Quality System Engineer Resume Samples
4.6
(146 votes) for
Quality System Engineer Resume Samples
The Guide To Resume Tailoring
Guide the recruiter to the conclusion that you are the best candidate for the quality system engineer job. It’s actually very simple. Tailor your resume by picking relevant responsibilities from the examples below and then add your accomplishments. This way, you can position yourself in the best way to get hired.
Craft your perfect resume by picking job responsibilities written by professional recruiters
Pick from the thousands of curated job responsibilities used by the leading companies
Tailor your resume & cover letter with wording that best fits for each job you apply
Resume Builder
Create a Resume in Minutes with Professional Resume Templates
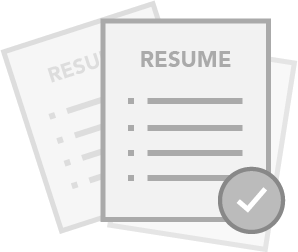
CHOOSE THE BEST TEMPLATE
- Choose from 15 Leading Templates. No need to think about design details.
USE PRE-WRITTEN BULLET POINTS
- Select from thousands of pre-written bullet points.
SAVE YOUR DOCUMENTS IN PDF FILES
- Instantly download in PDF format or share a custom link.
VB
V Braun
Verdie
Braun
841 Lindsey Field
Boston
MA
+1 (555) 958 4629
841 Lindsey Field
Boston
MA
Phone
p
+1 (555) 958 4629
Experience
Experience
Detroit, MI
Quality System Engineer
Detroit, MI
Becker-Swaniawski
Detroit, MI
Quality System Engineer
- Work with IT to understand and manage roles and workflow within change management system
- Performing process reviews and assists Operations engineers with process improvement or cost improvement projects
- Coordinating the quality management review, follow and validate the continuous improvement projects identified by management review
- Work closely with Facility Operations personnel in process development and process improvement
- Work with peers within Milford and across Waters’ sites to improve and harmonize change management processes
- Understand sales goals and assist manager in establishing and applying business plans
- Assist in preparation for management reviews, internal audits, and 3rd party audits
Detroit, MI
Senior Quality System Engineer
Detroit, MI
Rohan, Hudson and Lynch
Detroit, MI
Senior Quality System Engineer
- Act in the role of CAPA owner when assigned and lead teams through structured problems solving and other phases of the CAPA process
- Collaborate with internal groups to ensure quality standards are in place and improvements are implemented according to defined plans
- Coach CAPA Owners to ensure investigations are complete and documentation stands on its own during external review
- Support and/or facilitate recalls and field corrective actions according to corporate procedure
- Provide subject matter expertise, support and direction for the Milford CAPA and internal audit systems
- Interface directly with field service, technical support and sales personnel to ensure alignment of complaint data, warranty cost data and technical support calls with customers and service engineers
- Review PKI Customer Feedback and Complaint handling related procedures to ensure compliance with ISO 9001/13485 system and participate in internal/External ISO audit of the complaints handling processes
present
Houston, TX
Senior, Quality System Engineer
Houston, TX
Reilly-Mueller
present
Houston, TX
Senior, Quality System Engineer
present
- Provide support to Sr. Management. Schedule and chair Management Review meetings
- Works with individual departments to help them create process documentation that complies with the company’s standards
- Publish On-Time Performance to management team
- To advise the management team on the status of Schneider Electric’s Quality System and efforts that are being implemented to improve our Quality Systems
- Create a Procedure Documentation Standard Guide to describe how process documentation should be created in all departments
- Determine, document and maintain QA systems: QA Manual, QSPs, Work Instructions, forms
- Monitor, maintain and improve reporting customer metrics
Education
Education
Bachelor’s Degree in Engineering
Bachelor’s Degree in Engineering
Florida Atlantic University
Bachelor’s Degree in Engineering
Skills
Skills
- Excellent spoken and written English language ability, Italian language will be
- Skilled use of Pack Office software: Excel, world, PowerPoint (SAP knowledge will be a plus)
- Apply business unit marketing policies, procedures and plans, and proactively report all new or unusual pertinent market conditions to supervisor as well as product performance information
- To be responsible and ability to work in team
- Familiar with mass production process and able to conducts internal audits inside organization
- Ability to travels
- Achieve sales objectives as set by management for the specific products in the assigned territory; Manage sales territory with general supervision and assistance
- A strong coordination and communication skills internal and external, ability to deal with quality issues adhere to the principle of strong sense of responsibility
- More than 5-year experience in quality function or project management, especially in mass production (automotive industry or others)
- Provide quality process and method related trainings
15 Quality System Engineer resume templates
Read our complete resume writing guides
1
