Customer Quality Engineer Resume Samples
4.6
(125 votes) for
Customer Quality Engineer Resume Samples
The Guide To Resume Tailoring
Guide the recruiter to the conclusion that you are the best candidate for the customer quality engineer job. It’s actually very simple. Tailor your resume by picking relevant responsibilities from the examples below and then add your accomplishments. This way, you can position yourself in the best way to get hired.
Craft your perfect resume by picking job responsibilities written by professional recruiters
Pick from the thousands of curated job responsibilities used by the leading companies
Tailor your resume & cover letter with wording that best fits for each job you apply
Resume Builder
Create a Resume in Minutes with Professional Resume Templates
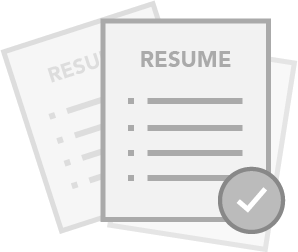
CHOOSE THE BEST TEMPLATE
- Choose from 15 Leading Templates. No need to think about design details.
USE PRE-WRITTEN BULLET POINTS
- Select from thousands of pre-written bullet points.
SAVE YOUR DOCUMENTS IN PDF FILES
- Instantly download in PDF format or share a custom link.
AS
A Schmidt
Art
Schmidt
120 Gislason Tunnel
Philadelphia
PA
+1 (555) 782 4526
120 Gislason Tunnel
Philadelphia
PA
Phone
p
+1 (555) 782 4526
Experience
Experience
Houston, TX
Customer Quality Engineer
Houston, TX
McClure-Price
Houston, TX
Customer Quality Engineer
- Develop/execute and automate test cases to cover customer workflows
- Provide assistance with RMA documentation and communication of issues to internal Failure Analysis teams. Work closely with FA teams overseas
- Assist to develop and maintain FMEAs and control documentation to effectively manage risk and meet customer specifications
- Develop, implement, and maintain technical quality management projects and tools that support and improve customer quality service
- Manage and guarantee resolution of customers concerns on a daily basis working closely with Production Quality ( Incident analysis, Action plan,…)
- Develop and drive quality improvement programs with customers
- Assist with project definition for overall quality improvement processes
Philadelphia, PA
Operations & Customer Quality Engineer
Philadelphia, PA
Schmeler, Kshlerin and Connelly
Philadelphia, PA
Operations & Customer Quality Engineer
- Manage external and internal resources for development or re-engineering of new or existing business processes
- Assists in the development, application, revision and maintenance of quality standards
- Assists in the development of methods and parameters, project methodology and/ or project proposals
- Ensures divisional business process organization is properly managed and staffed' define and implement cross functional performance measures
- Analyze operational data; Develop and implement recommendations. Participates in and may lead audits
- Develops methods and parameters, project methodology and/ or project proposals
- Develops quality training and courses. Monitors current quality training to ensure compatibility with current programs
present
Chicago, IL
Senior Customer Quality Engineer
Chicago, IL
Paucek-Harber
present
Chicago, IL
Senior Customer Quality Engineer
present
- Responsible for scorecard management reviews and applying corrective actions to manage the customer scorecard to ensure positive ratings for our products
- Recommend and drive improvements to facilitate customer satisfaction
- Investigate and recommend processes and improvements for resolving, eliminating and preventing negative quality issues
- Responsible for developing detailed knowledge of the customer’s product and processes
- Meet with customer representatives to provide technical support for product functionality or processing concerns
- Provide outstanding customer support with investigation updates
- Complete other projects and activities as assigned by Customer Quality Sr. Manager
Education
Education
Bachelor’s Degree in Engineering
Bachelor’s Degree in Engineering
University of Tennessee
Bachelor’s Degree in Engineering
Skills
Skills
- Nationally recognized quality certification desired. (e.g. American Society for Quality Certified Quality Engineer (ASQ-CQE) certification)
- Ability to interpret an extensive variety of technical instructions in mathematical or diagram form, and deal with several abstract and concrete variables
- Strong written and verbal communication and presentation skills and ability to influence others
- Ability to develop and maintain good relationships with customers
- Good English language ability in reading, writing and speaking
- Solid interpersonal skills and ability to effectively work with peers, both internally and with customers
- Basic understanding of the Woodward PLC process and quality planning tools
- Basic understanding of quality management systems
- Delivering quality work product while gaining experience and knowledge in specific area of focus and in company methods of operation and procedures
- Facilitate basic/local reviews with the support of senior team members. Gather solutions to quality issues with minimal supervision
15 Customer Quality Engineer resume templates
Read our complete resume writing guides
1
Senior Customer Quality Engineer China Shenzen Resume Examples & Samples
- Monitor customer quality performance, analysis of customer returns and maintain customer documentation database
- Flexibility, willing and able to travel to the customer’s site to assist in product quality problem solving and communications, locally within China, but also in adjacent markets of Japan and Korea
- Lead and organise customer meetings, and audits
- Manage and complete customer queries and questionnaires as required to ensure timely response
- Work closely with Sales and Field Applications Engineering to establish processes and reporting to measure responsiveness to customer requirements
- Benchmark MACOMs performance with Key customers versus our competitors
- Electrical Engineering Degree or equivalent level of experience and/or training. 5 years prior experience in a high-tech company. Excellent human relations skills
- Proactive and can demonstrate a track record of working on own initiative
- A good listener, experience with the concept of capturing the Voice of the customer in New Product design releases
- Familiarity with RF devices is a bonus
- Must have at least five years of working experience with broad exposure to IC wafer fab, assembly and test processes. Understanding how semiconductors work, how they are tested and how they fail is required
- Must have project management skills and a track record of successfully leading cross functional teams in 8D and/or quality improvement projects
- Must have a solid understanding of quality system requirements and quality tools such as 8D, Cause & Effect Diagram (fishbone), control plans, SPC, FMEA and demonstrated analytical skills to use the data driven approach to solve customer quality issues
2
Customer Quality Engineer Resume Examples & Samples
- Good knowledge of computer science (HW, SW)
- Be familiar with SMT process, factory operation, quality management system
- Good knowledge/experience in customer management
- Fluent written/read English
- Strong skills of interpersonal, communication/presentation, negotiation and/or influencing
- Bachelor or Mater's degree in Computer Science or Electrical Engineering
- At least 8 years of relevant working experience
3
Intern Customer Quality Engineer Resume Examples & Samples
- Supporting customers with Quality and/or Reliability issues or concerns, including information requests and managing customer technical issues to resolution
- Working on several improvement projects, including customer improvement projects as well as internal improvement projects, such as tools development (programming skills would be an advantage)
- Assisting with 'Keeping The Business Running' such as product health monitoring
- Ability to quickly learn about new products and technologies,
- Excellent verbal and written communication skills in English,
- Capable of working unsupervised by prioritizing work and focusing on meeting agreed objectives in required timeframe,
- Ability to integrate quickly with existing team so that maximum contribution to team goals can be quickly achieved,
- Excellent analytical problem solving skills,
- Good attention to detail,
- Understanding of basic PC architecture,
- Desktop and/or notebook hardware familiarity (practical skills),
- PC hardware and software architecture familiarity,
- Microsoft Windows* Operating System familiarity beyond that of a general user,
- Programming knowledge in HTML and/or XML, scripting languages would be an advantage,
- Keen personal interest in computing would be an advantage
4
DSS Maritime Customer Quality Engineer Resume Examples & Samples
- Provide general program support as required by program management and the DSS Customer Quality manager
- Interact with design engineering, manufacturing engineering, operations, and suppliers
- Present status updates to related IPT leads, Program Manager, Customer Quality Manager and the Customer when required. This is a Customer Quality Engineer (QE) position supporting the DSS Maritime Military program located in Stratford, CT. The QE will be expected to communicate between team members, Sr Management and in some cases, customer counterparts to provide assurance of contractual and specification requirements. In this role, the QE will
5
Customer Quality Engineer, Lights Resume Examples & Samples
- Establish and maintain metrics that represent the total picture of Lights quality
- Help to develop the structure for the various commercial platforms
- Lead efforts to perform root cause and corrective action activity on Product Quality investigations both manufactured and supplier parts
- Represent Customer Quality on various program related teams and provide support for CSS ACE objectives
- Provide program support as required by program management and the Sr. Customer Quality manager
- Provide Core Quality support as required by Core Quality Sr. Leadership
- Contribute to Integrated Product Team (IPT) initiatives
- Present status updates to related IPT leads, Program Manager, and Senior Customer Quality Manager
- International Trade Compliance
6
DSS Customer Quality Engineer Resume Examples & Samples
- Lead/coordinate efforts to perform root cause and corrective action activity on both manufactured and supplier parts
- Drive product and process improvements for military programs in all phases of production and acceptance
- Represent Customer Quality on various program related teams and provide support for program ACE objectives and flight safety part issues
7
Customer Quality Engineer Resume Examples & Samples
- Participate in team activities to maintain and continuously improve on the department’s KPI’s
- Prepare summary reports on non-conformances for Management review and corrective action
- Recommend solutions to non-conforming material through designated channels. Assist in the implementation and verification of the corrective action effectiveness
- Prepare management summary reports on customer issues for Management review and corrective action
- Participate in supplier and customer quality audits as directed by the Department Manager
- Liaison and coordinate activities to provide prompt resolution to customer directed concerns
- Monitor and respond to customer concerns using the customer prescribed format
- Provide communication link between the customer, liaisons and plant personnel
- Recommend solutions to customer concerns through designated channels
- Provide verbal and written communication to the costumer
- Assist Supplier Quality with issues that directly or indirectly effect the customer
- Participate in continuous improvement and APQP teams as assigned by the Department Manager
- Assist all personnel in the details of the control plan, customer quality specifications and quality expectations as directed by the Department Manager
- Flexible hours of work essential to support production and customer submission requirements
- Perform other duties as assigned by the Department Manager
- Minimum three years’ experience in quality and process control in automotive painted plastic parts manufacturing
- Demonstrated strong oral and written communication skills required
- Must be computer and internet savvy
8
Senior Customer Quality Engineer Resume Examples & Samples
- Be the lead Quality interface and Voice of the OEM Customer
- Champion suspect product (speaker, amplifier, head unit) field investigations to closure
- Provide outstanding customer support with investigation updates
- Conduct preventative quality visits at customer locations for a proactive quality approach
- Responsible for developing detailed knowledge of the customer’s product and processes
- Meet with customer representatives to provide technical support for product functionality or processing concerns
- Investigate and recommend processes and improvements for resolving, eliminating and preventing negative quality issues
- Recommend and drive improvements to facilitate customer satisfaction
- Responsible for scorecard management reviews and applying corrective actions to manage the customer scorecard to ensure positive ratings for our products
- Analyze, compile, review and regularly report customer quality metrics such as PPM/ 0km performance. Develop presentations for quality reviews by internal and customer groups
- Represent Harman at customer meetings, conferences and training; Assure Harman is current and in compliance with customer quality requirements
- Minimum education: Bachelor’s degree with a preference for engineering or equivalent (electrical or mechanical)
- Minimum 5 years of progressively responsible and successful experience in an automotive quality role, or a combination of engineering and quality roles in an operations environment
- Minimum 3 years of experience with automotive electronics, preferably audio and/or infotainment modules
- Must have 2+ years of experience using AIAG guidelines (APQP, PPAP, PFMEA)
- Practical experience in root cause analysis using tools, Fault Tree Analysis, Root Cause Failure Analysis, Fish bone, Pareto, 5Y, Is-Is not, Cause and Effect, etc
- Excellent interpersonal, organizational, verbal and written communication skills required
9
Customer Quality Engineer With German Resume Examples & Samples
- Give a continual, dedicated and focused support to the Customer on quality matters
- Improve continually the external (Customer) quality performance of the plant by interacting with other dept. within Honeywell bringing the Customer voice into the organization by setting-up specific opportunities
- Quality Performance: ensure a continual monitoring of the key metrics (e.g. PPM, nr. of Incidents). Perform numbers’ reconciliation in case of discrepancies
- PPAP: ensure basic requirements and Customer specific ones for new applications’ initial submissions and following all successive PPAP submission due to running changes (i.e. relay out, HLRR, capacity increase, design changes etc.)
