Supply Chain / Manufacturing Resume Samples
4.8
(120 votes) for
Supply Chain / Manufacturing Resume Samples
The Guide To Resume Tailoring
Guide the recruiter to the conclusion that you are the best candidate for the supply chain / manufacturing job. It’s actually very simple. Tailor your resume by picking relevant responsibilities from the examples below and then add your accomplishments. This way, you can position yourself in the best way to get hired.
Craft your perfect resume by picking job responsibilities written by professional recruiters
Pick from the thousands of curated job responsibilities used by the leading companies
Tailor your resume & cover letter with wording that best fits for each job you apply
Resume Builder
Create a Resume in Minutes with Professional Resume Templates
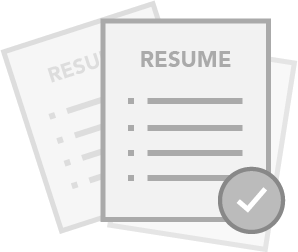
CHOOSE THE BEST TEMPLATE
- Choose from 15 Leading Templates. No need to think about design details.
USE PRE-WRITTEN BULLET POINTS
- Select from thousands of pre-written bullet points.
SAVE YOUR DOCUMENTS IN PDF FILES
- Instantly download in PDF format or share a custom link.
RM
R Marquardt
Reggie
Marquardt
811 Turcotte Run
Houston
TX
+1 (555) 623 2778
811 Turcotte Run
Houston
TX
Phone
p
+1 (555) 623 2778
Experience
Experience
Houston, TX
Supply Chain Manufacturing Co-op
Houston, TX
Connelly, Murazik and Bergstrom
Houston, TX
Supply Chain Manufacturing Co-op
- Work with in-house GDC toolmakers as well as vendors to develop prototypes for cadaver sessions and instruments for surgical evaluations
- Deliver end of semester presentations to showcase work to site management
- Assist with process improvements and mechanical design enhancements for our automation
- No immigration sponsorship provided for this role
- Participate and coordinate in process excellence (Lean, Six Sigma, etc.) improvement projects, Kaizen events, and other manufacturing initiatives
- Generate ideas & identify process improvement opportunities
- Create and update production records and equipment operating procedures
Phoenix, AZ
Supply Chain Manufacturing Test Engineer
Phoenix, AZ
Beatty, Wehner and Halvorson
Phoenix, AZ
Supply Chain Manufacturing Test Engineer
- Investigation, design, development and implementation of new manufacturing processes and technology for the introduction of new products. Liaise with Quality Assurance, Product Development, Manufacturing Engineering, Advanced Operations, Supply Chain, and others as necessary
- Develop procedures, methods and tools for automated test, verification and certification of the company’s products, validate testing activities and results of manufacturing equipment, participate in design verification of new equipment, and participate in preparing product compliance documentation
- Will assist external manufacturers in resolving manufacturing and quality issues in relation to: Audits findings, Problem-solving and resolution on relevant issues, Process validation, and Technical specifications
- Monitors product performance to optimize yields & margin to spec (GR&R, cpk) for products and major electrical-mechanical subassemblies
- Works with suppliers, test teams, & development engineers to resolve any issues
- Develops action plans to characterize & mitigate high risks due to new test techniques or product technologies
- Drives corrective actions between owners in supply chain, development, test teams, supplier quality teams, and suppliers
present
Boston, MA
Frito Lay Supply Chain Manufacturing Supervisor
Boston, MA
Davis and Sons
present
Boston, MA
Frito Lay Supply Chain Manufacturing Supervisor
present
- Manage the performance of direct reports through performance reviews, frequent discussions, coaching, and career development action plans
- Develop team to solve day-to-day operational issues and reach short- and long-term performance goals
- Communicate and collaborate cross-functionally to assist team to solve operational issues
- Optimize operational efficiencies to support the facility's production, packaging, warehousing, and shipping operations
- Directly oversees operational measures including but not limited to CIL/CL compliance, minor stop loss, SRC completion
- Flex production plans on a shift by shift basis, managing through issues to prevent service issues and operational inefficiencies
- Deliver effective change leadership - driving business changes while minimizing people impact
Education
Education
Bachelor’s Degree in Industrial
Bachelor’s Degree in Industrial
Hofstra University
Bachelor’s Degree in Industrial
Skills
Skills
- The ideal candidate will be a highly motivated team player with the ability to work with minimal supervision
- Quality improvement methods (pareto, root cause analysis, FMEA, 8D/DMAIC, etc), including leading a team quality improvement effort
- Excellent analytical skills .Excellent interpersonal communications skills
- Solid knowledge in electronics; analog, rf, optical, power and digital
- Working knowledge of computer systems, working knowledge of statistical methods and process capability, Minitab, ability to apply statistical tools – cpk, GR&R, tests for differences, DOE
- Knowledge of Quality Control principles and methodology is an asset
- Extremely proficient in the use of LabVIEW
- Good Communication and interpersonal skills
- Ability to operate in a fast paced environment, sometimes requiring extended work hours
- Strong background in automating test equipment using software tools
15 Supply Chain / Manufacturing resume templates
Read our complete resume writing guides