Vmware Quality System Engineer Resume Examples & Samples
- Determine a standard set of metrics and a tracking and reporting process for metrics and impact around activities
- Drive continuous improvement efforts in quality determined through detailed data analysis (of bugs, SRs, escalations, Customer surveys, etc)
- Report on data in an effective and meaningful way for different stakeholders as required
- Effectively influence teams to do the right thing for quality products though the use of data
2
Quality System Engineer Resume Examples & Samples
- Experience with ISO 9001 quality management system establishing and auditing
- Experience in maintaining a document control system
- Experience in assisting to create a new document control system would be beneficial
- Bachelor's from four-year College or university
- Manufacturing industry experience strongly desired
- Experience instructing in a quality educational program
- Strong PC skills ( Microsoft Office)
- Problem solving skills and attention to details
- Ability to be flexible and manage changing priorities
3
Quality System Engineer, Shanghai Resume Examples & Samples
- Job Summary
- Responsible for workshop production arrangement and people management
- Lead team to meet yield target, comply with quality standard and make production records
- Be familiar with the production process and equipment operation and solve general issues
- Cooperate with engineer for improvement to implement safe production and cost reduction
- Provide training to operators and conduct evaluation
- Perform any other duties as assigned by the supervisor
- Technical school or equivalent degree with major in engineering or other related disciplines
- 2+ years related working experience in production operation and management
- Good communication and leadership skills
- Initiative, good team player
- Willing to take shifts
- Basic English communication skill in written and good PC skills
- Possess working experience is foreign invested company is preferred
4
Quality System Engineer Resume Examples & Samples
- Bachelor’s degree in engineering or equivalent specialized experience
- 3+ years experience with Quality Assurance programs in a corporate environment preferred
- Bilingual English/ Spanish
- Additional education/training in Quality Assurance, management, statistics, and program management is desired
- Must excel at working in a team environment
- Ability to communicate detailed, technical initiatives to non-technical people
- ISO 9000 Internal Auditor Certification
- Understanding of problem solving methods (Six Sigma, 8D, root cause analysis)
- Strong communication, presentation, interpersonal, and organizational skills
- Ability to conceptualize, analyze, plan and organize projects
- Reasoning skills for problem identification and resolution
- Knowledge and ability to understand and apply process audit principles (ISO/ASQ)
- Experience in quality control program operations, to include standards
- Ability to apply quality control theories and principles to an operational environment
- Computer literate; able to utilize MS Office Suite
- Database experience beneficial
5
Quality System Engineer Resume Examples & Samples
- Achieve sales objectives as set by management for the specific products in the assigned territory; Manage sales territory with general supervision and assistance
- Understand sales goals and assist manager in establishing and applying business plans
- Apply business unit marketing policies, procedures and plans, and proactively report all new or unusual pertinent market conditions to supervisor as well as product performance information
- Maintain sales channels in the assigned territory and develop new channels independently
- Represent business unit products and services to customers and prospect and provide appropriate sales support services to customers and distributors
- Handel simple or moderate complaint independently and request instruction and assistance from superior in handling situations which require either greater or different experience or knowledge
- Bachelor’s degree or above
- 5+ years related working experience as sales engineer or business development in multinational company in related industry
- Solid knowledge of customer segments and their needs in the related market
- Advanced communication skills, influencing skills and selling skills
- Good time and territory management skill
- Fair English communication skill both in written and oral
- Fair PC skills
- Rich experience in new client development is preferred
6
Quality System Engineer Resume Examples & Samples
- The Quality Engineer shall support the quality assurance and various operations departments in the development, implementation and maintenance of the quality system at the Olive Branch, MS Facility
- The Quality Engineer will be primarily responsible for maintaining the facility CAPA program and ensuring that the CAPA program is adequate/suitable for detecting potential quality issues, determining the root cause of those issues and in cooperation with facility operations planning/implementing actions to drive improvement
- Scheduling and hosting regular reviews of quality data including but not limited to; quarterly reviews to upper management, monthly reviews to site management and weekly reviews to quality management with responsibility for the facility
