Product Quality Manager Resume Samples
4.8
(120 votes) for
Product Quality Manager Resume Samples
The Guide To Resume Tailoring
Guide the recruiter to the conclusion that you are the best candidate for the product quality manager job. It’s actually very simple. Tailor your resume by picking relevant responsibilities from the examples below and then add your accomplishments. This way, you can position yourself in the best way to get hired.
Craft your perfect resume by picking job responsibilities written by professional recruiters
Pick from the thousands of curated job responsibilities used by the leading companies
Tailor your resume & cover letter with wording that best fits for each job you apply
Resume Builder
Create a Resume in Minutes with Professional Resume Templates
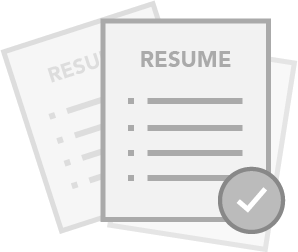
CHOOSE THE BEST TEMPLATE
- Choose from 15 Leading Templates. No need to think about design details.
USE PRE-WRITTEN BULLET POINTS
- Select from thousands of pre-written bullet points.
SAVE YOUR DOCUMENTS IN PDF FILES
- Instantly download in PDF format or share a custom link.
JR
J Roberts
Jose
Roberts
956 Trenton Bridge
Dallas
TX
+1 (555) 263 3553
956 Trenton Bridge
Dallas
TX
Phone
p
+1 (555) 263 3553
Experience
Experience
San Francisco, CA
Product Quality Manager
San Francisco, CA
Sanford, Herman and Barton
San Francisco, CA
Product Quality Manager
- Developing workforce shaping strategies and employee development initiatives
- Lead and manage manufacturing continuous improvement projects, as well as process improvement initiatives
- Develop and continuously improve Oculus’ Quality Management System
- Manage and develop a team of quality specialists and offer technical guidance and support to their activities
- Establish and maintain supplier performance metrics (cost, delivery, service, quality, innovation, social responsibility, etc.) together with the sourcing team
- Create & maintain a culture of continuous improvement throughout their team and organisation
- Keep Quality Management and team updated on issues which impact the business and work
San Francisco, CA
QA Product Quality Manager
San Francisco, CA
Ullrich-Stanton
San Francisco, CA
QA Product Quality Manager
- Fostering an environment of continuous improvement and providing leadership in this area
- As a key member of the pharmaceutical Site Functional Managers, work with colleagues throughout the plant to deliver on the plant goals
- Contribute to the decision making in the Management Team of the Quality Department concerning the general matters, organisation, resources, staffing policy
- Coaching of co-workers in the conduct of audits
- QA leadership/input for site development projects
- To manage a team of varying disciplines to deliver the responsibilities and mandate of the department
- To take the overall responsibility for delivering the departments functional goals including financial and people development
present
Boston, MA
Product Quality Manager Novecare
Boston, MA
Bradtke-Runolfsdottir
present
Boston, MA
Product Quality Manager Novecare
present
- Provide technological support and expertise to the business, production management and to product development departments
- Develop and implement process improvement programs
- Follow up the production performance and identify opportunities to improve competitiveness
- Approve the compliance of the product quality in case of change and ensure customer information through an established management of change MOC procedure
- Report to management results and developments realized in the department
- Ensure expertise is maintained, developed and exchanged within the team
- Define, defend, organize and supervise process improvement projects
Education
Education
Bachelor’s Degree in Engineering
Bachelor’s Degree in Engineering
University of North Texas
Bachelor’s Degree in Engineering
Skills
Skills
- Assures compliance with established policies/procedures of the Division and Corporation and complies with all applicable governmental regulations (GMP, etc.), both domestic and foreign
- Supports the development and maintenance of a Quality Agreement with the external parties/partners. May provide input into the development of contractual agreements with the external manufacturers
- Ability to make well-informed and conclusive decisions with vague and/or ambiguous data, including identifying trends, patterns, and applying business process analysis to make recommendations around these
- Create supplier performance reports, initiate actions based on gaps, and ensure timely follow up and review. Create supplier specific development road-maps to meet targets
- Develop and implement Advanced Product Quality Planning or similar process (i.e. PFMEA, process flow, control plan, SPC) for purchased parts on new and existing products
- Ability to juggle many projects and consistently deliver results with relentlessly high quality, accuracy and extreme attention to detail
- Responsible for evaluation and/or release of products to other sites and/or to the market with the assurance that the goods were produced in conformance to all applicable policies/procedures of the Company and compliance with all governing regulations
- Experience or knowledge in test engineering, reliability engineering and supplier quality engineering; A plus with experience working with high volume production and traveling to manufacturing sites
- Participate in the selection of new suppliers relating to the manufacture of products and systems. Support the project team during the development phase and coordinate the technical/quality interaction between the engineering department, the purchasing organization and suppliers