1
Supply Chain / Manufacturing Resume Examples & Samples
- Meeting with clients and conducting management consulting projects based on client needs
- All engagements require process analysis, project management skills and the ability to work in collaborative teams
- Facilitating user workshops to gather and document business needs, requirements and weaknesses and challenges
- Assisting business users, project managers and IT leadership in optimizing the scope, benefits and risks of proposed projects
- Conduct benchmarking research and analysis for IT spending, trends and industry practices
- Provide leadership in working with solution vendors
- Preparing reports on consulting services performed for clients, delivering reports where appropriate and discussing results and recommendations with clients
- Working with clients to provide analysis, development and documentation of improvement opportunities; this may include implementation and training components
- Completing client projects effectively and efficiently and maintaining a high level of proficiency
- Traveling to client locations as required
- Bachelor’s degree in MIS, IT or Computer Science from accredited university
- Minimum of 3-6 years of previous experience delivering Information Technology Integration, Outsourcing, and/or Management Consulting Services
- Minimum 2 years’ experience working in a large organization, professional services firm or CPA firm
- Must have experience delivering IT consulting services/solutions many of which encompass strategy, people, process, technology and infrastructure components. Prior solution selling training is a plus
- Verbal and written communication skills, ability to create effective requirements documents and review them with key project stakeholders at multiple levels of the organization
- Basic understanding of IT application lifecycle and methods
- Experience with any or all of the following highly desirable: ERP, CRM, financial reporting, portal, accounting systems
- A proven track record of successful project delivery within F5000 companies or a similar resume in the SMB space working with CXO/Owner
- Ability to travel up to 25-30% locally and in around Chicago and the surrounding states/Great Lakes region
- Functional understanding of IT operations and functions
- Additional major or minor in Accounting is a plus
- Ability to analyze details and summarize significant amounts of data
- Ability to articulate, write and present information in a clear and understandable manner
- Strong computer skills, including MS Office
- Eagerness to contribute in a team-oriented work group
- Motivated to work in a fast-paced environment
- Strong ability to build and manage client relationships
- Natural aptitude for solving problems
- Self-starter who can work independently with minimal supervision
- Driven to exceed client expectations
- Desire to learn and grow
2
Supply Chain Manufacturing Co-op Resume Examples & Samples
- Drive daily manufacturing operations to deliver targeted safety, quality, production, and cost results
- Develop capital approval requests and ensure assigned projects are completed on-time and within budget
- Gain knowledge in project planning, project management, managing external resources, and equipment reliability
- Implement best practices
- Pursuing a Bachelor’s degree in Industrial or Manufacturing Engineering, Chemical Engineering, Mechanical Engineering, or related major with an anticipated graduation date on or before December 2017-December 2018
- No immigration sponsorship provided for this role
- Ability to work as a member of a team
- Extensive PC spreadsheet skills
3
Supply Chain Manufacturing Engineer The Netherlands Resume Examples & Samples
- Designs, monitors and supports on-site processes ranging from inbound, outbound, storage and returns, partnering closely with management, quality representatives and 3rd party logistics providers
- Will act as document owner for all operation related Standard Operation Procedures (SOP)
- Coordinates SOP updates and subsequent 3rd party work instructions as part of general maintenance, or in support of operational changes using Ignite
- Will perform operator training where required and monitors effectiveness
- Develops & executes procedure optimization initiatives
- Prepares, evaluates and executes validation protocols
- Manages the carrier management system`s routing guides to ensure optimal performance of system and in an effort to meet customer`s shipping requirements
- Manages the JD Edwards Enterprise Resource Planning system (ERP) receiving routers
- Manage log-in requests to Edwards systems for 3rd party operators
- Will act as the primary contact for questions around labeling, IFU`s and packaging
- Supports the introduction of new products or product modifications by identifying and driving changes required to allow operational execution
- Monitors the quality, cost and efficiency of the movement and storage of goods as per pre-established KPIs
- Works with available data to monitor performance in the areas of cost, quality and customer satisfaction and plans improvements
- Actively identifies operational improvement opportunities, highlights them and drives the change
- Supports internal as well as external audits by providing on-site support ensuring the latest requirements are embedded in the operational design
- Ensure continuity of business and acts as a first respondent in case of adverse events
- Follows up on failed shipments, corrects and subsequently develops plans for sustainable improvement