- Writing document changes and modifying procedures in accordance with document change control procedures
- Assisting in root cause analysis/determination and action plan implementation for CAPAs
- Acquiring and analyzing data using appropriate standard quantitative and statistical methods across a spectrum of business environments to facilitate process analysis and improvements
- Lead/Participate in systematic problem solving team meetings and helping to analyze data trends for potential problems/improvement opportunities
- Leads/Supports ongoing facility lean/continuous improvement projects
- Performing process reviews and assists Operations engineers with process improvement or cost improvement projects
- Completing work while always in compliance with FDA Regulations outlined in 21 CFR 820 and ISO 13485, along with other applicable medical device standards / regulations and within safety guidelines
- Work closely with Facility Operations personnel in process development and process improvement
- Perform other related duties as directed by the Quality Assurance Manager
- Bachelor's degree in engineering or equivalent specialized experience
- 3+ years' experience within medical device / FDA regulated industry preferred
- Manufacturing or distribution experience preferred
- Familiar with cGMP and medical device manufacturing/distribution experience preferred
- Eagerness to learn and accept challenges and adaptable to change
- Ability to handle multiple projects and responsibilities
- Ability to solve problems and analyze data
- Ability to think and work independently but also work well in teams
- ASQ CQA and/or CQE
- Proficient in Microsoft Office including Word & Excel required
- Experience using various statistical tools and/or statistical analysis software packages preferred
7
Geoint Product Quality System Engineer Resume Examples & Samples
- Active TS/SCI clearance; with an ability to obtain a Poly
- Bachelors Degree and 10 years relevant experience. Relevant work experience can be substituted in lieu of educational requirements
- Relevant experience in the planning, execution, and operation of national technical means
- Knowledge of intelligence requirements from the IC, DOD and allied partners
8
Geoint Product Quality System Engineer Resume Examples & Samples
- Active TS/SCI clearance; with ability to obtain a Poly
- Bachelors Degree and 10 years relevant experience. Relevant work experience can be substituted
- In lieu of educational requirements
9
Global Quality System Engineer Resume Examples & Samples
- Execute systems to report on delinquencies or shortcomings in either the Audits or the Corrective Actions that might be required
- Conduct meetings and document results of those meeting with various groups of employees, including managers, as they carry out their responsibilities for BPMS improvement(s)
- Assist in the development of meeting plans for Top Management Reviews
- As requested, carry out defined action items from Top Management Reviews
- Act as Audit guide for ISO audits, agency audits(UL), customer audits, and any required quality system audit
- Manage the development of modules and reports in Q-Pulse and organize training where needed
- Exposure and experience with APQP methodology
- Must be broadly familiar with the ISO 9001 and be able to articulate and explain elements so that others in the organization can act on the requirements
- Must be well organized to efficiently maintain meeting plans, documentation and records, and electronic filing media. Must have verbal and writing skills that are well developed
- Must be able to interact effectively with various functions and all levels of the organization to carry out the BPMS annual plans
- Must be able to analyze data looking for cross-region improvement opportunities and best practices
10
Quality System Engineer Resume Examples & Samples
- Define and maintain the Quality Management System procedures to ensure compliance to Philips Policies, ISO 9001, ISO 13485, 21 CFR 803, 806 and 820, Canadian Food, Drugs, and Medical Devices Regulations (CMDR)and EU Medical Device Regulations
- Maintains, enforces, and manages a compliant and effective QMS for the activities in scope, as well as for effective and lean QMS structures and documents for Q&R processes at all levels
- Manage PQMS related deployments and implementations
- Ensures proper audit planning and schedule meets the requirements of internal policies and external regulations
- Establishes and executes a transition plan for all QMS related activities in scope while maintaining compliance and effectiveness throughout the duration of the transition to the PQMS
- Leads/participates in the maintenance of the quality documents until such time as they are determined to be no longer applicable as part of the PQMS transition
- Ensures the addition and management of any local QMS documents in line with the evolution of the PQMS
- Maintains, enforces, and manages a compliant and effective CAPA Process for the activities in scope, as well as for effective and lean structures and documents for Q&R processes at all levels including CAPA compliance to regulations and standards ensured through proactive support and facilitation of the CAPA activities with individual CAPA owners
