Plant Quality Manager Resume Samples
4.5
(124 votes) for
Plant Quality Manager Resume Samples
The Guide To Resume Tailoring
Guide the recruiter to the conclusion that you are the best candidate for the plant quality manager job. It’s actually very simple. Tailor your resume by picking relevant responsibilities from the examples below and then add your accomplishments. This way, you can position yourself in the best way to get hired.
Craft your perfect resume by picking job responsibilities written by professional recruiters
Pick from the thousands of curated job responsibilities used by the leading companies
Tailor your resume & cover letter with wording that best fits for each job you apply
Resume Builder
Create a Resume in Minutes with Professional Resume Templates
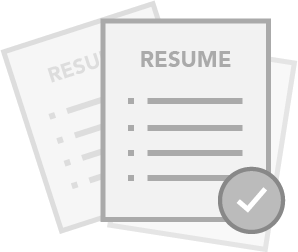
CHOOSE THE BEST TEMPLATE
- Choose from 15 Leading Templates. No need to think about design details.
USE PRE-WRITTEN BULLET POINTS
- Select from thousands of pre-written bullet points.
SAVE YOUR DOCUMENTS IN PDF FILES
- Instantly download in PDF format or share a custom link.
EE
E Erdman
Earnestine
Erdman
2961 Johnnie Heights
New York
NY
+1 (555) 994 4965
2961 Johnnie Heights
New York
NY
Phone
p
+1 (555) 994 4965
Experience
Experience
San Francisco, CA
Plant Quality Manager
San Francisco, CA
Reichel-Carroll
San Francisco, CA
Plant Quality Manager
- Evaluate the performance of the Quality Team to facilitate performance management, merit increases, promotions, job transfers, disciplinary action, etc
- Working knowledge of process improvement methodologies, such as Six Sigma, Lean Manufacturing, or Business Process Management
- Responsible for operations-level reporting on the performance of the quality system to management for review as a basis for improvement to the quality system
- Working knowledge of Process Improvement methodologies, such as Six Sigma, Lean Manufacturing, Business Process Management, etc
- Evaluates operational performance of the QA team to facilitate performance management, merit increase, promotions, job transfers, dismissals, commendations etc
- Assist in the statistical process control improvements with manufacturing and supplier base
- Develop a Quality culture that will drive Zero PPM and Zero Customer Complaints performance
Phoenix, AZ
Plant Quality Manager Closures Division
Phoenix, AZ
Davis-Wilkinson
Phoenix, AZ
Plant Quality Manager Closures Division
- Provide hands-on management of the elements of the QMS (Quality Management System.) These include quality action plans, corrective actions, supplier quality management, customer complaints, standard work, audit processes, standard procedures, test methods, and process controls
- Ensure Business Unit systems are tied into corporate standards via reviews and audits
- Responsible for managing all change control and line validation
- Generate scorecards and reports for all aspects of plant quality, not limited to and including VOC, CARs, SCARs, COAs, on-time and in-full deliveries, SPC reporting, losses, product safety, internal, third party & customer audits and change control processes
- Act as the lead plant representative for any meetings or interactions with customers as it relates to product or service quality
- Participate on teams and lead efforts toward continuous quality improvement initiatives within the plant
- Proficiency in Word, PowerPoint, Excel, MS Project & MS Share Point
present
Philadelphia, PA
Senior Plant Quality Manager
Philadelphia, PA
Lakin, Cruickshank and Beatty
present
Philadelphia, PA
Senior Plant Quality Manager
present
- Identify, develop, and lead continuous improvement processes across Design, Supply, and Build
- Work cross-functionally to drive continuous improvement processes of both products and systems
- Maintain quality objectives relative to business, product, and customer expectations
- Introduce and maintain a quality training administration system
- Develop relationships with personnel from major OEM's; other QA Managers/Directors/ Management within Corporate; AQSR Registration agency
- Develop, implement, and manage a product warranty system that provides feedback to responsible departments and assures permanent corrective action
- Maintaining quality data, providing operations with reports and utilizing Pareto analysis to drive performance improvements
Education
Education
Bachelor’s Degree in Engineering
Bachelor’s Degree in Engineering
University of San Francisco
Bachelor’s Degree in Engineering
Skills
Skills
- Excellent working knowledge of Quality Systems
- Strong leadership, problem solving (including root cause analysis), project management, presentation, and facilitation skills
- Strong communication, organizational, interpersonal and analytical abilities
- Strong computer skills and knowledge of Microsoft software programs
- Ability to understand timelines and current program status
- Ability to use statistical techniques/applications to solve quality issues
- Ability to strategize and implement solutions
- Core Tool Knowledge (APQP, PPAP, MSA, SPC, FMEA)
- Problem solving Knowledge (8D, 5Phase, 7Step, Root Cause Analysis etc.)