- Prepares insurance claims towards 3rd parties and/or internal corporate insurance to claim for losses
- Verification of freight invoices and first line approval
- Supports tender preparation and subsequent analysis of responses to support decisions
- Support the development of contracts and ensure execution in line with agreed SLA
- Affinity – with complex operational processes, labeling, packaging, bundling
- Attention to Detail – working precisely to ensure quality standards are met
- Solid analytical and statistical skills
- Good Relationship Management – Ability to work in good cooperation with other functional groups and 3rd party representatives
- Strong communication skills both oral and written
- Ability to successfully work to meet tight deadlines under pressure
- Judgment and Decision Making — Considering the relative costs and benefits of potential actions to choose the most appropriate one
- Creative Thinking — Able to provide suggestions and solutions to facilitate complex problem solving
- Good Time Management — managing one’s own time and the time of others efficiently
- Knowledge of Edwards’ products and company is an asset
- Experience in transportation, logistics, operations, or related activities are a must
- A bachelor's degree in engineering
- Any incremental degree in logistics/operations a plus
- Good organization, communication and detail orientation skills required. Must be able to successfully manage multiple priorities in a fast paced team-oriented environment and think independently and creatively in developing and proposing logistical solutions
- Strong problem solving skills essential
- Must be proficient with Excel and Word
- Familiarity with JD Edwards ERP, RLRP, Ignite & Trax is a plus
- Fluent in English – Any other spoken language being an asset, Dutch being a plus
4
Supply Chain Manufacturing Co-op Resume Examples & Samples
- Assist with process improvements and mechanical design enhancements for our automation
- Component design using SOLIDWORKS
- Preparation of manufacturing documents and specifications
- Assist with 6 sigma Black Belt and LEAN projects
- Mechanical Engineers and Industrial Engineers preferred. BioEngineering, Chemical Engineering and Electrical Engineering majors will also be considered
- Brainstorm instrument design concepts with GDC teammates and internal NPD teams
- Perform design reviews and provide design for manufacturability and instrument cost feedback to NPD teams
- Work with in-house GDC toolmakers as well as vendors to develop prototypes for cadaver sessions and instruments for surgical evaluations
- Participate in internal cadaver sessions as needed
- Research current and emerging technologies to identify potential lower cost manufacturing processes, utilizing six sigma and lean methodologies and knowledge where applicable
- Identify and implement methods to effectively streamline and optimize our NPD process
- Actively participant in pre-production and regular meetings that purchasing holds with vendors, visiting suppliers’ facilities as needed
- Work closely with supplier quality and R&D on identifying and qualifying the vendors on critical to function and quality dimensions as well as performing process capability, COV, and GR&R studies
- Maintain compliance with all company policies in regards to all safety, QSR and environmental issues
- Drive design control activities for new product development efforts
- Conduct Process Verification and Validation activities with our internal manufacturing team as well as our external suppliers
- Support voice of the customer sessions with key surgeon customers by assessing device performance in a cadaveric lab setting
- Lead process/design failure mode effects and analysis and mitigation of keys risks identified
- Develop inspection methodology and acceptance criteria for inspection sample plans
- Provide leadership in all areas of the Quality System, including, but not limited to Corrective & Preventive Actions, Nonconforming Materials, Risk Management, etc
- A minimum GPA of 3.0 Cumulative is strongly preferred
- Candidate must be actively enrolled pursuing either a Bachelors or Master’s degree ( but not necessarily taking classes)
- Candidate must have reliable transportation to and from work on a daily basis for the duration of the co-op
5
ERP IT Solution Architect Supply Chain & Manufacturing Resume Examples & Samples
- Perform as IT Solution Architect on Oracle ERP R12 with GE Digital Multi-Modal ERP team and GE India Supply Chain and manufacturing teams driving common global standards in design and build
- Understand and translate business requirements and requisite processes to software and program requirements
- Work with build teams to deliver the solution
- Work independently with functional team members to validate the solution built
- Influence business and IT partners to leverage industry standard processes and out-of-the-box configuration capabilities in supply chain and finance modules of Oracle EBS R12 (and necessary bolt-ons) to satisfy business needs
- Collaborate with technical architects, developers and subject matter experts to establish the technical vision and analyze tradeoffs between usability and performance needs, keeping customer needs in mind
- Partner with site functional teams towards achieving the “Brilliant Factory” goals for the site
- Bachelor's Degree in Information Systems, Information Technology, Computer Science, Engineering or related discipline from an accredited college or university