- Leads/participates in the maintenance of the CAPA documents and matrices for tracking trending and reporting
- Ensures the addition and management of any local QMS documents in line with the evolution of the CAPA
11
Senior Quality System Engineer Resume Examples & Samples
- Develop and improve customer complaints handling system at business unit and site levels to facilitate rapid identification, resolution and feedback loops of all customer and field issues in order to meet customer and product quality objectives
- Ensure the adequacy of Quality Management System procedures to support the complaint handling program; this will include working closely with the field service, customer care and technical support organizations to ensure that field and customer data is entered promptly and accurately into the complaints handling system
- Work with divisional IT and service organizations towards collecting and analyzing data from various databases, trend the data and identify key opportunities for improvement
- Generate and evaluate customer complaint related metrics, establish appropriate baselines and demonstrate continuous improvement results; support business unit objectives through reduction of complaints and improving first time right performance
- Interface directly with field service, technical support and sales personnel to ensure alignment of complaint data, warranty cost data and technical support calls with customers and service engineers
- Support global review of complaints and service costs and service metrics; lead the review by a cross functional team, prioritization and appropriate escalation to corrective and preventive action requests (CAPA)
- Apply statistical techniques, risk assessments, causal analysis, as needed
- Act in the role of CAPA owner when assigned and lead teams through structured problems solving and other phases of the CAPA process
- Support and/or facilitate recalls and field corrective actions according to corporate procedure
- Conduct necessary training to ensure that the customer complaints databases are being utilized and populated appropriately
- Review PKI Customer Feedback and Complaint handling related procedures to ensure compliance with ISO 9001/13485 system and participate in internal/External ISO audit of the complaints handling processes
12
Quality System Engineer Resume Examples & Samples
- RESPONSIBILITIES
- Responsible for DNV audit coordination
- Responsible for customer QMS audit coordination
- Internal audit coordination and builds up and trains internal auditor team
- In charge of DCC management
- Quality system structure review, interface with global for any procedure definition and improvement activity
- Scorecard monitoring
- Define and implement procedure together with related engineering function to make sure that it is consistent with quality system
- Facilitate management review to make sure top level management has the thorough understanding of each engineering function procedure compliance status and offer necessary support for their continuous improvement
13
Quality System Engineer Resume Examples & Samples
- Drive the implementation of management systems at the site level
- Lead the creation, maintenance, and distribution of documentation according to the requirements of the Quality Manual, Quality Management Systems, ISO 9001/TS16949/ ISO 14001 and other related standards
- Facilitate the implementation, review, and training of Quality System documentation and the related processes
- Maintain and control Quality Business System records, applicable regulatory documents, and documents of external origin
- Process and monitor corrective actions, Internal Audits (customer and internal) for resolution and effectiveness
- Plan, manage and conduct internal audits and serve as a Lead or Internal Quality Systems Auditor
- Train Internal Auditors
- Provide ongoing support for the effective implementation and improvement of the Quality Business System
- Optimize and maintain Quality Business System documentation of preventive action activities
- Assist in preparation for management reviews, internal audits, and 3rd party audits
- Ensures business systems are using best practice approaches and are adding value to the site (not just creating paperwork…)
- Adheres to quality and safety systems or maintenance of quality and safety standards
- Bachelor’s degree in engineering or related field
- 5+ years quality engineering experience in a manufacturing environment
- Good knowledge of quality concept and tools such as APQP, SPC, FMEA, etc
- Five years experience with quality/business management systems including creating and maintaining documentation according to the ISO 9001/TS16949 standards
14
Quality System Engineer Steel Piston Resume Examples & Samples
- Familiar with the global and local OEM quality management system requirements and trender,also be able to conduct to establish and pratical implementation of the QMS in plant
- Written and oral English skill
- Good team work spirit, good coordinate and implementation ability also can work under pressure
- Be responsible,self-driven and target oriented
15
Quality System Engineer Resume Examples & Samples
- Maintain the system ,beside TS16949、ISO14001 and OHSAS18001. compile the related quality documents, guide other departments to compile the system document