- Excellent Quality knowledge – PFMEA, Process Flows, Control Plans, 8D/CAPA, 6Sigma among others
15 Product Quality Manager resume templates
Read our complete resume writing guides
1
QA Product Quality Manager Resume Examples & Samples
- To take the overall responsibility for delivering the departments functional goals including financial and people development
- To manage a team of varying disciplines to deliver the responsibilities and mandate of the department
- Managing the Quality Assurance QA Product Quality Department in order to provide accurate, compliant, cost effective and timely support to the plant and agreed support for projects that may arise
- Anticipating and planning for future requirements in the area, including such aspects as procedural requirements, capital equipment planning, personnel recruitment planning, compliance requirements, efficiency developments and anticipated changes needed to reflect future demand for services from the department and reflecting these in a timely way in the area budgeting process
- Provide accurate, compliant regular reports on the status of the department
- Defining strategic & functional goals and objectives for the QA department
- Act as a QP Qualified Person for the manufacture of products manufactured at the Cork site and the release within the EU for products manufactured at the Shanghai site
- Fostering an environment of continuous improvement and providing leadership in this area
- As a key member of the pharmaceutical Site Functional Managers, work with colleagues throughout the plant to deliver on the plant goals
- Contribute to the decision making in the Management Team of the Quality Department concerning the general matters, organisation, resources, staffing policy
- Actively participate in Global Quality initiatives of harmonization of best practices and development of systems and processes to support efficient and effective quality systems
- Ensure Qualified and motivated co-workers, due to the implementation of a good department policy on recruitment, training, meetings, team building and employee performance
- Coaching of co-workers in the conduct of audits
- Global orientation (external looking) with a strong customer service focus
- QA leadership/input for site development projects
- QP Qualified Person
2
Product Quality Manager Resume Examples & Samples
- Acting as agent of change across the global Higher Education business to drive key change initiatives across the business to improve products, processes and ensure operational effectiveness, partnering with leads in product management, product engineering, project management, product strategy, and media development
- Actively identifying opportunities for process, product or service improvements related to global Higher Ed products, including leading retrospectives; selecting and prioritizing projects in conjunction with partners and stakeholders, aligned with strategic goals; and having accountability for projects targeted to address the opportunities
- Understanding how to effectively leverage best practice change management methods, tools and approaches to create an effective change plan to manage key change risks associated with deploying projects and deriving a return on investment
- Assessing and measuring quality of new and existing global Higher Education digital products by analyzing available data sets and gathering customer feedback via direct or indirect customer engagements. Drawing conclusions from this analysis and presenting it in a relevant manner to business partners and executive leadership
- Developing dashboards and presentations to display critical, actionable information and efficacy learner access data in a highly visual way that is consumable by a range of stakeholders, helping to drive organizational transparency around quality levels in support of Pearson’s commitment to efficacy and continuous improvement
- Maintaining a strong consumer sensibility while leading or participating in customer journey mapping or other user experience research sessions. Recommending areas within product experiences that are candidates for improvement or further user experience evaluation
- Support a range of activities to ensure Higher Ed product readiness and monitoring during key back-to-school peak periods
- 3+ years of experience in product development, project management, customer experience or marketing, or education
- Self starter, must be productive with minimal direction
- A history of positive teamwork, flexibility, and the ability to thrive in a fast-paced cross-functional environment with colleagues around the globe
- Ability to make well-informed and conclusive decisions with vague and/or ambiguous data, including identifying trends, patterns, and applying business process analysis to make recommendations around these
- Excellent communication skills (written and verbal) and ability to easily communicate complex ideas.and influence multiple stakeholders at various levels
- Excellent visual design sense regarding clear and accurate presentation of data
- Ability to juggle many projects and consistently deliver results with relentlessly high quality, accuracy and extreme attention to detail
- Outstanding productivity software skills, with a specific focus on Excel/Google Sheets and other data analysis tools and PowerPoint/Google Presentations
3
Product Quality Manager Resume Examples & Samples
- Ensure all records related to batches and shipments for the company label products are reviewed, accepted/reject and maintained