- Self-Assessment audit management as specific CSR (i.e. MMOG-LE (Volvo-GM-Ford)/QSB (PSA-GM)/Ford MSA/VDA 6.3 (German Customers) leading and coordinating the audit and action plan at plant level
- Product Launch: interact with CET organization in relation to new product launches managing the quality side and ensuring the Customer requirements’ implementation
- Product: interact with Application Engineering team on product improvements
- Corrective Action Management: lead the management of non-conformances/failures through the 8D systematic (CAR). Share information with Customer
- P-FMEA: participate to process FMEA teams, providing input on failures’ occurrence, severity and Customer requirements
- Process Auditing: leading BIQ (Built in Quality) and Gemba Walk on monthly basis on each Module in order to guarantee the respect of HTT and Customer Quality standard
- Process Auditing: participate to internal auditing by bringing the “Customer Eye” into processes. Leading Customer audits at Honeywell
- Fast response, including visit at Customer premises and/or suppliers for jointly analysis
- Reject Management (PLR and Warranty): facilitate/supervise the root cause definition, paying attention to minimizing the investigation lead time. Coordinate internal and external information flow (reports) and correct and reliable data recording
- Join actively on HOS review, leading Kaizen event and projects focused on Quality continuous improvement
- Join daily on Tier 2 and Tier 3 meetings
- Join on NPI regular meetings supporting proactively NPI/Running changes RAIL
- RMRA regular reviews with SQA Dept. in order to evaluate suppliers deviation requests
- Participate to the HLRR project by capturing, highlighting and ensuring Customer qualification requirements
- Technical Expertise: supervise the technical analysis performed by customer quality technicians
- Concession/Deviation Management: gather the concessions/deviations approvals from the Customers
- Warranty: provide support to regional organization
- University degree (engineer or equivalent) required
- Minimum of 3 years’ experience in industry, preferably in the automotive sector
- Fluent in Italian – mandatory
- Fluent in German - mandatory
- Lean Manufacturing skills
- Core Green Belt Certified
- Knowledge of Operational System principles
- Good leadership skills
- Good knowledge of company processes
- Very good verbal & written communication skills
- Good interpersonal skills with the ability to gain co-operation& commitment to activities required and with experience of developing and maintaining an effective network of business contacts in order to achieve goals /actions needed
- Good planning & organizing skills with experience of determining priorities, coordinating multiple activities meeting multiple timelines
- Good knowledge of production processes
- Very Good problem solving skills with experience of developing & implementing solutions to diverse issues
- Good knowledge of process auditing procedures of European Automotive Industries
- Good knowledge of PPAP, APQP, MSA, 8D, FMEA, SPC, Process Auditing
- Drawing reading and review
10
VW Customer Quality Engineer Resume Examples & Samples
- Coordinates all VW customer product quality issues (defects and malfunctions) as collected and reported via the VW Customer Product Quality Team
- Manages the data analysis process, providing root cause analysis, and providing recommended implementation steps to the Manager, Group Customer Quality
- Ensures that the agreed upon implementation steps are executed. Conducts direct follow-up with all relevant parties in production, technical development, and factory quality in order to see quality issues through to resolution
- Defines quality targets with key factory stake-holders to track and improve product quality
- Collaborates with relevant individuals at JD Power, Consumer Reports, and like entities to assure Group efforts realize maximum potential
- Provides support to the Product Design Manager and Marker Support Manager for VW and Audi to assure activities are aligned and best practices are shared
- 5-7 years of experience required
- Significant professional years of relevant engineering/technical experience with VW/Audi or other OEM
- Analytics and Statistics
- Working knowledge of computer systems and customary business applications
- Technical familiarity with Volkswagen products, market positioning, and competition
- Bachelor's Degree in Engineering, Quality, Automotive Technology, or related field or equivalent
- Master’s Degree in Engineering, Quality, Automotive Technology, or related field
- Strong networking, influencing, and negotiation skills
- Strong knowledge of quality processes
- Excellent customer focus and resource management
- Ability to evaluate quality complaints taking into account the US Markets' unique standards
- Technical knowledge of VW specifications
- German and Spanish Language skills beneficial
11
Customer Quality Engineer Resume Examples & Samples
- Coordinate with Quality, engineering & manufacturing teams to discuss and resolve product quality issues raised by customers
- Participate in product quality planning and control process based on customer’s specifications and requirements
- Support customer RMA tracking & resolution from receipt of RMA to customer shipment. Responsible for creation of customer related reports such as 8D reports
- Conduct internal process and product audits, report results to management and initiate appropriate corrective actions
- Coordinate RMA analysis for problem root cause determination and corrective action
- Perform quality inspections and evaluations of product to verify conformance to specifications and determine process capability
- Prepare and update all necessary quality reports as required by customers
- Participate in new product introduction design reviews. Generate and issue new product quality plans
- Review and approve ECR and ECO for conformance to quality standards and requirements
- Support all core quality systems requirements for ISO/TS management and coordination
- Quality or Manufacturing Engineering experience – 3-5 years
- Direct experience supporting an ISO/TS quality management system
- Experience conducting quality audits for process, product and QMS
- Well versed in the use of quality data analysis tools and statistical techniques
- Proficiency with Excel, database tools, and product lifecycle management and manufacturing systems is required
- Ability to plan and prioritize activities, perform and monitor multiple overlapping tasks/operations to meet schedule
- Must be able to travel (~25%)
12
Customer Quality Engineer Resume Examples & Samples
- Represents customer’s interest in the quality of the sold products, both in 0 km cases and during the warranty period
- Decides blocking/ unblocking the deliveries when quality issues impacting the client occur
- Coordinates the on-site homologation activities of the new products according to customer’s requirements. Is responsible for the PEP phase 5 to 8 associated to the job
- Participates to the homologation of the process and product modifications assuring that the customer requirements are followed
- Participates to the daily HOS meetings according to the plan
- Participates into daily „Gemba walk”( Go&See)
- Issues standard work
- Coordinates and conducts the teams designated to analyze customer quality incidents
- Is responsible for implementing immediate customer protective actions in case of customer complaints
- Collaborates with the other sites’ customer Quality engineers by sharing information related to quality issues and implemented solutions
- Evaluates the efficiency of the preventative and corrective actions initiated after a customer quality incident
- Coordinates the quality analysis of the customer returned products
- Coordinates the customer visits and audits on site
- Maintains up-to-date the customer incident reporting system
- Acts according to Honeywell behavior requirements for reaching the performance targets agreed with the manager through HPD system
- Uses LSW tool on a daily basis and updates it on a quarterly basis
- Actively contributes to the continuous improvement of the site performance indicators inconstantly identifies ways to reduce the wastes and to improve own activities as well as site ones
- Proposes the number of Kaizen ideas/ month according to the site’s objectives
- Participates in all the meetings where his/ her presence is required
- Follows the HS&E rules and responsibilities
- Any other tasks coming from hierarchical managers
13
Operations & Customer Quality Engineer IV Resume Examples & Samples
- Manages QMS and ensures compliance to requirements through internal audits, external certification ISO standards and sourcing audits via Applied's SSQA process
- Develop, applies, revises, and maintains quality standards for processing materials into partially finished or finished products. Designs and implements methods and procedures for testing and inspecting the quality level of products and equipment
- Identify systemic issues and drive continuous improvement across the assigned business unit
- Identify systemic issues and drive continuous improvement across the assigned business unit. Success in this role will be measured against business unit customer satisfaction indices and customer quality indices
- Drives enterprise wide change management to ensure proper alignment across regional business units and global factories in order to minimize quality issues and improve customer satisfaction
- Interacts with customers and functional managers and engineers in product development, design, test, marketing, sales, planning, manufacturing, etc. These interactions often are with regard to potential, real or perceived customer quality or reliability concerns arising from technical, administrative or logistical events
- Interfaces with customers, vendors, and various company departments to resolve quality problems and provide information
- Coaches, mentors and conducts training for targeted organizations on quality processes. Reduces qualification cycle time and cost while still meeting reliability performance requirements
- Demonstrates depth and/or breadth of expertise in own specialized discipline or field
- Communicates difficult concepts and negotiates with others to adopt a different point of view
14
Operations & Customer Quality Engineer Resume Examples & Samples
- Develops and applies quality standards in accordance with company and customer requirements. Develops and conducts related tests
- Designs and implements methods and procedures for inspecting, testing, and evaluating the precision and accuracy of products and/ or production equipment
- Develops methods and parameters, project methodology and/ or project proposals
- Develops and uses procedures. Prepares documentation for inspection/ testing procedures. Recommends corrective action for procedural, product, or process deficiencies
- Gathers operational and test data and evaluates results
- Utilizes drawings, specifications, industry standards, and sketches, adapting inspection measuring devices and procedures when necessary. Read and interpret technical drawings and specification requirements
15
Operations & Customer Quality Engineer Resume Examples & Samples
- Manages the company-wide administrative quality program and related business processes. This includes the definition, specification, and implementation of standards, methods and procedures for developing quality programs
- Create and Manage teams to drive center of excellence to support various corporate initiatives and drive value addition to centralized resource pool. E.g QMS, Analytics, Business Excellence, Common Tools and Methods
- Provides leadership and support to business groups in meeting quality assurance system requirements along with department and company goals and objectives with primary consideration for safety, quality, productivity and cost
- Develops quality training and courses. Monitors current quality training to ensure compatibility with current programs
- Develops strategic measurement systems to monitor company performance and analyzes data to determine requirements for quality programs. Owns and tracks business unit/ program/ project metrics and deliverables
- Evaluates current operations for performance against quality standards. Organizes interdepartmental activities ensuring completion of the project on schedule and within budget constraints. Provides feedback on employees’ performance to their respective managers
- Provides inputs and recommendations for the adoption of good quality practices in marketing, engineering, and manufacturing. Applies advanced principles, theories, and concepts
- Develop, deploy and maintain business process development programs for business units. Processes may include one or more areas such as manufacturing, IS&T, quality, service, design, reliability, etc
- Manage external and internal resources for development or re-engineering of new or existing business processes
- Responsible for linking business development or re-engineering activities and initiatives to business unit or division strategies and functional group objectives
- Ensures divisional business process organization is properly managed and staffed' define and implement cross functional performance measures
- Tracks business process policy implementation across business unit; coordinate cross company business process development initiatives
- Applies advanced principles, theories, and concepts
- Maintains an on-going quality improvement program aimed at enhancing the Company's quality systems, controlling manufacturing processes and improving end product quality. Plans designs, acquires, implements applications and tools, especially those which facilitate collaborative work and/or enhance productivity
- Proliferate the need of Living QMS/Business Process Systems and make QMS/Business Excellence respected within the organization
- Interface with Customers, External Auditing Agency and BU's on Audit Planning, Execution and CLCA's including report out to Mgmt. every Qtr. on the status
- Drive the need by creating value beyond QMS to Business Excellence and move the organization step by step towards that
- Drive integration by common processes, proliferate corporate standards, tools, processes, continuously drive BKM's across the BU's from the process/systems standpoint
- Work closely with the corporate M&A group and tie - in to their roadmaps for doing a due - diligence process audit and then coming up with a GQR Integration plan for new companies we acquire and do the best fit analysis on process integration
- Look at integrating new groups added through acquisition or newly created into the overall corporate ISO 9001 certification/ SSQA process
- Coordinate overall closed loop continuous improvements coming out of internal/external audits, customer escalations, business need and look at overall process change mgmt. including showing improvement metrics to link process changes to business gains
- Understand industry best practices and tie them in to quality roadmaps after business case preparation and acceptance with BU's
- Look at company wide process gaps through the corporate audit tool and trend them to go fix systemic issues across the board
- Compile and present corporate process scorecards to monitor the health of the QMS
- The above job duties and responsibilities are intended to describe the general nature of the work and are not intended to be an exhaustive list of all responsibilities. Duties and responsibilities may change or vary depending on the specific needs of the business unit