- Minimum of 10 years of experience with current information technologies and software development life cycle
- Minimum of 8 years of Oracle ERP hands-on application design and implementation experience
- Minimum of 5 years of design and implementation of solutions in supply chain and manufacturing modules of Oracle ERP
- Experience with ASCP and WMS modules
- Strong English verbal and written communication skills, and the ability to interact professionally with a diverse global group of executives, managers, and subject matter experts
- Strong ERP strategic and governance leadership skills, driving business transformation at enterprise level
- Strong facilitation and knowledge transfer skills
- Strong team player who works to make the entire team successful, regardless of reporting lines; not bound by strict role description
6
Supply Chain Manufacturing Co-op Resume Examples & Samples
- Gather and interpret process data to implement improvements in cycle time, yield, or quality
- Participate or conduct in troubleshooting efforts by analysis and correction of both chemical and mechanical operating problems to maintain or improve existing site operations
- Create and implement change control
- Create and update production records and equipment operating procedures
- Prepare and present oral and written reports, as needed, to technical and non-technical personnel
- Maintain process surveillance programs on issues such as process control, yields, cycle times, quality, and change over
- Participate in capital and engineering projects
- Participate and coordinate in process excellence (Lean, Six Sigma, etc.) improvement projects, Kaizen events, and other manufacturing initiatives
- Consult and interact with sales representatives, vendors, and contractors
- Learn and interact with different forms of equipment automation and plant control systems (PLC, BPCS, etc.)
- Deliver end of semester presentations to showcase work to site management
- Completion of at least freshman year of undergraduate academic program is required
- Availability to work a minimum of three alternating semester-long rotations is preferred (i.e. Spring 2017, Fall 2017, and Summer 2018)
7
Solutions Sales Consultant Supply Chain & Manufacturing Resume Examples & Samples
- Support sales cycles through effectively presenting Oracle's value proposition against client's current and future business requirements in the area of Supply Chain and manufacturing
- Present advanced product features and benefits, product / cloud strategy of Oracle’s Supply Chain and Manufacturing solutions
- Lead the account solutions planning in his area of expertise, to set the solutions positioning strategy at the customer
- Develop and manage reference sites through high quality technical, professional client relationships
- Represent Oracle and Supply Chain Solution in marketing/public events
- Demonstrate in-depth understanding of customers' industries and core business processes, and their technical and business requirements
- Use customer specific quantifiable reference points such as insight benchmarking, customer specific data, 3rd party studies, customer reference stories and personal experiences to strengthen the value proposition
- Build a strong business network and connects with customers and industry thought leaders to build knowledge and gather valuable insights for use during the sales cycle
- Leverage others' expertise, and share information, best practices and successes to achieve results
- Seek to maximise customer facing time, and opportunity work, and maintain a high weekly tempo of demonstrations and customer meetings
- Actively maintain in depth product knowledge and Supply Chain/ Manufacturing trends in the relevant industries
- Closely track competitor's product/solution offerings to be able to articulate Oracle advantages
- Solid understanding of Supply Chain and Manufacturing Processes and relevant industries
- Experience in Oracle’s Supply Chain or releated products of competitors
- Exprerience in cloud-based solutions is an advantage
- 10 years of experience in related area, as pre-sales, implementation consultant or end-user of Supply Chain Applications
- Confident in presenting to large audiences of up to 20 people and more informally with smaller groups of 2-3 and 1:1, with all levels up to C level
- Ability to use tools and modern demo techniques such as storytelling, whiteboarding, theatre, and multimedia to present Oracle solutions in a compelling, simple and memorable manner
- Excellent presentation & communication skills
- No barriers to Travel
8
Supply Chain Manufacturing Supervisor Resume Examples & Samples
- Develop team's ability to solve their own day-to-day operational issues
- Motivate Team Members to achieve plan goals
- Organize and facilitate work team meetings
- Ensure timely and effective team communication
9
Supply Chain Manufacturing Finance Manager Vina Vietnam Resume Examples & Samples
- Provide direct support and leadership to plant manager for all manufacturing financial information
- Lead factory transformation and growth by meeting the manufacturing target and operating budget
- Lead finance operations & planning
- Execute financial metrics for growing product volumes, provide forecasting and drive “say-do” financial results
- Track JIT operations in handling inventory & optimizing cash
- Optimize plant operating metrics (KPI’s) to include % Direct Labor, productivity, quality, inventory, cash, and environmental health and safety metrics
