management, monitoring purchasing plans and price development
- Monitor and report operation result of raw material & utilities in the plant
- Co-ordinate various stock taking in the plant organization
- Design and monitor the implementation of plant CAPEX purchasing
- Support plant personnel cost information
- Participate in the development and implementation of the plant development and budget planning of production
- Interprets, directs and ensures adequate internal and external financial controls are maintained so that inventories, M&E and other company assets are protected during all phases of plant operations
- Responsible for all general and cost accounting which includes systems and procedures to insure the accurate and timely financial reporting of site performance
- Directs the preparation of the site’s Operating Plan/Forecast to ensure accuracy and reasonableness of all forward looking data used for business group projections, including that the annual rate development process supports the annual spending plan
- Participate in ad hoc projects with controlling advice, as and when required
32
Supervisor, Production Still Resume Examples & Samples
- Demonstrated ability to collaborate cross-functionally and coordinate efforts around process improvement
- Working knowledge of basic elements of Good Manufacturing Practices in a manufacturing environment
- Working knowledge of key business drivers used to gauge the effectiveness and performance of an internal group or supplier
- Knowledge of PLCs, Ammonia Refrigeration and PMs on manufacturing equipment
33
Supervisor Production Resume Examples & Samples
- Directly responsible for the overall performance of the PVC Injection Molded Footwear manufacturing value stream including Safety, Quality, Delivery, Inventory and Costs
- Provides leadership guidance to ensure product scheduling; planning, manpower allocation and materials are effective in enabling the value stream to achieve customer requirements and financial objectives
- Drives the implementation of HOS and acts as the Lean Manufacturing resources responsible for eliminating waste and improving flow throughout the manufacturing process
- Ensures equipment and process troubleshooting and upkeep through the shift to maintain operations per schedule
- Maintain a safe work environment throughout the facility, instill a high level of safety awareness among team members and insure sustainment of 5S principles
- Prepare/coordinate production schedules and ensure teams are adequately staffed. Evaluate production needs for daily assignment of duties and allocate resources to ensure targets are met
- Communicate between and within shift s and different disciplines ensuring flow of information
- Coordinate with receiving and shipping operations to ensure proper material availability and accuracy
- Ensure procedures are in place and being followed for production efficiency, safety, and compliance with state/federal regulations and guidelines. Focus team on using standardized work practices
- Establish goals, set priorities and coordinate all related activities within the Value Stream to ensure drive and focus toward meeting and exceeding common business objectives from the site strategic objectives (RAIL)
- Encourage continuous improvement activities and seek opportunities and initiate action for process improvement. Serve as resource for team leads and team members to drive improvement opportunities. Identify gaps and implement countermeasures
- Mentor and develop team on HON behaviors and metrics. Listen, support, engage and encourage employee suggestions and input to achieve excellent results
- Build strong alliances between all functions and is strategic liaison to Maintenance, Technical, Quality, Scheduling, HSE, Distribution in order to meet customer and shareholder commitments
- Perform performance evaluations. Coach and support to ensure a high functional team
- Other duties and cross training as assigned
- Bachelor's degree and 1 year of leadership experience, or in lieu of a degree, 8 years of leadership experience in a manufacturing/production environment
- Customer focus, internal and external
- Excellent computer skills and organizational ability
- Strong presence on production floor continuously driving improvement
- Bachelor's degree in business management or engineering
- Experience in advanced manufacturing concepts (i.e. Lean, Six Sigma, TQM)
- Experience working in a functional organizational structure
- Experience working in the plastics industry and or chemical processing industry in a progressive manufacturing environment
34
Supervisor Production Resume Examples & Samples
- Ensure Safe, efficient operation of the HON Boyne City’s Machine Shop
- Leading Boyne City employees and managing personnel issues (Maintaining proper staffing “census” levels, hiring, discipline, performance management)
- Work with the Manager of Operations to ensure that realistic, but challenging production goals are set and met
- Initiate and/or lead Rapid Problem Solving Investigations as required production needs and HOS principles
- Maintain a strong working knowledge of the products manufactured, the tools utilized, & other assets in their departments
- Makes People Better encourages excellence in peers, subordinates and/or managers
- Fosters Teamwork and Diversity defines success in terms of the whole team
- 2 years of previous Supervision Experience in a mfg environment
- 1 Year of experience working within an ISO 9001 quality system or similar environment
- Preferred Technical/Engineering Bachelors degree and 2 years of mfg experience
- Experience in a union environment
- Experience with TPS or similar business system preferred
- 1 + years of machine shop experience
35
Supervisor Production Resume Examples & Samples
- The First Line Supervisor principal duties and responsibilities includ
- Support Maintenance and Engineering in the execution of projects
- Actively involved in preparation and execution of Lockout and Tag Out of equipment
- Minimum 3 months experience in manufacturing is required
- Bachelors Degree is preferred
- Minimum 2 years supervisory experience is desired
- Six Sigma and lean manufacturing experience and/or military supervisory experience preferred
- Experience in a union environment preferred
- Proficiency in Microsoft products, KRONOS and SAP preferred
- Hands-on LOTO experience preferred
- Ability and willingness to work some 12-16 hour days
- Demonstrated team player
- Demonstrated strong leadership traits
- Possess strong work ethic and commitment to the job
- Ability to quickly learn processes
- Understanding of chemical process is helpful
- Ability to lead and coach individuals to exceed performance goals and metrics
36
Senior Supervisor, Production Resume Examples & Samples
- Maintain an organized, safe and efficient work area at all times
- Ensure production goals are met
- Train technicians on the proper use of work instructions
- Solicit feedback and ideas from production personnel
- Other duties as may be determined by Management
- Talent Development activities which include developing training plans with employees to ensure they have the necessary expertise to successfully perform their jobs, provide ongoing guidance to employees, and career counseling to help employees develop and advance in their careers
37
Supervisor Production Resume Examples & Samples
- Associates Degree or equivalent technical certification
- At least 4 years professional experience as a Production Supervisor, Stage Manager, and/or related entertainment and audio/visual experience, preferably in the technical aspects of producing events, shows, business meetings, or large scale multi-media presentations and productions
- AutoCAD Experience
38
Supervisor Production Resume Examples & Samples
- Associate's and/or Bachelors of Business or related degree is preferred. However, consideration will be given for equivalent aircraft maintenance operational leadership experience
- A&P License required for Aircraft or Component Maintenance Supervisor positions
- A successful Line and/or Base station operations track record and experience at a crew chief, tech crew chief, or other related Level 4 supervisor position
- At least 5 years verifiable hands-on experience spent in the repair, maintenance, overhaul or manufacture of aircraft with a gross weight in excess of 70,000 lbs. (including fuel) or engines with 15,000 lbs, or more of thrust
- Experience managing, supervising and/or directing workgroups
- A successful track record and experience with process improvement in maintenance and/or production environments
- Experience in positions requiring budget understanding, resource forecasting and management, and workload planning in maintenance environments
39
Supervisor Production nd Shift Resume Examples & Samples
- Oversees day-to-day manufacturing operations to ensure that all requirements for safety, quality, delivery, inventory and cost controls are met
- Responsible for driving productivity improvement for the PCB Manufacturing Value Stream
- Coordinates production plans and implement production schedules, ensure the efficient utilization of plant facilities and manpower, and to meet immediate and future customer requirements
- Promotes and maintains a safe working environment to minimize employees' exposure to potential hazards, and ensures compliance to defined environmental requirements
- Develops safe and efficient production methods for new products and monitors existing processes to improve product quality and production efficiency
- Leads and motivates plant personnel to assure attainment of established objectives
- Maintains positive employee relations in a multi-cultural environment
- Ensures all production personnel are trained and qualified for their assigned tasks. Develops and monitors employee cross-training and development plans
- He/she should be strong analytically and have diplomatic problem solving skills. This candidate must be creative and strive for high levels of excellence
- 2+ years of direct supervisory experience (staff or 10 or more)
- 5+ years of experience in a manufacturing organization
- Experience in SMT Electronics Manufacturing and Box Build Final Assembly
40
Supervisor, Production Resume Examples & Samples
- Ensures production work is performed in assigned manufacturing functions for the 2nd shift
- Interfaces with other Production Management and support functions to ensure optimum productivity within Cost Center(s)
- Identifies and implements innovative approaches to tasks for responsible Cost Center(s) to ensure continual upgrading of work methodologies
- Ensures that labor and expense reporting within Cost Center(s) are precise and timely
- Ensures that area is at optimum manning and that craft workers are continuously and effectively employed
- Ensures that product quality is maintained
- Ensures that safety and environmental requirements are enforced
- Develop skills levels of craft workers in area of responsibility
- Ensures that Production schedules and budgets are met
- Ensures that policies, procedures and rules are followed within Cost Center(s)
- Perform other job related duties as assigned by management
- Five (5) plus years of experience in supervision or leading teams with one (1) year of experience as a Lead
- Demonstrated/proven leadership skills and sound organizational skills
- Excellent oral and written communication skills inclusive of presentation skills
- Ability to work independently and manage several projects simultaneously both within and across teams
- Demonstrated proficiency in MS software specifically, Outlook, Excel, Access, and Internet applications
- Demonstrated analytical skills including tracking/monitoring actual, budgeting, and preparing project estimates
- Ability to interface effectively and efficiently with peers, management, employees, subordinates and customers
- Demonstrated knowledge and proficiency with Outfitting, Painting and Structural functions
- Familiar with and/or knowledge of weld symbols, a plus
- Must be willing to work rotating shifts specifically the 2nd shift
- Willingness and flexibility to work extended hours as needed to accomplish the task or work with little or no prior notification
41
Supervisor, Production Resume Examples & Samples
- Hire, train and supervise an adequate number of employees to meet the needs of plant operations
- Based on sales and inventory needs, schedules pipe plant production
- Insures proper maintenance of plant production equipment to minimize lost production time. This includes maintaining adequate spare parts inventory
- Orders raw materials to meet production and inventory needs
- Insures safe work practice by all pipe plant employees
- Insures that production meets or exceeds established quality standards
- Maintain positive customer relations by responding to, and resolving complaints
- From time to time, may be requested to assist other pipe operations employees to solve complaints
- Perform routine mechanical/electrical repairs and preventative maintenance
- Perform troubleshooting and problem solving as needed
- Prepare daily production reports, down time reports, and other paperwork as required using CEMEX required computerized forms and systems. Responsible for filing and documentation systems
- Order supplies, parts, and materials required for operations
- Perform moisture analysis on aggregates daily; adjust mixes for moisture content
- Batch and adjust mix designs as required
- Train and cross-train plant personnel as required
- Perform plant startup and closing procedures
- Responsible for maintaining quality pipe production
- Performing bulk and physical inventories
- Responsible for maintaining a safe work environment
- Perform other duties and responsibilities as required or assigned
- Position requires the equivalent of a two year Associate degree and/or education in related areas
- A minimum of 5 years experience a production supervisory role
- A working knowledge of all aspects of control circuits
- Metal fabrication (welding and cutting)
- A basic knowledge of hydraulic and pneumatic controls and assemblies
- Knowledge of mix design and material requirements
- Basic OSHA requirements
- Good communication and human resources skills are required
- Strong maintenance knowledge/skills; strong electrical trouble-shooting skills
- Possess management skills
- Experience with the types of production equipment being used in the production process
- Familiar with the mill supply industry with respect to parts and purchasing
- Background in electrical and electronics areas
- Field experience with construction and particularly with the site contractors
- Possess background with experience in materials engineering
- Has the ability to motivate the production team
42
Supervisor, Production Management nd Shift Resume Examples & Samples
- Champion of cGMP and QSR concepts and procedures
- Champion 5S principles
- Champion Lean Manufacturing principles (including kaizen blitzes, IPK adherence, etc.)