- 18+ years quality directly related experience including 10 years project and management experience
16
Senior Customer Quality Engineer Resume Examples & Samples
- Supervise a team of Customer Quality Engineers and ensure all actions are completed to a high standard and on delivered on time
- Represent the voice of the customer, and to manage the maintenance and improvement of the customer concern process
- Manage APQP programs from design concept through to volume introduction into production and support new product launches and VA/VE programs
- Liaise with internal departments to assist in meeting product targets
- Develop, communicate and maintain quality system procedures and use appropriate improvement methodologies for processes and products
17
Customer Quality Engineer Resume Examples & Samples
- Coordinate the Customer Quality Engineering support for China Customers in cooperation with local Sales/Account team activities to ensure that customer requirements are understood and addressed in a timely and effective manner
- Directly Lead the Customer Quality communications for key Entegris product lines
- Oversee response programs internal/external quality metrics including but not limited to: Customer Requests, Customer Complaints, Customer Scorecards and Customer Audits and develop long term plans to address any gaps to customer expectations and requirements
- Ensure product implementation and compliance with SPC (Statistical Process Control) and SQC (Statistical Quality Control) in alignment with agreements with customers and in accordance with EQOS (Entegris Quality Operating System) protocols
- Ensure appropriate and timely communications of CIP (Continuous Improvement Process) programs to the customer as well as support effective and appropriate change management, in accordance with agreed upon customer requirements
- Document Customer Complaints (CC) and work to identify the root cause and implement corrective action to prevent reoccurrence based on the data provided by all internal functions/organizations and through support of direct customer interactions
- Develop relationships across worldwide quality teams, investigating issues and drive the Voice of the Customer (VOC) for quality throughout the operations organization
- Interpret and cascade the Entegris Quality Assurance philosophy to personnel in the organization
- Perform Quality Engineering reviews of design and documentation for both new and existing products
- Manage and report on Customer Quality status for all product lines and regional customers during regular management reviews
- Experience in a quality role, in the semiconductor industry and team management experience
- Experience with applicable quality tools such as pareto, FMEA’s, SPC/SQC, histograms, trend analysis, process mapping, design of experiments, cause and effect diagrams, 8D problem solving methodology
- Thorough understanding of requirements associated with the ISO 9001 quality standard
- Proficient and practiced level of Business English both Written and Spoken
- Communication skill, leadership ability to drive all action, high accountability to achieve the goal, customer management skill, problem solving skill, analysis skill, result driving
18
Senior Customer Quality Engineer Resume Examples & Samples
- Responsible for field containment and rework activities at customer locations, such as product diagnostic tests, assembly line investigations and assembly plant yard-hold management
- Support and maintain policies and practices related to manufacturing support of 0km issues at customer assembly plants and quality situations related to product application in vehicles
- Analyze, compile, review and regularly report customer quality metrics such as PPM or S-IpB for 0km performance. Prepare presentations from quality data for reviews by both Harman and customer management groups
- Obtain customer approvals for manufacturing process change(s) by providing supporting data for the change(s) and submitting to customer in their required format
- Lead problem analysis and improvement efforts by applying the use of modern quality tools such as FMEA, 8D, Kaizen, Lean Manufacturing principles and Six-Sigma methodologies
- Support AQP activities with customer and Harman manufacturing to facilitate PPAP submission according to customer schedule
- Complete other projects and activities as assigned by Customer Quality Sr. Manager
- Minimum experience: 5-7 years of in automotive quality and/or operations in electronics, or electromechanical manufacturing
- Minimum 3-5 years experience with automotive electronics. Audio and/or infotainment preferred
- Previous experience working with General Motors assembly plants and Supplier Quality. Working knowledge and use of GM SupplyPower web portal, especially GQTS and SQMS
- Must have 2+ years experience using AIAG guidelines (APQP, PPAP, PFMEA)
- Practical problem solving using: 8D, A3, Fault Tree Analysis, Pareto, 3L-5Y, Is-Is Not, Fish Bone, etc
- Excellent interpersonal, organizational, verbal and written communication skills
- Experienced presenter
- Skilled in Microsoft Office including Word, Excel, Visio and PowerPoint
- Familiar with CANALYZER / flash scripting, hardware and / or software experience
- Master’s Degree in Mechanical, Electrical or Industrial Engineering
- Electronics Knowledge
- ISO 14001 and TS 16949 Experience
- Strong computer background with ability to calculate and analyze data, generate reports
- Over five years of technical acoustic/electronic experience
19
Customer Quality Engineer Resume Examples & Samples
- Perform L0 triage including
- What and where analysis
- Determining whether a Micron-caused issue exists
- Identify the correct return location for FA diagnostics and provide customer with RMA number and return address
- Perform L1 triage where feasible (in discussion with FAE) to understand the isolate the root cause of the issue
- Determine if hot site support required SSD (SSD PE) and components (CEL)
- Review internal updates provided by SCQE and communicate ongoing progress to customer
- Review final FA or 8D report with customer and close customer request
- Manage Issue resolution process from customer receipt until close of TAT
- Make updates to action item tracking list for each and all RMA request per customer
- Responsible for internally communicating customer driven unplanned events
- Responsible for supplying input to Stop Ship and customer unplanned event scorecard
- Manage communication of resolution plans of internal and customer issued stop ships
- Collaborate with sales/supply chain/site CQE on missed shipments
- Determine if customer communication is required
- Deliver customer message and track to closure
- Provide data from customers to internal teams in the areas of QBR scoring, product performance (IFR, yields), and other key customer measures
- Drive quality score improvement plan for each customer by assigning actions, establishing owners, and establishing schedules
- Electronics
- Engineering - Electrical
- Engineering - Industrial
- Engineering - Materials Science
- Customer Experience
20
Customer Quality Engineer Resume Examples & Samples
- Define and enforce the scale of demerit products coherent with the customer's specifications
- Manage and guarantee resolution of customers concerns on a daily basis working closely with Production Quality ( Incident analysis, Action plan,…)
- Validate the packaging range and accept the packaging range
- Bachlor's degree in engineering
21
Customer Quality Engineer Ii Temporal aÑo Resume Examples & Samples
- Responsible for following and administering QSR policies and procedures, and ISO Standards
- Compliance with Environmental Management System (EMS) and Good Lab Practices (GLP)
- Other responsibilities may be assigned and not all responsibilities listed may be assigned
- Associate Engineer responsibilities above plus
- Ensures timely reporting of PI’s, MDR’s, Weekly/Monthly reports and PI status update is current in the network
- Ensures all necessary tools and equipment are available
- Performs and schedules resources for Product Complaint Analysis
- Assists with complaint analysis and failure investigations daily and documents analysis results and information for Med Watch Reports on all product families assigned
- Provides support in product transfers and new products development, as required
- Assists in training new associate Engineers or technician to complaint investigation process
- Initiates AFC and activity plan change requests process for their assigned franchise
- Participate in process/ quality improvements projects
- Contributes to writing customer letters as required using IFU’s and product investigation knowledge
- Primary Engineer -perform responsibilities above plus
- Responsible for performing and approving complaint analysis and failure investigations daily on all product families assigned
- Gets involved with providing feedback and assistance for product transfer analysis and new products development, as required
- Knowledge of all FGQA quality assurance functions for the product families assigned
- Responsible for ongoing improvement of analysis conclusions using IFU’s and product investigation knowledge
- Interacts with BU and Plant Quality teams to improve on quality issues
- Responsible for providing complaint information back to the BU and Plant Quality as required
- Establishes and maintains appropriate documentation as required for Quality improvement initiatives related to complaint process
- Bilingual: English/ Spanish required
- Analytical required
- PC experience mandatory
- Proficient in word processing, spreadsheet, presentation, database applications
22
Customer Quality Engineer Resume Examples & Samples
- Technical studies/ university degree
- Minimum 1 year experience in automotive industry
- English language full proficiency
- German Language required
- Quality core tools knowledge desirable; process capability, PPAP, MSA, 6 sigma
- MS Office package
- Driver license
- Mechanical drawing reading (ANSI & ISO)
23
Customer Quality Engineer Resume Examples & Samples
- Utilize statistical tools and appropriate investigative techniques to analyze complaint root cause and corrective actions
- Ensure complaint investigations are robust and well documented
- File MDR (Medical Device Reporting) and MDV(Medical Device Vigilance) reports as necessary to health authorities such as FDA
- Escalate events in a timely manner and per procedure
- Ensure key department metrics (such as complaint closure and health authority reporting timeliness) are met
- Summarize the results of various data analysis into clear and concise presentations and reports for peers, cross-functional teams and management
- Support such activities as post market surveillance, complaint reports and safety signal detection
- Interface with key business partners including research and development, regulatory and compliance, operations, service and repair, medical affairs, medical safety, post market surveillance and international affiliates as required
- Support the CAPA process as necessary
- Support any Internal and External Audits as necessary
- A minimum of 2 years of experience in a GMP and/or ISO regulated environment is required
- Experience in the Medical device industry is preferred
- Previous experience quality engineering is preferred
- Root cause analysis skills are required
- Experience conducting and reviewing complaint investigations highly preferred
- Knowledge and understanding of regulatory requirements relative to complaint handling is highly preferred
- Experience with Medical Device Reporting or Medical Device Vigilance forms is preferred
- Ability to collaborate with business partners at all levels is required
- Knowledge of process and design excellence tools preferred
- Excellent communication and presentation skills required
- This position will be located in Raynham, MA and will have up to 10% domestic travel
24
Customer Quality Engineer Resume Examples & Samples
- Bachelor or master's degree in engineering (preferred computer science or electronic engineering)
- Good knowledge on IT (computer, smartphone etc) HW and SW
- Fluent English both oral and written
- At least 5 years working experience, Factory work experience preferred
- Experience in SMT, mfg process and quality control
- Good inter-personal communications skills
25
Customer Quality Engineer Resume Examples & Samples
- Develop, implement, and maintain technical quality management projects and tools that support and improve customer quality service
- Drive resolution for customer quality issues
- Manage failure analysis and reliability
- Assist with project definition for overall quality improvement processes
- Lead project teams in related quality initiatives
- Provide customer quality engineering support for customer factory visits and audits
- Develop and drive quality improvement programs with customers
- Build strong customer relationships, and drive improvements to close requirements gaps
- Ideal candidate will have 10+ years of semiconductor engineering experience in a Reliability and/or Quality/Product Engineering role
- BS in Electrical Engineering, a MS or MBA is preferred
- Candidate is expected to be an extremely well organized individual with an ability to manage several competing issues simultaneously
- Strong customer interface, communication and presentation skills are necessary as well as structured problem solving and organizational abilities
- Understanding of quality and reliability engineering tools
- Deep knowledge of semiconductor manufacturing processes
- Experience applying JEDEC quality related standards, ISO and the science behind them
- Must know reliability fail modes of silicon/packaging technologies and fail mechanisms with respect to reliability
- Experience in auditing supplier sites, materials and processes
- Experience in driving suppliers in the areas of silicon Fab process / packaging / assembly, test, on-going reliability monitoring, post-production qualification
- ---
26
Customer Quality Engineer Seniors IN Resume Examples & Samples
- Six Sigma methodologies including Voice of Customer (VOC), Measurement Systems Assessment (MSA), Failure Mode Analysis (FMEA), Design Failure Modes and Effects Analysis (DFMEA), Cause and Effect(C&E), and Control Parameter Management (CPM)
- Change management tools and processes
- Pugh method and Minitab
- ISO 9000 and TS 16949 standard
- Diesel Engine performance to identify failure modes
- Advanced Product Quality Planning (APQP) and Product Part Approval Process (PPAP)
- Corrective action request (CAR) and supplier corrective action request (SCAR)
- Document in writing, draw conclusions, and make recommendations
27
Customer Quality Engineer Resume Examples & Samples
- Customer quality requirement implementation in company level
- Lead the new product and new project quality and manufacturing launch and to ensure the quality to meet customer requirements
- Review the quality documentation that to be submit to customer
- Prepare the quality issues report to customer
- Lead and push the company internal quality continuous improvement
- Monitor process quality and system
- Leading the six sigma project to save the cost
- Customer quality complaints handing
- To implement the corrective/preventive actions and reduce the DPPM to make customer satisfaction
- Customer quality and engineering support. To fast solve the problem in customer company
