Maintenance Superintendent Resume Samples
4.9
(110 votes) for
Maintenance Superintendent Resume Samples
The Guide To Resume Tailoring
Guide the recruiter to the conclusion that you are the best candidate for the maintenance superintendent job. It’s actually very simple. Tailor your resume by picking relevant responsibilities from the examples below and then add your accomplishments. This way, you can position yourself in the best way to get hired.
Craft your perfect resume by picking job responsibilities written by professional recruiters
Pick from the thousands of curated job responsibilities used by the leading companies
Tailor your resume & cover letter with wording that best fits for each job you apply
Resume Builder
Create a Resume in Minutes with Professional Resume Templates
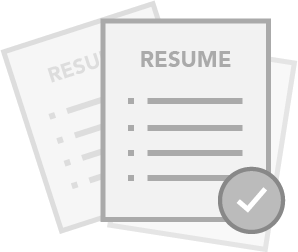
CHOOSE THE BEST TEMPLATE
- Choose from 15 Leading Templates. No need to think about design details.
USE PRE-WRITTEN BULLET POINTS
- Select from thousands of pre-written bullet points.
SAVE YOUR DOCUMENTS IN PDF FILES
- Instantly download in PDF format or share a custom link.
RD
R DuBuque
Reina
DuBuque
31713 Yundt Station
Detroit
MI
+1 (555) 520 3857
31713 Yundt Station
Detroit
MI
Phone
p
+1 (555) 520 3857
Experience
Experience
Houston, TX
Maintenance Superintendent
Houston, TX
Bruen, Schaden and Hilll
Houston, TX
Maintenance Superintendent
- Manage talent development and succession planning for staff, including team development and building/maintaining an engaged workforce
- Monitors repairs through systems and controls to ensure work orders and requests are executed in accordance to established work flow
- Assist in developing plans for engineering improvements
- Prepares work schedules. Makes work assignments to subordinates
- Monitor and help to identify continuous improvement opportunities to enhance the overall maintenance work process and improve cost effectiveness and efficiency
- Identify/prioritize/provide resources in an area to assist the manager to meet the annual operational plan and budgetary commitments,
- Ensures work performed by external service providers is in support of objectives, responsibilities, and contractual agreement
Philadelphia, PA
Maintenance Superintendent Qngr
Philadelphia, PA
Roob-Thiel
Philadelphia, PA
Maintenance Superintendent Qngr
- Monitor maintenance practices and the continuous improvement program with work instruction updates and development with the Training Coordinator
- Provide monthly reports to management on maintenance activities, team performance and customer issues
- Work with the Mobilisation team and provide support in all relevant depot and outstation design reviews and discussions
- Provide supervision of the A&M Services staff
- Monitor configuration management of the fleet for correctness
- Ensure Asset Management principles are adhered to and maintenance information recorded to a high standard in Maximo
- Implement and maintain operational initiatives
present
Detroit, MI
Case Ready Maintenance Superintendent
Detroit, MI
Kuhn-Christiansen
present
Detroit, MI
Case Ready Maintenance Superintendent
present
- Provide ongoing coaching to assist with development of maintenance staff
- Oversee that all computers and interface hardware (scales, scanners, etc.) are functioning properly including site telecommunications systems
- Ensuring the pro-active day-to-day safe and efficient maintenance, upkeep and repair of the facility by managing the day to day maintenance work
- Good working knowledge of Word and Excel
- Ensure workflow processes are followed; ensuring maximization of maintenance labor and resources
- Manage work quality
- Oversee failure maintenance and follow up work: Support the general processes and policies laid down by the maintenance department as well as the company policies
Education
Education
Bachelor’s Degree in Engineering
Bachelor’s Degree in Engineering
University of North Texas
Bachelor’s Degree in Engineering
Skills
Skills
- Uses and maintains technical and professional knowledge, shares that knowledge with others, and recognizes/applies new technology in a cost effective manner
- Ability to interpret a variety of technical instructions in mathematical or diagram form and deal with several abstract and concrete variables
- Ability to respond to detailed inquiries, and present information to groups and senior management
- Ability to plan, both short and long range, and ability to react and change priorities on short notice
- Knowledge of applicable safety and environmental regulations
- Knowledge of the bargaining unit Agreement (if applicable)
- Capability to conducts employee performance reviews based on job descriptions to determine competency, knowledge, and contribution of the maintenance personnel
- Ability to establish and maintain a positive and professional working relationship with all individuals
- Strong commitment to quality of product, processes, and service to both internal and external customers
- Excellent technical hands-on skills accompanied with in-deep working knowledge of an industrial environment standards and regulations
15 Maintenance Superintendent resume templates
Read our complete resume writing guides
1
Maintenance Superintendent Resume Examples & Samples
- Planning work priorities for the maintenance group in conjunction with the engineering group
- Ensuring the direction received from the Engineering Manager is followed
- Ensuring the availability, capability and development of competent technical and operational manpower
- Monitoring and providing feedback on systems and recognizing areas of “continuous improvement” and “best operational practices” in industry
- Planning, organizing, leading and controlling the work of daily tasks (planning, scheduling, execution, and close-out) and long term projects in order to meet department targets
- Understanding and interpreting applicable acts and regulations as it applies to the maintenance and services departments
- Managing and controlling of working cost and capital budgets, based on department requirements
- Responsible for the Maintenance department KOIs achievements, monitoring and variance analysis
- Ability to facilitate the development, implementation and continuous improvement of our standard operating procedures by educating, training, monitoring, and proactively coaching maintenance team
- Monitoring of the department budget and long term strategic planning
- Identify potential risk for the prevention of accidents, completing safety /housekeeping inspections, and resolving safety issues
- Managing outside trades/contractors performing jobs at MSS
- Ensure mutual collaboration with all MSS personnel
- Excellent mechanical, electrical and PLC working knowledge
- Solid computer skills required: proficiency in Microsoft Office, AutoCAD, MP2 and other related maintenance software
- Extensive strategic experience in leading medium size teams in an industrial maintenance environment with strong understanding of maintenance facility flow and maintenance facility management
- 8 to 10 years of relevant experience in a leadership position as maintenance superintendent or maintenance manager combined with excellent interpersonal, analytical, problem solving and team building skills
- 10+ yrs experience as a Journeyman: Millwright, Electrician, Machinist or Maintenance Engineering
- 5+ year experience working in JIT and unionized environment
- Proven ability in safety management, leadership, employee coaching and development
- Ability to prioritize of maintenance tasks, work orders, optimum downtime windows, and necessary lead times
- Experience overseeing the work to be performed and determining the best way to accomplish it
- Capacity to confirm that maintenance personnel are adequately trained, equipped, and motivated so that maintenance programs can be accomplished in a safe, timely, and cost-effective manner
- Experience with spare parts management and purchasing
- Demonstrate leadership skills to encourage and influence behavior and decision making
- Capability to conducts employee performance reviews based on job descriptions to determine competency, knowledge, and contribution of the maintenance personnel
- Ability to multitask, work under pressure and work flexible hours when required
- Self-started who can work within a team environment
- Experience with plant turnarounds and shutdowns
- Excellent technical hands-on skills accompanied with in-deep working knowledge of an industrial environment standards and regulations
2
Maintenance Superintendent Resume Examples & Samples
- 30% Leads the deployment of maintenance related Reliability Excellence activities across the plant and ensures the reliability culture is foundational to operations. Enforces common reliability processes and metrics (focus on reliability improvement, eliminating the root-cause of reliability problems, etc) to achieve targeted results from continuous improvement practices, and validates the importance of Reliability Excellence through key successes (i.e. scorecard and metrics control, total cost of maintenance, total cost of ownership, review of compliance audits, etc)
- 25% Supervises and provides coaching to Production Supervisors including coaching Cargill’s core values and guiding principles. Develops planning for future production workforce needs and participates in selection of employees. Responsible for developing strong leaders and a more diverse workforce by seeking multiple approaches to source/attract diverse talent. Implements Plant/BU operational/reliability/safety training programs and controls/monitors employee performance records on a daily, weekly and monthly basis. Accountable for production talent development and responsible for successful training and on boarding of new/transferred employees as well as workforce engagement, recognition, development and coaching. Implements systems and processes to maintain a highly engaged workforce. Holds direct reports accountable for actively addressing engagement issues and for identifying/leveraging best practices in engagement. Applies disciplinary actions when needed
- 15%-Responsible for the facility maintenance budget and for using maintenance and reliability principles to improve the facility costs and productivity
- 15%-Utilizes leadership and expertise in the principles of Root Cause Analysis and Reliability Centered Maintenance to create an environment of continuous, aggressive defect elimination program that drives asset reliability improvement. Reviews, analyzes, and develops conclusions in regards to maintenance/reliability maintenance metrics and performance. Leads and/or supports audit compliances, root/cause analysis processes within the maintenance team, which includes tracking and reporting on established metrics for a more complex site/plant/facility (i.e. Asset Health index; Total Maintenance Cost/RAV; Overall Equipment Effectiveness (OEE); and audits compliance)
- 15%-Manages ongoing maintenance/ reliability related projects (i.e. asset reliability/defect elimination) utilizing a deep knowledge of maintenance and reliability practices and procedures. May directly lead/oversee general project planning, cost estimation and tracking & payback justification. Recommends/approves selection of contractors/vendors. Manages, analyzes more complex maintenance vendor issues and contract administration. Oversees and ensures that reliability design criteria is included and adhered to basis total cost of ownership and reliability requirements
- Bachelor’s Degree OR in lieu of a degree a High School Diploma/GED with minimum 10 years technical experience
- Minimum 7-10 years of combined experience between operations management and project management
- Minimum 3 years of demonstrated supervisory experience
- Demonstrated ability to lead multi-functional teams
- Excellent written and oral communication skills (including the ability to present information to a formal group)
- Demonstrated ability to solve complex technical problems using formal maintenance & reliability techniques to evaluate systems, equipment, and failures
- Demonstrated ability to organize and implement projects that improve the operational effectiveness of an operating facility
- Experience using Reliability Centered Maintenance techniques, Cause Analysis, and Predictive Maintenance technologies (e.g. Vibration analysis, infrared, acoustic emissions, tribology, etc.) to create a proactive work environment that is focused on continuous improvement at best cost
- Working knowledge of OSHA and Environment regulations
- Bachelor’s Degree in Engineering
- Certified Maintenance Reliability Profession (CMRP) certification
- Qualification on Predictive Maintenance Technologies
- 10 years’ experience in engineering or operations
- Working knowledge of Food Safety
- 2+ years’ experience directly supervising maintenance employees
- Prior experience utilizing a computerized maintenance management system to manage maintenance activities
- Experience with continuous improvement tools such as 5 Why analysis, cause/effect mapping, 5S strategies, etc
- Application of precision maintenance techniques
- Familiar with reliability centered maintenance techniques
- Familiar with condition monitoring technologies and planning and scheduling processes to create a reliable plant
- SAP/MAXIMO
- KRONOS
- Informance/OSI-PI, i-Fix
3
Maintenance Superintendent Resume Examples & Samples
- Maintain, foster, and support a safe work environment, safe work practices, and environmental stewardship
- Continued implementation and enhancement of preventative maintenance programs
- Implementation of improvement projects
- Continuously optimize, evaluate and effectively use company and contractor resources and personnel
- Provide economic analysis, cost estimates and submit AFE requests
- Manage the contract warehouse facility
- Responsible for adding to and maintaining an approved contractor list
- Analyze purchases and invoices and identify improvement opportunities
- Handle basic regulatory and land issues as required
- Ensure company policies are upheld to the highest standard
- Review of department AFE’s
- Manage and report project budgets and cash flows
- Review of maintenance procedures
- Evaluation of company and contractor safety practices and performance
- Evaluation of equipment/system failure modes and rates
- Collaborate with other personnel to solve technical problems
- Ensure ongoing training and development of employees
- Participation in emergency response roles and training
- 10 years minimum experience in oil and gas industry
- Proven track record in managing oil and gas operations in a safe and efficient manner
- Knowledge of CO2 EOR operations
- Excellent communicator with the team, operations, and commercial groups
- Able to work in a fast paced environment, frequently under pressure, on multiple tasks
- Well developed interpersonal skills
- Experience in Microsoft applications and well versed in making/generating presentations
- Must be able to work with a team, take direction from supervisors, keep required work schedules, focus attention on details
- Required to carry a company provided cell phone/pager, and be available to respond during working and non-working hours
- Strong background in safe work practices and active participation in safety program
- Self starter and high drive for results
- Leads the maintenance department with an average of 21 direct reports ranging from Supervisors to roustabouts
- Engineering degree or advanced technical degree
4
Maintenance Superintendent Resume Examples & Samples
- 30% - Accomplish maintenance/reliability objectives by supporting/defining work and work practices; support planning/scheduling activities; coordinate work completion; audit work results; direct supervision of 3 maintenance supervisors, 5 maintenance assistant supervisors and 37 hourly maintenance technicians
- 20% - Reinforce the implementation of the Equipment Maintenance Strategies (EMS) in accordance with Cargill’s Asset Health Assurance Standard. Drive the execution of the maintenance management system to assure compliance with the fundamental plant reliability strategies, standards and practices. Ensure that work orders are correctly executed and completed in accordance to the established work flow. Reduce the effects of defects entering the system by improving maintenance procedures using Reliability Centered Maintenance techniques, 5 why, cause analysis, bad actor analysis, etc
- 20% - Achieve operational objectives by contributing information and recommendations to strategic plans and reviews; preparing and completing action plans; implementing production, productivity, quality, and customer-service standards; resolving problems; completing audits; identifying trends; determining system improvements; implementing change
- 10% - Accomplish human resource objectives by recruiting, selecting, orienting, training, assigning, scheduling, coaching, counseling, and disciplining employees; communicating job expectations; planning, monitoring, appraising, and reviewing job contributions; planning and reviewing compensation actions; enforcing policies and procedures; improving engagement
- 5% - Training and motivating employees to adhere to safety practices and procedures
- 5% - Meet financial objectives by forecasting requirements; preparing an annual budget; scheduling expenditures; analyzing variances; initiating corrective actions
- 5% - Update job knowledge by participating in educational opportunities; reading professional publications; maintaining personal networks; participating in professional organizations
- 5% - Liaises with facility management, work force, contractors, community, and local regulators in routine communications
- Minimum of 3 years supervisory experience in a production facility
- Demonstrated decision-maker who easily interacts with others, and who adopts a hands-on approach to leading and motivating a team
- Excellent leadership, interpersonal, organizational, motivational and communication skills
- Knowledge of continuous improvement programs
- Computer Literate, experience in MS Office systems
5
Maintenance Superintendent Resume Examples & Samples
- Proactively work to ensure that all ADM employees, visitors, vendors and contractors understand and comply with the ADM safety policies and procedures
- Support the production departments in the areas of safety and quality, including audit compliance
- Align, deploy and execute the ADM Milling Maintenance and Reliability vision/strategy
- Maintain the production equipment so that it is functioning as designed or expected
- Manage and implement preventative maintenance and reliability activities
- Lead and support root-cause analysis processes within the maintenance team in regards to failures, EDT and execute plan to correct
- Develop, review, and analyze maintenance/reliability maintenance metrics and performance. (Asset Health metrics, Total Mtce. cost, EDT, schedule adherence, planning efficiency, audit compliance, etc.)