- Track the corrective and preventive measures , validation work, ensure the system running smoothly
- Guide the document-control
- Organize the internal and external audit, push the management review
- Bachelor's degree in engineering with a specialisation in quality
- Minimum 3 years experience as an quality system engineer in an industrial environment
- Results oriented with strong written and oral communications skills
- Ability to work in a matrixed organisation
- International mind set, overseas experience a plus
- Minimum bi-lingual (English required)
16
Quality System Engineer Resume Examples & Samples
- Provide technical support and leadership within the Quality Assurance and Quality Systems organization to support the Quality Policy and Quality System
- Act as a technical resource within the facility for review, approval and resolution of non-conformities within the facility
- Site champion for elements of the Quality System such as Management Review, Audit Readiness, Readiness Review and Other Quality Assurance projects
- Review and approve CRs, PCAF, DCAF, for changes to existing and new processes from a quality perspective
- Revise standard operating procedures, performs investigation of Drug material through review of customer processing records and licenses data base in SAP
- Responsible for supporting the site Drug Pedigree program, maintain State Level Licensing for all states that require license to distribution prescription medical device or Prescription Drugs
- Ensure site is Verified Accredited wholesale distributor (VAWD) compliance and maintain on going relation with VAWD and have site ready bi-annually for VAWD audit
- Lead and manage projects associated with site quality initiatives to assure that the distribution center’s interests are accurately and objectively represented from a quality perspective
- Lead functional teams in developing solutions for quality related issues and seeking new opportunities for continuous improvement. Serve as Quality Assurance representation on project teams by providing guidance for maintaining compliance to regulatory and corporate requirements
- Lead and/or support continuous improvement projects, CAPA and LEAN initiatives
- Implement use of quality assurance tools both internally and externally with the goal of improving control or addressing gaps to manufacturing and distribution processes and to eliminate non-value added activities
- Performs other duties as required, including VIP
- Root cause analysis, and cause and effect analysis
- BS in an engineering discipline with 2-4 years of technical experience/Medical device or Pharmaceutical experience preferred
- ASQ CQE certification is a plus
- Certified Green or Black Belt is a plus
- Working knowledge of FDA QSR (21 CFR Part 820), ISO 13485, MDD/AIMDD, CMDR, JPAL medical device regulations; Ability to understand other medical device regulations and standards
- Experience in nonconforming material and CAPA methodologies/systems preferred
- Strong communication, presentation, facilitation, and project management skills
- Proficiency with Microsoft Office suite
- Applies continuous improvement principles in development of the quality system
- Driven, energetic, self-assured professional with high personal integrity
- Ability to develop effective, positive interpersonal relationship
17
Quality System Engineer Resume Examples & Samples
- Monitoring and maintain the ISO9001 and IATF16949 system running, ensuring the suitability adequacy and effectiveness of system documentation, organizing related departments discussion and take action if the actual process not consistent with the standard
- Internal audit (quality system, process and product) planning, implementation and reporting, organizing the nonconformance review and actions follow
- Continuous monitoring the process KPI and reporting to management, coordinate related department analyze and take corrective/preventive action if the KPI below the target,
- Coordinating the quality management review, follow and validate the continuous improvement projects identified by management review
- Preparation and accompany for customer audit and third party audit, organize the nonconformance review and corrective action following for all audit findings
- Oversee the formulation of quality systems 4 level documentation, responsible for the documents control and documents release
- Collection and filing for the daily quality document to keep the traceability and easy to be found
- Based on planning, collect and summarize the internal and external quality data to finish quality report and perform quality reporting
- College degree or above in Electrical/Electronic & Mechanical or related
- Minimum 5 years quality system experience in automotive company, familiar with the ISO9001 and IATF16949 quality system requirements,obtain the practical experience in establish, maintain and improve the quality system in plant
- Having the internal auditor certificate ISO9001,TS16949 with practical experience
- Be familiar with PPAP, APQP, SPC, FMEA, control plan, MSA, 8D process
- Good oral and writing English; Fluent use office software
- Good strong communication skill is essential, able to work with all level of people internally and externally