- Lead and manage projects (as assigned). Develop resources to accomplish tasks and manage
- Minimum of an AA degree and 7+ years of experience in a hands‐on role at a medical device or pharmaceutical company or equivalent combination of education and experience; Bachelor’s degree in engineering field strongly preferred
- 3+ years previous supervisory experience
- Experience in a Clean Room environment (CER)
- Strong written and verbal communications skills
- Ability to effectively interact with all levels of employees and management, both in the
- Manufacturing group and cross‐functionally
- Excellent computer skills ‐ including advanced working knowledge of Microsoft Office (Word, Excel,
43
Supervisor, Production Resume Examples & Samples
- Acts as primary back up to the Department Manager
- Manages and oversees training assignments for all department employees and ensures timely completion
- Reviews, and submits all training documentation to the department manager for review and approval
- In conjunction with other production supervisors, ensures daily pay period completion of all time cards, and pre approval prior to submission to payroll
- Supervises and facilitates the day-to-day shift activities of team. Utilizes knowledge and experience, providing training to team members. Responsible for their individual performance. Oversees scheduling, material handling issues and maintenance, as well as resolving production problems. Helps team achieve goals and has responsibility for personnel issues, including required employee coaching, counseling or discipline
- Works with employees to maintain a safe work environment. Encourages and leads team members to work in a safe manner and to seek improvement in work practices. Develops and implements safety procedures and supports Health, Safety & Environmental Manager in achieving departmental and plant safety goals
- Ensures that product quality, production efficiency, and overall productivity meet or exceeds established standards, and is directly accountable for expenditures exceeding budgeted levels
- Strives to be technically proficient on the machinery in the department. Provides assistance to the team in problem resolution and assures that testing and product development is carried out in a professional manner
- Must be supportive of GPI’s Mission, Vision, and Core Values (Integrity, Respect, Accountability, Relationships, and Teamwork)
- Must be supportive and involved in GPI efforts for LEAN, 5’s, Six Sigma and other Continuous Improvement programs and processes
- Strives to clearly understand customer requirements and delivers results to meet or exceed customer expectations
- Ability and responsibility to stop any process that is not meeting customer quality requirements
- Printing/packaging converting experience a plus (includes internships)
- Paper Mill experience a plus (includes internships)
- Prior supervisory experience a plus
- Advanced degree beneficial but not required
- Highly skilled in Microsoft office applications
44
Supervisor Production Resume Examples & Samples
- Supervises production employees which will include hiring, employee communications, training, disciplinary actions and performance evaluations
- Approves timecards, schedules overtime and weekend work
- Ensures that operators are properly trained and that work is performed in a safe and efficient manner
- Monitors and maintains safety procedures and conditions to prevent accidents and provide a safe workplace
- Ensures that products are produced in accordance with all manufacturing and quality specifications and leads the workforce in safe manufacturing procedures
- Ensures that production requirements and goals are met to meet customer requirements
- Provides leadership, direction and support through empowerment, teamwork, on the job assignments and utilization of implementation of continuous improvement concepts and methods
- Leads, coaches and trains employees towards team concepts to foster and build a positive work environment
- Will be facilitator to staff with regards to performance, quality, inventory management, process improvements and daily communications
- Ensures quality of work produced meets customer's requirements
- Establishes lean manufacturing practices in work areas
- College or technical degree preferred
- 3-5 years recent production supervisory experience in a manufacturing environment, preferably with custom molded rubber or plastics operations
- Prior experience supervising a unionized workforce
- Strong background with implementation of lean manufacturing principles and concepts
- Excellent interpersonal and communication skills required
- Must be able to work an off shift
- Must have good understanding with Microsoft Office systems
- Experience with Oracle and Kronos a plus
45
Supervisor, Production Resume Examples & Samples
- Conducts layered audits and machine process studies to ensure operations are capable
- Organizes material flows and inventory to reach productions targets and work in process goals
- Evaluates manpower needs and assigns available resources
- Compiles production data
- Ensures all equipment is routinely maintained
- Supervises and coordinates training for a team of production staff
- Drive OEE to 85% target
- Assure team follow the standards and company policies no matter what
- Bachelor Degree or equivalent experience preferred
- 3 to 5 years experience in manufacturing related field
- Experience supervising employees in a manufacturing environment preferred
- Self-Administered Teams Management
- Assembly process
- Safety and Ergonomics
- Personnel administration
- ISO/TS 16949 & ISO 14000
- English (desired)
46
Supervisor, Production Resume Examples & Samples
- Developing professional expertise, applies company policies and procedures to resolve a variety of issues
- Works on problems of moderate scope where analysis of situations or data requires a review of a variety of factors
- Exercises judgment within defined procedures and practices to determine appropriate action. Builds productive internal/external working relationships
- May directly manage 1 or 2 employees
47
Supervisor Production Resume Examples & Samples
- 1-3 years production/manufacturing experience
- Requires experience managing people/budgets
- 2+ years supervising production staff preferred
- Basic computer and database application skills
48
Supervisor, Production NJ nd Shift Resume Examples & Samples
- Coordinate the daily routine of the packaging area
- Efficiently assign jobs to personnel throughout the shift
- Track employee paid time off and employee attendance
- Adjust schedule daily to accommodate absences
- Maintain Line Leader and Operator job assignment to efficiently utilize available personnel
- Maintain a professional, motivated team of packaging personnel
- Insure Good Manufacturing Procedures training requirements are completed on time
- Assist in insuring packaging lines are properly purged
- Insure all required documentation is completed on the lines
- Maintain a safe department and complete accident reports as required
- Complete performance reviews for Line Leaders and Operators. Set objectives as required
- Coordinate additional temporary employees with Human Resources when required
- Solve personnel conflicts and administer discipline when required
- Analyze packaging to assist in determining the most efficient schedule
- Supervise Line Leaders and Operators in producing a quality product in an efficient manner
- Review, update, and write Standard Operating Procedures as required
- Maintain a positive attitude toward change and motivate subordinates to accept change
- Review packaging procedures and provide efficiency improvement ideas
- Assist in the execution of machine and product qualifications
- Insure all components are ready for the scheduled packaging run including checking in and returning components to and from the warehouse
- Train employees in cGMP and SOP and other important guidelines
- Deliver quality and quantity
- Maintain proper record keeping and inventory controls
- Reconciliation of batch records
- Accountable for quality verification, proper labeling, coding and packaging
- Maintain and meeting packaging schedules per company demands
- Knowledge of J.D. Edwards system and working and coordinating with warehouse personnel
- Updating batch records through the change control process
- Emailing production counts daily
- Assist with projects including serialization
- Carries out supervisory responsibilities in accordance with the organization policies and applicable laws
- Responsibilities include interviewing, hiring, and training employees; planning, assisting, and directing work; appraising performance, rewarding and disciplining employees; addressing complaints and resolving conflicts
49
Supervisor Production Resume Examples & Samples
- Requires similar PC, database management and accounting skills as outlined in Production Field Administrator III
- Makes independent decisions regarding planning, organizing and scheduling work for self and others
- May be responsible for supervision, development, training of more junior staff, and assisting Manager position
- 5+ years of experience in manufacturing.(i.e. JohnSmithResume.pdf or JohnSmithResume.doc)
50
Supervisor, Production Resume Examples & Samples
- Ensure all job-related accidents or injuries are reported and documented by those responsible, and take appropriate corrective action in an expeditious manner
- Inspect product to verify product standards and specifications are met
- Provide technical and behavioral coaching and development to employees
- Track absenteeism and timekeeping in Kronos
- Demonstrated successful ability to lead people and get results through others
- Successful experience in employee training and development including that of peers and subordinates
- Ability to balance and achieve positive results in the areas of safety, quality, productivity, cost and employee relations
- Excellent interpersonal and communication skills with the ability to interact with all levels of the organization
- Associate’s or Bachelor’s degree in related field
- Continuous improvement training such as Six Sigma or Kaizen
- Ability to speak and understand the Spanish language
- Exposure to systems controls such as ISO 140001
51
Supervisor Production Resume Examples & Samples
- Supervising a crew of multi skilled operators
- Executing production activities to plan through the management of people
- Leading, coaching and mentoring employees and direct reports to deliver the plan and build a high performance team
- Demonstrating and instilling an overriding commitment to health, safety, environmental responsibility and sustainable development
52
Supervisor Production Area Resume Examples & Samples
- Review processing schedules or production orders to make decisions concerning inventory requirements, staffing requirements, work procedures, or duty assignments, considering budgetary limitations and time constraints
- Direct or coordinate production, processing, distribution, or marketing activities of industrial organizations
- Develop or implement production tracking or quality control systems, analyzing production, quality control, maintenance, or other operational reports, to detect production problems
- Hire, train, evaluate, or discharge staff or resolve personnel grievances
- Prepare and maintain production reports or personnel records
- Set and monitor product standards, examining samples of raw products or directing testing during processing, to ensure finished products are of prescribed quality
- Develop budgets or approve expenditures for supplies, materials, or human resources, ensuring that materials, labor, or equipment are used efficiently to meet production targets
- Initiate or coordinate inventory or cost control programs
- Coordinate or recommend procedures for facility or equipment maintenance or modification, including the replacement of machines
- Ensure compliance with standard operating procedures, work instructions, quality systems, plant policies and plant processes to drive first pass yield. Conduct root cause/8D analysis and implement corrective actions for nonconformances
53
Supervisor Production Resume Examples & Samples
- Maintains close coordination with Supply Chain, Facilities, and Engineering to ensure availability of materials, equipment and services for the timely shipment of products
- Applies performance management, coaching, constructive feedback and progressive discipline tools/systems to promote strong individual and team performance and actively support employee development
- Maintains up-to-date knowledge of WIP, consumables and material levels within work centers
- Maintains daily open 2-way communication with direct reports, peers and leadership
- Bachelor’s Degree or 7-10 years of equivalent experience
- Working knowledge of continuous improvement and statistical tools. Six Sigma experience and Lean, Black Belt or Green Belt certification preferred
- Strong computer skills and proficiency with common business software/database applications
54
Supervisor Production Resume Examples & Samples
- Safety: Champion all aspects of personal and Plant safety, including STOP. Instill a sense of self-responsibility for safety among associates. Assure the safety of the associates and safe use of the equipment
- Financial: Support Plant budget by controlling labor and overtime, inventory and supply spending
- Leadership: Continually improve leadership and management skills
- Production Goals and Objectives: Monitor and achieve production's operating metrics, such as NFPM, MSI, percent uptime, waste reduction and housekeeping
- Customer Relationship: Promote a customer-centered culture at the plant, including customer sales visits, assuring on-time deliveries of a quality product, and supporting the development of new products and technologies
- Technical Knowledge: Develop and continually improve technical knowledge of processes in order to continually improve and problem solve, when necessary
- Continuous Improvement: Promote a culture of relentless pursuit of continuous improvement and lean practices, focused and data based
- People: Build a high performing team to instill ownership of production objectives through selection, performance assessments, training and development of associates. Administer discipline as necessary
- Quality: Optimize the production process to assure that quality is built-in, not inspected in. Quality levels must meet plant requirements
- Capacity Rationalization: Manage the capacity of the manufacturing processes and scheduling of associates to meet fluctuating customer demands
- Values: Model the Corporate Values and Principles
55
Supervisor, Production Resume Examples & Samples
- Prioritize work flow to ensure the manufacturing of products are meeting delivery requirements, company performance standards, and customer specification, in accordance with EDI’s policies and procedures
- Review parts shortages with purchasing, and adjust schedules as necessary