- Partner and interface with other departments, contractors, community and local regulators to ensure asset health and reliability
- Assist the production leadership staff in training operations personnel on proper operations, cleaning, lubrication, trouble shooting, and adjustments on the production equipment
- Manage an effective storeroom and spare parts inventory to ensure that needed parts are available
- Coordinate the maintenance program to schedule work with/around the production schedule
- Maintain an effective equipment history, work history, and preventative maintenance program using a Computerized Maintenance Management System (CMMS). Ensure that all maintenance work is documented
- Manage ongoing maintenance and reliability related projects (asset reliability and defect elimination)
- Responsible for people management and development including retention, recruiting and team engagement
6
Maintenance Superintendent Resume Examples & Samples
- Lead the development of maintenance goals, ensure implementation, monitor effectiveness, and take necessary actions to meet overall business objectives
- Set goals for staff, consistent with business and department needs, and hold them accountable for delivering results. Provide coaching and direction to ensure that they successfully meet individual objectives. Track Team Performance for success (KPIs / Metrics)
- Manage talent development and succession planning for staff, including team development and building/maintaining an engaged workforce
- Coach staff and support mutually agreed upon development needs and training opportunities
- Conduct job assignments considering developmental opportunities, train and coach so employees can be successful
- Support the development of reliability targets, consistent with business needs, and recommend necessary actions to achieve committed results
- Ensure that required capabilities, essential skills and precision work practices are maintained for all BASF and imbedded contract maintenance personnel
- Manage personnel items including: performance reviews, compensation programs, discipline, conflict resolution, short and long term disability, accommodation, consistent enforcement of rules and policies, change management, on-boarding of new employees, and engage in effective and clear communication
- Ensure all aspects of the maintenance execution work processes are being followed including notification, prioritization, planning, scheduling, execution, feedback, and reliability
- Ensure all routine, turnaround, and outage maintenance is executed in a safe, efficient, and effective manner
- Manage the work execution of BASF and Contract employees. Ensure work execution productivity (Time on Tools) and first-time repair quality supporting optimized maintenance cost
- Establish and monitor defined maintenance metrics and KPIs
- Ensure the application of all safety rules, assuring Maintenance personnel are aware of and employing safe working practices and promoting safety programs and behaviors
- Monitor accomplishments, validate, and report performance-to-plan in order to show trends and provide analyses with an emphasis on early performance indicators for the site
- Identify continuous improvement opportunities to enhance the overall maintenance work process and improve cost effectiveness and efficiency. Share with other areas and communicate lessons learned. Ensure consistent, use of best practices within maintenance execution
- Provide communication on status of maintenance activities to appropriate stakeholders via reports, and oral and written communications where and when appropriate
- Ensure all master data in the CMMS is maintained
- Develop and implement the maintenance strategy for each plant in the area, in partnership with Asset Managers and technical maintenance leadership
- Implement the reliability strategy for each plant in the area, in partnership with Asset Managers and technical maintenance leadership
- Monitor and help to identify continuous improvement opportunities to enhance the overall maintenance work process and improve cost effectiveness and efficiency
- Define and deliver the required level of maintenance to the operating units working in conjunction with the Asset Managers and technical maintenance leadership
- Recognize the need for and develop outside specialty services contractors
- Understand, champion and implement LEAN activities via role modeling activities, sharing best practices and holding staff accountable
- Serve as a representative to Professional Maintenance Organizations, and local councils
- Serve on BASF regional teams to develop and optimize maintenance execution, reliability, and work processes
- Function as a Technical and work execution consultant for other sites on maintenance execution, reliability, and work process related topics
- BS Degree in an Engineering discipline and 5+ years of manufacturing, maintenance and/or reliability experience or 10+ years of manufacturing, maintenance and/or reliability experience in a chemical/petrochemical or other similar manufacturing operation required
- Broad based knowledge and experience of all maintenance and reliability technical systems and processes
- Ability to communicate effectively with facts and figures along with the ability to influence, persuade and negotiate. Strong interpersonal skills are required in this position
- Deal effectively with the unknown and unexpected
- Work collaboratively with diverse multiple stakeholders, including Production, Engineering, Maintenance, Procurement, Stores, Accounting, Project Engineers, Engineering Managers, Site Leadership Team, Manufacturing Support Services, etc
- Balance priorities across multiple plants and situations within resource constraints, while preserving a maintenance and engineering perspective and intent
- Ability to influence, motivate, and coach personnel and teams in a professional leadership role including the ability to support and affect change
7
Fabrication Maintenance Superintendent Resume Examples & Samples
- 50% Supervise fabrication activities including predictive, preventative and reactive maintenance
- 25% Troubleshooting Plant Equipment Failures/Problems
- 10% Purchasing of all maintenance related items
- 5% Conduct employee development including technical training, EHS training, and PMP process training
- 5% Personally assist in plant repairs and maintenance
- 5% Perform miscellaneous job-related duties as assigned
- BS degree in Engineering or related field OR 2 year technical degree in related field OR equivalent experience
- Minimum of 5 years verifiable experience in maintenance or related areas
- Computer skills including use of CMMS and MS Office
- Ability to work with production and maintenance employees at all levels
- Strong leadership and conflict resolution skills
- Strong Communication Skills -- Oral/Written English
- Previous verifiable experience in the Beef Processesing Industry
- Previous verifiable experience with SAP
8
Intermediate Maintenance Superintendent Resume Examples & Samples
- Accomplish tasks defined by the I.M. Flight Commander
- Advises the I.M. Flight Commander o issues concerning intermediate level maintenance requirements,
- 1· High School Graduate, USAF NCO/SNCO Academy, Bachelor Degree recommended
- Professional / Specialty: General Aircraft Technician course, F15 airplane general course, from the US Air Force
- Total Number of years: 15 Years in Skill Level (if required): 5
- On Equipment of Weapon System or in required Specialty: Must have knowledgeably in all F15 aircraft systems
- Must have Management experience
- Must have good communications skills
9
Intermediate Maintenance Superintendent Resume Examples & Samples
- Accomplish tasks defined by the l.M. Flight Commander
- Advises the l.M. Flight Commander on issues concerning- intermediate level maintenance requirements Modifications, repairs, and problem areas
- Coordinates with Depot Supply, Base Supply, PDM and, all other maintenance organizations concerning the F-15C/D & S
- Monitors daily production and ensures all schedules are maintained
- Attends TCTO and other Maintenance meetings, to ensure continuity between the l.M. Commander and shops involved
- Supervises and directs contractor maintenance efforts where they are most needed IAW mission requirements and OIC direction
- Interface between Contract Employees, RSAF OIC and, Company
- Train RSAF to the 5, 5, 9 level
- Academic: High School Graduate/USAF NCO/SNCO Academy Graduate Bachelor's Degree recommended
- Professional / Specialty: General Aircraft Technician course, F-15 airplane general course, from the
- U. S. Air Force or equivalent studies
- Skill Level 9
- Total Number of years: 15
- Years in Skill Level (if required): 5
- On Equipment of Weapon System or in required Specialty
- Must be knowledgeably in all F-15 aircraft systems
- Must have management experience
10
Maintenance Superintendent Resume Examples & Samples
- 1) Investment planning and procedures involved in the installation of machinery
- 2) Maintenance of machinery, managing its working time and its repair
- 3) Co-ordination of regular and irregular maintenance activities handled by the factory workers
- 4) Preparing and improving the organisation of paper work and stock spare parts, according to the instructions given by the machine suppliers
- 5) Internal and external Maintenance costs controlling - To move actual experience in different / other area
- 6) To buy spare parts, tools, and other components that make up the production machine
- 7) To ensure the functionality of fork lifts, air compressors, cranes and to check the correct use- To check the stock
- 8) To make a maintenance plan (TPM) and create a job book
- 9) To improve the performance of the maintenance operators
- 10) To monitor the supplier to upgrade technical competence, verify alternative product, same quality at lower price / to reduce of spare parts and tools
- 11) Follow the guidelines of safety and hygiene and internal rules of the company
- 5 years experience in similar position
11
Maintenance Superintendent Resume Examples & Samples
- B.S. Degree in engineering with a minimum of 5 yrs of plant maintenance/manufacturing experience
- Excellent interpersonal skills including the ability to work as part of a team
- Ability to work weekends, holidays and respond to callouts on a non-routine basis
- Physical requirements – Must be able to lift 40 lbs, climb ladders and stairs. Walking, bending, stooping is required. Must be able to wear personal protective equipment including the use of a respirator. Must be able to respond to visual and audible alarms
- Good working knowledge of SAP
- Prior supervisory experience
12
Maintenance Superintendent Resume Examples & Samples
- BS in Mechanical Engineering or related preferred and 7-10 years maintenance experience in a supervisory function
- Experience with a maintenance management system, preferably AMMS or Maximo
- Experience developing/improving and managing preventative maintenance program
- Experience tracking maintenance performance metrics
- Strong computer skills including Excel and Word
- Knowledge in equipment reliability protocols
- Knowledge in Capital Job Order execution and management
- Experience in a Union environment preferred
- Equipment reliability
- Understanding process to engage cross-functional teams to solve problems
- Experience in driving culture change
13
Maintenance Superintendent Resume Examples & Samples
- 30% Provide ongoing coaching and supervisory staff development for the maintenance department; identify and effectively manage above and below expectation performers and administer organizational policies and procedures; council employees, ensure employee concerns are addressed, foster an atmosphere promoting feedback and communication; coach maintenance management and hourly personnel in operations, trouble shooting, repair, preventative and predictive maintenance procedures, root cause failure analysis, personal safety, food safety and operational excellence; lead the day-to-day activities of the maintenance area supervisors to ensure efficient and cost effective use of company resources is used to optimize equipment uptime; review area training and crewing needs and ensure that employee training and development provides sufficient craft skills and knowledge; use KPI’s to drive continues improvement
- 20% Ensure that the daily workload is being implemented as per demonstrated best practices, investigate opportunities in a timely fashion and implement corrective actions when needed; provide effective communication to operations and maintenance management relating to equipment operation; ensure correct follow up is applied as needed and equipment unscheduled downtime is reduced to a minimum by effective repairs; ensure normal and emergency coverage is provided in all areas; identify and manage needed outside resources to assist in repairs; drive the “Reliability Excellence” culture by working with Operations to deliver high performance results
- 15% Manage department safety activities and execution of successful safety management program; continue to coach and challenge employees to achieve safety excellence; provide accurate completion of all incident investigations and ensure that root causes are identified and proper corrective actions are implemented; ensure compliance with Cargill's policies and procedures in the areas of personal safety, food safety and environmental
- 15% Manage work quality to ensure all work is completed at the highest standard; ensure all necessary documentation, processes and workflows are used; mentor the hourly training for new hires and ensure the onboarding plan is being followed
- 10% Manage spending through regular review of R&M costs and provide solutions for deviations from targets, monitor departmental budgets, hold self and others accountable for achieving goals and targets
- 10% Communicate, advise and collaborate with operations management of modifications, equipment utilization and equipment repairs in their area; oversee emergency repairs and investigate and analyze asset defects and failures to find and address the root cause to prevent re-occurrence
- 2 or 4 year college degree in engineering or related technical discipline
- 10 years or more maintenance management experience
- Strong mechanical and electrical knowledge and aptitude; training and knowledge of predictive maintenance technologies
- Demonstrated leadership skills of team building, conflict resolution, innovation and change within the work force
- Ability to develop and manage good working relationships with internal departments, contractors, suppliers, inspectors and customers
- Strong organizational, written and verbal communication skills; ability to speak candidly and provide constructive feedback
- Ability to challenge and engage the workforce
- Advanced computer skills (SAP, MS Word, Excel, Access )
- Ability to take off-hour calls and rotate on call accountability with facility staff as necessary
- Working knowledge of SAP or other asset accounting system
14
Maintenance Superintendent Resume Examples & Samples
- Associate degree or higher in Engineering, Engineering Technology or Business Administration
- 7 or more years of General Maintenance experience working within an industrial/manufacturing operation
- 5 or more years of work experience specifically within maintenance supervisory positions – with responsibility for salaried direct reports
- Experience using the following Microsoft Office Software: Excel – (sorting data, creating tables and creating graphs); Outlook – (scheduling tasks, calendar invitations and general professional correspondence); Word – (document creation/editing); PowerPoint – (presentation creation/editing); and Project (creating a project plan, adding tasks, resources and milestones)
- Bachelor degree or higher in Engineering
- Leadership/supervisory experience in a manufacturing operation with focus on Electrical and Reliability Maintenance
- Experience planning, leading and executing major work outages
- Experience in a Pulp & Paper manufacturing operation
- Experience with industrial boilers and pulp recovery operations
- Experience using Root Cause Analysis (RCA)
- Experience applying financial and statistical skills within a manufacturing operation
15
Maintenance Superintendent Resume Examples & Samples
- Address and resolve technical issues relating to mechanical equipment
- Manage the response to completions related to plant or equipment failures
- Organize manpower resources, equipment and material
- Provide technical advice to supervisors and technicians
- Coordinate with construction and commissioning managers to ensure engineering and procurement elements support the handover milestones
- Monitor all ongoing jobs daily and update the progress accordantly to the client as needed