- Track Actual Manufacturing Hours vs. Plan, variance analysis and corrective action
- Lead site variable & base cost out financial productivity actions and drive financial accountability for cost
- Drive competitive Operating Cost per Hour (OCPH) to compete in global market
- Manage and track P&E investment/site expansion
- Develop leasing initiatives with GE Capital or other financial institutions for cash optimization
- Manage team of financial analysts supporting all financial activities for the operating team
- Work with Controller to oversee Balance Sheet and lead annual physical inventory
- Work with Controller to perform quarterly closing activities
- Support Integration activities
10
SAP Supply Chain & Manufacturing Functional Analyst Resume Examples & Samples
- Work directly with business stakeholders across business units to develop and support business processes and enable them in our SAP system
- Identify creative ways to efficiency and effectiveness by streamlining processes and systems (i.e. modification of responsibilities or consolidation of tasks, elimination of non-value-added processes, or complete re-engineering of processes and systems)
- Write business requirements and functional specifications that are clear and well understood
- Act as liaison between business and technical staff to find creative solutions to complex problems
- Develop and execute test plans and scripts that are traceable to documented requirements
- Participate in corporate change control processes
- Maintain documentation and updates; analyze lessons learned and share with the SAP CoE community
- Contribute to the development of an overall IS project delivery and support practice at Avigilon, ensuring work product is thorough and well-structured, and business needs are effectively and efficiently met
- Prior experience in a SC&M Support / Project role on multiple successful SAP implementations
- Expertise/strong working knowledge across the following SAP SC&M Modules ( MM,QM,PP,WM )
- Solid understanding of manufacturing/production processes
- Prior experience in a manufacturing environment is required
11
Supply Chain Manufacturing & Distribution Senior Analyst Resume Examples & Samples
- 5 years minimum experience in manufacturing, 3 years minimum experience in new product introductions, Electronic circuit knowledge a plus, Statistical process control . Material management experience typically obtained through APIC’s style training. Manufacturing, and product distribution, experience is needed. Candidate should be trained in manufacturing management( Bill of Material, MRP, Demand planning, and resource scheduling). Experience and understanding of forecasting and analytics. Inventory management and control experience. Understanding Order backlog key metrics and developing tools to find idleness and highlight improvement of delivery
- Manufacturing, distribution, and new product introduction experience is needed
- Experience in manufacturing management factories and Distribution Centers
- Experience and understanding of forecasting and analytics of the Supply Chain
- Inventory management and control experience -backlog key metrics and developing tools to improve delivery
- Computer aided Planning, material management and manufacturing
12
Product Specialist for Solution Build for Supply Chain & Manufacturing Resume Examples & Samples
- Bachelor`s Degree or above
- Good knowledge of Project Management
- Execution and result driven
- Continuous improvements mind-set
- Cross Team alignments
- Senior Management collaboration/communication
- Escalation Management experience
- Excellent presentation and networking skills
- Strong verbal and written communication skills with fluent English
- Cross-cultural sensitivity as part of the global team
- A strong team player
- Be customer centric: active problem analysis and providing solutions for customer messages
- Good performer, ability to deliver on time and ensure quality
13
Accountant, Supply Chain Manufacturing Resume Examples & Samples
- Active partnership with plant finance and operations in financial and analytical support of the month-end close process within the Thermal and Syrup Manufacturing Finance team
- Prepares account reconciliations, monthly operating reports, quarterly and year-end internal/external reporting packages, and government surveys
- Supply Chain Manufacturing Financial Routines & Process (50%) – Monthly financial close activities, including journal entries, account reconciliations, general ledger account analysis, balance sheet/P&L reviews, and financial statement preparation
- Centralized Reporting (20%) – Develop and maintain standardized reporting for actual/budget variance analysis of MV/CMV (manufacturing variances/controlled manufacturing variances) for weekly forecasting, rolling estimates, material usage, cost per case/cost per gallon, and other KPIs
- Annual Business Planning (10%) – Support the data collection and preparation of the business planning process with Impact ECS software, MFT, and SAP
- Strong understanding of GAAP and working knowledge of internal control principles
- Communication – Comfortable with communicating to varying levels of the organization
- Ability to work effectively as a team member
14
SAP Supply Chain Manufacturing Senior Manager Resume Examples & Samples
- 10 years of SAP ECC PP implementation experience
- Experience leading at least 3 full life-cycle implementations
- Project Management, SAP Manufacturing, SAP Plant Maintenance, SAP APO PPDS, and SAP MII experience