- Review department staffing for shift and makes necessary arrangements for coverage, overtime, etc
- Participate in tactical meetings by recommending improvements to plant layout, workforce planning, and equipment requirements
- Maintain departmental performance measures, including visual controls and provide regular progress reports to functional areas within organization including purchasing, engineering, etc
- Continually evaluate processes and methods, recommend measures to improve production methods, equipment, performance, utilization of people, and quality of product
- Participate and promote lean principles/concepts including visual factory, 6S, etc
- Ensure employees are trained on specific job requirements, safety, and quality
- Provide performance feedback to employees and conduct evaluations on time
- Monitors and reviews accuracy of all direct reports. Performs random periodic verification of product quality, paperwork accuracy and good manufacturing practices
- Champion effective communication across all-shifts & departments. Provide overall management direction and leadership to teams by coaching employees to develop critical skills, clearly communicating the organizations vision and strategies, and helping teams translate those business strategies to their daily work
- Responsible for promoting safety awareness and keeping safety as a number one priority on a daily basis
- Take a leadership role in Quality including managing, recording & delivering corrective actions
- Actively ensure employees are working within the safety and quality policies and procedures
- Minimum associate degree in applicable field with 2-4 years of experience within a manufacturing environment ( Bachelor’s degree preferred), or comparable number of years of experience
- Previous experience leading or supervising a team of employees within a manufacturing environment
- Previous experience with ERP/MRP systems
- Proven ability to lead a group of employees and establish outstanding communication rapport
- Solid independent judgment with excellent problem solving skills
- Analytical aptitude and strong organizational skills
56
Supervisor, Production Resume Examples & Samples
- Manage staffing levels to current labor standard requirements
- Assign responsibilities to team members, as required to meet planned production schedules
- Review shift activities and results, making adjustments as required for continuous improvement
- Investigate production delays and takes corrective action as necessary
- Minimum of 3 years of manufacturing supervisory experience, preferred
- Professional experience within packaging/food products industry, preferred
- Proficient in Microsoft Word, Power Point and Excel
- Ability to use innovative approaches to resolve complex problems
- Strong written and verbal communication skills, with the ability to effectively communicate throughout all levels of the organization
57
Supervisor Production Resume Examples & Samples
- Coordination of continued development and training of Production line associates
- Verify all required Production documentation properly filled out
- Production/manufacturing or warehouse experience preferred
- Food or Beverage experience preferred
- 2+ years supervising or leading teams a plus
- Familiarity with overall Manufacturing environment roles: Sanitation; QA; Maintenance
58
Supervisor, Production Resume Examples & Samples
- Assist with development, evaluation and improvement of manufacturing/fabrication methodologies and techniques
- Liaison between engineering and production departments to ensure optimal communication and partnering
- Resolve nonconformance issues including documentation of associated rework
- Effective Communication that supports a motivated workforce to deliver the company’s goals and objectives
- Continuously improving process and manpower efficiency, utilization, and productivity
- Lead and manage a staff of ~15 mixed skilled technicians including all performance management related tasks
- Responsible for assessing, implementing, and maintaining the safest work environment possible
- Identifying and set-up of training programs
- Provide required data & reporting to support departmental metrics and improvement objectives
- Maintains work flow by monitoring steps of the process; setting processing variables; observing control points and equipment; monitoring personnel and resources; studying methods
- Maintain tooling and consumable supply inventory
- Read, interpret and work from controlled documentation and processes
- Minimum of 5 years of experience within a spin form or CNC machining operation
- Minimum of 5 years in a high volume manufacturing sector
- Minimum of 2 years of formal leadership experience
- 2-year degree preferred
- Spin forming experience in a production environment is highly preferred
- CNC machining experience in a high volume production environment
- Heat treating experience in a production environment
- Experience bringing teams and processes from development to production desirable
- Demonstrated experience and ability to read, interpret and follow: schematics, engineering, and layout drawings, mechanical assemblies: mechanical drawings and parts lists
- Ability to effectively communicate (verbal and written) with engineering and production
- Able to adapt to constantly changing work assignments and fast paced work environment
59
Supervisor, Production Resume Examples & Samples
- Review production schedule, start up and shift change checklists, and shift performance records for accuracy and develop strategies to improve efficiencies
- Review daily shift schedule to plan and communicate work and associate assignments for assigned shift to ensure productivity meets projections
- Monitor performance during shift to ensure a safe & proper workflow
- Train and certify associates on work processes, standards and any equipment, safety standards systems or procedures necessary to ensure daily productivity goals
- Communicate with Manager, Assistant Supervisor and production associates at shift change to update/inform/get information on any issues
- Prepare required documentation for shift and respond prompty to inquiries about productivity or non-standard events. Maintain attendance, performance and training records
- Proficiency with computers and MS Office (Word, Excel, Outlook)
- Experience with SAP processes and transactions preferred
- Knowledge of manufacturing processes and of company products preferred
- Ability to write technical work standards
- Ability to multi-task and work cross functionally in a fast paced environment
- Ability to arrive at least 30 minutes prior to shift start up and work extended hours (including weekends) to meet company needs
- Ability to operate production equipment and work safely with power tools
- Ability to communicate effectively and present information to management and associates in individual or group settings
- Ability to read, write and speak clearly in English
- Demonstrated success with coaching, motivating, and interacting with team members
- Ability to handle confidential information and lead by setting a good example (role model) - behavior consistent with words
- Ability to plan and prioritize one’s own work and that of the team is necessary
- Ability to make decisions consistent with department guidelines and company policies
- Ability to demonstrate calmness under pressure
- Ability to add, subtract, multiply and divide with 10’s and 100’s. Ability to perform these operations using units of weight measurement, volume, square footage and distance. ability to compute rate, ratio and percent
- Ability to understand and carry out instructions furnished in written, oral or diagram form
- Ability to focus on details and block out continuous distractions
60
Supervisor Production Materials Resume Examples & Samples
- Monitor work being produced to make sure it meets all specifications
- Communicate progress against these goals on a regular basis
- Responsible for efficient processing of work orders, reviewing batch records, maintaining training records, facilitating efficient shift changeovers, production scheduling and reviewing timesheets
- Drive projects with line personnel to improve yield and reduce waste
- Manage the inventory control system (Kanban)
- Notify management of all requirements for tools, supplies, etc
- Talent Acquisition activities which include identifying needs of the shift, justification for budget to fill positions, coordinating with HR to market the position, review resumes, conduct interviews and identify and recommend a candidate as the potential hire, and employee orientation to the department and company
61
Supervisor Production Resume Examples & Samples
- Continuously improves the groups performance by implementing lean manufacturing concepts, techniques and processes
- Effectively implements new performance management systems, production plans and performance criteria; runs shift meetings; confirms production progress; responds to delays; takes corrective actions; records KPI performance
- Creates and implements group improvement plans
- Ensures team understands roles and responsibilities as it relates to the team and core Greif
- Encourages joint problem solving, personal safety, and individual development
- Supports Greif mission, follows values of Greif and works to better Greif's business as a whole
- Communicates goals and objectives, applies company policy, staffs, trains, coaches, recommends salary increases, administers discipline, insures positive employee relations and reviews the performance of employees
- 4 to 5 years experience in a dynamic production environment
- Supervisory or Lead person experience preferred
- Knowledge of industrial packaging
- Demonstrated supervisory, organizational, interpersonal, computer, problem-solving and multi-tasking skills
- Basic understanding of OSHA, DOT, labor and other federal regulations
- Understanding of basic machine operation principles
62
Supervisor, Production Resume Examples & Samples
- Minimum of 5 years of experience working in a high volume manufacturing sector
- Minimum of 2 years of formal leadership experience in a manufacturing environment
- Preferring a bachelor's degree from an accredited university
63
Supervisor Production Operation Resume Examples & Samples
- Supervises the day-to-day operations for the staff by establishing priorities, scheduling and assigning work, adjusting schedules when necessary to meet completion dates, and assisting others with resolving problems in order to achieve good business outcomes
- Provides management with input on the development of unique state/business requirements. Analyzes, researches and solves underwriting and regulatory issues, provides systems development support and makes recommendations for improvements, including impact on FTE needs. Implements with management approval
- Interacts with other departments to ensure the availability and integrity of all information to customers
- Tracks, analyzes and reports on historical production inventory data to determine trends in work volume. Utilizes analytical tools to create ad hoc reports/analysis to more effectively manage the unit
- Ensures that the department/unit work is being completed in a timely and efficient manner through appropriate control, monitoring and review of workflow. Implements procedures to increase efficiency. Ensures requirements of various regulatory agencies are being met
- Partners with other departments (Underwriting, State Management, Systems, etc) to solve problems and ensure optimal customer service
- Leads/participates in a variety of projects to provide business specifications, develop, test and implement new systems/procedures
- Participates in the unit costing/budget process and explains the financials to staff to ensure common understanding/support of department goals
- Associates degree or equivalent or a minimum of 5 years of progressively more responsible related work experience
- Full accountability for training, developing, and supervising staff within a department/unit
- Responsible for administration, analysis and solutions to quality and productivity gaps, maintenance of discipline, hiring of new employees, transfers, etc
- Typically oversees a group of 10 to 20 direct reports performing highly complex and independent jobs
64
Supervisor, Production Resume Examples & Samples
- Plans production operations, establishing priorities and sequences for manufacturing products, utilizing knowledge of production processes and methods, machine and equipment capabilities, and human resource requirements and capabilities
- Makes decisions on job assignments and work priorities
- Reviews production and operating reports and resolves operational, manufacturing, and maintenance problems to ensure minimum costs and prevent operational delays and downtime
- Responsible for equipment condition and department housekeeping
- Researches, complies and prepares reports, correspondence, and other information required by management, as well as, identifies and resolves report discrepancies or errors
- Works with employees to maintain a safe work environment. Leads and supports subordinates to work in a safe manner and to seek improvements in work practices
- Ensures that product quality and production efficiencies meet or exceed established standards
- Examines procedures and recommends changes to save time, labor, and other costs and to improve quality control and operating efficiency
- Supervises and coordinates activities of support resources such as quality, maintenance, shipping and receiving, and technical trainers
- Observes subordinates to ensure compliance with safety, quality, and productivity standards
- Verifies completeness and accuracy of subordinates’ work, computations, and records
- Participates in work of subordinates to facilitate productivity or overcome difficult aspects of work
- Instructs subordinates in job duties or arranges for training to be provided
- Facilitates team meetings, intervenes as necessary to keep the team’s goals and results consistent with company direction, and works with the team members to develop their full potential
- Initiates and conducts personnel actions such as discipline, performance evaluations, and payroll
- Evaluates subordinate job performance and recommends appropriate personnel action
- Administer, communicate and interpret work procedures and company policies to subordinates
- Provides subordinates with guidance in handling difficult or complex problems and in resolving grievances or submits unsettled disputes to management
- Shares an obligation to protect and strengthen Graphic Packaging International’s good reputation in our relationships with customers, employees, suppliers, competitors, investors, and governmental agencies, and to act consistently with our core values: Integrity, Respect, Accountability, Relationships, and Teamwork
- Leadership Skills - ability to motivate people to perform at high level
- Organized
- Computer Skills: SAP, MS Office, and database programs
- Requires use of all general office equipment (e.g. fax, copier, telephone, etc.)