- Ensure adequate oversight and review of Deviations, Investigation reports and the assessment of assigned CAPA's and timely follows up with contract manufacturers as needed to ensure effective resolution
- Ensure Review of Process validation and annual product reviews of products at contract manufacturers to ensure products are validated and remain validated
- Ensure appropriate technical documents are available and accepted to support distribution of NH labelled product including stability studies, analytical and process documentation
- Implementation of systems for trending critical analytical data and stability data as appropriate for all company products
- Help develop the oversight of temperature studies from transport activities, identify issues and follow up as appropriate
- Manage and develop a team of quality specialists and offer technical guidance and support to their activities
- Empower and oversee team to employ technical judgement on analytical results, make decision and decide on the disposition of supplier batches and shipments on behalf
- Ensure product quality policies are conducted correctly and efficiently
- Liaise and build relationships with manufacturers and involved parties to ensure product quality issues investigated and documented appropriately
- Responsible for verifying contact manufactures maintain compliance with quality agreement
- Provide quality leadership, direction and support to NH quality staff and manufacturers
- Liaise with the Supplier Quality Group, to focus on key quality areas of outsourced activities during supplier audit and technical visits
- Create & maintain a culture of continuous improvement throughout their team and organisation
- Keep Quality Management and team updated on issues which impact the business and work
- Liaise with internal and external customers, provide data and assistance to ensure company activities run smoothly
- Participate in and lead regular team and group meetings
- Educated to degree level or higher, ideally B.Sc. or post graduate studies in Chemistry, Chemical Engineering; other related scientific disciplines may be considered
- 5+ years' experience including 2 years managerial in finished dose pharmaceutical manufacturing and preferable in a progressive multinational organization. The post holder will have technical manufacturing, quality or laboratory experience
4
Product Quality Manager Novecare Resume Examples & Samples
- To analyze and improve current technologies and production processes, and to develop, test and implement new technologies and production processes in order to ensure the long term competitiveness of the Site production processes, control of risks related to products and support the team on HSE risks control
- To improve the performance of the site production units, by supporting mainly the Production Unit Manager and the QHSE manager, as well as the other department on specific topics, in the various fields (HSE aspects of products and processes, quality of products, process capabilities, process reliability, capacity, competitiveness), or by defining projects, together with R&I, Engineering and the Technology team of the GBU, to deal with recurrent issues or opportunities in order to implement a continuous improvement process, to comply with regulatory, legal, company standards and to develop customer orientation by implementing solutions to their expectations
- Develop and implement process improvement programs
- Direct and execute both short term and strategic studies regarding production cost optimization, production capacity utilization, information and material flows.
- Follow up the production performance and identify opportunities to improve competitiveness
- Define, defend, organize and supervise process improvement projects
- Define the optimal production set-up, according HSE and technical Group standards, to ensure the long term competitiveness of the industrial activities
- Support compliance with HSE regulations, quality standards and company policies
- Ensure compliance with quality policies and HSE rules, regulations and policies
- Assure the confidentiality of technological information
- Provide process technology information, support and advice to the organization
- Propose solutions for internal and external customer demands and complaints
- When demanded by the GBU, provide process technology support to customers, suppliers and auditors (if requested)
- Provide technological support and expertise to the business, production management and to product development departments
- Calculate and make available plant performance indicators, product and process capabilities and reliability indicators
- Exchange relevant technological information with other Group entities
- Manage own department and staff
- Define, propose, implement and follow up the department’s budget, objectives, policies and procedures
- Promote innovation and continuous improvement on site
- Report to management results and developments realized in the department
- Ensure expertise is maintained, developed and exchanged within the team
- Product Safety studies
- Manufacturing excellence projects
- Maintain product competitiveness
- Participate in defining Quality and Excellence Programs indicators shared at all levels of the site and ensures that they are tracked throughout the site
- Ensure that the product delivered agreed with specification procedures and test methods negotiated and approved with customers
- Approve the compliance of the product quality in case of change and ensure customer information through an established management of change MOC procedure