- Motivated, able to carry out work plan effectively, can work under pressure
18
Quality System Engineer Resume Examples & Samples
- Execute day-to-day document and engineering change requests. Review and approve requests for adequacy and compliance with the process
- Review records, procedures, work instructions, forms etc. to ensure that they are accurate, complete and compliant with the process and with the requirements of the quality management system / GMP
- Review engineering and sales data changes for accuracy and compliance with the change process
- Work with peers within Milford and across Waters’ sites to improve and harmonize change management processes
- Work with IT to understand and manage roles and workflow within change management system
- Develop, modify, apply, and maintain quality systems procedures
- Collaborate with internal customers to ensure quality standards are in place and compliant
- Support change management activities to ensure process changes are managed and approved effectively
- Minimum 4 years of experience within Quality Assurance or related field
- Experience in Document Control or Change Management
- FDA 21 CFR 820 or 211 - cGMP knowledge base in Biotechnology Industry (Biologics, Pharmaceuticals, or Medical Devices) OR
- Working experience and knowledge of quality management systems in ISO13485 or ISO9001
- Superior leadership, facilitation, and communication skills
- Ability to work independently across multiple organizations
- Good report writing and reviewing skills
- Experience using Sparta Trackwise or other electronic QMS systems
- Experience using SAP or Oracle
19
Senior Quality System Engineer Resume Examples & Samples
- Develop, implement, and sustain the Milford CAPA and internal audit process and systems to be compliant with regulatory and industry standards
- Provide subject matter expertise, support and direction for the Milford CAPA and internal audit systems
- Open, monitor, and track performance for all CAPAs. Close CAPAs when objective evidence is complete
- Coach CAPA Owners to ensure investigations are complete and documentation stands on its own during external review
- Drive failure investigations to ensure root causes are found and appropriate corrective actions are implemented to prevent repeat non-conformances
- Determine adequacy of CAPA investigations and make all necessary improvements
- Review documentation (records, procedures, work instructions, forms etc.) to ensure that it is accurate, complete, and compliant with the process and requirements of the quality management system / GMP
- Complete the yearly internal audit schedule, communicate the schedule to all affected parties, lead internal audits, ensure audit reports are issued on time, and manage follow-up activities with auditees to ensure non-conformances are addressed in a timely manner
- Collaborate with internal groups to ensure quality standards are in place and improvements are implemented according to defined plans
- Ensures that corrective measures meet acceptable standards and that documentation is compliant with all regulatory requirements
- Work across Waters’ sites to harmonize and improve Quality System processes
- Minimum 6 years of experience in Quality Assurance or related field
- Working experience with CAPA and internal audit systems
- Internal auditor experience (or supplier auditor)
- FDA 21 CFR 820 or 211 - cGMP knowledge base in Biotechnology Industry (Biologics, Pharmaceuticals, or Medical Devices)
- Working Experience and knowledge of quality management systems in ISO13485, ISO9001:2015, AS9100, or TS16969
- Demonstrated implementation of continuous improvement methodologies
- Working knowledge of ISO Quality Management Systems
- Exposure to process and/or software validation methods
- ASQ Certificate: CQE, CQA, CQT, CBA, etc
- Lead Auditor Certification and Training
- Operational Excellence/Six Sigma/Lean training or certifications
- Project management certifications (Black Belt, Green Belt, Certified Associate in Project Management (CAPM), Project Management Professional (PMP), etc)
- Experience using Sparta Trackwise or other electronic QMS system
20
Quality System Engineer Resume Examples & Samples
- Identifies and implements effective process and design control systems to support the development, qualification, and on-going manufacturing of products to meet or exceed internal and external quality and regulatory requirements
- Lead the implementation of assurances, process controls, and CAPA systems designed to meet or exceed internal and external requirements
- Act as team member in supporting quality disciplines, decisions, and practices
- Assure the development and execution of streamlined business systems, which effectively identify and resolve quality issues
- Advise management on potential improvements or enhancement to quality systems and processes in the company
21
Senior, Quality System Engineer Resume Examples & Samples
- Participate as Quality System lead on Certification / Customer Audits
- Plan, maintain and monitor internal audits
- Monitor effectiveness of Quality system
- Provide support to Sr. Management. Schedule and chair Management Review meetings
- Ensure proper documentation of meeting and that open issues are resolved
- Monitor, maintain and improve reporting customer metrics