- Assist QA Manager to control the project/product quality system
- Assist QA Manager in daily quality problem learning and solving
- Building up good team relationship with other department to achieve company top target
- Strong ability in organizing and prioritizing projects
- Conversant in MS Office applications both in English and Chinese versions
- Very good command of both written and spoken English
28
Senior Customer Quality Engineer Temporal aÑo Resume Examples & Samples
- Follow all company safety policies and other safety precautions within the work area
- Compliance with safety policies and procedures
- Inactive Records and Information Management, Vital Records and third party vendor if applicable
- If assigned as department records coordinator responsibilities listed in CP000263 are applicable
- Provides specific technical expertise to support product and process improvements
- Provides technical input to project teams, such as R&D, CAPA, and coordinates protocols, Engineering studies and/or pilot, processes as required
- Assists with implementation of EES applications for quality systems
- Owner for key operational metrics for their particular product families
- Responsible for ensuring that the NPD process with reference to the complaint analysis is transferred in a timely manner as it relates to the creation of AFCs, activity plans, and the execution of the protocol
- Review and approve AFC and activity plan change requests for their assigned franchise
- Ongoing interaction with the CAPA franchise for the product families assigned
- Have knowledge of all quality related aspects pertaining to complaints for the assigned franchise (CAPAs, NCRs, etc)
- Participate in the Rapid Respond teams for product families assigned
- .Assists in training engineers and technicians to complaint investigation process
- QSR/ISO knowledge preferred
- Technical writing skills for Customer Letters required
- Knowledge of risk management required
- Failure investigation tools knowledge preferred
- Strong Communications skills required
- Medical device product knowledge preferred
- Statistical Analysis Software
- Knowledge of EES information systems such as Siebel, AQR, CAF, NCR, CAPA, Audit and ERP preferred
29
Customer Quality Engineer Resume Examples & Samples
- Coordinate the Customer Quality Engineering support for European Customers in cooperation with local Sales/Account team activities to ensure that customer requirements are understood and addressed in a timely and effective manner
- Oversee response programs internal/external quality metrics including but not limited to: Customer Requests, Customer Complaints, Customer Scorecards & Customer Audits and develop long term plans to address any gaps to customer expectations and requirements
- Ensures appropriate and timely communications of CIP (Continuous Improvement Process) programs to the customer as well as support effective and appropriate change management, in accordance with agreed upon customer requirements
- Interprets and cascades the ENTEGRIS Quality Assurance philosophy to personnel in the organization
- Performs Quality Engineering reviews of design and documentation for both new and existing products
- 5 years of experience in a quality role, in the semiconductor or similar industry and customer communications experience
30
Customer Quality Engineer Resume Examples & Samples
- Bilingual (Slovak-English), French is appreciated
- Competency in relevant automotive quality practices and assigned customer’s specific requirements
- Competent in relevant languages: local plant’s, customer’s and English. (Customer or English language competency is required; both are preferred)
- Project management to lead cross-functional teams in CAR and other quality activities
- Six Sigma Green-belt and DFSS certification (minimum within 6 months); Black-Belt (preferred)
- Understands applicable product liability and legal requirements and procedures
- Responsive and responsible to deliver on commitments
- Strong communicator, externally and internally
- Motivates and influences others without direct authority
- Well organized to manage multiple competing priorities in parallel
- Assertive in representing customer internally and HTT externally
- Willing and confident to make commitments
31
Customer Quality Engineer Resume Examples & Samples
- Supporting customers with initial return evaluation in order to confirm component issue
- Interfacing with internal failure analysis (FA) teams and provide feedback from the customer to assist with the analysis
- Completing customer reports in a detailed and timely manner including translating internal analysis into various FA methods including 5-why, fishbone, fault tree analysis and FMEA (including RPN) as required for each incident or customer
- Developing instructions and procedures to assist with debug of image sensor based systems at the customer side in order to ensure efficient cycle times and minimise unnecessary returns
- Supporting customer audits and coordinate the implementation of any required improvements
- Liaising with the customer regarding all quality related communications including PCN, PPAP, RMA and customer returns
- Degree in Electronic Engineering or similar
- 2+ years experience working in the semiconductor or related industry
- Experience of electronic debug laboratory equipment and processes
- Excellent communication skills and an ability to work well with the customer
- Should be willing to travel including internationally. Typically up to 5 days per month
- Familiarity with image sensors would be a plus
- Experience in automotive electronics industry also a plus
32
Customer Quality Engineer Resume Examples & Samples
- Review complaint investigations to ensure that investigations are adequate and consistent
- Coordination and monitoring of complaints during the complete investigation phase, including overall responsibility of any assigned complaints
- Statistically review Complaints and investigation results to make assessments for escalation or review by cross functional team
- Identify potential Field Actions and initiate the necessary actions
- Communication of complaint investigations results to internal and external customers
- Perform product evaluations as necessary
- Maintain current knowledge of the MDD/FDA regulations
- When appropriate); consider innovative solutions to meet changing regulatory and internal compliance goals
- Strong written and oral communication and interpersonal (listening) skills
- Must have ability to lead efforts aimed at the identification of problematic situations, the reporting of issues, and the development of resolutions and decision making
- Experience in a regulated industry (medical device or pharmaceutical). Post market regulatory, quality or compliance areas preferred
- Must be able to read drawings and analyze quality documents
- Good knowledge of the ERP system (SAP) to track products
- Familiarity with basic quality tools and techniques
- Analytical and Critical thinking skills are essential
- Knowledge and understanding of regulatory requirements relative to complaint handling and quality systems as a whole
- A minimum of a Degree in an applicable scientific/engineering or regulatory/quality discipline is required and a minimum of 3 years’ experience years’ experience in a regulated industry (medical device. pharma, automotive, and/or pharma) is preferred
- A minimum of 3 years of experience working within complaint handling, Regulatory Affairs, Quality Assurance or product complaints is required
- Extensive knowledge of Quality Systems (21 CFR 820/ISO 13485) within a regulated environment
- Excellent problem solving and decision-making skills are required
- Working knowledge of statistical techniques is required
- This is a hands-on position that will require a self-motivated individual with excellent written and oral communication skills
- The ideal candidate for this role will have the ability to collaborate with business partners at all levels with multiple functional groups in an environment that embraces teamwork and risk-based decision making
33
Customer Quality Engineer Resume Examples & Samples
- Acts as the Customer Advocate within Woodward processes and systems
- Acts as the Customer liaison for compliance to customer quality requirements and customer satisfaction relative to quality of products and services
- Responsible for a medium number or size of customer accounts. Consults with leadership or higher level customer quality engineers on advanced or complex issues
- Responsible for monitoring and tracking customer quality data
- Drives root cause analysis and problem solving utilizing Six Sigma methodology and Woodward Quality Management System processes
- Monitors and drives improvements to customer quality metrics throughout Woodward
- Ensures adequacy of documents and interfaces with customer for required validation documentation to customer quality requirements such as MPP, PQP, PPAP, ISIR, etc
- Leads and follows up on internal and external quality audits as required
- Monitors and reports on customer score cards
- Familiarity with regulatory and compliance requirements
- Site Specific
- Working knowledge of Woodward's organizational structure, information systems and products
- Demonstrates the ability to regularly utilizes Six Sigma principals, tools and methodology
- Writes and presentsstandard technical reports to peers, management and customers
- Proficiency to capture important data, analyze data and report appropriate conclusions: able to identify and address the critical few from the trivial many
- Proficient inunderstanding and interpreting engineering specifications, mechanical drawings, and/or electrical schematics, and Geometric Dimensioning and tolerencing (GD&T)
- Solid understanding of quality management systems including ISO9001, AS9100, TS16949, and/or QS9000
- Able to analyze systems and processes against those requirements and identify gaps
- Solid understanding of the Woodward PLC process and quality planning tools
- Demonstrated ability to coordinate and lead small cross-functional teams
- Provides technical problem-solving guidance to others on the team
- Ability to effectively and efficiently prioritize and manage multiple tasks
- Solid interpersonal skills and effectively work with various levels within the organization and with peers at customer sites or at regulatory agencies
- Ability to drive and implement activities to meet customer quality expectations
- Ability to provide customers with excellent service and support
- Establishes and maintains effective relationships with customers and gains their trust and respect
- With 2 year Associates degree, must have a minimum of 2 years of quality related experience
- With no degree, a minimum 4 years experience in quality engineering or quality management is required
34
Customer Quality Engineer Resume Examples & Samples
- Representing clients interests in the organization on the quality of both products to 0 km and during the warranty period
- Decide locking / unlocking delivery of quality problems that impact customer
- Coordinates and conducts activities at the plant, associated approval processes for new products according to specific conditions required by clients. Reply actions specified by PEP phases 5-9
- Participate in activities certification process modifications / product, checking compliance with the specific requirements of customers
- Prepares the standard of work
- Coordinates setting up teams to analyze incidents impacting client and establish corrective actions
- Responsible for implementation of immediate protective action if customer complaints received
- Collaborate with counterparts in other plants of the company by transferring information about customers and how to handle problems
- Evaluate the effectiveness of corrective and preventive actions initiated as a result of defects impacting customers
- Coordinate analysis of products returned by the customer
- Coordinates customer visits and factory audits
- Maintains and updates the reporting system and database client on quality issues
- Performs other tasks received from the higher echelons or that it has assumed
35
Customer Quality Engineer Resume Examples & Samples
- Studii superioare profil mecanic, domeniul auto/motoare
- Experienta de lucru in domeniul tehnic: minim 3 ani
- Experienta in domeniul calitatii si al relatiilor cu clientii: minim 2 ani
- Cunostinte despre control statistic
- Cunostinte foarte bune de desen tehnic in ceea ce priveste citirea si interpretarea conform standardelor ANSI si ISO
- Limba franceza si engleza fluent
- Cunostinte operare calculator (Excel, Word, Power Point, Outlook)
- Aptitudini de comunicare pe diferite niveluri
- Capacitate de analiza relationala si de sinteza
- Autonomie si capacitate de lucru in echipe transversale
- Respectare riguroasa a angajamentelor si termenelor
- Disponibilitate pentru deplasari la clienti si program prelungit
- Permis auto categoria B
36
Customer Quality Engineer Resume Examples & Samples
- Knowledgeable in program launch processes and APQP requirements
- Knowledgeable of Automotive OEM CSRs
- Knowledge of automotive problem solving tools (8D, 5 Why, Ishikawa analysis) required
37
Customer Quality Engineer Resume Examples & Samples
- Monitors customer integration and field quality, works with the field and factory quality organizations to achieve customer targets, and develops and implements quality improvement plans directed at achieving Best-in-Class status
- A focal point for all customer specific quality escalations and defines what type of support within the Design Center is necessary to support failure analysis, coordinates the appropriate resources within the Design Center, drives the actions to completion and coordinates results with Customer Technical Support to close the escalation
- Champions unique customer requirements by being the liaison between our key OEM Customer Technical Support team, internal design engineers, and internal core teams. They are responsible for the integration of Seagate enterprise products into customer systems. This position requires hands-on characterization, qualification, and troubleshooting of customer systems
- Works on problems of very diverse scope and requires the ability to solve complex customer issues during and after new product qualifications
38
Customer Quality Engineer Resume Examples & Samples
- Part Development: Lead for New program Development(NPD) and similar process such as APQP
- Controlling of all quality issues from customers (0Km, and Warranty)
- Proceed PPAP(ISIR) for new projects and during mass-production
- Doing customer process audit
- Implementing meeting with customers and suppliers
- Controlling all customer PPM and Supplier PPM
- Reporting all customer quality issues to customer
- Knowledge of TS16949 required include APQP and PPAP
- Knowledge of SPC required
- Experience the communication with customers a plus
- Knowledge in manufacturing problem solving (8-D Methodology) and manufacturing processes required
- Effective at defining problems, collecting data, establishing facts and drawing valid conclusions. Ability to interpret a variety of technical instructions in mathematical or diagram form and deal with abstract and/or concrete variables. Proficient at developing trip reports, general business correspondence, and procedure manuals. Effective presentation skills and ability to respond to questions from management and/or customers.