- Ability to effectively manage employees, vendors and customers
15 Plant Quality Manager resume templates
Read our complete resume writing guides
1
Plant Quality Manager Resume Examples & Samples
- Responsible for providing leadership; instilling a sense of urgency; and driving problems towards resolution to ensure that quality systems, procedures and instructions meet Customer requirements, Autosystems objectives, and regulatory compliance in the following areas
- Direct 8D problem solving team for all Customer-related quality issues, including tracking, reporting, problem solving issues; retain and maintain records as required
- Primary contact on all Customer quality concerns; ensuring all quality concerns are communicated accordingly
- Provide support to all departments for quality system development, corrective and preventative action and problem solving resolution
- Assist in Supplier selection and certification as required
- Assist in the statistical process control improvements with manufacturing and supplier base
- Complete all APQP-related activities, ECR processes, PDP (*D), and all other Quality Management System requirements as needed
- Ensure that conflict and productivity issues are managed directly , constructively, and professionally in all circumstances
- Drive year over year continuous quality improvement
- Develop the annual Quality plan
- Ensure enforcement of Customer Specific Requirements and compliance
- Adhere to all Autosystems and departmental procedures as required
- Attend training in order to develop and /or maintain relevant job-related knowledge, techniques, skills and/or certification
- Ensure, with the cooperation of other departments at Autosystems and Corporate, that the plant achieves and maintains the highest possible Customer rating for satisfaction and the lowest for PPM
- Independently designs and implements procedures and quality systems particular to manufactured products/processes that meet registration as well as Customer and Autosystems requirements
- Identify possible improvements related to quality, design, or production processes
- Supervise Quality Engineering, Lab personnel
- Build, strengthen, and maintain relationships with customers at all levels
- Monitor all customer related costs. (i.e. customer complaints, sorting, inspections etc.)
- Travel to customer sites as required. (i.e. presentations, corrective actions reports etc.)
- Post Secondary Diploma /Degree in an technical field or equivalent required
- ASQC Certified Quality Engineer/Certified Auditor, Certified Quality Manager an asset
- Lean Manufacturing experience required; formal training, an asset
- Knowledge of Autosystems products and process an asset
- Minimum 5 years experience in automotive OEM or Tier 1 required
- Minimum 5 years experience in management/ supervisory position required
- Lean Manufacturing experience required
- Strong leadership, problem solving (including root cause analysis), project management, presentation, and facilitation skills
- Strong communication, organizational, interpersonal and analytical abilities
- Ability to understand timelines and current program status
- Ability to strategize and implement solutions
- Problem solving Knowledge (8D, 5Phase, 7Step, Root Cause Analysis etc.)
- Present quality system findings and recommendations for improvement to all levels of the company through oral and written presentation
2
Plant Quality Manager, Roanoke Resume Examples & Samples
- Manage plant quality, champion plant quality initiatives and represent the Quality Department on the Material Review Board
- Track, report key plant quality metrics and establish plans to consistently improve key plant quality metrics
- Monitor trends in product and process quality
- Establish a continuous improvement process within the Quality Department at the plant level
- Apply analytical and statistical techniques to problem solving and continuous improvement opportunities
- Manage department expense, capital and personnel budgets and reduce cost of Quality at the plant
- Communicate supplier-related issues to Corporate Supplier Quality Engineer
3
Senior Plant Quality Manager Resume Examples & Samples
- Identify, develop, and lead continuous improvement processes across Design, Supply, and Build
- Work cross-functionally to drive continuous improvement processes of both products and systems
- Maintain quality objectives relative to business, product, and customer expectations
- Introduce and maintain a quality training administration system
- A minimum of 5 years of experience in a quality-focused leadership role in an industrial manufacturing setting
- Strong experience with leading and implementing quality management systems, specifically within New Product Introduction/Design, Build, and Supplier systems
- Experience within a low volume/high complexity OEM or tier-1 supplier
- ASQ certifications
- Six Sigma green or black belt certified
4
Plant Quality Manager Resume Examples & Samples
- Define Plant Quality objectives and monitor progress
- Manage the Plant Quality System in accordance with the Faurecia Excellence System
- Ensure the Plant's compliance with all Safety/regulation standards
- Report Quality results to all relevant parties and maintain Quality records/documentation
- Bachelor's degree in Engineering
- Minimum of 5 years of professional experience
- Customer relationship experience
5
Plant Quality Manager Resume Examples & Samples
- Represent Customer requirements internally
- Represent Faurecia Management at the Customer
- Responsible for the local CMM metrological room and metallurgical laboratory
- Responsible for customer quality complaints management and their problem solving path
- Ensure European Quality KPI’s are communicated, managed and achieved
- Responsible for deployment of Customer quality KPI’s, building Customer ownership at all levels
- Propose and manage implementation of process and product improvements to Customer Quality via Faurecia Functional teams
- Escalate high priority Customer Quality issues to senior FECT management
- Responsible for Customer Warranty management, technically and financially