- Ensure adequate documented process robustness, including prevention of cross-contamination and mix-up and traceability of materials
- Degree in General Chemistry (mineral, organic, polymers and surfactants)
- Experience in industrial project management
- Knowledge of Manufacturing Excellence approach, methods and tools
- Knowledge of responsible care, HSE regulations, Quality norms and knowledge of Safety Process tools and techniques
- Strong result orientation, ability to challenge, impact & influence
- LI-LT1
5
Product Quality Manager Resume Examples & Samples
- Ensure all records related to batches and shipments for the NorthStar label products are reviewed, accepted/reject and maintained
- Ensure adequate oversight and review of Deviations, Investigation reports and the assessment of assigned CAPA’s and timely follows up with contract manufacturers as needed to ensure effective resolution
- Implementation of systems for trending critical analytical data and stability data as appropriate for all Northstar products
- Empower and oversee team to employ technical judgement on analytical results, make decision and decide on the disposition of supplier batches and shipments on behalf of NorthStar
- Liaise with internal and external customers, provide data and assistance to ensure Northstar activities run smoothly
- 5+ years experience including 2 years managerial in finished dose pharmaceutical manufacturing and preferable in a progressive multinational organization. The post holder will have technical manufacturing, quality or laboratory experience
- Solid understanding and knowledge of cGMP and regulatory principles in a finished dose pharmaceutical manufacturing environment
- Thorough knowledge of pharmaceutical testing and batch release processes
- Proven record in analytical decision making on complex analytical issues
- Ability to work effectively with others to accomplish goals in a challenging
- Demonstrated ability to lead others to improve performance or effectiveness
6
Product Quality Manager Resume Examples & Samples
- 5+ years technical experience supporting high volume consumer electronics, preferably in handheld phones
- Good understanding of electronic assembly processes and testing methodologies
- Working knowledge of statistics; Knowledgeable in data analysis and interpretation
- Ability to work in a fast-paced, technically dynamic environment
7
Product Quality Manager Resume Examples & Samples
- Monitor and investigate reported quality issues, and perform or lead root cause analysis and solve issues through the corrective action process
- Train and educate suppliers to apply analysis and problem solving to their own factories. Coordinate preventive and corrective action implementation at suppliers
- Participate in internal quality & supplier review meetings and present product quality issues
- Participate in the selection of new suppliers relating to the manufacture of products and systems. Support the project team during the development phase and coordinate the technical/quality interaction between the engineering department, the purchasing organization and suppliers
- Promote early supplier involvement at project development stages
- Develop and implement Advanced Product Quality Planning or similar process (i.e. PFMEA, process flow, control plan, SPC) for purchased parts on new and existing products
- Ensure safe launch by conducting new product inspection for first few lots (hands-on experience)
- Establish and maintain supplier performance metrics (cost, delivery, service, quality, innovation, social responsibility, etc.) together with the sourcing team
- Create supplier performance reports, initiate actions based on gaps, and ensure timely follow up and review. Create supplier specific development road-maps to meet targets
- Minimum of 5-10 years of quality assurance, quality control, data analysis/reporting and supplier development experience; product engineering is a plus
- Specialization in electronics products (audio industry) and related parts (PCBA, transformers, metal, plastics, wooden cabinets, etc.) is strongly preferred
- Proficient bilingual skills (English & Chinese)
- Strong written and spoken communication skills specifically the ability to express ideas clearly and concisely
- Business knowledge of operations and supply-chain with exposure to working with suppliers
- Adaptable & flexible in approach with demonstrated ability to adjust to multiple demands
- Influencing skills with regard to business working relationships along with the ability to professionally assert ideas and opinions successfully
- High level of integrity and ethics
- Ability to travel and work domestically (China) and internationally
- Proficient in quality analysis tools - 8D, SPC, PFMEA
- Strong problem solving skills with the ability to teach basic problem solving techniques and/or facilitate problem solving at supplier locations
- Experience in developing part and product certification processes & vendor quality measures
- Strong knowledge of finished-goods-based quality control methods, tools & techniques
- Proficient in the utilization of MS Office specifically Word, Excel, and Powerpoint
- Working knowledge of ERP systems; experience with SAP strongly preferred
- Willingness and capability to learn new software
8
Product Quality Manager Resume Examples & Samples
- Acts as a voice of the Business and Product Quality to ensure the necessary quality measures for the products are identified, noted and done with respect to all requirements
- In the case of deviations, make sure appropriate corrective actions are taken and documented
- Acts as a voice of the customer