15
Supply Chain Manufacturing Analyst Resume Examples & Samples
- Provide strong data analytical skills to support the development of Global Supply Chain Metrics and Standards from source to shelf
- Designs and develops analytics to enable translation of findings into clear and compelling recommendations/solutions across the SC
- Ability to translate the complex into the simple and provide a source of business knowledge to ensure sounds analyses, specifically but not limited to Manufacturing
- Understand and have working knowledge of manufacturing programs. Collaborate with other K-C Supply Chain - Manufacturing Program teams to determine what connections might be made
- Actively participate in building and executing function capabilities, business strategies, objectives and plans. Shape, coordinate, and drive delivery of global projects/initiatives as required by function and BU leaders
- Helps build SC capabilities by delivering reports, building knowledge repositories, and driving innovation/creativity in our analytical toolkit to be shared broadly across the global organization
- Researches and leverages industry standard analysis tools, methodologies, and capabilities using case studies, templates, and software
- Becomes subject matter expert in areas assigned including inputs, processes and outputs, as well as tools and data (example: development of ATS metric through to automation)
- Demonstrate a commitment to quality performance through personal example by adopting a customer based approach to business support. Personally demonstrate KC’s leadership behaviors (build trust, make decisions, win consistently, think customer, continuously improve, and build talent)
- Bachelor of Business Degree in Supply Chain Management, Logistics, Engineering, Operations, or Strategy with equivalent experience
- 5-7 years of progressive work experience in business analysis/analytics within a function such as Supply Chain, Logistics, Finance, or Operations with a history of demonstrated business success with 3-5 years Practical operational experience in supply chain or related function
- Experience working with a manufacturing site is preferred
- Performing insightful business analysis, leading the use and integration of analytics and/or modeling for fact finding purposes
- Tenacious, innovative approach to resolving challenges
- Structured problem solving skills
- Strong project management experience – ability to deliver results against set expectations, timelines
- Capable of influencing senior level, peer groups and across organization
- Engaging and collaborative, working in a team environment
- Consumer goods experience not required but highly preferred
- Proficient in Microsoft Suite, project management, advanced Excel functionality, modeling, solvers
- Proficient in SAP and Tableau
16
Supply Chain & Manufacturing Operations Consultant Resume Examples & Samples
- Identifies operational and supply chain improvement opportunities and formulates solutions to be prioritized by leadership
- Represent the Product Supply organization on portfolio project teams with ownership of the roll-over process including ramp-up, ramp-down and initial deployment to all affected regions
- Lead multiple commercialization projects and cost reduction activities to ensure results are delivered within prescribed timelines and meet agreed upon scope commitments
- Maintain data integrity across all required systems relative to projects impacting the product portfolio
- Ensure optimal customer service performance and inventory management in accordance with Healthcare objectives throughout the project lifecycle
- Lead supply chain improvement initiatives by coordinating cross-functional implementation teams
- Support manufacturing sites to meet objectives in safety, cost, quality, productivity, and customer service
- Supports Material Creation in SAP, BOM's, material creation requests (RM, subs, trial)
- Manage supplier network to provide sufficient materials and services to meet highest short-range requirements, protect against temporary supply interruptions and provide for long-range growth needs. Develop and execute a plan to quickly and effectively manage any supply interruptions
- Interacts with business units to develop, engage and support supplier relationships for extracting the greatest value in cost, security of supply, risk management, sustainability and innovation
- Contribute to an environment in which all team members are respected regardless of their individual differences and are motivated to improve both their individual and team contributions to achieve desired business results
- Communicate fully with superiors, subordinates and others who have need to know in a way that is timely, complete, concise, candid, accurate, clear, and responsive
- Bachelor's degree in business, engineering, or related discipline
- 8 years experience in Manufacturing Ops and Supply Chain
- Demonstrated knowledge and experience in a supply chain processes and driving business results through influence and leadership
- Problem solving experience in reducing total costs, improving processes, and reducing supplier risk
- Experience with ERP system, Bill of Material (BOM) management, and material creation requests
17
SAP Supply Chain Manufacturing Senior Manager Resume Examples & Samples
- 10+ years of SAP ECC PP implementation experience
- SAP Plant Maintenance
- SAP APO PPDS
- SAP MII
18
SAP Supply Chain Manufacturing Consultant Resume Examples & Samples