39
Customer Quality Engineer Resume Examples & Samples
- Bachelor or above, major in Electronic or related
- Minimum 2years working experience, plus in semi-conductor industry
- Good English skill, CET-4 or above with good oral and read ability
- With working experience in customer services,8D reports
- Profient in the process and root cause analysis
- Implement the RMA for customer quality incidents
- Implement the CAB and follow the actions closely
- Result-orientation and aggresive
40
Customer Quality Engineer Resume Examples & Samples
- Working with customers to satisfy their requirements
- Understanding customer specific requirements
- Leading and/or participating in PQST (Product Quality Steering Teams)
- Utilize traditional and advanced Quality planning tools
- Reviewing and improving Control Plans
- 8D/Corrective action management for customer issues
- Supporting new business opportunities and new product development programs
- Supporting Change Manage Programs
41
Customer Quality Engineer Resume Examples & Samples
- Use of statistical analysis tools and methods for problem solving
- Facilitate and participate in quality metrics reporting and communication
- Set up specific quality systems per requirements
- Define and manage all customer quality plans
- Support product and process changes and evolution, ensuring product quality integrity is maintained
- Support quote and contract review process, ensuring customer quality requirements are met
- A minimum of a Bachelor's degree in engineering or related field or equivalent experience is required
- Experience of 5 years as an engineer is preferred for this position assuming education requirements are met
- Equivalent industry experience of 1 or more years is highly desirable
- Proficient working knowledge of quality systems and tools for applicable industry requirements (i.e. Aerospace, Medical, etc.)
- Basic Lean and Six Sigma skills
- Proficient presentation skills
- Ability to lead and multi-task in a dynamic environment
42
Customer Quality Engineer Resume Examples & Samples
- Education: CS/EE or background in areas related to large scale chip design & semiconductor MFG
- Experience
- Frequent travel capability
- Direct PE/Quality engineer role with industry experience
43
Customer Quality Engineer Resume Examples & Samples
- Develops sampling plans by applying attribute and variable sampling methods
- Analyzes data through hypothesis testing, control charts, measurement system analysis, and process capability
- Maintains professional and technical knowledge reviewing professional publications; establishing personal networks; benchmarking state-of-the-art practices and participating in professional societies
- Updating technical publications and manuals providing specification limits and tolerances of key parts along with proper testing tools and measuring processes
- 2-4 years of related experience working in a quality function positions
- ISO or Six Sigma certification
- Excellent skills in planning, organizing and project management
- Interpersonal flexibility, creativity, problem solving, and decision making skills
- Quality Functional Leadership training and Change Management training is desirable
- Reliability Engineering [Purpose: Understand and manage decision/actions base on Failure/Hazard Rate, Rate of Occurance of Failure (ROCF), Bathtube curve
44
Senior Customer Quality Engineer Resume Examples & Samples
- Minimum 4-5 years of working experience as QA, Testing Engr or Product Engr in Semiconductor or mobile phone company with a mid-level technical understanding
- Be accomplished in mobile phone quality and test requirement, and strong skills in problem solving for system level quality / application issue
- Knowledge of quality tools and reliability concepts is essential especially for Automotive level device
- Strong interpersonal communication skill with customer and internal team
- Team work for problem solving
- Proficiency in English
- Familiar with quality system
- Afford for frequent domestic and oversea travel
- Being honesty and initiative
45
Customer Quality Engineer Resume Examples & Samples
- Sensata offers a unique opportunity to engineer products and to get them to the market. TheCustomer Quality Engineer will work with other engineers and technical colleagues in a team environment to manage key customer accounts for Quality in the automotive industry. The Engineer will lead and solve problems with products for key customers. It is a tremendous opportunity for an electrical, mechanical, design or process engineer with strong technical and communication skills to impact the customer satisfaction of leading automotive companies worldwide, analyze Quality data to make informed decisions, and communicate the end result in a professional environment
- Working with customers to fully satisfy their requirements
- Performing risk assessments
- Reviewing Control Plans and improving them
46
Customer Quality Engineer Resume Examples & Samples
- Generating inspection plans and deliverables
- Failure analysis of returned products
- Reporting root cause and corrective analysis to customer
- Presenting fault categories and recommendations to drive product / manufacturing improvements
- Reviewing and understanding of technical drawings and/or specification
- Completing relevant customer specific documentation (8D, FIR etc)
- Liaising with all internal departments
- Supporting or leading customer visits
- Experience of customer or market quality assurance
- Sound understanding of inspection and test planning
- Good communication and negotiation skills, including written and verbal presentation skills
- Experience of preparing of inspection and test plans and deliverable documentation
- Previous experience of working in a manufacturing or production environment
- Ability to analyse problems, detect root causes and resolve all issues
- Excellent time management, planning, organisation and prioritisation skills
- Experience of working in a hands-on, logical problem-solving orientated quality assurance environment is essential
- Willing to travel (locally and on occasion, globally)
- HNC/HND or Degree or equivalent in related engineering discipline, desirable
- Competent user of MS office (Word, Excel etc.)
- Awareness of Rail industry standards, desirable
47
Customer Quality Engineer Resume Examples & Samples
- Support our customers who are facing product issues
- Interface between customers, sales force, application engineering department and European factories
- Initiate root cause analysis of problems
- Initiate inspection and testing process on returned products
- Coordinate problem resolution in close collaboration with other departments
- Customer visits
- Continuous process improvement
- Holds an Engineering or Industrial Engineering degree
- Has 3-5 years of relevant job experience in related industry (HVAC/R, automotive,...)
- Shows a systematic and analytical approach to problem solving
- Is an excellent team player and networker
- Is fluent in English and in either French, Italian or Spanish
- Brings competences like customer orientation, collaboration, effective communication and ensured accountability
48
Customer Quality Engineer Resume Examples & Samples
- Holds an engineering or industrial engineering degree
- Has 3-5 years of relevant job experience in related industry (HVAC/R, automotive,…)
- Is fluent in German and English; French is a plus
49
OEM Customer Quality Engineer Resume Examples & Samples
- Develop strong relationships and develop communication strategies with customer teams that facilitate positive interactions based on professional and timely responses
- Facilitate internal cross functional alignment on JCI direction and customer responses on quality topics. Generate effective and consistent communication packages supporting JCI direction including value to customers
- Work with plants and cross functional teams in generation of communication packages required for customer report outs. Facilitate standardization of internal expectations and responsibilities for customer reporting
- Provide internal visibility and facilitate resolution of customer quality and warranty concerns. Provide leadership and coordination of cross functional requirements and provide internal direction to ensure timely completion of assignments to resolve issue. Support problem solving initiatives
- Provide technical and quality expertise to support JCI commercial team in quality and warranty risk mitigation
- Facilitate communication and coordination of customer meetings addressing special cause quality or warranty topics
- Provide oversight and drive compliance to CSR requirements at all JCI locations and functions
- Internally support communication of Customer Specific Requirements as part of the PPAP and Change Management Process and verification that customer specific requirements are fulfilled (i.e. PPAP documentation, Testing, PTR, etc.)