- Responsible for Supplier Quality Assurance and problems follow-up after programs start-up. Collaborate with the Purchasing and Program organizations in all activities and initiatives concerning Supplier Quality Assurance
- Working with Customer Quality team, ensure Quality concerns are identified, reported and triaged based on Customer impact
- Ensure countermeasure actions are appropriate via cost-benefit analysis
- Provide both upstream and downstream reporting as required
- Prepare analysis/presentation material for Monthly Quality reviews
- Managing the social climate and labor relations
- Not to create or not to maintain any undisclosed or unrecorded funds, assets or branches of Faurecia, for any reason, of any nature
- Not to admit any offer, cash or in kind for the purpose of remuneration, sponsorship deals or any other form of remuneration to any customer or vendor representatives, directly or indirectly, for the purpose of the contract or any other commercial or financial benefits
- Min 5 Years’ Experience within an Automotive Tier-1 Company, with strong Manufacturing expertise and competence, Production oriented
- Knowledge of basics of TPS and WCM environments
- Ability to work in a stressful environment without losing control of operations and teamwork
- Open minded, respectful, listener and effective leader, capable to establish the right customer intimacy for a profitable relationship growth; self-motivated with strong written & verbal communication skills
- Ability to interrogate data, processes and systems to improve efficiency and quality
- Solid knowledge of Quality Tools in Production
- Highly competent with MS Office - Excel, Word, PowerPoint for daily management, data analysis, presentation and solution development
- Ability to organize and prioritize effectively ensuring deadlines are met
- Experience utilizing statistical techniques, six sigma methodologies, SPC, FMEA
- ISO-TS16949 deep knowledge and 1st/2nd party audit capabilities
- Minimum bi-lingual: Fluent in Italian and Proficient in English (C1) required
6
Plant Quality Manager Resume Examples & Samples
- Responsible for quality leadership for Plant Operations
- Position has the following direct reports: Quality Engineers; Quality Techs; Quality Systems Engineer; Supplier Quality Engineer. Supervises, leads, coaches and provides direction to these direct reports
- Position leads strategic quality action planning and implementation via communications updates of visual site management boards
- Supports Engineering test, audit, contamination and quality process improvement by organizing these functions within the plant
- Focus continuous improvement activities on current customer product while developing new systems for future customers and programs
- Coordinate value added improvement activities for assembly process and product
- Review and improve process control plans and PFMEAs (Process Failure and Mode Effect Analysis) for assembly
- Review and improve mistake-proof devices, designs or processes
- Coordinate scrap reduction activities and provide resource to support team –based cost reduction
- Coordinate incoming quality problem resolution and supplier response
- Coordinate warranty reduction programs for assembly based on customer historical database and analysis
- Promote and participate in work teams focused on the launch of new products using APQP (Advanced Product Quality Planning) tools
- Insures that a quality system is established and maintained in accordance with customer and TRW internal requirements as well as TS-16949
- Responsible for operations-level reporting on the performance of the quality system to management for review as a basis for improvement to the quality system
- Serves as liaison with customers or other external parties on matters relating to the quality system
7
Plant Quality Manager Resume Examples & Samples
- Ensures Quality organization support to Supply Chain management organization relative to the collection and analysis of supplier quality data and assists suppliers with product and process quality requirements
- Leads the development, implementation, and improvement of the appropriate Quality Management Systems throughout the operation, providing quality leadership and support in the development and launch of new products, processes and services
- Analyzes organizational Quality Metrics and performs managerial reviews to evaluate results and recommend action plans to close gaps at an operational level
- Develops and implements a Quality structure capable of supporting strategic plans and initiatives
- Designs and implements Quality Assurance training programs and conducts training in quality related topics relative to the work
- Leads improvement teams in the development and evaluation of process capability, process control plans, analysis of out of control conditions and process audits
- Ensures development, implementation and audit of complex inspection and test plans, standards and acceptance criteria and procedures/work instructions
- Coordinated and assists with corporate or division initiatives, participating on teams in order to drive best practices across Eaton Corp
- Designated as the Management Representative with responsibility and authority that includes
- Possesses a thorough understanding of problem solving methods (e.g. Six Sigma, 8-D root cause analysis and associated statistical tools) Quality Systems, and Mil-Stds
- Minimum five (5) years working in the Quality function within a manufacturing environment
- Minimum of two (2) years in a supervisor or leadership role
- Must be eligible to work in the US without sponsorship
- Prefer CQE and/or CQM
8
Plant Quality Manager Resume Examples & Samples
- Achieve product quality systems goals/site
- Assure execution of the quality system at the plant, and utilize process excellence tools/ methodology for continuous improvement and predictability
- Ensure that the Quality System is regularly audited/reviewed and that changes needed are implemented in a timely fashion
- Serve as a resource by recommending appropriate compliance efforts and proposing improvements to the Quality System
- Ensure all facility associates are educated in the regulatory requirements
- Maintain plant in compliance with Quality System Regulations