- 3+ years of SAP ECC PP implementation experience
- At least 3 full life-cycle implementations
- Experience working with clients to solve business issues supported through technology
- Experience with Supply Chain Manufacturing execution processes as well as some of the following functions: Production Planning, Quality Management, Plant Maintenance, MES, IOT, EHS, and EWM for Manufacturing
- Experience defining requirements as well as solutions to the requirements
- Experience leading teams and building skills of others in the Supply Chain Manufacturing business processes
- Experience interacting with mid to senior level supply chain executives displaying knowledge, experience, and leading practice advice to identified issues
19
SAP Supply Chain Manufacturing Resume Examples & Samples
- Advise on best practice Supply Chain Manufacturing process design
- Design, architect, configure, implement a large scale, complex SAP enabled Supply Chain Manufacturing transformation solutions
- Participate in design authority forums to provide direction, advise on best practices and make design decisions
- Assurance that core elements of the Supply Chain Manufacturing functional design confirm to standards, best practices and design principles
- Managing the configuration of SAP to ensure it meets best practice design
- At least 5years of experience in SAP supply Chain Manufacturing Solutions
- Ability to understand the business requirements and manage the conversion of them into best practice Supply Chain Management designs, configuration / Functional – Specifications while maintaining the integrity of the overall application design
- Able to architect a Supply Chain Manufacturing solution covering the end to end integration of SAP with other applications and devices
- Strong problem solving skills to drive resolution of defects and issues by understanding client needs and presenting options to resolve the problem
- Fluent in spoken & written English and Spanish
- Proven ability to deliver high profile activities to tight timescales
- Strong stakeholder management skills
- An ability to identify, develop and implement solutions to gaps to meet the needs of the business
20
Supply Chain / Manufacturing Resume Examples & Samples
- * We are looking for individuals who have a manufacturing/automotive, supply chain background who can bring their expertise to our dynamic clients****
- Working with clients toprovide analysis, development and documentation of improvement opportunities; this may include implementation and training components
- Bachelor's degree in MIS, IT or Computer Science from accredited university
- Minimum 2 years' experience working in a large organization, professional services firm or CPA firm
21
Supply Chain Manufacturing Test Engineer Resume Examples & Samples
- Investigation, design, development and implementation of new manufacturing processes and technology for the introduction of new products. Liaise with Quality Assurance, Product Development, Manufacturing Engineering, Advanced Operations, Supply Chain, and others as necessary
- Design for Testability of PWB, PWA and Mechanical Assemblies, Pre and post build DFA / DFM reviews, Drive DFX issues from End of Build Reports
- Design for Testability - assure the detection of all faults in a circuit, reduce the cost and time associated with test development, reduce the execution time of testing
- Develop procedures, methods and tools for automated test, verification and certification of the company’s products, validate testing activities and results of manufacturing equipment, participate in design verification of new equipment, and participate in preparing product compliance documentation
- Develop procedures and tools for testing, calibration and verification of the equipment, cooperating with the developers, ensure the equipment is properly tested, calibrated and certified according to the corresponding procedures, participate in Root Cause Analysis when repetitive failure of company’s products occur, or failure under warranty; ensure accurate document, record and archive measurement data pertaining to product parameters and process control performance
- Assist and train the Test Technicians, when required, in troubleshooting and repairing returned products
- Monitors product performance to optimize yields & margin to spec (GR&R, cpk) for products and major electrical-mechanical subassemblies
- Works with suppliers, test teams, & development engineers to resolve any issues
- Develops action plans to characterize & mitigate high risks due to new test techniques or product technologies
- Either independently or by leading a problem-solving team, identifies and resolves quality, reliability, yield and cost problems
- Drives corrective actions between owners in supply chain, development, test teams, supplier quality teams, and suppliers
- Helps determine test requirements for new products & technologies and ensures those solutions are optimized for cost & quality
- Presents experiment results and proposals to development teams & mgmt
- Perform design reviews with development engineering for manufacturing and test
- Execute all administrative and regulatory requirements necessary for proper documentation and record keeping associated with new process/product introductions
- Compilation of Capital Expenditure requisitions for new process equipment as required
- Validation of new manufacturing equipment, tooling and fixtures
- Development automated test solutions for new products (LabVIEW, C++, etc.)