- Coordination of unique customer test and quality requests requirements test samples, Run @ Rate, PV trials and PTR in support of product/process change approval and new product/program launch
- Ensure Submission of final PPAP documentation (JCI internal and customer specific requirements)
- Provide oversight on scheduling and support customer on-site visit /audit of manufacturing process (Run @ Rate, STAR Audits, QSB Audits, etc.) Note: Plant QA Staff responsible for facilitation, documentation and open issue resolution
- Support review and presentation of PPAP package/ follow up on open issues to customer
- BS Engineering or foreign equivalent, technical degree or related experience
- Minimum 6 years of experience in technical customer support, interacting with different level of management of clients, specifically Automotive OEMs, being able demonstrate ability to navigate complex organizational matrix and effective communication skills
- Minimum 4 years of experience in Automotive, Automotive Systems, Electrical, Battery or technical field
- Demonstrated knowledge of core quality tools including: Process control plans, process flow diagrams, FMEA, MSA, SPC
- Travel expectation up to 25% of time. (Mostly local travel)
- Proficient in Microsoft: Excel, Power point, Program Manager
50
Customer Quality Engineer Resume Examples & Samples
- Degree in Engineering, Mathematics, Statistics or related field
- Excellent interpersonal/communication skills. Ability to converse and direct customer resolution calls and meetings
- Effective presentation skills
51
Customer Quality Engineer Resume Examples & Samples
- Clone/move configurations from customer orgs to QA orgs
- Create test data and verify cloned configuration is fully functional
- Gather customer test scenarios/cases and make available to QA engineers
- Reverse engineer configurations to determine business/functional intent
- Develop/execute and automate test cases to cover customer workflows
52
Customer Quality Engineer Resume Examples & Samples
- Clarify customer requirements and communicate to the appropriate Gentex teams (lab / production / FMEA team)
- Attend preproduction builds; highlight and resolve quality issues
- Lead customer communication resulting from customer non-conformances
- Direct problem resolution teams (events/assignments/timing)
- Provide customer performance feedback to the organization
- Support new product development utilizing the Gentex Milestone process
- Prepare and submit all required quality documentation to the customer for new product launches and process changes
- Assist to develop and maintain FMEAs and control documentation to effectively manage risk and meet customer specifications
- Aggressively pursue root causes of production quality problems
- Aggressively pursue implementation, including peripheral view, of product/process improvements
- Apply appropriate quality tools to analyze and resolve issues
- Maintain a high level of awareness and knowledge of Gentex technologies (product standards/specifications and operational technologies/capabilities)
- High degree of capability in managing workflow (scheduling/maintaining deadlines)
53
Customer Quality Engineer Resume Examples & Samples
- Acts as the customer advocate within Woodward processes and systems
- Acts as the customer liaison for Woodward compliance to Customer Quality Requirements and Customer Satisfaction relative to quality of products and services
- Responsible for a small number or size of customeraccounts
- Consults with leadership or higher level customer quality engineers on advanced or complex issues
- Facilitates root cause analysis and problem solving utilizing Six Sigma methodology and Woodward Quality Management System processes
- Reviews and interfaces with customer for required validation documentation to customer quality requirements such as MPP, PQP, PPAP, ISIR, etc
- Supports internal and external quality audits as required
- Supports the reporting and monitoring of customer score cards
- Ability to understand Woodward's organizational structure, information systems and products
- Basic understanding on Six Sigma principals, methodologies and tools
- Writes and presents basic technical reports to peers
- Ability to capture important data, analyze data and report appropriate conclusions
- Ability to understand and interpret engineering specifications, mechanical drawings, and/or electrical schematics, and Geometric Dimensioning and Tolerencing (GD&T)
- Basic understanding of quality management systems
- Basic understanding of the Woodward PLC process and quality planning tools
- Ability to effectively operate in a project team environment and communicate with customers
- Ability to manage multiple tasks effectively with input for priority setting
- Solid interpersonal skills and ability to effectively work with peers, both internally and with customers
- Ability to drive and implement activities to meet customer expectations
- Recognizes customer service as a critical factor
- Handles customers politely and professionally
- Associates degree, no experience required
54
Customer Quality Engineer Resume Examples & Samples
- Support customers with matters dealing with product quality for product qualified in customer systems, with a particular focus on semiconductor Lasers/LEDs and Detectors, as well as fiber optics
- Be responsible for quickly resolving quality issues at customers, to keep disruption of customer production as low as possible
- Provide first-level technical information gathering and debugging in the customer application. May require technical analysis either at customer sites or in Finisar lab
- Provide assistance with RMA documentation and communication of issues to internal Failure Analysis teams. Work closely with FA teams in the US, Malaysia, Australia and China
- Ensure Failure Analysis Reports are received and accepted by customer on time
- On as-available basis, provide pre- and post-sales product application, test, failure analysis, and reliability specification support to Japan-based customers for general Finisar optical components. Interact directly with customers in supporting their technical questions and requirements
- Work as a team with the local FAE and the Regional Sales Managers
- Some domestic and international travel is a necessary part of the job
- Focus on maintaining high scores on Customer Quality Score Card
- Candidate must have a Bachelors degree (and preferably a Masters degree) in Engineering or Science
- Must have a minimum of 5 years experience with semiconductor Lasers/LEDs and Detectors
- Familiarity with general semiconductor devices and fabrication processes as strong plus
- Become familiar with product performance specifications and methods used by the factory to ensure product meets specification
- Strong technical, written and verbal communication skills are a requirement
- Good Communication skills in English and local language (Japanese or Korean) are necessary
- Ability to develop and maintain relationships at within customer organization
55
Customer Quality Engineer Resume Examples & Samples
- Acting as primary supplier Technical Service liaison for quality matter
- Acting as primary customer Manufacturing liaison for quality matter
- Actively participate in cross-functional team (manufacturing, engineering, service) to assist in the development and monitor execution of action plans to ensure timely resolution
- Develop, prepare, analyze and deliver accurate and timely required reports
- Communicate the results internally and externally
- Develop a closed loop system to record the corrective actions taken, supporting the Quality manager
- Monitor the consistent implementation of the corrective actions
56
Customer Quality Engineer Resume Examples & Samples
- Expertise in 8D, PPAP, APQP and QC tools preferred
- Working knowledge of global quality systems (ISO9001, TS16949, and VDA etc)
- Good team player, logical thinking and communication skill
- Automotive experience preferred
- Good English language ability in reading, writing and speaking
57
Customer Quality Engineer Resume Examples & Samples
- Lead customer satisfaction through effective tracking on Customer Score Card
- Effective communication of customer specific requirements to the site
- Successful interface with Supply Based, Supply Chain, 3PL, ME & AE related to associate projects / task for Customer Requirements
- Keep Internal data on Honeywell Systems aligned with the customer’s portal
- Report, Track & Lead 8D/CAR teams to contain and permanently resolve quality issues according to customer expectations for response time and technical data. Works with and across functions as needed for issue resolution. This responsibility requires a strong knowledge of all production lines and controls related to assigned customer
- Contribute to achieve Plant Quality metrics
- Support PEP phase 5-9 projects as requested
- Responsible for preparing and/or approving customer and internally required quality deliverables such as, PPAP, ECN, etc.). In conjunction with NPI Leader / Manager / Program manager, the QE is responsible from Quality side for the pilot runs of new launches, assuring that proper controls are in place
- Obtains customer approvals (i.e. homologation, process changes/upgrades) as required for changes to products, processes and/or suppliers
- Assures that all customers required quality documentation is completed and assure systematic storage of data and set audit as needed to assure effectiveness of traceability
- Responsible of Green Run analysis and provide support for Warranty analysis activities, including follow up of RMA process until Debit be completed or negated. Ensures reviews are performed on a timely basis, with proper rigor, and that information is entered into relevant systems and communicated
- Develops and executes projects to meet customer expectations
- Develop Supplier Quality Scorecard & Assure Supplier Certificates are on time
- Support Production Cells in case of supplier issue cause impact into the operation through effective containment actions related to raw material
- Sorting processes control and evaluation. Coordinating and establishing correct and effective internal sorting mechanisms and outsource companies as well
- Evaluation and application of Objective of Cost of Pour Quality (COPQ)
- Effective material control and disposition in MRB/RTV area
- Set proper escalation with suppliers quality management level and SQD organization
- Responsible of quick kaizen, Kaizen events & knowledge sharing to ensure Continuous Improvement throughout the process
- Schedule visit to Customer as requested
- Perform Quality Audit into Supplier Sites as requested
- Experienced quality engineer or complementary skills (e.g. product or manufacturing engineering). 5 years minimum
- Competency in relevant automotive quality practices
- Six Sigma Green-belt; Black-Belt (preferred)
- Full understanding and application of ISO/TS 16949 Guidelines
58
Operations & Customer Quality Engineer Resume Examples & Samples
- Analyze operational data; Develop and implement recommendations. Participates in and may lead audits
- Evaluates work methods, procedures and policies. Tracks progress of qualification status, reviews reliability test results, determines disposition of non-compliant products, reviews and releases qualification packs
- Explains difficult or sensitive information; works to build consensus
59
Senior Customer Quality Engineer Resume Examples & Samples
- BS Degree in Electrical Engineering, Computer Science, or related degree
- 5+ years technical project management
- Experience with TS169 and other automotive requirements: PPAP, PFMEA
- Proficient working knowledge of quality systems and tools for applicable industry requirements
- Proven ability to drive measurable positive changes with a direct impact on the customer experience
- Must demonstrate leadership ability with persuasive skills and an aptitude to deal with multiple issues of varying complexity, in order to address complex customer concerns
- Strong communication skills – written and verbal – are needed as well as an ability to work comfortably across organizational boundaries to drive change and influence actions without direct authority
- Broad industry awareness and expertise
- Proven record of successfully using six-sigma, lean, process improvement tools
60
Customer Quality Engineer Resume Examples & Samples
- Lead Customer Quality activities – issue resolution, 8D report submission in customer specific format, prevent recurrence, PPM, R/1000 metrics tracking
- Customer interface for all product deliveries on quality measurables
- Review issues with customer on periodic basis, for closure
- Ensure PPM, R/1000 metrics are within objectives
- Engage customer on revoking rejections which are not as per our AOI / PPAP samples and in case of any customer abuse
- Work with Service provider – implement service network, train service center technicians, ensure service infrastructure in line with standards, track and close all warranty issues, track the efficiency / effectiveness of service centers – quality of service, TAT, reporting, spares / bank unit stock reconciliaton
- BE / B Tech with 6 to 8 years experience
- Experience in Automotive Tier1s
- Prior experience in handling customer quality / after sales support in automotive context is mandatory
- Prior experience in setting up and working with a service network is mandatory
- Negotiaton skills, communication skills, process knowledge on quality systems is desirable
61
Operations & Customer Quality Engineer Resume Examples & Samples
- ISO 9000 experience
- SAP experience a plus
- Certified Black Belt a plus
62
Senior Customer Quality Engineer Resume Examples & Samples
- Ability to interpret an extensive variety of technical instructions in mathematical or diagram form, and deal with several abstract and concrete variables
- Demonstrates advanced functional and technical skills and basic process skills
- Demonstrates advanced operations, technical and people and/or process skills as well as customer (external and internal) relationship skills
- Demonstrates knowledge of multiple functional technologies/ processes, industries or functions and understanding of interdependencies of such processes at the site
63
Customer Quality Engineer Resume Examples & Samples
- Responsible for the execution of the Diabetes Care Franchise (DCF) Complaint Management process as assigned by product or region: complaint capture, investigation, trending and reporting, escalation, timeliness, and customer insights
- Responsible to support complaint handling systems, software, and report applications: identify and correct systems issues and reports, and identify and improve systems and processes
- Troubleshoot and correct issues identified through DCF Quality Systems
- Represent Customer Quality on new product launch teams and significant initiatives. Act as primary contact responsible for ensuring customer and product insights are understood and available to the various stewardship, sponsor, and other development teams
- Identify, raise, and escalate G-Tracks to support IT improvements to the complaint management systems
- Provide technical systems knowledge to team and act as trainer where required on systems capabilities
- Provide on-boarding and coaching of co-ops and temporary resources
64
Customer Quality Engineer Resume Examples & Samples
- Minimum Bachelor degree in Electronics Engineering or Mechanical Engineering or Equivalent
- Preferably with Quality systems and/or process engineering knowledge
- More than 3 year experience in Quality Assurance Experience in electronic field
- Strong command in English
65
Customer Quality Engineer Resume Examples & Samples
- Provide assistance with RMA documentation and communication of issues to internal Failure Analysis teams. Work closely with FA teams overseas
- On as-available basis, provide pre- and post-sales product application, test, failure analysis, and reliability specification support to Korea-based customers
- Work as a team with the local Field Applications Engineers and Regional Sales Managers
- Good Communication skills in English and Korean are necessary
- Ability to develop and maintain good relationships with customers
66
Customer Quality Engineer Resume Examples & Samples
- Assures product, process, and system quality requirements are determined, planned for and achieved during new product development, launch, or at design or process change
- Utilizes appropriate change management system for all product or process changes
- Problems are investigated, defined, analyzed and resolved effectively and responsively
- Assures and continually improves product and process quality; records maintained
- Responds to Customer in an expedient and professional manner
- Follows all Company policies and procedures
- BS Degree in related field
- Above average organizational skills
- Required PC Skills: Operating Systems (Windows 7 or higher), MS Office (Word, Excel, PowerPoint, Outlook)
- Preferred PC Skills: Minitab, WinSPC
- Hands-on skill set with decision-making capability
- Quality data analysis skills
- Quality Engineer Certification preferred but not required
- 5+ years of Quality Engineering experience, automotive industry experience preferred
67
Customer Quality Engineer Resume Examples & Samples
- Be local key customer point of contact to manage Customers’ Quality requirements and ensure all are fulfilled
- Ensure world class Customer Quality Experience, accountable for the customer’s product quality and reliability
- Proactively measure customer’s satisfaction and expected quality score: ongoing customer quality reviews, scorecard performance and/or customer quality perception
- Proactively work with the customer to assess their needs and drive plans and actions internally
- Interact regularly with sales, field application engineers and internal stakeholders to maintain alignment on quality and reliability issues, proactively communicate feedback from the customers to internal functions
- Support customer visits and or audits at our plants
- Effective customer quality issues management- timely containment, communication and resolution
- > 5 years’ experience as Quality Engineer in front of customers or similar position
- >2 years’ experience in quality of optical interconnect products and processes, preference to major international key-players companies
- Understanding of quality terminology, methods and tools, Failure Mode Effect Analysis (FMEA), SPC, 8D, Six Sigma, Poka-Yoke, sampling plans and statistics, etc
- Familiar with industry standard specifications (GR-468, IEEE, IPC, JEDEC etc.)