- Maintain strict compliance with Company and Client procedures and guidelines
- Must be strong in static, rotating equipment and piping systems
- Experienced in the refinery or petrochemical industry resolving technical issues relating to mechanical completion
- Working as part of the client team you will supervise the maintenance of equipment during the construction and commissioning phase of the project
- Well organized and proactive with excellent communication skills
- Extensive interpersonal and supervisory skills, and broad knowledge of construction, commissioning and maintenance disciplines to ensure work completion is in compliance with project specifications, codes, standards and procedures
- Proven leadership skills within large organizations
- Maturity of judgment under pressure and ability to resolve problems
- Ability to achieve business results working in a multi-cultured environment
- Assists the business team by providing input to identify key success factors, timing of design, procurement deliverables, and establishing common work breakdown structures
16
Maintenance Superintendent Resume Examples & Samples
- Promotes productivity and teamwork in assigned area with open communication, timely decision making, and use of personal leadership skills to set high standards of performance while providing the direction necessary to achieve that performance
- Promotes and supports the development of technical, leadership, and business skills of employees to carry out responsibilities in a competitive environment
- Provides regular feedback to employees on their performance to allow them to capitalize on their strengths and focus on opportunities for improvement
- Demonstrates behavior that encourages and rewards employee involvement, innovative thinking, adaptation to change, responsible risk taking, customer focus, and continuous improvement
- Ensures development and implementation of assigned area goals, objectives, and initiatives
- Supports and emphasizes importance of safety and environmental programs and ensures regulatory compliance
- Reviews performance with customers/clients and addresses opportunities for improvement
- Ensures all Company resources are utilized in a cost effective manner, estimates resource requirements, monitors expenditures, and reports on performance of assigned area
- Assigns work and holds employees accountable for their performance
- Prepares work packages addressing work to be performed which includes scope, safety and environmental instructions
- Performs field inspections of job sites and work in progress
- Recognizes problems and is proactive in helping to resolve them
- Ensures development, implementation, and monitoring of work plans and schedules in their area of responsibility
- Ensures work performed by external service providers is in support of objectives, responsibilities, and contractual agreement
- Maintains working relationship with employees consistent with personnel policies and procedures, and where appropriate, with the principles of the bargaining unit Agreement
- Coordinates application of internal and external resources to area of responsibility to support maintenance activities, projects, programs, etc
- Maintains a current assessment of the maintenance backlog
- Provides leadership, support, and coordination of maintenance work consistent with the operating requirements of the plant
- Develop and monitor progress of long-range maintenance plans to ensure cost effective maintenance through implementation of predictive, preventive, and cost analysis tool
- Bachelor's Degree in Engineering or a related technical discipline
- Experience with using Work Management Systems
- Prior experience supervising bargaining unit employees
- Understands the processes, systems, assets, resources, key personnel, and business functions of the SBU
- Knowledge of power plant systems and operations, and comprehensive knowledge in the area of responsibility
- Demonstrated effective leadership and personnel management skills
- Demonstrated ability to operate effectively in a team environment
- Ability to effectively communicate (verbal and written) at all levels of the organization
- Ability to establish and maintain a positive and professional working relationship with all individuals
- Ability to use a personal computer and standard business software
- Ability to read, create and follow written policies and procedures
- Ability to understand and use work management systems
- Knowledge of the bargaining unit Agreement (if applicable)
- Knowledge of applicable safety and environmental regulations
- Uses and maintains technical and professional knowledge, shares that knowledge with others, and recognizes/applies new technology in a cost effective manner
- Obtains and applies knowledge of competitive business practices in daily work activities and decision making
- Seeks and understands the customer/client’s needs and focuses on meeting and exceeding their expectations
- Anticipates and accepts changes in the organization and adapts to meet the new requirements
- Committed to making the workplace safe and environmentally sound
- Willing to accept accountability for own decisions, performance, and behavior, as well as the performance of assigned employees
17
Maintenance Superintendent Resume Examples & Samples
- 30% EHS and Food Safety: Be a Safety and Food Safety Champion. Create an environment in which employees go home in the same (or better) condition than they arrived. Actively work to prevent/eliminate hazards that cause injury or illness. Champion safety processes, ergonomic efforts and hold team accountable for keeping their co-workers safe. Champion the elimination of adulterants in our products. Ensure all processes are being followed that help minimize risk to consumers, customers and the company. Ensure compliance with applicable local, state and federal environmental laws and regulations
- 30% Maintenance Management: Ensure effective and efficient maintenance operations through preventative maintenance, work execution, and daily schedule control. Maintain the physical condition and appearance of the facility which reflects the standards of quality and service of our business. Collaborate with other department Manager’s to ensure highest levels of service and plant efficiencies. Develop leaders for Cargill and provide tools and structure for team to meet their operating plan objectives
- 20% Engaged Employees: Be an employer of choice in the community. Create an environment where all employees are expected to be active, contributing members of the business. Hold team accountable to values, principles and goals. Recognize successes and challenge people to be better than they thought possible. Create opportunities for growth and development
- 15% Continuous Improvement: Champion the use of Continuous Improvement to eliminate losses. Leverage maintenance reliability technology and techniques to maximize equipment reliability and longevity
- 5% Capital Planning: Oversee minor capital projects of $100,000 or less. Coordinates with Operations and Engineering on project identification, planning, and execution to achieve business goals. Provides resources to project managers as needed
- Bachelor's degree or higher, associate degree with experience will be considered
- Minimum 5 years manufacturing experience with various roles and progressive responsibility
- Minimum 3 years of direct management/leadership experience (influencing, coaching, managing through others, developing diverse work teams)
- Demonstrated ability and understanding of both mechanical and electrical systems to include PLCs and basics programming
- Demonstrated experience and proven track record in continuous improvement and managing multiple priorities in a fast-paced work environment
- Demonstrated experience in building relationships with internal customers
- Must be able to communicate effectively written, verbal and in presentation with all levels of the business
- Proficient in Maintenance Reliability and Continuous Improvement tools/techniques
- Proficient in Maximo/SAP or similar software
- Must be able to travel 5%. Ability to work varied hours, including weekends and evenings
- Strong team builder and team player (player/coach principle)
18
Maintenance Superintendent Resume Examples & Samples
- Oversee and lead a maintenance team that could include supervision, engineering, crafts and planning personnel to support operations in an area
- Oversee planning and execution of semiannual shutdowns and other projects
- Ensure compliance as it relates to PMs, maintenance documentation, training, quality, 6s, safety
- Provide a positive and equitable working environment emphasizing the Baxter Shared Values – Respect, Responsiveness and Results
- Support and Emphasize the Safety and Quality commitments of the department – make decisions concerning these commitments within the area
- Provide direction of resources in the most efficient and productive manner possible
- Identify/prioritize/provide resources in an area to assist the manager to meet the annual operational plan and budgetary commitments,
- Facilitate, verify, and even conduct appropriate training for employees in the area (including but not limited to GMP, troubleshooting, maintenance skills, and safety)
- Ensure compliance with all GMP rules, specifications, SOPs, and FDA requirements as required
- Commit to employee feedback and developmental process – support Talent Management goals, conduct recognition and disciplinary action for employees, facilitate employee representation throughout the organization
- Submit and/or maintain and distribute reports related to attendance, labor, maintenance metrics, safety, and others as needed
- Demonstrated communication, administrative and strong technical leadership skills with ability to interface well with other departments, and lead effectively and efficiently in a team environment. Solid professional writing skills
- Ability to manage multiple priorities in a manufacturing plant setting
- Good assessment and troubleshooting skills (mechanical, electrical, and process) with demonstrated and proven experience and background
- Good computer skills to include Microsoft Office including Project
- Solid understanding of maintenance systems to include preventive maintenance and CMMS
- Ability to understand regulatory and safety guidelines applicable to the medical / pharmaceutical industry and industry in general. Must have experience and knowledge with Lockout / Tagout and other Safety Programs
- Interact with all levels of personnel to analyze and solve problems related to equipment but also with manufacturing, quality, engineering, and personnel issues
- Knowledge of WCM methods (Lean, Six Sigma, and QLP)
- Ability to respond to detailed inquiries, and present information to groups and senior management
- Have good project management skills and ability to organize many projects and priorities as required
19
Maintenance Superintendent Resume Examples & Samples
- 25% This is a working position in the sheet metal department, under the organization structure of the Facility Maintenance department, and is responsible for the fabrication and installation of all sheet metal equipment and components, in addition to all roof repairs, roofing inspections and roofing inventory as well as welding. It also involves analysis and consulting with the refrigeration department on duct work and air volumes. These operations for the LSU campus encompass more than 475 buildings with a total combined floor space that exceeds over 9,000,000 square feet
- 25% Record Management-Maintains records on roofing and sheet metal work orders, number of people needed to complete projects; size of crew, manpower hour, cost of job (labor and material). The sheet metal and roofing departments are responsible for completion of approximated 500 work orders annually
- 25% This position must interrelate will all departments on campus to perform projects while simultaneously maintaining low job profile in order to avoid undue concerns by facility, staff, students, and the general public
- 10%Material Purchasing-Requisition materials and supplies for in-house sheet metal crews and roofing, roofing contract workers and sheet metal contract workers. Annul estimated budget for all materials and supplies is $150,000 annually
- 10% Oversees sheet metal contractors, time and material. Generates monthly and yearly reports on sheet metal projects
- 5% Oversees the use of standard and special tools and equipment such as circular and square shears, press bar folders, hand brakes, trimming, wiring, burning, and setting down machines, drill presses, embossers, and electric and acetylene welding equipment
20
Road Maintenance Superintendent Resume Examples & Samples
- Accredited colleges and universities include all four-year colleges and universities, and two-year colleges (i.e., community, junior colleges) that meet the accreditation guidelines indicated on the bulletin
- Successful completion of courses in Public Works, Construction Maintenance or Construction Technology from an accredited college or university.**
- Clear and concise verbal and written communication skills
21
Maintenance Superintendent, st Shift Resume Examples & Samples
- Utilize working knowledge of electrical systems, both controls and industrial wiring systems, pipe fitting, plumbing, welding and shop machinery
- Prepare work schedules and make work assignments for subordinates
- Train mechanics on procedures and policies as needed
- Identify areas of opportunity for maintenance processes, and develop solutions to problems as they arise
- Develop Supervisors and Leads throughout the Maintenance Department to be more effective leaders
- Minimum of High School diploma, GED or equivalent
- Minimum of 3-5 years of experience in industrial maintenance
- Strong mechanical and electrical skills
- Strong trouble shooting skills and decision making skills
- Must be able and willing to work 3rd shift
- Must be able to stand for 10 hours in a cold and wet environment
- Cold and wet environment
22
Maintenance Superintendent, nd Shift Resume Examples & Samples
- Supervise employees in installation and repair of mechanical equipment, as well as maintaining equipment and servicingthe plant
- Interpret company policy to members and enforce company policy and practices
- Work with QA to perform Foreign Material investigations
- Develop and Implement Corrective Actions to address Foreign Material Issues
- General knowledge of machinery associated with the industry
- Able to communicate in English, both verbally and in writing
- Ability to create, read, analyze, and interpret reports, technical procedures, and/or governmental rules and regulations
- Knowledge and understanding of Good Manufacturing Practices (GMPs)
- Must be able to grasp, push and pull, and perform repetitive motions
- Must be able to lift and carry a minimum of 75 lbs
- Loud noise levels, requiring hearing protection
23
Maintenance Superintendent Resume Examples & Samples
- Utilizes working knowledge of electrical systems, bothcontroal and industrial wiring, pip fitting, plumbing, welding, shop machinery, sheet metal, hydraulics, pnewmatics, electrical controls and instrumentation to maintain plant equipment at optimal level. Utilizes knowledge of automatic equipment opertion, to include setup, repair and tear down, to maintain plant equipment at optimal levels. Inspects completed work for conformance to blueprints, specifications, and standards
- Interprets company policy to employees and enforces company policy and practices
- Establishes and maintains preventive maintenance programs and procedures. Administers training programs to ensure proper operations, preventive maintenance, and repair programs and procedures
- May direct workers engaged in ground maintenance activities such as mowing lawns, trimming hedges, removing weeds, raking and disposing of leaves and refuse, and snow removal. May supervise custodial services
- Must have working knowledge of PLC's
- Must have working knowledge of electrical systems, both control and industrial wiring
- Must be proficient in the following areas: Pipe fitting,/Plumbing, Welding, Shop Machinery, Sheet metal, Hydraulics, Pneumatics, Electrical Controls & instrumentation, Automatic Equipment Operation (setup, repair, and tear down)
- Must be capable of becoming Haz-Mat team qualified
- Must be highly motivated, self-starter
24
Maintenance Superintendent Resume Examples & Samples
- Estimating costs
- Ordering material
- Tracking time and costs
- Meets with supervisor at beginning and end of shifts
- Monitors daily bagger operations including overfill and piece count
- Education: Extensive post-high school education of training in mechanical maintenance and repair
- Must High degree of human relation skills and ability to deal with several levels of employees in a positive and consistent way