- Ensure plant have appropriate resources with the right competencies to execute the Quality System
- Maintain systems that assure only acceptable raw materials are used in processes and that only acceptable materials are shipped
- Provide timely information to Management on the status of conformance to requirements
- Maintain an effective Quality Information System (Doc Management, NCR, etc)
- Review and act as approval authority or delegated authority, retaining responsibility for all specifications, protocols, validations, fact books, and non-conformances
- Enforces, promotes and observes all safety, industrial hygiene rules and regulations established by the Company
- Takes appropriate actions to create and maintain a working environment aligned with OUR CREDO
- Support Quality Improvement Processes, Affirmative Action objectives and all activities to achieve World Class Manufacturing plant
- Participate or support major plant projects, such as transfer of new product or process
- Establish, and operate within, an effective budget and manpower plan for the QA organization
- Recruit, select and develop adequate human resources
- Support plant objectives in Safety, Health and of maintaining environmentally neutral operations
- Scope of operation encompasses approximately 20 - 30 employees on multi shift chedules
- Direct subordinates are Quality Operations Leader
- Annual appraisal of team members
- Appraise direct reports performance & recommends salary increases and promotions for direct subordinates
- AUTHORITIES (if applicable)
- 1 Education: Master / Bachelor degree
- 2 Experience: 12 to 15 years in Quality Assurance and/ Medical Device IndustryQuality Assurance
9
Plant Quality Manager, Illinois Resume Examples & Samples
- Involve plant and corporate management to develop practices and procedures that promote product, manufacturing process, and business system process quality
- Manage the Quality Engineering, Plant Training, Quality Auditing and Quality Technician functions at the plant level
- Liaison with Corporate Quality, Research and Development, Purchasing, Operations, and Process Development to resolve corporate level quality issues
- Organize and schedule laboratory testing
10
Plant Quality Manager Resume Examples & Samples
- Working with business leaders to identify and scope new process improvement opportunities in the areas of quality, cost, and service
- Driving continuous improvements in product quality by managing and executing process improvement projects using appropriate process improvement tools and methodologies
- Developing and managing controls and product audit processes within the plant
- Working with equipment and raw materials suppliers and trade groups to identify new technologies for improving product performance and cost reduction
- Working with the plant to identify and troubleshoot processing issues
- Eliminating waste and streamlining manufacturing flow using lean methodologies
- Ensuring the resolution of the complaint and claims processes in collaboration with corporate quality assurance and technical sales management
- Identifying best practices through data analysis and standardizing those practices by developing Standard Operating Procedures (SOPs)
- Driving the SOP and pre-ISO 9000 certification process
- Identifying training needs and providing training and coaching to improve operational efficiencies
- Ensuring compliance with the change management process to ensure that critical-to-customer product attributes are maintained or improved upon
- Training all quality control personnel including supervisors, inspectors, graders and operators
- Bachelor's degree in quality, engineering, or related discipline, or equivalent work experience
- 5+ years of quality management experience in a manufacturing plant environment
- Working knowledge of process improvement methodologies, such as Six Sigma, Lean Manufacturing, or Business Process Management
- Experience managing significant budgets, cost centers, and projects
- Prior experience training and coaching others on process improvement methods
- Strong facilitation and project management skills and the ability to lead cross-functional teams
- Excellent analytical, communication, and interpersonal skills
- Proficiency in computer applications, including Microsoft Office
- Master's degree in a related field
- ASQ certification (Certified Quality Engineer)
- Six Sigma Black, Green Belt, or Lean Certification
- Experience in flooring, paper, plastics or similar manufacturing industry
- Previous experience working with a unionized workforce
11
Plant Quality Manager Resume Examples & Samples
- Bachelor’s degree in a technical field
- 5-10 years of experience working with quality tools and methodologies
- Experience with ISO/AS/ASME/NBBI quality systems
- Management experience with direct reports desired
- Must possess organizational skills with the ability to use resource materials to manage multiple projects
12
Plant Quality Manager Resume Examples & Samples
- Develop, execute, and continually improve a comprehensive quality program as defined by the Pepperidge Farm QPM and CSC North American Quality Policies. (Compliance Quality)
- Drive process / continuous improvement initiatives through staff, work group, Plant group, Pepperidge Farm Quality staff, and R&D (Process/Food Quality)
- Manage & Drive Consumer Complaint programs, initiatives, and consumer delight models for each business
- Manage department & people by establishing goals, objectives, IDP, and coaching
- Support plant programs, safety, reliability and employee relationships
- Expert abilities and decision making in Food Safety, Regulatory, and Quality Systems and their application within food processing
- Expert knowledge in Sanitation and GMP Practices, familiarity with Pest Control programs and techniques
- Knowledge of Quality Standards, and Quality Policies, with skills and ability to execute against requirements
- Knowledge and general business acumen to support and influence Manufacturing, including best practices and innovative technologies
- Knowledgeable in industry Food Safety/Quality audit practices, and skilled in adapting to achieve business best practices