- Familiar with SMT, mechanics assembly process and quality gates
- Ability to read electronics / mechanical drawings and datasheet
- Fluent Chinese, Good English skills– (write and speak)
- Eng / practical eng in Mechanical / Materials / Electrical / Engineering or related fields
- IPC certified
- Quality system and process audit experience
- Personal
- Team player, service oriented
- High interpersonal skills to allow good communication internally and externally
- High motivation to work and learn in proactive. Ability to work independently and under pressure
- Willing to travel per requirement
68
Customer Quality Engineer Resume Examples & Samples
- Manage customer return process including problem solving process
- Provide follow-up on all customer failure analyses, communication and issue resolution at all levels
- Act as customer advocate for product quality. This includes customer and internal management communications and presentations, for customer and internal quality reviews
- Customer interaction and negotiation on quality cases solving
- Customer loyalty development
- Product Support
- Interface with internal and external factories on reliability and quality issues
- Support continuous improvement, defect reduction activities, and cost reduction activities
- Lead product teams, factories, and associated support through quality issue resolution process
- Support customers with technical reliability and quality consult
- Work with customers to address product reliability and quality issues
- Coordinate and/or Participate in the Change Action Board (CAB)
- Participate in Material Review Boards (MRB)
- Bachelor Degree or above in Electrical Engineering, Science
- Application Engineering or Design Experience on microprocessor
- Demonstrated data analysis and problem solving skills
- Ability to resolve complex customer issues and lead cross-functional teams
- Strong written and verbal communication and presentation skills and ability to influence others
- Process control and other six sigma tools knowledge
- Flexibility to adjust to change and multiple ongoing issues in a fast-paced,customer-focused environment
- Ability to work independent of management with leadership skills
- Application Engineering experience would be an advantage
- Overseas education and/or working experience are preferred
69
Customer Quality Engineer Resume Examples & Samples
- Offer a rapid response to customer quality issues to ensure that the right diagnostics are applied in order to minimise unnecessary product removals
- Own and execute detailed investigations into customer issues using appropriate problem solving tools to establish root causes and corrective actions
- Carry out containment and trace activities to protect customers
- Work with customers to define problems and capture 'crime scene' evidence
- Define investigation plans and expedite associated hardware movement
- Write and issue 8D investigation reports
- Maintain investigation tracking tools with current status, support customer meetings/communications and become a customer advocate within Rolls-Royce Control Systems
- Collaborate with members of other teams, particularly Manufacturing Value Streams, Supply Chain, Engineering, Technical Services, Planning and Logistics
- Lead /support Major Disruptive Events
- Provide coaching in disciplined problem solving and advice on technical issues
- Manage non-conformance
- Analyse trends in data in order to identify improvement projects
- Play a role in continually improving Rolls-Royce processes
- Degree qualified in a relevant Engineering/Manufacturing discipline or equivalent would be an advantage
- Proven experience in an engineering/manufacturing environment
- Highly self-motivated, with strong interpersonal, team working and influencing skills
- Able to make sound, logical decisions, based on available data
- Aptitude to develop functional understanding of complex products/systems at pace
- Professional courage to highlight areas of concern and risk with regard to suitability of a product to meet its requirements for safety and fitness for purpose
- Able to summarise complex technical issues to suit different audiences
- Proven track record of successful problem solving using 7-step, 8D or similar process
- High standards of written and verbal communication with keen attention to detail
- Able to prioritise concurrent tasks appropriately
70
Manufactuing & Customer Quality Engineer Manager Resume Examples & Samples
- Considered subject matter expert in managing company-wide, cross functional quality program and related business processes. This includes the definition, specification, and implementation of standards, methods and procedures for developing quality programs
- Develop, deliver, and cascade quality training and courses. Monitors current quality training to ensure compatibility with current programs
- Establishing, influencing, and managing multiple business segments with focus on business and operational results through use of continuous improvement methods
- Provides leadership and support to subordinates in meeting quality assurance system requirements along with department and company goals and objectives with primary consideration for safety, quality, productivity and cost.Evaluate the performance and effectiveness of audit staff at the projects completion. Evaluate and develop direct reports via IDP, EDR, continuous feedback, and annual performance review
- Maintains an on-going quality improvement program aimed at enhancing the Company's quality systems, controlling manufacturing processes and improving end product quality
- Selects, evaluates and manages employees to ensure the efficient operations of the function
- Responsible for overseeing division's ISO Certification process. Handles special projects, as assigned
- Demonstrates comprehensive understanding of concepts and principles within own job family and knowledge of other related job families
- Influences others internally and externally, including senior management
71
Customer Quality Engineer Resume Examples & Samples
- Liaison between customer and Harman. Coordinates activities of internal and external resources. Serves as resource for problem solving by initiating actions to address issues and prevent potential quality problems
- Lead and manage problem resolution activity and improvement efforts by applying the use of modern quality tools such as FMEA, 8D, Kaizen, Lean Manufacturing principles and Six-Sigma methodologies
- Analyze, compile, review and regularly report customer quality metrics such as PPM, or 0km performance. Prepare presentations from quality data for reviews by both Harman and customer management groups
- Represent Harman at customer meetings, conferences and training on behalf of the manufacturing plants and effectively deploy the information throughout the organization. Ensure Harman is current with the customer’s quality policies
- Ensure information for customer issues flows internally to appropriately address the design (hardware and software), manufacturing, packaging and logistics causes. Facilitate awareness of issues and deploy countermeasures as lessons learned, conduct Yokoten
- Assist internal and external contacts to resolve product and process problems. Investigate and solve manufacturing-related problems
- Champion continuous improvement efforts. Researches, recommends, implements and administers new and/or existing quality assurance processes
- Minimum education: Bachelor’s degree, with a preference for Electrical or Mechanical Engineering
- Minimum experience: 5+ years in Automotive Quality, Design and/or Operations in electronics, or electromechanical manufacturing
- Knowledge of the principles and procedures related to Manufacturing Quality Engineering, electronic & mechanical manufacturing, statistical process control (SPC), problem solving and automotive production part approval process (PPAP)
- Analytic capability; design critical data sets, organize data, and identify defensible trends
- Work experience with APQP, PPAP, PFMEA (using AIAG guidelines)
- Previous experience working with Asian OEMs strongly preferred, particularly Toyota and Subaru
- Certifications/Licenses: ASQ, CQE, Six Sigma Green Belt
- Electronics Knowledge - Audio and/or infotainment experience
- Manufacturing and Design discipline
- Ability to specify, develop and operate specialized equipment used for product analysis
72
Senior Customer Quality Engineer Resume Examples & Samples
- Lead weekly 0-km response cross-functional team meeting to drive root cause analysis to resolution/closure in a timely manner ensuring PDCA for corrective actions
- Investigate any End Of Line test (Huntsville) related concerns using diagnostic tools available and document the findings which includes (but not limited to): part number level, VIN, SW level, serial number, observed DTC/EOL failure
- Obtain vehicle BUS logs of concerns as they occur in vehicle and incorporate in problem solving
- Represent Harman at customer meetings for quality/warranty issues
- Support customer quality continuous improvement initiatives and Safe Launch Plan activities
- Lead weekly warranty response cross-functional team meeting to drive root cause analysis and ensure completion of PDCA for corrective actions
- Support and set up warranty return analysis with the OEM, including in-vehicle evaluation (where needed)
- Lead problem analysis and improvement efforts by applying, training and encouraging the use of modern quality tools - such as FMEA, 8D methodologies
- Ensure information flow related to customer returns and warranty problems to appropriately address both design and manufacturing causes; and to facilitate awareness and deployment of countermeasures as lessons learned
- Five or more years of previous experience in Quality or Manufacturing Engineering
- Bachelor’s Degree with five years of experience with automotive, electronics, or electromechanical manufacturing highly desired
- Experience with statistical methods, problem solving methodologies, PPAP, FMEA, and automotive quality management systems
- The physical demands described here are representative of those that must be met by an employee to successfully perform the essential functions of this job. Reasonable accommodations may be made to enable individuals with disabilities to perform the essential functions. While performing the duties of this job, the employee is regularly required to sit; use hands to finger, handle, or feel; and talk or hear. The employee frequently is required to reach with hands and arms. The employee is occasionally required to stand and walk. The employee must be able to lift up to 50 lbs
- Experience with FCA manufacturing, quality and engineering
- FCA Supplier Portal
- Over five years of technical electronics manufacturing experience highly desired
73
Customer Quality Engineer Resume Examples & Samples
- Warranty analysis/Data management
- Customer survey analysis
- Participate in the warranty parts return process
- Identify components that need to be returned from dealerships for root cause analysis
- Meeting facilitation/agenda creation
- Create monthly warranty presentation
- Issue management
- Ad hoc reporting around various Quality metrics
- Interaction with Program Team Leadership regarding high priority projects and roadblock removal
- Single point contact for assembly plant regarding PRTS training
74
Customer Quality Engineer Senior Resume Examples & Samples
- Develop analytics to correlate issues between MFG and Install to prioritize and resolve
- Support globalization of Best Known Mfg Quality practices throughout Lam’s Global Manufacturing infrastructure
- Own “As shipped” Quality Defect rates (DPMs). Drive down DPMs by assessing and monitoring trends, systemic issues and chronic issues across install base
- Assess all quality issues impacting Install, verify resolution activities are in process, and partner with respective organizations where necessary to drive corrective action
- Own and manage quality expectations of new orders (systems, upgrades, retrofits, refurb) for Lam
- Demonstrated problem solving and data driven decision making Skills
75
Customer Quality Engineer Resume Examples & Samples
- Have good communication with customer to get latest customer requirement and quality status
- Initiate and follow up warranty improvement projects
- Perform any other duties as assigned
- Bachelors degree, preferably in Engineering, and Chemical
- Has production and quality management experience and good understanding about battery manufacturing process
- Be familiar with product quality basic knowledge
- Good intermediation ability with different department
- Good communication skills, written and verbal
- The ability to speak and write in both Mandarin Chinese and English
76
Customer Quality Engineer Resume Examples & Samples
- Performs more challenging entry level assignments. Has acquired knowledge, skills, exposure to fundamental quality tools and methods and Training for FSO demonstrates competency by performing structured work assignments such as provide training with support from others
- Perform corrective action activities with assistance from others document all corrective action activities
- Facilitate basic/local reviews with the support of senior team members. Gather solutions to quality issues with minimal supervision
- Understand the field issue that needs to be closed Identify and implement corrective actions with support from others
- Understand the purpose of QMS reviews such as annually in preparation for ISO external and customer audits
77
Operations & Customer Quality Engineer Resume Examples & Samples
- Assists in the development, application, revision and maintenance of quality standards
- Assists in the design and implementation of methods and procedures for inspecting, testing and evaluating the precision and accuracy of products and/ or production equipment
- Assists in the development of methods and parameters, project methodology and/ or project proposals
- Assists in the development and uses test procedures. Prepares documentation for inspection/ testing procedures. Recommends corrective action for procedural, product, or process deficiencies
- Evaluates work methods, procedures and policies. Participates in audits
78
Customer Quality Engineer Resume Examples & Samples
- BS in Electrical/Electronic Engineering, Computer Engineering, Systems Engineering, Chemical or Materials Science Engineering, or related Engineering field
- 8yrs experience in semiconductor/systems industry, with demonstrated capability in Quality, Reliability, or QA functions, and experience working with end-customers
- Excellent technical leadership skills, demonstrating ability to drive technical product issues to resolution
- Demonstrated ability to lead cross-functional/cross-geo teams in developing debug, resolution, exit strategies, and executing test plans, and utilizing data and results to complete milestones towards issue closure
- Exhibits strong communications skills: written, verbal, and presentation - with clear ability to communicate at different levels of detail to different audiences, from technical contributors up to executive management levels
