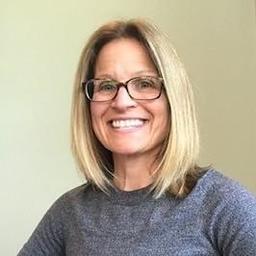
Kate Hatem-Pritchett
Manufacturing & Supply Chain Director
Summary
A highly accomplished ‘forward-thinking’ Manufacturing & Supply Chain Director with over twenty years of progressive success guiding performance improvement and building cultures and teams that optimize plant operations to meet performance and financial goals. Respected as a visionary leader who champions people and processes to seamlessly deliver multiple projects, foster and train teams in continuous improvement, lean manufacturing and leadership development that improves profit and performance.
Experience
Director Of Manufacturing Operations
XL Fleet Corporation / Quincy, IL
Led manufacturing operations, site safety, quality output, performance, team development. Developed and implemented standard work.
- Led manufacturing operations, production, fulfillment, and warehousing of $15M inventory.
- Oversight of shipments from 3 site facilities with full Manufacturing and SOX compliance.
Director of Operations
Ascend Illinois / Barry, IL
Lead facility operations, safety, quality, compliance, performance, and people for facility in rapid team, product, and equipment growth.
- Managed budget, production, and capacity planning to meet sales demands. Drove production revenue from $2.75-5.6M.
- Implemented operations standards for safety, QA, team performance and continuous improvement principals.
- Implemented policies and processes for facility for pay equity, leader roles, document control, and Covid-19 protocols.
Site Safety Manager: Human Safety
General Mills / Hannibal, MO
Site coach and resource to set up Site Central Safety Committee including safety observations, incident investigations, risk assessment.
- Analyzed incident data and behavior patterns to eliminate risks. Led post-incident care and response from first-responder program.
- Developed and lead safety training, culture change, safety leadership behaviors and OSHA requirements.
General Mills
Site Zero Loss Culture Manager: Continuous Improvement & Human Safety
General Mills / Hannibal, MO
Leader of Zero Loss Culture Implementation for site, including creating and implementing site. Led culture change and continuous improvement and human safety leadership. Ensured CI practices and processes ae rolling out Line-centric teams across site.
- Influenced and created change in plant operations, leadership teams, organizational redesign, structure implementation.
Manufacturing Manager
General Mills / Hannibal, MO
Lead operations, operators, mechanics, and professional staff of 125, ensuring safety of all team members, production of safe high-quality foods, executing multi-million-dollar annual budget.
- Led 3 years performance results of zero OSHA incidents and under financial budget performance. Managed strategy of monthly development sessions.
- Led multiple equipment installations and product line expansions.
Manufacturing Team Leader & Continuous Improvement Roles
Multiple Front / Hannibal, MO
Lead operations, operators, mechanics, and professional staff of 125, executing department annual plan and budget.
W. R. Grace, Manufacturing Leadership Program Chicago, IL
Led plant transition to commercialization of VERIFI, led union employees, human safety, quality control, drove new delivery model. Developed freight tracking system that saved $456K
Education
Procter & Gamble Autonomous Maintenance (AM) College
Certification
| Procter & Gamble Autonomous Maintenance (AM) College
| Six Sigma Certification, Six Sigma Green Belt
| Dupont Safety Culture
| Procter & Gamble Reliability Technology
| Penn State University Executive Programs, Managing Effective Supply Chain
| Negotiation
| Front Line Leadership
| Interpersonal Skills
| MS Office, Project, MRP Systems, ERP Systems, Acumatica, SAP
Rensselaer Polytechnic Institute
B.S. in Chemical Engineering, Chemical Engineering
B.S. in Chemical Engineering, Rensselaer Polytechnic Institute, Troy, NY