- Full support of product lines for manufacturing issues, Weekly Quality review of production yields, EOL support
- Handover of new processes from development to production. Ensure all appropriate engineering prints, work instructions and all other essential process related documentation is in place prior to production start
- Ensure the efficient and timely transfer of process knowledge from project personnel to manufacturing engineers and coordinate the training of production team members on new processes and equipment
- Ensure all appropriate documentation is in place prior to production start
- Will assist external manufacturers in resolving manufacturing and quality issues in relation to: Audits findings, Problem-solving and resolution on relevant issues, Process validation, and Technical specifications
- The ideal candidate will be a highly motivated team player with the ability to work with minimal supervision
- 5+ Years related Engineering experience in a manufacturing test environment
- Bachelor Engineering Degree (Mechanical Engineering, Manufacturing Engineering, or Electrical Engineering)
- Experience in testing electronic boards, modules and test equipment
- Solid knowledge in electronics; analog, rf, optical, power and digital
- Strong background in automating test equipment using software tools
- Extremely proficient in the use of LabVIEW
- Knowledge of Quality Control principles and methodology is an asset
- Good Communication and interpersonal skills
- Analytical reasoning and problem solving
- Working knowledge of computer systems, working knowledge of statistical methods and process capability, Minitab, ability to apply statistical tools – cpk, GR&R, tests for differences, DOE
- Working knowledge of Valor and Mentor is a plus
- Quality improvement methods (pareto, root cause analysis, FMEA, 8D/DMAIC, etc), including leading a team quality improvement effort
- Ability to operate in a fast paced environment, sometimes requiring extended work hours
- Must be able to plan, organize, and implement multiple concurrent tasks and projects
- Must be able to routinely make decisions which effect immediate operations and have the ability to read complex engineering drawings
- Must be able to generate, follow and explain detailed proposals and operating procedures (i.e. assembly instructions, inspection procedures, capital proposals)
- Must be able to analyze and correct complex product and/or process issues using independent judgment
- Excellent analytical skills .Excellent interpersonal communications skills
- Demonstrate mechanical and/or electrical problem solving skills. Good computer skills (word processing, spreadsheets, data base)
- Coaching/mentoring of less senior engineers (where applicable)
22
Frito Lay Supply Chain Manufacturing Supervisor Resume Examples & Samples
- Optimize operational efficiencies to support the facility's production, packaging, warehousing, and shipping operations
- Optimize ingredient and packaging material usage to minimize waste
- Ensure PepsiCo financial and accounting control procedures are followed to ensure accurate inventory records are maintained
- Flex production plans on a shift by shift basis, managing through issues to prevent service issues and operational inefficiencies
- Identify and coordinate operations improvements necessary to deliver the site annual operating plan (AOP). Ensure cost performance gaps are identified, action plans are developed, and resources are properly allocated
- Builds people capability through effective employee relations, hiring, training, and communication for front-line hourly personnel
- Manage the performance of direct reports through performance reviews, frequent discussions, coaching, and career development action plans
- Deliver effective change leadership - driving business changes while minimizing people impact
- Communicate and collaborate cross-functionally to assist team to solve operational issues
- Champion and lead an effective safety culture. Coach for safe behaviors and compliance with safety policies and procedures
- Coach teams to demonstrate continuous improvement in profitability margins, efficiencies, and cost savings initiatives
- Lead the implementation of the AM pillar
- Directly oversees operational measures including but not limited to efficiency, yield loss, product quality, inventory accuracy, transactional accuracy
- Directly oversees operational measures including but not limited to CIL/CL compliance, minor stop loss, SRC completion
- This role requires lifting up to 40 lbs. occasionally
- This role may operate forklift and manufacturing equipment occasionally
- This role may require some travel (less than 5%)
- Bachelor's degree or equivalent experience required. Preferably in engineering, business, operations management, or similar field
- Minimum of 2 years of experience in manufacturing preferred preferably food/beverage experience
- Must possess strong skills, knowledge and capability in lean manufacturing, finance and accounting, project management, human relations, effective communications, and statistics/logical problem solving
- Ability to give and receive constructive feedback
- Ability to lead a team-based approach to decision making