- Ability to plan, both short and long range, and ability to react and change priorities on short notice
- Ability to coordinate and cooperate with others in problem resolution situations
- Skill that provide leadership and motivation to change, both for subordinates and employees that work in subordinate departments
- Strong commitment to quality of product, processes, and service to both internal and external customers
- Applicable licenses and certifications as required
- Possess the ability to understand and follow Maintenance Procedures, Good Manufacturing Practices, HACCP regulations, safety requirements, work rules and all work related procedures
25
Maintenance Superintendent Resume Examples & Samples
- Demonstrate a strong sense of responsibility and accountability in safety programs
- Ensure exceptional safety performance through a trained, caring, participatory culture
- Lead the development and improvement of preventive and predictive maintenance programs to world class practices across the site
- Lead the implementation of effective planning and scheduling practices
- Lead cultural change
- Coach, support, and develop leaders reporting to this position
- Oversee all mechanical, electrical, instrumentation and other tradespersons engaged in installation, repair, upgrade and maintenance activities on the plant site
- Involves the management of people and systems, including hiring, planning work, supervising, evaluating job performance, development of work systems and trade skills/continuity, and conducting salary reviews
- Involves management of, storeroom, mechanical and electrical personnel
- Manage the capital improvement process in coordination with Operations, including the Gate process
- Initiate and manage pool capital projects
- Develop the PDM adder and maintain the skills upgrade process
- Must be flexible to support a 24 X 7 operation, which includes sharing scheduled weekend work and anytime response support
- 5+ years experience in manufacturing or industrial leadership role
- Demonstrated success in developing and leading a maintenance team/organization and achieving business goals
- Strong communication skills and interpersonal skills and the ability to work effectively at all levels in the organization
- Demonstrated ability to manage supervisors and work closely with other superintendents and managers
- Ability to facilitate and lead people through multiple priorities in a changing environment
- Proficient computer skills in MS Office, other windows based programs, and internet skills
- Bachelor's degree or higher preferred, particularly engineering degree
26
Maintenance Superintendent Resume Examples & Samples
- Acts as a champion of the maintenance execution work process in support of the business goals and safe, quality and reliable maintenance services
- Provides overall management of maintenance and operations work orders including creation (as needed), prioritization, release, review of plan and closure
- Direct reports (13 full time): Turnaround Coordinator, Maintenance Coordinator, Maintenance Planner/Scheduler, 5 Instrument & Electrical Technicians, 5 Mechanical Technicians
- Assures and optimizes maintenance execution practices and procedures to achieve cost-effective results, including efficient scheduling of resources, proper training and performance of craft personnel, and high-quality execution of work with a focus on Safety and Reliability
- Leads execution of planned and unplanned unit shutdowns executed by the Maintenance team, including job plans and critical path schedule development, and tracking and closeout activities
- Accountable for execution of major and minor plant turnarounds (TAR Coordinator on the team runs the effort)
- Performs regular review of execution quality and efficiency
- Responsible for implementation and utilization of disciplined maintenance execution practices and standards
- Assists in the development of the maintenance budgets, and in controlling spending through appropriate tracking, forecasting, and adjustments
- Supports the use of high-quality Maintenance and Reliability Key Performance Indicators (KPI’s) along with other input to drive performance and implementation of improvements as appropriate
- Approves and prioritizes maintenance work notifications in EAM to ensure that maintenance is properly directed toward the goals of plant reliability and availability in a cost effective, productive manner
- Responsible for eliminating unnecessary or redundant work and for managing the backlog of approved work
- Communicates daily with the Facility Managers and Shift Supervisors to clarify work priorities and to react to schedule breaks
- Provides troubleshooting support to operations personnel as needed, and works with various departments as required to obtain technical and procurement support
- Participates in root cause failure analyses and in corrective actions for bad actors
- % Overtime
- Maintenance Cost
- Maintenance Schedule compliance
- Maintenance Execution Efficiency
- Emergency Work Order reduction
- Repetitive failures
- Contractor and maintenance personnel safety performance
- Maintenance backlog efficiency
- Work order completion as expected by priority setting
- Minimum 10 years relevant experience in maintenance repairs, engineering and reliability activities, and must have demonstrated strong leadership capabilities
- Key skills include communication, interpersonal relationships, facilitation, influencing, negotiating and the ability to work within a matrix organization
- Successful candidate must be able to develop others and foster diverse relationships throughout the organization
- Must have a detailed understanding of equipment and overall plant manufacturing processes
- Requires familiarity with environmental, safety, and health procedures and issues
- Must have understanding of mechanical and instrument equipment and their maintenance, mechanical integrity, and the inspection process
- Requires familiarity with turnaround execution, maintenance programs, work processes and best practices
- Must have technical competencies of troubleshooting, root cause failure analysis, general computer skills, work planning and estimating
- Must be able to manage multiple priorities, drive issues to completion, and obtain results
- Must be proficient in the use of Microsoft Word, Excel and PowerPoint
27
Maintenance Superintendent Resume Examples & Samples
- Ensures that all work is being performed safely and according to standard operating procedures
- Directs and supervises the maintenance Union personnel by setting work priorities, planning work activities, monitoring progress, following up on maintenance activities on a daily basis and managing administrative duties for time and attendance and other areas of labor relations
- Inspects all jobs and analyzes the operation with respect to potential failure and provides preventive maintenance in these areas
- Regularly conducts safety meetings and coordinates routine safety audits and training of employees
- B.S. in Mechanical Engineering or related field, preferred
- A minimum of 5-7 years of maintenance experience within a chemical manufacturing facility with previous management/supervisory experience, required
- Experience in a Union environment, preferred
- Strong communication and leadership skills required
28
Assistant Maintenance Superintendent Resume Examples & Samples
- Partner with other Maintenance Superintendents in the Eastern Region to successfully complete the agency's objectives
- Prioritize and coordinate the work of the Eastern Regional Crews
- Act as the Superintendent in the absence of the Area 1 Superintendent
- Assist in the implementation and management of the Area 1 Safety Program
- Work with the public, including conducting official meetings
- Provide sound judgment and solid decision making skills to effectively meet and exceed area regional goals
- Ensure proper application of Civil Service rules, collective bargaining agreements, and personnel policies, as well as environmental, safety and other state/federal regulations
- Perform workload planning based on seasonal needs. Evaluate fleet and facility needs
- Conduct budget planning and expenditure tracking
- Monitor and inspect work performed by contractors
- Maintain responsibility for emergency management and disaster preparedness procedures
- Oversee accurate and accountable inventories, including minor capitol (tools) and consumable inventories
- Monitor environmental regulations and ensure compliance
- Coach/mentor/supervise staff and conduct interviews for hiring and promotional opportunities
- Work with a diverse staff
- Conduct investigations and disciplinary actions
- Possess and maintain a valid Washington State driver's license
- Possess a high school diploma or GED equivalent
- Ability to provide leadership to the Spokane Maintenance Area, including mentoring and developing employees' skills for present and future promotional opportunities
- Demonstrated ability to effectively communicate with diverse groups
- Knowledge of basic fleet equipment and types of operation each machine safely performs
- Knowledge of workplace and highway work zone regulations and permitting requirements/processes for encroachment compliance related to environmental, safety and state regulations, including OSHA/WISHA policies
- Intermediate-level ability to operate hand-held data collection devices, laptop computers, GPS, and software associated with the Maintenance and Operations Programs (such as Word, Excel, Outlook, and Data Mart)
- Demonstrated history of ethical standards of conduct, integrity and honesty
- Experience supervising staff and employing conflict management skills
- Experience working with the MUTCD, Standard Specifications, Right of Way plans and Contract Plans
- Possess and maintain a valid Washington State Department of Agriculture Public Operator Pesticide License or must obtain this license within the first six months
- Working knowledge of budget development and expenditure tracking, managing allocations to obtain maximum efficiencies while meeting goals and priorities
- Thorough understanding of Maintenance Accountability Process, Emergency Management Plan, contracting procedures for private sector work and other public agencies, and environmental compliance
- At least two (2) years experience in a position that plays a significant role in administering a program, including management of a biennial budget, budget analysis, directing and/or supporting emergency operations, and monitoring supply inventory
- At least four (4) years experience as a Maintenance Supervisor with hands on experience in all elements of state highway maintenance, including but not limited to, budget analysis, inventory, roadway, drainage systems, roadside/landscape, traffic control, and snow and ice control OR A two (2) year college degree and at least two (2) years' experience as Maintenance Supervisor, as described above
- Experience with integrating workforce safety in all work
29
Maintenance Superintendent Qngr Resume Examples & Samples
- Ensure fleet availability is achieved on a consistent basis
- Provide supervision of the A&M Services staff
- Be conversant with technical facets of the MU for fault finding debates both electrical and mechanical systems
- Lead and schedule toolbox talks and safety committee meetings and action items
- Ensure Asset Management principles are adhered to and maintenance information recorded to a high standard in Maximo
- Implement and maintain operational initiatives
- Organise and direct the service operations team IAW work instructions, check sheets, schedules and quality requirements
- Coordinate plant, equipment and tools to meet services and facility requirements and availability
- Delivering safe and reliable daily Train Services according to the Train Plan
- Monitor configuration management of the fleet for correctness
- Ensuring Depot Asset availability with the Depot Asset Coordinator and supporting certain maintenance elements with the use of and sharing of resources
- Build and maintain a positive team approach to safety culture, quality culture and adherence to QHSE processes and procedures
- Provide the vision, expectations and training in order to build the requisite services team culture and capability
- Monitor maintenance practices and the continuous improvement program with work instruction updates and development with the Training Coordinator
- Work with the Mobilisation team and provide support in all relevant depot and outstation design reviews and discussions
- Build a cohesive team with positive employee engagement and direction
- Ensure compliance with all relevant safety, quality & environmental statutory and contractual requirements
- Provide monthly reports to management on maintenance activities, team performance and customer issues
- Mobilisation of the Technical teams including on-call staff for MU defect rectification
- Relevant tertiary qualifications
- Proven Supervisory experience in a rolling stock maintenance environment (at least 5 years), preferably in a Fleet Maintenance environment
- Demonstrable safety culture experience and approach to continuous improvement in terms of safety, quality and employee engagement
- Competent in forecasting and strategic planning with strong written and verbal communication skills in order to communicate with all levels within the Bombardier and Customer’s organisations
30
Maintenance Superintendent Resume Examples & Samples
- 5-7 years of related experience and/or training
- Ability to interpret a variety of technical instructions in mathematical or diagram form and deal with several abstract and concrete variables
- Ability to read, analyze, and interpret general business periodicals, professional journals, technical procedures, or governmental regulations
- Ability to effectively present information and respond to questions from groups of managers and customers
- Ability to manage conflict with good communication and personnel skills
- Must have the ability to accept and work with constant change
- Must be familiar with FDA GMPs, ISO standards, OSHA, and other state and federal laws
- Ability to plan, organize and prioritize
- Ability to make good judgment calls
- Getting work done through others that are not direct reports
- Motivating others
- Building relationships with other departments
- Interviewing and presentation skills
- Managerial experience
- Strong coaching and development skills
31
Asu Maintenance Superintendent Resume Examples & Samples
- Actively participate in safety programs, promote and enforce safety rules and good housekeeping methods
- Lead the La Porte maintenance team to ensure compliance to the daily/weekly maintenance schedule, maintenance & safety KPI's and area plants requirements
- Minimum of 10+ years in a petrochemical or manufacturing environment with maintenance, and/or operations roles is desired. Prior supervisory experience is a plus. Demonstrated leadership and decision making skills are critical to the position
- College degree in engineering. Relative experience will be given strong consideration in lieu of formal education. Trade school for maintenance and or instrumentation would be desired for those without the formal education piece
- Strong leadership abilities coupled with excellent broad based technical skills and good business sense
- Strong organizational, planning, interpersonal, and communication skills are essential to the position
- Credibility and respect across the organization is important
32
Drainage Maintenance Superintendent Resume Examples & Samples
- Less than 1 year
- 1 year to less than 2 years
- 2 years to less than 3 years
- 4 years to less than 5 years
- 6 years to less than 7 years
- Required Question
33
Maintenance Superintendent Resume Examples & Samples
- Keeps the plant in optimum operating condition
- Supervises and coordinates the scheduling, diagnosis and repairs of plant equipment through subordinates
- Performs administrative duties preparing and maintaining records and writing reports in the areas of maintenance, personnel and work orders
- Takes the lead role of formulating preventive maintenance programs and to keep the plant operating effectively and efficiently
- Works with Division Manager and plant superintendents on the installation of new equipment and maintaining plant equipment in operating order
- Selects and terminates immediate subordinates
- Develops strategic short and long-term plans and objectives to keep the plant operating at optimum efficiency
- Formulates and recommends annual budget
- Coordinates and provides direction and guidance to maintenance personnel
- Provides the Division Manager with reports and information as necessary or as required that will enable him to review the maintenance effort and to provide constructive advice and guidance as to opportunities and adjustments