- In the case of deviations, make sure appropriate corrective actions are taken
- Disciplinarily independent of the project manager as an independent assessor of project status and risk
- Audit, review and improve manufacturing quality control programs
- Regular manufacturing plant visits
- Drive defect containment and assure problem resolution in a timely manner for component or material quality issues impacting production lines and external customers
- Drive and monitor APQP process with customer and report trends
- Interact with all internal departments (engineering, program management, operations, purchasing, manufacturing) and be accountable for results
- Review supplier design engineering, manufacturing, purchasing, and quality documentation, which may include 8D’s, for compliance to Continental and customer requirements
- Main emphasis of the position is quality assurance and improvement activities supporting new product launch design and manufacturing teams
- Lead multidisciplined teams in Problem Solving to address quality issues and concerns to meet the satisfaction of Continental and customer representatives
- Postlaunch activities for support of design changes and in resolution of design issues which impact customer satisfaction
- Bachelor's Degree in Engineering or a technical equivalent discipline
- 5+ years of experience working in high volume electronics manufacturing environment; Automotive production process knowledge is a plus
- 3+ years experience working directly with customers and suppliers
- Strong facilitation skills and the ability to build positive working relationships within a variety of organizational departments
- Strong communication and presentation skills, both written and oral
- Developing and presenting formal presentations to senior leadership
- Microsoft Office and Mini-tab (or a comparable) skills
- 7+ years experience working in high volume electronics manufacturing environment; Automotive production process knowledge is a plus
- 5+ years experience working directly with customers and suppliers and facilitating
- Experienced with maintaining ISO standards and APQP process
- Black Belt or Green Belt Certification
9
Product Quality Manager Resume Examples & Samples
- Performs a variety of post contract award functions, e.g., prepares Quality Assurance Letters of Instruction (QALI); prepares QA Post Award Agenda and conducts QA Post Award Conference; reviews First Article Acceptance Test (FAAT) and Lot Acceptance Test (LAT) plans and reports, and recommends acceptance or rejection; review TDP for completeness and adequacy; performs liaison with the appropriate contract administration service, conducts on-site visits to ensure that uniform application of quality assurance requirements is maintained; investigates manufacturing field problems and resolves quality deficiency reports; performs root cause analysis; enforces QA contractual requirements; reviews quality assurance plans to domestic and/or international standards
- Performs audit and analysis functions to include conformance, product and process audits at government and commercial facilities; performs analysis of manufacturing and statistical process controls using empirical and statistical means; has a working knowledge of such tools as Taguchi Methods, Design of Experiment, Pareto Diagram, Ishikawa Diagram etc. Serves as a resource for supporting answers concerning audits and analysis
- Provides necessary QA support, policy, and guidance to munition programs, e.g., provides input to Configuration Control Board relative to ECPs, RFVs; reviews demil plans; provides support on environmental contracting issues; participates in Quality System Reviews, Should-Cost Teams, and Configuration Item Verification Reviews; maintains Contractor History File; when designated, serves as a Functional Manager for assigned munitions items; provides input to legal actions as required; participates as a voting member of various boards; provides inputs to briefings to various command levels and contractor personnel; provides staff support to various command taskings concerning QA issues/topics
- Bachelor’s Degree from accredited university and at least ten (10) years relevant experience, including three (3) years of at least one or some combination of quality management, lab management, quality engineering or leading continuous improvement initiatives
- Proficient in statistical analysis
- Ability to communicate, both written and verbally, with individuals at all levels in the organization
- Knowledge of the full range of principles, concepts, and methods as to procurement quality assurance for munitions and the production methods involved. Serves a technical resource for acquisition quality assurance
- Broad knowledge of practices, policies, and procedures of related organizations such as procurement, production, engineering, test activities, customers, and skill in effectively and diplomatically dealing with these organizations, contractor, and other Government agencies
- Knowledge of a wide range of methods, principles, and practices directly related to the quality of control/QA fields including such areas as statistical analysis, control and sampling; and quality data analysis and evaluation to determine contractor compliance with the many associated aspects of quality control
- Knowledge of audit protocols, procedures, and methods for conducting a wide-range of product and process, and system related audits
- Must favorably pass a National Agency Check with Local Agency and Credit Checks (NACLC), as well as obtain and maintain a DoD security clearance