- Visual Color Discrimination, the ability to match or detect differences between colors, including shades of colors
- High School Diploma, GED
- BS degree in related field and/or equivalent experience in a converting facility is preferred
- Experience with web presses and straight-line gluers is preferred
65
Supervisor, Production Resume Examples & Samples
- Supervises assigned manufacturing area daily to achieve department goals
- Hires, trains, evaluates, motivates and develops employees in production areas
- Ensures that products manufactured meet all quality and customer service standards
- Monitors and adjusts production schedules to optimize throughput and customer service. Anticipates and reacts to labor and material shortages
- Investigates root cause of quality, quantity or processing issues and implements solutions to prevent reoccurrence
- Ensures safety and environmental awareness and compliance by all department employees. Participates in the establishment of area safety rules
- Participates in the development of operating budgets including materials, staffing, expense and capital expenditures
- Participates in ongoing cost reduction program
- Assures compliance to all regulatory standards, including on-time compliance training for employees
- Completes and reviews critical documentation including SOPs, Batch Records, and Exception Documents
- Perform other related duties as assigned or required
- Bachelor’s Degree is required: Pharmacy, Chemistry, Biology, Engineering, or Business
- Significant experience in manufacturing, acquired as a Production Specialist, Supervisor, Engineering Technician, or similar position is required
- This position requires leadership, coaching, or supervisory experience
- Must have demonstrated ability to effectively react to a variety of problems in minimum time
- Must have demonstrated ability to anticipate and resolve problems with minimum negative impact on production quality, quantity, and cost
- Prior supervisory experience in pharmaceutical, food or cosmetic manufacturing is preferred
66
Supervisor Production Resume Examples & Samples
- Supervisor oversees ingredient ordering, sampling, testing and release
- This position is responsible for coordinating the scheduling, planning, procurement, and distribution of material for both internal and external customers
- Coordination of packaging material sampling, testing and release
- Provides a safe work environment and sets expectations around safety with direct reports
- Ensures compliance with work orders, GMP’s and internal/external policies, procedures, guidelines and regulations
- Adjusts labor resources to cover for vacations, meetings, overtime and sick time
- Organizes and monitors the labor resources to match the day’s workload
- Communicates meetings and general information to everyone working in the department
- Continues to serve in individual contributor role in area of specialty in addition to supervisory responsibilities
- Provides materials and scheduling support for PP and PRL operations including, inventory of materials/finished goods, weighing, dispensing, shipping, and receiving
- Responsible for coordinating with plants, third party manufacturers (TPM’s), and R&D scientists in executing Pilot Plant studies requiring outside support
- This includes transportation of goods, coordination of plant line scheduling, and work order execution (instructions/weigh sheets)
- Assure that quality documents are properly distributed and controlled internally
- Interface with Product R&D to resolve issues prior to production. Maintain training records for Process Research Operations, track delinquencies, and update training profiles as required
- Completes computer data entry and enhancement; maintains material control databases (AMAPS, POMSnet, S&D) and DQA vendor tracking database
- Completes resolution of documentation and quality issues with plant, manufacturing and/or vendors
- Coordinate departmental activities with Abbott departments through daily and weekly meetings and conference calls
- Responsible for training new lab employees on laboratory operations which includes methods, procedures, documentation, maintenance and safety
- This individual must ensure that the department vision incorporates the ideas of all employees and is flexible to change as the environment changes
- Team building and employee development is critical
- This individual must build and inspire the team through cross-training, developmental training, employee recognition, and acknowledgement of hard work
- Responsible for providing performance feedback through the Performance Excellence system and growth/development planning
- The position reports to the Group Manager R&D Operations. Budgets are managed at the Group Manager level although some cost control such as departmental expenses, production materials, and supplies will be delegated on a routine basis to the Supervisor
- This position is accountable for ensuring compliance with applicable FDA (GMP), FSMA, ODA, USDA, OSHA and Abbott regulations, policies, procedures or guidelines
67
Supervisor Production Resume Examples & Samples
- Safety: Instill a sense of self-responsibility for safety among associates. Assure the safety of the associates and safe use of the equipment
- Production Goals and Objectives: Monitor and achieve production's operating metrics, such as NFPM, MMSI, percent uptime, waste reduction and housekeeping
- Customer Relationship: Promote a customer-centered culture at the plant, including customer sales visits, ensuring on-time deliveries of a quality product, and supporting the development of new products and technologies
- Technical Knowledge: Develop and continually improve technical knowledge of processes in order to continually improve and problem solve
- Continuous Improvement: Promote a culture of relentless pursuit of continuous improvement, focused and data based
- People: Build a high performing team to instill ownership of production objectives through selection, performance assessments, training and development of associates. Assure the development of people at all levels
- Quality: Optimize the production process to assure that quality is built-in, not inspected in. Quality levels must meet customer requirements
- Vendor Management: Manage assigned vendor relationships for the Plant
- High school education or equivalent required
- Bachelor’s degree in Supply Chain, Operations, Business, etc. strongly preferred
- Management experience in the printing industry preferred
- Proven ability to run a manufacturing operation required
- Minimum 5 years press operating experience strongly preferred
- Lean manufacturing formal training and/or experience strongly preferred
- Strong math and measurement skills
- Experience using computers for mathematical equations, data entry, etc. required
- Ability to analyze data, draw conclusions, make recommendations, and present findings
- Ability to make decisions quickly that are rational, logical, and fact driven
- Experience with Microsoft Office Suite required – must be proficient in Outlook, Word, PowerPoint, and Excel (utilization of formulas, pivot tables, etc.)
- Proven experience with Radius, SAP, or other Production and Customer Management System required
- Ability to safely lift up to 50 lbs., 50 feet in distance frequently; more weight in shorter distance may occasionally be required
- Proven experience leading, managing, and supervising others
- Candidate must exhibit the following
68
Senior Supervisor, Production Resume Examples & Samples
- Provides one-to-one feedback to area leads and direct reports regarding team/individual performance
- Develops a plan, with staff, to achieve goals and tracks progress-to-plan using performance metrics
- Implements ownership culture and management routines to improve compliance, equipment efficiency and personnel efficiency
- Maintains consistency with peers to ensure smooth transitions and continuity across shifts
- Leads Root Cause Problem Solving (RCPS) sessions to drive continuous performance improvement
- Works with Maintenance to predict and prevent unplanned downtime
- Assists with quality investigations and CAPA (Corrective and Preventative Actions)
- Performs reviews and approval of completed batch records
- Implements shop floor schedule based on product demand
- Performs job functions in accordance with company policies and procedures, Good Manufacturing Practices (cGMP’s), and Batch Record instructions
- Requires a high school diploma or equivalent
- Prefer bachelor’s degree
- Requires a minimum of 3 years of relevant experience in a regulated industry
- Requires minimal 5years experience in a leadership role and or equivalent education and experience
- Computer proficiency with knowledge of automated systems (i.e. ERP) preferred
- Interact positively with co-workers and management
69
Supervisor Production Resume Examples & Samples
- Proactively foster and promote the safe work habits of employees. Ensure proper safety policies and procedures are followed. Active participation in health & safety initiatives, taking a lead role in safety optimization and the drive towards zero incidents
- Work closely with the Shift Manager and the other Production Supervisors to achieve production goals and KPIs efficiently. Responsible to ensure the production department meets targets set forth in quality, safety, productivity, cost, delivery, morale and environment (QCDSME)
- Win with customers and consumers by ensuring all product quality specifications are being followed and adhered to, with an emphasis on minimizing variance and eliminating customer complaints
- Ensure all HACCP guidelines, rules and regulations are being followed throughout their area of responsibility, including the proper completion of all required documentation
- Performance management for hourly shift employees including performance appraisals and coaching and progressive discipline as required
- Develop the continuous improvement spirit through the support of Lean/Sigma principles and Kaizen breakthrough events
- Prepare schedules; manage vacation planning, and other scheduling activities
- Willing to work scheduled days off to attend scheduled training seminars
- Flexibility to work on any team and change shifts when requested
- Backfill other Supervisors as required
- Support and Drive McCain initiatives
- Demonstrated progressively responsible experience working in various factory positions successfully meeting all objectives and responsibilities as required of each role
- Experience in a supervisory capacity will be considered an asset
- Excellent communication skills (both verbal & written)
- Ability to multi-task and prioritize efficiently using effective time management and organizational skills
- Experience with Infinity QS or other Statistical Process Control (SPC) software
- Post-Secondary education is a requirement
70
Supervisor, Production Management Resume Examples & Samples
- EDUCATION/EXPERIENCE
- 7+ years of experience in a hands‐on role at a medical device/ pharmaceutical company (or equivalent industry) PLUS 3+ years of /supervisory experience
- Experience working in a Controlled Room environment (i.e. cleanroom)
- Must be able to multi‐task and operate in a fast paced environment with minimal training and
- Ability to effectively interact with all levels of employees and management, both in the Manufacturing group and cross‐functionally
- Excellent computer skills ‐ including intermediate working knowledge of Microsoft Office (Word, Excel,
- Outlook, etc.)