- Responsible for plant sanitation
- Operates within a pre-set budget
- Orders parts and materials necessary for the plant to stay in optimum operating condition
- Ensures the plant has been properly sanitized, will pass USDA inspection at start-up, and maintains the buildings and grounds
- Coordinates safety items for corrective action
34
Maintenance Superintendent Resume Examples & Samples
- Ensure the on-going office and manufacturing capabilities of the Milwaukee, National Avenue facilities through effective plant, equipment and building maintenance
- Develop, approve and implement capital expenditure projects for the Milwaukee Operations (National Avenue and Orchard Street Facilities). Monitor and track capital expenditures to ensure timely completion within budget
- Develop and implement a strategic plan for Maintenance and Facilities including defining and developing core competencies, evaluating and implementing Reliability Centered Maintenance, etc
- Maintain the plant engineering function to provide accurate data on the physical lay-out of all buildings including power, water, sewer, air, fire suppression, etc. Ensure jointly with the Safety department that all environmental compliance is maintained through proper documentation
- Monitor the availability of plant equipment and status of repair projects to ensure proper attention is focused on critical machine tools
- Review capital projects to ensure tasks are being completed on time and within budget
- Ensure preventative maintenance programs are developed and being followed to avoid unexpected failure
- Develop annual and 5 year capital plans to ensure we are adequately maintaining our capabilities and investing in the right areas to meet growth opportunities
- Evaluate budget status and identify trends. Investigate problem areas or unusual events to minimize the impact to the overall cost of the facility
- Evaluate employee performance, coach and review expectations
- Monitor and evaluate supplier performance and provide feedback both positive and negative
- Participate in safety team meetings. Ensure that safety issues receive immediate attention and are resolved in a timely manner
- Meet with other factory and department managers to ensure all of my departments are meeting expectations, review areas of weakness and identify opportunities for improvement. Develop, monitor and revise department objectives to meet the needs of these other areas
- Monitor industry trends and technology developments to ensure we are maintaining our competitiveness
- Negotiate with suppliers for parts and service on price, delivery, quality, and other commercial terms
- Manage union employee relations through direct communication and feedback, participation in joint union management committees (Safety and Productivity). Prepare for and participate in grievance meetings
- Develop and continue to improve our relationship with the Village of West Milwaukee
- Ensure efficient and proper response on all 1st responder and emergency calls
- Review, document and sign-off on capital expenditure authorizations for Maintenance
- 7 - 10 years experience in Manufacturing/Operations management
- Bachelors degree in Engineering, Operations Management or similar field
- Experience in electrical or mechanical maintenance, assembly, welding, machining is helpful
- Understanding of facility management, plant engineering and preventive maintenance concepts and programs
- Negotiation experience with an understanding of purchasing philosophy and contract management
- Experience managing in a Union environment
- Must possess analytical/critical thinking skills and the ability to determine root cause
- Knowledge of general physical plant security requirements
35
Maintenance Superintendent Resume Examples & Samples
- Perform the primary thinking encompassed by this job description
- Meets requirements of Maintenance Supervisor
- Coordinates activities of workers fabricating or modifying machines, tools, or equipment to manufacture new products or improve existing products
- Develops preventative maintenance program in conjunction with engineering and maintenance staff
- Inspects operating machines and equipment for conformance with operational standards
- Plans, develops, and implements new methods and procedures designed to improve operations, minimize operating costs, and effect greater utilization of labor and materials
- Reviews new product plans and discusses equipment needs and modification with design engineers
- Confers with management, engineering, and quality control personnel to resolve safety issues and maintenance problems and recommends measures to improve operations and conditions of machines and equipment
36
Maintenance Superintendent Resume Examples & Samples
- Communicates with employees to schedule training, staffing, machine maintenance, repairs and overall plant improvements
- Supervises and schedules necessary repairs to equipment, and setup, design and installation of new equipment, buildings and facilities
- Creates and reads drawings for all aspects of the maintenance division
- Supervises parts supplies inventory and replenishment systems
- Completes required paperwork and reports
- Reviews safety, production, quality control and maintenance reports and statistics to coordinate, plan and modify maintenance activities
- Utilizes outside contractors/vendors for tools, materials, equipment or techniquest to imrpvoe the performance of the plant equipment and maintenance
- Makes budget recommendations and manages maintenance related operational budgets
37
Maintenance Superintendent Resume Examples & Samples
- Ability to identify, propose, and implement process & continuous improvements
- Proven experience developing preventative and predictive maintenance programs
- Possess knowledge, as well as, understanding of electrical systems, PLC/computer operated automation, thermal management at a machine and facility level, and automated systems development and maintenance practices
- Maintain and repair Trane VAV boxes with electric reheat; and Trane and intellipack roof top units
- Filter changes of all HVAC equipment
- Maintain and repair small kitchen equipment (coolers, freezers, etc.)
- Experience running electrical circuit using commercial specs
- Able to diagnose electrical problems in a circuit (short, ground, etc.)
- Strong communication and organization skills, be knowledgeable of environmental issues and OSHA safety guidelines, and be able to display independent judgment and initiative
- Develop a strong customer service oriented relationship with client employees and managers as well as solve client facilities related problems
- Ensure positive communication, responsiveness, efficiency and cost effectiveness on all client service requests and projects. Supervise execution and completion of all maintenance work orders and service requests from beginning to end to include managing vendors/subcontractors or in house staff
- Implement safety policies and train on site personnel to ensure safety in the workplace as per governmental regulations and corporate safety programs
- Conduct onsite inspections to obtain facility condition assessments
- Identifies opportunities and cost saving potential
- Tracks and reports equipment uptime while identifying recurring problems and implementing solutions that prevent the recurrence
- Will implement a Preventative and Predictive Maintenance Program for all major pieces of equipment
- Ensure compliance with vendor/subcontractor agreements, and all federal, state, and local laws
- Has excellent attention to detail and follow-up skills
- Prepares and reviews status reports and modifies schedules or plans as required
- Confers with required personnel to provide technical advice and to resolve problems
- Willingness to work evenings, weekends and holidays as required
- Willingness to perform other related duties as needed, required or assigned
- Supervise maintenance personnel as assigned
- Minimum of five (5) years relevant experience with education or certification in facilities related field
- EPA Certification for CFC’s, a plus
- HVAC (Heat Pump) Certification Maintenance experience is required
- Plumbing experience (working knowledge of water heaters, faucets, drain lines.)
- Appliance repair ( troubleshooting refrigerators, DWs, Ranges and MWs)
- Electrical experience ( troubleshooting switches, breakers, panel boxes, receptacles, bad wiring)
- Heat pump experience (troubleshooting condensers to include replacement if a necessary; troubleshooting air handler, thermostats, and coils.)
- Carpentry experience (repairing drywall, door replacements, trim repair/replacements.)
- Must have hands-on experience of construction methods, processes and materials, including HVAC, Electrical, Plumbing and Maintenance
- CPO Certification a plus
- Must be proficient in balancing a budget and making forecasts for future costs
- Experience working with contractors, engineering firms, internal personnel to ensure procedures and execution for accomplishing project including; staffing requirements, identification and avoidance of conflicting tasks
- Works with equipment manufacturers, contractors, riggers, freight agencies, etc. to obtain critical details required to complete projects ensuring minimal interruption to normal production operations
- Working knowledge required of MS Office products and computerized maintenance management systems
- Strong focus on providing excellent customer service
38
Maintenance Superintendent Resume Examples & Samples
- BS degree in engineering or technical field
- 5 years of maintenance experience or equivalent industrial experience
- Good working knowledge of industrial safety, maintenance practices, and human resources management is required
- Must also be knowledgeable in the areas of proactive maintenance practices, project management, and basic accounting
- Proficiency in Microsoft Office and CMMS software is required
39
Maintenance Superintendent Resume Examples & Samples
- Ensuring the safety and health of the Mechanical Maintenance team, and adherence to corporate and site-specific standards and statutory legislation as applicable to machinery and related work
- Overall maintenance responsibility for the ore processing facility, comprised of crushers, conveyors, rotary scrubbers, screens, pumps, sorters, and related components. Direction of the maintenance function in accordance with established maintenance strategies and work management practices, with an emphasis on planned maintenance and schedule execution
- Assessing current maintenance strategies, tactics, and plans for process equipment; making recommendations and implementing changes as necessary
- Developing annual operating budgets for the maintenance of process equipment, with subsequent budget ownership and responsibility for cost management against targets for the section
- Leading capital replacement and overhaul projects for process equipment, including equipment life-cycle analysis, project motivation & execution, and capital budget management
- Management of maintenance workshops, facilities, and tools for the section
- Personnel management for the section, including hiring, development, and discipline. Providing leadership to direct reports and contractor employees
- Managing service agreements and vendors for specialized contracted maintenance services
40
Major Maintenance Superintendent Resume Examples & Samples
- Lead the development and implementation of the major maintenance framework and system across all Chevron Australia assets
- Manage multiple Major Maintenance teams who are assigned with the conceptual development, work development, detailed planning, pre-work, execution and closeout of all major maintenance activities across Chevron Australia, including all turnarounds
- Coach Major Maintenance Team Leaders and Coordinators on initiatives for managing pacesetter turnarounds (IMPACT) process and associated requirements
- Lead the development and implementation of the IMPACT process for Chevron Australia – ensuring all required steps are followed, documented and closed out in a timely and appropriate manner
- Develop the strategy for all shutdown related activities, contributing to the tendering and evaluating contracting process, establishing the contracts and overseeing the associated interactions with stakeholders
- Provide visible leadership by adopting and implementing the transient contractor management strategy
- Supervise the development of the shutdown planning processes
- Promote a positive safety culture by actively participating in the development, implementation and enforcement of the safety procedures for major maintenance activities
- Demonstrated experience in successfully managing and executing major turnaround and shutdown events
- Significant experience (15+ years) within oil and gas, refining or heavy industry
- Experience in managing shutdown events within the LNG industry will be highly regarded
- Demonstrated experience in using phase gated maintenance frameworks and systems to plan and execute complex major maintenance events
- Demonstrated leadership skills with the ability to influence and negotiate successful maintenance outcomes across multiple assets
- Previous people management experience having managed large multidisciplinary teams
- Experience in developing and executing work plans and budgets
- Flexibility to work across planned and unplanned maintenance events with travel to Barrow Island and Wheatstone Project facilities as required
- Demonstrated ability to identify and build key relationships that contribute to high-class business results
- Demonstrated commitment to Chevron’s values of integrity, partnership and trust and achieving an incident and injury free environment
41
Maintenance Superintendent Resume Examples & Samples
- Ensure compliance with all standards and programs (safety, environmental, quality, maintenance and manufacturing policies and procedures) within area of responsibility
- Lead staff development in: hiring practices, orientation, training, and evaluating & guiding performance
- Forecast, develop, and manage the maintenance budget
- Work cooperatively with other departments to meet plant objectives, diagnose complex equipment problems, meet plant goals and manage department budget
- Develop and lead preventative/predictive maintenance, including working with Hydraulics, Electrical, Pneumatic, Power Transmissions, Welding, and Fabrication, vibration analysis, balancing, alignment, oil analysis and NDT
- Manage and oversee parts and maintenance programs and inventory
- Assist in developing plans for engineering improvements
- Initiate & lead in process improvement, cost reduction and capital project programs
- Work closely with vendors, regulatory agencies, corporate engineering and project managers to accomplish plant goals and objectives
- Effective leadership, interpersonal, and motivational skills
- Knowledge of company products, policies and procedures
- Knowledge of plant equipment, operations, predictive/preventative maintenance systems and effective project management practices
- Knowledge of current management and supervisory techniques
- Thorough knowledge of plant equipment
- Demonstrated organizational, budgeting and computer skills
- Ability to troubleshoot and repair machinery through the use of blue prints, P&ID schematics and root/cause failure analysis
- Ability to manage and direct a capital management system
- 7+ years’ directly related maintenance management experience
- Demonstrated experience supervising a large group of employees
- Demonstrated experience working with Hydraulics, Electrical, Pneumatic, Power Transmission, Welding, and Fabrication
42
AEI Maintenance Superintendent Resume Examples & Samples
- Provide expertise in the areas of automation, electrical, and instrumentation for all projects based on current best practices using approved components and standards. Must be fluent in all three areas of control automation, electrical and instrumentation
- Develop and manage the design and operational requirements for the functional area against corporate standard
- Managing/advise on development of new processes/tools
- Champion Root Cause Analysis efforts and solutions
- Participate in post project evaluations and distribution of lessons learned
- Update or creation of documentation
- 25% - Provide technical expertise to site personnel relative to project design/build/maintain, training and development as well as support to address issues with existing equipment and processes
- 25% - Strategic project development and execution
- 20% - Monitor and enforce alignment of automation, electrical and instrumentation work practices with Plant Systems and Controls standards, corporate safety/food safety policies, local/federal codes and/or regulations and good engineering practices