10
Product Quality Manager Resume Examples & Samples
- Key Qualifications
- International experience, particularly in Asia is a plus
- 5+ years of experience in manufacturing and Quality Control
- Experience developing process quality plans, supplier quality audits, and driving corrective actions and failure analysis efforts
- Experience with the development and evaluation of measurement systems
- Knowledge of programming OMM, CMM, contour machine, interferometer, 3D scanning and other high precision equipment
- Disciplined in GD&T practices with close attention to datum establishment and tolerance analysis
11
Product Quality Manager Resume Examples & Samples
- Responsible for 0km / field return reporting and escalation of line and field issues within to BU Management
- Responsible to coordinate engineering and to setup "Task Force" teams with engineering to solve issues
- Responsible to develop risk assessments for deviations, documentation of decisions and approvals to risks
- Responsible to discuss re/qualification coverage in operations with customer
- Responsible to adjust customer returns process with customer in series (eg. Relocation, new customer)
- Responsible to perform Lessons Learned (over all plants)
- Support customer returns with 0km / field return reporting, analysis of customer claims and regular meetings with customer (for returns)
- Support plants with product specific approvals of lines and production equipment (MSA, GR&R, Control Plans, PFMEA’s), PPAP release; product release at series production line; product/process audit, Run at Rate, two-day production with customer, definition of rework processes and line relocation
- Approve customer and plant change management in series
- Ensure Quality in series and support product support team to achieve quality targets
- Develop and implement action plans to achieve assigned departmental goals
- Lead multi discipline teams in Problem Solving to address quality issues and concerns to meet the satisfaction of Continental and customer representatives
- Post launch activities for support of design changes and in resolution of design issues which impact customer satisfaction
- Domestic and International travel to manufacturing production sites, supplier and customer locations
- No visa sponsorship or relocation support will be provided for this role
- Bachelor’s of Science degree in Engineering
- 3+ years experience in a Quality focused role
- Must be experienced working directly with Customers
- Must have strong interpersonal skills and leadership to work in a team
12
Product Quality Manager Resume Examples & Samples
- Develop and continuously improve Oculus’ Quality Management System
- Chair periodic Quality Management Reviews consisting of Cost of Quality, Voice of Customer, Failure Analysis and Factory Quality data
- Implement lessons learned process
- Conduct quarterly business reviews (QBR) with key suppliers
- Supplier Quality Requirements Documentation
- Develop Product Quality Plan and ensure its execution with suppliers
- Partner with Engineering to define Product Acceptance & Validation plan based on PRD
- Execute Ok2Ship Process for new products
- Manage the Early Field Failures Analysis Process
- Develop Quality Metrics Dashboard and Analytics
- Support new product development builds at factory as required
- Bachelor degree in Mechanical, Manufacturing Engineering or equivalent
- 7+ years’ experience in high volume consumer electronics manufacturing
- Familiar with DOE, DFMEA, SPC, Sampling Plans
13
Product Quality Manager Resume Examples & Samples
- 0 to 3 years work experience
- Love of fast-pace environment : super energetic & pro-active personality
- Amazing interpersonal skills
- Great organisational skills, be very rigorous
- Data passionate & detail oriented
- Fluent in French & English required
- Salesforce knowledge is a plus
14
Product Quality Manager Resume Examples & Samples
- Assures compliance with established policies/procedures of the Division and Corporation and complies with all applicable governmental regulations (GMP, etc.), both domestic and foreign
- Supports the development and maintenance of a Quality Agreement with the external parties/partners. May provide input into the development of contractual agreements with the external manufacturers
- Reviews all audit outcomes pertaining to external manufacturers and ensures appropriate and timely corrective actions, where warranted
- Responsible for coordination, oversight, and communication on matters related to the GMP status of the external manufacturer. Must be conversant with applicable regulations and compendia (domestic and foreign) governing the external party/partner’s operations
- Closely collaborates with appropriate business/operations and technical areas to achieve the Company’s objectives
- Tracks and monitors operational and quality performance of the external party/partner
- Works with the external party/partner to ensure that effective and robust Quality systems and Quality management are in place
- Provides guidance to the partner on conducting investigations of batch rejection, atypical events, customer complaints, etc. where warranted
- Responsible for evaluation and/or release of products to other sites and/or to the market with the assurance that the goods were produced in conformance to all applicable policies/procedures of the Company and compliance with all governing regulations
- Minimum of 5 years of experience in pharmaceutical industry with a thorough knowledge of quality systems, regulatory requirements and GMP
- Must have strong knowledge of and broad experience in product Quality Assurance and Quality Control activities