- Willingness to travel to other Intel sites, and to visit customers
79
Customer Quality Engineer Resume Examples & Samples
- Degree in chemical engineering, chemistry, electrical engineering, and related chemical & engineering
- Experience of 10 +/- years as an engineer/manager is preferred for this position assuming education requirements are met
- Good inter-personal and communication skills
- Self motivated initiative in abundance
- Good problem solving skills, along with an ability to apply the problem solving skills to real work problem
- Capability to communicate in Verbal and Written English
- SPC/SQC Knowledge are preferred
- MS Office Tool(Excel, Word, Power points) Skill are required
- Good work ethic /commitment
- Willing to travel within Country
80
Customer Quality Engineer Resume Examples & Samples
- RESPONSIBILITIES
- Understand the FA indicators to find the true defects causing failure
- Working with global and multifunctional teams to cope with quality issues
81
Customer Quality Engineer Resume Examples & Samples
- Lead customer satisfaction for specific customer(s)
- Successful interface with the customer’s Supplier Quality Engineer
- Must have experience and competency to work with customers. Responds quickly and effectively to customer issues and requests
- Track & report key customer quality metrics (e.g. ppm, 8D/CAR response) keeping internal data aligned with the customer’s view
- Lead 8D/CAR teams to contain and permanently resolve quality issues according to customer expectations for response time and technical rigor. Works with and across functions as needed for issue resolution. This responsibility requires a strong knowledge of all production lines and controls related to assigned customer
- Responsible of achieve quality goals
- Support PEP phase 5-8 projects. Responsible for preparing and/or approving customer and internally required quality deliverables such as, PPAP, ECN, etc.). In conjunction with NPI Manager and Program manager, the CQE/CQT is responsible from Quality side for the pilot runs of new launches, assuring that proper controls are in place
- Obtains customer approvals (i.e. homologation) as required for products, processes and/or suppliers. (ECN process) changes
- Assures that all customers required quality documentation is completed and stored in applicable systems for retrieval and audit as needed
- Communicate, document and assure that all customer specific requirements, critical information, incidents and risks that concern their customer with the objective of achieving customer satisfaction with HTT quality
- Responsible to prepare customer visit and audit with the right plant functions
- Responsible to notify the plant quality manager where critical quality standards are known to be compromised. Actively works to resolve such issues quickly and effectively
- Drives successful customer and internal quality objectives
- Timely disposition of any product that has been held
- Partners with Peers HSE, Operations, Plant Engineering, HOS & functions Human Resources, IT and Finance Management to reach goals, identify and resolve problems
- With personnel of other Honeywell plants to complete goals of the organization, identifying and resolving problems mainly with Quality Function & Customer
- Ensure Customer Specific Requirement are cascaded to the concerned functions
- Observes the obligations and duties resulting from the management systems in production, quality, HS&E areas and other external and internal standards and regulations
- Observes work rules and internal HS&E guidelines in the current wording
- Bilingual (Slovak-English)
- Bachelor degree on Industrial Engineering or related areas required
- Experienced quality engineer or complementary skills: 3 years minimum
82
Customer Quality Engineer Resume Examples & Samples
- Collaborate and partner with cross-functional teams to achieve quality goals for Instant Ink
- Lead data gathering and insights generation efforts to identify and resolve in-region service quality and customer experience issues
- Develop and report/present holistic and detailed analyses of product quality trends and issue paretos
- Translate/interpret customer field signals into initial first level root cause analysis and identify key partners to drive to root cause
- Assess, prioritize, and ensure issue resolution, working closely both with regional & WW Support, Operations, and Quality teams as required
- Garner learnings from current service issue resolution, and feed forward to future programs
- Provide regular updates to partners and management on service & experience performance
- Advocate for the Voice of the Customer into the Design Center (GBU)
- Create and maintain appropriate customer-facing self-assist and agent training documentation
- Lead projects and project teams as-required on specific strategic or improvement-related initiatives
83
Customer Quality Engineer Resume Examples & Samples
- Excellent verbal communication skills with external and internal customers
- Problem Solving And Quality Improvement - Demonstrates commitment to and creative thinking for continuous improvement
- Product Or Service Familiarisation - Understanding of the product line or services of the specific business
- Quality System Development, Implementation and Verification
- VPI (Value Package Introduction) - Understanding of the Cummins VPI process, its phases, cross functional activities and responsibilities
- Management of customer issues
- Representing the customer within the plant
- Building and maintaining relationships and communication channels with the customer and account teams
- College, university, or equivalent degree required
- 8% Variable Bonus dependent on company performance
- 25 days holiday + 8 Statutory
84
Customer Quality Engineer Resume Examples & Samples
- Support customers with matters dealing with product quality for product qualified in customer systems
- Be responsible for quickly resolving quality issues at customer, to keep disruption of customer production as low as possible
- Minimum master degree in Engineering or physics
- Minimum of 5 years’ experience in telecommunication product engineering and test
- Some design or working knowledge of optical Transceivers is preferred
- Familiar with product performance specifications and methods used by the factory to ensure product meets specification
- Familiarity with transceiver and system test is necessary
- Experience in working with global teams
85
Customer Quality Engineer Resume Examples & Samples
- Responsible for a small number or size of customer accounts. Consults with leadership or higher level customer quality engineers on advanced or complex issues
- Effective written and verbal communication skills including presentations. Writes and presents basic technical reports to peers
- Ability to drive and implement activities to meet customer expectations. Recognizes customer service as a critical factor. Handles customers politely and professionally
86
Customer Quality Engineer Resume Examples & Samples
- Degree in Electronics Engineering or science disciplines
- Additional training in the followings would be advantage
- Familiarity with semiconductor device Manufacturing process and wafer fab process is a plus
- Knowledge of physics and optics related to camera modules preferred
- Ability to work well and lead in a team environment
- Minimum 5 year working experience in semiconductor industry
87
Customer Quality Engineer Resume Examples & Samples
- Reporting to the Customer Quality Engineering Manager, you will have direct responsibility for all customer quality concerns and be a key player in establishing and maintaining customer relationships. As the champion of investigations, you will be the ‘voice of the customer’ and coordinate cross-functional teams in order to resolve customer quality issues, ensuring timely implementation of interim and permanent corrective actions to meet our customers’ requirements. You will work closely with our Sales and Marketing team as a technical advisor for negotiations and fulfilment of terms and conditions of warranty contracts
- Degree in Electronics Engineering or similar discipline
- Minimum of two years’ experience in a product development/manufacturing environment
- Experience in quality tools such as 8D, FMEA etc
88
Customer Quality Engineer Resume Examples & Samples
- 5 years of experience in a quality role, in the semiconductor industry and customer communications experience
- Experience with applicable quality tools such as pareto, FMEA’s, MSA, SPC/SQC, histograms, trend analysis, process mapping, design of experiments, cause and effect diagrams, 8D problem solving methodology
- Proficient and practiced level of Business English both Written and Spoken. Good skills in oral and written Korean is plus
89
Customer Quality Engineer Resume Examples & Samples
- Helps the diverse Engineering life cycle functions deliver consistent customer experience
- Subject Matter Expert to be able to narrow down impacted component/Engineering ownership and to directly resolve complex configuration issues
- Leverages deep cross-product expertise (XenFamily, Networking, ShareFile) to expedite interop issue resolution
- Identify issues that need extra attention based on a pre-defined selection criteria
- SMEs responsible for narrowing down component/ownership/etc
- Drive resolution on complex issues and key accounts including limited on-site engagements
- Monitor and drive resolution of issue within agreed SLA
- Create KB articles, product requirements, and training material to better spread the information and improve product and supportability
- Monitor technical and customer forums to provide quick support
- Perform environment health checks (limited) and/or create tools / requirements / recipes to successfully perform a health check
- Communicating technical issues; assisting with technical specification documentation and review
- Implementing and maintaining quality improvements to processes and products
- Establishing and maintaining thorough documentation of all work
- Delivering quality work product while gaining experience and knowledge in specific area of focus and in company methods of operation and procedures
- Bachelors or Master’s degree in Computer Science, Computer Engineering, Information Systems, Information Technology or related field; Bachelors with equivalent experience may be substituted for graduate education
- 4+ years relevant work or project field experience
- Strong knowledge of networking protocols i.e. TCP/IP (L4-L7)
- Server Operating Systems (Linux/Unix & Windows), installation and configuration
- Hands-on Enterprise Class Client-Server/Web-based products
- Understanding of LDAP/AD, DNS, Proxy, SSL/TLS, GPKI, MS CA, WebServer (IIS, Apache), SSH, Web APIs (SOAP/REST), NAT, HA Cluster, Load Balance
- Database: MS SQL, MySQL or PostgreSQL
- Tools: Wireshark, Fiddler, XenCenter, Jmeter, WinSCP, Putty, Rest Client, XMAnalyzer, etc
- Must have strong knowledge of operating system fundamental concepts
- Strong debugging, troubleshooting skills and build complex setup for reproducing customer issues
- Understanding of Computer Science fundamentals (e.g., design patterns, data structures and algorithms, threads, multithreaded/concurrent programming, operating systems)
- Demonstrate teamwork and communication skills
- Ability to juggle multiple assignments
- Programming Languages: Python, Java, Perl, C#, Powershell, Shell Scripting, Selenium, QTP is a plus
- Citrix products (Netscaler, XenMobile, XenApp, etc.) experience is a plus
90
Customer Quality Engineer Resume Examples & Samples
- Prepare presentations from quality data for reviews by both Harman and customer management groups
- Engage in problem analysis and improvement efforts by applying the use of modern quality tools such as FMEA, 8D, Kaizen, Lean Manufacturing principles and Six-Sigma methodologies
- Ensure information flow related to customer returns to appropriately address design (hardware and software), manufacturing, packaging and logistics causes. Facilitate awareness of issues and deploy countermeasures as lessons learned (Yokoten)
- Complete other projects and activities as assigned by Senior Customer Quality Manager
- Education: Bachelor’s degree, with a preference for Electrical or Mechanical Engineering
- 3 years of experience in automotive quality and/or operations in electronics, or electromechanical manufacturing (additional experience can be substituted for education)
- 3 years of experience with automotive electronics. Audio and/or infotainment preferred
- Manufacturing discipline
91
Customer Quality Engineer Resume Examples & Samples
- Compiles and writes training material and conducts training sessions on quality control activities
- Initiates corrective action requests as needed and tracks to satisfactory completion
- Ability to read, analyze and interpret general business periodicals, professional journals, technical procedures or governmental regulations
- Ability to effectively communicate with managers and employees of the organizations
- Ability to read, analyze and interpret common scientific and technical journals
92
Customer Quality Engineer Resume Examples & Samples
- Be responsible for new product development quality scheme
- Be responsible for Production Quality Assurance Planning for new or relocation projects, new/modified products and ensure continuous
- Be responsible for submit PPAP documents to customer
- Develop application of quality specifications in both the customer requirements and product specifications
- Collaborate closely with team member and keep making continuous improvement on quality system
- Work with service group to establish a robust monitoring mechanism for field quality
- Initiate action to prevent the occurrence of product non-conformity and system deficiency
- Communicate with customer. Understand customer requirement and transmit customer voice at the plant
- Feedback customer complaint on time and follow the correction action plan
- Warranty claim management, including warranty parts analysis and report, claims
- Seek opportunities for continuous improvement through the warranty analysis and report
- Train customer quality engineer to correctly analyze the returned parts
- Maintain lesson learn system and share good idea with team
- Establish a robust feedback proscenium for customer satisfaction data
- Work with service group to establish a robust monitoring proscenium for field quality
- Employees should strictly abide the EHS rules and regulations and behavior guide line in the plant; wear PPE in right way; actively participate in EHS training; do housekeeping at work; report accidents and unsafe issues immediately, join the accident disposal
- Bachelor's Degree or equivalent in Engineering of Internal combustion engine
- 2 years or above related experience
- Familiar with TS16949 and ISO14001 ,Knowledge of Quality Systems
- Environment systems and Lean Manufacturing
- Process improvement leader
- Coaching and Leadership skills,
- Good communication and negotiation skill
- Understanding of engineering techniques and engine principle
- Fluent English/Mandarin