- Capable of engaging other businesses unit quality in development and standardization of; Quality manuals, policies, procedures, and data templates, audit standards and procedures, and Quality Key Performance Indicators
- Knowledgeable in Statistical Process Control programs and Process capability studies
- Ensures plant personnel is technically capable of handling non-routine quality system issues and that issues are investigated, documented, and resolved
- Ability to drive organizational alignment on Quality objectives with an enterprise-wide mindset, and the adaptation of structure, processes, and systems to achieve objectives
- Capable of influencing development steps used in the Innovation and Commercialization process to leverage Design in achieving consumer safety and quality objectives (example; HACCP Assessment)
- Assertive, Outspoken, yet collaborative. Demonstrated skills influencing components of the company, tough-mindedness, vision, and political savvy to manage internally and externally
- Dedicated work habits, takes initiative, sets high standards
- Knowledgeable and capable of collaboration on quality programs; drives improvement of consumer based specifications
- Aware of Continuous Improvement tools
- Ability to manage and recognize talent and skills needed for the job
- Ability to manage, coach and develop people, talent and skills
- Ability to demonstrate & execute against leadership behaviors
13
Plant Quality Manager Resume Examples & Samples
- Lead all manufacturing sites efforts to ensure customer quality performance expectations and requirements are effectively managed
- Leads implementation of customer requirements at the manufacturing sites including coordinating/leading customer visits and acting as liaison with vendors to ensure their products meet the needs of Tenneco & customer requirements
- Lead facilities effort to eliminate product and process defect causes by utilizing Team-Oriented Problem Solving methodology and recommending changes or solutions to problems. Lead the resolution of customer complaints management process at the manufacturing sites. Institute processes to ensure timely and effective resolution of customer complaints via appropriate team-oriented problem solving methodology (Red X, Global 8D, Kepner-Tregoe, Six Sigma, etc..)
- Leads the manufacturing sites overall Quality Management System (ISO/TS 16949 and IATF 16949) development, implementation, and monitoring to ensure manufacturing sites business objectives are achieved
- Maintain tracking and reporting manufacturing sites performance and customer satisfaction metrics and publish reports / improvements actions needed to achieve manufacturing sites/business unit’s objectives
- Develop a Quality culture that will drive Zero PPM and Zero Customer Complaints performance
- Drive improvement projects at the manufacturing sites focused on Quality initiatives that supports Tenneco’s Business Systems / Total Quality Management. Participate, support and lead projects for the manufacturing sites/business units that adapt and implement best practices in Quality Assurance. Support the manufacturing sites effort in driving reduction in Cost of Poor Quality
- Manage and develop Quality professionals and direct their training, quality functional competency development activities to drive enhanced levels of quality team performance in achieving business objectives
- Support the Engineering, Sales and Launch teams in executing New Product Launches via the TENPlus process to ensure new product and process are launched flawlessly. Must be able to apply the Project Management principals to ensure timely completion of project tasks
- Develop in coordination with Supply Chain organization a robust Supplier Management processes that supports the needs of the manufacturing sites & business unit
- Establish Warranty Management Process, that clearly established the work flow process, captures current warranty performance, develops reliability predictive models to forecast future trends and drives improvement projects to reduce warranty costs to the business
- Bachelors in Engineering disciplines
- Minimum of 10-15 years of work experience preferably in automotive manufacturing environment
- Prefer candidates with ASQ Certification in any of the following: Certified Manager of Quality/Organization Excellence (CQM/OE), Certified Quality Engineer (CQE), Certified Reliability Engineer (CRE) and Six Sigma (SSGB/SSBB)
14
Plant Quality Manager Resume Examples & Samples
- Assist plant management in setting and maintaining quality objectives and assures plant quality objectives are being met. Identify appropriate tasks and schedules required to accomplish goals and continuous improvement in the process
- Assist in organizing and understanding customer satisfaction based upon product and service performance
- Facilitate problem solving activity through TQM, team building and quality systems tools and methods. Works with the line and process supervisors in identifying negative quality trends and repetitive defects. Assist in the problem solving process
- Establish customer relationships by ensuring consistency of 5 UPS, making customer visits as appropriate and assisting in implementing customer quality management systems
- Investigate customer complaints and work with appropriate management to resolve issues. Assist process managers in preparing customer complaint responses and maintain data base on all customer complaints
- Apply technical expertise in problem identification in the following areas: Glass properties/bottles design/attributes, Line/handling requirements, Carton specifications/makeup/requirements, Customer processing, Fracture analysis
- Administration of in-plant and outside warehouse GMP programs and may direct outside warehouse reselect activity
- Responsible for coordinating plant activities to execute sampling requests
15
Plant Quality Manager Resume Examples & Samples
- Act as the management representative managing ISO 9001 certification activities including authority on ISO 9001 requirements
- Manage Final and In-Process inspections necessary to ensure Quality products to customers. Drive error-proofing solutions at the source to address issues found during inspections