- 15% - Active and ongoing communication with CAP Plant Floor System team and Corporate Process and Controls COE to ensure alignment of strategic direction, collaboration and project development/execution
- 15% - Standards development and delivery of best practice solutions
- Process control experience 7+ years electrical, automation, or instrumentation knowledge
- Fundamental understanding of National Electric Code, NFPA 70, and NFPA 70E and their application
- Fundamental understanding of industrial electrical systems from 120V DC to 4160 V AC
- Must work equally as well in a team environment and alone. A self-starter
- Must have a firm understanding of process control strategies
- Must be able to design and troubleshoot a range of electrical and instrumentation systems
- Must be able to configure and program a variety of control systems including DCS and PLC systems
- Four-year related college degree (engineering, sciences, etc.) or a minimum of 7+ years Technical Operations experience / AEI Work Experience
- Knowledge of IEC 61131 as well as other proprietary programming languages
- Ability to read and update electrical schematics skills a requirement
- Understand various electrical schematics including one lines and others
- Knowledge of reliability centered maintenance, planning and scheduling desired
- Design and implementation knowledge of plant digital bus technology
- Understanding of process instrumentation ranging from pressure, temperature, level, flow, pH, conductivity, vibration, etc
- Understanding of common software application development tools
43
Maintenance Superintendent Resume Examples & Samples
- Responsible for aligning, deploying and executing the Ag Services Maintenance and Reliability vision/strategy as well as direct program administration
- Promotes a culture that builds, operates and maintains plants that are operationally sound, safe and reliable. Implements leading reliability practices and aggressively raises the performance of under-performing departments by monitoring key performance indicators
- Supports the deployment of Reliability processes across departments and ensures the reliability culture is foundational to operations. Enforces common reliability processes and metrics (focus on eliminating the root-cause of reliability problems) to achieve targeted results
- Partners with the Ag Services Maintenance and Reliability team to identify, deploy and leverage opportunities for continuous improvements applicable to the entire business unit
- Champions the plant Environmental, Health, Personnel Safety and Food Safety processes Conducts Job Safety Analysis/Job Cycle Checks and takes a leading role in these areas
- Manages and implements preventative maintenance and reliability activities at the plant. Partner/interfaces with other departments, personnel facility management, contractors, community and local regulators to ensure asset health and availability
- In accordance with Ag Services/plant maintenance and reliability strategies, standards and practices, supervises, monitors and reviews ongoing maintenance activities and records to ensure asset health and adherence to guidelines, codes, regulations, requirements and overall production quality
- Oversees the execution of repair procedures and tasks to ensure compliance with the fundamental plant reliability strategies, standards and practices
- Monitors repairs through systems and controls to ensure work orders and requests are executed in accordance to established work flow
- Reviews and analyzes maintenance/reliability maintenance metrics and performance
- Leads and/or supports audit compliances, root/cause analysis processes within the maintenance team
- Partners with Ag Service Resources to develop strategies for operations of assigned areas, (electrical/mechanical/control systems) which includes technical optimization of processes
- Develops, maintains and applies consistent maintenance and reliability best practices
- Has knowledge of and is responsible for understanding the latest innovations, technology and trends for maintenance & reliability practices
44
Mobile Maintenance Superintendent Resume Examples & Samples
- Minimum 5 years experience in a leadership capacity
- Minimum of 10 years in underground maintenance experience
- Certification in mechanical Trade or degree mechanical Engineering would be considered an asset
- Up to date technical knowledge and mechanical skills
45
Maintenance Superintendent Resume Examples & Samples
- 5 years minimum as a mechanic or other technical tradesman
- 2-3 years experience leading a team
- Troubleshooting experience
- Able to read technical manuals/blueprints
- Understanding of GMP
- SKILLS REQUIRED
- Mechanical, electrical, pipefitting, rigging
- Job Hazard Analysis and safety compliance
- Computer proficiency (Microsoft office, email, etc.)
- Excellent Verbal and Written Communication skills
- Report writing
- Ability to train others
- Ability to work any shift, weekends, holidays to support 24/7 operation
46
Maintenance Superintendent Resume Examples & Samples
- Accountable for the safety standards and performance across your area
- Coaching and developing maintenance staff personnel including supervisors, engineers and technologists, and promoting BC Works within the community
- Improving equipment availability/reliability and eliminating defects
- Accountable to deliver on key indicators such as productivity and quality
- Fostering a culture of continuous improvement, supporting the team in the implementation of improvement initiatives, competency training, and technical advances
- Preparing and managing capital and operating budgets to achieve business outcomes
- A Bachelor's degree in Engineering or a related field
- 5+ years of prior industrial maintenance experience
- Prior leadership experience and ability to coach, mentor, and develop people
- Ability to communicate effectively with stakeholders at all levels
- Understanding of cost structure and optimization
47
Maintenance Superintendent Resume Examples & Samples
- Actively participates, as member of refinery leadership team, in development of refinery’s strategic and operational plans. Establishes Maintenance-specific objectives aligning with refinery’s targets for safety, regulatory compliance, reliability, and efficiency
- Ensures risks associated with Maintenance activities are appropriately managed
- Manages efforts to improve effectiveness and efficiency while ensuring departmental activities are conducted in safe, environmentally sound and regulatory compliant manner
- Manages development and execution of department’s policies, programs and procedures to maximize operating efficiency. Ensures adoption of and adherence to engineering guidelines, industry standards and best practices. Promotes culture of continuous improvement
- Manages budget. Exercises financial stewardship to control expenditures
- Manages staff. Initiates selection, promotion and corrective actions when appropriate; accountable for fair and uniform application of human resources policies. Leads design and implementation of hourly skill development programs. Oversees career paths and succession planning
- Minimum 10 years refinery maintenance experience with at least 5 years supervisory/management experience in progressively responsible positions
- Must have physical ability to perform all essential job duties and work extended hours, including nights and weekends in a process operations environment. Work may be conducted during periods of inclement weather. Must have physical ability to access all areas of the refinery including use of stairs and/or ladders to inspect critical process and mechanical equipment. Must be available to respond to upset conditions during off-hours
48
Maintenance Superintendent Resume Examples & Samples
- 60% - Maintenance and Reliability: Leverage labor, materials and equipment to prevent, and eliminate, equipment failures through targeted deployment of maintenance strategies, reliable execution of work management practices and reliability engineering principles. Champion failure investigation and problem identification and resolution activities
- 20% - Talent Management:Lead the development of human assets by effectively training, engaging, promoting, coaching, appraising and responding to the needs of employees. Ensure key results areas, and goals, are aligned with the organization’s strategy and long term success
- 15% - Food and People Safety: Ensure all engineering practices and procedures support a safe working culture and one that promotes the manufacturing of healthy and safe food and food ingredients
- 5% - Plant Leadership: Serve as a key member of the plant leadership team, providing overall plant and business leadership, role modeling, mentoring and coaching to others in all functions and at all levels of the operation
49
Case Ready Maintenance Superintendent Resume Examples & Samples
- Responsibilities include but are not limited to continuous improvement maintenance programs
- Oversee that all computers and interface hardware (scales, scanners, etc.) are functioning properly including site telecommunications systems
- Spare parts analysis and asset record development
- Ensuring the pro-active day-to-day safe and efficient maintenance, upkeep and repair of the facility by managing the day to day maintenance work
- Ensure workflow processes are followed; ensuring maximization of maintenance labor and resources
- Oversee failure maintenance and follow up work: Support the general processes and policies laid down by the maintenance department as well as the company policies
- Lead the proactive maintenance program and drive toward the standards required by the company
- Manage work quality
- Develop and implement the proactive maintenance program and spare part management to ensure maximum efficiencies
- Manage department safety activities and execution of successful safety management program
- Provide ongoing coaching to assist with development of maintenance staff
- Weekly review of expenses and KPI’s, provide solutions for deviations from targets, monitor departmental budgets, hold self and others accountable for achieving goals and targets
- Engineering degree (or equivalent experience)
- PLC knowledge a plus
- Must speak, read and write English
- Good working knowledge of Word and Excel
50
Maintenance Superintendent Resume Examples & Samples
- Assist in identifying, developing and implementing maintenance programs or special projects that will result in achieving or exceeding established labor goals by recommending new methods, layouts and/or equipment changes
- Assist in the planning and developing of short and long range operational method plans that will position Seaboard Foods to capitalize on current and future market conditions with competitive operating cost
- Assist in the planning, developing and implementing of effective preventative maintenance and crisis management programs in all production departments to minimize downtime and costs
- Plan, develop and implement a parts inventory control program providing dollar value and status inventory. Control mechanical expenses within established budget and actively pursue cost reduction opportunities in labor, material cost and inventory balance
- Establish and clearly communicate realistic job requirements for subordinates; provide frequent feedback and review on performance and accurately appraise performance results against communicated expectation
- Identify training needs (both technical and managerial) for your people which will result in measurable performance improvements if pursued
- Provide timely and accurate performance information on all aspects of the operations at the plant within area of responsibility to include an explanation of all variances and actions you plan to take to correct the situation
- Be familiar with OSHA and FSIS regulations and work with FSIS to receive, evaluate and report work needed to keep the plant running in accordance with government requirements
- Defines and recommends objectives in area of responsibility. Develops specific short-term and long-term plans and programs. Reviews and makes recommendations on cost control, cost estimates, and manpower and facilities requirements forecasts
- Coordinates and collaborates with other departments in the facility in establishing and carrying out responsibilities
51
Maintenance Superintendent Resume Examples & Samples
- Manage computer based maintenance program (EAM or equivalent) that tracks activities, schedules, labor, and parts building a history on equipment
- Demonstrated knowledge of plant equipment
- Good organizational, budgeting and computer skills
- 5+ years’ mechanical and/or electrical supervisory experience
52
Maintenance Superintendent Resume Examples & Samples
- Supervision of the maintenance and repair of equipment, as directed by the Equipment Superintendent, for assigned facility in accordance with Granite’s Corporate Equipment Standards
- Manage maintenance and repair activities as needed
- Maintain equipment files including inventory, repair, maintenance, oil sampling, and servicing to ensure the preservation of company investments
- Manage special projects required to support the assigned facility as needed
- Inspect equipment on a regular basis to identify mechanical or safety problems and ensure a safe working environment
- Compare costs and best value of equipment repair including parts, contracting outside vendors, using in-house labor or equipment replacements to ensure the most cost effective choices are made
- Comply, understand, and support corporate safety initiatives including holding weekly safety meeting with staff to ensure a safe work environment
- 1 – 4 years experience in equipment or construction-related field
- Strong demonstrated supervisory skills and leadership ability
- Practical knowledge of the function, operation and maintenance of construction equipment and/or education & experience in heavy equipment maintenance and repair
- Expert computer skills including all MS Office products (Word, Excel, PowerPoint, etc.) and familiarity with Oracle Enterprise One (e1) Capital Asset Management (CAM) module
- Strong written and oral communication skills to effectively disseminate information
- Excellent communication (both written and verbal) and organizational skills
- Ability and willingness to abide by Granite’s Code of Conduct on a daily basis #LI-
53
Fabrication Maintenance Superintendent Resume Examples & Samples
- Meet plant objectives as a cross-functional team member with operations, food safety, and safety departments
- Develop and grow a trusting relationship with the USDA to insure that their requirements are being met
- Develop capital investment projects that support areas of responsibility
- Develop and manage the repair and maintenance budget
- Develop and maintain contractors and vendors to supplement the maintenance department
- Manage the storeroom inventory for the best economic advantage
- Ensure consistent application of the collective bargaining agreement
- Active involvement in employee relations, retention best practices, and administration of all company policies and procedures
- Job responsibilities typically require extended hours and weekends
54
Maintenance Superintendent Resume Examples & Samples
- Higher National Diploma or Degree in Mechanical Engineering and two (2) years of experience in safety management in hydrocarbon processing operations
- Chief Engineer unlimited as per STCW Reg. A. III/2 and two (2) years of experience in safety management in hydrocarbon processing operations
- Supervisory experience of Permit to Work, Mechanical and Electrical Isolation Standards, and Risk Assessment
- Medically fit to offshore international standards such as ENG1 or equivalent
- Promote safety awareness and application of company Management System (MS), COPs, and prime policies
- Report concisely in accordance with MS requirements with due regard for document control
- Ensure timely and effective closeout of survey and relevant audit actions
- Manage welfare and disciplinary issues at departmental level with appropriate reference to OIM and Fleet HR
- Ensure full compliance with PTW system, risk assessment, and verification
- Ensure full compliance with Class, Flag, and Port State requirements, preserving the vessel’s operational status
- Effective supervision of project, sub contract, and vendor personnel
- Responsible for condition monitoring, maintenance, and repair of vessel and process systems
- Manage parts control, inventories storage record keeping, shipping, and receiving by use of AMOS
- Manage operations in conjunction with all department heads to maximize efficiency and uptime
- Maintain effective cost control and promote cost awareness in others