- AA degree or above preferred
- Strong Lean Manufacturing background preferred
- Supervises a group of 20 or more manufacturing employees
71
Supervisor Production Resume Examples & Samples
- Train, coach, mentor, and provide feedback/recognition to associates
- Ensure that set standards are adhered to at all times with regard to Safety and Quality
- Lead the Business Unit by ensuring daily focus on SQDCG (Safety, Quality, Delivery, Cost & Growth) visual management process to ensure goals and consumer needs are met
- Responsible for monitoring the performance and corrective actions for the Business Unit, ensuring that information boards are continually updated with daily, weekly and monthly information
- Review long-term data trends and facilitate remedial activities using CI methodologies to determine root cause and fix
- Ensure that Safety, Quality and 5S auditing and corrective measures are complete for all areas within the Business Unit
- Develop detailed manpower and material resourcing plans to ensure that bottlenecks are removed and all delivery commitments are met on time and in full
- Champion the deployment of business systems
- Lead / facilitate / participate in continuous improvement events
- Communicate effectively across all levels of the organization, keeping teams updated regarding issues affecting performance and seeking guidance where needed
- Lead the team and manage any employee relation matters, with guidance sought from HR
- Ensure appropriate knowledge of facility and industry related regulations, support and deploy all plant initiatives such as: MOS (management operating system), TPM (total productive maintenance), Maintenance Excellence, SQF (safe quality foods), etc
- Maintain audit ready status
- Clear and concise verbal and written communication skills
- Demonstrated ability to build strong, effective teams
- Ability to mentor and develop productive staff
- Basic understanding of budgeting and cost control
- Ability to work with individuals at all levels of the organization
- Bachelor’s degree or equivalent of education and experience
- Five to ten years related experience and/or training
- Food processing experience is preferred
- Combination of education, experience or training that would provide the level of knowledge, skill and ability required is acceptable
72
Supervisor, Production Resume Examples & Samples
- Prepares food items necessary for assigned area
- Assigns specific duties to associates under supervision for efficient operation of the kitchen
- Ensures proper storage and handling of products; uses portion, presentation and recipe controls
- Maintains cleanliness of all kitchen areas, including food and non-food working areas
- Reports equipment repair/maintenance to appropriate supervisor or facility department
- Supervises team members in absence of Sous Chef; disciplines, trains and schedules associates
73
Supervisor Production Senior Resume Examples & Samples
- Manage Safety, Quality, Output, Productivity, and Cost for their groups
- Support their assigned team leaders (Cell Coordinators)
- Manage development of their workforce to ensure flexibility and job rotation
- Continuous improvement to meet company goals
- Use Root Cause Corrective Action/5 Why Analysis to be an effective problem solver
- Improve the methods
- Administer time and attendance
- Lead employee corrective action efforts
- Ensure the proper use shift start meetings, 5S, tiered accountability, and visual controls are used
- Growth and Customer Focus recognizes that we need to think differently in order to grow. The customer is the cornerstone of our success
- Leadership Impact means thinking like a leader regardless of your job, delivering on commitments and being a role model for others
- Gets Results Quickly translate business requirements into actions by defining "who does what by when" to ensure plans are executed
- Champions Change drives continuous improvement & reflects a constant commitment to do things better
- Training and experience in Six Sigma and Lean Manufacturing
- Experience with the Toyota Production System or similar business system preferred
- Experience working within an ISO 9001 quality system or similar environment
- Aerospace or Automotive experience
74
Supervisor Production Execution Resume Examples & Samples
- Integrate with Maintenance counterparts to ensure effective, pro-actively planned maintenance
- Review work practices to ensure best practice
- Actively manage employee performance
- Promote continuous improvement with the Smelting area
75
Supervisor, Production Resume Examples & Samples
- Performs daily walks and visual inspections of the Production Department in observation of unsafe acts or conditions; takes immediate corrective action where necessary
- Trains employees to ensure safe operating procedures are followed, including lock-out and tag-out
- Maintains adequate knowledge of products and equipment to ensure the ability to direct employees to perform the job properly
- Walks the production floor daily and holds monthly line meetings to address questions and concerns
- Maintain or exceed goals on yields and efficiencies
- Works with the Operations Managers and/or Superintendents/Supervisors to maintain knowledge of yields and variances, methods of calculations, typical problem areas and methods for corrections and improvement
- High school diploma or general education degree (GED) and 2 years related experience and/or training; or equivalent combination of education and experience
- Able to lead problem solving and troubleshooting efforts associated with high-level process issues
- May be required to work long hours and weekends
- Frequently required to stand; walk; use hands to handle, or feel; reach with hands and arms; stoop, kneel, crouch, or crawl and talk or hear
- The plant environment will include wet or humid conditions (non-weather related), extreme cold and heat (non-weather related), working near moving mechanical parts, exposure to fumes or airborne particles, and chemicals
76
Supervisor Production Resume Examples & Samples
- Lead shift production process areas thru activities of operators in operational and utility areas
- Supervising and coaching hourly personnel - engaging hourly personnel in problem solving and continuous improvement
- Complying with SOPs, maintaining standard work
- Determining maintenance needs and creating notifications
- Reporting process deviations/issues to production management and engineering
- Tracking raw material inventories
- Tracking and communicating production goals (AOP, etc.) to hourly personnel
- Provide and promote a safe, environmentally sound work environment
- Issuing, verifying and signing special work permits, confined space entry permits, and tank entry permits
- Fulfilling ERT roles
- Ensuring compliance with all safety, environmental, nuclear regulations and MTW procedures
- Investigating incidents - health, safety, environmental, and process
- Ensuring compliance with Honeywell Corporate and MTW policies
- Maintaining housekeeping and driving workplace organization in assigned areas
- Conducting elements of Honeywell Structured Safety Process
- Assist in operator training to enable top performance
- Monitoring training for hourly personnel, as required (OJT, JPM, etc.)
- Coordinates proper manning levels to ensure stable operations
- Ensuring production units sufficiently manned
- Approving and scheduling overtime
- Ensuring compliance with the Collective Bargaining Agreement
- Relief Supervisor - breaking for Production Shift Supervisors
- Perform special assignments (Lock, Tag and Try templates, verifying procedures, training, audits, etc.)
- Communicates status of area operations and performance
- Communicates plant announcements/information to hourly personnel (ie. postings, meetings, etc.)
- Day shift position but will provide relief to night shift as needed
- BS/BA Degree and 2 years of supervisory experience OR 5 years of manufacturing/maintenance supervisory experience
- 2 years chemical, nuclear or related plant experience or equivalent Military leadership experience
- Prefer candidate with understanding of federal regulations
- Ability to work with union employees and understand union contracts
- Ability to work in a nuclear plant and pass a thorough background investigation
- SAP knowledge a plus
- Six-Sigma training a plus
- Ability to read and understand P&IDs and PFDs
77
Supervisor, Production Resume Examples & Samples
- Willing to work 2nd and/or 3rd shift
- Strong computer and Microsoft Suite skills
- 3 years' manufacturing background or equivalent training and experience
78
Supervisor, Production Resume Examples & Samples
- Strong PC Skills - MS Office, SAP
- High Level of numeracy
- Manufacturing experience a strong advantage
- The ability to work as part of a team is essential
- Team Leader experience essential along with being comfortable operating as part of a dynamic and diverse cross functional team
- Good planning skills required as well as experience working to tight deadlines
- Lean experience advantageous
- Understand the need to work within procedures and systems where necessary
- Be open to the process of Continual Improvement in their role
- A good level of spoken English
79
Supervisor, Production Maintenance Resume Examples & Samples
- Perform all functions in full compliance with corporate policies and procedures and all other applicable environmental, health, safety and GMP requirements
- Directs the maintenance work force and provides onsite expertise
- Reviews work planning and scheduling with appropriate groups to achieve the goals of the plant
- Ensures equipment availability is adequate to meet the operating campaign
- Work with operations supervisors and point people to ensure Area Based Ownership activities are being executed
- Verifies the qualifications of the Reliability Technicians and recommends training as necessary
- Highly visible in the field
- Champions proactive maintenance activities over reactive activities
- Ensures timely completion of all CPMs, PMs, calibration, corrective work orders and emergency work orders to include external/internal audit finding follow-ups. Makes sure data entered into CMMS is technically accurate and complete
- Supply technical information to the Maintenance Reliability area by identifying opportunities related to specific areas of responsibility and defines the appropriate path forward to increase site reliability
- Align with key stakeholders to understand critical business needs
- Support the four main pillars of reliability based maintenance strategy
- Strong knowledge of Reliability Centered Maintenance principles
- Experience with Computerized Maintenance Management System (CMMS) and the use of CMMS for the execution of maintenance business processes
- Understanding of Predictive Maintenance (PdM) and Condition Based Monitoring (CBM)
- Understanding of industrial electro-mechanical concepts such as PLC and field instrumentation, variable frequency drives, basic hydraulics and pneumatics, etc
- Proven decision making skills
- Ability to communicate and work effectively in a team oriented environment
- Self-starter with strong leadership, analytical, administrative and people skills
- Results oriented, accountable for decisions
- Ability to establish rapport and energize employees to work as a team in a transitional business unit
- Understanding of customer service support a must
80
Supervisor, Production Resume Examples & Samples
- Implements a staffing plan by identifying resource requirements, writing justifications for additional personnel, obtaining approval for changes, and coordinating the selection process with Human Resources
- Foster a continuous improvement culture by identifying and tackling improvements opportunities
- Bachelor 's Degree in Engineering is required. Industrial Engineering degree is preferred
- 0- 2 years of experience of related work experience
- Previous COOP/Intern or job experience in a FDA regulated industry is required
- Experience in FDA regulated environment
- Proven continuous improvement experience (Lean Mfg/DIMAIC) is preferred
- Must be able to work on a 2nd Shift
- Fully Bilingual (English and Spanish)
81
Supervisor, Production Resume Examples & Samples
- Bachelor 's Degree is required
- 0-2 years of experience of related work experience
- Must be able to work 3rd Shift
82
Supervisor Production Weekend Resume Examples & Samples
- Lead entire off-shift operations while delivering key performance indicators (safety, quality, cost and service)
- Manage production, warehouse, quality and maintenance teams
- Verify the readiness of the production line at start-up and supervise change overs
- Manage overall package and product quality to ensure all standards and specifications are maintained
- Ensure completion of the daily Production Run schedule
- Bachelor's Degree or equivalent work experience; Engineering degree preferred
- Knowledge of Lean Six Sigma or other Organizational Effectiveness practices
- Requires experience managing people and performance metrics
- Strong computer and database application skills
- Familiarity with manufacturing systems
- Strong SAP knowledge and application highly preferred
83
Supervisor Production Resume Examples & Samples
- Executes the manufacturing schedules based on information and requirements from management and customer
- Oversees and assists in the ordering of all raw materials and consumables used in the production of titanium sponge, and ancillary processes associated with the sponge production and the maintenance of process equipment
- Supervises the leads and personnel in the production and maintenance departments, utilizing them to fulfill the requirements of the department
- Monitors and controls the quality of the product through regular training and Standard Operating Procedure review for thoroughness and process improvement
- Utilizes Six-Sigma Lean Manufacturing tools to evaluate existing and alternative production methods and integrates them into standard operations on a cost-effective basis
- Coordinates with the HS&E Department to maintain production facilities, processes, and personnel in compliance with corporate health, environmental, and safety policies
- Coordinates PM schedules and equipment repairs with Maintenance and Electrical