- Lead plant Supplier Quality activities to ensure the incoming Quality of purchased parts
- Coordinate and manage continuous improvement activities related to Quality including 8D’s, Kaizen events, BPI’s, Six Sigma projects, and other problem solving activities
- Develop and maintain an appropriate departmental budget and ensure the operation of the Quality Department within budget
- Evaluate the performance of the Quality Team to facilitate performance management, merit increases, promotions, job transfers, disciplinary action, etc
- Bachelor’s degree in Engineering or Business from an accredited institution
- Five (5) years experience in quality, manufacturing or engineering
- Two (2) years experience developing and leading strategic quality, manufacturing or engineering projects
- Understand EQS, ELSS, & EBE as components of the EBS, including the assessment process and criteria
- Technical degree preferred
16
Plant Quality Manager Resume Examples & Samples
- Leading the plant Quality Department team to ensure daily production is within specification, including training and accountability
- Maintaining proper calibration of all quality measurement tools and associated record keeping
- Maintaining quality data, providing operations with reports and utilizing Pareto analysis to drive performance improvements
- Responsible for maintaining all documents on Gateway
- Responsible for maintaining finish line ticker so that it reflects most current product specifications
- Owning the DSQ Process and Data
- Working with corporate Quality Assurance and plant operations to quickly resolve customer quality concerns and claims
- Ensuring on-going compliance to corporate Quality Management System
- Leading projects to improve real time quality adherence
- Leading the investigation and integration of new raw materials
- Participating in new product development
- Bachelor’s degree in quality, engineering, or related discipline
- 5+ years of quality or operations management experience in a manufacturing plant environment
- Working knowledge of Process Improvement methodologies, such as Six Sigma, Lean Manufacturing, Business Process Management, etc
- Experience managing significant budget, cost centers, and projects
- Experience training and coaching others on process improvement methods
- Strong facilitation and project management skills and ability to lead cross-functional teams
- Excellent analytical, communications, and interpersonal skills
- Proficiency in computer applications, including MS Office
- Six Sigma Black or Green Belt certification
- Lean certification
- Experience working with a unionized workforce
17
Plant Quality Manager Resume Examples & Samples
- Minimum ten (10) years in Quality environment with a minimum of 3 years of experience working in the Aerospace Industry
- Minimum of five (5) years in a supervisor or leadership role
- US citizen or others with permanent residency authorization (Green Card or equivalent)
- Must be able to work in the United States on a continual basis without requiring corporate sponsorship
- 10 years of experience in problem solving methods (e.g. Six Sigma, 8-D root cause analysis and associated statistical tools) Quality Systems, and Mil-Stds
18
Plant Quality Manager Resume Examples & Samples
- Optimize, harmonize and continuously develop the quality systems
- Interface with customers to resolve quality issues by driving permanent and effective corrective/preventative actions
- Manage and develop the quality team
- Continuously develop systems and processes for Quality management
- Manage audits and certifications
- Benchmarking of the internal quality systems to stimulate development
- Manage customer and consumer complaints according the Hygiene process and system (SAP)
- Maintain and develop our quality benchmarking system an process
- Develop KPI systems to monitor quality development
- Support the implementation of the Global Hygiene Supplier Standard
- Interface with customers to resolve quality issues
- Drive permanent and effective corrective/preventative actions
- Work with all departments to ensure customer quality requirements are understood and met
- Provide effective feedback to the management team with regard to customer concerns and issues
- Represent Gemerska Horka in international SCA quality networks
19
Plant Quality Manager Resume Examples & Samples
- Performs two (2) Safetrack observations per month
- A minimum of three years related experience including supervisory experience
- Proficiency in a Windows operating environment, including email and Microsoft Office software
- Demonstrated planning, problem solving, data analysis, GD&T, blueprint reading, organizing, inter-personal, and communication skills with proven leadership skills and decision making abilites
- Strong knowledge of manufacturing procedures, production methods (including machining and welding), shop standards, team building, SPC and modern quality assurance applications
20
Plant Quality Manager Resume Examples & Samples
- Provide hands-on management of the elements of the QMS (Quality Management System.) These include quality action plans, corrective actions, supplier quality management, customer complaints, standard work, audit processes, standard procedures, test methods, and process controls
- Generate scorecards and reports for all aspects of plant quality, not limited to and including VOC, CARs, SCARs, COAs, on-time and in-full deliveries, SPC reporting, losses, product safety, internal, third party & customer audits and Change Control processes
- Where applicable, manage the food safety team and organize its work, ensure relevant training and education of the food safety team members, ensure the food safety management system is established, implemented, maintained and updated, and report to the organization's top management on the effectiveness and suitability of the food safety management system
- Participate on teams and lead efforts toward continuous improvement initiatives within the plant
- Participates in cross-divisional teams or audits
- 4-year degree in Engineering
- 3-5 years work experience in manufacturing related role