- Must have strong demonstrated interpersonal, communication, negotiation, and persuasion skills
- Communicates easily in English both verbally and in writing
- Some level of contractual and financial awareness is required
15
Product Quality Manager Resume Examples & Samples
- Leading quality improvement initiatives
- Bachelor's degree from an accredited institution
- 5 years of experience in the Aerospace Industry
- Minimum of 5 years of Aero-Structure experience
16
Product Quality Manager Resume Examples & Samples
- Experience in metrology and standard manufacturing quality control practices
- Excellent written and verbal communication skills in English. Mandarin language skills are a plus but not required
- Experience in electro-mechanical products high volume manufacturing
17
Product Quality Manager Resume Examples & Samples
- Bachelor's degree in Biology, Food Science, Meat Science or related Field
- 5 years of Manufacturing or Quality Assurance experience; meat industry experience preferred
- Relevant training and/or certification in the following areas: HACCP, GMP, Food Microbiology, Internal Quality Auditing, Statistical Process Control, Regulatory Training, Food Protection Management, American Society for Quality-Certified Quality Auditor
- Demonstrated experience implementing quality management principles and concepts and troubleshooting gaps in existing systems
- Demonstrated experience using quality assurance tools to monitor, control, and predict manufacturing processes and product performance
18
Product Quality Manager Resume Examples & Samples
- Lead a team of specialist engineers and insight analysts to provide full support to the business across the spectrum of safety, reliability and customer satisfaction
- Assessment of reliability in market and the ability to manufacture products in control
- Assess and influence support strategy for products alongside Quality Service Lead to define serviceability of product design
- Provide insight to early stage design of all relevant information related to product quality including new product launch information and customer perception of quality
- Feedback all manufacturing and supplier quality issues to early stage design
- Ensure that all product claims critical to quality are controlled in production
- Working with the Product Quality Managers in UK to ensure affective handover of Quality management of projects as they transfer to SEA
- Define a campaign of Continuous Improvement , across multiple functions, to improve products for our customers
- Maintain and report Quality status of product range to the business
- Work with the wider Quality team in markets to support territory specific requirements, Product Specification requirements as well as market specific product insight
- Manage a team of product and manufacturing quality engineers
- Ability to lead and motivate others to achieve outstanding results
- Excellent Quality knowledge – PFMEA, Process Flows, Control Plans, 8D/CAPA, 6Sigma among others
- Technical and personal credibility to work effectively with cross functional teams and other business functions
- Good commercial awareness with pragmatic approach to technology development with a business focus
- Educated to degree level in engineering or quality
- Formal quality training - six sigma, ISO standards etc
19
Product Quality Manager Resume Examples & Samples
- Provides leadership and facilitates problem resolution, resource utilization, career counseling, coaching and mentoring of team members
- 3+ years of experience in the following
- Experience in leadership role
- Working knowledge of Control of Nonconforming Product activities and requirements
- Working knowledge of medical device regulations (including FDA QSRs, ISO13485)
- Experience in personnel management
- Experience with other QA Operations disciplines including: equipment controls (CAL/PM), Receiving and Final Inspection and Process Validation
- Ability to influence positive change effectively
- Demonstrated experience developing and creating strong functional teams with robust talent pipeline
- Quality-Focused, Attentive to Detail and Results-Oriented
- Experience with development and implementation of quality system procedures
20
NPI Product Quality Manager Resume Examples & Samples
- Successful candidates will have the following attributes: a drive to innovate and influence, ability to learn and adapt to cutting edge technology
- Exceptional ability to build relationships; clear, consistent communication; data-driven and results-oriented; enthusiastic and motivated
- Industry experience in one or more of the following disciplines: New Product Introduction / Design Engineering / Manufacturing Operations
- Experience working with manufacturing facilities
- Direct experience managing a functional teams and/or projects (ME, EE, TE, DFX or other)
21
Product Quality Manager Resume Examples & Samples
- Successful candidates will have the following attributes: exceptional ability to build relationships; clear, consistent communication; data-driven and results-oriented; enthusiastic and motivated
- 5+ years of industry experience in one or more of the following disciplines: Product Quality / Service Quality / Manufacturing Operations / Design Engineering
- Experience or knowledge in test engineering, reliability engineering and supplier quality engineering; A plus with experience working with high volume production and traveling to manufacturing sites
- Direct experience managing a functional engineering teams (ME, EE, TE, DFX or other)