- Participates in the design and modification of specialized equipment used in the sponge production process
- Provides cost accounting information for monthly inventory
- Conducts performance evaluations for the production leads, process operators and maintenance personnel
- Conducts interviews and hires production and maintenance personnel
- Coordinates and prioritizes capital projects and process improvements
- Promotes Environmental Health and Safety goals to foster safe work practices and environment
- Prepares, monitors, and manages all relevant budgets
- Actively participates in helping to improve the work environment through cleanliness, good housekeeping and adherence to all environmental, health and safety policies
- Supports and participates in all Zero Incident Culture activities, as outlined in the site ZIC Manual
- Complies with Honeywell Cardinal Rules and Environmental Management policies
- Supports the Honeywell Operating System (HOS) by
- Owning the continuous improvement process for area of responsibility and actively supporting other areas; ensuring all employees are engaged in daily improvement activities
- Providing direction and guidance on where to focus attention and improvement efforts
- Teaching, mentoring and coaching employees on the key lean concepts, observation methods and the continuous improvement process, including their responsibilities to actively participate in the continuous improvement process
- Bachelor’s Degree in engineering or equivalent technical degree
- Minimum five years experience in a manufacturing environment or equivalent, including at least two years of supervisory experience
- Certified Green Belt preferred (or will be required to achieve in first 12 months)
- Prior experience with process engineering preferred
- Ability to define and solve technical problems
- Knowledge of Microsoft Windows, document control system, Excel, Access, and SAP
- Excellent verbal, written and presentation skills required
- Demonstrated ability to effectively supervise, motivate and direct production personnel
- Demonstrated skills in management and development of subordinates
84
Green End Supervisor, Production Resume Examples & Samples
- Actively support the company's vision and values
- Provide leadership in the areas of safety, quality and production
- Help drive safety improvement for the Weed operations
- Sets clear expectations for crewmembers and expects clear expectations of management
- Maintains focus on internal and external customer's needs
- Strive to increase quality and efficiency of department
- Manage employee time and attendance w/ Kronos system
- Identify and implement opportunities for continuous improvement
- Coordinate production activities between departments
- Interpret/enforce company policies and procedures
- Prefer college degree and/or supervisory experience
- Ability to coach and lead a diverse workforce
- Comprehensive knowledge of machine centers preferred
- Good at multi-tasking
- PC operation (Word, Excel)
85
Supervisor Production Execution Goldroom Resume Examples & Samples
- Manage all aspects of shift performance including safety, production, personnel and budgets
- Lead the implementation and monitor effectiveness of improvement initiatives
- Identify, build and develop team capability through ongoing and regular coaching and development
- Be responsible and accountable to ensure that critical controls are effective
- Collaborate with other areas and departments
- Ensure that costs are managed and support the department budget
86
Supervisor, Production Resume Examples & Samples
- Lead, coach, motivate and develop team members
- Provide tools and resources to the department team to be successful
- Implement policies in the Associate Handbook
- Meet production operational standards by implementing production, productivity, quality, and customer service standards
- Lead manufacturing team, plan and schedule work to utilize equipment and maintain maximum productivity levels
- Lead effort in plans to improve productivity, cost reduction a as it relates to the hourly workforce
- Facilitate daily and monthly communication meetings with crew
- Measure, track and report on all operation status metrics
- Utilize appropriate leadership styles and methods in guiding workforce towards task accomplishment, work quality/skill improvement, and engagement
- Understand and administer handbook policies assure production activities are in compliance with company policies and procedures
- Drive high standards for facility cleanliness and conduct safety audits
- Ensure that all product is of high quality
- Set continuous improvement targets
- At least 3 years warehouse, production or manufacturing experience required
- At least 1 year lead or supervisory experience required
- Proven leader of a production team
- Detail oriented, excellent problem solver
- Strong analytical, verbal, and interpersonal skills
87
Supervisor Production Resume Examples & Samples
- Actively promote plant safety and environmental programs and procedures that are in compliance with corporate and regulatory requirements
- Fully implement and maintain SQF 2000 Certified System requirements, including training verification, within area of responsibility
- Actively promote adherence to plant quality system, sanitation, GMP and HACCP standards to achieve a finished product within quality control specifications
- Manage staffing levels to current labor contract / labor standard requirements
- Keep management informed of the status of production and promptly notify appropriate member(s) of management of issues impacting food safety, food quality, or production
- Three (3) or more years of leading employees in a manufacturing environment, preferred
- Experience in a food production/packaging environment, preferred
- Experience working with Continuous Improvement methodologies, preferred
- Able to use MS Office programs (Word, Excel, PowerPoint, and Outlook)
88
Supervisor Production Resume Examples & Samples
- Train, provide guidance, and counsel employees in a manner that assures maximum development and utilization of talent
- Achieve production standards in a safe, efficient manner while maintaining quality and sanitation standards
- Operate within established quality standards to maintain lowest possible held, repacked or dumped product
- Assure that departmental safety meetings are being implemented
- Direct the Production/Quality employees, schedule weekend work, overtime, clean-up or regular production
- Complete necessary reports including Quality accurately and in a timely manner
- Communicate upward, laterally, and downward all pertinent and necessary information
- Facilitate all Quality labs and equipment up-keep, purchase and replace equipment, Quality supplies and distribution as needed
- Achieve correct daily product cuttings, test runs on product and equipment while gathering data for projects
- Facilitate corporate investigations, concerns, consumer complaints and foreign material documentation
- Coordinate equipment malfunctions with the Maintenance Department to minimize downtime
- Be familiar with cribbed product in cold storage and insure available dry supplies to gain optimum results. Utilize bulk product as the ability to do so arises
- Know the status of product in production at all times
- Guide the efforts of clean-up and paint crews in a safe and efficient manner during shutdown
- Communicate McCain goals, MCE philosophy and objectives to the employees
- As a member of the leadership team at the facility, your participation in the continuous improvement process is expected. This includes taking an active role in process improvement initiatives, employee training and upgrading your current skill base
- Must be able to have flexible work schedule working nights and weekends as needed in production
89
Deboning Supervisor Production Resume Examples & Samples
- Oversee and assist Production Supervisors with supervising and training employees while providing an environment for employees to achieve maximum quality and productivity performance
- Work with Quality Assurance ensuring a food safe and sanitary environment within specifications and USDA requirements
- Optimize profit reducing costs with continuous improvement activities through employee involvement and positive leadership
- Perform all other duties as assigned
- 1 – 10 salaried Production Supervisors and indirect responsibility for 100+ hourly production employees
- High school diploma or equivalent AND a minimum of 4 years’ relevant experience in a similar manufacturing environment; OR Associates Degree in a relevant discipline AND 2 years’ relevant experience in a similar manufacturing environment
- Minimum 2 years’ leadership and/or supervisory experience of 20+ persons
- 5+ years’ experience within the food manufacturing industry
- Working knowledge of poultry processing, food safety regulations, OSHA guidelines, GMPs and HACCP
- Demonstrated leadership skills and abilities
90
Supervisor Production Operations Resume Examples & Samples
- Supervise operatives in day to day operations by spending at least 50% of available time interfacing with employees to ensure that every product unit is of high quality and exceeds all the Company’s current Good Manufacturing Practices (cGMPs)
- Ensure that production schedule is met by distributing workload in accordance with changing priorities
- Ensure sterile production operations are properly controlled and regulatory compliance requirements are met by ensuring batch documentation is accurate, Standard Operating Procedures are accurate and personnel training is current, critical documentation templates are accurate, equipment is in good repair and current calibration, and high standards of housekeeping are maintained in all areas of responsibility
- Prepare planners for all personnel and evaluate personnel performance. Provide feedback for continuous improvement. Assist with hiring and disciplining staff as required. Maintain a work environment with fosters teamwork and supports the Company’s Continuous Business Improvement Process
- Support the company’s safety program to maximize safety awareness and provide a safe work environment
- Evaluate /solve production problems by reviewing the area of concern, developing potential solutions, technically evaluating or testing the solutions, and preparing summary reports/recommendations for management
- It is the responsibility of each employee to work in a safe and responsible manner in order to create an injury-free and incident-free workplace
- Comply with all job-related safety and other training requirements
91
Supervisor, Production Resume Examples & Samples
- Ability to prioritize and organize work based on demand
- Oral & Written communication skills up to high school level
- Reading comprehension skills up to high school level
- Math skills – basic arithmetic, addition, subtraction
- Reading comprehension skills
- Ability to work safely and adhere to safety guidelines in a warehouse environment
- Ability to manage a team of associates
- Ability to work independently or collaborate in a group environment
- Ability to be flexible/multi-task based on workflow demands
- Ability to maintain reasonably reliable attendance
- Ability to read, write, speak, hear, see, think, communicate, concentrate, learn, and work
- Personal computing skills including PC based applications (Office, Excel, Word and Outlook programs)
- Ability to supervise the work of others
- Knowledge of manufacturing safety procedures and processes to include OSHA guidelines and practices
- 2 Years experience in a supervisory position within a print production environment, or comparable management experience
92
Supervisor Production Processing Resume Examples & Samples
- Oversee all CHPP operations across the site to ensure production and coal quality targets are achieved
- Guide and support a small team of operators working towards operational excellence in terms of safety, productivity and culture
- Identify improvement opportunities and work collaboratively with other departments to ensure efficiency and production is maximised
- Ensure data integrity, safety, improvements and production are managed appropriately in management systems for reporting and execution purposes
93
Supervisor Production Resume Examples & Samples
- Promote safety throughout assigned work area
- Ensure proper staffing before start-up of production line, and oversee job rotation facilitating ergonomics
- Supervise, coach and train employees, providing professional development through ongoing feedback concerning strengths and areas in need of improvement
- Establish and adjust procedures meeting production schedules, production efficiencies, and budget objectives
- Plan and implement process improvements
- 30 - 100 hourly production employees
- Minimum 1 year leadership and/or supervisory experience of 20+ persons
- 3+ years’ experience within the food manufacturing industry
- 3+ years’ supervisory and/or leadership experience
- Proficient knowledge of production processes, general line maintenance and staffing
- Demonstrated success building effective teams with proven ability to lead by engaging and motivating a team and influencing an organization
- Effective interpersonal communication skills sufficient to communicate and interact effectively with all levels within the organization
- Ability to work in fast paced environment with multiple priorities
- Manage multiple tasks and projects simultaneously and prioritize work accordingly
94
Supervisor Production Resume Examples & Samples
- Manage production process and employee performance, providing positive and/or corrective feedback
- Review and ensure reporting requirements are fulfilled in a timely manner
- Bachelor’s Degree in a relevant discipline from an accredited institution
- 5+ years’ supervisory and/or leadership experience
95
Supervisor, Production Resume Examples & Samples
- Creating and maintaining staffing plans
- Responsible for selection, hiring and training of direct reports
- Trains, coaches and motivates employees to maintain and develop the skills necessary to meet and exceed production goals
- Develop and execute daily work schedules
