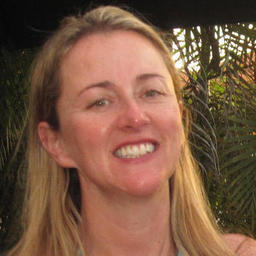
jane Martin
Senior Director Sourcing; Product Development, Fabric Development and Quality.
Summary
I am an innovative, highly experienced product development and quality assurance executive with an expertise in textile and garment development and sourcing, implementing sustainable sourcing practices for global companies and driving cost efficiency. I have 15+ years of experience in manufacturing with a track record of success in creating and executing sourcing strategies and developing and scaling design into mass production for brands. I am passionate about problem solving for sustainability and quality. My specialties include a deep knowledge of fibers and fabric development, quality process and protocol creation, and all aspects of garment creation and production.
Experience
Senior Director of Sourcing; Quality Strategy,Operations and Product Development
Old Navy / San Francisco
Led development and implementation of the Quality Vision, Strategies, and LRP informed by Product LRPs, Commercial Plan and Customer Insights. Managed the quality process for 550M units annually.
Established policies and procedures to ensure products were developed and manufactured consistently within Gap Inc quality standards and regulations, proactively addressing issues.
Led engagement with Merchandising, Design and Production teams to ensure aligned understanding of strategies, process and expectations on each function to support, driving accountability and collaboration cross-functionally for product to be developed and delivered within these guidelines.
Spearheaded engagement with Sourcing Teams to investigate and resolve issues in fit, fabric, and garment execution, developing processes to support timely and sustainable issue resolution.
Developed and implemented Gap Inc.’s Voice of the Customer (VOC) model and reporting for mining and interpreting customer feedback and identifying quality issues and quality wins across 60K-80K customer reviews per month; initiated and drove action plan to address issues and apply learnings to future product development, reducing in-market issues 45%.and increasing positive brand reviews 15%.
Drove continental feedback loop on product quality and fit using reporting developed utilizing text analytics and sentiment which mined actionable customer insights and track performance improvements for product teams.
Developed and led implementation of Brand quality initiatives (aligned on by Brand Leadership) for Old Navy to deliver strategies; initiatives included Denim for Family, Performance Active Bottoms, Women's Dresses and Sweaters, driving 10% increase in positive quality reviews.
Conceptualized new performance standards and made updates to testing protocols and SOPs across all product categories as a response to customer insights, enabling GAP Inc to have best in class standards and remain cutting edge in fabric and garment innovation.
Drove product teams to make informed decisions that were better aligned with customer, resulting in cost savings.
Managed risk review and resolution of all production issues related to quality / fit in bulk production which contributed to decrease of quality issues in market and improvement in fit ratings.
Led investigation and resolution of brand’s quality issues in fit, fabric, and garment execution, developing processes to support sustainable issue resolution.
Drove Old Navy to garner highest percentage of positive reviews and highest percentage of star ratings across all of Gap Inc., increasing positive reviews 6%, and negative reviews decreased 2%.
Senior Director of Fabric Development,Sourcing Strategy and Quality
Old Navy / San Francisco
Led team of 15 associates responsible for sourcing and delivery of on trend raw materials and products that met brand’s cost, aesthetic, and quality goals across all product categories. Managed $1B of sourced product / 400M yards worth of fabrics and yarns each year. Built and implemented internal quality processes, standards, reporting, and metrics.
Drove fabric strategy and sourcing for $120M worth of fabric annually, controlling end-to-end process for quality on product.
Led fabric trend reporting, increasing performance of platformed fabrics across Old Navy from 48% to 72%; drove cost savings of $10-$16M annually through counter sourcing (identifying cost effective options without sacrificing quality) and fabric consolidation.
Created products utilizing more sustainable sources: current 40%+ garments using Better Cotton Initiative (BCI) cotton, 60% of denim using water saving techniques on path to meet goals of 100% of cotton used purchased from a sustainable source by 2022 and 100% of denim using water saving techniques by 2022.
Drove consolidation of fabric bases, generating $10M of annual savings.
Delivered sustainable initiatives for raw materials and finished productsDirector of Quality Management
Gap Inc / San Francisco
Owned evaluation and management of specific In-Market Investigations and Escalations from Brand Quality Management (QM) leads and other internal and external sources. Created, developed, and implemented in-market issue, escalation, and resolution processes / standard operating procedures (SOP).
Managed team of 7 and developed SOPs, introducing best quality and testing practices across multiple brands.
Developed standardized actionable quality reporting across brand as well as monthly reports on issues with action items, using customer feedback to create products wanted and enabling a much better connection to what customers were portraying in feedback provided.
Revised Gap Inc. testing manual, developed and negotiated new testing packages and pricing which kept standards current and up to date with changing trends in fabric bases and product types, avoiding product failure for customers.
Created and executed Gap Inc.’s distribution center audit process to align with company goals by developing and implementing in-market issue and chargeback processes utilized across Gap Inc.