- Demonstrate through exercises and scenarios, knowledge and awareness of emergency response techniques and potential impact of incidents and scenarios on vessel safety and security
- Contribute effectively to preparation of useful exercises and to post exercise, incident review, and investigation
55
Sumter Maintenance Superintendent Resume Examples & Samples
- Supervises workers engaged in major painting projects, performing structural repairs to masonry, woodwork, and furnishings of buildings, and maintaining and repairing building utility systems such as electrical wiring and controls, heating, and ventilating systems
- Supervises workers engaged in installing, servicing, and repairing mechanical equipment. Supervises employees who maintain, repair and service plant equipment, buildings, and facilities
- Prepares work schedules. Makes work assignments to subordinates
- Analyzes and resolves work problems or assists employees in solving work problems
- Works on projects involving the construction of new buildings and facilities and the alteration or modification of existing ones
- Maintains production equipment in a manner that meets organization standards and ensures minimum equipment downtime. Requisitions tools, equipment, and supplies
- Must have 4 years experience in poultry maintenance / food manufacturing experience
- Must have experience with further processing equipment
- Must have working knowledge of refrigeration
- Must have good computer skills
56
Maintenance Superintendent Resume Examples & Samples
- Provide solid leadership of the maintenance team and assist in the development and success of the maintenance team members
- Review, implement and monitor a preventative maintenance program which includes both regular maintenance items and assisting in the identification and 5-year planning of capital projects as needed
- Ensure the timely completion of work orders. Review statistics, follow up with residents for quality control, document information in software and address and productivity concerns
- Complete reports as required on daily, weekly, monthly, quarterly and annual basis
- Participate in annual budget process and remain engaged in budget decisions and variance reports
- Purchase materials, supplies and monitor inventory levels. In many cases, it will be necessary to solicit 3 bids with consistent scope of work and prepare a complete bid summary for supervisor approval
- Manage vendor contracts, expectations and relations. Consistently follow up on work completed to ensure quality
- Special projects as assigned by the property manager and additional duties as per the job description that will be provided
- Must have 5+ years successful experience in apartment maintenance with a minimum of 3+ years as supervisor of multiple staff members
- Must possess thorough knowledge and understanding of building systems including: HVAC, Plumbing, Electrical, BMS, Fire & Life Safety and all related systems
- Ability to read and interpret drawings, blue prints, and specifications
- Good knowledge of Excel, Word, Onesite, YARDI or similar software is a plus
- Excellent leadership, communication, customer service, and interpersonal skills
- Strong understanding of the latest technologies in energy management & building technologies
57
Maintenance Superintendent Resume Examples & Samples
- Ensure compliance with all statutory and regulatory requirements and all Peabody and Millennium site policies and procedures,
- Delivery of a safe and healthy workplace and ensure all safety incidents and actions are closed out in a timely manner
- Ensure the delivery of effective maintenance planning, forecasting and budget outcomes for the Millennium fleet
- Ensure all statutory inspections and maintenance tooling/safety equipment is maintained and periodic calibrations/inspections are recorded
- Develop a continuous improvement pipeline along with consistently delivering solutions that enhance business outcomes including where required working with OEMs and other Peabody sites
- Ensure machine health monitoring and assessment information is actioned to delivery machine and component life
- Minimise production downtime & scheduled maintenance through effective planning/delegation techniques
- Actively promote the four pillars of the Peabody Leadership Model (Inspire, Innovate, Execute, Collaborate)
58
Underground Mine Maintenance Superintendent Resume Examples & Samples
- Ensure department’s compliance with the requirement of Government of Ghana Agencies, lending institutions, shareholders’ interests, environmental, health & safety legislation and company regulation
- Responsible for Safety, Environmental, and Social Responsibility policies. Creates a suitable work environment to motivate staff, employees and business partners to achieve optimum effectiveness, productivity and operating costs
- Accept personal responsibility for the health and safety of every mine worker under or assigned to his/her supervision
- Provides strategic direction and leadership and establishes and manages Mine Maintenance department goals and objectives
- Creates and implements policies and procedures and promotes projects and programs within the Mine that provide continuous improvement in the areas of safety, environment, production and efficiency
- Prepares, negotiates, and implements various Maintenance and Repair Contracts
- Manages implementation and maintenance of all underground IT systems including communications, PED, tracking, fleet management, Ventilation on Demand, semi-autonomous haulage
- Assists in the design and manages the maintenance of all Subika underground fixed plant including but not limited to: the truck shop, fueling, wash bay, welding, tire shop, stores, water treatment plan, sewage treatment plant, metal removal plant, primary vent fans, and refrigeration plant maintenance facilities
- Ensures all equipment including Business partner is properly serviced and maintained; responsible for all owner and contract maintenance personnel supporting the mine maintenance effort
- Responsible for mine maintenance budgeting, performing capital evaluation of projects, producing management reports
- Degree in Mechanical or Mining Engineering
- A minimum of 10 years’ experience as a maintenance superintendent or equivalent management position
- Experience with facility designs, equipment, development and management of business partners and sub contractors
- Knowledge of computer management tools such as Pitram, VIMS, and SAP is recommended
- Experience in the management and administration of budgets in a multinational company
- Strong PC skills using office software such as Excel, Word and Power Point
- Strong presentation, facilitation, and consultation skills. Excellent interpersonal skills. Negotiation and conflict resolution skills
- Ability to identify and analyze organizational needs
- Demonstrate strong supervisory, verbal and written communication skills
59
Maintenance Superintendent Resume Examples & Samples
- Preventative/scheduled maintenance program and staff supervision
- Repairs projects
- Purchases and maintains materials, supplies, inventories and good vendor relations
- Site Custodial Work
- Site ground work and staff supervision
- Assist with hazardous weather issues
- Cycle painting – interior/exterior
- Apartment renovations/turns and staff supervision
- Site extermination program
- General site administration
- Special projects and other tasks, as assigned by the District Manager
- General computer knowledge of Microsoft Word and Excel
60
Maintenance Superintendent Resume Examples & Samples
- Strong maintenance planning background within an open cut mine
- Diverse maintenance experience covering field and mobile equipment
- Extensive experience with SAP
- Engineering qualifications highly desirable
61
Field Maintenance Superintendent Resume Examples & Samples
- Technical knowledge to assure that road construction, maintenance or repair projects comply with departmental policies and procedures as well as with engineering standards and relevant laws and ordinances pertaining to road constructions.
- Ability to consistently maintain effectiveness and poise when changes in work priorities require prompt action to accomplish objectives, problem-solving techniques, and processes to facilitate the identification and resolution of problems and issues related to the completion of work assignments.
- Ability to project management principles and techniques to supervise the progress of a variety of project activities.
- Ability to implement workflow principles and concepts to establish and maintain accurate work records and documentation depicting project status and progress.
- Ability to represent the Agency to citizens on issues concerning interpreting relevant laws and ordinances and resolving complaints; contacts property owners, public utilities employees, governmental units and civic groups to secure cooperation on road maintenance matters of present and future concerns.
- Ability to establish and maintain effective working relationships with governmental officials, subordinates, and the general public and be an approachable and politically astute leader with a style that elicits the trust of staff and others; able to inspire confidence and build support within and outside the organization
- Methods, materials, blueprints, tools and equipment used in the maintenance and construction of roads, flood control structures, and related facilities
- Agency rules and procedures
- Techniques for estimating materials, tools, equipment and staffing necessary to complete projects
- Construction safety practices
- Contemporary supervision and organization principles and practices
- Budgetary methods, procedures and techniques
- Operational and financial record-keeping methods
- Maintenance or roads, flood control structures, landscape, street lighting, traffic control signals and related public infrastructure
- English usage, grammar, spelling, vocabulary and punctuation
- Plan, organize, coordinate and supervise a maintenance and construction program for road and flood control facilities
- To determine equipment and personnel resources required for maintenance operations
- Direct the work of others through subordinate supervisors
- Understand and follow complex instruction and technical specifications
- Determine the condition of facilities by inspection and estimating accurately the time, materials, equipment, and cost of specific jobs and programs
- Work harmoniously with other people and agencies, and maintain good relations with the general public, other departments, and outside agencies
- Keep operational and financial records
- Operate a standard office computer to enter data, retrieve data, utilize spreadsheet and other applications
- Make decisions
- Plan and organize
- Perform administrative functions
- Deal with citizens’ concerns in a tactful manner
- Analyze and problem solve
- 2) A review of candidates’ Supplemental Questionnaires to select the best qualified applicants to continue in the process
- 3) An oral interview which will be weighted as 100% of the candidate's final examination score. The oral interview may contain situational exercises
62
Maintenance Superintendent Resume Examples & Samples
- Manage and lead the activities of the Maintenance Team (either craft workforce or planners/schedulers) to ensure process safety, safety, environmental, reliability, and cost goals of the refinery are achieved
- Ensure compliance with safety, procedures and objectives and as well as acts, and regulations and the commitment to achieving a safe work environment through behavioral based safety leadership
- Implement and manage the environmental requirements ensuring compliance with federal and state regulations and rules
- Utilize sound human relations and communications skills to provide development of direct reports and motivation of staff resulting in a reliable and competent work force
- Interview candidates, determine development needs, evaluate performance, and address personnel issues including training, coaching, mentoring and disciplining of subordinates
- Supervise, coach and mentor maintenance supervisors and planners/schedulers on maintenance priorities and schedules, policies and procedures, employee relations and work activities
- Collaborate with Maintenance Leadership to set maintenance department objectives and strategies
- Establishes department goals creating an atmosphere of continuous improvement
- Develop and track department scorecard matrix of maintenance department’s goals, objectives and strategies; accountable for all field requisitioning functions including stores/stock inventory, and the preparation and execution of plant service contracts and related activities
- Ensure proper training of technicians and specialists, proper documentation is provided for the timely completion of work, and all necessary tools are available and in good working order
- Direct, supervise and provide technical guidance for plant maintenance work activities to keep plant equipment in good operating condition, and produce a favorable economic balance between maintenance costs and downtime
- Support turnaround and unit shutdown planning and execution through active participation in scope development, providing justification for work items, and providing support during commissioning of equipment, shutdown/startup and outage timeframe
- Review equipment specifications and maintain equipment records,
- Develop and manage preventative and predictive maintenance activities, procedures and programs
- Assist in the development of maintenance department budget
- Manage the department’s operational budget and provide periodic reports on its status
- Initiate and coordinate service contracting functions to meet the company legal risk management and plant objectives
- Provide general supervision of contractors
- Manage maintenance work backlogs and verify priorities to meet plant goals
- Approve requisitions and contract service authorizations within the Delegation of Authority limits
- Bachelor’s Degree in industrial, engineer or business discipline with two (2) years of experience in maintenance role; or High School diploma or GED with four (4) years of experience in maintenance role and two (2) years of experience in a maintenance leadership role; or Military equivalent experience
- Proven leadership skills in a fast paced work environment
- Excellent written, oral, interpersonal, and presentation skills to effectively communicate with all levels of the organization
- Demonstrated experience in planning and scheduling maintenance or turnaround work packages
- Proficient in Microsoft Office Suite office; Word, Excel, PowerPoint and Outlook
- Proven knowledge of Maintenance CMMS software
- Demonstrated knowledge of electrical, instrumentation and analytical equipment in regards to operation, maintenance and best reliability practices
- Ability to manage multiple priorities with deadlines in a fast paced and dynamic environment
- Strong skills in areas of: operational analysis, budget, problem solving, project management, communication, organizational and leadership
- Ability to achieve maintenance excellence by establishing and communicating goals
- Solid organization skills
- Able to travel as required
- Working knowledge of various industry standards such as API & NFPA
- Must be able to pass pre-employment background screening and drug screen
- Completion of maintenance certification or apprentice program
- Five (5) years of experience in a maintenance leadership role
- Previous experience supervising maintenance activities in a refinery/petrochemical facility
- Experience with meeting process safety requirements including management of change, mechanical integrity, and safe work practices
- Experience with EAM and/or SAP
- Experienced in managing in an union environment
- Knowledge/experience with 5-S, Six Sigma or Lean Manufacturing principles
63
Mobile Maintenance Superintendent Resume Examples & Samples
- Establishing and maintaining safe work practices and environment and ensuring legal compliance
- Managing and overseeing condition monitoring; ensuring that standards, procedures and best practices
- Managing and overseeing the Mobile Maintenance Planning Department to ensure accurate scheduling of all maintenance of mobile equipment, and accurately capturing downtime on all equipment
- Implementing and updating an asset management system for the operation that is aligned with DBCI Asset Management Strategy, ensuring that reports on the availability of the machinery are compiled
- Calculating the mean time between failures of machinery and make recommendations based on report findings
- Managing and overseeing the maintenance services contractor
- Managing and controlling working costs and capital budgets