- Communicates production goals to operators in area of responsibility, and provides resources and motivation to meet or exceed goals
- Accountable for meeting production expectations through safe operation in accordance with established procedures and within specified process settings
- Conducts and documents effective safety meetings at required intervals
- Review and update safety and environmental employee awareness training plans
- Coordinates communication of Engineering Change Notices, Test Approvals, and engineering and maintenance projects to direct reports
- Serves as focal point of contact to coordinate all projects, tests and process improvement work in the assigned process area
- Assists in the coordination of team based activities that result in waste elimination or added value
- Assist Sr. Production Supervisor in the department performance and vertically integrating all shifts into one cohesive team
- Ability to solve problems independently
- Ability to read and write through various means of communication
- Computer skills with the ability to manage different types of electronic data files
- Associates Degree in Manufacturing, Business Management or Engineering preferred
- Minimum 2 years experience in manufacturing environment
- Experience with Microsoft Excel and Word
- Good communicator with the ability to work in a manufacturing environment
96
Supervisor, Production Resume Examples & Samples
- Supervises the daily operations of the team, including but not limited to: establishing mutual goals, assigning tasks, and maintaining schedules
- Administers company policies, processes, and procedures that directly affect subordinate employees and the workflow unit. Recommends changes to unit or sub-unit policies
- Decisions impact work unit operations; usually limited to “how to” execute within defined processes
- Frequently interacts internally with subordinates and other supervisors and functional peer groups. Interaction normally requires the ability to gain cooperation of others, conducting presentations of technical information concerning specific projects or schedules and basic problem resolution
- External interaction is typically with suppliers, vendors, and/or customers. May work with external companies or vendors to resolve routine problems and/or facilitate work flow
- Drives improvement and change by executing on key business initiatives, promoting employee engagement, and acting as a continuous improvement leader
- Promotes a patient first quality culture with production team members
- Executes projects to improve efficiency and yields
- Acts as Back-up Production Manager, when he/she is absent
- Minimum 2 – 3 years of related experience in a Senior/Lead level role; 1 – 3 years of experience as a supervisor (external hire) preferred
- Establishes and promotes a work environment that supports the patient centered quality system
- Excellent computer skills required including Excel, Word and PowerPoint
- Experience in regulated environment highly preferred
- Excellent Communication/Presentation Skills, solid reporting writing skills
- Knowledgeable in SAP, GDP, Production Scheduling, PQTS, ComplianceWire and basic computer operations Microsoft excel Word, PowerPoint, etc
- Must have knowledge of the Fresenius product line
- Reads written job procedures and write required test results
- Effective communicator verbal and written
- Experience in production planning
97
Supervisor, Production Resume Examples & Samples
- Supervise daily operations in a fast-paced and continuously changing production – warehouse environment
- Compile department productivity statistics on a scheduled basis
- Train and schedule full-time, part-time, and temporary warehouse personnel
- Coordinate daily departmental activities
- Ability to operate department equipment, i.e. material handling equipment; such as the forklift and pallet jack
- Complete departmental work as needed
- Project and maintain proper staffing and make recommendations to management
- Monitor inbound warehouse inventory and the flow of product to the processors
- Coordinate and oversee the processing of disposition product with Manager
- Maintain high standards for safety, security, and quality practices in the work environment
- Work in conjunction with systems support on daily upkeep and maintenance of computer system
- Monitor opening, closing, and breaks to insure proper compliance by all employees
- Establish and maintain departmental production standards, and maintain established quality and accuracy levels
- Operate facility in strict accordance with all SOP’s
- Report all customer issues to Management and/or client services in a timely manner
- Monitor employee performance and make salary recommendations
- Perform client presentations/warehouse tours in conjunction with Manager
- Report all attendance variances for employees in accordance with Inmar Reverse Logistics’ attendance policy; approve time off for department employees while considering departmental production needs and policies
- Maximize department performance by effectively interviewing, selecting, training, appraising, coaching, and counseling employees
- Discipline employees in conjunction with Manager and/or the Great Teams! Department
- Maintain accurate, factual, and thorough employee performance and attendance records, and documentation of counseling/coaching exchanges
- Contribute to employee development by providing training, coaching, and promotional opportunities
- Ensure that deadlines are met by monitoring and directing department activities and making adjustments in staffing and priorities
- Update and maintain all manuals, forms, and files associated with department operations
- Responsible for providing employees with training/business updates as needed
- Associate degree in Business Administration, Management, Accounting, or Finance; or High School diploma or its equivalent with a minimum of one (1) year managerial/supervisory experience in the pharmaceutical, logistics, manufacturing, trucking, or warehouse industry; or any equivalent combination of experience and training that provides the required knowledge, skills, and abilities needed to perform the responsibilities of this position
- Proven interpersonal and communication skills, and the ability to delegate and prioritize work
- Working knowledge of computers and programs specific to operations and operations reporting including MS Office (Excel, MS Word)
- Knowledge of warehouse safety and security practices
- Ability to package, label, load/unload Hazardous Materials and Hazardous Waste, sign Hazardous Waste manifests
- Ability to perform the functions of a hazardous waste generator, including but not limited to, identification, sorting, packaging, segregating, labeling hazardous waste generated from daily operational activities
- Ability to work under time pressure and meet production goals
- Ability to assist other operations within the warehouse, as needed and if applicable
- Ability to meet set production and quality goals and follow standard operating and safety procedures
- Ability to work in a non-climate controlled environment
98
Supervisor, Production st Shift Resume Examples & Samples
- Responsible for process improvements
- Responsible for procedures and written content of those procedures in the SOP’s
- Responsible for the quality, efficiency, and timeliness of outputs
- Ability to obtain comprehensive knowledge of cGMP’s and accepted industry standards
- Must possess strong reasoning skills, and the ability to make sound decisions based upon data
- In the event of a processing deviation or non-conformance, must be able to effectively sort through data and interview involved associates to determine both the nature of the event, plan the most appropriate corrective action, and to develop a plan to keep similar instances from occurring in the future
- This associate will be responsible for implementing and training the group over changes that were made as a result of the actions taken in the bullet above
- Ensure compliance with safety guidelines and proper operating parameters
- Understanding of pharmaceutical operations or manufacturing operations preferred
- GMP experience is preferred
- Experience writing and updating standardized working procedures is required
- Strong communication and team skills are required
- At least intermediate level skills in Microsoft office are required
- Proven ability to effectively operate in a maxtrixed organization is preferred
- Experience in the contract pharmaceutical industry preferred
- Experience with Lean Manufacturing, 5S, and Continuous Improvement is preferred
99
Supervisor, Production Resume Examples & Samples
- Manage scheduled priorities and capacity to achieve the highest customer service level
- Monitor production levels, direct labor utilization, and component usage; prepare activity reports
- Achieve departmental goals and drive results through effective communication, collaboration and accountability
- Dynamic and analytical approach to problem solving and identification, solution and efficiency improvements
- May be required to handle containers of hazardous waste
- Candidate must be able to work on any of the three shifts (day/evening/night)
- Knowledge of MS office and SAP applications preferred
- Required to have and maintain a good attendance record
100
Supervisor, Production Resume Examples & Samples
- Hold team accountable for safety, behavior, housekeeping, teamwork, and professionalism
- Supervise the “production work” components of the Front Line Planning & Scheduling business process
- Carryout tasks as assigned by the Superintendent or his/her designate to achieve the desired results within an agreed upon timeline and end state
- Work within budget, guidelines and standards to execute Safety and Production Plans as established by the Superintendent or his/her designate
- Work with the team to develop a truly collaborative workplace environment
- Foster a climate of safety, mutual trust, and respect among all members of his/her team
- Work collectively with peers and cross functionally with colleagues in engineering, geology maintenance, and services to achieve the objectives of the mine
- Request training in skills development where required and communicate needs to the Superintendent
- The ideal candidate will have a minimum of 2 years of progressive experience
- Ability to decipher and prioritize multiple tasks
- Hold people accountable for working within boundaries of SafeProduction
- Verbal and written communication, the candidate must be able to accurately inform, capture interest and gain support in a clear and concise manner
- Health safety and environment, the Candidate must be able to recognize, prioritize, and understand the controls required to mitigate risks in the workplace
- Judgment, the candidate must be able to consider the situation, the issues and the people involved. This involves identifying, defining and analyzing problems or situations. It also involves the use of reason and the formulation of viable solutions and potential improvements
- Courage - must be able to demonstrate a reasonable trust in personal abilities
- Business sense - must be able to use the formal and informal technical and human resources systems and contacts, including supervisors, managers, departments, etc., to achieve needed results
101
Supervisor, Production Resume Examples & Samples
- Manage the conversion of raw materials into finished goods
- Hourly associate management – accountable for daily management of all those listed in organizational structure, inclusive of: timecard management, dealing with absenteeism, staffing re-arrangement & scheduling, assigning work, giving direction based on production activities, managing performance expectations and giving appropriate feedback, as well as providing leadership and direction
- Ensure that safety and quality standards are met, including direct reports in Production, as well as indirect reports in Maintenance, Quality, and Distribution Centre
- Develop the skills and knowledge of an assigned group of Production Associates through formal training, and regular coaching
- Monitor, optimize, and report shift performance (equipment and staffing) in the areas of Safety, Quality, Schedule Conformance and Cost
- Lead continuous improvement initiatives through Operational Excellence
- Adjust raw material delivery schedules (non-day shifts only) as required by plant performance
- Interpret and administer the Collective Agreement
- Respond to Grievances at Step 1
- Special Projects as assigned
- Minimum 2 years of manufacturing related experience
- Previous experience managing people
- Computer skills required – SAP, MS Word, Excel, Access, email
- Previous experience processing timecards using an automated time and attendance system is an asset
- Must be willing to work shift work as per business requirements
- Must be willing to work overtime and weekends as required to support business needs
- Some experience in Labour Relations and working with under a Collective Labour Agreement
- Project Management skills are an asset
- Must have working knowledge of relevant legislation (i.e. Employment Standards Act, Occupational Health and Safety Act)
- Working Knowledge of Quality Standards & Systems
- Working Knowledge of all Plant Systems & Processes (e.g. Refrigeration, Compressed Air, Production Equipment, Cleaning Equipment)
102
Supervisor Production Resume Examples & Samples
- Provide direct reports with leadership, direction, and coaching to achieve work objectives and improve performance and skills
- Provide development to others to support their ability to complete their work responsibilities effectively
- Prepare (e.g., inspect, verify condition) all equipment used in the manufacturing process prior to use in order to ensure smooth, sanitary and safe operation
- Maintain product, packaging and material inventory/availability using demand forecasts, historical orders and software tools in order to support the operations plans and customer demand of the plant
- Check daily production records against sales and operations plans, stock available and forecasts in order to give appropriate early warning to management of potential production issues