- Ability to travel internationally and domestically about 20%
22
Product Quality Manager / Technical PM Resume Examples & Samples
- Work with suppliers and internal teams to build, communicate and maintain development plans, schedules and milestones that are aligned with overall project goals while enabling the highest levels of quality and reliability to be built into the product
- Identify project risks and drive mitigation plans, prioritizing activities and influencing internal teams and vendors
- Develop Program level quality plan congruent with business needs
- Be the voice of the customer. Establish product quality and CSAT metrics and goals, and develop monitoring and reaction protocols. Influence design based on DFx, past product learnings, design risk assessment. Influence manufacturing process and design based on PFMEA & lessons learned
- Develop robust quality gates to ensure quality problems are not passed on and are detected early
- Build in quality into production processes via specs and controls
- Own OK2SHIP activity and drive CTQ, xFMEA, or other risk based design feedback and mitigation
- Use field data to drive quality improvements through cross functional quality improvement forum and convert product weaknesses and CSAT detractors into lessons learned feedback. Own Mountain View based failed device FA program
- Support development of system architecture that enable quality operations. Establishing dogfood program on NTF field returns EUT/OBA and customer experience quality gate development
- Coordinate cross-functional activities in the module/component supply chain for Technical Operations readiness in all New Product Introduction (NPI) phases leading into Mass Production. Highlight gaps and work out most efficient solutions under given circumstances
- Manage Phase Gate Process and partner with internal and external development teams to meet defined milestones leading to successful launch
- Identify stakeholders and coordinate Ship decisions for development builds. Anticipate problems and formulate solutions so as not to impede progress of the project
- Own development schedules working directly with vendors, SDEs and internal teams on complex process technologies to ensure alignment with overall project schedules and timelines. Drive reviews with vendors and module teams to monitor progress against development plans
- Manage communications and executive reviews on manufacturing process and supply chain readiness status/progress for all development builds and ramp
- BS in Engineering required
- 5 to 7 years of experience in Product Quality & Manufacturing/ Technical Program Management
- ICQ/OCQ required
- Experience working with OEM partners
- Proven experience in debug, troubleshooting, and failure analysis investigation
- Familiar with building and launching consumer electronics products
- Experience working with interdisciplinary teams in lean, fast-paced environments
- Flexible, organized, efficient, and process-oriented. Self-motivated and proactive team member
- A self starter with innovation, integrity and attention to details
- Organized and methodical with great verbal and written communication skills
23
Product Quality Manager Industrial Power Control Resume Examples & Samples
- Be a member of international project teams, assuring that the quality targets are met for the respective product and technology development projects
- Define qualification strategies according to product segment quality targets, application requirements and customer requests
- Manage the overall planning (timelines, resources, qualification samples), coordination and monitoring of qualification tests
- Ensure a proper documentation of customer/application specific requirements and qualification results
- Represent the Quality Managementfunction in respective product segments and participate in product quality related customer meetings
- Guide 8D teams (problem solving method) and FMEA meetings (risk assessment method). You will manage crisis in case of quality events, driving assessments, containment, corrective and preventive actions
- Ensure high customer satisfaction by supporting product related complaints and questions. You will work out appropriate corrective actions within the international network (frontend, backend, development, application) to avoid reoccurrence
24
Product Quality Manager Resume Examples & Samples
- Expert quality management, planning, and engineering skills
- Subject matter expert for all things quality including Quality Plans, FMEA’s, auditing, corrective and preventative actions, and sampling methodologies for IQC, assembly, and OQC
- Demonstrated capability with quality statistical techniques including SPC, sampling AQL’s, and measurement system analysis
- Working knowledge of advanced quality techniques such as design of experiments, correlation analysis, and reliability analysis
- Basic understanding of metrology and GDT
- Discriminating eye for demanding cosmetic categorization and supplier inspection
- Keen problem solving analytical skills capable of getting to root cause quickly in challenging environments and with tight deadlines
- Effective interpersonal and communication skills with the ability to manage and drive issues to closure in a global organization and in a global supply base
- High volume manufacturing experience with a detailed understanding of production processes, testing, kitting, and packaging (e.g., consumer electronics, automotive, medical devices, etc.)
- Supplier management experience; Asia suppliers is a plus
- Detail oriented with excellent written and verbal communication skills; Mandarin is a plus