- Lean six sigma experience
- Statistical analysis expertise
- Ability to work across multiple functions and lines of business
- Proficiency in the following software: Word, Power Point, Excel, MS Project, Visio, Share Point, SPC software & Agile
- Statistical analysis proficiency
- Green belt certification
- Strong verbal & written communications skills
21
Plant Quality Manager Resume Examples & Samples
- Ensures policies, programs, plans, procedures and practices are carried out consistently and accurately. Audits work records and documentation for accuracy, to conduct analysis of trends and to produce forecasts
- Evaluates and recommends changes in methods, sampling techniques and control procedures and process
- Acts as liaison with plants and other Divisions including production, engineering and sales
- Estimates personnel needs and develops work methods to accomplish assigned work
- Sets direction for error, spoilage and salvage reports
- Oversees multiple plant representatives for QS9000 and ensures compliance with governmental regulations
- Visits customers and suppliers to confer on specific quality issues and develops solutions as required to support plants
- Performs such individual assignments as the supervisor may direct; establishes and maintains effective work relationships within the Division, the Corporation and the community; and maintains the professional competence, knowledge and skill necessary for the satisfactory performance of all assigned responsibilities
- Performs those administrative activities necessary for the effective management of the department, including provision for the selection and development of employees, employee safety, pay administration, budget administration, employee counseling and motivation, organization goals and objectives, and planning, organizing, integrating, and measuring the work performed within the department and ensures adequate and continuous control is exercised over the activities affecting quality
- Lead and direct the work of others
- Performs related duties and special projects as assigned
- Regular and predictable attendance
- Performs those administrative activities necessary for the effective management of the division
- Plans day-to-day division operations
- Acts as liaison with other divisions including production, engineering and sales
- Prepares error, spoilage and salvage reports
- Serves as Divisional representative for QS9000 and ensures compliance with governmental regulations
- Visits customers and suppliers to confer on specific quality issues and develops solutions
- Self-directed with a high degree of self- motivation
- Proficient computer skills and abilities with Microsoft Office products (Outlook, Excel, PowerPoint, etc)
- Some production or manufacturing experience, and accreditation as a quality engineer
- Ability to travel (domestic and/or international) including air travel and long automobile trips
22
Plant Quality Manager Closures Division Resume Examples & Samples
- Ensure Business Unit systems are tied into corporate standards via reviews and audits
- Responsible for managing all change control and line validation
- Participate on teams and lead efforts toward continuous quality improvement initiatives within the plant
- Promote awareness of customer requirements for the plant
- Some level of travel required
- 2+ years work experience in a corporate or plant setting (engineering or leadership role)
- Analytical skills and statistical analysis proficiency
- Experience as a leader of project teams
- Proficiency in Word, PowerPoint, Excel, MS Project & MS Share Point
- Quality Management Systems experience with ISO9001 a plus
23
Plant Quality Manager Resume Examples & Samples
- Generate scorecards and reports for all aspects of plant quality, not limited to and including VOC, CARs, SCARs, COAs, on-time and in-full deliveries, SPC reporting, losses, product safety, internal, third party & customer audits and change control processes
- Actively leads cross-divisional teams toward continuous improvement initiatives
- Leads cross-divisional quality improvement initiatives and audits
24
Plant Quality Manager Resume Examples & Samples
- Minimum of five (5) years regulated environment industry experience
- Minimum of five (5) years of supervisory experience
- Lean Six Sigma Black Belt Certification
- Knowledge and experience implementing the key elements required to be successful in managing in a regulated environment
- Ability to lead and influence an organization to achieve performance excellence
- Ability to lead and execute regulatory/customer site inspections
- Ability to negotiate
25
Plant Quality Manager Resume Examples & Samples
- Manage supplier’s non conformity and monitor supplier’s progress
- Report to the management about the quality system and needs for improvement
- Quality representative for Hlohovec and Bratislava plant
- Special requirements for CCC (Chinease Compliance Certification)
- Ensuring that quality system, which meets the requirements of this document (Requirements on the quality assurance capabilities of the factories for CCC certification) is established, implemented and maintained
- Ensuring that the products with the compulsory certification mark are produced in conformity with the standards according to which they have been certified
- Establishing documented procedures to ensure that Compulsory certification marks are kept and used appropriately
- Establishing documented procedures to ensure that the compulsory certification mark is not affixed on any non-conforming product or changed product that was not notified to the certification body
- Minimum 3 years of professional experience as Quality Manager
- Active knowledge of English and German language
26
Plant Quality Manager Resume Examples & Samples
- Formulate and execute quality assurance objectives in alignment with Corporate, Business Unit, Plant goals and requirements
- Coordinate objectives in collaboration with the VP of Quality Asia Hub and Yonezawa plant manager to maximize product quality, performance, reliability and minimize costs
- Perform Gap Analysis between established goals and objectives and current plant QA capability and rapidly develops and communicates plans to close critical QA gaps