- Supports Safety initiatives by pro-actively participating in planned safety events (meetings, LOTO, ergo, etc.) and supporting plant goals of maintaining a safe work environment
- Check daily production records in order to give appropriate early warning to management of potential production issues
- Perform production activities for scheduling set-up, package filling and labeling
- Perform records retention activities using The Coca-Cola Quality System guidelines in order to ensure product quality and customer satisfaction
- Implement process improvement initiatives
- Investigate and identify root causes of any facility safety or security incidents
- Ensure employees adhere to safety and operating policies and Good Manufacturing Practices (GMP) using Company policies and procedures
- Perform other job related duties as assigned
- Good Manufacturing Practices; Knowledge of the basic elements of Good Manufacturing Practices (GMP) in a manufacturing environment and the ability to apply them
- Process Improvement: Ability to collaborate cross-functionally and coordinate efforts around process improvement. Ability to analyze business processes and develop systems-based solutions that will improve current state
- Troubleshooting: Ability to identify and resolve process, system and/or mechanical failures (e.g., dispensing equipment, manufacturing equipment, software tools, supplier network, parts return, order flags)
- Production Management: Knowledge of the principles of production management in order to effectively communicate and manage change in a production environment
- Equipment Evaluation: Ability to assess gaps in design and performance of equipment (e.g., manufacturing plant processing equipment), design corrective actions, and make basic corrections and repairs. Includes the ability to oversee trouble-shooting, commissioning, repair, removal and improvement of equipment
103
Supervisor Production Resume Examples & Samples
- Possess a high level of critical thinking skills and be able to manage strategically and manage operating priorities to attain desired production outcomes
- Leverage interpersonal skills and leadership traits to inspire and motivate the staff assigned to your area of responsibility
- Plan and establish work schedules and assignments. Assist in production sequence planning to meet production goals and provide superior customer service
- Manage departmental objectives and operate to plant performance KPI’s
- Complete and analyze weekly departmental performance reports
- Manage, document, and implement new and improved processes, and train staff for effective execution
- Ensure team members take scheduled breaks and lunches, and finish shifts on time
- Address and correct employee performance issues promptly and effectively
- Manage and execute the training of team members on Department and Earthbound Farm policies and procedures
- Ensure employees work in a safe manner, that equipment is properly maintained to operate safely, and that hazards are promptly identified and corrected
- Monitor and maintain department housekeeping, ensuring audit and inspection readiness at all times
- Inspect materials, products, or equipment to detect defects or malfunctions. Request materials, supplies, equipment parts, or repair services
- Communicate any process deviation or product contamination issues to Production and Quality Assurance management
- Participate in daily Operations staff meetings and weekly tailgate meetings
- One (1) to three (3) years relevant supervisory experience in a large-scale Manufacturing environment required
- Ability to speak, write and read in the English language (i.e. digital displays and written documents such as safety rules, operating and maintenance instructions and procedure manuals); Bilingual/Bi-literate English and Spanish skills preferred
- Must be willing and able to work in extremely cold temperatures (34-36 degrees F) and wet conditions
- Up-to-date knowledge of State and Federal food safety regulations, Good Management Practices (GMP) and Hazard Analysis and Critical Control Points (HACCP) programs
- Hazard Analysis and Critical Control Points (HACCP) certification a plus
- Computer skills – Microsoft Office skills (Excel, Word, PowerPoint, and Outlook)
- Knowledge of Kronos Workforce Timekeeper a plus
- Knowledge of Warehouse Management Software a plus
104
Supervisor Production Resume Examples & Samples
- Must adhere to the blending and packaging schedules, with focus on safety and quality standards
- Manage personnel and payroll administration functions
- Manage line efficiencies, key performance indicators and LIS down time
- Manage processing, blending, tank farm receiving operations
- Manage special projects or new installations, as assigned
- Monitors the production filling and packaging process; makes periodic checks and adjusts equipment
- Monitors work practices according to standard operating procedures
- Ensures equipment is in working order and that working conditions are safe at all times
- Verify the readiness of the production line at start-up and supervise package and flavor changeovers
- Manage overall package and product quality to ensure all standards and specifications are met
- Manage GMP and Plant Sanitation
105
Supervisor, Production Resume Examples & Samples
- Lead and manage a staff of ~40 technicians including all performance management related tasks
- Responsible for assessing and vetting the appropriate skillset needed
- Identify training needs and developing training programs
- Accomplish production results by communicating job expectations; planning, monitoring, appraising job results
- Maintain work flow by monitoring steps of the process; setting processing variables; observing control points and equipment
- Initiate and foster a spirit of cooperation within and between departments
- Continuously improve process and manpower efficiency, utilization and productivity
- Minimum of 6 months in a leadership position leading a team of at least 15+ technicians
- 3 years of experience in the manufacturing of aerospace hardware
- Experience bringing teams and processes from development to production
- Experience with applying lean manufacturing principles
- Safety training and/or safety certifications
- Lean manufacturing training and experience
- Experience monitoring, tracking and continually improving the total cost equation
- Experience with applying lean manufacturing principles, efficiency methods
- Experience solving manufacturing problems related to incapable processes and or designs
106
Supervisor, Production Resume Examples & Samples
- Effectively communicate and motivate the workforce to deliver the company’s goals and objectives
- Continuously improve process and manpower efficiency, utilization, and productivity
- Lead and manage a staff of mixed skilled technicians including all performance management related tasks
- Assess, implement, and obtain, the safest work environment possible
- Identify and set-up of training programs
- Accomplish production results by communicating job expectations, including planning, monitoring, and appraising job results
- Maintain work flow by monitoring steps of the process, setting processing variables, observing control points and equipment, monitoring personnel and resources, and studying methods
- Develop and implement cost reductions, and processes and efficiency improvement measures
- 1 year of experience with applying lean manufacturing principles and efficiency methods
- SQL experience
- Experience leading/closing cross-department process improvement projects
- Pressure vessel production experience
- Filament winding experience
- Spin forming experience in a production environment
- Experience bringing teams and processes from development to mass production
- Demonstrated experience and ability to read, interpret, and follow schematics, engineering, and layout drawings, mechanical assemblies, mechanical drawings and parts lists
- Ability to adapt to constantly changing work assignments and fast paced work environment
107
Supervisor Production MPU Pa Resume Examples & Samples
- MSc in (Bio) Engineering or Sciences or BSc with minimum 5 years’ experience acquired from pharma production environment
- Strong command of English and/or French and a willingness to achieve fluency in both
- Work experience from industrial/production environment
- Knowledge in processes and biopharmaceuticals technologies
- Basic understanding of GMP
- Supervises / Manages day to day vaccines operations (Bulk, Formulation and Filling) in a multiple products environment
- Ensures compliance of the operations with GMP and Authorities requirements. Monitors quality of the production in close collaboration with QC and take corrective actions when necessary. Responsible to implement the Operational Excellence Process in
108
Supervisor Production Resume Examples & Samples
- Bachelor's degree in a technical mining related discipline with at least one summer internship experience (or equivalent) working in a mining or industrial environment
- Knowledge of supervisory methods and techniques
- Ability to communicate effectively, both orally and in writing
109
Supervisor Production Overburden Resume Examples & Samples
- A background in leading a large team in a frontline supervisory capacity
- Experience in supervising fleets of equipment including 600t excavators, 4100 Shovels and Ultra-Class Trucks
- Sound MS Office skills
- The collaboration skills to work across various stakeholders to ensure overburden activities are performed in line with the mine plan
110
Associate Supervisor, Production Operations Resume Examples & Samples
- Engages a wide range of advanced tasks which include audio and/or video production assignments that may include training and have expectations including any of the following
- Expertise and highest standard of Master Control functions, (e.g. setting up, controlling and monitoring TV Production equipment to transmit live and taped programming, commercials and network branding graphics) Comprehensive experience with integrated automation systems including, but not limited to; managing files, troubleshooting error messages and delivering content
- Providing expert levels and highest standard of Technical Directing functions, e.g. operating video switchers, implementing sources, creating displays, interfacing with external devices, creating user and suite preferences. Comprehensive experience of TV Production measurement, formats, and language and full oversight of quality control of audio and/or video inputs and signals prior to and on air
111
Supervisor, Production Resume Examples & Samples
- Direct activity of Production/Assembly personnel
- Work with Leads; manages the function. Ensures that employee communications are occurring in a timely and effective manner
- Monitor and track performance for the Assembly plant for both internal and external customers
- Direct the daily planning activity
- Coordinate with IT department on planning process improvements and system changes as required
- All duties as assigned by the Production Manager or General Manager
- Bachelor’s Degree and 3-5 years’ experience in the Aerospace industry, or the equivalent in training, education and experience
- Minimum 3 years’ supervisory experience
- Customer Service focused with previous experience required
- Working knowledge of JobScope and AS400 systems
- Working knowledge of MicroSoft Office; Outlook, Word, Excel, and PowerPoint is required. Experience with Access software is desired
- Ability to work effectively in a team based environment
- Aerospace industry knowledge required
112
Supervisor Production Resume Examples & Samples
- Oversee the daily operations of the manufacturing and/or production functions for assigned product or process for assigned shift
- Manage the distribution of staff’s work loads and assignments. Direct staff’s work activities
- Manage costs to achieve margin objectives
- Ensure the appropriate manpower and supplies are available to complete work assignments
- Review in progress and completed jobs to verify scope of work completed appropriately and safely
- Establish work standards and evaluate staff’s performance
- Hire, counsel, and discharge staff as necessary
- Ensure performance of all work is done in accordance with quality and quantity standards and established safety procedures
- Report any process and equipment problems to management
- Resolve customer issues and complaints
- Ability to use thinking and reasoning to solve a problem
- Ability to communicate in writing clearly and concisely
- Ability to take care of the customers’ needs while following company procedures
- Ability to pay attention to the minute details of a project or task
- Ability to make decisions or take actions to solve a problem or reach a goal
- Ability to complete assigned tasks under stressful situations
113
Supervisor Production Resume Examples & Samples
- Experience leading a team and working in a supervisory capacity
- Understanding of an open cut mining environment
- Exposure to production execution preferably supervising bulk dozer push
- Dewatering and earthworks experience is highly preferable
114
Supervisor Production Resume Examples & Samples
- Supports without hesitation General Plant Safety (priority #1), Food Safety, Food Defense Initiatives and Good Manufacturing Practices with an understanding that these are absolutes
- Ensures product quality by utilizing data analysis tools, Plant Teams and outside resources
- Review and input dough and wrap schedules into quality system to obtain optimum shift productivity
- Generate reports through quality system to measure daily production against Plant goals
- Review production conformance reports to ensure associates are adhering to standard operating procedures
- Coordinate schedules with sales and shipping departments and adjust accordingly to maintain a constant production flow
- Drive quality improvement and process waste elimination through functional and shift team leadership
- Report accurate counts to office staff for tracking labor, waste and damaged product on a daily basis
- Ensure production lines are adequately crewed with qualified associates to complete each scheduled order
- Enforces Company policy pertaining to good manufacturing practices and safety standards