- Evaluating systems and procedures to gauge effectiveness, then develop and implement alternative systems through innovation and creative thinking
64
Underground Production & Maintenance Superintendent Resume Examples & Samples
- Underground Production & Maintenance Superintendents/ Coordinators
- Coal Handling & Process Plant Production & Maintenance Superintendents/ Supervisors
- Process Engineering Professionals
- Geotechnical Engineering Professionals
- Ventilation and Gas Professionals
- Mining Engineering Professionals
- Geology Professionals
65
Maintenance Superintendent Resume Examples & Samples
- Purchase and maintains materials, supplies, inventories and good vendor relations
- Site custodial work and staff supervision
- Investigate accidents
- Previous maintenance experience in various maintenance areas including: plumbing, electrical, carpentry, painting, and general building operations
- Specific licenses and/or certifications may be required
66
GB Maintenance Superintendent Resume Examples & Samples
- 5 -7 years relevant experience in the meat maintenance industry
- Proficient in the use of CMMS (SAP preferred)
- Understanding of predictive maintenance techniques
67
Fixed Maintenance Superintendent Resume Examples & Samples
- Manage the maintenance team and activities within the concentrator and other assigned fixed equipment areas, including the port, powerhouse, power distribution and site facilities
- Direct activities and priorities of maintenance supervisors, planners, engineers and technicians and ensures maintenance workflow processes are followed and improved upon
- Develop maintenance budgets and monitors performance vs. budgets
- Ensure a high degree of reliability of equipment, and that safe work practices are followed in all areas
- Work closely with operations and support personnel to provide maintenance and reliability services aligned with the Work Management Processes established within the site’s Assett Management Framework
- Ensure that maintenance, plans and schedules, reliability and plant integrity programs are in place and monitors key plant and team performance indicators to define and lead improvements
- Provide strategic leadership on plant reliability and associated reliability improvement plans (RIP)
- Ensure that training needs are analyzed, planned, and delivered
- Manage the implementation and operation of the CMMS within SAP
- Engage with the SAP community of practice to ensure that work order, equipment history, and cost tools meet the needs of the maintenance group
- Integrate the maintenance team with warehouse personnel to develop on-going inventory optimization program for spares, and materials planning management program
- Act as a key member of Concentrator and the site’s leadership team to ensure continuous alignment of the maintenance team’s behavior’s with the site values and vision of a World Class Workplace
- Develop successful performance environments for each of the Maintenance teams with focus on engagement
- Engage with site fixed plant operations and project personnel to develop functional specifications, commissioning and start-up strategies, to ensure integrity of equipment, and monitor installations and provide required input with respect to maintenance access and requirements
- 10-15 years experience in mining/processing maintenance environment in a senior level, new plant start up, and the development and rollout of system using Mincom/Ellipse, or other comparable CMMS system
- Experience with CMMS systems (SAP preferred)
- Experience in Maintenance Leadership specific to mining operations
- Strong knowledge and experience in Operations and Maintenance systems, processes and facilities
- Excellent Organizational, Leadership, Adaptability, and Communications skills
- Proven track record in leading maintenance activities
68
Maintenance Superintendent Resume Examples & Samples
- 30% - Operational Effectiveness/Continuous Improvement (prevent, maintain and repair)
- Manages and implements preventative maintenance and reliability activities for the facility
- Partner/interfaces with other departments, personnel facility management, contractors, community and local regulators to ensure asset health and availability
- In accordance with BU/plant maintenance and reliability strategies, standards and practices supervises, monitors and reviews complex ongoing maintenance activities and records to ensure asset health and adherence to guidelines, codes, regulations, requirements and overall production quality
- Oversees the execution of complex repair procedures and tasks to ensure compliance with the fundamental plant reliability strategies, standards and practices
- Monitors repairs through systems and controls (i.e. CMMS) to ensure work orders and requests are executed in accordance to established work flow
- Reviews and analyzes maintenance/reliability maintenance metrics and performance. Leads and/or supports audit compliances, root/cause analysis processes within the maintenance team, which includes tracking and reporting on established metrics for the facility (i.e. Asset Health index; Total Maintenance Cost/RAV; Overall Equipment Effectiveness (OEE); and audits compliance)
- Partners with BU/Reliability Engineering department to develop strategies for operations of assigned areas, (i.e. electrical, mechanical, systems, operations, etc) which includes technical optimization of processes
- 25% - Reliability Excellence Governance (develop, align and implement RE practices and programs)
- Responsible for aligning, deploying and executing Business Unit wide reliability excellence vision, strategy as well as direct program administration for the facility
- Promotes a culture that builds, operates and maintains plants that are operational sound, safe and reliable. Implements leading reliability excellence practices and aggressively raise the performance of poor departments by monitoring key performance indicators (i.e. yield optimization, energy/water usage reductions, operator safety indexes, etc) for a less complex plant and/or more complex department
- Supports the deployment of Reliability Excellence processes across less complex plant and ensures the reliability culture is foundational to operations. Enforces common reliability processes and metrics (focus on eliminating the root-cause of reliability problems, etc) to achieve targeted results from continuous improvement practices, and validates the importance of Reliability
- Excellence through key successes (scorecard and metrics control, total cost of maintenance, total cost of ownership, monthly review of compliance audits, etc)
- Partners with Reliability Excellence COEs to identify, deploy and leverage opportunities for continuous improvements applicable to the entire business/platform
- 20% - People/Budget Management
- Responsible for the people management in area of responsibility including recruiting, retention, development and engagement of team
- Responsible for the appropriate scheduling and delegation of activities for a team of maintenance/reliability employees and 3rd party contractors
- Establishes and manages overall plant/department/areas maintenance budgets for a less complex plant and/or a sub-set (departmental budget). Has responsibility for a significant subset of cost control of repairs and maintenance and also maintenance labor and parts
- 15% - Project Planning, Contractor/Vendor Management
- Manages ongoing maintenance/ reliability related projects (i.e. asset reliability/defect elimination) utilizing a broad knowledge of maintenance and reliability practices and procedures
- May directly lead/oversee general project planning, cost estimation and tracking & payback justification
- Recommends/approves selection of contractors/vendors. Manages, analyzes complex maintenance vendor issues and contracts administration
- Oversees and ensures that reliability design criteria is included and adhered to basis total cost of ownership and reliability requirements
- 10% - Best Practice Application, Training and Support
- Develops, maintains and applies consistent maintenance and reliability best practices (i.e. safety programs, routine safety audits, RCM methodology and FMEA to determine optimum defect elimination strategies)
- Has full knowledge of and is responsible for understanding the latest innovations, technology and trends for maintenance & reliability practices
- Identifies training opportunities/needs and facilitates training sessions for maintenance personnel, focusing on skills training and development, safety practices and work standards. My provide ad-hoc technical support as needed. Serves as a source of maintenance/reliability information for the facility. Supports operations by analyzing and developing conclusions in regards to failures, downtime and lost production and identifies opportunities to improve operator reliability and/or determines acceptable risk tolerance for asset
- Bachelor’s degree or higher, associate degree with experience will be considered
- 5+ years manufacturing experience with various roles and progressive responsibility
- 3+ years of direct management/leadership experience (influencing, coaching, managing through others, developing diverse work teams)
- Demonstrated ability and understanding of both mechanical and electrical systems to include PLCs and basic programming
- Working knowledge of maintenance work management processes (ie planning and scheduling)
- Work experience in refrigeration, utilities and waste water treatment equipment and processes
- Managing complex projects in a plant environment
- Lean, 6 Sigma, or other Quality Management Skills
- Basic Level one understanding of Vibration, Infrared, MLT, Ultrasonic, and Motor Circuit evaluation
- Experience with CMMS- Maximo and or SAP
69
Mine Maintenance Superintendent Resume Examples & Samples
- Bachelor’s degree in Engineering, with a major in Mechanical, Mining, Electrical or Civil or Jouryneyperson Trade is an asset
- P. Eng or equivalent
- 4 years of experience in Engineering and 10 to 15 years of experience in maintenance is preferred
- 5 years of supervisory experience is required
- Basic computer skills, work order and accounting computer package system (Empac and Oracle), and Kronos experience
- Leadership, people management, communication, decision making, and budget control
- Must also know the Collective Agreement, OH&S Codes, and Mine Regulations
70
Maintenance Superintendent Resume Examples & Samples
- Organizing, implementing and directing the activities of the maintenance department at the mine-site to establish effective maintenance management systems and achieve “superior” maintenance standards
- Developing and managing the maintenance budget
- Ensuring all activities in the maintenance department are in compliance with environment and safety legislation, regulations, policies and guidelines and standard mine operating procedures
- Establishing a positive working environment by conducting and participating in activities that contribute to an effective working relationship with all employees
- Promoting teamwork and employee development through effective communication and implementing and monitoring performance standards
- Assuming other duties and/or responsibilities as required in response to changing circumstances and the economic and physical environment of the Mine or Company
- Demonstrate excellent interpersonal, communication, leadership, and organizational skills
- Have a minimum of 15 years of related mining experience in a managerial/supervisory role would be preferred
- Possess a Journeyman’s Trade certificate, or an Engineering Technologist diploma or mechanical Engineering degree; however, other combinations of education and experience may be considered
- Have knowledge of all mining equipment and installations as well as experience and knowledge of current safety procedures
- Possess an understanding of various mine maintenance software tools
- Have the ability to learn quickly and maintain motivation even in the face of inevitable delays, setbacks, and policy, shift and schedule changes
71
General Maintenance Superintendent Resume Examples & Samples
- Must possess the skills for effective problem solving and demonstrated ability to make recommendations and to take action
- Must have solid verbal and written communication skills to provide instruction and information to staff, peers, other managers, bargaining unit, as well as outside agencies
- Must be able to assign priorities and determine work sequences and be capable of administering all department activities, including budgeting, training and contract adherence
- Must have demonstrated capability of managing bargaining unit personnel, as well as supervises and engineers
- Needs to be able to communicate effectively and influence other managers
72
Maintenance Superintendent Resume Examples & Samples
- Comply with Kinder Morgan, ESDC and Vancouver Wharves terminal safety and security regulations/requirements and adhere and follow all Environmental Health and Safety procedures
- Improve the reliability of the equipment at the terminal through detailed planning and scheduling, prioritization of maintenance activity based on criticality and engagement with the groups performing the work
- Lead a team of both mechanical and electrical foremen and trades
- Assist in scheduling and dispatching the Longshore workforce based on terminal requirements
- Responsible for the allocation of resources within the confines of the maintenance labour and equipment budget including procurement of parts and services from vendors as required
- Understand the terms contained within the applicable ILWU Local 500 and Local 514 collective agreements regarding performance, pay and behavior at the Terminal
- Interface with capital project teams on the requirements of the maintenance department
- Supervision experience with trades in a union environment
- Experience working in a unionized heavy industrial environment is essential; experience working at a marine terminal is preferred
- A strong mechanical aptitude and familiarization with conveying equipment and mobile machines is required
- Computer proficiency with PCs, Microsoft Word, Excel, and Outlook software programs
- Excellent communication skills; ability to work collaboratively with others and to direct union labour
- Flexibility in adapting to changing needs; detail oriented and adept at analytical problem solving
73
Maintenance Superintendent Resume Examples & Samples
- Briefly describe your experience developing and implementing work plans, including your specific roles and responsibilities. Indicate the type(s) of work plans you developed, your level of involvement, and how you balanced multiple tasks and competing priorities
- How have you used your technical knowledge to solve a challenging problem for which there appeared to be no clear answer? Provide an example of when you did this. Please describe the problem, the techniques and knowledge you applied, and the outcome
- Describe actions you have taken in your current or past work environment, to be a positive influence on coworkers and staff. Please provide at least two (2) examples
- How have you prepared yourself for this position?
74
Maintenance Superintendent Resume Examples & Samples
- Ensure safety policies and procedures are followed in the shop
- Reviewing daily work product from maintenance supervisors and foremen and ensuring compliance with all SOP's
- Track and analyze roadcalls, comebacks, rework of mechanics
- Take necessary action to remedy any deficiencies
- Monitor oil analysis program ensuring re-sampling or follow up is performed in a timely manner
- Follow up with supervisors and foremen of any shift issues
- Review with Supervisors and QA Manager, the Foremen PMI Audit results. Ensure corrective action and training
- Meet with maintenance director as needed, no less than every other day, on any maintenance, productivity or contract performance issues
- Ensure information is distributed to shop supervisors, foremen and mechanics regarding contract performance, RTC issues and directives
- Ensure all administrative tasks are handled as they relate to RTA
- Communicate with OEM on problems identified with parts
- Work closely with stores manager to ensure needed parts and inventory levels are maintained at efficient and optimum levels
- Conduct performance evaluations for subordinate staff
- Provide support to the maintenance director as assigned
- Conduct weekly toolbox meetings with Maintenance Director to ensure information is distributed, including contract performance, RTC SOPs, maintenance areas of concern or trends, and client and employee issues
- Work closely with Stores Manager to ensure needed parts inventory levels are maintained at an efficient and optimum level
- Monitor electronic vehicle inspection process
- Assume an additional role of Technology Champion as detailed by Maintenance Director