- Publish On-Time Performance to management team
- Maintain Quality system in accordance with ISO 9001
- Determine, document and maintain QA systems: QA Manual, QSPs, Work Instructions, forms
- Create a Procedure Documentation Standard Guide to describe how process documentation should be created in all departments
- Create procedures, process flow diagrams, instructions, forms and checklists (process documentation) as required
- Works with individual departments to help them create process documentation that complies with the company’s standards
- To advise the management team on the status of Schneider Electric’s Quality System and efforts that are being implemented to improve our Quality Systems
- Disseminate and train staff on changes to Quality department documents
- Back up to the QM
- Perform all other duties as assigned or required
- Typically, at least 5 years of progressive experience, including 2 years of specialized or complex work
- ISO 9001 Auditor Leader, plus V2015
- ISO 14000 Auditor, plus V2015
- OSHAS Auditor Plus
- ISO 50000 Plus
- Green Belt Cert Plus
- 100% Leadership
22
Quality System Engineer Resume Examples & Samples
- University education, mechanical or technical
- More than 5-year experience in quality function or project management, especially in mass production (automotive industry or others)
- A strong coordination and communication skills internal and external, ability to deal with quality issues adhere to the principle of strong sense of responsibility
- Excellent spoken and written English language ability, Italian language will be a plus
- Skilled use of Pack Office software: Excel, world, PowerPoint (SAP knowledge will be a plus)
- Familiar with the ISOTS 16949 and ISO 9001 quality system requirements, VDA6.3 standard
- Familiar with mass production process and able to conducts internal audits inside organization
- To be responsible and ability to work in team
- Ability to travels
23
Quality System Engineer Resume Examples & Samples
- Work with the Divisional quality directors to drive, facilitate and support the implementation of the Danfoss TS processes
- Represent PS in Danfoss workgroups, QMS meetings and with certification bodies
- Maintain the PS QMS portal and share points
- Run regular process development workshops in PS to ensure applicability and relevance
- Provide leadership, support, coaching and training to all PS employees in the application and value of quality systems
- Capture lessons learned and process weaknesses as part of daily business and continuously improve the QMS
- Take an active role in the PS GQDT and act as a strong ambassador for the process approach
- Implement the TS audit tools and processes (internal audits)
- Drive a PS wide audit process, nominate and manage local auditors, identify process weaknesses and continually improve the QMS
- Regularly visit the facilities and FAs and complete personal audits of the systems to ensure compliance
- At least 6-10 years of Quality experience
- Bachelors degree preferably in Engineering
- Typical background from a quality function with experience as lead auditor within ISO9001/TS16949
- TS Core Tools training and experience
- Expert in TS16949 application
- TS 16949 Lead Auditor Certificate
- Six Sigma black belt
24
Quality System Engineer Resume Examples & Samples
- A minimum of a Bachelor of Science degree in Electrical Engineering or equivalent (Mechanical/Materials/Chemical/Civil/Aerospace/Computer) from an ABET accredited university; other technical degrees considered when combined with substantial Quality experience
- Minimum of 8 years of experience in automotive engineering, manufacturing, or quality
- Minimum of 3 years of experience working on electrical systems
- Ability to engage and motivate team members
- Proven ability to deliver in a fast-paced work environment with minimum assistance
- Proactive DFSS Green/Black Belt certification
- Working knowledge of GD&T and Tolerance Stack-up Analysis
25
Quality System Engineer Resume Examples & Samples
- External IATF 16949 Audits
- Internal IATF 16949 Audits – including audits conducted by ZFLS Germany
- Fulfill required responsibilities as the assigned Management Representative for the ZFLS Florence / Plymouth IATF 16949 QMS
- Determine and Conduct preparation activities for upcoming Audits
- Review Audit Non-conformances (NC’s) and Opportunities for Improvement (OFI’s) with the applicable Departments
- Review responses and determine if stated Root Cause(s) and Corrective Actions are adequate to address the NC’s and OFI’s
- Provide assistance in developing Root Cause(s) and Corrective Actions, when required
- Ensure responses to NC’s and OFI’s meet Audit Timing
- Monitor progress of the applicable Departments in implementing the Corrective Action(s) per the Audit Timing plan
- Ensure submission of final NC Responses per the Audit Timing Plan
- Escalate issues that may prevent Audit Responses from meeting the Timing Plan
- Conduct and coordinate Pre-Audits as required by the TS Registrar, Bosch Automotive Steering Germany, or Customers
- Conduct proactive audits of processes or areas that have known QMS weaknesses
- Review Bosch Automotive Steering Corporate Guidelines and Directives to determine applicability to Bosch Automotive Steering Florence / Plymouth