- Develop analyze and reports statistical data relative to quality systems performance and implementation, ensuring customer expectations are maintained
- Develop and maintains audit functions ensuring quality systems and products are consistent with internal documentation, standards and customer requirements
- Ensure documentation management systems and processes are established which maintain effective control of design specifications, component/product drawings,and manufacturing processes and records
- Plan, promote and organize training activities related to quality and inspection activities
- Develop and maintain failure analysis process ensuring feedback and corrective action communication and implementation is consistent with customer expectations
- Direct employees engaged in inspection and testing activities to ensure continual and effective control over materials, facilities, processes and products
- Act as Plant Management representative and ensure full compliance to ISO 9000 standards
- Establish and maintain Plant Quality budgetary responsibilities
- Bachelor’s degree and Quality management experience in a progressive quality environment
- Excellent experience with implementing Six Sigma, Statistical Process Control (SPC), FMEA, process audits and other proactive quality management practices
- Management and leadership skills with an ability to collaborate with R & D, Product Management, Process Engineering and all other functions
- Experience in the semiconductor industry will be an advantage
- Interviewing, hiring, and training employees; planning, assigning, and directing work; appraising performance; rewarding and disciplining employees; addressing complaints and resolving problems
- Six sigma black belt certification / experience preferred
- Physical effort normally found in an office environment
- Frequent visits in clean room manufacturing auditing processes and people, standing, walking observing, etc
- Occasional lifting and/or carrying of small objects and tools
- Travel within Japan and to foreign countries on an occasional basis
27
Plant Quality Manager Resume Examples & Samples
- Ability to define problems, collects data, establish facts and draw valid conclusions
- Ability to effectively present information to large groups
- Good communication skills (presentation, written, and oral). Proven leadership skills
- Must be able to recognize and support plants performance and priorities
- Experience: 3+ years of experience in a leadership role in QA/manufacturing environment in a medical device company or other regulated, critical end-use product industry. Mechanical assembly and chemical manufacturing processes
28
Plant Quality Manager Resume Examples & Samples
- Manage the preparation, implementation, and maintenance of the Quality Management System to comply with EQS and ISO 9001
- Develop and implement strategic projects and tactical initiatives to continually improve the overall Quality of products, information, and services
- Interface with customers, suppliers, partners, and internal stakeholders in both the plant and at customer locations to enhance their perception and understanding of the plant Quality systems
- Facilitate customer Quality audits and inspections as appropriate to demonstrate compliance
- Manage and effectiveness of the internal audit and corrective action programs
- Help collect and analyze key quality data to key performance indicators by using statistical tools
- Work manufacturing and product engineering to ensure successful new product launches
- Bachelor’s degree in engineering, technology, or business
- Three (3) years experience in quality, manufacturing or engineering
- Understand EQS, ELSS
- EBE as components of the EBS, including the assessment process and criteria
29
Plant Quality Manager Resume Examples & Samples
- Work as part of the new site project management team to ensure that EHS and Quality issues are considered and built in to all new systems and ways of working during the set-up of a new greenfield facility
- Ensure the company observes the highest level of EHS standards
- Develop and Maintain top level and appropriate site Quality KPI’s. Define and set targets with stakeholders
- Collaborate with teams, and stakeholders, introducing new products to ensure quality standards are met from launch
- Support operational objectives to reduce wastage, install 5S philosophy and reduce non unit based costs
- Engage in customer audits to ensure there are adequate quality controls to conform to our audit specifications
- Knowledge, and understanding, of relevant Quality Standards
- Proven experience of implementing world class system, with the ability to drive high quality processes
- Ideally have working knowledge of ISO9001, TS/IATF 16949, ISO 14001 and OHSAS
- A degree or equivalent experience within a relevant field
- Strong focus and proven experience in applying Six Sigma techniques and tools in Quality Improvement processes
- 30th June 2017
30
Plant Quality Manager Resume Examples & Samples
- Bachelor’s degree in Engineering or BS Equivalent with emphasis on Quality Management
- Eight (8) years of related experience in a high-paced manufacturing environment in the role of Quality Control Manager
- Six Sigma black belt trained or certified highly preferred
- Proficiency in Microsoft Suite Applications (Word, Excel, Access, & PowerPoint) and Internet software and email is required
31
Plant Quality Manager Resume Examples & Samples
- Bachelor degree or similar in Quality Management or Engineering
- 10+ years of quality management experience within an international manufacturing company in the FMCG or pharma industry
- Process/Packaging experience in EBM, ISBM, etc. is of advantage
- Knowledge of ISO quality standards and experience performing quality and food safety system audits
- Professionalism and dedication to excellence in quality and customer care
- Excellent relationship building skills and communication skills in Arabic and English
- Proven track of leading people and passion to develop employees
- Highly self-motivated and self-driven
- Profound MS Office skills